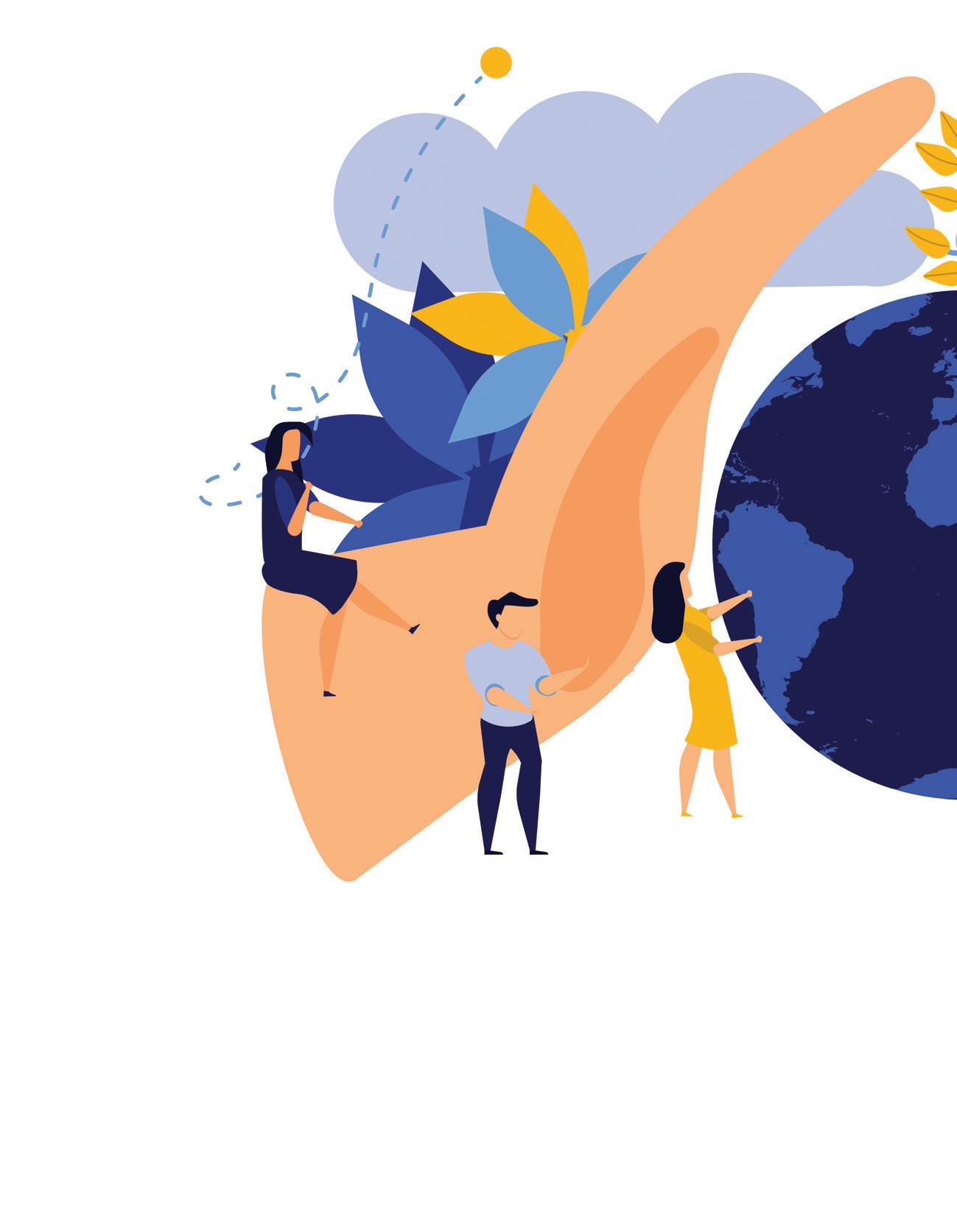
37 minute read
Nuestro Entorno
Nidec Global Appliance Se une a la celebración del Día Internacional de la Preservación de la Capa de Ozono
Con información de: Nidec Global Appliance imágen de: 123RF
Cada 16 de septiembre se celebra el Día Internacional de la Preservación de la Capa de Ozono, el cual fue instaurado con la firma del Protocolo de Montreal en 1971, relativo a las sustancias y acciones que agotan la capa de ozono. De acuerdo a la Organización de las Naciones Unidas sustituir el uso de hidrofluorocarburos y aumentar la eficiencia energética en la industria de la refrigeración, es ampliamente recomendable para contribuir a la reducción de dióxido de carbono que ayuda a proteger el ozono.
El Programa de las Naciones Unidas para el Medio Ambiente indica que unos 3,600 millones de equipos de refrigeración están en uso actualmente, y la demanda aumenta a medida que las temperaturas incrementan por el calentamiento global. Si para el 2050 toda la población del mundo tuviera acceso a este servicio vital para preservar los alimentos y las vacunas -como la esperada para la cura del Covid19-, se necesitarían hasta 14,000 millones de equipos.
Ante este panorama, la organización espera que gracias a diferentes tecnologías que ayudan a generar la eficiencia energética de la industria de la refrigeración y los electrodomésticos, se pueda reducir entre 210,000 y 460,000 millones de toneladas de emisiones de dióxido de carbono en las próximas cuatro décadas.
Es así, como cada día más empresas están involucrando en sus productos tecnologías que cuiden el medio ambiente, ayudando a bajar el consumo de energía y químicos dañinos. Una de ellas es Nidec Global Appliance, a través de su marca de compresores Embraco, quien desde 1971 ha sido referencia mundial en innovaciones para el sector de la refrigeración, ofreciendo soluciones con uso de tecnología que supera las demandas más desafiantes del mercado, siendo pionera en fomentar el desarrollo temprano de compresores con tecnología inverter y refrigerantes naturales.
“La creciente búsqueda por sistemas de refrigeración con mayor eficiencia energética y uso de refrigerantes naturales es derivada de nuestra motivación por lograr nuestra aportación al cuidado del medio ambiente a través del uso de tecnologías responsables que además aportan mayor fiabilidad a nuestra industria”, comentó David Ramírez, Ingeniero de aplicaciones en Soporte Técnico de Embraco.

En este contexto es que Nidec Global Appliance ha desarrollado compresores con tecnología inverter o velocidad variable, que combinados con el uso de refrigerantes naturales se han convertido en la opción para empresas que buscan ofrecer a sus clientes opciones altamente responsables con el cuidado del planeta y el ozono.
Los compresores inverter ofrecen una serie de beneficios que pueden conducir a una mayor vida útil del equipo de refrigeración, estabilidad de temperatura y ahorro de energía.
En el marco de la celebración del Día Internacional de la Preservación de la Capa de Ozono, Nidec Global Appliance refuerza su compromiso con al planeta para ofrecer soluciones con una alta eficiencia energética y reducción de gases dañinos, siendo esto un imperativo estratégico para todos sus colaboradores, que trabajan continuamente para encontrar formas de reducir el impacto ambiental durante todo el ciclo de vida de sus productos.
Por su parte, Embraco siempre está a la vanguardia cuando se trata de innovación. Siempre pensando en el mañana, tiende puentes hacia el futuro a través de sus laboratorios y profesionales que se dedican a trabajar y anticipar las tendencias, previendo las necesidades futuras del mercado y la sociedad, preparándose para satisfacerlas.
