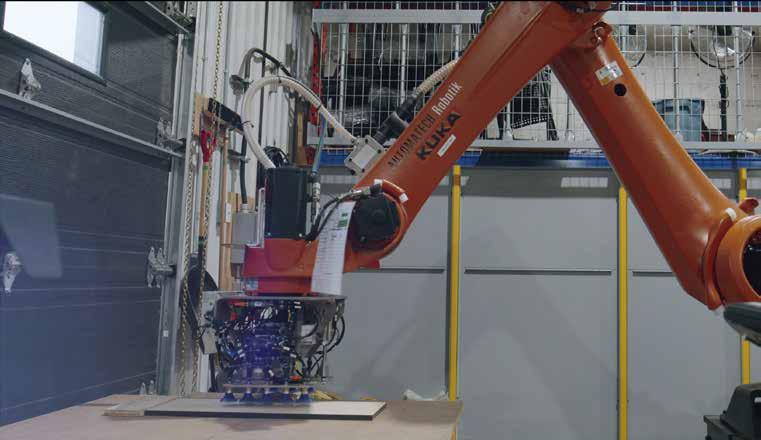
5 minute read
Automation & Robotics
from WI Summer 2021
by MediaEdge
A human process
By Grace Tatigian
In the last five to seven years, we have seen a considerable increase in robotic solutions in commercial woodworking. From CNC machines to fully automated panel process lines, these devices are playing a pivotal role in the production of pretty much every household wood item and beyond.
“Everyone wants to talk about robots; everyone wants a robot,” says Tommy Gagnon, CEO of AutomaTech Robotik. “But it might not be the right thing for the company; they might not be ready yet.”
It seems strange for a robotics company to discourage people from buying his products, but what he really wants is for his customers to do their research and invest in the right tools for their business. If a shop doesn’t even have a CNC yet, for example, then they’re not ready for the level of technology that AutomaTech Robotik supplies. He doesn’t want business owners to start on the wrong foot and lose their taste for automation; it has so much potential. Gagnon mentioned that he’s even hesitant to refer to this kind of machinery as equipment yet.
“I would say it’s more of a project,” he explains. “There is so much to learn, maintain, and update as the technology
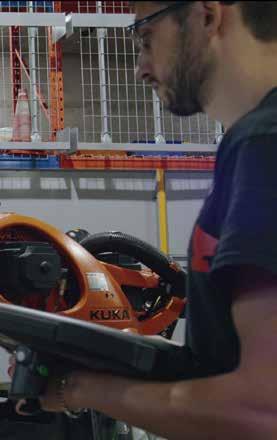
advances that I would say it will still be another ten years before we can call it equipment.”
Robotics can increase productivity, profitability, and production if the users know what they’re doing. These machines can do amazing things, but if they aren’t operated or maintained correctly, it’s impossible to use them to their full potential.
Essential to achieving the full potential of these projects are two things: education and maintenance. The two go hand-in-hand. It’s necessary to understand precisely how the machine works to maintain it effectively. There is a large number of how hard it is, to use the tool effectively.”
Operators need a thorough understanding and continued training to ensure that owners get a strong return on investment on their purchased robotic solutions. Since automation hasn’t quite hit the mainstream yet, many smaller manufacturers are still trying to figure out how to integrate hightech solutions into their company. Sometimes the solution is outsourcing production.
industry professionals out there who use these tools without thinking about how they work. Frank Horvath, Director of Sales and Marketing of FSTools, pointed to a fundamental misunderstanding of something as basic as cutting as an example.
