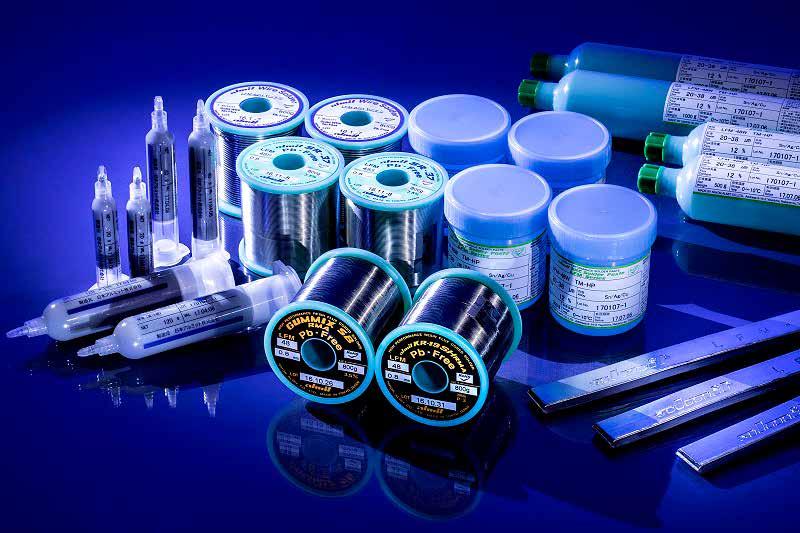
22 minute read
Fabricants d’électronique
ROHS SANS PLOMB : Le passage aux alliages ROHS sans plomb est une avancée majeure en terme environnementale et sécurité des personnes travaillant sur les assemblages électroniques.
Cette avancée ne s’est pas faite sans mal, mais a permis de pousser tous les acteurs du métier dans un même sens, avec une progression technologique importante sur les moyens et procédés, la maitrise et la qualité de conception des fils d’alliages et flux associés et bien sur humaine par la montée en compétences nécessaires pour la mise en œuvre et l’utilisation de ces mêmes avancées. De nouvelles problématiques sont apparues avec ces nouveaux alliages : retassure, filet soulevé… et l’association américaine IPC avec notamment l’IPC-A-610, a pris en compte ces points et a défini des critères d’acceptabilité.
Toutes les parties prenantes de ce changement peuvent être satisfaites du résultat que l’on connait maintenant avec un niveau de fiabilité qui est proche de celui des alliages plomb.
Avec le recul que l’on a maintenant sur les assemblages sans plomb, les acteurs de pointe de l’aéronautique, du spatial et du médical se sentent rassurés et ont commencé à utiliser ces nouveaux alliages sur de nouveaux produits et sur certains assemblages existants lorsque les coûts de qualification ne sont pas trop exorbitants. Deux grandes familles d’alliages ROHS ont été développées : • Les alliages SAC : étain, argent, Cuivre • Les alliages SnCu : étain, cuivre, intéressants pour les process « vague » car sans argent et donc moins onéreux.
Interview – Michael Mendel – CEO Almit Germany Evolution du brasage automatique vu par un fabricant d’alliage de brasage Dans quels domaines le brasage robotisé offre-t-il des avantages par rapport au brasage manuel ?
Avec le brasage manuel, des erreurs de processus sont fréquentes. Le brasage robotisé offre des possibilités techniquement différentes du brasage manuel, comme la mesure automatique de la température de la panne, des profils de brasage prédéfinis et la possibilité de paramétrer le robot. De cette manière, les erreurs de production peuvent être considérablement réduites et la qualité de chaque joint de brasage peut être garantie. Cela augmente
L’avantage des fils à souder Almit est un noyau continu à 100%. Les fils de brasage conventionnels présentent souvent le problème suivant: le noyau du flux est interrompu par des inclusions d’air. Ces dernières entravent la qualité finale du joint de brasage...


également l’efficacité économique, grâce à la production en masse des brasures. Le brasage automatique peut être réalisé avec une précision et une répétabilité élevée, des avantages indispensables pour les normes de qualité d’aujourd’hui, toujours plus élevées dans l’industrie de la fabrication électronique.
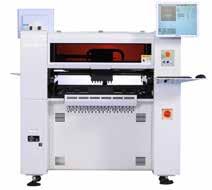

Comment le brasage automatisé a-t-il évolué au cours des dernières décennies ?