Hay una cautela cada vez mayor en el mundo sobre el peligro de instalar equipos sobre montajes flexibles en zonas sísmicas sin el apropiado refreno. Además los sistemas de aire acondicionado montados en las instalaciones militares sufren los efectos de las explosiones cercanas de bombas. Estas fuerzas son similares a las producidas por los terremotos. Cuando tiene lugar un terremoto o la explosión de una bomba, el suelo se acelera a través de una serie de frecuencias. El daño no ocurre tanto como por la fuerza del terremoto en uno o múltiples impulsos como por la introducción de una particular frecuencia del terreno que tiene suficiente energía como para hacer vibrar y por último resonar o el edificio entero o la maquinaria que haya en él. Los grandes desplazamientos por resonancia causan sobre esfuerzos y fallas. Un espectro de respuesta es una curva dibujada con papel logarítmico que describe un terremoto o una explosión de bomba. La forma de la curva depende de la intensidad, frecuencias del suelo, elevaciones de una estructura, etc. La figura 1 es una curva típica y no para usarla en ninguna aplicación especifica. El eje horizontal se refiere a la resonancia o frecuencia natural del objeto afectado por el terremoto. El eje diagonal que llega hasta la esquina superior derecha muestra las máximas aceleraciones a las que se sujeta el objeto. Los ejes de los ángulos a la derecha de este leen el desplazamiento del objeto en relación al suelo o el soporte rígido.
Superpuestas a estas escalas están las curvas de respuesta. Las tres curvas indican 0, 1 y 2 % de amortiguación crítica. Valores más altos son inusuales; esta curva en particular se refiere a un espectro de respuesta de 0,5 g por encima de una resonancia de 40 Hz.
Ahora veamos cómo se comportaría un equipo con diferentes frecuencias naturales durante un terremoto descrito por estas curvas. La referencia de la curva de amortiguación O muestra las condiciones más extremas.
Si el objeto a estudiar tiene una frecuencia natural de 1 Hz se comienza en la parte inferior de la carta en 1 Hz y se mueve verticalmente hasta interceptar con la curva de respuesta en el punto A. Moviéndonos al extremo derecho desde el punto A, la velocidad es de 55 pulg. (1.375 mm)/s.
Siguiendo la línea de desplazamiento en Figura 1 Espectro de respuesta
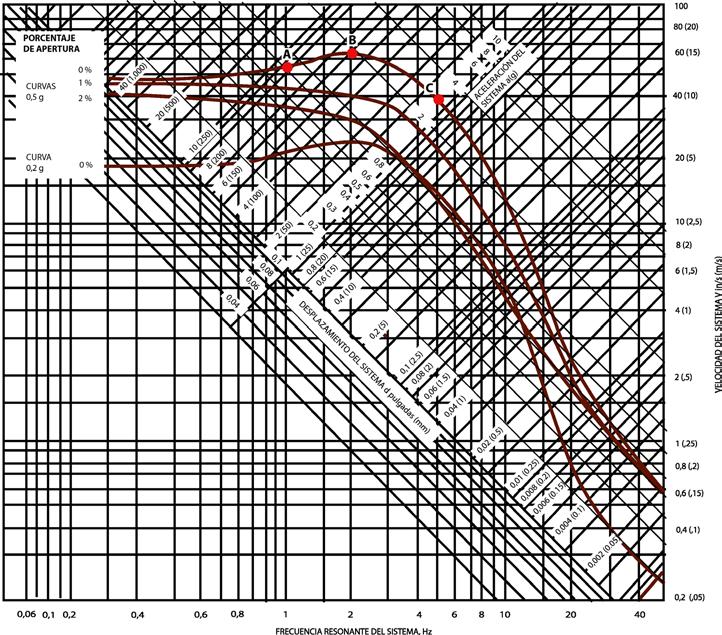
diagonal bajando hacia la izquierda, vemos que el desplazamiento es de 9 pulgadas (225 mm). Siguiendo la línea de aceleración hacia abajo y a la derecha, vemos la aceleración en 0,9 g. Si posteriormente consideramos una frecuencia natural de 2 Hz. y trabajamos desde el punto B, la velocidad máxima sería 62 pulgadas (1,550 mm)/s, el desplazamiento 5 pulg. (125 mm) y la aceleración máxima de 2 g; con una frecuencia natural de 5 Hz, punto C, la velocidad máxima sería 38 pulgadas (950 mm)/s, el desplazamiento 1,2 pulg. (30 mm) y la aceleración máxima de 3 g. Con 25 Hz, punto D, el área es asintónica con una velocidad máxima de 0,6 g. Hay que notar que los valores varían ampliamente como se dijo antes, dependiendo de la frecuencia natural del objeto expuesto a este terremoto particular.
Volviendo a la referencia del punto A, el desplazamiento de de 9 pulgadas puede muy bien partir o estirar el muelle. este punto puede resaltarse en referencia a un sistema con una frecuencia de resonancia de 0,4 Hz. Siguiendo el mismo procedimiento que para los puntos A, B y C pero sólo en referencia al desplazamiento, podemos ver que la amortiguación 0 el desplazamiento de resonancia que provoca el fallo y hace impracticable cualquier tipo de conexión flexible. Para proteger el equipo de montaje sobre elásticos contra esos sucesos, es más importante introducir un mecanismo de frenado elástico (figura 2) para limitar las fuerzas de aceleración y controlar amplitudes. Estos mecanismos de frenado están fabricados con espacios de aire para que durante el trabajo normal (sin terremotos) no interfieran con el circuito de vibraciones.
La mayoría de los códigos antiguos exigen el frenado sólo en términos de capacidad estática. El suministrador sólo necesita someterse a cálculos mostrando que si las fuerzas actúan a través del centro de

gravedad en diverso grado, el mecanismo de anclado o frenado soportará algunas fuerzas estáticas definidas como 0,5 g, 1 g, etc. El mejor método (que pasará a ser estándar) es un estudio dinámico ya que un terremoto no es suceso estático.
Todo equipo tiene un nivel de fragilidad; por definición, nivel de fragilidad significa que soportará una fuerza de tantas g en cualquier dirección y aún permanecerá operativo. El transporte normal sujeta al equipo hasta a 5 g y en ocasiones y en raras ocasiones incluso a 10 g. Por tanto, un standard de protección arbitrario de exposición máxima de 4 g es aceptable, o alguna fuerza g menos si el fabricante advierte que el equipo es incluso más frágil. El diseño sísmico se limita entonces a nivel de fragilidad de esa pieza concreta del equipo. Se realiza un análisis computarizado en todos los grados y se ha demostrado que el mecanismo elástico frenado no sólo permanecerá en su sitio, sino que las fuerzas en el equipo serán de 4 g o menos. El equipo se mantendrá entonces operativo durante y después del terremoto.
A continuación, se toma como ejemplo el análisis del estudio de los Estados Unidos de América, país desarrollado en este tipo de investigaciones. No dudamos que algún país latinoamericano esté desarrollando y aplicando este sistema de trabajo para su país; sin embargo la mayoría no cuenta con lo que a continuación trataremos.
Las siguientes especificaciones típicas describen tanto este tipo de freno como el sistema computarizado que puede especificarse con él. En esta especificación las zonas sísmicas se muestran en el mapa de zonas sísmicas de los EE.UU. del código de edificios uniformes (figura 3). Desafortunadamente, las zonas no se describen en términos de niveles de g sino solo en términos de daños. Figura 2 Mecanismo de frenado
Las zonas en este mapa se definen numéricamente de 0 hasta 3. La zona 0 donde no se producen daños por un terremoto; en la zona 1 daños menores, en la zona 2 daños moderados y en la zona 3 daños importantes. Por ello, en todas las zonas que no sean 0, parece que deberían hacerse algunas precisiones sísmicas y cómo el espectro de respuesta tendrá valores mucho mas bajos en la zona 1 que en la 3, la aproximación básica al problema sigue igual. Es interesante resaltar lo pequeña que es en los EE.UU. la zona 0.
ESPECIFICACIONES SÍSMICAS
La especificación I se propone para los edificios donde se dispone de las curvas de respuesta sísmica en todos los niveles. Este es normalmente el caso de los grandes edificios en la zona 3 y en los equipos de instalaciones militares.
