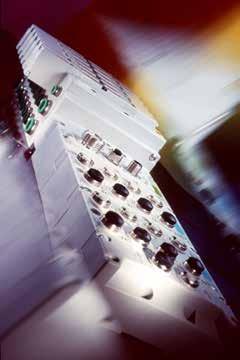
110 minute read
Dossiers
Editorial
Stéphane ELKON Co-fondateur de *Hardware France A un mois du CES, 6 raisons de s’intéresser aux fabricants de biens électroniques français
La grande messe de l’électronique mondiale ouvrira ses portes dans un mois. La France est connue pour sa participation massive. Plus d’une centaine de startups, PME et PMI font le déplacement, chaque année, pour montrer leur excellence et créativité.
La France des biens électroniques brille aujourd’hui, et brillera plus encore demain.
Pourquoi ? La première raison réside dans les capacités de conception et de production qui rendent à présent possible le made in France. La crise du Covid a en effet eu un double effet : d’une part, elle a incité certains sous-traitants français qui travaillaient exclusivement pour certaines verticales (aéronautique, automobile..) à diversifier leur portefeuille de clients. D’autre part, les porteurs de projets se sont rendus compte que la fabrication des produits en Asie faisait de moins en moins sens, notamment en raison des coûts de transport. Ils se sont alors adressés aux sous-traitants français qui sont parvenus à proposer des coûts équivalents, grâce à l’optimisation de la conception produits, à leur compétence en matière d’industrialisation et à l’automatisation des chaînes de montage.
La deuxième raison est à rechercher dans le positionnement des produits électroniques français. Nos fabricants nationaux ont une approche du marché particulièrement adroite. Certains réinterprètent ou transcendent un produit existant et font preuve d’une grande ingéniosité pour se différencier en matière d’usage et de performances. D’autres créent des produits totalement nouveaux, car ils ont compris que les produits électroniques sont appelés à répondre à des besoins toujours plus spécifiques. Le temps où les « couteaux suisses numériques » (smartphones, ordinateurs) régnaient en maîtres touche à sa fin. La garantie d’usage sûr et à faible emprunte environnementale est un autre atout des produits électroniques made in France. Les clients sont chaque jour plus sensibles à la sécurité et l’impact écologique des produits et les biens made in France se distinguent vis-à-vis de ces attentes. Il est même probable que dans l’esprit du consommateur, la perception des produits électroniques français deviendra semblable à celle qu’ils ont des produits « bio », des produits qui ne trichent pas et qui sont bons pour l’environnement et la santé. La quatrième raison tient au progrès technologique, qui rend possibles de nouveaux usages, services et revenus. Les produits électroniques embarquent en effet de plus en plus d’intelligence dans leurs circuits, grâce notamment à l’avènement des puces IA. Cela ouvre des horizons totalement nouveaux, en termes de revenus récurrents, de services à forte valeur ajoutée et d’écosystèmes de services associés fidélisant les clients. Les fabricants ne perçoivent plus un seul paiement, au moment de la vente du produit, mais tout au long de sa durée de vie. Autrement dit, le mariage des business models hardware et software est annoncé !
La cinquième raison réside dans la protection renforcée de l’innovation. Jusqu’ici, les fabricants disposaient de la seule protection des brevets. Avec l’avènement des produits électroniques intelligents, ils vont pouvoir donner davantage de fil à retordre à leurs concurrents. Ceux-ci pourront toujours démonter le produit et s’inspirer de ses composants, mais il leur manquera un élément clé : le logiciel intégré, source de l’intelligence. En détenant les clés d’accès au cœur de leur produit, les fabricants pourront ainsi bénéficier d’une solide avance sur leurs concurrents.
Enfin, les biens électroniques français portent de plus en plus d’enjeux pour notre pays. Le monde numérique de demain ne sera plus basé sur des ordinateurs et des smartphones, sur lesquels tout logiciel peut fonctionner. Il sera composé d’une multitude de produits électroniques protéiformes (robots, automobiles, assistants ...), qui feront tourner des logiciels. Grâce à une position forte sur le hardware, nous garderons notre position de leader dans le domaine du logiciel. Par ailleurs, les enjeux en termes de souveraineté de l’électronique pour notre pays ne sont aujourd’hui plus à démontrer. Plus notre pays brillera dans les produits électroniques, plus il pourra se préserver des effets des crises mondiales et garantir sa souveraineté. Le « numérique du tangible » arrive. Il constitue non seulement une opportunité unique, pour notre pays, mais également une nécessité. Alors, allons applaudir l’« équipe de France » des biens électroniques qui ira défendre nos couleurs au CES début janvier !
*Hardware France est une association qui réunit, pour la première fois, les fabricants français de produits finis électroniques/ hardware et les acteurs de l’écosystème contact@hardware-france.fr https://www.hardware-france.fr/
Membres fondateurs : Acepelec, Altyor, Artifeel, Bycol, Centiloc, Covade, D’Com Conseil, Enéad, Esquisse 3D, FCDRA, Good Angel, Mootion, My Goodlife, Prisme Studio, Prisme Technologies, uPesy, Vialog, Yomy
La mécatronique s’offre un bon 3ème trimestre mais se prépare à des mois difficiles
Présentes dans toutes les machines industrielles ou mobiles, et dans tous les moyens de transport, les professions d’ARTEMA – l’organisation professionnelle des industriels de la Mécatronique - réalisent globalement un 3ème trimestre correct mais s’inquiètent beaucoup de la conjoncture des prochains mois...
Laurence Chérillat, déléguée générale d’ARTEMA
Laurence Chérillat, déléguée générale d’ARTEMA déclare « Avec le même nombre de jours ouvrés que l’année dernière, l’Indicateur global ARTEMA a bien résisté pendant le troisième trimestre avec une reprise des facturations due en grande partie au secteur Automobile qui a vu ses immatriculations repartir en zone positive par rapport à la même période de 2021. Cependant, ce marché reste morose et le niveau de 2019 reste un lointain souvenir. » L’Industrie hors automobile se porte bien dans l’ensemble. Certaines professions ont observé un été plutôt calme mais sans inversion de tendance. Les commandes étaient moins nombreuses mais toujours là. Le mois de septembre a confirmé cette tendance.
Le carnet reste toujours solide, mais moins garni qu’au printemps. Pour beaucoup, l’année calendaire est déjà faite et sauf catastrophe, 2022 s’annonce positive, en valeur, en raison de carnets de commandes qui ont été bien garnis en 2021 et sur la 1ère partie de l’année. « Mais l’avenir s’assombrit : les soucis de matières, de pénuries de produits chez les clients engendrent parfois de lourdes conséquences. Pour une pièce (parfois même très petite et peu coûteuse) qui manque et plus particulièrement les semiconducteurs, les clients ne peuvent livrer leurs machines et donc reportent leurs commandes aux fabricants de composants. »
INDICATEUR GLOBAL ARTEMA ZOOM 2016-2022
( 100 répondants chaque mois)
+100 : Tous les répondants ont réalisé un meilleur mois que l'année dernière
janv-16 févr-16
mars-16 avr-16 mai-16
juin-16 juillet-août 16 sept-16 oct-16 nov-16
déc-16 janv-17 févr-17
mars-17 avr-17 mai-17 juin-17 juillet-août 17
sept-17 oct-17 nov-17
déc-17 janv-18 févr-18 mars-18 avr-18
mai-18 juin-18 Juillet-Août
sept-18 oct-18 nov-18 déc-18 janv-19
févr-19 mars-19 avr-19
mai-19 juin-19 Juillet-Août 2019
sept-19 oct-19 nov-19 déc-19 janv-20
févr-20 mars-20 avr-20
mai-20 juin-20 Juillet-Août 2020 sept-20 oct-20
nov-20 déc-20 janv-21
févr-21 mars-21 avr-21 mai-21 juin-21
Juillet-Août 2021 sept-21 oct-21
nov-21 déc-21 janv-22 févr-22 mars-22
avr-22 mai-22 juin-22
Juillet-Août 2022 sept-22
Activité du mois étudié
Activité des 3 prochains mois
Carnet à la fin du mois étudié
-100 : Tous les répondants ont réalisé un mois inférieur à l'année dernière Le carnet reste toujours solide, mais moins garni qu’au printemps. Pour beaucoup, l’année calendaire est déjà faite et sauf catastrophe, 2022 s’annonce positive, en valeur, en raison de carnets de commandes qui ont été bien garnis en 2021 et sur la 1ère partie de l’année.
Ilot de distribution
Droits réservés ARTEMA
« Mais le pire est ailleurs, un cataclysme énergétique et financier se profile à l’horizon. La hausse du prix du gaz et de l’énergie en général induit une multiplication des factures énergétiques par 4 ou même par 7 chez nombre d’industriels, en particulier pour ceux qui intègrent du traitement thermique, opération indispensable pour la mécatronique, » reprend Laurence Chérillat.
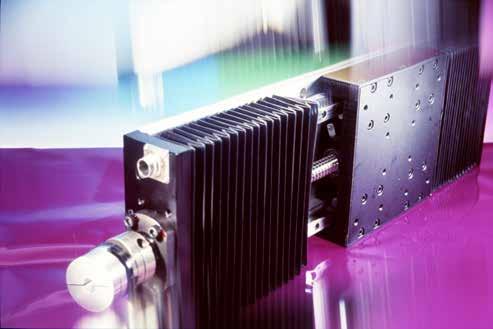
Les filières amont : forge, fonderie, sidérurgie, traitement de surface… et toutes les industries fortement consommatrices d’énergie se voient menacées dans leur existence même et risquent d’être obligées d’arrêter leur production. Autres indicateurs préoccupants : l’Allemagne qui est le principal pays client de la France s’attend à une récession imminente. La Chine, elle, traverse une crise immobilière et peine à recruter, sans compter la reprise des confinements dans certaines zones. Les révisions à la baisse des prévisions de croissance du pays s’enchaînent. De manière générale, l’économie mondiale change. L’inflation mondiale est bien présente, les crises des matières premières et les différentes pénuries, les conséquences du conflit en Ukraine, ont été des éléments qui ont incité les banques centrales à remonter leurs taux, ce qui conduit notamment de manière automatique à faire baisser les marchés financiers.
« Dans ce contexte de plus en plus fébrile, terreau fertile pour de nouvelles crises, les prévisions deviennent de plus en plus difficiles. Les professions ressentent toutes cette inquiétude générale, notamment pour le 2ème semestre 2023 mais à ce jour l’activité reste, tant au niveau des chiffres que des carnets, relativement correcte » conclut Laurence Chérillat.
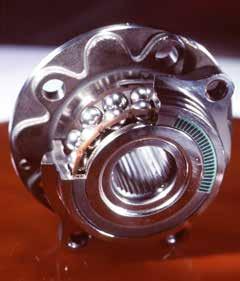
À propos d’ARTEMA
ARTEMA est l’organisation professionnelle de référence des industriels de la Mécatronique. Elle rassemble 150 entreprises qui conçoivent, produisent, commercialisent et assurent la maintenance des composants, solutions ou systèmes qu’elles fabriquent. Les adhérents sont des PME, ETI ou groupes internationaux des domaines suivants : Etanchéité industrielle ; Fixations ; Mécatronique ; Roulements et Guidages linéaires ; Transmissions Hydrauliques, Transmissions et Automatismes Pneumatiques et Transmissions Mécaniques.
Ces professions représentent : - 7,6 milliards de chiffre d’affaires dont 50 % à l’export, - 35 000 salariés dédiés. ARTEMA est membre de la FIM (Fédération des Industries Mécaniques) et des comités européens CETOP, EIFI, EUROTRANS et FEBMA. Communiqué de presse à retrouver dans les publications du site artema-france.org
Table mécatronique
Droits réservés ARTEMA
Contact presse : Marion Poulain – ARTEMA Tél : 01 47 17 63 07 06 10 41 22 07 mpoulain@artema-france.org
Sobriété énergétique : les industriels traquent les économies d’énergie
Par Dominique Lemière, reporter
Confrontés à une situation inédite, les industriels se mobilisent pour juguler leur dépense énergétique. Ils nous livrent leur méthode, mais aussi leurs inquiétudes.
Aux entreprises comme aux particuliers, le gouvernement le martèle à qui mieux mieux : chacun doit faire des efforts de sobriété énergétique pour tenter d’éviter les coupures d’électricité et de gaz que l’Etat redoute pour cet hiver. Ainsi, Agnès PannierRunacher a annoncé fin juin le lancement d’un « Plan sobriété énergétique » Objectif : réduire de 10% nos consommations d’énergie d’ici à 2024, et de 40% d’ici à 2050. Mais ce plan, jugé plus proche de l’usine à gaz que d’un bouclier pour lutter contre la hausse du prix de l’énergie, n’a pas convaincu les industriels : trop lourd, trop compliqué. Les entreprises ne se sont pas bousculées aux guichets. Le ministère de l’Economie et des Finances ne s’est pas déclaré vaincu pour autant. Il s’est attelé à élaborer un nouveau plan dévoilé le 19 novembre et censé se révéler plus attractif. Il est trop tôt, à l’heure où nous écrivons, pour savoir si ce plan séduira davantage les intéressés.
Quoi qu’il en soit, force est de constater que depuis un an, le bouclier tarifaire s’est imposé dans le vocabulaire et la panoplie de mesures anti-inflation du gouvernement. Bouclier pour le Covid, bouclier pour l’énergie nous voilà donc amenés à croire que nous sommes d’une certaine façon, protégés. Mais dans la réalité ces boucliers sont des trompe-l’œil. Sans minimiser leur nécessité ponctuelle, les boucliers, comme les médailles, ont leur revers. Et il n’est pas sûr que ces revers ne soient pas à terme, plus pernicieux que leurs avantages supposés.
Fortes incertitudes
A quoi servent les boucliers tarifaires ? La question peut paraitre simpliste : ils neu-
Les boucliers masquent les prix réels. Ils les bercent d’illusions sur la santé réelle de l’économie du pays. Les industriels ne s’y trompent pas. Si le recours aux aides du premier plan n’a pas eu le succès escompté, c’est que les incertitudes restent fortes.
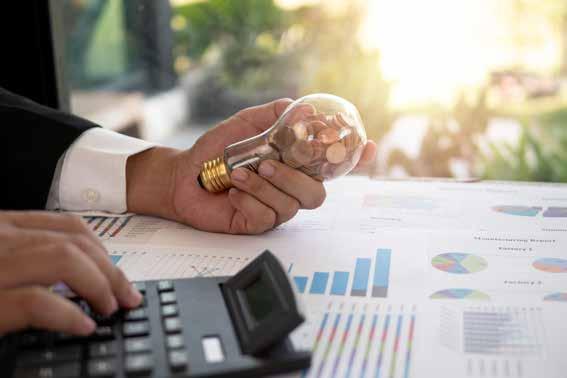
iStock : x-refleynaja
tralisent en principe les hausses de prix. Mais ils induisent également l’idée que l’inflation est plus basse en France que chez nos voisins européens. Les boucliers masquent les prix réels aux citoyens. Ils les berce d’illusions sur la santé réelle de l’économie du pays.
Les industriels ne s’y trompent pas. Si le recours aux aides du premier plan n’a pas eu le succès escompté, c’est que les incertitudes restent fortes. Comme en 1973, la hausse des prix de l’énergie a pris par surprise les gouvernements européens. Ils ont été rapides à imposer des sanctions à la Russie après son invasion de l’Ukraine, mais plus lents à réfléchir aux conséquences économiques. En ce qui concerne la France, aujourd’hui on ne sait pas quel sera le volume d’Arenh*, c’est-à-dire le nombre de mégawatts vendus à prix cassés par EDF. La France est en ce moment en discussion avec la Commission européenne à ce propos. Ce chiffre est important, puisqu’il conditionne le calcul de l’augmentation des prix tel que calculé par la CRE* en janvier. Il déterminera le montant de la compensation pris par l’Etat suite à sa décision de bloquer l’augmentation à 15 %. Inconnus aussi, les prix du gaz et de l’électricité de décembre sur lesquels s’appuiera la CRE. D’autant que si la Commission s’agite pour plafonner les prix, on ne sait pas ni comment, ni quand, ni dans quelle mesure cela aura une influence sur les prix. La raison : la situation catastrophique d’EDF, plombée par une dette record, qui l’empêche d’investir et de redresser ses finances et qui n’entend pas brader ses très précieux KW…
Coup de bluff
Autre coup de bluff, le gouvernement s’évertue à faire croire que nos difficultés relèvent de la guerre russo-ukrainienne et nommément de Vladimir Poutine. Sans rien vouloir enlever au pouvoir de nuisance du Maître du Kremlin, c’est bien la politique menée par nos gouvernements, et notamment celle qui a mené au sabotage de notre industrie nucléaire, sous la pression des écologistes français et allemands. C’est cette politique qui est responsable de la dépendance énergétique absurde dans notre pays - puisque nous avions toutes les cartes en main pour l’éviter. Cette situation qu’on peut qualifier de suites d’erreurs dramatiques et d’absence de prospective impardonnable est parfois vécue comme une trahison par les industriels : certains s’en sont exprimés dans le cadre de cet article. Voici, à micro ouverts, ce qu’ils ont confié aux Cahiers.
Alain-Michel Ceretti – Directeur commercial d’Europlacer : DES SITUATIONS
CONTRASTÉES.
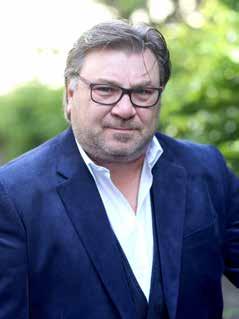
« Je déplore que mes clients, les sous-traitants, soient hyper exposés. Au-delà des divers plans du gouvernement pour aider les industriels, je ne suis pas sûr que certaines PME de la sous-traitance soient en mesure d’absorber le choc. Je crains que cela ne soit pas suffisant pour certains. La situation est très différente d’une entreprise à l’autre. J’ai des clients dont le contrat EDF de 3 ans a été renouvelé en 2021 à 120 € le MWh. Pour eux ça passe. Mais d’autres, pour qui l’échéance arrive fin 2022, ne savent pas encore ce qui va se passer. Ils ne connaissent pas encore les tarifs qui leur seront appliqués. Cette situation est terrible. »
Jean-Baptiste VENE – directeur général de Fenwick, distributeur FUJI depuis 1981) : NE PAS ABANDONNER LE
SOUTIEN À L’INDUSTRIE TROP TÔT . « Pour un distributeur comme Fenwick, l’impact des coûts énergétiques est beaucoup moins dramatiques que pour certains industriels. En revanche, nous sommes touchés parce que nos clients sont touchés. En France, on ne ressent pas encore tellement le problème, parce qu’à mon avis, nous sommes mieux protégés que d’autres pays d’Europe. Mais Fenwick opère aussi en Espagne, au Portugal, en Italie et au Benelux. En Italie, le problème est ressenti depuis le début de l‘été, l’impact sur nos clients a été plus violent et plus immédiat qu’en France. Nous connaissons actuellement quelques ralentissements de paiement avec certains clients. Certains nous demandent de la flexibilité sur les termes de paiement. En cause, des problèmes de trésorerie générés par les stocks intermédiaires qui se sont empilés en raison des ruptures d’approvisionnement des composants. Ce problème est amplifié ou encore davantage, par leur facture d’énergie. Et tout cela malgré des mix énergétiques avec par exemple des panneaux solaires sur le toit des usines. Cela a bien sûr des conséquences sur Fenwick en tant que distributeur. D’ailleurs, le Groupe Fenwick n’élude pas la problématique d’énergie : notre siège social a été réaménagé il y a 3 ans notamment en tenant compte d’économies d’énergie souhaitées. En Italie, où nous sommes propriétaires de notre siège social, nous avons fait construire un nouvel immeuble en 2019, où nous avons mis en place un mix avec des énergies renouvelables, et des panneaux solaires sur le toit. A titre personnel, j’espère que le gouvernement va soutenir les industriels : il s’agit d’un écosystème. Dans une période où le sentiment pro business dans ce pays semblait enfin revenu ; dans une période où l’on commençait à entendre parler de petites relocalisations chez certains clients ; dans une période où l’on percevait que le climat était de nouveau un peu plus favorable à l’industrie, ce serait dommage de tout gâcher et tout remettre en question parce que, malheureusement, nos coûts d’énergie s’envolent, comparativement à d’autres grandes régions du monde que sont l’Asie ou l’Amérique. Dans un pays où l’on devrait avoir de l’énergie nucléaire bon marché, on a arrêté d’investir dans les réacteurs d’EDF pour des raisons idéologiques et politiques aberrantes prises il y a des années : on en paye le prix aujourd’hui. C’est une situation ubuesque.
Grégory Lacroix, patron de G4-Sourcing : IL FAUT REVENIR A DES METHODES DE TRAVAIL PLUS SOBRES. Le distributeur héraultais vient de finaliser la construction d’un nouveau bâtiment résolument économe en énergie
« Nous avons construit ce nouveau bâtiment avec un coût de l’investissement de plus d’un million d’euros au total. Nous prévoyons un budget électricité de 21 000 € pour 2023. Nous pensons dépenser 54 KWh sans bouclier tarifaire. Uns fois connu ce bilan pévisionnel de consommation, nous avons lancé notre projet immobilier. Et maintenant, nous devons faire vivre tout cela !
