
50 minute read
NEWS
Batek Makina takes over Bertola
Batek Makina, the Turkish battery equipment manufacturer, signed the final take-over documents for its acquisition of Italian formation firm Bertola and its subsidiary Moran on January 14.
“We had negotiated most of the deal about a year and a half ago,” says Celal Saricam, managing director and cofounder of Batek.
“But the pandemic has delayed our earlier plans until now.”
The immediate aim will be to ship Bertola equipment from its operations in Milan to Batek’s new plant in Dilovasi, Kocaeli. All existing users of Bertola and Moran equipment will be served by Batek from now on.
Saricam says the formation side of the business should be ready to start in March.
The acquisition of Bertola is a bold initiative by Batek in that the formation business is very different from other sectors of battery machine manufacturing. Only a couple of firms, such as Sovema, include formation equipment as part of their wider product offering.
“One of our objectives through this was to invest in our core business in a distinct way that would basically ensure vertical growth while bringing some aspects of diversification,” Saricam told Batteries International.
“Bertola definitely fits our agenda of investing in this fashion as the battery formation business typically is a separate branch of technology.
“We hope to revitalize the legacy of Bertola — one of the best known names in the formation business— and the Moran brands,” he says.
Bertola is one of the oldest firms in the battery charging equipment industry. Its formation business was founded in 1958 in Italy, where it developed several technologies that eclipsed others in the industry such as IGBT-based battery formation rectifiers.
Bertola is a family-owned business and one of the reasons for the sale was the difficulty of passing on the company to the next generation. A previous sale of the business fell through a couple of years ago. For the past year the firm has been winding itself down, but its key staff will be on hand to pass the business on smoothly.
Bertola acquired Moran, another pioneer in the battery formation and testing equipment industry, in 2008.
Saricam says the technologies incorporated by this acquisition will include battery formation systems for both automotive and industrial applications, battery testing systems and software development for battery charging.
Saricam sees the acquisition in a larger fashion.
“The pandemic has disrupted traditional supply chains and deglobalization is occurring,” he says.
“Our ability to service another part of the battery manufacturing industry can only be an asset in these troubled times.
The new plant in the port town of Dilovasi — about 70 kilometres from Istanbul — is the third new manufacturing facility Batek Makina has had since it was founded in 2003.
“Our new state of the art plant is double the size of the previous one,” says Saricam. “Not only will it offer us vast capabilities in building more of our existing machinery — and possibly developing new machinery — but it also motivates us to strive to continue to provide excellence.
“For us, understanding the specific conditions and needs of battery manufacturers is a key to being able to deliver successful projects.
“Despite megatrends in the industry that favour standardization of products and common procedures, the reality on the factory floor is that we need to build in design flexibility and offer a variety of production methods.”

California DTSC issues writ to recover Vernon clean-up costs following October report
The California Department of Toxic Substances Control on December 14 filed a sweeping court action against major battery firms for the cost of the clean-up of the former Exide Technologies lead battery recycling site at Vernon.
Clarios, Trojan Battery and Quemetco are among the defendants listed in the writ filed in the Central District of California district court, which claims reimbursement for the DTSC’s costs in investigating and cleaning up the costs involved in the contamination.
It also calls on the defendants to complete the remaining work, most of which, it says, has been left ‘unremediated’.
In May last year, Exide’s North American side of the business entered Chapter 11 bankruptcy for the third and final time, and the ensuing bankruptcy ruling effectively allowed Exide to walk away from any responsibility to close and clean the site.
In July Atlas Holdings bought the North American business and set up two standalone companies — Stryten Manufacturing and Element Resources — to make and recycle lead batteries.
Exide CEO Tim Vargo was appointed CEO of the new Stryten alongside Mike Judd, former president and COO of Exide.
Element Resources was set up to own and operate recycling plants in Canon Hollow, Missouri and Muncie.
A Stipulation and Order in 2014 had required Exide to provide financial assurance for its post-closure plan and undertake ‘extensive onsite corrective action’, as well as provide interim measures for residential off-site action.
“Exide filed a bankruptcy petition on May 19, 2020, and the implementation of these measures, and of the off-site corrective action, has not been completed,” the court document says.
Over the objections of state and local officials, Bankruptcy Judge Christopher Sontchi in Delaware approved a bankruptcy settlement on October 16 allowing Exide Technologies to abandon its former battery-recycling plant in Vernon, leaving the state and taxpayers on the hook to pay for continued environmental clean-up of the site.
The writ says that Exide transferred the title of the Vernon Plant to the Exide Vernon Environmental Response Trust on October 26, 2020, which was required to continue implementing closure activities and corrective action — “but the trustee has insufficient resources to complete these actions”.
Other parties named on the document as responsible for contamination as previous owners in some way are NL Industries, Gould Electronics and JX Nippon Mining and Metals.
Kinsbursky Brothers, Ramcar Batteries, International Metals Ekco and Blount, or their corporate predecessors, are named along with Clarios, Trojan and Quemetco as transporting ‘the majority of the hazardous substances that were disposed of or treated at the Vernon facility in the last approximately years of the facility’s operation’.
“These parties share the responsibility for the contamination plaguing the thousands of people and families who live and work in the shadow of this site,” said DTSC director Meredith Williams.
Separately, the DTSC responded on October 27 to a damning report by the state auditor on the management of the residential clean-up around the shuttered Exide Vernon lead battery recycling site.
The State’s Poor Management of the Exide Clean-up Project Has Left Californians at Continued Risk of Lead Poisoning report, number 2020-107, makes a number of criticisms about the cleaning operation. These include the fact that despite early identification of 50 contaminated properties, including schools and childcare centres, after five years 31 of them have still not been cleaned by the DTSC.
“In fact, it has cleaned only one of these properties since May 2018,” says the report. “In addition, DTSC has been unable to maintain the clean-up pace it presented in its 2017 plan for cleaning the most contaminated properties.
“As a result, it is significantly behind schedule and is unlikely to meet its goal to clean the 3,200 most contaminated properties by June 2021 — extending the time that residents in the clean-up site are exposed to dangerous levels of lead.”
It says the DTSC has not set a timeline for cleaning an estimated 4,600 properties that still have dangerous levels of contamination.
The cost, which has been left to the state to cover since Exide Technologies was sold off in July, has ballooned, the report says — and likely to be in the region of $650 million in total, far more than the $251 million that had already been provided to the DTSC by the state.
“DTSC’s estimates of per-property clean-up costs were inaccurate because it failed to account for predictable costs, such as inflation and payment of legally required prevailing wages,” the report says.
“Finally, DTSC has paid about $17 million more than it anticipated to clean 768 properties because it did not establish adequate protections in its agreement with its largest clean-up contractor.”