La especificación II incluye estructuras más modestas, donde no se dispone de estos datos de diseño y posibles aplicaciones a grandes estructuras en las zonas 1 y 2. La especificación II es una mejora definitiva de la aproximación estática al problema y ciertamente representaría una mejora en el régimen de esfuerzo por parte del consultante.
Un consultante mecánico tiene la opción adicional de usar las especificación I y proporcionar las curvas de respuesta típicas propuestas por una autoridad sísmica más que las curvas de respuesta específicas calculadas para un edificio particular. Las especificaciones sísmicas son suplementarias a las necesidades de control de las vibración.
Especificación I: Especificación de freno sísmico utilizando datos del espectro de respuesta
Todo equipo aislado de la vibración se montará en estructuras de acero rígidas o bases de hormigón como se describe en las especificaciones de control de la vibración a menos que el fabricante del equipo certifique capacidad de sujeción directa. Cada base montada en muelles tendrá in mínimo de 4 frenos sísmicos dirigibles de doble efecto y colocados cerca de los aislantes de vibración si es posible para facilitar el enganche tanto a la base como a l estructura (figura 4). Los frenos consistirán en piezas de metal engranadas refrenadas por materiales
0 1 2 3
Sin daños
Daños menores
Daños moderados
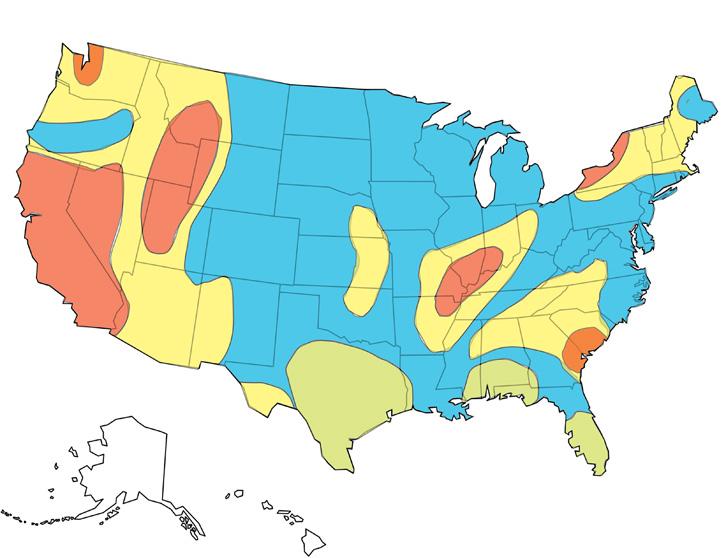
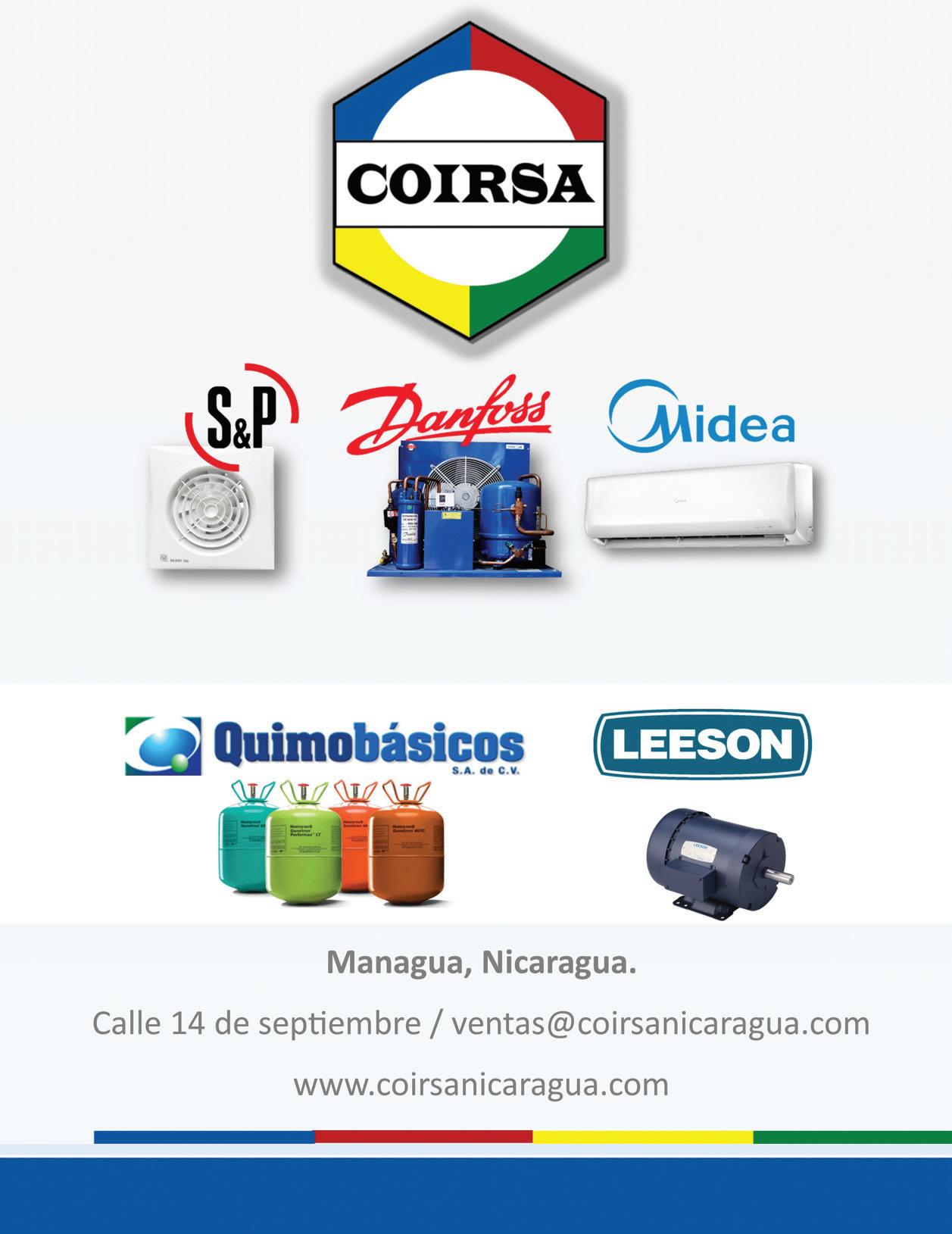

de caucho absorbe impactos montado en soportes de puente como se expone en la tabla 1.
Los materiales elastómeros serán reemplazables y de un grosor mínimo de 3/4 pulgadas (19 mm). Se incorporará un espacio de aire mínimo de 1/8 pulgadas (3 mm) en el diseño del freno en todas direcciones antes de que se realice el contacto entre las superficies rígidas y elásticas. Los frenos se instalarán de fábrica; las referencias incluirán curvas de flexión de carga hasta 1/2 pulgadas (12,7 mm) de flexión en los planos X, Y y Z. Los tests de destrucción se realizarán en un laboratorio independiente o bajo la supervisión de un ingeniero registrado independiente. Los ensamblajes del freno se atornillarán a la máquina de test con el freno normalmente instalado. Los informes del test certificarán que ni los elementos de neopreno en el cuerpo del freno sufren una deformación evidente tras realizar una carga de 1/2 pulgadas (12,7 mm) de flexión.
La selección del freno sísmico particular se basará en un análisis dinámico completo proporcionado por el vendedor basado en datos de respuesta sísmica.
El informe de computadora incluirá la siguiente información en los ejes X, Y y Z: Figura 4 Base montada sobre muelles con freno
1.- Las seis frecuencias naturales del sistema con y sin frenado. 2.- Los movimientos más probables (valores en raíz cuadrada o rms) en todos los montajes de vibración o combinación de montaje y freno y en puntos remotos como conexiones de conducto, tuberías y eléctricas y en los extremos de la máquina. 3.- Aceleraciones máximas en el centro de cada elemento significativo del sistema como en el motor, ventilador, compresor, intercambiador de calor o bombas y en las ubicaciones de los montajes o combinaciones de montajes y freno, todo expresado en unidades g. 4.- La fuerza más probable (valores (rms) en cada montaje o combinación de montaje y freno expresada en libras (kg).
la aceleración no exceda 4 g o el recorrido desde el centro 5/8 pulgadas (16 mm) en los frenos.
