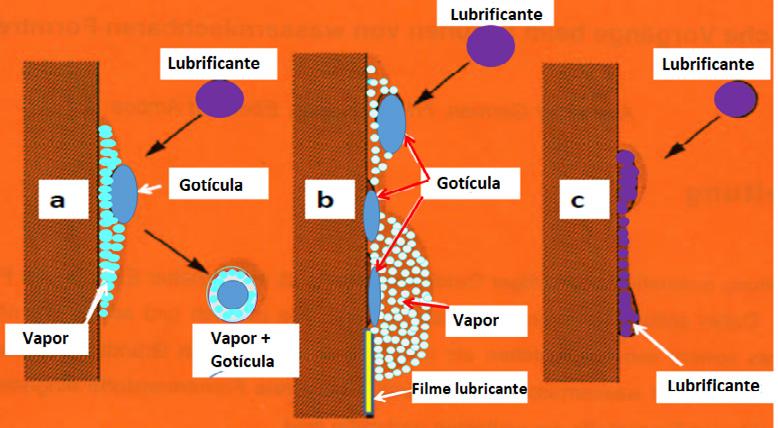
4 minute read
FICHA TÉCNICA
ROTAS NITRETAÇÃO + OXIDAÇÃO PARA MOLDES
HAIKAI TÉCNICO 013
Advertisement
Para produzir as camadas “de nitretação e de óxidos” na superfície de moldes de injeção de alumínio, a Isoflama considera mandatório a realização de duas operações industriais descritas a seguir:
1. DESGASEIFICAÇÃO A VÁCUO Limpeza da superfície e canais de refrigeração realizada em forno a vácuo para eliminar produtos como “silicone de furos com roscas”, “restos de óleo”, “restos de desmoldantes”, “água”, e outros produtos voláteis.
2. JATEAMENTO COM MICROPARTÍCULAS O jateamento uniformiza a superfície quanto à rugosidade e contribui para a formação de uma uniforme camada nitretada. A leve alteração da rugosidade original produzida pelo jateamento de micropartículas corrobora para evitar o escorrimento do desmoldante e assim proteger e agir efetivamente como lubrificante na injeção do Al. A Figura abaixo ilustra essa situação.
A NITRETAÇÃO A PLASMA O Molde de Injeção de Al completamente limpo e superfície jateada não contaminaria a atmosfera “nitretante” do plasma formada a partir da mistura de gases Nitrogênio e Hidrogênio em baixa pressão e, consequentemente, não altera o Potencial de Nitrogênio, ou mesmo “não apaga” o plasma durante o processo. Isso permite a condução do processo de nitretação a plasma de maneira estável, garantindo a produção de uma fina e uniforme camada nitretada – 0,030 a 0,060 mm – sem “camada branca” e, na sequência, formar uma reduzida camada de óxidos.
A OXIDAÇÃO A PLASMA Uma vez concluída a etapa de Nitretação a Plasma, a etapa imediatamente seguinte é a Oxidação a Plasma, produzindo uma fina camada de óxidos, preferencialmente Magnetita, de espessura 0,001 a 0,003 mm.
Através da técnica de penetração de raio-X na superfície nitretada, da ordem de 5 a 8 µm permitindo atingir a matriz ferrosa, torna possível determinar os tipos de nitretos que constituem a camada branca formada.
Figura: Esquematização do processo de jateamento do lubrificante na superfície do molde 1
¹Apresentação “Influencing parameters on die failure” de Horst Lindow, Isoflama 2016
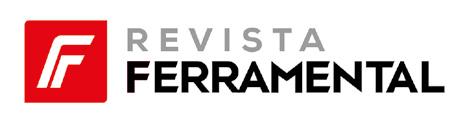
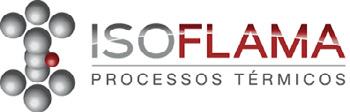
TÊMPERA VERSUS MARTEMPERA HAIKAI TÉCNICO 014
O processo térmico Têmpera consiste de resfriamento direto.