In response, the DTSC said it was conducting clean-ups at a faster rate and with more stringent standards than other residential lead clean-ups across the nation.
“To date, DTSC has cleaned up more than 2,000 properties with the highest levels of lead and is on pace to complete more than 90% of the clean-ups planned,” it said.
The DTSC also pledged to implement all of the state auditor’s recommendations, including cleaning up childcare centres, parks and schools, deploying resources to the most contaminated properties and setting a deadline of April 2021 for identifying the date by which all works are completed.
Welcoming the next
The international battery separator firm is celebrating 90 years of its existence. Chad Schuchmann, Daramic President, looks back over the firm’s history and explains why its separators have been at the core of battery manufacturing innovation since 1930.

— Chad Schuchmann, President

Owensboro, Kentucky, 1930: history being made as ground is being broken on the first rubber separator plant in the world. US Patent 1,745,657 awarded on February 4, 1930 might have seemed just another day in the convoluted workings of the US Patent Office. But it was to be a key date in the development of the battery industry.
It was also to result in the creation of the international battery separator giant, Daramic.
The reason is simple. Herman Beckmann, a German academic completing his research to become an associate professor at AFA in Berlin had formulated a better type of separator made of a microporous rubber.
The idea itself wasn’t new. Talk about rubber as a battery separator dates back to a patent issued in 1904. But this was a separator recipe that worked.
Two astute ex-US army businessmen —Bradley Dewey, a former colonel, and Charles Almy, an ex-lieutenant colonel — by all accounts had followed Beckmann’s work with interest. The two had founded specialist chemical firm Dewey & Almy just after the close of the first world war. To them a rubber separator was a clean step away from traditional ones that used such natural products such as cedar wood.
The result was that late in 1930 Dewey & Almy broke ground on the first rubber separator plant in the world.
One of the interesting facts of Daramic has been the emphasis on turning theory into practice. A quick look through the patent catalogues reveals that the firm — then still in its Dewey & Almy days — had patented ribbed separators as early as 1945.
The firm Dewey & Almy was acquired by W. R. Grace & Co in 1954.
And it was with Daramic — this new division in W. R. Grace — that the next leap forward in separator development happened: the invention of the polyethylene separator in 1969. By 1972 manufacturing had begun at the Owensboro plant of the firm in Kentucky.
The breakthrough with the PE separator was as significant as that of the rubber separator. It is constructed out of ultra-high-molecular-weight polyethylene, precipitated silica, and mineral oil which yields unique separator properties because of their high mechanical strength, stability in acid, and resistance to oxidation.
The PE separator has, for the most part, become the material of choice in flooded lead-acid batteries.
Not to be forgotten in Daramic and its forebears’ long history of innovation is the invention by W. R. Grace in the 1960s of the phenolic resin separator, also called Darak which is still in use today.
Due to its high temperature stability, low electrical resistance, and very low acid displacement, Darak separators are suited for batteries with gelled electrolyte or in conventional flooded high performance batteries.
Although Daramic had shipped its separators abroad from early on, it was only in the late 1970s Daramic looked to manufacture its separators abroad. In 1980 and 1981 it set up facilities in Norderstedt, Germany and Selestat, France. It was not long before the French and German operations’ output contributed more to sales figures than the original manufacturing units in the US.
Daramic was to go through swift periods of change.
The big change over the period was to unleash the company’s creative potential — not just for technical products but for commercial acumen. Perhaps the key to its success during this time was a far-sighted move into Asia.
This started relatively quietly with the creation of a manufacturing plant in Prachinburi, Thailand and by the time Polypore and its Daramic division were sold in 2004, plans were already advanced to set up operations in Tianjin in China in 2006.
The new owners, high-tech venture capital giant, Warburg Pincus, led the way further with a two pronged attack on Asia.
The first was in customizing existing
generation of invention
products to meet the specific needs of the Asian marketplace and environment.
The second was in establishing operations in the heart of the continent. In 2007, another major step for Daramic was when Polypore with Daramic went public and listed on the New York Exchange.
The next area of growth was India, Asia’s second largest market. In April 2008 Daramic acquired Super-Tech Battery Components Pvt in Bangalore.
In India, its customer base was strong — it was a supplier to all major lead battery manufacturers in India. It also was a well known supplier to medium sized firms and a host of other small and medium sized battery manufacturers across India.
For the last decade Daramic’s expansion into the Asian marketplace has proceeded at a steady pace. In 2011 it established a plant at Xiangyang, China. That year too Daramic India relocated to a new and larger facility in Bangalore, India. By the following year its expanded manufacturing line in Prachinburi, Thailand was operational.
In 2015 the final change of ownership took place when Asahi Kasei, the Japanese chemical giant with some $20 billion annual sales, acquired Polypore International, the parent company to Daramic and its affiliates.
“Since then it’d be fair to say that the pace of innovation has even speeded up,” says Chad Schuchmann, president of Daramic since last August and previously its chief operating officer. Schuchmann has been with Polypore and its subsidiaries since 2002.
“You only have to look at our portfolio of patents — there’s well over 20 been granted since we became part of Asahi Kasei. Our approach to innovation is part of our DNA.
“Keeping the world in motion is going to be the theme of the next 10 years while at the same time it is clear that the main trend is going to be greater electrification of everything as we move away from fossil fuels,” says Schuchmann. “We aim to be at the heart of this new energy revolution and remain a key figure in taking the lead battery to levels of performance similar to that now found in lithium.
“There’s a new automotive world emerging. In the past battery development has mostly been driven by the US which has then diffused into Europe and then into Asia. Now it’s the other way about — China and Asia are setting the direction in electric vehicles and electrification which is then diffusing into Europe and then to North America.”
Interestingly development of a lot of Daramic’s latest product range — think RickLife™, HiCharge® and XCharge™ — is specific to Asian driving requirements and much of the development has come from its Asian research centre which has been relocated to Gujarat, India.
These include a reversal of imposing the standard western template on an Indian battery. So, for example, one key product in this range known as DuraLife® followed the unusual pattern of being launched in the Asian market first and then two years later, in 2016, released worldwide.
Schuchmann believes that in the automotive sector the use of enhanced 0 flooded batteries will eventually become the norm as start-stop cars become almost universally standard. Start-stop vehicles make heavy demands on the battery life due to being charged and discharged while in a PSoC (partial state of charge).
Daramic has looked at three particular areas in boosting the performance of PE separators: adjusting the separator profile; improving the separator formula; and, how additives, notably carbon, boost performance.
In a recent presentation the firm showed that the 2022 targets set by the Confederation for Battery Innovation in four different areas — cycle life when operating at a partial stage of charge @17.5 depth of discharge; dynamic charge acceptance; reduced water loss; and grid corrosion according to the J2801 life test — had been almost achieved in the summer of 2020.