Cuando los análisis muestren que ocurren niveles mayores a 4 g en los frenos a causa de una amplitud máxima permitida, el vendedor propondrá un sistema de montaje alternativo basado en análisis dinámicos adicionales que mantendrán el nivel de 4 g. Se aceptará por el consultante el nivel g más elevado o el método alternativo.
El análisis será la lectura de un programa computarizado en el equipo esquematizado como un cuerpo rígido simple tridimensional compuesto por varias masas rígidamente anclados. Para el objetivo del análisis de cada soporte, la combinación no lineal del muelle aislante-freno puede sustituirse por un muelle lineal simple equivalente que depende de la amplitud del desplazamiento. El sistema debe ser conservador y tener seis frecuencias y modos naturales.
Los valores finales se obtendrán como combinación de las respuestas del modelo en forma de un valor “más probable” (rms de seis modos) y un valor “superior” suma de los valores absolutos de seis modos.
Especificación II: Especificación de freno sísmico sin datos del espectro
Es el propósito de la especificación que
Todo equipo aislado de la vibración se montará en estructuras de acero rígidas o bases de hormigón como se describe en las especificaciones de control de la vibración a menos que el fabricante del equipo certifique capacidad de sujeción directa. Cada base montada en muelles tendrá un mínimo de 4 frenos sísmicos dirigibles de doble efecto y colocados cerca de los aislantes de vibración si es posible para facilitar el enganche tanto a la base como a la estructura (figura 4).

(a)
Durómetro
40 ± 5
40 ± 5
40 ± 5
Propiedades físicas orginnales (b) (b)
Fuerza tensora (min)
Lb/pulg 2 (kg/cm 2 ) Extensión en la rotura (min)
2.000
2.500
2.500 (140) (175) (175) 450 %
400 %
350 % (c) Test de envejecimiento (d)
Envejecimiento al horno 70 h/212 ºF (100 ºC)
Dureza (máx)
Fuerza tensora (máx) Extensión de la rotura (max)
+15 %
+15 %
+15 % ±15 %
±15 %
±15 % -40 %
-40 %
-40 %
Ozono en aire 1 ppm en volumen. Esfuerzo a 100 ºF Sin ruptura Sin ruptura Sin ruptura
(e)
Equipo compresor 22 h, 70 ºC, métodp B
30 % (máx.) 25 % (máx.) 25 % (máx.)
Los frenos consistirán en piezas de metal engranadas refrenadas por materiales de caucho absorbe impactos montado en soportes de puente como se pone en la tabla 1.
Los materiales elastómeros serán reemplazables y de un grosor mínimo de 3/4 pulgadas (19 mm). Los frenos se fabricarán con un espacio de aire entre el material duro y el elástico de no menos de 1/8 pulgada (3 mm) y no más de 1/4 pulgada (6,4 mm). Los frenos se instalarán de fábrica con huelgos.
La capacidad de freno sísmico en un flexión de 3/8 pulgada (9,5 mm) será de 3 a 4 veces la carga asignada al grupo de montaje en esa área inmediata. Las sugerencias incluirán curvas de flexión de carga de hasta 1/2m pulgadas (13 mm) de flexión en los planos X, Y y Z. Los test se realizarán en un laboratorio independiente o bajo la Tabla informativa
TACO DE GOMA que se mantiene fuera del hormigón durante el vertido. Eliminar el taco una vez que se ha vertido el hormigón. Atornillar la rosca de ajuste en el encastrepara elevar el suelo
supervisión de un ingeniero registrado. Los ensamblajes del freno se atornillarán a la máquina de test con la instalación normal de freno. Los informes del test certificarán que ni los elementos de neopreno ni el cuerpo del freno sufren ninguna deformación evidente tras la realización de la carga.
TEORÍA Y MÉTODOS
Una vez que se ha comentado completamente el problema de la vibración, podemos preocuparnos de la transmisión de sonido a través de paredes, suelos y techos. Esto ocurre cuando un edificio no tiene suficiente resistencia a la transmisión de sonido para aguantar el ruido de transmisión aérea en oposición al ruido transmitido mecánicamente. El ruido de transmisión aérea es sonido irradiado desde un equipo mediante pulsaciones del aire. Esta presión variante del aire mueve los suelos y paredes de manera muy parecida al cono de un altavoz. Cuando los componentes de un edificio no tienen la suficiente masa, la amplitud se mantiene con la suficiente fuerza para radiar el sonido al otro lado del elemento arquitectónico con intensidad suficiente para ser molesto. El problema podrá solucionarse aumentando la masa de los componentes pero esto normalmente es imposible ya que incluso la construcción de hormigón de 12 pulgadas transmitirá ruido apreciable si los niveles de sonido son lo suficientemente altos en la sala de máquinas.
Un segundo método se ha hecho más práctico, es el sistema de suelo flotante, usando encima o debajo de las salas de máquinas dependiendo de la necesidad del espacio silencioso. En la mayoría de los casos, las salas de máquinas están en el tejado y el mayor problema es debajo. Un suelo flotante consta de un suelo de hormigón secundario, normalmente de 4 pulgadas
Figura 5 Aisladores del sistema del suelo flotante (1pulg. = 24,4 mm)
PATILLA DE CAUCHO sobresale sobre el vertido Los agujeros de relleno se enrasan una vez que el suelo se ha levantado SUELO FLOTANTE
ENCASTRES 1337 Las piezas de fundición están codificadas por colores BARRAS o MALLAZO según se requiera PLACA DE ACERO
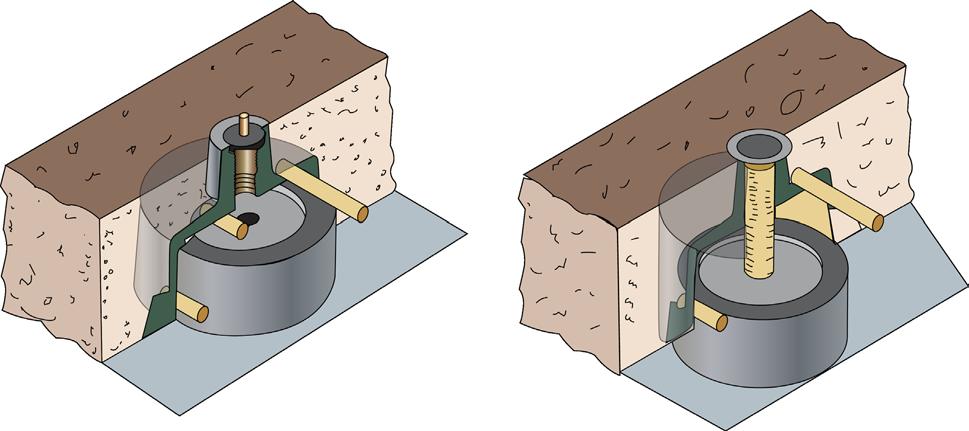
Plancha de polietileno o superficie de separación del hormigón Rosca de ajuste y de 3/4-10 NC
Elemento con especificaciones de AASHO
Figura 6 Desagüe de suelo flotante

de grosor, separado de una estructura principal del edificio de aire y soportado por elemento elásticos. La introducción de esta construcción puede elevar el valor teórico de un suelo de hormigón normal de 6 pulgadas desde un STC de 54 a un STC de 79 si se eliminan todas las viñas laterales.
