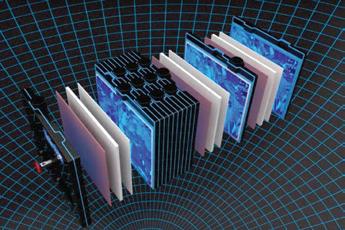
42 minute read
NEWS
Gridtential to develop pilot biplate line with Hammond and Wirtz
Gridtential Energy announced mid-July that it will partner Hammond Group and Wirtz Manufacturing to develop a pilot manufacturing line to produce the biplate at the heart of its bipolar battery at Hammond’s facilities in Indiana.
This, it says, will help simplify the production process for battery manufacturers trying to integrate the firm’s bipolar technology, known as Silicon Joule, into their manufacturing facilities.
“Together, the companies will develop and produce the biplate inside a Silicon Joule battery that greatly simplifies the production process for battery makers, combining time-consuming steps and saving the production cost of stacking and adding active materials,” said a Gridtential statement.
“Our 15 current development partners will be able buy biplates directly and incorporate them into their volume factory lines. The biplates will be the first readymade component for Silicon Joule-enabled batteries.
“The partnerships with Hammond and Wirtz will merge three production steps our partners would have to take into a single, ready-made product.”
Terry Murphy, CEO of Hammond Group, said: “We’re very excited about the potential bipolar configurations have for the lead battery industry. Bipolar batteries made by Gridtential as well as ABC work. This is a proven technology and huge leap forward bringing higher performance lead-based batteries to compete with lithium ion technologies.”
Gridtential CEO John Barton said: “Our readymade biplate solutions speed up the commercialization timeline for many of our partners, and we are targeting 2023 or 2024 for commercial production launch.”
Gridtential’s development partners have yet to solve the mass mechanization of its Silicon Joule, technol-
Barton: "Our ready-made biplate solutions speed up the commercialization timeline for many of our partners, and we are targeting 2023 or 2024 for commercial production launch.”
ogy, which deploys fragile silicon wafers into their high-volume lines.
In April 2021, Gridtential said it was ready to launch a series of AGM batteries produced on a prototype line at East Penn Manufacturing.
In November 2019 Gridtential said it was in the middle of what it called the ‘industrialization’ of its technology — effectively converting what can be done manually into automated processes to achieve the costs and process control such advanced batteries will need.
The first part, high-speed precision pasting onto a carrier rather than a grid, had then been accomplished using pasting tools developed by Wirtz Manufacturing.
In October 2019, the firm presented a manual assembly of the battery at Crown Battery to MAC Engineering, Sovema Group, TBS Engineering and Wirtz. The objective was to let mainstream equipment companies see first-hand the components and sequencing needed in planning a highspeed assembly line.
ABC, Monbat unveil bipolar mass production plans
Advanced Battery Concepts and Monbat announced plans on June 9 to develop a commercial bipolar battery for mass production in an investment deal worth around €16 million ($17 million).
The partners said they were aiming to design a battery based on ABC’s GreenSeal technology for production at a future 1GWh Monbat facility to be built in Bulgaria.
The announcement came after ABC said in December 2018 it had given licensing rights for its GreenSeal technology to Monbat.
Under the latest agreement, in the first stage of their development program, ABC will produce the so-called ‘Alpha Samples’ of Block B batteries at its plant in Michigan.
Block B is a 48V, 32Ah industrial battery aimed at telecoms and BESS applications.
The batteries will be delivered to existing Monbat clients and special projects requiring BESS for on-site deployment — which the firms say will supply the data needed for future mass production.
Monbat says it has intensively tested prototype Block B batteries since 2019 in its certified testing laboratories.
Ed Shaffer, founder of ABC, said: “Monbat’s aggressive adoption of the GreenSeal technology for next generation products is important for more than just economic reasons.”
While the bottom-line results are important to Monbat’s business, additional benefits for both sides include providing “environmentally, socially, and economically responsible” energy storage products and solutions, Shaffer said.
Monbat CEO Viktor Spiriev said the company was “determined to become the first massscale producer of bipolar leadacid batteries in the world”.
