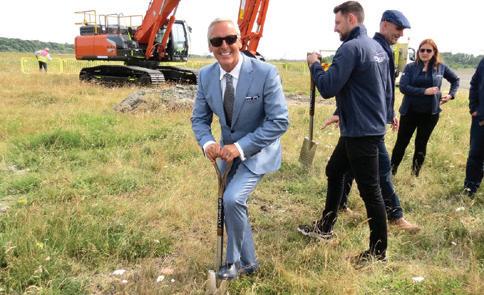
38 minute read
NEWS
ENTEK closes acquisition of NSG separator division
International battery separator firm ENTEK closed its acquisition of Nippon Sheet Glass’ lead acid battery separator division on September 1.
The acquisition means ENTEK will add AGM separators to its portfolio, which so far consists of PE separators and lithium battery separators. It becomes the first firm to manufacture separators in all three primary battery technologies.
The new company will own all of NSG’s battery separator facilities in Japan and China for both OE separators and AGM separators, the firm said.
The acquisition was announced on May 10.
Clint Beutelschies, vice president for global sales & marketing, told Batteries International in May that the firm’s majority stake in the battery separator division of the Japanese firm, which predominantly makes glass for automobiles, will push ENTEK into a leading position in Asia, a region where until now it has had a relatively small footprint.
“Among the three major regions of the world, Asia has by far the highest growth rate, and it’s important for us to take our industry leadership and have our local presence in that region,” he said.
“In the Americas we are the largest producer of separators for the lead-acid battery separator industry, far ahead of our nearest competitor. In Europe we are the leaders for auto separators as well.”
ENTEK began to take more of a presence in Asia with the acquisition of a plant in Indonesia in late 2017, but this was just the start. The company made plans to double the plant’s capacity with another production line, and although the pandemic delayed things, the ultimate goal remains the same.
“In Asia we were a relatively small player, with just the investment in our Indonesian plant in 2017,” Beutelschies said.
“Before that we didn’t have a manufacturing plant in Asia, so we had some catch-up to do. NSG was our joint venture partner in the Indonesian plant, so we know them quite well. Their battery separator division is a great fit for ENTEK, and to their credit, from the CEO Shigeki Mori, right on down, they recognized we would be a great partner — so now we’re off to the races.”
A full statement by the firm said: “With this strategic acquisition, ENTEK becomes the only separator manufacturer in the world producing all three primary separator technologies (PE, AGM, and lithium separators) for the global energy storage industry.
“Considering ENTEK’s established business foundation and mutual trust, NSG Group has decided that the best option for the BSS business as well as for the customers and the stakeholders is for BSS to be integrated with and managed by ENTEK so that it can develop further and enhance its value for customers.”
we’re off to the races” — Clint Beutelschies, ENTEK
ENTEK forms innovational relationship with nascent UK Britishvolt gigafacory
Britishvolt, the company building the UK’s first lithium-ion battery gigafactory, on June 14 signed a MoU with ENTEK that means separators will eventually be domestically produced in the UK and supplied straight to the production line.
Britishvolt held a groundbreaking ceremony on the opening of its plant £2.6 billion ($3.4 billion) in early August. Two other huge lithium battery factories in the UK — see European gigafactories feature in this magazine — may be active shortly.
The MoU will look at how ENTEK’s separators can be used in Britishvolt’s batteries and following that, a potential investment in a facility to produce the ceramic coated separator materials.
ENTEK already has a plant in Newcastle-uponTyne, in the north of England, and the plans are for another one next to Britishvolt’s gigafactory in Blyth also near to Newcastle-upon-Tyne.
“We are delighted to have been selected as Britishvolt’s preferred lithium-ion battery separator partner and eager to align our objectives and investments with their transformational plans to build a 30GWh+ factory in the UK,” said Larry Keith, ENTEK CEO.
“Co-location at Britishvolt’s site will allow access to an abundance of renewable energy, essential for power intensive manufacturing processes,” said Britishvolt.
“It will also reduce the length of the supply chain and along with it the carbon footprint of battery production.”
Supply of lithium is also a concern, although two firms — British Lithium and Cornish Lithium — are exploring known deposits of the element in the UK.
ENTEK’s Graeme Fraser-Bell breaking ground on the ground-breaking plant at Blyth on July 27
BCI victory as lead batteries removed from DTSC danger list
Lead-acid batteries have been removed from the California Department of Toxic Substances Controls’ danger list of potential ‘Priority Products’, Battery Council International announced on May 10.
The action is a major victory for the industry as a whole and BCI, which has been campaigning for years to make sure lead batteries are not included on this list.
‘Priority Products’, listed under the DTSC’s Safer Consumer Products Programme, have to undergo an Alternatives Analysis process whereby manufacturers have to seek other options to find less toxic chemicals to use in their products.
Lead-acid batteries were added to the DTSC 20152017 Work Plan for consideration as a potential Priority Product because they contain three ‘Candidate Chemicals’ lead, arsenic and sulfuric acid.