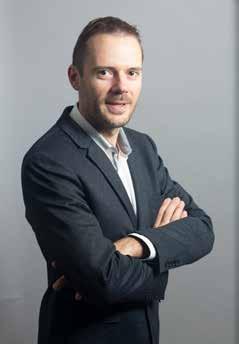
n’avons pas attendu le plan du gouvernement pour être sobres. Nous avons mené une vraie réflexion sur la façon de réduire les coûts à tous les niveaux dans ce nouveau bâtiment. Et ceci tout en maintenant un confort de travail et une qualité de service qui soient optimaux. Cela s’est traduit par exemple par l’isolation extérieure et intérieure de nos murs. Pas avec de l’isolant classique : mais des Isolants intérieurs de haute densité de 13 cm d’épaisseur.
La performance énergétique du bâtiment a été la première chose à laquelle je me suis intéressé. Outre les doubles vitres intérieures et extérieures, nous avons mis en place des panneaux solaires, parce que sur les compteurs jaunes, il n’existe pas de bouclier tarifaire. Aujourd’hui, on m’annonce une consommation de 21 000 euros par an. Ce qui signifie qu’avec les panneaux photovoltaïques, nous atteindrons pratiquement l’autoconsommation. J’ai pensé un moment revendre l’éventuel surplus : mais plus la surface des panneaux est petite, plus bas est le prix de rachat du KWh. Par exemple pour 250 m² on vous le rachète à 6 centimes – alors que pour 1 000 m² il sera racheté 11 centimes. Enedis argumentant que les frais de gestion sont plus élevés pour les petites surfaces. En bref, il faut savoir que plus vous avez une surface de panneaux importante plus vous pouvez réduire vos coûts de production.
Nous avons électrifié notre parc de véhicule avec des véhicules hybrides et des véhicules électriques. Mais nous avons aussi travaillé sur la consommation d’énergie en interne : nous utilisons notamment un contrôle hygrométrique pour les espaces de stockage. L’idée est de maintenir le taux d’humidité autour de 35%. Nous nous sommes beaucoup penchés sur le problème de la qualité des équipements, car il y a différents produits avec des performances plus ou moins bonnes. Nous avons donc porté notre choix sur du matériel premium. Autre source d’économie : les écrans. Nous en avons 18 classés en catégorie F. Ce sont de très grands écrans de 49 pouces, qui permettent d’avoir plusieurs pages ouvertes simultanément. Désormais, ces écrans se mettent en veille au bout de quelques minutes. On pourrait avoir l’impression que c’est une économie marginale : mais en fait, ce sont plusieurs centaines d’euros qui sont épargnés annuellement.
Enfin, les salaires des collaborateurs aux plus faibles revenus ont été revalorisés afin, notamment, de réduire l’impact de la hausse du prix des carburants. Certaines personnes de mon entreprise ne peuvent pas covoiturer, et font plus de 500 km par semaine ! Une situation qui ne peut pas être éludée, mais impérativement prise en compte.
Aujourd’hui, bien sûr, nous n’avons pas eu le recul suffisant pour mesurer ces économies. Cependant, je suis persuadé qu’il faut revenir à des méthodes de travail plus sobres, à des modes plus rationnels. Même si ce n’est pas simple, c’est un effort nécessaire !
Rémy Lutz, manager France de Kurtz Ersa : LA FRANCE A BESOIN D’UNE CONTINUITÉ INDUSTRIELLE. Kurtz Ersa, la très ancienne entreprise allemande compte trois divisions : les équipements de production électronique, les imprimantes 3D et les solutions d’automatisation spécifiques.
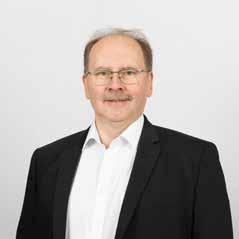
Pour Rémy Lutz, « les conséquences des prix de l’énergie sont ressenties chez Ersa selon nos domaines d’activité : nous sommes concepteurs et fabricants d’équipements de production. Chez Ersa nous sommes bien sur impactés par l’augmentation du prix de l’énergie en Allemagne où sont assemblées toutes nos machines. Nous sommes aussi impactés par l’augmentation du prix de l’énergie dans les pays , très majoritairement européens où sont implantés nos fournisseurs de systèmes électroniques, plasturgie, mécanique de précision, etc. Le bouclier tarifaire allemand sur le prix de l’énergie, qui devrait être mis en place dès le 1er janvier par le Gouvernement allemand devrait atténuer les effets négatifs de cette spirale inflationniste déjà alimentée depuis de longs mois par l’augmentation du prix de nombreuses matières, dont les composants électroniques. Nos clients, tant les sous traitants que les fabricants de produits propres, nous ont rapporté avoir vu les prix de l’énergie multipliés par 2 par 3, voire par 4. Cela épuise leur trésorerie. Dans le même temps, le prix d’achat des composants a lui aussi augmenté de façon drastique. Combinés ces éléments retardent les investissements et là nous sommes directement concernés. Et je pense que le prix de’énergie aura un impact encore plus fort dans les mois ou les années à venir sur la capacité d’investissement de nos clients.
Réduire la consommation énergétique en production
Depuis plusieurs années déjà, nous nous sommes attaqués au nerf de la guerre : la réduction de la consommation énergétique des machines. Nous avons déjà enregistré des résultats probants, mais cela sera-t-il suffisant ? Sans doute, mais à la marge. Si nous réduisons la consommation d’énergie de 10%, cela aidera, mais ne cela ne sera pas la panacée.
Il est clair qu’avec une carte électronique qui nécessite un passage au four, on ne peut pas changer le process, il faut bien apporter l’énergie nécessaire. Mais en revanche on peut tenter de faire en sorte qu’elle soit utilisée et réutilisée au mieux. Et il existe des possibilités. Chez Ersa nous avons conçu le four de refusion Hotflow three, présenté l’an dernier à Productronica, qui ne rejette pas de chaleur dans une pièce climatisée. C’est une performance de sobriété. Cependant, je crains que 2023 s’annonce comme une année compliquée : la crise va s’étendre à d’autres domaines, notamment lorsque le gouvernement réduira ses aides sous toutes ses formes. Je pense que certaines sociétés vont avoir beaucoup de
mal. Et n’oublions pas que les nouvelles centrales nucléaires ne seront en capacité de produire que d’ici plusieurs années ! En outre, au regard du projet du tout électrique en 2035, la question est de savoir comment nous produirons l’électricité nécessaire … Personne n’en parle car aujourd’hui il n’y pas de réponse. Déjà cet hiver on nous annonce des délestages. Mais qu’en sera-t-il des voitures électriques dans 10 ans alors que les centrales ne se seront pas en mesure de leur fournir l’énergie nécessaire ?
Personne ne parle non plus du recyclage des batteries. Il n’ existe pas car là encore, rien n’a été réellement envisagé ni prévu. Nous avons besoin d’une continuité industrielle en France, comme l’Allemagne a su le faire. En France, on assiste à des saupoudrages d’argent ici et là, mais pas à une politique structurée qui doit commencer par la mise en place de cursus de formation, notamment en électronique. Il faut assurer aujourd’hui la formation de gens compétents pour prendre la relève de ceux qui partiront à la retraite. En France il y a toutes les conditions pour réussir ce challenge et il faut s’y consacrer. Il faut encourager les élèves à s’investir dans les filières industrielles. Parce qu’il y a un monde entre les études, et la vraie vie.»
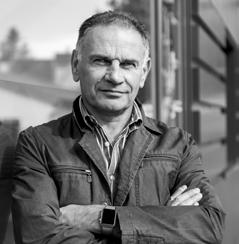
Serge Calmard, patron de SUDELEC : LES RAISONS DE LA COLERE. Sudelec est expert dans la fabrication de cartes et systèmes électroniques depuis sa création en 1982 à Usson-en-Forez (Loire) par Serge Calmard
« Je ne vois pas trop ce qu’on peut faire dans cette situation. Le prix de l’énergie est ce qu’il est, nous n’avons aucune emprise à ce niveau. Que puis-je faire face aux prix multipliés par trois ? Au niveau des solutions d’économie, nous avons toujours été économes. J’étudie la solution des panneaux solaires, même si je ne suis pas convaincu de leur intérêt écologique ... Répercuter ces augmentations sur les prix n’est pas facile – les clients ne sont naturellement pas enthousiastes ! Ceci étant, le coût l’énergie est un élément parmi d’autres augmentations : les salaires, les assurances, l’inflation … Et augmenter le prix de nos produits ne compensent pas ces hausses, et nos marges en souffrent.
Des préconisations irréalistes
Bien sûr, je mets un four en route quand j’en ai besoin ! J’ai entendu ce matin parler d’usines qui travaillent la nuit pour faire des économies. Je ne me vois pas annoncer ce genre de décision à mon personnel ! Je subis ! Il ne me semble pas avoir d’action à mettre en œuvre pour limiter les dépenses énergétiques. La température à 17° dans les locaux est irréaliste. Demander à quelqu’un qui est assis sur une chaise dans une pièce froide, de faire des gestes précis est impossible. Comme d’habitude les suggestions du gouvernement sont aberrantes. Pourquoi le prix de l’électricité est-il aligné sur celui du gaz ? Nous payons les conséquences de décisions irresponsables de nos hommes politiques, tant dans la crise actuelle, comme il y a quelques années la décision de stopper le nucléaire. Ces gens là aujourd’hui, quelles responsabilités portent- ils ? Aucune ! Leur seule vision est la réélection ! Nous sommes obligés de supporter tout cela. Comment voulez vous qu’une petite boite comme la mienne avec 30 personnes, ait la moindre influence sur son fournisseur d’électricité ? Nous n’avons aucun pouvoir. Les aides gouvernementales, ce n’est pas ce dont nous avons besoin. Qu’ils arrêtent de nous donner de l’argent ! Nous ne sommes pas là pour faire la mendicité ! Nous avons connu en France des gens capables de prendre des grandes décisions, de faire du nucléaire, de lancer le TGV, le Concorde et Airbus. Des décideurs qui avaient une vision – Actuellement nous avons affaire à des gens qui vivent dans l’inertie, qui ont fait le choix de faire l’impasse sur l’entretien du réseau ferré et des centrales nucléaires ! Nous sommes dans le mur.
La France mérite mieux. Nous avons des gens intelligents, des gens compétents qui veulent s’impliquer, qui ont envie de faire des choses. Mais on prend ces gens pour des idiots, alors qu’ils sont tout sauf cela. Ce sont des bosseurs, des gens méritants. En réalité, le gouvernement distribue de l’argent pour cacher ses manquements, erreurs de jugement et mauvais choix politiques au nom du maintien de la paix sociale.»
Caroline GUERIN, Responsable de projets chez OSE : PARTAGER L’EFFORT COLLECTIF.

Située à Corps dans le sud de l’Isère, le fabricant de cartes électroniques OSE a revu son organisation industrielle pour répondre plus rapidement aux demandes clients. Une extension flambant neuve abrite désormais un atelier intégration.
« Lors de notre grand projet de modernisation en 2020, nous avons porté nos efforts sur la sobriété énergétique, notamment pour notre installation chauffage et climatisation. Aujourd’hui nous avons terminé la rénovation des anciens bâtiments ou subsistaient encore des radiateurs « grille-pain », remplacés par un système de pompe à chaleur qui nous permet de stabiliser et contrôler nos consommations. Nous sommes équipés d’un système de pilotage du système de chauffage et de climatisation pour réguler et optimiser la température selon les zones d’activité.
La hausse du prix de l’énergie va nous toucher, mais de façon atténuée : nous avons des accords de prestations avec notre fournisseur GEG (Gaz Electricité de Grenoble). Ce contrat court jusqu’à fin 2023. Nous serons, malgré les hausses, plutôt mieux lotis que certains de nos confrères. A ce jour, nous ne pensons pas avoir recours aux panneaux photovoltaïques, qui sont très onéreux et pour lesquels il n’existe aucune aide. Nous abordons aujourd’hui plus sereinement ces hausses que l’augmentation du prix du gasoil, ce qui pourrait nous conduire à ajuster nos prix..
Entreprises peu gourmandes en énergie-
Nous appliquons le plan sobriété, parce que nous avons à cœur de participer à l’effort collectif. Nous partons du principe que si l’on joue le jeu, on peur faire bouger quelques petites choses. Il faut tout de même souligner qu’en tant qu’entreprise, nous sommes peu gourmands en énergie, si l’on se compare au transport aérien, ou maritime ou bien d’autres activités. Avec le renouvellement de nos investissements chauffage, les bureaux sont désormais chauffés à 19°, les salles de réunions à 17° quand elles ne sont pas occupées. Par contre dans les ateliers, là où les personnes sont sur des postes statiques, le chauffage est à 20°/22°: cela dépend des ateliers et des personnes. Nous faisons attention - mais nous avons toujours été, par nature, économes. Nous ne savons pas ce qui va se passer demain, nous avons investis dans le renouvellement de nos installations au bon moment. Si l’on ne l’avait pas fait, je suis sûre que je tiendrais aujourd’hui un autre discours. »
Fabrice Castes (SYSELEC) : LE CHOIX RAISONNÉ DES PANNEAUX SOLAIRES. Fabrice Caste est le patron de Syselec, entreprise située à Castres (Tarn), spécialisée dans l’électronique et le câblage d’armoires et des solutions d’électricité industrielle. Le groupe SYSELEC emploie 50 personnes et réalise un chiffre d’affaires de 14 millions d’euros. En 2020, la construction d’un nouveau bâtiment équipé de panneaux solaires devrait lui permettre de diviser sa facture d’énergie par deux.
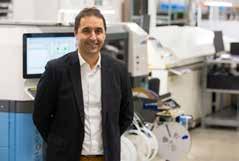
« Nous sommes passés de 52 euros le MW à 480 € : cela nous fait un surcoût de près de 100 000 euros pendant 3 ans. Je me suis engagé sur 3 ans et pour ce faire, j’ai déjà 100 KW - crête* de production sur le toit de l’usine. Je vais rajouter 200 KW de plus donc j’aurais 300 KW - crête en production. A cela, je vais encore additionner 400 kilowatts heure de stockage avec des batteries lithium-ion. L’idée, en fait, c’est de pouvoir produire suffisamment d’électricité. Donc, la centrale voltaïque est surdimensionnée dans le sens où elle va, dans la journée produire pour les besoins de fonctionnement de l’usine et que le surplus sera stocké. Nous avons dimensionné la puissance des batteries en conséquence. Cette électricité sera consommée la nuit ou les jours de mauvais temps où les panneaux ne produisent pas beaucoup d’électricité. Le but est de limiter le tirage sur les réseaux. Aujourd’hui nous consommons 250 MW à l’année et nous allons produire 150 MW. Au final, nous consommerons sur notre réseau 100 MW et ainsi diviser notre consommation par deux. Cela se résume à un mix énergétique de 40 % sur le soutirage du réseau et 60 % de notre consommation. C’est un investissement de 400 000 € - et sans aides actuellement. Cet investissement se fait au détriment de l’investissement que j’avais prévu de faire sur des machines pour favoriser la croissance de mon entreprise. Malgré tout, ces équipements vont nous permettre l’autonomie énergétique d’avril à septembre. Au total, pendant 6 mois de l’année nous serons autonomes, et les mois d’hiver nous produirons un petit peu et nous serons obligés de recourir au réseau.
Panneaux solaires vs groupe électrogène Maintenant je vais prier pour la sécheresse ! Les panneaux photovoltaïques ne produisent pas davantage l’été car quand il fait très chaud, ils baissent de puissance. L’idéal c’est le printemps, quand il fait frais et ensoleillé car les panneaux ont une production optimale. L’été par contre, la durée d’ensoleillement est plus longue, ce qui d’une certaine manière, compense.
Il faut savoir qu’au delà de 300 euros le MW, il est rentable de faire du courant avec des groupes électrogènes et un moteur diesel. Mais SYSELEC ne consommera jamais 400 000 € de gas-oil en un an !
Je fais plutôt le choix du long terme. Parce qu’avec le prix du MW aujourd’hui, j’amortis mon installation en 6 ans, et dans 6 ans j’aurai 6 mois de l’année où le courant sera gratuit pour moi. Pout arriver à ce constat, j’ai fait le calcul suivant. Soit la réflexion est purement financière et on fait tourner le groupe diesel ; Soit on est moins financier, et plus rationnel et on fait le choix du photovoltaïque. Mais beaucoup d’entreprises choisissent pourtant le moteur diesel car leurs installations ne sont pas adaptées aux panneaux photovoltaïques - le poids qu’on rajoute sur le toit est évalué à une dizaine de tonnes.
Lexique : *Le kilowatt - crête (ou kWc) est une unité de mesure utilisée pour évaluer la puissance atteinte par un panneau solaire lorsqu’il est exposé à un rayonnement solaire maximal. * Arenh : Accès Régulé à l’Électricité Nucléaire Historique *CRE : Commission de Régulation de l’Énergie
Bac pro, BTS, BUT, licence, mastère... : où sont les étudiants en électronique ?
Par Jeanne BIGOT, reporter
La rédaction des Cahiers de l’Industrie Électronique et Numérique s’est attaquée, en cette rentrée scolaire 2022, à la question des formations aux métiers de l’électronique. Un sujet complexe et qui devrait bouger courant 2023, décliné en plusieurs épisodes au fil de la parution du magazine et de l’actualité. Ce premier volet s’intéresse aux formations post bac, et à l’intérêt encore modeste que leur porte la jeunesse aujourd’hui.
50 millions d’euros. Voici l’investissement annoncé par le gouvernement en faveur de la formation, dans le cadre du plan de soutien France 2030. « Un des enjeux majeurs est celui de soutenir l’émergence de talents et d’accélérer l’adaptation des formations aux besoins de compétences des nouvelles filières et des métiers d’avenir » indique en ligne l’agence nationale de la recherche. Mais aujourd’hui, l’électronique semble être le parent pauvre du ministère de l’Enseignement supérieur de la Recherche de l’Innovation, et risque de ne bénéficier que de très peu de ces 50 millions. Pourtant, la filière alarme sur ses difficultés de recrutement : « Nous pourrions augmenter nos équipes de 15%, mais c’est très difficile de recruter. Nous recherchons tout type de niveau, de cursus et pour tous les postes du pilote de ligne CMS au câbleur électronique, en passant par le magasinier, le service qualité, SAV et achat… » confiait Emmanuel Delaunay, directeur général d’ADEX Electronics il y a quelques mois. Pour comprendre cette crise du recrutement, il faut remonter à la rentrée 2016, où le baccalauréat professionnel Système Électronique et Numérique (SEN) a été remplacé par un baccalauréat Système Numérique (SN). Il propose 3 options : sûreté et sécurité des infrastructures de l’habitat et du tertiaire (SSIHT) ; audiovisuel, réseaux et équipements domestiques (ARED) ; réseaux informatiques et systèmes communicants (RISC). Pas ou peu d’électronique avant le bac donc, ce qui ne pousse pas les jeunes étudiants à s’y plonger par la suite.
Du bac+2 au mastère
Pourtant, passé le bac, les formations, bien que peu nombreuses, existent. Nous
Aujourd’hui, l’électronique semble être le parent pauvre du ministère de l’Enseignement supérieur de la Recherche de l’Innovation, et risque de ne bénéficier que de très peu de ces 50 millions.