Monbat says it is the fourth largest lead-acid battery producer in Europe. The company has manufacturing facilities in Bulgaria and Tunisia and recycling plants in Romania, Serbia and Italy.
On May 2, ABC received Battery Council International’s 2022 innovation award in recognition of the company’s Home Emergency Energy Storage System, which builds on the firm’s GreenSeal technology.
Industry steps up calls to drop ‘lithium hazard’ classification
Investments in both the lead and lithium battery sectors in Europe are now at risk, with a leading global chemicals producer warning that new draft proposals designating certain materials as ‘hazardous’ could choke-off financial backing at a crucial time for the EU.
European battery industry chiefs urged EU leaders on July 4 to reject draft proposals that could mean the lithium used in electric vehicle batteries is designated as a hazardous material.
EUROBAT and Recharge — the European industry association for advanced rechargeable and lithium batteries — joined battery material producers in writing a letter to express “deep concern” about the proposals by the European Chemicals Agency’s Committee for Risk Assessment* (RAC). Those proposals suggest lithium carbonate, chloride and hydroxide should receive a ‘Category 1A’ (a known human carcinogen) classification.
In the letter to top EU commissioners including Frans Timmermans, EU executive vice-president for the Green New Deal and Maroš Šefcovic, vice president for strategic foresight, industry leaders said “the scientific evidence is too weak and does not justify such a severe classification, which would have a major impact on Europe’s industrial goals for electric vehicles, batteries, and critical raw materials”.
The letter called on the European Commission to reject a Category 1A classification for the three lithium salts and urges a “re-evaluation at the scientific level”.
“An unjustified lithium salts classification will be a red flag that brings great uncertainty to companies looking to make long-term investments into European refining and recycling capacity, risking delays or different investment decisions towards competing markets,” the letter said.
The letter came after US-based speciality chemicals producer, Albemarle, told BI in June that the classification “would have a negative impact on the possibility of establishing lithium conversion plants in Europe”.
Albemarle said that if the proposals went ahead, “lithium carbonate and hydroxide could be processed outside of Europe and then imported, with negative effects on European strategic autonomy”.
“Inappropriate classification of the three lithium salts would create business uncertainty on which markets could be served, for which applications, but also on the industrial processes and which safety measures and plant requirements would apply, deterring investors from committing to Europe at a crucial time for the entire lithium value chain. Investors could therefore find other markets more attractive.”
“Similar limitations on investments would likely occur for the recycling of waste batteries and lithium-rich slag, due to regulatory uncertainty caused by this classification.”
Asked whether the proposals put the future of Albemarle’s Langelsheim plant in Germany at risk, the company said: “While the impact to our speciality customers is unclear at this point, we do not anticipate closure of Langelsheim.”
However, Albemarle said several of Langelsheim’s industrial customers do not use any other 1A substances and “would be forced to implement very strict rules to control the substance or look for alternatives, which are often not available or less performing”.
This would have a “direct impact on the plant revenue, which will already have to face higher operating costs compared to non-EU competitors due to the proposed classification”.
In March, a report published jointly by EUROBAT and industries representing manufacturers of batteries, ceramic frits and complex inorganic colour pigments, lubricants and greases and vehicles, said the three lithium salts were “fundamental and irreplaceable building blocks for the shift to electric mobility, the integration of renewables in the energy mix and more generally the achievement of the Green Deal objectives”. *The RAC’s ‘Opinion proposing harmonised classification and labelling at EU level of lithium carbonate, lithium chloride and lithium hydroxide’ are being considered by EU member states, with responses expected to be made later in the year.
Monbat managers acquire shares to secure near 21% group stake
The senior management team of Monbat has secured a 20.78% stake in the lead batteries group and pledged to further develop operations, Monbat announced in a June 28 regulatory filing.
The six-member management team buy-in acquired shares, for an undisclosed sum, that were disposed of by the European Bank for Reconstruction and Development (EBRD) and CEECAT Capital.
EBRD and CEECAT sold their shares in Prista HoldCo Cooperative, which had held the 20.78% stake in Monbat, to HoldCo Investment — which is indirectly owned via EKIP Monbat by the six managers.