“A blade isn’t technically cutting the material,” says Horvath. “It’s acting as a wedge which is causing the material to break apart. It’s important to understand the properties of the material in question, things like
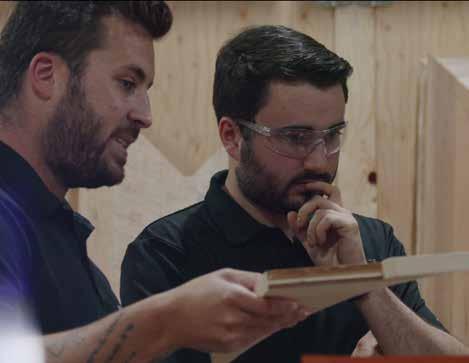
LEFT: KUKA Robotics and AutomaTech Robotik collaboration RIGHT: AutomaTech Robotik team in the workshop
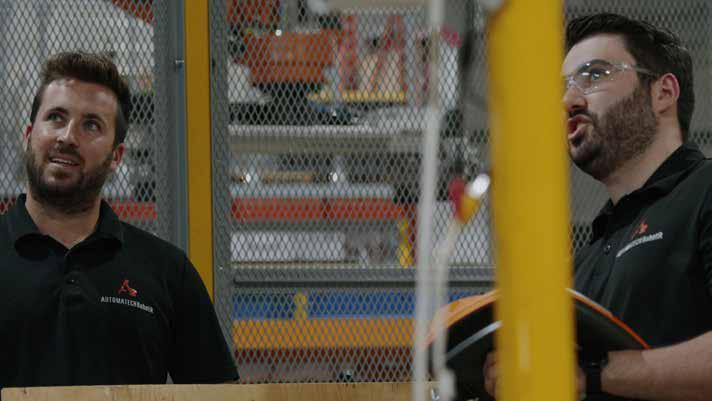
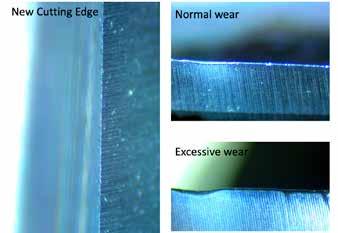
TOP: AutomaTech Robotik team in the workshop BOTTOM: FSTool’s depiction of the effects of a worn blade
Alain Albert, the founder of Woodoer, is big on collaboration. For years, he worked in consulting, working with cabinet makers all across the country. Albert saw an opportunity in that many people weren’t aware of what the tech could do for them. Now he
“If we train people on how to use the software, they can create better files for us to manufacture,” says Albert.
Albert agrees that it comes back to education, knowing and understanding the best way to tackle a project. It’s about finding new and innovative ways for people to do the work. The concern that many have with technology like this is that they think it will destroy jobs. Gagnon says it’s the opposite.
“The kind of work that people want to do has changed,” he explains. “Workers are more educated than ever, and they want to use their skills and continue to learn. It’s easier to find people who have the skills to work with robots than it is to find people who want to do manual labour.”
It’s partly a generational thing; young people entering the workforce aren’t interested in working on a factory floor, so he believes that companies need to adapt to what their employees are willing to do.
“Those who can bring the organization farther want the technology,”
runs a company that provides CNC manufacturing services for small cabinet shops looking for higher-tech solutions. But it isn’t just manufacturing; Woodoer also provides training and support for software like Cabinet Vision.
THERE IS SO MUCH TO LEARN, MAINTAIN, AND UPDATE AS THE TECHNOLOGY ADVANCES THAT I WOULD SAY IT WILL STILL BE ANOTHER TEN YEARS BEFORE WE CAN CALL IT EQUIPMENT.
says Gagnon. “And if you don’t offer it to them, they’re going to leave and go somewhere else where their drive and skills are appreciated.”
Gagnon says that he’s never had a customer who had to let someone go because of purchasing a robot. If anything, it has helped create jobs. Having new technology in the shop allows employees to put their skills to use elsewhere within the company, which ultimately adds more value because there are still many things that robots can’t do. So not only can robots create more jobs, they can create better jobs.
“If you’re going to trust someone to operate a multi-million dollar piece of equipment, you’re going to pay them well,” says Gagnon.
So if a company is investing money into machinery and operators, they should also invest in maintenance and education to take care of their investment. It’s beneficial not only for dayto-day use but also for troubleshooting when something goes wrong.
“That way high end, high-quality products can excel in the hands of highly trained operators,” says Horvath.
For manufacturers looking to scale their business, automation and robotics is definitely a solution to consider. Still, to be worth it, buyers must be willing to spend more than just the cost of the machinery. In-depth research is required to find the best technical solution. It’s essential to factor in education, safety, and operations costs to get the highest possible return on investment, which benefits everyone involved.
Elevate your design with our new Mid-Century Modern Collection! The product line features round tapered wooden legs, metal hairpin legs, leg mounting sets, floating shelf hardware and more.
MID-CENTURY MODERN
by Osborne Wood Products, Inc.
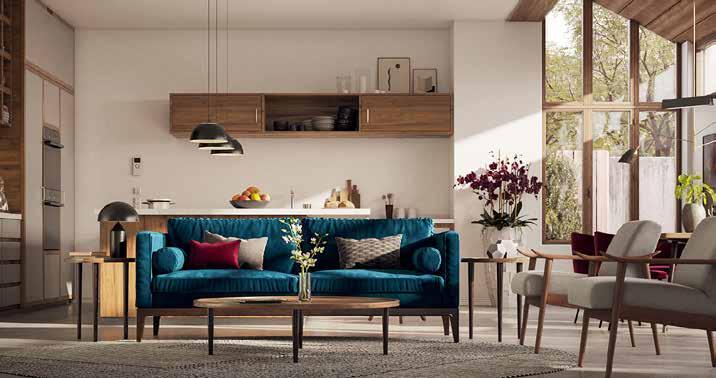
Browse our inventory at www.osbornewood.com or call for more information at (800) 481-2364 Scan the QR code to view the full Mid-Century Modern Collection