L’évolution de l’industrie électronique a façonné le développement du brasage automatique. Une variété d’outils de brasage ont été développés spécifiquement pour les robots au cours des dernières décennies. Les composants étant de plus en plus petits et sensibles, les solutions de brasage manuel ne sont parfois pas suffisantes. La technologie du brasage automatique a évolué de pair avec la complexité des cartes à réaliser…
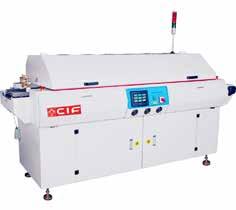
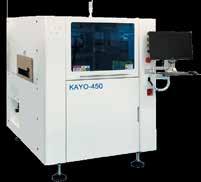
Quels sont les défis actuels auxquels vous êtes confrontés en matière de développement de produits ?
Ce sont sans aucun doute, les exigences sans cesse croissantes du marché en matière d’optimisation des processus et d’efficacité économique. En tant que pionniers dans le développement de matériaux de brasage, nous essayons d’avoir toujours une longueur d’avance afin de pouvoir accompagner nos clients de manière optimale à tout moment.
Quels sont les enjeux de demain ?
Nous ne nous concentrons pas seulement sur les besoins actuels de nos clients, mais nous voulons aussi anticiper les problèmes et proposer des solutions pour les besoins futurs du marché. Lorsqu’il s’agit de la qualité de la brasure, le flux joue un rôle décisif. Dans le monde entier, seuls quelques fabricants de brasure produisent encore leur propre flux. La mise au point d’un flux est très complexe. Outre l’exigence susmentionnée d’un noyau de flux continu sans inclusion d’air et d’humidité, les différents composants doivent être précisément adaptés les uns aux autres afin d’obtenir un résultat de brasage parfait.

Quelles sont vos dernières innovations en tant que fabricant de matériel de brasage ?
Notre dernier fil de brasure DB-1 RMA, atteint une nouvelle dimension en matière de mouillage grâce à son flux innovant. Grâce à la combinaison d’un flux à action rapide et d’un flux persistant, il offre un double effet de renforcement du mouillage. Un tel flux est à ce jour unique sur le marché. Il offre à nos clients, un résultat de brasage de haute qualité, un temps de traitement considérablement réduit ainsi qu’une réduction à long terme des coûts de fabrication.
Comment se distinguent les produits de brasure pour le brasage automatique ?
Almit propose des fils et des crèmes à braser pour tous les procédés de brasage automatique. L’avantage des fils à souder Almit est un noyau continu à 100%. Les fils de brasage conventionnels présentent souvent le problème suivant: le noyau du flux est interrompu par des inclusions d’air. Ces dernières entravent la qualité finale du joint de brasage. DU NOUVEAU DANS LA GAMME CIF PROD
BRASAGE SELECTIF GAMME SASINNO
PLACEMENT CMS AUTO GAMME KAYO
FOURS CONVOYEUR EN LIGNE GAMME ATHOS
SERIGRAPHIE AUTOMATIQUE GAMME KAYO
LAB
LES SOLUTIONS POUR VOS PROTOTYPES ET MICRO-SERIES prod
LES SOLUTIONS POUR VOS PETITES SERIES ET PRODUCTION
Quels sont les produits offerts par Almit pour le brasage automatique ?
Nous proposons des alliages brevetés qui protègent les pannes de l’érosion et de l’oxydation. Cela permet de réduire la consommation de pannes, le temps de travail et de réaliser des économies. Notre flux Gummix a été développé spécialement pour le brasage sans contact. Il se distingue par son comportement qui minimise les billes de brasures. Gummix est disponible sous forme de fil et de crème à braser. Les crèmes à braser Almit constituent également une solution optimale pour les composants à pas fin.