A Monbat spokesperson told BI the six who share the stake equally are CEO Viktor Spiriev, board chairman Chavdar Danev, COO Peter Boyadjiev, procurator and Montana plant manager Peter Hristov, sales director starter battery division Vili Kamenov, and industrial battery division manager Bozhidar Nekeziev.
Monbat’s majority shareholders, who hold a 49% stake, continue to be Atanas Bobokov and Plamen Bobokov, the spokesperson said.
CEO Spiriev said: “Taking the next step and now being further vested as shareholders, the management of Monbat is fully committed to the future development of the group.
“During our involvement as management, Monbat has become one of the five largest manufacturers of lead acid batteries in Europe, and has also launched and expanded operations in Romania, Serbia, Italy, Germany and Tunisia.”
Ecobat silent on Stolberg future after sale to Trafigura Group
Nyrstar, the new operator of German lead production plant Stolberg, told BI on July 21 there would be a “continuous assessment” of the potential for future investment in the site — but declined to be drawn on the plant’s future.
Nyrstar’s parent company, the Trafigura Group, announced earlier in the month it had entered into a binding agreement to acquire Ecobat Resources Stolberg (ERS), which owns the Stolberg multi-metals processing plant.
Stolberg will be operated and managed by Nyrstar, a multi-metals mining and smelting company, which is a market leader in the production of zinc and lead metal.
But a Nyrstar spokesperson declined to discuss plans for the primary lead smelter site, which has been out of action since declaring force majeure last year after devasting floods in Europe.
Asked if there will be new investment in the site, particularly in terms of lead and lithium battery recycling, the spokesperson said: “The first priority will be the execution of the current business strategy for the Stolberg business.
“Going forward, we will assess on a continuous basis how this might evolve as we optimize opportunities and leverage synergies between the Nyrstar businesses.”
Stolberg has only produced about 100 kt/a for the past few years of full production, as it has been focused on optimizing the type of throughput rather than maxing out on tonnage, said lead com-
Campine acquires Recyclex for €3.5m
Belgian metals recycling and speciality chemicals group Campine acquired French lead recycler Recyclex on July 7 for around €3.5 million ($3.5 million).
The move came after the Paris Commercial Court approved Campine’s offer to take over Recyclex’s lead battery recycling plants in Escaudoeuvres and Villefranche-sur-Saône, as well as the plastics recycling company C2P — a Recyclex subsidiary also operating at Villefranche.
Campine’s bid was one of several announced on April 15 for parts of Recyclex, after the French group failed to organize an amicable debt restructuring process under an assets disposal program launched in May 2021.
None of Recyclex’s debt liabilities have been transferred to Campine and a ‘Recyclex SA’ entity will continue to exist under insolvency proceedings in a bid to agree a debt restructuring process — which the entity has said is still “very uncertain”.
Campine also plans to invest between €8 million and €10 million across all three factories over the next four years. Recyclex posted annual sales for 2021 of around €88 million for the assets acquired by Campine.
The two lead battery recycling sites employ around 60 and have a recycling capacity of some 90,000 tonnes of used batteries and 11,000 tonnes of polypropylene plastic waste.
The acquisition is a substantial upstream expansion of Campine’s battery recycling scope and adds recycled plastics as an additional material output, the company said.
Campine CEO Wim De Vos said: “This is a huge step for us. Campine is now really a multi-material recycling enterprise.” mentator Farid Ahmed.
“It refurbished and expanded its silver plant a few years ago and wants to get as much by-product value out of that, which means taking more complex feed which doesn’t work through the whole smelting process so quickly.”
Financial details of the acquisition, which is expected to be completed in the third quarter of this year, were not disclosed.
Nyrstar and Trafigura have a long history of rarely giving out information about their activities, be this commercially sensitive or not.
ERS was founded in 1848 and has one of the largest and most modern primary lead smelters in the world, according to Ecobat.
The facility has the capacity to produce 155,000 tonnes of lead and more than 100 different specifications of market-leading lead alloys and produce 130,000 tonnes of sulphuric acid.
Ecobat CEO Marcus Randolph said the sale was “consistent with our strategy to concentrate on our core business of battery recycling and represents a significant step in the rationalization of our portfolio”.