“Lead exposures to workers and neighbouring areas may occur during recycling and manufacturing operations,” the Work Plan said. “Lead exposures are
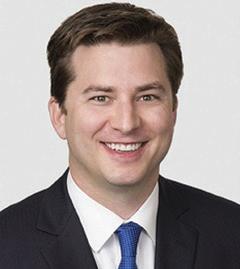
Roger Miksad
known to cause neurological as well as other effects, and arsenic is a carcinogen. Lead exposure to children is especially of concern since there is no known threshold concentration for neurological effects.”
But among other arguments against the potential move, put forward by the industry, is that the sector is already extremely tightly regulated and poses no harm to consumers.
After a rigorous evaluation of potential life-cycle impacts, current regulations and product innovation, the DTSC has now agreed to exclude lead batteries.
BCI has been working for years for this outcome, saying inclusion on the list would be ‘inappropriate and unlawful’.
In a nine-page letter to the DTSC in March 2018, the council said: “Prematurely mandating that California consumers and businesses switch from a proven safe, economical and proven battery technology to new and unproven battery technologies with known significant environmental and public safety risks, and unknown long-term impacts, would not meet the agency’s statutory mandate.
“DTSC action on lead batteries may also have the unintended consequence of reducing the value of recycling for lead batteries, upending the current closedloop life cycle.
“This could perversely cause more lead batteries to wind up in landfills or with less responsible processors, a result nobody wants to see.”
In its final Priority Product Work Plan for 20212023, the DTSC concluded that ‘listing lead-acid batteries as a Priority Product is not likely to further enhance protection to human health’.
“This outcome is the right one and recognizes that lead batteries are critical to meeting America’s energy storage needs and are already well regulated,” said BCI executive vice president Roger Miksad.
“The industry’s highly successful closed-loop recycling system and investment in new technologies and innovations also means that lead batteries hold the promise of delivering safe, sustainable energy storage in the future.”
Miksad thanked DTSC staff on behalf of the industry for the ‘dedication and care’ they had put into their review of lead batteries over the past five years.
US battery firms form research group to improve cycle life
Five US lead battery firms have formed a research group with the Argonne National Laboratory and the University of Toledo to improve battery cycling efficiency, Battery Council International said on July 29.
Clarios, Crown Battery, EnerSys, East Penn Manufacturing and Ecobat are joining up to improve the efficiency and lead to longer-life batteries ‘as new applications emerge in an increasingly decarbonized market’, BCI says.
“This new research is unique because it is focused on improving the performance of advanced lead batteries, which are fully recyclable, and for which recycling capacity already exists in the US,” the BCI says.
Cora Lind-Kovacs, professor in the UToledo Department of Chemistry and Biochemistry, will work with Argonne’s Material Science division, which will lead the research over the next two years.
It will conduct an atomiclevel examination of the organic materials used in expanders to extend battery life by improving their cycling efficiency.
Specifically, the programme will study the atomic structure of lignosulfonate molecules to improve or replace them with other naturally derived elements.
Understanding the interactions between lead, lead sulfate and lignosulfonates, according to the research, is key to guiding the design of additive molecules that can aid with fast charging and thus prolonging the life of the battery.
In turn this has benefits for long-duration storage — a vital attribute for lead batteries if they are to remain competitive as demand grows in more and more applications.
“This partnership can help industry meet society’s demanding requirements in vital industries like transportation and electric power,” said US representative Marcy Kaptur, chair of the US House Appropriations Energy and Water Development Subcomittee and instrumental in bringing the parties together.
“UToledo’s chemistry department will bring their expertise to help meet the growing need for more efficient and sustainable rechargeable batteries to support a changing economy.”
Pilot Battery signs evaluation agreement with Gridtential
A formal agreement to evaluate a combination of 6V and 24V silicon joule batteries was signed on June 15 between Taiwanese battery firm Pilot and the silicon joule wafer creator Gridtential.
The agreement has been hailed by the firms as one that ‘could kickstart a new era of Taiwanese and Asian Pacific battery production for the energy storage systems market’.
Using development kits by Gridtential, Pilot will produce prototype batteries to prepare for future production. “Pilot will integrate its own active material in the battery to validate impact on cycle life, energy density, battery efficiency, charging rates and manufacturability,” say the firms.
Pilot Battery makes lead carbon and VRLA batteries for applications from UPS to SLI. The Taiwanese government has set a target of 27GW of renewable energy installation capacity by 2025, which will need energy storage alongside.
“The AGM market will be examined closely as a good solution for that increased demand,” it says.
Gridtential says its silicon joule wafer technology increases the power density of a battery by five times and the discharge rate by two, with a 75% lower levelized cost of electricity than conventional lead-acid batteries.
“The superior treatment for the silicon wafer we’ve developed from many decades in the solar industry could make a great match with the silicon joule bipolar design,” said Pilot president Chunyi Hong.
Gridtential has 12 licensing agreements with battery makers for its silicon joule design.
The evaluation agreement comes on the back of a launch a series of AGM reference batteries produced on East Penn Manufacturing’s prototype line. “These are not just samplers but also batteries that are ready to be sold to the market,” John Barton, Gridtential CEO, told Batteries International.
The first commercial product is a single-block 24V lead battery optimized for deep-cycle applications. A 12V power version will follow late spring, with 48V versions of each appearing in the second half of the year.
Gridtential says its Silicon Joule AGM battery delivers up to five times the power density, four times the cycle life and twice the discharge rate at a 75% lower levelized cost of electricity than conventional lead batteries.