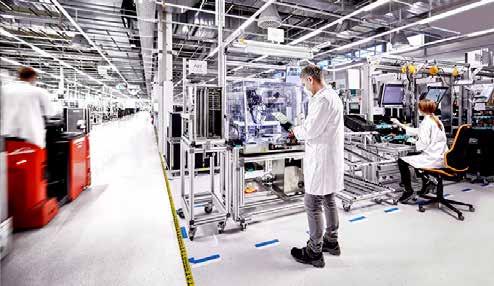
L’évolution du brasage automatique vue par un fabricant de robots
Raphael LUCHS
Revue de Raphael Luchs – CEO Elmotec
Il y a plus de 50 ans, des visionnaires ont commencé à développer des solutions de brasage automatisées au fer pour remplacer le brasage manuel. Depuis, beaucoup de choses se sont améliorées et ont conduit à une nouvelle industrie : le brasage automatique. L’objectif du brasage robotisé est toujours le même : obtenir une qualité et un rendement plus élevés, en remplaçant le facteur humain dans le processus. Cela est devenu plus important que jamais. Non seulement la pandémie a accru le besoin d’automatisation, mais le marché demande un volume, une qualité et une traçabilité plus élevés. Ceci peut être réalisé avec des solutions de brasage robotisées.
Le principe de base du brasage robotisé est de remplacer le mouvement de la main de l’opérateur. Aux prémices, le mouvement était effectué par le robot avec un axe linéaire pneumatique. Aujourd’hui, le mouvement est effectué par des systèmes d’axes linéaires électriques ou des bras de robot. L’évolution a permis d’atteindre une plus grande précision, plus de flexibilité dans le positionnement des pannes et d’avoir des coûts d’exploitation plus bas. sa fiabilité et de son rapport qualité-prix. Mais, pour la production à haut volume, les bras de robot sont plus efficaces. Les bras de robot, comme le robot à 4 axes (robot scara) ou le robot à 6 axes atteignent une vitesse plus élevée et peuvent effectuer des mouvements avec plus de possibilités d’angles différents, mais sont plus chers qu’un système d’axe linéaire. Le système de mouvement de la solution de brasage automatique offre la possibilité d’installer diverses technologies de chauffage. La technologie de chauffage chauffe les joints de soudure et les fait fondre avec le fil de brasage.
Le brasage robotisé a commencé avec le brasage au fer, mais il s’est développé avec les nouvelles technologies et a trouvé plus d’applications. La gamme de technologies de chauffage comprend le fer, le laser, la vague, la refusion, les ultrasons et autres. Ces technologies ont des caractéristiques différentes et doivent être soigneusement sélectionnées en fonction des joints de brasage, du matériau, du volume de production et du budget. De nombreuses nouvelles fonctionnalités ont soutenu le développement du brasage et ont permis d’atteindre une plus grande précision dans le processus robotisé. Il est important d’avoir une technologie de chauffe performante et de réaliser le joint de brasage dans une position précise. Les deux doivent être corrects pour avoir un processus de brasage automatisé réussi. Par exemple, le fer est positionné et vérifié avec un étalonnage du point zéro pour s’assurer d’avoir la plus haute précision. Aujourd’hui, des nouveaux systèmes de capteurs et de vision sont développés tous les jours pour permettre d’atteindre une plus grande précision. paramètres stables. Ces paramètres peuvent être facilement mesurés. Les nouvelles technologies de communication transfèrent les informations du robot à un système informatique en temps réel. Cela permet d’avoir un suivi de la qualité de la production en direct. Le paramétrage des logiciels est facilement accessible et surveillé. Cela permet au fabricant de contrôler son processus, d’augmenter la qualité et de faire fonctionner et d’entretenir le robot à distance. Grâce aux nouvelles technologies de chauffe, aux systèmes de déplacements plus rapides et à la nouvelle intelligence logicielle, le brasage robotisé permet d’aller vers de nouvelles voies dans la conception des pièces et des joints de brasage. Il remplace également d’autres équipements de brasage traditionnels (comme le brasage sélectif), car le brasage robotisé nécessite moins d’énergie, des coûts de maintenance et un encombrement réduits. Plus important encore, il est devenu plus abordable, ce qui le rend plus attrayant pour de nouvelles applications et pour un plus grand nombre d’entreprises. Dans les prochaines années, le brasage robotisé va continuer à se développer, notamment la partie « logiciel »... Soyez prêt pour l’avenir et restez à l’affût des nouvelles solutions !