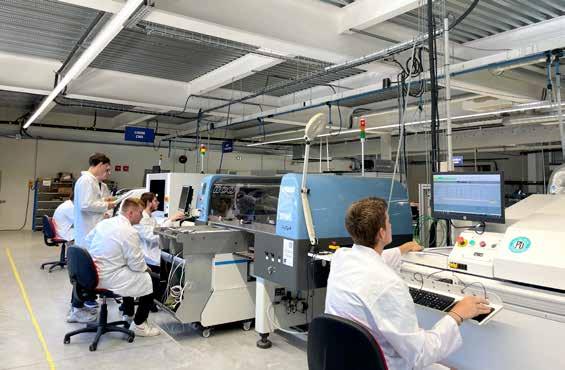
pouvons citer le BTS système numérique avec option électronique et télécommunication ou le bachelor universitaire et technologique (BUT) génie électrique et informatique industrielle (GEII). Et plus l’étudiant avance dans son parcours d’étude supérieur, plus il a la possibilité de se former précisément en l’électronique : plusieurs licences professionnelles existent, tel que la licence CPSE (Conception et production de systèmes électroniques) de l’Université de Toulouse ou la licence PASTEL (production assemblage des système électronique), dispensé par l’École Supérieure des Technologies Industrielles (ESTI), au sein du GIP CEI (Groupement d’Intérêt Public). Cette dernière a par ailleurs choisi de proposer à ses étudiants de pousser la formation encore plus loin, grâce à un mastère unique en France nommé MLAI option électronique, industrialisation et supply chain. « Nous avons ouvert ce mastère à la demande des entreprises », fait valoir Jamal Rammal, responsable du département électronique de l’ESTI. « C’est le parfait mélange entre la logistique et la technique : l’objectif est de faire le lien entre les bureaux d’études, chargés de la conception des cartes, et la production. Pour produire efficacement, tout en optimisant les frais, il est indispensable d’avoir des collaborateurs capables de communiquer avec les deux parties. » Cette poursuite d’études en deux ans, ouverte à la rentrée 2022, a déjà convaincu 19 étudiants qui seront sur le marché du travail d’ici septembre 2024. Face aux besoins de nouveaux collaborateurs des entreprises, l’ESTI propose également de former en électronique des demandeurs d’emploi, ou des personnes en reconversion, grâce à une formation en 2 ans, permettant de devenir électronicien de tests et développement. Au cours de celle-ci, la douzaine d’étudiants qui y prennent part chaque année développent des compétences dans le diagnostic, les tests, le dépannage mais aussi l’assemblage des cartes. La quasi-totalité des formations en électronique, jusqu’au mastère, s’effectue en apprentissage. Un point clef, sur lequel il ne faut pas transiger selon Christina Villeneuve, responsable de la licence professionnelle CPSE : « Nos jeunes passent 30 semaines dans leur entreprise, et 150 heures sur un projet de type industriel pendant la formation. Il s’agit de diplômer des personnes qui ont déjà une bonne expérience, et qui seront donc autonomes dans leur entreprise. »
Le software, encore et toujours privilégié
Bien qu’elles ne soient pas très nombreuses, les formations en électronique, post-bac, existent. De l’autre côté du spectre, les entreprises sont en demande de nouveaux collaborateurs, et recrutent dès la mise sur le marché du travail de l’un d’entre eux. « Les entreprises courent derrière nos étudiants » se targue Jamal Rammal. Pourtant, ces métiers, notamment en fabrication, n’attirent que peu et d’autant moins depuis la réforme du bac professionnel en 2016. « Nous on a la capacité d’accueillir plus d’étudiants, mais il faut voir si les jeunes sont intéressés. C’était une erreur d’enlever l’électronique du bac pro SEN, car maintenant les jeunes se positionnent bien plus sur l’informatique ou la robotique… » regrette Jamal Rammal. Le software attire ainsi plus, car moins associé à l’industrie mais aussi, car il paie souvent plus : un développeur peut toucher en moyenne 2400 euros brut en début de carrière selon l’ONISEP, contre 1950 euros pour un électronicien. Les entreprises sont les premières qui trinquent, forcée d’augmenter les salaires, ou de former ses nouveaux collaborateurs en interne afin d’équilibrer la balance pour le salarié. Autre point clef selon Christina Villeneuve-Fauve, les appétences des étudiants au sein même des formations en électronique ont changé au fil des années : « Avant, nos jeunes avaient des projets professionnels précis lorsqu’ils rentraient en formation, tandis qu’aujourd’hui ils sont plus opportunistes et n’hésitent pas à s’éloigner de la fabrication notamment. De plus, ils se tournent souvent vers des études complémentaires, pour être manager ou ingénieur. » Face à ce difficile regard sur l’industrie de l’électronique et notamment les métiers de la fabrication, la sensibilisation semble être la meilleure attaque : salons et journées portes ouvertes sont des moments clefs de l’année pour ces centres de formations, mais aussi pour les entreprises. Leur rôle dans la formation de leurs futurs salariés est indispensable : certaines s’impliquent ainsi en dispensant des cours, en privilégiant des recrutements en apprentissage, et d’autres n’hésitent pas à ouvrir leurs portes à des collégiens ou lycéens, afin de faire découvrir ses métiers, leurs richesses, et ainsi peut-être d’inspirer des carrières.
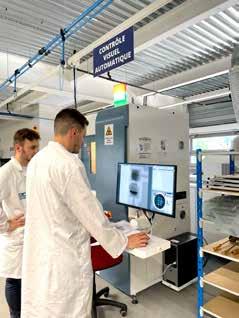
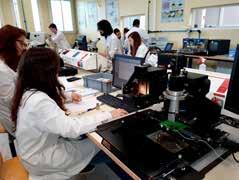
Plateforme de la licence pro CPSE Des formations qui nécessitent de lourds investissements
En plus de la différence d’intérêt porté aux métiers du hardware par rapport au software, les coûts de ces formations ne sont pas les mêmes. Ligne CMS, bancs, logiciels… Les écoles doivent investir et s’équiper pour leurs étudiants. L’ESTI a ainsi investi un total de 5 millions d’euros dans une plateforme technologique de 1000 m2. Christina VilleneuveFauve, responsable de la licence professionnelle CPSE de l’Université de Toulouse, salue, elle, le soutien indispensable de la plateforme Micropacc : « Si l’on n’avait pas cette plateforme, on ne serait peut-être pas là. On y partage du matériel, que l’on peut utiliser pour les TP, et les projets. Elle nous apporte également un lien privilégié avec les entreprises. »
ESTI / GIP CEI LICENCE PASTEL Jamal RAMMAL +33(0)2 99 71 80 60 20 contact@gip-cei.com www.gip-cei.com
LICENCE PRO CPSE Christina VILLENEUVE +33(0)5 61 55 84 10 christina.villeneuve@laplace.univ-tlse.fr www.lipro-cpse.fr
PFT MICROPACC Marc ALARY +33(0)5 63 92 63 43 micropacc@ac-toulouse.fr www.micropacc.fr
Vendre des TPE-PME comme sur Leboncoin
On trouve de tout sur Leboncoin ! Sauf des entreprises. Pourtant, ce marché n’est pas négligeable puisqu’il y a entre 50.000 et 60.000 transmissions d’entreprises chaque année en France. Selon une étude récente d’In Extenso et Epsilon Research, le marché le plus actif est celui des plus petites PME et TPE dont la valorisation est inférieure à 5 millions d’euros. Pour acheter ou vendre ces entreprises, il faut se rendre sur des sites spécialisés comme Cession PME ou Fusacq, ou sur le site d’annonces de Bpifrance ou encore sur les réseaux des Chambres de Commerce et d’Industrie.
Quand vous avez un petit business, c’est très compliqué de le vendre. Vous ne pouvez pas aller voir une banque d’affaires car ce n’est pas économiquement viable », précise un banquier d’affaires spécialisé.
Mais depuis peu, il est possible de se rendre sur Alvo. Cette start-up lancée avant l’été a bouclé une levée de fonds d’un million d’euros uniquement auprès de business angels, dont les fondateurs de Qonto et Olivier Brourhant créateur de Mantu, le mercenaire du conseil. « Le marché de la fusion-acquisition sur les TPE/ PME est complètement cassé et opaque », estime Matthieu Stefani, cofondateur de la jeune pousse issue de la start-up studio de son agence CosaVostra. Cette nouvelle place de marché, qu’il a créée avec Germain Michou-Tonning (ex-directeur des partenariats de Qonto) et Thomas Colin (conseil en direction financière), recense des TPE-PME valorisées moins de 5 millions d’euros. Alvo ne prend en revanche pas les mandats en dessous de 500.000 euros car son modèle ne serait pas rentable. Certains documents sont générés automatiquement (info mémo, accord de non-divulgation…) et la « due diligence », c’est-à-dire l’ensemble des vérifications qu’un éventuel acquéreur va réaliser avant une transaction, est plus rapide. Mais tous les processus en amont d’une fusion-acquisition n’ont pas été automatisés. « On ne vend pas une voiture !», avoue le dirigeant. Même si les annonces de sociétés à moins de 500.000 euros ne seront pas opérées par Alvo, elles sont tout de même visibles pour permettre aux
Un nombre croissant d’entreprises aéronautiques abandonnent la pratique coûteuse et rigide de l’acquisition de nouveaux équipements de test au profit d’une méthodologie plus polyvalente et économiquement viable basée sur la location ou l’acquisition d’équipements d’occasion de haute qualité.
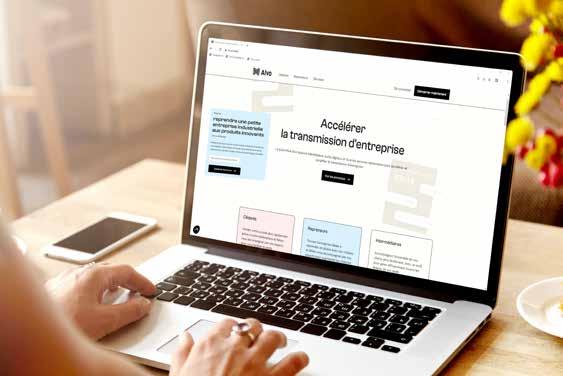
acquéreurs et parties prenantes (avocats, experts-comptables, notaires…) d’utiliser les outils d’automatisation d’Alvo. La start-up facture alors un abonnement, tandis qu’elle prend un pourcentage quand elle a un mandat.
« Ce système de place de marché impose de faire grossir parallèlement l’offre et la demande. C’est cher et dur mais une fois passé un certain cap, c’est gagnant », souligne Arthur Porré. Pour attirer les deux parties, Alvo cible principalement les experts-comptables et compte s’appuyer sur les réseaux respectifs des fondateurs. A ce jour, elle recense une vingtaine d’annonces, revendique 1 000 inscrits sur sa plateforme et a signé dix mandats.
ALVO hello@alvo.market www.alvo.market
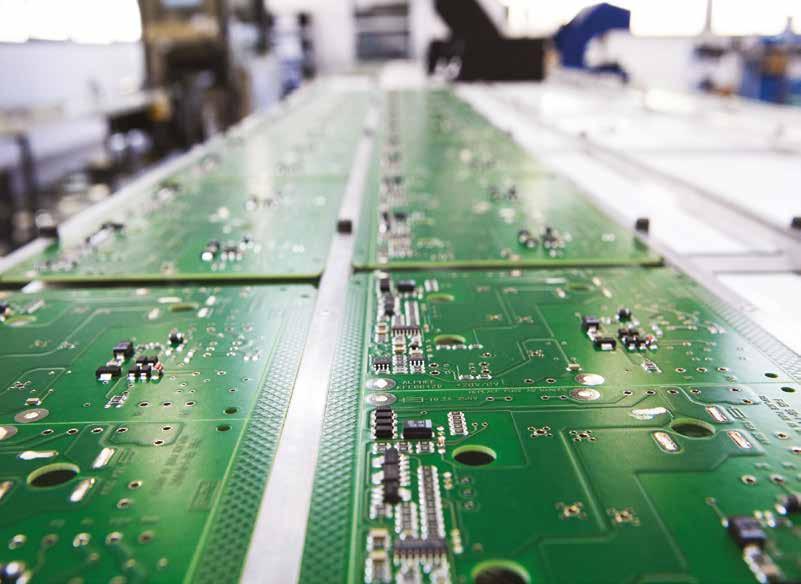
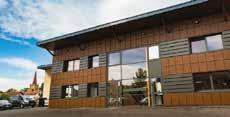
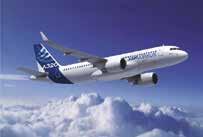
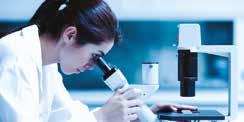
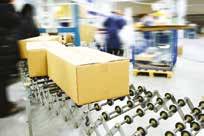
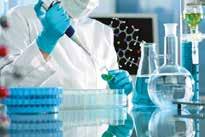

GI Lyon 2023 : L’industrie se mobilise du 7 au 10 mars 2023, à Eurexpo Lyon
Plus grande vitrine française de l’innovation industrielle, Global Industrie réunira cette fois encore l’ensemble des secteurs de l’industrie. Directement impactées par la conjecture internationale actuelle, les entreprises et chaînes de production françaises y trouveront des solutions et savoir-faire qui les aideront à relever les défis des multiples transitions en cours, qu’elles soient écologiques, énergétiques, sociétales, liées aux métiers ou aux relocalisations.
Les solutions pour accompagner ses transitions
Global Industrie 2023 sera le grand rendez-vous des solutions concrètes qui répondent aux enjeux actuels auxquels sont confrontés les industriels.
Ainsi, l’offre des 2 500 exposants (offreurs de solutions, prestataires de services, soustraitants, fabricants et distributeurs…), répartis dans 15 univers (voir encadré), et les innovations récompensées par les GI Awards, seront autant de leviers techniques leur permettant d’améliorer leur productivité et de répondre à leurs problématiques énergétiques et environnementales.
15 univers
• Assemblage, montage, fixations industrielles • Électronique • Énergies & production durable • Fabrication additive & 3D • Finition & traitements des matériaux • Forge & fonderie • Matières & produits semi-finis • Mesure, contrôle, vision, instrumentation • Plasturgie, caoutchouc, composites • Régions & pays • Robotique • Services & aménagement de l’entreprise • Smart : digitalisation, automatisation, mécatronique • Tôlerie, mise en forme des métaux, soudage • Usinage & enlèvement de matière
Valoriser les savoir-faire et les métiers de l’industrie
L’industrie française est en effet un vivier d’emplois dont beaucoup demeurent non pourvus. Depuis sa création, Global Industrie accompagne les entreprises en recherche de nouveaux talents en mettant en place plusieurs outils complémentaires.
Dédié aux formations, à l’emploi et aux métiers, l’espace GI Avenir est un incontournable de Global Industrie. Jeunes scolarisés, demandeurs d’emploi et personnes en reconversion professionnelle s’y informeront sur les différents métiers de l’industrie, les secteurs qui recrutent et les métiers d’avenir.
Global Industrie souhaite permettre aux industriels de tirer parti des grands enjeux du moment, en leur apportant des pistes technologiques et de réflexion, et que l’industrie française en ressorte grandie.
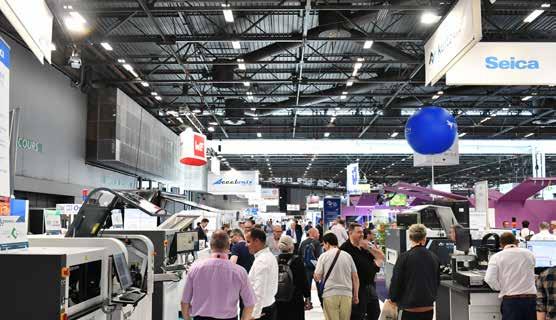
Sébastien Gillet, Directeur de Global Industrie
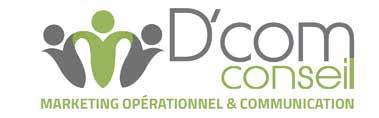
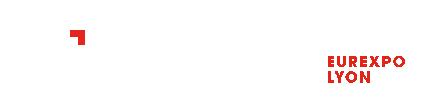
UNIVERS ÉLECTRONIQUE ENTRÉE HALL 6 Ils seront présents, pourquoi pas vous ?
A2E ACCELONIX ACEA ADEX ELECTRONIQUE ALCYON ELECTRONIQUE ALLIANSYS ALTRICS CATS POWER DESIGN CANON BRETAGNE CEISTA INTERNATIONAL CEPELEC CIRLY CORDON CMS CREATIVE EURECOM DAVUM TMC ELENTICA EOLANE ESTELEC EUROCOMPOSANT EUROPLACER INDUSTRIES EXCALIBUR ERP PAR OC2I FIRST INDUSTRIES G4 SOURCING GERAL GROUPE ZEKAT IFTEC IPC CONCOURS DE BRASAGE JFIE KURTZ ERSA FRANCE LAUDREN Les Cahiers de L’Industrie Electronique et Numérique METRONELEC MYCRONIC ODU FRANCE OEM INDUSTRY OSE PHOENIX CONTACT PIGE ELECTRONIQUE PIM INDUSTRIE POLYGONE CAO PROTO-ELECTRONICS SAFE PCB SECTRONIC SEICA FRANCE SEICO SN SERITECH SOUDOTIQUE SUDELEC SYNOV TEST-OK VILLELEC WURTH ELEKTRONIK
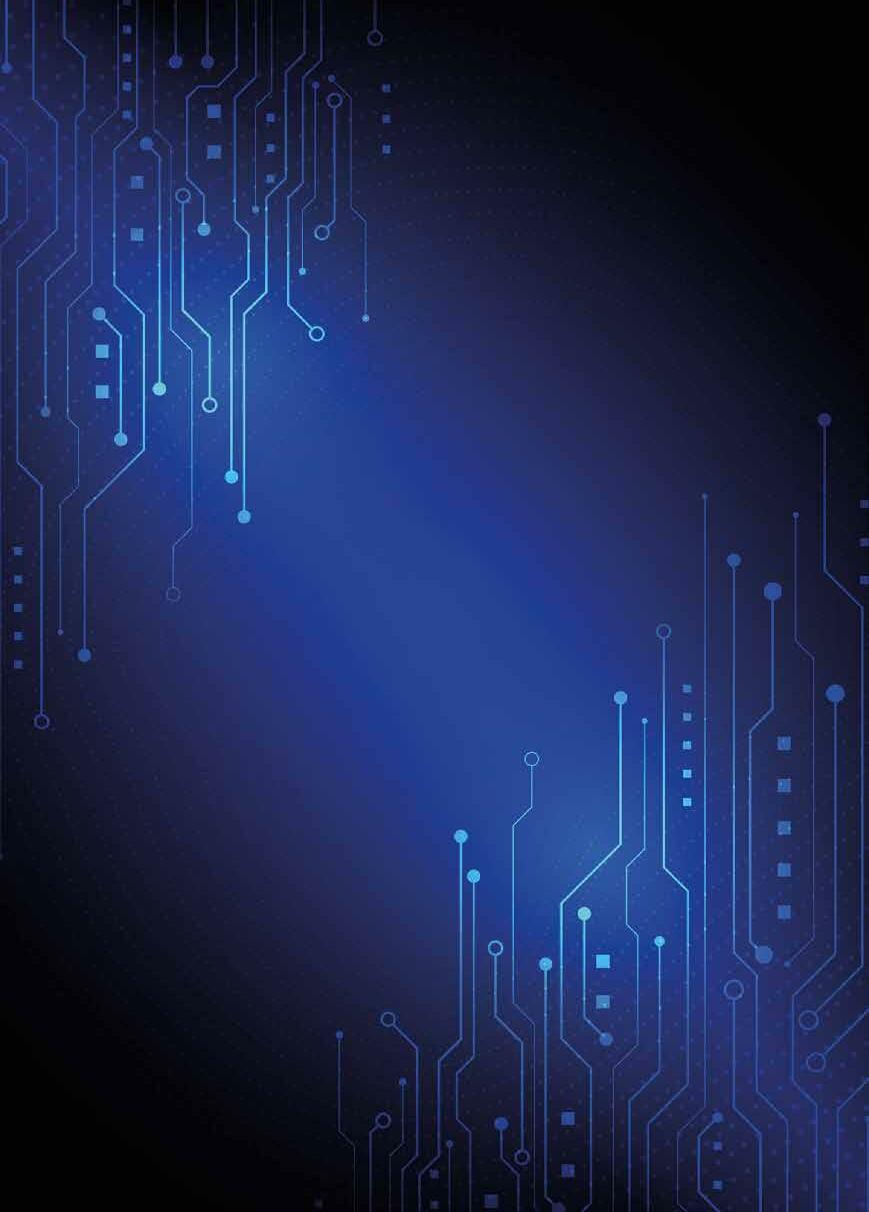
Vous souhaitez exposer ? contactez Franck Rannou 02 98 50 18 53 frannou@dcomconseil.com
Design D’Com Conseil - Crédit photo : iStock Foryou13
Les Cahiers de l’Industrie Électronique et Numérique -décembre 2022 Liste non exhaustive au 5 décembre 2022 des exposants inscrits auprès de D’Com Conseil - n° 114 - 25
Pour présenter leurs offres d’emploi, les services RH des entreprises disposeront notamment d’une plateforme de recrutement en ligne, de sessions de job datings…
Les Golden Tech, 2e édition du concours d’excellence industrielle
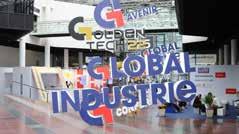
La valorisation des métiers sera aussi au coeur du concours industriel les Golden Tech. Durant 4 jours, ce show en continu célèbre les hommes et les femmes qui incarnent l’industrie d’aujourd’hui dans différents métiers (voir encadré). Ce sera pour eux l’occasion de démontrer leur savoir-faire, se challenger et porter haut les couleurs de leur entreprise.
Tous les professionnels peuvent s’inscrire en ligne et participer à la sélection. Les partenaires s’appuieront sur les connaissances et les motivations de chacun, afin de réunir 11 candidats maximum par métier. Pour 2023, les Golden Tech ont choisi le thème de « la voiture à hydrogène ». Les sujets élaborés en collaboration avec des partenaires métiers, et dévoilés 1 heure avant l’épreuve, porteront sur la conception, le stockage ou la distribution de ces véhicules. Les candidats auront ensuite 2 heures pour y répondre au mieux avant d’être évalués par un jury d’experts. Les résultats (médaille d’or, d’argent et de bronze) seront dévoilés le vendredi 10 mars 2023. Le vainqueur dans chaque catégorie recevra un chèque de 1 000 euros. En lien avec la thématique automobile de la compétition, l’espace des Golden Tech présentera quelques concept-cars d’exception, comme le prototype H2 des 24 heures du Mans.
Les compétitions des Golden Tech
• Concepteur / Designer • Maker • Fraiseur / Tourneur • Rouleur • Soudeur • Métrologue • Roboticien • Automaticien • Responsable Motion Control • Concepteur de Réseaux d’automatismes • Data Manager Automation • Programmeur d’automatismes • Responsable Amélioration Continue • Responsable Supply Chain Informations et inscriptions : www.goldentech.fr
Veille et prospectives
Global Industrie est aussi le lieu où convergent les nouvelles idées et prospectives qui visent à répondre aux différents enjeux de l’industrie. En 2023, les conférences aborderont les questions liées aux transitions, sous la forme d’éclairages sur des solutions existantes et des retours d’expériences.