“We’re offering highperformance batteries as an attractive alternative to lithium-ion,” says Barton. “Customers don’t need to wait for multibillion dollar factories to be built — manufacturers can move directly from prototype to mass production, with 90% of the required equipment already in use -in their factories.”
Gridtential battery technology substitutes treated silicon wafers for conventional lead grids and combines them using as what it describes as a patented stack-and-seal architecture. This, the firm says, provides uniform current distribution and efficient thermal management, minimizing failure modes such as sulfation, corrosion and grid growth.
Gridtential says it will offer a range of products for a variety of energy storage applications, from personal mobility to home energy storage to hybrid automotive: • 24V deep-cycle (available now): electric sweepers, scooters, wheelchairs, riding lawn mowers, e-bikes • 12V power (available Q2 2021): power-sports SLI, automotive start-stop and
EV auxiliary • 48V deep-cycle (available 2H 2021): golf carts, etuk-tuks, renewable energy storage, telecoms, data center backup, micro-grids • 48V power: (available 2H 2021): mild-hybrids, EV auxiliary, ADAS, startstop, infotainment and regenerative braking.
Separately, Gridtential announced on April 27 that it had closed a further $12 million funding round. Gridtential has raised $28 million to date. Participants were Silicon Valley Bank, August Capital cofounder David Marquardt, ReneSola CEO Yumin Liu and existing investors that include East Penn Manufacturing, Crown Battery and the Roda Group.
Gridtential’s business model works on a licensing basis.
East Penn, Crown and Leoch are fully licensed to mass produce Silicon Joule batteries, and nine additional manufacturing partners — mostly international — are piloting the technology. “Several have already produced batteries off testing lines in their factories,” says Barton.
India ups the ante with a raft of opportunities for battery storage
Indian government is putting up billions of dollars of cash, offering tenders and incentives to battery firms to put in place more than 50GWh of storage over the next few years.
Policies in line with the country’s aims to Aatma Nirbar Bharat — Make in India — include a $2.5 billion ‘Production Linked Incentive’ scheme to achieve manufacturing capacity of 50GWh of advanced chemistry cell (ACC) battery storage and 5GWh of Niche ACC; floating tenders for 4,000MWh of battery storage; and a 2,000MWh standalone energy system.
“All the demand of the ACCs is currently being met through imports into India. The National Programme on ACC Battery Storage will reduce import dependence. It will also support the Aatma Nirbar Bharat initiative.”
ACC battery storage manufacturers will be selected through a transparent competitive bidding process, and the manufacturing facility will have to be commissioned within a period of two years.
“With the approval of the PLI scheme many global companies are looking at entering the Indian market,” says a spokesperson with the India Energy Storage Alliance. “Companies such as Amara Raja and Nexcharge have acquired the land for setting up the gigafactories. Both companies are leading India’s energy storage market.
“Some of the major companies planning to set up cell manufacturing plants in India include Exicom TeleSystems, Samsung SDI, Panasonic Corporation, Tata Chemicals, and TDSG.
“Under Niche ACC, alternative technologies such as sodium-based, zinc air and aluminium batteries will get a boost, having better battery density, cycle life and safety. So the market looks quite promising for domestic and international players.”
The IESA says most of the tenders are technology agnostic.
Sodium ion batteries to pose threat to lithium and lead industries
Chinese news reports at the end of May have said that lithium-ion battery giant CATL has plans to start making sodium-ion batteries in what some say could be a direct challenge to leadacid.
According to the website www.equalocean.com, CATL chairman Robin (Yuqun) Zeng said the firm would start marketing sodium-ion batteries almost immediately. The decision to add the chemistry to its portfolio has been made to reduce its reliance on lithium imports, the report says.
“Currently, over 70% of China’s demand for lithium is fulfilled by foreign providers,” the report says. “Amid the Sino-American standoff, both nations’ finest hightech corporations have been investing lavishly in import substitution strategies.”
It also says that shares of Sacred Sun and Lanta industrial have soared because they are key providers of materials for sodium-ion batteries.
“Sodium-ion cells have a lower energy density, ~100-150Wh/kg, in comparison to lithium-ion cells’, 330Wh/kg,” says James Frith, head of energy storage at BloombergNEF. “So expect them to be used to replace lead-acid initially, in applications such as backup power and two and three-wheelers.
“In the long run, stationary storage markets could be suitable for sodium-ion deployments.”
The UK Faraday Institution says: “Sodium-ion batteries are an emerging battery technology with promising cost, safety, sustainability and performance advantages over current commercialized lithium-ion batteries.
“Key advantages include the use of widely available and inexpensive raw materials and a rapidly scalable technology based around existing lithium-ion production methods. These properties make sodium-ion batteries especially important in meeting global demand for carbon-neutral energy storage solutions.”
Umicore and BASF sign agreement to develop cathodes and precursors
Umicore, the metals and battery recycler, and multinational chemicals company BASF on May 4 said they had signed a cross-licence agreement to develop cathode materials and precursors in a wide range of battery chemistries based on nickel and manganese.
Precursors are cellular components from which another component is formed — and with the cathode materials are an essential part of rechargeable lithium-ion batteries, said Marjolein Scheers, media relations manager with Umicore.