BCI calls for new standards for battery labels
Battery Council International urged US environment chiefs on July 11 to strengthen battery collection and recycling processes and to raise the standards of labelling for all battery chemistry products.
BCI’s call came in response to a June 9 request for information from the Environmental Protection Agency (EPA) on how to develop best practices for battery collection, recycling and labelling.
BCI has long campaigned for better practices governing the labelling and collection of lead and lithium batteries. The addition of lithium batteries into a lead battery breaker causes potential fatal explosions when sulfuric acid mixes with lithium.
However, BCI warned it would be “counterproductive to adopt guidelines or requirements that could interrupt the existing, extremely successful, and industryfunded retail collection network for lead batteries”.
BCI said improved labelling would reduce the cross-contamination in recycling that leads to safety hazards, increased processing costs, and reduces the quality of recovered materials.
The trade body said all batteries, regardless of chemistry, should have labels “with a consistent and simple marking to encourage and aid recycling”.
On the lead battery industry’s recycling record, the EPA acknowledged that lead acid batteries “are manufactured with antimony, a critical mineral, and are currently recycled at a high rate”
The EPA stressed that its focus was on improvements for battery chemistries that have a lower recovery level of critical minerals.
ACE Green Recyling to produce US lead in 2023 says VP Ahmed
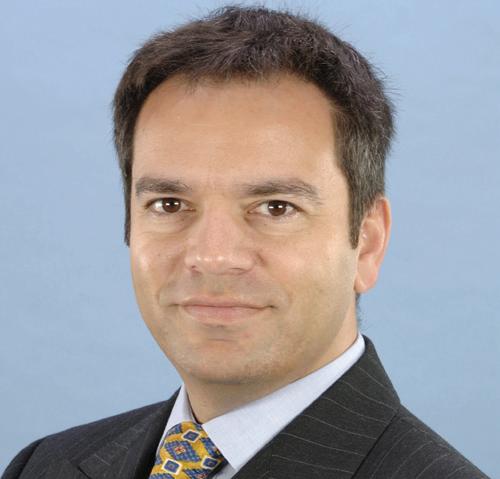
Lead analyst Farid Ahmed, the newly-appointed vice president of global strategy and business development for ACE Green Recycling, has told BI the company is on track to produce refined lead in the US towards the end of next year.
Some industry commentators say that the hydrometallurgical process for battery recycling is fraught with potential commercial and technical difficulties, making such projects unfeasible (see Batteries International issue No.121).
However, the lead and lithium batteries recycling company ACE expects production to start at the plant it is building in Texas around the fourth-quarter of 2023, says Ahmed (pictured) — until recently an analyst with Wood Mackenzie.
And Ahmed said he looked forward to making a “bigger contribution to the sustainability and perpetuity of the lead industry while also gaining a footing in the lithium-ion sector”.
ACE unveiled plans on May 10 to build and operate what it claims will be an “electric-powered, emissionfree” lead and lithium batteries recycling facility in Texas.
To date, the US-registered company has been cautious about releasing details of the technology it has developed, which Ahmed said is with good reason. ACE lists five battery recycling projects on its website, including Texas, as “coming soon” but is starting to disclose information such as the projected annual recycling capacities of 100,000 tonnes of lead batteries and 20,000 tonnes of Li-ion batteries at its Texas facility.
“There is a delicate balance between having your IP and processes fully protected by patents and discussing processes openly,” Ahmed said.
“I have known the company for more than a year and I have seen their very detailed process mass balance models and scrutinising all that gave me the confidence to accept the offer to join the company. Its technology is built on sound foundations.”
ACE developed what it described as a small commercial plant in India, near Delhi, where Ahmed said customers saw the lead recycling facility in operation. “With the lead recycling process having been proven, the equipment has now been disassembled and a lithium recycling plant is being built there to demonstrate and optimise that technology,” Ahmed said.
Meanwhile, Ahmed said the firm is constructing equipment for two major Asian lead recyclers, which is due for delivery in August and slated to be producing lead by late September.
