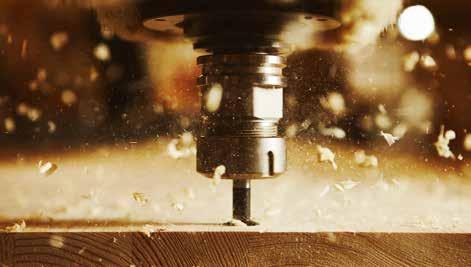
10 minute read
The Beginner’s Guide to Flat Table CNC Machines
from WI Summer 2021
by MediaEdge
What to Expect When You’re Expecting a New CNC
By Christine Bergeron, Technical Consultant, Planit Canada Christopher Manclière, Senior Software Specialist, Planit Canada
Congratulations on your new CNC! Much like the arrival of a new baby, the delivery of your first Flat Table CNC means you have to become an expert at a whole lot of things very quickly. You may find yourself awake in the middle of the night, frantically Googling “what is a controller?”, “vacuum optimization,” or “what does a CNC operator do?”
The first step in knowing how you’re going to operate your new baby is to understand how to communicate with it. Rather than adorable baby-talk, your control software will be in charge of reading pre-programmed commands that tell your machine how to execute actions to make a part.
G-Code is a common CNC language, which looks just like a text file that the machine can read and then execute. (Awww! So cute!) Some machines will use proprietary language. The device will only accept the format defined by its controller, and if it doesn’t understand a command, it will stop the program’s execution and spit up an error message. Less cute.
Creating programs for your CNC, or CNC programming, is done using one of three methods: with a code editor, with CAM software, or with a CAD/CAM software.
The code editor is probably the most tedious way to create a CNC program. It requires you to write the G-code from scratch. While it could be a decent solution for making parts with simple operations, it would involve writing thousands of lines of code to execute complex functions.
To speed things up, you can use CAM software. This method allows you to import or draw a CAD file, and the software will automatically generate the CNC program for you. You’ll have a graphic interface allowing you to see your part and verify the machining is correct. Your CNC programmer may need to manually modify operations for each piece before generating the files for the machine.
The third option is the CAD/ CAM software which is a fully integrated solution. The same software you use to create your drawing will also generate your CNC program. It will take you from design to manufacturing without requiring the use of 2 or 3 other solutions to create a program for your CNC. Your workflow is simplified, and you won’t need complex programming skills.
Now that you can talk to your baby, you’ll need to set up your spoilboard. You want to be thinking about maximizing the vacuum on your CNC to hold parts and make sure they don’t move. Before mounting the LDF or MDF board onto your CNC’s permanent table, you’ll want to ensure you’ve got flat, even surfaces with four sealed edges. We recommend using two coats of paint to seal the edges and prevent bleeding airflow or losing vacuum at the top of the board.
Your CNC machine will have a surfacing program for flattening the spoilboard, and every member of your team must be familiar with how to use it. You’ll need to have the right tool - a spoilboard surfacing cutter with a wide diameter. Remember to enter the new board thickness into the controller after running the program. Once in a while,
you’ll want to flip the spoilboard to prevent warping and to ensure your pump can keep the spoilboard in place.
Understanding how to optimize your CNC vacuum is critical when cutting parts that are smaller than the table. To ensure the vacuum holds your sheet down properly, you’ll want to use scrap material to cover the space on the table to block airflow.
The decision to screw or not to screw the spoilboard to the permanent table is entirely up to you. If you prefer not to screw the board to the table, make sure that you keep your vacuum rubber seal in good condition and that you clean away the dust between the table and the spoilboard regularly.
You’re now becoming a fantastic CNC parent but will still need to have some essential parts on hand for quick replacement and to avoid the stress of waiting for rush delivery from your provider. Maintenance emergencies for your baby come with a high price tag when you consider lost production, rescheduling technicians, and rushed parts delivery.
Depending on the type of production you have, you’ll want to consider having: a flycutter to resurface your spoilboard, a compression bit for the outline cut (typically ½” or 3/8” compression bit), 3mm, 5mm, 8mm, 10mm drills depending on the type of hardware you use, down cut tools with various diameter to create the dados or any other cuts that do not cut through, and mitre bits of various angles. If you are machining MDF doors, you’ll have a longer list. Make sure you have tool holders with the proper shank diameter for all the tools you’ll need.
