Global Aluminum Market: Growth Analysis & Upcoming Trends
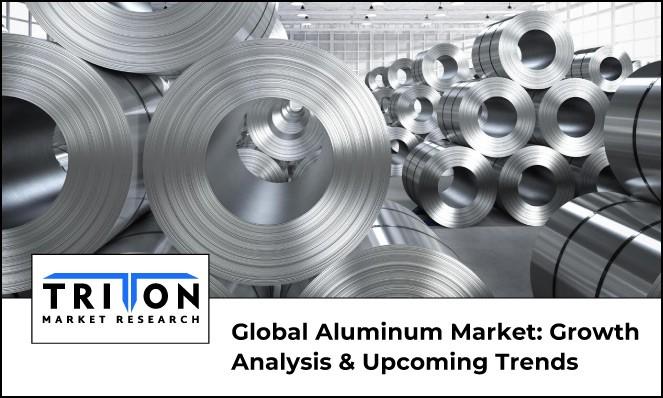
Aluminum is one of the most widely used metals globally, finding extensive applications across transportation, construction, packaging, machinery, electrical transmission, and consumer goods sectors. Global demand for aluminum has witnessed steady growth over the past decade, driven by rapid industrialization, urbanization trends, and infrastructure development across emerging economies. According to Triton Market Research, the Global Aluminum Market is expected to experience a steady CAGR of 5.37% over the forecast period from 2024 to 2032.
Aluminum Market: Utilities Driving Global Growth
Demand Driven by Automotive and Aerospace Sectors:
The transportation industry accounts for over 27% of global aluminum consumption as of 2022. Within this, the automotive segment is the leading consumer, followed by aerospace manufacturing
Aluminum is favored in auto-making for its light weight, strength, durability, and corrosion resistance. The metal helps enhance fuel economy and lower carbon emissions. As per estimates, an average mid-size vehicle now incorporates over 130 Kg of aluminum components. Luxury and performance vehicles use even higher quantities, nearing 230 kg. Companies like Audi, Jaguar, and Porsche aim to reduce curb weight and improve acceleration, speed, and handling.
On the other hand, the aerospace sector relies on lightweight, high-strength aluminum alloys to manufacture aircraft bodies and components. Major plane-makers forecast a need for over 1 million metric tons of new aluminum capacity by 2032 to meet production targets.
Aluminum’s Growing Efficacy in Construction and Packaging
Accounting for over 75% of global consumption, the building and construction sector is the largest end-user of aluminum today. Architectural demand is driven by the metal’s aesthetics, strength, longevity and flexibility in fabrication. Aluminum framing, cladding, windows, and curtain walls are gaining momentum in sustainable building projects.
At the same time, aluminum packaging, especially cans and foils, is witnessing high growth buoyed by rising hygiene awareness and trends such as online food delivery, packaged meals and beverages.
Rising Electricity Costs Compel Producers to Enhance Energy Efficiency
Aluminum production is an energy-intensive process. On average, electricity expenses account for around 40% of operating costs for aluminum smelting companies. Over the past few years, power tariffs have risen globally, compelling businesses to focus on enhancing energy efficiency.
Many older smelting facilities built in the 1960s-80s used outdated technologies that consumed over 15,500 kWh to produce one ton of aluminum. With electricity prices rising, producers are now retrofitting plants with modern cell designs, smart automation and advanced process controls. These upgrades can reduce energy usage by 20-30%.
For instance, Norsk Hydro’s HAL300 technology cuts power consumption down to just 13,500 kWh per ton. RUSAL’s RA-550 electrolysis technology brings further savings, using only 12,800-13,000 kWh. By enhancing energy efficiency, companies aim to curb expenses and bolster profit margins.
China Hongqiao Group, the world’s largest aluminum producer, is adopting digitization and big data analytics to optimize energy utilization across its smelting operations. This has enabled the company to cut power usage by over 15% in the past five years.