“The focus here is to increase the ability to customize cathode materials to the increasingly diversified and complex customer requirements at battery cell and application level and to increase product development speed,” she said.
The collaboration is a natural fit, with both companies for many years ‘investing intensively in product innovation for low, medium and high nickel precursors and cathode materials resulting in each company owning sizeable and largely complementary patent portfolios’, a statement said.
The chemistries named as in line for development are nickel manganese cobalt, nickel cobalt aluminium, nickel manganese cobalt aluminium and high manganese.
The work will look at the best chemical composition, powder morphology and chemical stability for each application ‘to meet the increasingly diversified and complex customer requirements’, as well as examine energy density, safety and cost issues.
“This agreement with BASF is an important step in promoting cathode material innovation,” said Umicore CEO Marc Grynberg. “It strengthens our technology positioning and further increases our ability to develop bespoke solutions which meet the most stringent performance and quality standards of our battery and automotive customers.”
“The continuous development of battery materials will accelerate the transformation towards full electrification,” said Peter Schumacher, president of BASF Catalysts.
Lithium batteries in Europe to make up entire industrial battery sector by 2030
Lithium-based batteries will make up almost the entire sector of industrial batteries by 2030, according to EUROBAT’s analysis of a market report by Avicenne Energy on May 17, with lead-based batteries only remaining dominant in UPS and telecoms applications.
The key conclusions in Avicenne’s EU Battery Demand and Supply (204192030) in a Global Context report include the prediction that the preferred technology in the industrial battery sector — which includes energy storage systems, motive batteries, UPS and telecoms — will see a major shift to lithium, with ESS almost exclusively lithium-ion.
In motive power, where lead batteries are dominant today with a 90% share, the preference will shift dramatically in lithium’s favour until it is the majority technology.
Lead will hold its own in UPS and telecoms.
However, the lead battery sector will remain dominant across all levels of e-mobility, the report says, and continue to be dominant in the 12V market for SLI and auxiliary functions.
The report also predicts massive growth in lithiumion battery production in Europe, with a 10-fold future growth potential.
“Europe is ready to meet demand, although currently heavily reliant on imports,” it says, with emobility being the driver for growth.
With lead-based batteries, “Europe will retain its strong position in 2030 and remain very competitive, but ongoing investment is needed to maintain/improve production and for R&D,” it says.
Exide saga continues with $291 million general fund to clean up Vernon environs
The governor of the state of California in his May Revision Budget for 20212022 has earmarked a further $291 million to clean up more properties in the city of Vernon around the controversial lead battery recycling plant owned by the former Exide Technologies.
Gavin Newsom’s May Revision proposes that the money should be spent over three years and focus on properties with specified lead contamination levels near the former Exide site.
“To date, the state has provided over $251 million General Fund for residential clean-up and other costs associated with Ex-
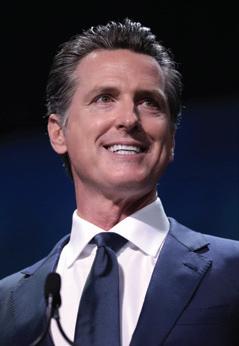
Covernor Newsom’s May Revision proposes that the money should be spent over three years and focus on properties with specified lead contamination levels near the former Exide site. ide,” says the Revision.
“The bankruptcy settlement allowed Exide to walk away from its obligations to complete the closure of the facility; however, the administration remains committed to pursuing cost recovery from responsible parties for Exide.”
Separately according to a law report, the California Department of Toxic Substances Control lost its appeal against the Chapter 11 plan of battery recycler Exide Holdings. on July 26 when a US District Court judge said it would be a ‘moot exercise to unwind the company’s confirmed bankruptcy plan’.
The reason being that Exide’s plan that transferred its 10 facilities into an environmental remediation trust to maintain and clean up the locations had been largely consummated and the agency wasn’t facing any risk that the debtor’s site in California would be abandoned.
In December 2020, the California Department of Toxic Substances Control filed a suit against a number of companies, including Clarios, Quemetco, Trojan Battery and Ramcar Batteries, claiming they were also responsible for the contamination around the site by transporting hazardous waste to it.
The outcome of the case is not known yet.
Gopher Resource taken to court for lead poisoning
Gopher Resource, the lead battery recycling firm in Florida undergoing an inspection by the local Occupational Health and Safety Administration, was taken to court on June 2 by the family of a former worker who claim their son’s disabilities are a result of his father’s exposure to lead dust.
Ko Brown, who worked at the plant, alleges that Gopher failed to prevent him from carrying toxic dust home and exposing his son, Colin, to the poison when he was an infant and had lead recorded in his blood.
The lawsuit maintains that Colin has suffered disability and emotional distress.
Gopher denies claims made by local media that damning levels of harmful lead contamination has been found in the blood of its workers.
When the OSHA inspection was begun in April, Gopher was fully supportive, saying it had spent more than $230 million on making the facility safe. Average blood lead levels among staff, it said, were actually half what they were when Gopher bought the plant in 2006.
“Protecting our Tampa employees and the surrounding community is a core value of Gopher Resources and its workforce,” the company said.