Daramic has come a very long way in its first 90 years of existence. If anything the momentum for innovation has never been so high. It will be interesting to see where the firm has taken separator technology to when it celebrates its first century.
Effect of Carbon on Cycle Life and DCA VW 17.5% Partial State of Charge (PSoC) Test (1) VW DCA at 70% SOC (1) (2)
2.3 Standard SLI 3.6 Standard SLI Riptide C RipTide C* 3.2 Riptide C RipTide C* End of Discharge Voltage(V)End of Discharge Voltage (V) 1.8 1.9 2.0 2.1 2.2 Riptide C with Carbon v1 Riptide C with carbon v2 2022 CBI Target: 2000 cycles RipTide C* with Carbon v1 RipTide C* with Carbon v2 DCA (A/Ah) 0.8 1.2 1.6 2.0 2.4 2.8 Riptide C with Carbon v1 Riptide C with Carbon v2 2022 CBI Target: 2.0 A/Ah RipTide C* with Carbon v1 RipTide C* with Carbon v2
End of Life
1.7 0.4 2018 CBI Target: 0.4 A/Ah 0 200 400 600 800 1000 1200 1400 1600 1800 2000 2200 10 20 30 40 50 60 Cycle Time (sec) Cycle life improvement by 2.6x DCA improvement by 3.8x 1 - Average three cells 2 - after 510 PSoC Cycles * Daramic Proprietary Intellectual Property
Drawing closer to 2022 CBI Goals in Cycle Life and DCA
17© 2020 Daramic, LLC. ALL RIGHTS RESERVED Clearly this is drawing closer to 2022 CBI goals in terms of cycle life and DCA
Effect of special additive on water loss VW 17.5% Partial State of Charge (PSoC) Test
VW 17.5% PSoC Test 2.4 Rip Tide-C + Carbon V2 End of Discharge Voltage (V) 1.8 1.9 2 2.1 2.2 2.3 Rip Tide-C + Carbon V2+ Additive End of life 2022 CBI Target : 2000 Cycles 1465 cycles 2050 cycles Neg with electrode after PSoC Cycling RipTide C + Carbon separator 1.7 1.6 200 400 600 800 1000 1200 1400 1600 1800 2000 2200 Neg electrode after PSoC Cycling (1)data based on 2 cells each Cycle (#) with same separator + Additive 19© 2020 Daramic, LLC. ALL RIGHTS RESERVED Combination of profile (RipTide C), carbon coating and additive exceeded 2022 CBI target in terms of PSoC cyclingA combination: RipTide C™, carbon coating and additive exceed 2022 CBI target in terms of PSoC cycling
Water Loss (WL) Estimation WL estimation using Constant Overcharge for 96 hrs Battery Testing versus Cell Testing
Water Loss Estimation 40 ( Const. Overcharge for 96 hrs) 6 Battery Testing Vs Cell Testing Overcharing current 10 15 20 25 30 35 Weight Loss (g/Ah) VW 42 days of overcharging test 2 2.5 3 3.5 4 4.5 5 5.5 Standard SLI Rip Tide C Rip Tide C + Carbon V1 Rip Tide C + Carbon V2 2022 CBI target: 3g/Ah 5 Rip Tide C + Carbon V2 + Additive
( Estimated value)
1.5 5 10 15 20 25 30 35 40 45 Rip Tide-C + Carbon V2 Rip Tide-C + Carbon V2+ Additive Steady State Overcharging current (mA) Modified SAE-J537 overcharging test
RipTide C + Carbon coating + Additive can achieve < 3 g/Ah water loss
20© 2020 Daramic, LLC. ALL RIGHTS RESERVEDRipTide C™ + carbon coating + additive can achieve <3g/Ah water loss
Summary
DARAMIC’s 2 V cell test results compared to CBI targets:
Key Performance Indicators CBI 2018 ( 2019 Daramic) ( 2020 Daramic) CBI 2022
PSoC Cycle life 1500 1600 2050 2000 DCA (A/Ah) 0.4 1.7 1.7 2.0 Water Loss (g/Ah) <3 4.25 < 3 <3 Corrosion, J2801 (units) 12 -- tbd 18 Daramic has provided improvements to Enhanced Flooded Batteries by:
Modified Separator profile Effect Improvements on
- Negative Cross Ribs Acid to negative plate PSoC cycling - Serrated Ribs Prevent Active Mass Swelling PSoC cycling, DCA
Modified Formula/Additives
- Addition of Carbon In contact where PbSO4 first forms PSoC cycling, DCA (but: Issue water loss) - All above + Addition of additive Reduction of water loss Potential to Reach 2022 CBI Targets © 2020 Daramic, LLC. ALL RIGHTS RESERVED 21 Putting it all together. Daramic is already beating some CBI targets and is progressing to meet the rest
GS Yuasa to extend partnership to create UK local energy centres
Japanese lead and lithium battery maker GS Yuasa said on November 19 that it and Infinite Renewables, a UK renewable energy firm, were launching a project with Albion Community Power to integrate Yuasa’s hybrid lead/lithium battery system with renewable wind and solar power sources.
The so-called Generation Storage Consumption Supply project is being partly funded by the European Regional Development Fund, and will seek to integrate the systems in ‘local energy centres’ for various applications.
In total seven of the centres will be built in industrial areas in various parts of Wales. The first is at GS Yuasa’s factory in Ebbw Vale, Wales, where 2,900 solar panels are to be installed to provide around 5% of the factory’s power needs.
The factory makes the lead-acid batteries for the hybrid installations, and the lithium batteries are shipped in from Japan.
In June, Yuasa was hired to provide a 100kW pilot hybrid battery at the port of Portsmouth on the south coast of England.
The batteries will be connected to a rooftop solar array in an area of the port where 24-hour loading needs continuous power.
“The lead-acid battery provides the bulk of the energy storage capacity for cost-effective harvesting of renewable energy, and the lithium-ion battery provides high power discharge capability for EV fast charging,” said a spokesperson for Portsmouth International Port.
Chinese battery-making region forced to close due to new Covid-19 surge
A new surge of coronavirus cases in the Chinese province of Hebei is having an impact on lead battery makers in the region, who stopped production between January 6-9, according to news outlets such as the Shanghai Metals Market and Reuters.
The outbreak, in the provincial capital city of Shijiazhuang, has resulted in the lockdown of 11 million people in a ‘state of wartime’ imposed on January 5.
Since January 2, the province has reported 223 locally transmitted confirmed Covid-19 cases and 161 asymptomatic carriers.