En complément, Global Industrie réalisera de nombreuses interviews sur le Plateau TV du salon diffusées sur les chaînes digitales GI Channel. Sur les stands des représentants économiques ou institutionnels, les entreprises s’informeront sur les dispositifs de financement ou d’aide mis en place par l’État ou les collectivités dans le cadre de relocalisation, création d’emploi, transition environnementale…
L’univers électronique
Installé à l’entrée du hall 6, l’univers Electronique présentera tous les secteurs de cette industrie : la conception, l’industrialisation, la fabrication, l’intégration et la maintenance des cartes et systèmes électroniques, les fournisseurs d’équipements de production et de test, les fournisseurs de consommables et la formation. Seront également accueillis les fournisseurs de tous types de composants ainsi que les services associés à l’industrie électronique. La page précédente vous présente les sociétés inscrites auprès de D’ComConseil, sur le Village des Industries Electroniques. (liste non exhaustive au 1er décembre 2022)
Global industrie en chiffres :
Le monde de l’industrie, dans tous les sens du terme, ne s’y est d’ailleurs pas trompé. Global Industrie, c’est ainsi : 85 pays représentés par ses visiteurs 40% d’exposants étrangers venus de 40 pays 2500 exposants couvrant l’ensemble de l’écosystème industriel 100 000 m² d’exposition 45 860 visiteurs (en 2019) Seulement 7% de visiteurs communs entre les éditions parisiennes et lyonnaises. Placé sous le haut patronage du président de la République depuis sa création en 2018, Global Industrie rassemble chaque année plus de 2 000 entreprises françaises et internationales et présente les dernières innovations qui feront l’industrie du futur.
En décidant de se doter d’une fonction de président et en proposant à Nicolas Dufourcq d’en être le premier titulaire, Sébastien Gillet, directeur de Global Industrie, a souhaité consolider la stratégie institutionnelle du salon, par une incarnation forte, à la hauteur des enjeux de l’industrie d’aujourd’hui.
Cette nomination témoigne également de la forte présence de Bpifrance aux côtés des entreprises industrielles, appelées à jouer un rôle moteur dans l’économie française de demain. Alors que les industriels sont plus que jamais mobilisés pour relever le défi des transitions environnementale, sociale et technologique, c’est un signal fort qui leur est adressé, en renfort des dispositifs d’accompagnement et d’aide déjà déployés par l’État et les Régions.
« Je suis particulièrement heureux de prendre la présidence de Global Industrie, explique Nicolas Dufourcq. C’est une concrétisation forte de l’engagement historique de Bpifrance aux côtés des entreprises de la French Fab qui oeuvrent à la renaissance de l’industrie française. Innovation, décarbonation, création d’emploi, développement des territoires… : tous les leviers de la relance sont représentés sur Global Industrie. »
« Nous sommes fiers que Nicolas Dufourcq ait accepté de devenir le premier président de Global Industrie. C’est une excellente nouvelle pour le secteur industriel, analyse Sébastien Gillet, directeur de Global Industrie. Il est un signe de la très forte synergie qui se met en place, entre les entreprises et les acteurs publics, pour accompagner le développement et le rayonnement de l’industrie française de demain – et dont Global Industrie est fier d’être une fois de plus à l’initiative. »
Nicolas Dufourcq, (Bpifrance) nommé président de Global Industrie
Nicolas Dufourcq, directeur général de Bpifrance prend la présidence de Global Industrie.
Piratage informatique : ses différentes formes
Le terme de piratage informatique et ses variantes sont souvent surutilisés à la place d’autres formes de cyberattaques. En pratique, le piratage signifie le fait de s’introduire dans une ressource à l’insu de son propriétaire. Il existe donc deux principaux types de piratage : - le piratage d’appareils, - le piratage de comptes en ligne.
Le piratage consiste à pénétrer sans autorisation dans des technologies telles que des ordinateurs, des serveurs, des réseaux, des services en ligne ou des téléphones portables. Dans les deux cas, le but du pirate est de prendre le contrôle de la ressource concernée et de dérober des informations (personnelles, confidentielles, etc.) dans le but de les utiliser à des fins malveillantes comme une usurpation d’identité, une fraude bancaire, un gain d’argent, des activités d’espionnage, de sabotage, réclamations, extorsion, vandalisme, etc.
Le piratage informatique a un grand nombre de sens très différents dans le langage courant, parfois utilisés de manière abusive, que ce soit par commodité, par raccourcis, ou encore par méconnaissance. Souvent, nous qualifions de «piratage informatique» des cybermalveillances qui ne le sont pas. Pour pouvoir parler de piratage informatique, il faut qu’il y ait intrusion. Le piratage de compte en ligne désigne la prise de contrôle par un individu malveillant d’un compte au détriment de son propriétaire légitime.
Le terme « hack » ou « hacking » est souvent utilisé pour désigner un piratage informatique ou une cyberattaque. De même,
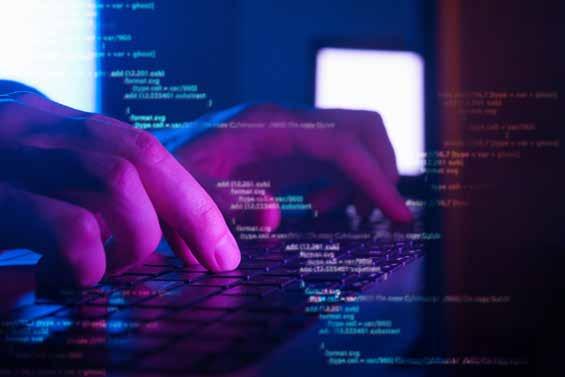
iStock : Sergey Shulgin Les professionnels possèdent davantage d’équipements susceptibles d’être piratés. Ils représentent une cible plus intéressante voire plus lucrative pour les pirates informatiques, car ils disposent souvent de moyens financiers plus importants, et peuvent avoir des activités particulièrement critiques et/ou des données personnelles ou professionnelles confidentielles. Le piratage informatique d’un système informatique professionnel peut ainsi avoir de lourdes conséquences pour l’organisation qui en est victime puisqu’elle peut entraîner le vol, voire la perte totale, des données du système touché.
lorsqu’il s’agit d’évoquer les individus à l’origine de ce piratage, sont utilisés les termes « hacker » ou « hackeur », c’està-dire un « pirate informatique », un attaquant, un cyberattaquant ou un cybercriminel en français.
Les causes et origines du piratage informatique
Il existe diverses causes ou origines au piratage informatique ce qui entraine un amalgame récurrent entre l’intrusion et le vecteur qui a permis l’intrusion dans une ressource. Par exemple, recevoir un message d’hameçonnage ou de phishing n’est pas une intrusion en soi, mais peut être un vecteur d’intrusion. C’est-à-dire que l’hameçonnage peut entrainer un piratage informatique. En effet, lorsqu’une victime reçoit une tentative de phishing par e-mail, il n’y a pas d’intrusion ni sur son compte en ligne, ni sur son équipement. Par contre, une tentative de phishing peut générer une intrusion et donc entrainer un piratage informatique si la victime, en cliquant sur la pièce-jointe d’un mail de phishing, installe à son insu un logiciel malveillant (virus) sur son ordinateur. Dans ce cas-là, on observe bien une intrusion sur l’équipement de la victime véhiculée par le mail de phishing. A contrario, si la victime ne clique pas sur la pièce-jointe, aucune action ne sera engendrée. Autre exemple, une attaque par rançongiciel ou ransomware peut également survenir suite à un piratage informatique. Un rançongiciel n’est pas toujours qu’un simple virus mais peut aussi être une technique d’attaque qui peut revêtir des formes différentes. Il peut ainsi s’agir d’un piratage informatique, au sens d’une intrusion dans le réseau informatique ou l’équipement d’une victime, pour pouvoir le chiffrer et ainsi poursuivre différents objectifs (vol de données, etc.). En revanche, réaliser une attaque en déni de service (ou DDoS) dans le but de saturer le serveur d’une organisation ne peut être réellement considérée comme un piratage informatique, même si c’est souvent appelé comme tel. En effet, il ne s’agit pas à proprement parler d’une intrusion dans un serveur, mais de l’envoi de multiples requêtes jusqu’à le saturer pour qu’il ne puisse plus répondre.
Les équipements visés
Il peut s’agir d’un ordinateur, d’un appareil mobile (tablette, smartphone…), d’un objet connecté, etc. Toutefois, il peut y avoir dans la sphère professionnelle d’autres types d’équipements plus spécialisés comme des serveurs, des routeurs, des réseaux, etc. Les professionnels possèdent davantage d’équipements susceptibles d’être piratés. Ils représentent une cible plus intéressante voire plus lucrative pour les pirates informatiques, car ils disposent souvent de moyens financiers plus importants, et peuvent avoir des activités particulièrement critiques et/ou des données personnelles ou professionnelles confidentielles. Le piratage informatique d’un système informatique professionnel peut ainsi avoir de lourdes conséquences pour l’organisation qui en est victime puisqu’elle peut entraîner le vol, voire la perte totale, des données du système touché.
Quels sont les moyens d’intrusion ?
Il existe différentes manières de pirater un système informatique : • après avoir exploité ou utilisé une faille de sécurité ; • Suite à une mauvaise configuration d’un logiciel ou d’un équipement ; • Après avoir été infecté par un malware (virus informatique) ; • Recevoir des appels téléphoniques ou des e-mails frauduleux visant à récupérer vos identifiants de connexion à votre compte à votre insu ; • Utiliser des mots de passe trop faciles à deviner, des mots de passe par défaut qui n’ont pas été modifiés, etc. Le pirate peut alors chercher à se propager à d’autres appareils du réseau attaqué. La source de l’intrusion peut être externe (cybercriminels) ou interne (négligence des propriétaires d’appareils, des proches, des employés ou des prestataires de services ; insatisfaction intentionnelle des employés ou des prestataires de services...).
Un site internet pour vous informer et une aide de l’Etat
En moyenne, une PME sur deux fait faillite dans les dix-huit mois après une attaque. Dans les grandes entreprises, il y a en moyenne un spécialiste cybersécurité pour 1 400 personnes. Ce que n’ont pas les PME. D’autant plus qu’il y a un déficit crucial d’experts en matière. Il y a donc urgence a bien s’informer et à agir.
Cybermalveillance.gouv.fr est le dispositif national d’assistance aux victimes d’actes de cybermalveillance, de sensibilisation des publics aux risques numériques et d’observation de la menace en France. Il est piloté par plusieurs ministères et l’agence nationale de la sécurité des systèmes d’information (ANSSI)
Sur ce site vous trouverez une multitude d’informations pratiques, et vous pouvez (devez !) vous abonner à une excellente lettre d’information. Elle est gratuite et riche d’informations d’actualité.
Le 16 novembre dernier, à Rennes, Jean-Noël Barrot, Ministre délégué chargé de la Transition numérique et des Télécommunications a présenté un plan de 30 millions d’euros, déployé en 2023 pour tous les Français (particuliers, collectivités et entreprises). Ainsi, 750 PME-ETI de certains secteurs couverts par la directive NIS2, seront accompagnées par l’Etat pour sécuriser leurs systèmes d’information.
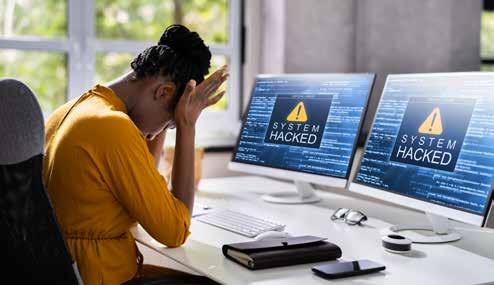
Crédit photo : MINEFI
Des entreprises, des femmes et des hommes
L’accroissement de la numérisation échanges, effet direct de la mise en œuvre des principes directeurs de l’Usine du Futur, ainsi que le confinement sanitaire et le télétravail peuvent laisser penser que les échanges interentreprises sont sur la voie de la déshumanisation. C’est oublier que le moteur principal de toute entreprise reste les femmes et les hommes qui ont concouru à sa création et qui œuvrent à son développement, son rayonnement et sa longévité. Une entreprise de la filière électronique, Europlacer Industries illustre cette dualité, s’inscrire dans le mouvement de l’Usine du Futur et maintenir un faisceau relationnel dynamique et durable, tant en interne qu’avec leurs clients et fournisseurs.
EUROPLACER INDUSTRIES est l’un des leaders dans la fabrication et la distribution d’équipements destinés au marché de l’assemblage des cartes électroniques depuis plus de 40 ans
Rencontre avec Alain Michel Ceretti, directeur commercial Europe.
Histoire : C’est en 1978 sur une idée de M Gerard Plet fondateur de Tronico que la société Numergo basée à Rocheservière en Vendée fut créée
La société fut ensuite cédée en 1981 à Eurosoft pour devenir 10 plus tard en 1991 la société Europlacer Industries que nous connaissons. Après un premier agrandissement en 1998 puis un second en 2017, le site de Rocheservière s’étale aujourd’hui sur 3500 m² et emploie 90 personnes. En 1978, les premiers équipements fabriqués dans l’usine de Rocheservière avant l’arrivée des composants CMS furent des machines à wrapper.
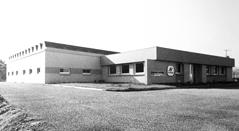

Usine de nos jours En électronique au milieu des années 70, le wrapping est une technique alternative de réalisation de circuits imprimés consistant à remplacer les soudures par des fils enroulés sur les broches des composants. L’entreprise déjà basée à Rocheservière comptait alors une vingtaine d’ingénieurs et techniciens. C’est en 1981 que la première machine de pose de composants « Ergonic » a été livrée à la société Thomson CSF Malakoff en région parisienne. A cette époque on ne parlait pas encore de composants CMS, mais de composants « hybrides » hyper miniaturisés issus de la micro-électronique sur céramique.
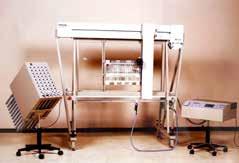
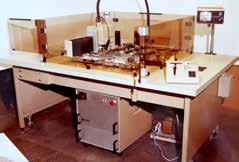
Ce développement pour Thomson a permis à la société de prendre une avance certaine qui verra deux ans après en 1983 l’arrivée des composants dits « montés en surface ». La première machine industrielle dédiée à la pose des composants CMS voit ainsi le jour : la ROBONIC 140. Cette pionnière posait 400 composants à l’heure conditionnés en bobines et déjà en sticks.
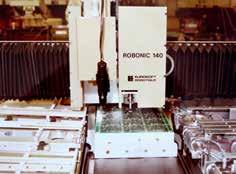
ROBONIC 140 en 1983
Europlacer : un visionnaire à l’écoute des
besoins de ses clients. Durant ces 40 dernières années, les machines de pose de CMS Europlacer n’ont cessé d’évoluer tout en conservant un taux de fiabilité élevé. iineo+, aujourd’hui fleuron de la marque, offre des performances en adéquation avec les besoins des prototypistes tout comme pour les assembleurs de cartes en série.
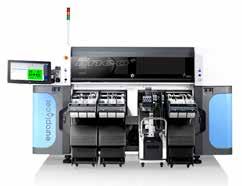
Machine de placement CMS – iineo+ Tous ces équipements sont assemblés dans l’usine de Rocheservière en Vendée.
Le bureau d’études en recherche et développement basé à Rocheservière est composé de 20 ingénieurs maîtrisant l’électronique, la mécanique et l’informatique. La traçabilité et l’industrie 4.0 sont au cœur de ces développements depuis 2016. Le Soft ii-4.0 Software Suite d’Europlacer qui s’appuie sur la certification CFX IPC acquise en 2021 par Europlacer propose un écosystème CFX interconnecté pour l’environnement de production en atelier d’assemblage.
En phase avec l’objectif d’automatisation et de la maîtrise des process que représente l’industrie 4.0, Europlacer offre des solutions hardware et logicielles qui travaillent et communiquent ensemble pour apporter productivité et adaptabilité. Il s’agit notamment d’anticiper les événements indésirables susceptibles d’interrompre ou ralentir la production, mais aussi de remonter des données de production sur un format unique (CFX) pour analyser et améliorer en continue la qualité et la productivité. Très implanté dans l’industrie spatiale, Europlacer propose un testeur de composants, embarqué sur toutes ses machines de pose ainsi qu’un logiciel de traçabilité qui répond aux besoins les plus exigeants de la profession. Avec l’arrivée du CFX et de l’industrie 4.0, Europlacer a investi sur les outils de mobilité tels que les tablettes. Ce sont de véritables tableaux de bord nomades à destination des opérateurs et cadres de production. En tant que constructeur français, tous les softs et manuels sont en français avec une hot line basée en Vendée. Europlacer dispose d’une large gamme de machines de pose CMS, allant de la machine conçue pour les prototypes et petites séries à la machine haute cadence avec la gamme ATOM sans renoncement pour autant à la souplesse et la flexibilité. d’équipements CMS, nous sommes les mieux placés pour offrir à notre clientèle une sélection d’équipements de production de qualité conçus par des équipementiers de confiance et soigneusement sélectionnés.
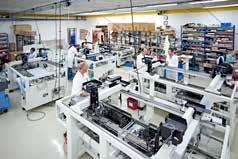
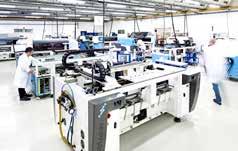
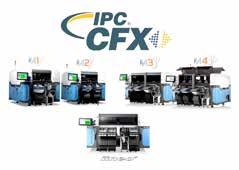
Nous proposons des équipements qui s’interfacent parfaitement avec les machines Europlacer en cohérence avec leurs performances et spécificités. Europlacer propose depuis plus de 25 ans des équipements périphériques complémentaires, en particulier, des fours de refusion avec la gamme BTU avec plus de 300 fours installés en France depuis 1995, des machines AOI et SPI avec la gamme MIRTEC, avec plus de 100 machines installées en France depuis 2006.
Enfin, une gamme complète de transitique pour la mise en ligne des machines avec la gamme SOVTECH qui propose des convoyeurs d’interface, des empileurs et dépileurs, des buffers pour AOI et globalement toute la transitique nécessaire pour une mise en ligne. Plus récemment, Europlacer à la demande de ses clients, a introduit une gamme de machines de nettoyage de cartes et d’écrans de Sérigraphie. Nous avons choisi le constructeur Tchèque PBT Works et disposons d’une trentaine de machines en fonctionnement en France.
Maîtriser la dépose de crème à braser
Pour que la pose des CMS soit optimale, il est nécessaire que la dépose de la crème à braser sur le PCB soit maitrisée et de qualité. Cette étape est primordiale ! On pourra toujours avoir la machine de pose la plus performante, mais si la crème à braser n’est pas bien déposée, un grand nombre d’anomalies ne pourrons être corrigées simplement.
C’est pour cette raison qu’en 1995, Europlacer a racheté l’équipementier Anglais Speedprint aujourd’hui une filiale à 100% d’Europlacer. Speedprint, est l’un des leaders mondiaux des équipements de sérigraphie de crème à braser sur PCB. Avec plus de 100 machines installées en France, Europlacer s’est imposé sur le territoire national comme un fournisseur incontournable de machines de sérigraphie capables aussi de poser les étiquettes sur PCB et de reporter sur le circuit des points de colle ou de crème à braser.
Aujourd’hui la marque Speedprint a disparu et toutes les machines de sérigraphie sont commercialisées sous le nom d’Europlacer.
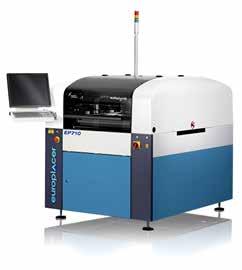
Machine de sérigraphie EP710
Europlacer, un rayonnement international
Europlacer possède 7 filiales dans le monde : USA, Chine, Taïwan, Allemagne, Espagne/ Portugal, Angleterre, Italie / Slovénie. Des distributeurs indépendants et exclusifs représentent Europlacer dans les autres pays, notamment en Scandinavie, Benelux, Inde, Europe de l’est et Amérique du Sud. Nos équipes françaises supervisent nos activités en Afrique avec en 2020 une première installation en Afrique subsaharienne au Kenya.
Nous disposons de deux sites de production. En France en Vendée pour la fabrication des machines de pose, et à Upton au sud de l’Angleterre pour les machines de sérigraphie.
Le service après-vente : Un Support Incomparable.
“Au top” c’est comme cela que nos clients qualifient le support que nous leurs offrons. Nous portons une attention toute particulière à notre service SAV et ce partout le monde. Nous savons que ce qui est crucial pour nos clients, c’est la rapidité et la qualité du service. Les industriels quels qu’ils soient où qu’ils soient se plaignent de ne pas trouver la main d’œuvre qualifiée dont ils ont besoin. De fait, ils se reposent de plus en plus sur leurs fournisseurs d’équipements pour en assurer la maintenance. Nous proposons donc un ensemble de services pour répondre à ces exigences nouvelles : • Diagnostiques et assistance sur place ou à distance (nos prenons la main à distance sur nos machines) • Une équipe de 14 techniciens en France dédiés au SAV • Des contrats de maintenance sur mesure et un service pièces détachées • Des audits de productivité chez les utilisateurs Europlacer • Des formations réalisées en interne chez nous ou chez nos clients. A noter qu’Europlacer est certifié Qualiopi. En effet, depuis le 1er janvier 2022, cette certification qualité est obligatoire pour que nos clients puissent accéder aux fonds publics pour la prise en charge des formations en entreprise.