“Since 2006, we have invested more than $230 million to modernize the Tampa facility, which included installation of state-of-theart pollution control, and health and safety measures including filtration and ventilation. The standards we hold ourselves to are more stringent than regulatory standards.”
Nyrstar accepts responsibility for acid leaks at Port Pirie
Global metals company Nyrstar on May 24 told a court it had accepted responsibility for a sulfuric acid leak at its Port Pirie lead smelter in 2019, according to Australian news outlets.
The Environment, Resources and Development Court heard that the smelter, north of Adelaide in South Australia, had leaked an estimated 700 litres of the acid into waterways near the site at the end of January 2019, according to court reports.
Nyrstar could face a fine of up to $250,000, to be decided at the next court hearing in July.
How much harm was caused to the area was not quantifiable, the court was told, but the leak was not stopped for at least eight hours.
News agencies quoted Nyrstar lawyer James Levinson saying that a spillage prevention mechanism had failed and the wrong type of valve had been installed in the conveyance pipe.
“There certainly was the best of intentions and the respondent fully accepts that it operates on this site subject to it complying with the law,” Levinson is quoted as saying.
In June 2019, Port Pirie suffered an unplanned outage that caused lead prices to soar by around $250 per tonne.
In November that year the sinter plant had to be closed down to restart the top submerged lance furnace and peripherals before full production could restart after a few weeks’ closure. In June 2020 the smelter owners were told by the Australian Environmental Protection Agency to cap emissions by 20%.
Port Pirie has been in almost continuous operation for 129 years.
Major Indian lead recycler signals plans to process lithium batteries
Indian business news website Money Control said on June 29 that the largest lead battery recycling company in the country, Gravita, had decided to enter the lithium battery recycling sector.
Quoting Gravita India’s CEO Yogesh Malhotra, the site said ‘talks are at an advanced stage’ with a European firm that could provide the technology for recycling lithium batteries.
“Demand for recycling lithium batteries is expected to become viable in six to seven years, by when Gravita India will be ready for the market,” the site said.
With the Indian government, as with many others across the world, mandating that only new electric cars will be sold after 2030, the need for lithium battery recycling is bound to surge.
At the moment, Gravita smelts lead ore, concentrate and battery scrap, as well as aluminium scrap, to produce lead and aluminium ingots.
California DTSC threatens $25K a day fine for lead recycler
California’s Department of Toxic Substances Control in June threatened a local car breaker with fines of $25,000 a day if it fails to stop releasing hazardous waste, including lead, into the environment.
The DTSC has filed a request to Los Angeles County Superior Court to impose the penalties on Dick’s Auto Wreckers for each violation of the hazardous waste law.
The company has been ordered to investigate any spread of contamination into the surrounding neighbourhood and clean it up.
“DTSC has a profound responsibility to protect all Californians from the effects of hazardous chemicals,” said DTSC director Meredith Williams.
“We remain steadfastly committed to robust enforcement of hazardous waste laws, especially in our vulnerable communities where residents for far too long have disproportionally suffered from pollution.”
UK battery recycler to increase capacity by 50%
UK lead battery recycler Enva will increase its capacity by 50%, the firm announced on July 1.
The firm says it has invested in new material handling and processing lines and has upgraded its facility licences with the country’s environment agency to increase annual output and also allow other types of battery chemistries to be handled.
“Recycling batteries ensures valuable resources can be reused in more sustainable products and aren’t lost forever via landfill or incineration,” said battery business general manager Arvydas Pocevicius.
“This expansion of our operations represents a significant increase in the UK’s lead acid battery recycling capacity. It will result in fewer batteries needing to be exported for treatment, driving additional CO2 savings.”
Aqua Metals signs letter of intent with Taiwanese lead refiner
Aqua Metals, the lead battery recycling company, on July 29 said it had signed a definitive agreement with Taiwanese lead refining company ACME Metal Enterprise to use Aqua Metals’ equipment at a facility in Keelung.
“The agreement also defines a phased deployment of AquaRefining technology and provisions for ACME to work with Aqua Metals and one or more large battery manufacturers to develop a second methodology to produce oxide directly from AquaRefined material,” said an announcement.
“This can significantly improve economic costs, safety, environmental impact and streamline the link between battery recycling and new battery manufacturing.”
Effectively the two companies intend to develop a process to convert the briquettes formed with the AquaRefining technique directly into battery-grade lead oxide with the use of a ball mill. Aqua Metals has already, it says, converted briquettes into lead oxide using the Barton pot method.
Aqua Metals intends to begin shipping its ‘aqualyzers’ and supporting equipment to ACME during the next few months for phase one of the deployment, which is expected to begin operating by the fourth quarter of 2021.
The specific financial terms of the agreement will remain proprietary for commercial and competitive reasons, according to the two firms.
ACME Metal Enterprise is headed by Linus Lu, who took over in 1984. “This partnership allows ACME to expand its business relationships with large battery manufacturers and establish itself as the first green tech lead recycler in Asia,” he said.
The company’s main products are lead calcium and lead antimony alloys, which it began to market in 1993.
Li-Cycle signs deal with new JV to recycle battery scrap
Canadian lithium battery recycling firm Li-Cycle signed an agreement on May 11 with a General Motors joint venture to recycle scrap materials from battery cells.