“It is understood that logistics and transport services have been seriously disrupted by the lockdown in Shijiazhuang,” says the SMM. “Some companies in the metals industry have suspended production more than one month ahead of the Chinese New Year, closing their doors for an ‘early holiday’.” The Spring Festival does not begin until February 12 this year.
“It is worth noting that Shijiazhuang borders Baoding and Xingtai,” says the SMM. “Baoding is a concentrated area of lead-acid battery makers and secondary lead smelters.”
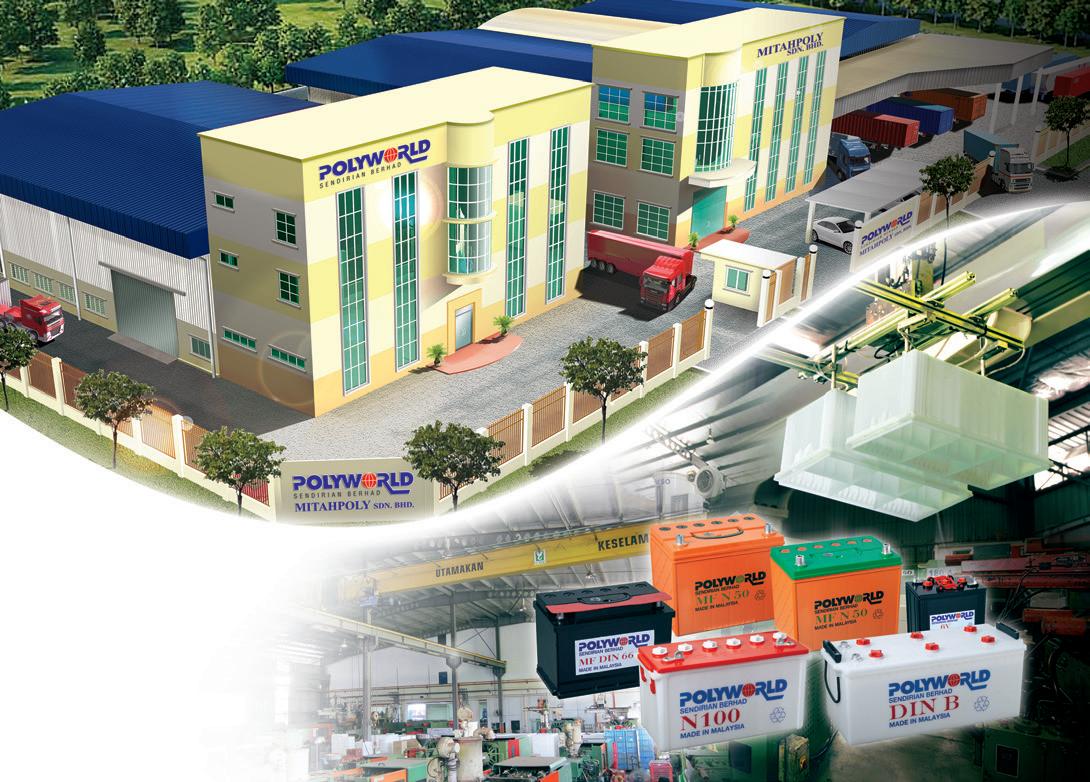
POLYWORLD SDN BHD, since 1989 designs and manufactures battery containers and covers (boxes and lids) according to JIS, DIN, and BCI standards. With innovative and unique designs,we are committed to serving clients in all regions.
New European research collaboration optimizes lead battery performance for micro-hybrid vehicles
A new European research collaboration between two leading academic institutes — the Fraunhofer Institute for Silicate Research (Fraunhofer ISC) and Wrocław University of Science and Technology (WUST) — was announced by the Consortium for Battery Innovation (CBI) in mid-October.
The two-year research project will explore the fundamental properties of carbon additives with focus on surface functional groups, and the effect they have on lead battery performance. Specifically, it will look at the impact on key performance indicators in lead batteries: • Cold cranking amperage:
The high discharge pulse
power responsible for starting a car, rated at -18 °C for 30 seconds. • Dynamic charge acceptance: The ability of a battery to accept instantaneous energy during charging. • Hydrogen evolution reaction: The side reaction occurring on a negative electrode surface, which accelerates electrolyte loss.
Studies of these three performance indicators will use screening techniques combined with tailor-made carbons to examine how carbon chemistry interacts with lead and other common additives.
Carbons are a popular additive for enhancing battery performance, and this research project is building on existing research by using innovative techniques to conduct in-depth exploration of additive effects, according to the CBI, which has coordinated the partnership.
This knowledge is essential for improving the DCA of lead batteries and increasing their uptake in start-stop, micro and mildhybrid applications, one of the fastest growing automotive markets worldwide and a vital market for delivering cleaner mobility.
Alistair Davidson, director of CBI, said: “Responding to market demand from the automotive sector, this new research project is building on collaborative workshops organized by the Consortium in partnership with OEMs and car companies over the last few years.
“It’s one of a new set of exciting projects aiming to enhance the performance of lead batteries to meet the technical requirements of start-stop and micro-hybrid vehicles.”
Gas Supply Solutions for lithium-ion battery lifecycle management

Industrial gases are indispensable component during various processes of the lithium-ion battery lifecycle. Air Products, with more than 80 years of experience, offers tailor-made gas supply solutions, from production, reuse and recycling of lithium-ion batteries.
We can help you meet your sustainability goals.
For more information please contact us at:
T +44 1270 612708 apukinfo@airproducts.com
tell me more
airproducts.com
© Air Products and Chemicals, Inc., 2020 (43539) 330-20-008-EN
Battery industry bodies react to milestone in EU new regulation
The most significant EU legislation on batteries since 2006 has been met largely with approval from the lead battery industry, which has welcomed the 158-page December 10 Batteries Regulation, even if some have warned of over regulation and complexity.
EUROBAT said it was ‘a crucial piece of legislation that will define our industry for the next 15 years’, and ILA managing director Andy Bush said the association was pleased that the proposal — which should go in force in January 2022 — included a large focus on sustainability.
Claude Chanson, general manager of the Advanced Rechargeable and Lithium Batteries Association (RECHARGE), said the legislative framework would close gaps in existing legislation and level the playing field with international actors.
The proposal identified several reasons for the new directive, including the need for batteries to participate in Europe’s ‘clean energy transition’.
It said the European Investment Bank would increase support for battery projects to more than €1 billion ($1.2 billion) within a year, and the World Economic Forum said battery production had to increase by a factor of nine to achieve a reduction in CO2 emissions.
To achieve this it was essential to address the lack of policy framework, incentives, efficiency in the single market, sub-optimal recycling processes and supply chain problems, the EU said, and this is what the proposal set out to do.