Also, make sure you get the specs from your tool provider to know their speeds and feed rates. You don’t want to break them or burn your table if they’re not running fast enough. As you know all too well – friction, wood, and vacuum are a terrible mix.
Now, who will care for your new baby while you’re doing other things? Your CNC Operator will be up to the task once they’ve mastered these essential skills: keeping the machine clean, resurfacing the spoilboard, loading tools, setting the tool length offset and diameters so you can use cutter radius compensation, loading programs onto the device, and of course, doing the daily and weekly maintenance according to your schedule.
Ultimately, you are responsible for maintaining your baby. We strongly suggest having a preventive maintenance plan with tasks your operators can easily do themselves with daily or weekly maintenance to control dust, check hydraulic pressure and fluids, lubricant levels, seals, filters, and keeping tools in good shape. For monthly, quarterly, and yearly maintenance, you may want to hire a mechanic or a CNC technician.
They grow up so fast, don’t they?
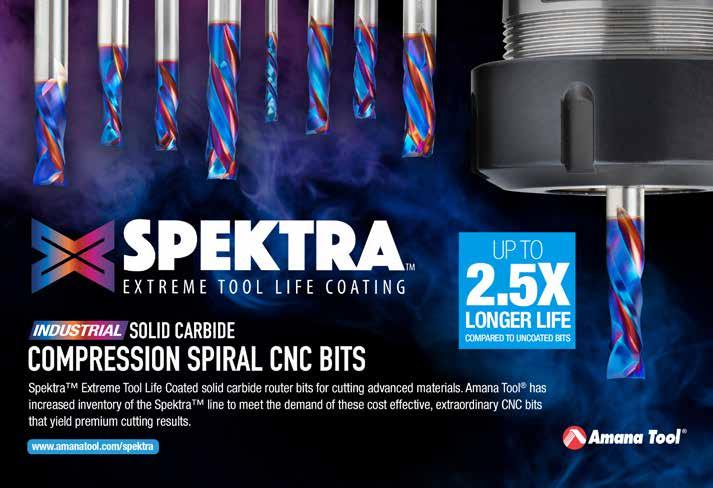
LIVE IN LAS VEGAS
AWFS Fair to Take Place in Person
By Grace Tatigian
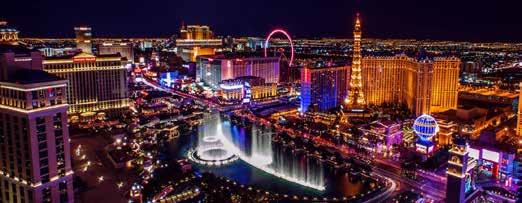
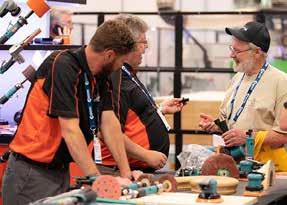
For years, the AWFS® Fair has been a must-attend event for innovators in the industry. This is where so many businesses introduce their products to the market for the first time, and so it’s always been essential for anyone who wants to stay in the know. To date, approximately 400 companies have booked exhibitor booths for the event, so it promises to be as full of innovation as ever.
The elephant in the room, or rather, the exhibit hall, is, of course, COVID-19.
“We talk about it every day; it’s a constant moving target,” says Elena Potter, Marketing Coordinator for AWFS®. “We’re making sure to stay up-to-date so we can provide a safe experience for everyone.”
Unfortunately, the event won’t have any virtual events for those unable to attend in person. And with international travel restrictions in place worldwide, it will be challenging to have as many countries represented as usual. This, however, has not deterred the Association of Woodworking and Furnishings Suppliers.
“The big draw to the AWFS® Fair is seeing the products in person and seeing them in action,” explains Potter. “We’ve had some feedback from others in the industry, and a lot of people agree that an online version of this kind of event doesn’t hold the same kind of value. So we’ve decided to do it exclusively in person.”
And so, to make sure it’s worth it, they’re refining their offerings, making sure to expand on what has been popular in the past, and include new features based on previous feedback. One such feature is the Safety Zone. This will be a section of the floor dedicated to exhibitors looking to highlight and promote that they are committed to providing safety gear for the industry. Safety for the job site and in the shop is essential every day, and in today’s world are even more necessary.
Another new feature will be the Tool Tour. By popular request, exhibitors who specialize in hand and power tools will be placed around the show floor. With the help of the AWFS® Fair app, attendees will be able to go on a tour of all these exhibitors and see what fun new tools they can snag for their shop.