GM and LEG Energy Solution have formed the JV ‘Ultium Cells LLC’, which will use a hydrometallurgical process to extract cobalt, nickel, lithium, graphite, copper, manganese and aluminium from dead batteries and process the materials to use in the production of new cells.
Having spent $2.3 billion on the new company, based in Ohio, US, GM says its facility will have an annual battery production capacity of 30GW. The firm has already posted dozens of jobs on its new website.
Re-iterating its company’s recycling technology as a more sustainable alternative to mining, Li-Cycle president and CEO Ajay Kochhar said the combined efforts of all companies involved would ‘be instrumental in redirecting battery manufacturing scrap from landfills and returning a substantial amount of valuable battery-grade materials back into the battery supply chain’.
“GM’s zero-waste initiative aims to divert more than 90% of its manufacturing waste from landfills and incineration globally by 2025,” said GM president of electric and autonomous vehicles Ken Morris.
Monbat joins European Battery Alliance
Bulgarian lead and lithium battery maker Monbat has joined the European Battery Alliance, it said on July 20.
Its accession to the alliance will enable it to open lines of cooperation for the development of leadacid battery technology with the application of nanotechnologies ‘improving exploitation characteristics and prolonging battery life-cycle, as well as creating an optimal environment for competitive manufacturing of lithium-ion battery systems for various transportation and industry purposes’, it says.
Monbat joins another 600 industrial and academic stakeholders in an alliance that seeks to build a pan-European battery industry to help the continent capture a booming global market that is estimated to be worth €250 billion ($296 billion) a year by 2025.
The EBA was set up in 2017 and is managed by EIT InnoEnergy, an EU-funded agency that was set up to accelerate the energy transition, and which focuses on three areas: battery storage, green hydrogen and solar power.
Monbat is the fourth largest producer of lead-acid batteries in Europe. It also owns the Germanybased EAS Batteries, which makes lithium-ion battery systems.
Ending lockdowns causes surge of demand for replacement car batteries
A leap in demand for replacement auto batteries that have died while cars have sat on people’s drives during national lockdowns has led to a surge for replacement batteries as restrictions have lifted — and an ensuing hike in lead price rises, reported Reuters on July 6.
Commodity analyst firm Wood Mackenzie predicted the demand for lead needed in replacement car batteries would rise by almost 6% on 2020 levels to 6.5 million tonnes in 2021, similar to pre-pandemic levels.
Lead hit its highest price since July 2018 at $2,344 a tonne on July 12, according to the LME, although it had dropped to around $2,300 on July 13 (see analyis on page 6).
According to Reuters, stocks of lead in warehouses registered with the London Metal Exchange were down 11,000 tonnes in the first four months of 2021 compared with 2020, when they held 30,000 tonnes.
Shortages were felt most acutely in the US automotive sector, which in turn drove up global prices.
Quoting Asia Metals, the agency said part of the reason behind shortages was tight concentrates — which ‘can be seen in treatment charges paid by miners to process concentrate into refined metal, dropping to their lowers since September 2019 at $50 a tonne’.

Stryten Manufacturing joins BCI and CBI associations
US lead-acid battery maker Stryten Manufacturing joined two leading lead battery associations — Battery Council International and the Consortium for Battery Innovation — in June.
Announcing it had joined Battery Council International on June 24, the firm said membership would ‘help advance critical issues in the lead battery industry, including the role of lead-acid batteries in energy storage, industry collaboration, technology innovation, lithium battery safety and sustainability’.
“Our industry is at the forefront of some of the biggest technology innovations that will change how the world operates,” said Stryten CEO Tim Vargo.
“BCI and its members do important work in shaping the future of energy storage and we’re ready to roll up out sleeves together to tackle new challenges.”
On June 29 Stryten said it had joined the Consortium for Battery Innovation and Vargo said that the partnership would help ‘not only provide innovative solutions to meet our customers’ evolving needs, but also set new standards for safety, sustainability and performance that will help meet the ever-increasing needs of the entire energy sector’.
The lead battery manufacturer, which also owns the motive power arm GNB Industrial Power, was formally formed in August 2020.
Watt-Flex® heaters have a patented split-sheath design that eliminates costly BORE SEIZURE. Continuous coil technology offers the longest lasting, most even heat used in:
- GRID CASTING and FORMATION - COS DIE and LEAD PUMP - COVER SEALING PLATEN
It's time you switched to Watt-Flex® cartridge heaters.
DaltonElectric.com 978-356-9844
ALL YOU NEED
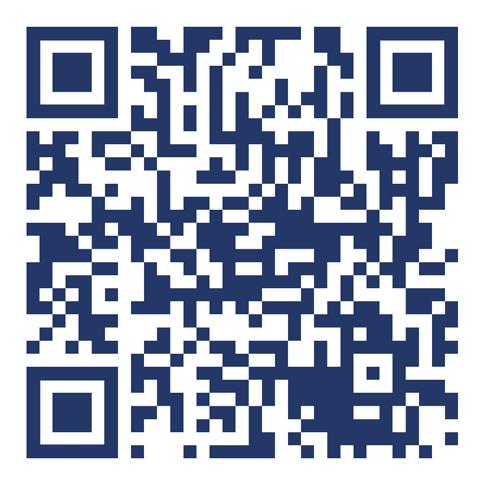
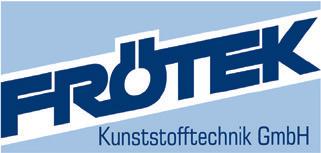
CBI and BCI produce ‘call to arms’ report for battery industry
Battery Council International and the Consortium for Battery Innovation in a report released on July 14 have called on the battery industry to work on key areas of research to cement lead batteries’ place in the future of energy storage.