The main points include recovering increasing amounts of raw materials from all kinds of batteries; raising collection and recycling rates; providing detailed information on what each battery contains, including how much of the materials in each has been recovered; reducing the EU’s reliance on imports of materials; strengthening internal market processes and a circular economy with common rules for the single market; and reducing environmental impacts.
The amount of recovered material identified will be increased each year.
ILA response
“Advanced lead batteries — which already supply more than 70% of rechargeable battery energy storage globally — will play an increasingly important role supporting a low carbon future, which is why welcome the ambition to both enhance Europe’s battery manufacturing capability and increase the amount of batteries recycled,” said Andy Bush.
“Lead batteries are already the most recycled battery in Europe, with all batteries which are collected at the end of their life recycled in closed loop.
“Currently, 80% of a new lead battery made in Europe is made up of recycled materials collected in Europe and of course we support thousands of jobs and supply many other key industries and services with products that deliver clean energy that is the key to the European Green Deal.”
RECHARGE response
But the specifics in the proposal should be carefully laid out, says Pia Alina Lange, head of internal and external communications with RECHARGE.
“We do see certain areas that have the potential of hampering the innovation and development of our products and industry,” she says. “The specifics will have to be carefully defined in the next steps of the secondary legislative process. RECHARGE will play a constructive role in contributing to viable calculation methods for recycling efficiencies or recycled content as well as to standards and common specifications on the performance and durability of batteries, for example.
“As regards the recycled content measure, we believe that a stepwise implementation of such measures is crucial and we welcome that this concern has been reflected in the proposal.
“The burdens on industry to implement recycled content obligations at a time when volumes of available secondary raw materials are insufficient would have risked jeopardizing the competitiveness of European batteries.
“Nonetheless it is questionable if such an obligation will still result in a better environmental performance. Studies have shown the environmental benefits of recycled content are very limited. Overall, implementing and controlling a recycled content obligation seems disproportionate when recycling efficiencies and recovery rates already exist.
“Control, verification and enforcement are particular areas of attention for us. On the latter, it is difficult to distinguish a recycled metal from a virgin material and auditing of non-EU secondary material supply chains will be very challenging.”
The proposal also mentions the use of hazardous chemicals, in particular mercury and cadmium, and does not include lead — which in the past has been at risk of regulation by the REACH committee, a regulatory body affiliated to the European Chemicals Agency.
REACH context
In February 2019, the ILA and EUROBAT were able to delay attempts by REACH to add four lead compounds to its candidate list of chemicals which would require special authorization before being used — potentially causing a devastating impact on the European lead battery industry.
“We are encouraged that the proposal properly recognizes that restriction of hazardous substances in batteries should only occur where an assessment risk to human health or the environment demonstrates it is not adequately controlled and moreover should also take into consideration an evaluation of socio-economics,” said Bush.
“Streamlining this assessment with existing mechanisms in the REACH regulation is also welcomed and addresses our previous concerns regarding overlap and coherence between EU regulation.”
EUROBAT response
“This proposal is an important milestone,” said EUROBAT president Marc Zöllner, also Hoppecke Batteries CEO.
“All battery technologies and applications will be regulated by this new piece of legislation, stretching all the way from batteries in vehicles and forklift trucks to energy storage and telecommunications. European manufacturing must take a leadership role for a sustainable future, to which all battery technologies will contribute.”
EUROBAT says the proposal aims to build the most environmentally sustainable energy storage solutions, but warns that to avoid ‘hindering innovation in a relatively new sector’, the regulation should not be too prescriptive. It cites standardizing battery packs, saying this ‘would go against high performance, energy-efficient battery products’.
“We appreciate that in most cases the proposal looks at the specificities of each battery technology and applications when it comes to recycling efficiency, collection and information requirements,” EUROBAT said. “For instance, the proposal correctly recognizes that automotive and industrial batteries are collected at the end of their life, and rightly includes a continuation of the current no-losses policy in this regard.”

Later concerns
However, EUROBAT on January 7 issued a further response saying that broadly the approach was good, but that there were concerns.
The proposal, which EUROBAT does not believe will be implemented until the middle of 2022, was made for several reasons, not least of which is so that the battery industry can participate in Europe’s ‘clean energy transition’.
To achieve aims such as increasing battery production by enough to see a reduction in CO2 emissions, the EU says it is essential to address the lack of policy framework, incentives, efficiency within the single market, sub-optimal recycling processes and supply chain problems; and this is what its proposal sets out to achieve.
While welcoming the European Commission’s proposal to promote ‘green batteries’ made in Europe by restricting access to non-sustainable batteries, the response says the scope of the proposed measures is too wide-ranging and deviates from the original intention, without due consideration of technical expertise.
“It is unacceptable that the Commission wants to take the place of national technical experts on matters which are by mature extremely technical, and that refer to how the products are designed, produced and operated,” it says.
“We therefore strongly suggest removing Article 16 in its entirety, and to allow national, European and international standardisation committees to do their work on standards development.”
Another concern raised in the response is the lack M of content in the proposal regarding recycling.
“The Commission did not address any of the concerns that emerged during the stakeholders’ meeting, and correctly reported in the Impact Assessment,” it says.
“For instance, there is no clarification on how the recycled content can be calculated and verified, above all for imported batteries, with the concrete risk of damaging the EU battery industry vis-à-vis international competitors.”
It says the push for second-life applications is in direct contradiction with high levels of recycled content in new batteries and that the measure should not apply to batteries across the board regardless of their characteristics.
The battery association suggests policy makers streamline their administrative processes and cut red tape, for instance by avoiding duplicating processes and simplifying its labelling.
“We worked with the EU prior to the publication of their proposal,” said Gert Meylemans, communications director with EUROBAT.
“Our next focus in terms of EU policy makers will be the EU Parliament and Council, as well as the national ministries. In a few months it will be time for amendments to the regulation from the European Parliament and Council, which will be negotiated in what we call triologues.
“However, before that happens, the EP and the Council need to develop their own position to start the negotiations with the EU Commission, which wants to have it done by the end of this year.
“For us, and other relevant stakeholders, this is too ambitious. We would say mid-2022 at the very best.”
C Y CM MY CY CMY K “It is unacceptable that the Commission wants to take the place of national technical experts on matters which by nature are exceptionally technical”
Final Ad.pdf 1 9/17/2019 3:13:17 PM
Lower Prices. Better Service.
Using the expertise acquired through more than 25 years, we offer our international customers top quality, excellent service and the lowest prices.
New Equipment
From All Major Manufacturers
Spare Parts
Quality built, reliable replacements keeping your machines up and running
Material Supplies
Negative Expander, Fiber Flock, Flux, Cork Powder, Pasting Belts & More Clean-All Heavy Metals®Soap
The only soap that allows workers to eliminate lead residue from their skin without harsh scrubbing. Keep your workers safe and clean.