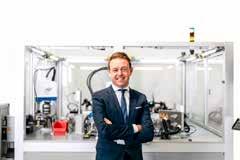
CEPELEC Mélissa LANFREY +33(0)4 76 49 00 37 cepelec@cepelec.com www.cepelec.com
Dossier Sérigraphie
SÉRIGRAPHIE : L’automatisation des changements de pochoirs de sérigraphie et de pâte à braser améliore la productivité de la production CMS
Aujourd’hui, les entreprises de fabrication électronique, qu’il s’agisse de fabricants d’équipements d’origine ou de sous-traitants, doivent être en mesure de gérer des composants variés, des plus petites puces CMS aux gros semi-conducteurs, ou inhabituels, comme les connecteurs traversants de grande taille. En outre, elles connaissent toutes des changements de produits fréquents, qui doivent être effectués de manière aussi rapide et efficace que possible
Laccélération des changements de produits
Pour l’assemblage de cartes à grande vitesse sur une ligne de production CMS, et dans les scénarios de fabrication qui impliquent de nombreux changements quotidiens, l’automatisation d’un maximum de tâches liées aux changements de produits permet de gagner du temps et d’éviter les erreurs humaines susceptibles d’entraîner des pertes de production et de nécessiter un temps supplémentaire pour les corriger. Les systèmes de basculement de programme automatique (APCO) accélèrent les changements de programme et garantissent que le programme correct soit chargé sur toutes les machines de la ligne. Au niveau des machines de placement de composants, il est possible de configurer les chargeurs pour enchaîner plusieurs produits. Les reparamétrages des chargeurs peuvent être effectués hors ligne avant de les replacer sur la machine à temps pour le changement de produit. Les feeders à chargement automatique peuvent ensuite commencer à fournir les nouveaux composants à la machine. Les changements sont plus complexes dans le cas de la sérigraphie, car il faut généralement retirer la pâte du pochoir, le nettoyer, le retirer et le remplacer par un autre pochoir, reconfigurer les pions de maintien et réinitialiser la racle. L’Illustration 1 récapitule toutes les actions nécessaires. À chaque changement, l’assemblage doit être interrompu et ne peut reprendre qu’une fois toutes ces actions terminées. Comme indiqué, l’ensemble du processus peut prendre 10 à 15 minutes. Parmi ces tâches, les opérations telles que le retrait et le remplacement du pochoir nécessitent généralement un opérateur parfaitement formé pour être exécutées correctement. Ce sont des tâches minutieuses, généralement difficiles à automatiser lors des changements de produits en sérigraphie. Aujourd’hui, après avoir revu en profondeur la structure interne de sa machine de
L’ensemble du processus de changement dure 3 à 5 minutes seulement et la production peut reprendre immédiatement, sans autre vérification, réglage ou conditionnement de la pâte à braser...
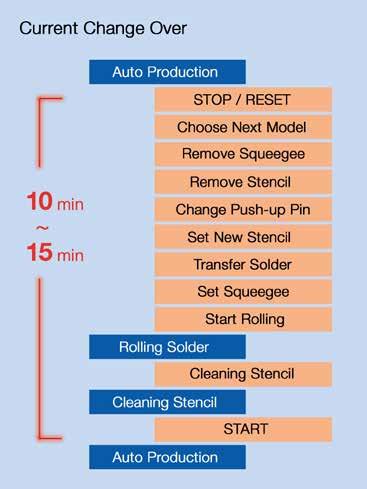
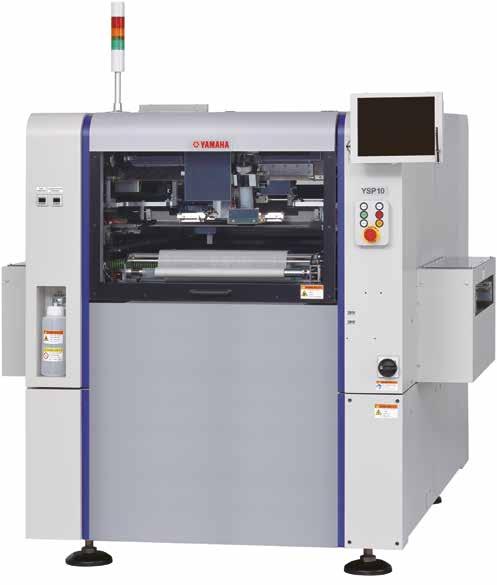
Illustration 2. La machine de sérigraphie YSP10 de Yamaha, conçue pour les changements automatiques
sérigraphie standard, Yamaha a créé la nouvelle YSP10 (Illustration 2), lauréate du prix Global SMT, qui permet des changements automatisés : remplacement du pochoir, repositionnement des pions de maintien des cartes, retrait et remplacement du rouleau de pâte à braser sur le pochoir suivant. L’ensemble du processus de changement dure à 3 à 5 minutes seulement et la production peut reprendre immédiatement, sans autre vérification, réglage ou conditionnement de la pâte à braser. La séquence indiquée sur l’Illustration 3 montre cette réduction drastique du temps de changement.