ESPECIFICACIÓN
Una especificación típica usando un método de elevación de losa es como sigue:
A) Objetivo:
• Aislar suelos flotantes de la estructura del edificio por medio de aisladores prensados y reborde de aislamiento del perímetro.
B) Materiales:
• Hojas o planchas de plástico: grosor 1,52 mm • Aislantes (fig 5) Encastres de hierro colado acampanado completado con gatos de acero de 3/4 pulgadas de diámetro mínimo y aislantes de neopreno de grado de soporte de puente de 2 pulgadas de grosor cumpliendo las propiedades de la tabla 1. Las flexiones no sobrepasarán de 0,3 pulgadas y la frecuencia dinámica de 10 Hz, a través de toda la escala de carga. Los encastres metálicos de paredes ligeras o materiales aislantes que requieren recubrimientos protectores no son aceptables. • Reborde de aislamiento de perímetro: grosor 3/4 pulgadas de fibra de vidrio de 10 lb/pies 3 o esponja de neopreno de 1/2 pulgada. • Compuesto de retocado: de grado de fluencia, no secante, no sangrante, no endurecedor. • Desagües de suelo flotantes (figura 6) cubiertas en cazoleta de hierro colado con rejas de hierro colado y flancos largos para cubrir las aperturas de estructuras completadas con anillo de presa a prueba de agua. • Sellos elevadores (figura 7) cilindros de acero que contienen esponja de neopreno para suelo flotante y de estructura.
C) Procedimiento de construcción del sistema de suelo:
• Proporcionar pedestales de hormigón 10 pulgadas de alto, soportados por la estructura principal para todos los equipos mecánicos de 75 hp (60 kW) y más. Los pedestales individuales pueden usarse como pies de refrigeradores. • Colocar los desagües a prueba de agua y sellos del entubado inferior con especificaciones contra el agua. • Cementar el reborde aislante del perímetro alrededor de todos los pedestales, paredes, columnas, sujeciones, etc. • Cubrir el área entera del suelo con hoja o plancha de plástico de 1,52 mm y llevar la hoja o plancha por encima del borde aislante del perímetro. • Tapar todas las juntas con trencilla a prueba de agua. • Colocar los encastres acampanados en una distancia máxima entre centros de Figura 7 Sello elevador de suelo florante esquemas preparados por el fabricante del aislante. • Colocar el refuerzo como se muestra en las figuras anteriores y extender por el suelo. • Después de que el hormigón haya
fraguado completamente, desplazar el equipo por el suelo y colocarlo en los pedestales de hormigón o en los encastres forrados que se exigieron en el punto 1. • Elevar el suelo 2 pulgadas mediante los gatos de acero. Si la secuencia de construcción ordena elevar el suelo antes de colocar la maquinaria, debe usarse un entarimado grueso para proteger el suelo mientras la maquinaria se coloca en posición. 48 pulgadas de acuerdo estricto con los
• Rebajar el reborde de aislamiento del perímetro en toda su extensión. • Rellenar con cemento.
D) Ofertas
• Curvas de flexión y carga de todos los aislantes. • Certificación del compuesto de neopreno según las especificaciones. • Datos de test que verifiquen una frecuencia dinámica máxima de 10 Hz. • Datos de test acústico de un laboratorio independiente mostrando mejoras mínimas. • Datos de test de la estructura del suelo flotante con refuerzos menores o específicos.
E) Fabricante:
• La colocación de todos los materiales aislantes y el levantamiento de los suelos se realizará por o bajo la supervisión del fabricante del aislante.
Los consultores acústicos y los fabricantes de material para control de vibración pueden ofrecer asistencia similar para aumentar la disminución en transmisión de sonido a través de paredes y techos.
En este artículo analizaremos un tema muy importante en los sistemas de Aire Acondicionado y la Refrigeración que tiene que ver con la presencia de aire en el interior de un condensador enfriado por aire. Como bien sabemos, el condensador es el encargado de llevar a cabo la condensación del refrigerante en pocas palabras es el encargado de hacer cambiar de fase al refrigerante del estado gaseoso al estado líquido. Es por esto, que el condensador debe estar libre de cualquier tipo de impurezas, humedad y aire ambiente para ello como bien sabemos es importante realizar un barrido total y un buen proceso de vacío para eliminar sobre todo la humedad interior y evitar la presencia o atrapamiento del aire exterior en el interior de los tubo que conforman el condensador. A continuación describiremos temas importantes referentes a un condensador los cuales son:
EXCESO DE REFRIGERANTE…
El exceso de refrigerante en un sistema de refrigeración tendrá como resultado un aumento en la presión de descarga o de condensación del sistema además, de un aumento en la temperatura de condensación y por consiguiente una alta caída de temperatura en el condensador lo cual, es muy perjudicial para un sistema de enfriamiento ya sea de aire acondicionado o de refrigeración (media o baja temperatura) ya que con altas temperaturas el desgaste de los componentes internos del compresor y el aceite lubricante se desgastarán prematuramente provocando la falla de su compresor y con el problema principal de que la temperatura deseada en su o sus cámaras NO se lograran abatir.
Los límites de temperaturas que se emplean para determinar las caídas de temperatura en un condensador son de 10.0 °C a 16.0 °C para condensadores de equipos de aire acondicionado y de media temperatura y de 5.0 °C a 8.0 °C para condensadores de equipos de baja temperatura.
Una alta caída de temperatura principalmente se debe a que muy probablemente se tiene una restricción de flujo de aire. Cuando el aire se restringe en los serpentines del condensador, el refrigerante no se enfría apropiadamente causando con ello una presión mayor que la esperada. Igualmente la temperatura de condensación será más alta por lo cual, la caída de temperatura será más alta que lo normal; este problema se puede deber a las siguientes causas: • Paso entre aletas obstruidas (serpentín condensador sucio). • Motor ventilador defectuoso. • Descarga del aire de los motores ventiladores descargando en sentido contrario a la corriente del aire ambiental.
“Importante: cuando cicle los motores ventiladores de un condenador enfriado por aire, siempre los motores ventiladores más próximos al cabezal de entrada al condensador DEBEN siempre estar permanentemente funcionando por la simple razón que se requiere que inmediatamente en cuanto entre el gas caliente al condensador, este inicie su condensación”.
Cuando no hay tanque recibidor de refrigerante, la sobrecarga de refrigerante se puede determinar midiendo la temperatura de condensación y la temperatura del refrigerante líquido saliendo del condensador. Si la diferencia entre ambas temperaturas es mayor de 3.0 °C; el sistema se encuentra muy probablemente sobrecargado de refrigerante.
Invariablemente cuando un sistema se encuentra sobrecargado de refrigerante, la temperatura de líquido a la salida del condensador será menor que la temperatura de condensación y a medida que esta sobrecarga sea mayor, también será mayor la diferencia entre ambas temperaturas.
“La presencia de aire en el interior del condensador provoca una alta caída de temperatura en dicho condensador”. Otro tips importante de la presencia de aire en el interior del condensador que que cuando colocamos un manómetro en el condensador o línea de líquido; la aguja experimentara una cierta vibración saltando o moviéndose de un lugar a otro (presión mayor a presión menor) no registrando una presión estable.
COMO DETECTAR LA PROBABLE PRESENCIA DE AIRE EN EL CONDENSADOR…
Si el equipo se encuentra funcionando, se debe realizar los siguientes pasos: 1. Detener la unidad condensadora. 2. Cerrar válvula de paso de la línea de líquido ya sea tipo bola o del tanque recibidor de refrigerante. 3. Poner a funcionar el motor o motores ventiladores del condensador. 4. Instalar un manómetro en la descarga del compresor (válvula de servicio de descarga del compresor). 5. Esperar el tiempo necesario para que se estabilicen las condiciones de operación del sistema y tomar o registrar la presión registrada por el manómetro y con la ayuda de la tabla presión – temperatura obtener la temperatura que le corresponda a dicha presión de condensación. Posteriormente registrar la temperatura del aire exterior entrando al condensador. 6. Realizar la diferencia (resta) entre las dos lecturas de temperaturas descritas en el paso No. 5. 7. Comparar el resultado obtenido en paso No. 5, si no existe aire o gases
No condensables en el interior del condensador, el resultado debe estar entre 1.0 °C y 2.0 °C.