Global Shipping
We offer full air, ocean and courier services at low rates. Or ship with your own carrier. You are in control.
LOCATIONS: CONTACT:
Miami Beach, FL 33139 U.S.A. TEL: 305-695-8990 Denver, CO 80234 U.S.A. FAX: 305-695-8991 www.sashas.net Email: sashas@sashas.net
Sasha’s International, Inc.
The World’s Price Leader for the Battery Industry
UK to bring forward ban on sales of new ICE vehicles by 10 years
The UK government on November 17 announced it was bringing forward a ban on the sale of new petrol and diesel cars by 10 years as part of a 10-point ‘Green Plan’ to meet its zero emissions target by 2050.
The move will mean a gradual phasing out of the traditional 12V automotive battery, however, a smaller lead battery will still be required for all electric and hybrid vehicles.
The decision was made as part of Boris Johnson’s £12 billion ($15 billion) spending plans to ‘create and support up to 250,000 highly skilled green jobs in the UK’, the government says.
Top of the 10-point list is quadrupling the amount of offshore wind power, to 40GW by 2030.
The ban on sales of new ICE cars comes in at number four, where the government says it will be ‘transforming our national infrastructure to better support electric vehicles’.
According to the Society of Motor Manufacturers and Traders, more than 2.3 million new cars were registered in 2019 in the UK, with just 28,000 of them pure battery electric vehicles.
Of the 2.3 million, 1.3 million were petrol, 0.5 million diesel, and 0.6 million plug-in hybrids. This means there will have to be a huge shift in customer mindsets before the number of ICE vehicles is replaced with electric models.
In the short term the policy will have little impact on lead battery makers, with a strong aftermarket and the remaining need for small lead batteries in all electric vehicles.
“I don’t think this generation needs to worry about the UK car rule because it would take at least another 30 years for the petrol car battery to be off the market — and electric vehicles also need lead acid batteries at the moment,” said CEO and president of Leoch Battery Dong Li.
“It is a smaller battery, but the aftermarket will need a big battery supply for some years, some lead-acid battery EVs will expand their market, and with some new applications there is still at least another 30 or 40 years’ life cycle left.
“However, while the news will discourage new investment, I don’t see a problem for existing investment.”
Clarios, the world’s biggest lead battery maker, said it is focusing on start-stop applications.
“Already today, more than 90% of all new vehicles are equipped with fuel-saving start-stop technology,” said Niklas Volke, specialist communications with Clarios EMEA.
“Market trends show that this is the decisive technology both in original equipment and the aftermarket. Some 80% cent of new start-stop vehicles are equipped with an AGM or EFB from Clarios, and we reckon that the share in the EU car park will nearly double between 2018 and 2023.
“The Clarios lead-acid portfolio is also designed to support upcoming electric and driverless vehicles and will deliver an essential contribution to the energy demand of vehicles even in times of electrification. They support the system when the main battery is switched off or failing.
“Today we are already supplying well-known global players in the field of electromobility with our 12V batteries.”
Geoffrey May, director of Focus Consulting, said the UK policy had been badly thought out.
“It’s headline grabbing for the green agenda but seems to lack proper consultation with industry, the public and all the various stakeholders,” he said.
“The reduction of greenhouse gas emissions from transportation is an important objective and needs to go hand in hand with reductions in the carbon intensity of electricity generation, which was partially addressed in today’s announcement.
“The automotive industry is worldwide in organization and highly integrated in Europe. It would be much better for the UK to remain aligned with EU rules for vehicle emissions and set standards that allow the motor industry to work together.
“Clearly increased automobile electrification has an impact on the lead battery industry but there is a continuing need for batteries to power 12V systems as auxiliary batteries for safety and security and there is a huge market for replacement batteries, which has to be satisfied long after vehicles have gone into service.
“Lead batteries are preferred for auxiliary applications because they are safer, have proven reliability and are cheaper.”
According to the US-based Union of Concerned Scientists, the UK contributed 1% (0.34 giga tonnes) of global CO2 in 2018, 17th in the world rankings behind China in first place with 28% (10.06GT) and the US second, with 15% (5.41GT).
The only European country in the top 10 was Germany, contributing 2% (0.75GT).
Independent law firm clears Monbat group of irregular waste handling
Bulgarian and eastern European battery and recycling group Monbat announced in September that it had been cleared of mishandling hazardous waste by law firm Wolff Theiss.
It also said the results of the independent review showed it had operated in compliance with legal and regulatory requirements.
The statement was made in response to an investigation in May into whether Monbat CEO Atanas Bobokov, his brother Plamen Bobokov and Bulgaria’s deputy environment minister Krassimir Zhikov were involved with a crime group that mismanaged product waste, including lead waste.
The two brothers and Zhikov were detained for 24 hours and in June, Atanas Bobokov resigned from his post, although remaining as chairman of the board.
Wolff Theiss was appointed the same day ‘to conduct an independent audit into the matters related to the ecological aspects of the company’s activity and compliance with Bulgarian and European legislations’. The firm said there was no irregularity with declared quantities of waste, and that “incoming and outgoing flows were only in relation to materials and waste related to its production and no illegal import/export was made”.
“Processing of RDF waste (household waste) is incompatible with Monbat’s technological capabilities and Monbat Recycling has never been engaged in this segment of waste management,” the firm said.
Wolff Theiss said all documentary processes that had been carried out were appropriate.
The CBI has come a long way in the past two years. Batteries International interviewed the consortium’s director, Alistair Davidson, about its achievements so far.
Breaking the mould
The Consortium for Battery Innovation hit the ground running when it was officially set up two years ago in February 2019. A stream of energetic initiatives and demanding performance targets were rolled out and the first harvest of that energy is now on display. Some of CBI’s success to date has been measurable, performance targets being met ahead of time, for example. But it is also making ground in the articulation of a clear message — advanced lead batteries will be a major feature in the energy storage universe of the future.
The emphasis, as before in its previous incarnation as the ALABC (Advanced Lead Acid Battery Consortium), is on pre-competitive research.
Driving the programme under way at CBI is a technical roadmap, elaborated in 2019, which set out research goals based on commercial logic — what advances in lead battery technology will be needed in the future?
Dynamic charge acceptance (DCA), for example, is a performance enhancement crucial for the growing micro-hybrid market, where stopstart cars could represent more than 80% of European car sales by 2030.
CBI’s specific 2022 targets, set out two years ago, were aggressive to say the least. Automotive batteries were to achieve a cycle life of 2,000 times while at a partial state of charge for enhanced flooded batteries; DCA was to improve five times to 2.00A/Ahr; there would be a water loss figure of under 3g/Ahr; and grid corrosion according to J2801 units of 18.