Allier la nouveauté aux éléments éprouvés
La tête 3S (swing single squeegee) de Yamaha (Illustration 4) optimise l’angle de racle grâce à un réglage servocommandé pour assurer une ouverture optimale. On sait que l’angle de racle impacte davantage le dépôt de pâte que d’autres paramètres comme la vitesse et la pression de la racle. Attention, il est possible qu’un solvant présent sur la surface du pochoir à la toute fin d’un cycle de nettoyage entraîne des dépôts de brasure défectueux sur les premières cartes à sérigraphier après le redémarrage. C’est pourquoi notre machine de sérigraphie est dotée d’un système d’ajustement automatique de l’ouverture, qui modifie automatiquement l’angle de racle pour compenser les différences de remplissage dues au solvant. Cette fonction permet d’éviter des défauts de sérigraphie, sans aucune action ni aucun délai supplémentaires pour le séchage du pochoir.
La conception de la tête s’appuie sur une technologie de racle unique, dotée d’une lame flexible d’une épaisseur de 100 microns seulement, avec un revêtement antifriction de 10 microns identique à celui appliqué sur les parois des cylindres des moteurs de motos haute performance de Yamaha, afin de minimiser le gaspillage d’énergie et de prolonger la durée de vie. Ce revêtement prévient l’usure de la racle et du pochoir, d’où une meilleure répétabilité, de meilleurs résultats en cas de sérigraphie avec des pochoirs étagés, mais aussi une réduction du coût total de possession du processus de sérigraphie.
La racle, associée à la tête 3S, donne des résultats supérieurs dans l’exécution de certains processus comme la technologie pin-in-paste. La sérigraphie peut remplir des trous métallisés (PTH) en un seul passage de racle, contrairement à d’autres systèmes avec un angle fixe et une lame rigide. Les fabricants qui doivent effectuer des processus pin-in-paste efficaces pour des assemblages contenant, par exemple, de gros connecteurs automobiles multibroches traversants, apprécieront le gain de temps, de qualité et de répétabilité qu’offre ce système.
La nouvelle disposition interne de la machine de sérigraphie permet des changements automatiques de pochoir. Le mécanisme de maintien sous vide du pochoir assisté de Yamaha garantit en effet une précision et une répétabilité de positionnement élevées. Le vide appliqué sur la partie métallique du pochoir élimine
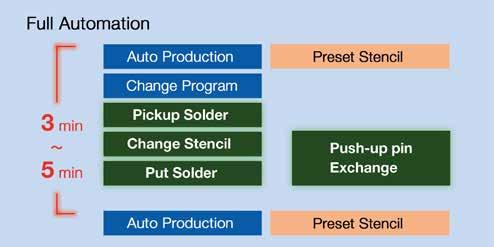
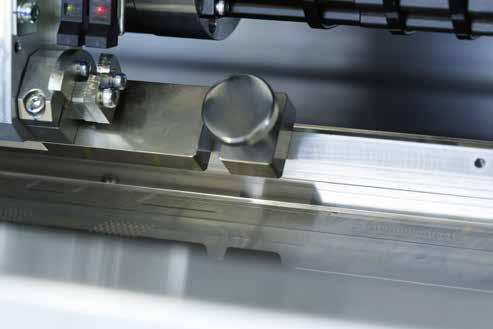
Illustration 4. La tête 3S permet d’optimiser automatiquement l’angle de racle
les effets de distorsion du cadre du pochoir et minimise les imprécisions lors du passage de la racle. Les capacités de sérigraphie et la régularité du dépôt de pâte à braser s’en trouvent toutes deux améliorées. En plus du mécanisme de maintien du pochoir, le système d’alignement visuel graphique de la machine facilite l’alignement rapide et intuitif du pochoir et de la carte, pour qu’il soit parfait même lorsque les mires sont médiocres, voire inexistantes.