The Lead Battery Grand Challenge Executive Summary is a roadmap that identifies 13 ‘work areas’ under three specific headings: Lead Battery Science Research; Supply Chain Issues; and Energy Storage System Demonstrations.
The paper, which focuses on the US industry, calls on lead-acid battery makers, the US Department of Energy and national laboratories ‘to partner on collaborative research that takes science from the laboratory to the marketplace’, BCI executive vice president Roger Miksad said.
“The lead battery industry believes that by using its experience in combination with the scientific skill and expertise of the DOE’s national lab system it can yield significant performance gains that could double, or provide even greater advances to, cycle life and energy density,” he said.
“This would further cement lead batteries as the only energy storage solution with intrinsic safety measures, that is highly sustainable, manufactured domestically, and meets the techno-economic needs of the US utility sector for decarbonization and distribution of the US grid.”
The report was released on the same day that DOE secretary Jennifer Granholm announced the department’s goal of reducing the cost of grid-scale, long-duration energy storage by 90% within a decade.
The ‘Long Duration Storage Shot’ was one of the targets set in the DOE’s Energy Earthshots Initiative, which also includes $52.5 million spending on hydrogen technology.
“We’re going to bring hundreds of gigawatts of clean energy on to the grid over the next few years and we need to be able to use that energy wherever and whenever it’s needed,” Granholm said. “Cheaper and more efficient storage will make it easier to capture and store clean energy for use when energy generation is unavailable or lower than demand.”
BCI said: “The nation’s electric power industry depends on a wide spectrum of technologies — including lead batteries — for functions ranging from back-up power supply during system disruptions (such as those seen in Texas last winter, when power was out for days, and the wildfire season in California, which is currently threatening to knock out critical power lines across southern Oregon) to facilitating the integration of power from variable resources such as wind and solar to the electric grid.
“A resilient infrastructure needs to have a diverse range of energy sources and given its unique features, lead batteries must be a key part of that mix.”
Lead battery makers face shortage of lead supply
Lead prices and stock shortages have become a cause of concern for battery makers as demand picks up following a year and a half of lockdowns, Reuters reported on August 9.
In London after reaching a threemonth high of $2,412.50/tonne on August 4, lead prices dropped to $2,275 before rising slightly to around $2,325 on August 10, but LME stocks are ‘super low’ with the physical supply chain ‘super stressed’, according to Reuters.
“All the world’s lead seems to be in China, where warehouses are full to bursting,” said the news agency. “Some of that surplus should be seeping out through the arbitrage window but so far there has been little sign of movement.”
LME stocks total 58,500 tonnes, Reuters says, down by almost 75,000 tonnes on the start of 2021.
In Europe, supplies have been hit by flooding at Germany’s Stolberg primary lead smelter, which has declared force majeure after devastating floods, causing it to halt shipments by at least a month.
And in North America, reduced operations at Canada’s Teck Resources’ Trail smelter, due to poor air quality caused by wildfires, are adding to supply issues.
“China is swimming in excess lead and the high SHFE price encourages smelters to keep making it and dumping it into warehouses to trouser the cash,” said Wood Mackenzie principal analyst, lead markets Farid Ahmed. “The options are that China starts exporting refined lead to the West where it’s needed, but this depends on the arbitrage window.”
Because the cost of local lead is usually far lower than refined lead imports, which are priced at its LME value plus premium, with import duty and VAT on top, it does not usually make sense for China to export it to the US, Ahmed said.
North America also has an issue with importing the batteries themselves because of congestion at the Los Angeles and Long Beach ports, as well as rail and truck networks further on, media reports say.
“Together, the two ports account for over one third of these imports,” says Ahmed. “But they are experiencing near-record delays, with dozens of ships anchored off the coast waiting for a slot to dock and unload. Some ships have been waiting offshore for weeks.”
Remy Battery completes first article testing of military batteries
Remy Battery has completed the first article testing of a $43 million US Department of Defense contract to supply 83,000 batteries a year for three years.
There are also two one-year option years to provide the 6TL batteries, which were partly chosen because they come in Remy’s FreshStart packaging, a finalist entry in the 2018 BCI Innovation Awards.
The packaging is specifically for dry-charged batteries, which means no excess chemicals need to be stored, reducing hazmat shipping costs and allowing battery activation by a single person.
Along with the dry-charged battery, FreshStart contains individually packaged portions of the electrolyte required for each cell.
Passing the testing means Remy can begin shipping the batteries to the government, which should begin imminently.
“We’re excited!” said Remy’s government sales manager Kevin Fleischman. “The US military has certain specifications that varied from any 6TL offered in the commercial market and we understood this.
“We’ve worked very hard with the battery plant and the DLA to see that our battery meets the expectations of the US government’s requirements and after two years, passing the first article testing was the last hurdle before we begin shipping.