“We are seeing exciting results from our research programme,” says Alistair Davidson, the director of CBI. “It’s clear that lead batteries are well on track to meet the targets and some members are already reporting achieving these performance improvements.”
The importance of what CBI is doing has been reflected by the rapid increase in its membership — up from 72 at its start to 107 at present.
But the role of the CBI is more than just acting as a research conglomerate: it has a duty to communicate its findings to the industry as well as help the battery business communicate among itself.
CBI continues to hold various technical meetings and workshops around the world. Its most recent virtual one in China was attended by 150 delegates. CBI expects that number to rise to around 200 next time.
“We’re showing that our research projects are well worth knowing about — people are very excited, for example, about our work and the data we produce about carbon and other additives,” Davidson says.
He says there will be a new call for research towards the end of this year, where the emphasis will be on larger scale energy storage system projects. Davidson added: “Building on our progress to date we have some impressive projects in the pipeline, which we hope to announce in the coming months. Our portfolio of research is growing very rapidly, but that’s a nice problem to have and it’s great for the industry’s future.”
One change taking place was the appointment of Christian Rosenkranz as the new consortium chairman this January. Rosenkranz is the VP for industry and government relations for EMEA for Clarios and a global leader in automotive batteries.
“We’re seeing a big focus in the United States under Biden and in Europe on batteries and energy storage, all linked to the low carbon agenda. This is a major opportunity for our industry and cutting-edge research will be even more critical,” Davidson says.

BATTERY MATCH
The latest initiative from the CBI, launched last August, provides a matchmaking service for utility companies seeking to plan their energy storage with battery makers who can fulfill that need.
Put simply, the energy storage company inputs its technical requirements — for instance, will the batteries be needed for peak avoidance, renewable firming or say power correction — as well as its timeframe, and is provided with details of the CBI battery members and their products that would fit these criteria.
“We’ve had a good response to this so far,” says Davidson. “It shows that people when given the chance to explore the capabilities of advanced lead batteries will do so.”
Residents’ anger over decision to overturn block on lead smelter
Residents at Hazelwood North, an industrial park near a farming community in Victoria, Australia, have reacted with shock over the state government’s decision earlier in January to overturn a refusal by local Latrobe City Council for a Chinese secondary lead smelter to be built on their doorstep.
Under its plans, the Chunxing smelter will recycle 50,000 tonnes of used lead acid batteries a year, to produce 28,000 tonnes of refined lead.
The decision to allow the smelter to be built has been made ahead of a tribunal already scheduled for April that was due look at the matter again.
Planning minister Richard Wynne’s intervention means the tribunal will not now be held. Residents have formed a protest group at Hazelwood North, with a Facebook page showing the protests they have held.
The approval has been given despite a report from Mark Stevenson, a lead smelting expert, who was contracted by the EPA to provide his assessment.
In the report he outlines concerns about stock storage, pollution controls, treatment of spent acid, slag production and the proposed furnaces.
Chunxing sought to allay fears about the project on its website, promising that lead emissions from the new site in a worst-case scenario would be 300 times lower than EPA standards.
The company came under fire in 2008 in Chinese newspaper reports, which said its facility in Pizhou, Jiangsu Province, had poisoned 41 children in the village of Xinsanhe.
Then named the Chunxing Alloy Group, the company expanded near the village, generating large amounts of dust, according to Justice Atlas, an environmental NGO.
After months of protests about contaminated groundwater, villagers eventually succeeded in getting treatment for their children and forcing the plant to be relocated.
On September 17, Latrobe City Council refused to grant planning permission at Hazelwood North – and in light of the decision being overturned by the state of Victoria the area expects further protests will be planned.
Campine introduces new process for antimony extraction from ULABs
Belgian recycling firm Campine said on January 11 it was expanding its activities with a process to extract antimony from older lead batteries which have far greater amounts of the element than more modern batteries.
The antimony extracted is then transformed into trioxide, which is used as an ingredient in fire retardant paints, plastics and other materials.
“This innovation is almost exclusive to Campine, as we are the only company in Europe and by extension in the world, that combines the recycling of lead-acid batteries and the manufacturing of antimony trioxide,” said Hilde Goovaerts, head of metallurgical technology at Campine.
CEO Wim De Vos said the antimony trioxide grade ‘ReGen’ that the company introduced in 2018 immediately sold out — but Campine’s new process means it can be produced on an industrial scale for customers who can complement the recycled polymers they already use with recycled additives.
“On top of this, it makes Campine — and to some extent Europe — less dependent on the dominant Chinese imports of antimony metal,” he said. “Campine wants to provide at least 20% of its antimony metal demand through this type of recovery from regional waste streams. The new process to recycle antimony is already in its start-up phase.”
Alongside its antimony recycling, Campine has also been expanding its extraction of other metals such as tin, silver and gold from industrial waste streams.
In May 2018, the company announced its intention to invest up to €25 million ($30 million) in recycling projects, with the largest single amount going into recycling the plastic housing of batteries.
“With China closing its borders for plastic waste, we see growing opportunities to recycle even more plastics in Europe,” De Vos said at the time.
Bolivian lead smelter to be upgraded after running at 10% capacity
The 40,000 tonnes a year Karachipampa zinc-leadsilver smelter in Bolivia is to be upgraded after being operated by state mining firm Comibol at just 10% of capacity for the past year, the country’s mining ministry said on October 28.
Energy and commodities news agency S&P Global Platts said the underperformance had been due to a faulty blast furnace, and local contractor firm Kimmaera had been hired to bring it back online.
Five investor groups have already signalled their interest in participating in mining projects across the country.
Lead concentrates production fell by half in September, Platts reported, along with zinc, tin and copper, after a two-month lockdown due to the virus.
Bolivia is ranked 18th in the world in terms of lead production, producing around 88,000 tonnes in 2019, according to data firm CEIC.
This was a decrease over 2018, which was recorded at 112,000 tonnes, although that figure was an all-time high.
Just two weeks ago a socialist government led by Luis Arce was elected on October 23. He has promised to rebuild the country after a year of political turmoil capped by this year’s pandemic.
Eternity Technologies launches range of gel bloc batteries made in the UAE
Eternity Technologies, the UAE industrial battery plant launched a new range of Bloc batteries in dearly November.
The Eternity Technologies Gel Bloc is a new generation of maintenance free product using VRLA Gel technology to provide extensive cycle performance, high resilience to deep discharge, longer life in harsh conditions and fully recyclable.
The Eternity Gel Bloc range will be made in three variants traction, leisure and solar) to serve applications such as
marine, cleaning machines, automated guided vehicles, aerial work platforms, motorhomes, solar and wheelchairs. Products will be available in 6V or 12V with capacity from 25Ah up to 300Ah.