Enfin, des fonctions comme l’autoapprentissage des pions sont devenues incontournables sur les dernières générations de machines de sérigraphie. Elles simplifient la génération de programmes en déterminant automatiquement la position optimale des pions de maintien à partir d’informations de CAO (par ex. données Gerber) ou d’une image numérique haute résolution de la carte. La suite d’outils de changements automatisés gère donc désormais aussi le changement automatique des pions.
La manipulation du rouleau de pâte à braser est également automatisée afin d’optimiser la gestion de la pâte à braser restant sur le pochoir au moment du changement. La pâte est automatiquement retirée du pochoir et conservée sous sa forme de rouleau. Elle peut ensuite être redéposée sur la surface du nouveau pochoir. Avant de relancer la sérigraphie, le diamètre du rouleau de pâte est mesuré, et plus de pâte à braser est ajoutée si nécessaire, en fonction du système de contrôle de la stabilité de sérigraphie (PSC). Ce mode de fonctionnement présente deux gros avantages : l’opérateur n’a plus de contact avec la pâte à braser, et il n’y a pas de perte de temps associée au reconditionnement de la pâte fraîchement déposée. La sérigraphie peut se poursuivre immédiatement, en suivant le nouveau programme, dès l’entrée de la première carte du nouveau lot dans la machine. Le système PSC mesure régulièrement le diamètre du rouleau de pâte pendant le fonctionnement normal de la machine, ce qui améliore la répétabilité du processus en garantissant un dépôt homogène.
Une inspection précise intégrée
D’après un utilisateur basé en Belgique travaillant sur une ligne de production dédiée à l’assemblage automobile, le système d’inspection en 2D intégré de notre machine de sérigraphie YSP10 affiche une précision comparable à celle d’un système d’inspection de la pâte à braser (SPI) dédié en 3D. De fait, ce système 2D intégré (Illustration 5) garantit des résultats fiables d’inspection de la pâte à braser dans le temps de cycle standard de la machine de sérigraphie. Doté d’un champ de vision de 30 mm x 22,5 mm et d’une résolution de 18,7 µm, ce système peut déceler les défauts de sérigraphie sur des modèles de dépôt délicats pour des composants tels que les petites puces CMS et les boîtiers BGA de 0,5 mm. Il renvoie alors automatiquement des informations pour déclencher le nettoyage du pochoir si des problèmes de pâte sont décelés.
Conclusion
Les tâches associées aux changements de sérigraphie sont depuis toujours les plus difficiles à automatiser. Les opérations aval comme le montage et l’inspection ont bénéficié d’une automatisation, mais les changements de sérigraphie restent une tâche qui revient aux opérateurs. Cette dernière barrière vient de tomber, permettant l’automatisation des tâches liées aux changements de produits sur toutes les machines de la ligne de production CMS, d’où une productivité et une qualité renforcées.
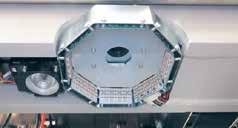
Illustration 5. L’inspection 2D intégrée peut être aussi précise qu’un système SPI dédié.
YAMAHA MOTOR Oumayma GRAD +49-2131-2013538 oumayma.grad@yamaha-motor.de www.yamaha-motor-im.de
ESTELEC GROUPE surfe sur les crises et vise un chiffre d’affaires de 30 M€ à l’horizon 2025.
Par Dominique LEMIERE, reporter.
Appuyé sur une stratégie volontariste, le sous-traitant alsacien maintient une croissance forte dans un contexte économique en pleine mutation.