Cuando se detiene un compresor, el flujo de refrigerante cesa, y como resultado la temperatura y presión de condensación disminuyen gradualmente. De igual forma, con el condensador aislado (como se menciona en paso No.2), la presión de refrigerante dentro del serpentín del condensador disminuirá poco a poco.
“Es importante recordar que si existiera aire o gases no condensables en el sistema (condensador principalmente), la temperatura correspondiente a la presión de un condensador aislado, será mayor que la temperatura del aire ambiente exterior; dando como resultado la disminución de la capacidad calorífica de los equipos de refrigeración”.
EFECTOS DEL ACEITE EN EL FUNCIONAMIENTO DEL CONDENSADOR…
El aceite lubricante acumulado en el interior de los tubos del serpentín del condensador produce los siguientes efectos: • Reduce la capacidad de transferencia de calor. • Reduce la capacidad volumétrica del condensador y a su vez reduce la cantidad de refrigerante haciendo asimismo, que el compresor funcione por un mayor periodo de tiempo para poder pasar la cantidad requerida de refrigerante al condensador.
¿SABES COMO DETERMINAR LA PRESION DE DESCARGA (PRESION DE CONDENSACIÓN) DE UN SISTEMA DE REFRIGERACIÓN?
El tema de la presión de condensación o presión de descarga de un sistema de refrigeración (media o baja temperatura) la podemos determinar con la siguiente ecuación matemática sencilla: TCond. = TAmbiente + DTCond., …………(1) Donde: TCond.; Es la Temperatura de condensación. TAmbiente; es la temperatura del aire ambiente a la entrada al condensador (condensador enfriado por aire). DTCond.; es el diferencial de temperatura de condensación el cual de diseño óptimo para los sistemas de refrigeración presenta un rango que va desde + 7.0 °C hasta 10.0 °C.
Con lo anterior hagamos un ejemplo práctico imaginémonos un sistema de refrigeración que se encuentra funcionando con refrigerante HFC-404A en un puerto costero por ejemplo mi bello Acapulco donde una temperatura de diseño de la temperatura ambiente es de 38.0 °C. Con esto, haciendo uso de la ecuación (1) tendremos lo siguiente: TCond. = TAmbiente + DTCond., ………(1)
Como tenemos un rango mínimo y máximo de DT de condensación entonces haremos lo siguiente:
Con DT de condensación mínimo de 7.0 °C tendremos:
TCond. = 38.0 °C + 7.0 °C = 45.0 °C, con esto y auxiliándonos con la tabla P vs T o con la ayuda de una tableta o celular nos apoyamos con alguna APP de P vs T de algunos de los fabricantes de Refrigerantes o Compresores (Chemours (ExDupont), Genetron (Quimobasicos), Bitzer, Danfoss, etc..
Con la ayuda de la tabla P vs T de refrigerantes, por ejemplo para nuestro caso de ejemplo nos menciona que el sistema de refrigeración está usando refrigerante HFC404A con esto localizamos la temperatura de condensación obtenida de la ecuación la cual es de 45.0 °C, la tabla de comportamiento de los gases nos dice que a esa temperatura de condensación de 45.0 °C le corresponde una presión de condensación de 284.0 Psi..
Ahora bien, haciendo el mismo ejemplo pero ahora usando el valor máximo de DT de condensación de 10.0 °C tendremos una temperatura de condensación de 48.0 °C a la cual de acuerdo a la tabla presión temperatura nos dice que le corresponde una presión de condensación de 303.8 Psi.
Bueno hasta aquí todo muy bien ya hemos arrastrado el lápiz y con números bonitos hemos ya realizado la operación pero y eso que?, que me quiere decir lo anterior? Como lo interpreto en la operación real de mi sistema de refrigeración?
Muy bien empecemos con el análisis del significado de las presiones de condensación y/o temperaturas de condensación. Primer Análisis: El Aceite lubricante por el momento no nos podemos preocupar ya que solo tenemos 48.0 °C de temperatura y el aceite lubricante empieza a perder sus propiedades lubricativas a partir de los 120.0 °C entonces el tema del aceite lubricante no es problema. Segundo Análisis: Técnicamente cuando se emplea HFC-404A/507 estas presiones de condensación desde el punto de vista comportamiento y rango de funcionamiento de este tipo de refrigerante son presiones NORMALES y no debemos de preocuparnos no se preocupen NO SE VA A DESCOMPONER O DESINTEGRAR LOS COMPONENTES QUE FORMAN PARTE DE ESTA MEZCLA DE REFRIGERANTE. Tercer Análisis: Lo que nos quiere decir las presiones de condensación antes obtenidas es que como máximo podemos tener nuestro sistema de refrigeración en este caso a nuestro compresor a una presión máxima de 303.80 Psi y como mínimo a una presión de 284.0 Psi siempre y cuando tengamos la temperatura del aire ambiente entrando a nuestro condensador a 38.0 °C y no tenemos por qué alarmarnos ya que para esa temperatura ambiente de 38.0 °C esas son presiones NORMALES de operación. Importante!!! Recuerden a mayor temperatura del aire ambiente entrando al condensador, mayor será la temperatura de condenación y a su vez mayor será la presión de condensación. Cuarto Análisis: Ahora en este cuarto análisis vamos analizar el comportamiento del compresor ya sea Hermético de Pistón, Hermético Tipo Scroll, Semihermético o Tipo Tornillo no importa el tipo o la capacidad calorífica del compresor y mucho menos la marca del compresor; el performance es el mismo el cual, nos dice: a mayor temperatura de condensación menor capacidad calorífica y a menor temperatura de condensación mayor es la capacidad calorífica de un compresor por el momento no vamos a tomar en cuenta a la temperatura de evaporación o temperatura de saturación de succión (SST por sus siglas en inglés) ya que también nos dice el performance de un compresor que a mayor temperatura de evaporación mayor
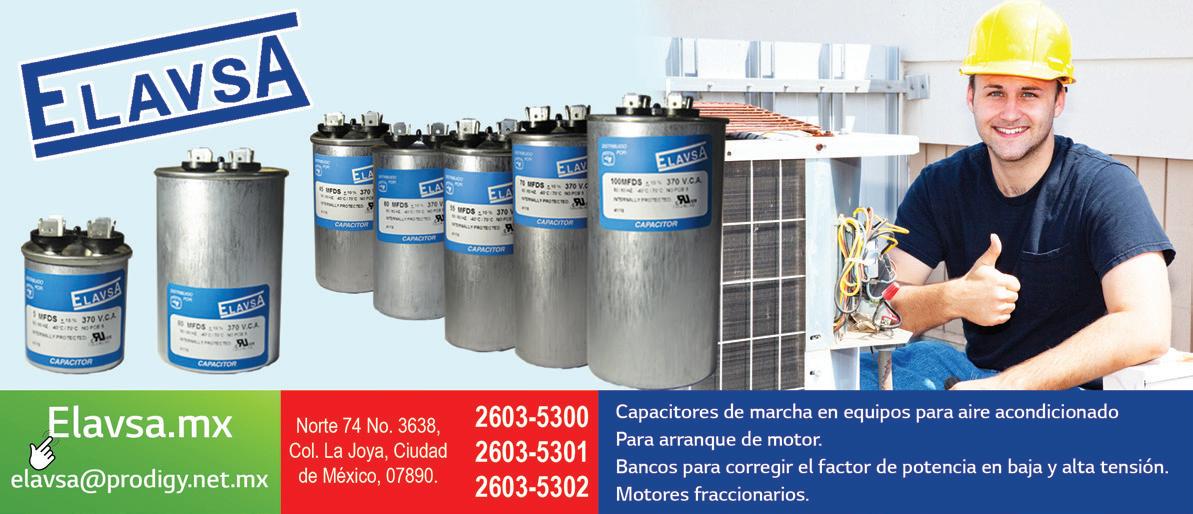
es la capacidad de un compresor o a menor temperatura de evaporación menor es la capacidad calorífica de un compresor (BTUH, Kcal/hr, Watts, etc.).