Europlacer c’est aussi l’Académie Europlacer
Avec 30 ans d’expérience, les experts Europlacer ont développé une gamme complète de programmes de formation. Nous sommes fiers de pouvoir ainsi servir nos clients : • Dans un environnement adapté à la formation • Avec des salles de formation équipées des machines adéquates • Avec des présentations, des carnets de travail, des ensembles mécaniques complets à la disposition des formateurs… • Des outils modernes d’évaluation des compétences. A ce propos, notre “QUIZ” interactif nous aide à mieux évaluer la demande de nos clients afin qu’ils maintiennent à niveau leurs systèmes qualité.
Représentation
A Rocheservière, nous disposons d’un showroom de 250 m².
Les démonstrations y sont bien évidemment organisées régulièrement, mais nous pouvons également faire des démonstrations en visioconférence. Europlacer en 30 ans s’est imposé comme un acteur majeur de l’industrie électronique. Très implanté chez les sous-traitants, Europlacer s’est imposé en quelques années dans l’industrie Aéronautique Spatiale et militaire avec des grands noms comme Airbus, MBDA, Thales Aliena, BAE Boeing ou Rolls-Royce qui ont décidé de choisir Europlacer pour poser aujourd’hui leurs composants CMS.
Attachés à ses racines françaises, la production de nos machines de pose CMS est enracinée en Vendée depuis toujours. Si en 2000 les exportations représentaient 20% de notre chiffre d’affaires, aujourd’hui il s’agit de plus de 80%. Avec 250 employés répartis sur tous les continents, et un chiffre d’affaires de près de 40M€, Europlacer Industries démontre que le savoir-faire français dans l’industrie électronique sait s’imposer durablement tant dans l’hexagone qu’à l’international.
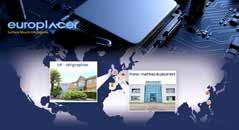
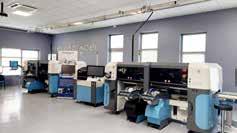
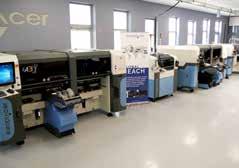
EUROPLACER INDUSTRIES Alain-Michel CERETTI +33 (0)2 51 31 03 03 alain-michel.ceretti@europlacer.fr www.europlacer.com
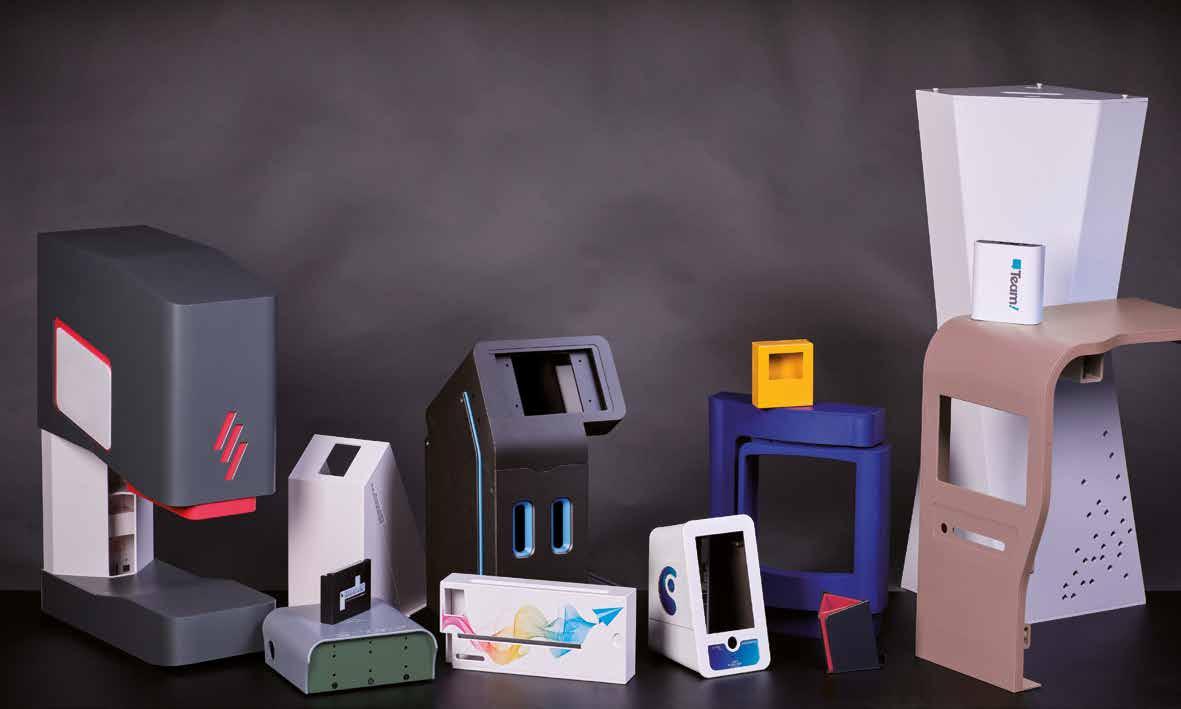
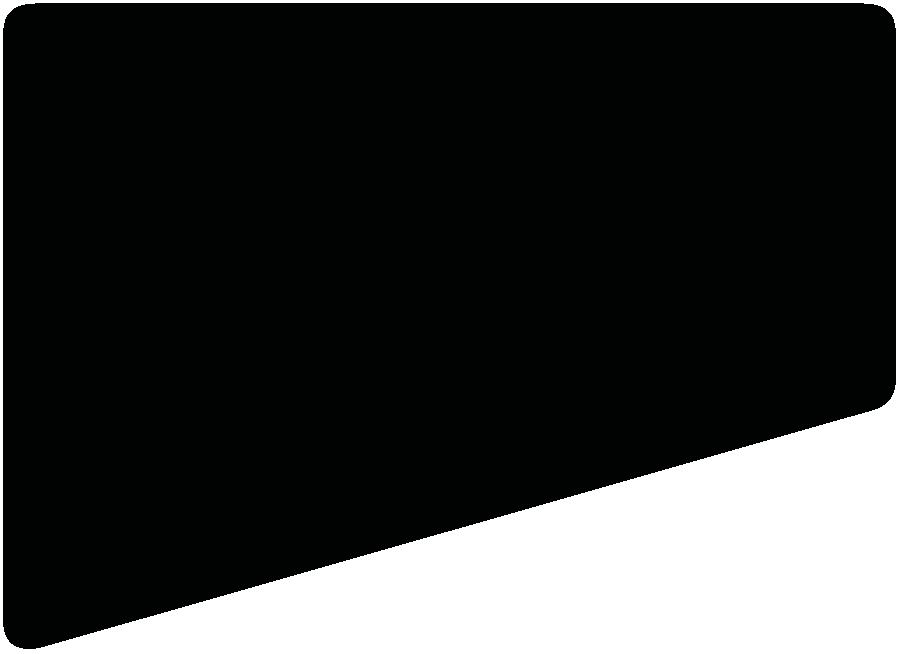
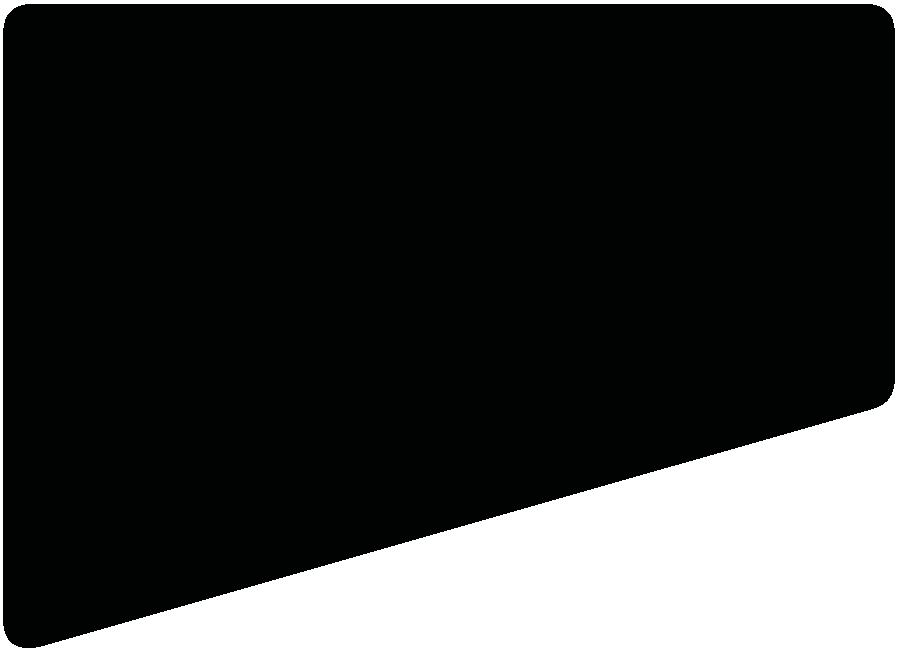
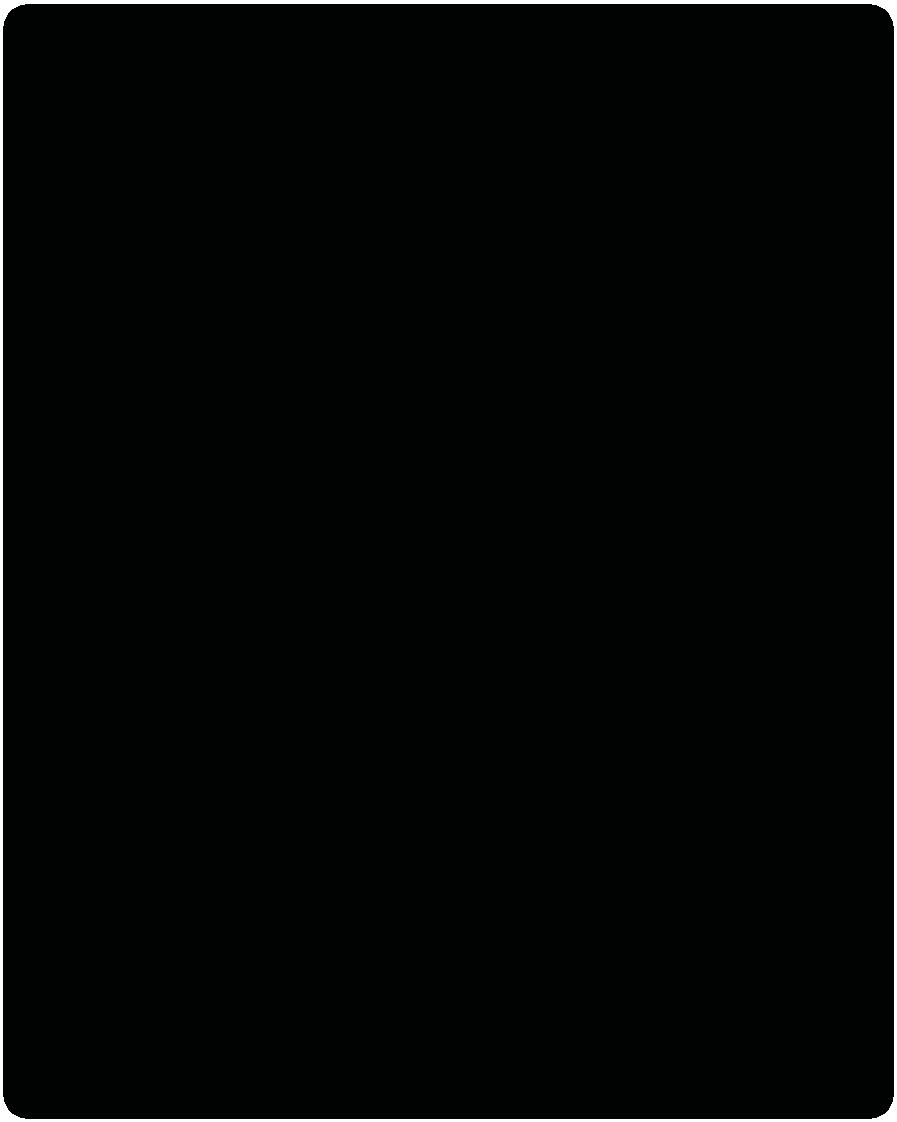
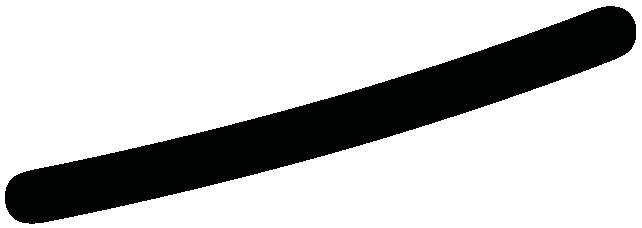
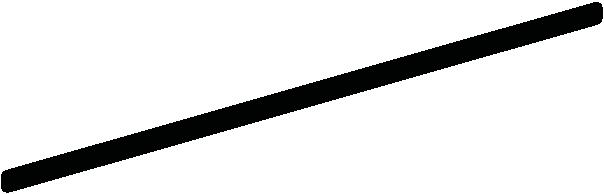
Tour d’horizon des technologies de
brasage des CMS pour protos et micro-séries
Nous vous proposons de comparer les différentes technologies de brasage des cartes électroniques avec les avantages et inconvénients de chacune des solutions pour que vous puissiez définir la technologie qui correspond à votre besoin.
Nous traiterons ici que des systèmes fermés statiques pour le brasage des CMS par oppositions aux systèmes de brasage manuel ou systèmes de réparation.
Technologie de chauffage par élément chauffant (résistance électrique ou résistance blindée)
Le chauffage par les éléments chauffants est généralement couplé avec une convection de l’air pour permettre un chauffage plus homogène. Cette technologie est souvent la moins onéreuse et présente peu de coûts de maintenance. Ce sont là ses principaux avantages. Il est souvent difficile avec cette technologie de tenir les rampes de chauffage recommandées par les normes IPC. En effet, les résistances chauffantes ont une inertie thermique importante ce qui entraîne un manque de réactivité du système sur les phases de montées en température et de refroidissement. Ce type de système est généralement réservé en prototypage à des fonctions d’étuvage plutôt que de brasage.
Technologie halogène/infrarouge
Cette technologie est souvent considérée comme la solution classique dans le domaine du prototypage et c’est bien souvent la plus répandue. Elle utilise des éléments chauffants de types quartz ou halogène pour permettre de chauffer ; elle est généralement combinée à une convection forcée de l’air pour aider à une répartition homogène de la température.
Les principaux avantages de cette technologie sont : - Peu onéreux à l’achat - Maintenance abordable - Systèmes simples à mettre en œuvre - Permet de suivre les rampes de température recommandée par les normes IPC (Hausse supérieure à 1 degré par seconde) - Certains systèmes avancés permettent de reproduire le comportement d’un four en ligne avec des fonctionnalités dites multi-paliers pour reproduire le comportement des différentes zones de chauffe des fours de production en ligne. Cela permet de reproduire un
Exemple d’une résistance blindée
Cette technologie [Le brasage phase vapeur] est par sa simplicité de mise en œuvre et la qualité des joints brasés produits très plébiscitée et adaptée aussi bien au prototypage qu’aux micro-séries.
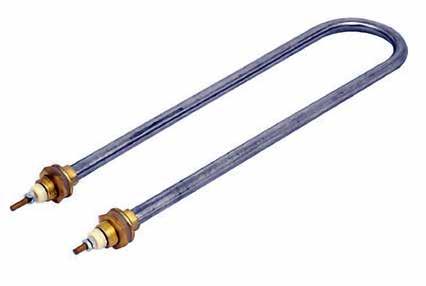
profil thermique similaire aux conditions de production. - Consommation d’électricité pendant les phases de chauffe importante mais uniquement pendant l’utilisation. Il est généralement recommandé d’effectuer un cycle à vide pour mettre le système à température afin de garantir les performances optimales et une répétabilité du process. Après ce préchauffage, la consommation correspond uniquement à celle du cycle de production.
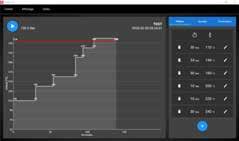
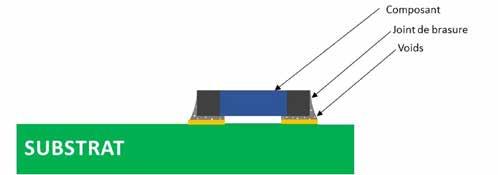
Exemple du logiciel SMTIX 2.0 permettant le contrôle multi-paliers
Technologie d’inertage sous azote
Cette technologie est une combinaison de l’une des deux précédemment évoquées avec l’adjonction d’azote pour remplacer dans l’enceinte du four l’oxygène contenu dans l’air. On la retrouve de manière générale pour le brasage en prototypage combinée avec la technologie de chauffage halogène/infrarouge. Cette technologie permet d’éviter les processus d’oxydation des joints de brasure. Si c’est un point souvent essentiel voir indispensable en production pour garantir la fiabilité dans le temps d’un produit fini, ce n’est pas toujours le cas en prototypage où le contrôle d’un test fonctionnel ne nécessite pas nécessairement l’absence d’oxydation.
Cette technologie peut s’avérer très coûteuse par la consommation d’azote qui est très importante. Par ailleurs pour être efficace et tirer le bénéfice de l’inertage il est indispensable que la saturation de l’air en azote dans la chambre de traitement atteigne une concentration minimale de 99.95%. Il est malheureusement très rare sur les équipements de prototypage de constater un tel niveau.
A l’inverse, les deux technologies suivantes peuvent présenter des avantages certains dans des tests fonctionnels sur des prototypes, comme par exemple dans l’électronique de puissance. ment pendant le processus de refusion. Les deux principaux avantages de cette technologie sont l’inertage. Lors de la création du vide dans la chambre de traitement, il n’y a plus d’air et donc plus d’oxygène présent. On évite ainsi toute oxydation. L’autre avantage de cette technologie est la réduction des voids (ou micro-cavités). Le vide pendant la phase du liquidus assure l’absence de formation de voids. C’est la technologie qui offre la meilleure performance sur ce point. La réduction voire l’absence de voids est indispensable pour l’usage de courants forts et la fiabilité à long terme.
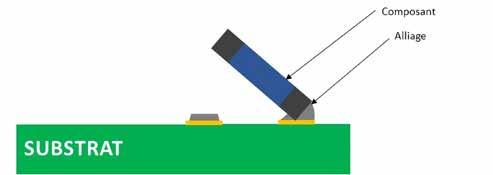
L’une des difficultés de cette technologie réside dans l’inertie thermique et le stress thermique engendré par l’infrarouge. La particularité de l’infrarouge est que la chaleur est transmise par des ondes lumineuses (rayon lumineux) et l’absence d’air dans la chambre de traitement implique que seules les ondes IR transmettent la chaleur. Ainsi en fonction des couleurs, de la hauteur des composants (qui créent des zones d’ombre) et de l’inertie thermique de chacun des éléments composants la carte, il est difficile d’obtenir une montée en température homogène et uniforme et de surcroît en respectant les profils thermiques des crèmes à braser. Cette technologie est sujette aux over-shoots (dépassement de la température souhaitée) pouvant endommager certains composants et à des stress thermiques (notamment divergences importantes de températures sur la carte) facilitant l’effet tombstone et pouvant aller jusqu’à entraîner des déformations mécaniques du substrat.
Technologie du brasage phase vapeur
Cette technologie consiste à utiliser un médium pour transmettre la chaleur à la carte électronique et ses composants. Le médium utilisé est un Perfluoropolyether (PFPE) qui se présente à température ambiante sous forme de liquide et qui a la particularité d’être inerte et d’offrir à l’état gazeux une excellente stabilité thermique. La température de la vapeur est déterminée par le médium utilisé. Un médium de grade 230 par exemple aura une température à l’état gazeux (vapeur) de 230 °C. Le Galden® est un médium très répandu pour cette technologie.
Vous pouvez retrouver plus d’information sur ce produit en consultant le site : https://www.solvay.com/en/brands/galden-pfpe Des éléments chauffants généralement de type résistances électriques sont utilisés pour chauffer le medium pour qu’il passe à l’état gazeux. La carte à braser est alors plongée dans la vapeur générée qui transfert sa chaleur à la carte pour effectuer le brasage. Cette technologie a comme avantages principaux : - L’inertage - La réduction des voids - Réduction du stress thermique avec un delta de température entre composants incomparable aux autres technologies - Pas d’over-shooting - Pas d’erreur de manipulation possible pendant le cycle - Simplicité de réglage et de mise au point du profil de refusion -Possibilité de mettre des cartes de designs différents pendant un même cycle si une crème à braser avec une même température de liquidus (fusion) est utilisée.
Illustration de la présence de voids dans un joint brasé
Illustration de l’effet tombstone
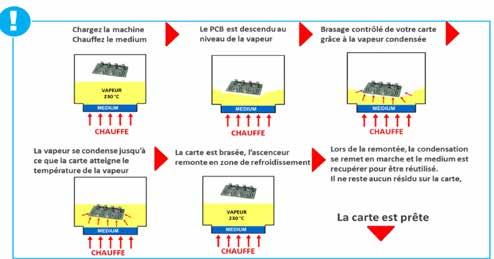
Illustration du process de brasage avec un système phase vapeur avec ascenseur
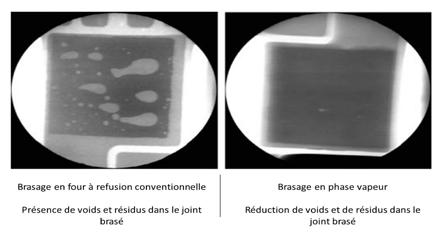
Cette technologie nécessite l’utilisation de médium qui est onéreux. Cependant la consommation peut être limitée grâce à des systèmes performants de récupération des vapeurs en fin de cycle. Cette technologie est par sa simplicité de mise en œuvre et la qualité des joints brasés produits très plébiscitée et adaptée aussi bien au prototypage qu’aux microséries.