O processo térmico Martempera consiste de resfriamento com parada intermediária. Para os aços ferramenta esses dois processos podem ser aplicados.
A análise crítica de uma peça com vistas à seleção de um, ou outro processo térmico, deve levar em conta a geometria da peça, dimensões, peso e, principalmente, a tecnologia de resfriamento a ser utilizada para permitir o correto controle e monitoramento dos parâmetros de processo.
No resfriamento em óleo, geralmente, recomendável adotar a Martempera para peças de grandes dimensões / peso em razão do elevado risco de trinca no resfriamento direto (alta taxa / severidade de extração de calor no óleo). Quando resfriamento com gás nitrogênio sob pressão, mesmo peças de grandes dimensões, a Têmpera seria preferível (menor taxa / severidade de extração de calor em relação ao óleo), isto se as condições de construção da peça sem “grandes riscos” para desenvolver trincas e elevadas deformações.
A associação norte americana de moldes para fundição de alumínio e forjamento a quente (“Nadca”) faz recomendações para a seleção das rotas Têmpera, ou Martempera, condicionada ao monitoramento das temperaturas de superfície e núcleo no aço do molde, por exemplo, e que no estágio de resfriamento entre 1.000 e 540 °C a diferença destas estimada como superior a 120 °C, aproximadamente. O resfriamento módulo Martempera pode ser realizado com gás nitrogênio sob pressão, sendo uma boa opção, em geral, para uma peça de grande dimensão, com pouco sobremetal e quando a análise crítica das condições de construção desta identificar riscos de trincas em razão de:
1.
2.
3.
4.
5. Projeto de desbaste por usinagem mal executada (usinagem grosseira); Riscos profundos na superfície, marcas, buracos, acabamento grosseiro etc; Rebarbas, furos paredes finas, cantos-vivos /mínimos raios de concordância; Remoção excessiva de aço, principalmente em áreas de mudança de forma; Na faixa de resfriamento 1000 e 540° C a previsão de diferença de temperatura entre superfície e núcleo na peça muito superior aos 120 °C recomendados pela Nadca.
O processo Martempera mitigaria os possíveis efeitos não desejáveis nas situações descritas acima, porém não elimina totalmente os riscos para deformação elevada, ou mesmo para o desenvolvimento de trincas. As ilustrações abaixo mostram os dois processos possíveis realizar a partir da temperatura de “austenitização” que estão sinalizados pelas curvas de resfriamento “superfície” e “núcleo”. A Figura abaixo mostra duas curvas em forma de “C” que representam o início e fim de transformação da reação “austenita em outros produtos microestruturais”, sendo “Ms e Mf” as temperaturas efetivas de início e fim de transformação da “austenita” em “martensita”.
Assim, da Figura, tem-se dois diferentes modos de resfriamento:
• “Contínuo”
Têmpera (a) que consiste do resfriamento direto desde temperatura austenitização, ou temperatura de têmpera, até determinada temperatura pouco acima de ambiente;
• “Parada intermediária”
Martempera (b) convencional que consiste do resfriamento desde temperatura de austenitização até temperatura pouco acima da temperatura “Ms” e, nesta temperatura, interromper o resfriamento para aguardar a redução da diferença de temperaturas superfície e núcleo alcançar a ordem de 120 °C (recomendação “Nadca”-North American Die Casting Association”);
Existiria ainda uma terceira opção de martempera, não convencional, muito utilizada no resfriamento em banho de sal fundido, que seria realizar o resfriamento até uma temperatura entre a “Ms” (temperatura de início de formação da martensita) e “Mf” (temperatura final de formação da martensita). Os três processos de resfriamentos devem produzir ao final uma microestrutura constituída do microconstituinte “martensita”.

Figura: a) resfriamento contínuo; b) resfriamento com parada intermediária