“It will be kind of like an interactive tour,” explains Potter. “Each attendee will get a bingo card with the different exhibitors included in the Tool Tour. When they go to a designated booth on the tour, they can get a stamp on their card. It’s a little like a treasure hunt. When you fill the card, you can present it for a concert-style t-shirt that features all the Tool Tour exhibitors like at Coachella.”
Fan favourites will also return to the Fair, some of them with a twist. When the Closets & Storage Pavilion came up in conversation, Potter couldn’t say much.
“We’re in the process of adding a more interactive element,” she explained at the time of the interview in late April. “It’s in the works, and we’ll be announcing it soon.”
But some tried-and-true features of the Fair will stay the same such as the Rapid Fire Presentations. Less formal and more spontaneous than the College of Woodworking Knowledge™, these quick, 15-minute exhibitor-led presentations happen on the show floor to demonstrate products and talk about the industry. They’re an excellent opportunity for someone who wants to stay on the move and can’t necessarily want to devote their time to the popular CWWK education program.
The two competitions: the Fresh Wood Competition and the AAW Turning to the Future Competition, will also be back. The Fresh Wood Competition allows attendees to see high school and post-secondary students’ outstanding construction and design achievements. The AAW Turning to the Future Competition is where high school and postsecondary students submit projects made with lathes; finalist projects will be on display, and winners will also be announced at the awards ceremony. This is a fun way to see what young, upand-coming woodworkers are creating.
“People love to check in on the competitions and see what students are making,” says Potter. “It’s a great chance to see some fine woodworking from students all across the country.”
Besides these two student competitions, many other achievements will be recognized at the AWFS® Visionary Awards. The New Product Awards are prestigious awards recognizing exhibitors for innovation and new-to-market products, including any product introduced to the industry since July 2019. All companies whose entries are accepted will have their product featured in the Visionary New Product Showcase for the show’s duration.
“These awards are rigorously judged,” says Potter, referring to the panel of third-party judges who select the winner. “So it’s a big deal to get an award.”
Products go head-to-head in the following categories: components; software; industry 4.0; raw materials; plastic machinery/supplies; tooling; machinery under 50K; machinery over 50K; power tools and hardware. Applications for the Visionary Awards remain open until June 2021, and exhibitors can apply online.
While COVID-19 will definitely be an added challenge in organizing the Fair, AWFS has proven itself to be a leader in innovation and is up to the task.

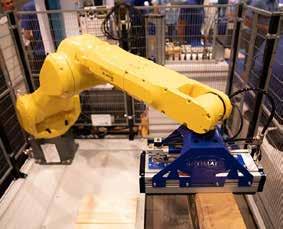
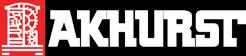
everything you need in ONE PLACE
ARE YOU LOOKING TO INCREASE PRODUCTIVITY WITHOUT INCREASING YOUR LABOUR? LOOK NO FURTHER THAN GANNOMAT’S RANGE OF DOWEL & CASE GOOD PRODUCTION SOLUTIONS.
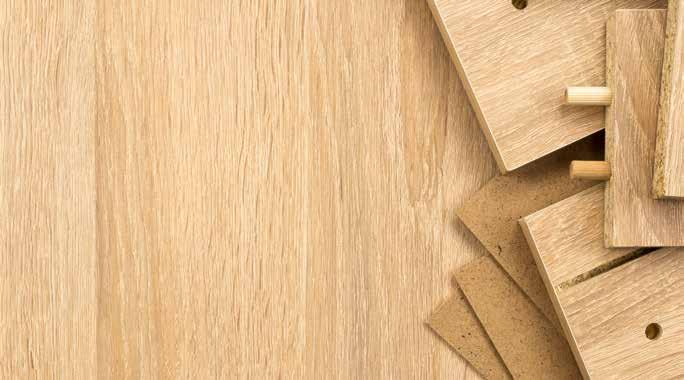
INDEX LOGIC
CNC Dowel Drilling, Gluing, & Inserting Machine
CONCEPT ECO
Lamellar Case Clamp
EXPRESS S2
Dual Hinge Drilling & Inserting Machine
@AkhurstWood @Akhurst.Machinery @AkhurstMachinery @AkhurstMachinery 1.888.265.4826 | www.akhurst.com