Pour Rémi Boehler cogérant d’Estelec, crise n’est pas synonyme de repli, bien au contraire. « Je n’irai pas jusqu’à dire que cette attitude nous caractérise », risque-t-il, « mais à chacune des crises que nous avons traversées, nous avons de façon constante amplifié l’investissement ». L’entreprise alsacienne, qui compte 100 salariés et réalise 16,5 M€ de chiffre d’affaires n’a pas dérogé à ses objectifs de croissance, malgré la crise sanitaire et la pénurie des composants. Aujourd’hui, le fabricant d’ensembles et sous-ensembles électroniques de Scherwiller (Bas-Rhin) ne fait pas mystère de son ambition de doubler son chiffre d’affaires en 3 ans et d’atteindre la taille d’une ETI sous quelques années. Et par-delà, prendre la tête du marché de l’électronique du Grand Est. La stratégie de déploiement mise en place vise 3 objectifs majeurs : défendre durablement la production de cartes, de sous-ensembles et ensembles électroniques en France, diversifier ses services afin d’accompagner les clients vers des solutions intégrées, et augmenter la masse critique afin d’accroître les investissements et anticiper les sauts technologiques de la filière. Les projets foisonnent et prennent corps. « Nous nous sommes toujours battus pour nous développer commercialement, nous n’avons jamais abandonné la prospection, l’investissement dans les équipements, la formation, quelles que soient les circonstances » revendique Rémi Boehler.
Le plan France Relance a désigné Estelec Groupe parmi les 42 lauréats du volet « Relocaliser ». Ce soutien aux investissements de secteurs aussi stratégiques que
Le plan France Relance a désigné Estelec Groupe parmi les 42 lauréats du volet « Relocaliser ». Ce soutien aux investissements de secteurs aussi stratégiques que l’électronique « Made in France » est une aubaine et un encouragement pour le groupe alsacien - pour mener à bien sa mission de motiver les donneurs d’ordres à relocaliser leurs productions en France ...
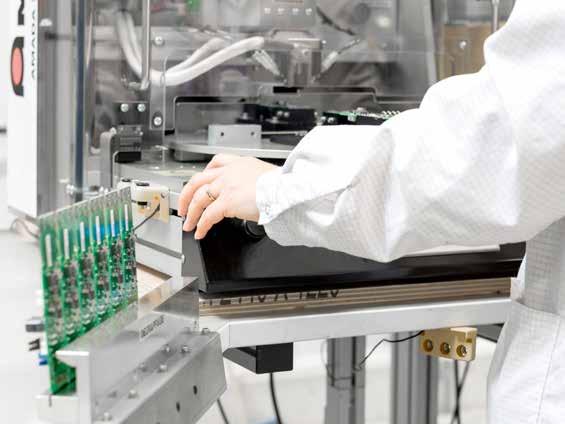
l’électronique « Made in France » est une aubaine et un encouragement pour le groupe alsacien - pour mener à bien sa mission de motiver les donneurs d’ordres à relocaliser leurs productions en France. L’enveloppe de ce fonds, qui financera 800 000 € sur les 3 millions d’investissements prévus sur deux ans, va permettre à Estelec de poursuivre sa modernisation industrielle et embaucher du personnel ad’hoc. En outre, Estelec Industrie fait partie du programme d’accélération de la BPI destiné à transformer des PME en ETI, et tracer la feuille de route d’une stratégie de croissance ambitieuse.
« Inciter nos clients à fabriquer en France » Bien qu’Estelec Groupe fasse partie des fabricants français qui ont choisi de conserver l’intégralité de leur production de cartes et câbles électroniques en France, la crise sanitaire a brutalement révélé la réalité de la dépendance à l’Asie : une situation somme toute confortable, pratiquée pendant des décennies, et qui s’est muée en quelques semaines en cauchemar lorsque la Covid a quasi totalement bloqué les échanges commerciaux.
Rémi Boelher se souvient de cette année 2001 où fut décrété que les usines devraient majoritairement être « fabless » en France. « Je n’étais pas d’accord, je pensais que c’était de la folie. » « Peut être était-ce valable pour certains produits grands public, livrés à une forte concurrence », admet-il. « Cependant, l’idée dominante était qu’on avait plus grand-chose à faire en France et qu’il fallait à tout prix délocaliser. Ce message qui passait par les acheteurs avait gagné les banques, qui se sont montrées très réticentes à prêter de l’argent aux industriels de l’électronique ».