Technologie combinée brasage phase vapeur et brasage sous vide.
Cette technologie consiste à essayer de tirer profit des avantages des deux technologies précédemment présentées en réalisant dans un premier temps le process du brasage phase vapeur, puis au moment du liquidus d’aspirer l’intégralité du gaz de la chambre de traitement afin d’y assurer le vide pour supprimer les éventuels voids restants. Cette technologie offre les meilleurs niveaux de qualités des joints de brasure et de réduction du stress thermique. En raison du coût de cette technologie, elle est réservée pour le prototypage généralement aux applications les plus exigeantes qui ne supportent aucun voids.
Il s’agit d’un tableau synthétique pouvant varier en fonction des équipements utilisés, de leurs options ainsi que de l’ensemble du process (crème à braser, process de dépôt, process de placement…)
CIF
Alexis ALBRIEUX +33 (0)1 39 66 96 83 adm@cif.fr www.cif.fr
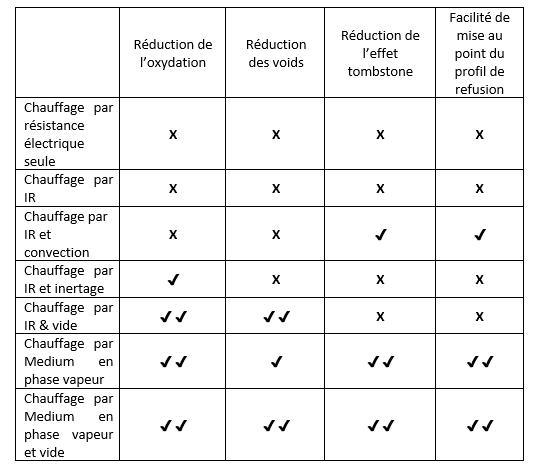
La durabilité : Un voyage à travers 25 ans de technologie de réparation Ersa
Rencontre avec Jörg Nolte, chef de produit Tools, Rework & Inspection chez Ersa
Depuis 25 ans, Ersa s’est investi dans la réparation de modules électroniques, et tout particulièrement des composants CMS à haute polarité. En ces temps de pénurie de composants et de chaînes d’approvisionnement interrompues, il est important de maintenir l’intégrité de votre production, tout en restant dans l’optique d’une économie durable. Jörg Nolte, chef de produit chez Ersa, donne un aperçu de cette technique fascinante.
Tout a commencé en 1997 avec l’IR 500 A, le premier système de réparation infrarouge d’Ersa. Il a été développé en collaboration avec la petite entreprise Rewatronik, afin de pouvoir dessouder et souder en toute sécurité les composants «Ball Grid Array» (BGA), encore nouveaux à l’époque. Très rapidement, une autre coopération avec le spécialiste suisse Essemtec a permis de concevoir un système de placement de composants. En effet, les composants Fine-Pitch et ceux dont les connexions étaient cachées ne pouvaient pas être placés à la main avec suffisamment de précision. «Lorsque je suis entré chez Ersa en 2000, la réparation CMS/BGA en était encore à ses débuts», raconte Jörg Nolte, chef de produit chez Ersa et responsable de la division Rework. Et il ajoute : «Mais ensuite, les choses n’ont cessé de progresser, car on avait parié sur le bon cheval. La banalisation des BGAs, difficiles à maîtriser au début, n’a cessé d’augmenter et, avec elle, le besoin de retouches qualifiées». Aujourd’hui, le BGA fait partie de la famille des « Bottom Terminated Components » (BTC), c’est-à-dire des composants dont les connexions à souder se trouvent sur leurs faces inférieures. Dans les premières années, les BGA étaient souvent les composants les plus sensibles d’un module : si l’équilibre thermique n’était
Réparer pour une production durable. Ersa a investi énormément de temps et d’énergie pour convaincre les utilisateurs du centre de service de téléphonie mobile à l’industrie électronique, du bienfondé de la technologie infrarouge.
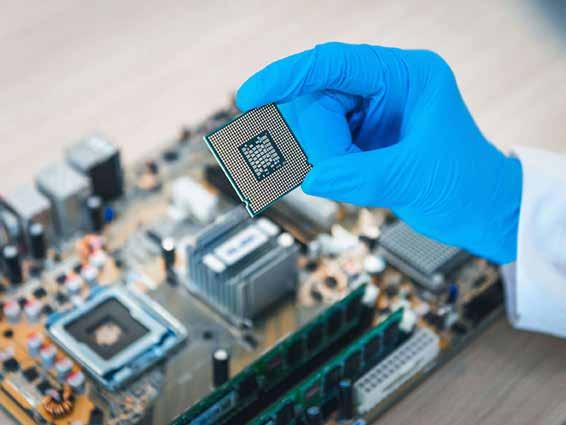
pas totalement équilibré lors du process de soudage, le composant se déformait, ce qui entraînait souvent la formation de ponts ou d’autres défauts. Les pannes étaient donc fréquentes et les réparations nécessaires. Dans la plupart des cas, les BGA souffrent d’une tension trop importante dans les billes situées aux coins et in fine des microfissures qui en découlent. Faire refusionner le BGA en y ajoutant un peu de flux reste à ce jour un moyen reconnu de réparer de tels défauts. Aujourd’hui encore, les nouveaux composants issus des BGA sont sensibles à différents paramètres du process de refusion. Ainsi, les composants «Micro Lead Frame» (MLF) ont tendance à flotter si la quantité de soudure est mal dosée, entrainant des problèmes de contacts. La liste erreurs possibles est sans fin, c’est la raison pour laquelle un process de réparation sécurisé et reproductible doit être établi pour tous les cas de figures.
Technologie IR
Aujourd’hui encore, on trouve sur Internet des vidéos montrant des tentatives de remplacement de processeurs ou d’autres composants à l’aide de pistolets à air chaud. Pour quel résultat ? Plus que douteux ! Ersa a investi énormément de temps et d’énergie pour convaincre les utilisateurs, du centre de service de téléphonie mobile à l’industrie électronique, du bienfondé de la technologie infrarouge. Il fut un temps où même les fabricants de systèmes de réparation à air chaud ont tout fait pour torpiller la technologie IR. «On prétendait que les composants étaient trop chauds, que le process n’était pas contrôlable, que les surfaces réfléchissantes ne chauffaient pas, ou même que l’utilisateur pouvait se blesser à cause du rayonnement IR !», se souvient Nolte en évoquant les blocages des premières années. La chaleur radiante à ondes moyennes émises par des éléments chauffants en céramiques est invisible et présente un énorme avantage : contrairement aux éléments chauffants à quartz, leur spectre de rayonnement convient parfaitement pour chauffer rapidement et de manière homogène les métaux, les matières plastiques, les céramiques et les résines époxy. Les différences de température mesurées sur un composant (delta T) sont inférieures à 6 °C. De nombreux utilisateurs ont rapidement compris que la refusion asservie par capteur d’un système de réparation IR à ondes moyennes présentait d’autres avantages par rapport aux techniques classiques : le profil de brasage suit très précisément la consigne en raison du contrôle précis de la température. Les composants et les sous-ensembles sont chauffés de manière homogène et en douceur. Comme il n’est pas nécessaire d’utiliser des buses spécifiques, le process de refusion peut être observé avec une caméra.
Réparation sans plomb
Avec l’introduction des alliages sans plomb en 2006, la hausse du liquidus (183 °C pour un alliage au plomb contre environ 217 °C pour un sans plomb) a eu pour conséquence des exigences plus élevées concernant les équipements de brasage et les systèmes de réparation. Des températures plus élevées entraînaient des fenêtres de process plus étroites au regard de spécifications des composants. Dès lors, un contrôle précis du process devenait de plus en plus important. C’est dans ce contexte que l’Ersa IR/PL 550 et son grand frère l’IR/PL 650 ont marqué l’histoire de la réparation industrielle. La mesure de la température sans contact à l’aide d’un pyromètre a été introduite pour la première fois dans ces systèmes, ce qui constitue une innovation majeure. Les exigences en matière de réparation sur très grands circuits imprimés provenant des infrastructures informatiques ont donné naissance au premier système de réparation vraiment grand format, l’Ersa IR/PL 650 XL (pour un prestataire de services EMS américain). Depuis, la réparation s’est encore professionnalisée, même si certains secteurs continuent de l’exclure. Des études comme le «Leitfaden Rework elektronischer Baugruppen» du ZVEI (publié en 2017) montrent que la réparation professionnelle donne des résultats fiables si, comme dans un process de ligne, tous les paramètres importants sont respectés. «Souvent, ce n’est pas un manque de confiance dans le process de réparation à proprement parler, mais c’est le travail d’homologation qui justifie cette réticence», explique Jörg Nolte. A ce stade, une coopération plus approfondie entre les utilisateurs, les fabricants et les institutions est souhaitable. Tout a commencé en 1997 avec l’IR 500 A, le premier système de réparation infrarouge d’Ersa. Il a été développé en collaboration avec la petite entreprise Rewatronik, afin de pouvoir dessouder et souder en toute sécurité les composants «Ball Grid Array» (BGA), encore nouveaux à l’époque. Très rapidement, une autre coopération avec le spécialiste suisse Essemtec a permis de concevoir un système de placement de composants. En effet, les composants Fine-Pitch et ceux dont les connexions étaient cachées ne pouvaient pas être placés à la main avec suffisamment de précision. «Lorsque je suis entré chez Ersa en 2000, la réparation CMS/BGA en était encore à ses débuts», raconte Jörg Nolte, chef de produit chez Ersa et responsable de la division Rework. Et il ajoute : «Mais ensuite, les choses n’ont cessé de progresser, car on avait parié sur le bon cheval. La banalisation des BGAs, difficiles à
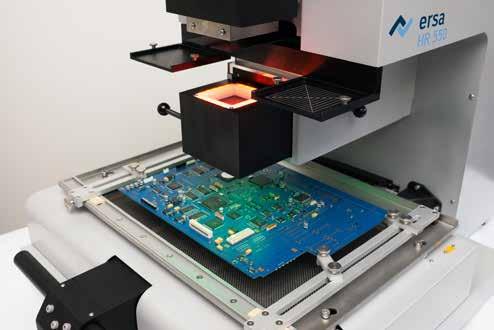
Ersa HR 550 – système de réparation semi automatique puissant de dernière génération
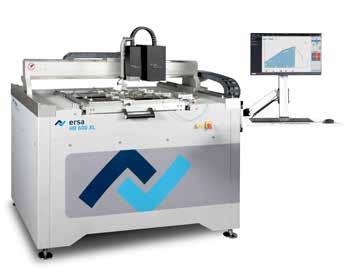
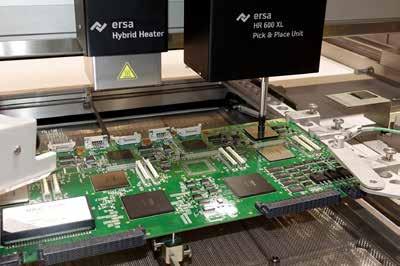
Réparation professionnelle des PCBs grands formats grâce au système hybride HR 600 XL, capable de traiter des cartes 625 x 1,250 mm. Logicel de pilotage HRSoft 2.
maîtriser au début, n’a cessé d’augmenter et, avec elle, le besoin de retouches qualifiées». Aujourd’hui, le BGA fait partie de la famille des « Bottom Terminated Components » (BTC), c’est-à-dire des composants dont les connexions à souder se trouvent sur leurs faces inférieures. Dans les premières années, les BGA étaient souvent les composants les plus sensibles d’un module : si l’équilibre thermique n’était pas totalement équilibré lors du process de soudage, le composant se déformait, ce qui entraînait souvent la formation de ponts ou d’autres défauts. Les pannes étaient donc fréquentes et les réparations nécessaires. Dans la plupart des cas, les BGA souffrent d’une tension trop importante dans les billes situées aux coins et in fine des microfissures qui en découlent. Faire refusionner le BGA en y ajoutant un peu de flux reste à ce jour un moyen reconnu de réparer de tels défauts. Aujourd’hui encore, les nouveaux composants issus des BGA sont sensibles à différents paramètres du process de refusion. Ainsi, les composants «Micro Lead Frame» (MLF) ont tendance à flotter si la quantité de soudure est mal dosée, entrainant des problèmes de contacts. La liste erreurs possibles est sans fin, c’est la raison pour laquelle un process de réparation sécurisé et reproductible doit être établi pour tous les cas de figures.
Technologie IR
Aujourd’hui encore, on trouve sur Internet des vidéos montrant des tentatives de remplacement de processeurs ou d’autres composants à l’aide de pistolets à air chaud. Pour quel résultat ? Plus que douteux ! Ersa a investi énormément de temps et d’énergie pour convaincre les utilisateurs, du centre de service de téléphonie mobile à l’industrie électronique, du bienfondé de la technologie infrarouge. Il fut un temps où même les fabricants de systèmes de réparation à air chaud ont tout fait pour torpiller la technologie IR. «On prétendait que les composants étaient trop chauds, que le process n’était pas contrôlable, que les surfaces réfléchissantes ne chauffaient pas, ou même que l’utilisateur pouvait se blesser à cause du rayonnement IR !», se souvient Nolte en évoquant les blocages des premières années. La chaleur radiante à ondes moyennes émises par des éléments chauffants en céramiques est invisible et présente un énorme avantage : contrairement aux éléments chauffants à quartz, leur spectre de rayonnement convient parfaitement pour chauffer rapidement et de manière homogène les métaux, les matières plastiques, les céramiques et les résines époxy. Les différences de température mesurées sur un composant (delta T) sont inférieures à 6 °C.
De nombreux utilisateurs ont rapidement compris que la refusion asservie par capteur d’un système de réparation IR à ondes moyennes présentait d’autres avantages par rapport aux techniques classiques : le profil de brasage suit très précisément la consigne en raison du contrôle précis de la température. Les composants et les sous-ensembles sont chauffés de manière homogène et en douceur. Comme il n’est pas nécessaire d’utiliser des buses spécifiques, le process de refusion peut être observé avec une caméra.
Réparation sans plomb
Avec l’introduction des alliages sans plomb en 2006, la hausse du liquidus (183 °C pour un alliage au plomb contre environ 217 °C pour un sans plomb) a eu pour conséquence des exigences plus élevées concernant les équipements de brasage et les systèmes de réparation. Des températures plus élevées entraînaient des fenêtres de process plus étroites au regard de spécifications des composants. Dès lors, un contrôle précis du process devenait de plus en plus important. C’est dans ce contexte que l’Ersa IR/PL 550 et son grand frère l’IR/PL 650 ont marqué l’histoire de la réparation industrielle. La mesure de la température sans contact à l’aide d’un pyromètre a été introduite pour la première fois dans ces systèmes, ce qui constitue une innovation majeure. Les exigences en matière de réparation sur très grands circuits imprimés provenant des infrastructures informatiques ont donné naissance au premier système de réparation vraiment grand format, l’Ersa IR/PL 650 XL (pour un prestataire de services EMS américain). Depuis, la réparation s’est encore professionnalisée, même si certains secteurs continuent de l’exclure. Des études comme le «Leitfaden Rework elektronischer Baugruppen» du ZVEI (publié en 2017) montrent que la réparation professionnelle donne des résultats fiables si, comme dans un process de ligne, tous les paramètres importants sont respectés. «Souvent, ce n’est pas un manque de confiance dans le process de réparation à proprement parler, mais c’est le travail d’homologation qui justifie cette réticence», explique Jörg Nolte. A ce stade, une coopération plus approfondie
Durabilité
Eviter le gaspillage en réparant par exemple un pont sur un QFP ou un BGA, ouvre la voie d’une action durable. Le «droit à la réparation» exigé par la Commission européenne permet d’éviter les déchets électroniques et pousse la production électronique à la préservation des ressources et à l’économie circulaire. Dans l’industrie et les centres de service, des milliers de cartes électroniques sont traitées chaque jour dans le monde entier avec des systèmes de réparation Ersa et sont ainsi sauvées d’une mise au rebut ! Ersa a également défini la durabilité à un autre niveau : Au cours des 25 dernières années, de nombreux fournisseurs de systèmes de réparation sont apparus puis ont disparu, tandis qu’Ersa s’est imposé dans ce domaine de l’industrie électronique. Des relations à long terme avec les clients, un SAV exemplaire dans le monde entier et une très longue disponibilité des pièces de rechange (même pour les produits obsolètes), témoignent de cette philosophie. Pour le plaisir du chef de produit Jörg Nolte : «Nous recevons aujourd’hui des demandes de pièces détachées pour des systèmes vendus il y a 15 ans, c’est formidable !»
Ersa devient hybride et automatique
La technologie hybride fait d’abord son apparition sur les systèmes de réparation HR 100 et HR 600. La technologie de chauffe IR est couplée à une partie de convection dans la tête de chauffe supérieure. Ainsi, le rendement énergétique est amélioré et le composant à traiter est chauffé plus rapidement. Les principaux défauts des systèmes à air chaud, comme le soufflage des plus petits composants, n’ont pas lieu ici car on travaille avec de très faibles quantités d’air.
L’ HR 600, lancée en 2012, répond en outre à une demande importante des clients : plus d’automatisation ! Pour la première fois, les étapes de dessoudage, de placement et de soudage des composants sont liées de telle manière que l’opérateur n’a pratiquement plus d’influence sur le résultat final. Fiabilité et répétabilité sont désormais mis à l’honneur. La particularité de la HR 600, qui reste à ce jour l’un des systèmes de réparation les plus populaires, réside dans le placement automatisé des composants. À l’aide de deux caméras, d’un algorithme de traitement d’image et d’un système d’axes de haute précision, le composant est automatiquement placé sur sa plage d’accueil avant d’être refusionné. L’ HR 600/2 marque une étape importante en terme de productivité et de répétabilité des process de réparation.
La nouvelle génération
Depuis, la gamme de systèmes de réparation Ersa s’est enrichie de nouveaux membres : «De l’HR 500 jusqu’à l’ HR 600 XL, la gamme de produits actuelle répond à l’ensemble des exigences clients à travers le monde», résume Jörg Nolte à propos du positionnement de la marque Ersa. Les systèmes les plus récents impressionnent tant par leur technologie que par leur pilotage avec une plate-forme logicielle uniforme. « L’utilisateur passe facilement d’un système à l’autre, tout est structuré de la même manière », précise Nolte. C’est tardivement, avec l‘HR 550, qu’ERSA a pris la décision de produire ses systèmes entièrement en interne. Jörg Nolte: «Bien sûr, cela a été un long apprentissage pour nous, mais nous avons maintenant toute l’expertise en ingénierie et pouvons mieux réagir aux mouvements du marché. C’est un facteur décisif aujourd’hui, en particulier dans la technologie logicielle.“
Pour le fleuron de la gamme, l’ HR 600 XL, il a ainsi été possible de développer rapidement et avec une grande qualité les extensions et optimisations fonctionnelles demandées par les clients. Par exemple, grâce à une extension de la chauffe inférieure, le système peut aujourd’hui traiter des cartes allant jusqu’à 625 x 1.250 mm, et avec la tête de chauffe supérieure spéciale, des composants de plus de 100 mm !
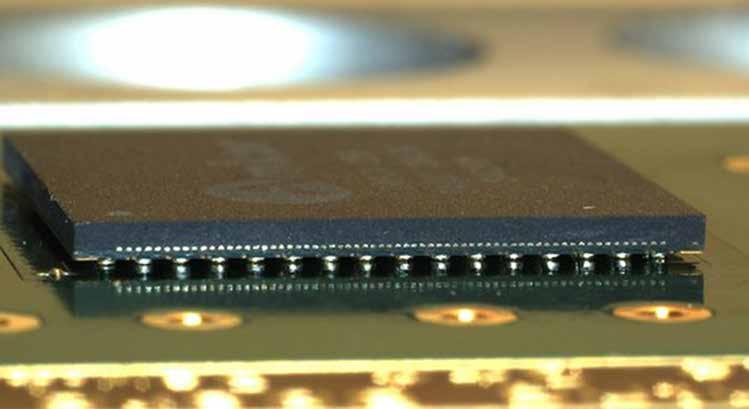
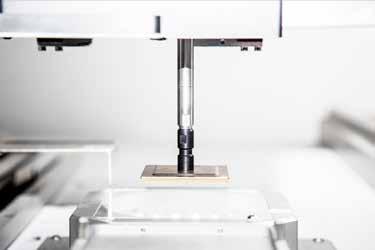
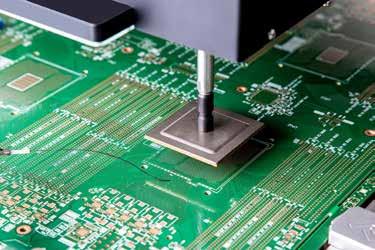
Placement précis des composants allant jusqu’à 100 mm de coté. A gauche, BGA métallique au dessus du dôme permettant de détecter les connexions du composant. A droite, le déplacement au-dessus de la carte
Et ensuite, que va-t-il se passer?