Con lo anterior, Ustedes muy probablemente se estén preguntando bueno y cuál es entonces la mejor temperatura o presión de condensación de mi sistema de refrigeración la respuesta es la siguiente.
Las presiones de condensación menores son muy buenas para así obtener la mejor eficiencia de un compresor pero a la vez NO son tan buenas como por ejemplo en aquellos lugares con temperaturas extremosas (Inviernos muy frío y veranos muy calurosos) en invierno es común trabajar los sistemas de refrigeración con presiones de condensación menores pero nos traen el inconveniente por ejemplo hablando de los compresores semihermético a quien no le ha pasado que un sistema de refrigeración funciona perfectamente en verano pero llega el invierno y lo primero que se nos presenta por las mañanas es que ya nos están reportando que el compresor amaneció protegido por falta de aceite, baja presión de lubricación o en pocas palabras cuando se usada el control de aceite famoso Sentronic o P545 de Johnson Control ahora es el nuevo Coresense siempre amanecía protegido por este control y que creen a que se debía A LA BAJA PRESION DE CONDENSACION QUE FUNCIONABA EL SISTEMA DE REFRIGERACION POR LAS NOCHES-MADRUGADAS MUY FRIAS que es cuando se tienen como ya hemos mencionado presiones de operación muy bajas principalmente en invierno pues la respuesta era que el aceite migraba a aquellos puntos más fríos poco a poco se iba quedando por simple transferencia de calor y en muchas de las veces se aloja en el evaporador y aunado a esto no se cuenta con suficiente presión, el problema se vuelve más crítico. Una de las soluciones a esta problemática es ciclar o parar motores ventiladores del condensador para que la presión de condensación no se nos caiga y mantenerla mínimo a 180.0 Psig o superior. Presiones de condensación por debajo de los 180.0 Psi seguro tendrán problemas de funcionamiento. Lo cual quiere decir que la presión mínima de un sistema de refrigeración como recomendación DEBE ser de 180.0 Psig. Y la otra recomendación es mantener presiones de condensación máximas por debajo a la presión mínima calculada con la ecuación (1) con el DTcond. De 7.0 Psi y NUNCA irnos al extremo de diseño que es la presión calculada con la ecuación (1) con el DTcond. De 10.0 °C para así aprovechar la máxima eficiencia (capacidad) de mi compresor o sistema total de refrigeración. IMPORTANTE!!! La recomendación antes mencionada aplica para todo tipo de sistema de refrigeración (media o baja temperatura), aplica para cualquier temperatura ambiente, aplica para cualquier tipo de refrigerante, en general aplica aquí en México y en China señores.
Bibliografia:
Experiencias propias de campo, Handbook de refrigeración ASHRAE.
Sobre el autor…
El M. En C. Ing. Raúl Flores Rodríguez es Ingeniero Mecánico egresado de la Escuela Superior de Ingeniería Mecánica y Eléctrica del IPN en la especialidad de Térmica e Hidráulica. Estudios de Maestría en Ingeniería Mecánica con Especialidad en Energética en la Sección de Estudios de Postgrados del IPN.
Cuenta con más de 20 años de experiencia en el área mecánica como Ingeniero Especialista, participando tanto en el Instituto Mexicano del Petróleo en diversos proyectos de la industria petrolera, diseñando y evaluando técnicamente equipos rotativos (Onshore y Offshore), como en la iniciativa privada encargado del diseño, instalación, arranque, pruebas, mantenimiento preventivo y correctivo de equipos mecánicos y de refrigeración, laboró en la empresa Bohn de México por 14 años Como Ingeniero de Aplicación y Servicio realizando actividades de análisis de cargas térmicas, selección y recomendación de equipos de refrigeración.
rflores_r@hotmail.com

Es la pregunta que le hicimos, como parte de una encuesta, a un número significativo de Consultores, Usuarios Finales, Fabricantes y Contratistas que tuvieron la oportunidad de visitar nuestro Centro de Innovación Tecnológica “The HELIX” en Dayton, Ohio en Estados Unidos recientemente.
Por sorprendente que parezca, todos coincidieron en señalar seis características comunes básicas. Según ellos, los Sistemas de Refrigeración Comercial deben ser: de Baja Complejidad, Simples Para el
Servicio, Sustentables, Seguros, Estables,
e Inteligentes. La palabra en inglés que define cada una de estas características empieza con la letra “s” (Simple, Serviceable, Sustainable, Safe, Stable, Smart). De ahí la denominación “6Ss” que identifica este concepto. Intentaremos cubrir brevemente cada una de esas características.
Baja Complejidad,
Los fabricantes de equipamientos de refrigeración buscan diferenciarse; y no hay nada de malo en ello, aunque en su afán por hacerlo, pueden agregar niveles de sofisticación tecnológica que, en algunos casos, convierten a una supuesta solución en un problema a lo largo de su ciclo de vida.
Sistemas que combinan más de un tipo de fluido refrigerante; o sistemas que emplean controles electrónicos demasiado sofisticados; o que incorporan componentes cuyo concepto de funcionamiento puede resultar desconocido para los instaladores, contratistas, operadores y personal de manteamiento en general; todo lo anterior son solo algunos ejemplos que pueden agregar complejidad en mayor o menor medida.
Todos los encuestados coincidieron en afirmar que buscan soluciones simples, con tecnologías mayormente conocidas, de baja complejidad, y con pocos componentes.
Simples Para el Servicio
La baja complejidad aporta positivamente a esta otra característica. Un sistema menos complejo, generalmente facilita el servicio.
La falta de capacidad técnica del personal de servicio en la industria de la refrigeración comercial suele ser un desafío importante, y no lo es solo en Latinoamérica. El acceso a capacitación ha mejorado un poco, gracias a la proliferación de herramientas electrónicas de fácil acceso para tal fin, pero aún no es suficiente. Aún existen deficiencias en la educación teórica y práctica especializada disponible para todos los niveles técnicos de esta industria. Y, además, la permanente evolución tecnológica exige una actualización continua de conocimientos técnicos.
Un aspecto específico e importante para considerar son las puestas en marcha de los equipamientos, lo cual es parte del servicio. Los usuarios finales buscan plazos de entrega más cortos y proyectos de ejecución más rápidos que permitan acelerar la apertura de sus nuevos locales, o que eviten extensas interrupciones en la operación de locales comerciales existentes durante las remodelaciones.
La disminución de la proliferación y disponibilidad de componentes y partes para la ejecución de los proyectos y posterior servicio postventa, también resultaron ser temas clave durante esta encuesta.
Sustentables
El impacto ambiental directo generado por el Potencial de Calentamiento Global (GWP) y la carga total del gas refrigerante, además del porcentaje de fugas a lo largo del ciclo de vida del sistema, es solo una parte del impacto ambiental total de un sistema. El impacto indirecto es la otra porción, y está relacionado con el nivel de emisiones de CO 2 que genere cada kW que el sistema energéticamente consuma. La eficiencia energética juega entonces un papel clave, ya que contribuye a disminuir el impacto ambiental total y optimiza el retorno de la inversión, particularmente en aquellas regiones donde el costo de la energía es alto y su generación no es renovable.