Des limites acceptables
« C’est désormais à nous de convaincre nos clients de ne pas s’engager dans ce processus », martèle Rémi Boehler. « Nous avons des prospects - qui viennent à nous et qui n’avaient pas ce réflexe auparavant, le produit partait directement au Maghreb ou en Asie, sans la moindre consultation sur le sol national. » Aussi, la démarche pro-active d’Estelec vise des secteurs comme le médical ou le ferroviaire, qui ont besoin de moyennes séries et de réactivité. Ceux-là pourraient privilégier une production locale. Ou encore envisager une relocalisation hybride, dans laquelle leurs clients continueraient à envoyer la majeure partie de leur production électronique vers les pays à bas coût - tout en conservant une partie en France. « Ils seront sans doute intéressés par une production locale, si l’écart de prix reste dans des limites qu’il jugent acceptables ». Rémi Boelher analyse qu’au-delà des problèmes purement liés à la logistique, les émissions de CO2 sont devenues une préoccupation mondiale. « Le Made in France est un bon argument de vente. Mais cela ne sera jamais suffisant si on ne répond pas avant tout aux besoins du marché. Beaucoup de petits composants achetés en Asie n’ont pas une empreinte carbone très forte. En revanche, faire l’assemblage et la valeur ajoutée en France, cela a quand même du sens ! Pour certains de nos clients, la réduction de l’empreinte carbone est une préoccupation forte, qu’ils ont à l’esprit ». En termes de croissance externe, l’acquisition intervenue au 1er janvier 2021 de Scaita, une société basée à AspachMichelbach, spécialisée dans la fabrication de carte, faisceaux et câbles électroniques - laquelle compte 34 salariés et a réalisé un chiffre d’affaires de 5,5 millions d’euros en 2019 - permet aujourd’hui à Estelec de proposer des solutions d’intégration et de test de haut niveau.
Dès la mi-2022, le site de Scaita sera en outre étendu de plus de 1000 m2 pour accueillir les nouveaux services d’Esteconnect, des faisceaux et câbles électroniques et d’Estebox pour l’intégration de produits électroniques. Le site Estelec Industrie devrait encore doubler sa surface de production d’ici 2022/2023 et y développer son offre Estest pour le test, et l’offre Estecarte pour les très grandes séries. Pour accompagner son développement par croissance externe, Estelec Industrie a changé de nom pour devenir Estelec Groupe. Ses deux sites de production gardent leur désignation d’Estelec Industrie pour le site de Scherwiller ; et de Scaita pour celui d’Aspach-Michelbach.
« La fin de la crise arrivera »
Crise sanitaire, pénurie des composants, pareil background aurait pu freiner les projets des dirigeants d’Estelec. « Cela n’est pas arrivé », indique Rémi Boehler « En pleine crise il y a beaucoup d’inquiétudes, on se pose davantage de questions. Pourtant, ce que nous gardons à l’esprit, c’est que la fin de la crise interviendra à un moment ou l’autre. La crise que nous vivons aujourd’hui est particulière : on ne pensait pas qu’elle allait durer aussi longtemps, c’est un élément nouveau dont il faut tenir compte. Mais nous avons choisi de faire front, de rester malgré tout fidèles à notre stratégie de nous développer sans relâche. Nous avons continué à investir en moyenne 5 à 10 % du chiffre d’affaires, y compris avec des embauches, au moment où tout s’arrêtait à cause de la Covid. Pas nous ! Nous avons toujours opposé aux crises une stratégie volontariste. En 2003, nous avions acheté une ligne CMS d’un million d’euros. En 2008, nous avons investi 2,4 M€ pour un bâtiment sur le site de Scherwiller. Nous avons embauché 15 personnes depuis début 2021 et nous restons dans cette dynamique, en prévoyant l’embauche d’une vingtaine d’ingénieurs, techniciens et agents de production sur deux 2 ans. »
Sonnette d’alarme
L’autre crise, celle de la pénurie de composants qui sévit depuis plus d’un an n’a pas épargné le sous–traitant alsacien. Estelec a partiellement réussi à en amortir le choc en tirant la sonnette d’alarme. « Un certain nombre de nos clients avait
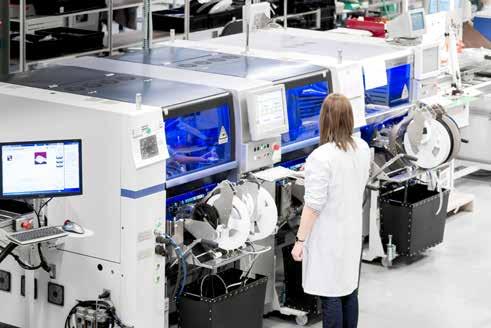