“At three to four truckloads a week, now the real work begins!”
Eurobat endorses EU climate policy
European battery organization EUROBAT said it welcomed a climate and environmental policy launched by EU policymakers on July 14 as ‘an important milestone on the path to net-zero emissions’.
The EU’s package — coined ‘Fit for 55’ to express the aim of reducing car CO2 emissions by 55% by 2030 — is part of the bloc’s European Green Deal, in which all 27 member states will work with industry to achieve the reduction.
“Overall, the package strengthens eight existing pieces of legislation and presents five new initiatives, across a range of policy areas and economic sectors: climate, energy and fuels, transport, buildings, land use and forestry,” the summary says.
“Energy use accounts for 75% of the EU’s emissions, so the transformation of our energy system is central to our climate ambitions. Saving more energy and using more renewables in the energy we do use is a key driver for jobs, growth and emission reduction.”
The package comes seven months after the EU published its draft Battery Regulation, which was broadly welcomed by EUROBAT and the lead battery industry, despite concerns that it was too complicated and would be over-regulatory.
“All battery technologies have a critical role to play if the EU is going to meet its 2030 and 2050 emissions reduction targets and deliver decarbonization across the economy,” said Rene Schröder, EUROBAT executive director.
“We look forward as an industry to working together with policymakers to ensure that this package of legislation, alongside the new Batteries Regulation, provides the European battery industry with the strong legislative foundations it needs to help the EU deliver on its promise of a carbon neutral society by 2050.”
EC partners battery association to strengthen value chain
BEPA, the Batteries European Partnership Association, on June 23 signed a memorandum of understanding with the European Commission to launch a €925 million ($1.1 billion) programme aiming to develop a ‘competitive and sustainable industrial battery value chain’.
BATT4EU will be run under Horizon Europe, a research and innovation framework that comes under the European Union. This will provide the funding that will go towards ‘research and innovation to develop a variety of differentiated technologies that will result in a competitive, sustainable and circular European battery value chain’.
The EU recognizes it has fallen behind Asia in the global battery race. Some analysts say Europe is around a decade behind the top Asian players.
“The demand for batteries is continuously growing, however, the production of batteries is still highly concentrated in Asia: for instance, less than 1% of global lithium-ion battery cells are currently manufactured in Europe, compared to over 90% in Asia,” the announcement says.
“Europe needs to catch up in this important area and it will do so by putting environmental sustainability and circularity at the heart of its battery production to address the ambitions of the green energy transition.
“By mobilizing €925 million, the partnership will boost research and innovation to develop a variety of differentiated technologies that will result in a competitive, sustainable and circular European battery value chain.”
ILA signs up New Chunxing as first Chinese member
The International Lead Association on May 4 announced it had signed up its first Chinese company, the Jiangsu New Chunxing Resource Recycling Company, which is based in Pizhou, midway between Shanghai and Beijing.
The company was founded more than 40 years ago, it says, with ISO 14001 and 45001 certification achieved in 2013, according to chairman Yang Chunming.
“We are delighted to welcome New Chunxing as our first Chinese member and look forward to collaborating in our work to promote the responsible management of lead worldwide,” said Andy Bush, managing director of ILA.
New Chunxing was the target of protests in Victoria, Australia last year, when locals opposed the company’s proposed lead battery recycling plant in Latrobe Valley, where 50,000 tonnes of used batteries a year are to be processed.
The company rejected the fears, saying emissions would be far lower than EPA standards — and in September, the state approved the construction of the plant.
In 2008, Chinese newspaper reports said a facility owned by the company, then named the Chunxing Alloy Group, was responsible for the poisoning of several children in the village of Xinsanhe, in Pizhou. The plant was forced to relocate to a nearby industrial park.
Speaking to the ILA, Yang Chunming said the company was committed to contributing to China’s circular economy and was looking forward ‘to working together with ILA to positively impact the sustainability credentials of the lead battery industry in China’.
Exide unveils new-look carbon cutting batteries
Exide Technologies, the Europe-based lead-acid battery maker, unveiled a new design of its Premium battery on May 4, which it says will cut carbon emissions and water use, as well as speed up recharging.
The new design will also be introduced across the rest of Exide’s conventional batteries, the company says.
One of the key selling points of the new batteries is that their boxes and lids are made from recycled plastic as opposed to virgin plastic, which is where the emissions and water are saved.
Using data from the plastic manufacturing industry and various independent university studies, Exide has calculated that this will lead to savings of 2,700 tons of CO2, eight million litres of water and 1.2 million litres of crude oil in Exide’s manufacturing each year.
Another feature of the new Premium batteries is its Carbon Boost formula, which Guido Scanagatta – Senior Product Manager EMEA, describes as “a proprietary recipe for the optimal mix and application of different types and proportions of carbon additives to the negative active mass to provide the best possible result for the performance of our batteries”.
“We have been working with these carbon additives and validated their effects through testing (cycling, charge acceptance, chargeability, etc) for 10+ years and have vast R&D experience in this field,” Scanagatta says.
Production of the new design began in April, and the first deliveries have already reached customers, he says, adding that it will take time for old stock to be fully replaced throughout the supply chain.
Exide has two R&D facilities, nine production locations and three recycling plants in Europe.