Lorsqu’on lui demande si tout a été fait en 25 ans, Jörg Nolte sourit et explique : «En principe, oui. Mais le développement se poursuit. Et c’est bien ainsi. Car contrairement à toutes les prédictions, les cartes électroniques devront vraisemblablement continuer à être retouchées». Le nettoyage automatique des plages d’accueil sur le système HR 600 XL est sur le point d’être lancé sur le marché. Dans le domaine des capteurs, on travaille à l’optimisation de la technique de mesure sans contact. Différents sujets, comme la précision de placement, l’amélioration de la technologie de chauffe, ou encore l’intégration des données récoltées à un MES sont aussi à l’étude. Ainsi, la réparation devient une partie à part entière du process de production avec comme vision une production durable. Et bien sûr, l’émergence de nouveaux types de composants doit rester en ligne de mire, tout comme les coûts de fabrication des appareils. Lorsqu’on lui demande ce qui le réjouit le plus à propos des 25 ans d’existence des systèmes de réparation Ersa, Nolte répond : «C’est un sentiment agréable de fournir des outils utiles à nos clients !» Et que va-t-il se passer ensuite ? Certainement encore beaucoup de choses coté réparation, car contrairement à de nombreux pronostics, les cartes électroniques auront toujours besoin d’être réparées…
Les 10 bonnes raisons de réparer
des cartes électroniques :
1) Il y a un défaut sur le composant. 2) Le mauvais composant a été monté. 3) Le composant a été monté dans le mauvais sens. 4) Un composant a été mal soudé (ponts, soudures ouvertes, etc.). 5) Un composant est mal programmé. 6) Un composant est démonté sauvegardé en vue de sa réutilisation (recyclage). 7) Une modification est apportée à l’assemblage (redesign). 8) La carte est un prototype que l’on doit modifier. 9) Des tests sont effectués sur la carte, par exemple un échange croisé (testing). 10) Les données d’un composant provenant d’une carte défectueuse doivent être sauvegardées.
KURTZ ERSA FRANCE Cyril DESCOMBAZ +33(0)6 31 83 38 10 cyril.descombaz@kurtzersa.com www.kurtzersa.com
Les PCB Ultra HDI imposent de fortes exigences en matière de technologie et de fabrication
L’industrie électronique d’aujourd’hui se caractérise par toujours plus de miniaturisation qui concerne un nombre sans cesse croissant d’applications électroniques. Ainsi, les composants BGA ont aujourd’hui des largeurs de piste extrêmement réduites et un isolement minimal sur les PCB pour une utilisation dans des conceptions encore plus denses qui portent sur des largeurs de piste et des isolement inférieurs à
celles des cartes HDI actuelles..
Pour en savoir plus, les Cahiers ont consulté NCAB Group, résolument engagé dans les travaux de l’IPC visant à développer des normes pour les PCB Ultra HDI que le groupe sera en mesure de livrer à ses clients en 2023. Notre mentor est Jan Pedersen, directeur de la technologie. Bienvenue dans le monde de l’ultra HDI.
Les Cahiers : Les nouveaux composants hautement miniaturisés sont utilisés, entre autres, dans la technologie des télécommunications 5G, dans les capteurs et dans les smartphones haut de gamme. Cette technologie commence à s’étendre à d’autres segments de l’industrie. C’est notamment le cas pour certaines applications médicales et dans l’industrie automobile. Jan Pedersen, expliquez à nos lecteurs ce qu’est un PCB Ultra HDI. Jan Pedersen : Pour être défini comme une carte Ultra HDI, le PCB doit avoir une largeur de piste et un isolement inférieurs à 50 µm, une épaisseur diélectrique inférieure à 50 µm, un diamètre des microvia inférieur à 75 µm et des caractéristiques supérieures à la norme IPC 2226 niveau C existante. Mais un problème se pose concernant la conception de ces PCB et les exigences de performance et de qualité à satisfaire. En effet, les normes industrielles manquent. Les fabricants qui, à ce jour, produisent des cartes Ultra HDI travaillent depuis longtemps avec de grandes entreprises telles qu’Apple, Intel, Samsung et d’autres encore. Ces acteurs ont massivement investi dans les usines concernées, compliquant ainsi l’accès à la technologie pour les autres.
Certaines usines peuvent fabriquer des PCB avec une épaisseur de diélectrique et des isolements inférieurs à 50 µm. Cependant, elles ne sont pas toutes en mesure d’obtenir des isolements très faibles, par exemple 20 à 25 µm, qui peuvent être requis aujourd’hui. Pour remédier à ces problèmes
NCAB reçoit tous les jours des demandes de renseignement concernant des circuits imprimés dont les exigences portent sur des largeurs de piste et des isolements inférieurs à celles des cartes HDI
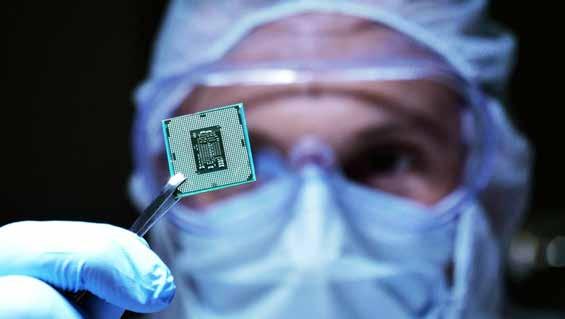
Jan Pedersen. Director of Technology, NACB Group.
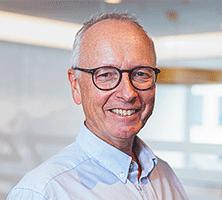

On entend par PCB Ultra HDI des produits dont les largeurs de piste, les isolements et l’épaisseur diélectrique sont inférieurs à 50 µm, dont le diamètre des microvia est inférieur à 75 µm et dont les caractéristiques dépassent la norme IPC 2226 niveau C existante.
et créer une norme industrielle adaptée, l’association mondiale des IPC a créé un groupe de travail dédié à l’Ultra HDI. J’ai l’honneur de présider ce groupe. Les Cahiers : Comment avez-vous été désigné à ce poste ? Jan Pedersen : J’étais Président de la Commission Médicale de l’IPC, où nous discutions de la question des nouvelles exigences et des nouveaux paramètres. Ce débat a progressivement évolué pour finalement aboutir à la formation de ce groupe de travail. Au cours des trois dernières années, ce groupe a travaillé à la mise en œuvre d’une nouvelle norme IPC relative à ce que nous appelons aujourd’hui les PCB Ultra HDI. Nous avons également réalisé un guide afin d’établir des normes de conception et de fabrication pour ces cartes. Les Cahiers : Quels sont les challenges que les fabricants de PCB doivent relever pour fabriquer ces circuits d’un nouveau genre ? Jan Pedersen : Pour permettre aux usines de fabriquer des PCB Ultra HDI, de nombreux changements sont nécessaires. Des investissements doivent être réalisés à la fois dans les équipements et dans les procédés de fabrication.
Auparavant, les développements subissaient le « paradoxe de l’œuf et de la poule ». Aujourd’hui, pour que les usines puissent développer leurs capacités, elles ont d’abord besoin d’une norme qui leur servira de base pour la fabrication des PCB. Grâce aux directives que le groupe de travail des IPC publiera prochainement, l’industrie disposera d’un plan d’action commun sur lequel s’appuyer.
Chez NCAB, un conseil technique interne travaille pour aider nos usines à renforcer leur capacité à répondre aux exigences de l’Ultra HDI. Notamment le « mSAP » - modified Semi-Additive Processing, consiste à déposer du cuivre sur une fine couche au lieu d’être gravé sur une épaisseur plus importante. Il s’agit d’un process « additif » et non « soustractif » de cuivre. De plus, cette méthode est également meilleure pour l’environnement, puisqu’elle nécessite moins de cuivre. Certaines usines sont déjà en mesure de l’utiliser. Le niveau accru de miniaturisation exige également que le schéma puisse être transféré sur le PCB à une résolution suffisamment élevée. L’usine doit donc disposer d’un équipement de pointe d’imagerie directe au laser LDI – Laser Direct Imaging. De plus, l’environnement de travail doit être extrêmement propre pour éviter la contamination et la poussière, ce qui nécessite des investissements considérables. Les processus de test et l’équipement d’inspection optique automatique AOI doivent également faire l’objet d’une mise à jour afin de détecter et d’éviter les défauts potentiels des cartes. De même, il convient de tenir compte de l’équipement et de la chimie durant la métallisation du cuivre. La miniaturisation va également générer un besoin de matières plus propres et plus homogènes. Dans le travail de soutien que NCAB apporte à ses usines, ma position de Président du groupe de travail IPC est bien sûr un avantage : j’ai une bonne connaissance des défis qu’implique l’Ultra HDI. Nos usines, notamment celles présentes en Chine, sont déjà pleinement engagées dans le développement de leurs capacités et nous espérons qu’elles commenceront à livrer des cartes Ultra HDI en 2023.
Les Cahiers : Les usines de PCB qui se lancent dans la fabrication de cartes Ultra HDI doivent répondre à des exigences plus strictes en matière d’équipement et d’environnement de production. Lesquelles ? Jan Pedersen : Voici les principaux impératifs : - un équipement LDI de pointe, - un environnement extrêmement propre, - des tests plus approfondis, - un équipement AOI de dernière génération, - un équipement pour la métallisation du cuivre de dernière génération, - la maîtrise des nouvelles méthodes telles que le mSAP, - l’utilisation de nouveaux matériaux plus propres et plus homogènes.
Les Cahiers : Comment avez-vous organisé la phase actuelle de mise en œuvre des moyens de production adaptés à cette nouvelle technologie ? Jan Pedersen : Je dirige le conseil technique interne de NCAB qui réunit 60 techniciens. À l’intérieur de ce conseil, treize groupes de réflexion plus petits ont été créés afin d’acquérir un savoir spécialisé dans différentes technologies pour répondre aux besoins variés de l’industrie. L’un de ces groupes est dédié à l’Ultra HDI qui collabore actuellement avec les usines de PCB de NCAB pour leur permettre de répondre aux besoins de miniaturisation.
Deux autres groupes interviennent sur des sujets exprimés par nos clients. L’un d’eux rassemble et documente les questions techniques courantes que notre équipe de Factory Management reçoit des usines de PCB avec lesquelles nous collaborons. Les questions concernent généralement des sujets tels que des conceptions que les usines ont jugé inadaptées à la fabrication. Actuellement nous compilons toutes ces données dans un document de formation pour permettre à nos clients, à nos usines et à nous-mêmes chez NCAB d’en tirer des enseignements. Côté fournisseurs, il peut nous aider à mieux gérer des problèmes de toutes sortes.
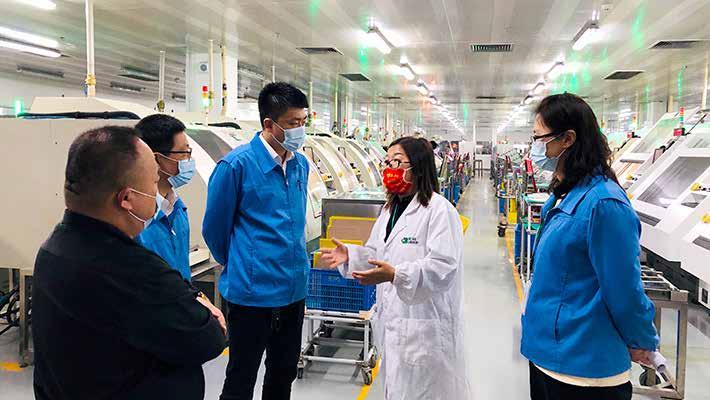
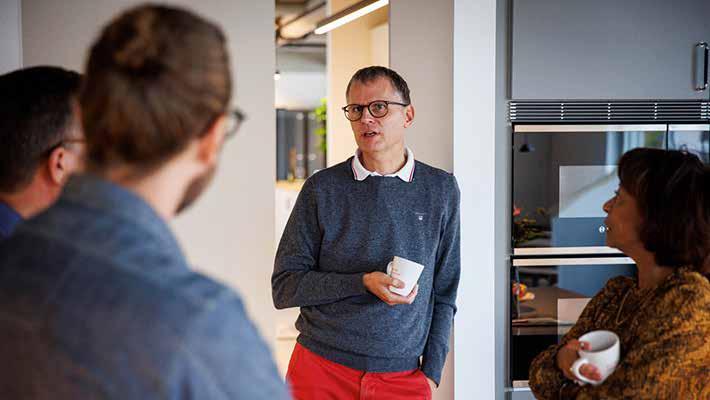
Bengt Boström, PCB Engineer, et Luisa Lindstrand, Quality Manager, tous deux de NCAB Suède, font partie du conseil technique interne de NCAB, qui réunit tous les techniciens de l’organisation..
Le second groupe de discussion, récemment créé, concentre ses efforts sur le développement durable. Ce groupe examine dans quelle mesure il est possible de calculer l’impact des différentes technologies et des procédés liés à la fabrication de PCB sur l’environnement. Le développement durable est très important pour NCAB. Nous aidons nos clients à prendre des décisions informées qui incluent également une dimension environnementale. Par exemple, nous pouvons expliquer à un client l’impact du passage d’une carte de 6 à 12 couches. Nous sommes aujourd’hui à la recherche de méthodes pour quantifier et rendre mesurable ce type de facteurs, ce qui serait totalement inédit dans le secteur.
NCAB GROUP Carol OUCHAKOFF +33(0)2 18 20 01 41 carol.ouchakoff@ncabgroup.com www.ncabgroup.com
M12 PINCE CAGE
Connecteurs mâle ou femelle à confectionner Versions droites ou coudées 4 et 5 contacts Coding A, B & D Blindé ou non blindé
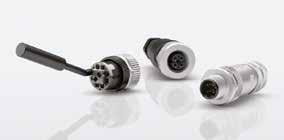

www.binder-connector.fr
SIPLACE SX d’ASMPT : comment répondre aux problèmes de la fabrication HighMix ?
Le traitement de composants de grande taille dans le cadre du procédé de Pick & Place pose des exigences élevées aux machines de placement. Des solutions performantes, extrêmement précises et flexibles sont requises.
De nombreuses applications nécessitent le placement de composants de grande taille, y compris de composants de forme irrégulière (Odd Shaped ou OSC) et de composants THT. Cela peut constituer un défi, en particulier pour les fabricants qui ont un mix élevé de produits dans des volumes réduits : des composants inhabituels, des situations de demande fluctuantes, des changements fréquents de produits, des tailles de lots modifiées à court terme – de nombreuses productions et lignes de CMS ont du mal à réagir à ces situations sans perte grave de productivité. Avec la machine de placement SIPLACE SX, le leader technologique ASMPT offre des réponses aux problèmes de la fabrication HighMix avec un large éventail de composants : les changements de portiques sur la SX, uniques en leur genre, permettent de faire évoluer la capacité de placement des machines et des lignes. Des têtes de placement innovantes et de nombreuses options permettent de placer de manière fiable des modules complexes et des composants spéciaux.
Alimentations pour tous types de composants
Les premiers obstacles dans le traitement de composants plus grands ou même OSC apparaissent souvent dès l’alimentation : en raison de leur forme, de leur taille ou de leur poids, les formes irrégulières ou Odd Shapes ne peuvent souvent pas être convoyées de manière classique et nécessitent des solutions spécifiques pour leur alimentation. ASMPT propose déjà une très large gamme de feeder, mais avec la SIPLACE SX, elle s’ouvre délibérément aux fournisseurs tiers de solutions spéciales. Avec le « Feeder Development Kit » (FDK), ces spécialistes reçoivent toutes les informations d’interface nécessaires et le savoir-faire technique indispensable pour intégrer de manière complète leurs propres solutions d’alimentation spéciales dans la SIPLACE SX.
les changements de portiques sur la SX, uniques en leur genre, permettent de faire évoluer la capacité de placement des machines et des lignes. Des têtes de placement innovantes et de nombreuses options permettent de placer de manière fiable des modules complexes et des composants spéciaux.
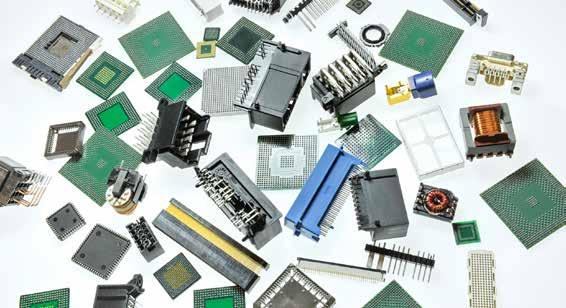
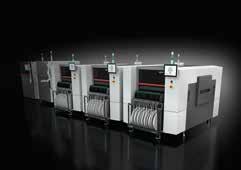
La dernière génération de la SIPLACE SX est le résultat de 35 ans d’expérience dans l’assemblage CMS automatisé. Elle allie flexibilité et performance maximales pour toutes les tâches de Pick & Place .
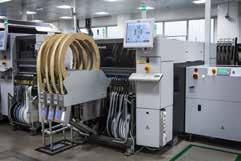
Le Feeder Development Kit d’ASMPT met à disposition des fournisseurs tiers toutes les informations sur les interfaces et l’assistance technique nécessaires à l’intégration de leurs solutions spéciales dans les machines de placement d’ASMPT. (photo : SEMO)
Des concepts de têtes de placement innovants
ASMPT a réussi à couvrir la gamme de composants pertinents pour l’assemblage CMS avec seulement trois têtes de placement différentes : il s’agit de la tête de placement Collect&Place SIPLACE SpeedStar CP20P2 pour les vitesses les plus élevées, de la tête multitalent SIPLACE MultiStar CPP et de la tête Pick&Place extrêmement précise SIPLACE TwinStar.
Dans sa dernière génération, la tête de placement haute performance CP20P2 à 20 segments augmente les performances de placement par tête à plus de 43 000 composants/heure. La tête CPP offre aux utilisateurs la plus grande flexibilité d’utilisation possible, elle combine le placement à grande vitesse en tête de ligne avec le placement en fin de ligne. La tête de placement unique en son genre maîtrise pour cela trois modes de placement différents : le mode rapide Collect&Place, le mode haute précision Pick&Place et un mode combiné. L’avantage en ligne : il est ainsi possible de prendre en charge d’un seul coup un large éventail de composants aux caractéristiques différentes et de les assembler dans le mode le plus approprié. La gamme de composants de la CPP s’étend de 01005 à 50 x 40 millimètres et 15,5 millimètres de hauteur, avec une force de placement allant jusqu’à 15 Newton. Par ailleurs, une reconnaissance automatique des broches est disponible. La capacité de placement de référence, qui peut atteindre 23 000 composants par heure, montre que la flexibilité ne doit pas se faire au détriment des capacités de placement.
Ce multitalent offre de très grands avantages en termes de productivité, car la CPP équilibre ainsi automatiquement les lignes lors des changements de produits : en mode Collect&Place, elle peut prendre en charge le traitement rapide de petits composants, en mode mixte, elle peut équiper rapidement des composants de taille moyenne ou en mode Pick & Place, elle peut décharger le placement en fin de ligne de composants plus grands – dans de nombreuses applications, le goulot d’étranglement pour le rendement et la productivité. Le logiciel change les modes de placement sur la CPP de manière entièrement automatique.
Pour l’utilisation « Heavy Duty » en fin de ligne CMS, la SIPLACE TwinStar traite des composants de la taille 0201 jusqu’à des dimensions de 200 x 125 millimètres, une hauteur allant jusqu’à 50 millimètres et un poids allant jusqu’à 240 grammes. La précision de placement est de 22 µm à 3 σ. Dans la variante « Very High Force », elle offre une force de placement allant jusqu’à 100 Newton. Une force suffisante pour enfoncer de manière fiable les connecteurs les plus exigeants dans une carte. Avec des milliers de pipettes et environ 120 pinces standard, la tête de placement couvre déjà un énorme éventail d’OSC courantes. Pour les composants spéciaux individuels, le Multi Gripper Kit (kit de préhension multiple) d’ASMPT permet de composer soi-même des variantes individuelles en nombre presque illimité. L’assemblage s’effectue en quelques minutes. Les fabricants à la commande sont ainsi équipés pour toutes les commandes urgentes.
Une ligne flexible, peu d’efforts
Les portiques de changement SX sont uniques dans le secteur et constituent la caractéristique principale de la SIPLACE SX. Ils peuvent être montés et démontés avec la tête de placement en seulement 30 minutes environ, ce qui permet une mise à l’échelle extrêmement rapide et simple de la capacité de placement. Dans de nombreuses productions, il est ainsi intéressant d’adapter la capacité de placement des lignes en fonction des besoins. Chariots portiques, connexions, auto-calibrage, mémoire de configuration, adaptation automatique des programmes de placement et outils pour la transformation – sur les changements de portiques dans le concept ASMPT de « Capacity on Demand » (Capacité à la demande), tout est conçu pour des changements rapides. La performance des lignes est ainsi adaptée de manière flexible à la demande et les configurations rigides sont évitées : la capacité d’une machine de placement peut être rapidement doublée via un portique ou les configurations des lignes peuvent être modifiées sans trop d’effort lors d’un changement de produit. De plus, en cas de pics de commandes et de surcharge d’une ligne, une autre ligne moins fréquentée peut rapidement « dépanner » avec un ou plusieurs portiques. À titre de comparaison : sur les machines d’autres fabricants, les nouvelles configurations et les changements de têtes de placement sur la ligne peuvent nécessiter plusieurs heures de travail.