Seguridad
Esta característica cobra mayor importancia a medida que las tendencias globales en nuestra industria se mueven hacia refrigerantes con un menor impacto ambiental. Refrigerantes alternativos con un Potencial de Calentamiento Global (GWP) menor de
Control del edificio Sistemas Distribuídos 40 HP
Controlador del sistema
Fig.1: Unidad Condensadora de Aplicación Interior con Control Electrónico

Compresor Scroll
Fig.3: Sistemas Distribuidos, más eficientes y con menor carga de gas
600, tienden a ser ligeramente inflamables (A2L), como lo son algunas mezclas de HFO; o incluso altamente inflamables (A3) como el Propano. El amoníaco (NH3) es un refrigerante natural tóxico y el CO 2 opera a presiones considerablemente más altas que el resto, particularmente en régimen transcrítico.
La inflamabilidad y la toxicidad no son temas menores. Y deben ser tratados en un total acuerdo con las regulaciones, normas, y estándares locales e internacionales existentes. Los tomadores de decisión que formaron parte de esta encuesta coincidieron en que la solución ideal debe ser indiscutiblemente segura, y en el marco de esta discusión, la mitigación del riesgo suele agregar complejidad al sistema de refrigeración.
Estable
Un sistema debe operar de manera estable todos los días a lo largo del año, bajo todas las condiciones ambientales, variaciones estacionales, y ante los continuos cambios en Fig. 4: Unidad Condensadora Para CO 2 Transcrítico A1, no tóxico ni inflamable la carga frigorífica.
Por otro lado, dos de los factores más importantes en el análisis del costo de operación de un sistema de refrigeración comercial son la eficiencia energética y el costo de mantenimiento. Este último está íntimamente ligado al tercer factor que es la pérdida de productos frescos o las mermas.
De ahí que un sistema estable tiende a ser más confiable y eficiente a la vez, lo cual se traduce en un menor costo por mantenimiento y una menor pérdida de mercadería. Todo esto impacta positivamente en el período de retorno de la inversión inicial.
Estable
Un sistema debe operar de manera estable todos los días a lo largo del año, bajo todas las condiciones ambientales, variaciones estacionales, y ante los continuos cambios en la carga frigorífica.
Por otro lado, dos de los factores más importantes en el análisis del costo de operación de un sistema de refrigeración comercial son la eficiencia energética y el costo de mantenimiento. Este último está íntimamente ligado al tercer factor que es la pérdida de productos frescos o las mermas.
De ahí que un sistema estable tiende a ser más confiable y eficiente a la vez, lo cual se traduce en un menor costo por mantenimiento y una menor pérdida de mercadería. Todo esto impacta positivamente en el período de retorno de la inversión inicial.
Inteligente
Suena a algún tipo de sofisticación electrónica, pero en realidad no lo es. Las soluciones tecnológicas inteligentes tienden a ser modulares y fácilmente escalables. Están inteligentemente concebidas para para ser flexibles y adaptables a la realidad, las exigencias y los desafíos de cada mercado. La electrónica debe contribuir a alcanzar todo lo antedicho, sin agregar complejidad.
Fig. 5: Sistema Descentralizado con Modulación Digital, estable y eficiente
En resumen, nuestra industria busca soluciones concebidas inteligentemente para poder enfrentar los desafíos actuales y futuros. Esto implica un enfoque holístico y diferente en la discusión de las mejores soluciones, que involucre a todas las partes involucradas (Consultores, Usuarios Finales, Fabricantes, Contratistas, y Servicio Postventa) con un propósito en común: optimizar el costo de operación a lo largo del ciclo de vida de las instalaciones, disminuyendo a la vez su impacto ambiental
Unidad condensadora para exterior de MT
total.
Unidades interiores para BT
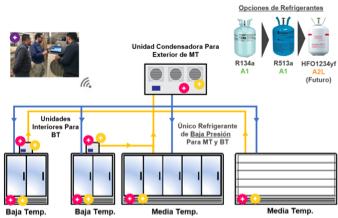
Único refrigerante de Baja Presión Para MT y BT
Baja Temp.
Baja Temp. Media Temp. Fig. 7: Sistema Micro-Booster, flexible, modular, escalable
Media Temp.

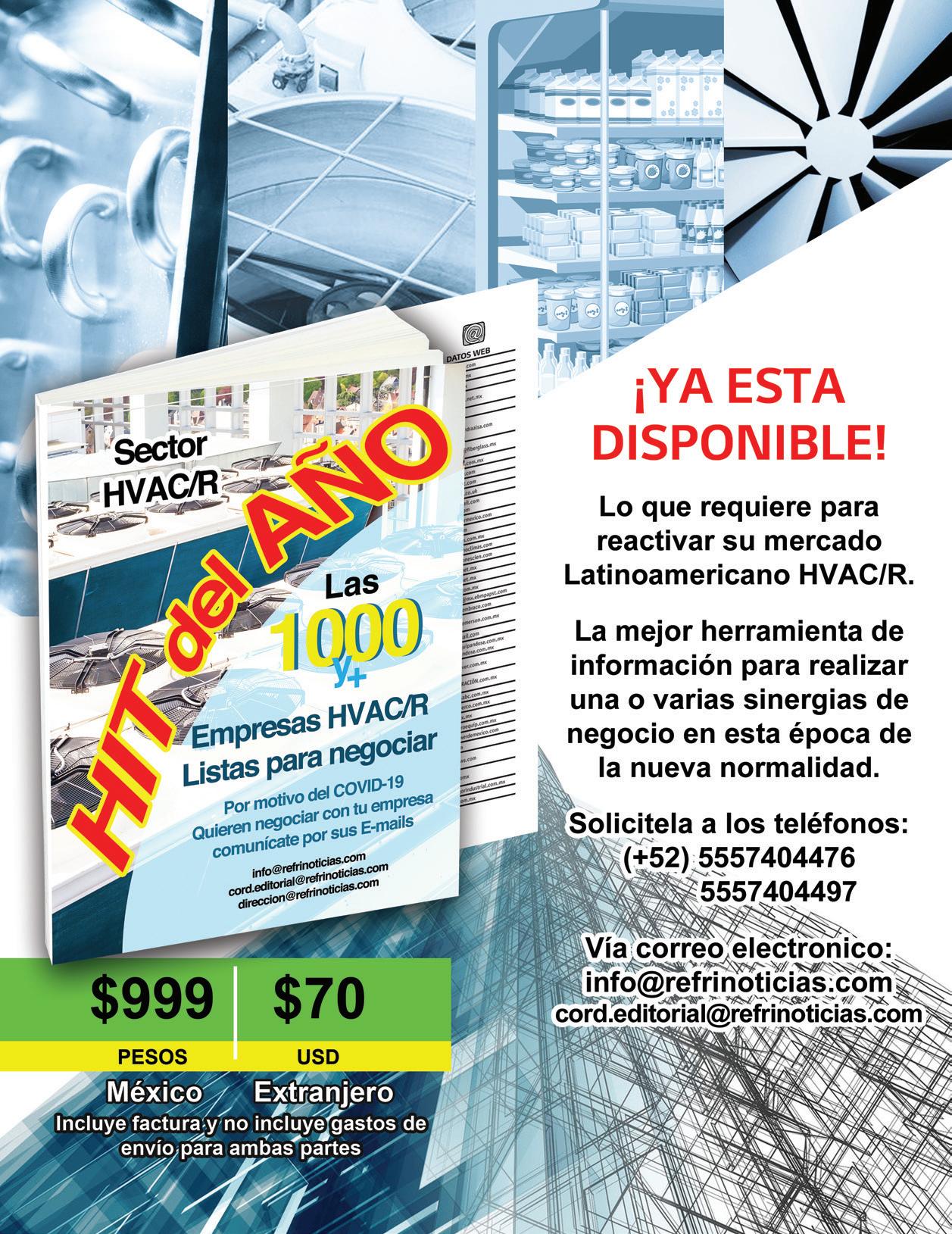