The range will be manufactured out of a brand new plant in the UAE, using the latest generation of production equipment, with a production capacity of 1 million Blocs annually to serve the global market. “We are excited to be able to respond to the growing demand of battery solutions with the most reliable and cost effective technology” said Mark Stevenson, the CEO of Eternity Technologies.
Chinese secondary lead smelters drop operating rates as new plants open
Operating rates in secondary lead smelters across the Chinese provinces of Jiangsu, Anhui, Henan and Guizhou saw an average drop in the last week of October, all operating at an average of just over 50%, the Shanghai Metals Market reported on October 30.
This is in spite of a November 4 report by Transparency Market Research, which says the battery recycling sector in the Asia-Pacific region, led by China, would have a CAGR of around 10% up to 2027 because of the growing requirements of governments to reduce environmental impact.
“Recycling and disposal of spent batteries are a key concern for economies in the light of reducing the environmental impact of the battery industry, as well as the mining of key minerals used in the battery making,” it said.
“They have framed numerous regulations, and stakeholders in the value chain are leaning on complying with those. This has spurred the opening of new recycling plants and, more importantly, has fuelled constant technological advances in older plants.”
China’s industrial output has rebounded to preCovid-19 levels, according to the National Bureau of Statistics, which recorded an overall 2.4% decrease in the first nine months of 2020 then a surge of 4.9% from July.
It means China is now back at a 6% growth rate, according to its own figures.
Aqua Metals debt-free after $24.3 million insurance payments
Aqua Metals, the lead battery recycling firm, said on December 15 that it had paid off a $9 million loan to the Veritex Bank and was now debt free, almost exactly a year after a fire tore through its Nevada site, destroying all of its Aqua refining modules.
In the same statement, the company said it had received another insurance payment in respect of the fire, with total payments received now totalling $23.4 million.
“The company anticipates collecting additional insurance proceeds for the replacement value of its damaged assets and potential business interruption recovery proceeds,” the company statement said.
“Eliminating our debt significantly strengthens the balance sheet and completely removes the burden of restrictive loan covenants,” said CFO Judd Merrill. “In addition, this step improves the company’s cash burn rate by eliminating $0.9 million annually in debt service payments, including $0.6 million in interest expense. We are also pleased with the continued progress made in recovering the losses through our insurance collection efforts.”
Canadus combines solar power with reconditioning BMS to lengthen battery life
Lead acid battery technology company Canadus Power Systems, based in the US state of Ohio, has combined its battery reconditioning system with solar panels to maintain the health and charge of batteries in applications where they sit idle for long periods of time, the firm said on December 1.
Batteries only used intermittently in fleet or military vehicles and construction equipment, for example, slowly lose their charge when not being used, shortening the life of the battery.
By using the new system, the solar panels keep the battery charged, while the Canadus reconditioning technology desulfates it — avoiding one of the leading causes of lead-acid battery failure.
“The benefits of the solution will repay the initial investment many times over the long term,” said Canadus marketing director Jeff Scott. “Not only does it increase the battery life by up to five times, it also ensures that your equipment is ready when you need it. This reduction in downtime itself will save the end user a great deal of money.”
The company is using solar panels by the California-based Merlin Solar, which are sized to provide enough supplemental charging to prevent the discharge of any specific vehicle.
Merlin also activates the battery reconditioner — the Canadus HD-1224 — which cleans the build-up of hardened lead sulfate crystals from the battery’s plates.
Ultracaps ‘now compete head on’ with lead and lithium batteries‚ says IDTechEx
A November 2 report by the market research firm IDTechEx says large supercapacitors “now compete head on” with batteries — with greater energy density than lithium-ion batteries, offering up to 1MWh of storage.
IDTechEx’s report looks at how supercapacitors can be a good option in tidal power, which by its nature is not uniform and requires smoothing to maintain output.
Some supercapacitors, says IDTechEx, are drop-in lead acid and lithium ion battery replacements, others are bought as uninterruptible power supplies with the ability to offer peak shaving, with power density 10 times that of lithium, and series resistance low.

IDTechEx’s Raghu Das: It is now obvious that supercapacitors will be one of the very big nails in the coffin of lead acid batteries over the next few years
“Frequently, supercapacitors are used as an energy storage device to smooth the output power and improve the low-voltage ridethrough capability of energy conversion systems, being fit-and-forget and wasting 14% less electricity than lithium-ion batteries,” said IDTechEx CEO Raghu Das.
“Output power fluctuation caused by the swell effect (opposite of voltage dip) is efficiently smoothed by supercapacitor energy storage systems.”
Despite the apparent advantages of supercapacitors over other batteries, they have still not made much of a dent in a market that IDTechEx in 2012 admitted was overlooking them.
“It is now obvious that supercapacitors will be one of the very big nails in the coffin of lead acid batteries over the next few years, yet that is only part of the story as their parameters are being improved faster than the competition,” a ‘Supercapacitors replace batteries’ report by IDTechEx chairman and founder Peter Harrop had said in May 2012.
“Yet supercapacitors are an aspect of electronics and electrical engineering that is curiously neglected or talked down by the press, investors, potential suppliers and others living in the past despite a multi-billion dollar market rapidly emerging,” Harrop said.
Other market research firms have indicated the outlook is rosy for supercaps, with Allied Market Research estimating a CAGR of 23.3% from 2020 to 2027, increasing the market size in value from $3.27 billion in 2019 to $16.95 billion by 2027.
Skeleton raises €41.3m in new bid to improve technology and replace lead batteries
Skeleton Technologies, the supercap manufacturer, announced on November 3 it had raised €41.3 million ($48.5 million) in a series D financing round. This brings its total capital raised to over €93 million.
The company says its technology can replace lead acid batteries in ICE and electric vehicles, and its Skeleton Gen 3 supercap can provide more than 60Wh/kg as opposed to 25-30Wh/kg from a lead battery.
“All existing investors in the company joined the equity raise: EIT InnoEnergy — early investors in European gigafactory startup Northvolt — FirstFloor Capital, MM Grupp and Harju Elekter,” the firm said.
“Ultracapacitors are a key enabler for lowering emissions — we are not competing with lithium-ion batteries and hydrogen fuel cells; we are complementary in improving performance and lowering cost,” said head of Skeleton Taavi Madiberk.
“Our ultracapacitors have four times the power density of Tesla’s. The clear competitive advantage is not only proven by our blue chip customer base, ranging from German automotives to leading truck OEMs, grid integrators to the European Space Agency, but also by an independent study backed by the US Office of Naval Research.
“We have a clear roadmap to further increase our competitive advantage and increase both the energy and the power density of our products.”