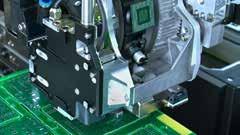
La SIPLACE MultiStar CPP maîtrise aussi bien le mode Collect&Place que le mode Pick&Place et peut même placer des composants dans les deux modes en même temps, ce qui augmente non seulement la vitesse globale, mais contribue aussi à un équilibrage de ligne nettement amélioré. (photo : ASMPT) La SIPLACE TwinStar pour le placement en fin de ligne se caractérise par une précision et une force de placement maximales pour les composants de grande taille. Elle maîtrise même les formes de construction les plus exotiques. (photo : ASMPT)
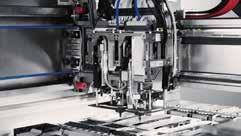
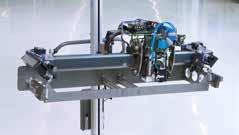
Les portiques de changement SIPLACE SX permettent de remplacer facilement les têtes de placement en seulement 30 minutes environ. Cela permet d’obtenir un équilibrage des lignes nettement plus important et des vitesses de ligne plus élevées, même lorsqu’une grande quantité d’OSC doit être traitée (photo : ASMPT)
Avec l’outil de clinchage passif, ASMPT amène directement sur la ligne un processus de transformation qui serait autrement très coûteux. L’avantage pour les utilisateurs : plus de machines spéciales coûteuses, plus de processus spéciaux et plus de perte de temps dans l’assemblage THT. (photo : ASMPT) Le SIPLACE Glue Feeder se prépare simplement comme un feeder standard, mais sert à placer des points de colle sans contact aux endroits prévus à cet effet. (photo : ASMPT)
THT et clinchage
Le clinchage des composants THT fait partie des processus les plus complexes dans le traitement des circuits imprimés et est souvent externalisé, en tant qu’étape de fabrication à part entière, sur des machines spéciales coûteuses. Cela augmente la charge de travail, les coûts et occupe un espace précieux dans les ateliers.
Avec le développement d’un outil de clinchage adaptable pour la SIPLACE SX, ASMPT intègre désormais le processus de clinchage directement dans la ligne de CMS. Le grand avantage : si nécessaire, le système est simplement intégré dans la machine de placement et fait ainsi directement partie du processus de traitement. ASMPT mise sur le procédé passif avec un dispositif de levage et des plaques interchangeables spécifiques aux circuits imprimés, qui contiennent tous les boulons de clinchage nécessaires pour le pliage des leads. Comme tous les boulons sont levés en même temps, les composants comportant de nombreux leads peuvent être clinchés en une seule opération, ce qui représente un gain de temps considérable. La structure permet un montage et un démontage simples et rapides et rend par ailleurs l’outil robuste et nécessitant peu d’entretien.
Manipulation optimisée pour le processus Pick&Place : paquet OSC
Le système de vision optimisé joue un rôle décisif dans la flexibilité encore accrue de la nouvelle SIPLACE SX. Ainsi, ASMPT propose à ses clients un paquet OSC spécial pour pouvoir placer de manière fiable des snap-ins, des composants radiaux, axiaux et autres composants exigeants. Au lieu d’une seule prise de vue, le système de vision effectue ici deux prises de vue des composants. Des algorithmes puissants calculent une image tridimensionnelle du composant qui, outre la forme, permet de bien voir les broches, les billes et les éléments de connexion. Des assistants logiciels différenciés selon les types de composants aident à définir les paramètres d’exposition spécifiques aux composants pour ces mesures stéréo. L’alignement correct peut être déterminé de manière plus fiable et les erreurs telles que les broches, les billes et les connecteurs manquants ou déformés peuvent être détectées. Autres fonctions du paquet OSC : les réglages supplémentaires de la force de placement et la vitesse de déplacement de la tête de placement sont automatiquement adaptés au composant, l’ancrage correct des snap-ins est vérifié et, pour les processus Pin-in-Paste, la hauteur de la pâte est contrôlée. La somme de ces fonctions augmente considérablement la fiabilité lors du placement. Les processus OSC perdent en risques et les revenus des fabricants de composants électroniques augmentent.
Grâce au système de vision, la SIPLACE SX détecte également les déformations du circuit imprimé (Warpage) et adapte le placement en conséquence. Il est ainsi possible de travailler avec précision même sur les circuits imprimés bombés. Des capteurs de force de placement sur les pipettes garantissent par ailleurs que chaque composant est placé avec la force de placement optimale ou sans aucun contact (touchless).
Encore plus de possibilités
L’équipement optionnel d’ASMPT permet aux fabricants de composants électroniques d’intégrer d’autres étapes de traitement dans leurs lignes de production. S’il s’agit de processus qui ne sont pas nécessaires pour chaque produit ou qui sont utilisés sur différentes lignes, le but est d’obtenir un rééquipement aussi rapide et simple que possible. Ainsi, le SIPLACE Glue Feeder et le SIPLACE Measuring Feeder sont tout simplement équipés comme des feeders SIPLACE normaux. La première solution sert à appliquer sans contact de la colle pour les composants qui doivent être fixés. La deuxième solution contrôle les valeurs électriques de composants tels que les condensateurs, les résistances, les bobines ou les diodes à l’aide d’une unité de mesure CRDL.
Le module de transport d’ASMPT est une alimentation optionnelle qui permet de traiter sur la SIPLACE SX des circuits imprimés d’une taille allant jusqu’à 1 525 millimètres de long. L’adaptation de la largeur est effectuée automatiquement par la programmation dans la SIPLACE Pro.
Le bon mélange fait la différence
Avec la SIPLACE SX, ASMPT offre aux fabricants d’électronique un mélange optimal de flexibilité et de performance pour répondre aux situations de commande les plus diverses et pour pouvoir réagir à court terme aux exigences modifiées des clients. Les interfaces ouvertes permettent la communication entre les lignes, la surveillance et l’échange de données avec l’Integrated Smart Factory.
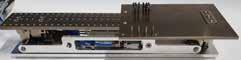
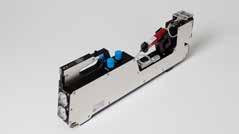
ASM Assembly Systems Mickael LANFANT +33(0)6 73 68 07 67 mickael.lanfant@asmpt.com Stéphane BROCHU +33(0)6 11 92 17 56 stephane.brochu@asmpt.com www.asm-smt.com
De toutes tailles et pour tous les ma-
tériaux : Prisme Technologies conçoit des machines d’usinage adaptées aux besoins des petites entreprises
Par Jeanne BIGOT, reporter
Permettre aux artisans, aux starts-ups, aux PME, et même aux étudiants de fabriquer des pièces avec une précision et une rapidité professionnelle, sans casser la tirelire. Cette ambition, portée par Guillaume Gourdin, fondateur de Prisme Technologies, s’avère porteuse : en seulement un an, 20 machines d’usinage ont été vendues.
C’est dans un petit atelier parisien que Guillaume Gourdin, 29 ans, s’est lancé dans l’assemblage de machines d’usinage. Un pari risqué pour le jeune entrepreneur, mais qui a rapidement payé : alors que Prisme Technologies n’a pas un an, une vingtaine de machines ont déjà été vendues. Les premiers clients de Guillaume Gourdin ne sont pas les industriels, mais des petites structures, du fablab aux entreprises : « J’ai développé une machine de 3,5 mètres par 2 mètres pour le principal partenaire pour l’agencement et la menuiserie des salles Arkoze, qui se charge de tout l’agencement bois des salles en Europe. Le fait d’avoir une machine à commande numérique lui permet de faire des tâches répétitives avec une précision inégalable à la main. » Menuisiers, artistes, PME ou encore écoles d’ingénieurs… Une clientèle privilégiée pour le chef d’entreprise, qui regrette la rivalité qui peut régner dans le monde des grandes entreprises. « Je suis porté par cet écosystème, c’est très réconfortant. J’ai la sensation que c’est exactement là où je devrais être. » Aujourd’hui, l’entrepreneur propose un catalogue de machines d’usinage, de la modélisation à la fabrication adaptée à tous types de matériaux, tels que le bois, les plastiques, le cuivre, le laiton ou l’aluminium.
Entre sur mesure et R&D
En parallèle de ce catalogue déjà bien fourni, Guillaume Gourdin propose des services sur-mesure, selon les besoins de ses clients : « Chaque secteur a ses exigences, ses particularités. Je maîtrise la mécanique, l’électronique, le logiciel, et j’ai une philosophie autour de la modularité : je peux donc proposer une très grande gamme, sans avoir à redesigner toutes les pièces ». Prisme Technologies joue notamment la carte de la taille : de la petite machine, abordable et tenant
Chaque secteur a ses exigences, ses particularités. Je maîtrise la mécanique, l’électronique, le logiciel, et j’ai une philosophie autour de la modularité : je peux donc proposer une très grande gamme, sans avoir à redesigner toutes les pièces.
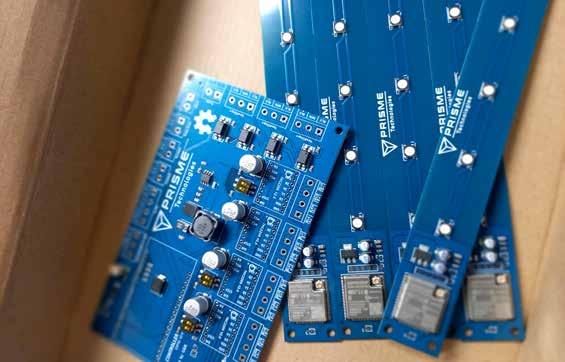
sur un bureau, à la fraiseuse XXL, de plusieurs mètres, telles que celles conçues pour la menuiserie. Cette modularité, le chef d’entreprise la puise aussi et surtout dans sa passion pour la R&D. Alors que plusieurs machines sont en cours de fabrication dans son atelier, des exclusivités voient doucement le jour. « Je fais toute ma R&D moi-même, et je suis actuellement en train de concevoir la version 2 des machines que j’ai déjà développées. » Plus puissante, plus rigide, cette nouvelle version de fraiseuses devrait dépasser les capacités déjà reconnues de la première. En parallèle, le passionné s’intéresse à la conception d’une machine dite de pick and place : « La machine place les composants sur la carte électronique, puis un passage dans un four permet de les souder. Cela permettra de disposer d’un outil abordable, rapide et efficace pour du placement de composant, grâce à la communauté open source. » D’autre part, le logiciel associé n’est pas à concevoir car c’est en open source, c’est juste que c’est très très complexe. « Je pousse toujours plus loin. Chaque fois que je passe une marche je vois qu’il y en a encore pleins d’autres ! Alors j’apprends, et ensuite je développe ! » se réjouit Guillaume Gourdin.
Combiner made in France, prix et approvisionnement
Alors que l’intégralité des clients de Prisme Technologies sont aujourd’hui français, l’entrepreneur met un point d’honneur à s’approvisionner au maximum en France. Les châssis des machines, en acier ou en aluminium, sont français. De même pour la peinture, produite en Ile-de-France. C’est lorsqu’il s’agit des composants électroniques que les choses deviennent plus compliquées : « Je n’ai aujourd’hui pas trouvé de fournisseurs aussi rapides, aussi abordables et avec un catalogue aussi large que la Chine… J’ai vu passer une entreprise qui propose des cartes électroniques, qui me coûterait hélas 50 fois plus cher que ce que je paie actuellement pour la même chose. » regrette Guillaume Gourdin. Autre écueil dans le choix de ses matières premières : les pénuries, qui ont évidemment lourdement touché Prisme Technologies. D’une part, les coûts de matières premières ont explosé de 30% selon l’entrepreneur, notamment à la suite de la guerre en Ukraine. En ce qui concerne les composants électroniques, ce dernier a observé une nette augmentation des frais de livraisons : « Les transporteurs ont explosé en termes de tarifs. Nous avons trouvé des solutions. Par exemple, pour notre microcontrôleur, la puce coûtait 10 fois plus cher qu’en temps normal. Nous nous sommes donc tournés vers des systèmes déjà montés, le temps que la crise passe. » explique Guillaume Gourdin. Pour mieux faire face à ce type de pénurie mais pas que, ce dernier s’engage en faveur de la réindustrialisation de la France, notamment via l’association Hardware France, qu’il a co-fondé avec Stéphane Elkon, expert en règlementation et en affaires publiques dans le domaine de l’électronique. Objectif de cette association, créée en 2021, fédérer les acteurs de l’électronique, afin de redynamiser la filière, tout en la représentant auprès des pouvoirs publics. « Nous sommes très complémentaires avec Stéphane : lui a travaillé avec des grands groupes et s’intéresse beaucoup à la réglementation. Moi je suis sur le terrain, je développe mes solutions, je suis confronté à la R&D, au suivi qualité, etc. »
Un emploi du temps à rallonge
Entrepreneur passionné et engagé, Guillaume Gourdin a de multiples casquettes, sans compter qu’il agit également en tant que prestataire pour certaines entreprises, via la société Prisme Studio, qu’il a créée un an avant Prisme Technologies. « Je fais de la modélisation 3D, du design de carte électronique, de l’usinage, du moulage… » liste le chef d’entreprises. Un accompagnement complet, « de la feuille blanche à la commercialisation » dédiée notamment aux jeunes entreprises qui n’ont ni les moyens ni les compétences pour investir dans une machine d’usinage. « J’ai effectivement pas mal de travail, entre l’assemblage des machines, la R&D, Hardware France et cette partie un peu conseil » admet Guillaume Gourdin. Pour l’accompagner dans ses journées à rallonge, un salarié a rejoint l’équipe de Prisme Studio et Prisme Technologies : un ingénieur en microélectronique, dont les compétences complémentaires à celles du chef d’entreprise lui ont permis d’apprendre encore plus. « À deux, nous pouvons tout faire. Répondre aux besoins des clients en matière de design, d’intégration… » fait-il valoir. Cette success story, Guillaume Gourdin s’en félicite aujourd’hui. Pourtant il se souvient des moments plus difficiles par lesquels il a dû passer. Notamment par une startup nommée Le Pavé parisien, qui fabriquait des enceintes en béton. Un projet qui a eu le vent en poupe, mais qui selon l’entrepreneur, ne répondait pas suffisamment à un besoin : « Cette question du besoin des consommateurs pour créer une start-up est primordiale, sinon, on va passer plus de temps à emballer les produits qu’à les vendre… » Puis il fonde Prisme Studio et ensuite Prisme technologies et le besoin, Guillaume Gourdin n’a pas besoin de le créer chez ses clients actuels, qui voient dans les machines Prisme Technologies une manière de gagner du temps mais aussi de la précision. L’entrepreneur n’a ainsi jamais fait appel à la publicité pour se faire connaître car le bouche à oreilles lui suffit.
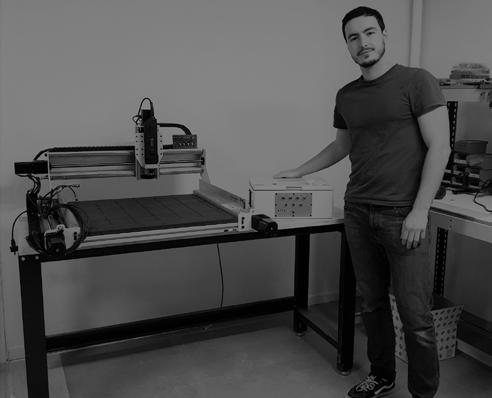
PRISME TECHNOLOGIES Guillaume GOURDIN g.prisme.paris@gmail.com www.prisme-technologies.fr
Yamaha fournit ses équipements CMS
Le sous-traitant néerlandais choisit les systèmes de sérigraphie, de placement et d’inspection de Yamaha pour améliorer la qualité, la flexibilité et la productivité.
La section CMS de Yamaha Motor Europe fournit à Faber Electronics ses équipements à grande vitesse pour deux lignes de montage en surface destinées à fabriquer des produits de haute technologie, notamment des équipements pour l’IoT, de l’électronique automobile, des dispositifs médicaux et des commandes industrielles.
Faber Electronics, prestataire néerlandais de services de fabrication électronique, a installé une machine de sérigraphie YCP10, deux machines de placement à grande vitesse YSM20R et un système AOI YSi-V pour l’inspection visuelle de fin de ligne.
« Nos clients travaillent sur des marchés qui exigent une fiabilité extrême des produits. Dès lors, un assemblage irréprochable à grande vitesse est une condition sine qua non », explique Tijmen Augustijn, directeur des opérations. « D’un autre côté, nous tenons à conserver notre flexibilité pour nous adapter rapidement à l’évolution de leurs besoins. Nous comptons sur nos partenaires technologiques et nos fournisseurs pour nous aider à satisfaire ces exigences. C’est dans cette optique que nous avons décidé de renforcer notre collaboration avec Yamaha en investissant dans de nouveaux équipements de la 1 STOP SMART SOLUTION. »
Nos clients comptent sur notre capacité permanente à répondre rapidement à leurs besoins. Les fonctions avancées et la facilité d’utilisation de nos lignes de montage en surface Yamaha contribuent à entretenir cette réputation; Nous sommes capables de gérer aussi bien des modifications de conception de dernière minute que des changements de produits fréquents, et ce, de manière rapide et efficace.

Marc Valk, ingénieur assurance qualité chez Faber Electronics
Les équipes d’ingénieurs de Faber Electronics ont constaté que la conception pour la fabrication et l’assemblage (DfM) et la conception en vue du test (DfT) permettent de gagner en fiabilité. Généralement, les circuits de toutes les cartes produites, ou presque, sont testés en fonction des attentes de chaque client. Le système AOI YSi-V présent sur chacune des lignes d’assemblage facilite l’assurance qualité et améliore la productivité en identifiant rapidement toute carte présentant des défauts visibles.
L’YSi-V de Yamaha
L’éclairage multi-angles et multi-longueurs d’ondes de l’YSi-V permet au système de repérer les défauts difficiles à voir à la lumière habituelle et empêche les ombres d’obscurcir certaines zones d’inspection. En outre, la mesure de la hauteur au laser permet de détecter les problèmes de coplanarité liés à des pattes de composants endommagées ou à un défaut de brasure. Ce système est le complément idéal de la machine de sérigraphie compacte YCP10, dotée de fonctions avancées et capable de traiter des cartes de grandes dimensions, ou encore de la machine de placement YSM20R haute efficacité, dont la capacité de placement atteint les 95 000 composants/heure. « Nos clients comptent sur notre capacité permanente à répondre rapidement à leurs besoins. Les fonctions avancées et la facilité d’utilisation de nos lignes de montage en surface Yamaha contribuent à entretenir cette réputation. Nous sommes capables de gérer aussi bien des modifications de conception de dernière minute que des changements de produits fréquents, et ce, de manière rapide et efficace », souligne Marc Valk, ingénieur assurance qualité chez Faber Electronics.
Pour Theo Loohuis, directeur des services d’Europe-SMT, distributeur de Yamaha pour le Benelux, la combinaison de la machine de sérigraphie YCP10, des machines de placement YSM20R et de l’AOI YSi-V sur chaque ligne offre des capacités avancées qui ne manqueront pas de répondre aux besoins de Faber Electronics pendant bien des années encore. « Toutes les lignes peuvent sérigraphier, placer et inspecter à grande vitesse des éléments variés, des plus petites puces CMS aux circuits intégrés de grande taille comme les circuits logiques programmables, en passant par les composants de grande taille comme les condensateurs et les connecteurs. Nous avons écouté l’équipe pour comprendre ses besoins et ses projets pour l’avenir. Nous avons ensuite travaillé avec Yamaha pour proposer les meilleurs équipements en réponse à ces besoins. Chaque ligne allie une qualité de production élevée et la flexibilité nécessaire pour répondre aux demandes diverses et changeantes des clients. »
Et Daisuke Yoshihara, directeur général des ventes de la section CMS de Yamaha Motor Europe, de conclure : « Faber Electronics dispose désormais de deux lignes CMS complètes, parfaitement adaptées aux demandes de ses clients, et qui lui garantissent un avantage concurrentiel certain et un retour sur investissement pérenne ». Rendez-vous sur le site https://smt. yamaha-motor-im.de/ En savoir plus sur Europe-SMT : www. europe-smt.com En savoir plus sur Faber Electronics : https://faber-electronics.nl/over-ons
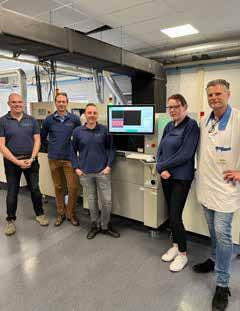
L’équipe de Faber Electronics
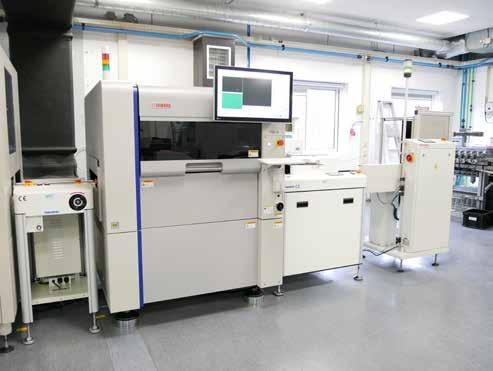