ACE recently established a UK entity, through which Ahmed works and which will focus on EMEA and global markets as the company develops partnerships in lithium battery recycling.
Ahmed has worked in and around the metals industry since graduating with a degree in Metallurgy in the mid-1980s and has specialized in lead since 1992.
He worked in R&D of platinum group metals for Johnson Matthey in the late 1980s and moved into lead in the early 1990s, working initially as a production metallurgist at Britannia Refined Metals before moving into the commercial sector of that company.
From the mid-2000s, he worked as a consultant to the lead industry, spanning the whole vertical sector from raw materials, production and processing to specialist sales, product development and market analysis. He joined Wood Mackenzie in 2015.
Banks in loans boost for Sunlight’s expansion plans
The Sunlight Group has received €275 million ($286 million) funding from Greek banks to support its expansion of lead and lithium production and R&D, the company announced on June 24.
Sunlight said the financial backing was in the form of seven-year loans and would form part of plans unveiled on May 11.
The loans will support plant upgrades and an expansion of production capacity and assembly lines in the company’s Xanthi facilities in Greece, Italy and in the US to boost output of both lithium ion and lead batteries and energy storage systems.
Sunlight said the loans would also enhance production of innovative motive power lead acid battery cells, with the installation of the latest automated production and assembly equipment.
The €275 million loan agreements comprise a €125 million syndicated loan from Eurobank and Alpha Bank (€62.5 million each) and a €150 million loan from the National Bank of Greece.
The announcement followed Sunlight’s pledge in September 2021 to spend €50 million to expand its lead and lithium manufacturing unit in Xanthi.

Metair expects strong lead sales despite Turkish economy woes
Lead and lithium group Metair reported strong production and sales of automotive batteries across the countries that mostly comprise its battery businesses, in a voluntary half-year update issued on July 20.
But the company told the Johannesburg Stock Exchange its formal interim results announcement will be delayed until around September 14.
This is because the firm will review figures in relation to its Mutlu Akü batteries operation in Turkey — which has been designated a hyperinflationary economy by the International Monetary Fund and leading accounting firms.
Mutlu Akü accounted for nearly ZAR4 billion ($237 million) of Metair’s turnover in the financial year ended December 31, 2021. The company said this represented about 31% of group turnover while 55% “was directly linked to hard currencies (US dollars or euros) through direct export and OEM sales, growing both volumes and price in the first half of 2022”.
Metair said it was reviewing the impact on its results of International Accounting Standard 29, which provides guidance on financial reporting on currencies of hyperinflationary economies.
However, Metair said its energy storage division, which includes Mutlu Akü, Rombat in Romania and First National Battery in South Africa, continued to perform well despite tough operating conditions including high energy and labour costs in Europe and Turkey.
Demand for lead acid batteries remained strong in all markets, especially in Turkey, despite the hyperinflationary economy classification for accounting periods ending on or after June 30, the company said.
Cumulative inflation rates in Turkey over a three-year period exceeded 100% as at April 2022,
Remy Battery acquires ‘friendly family-run rival’ Challenger
The Remy Battery Company has acquired Challenger Battery Service in a deal signed on May 31, the US-based family-run businesses announced.
Mike Moeller, Remy Battery’s president, said the firms “have always been friendly competitors, working together in time of need and respecting each other’s business”.
Remy Battery, which was established in 1931, specializes in predominantly lead batteries, cables, and battery accessories. Batteries specialist Challenger was established in 1952.
Remy Battery said the acquisition fitted into the company’s strategy of providing services at a community level. The deal allows “a long-standing local family-owned business in Waukesha, Wisconsin, to continue to service their community, which will now be led by another long-standing family-owned company that maintains the same values”.
Remy has two locations in Michigan’s Upper Peninsula, one in Wisconsin and Milwaukee, and now the Challenger site. Metair said.
Export sales are earned in hard currency and provide a natural hedge to limit the impact of foreign exchange volatility and inflationary pressures, Metair said.
Meanwhile, Mutlu Akü will be the driving force behind an expected overall group production total of around four million automotive batteries produced in the first half of 2022, Metair said.
The Turkish operation increased its export volumes by more than 40%, compared to the sixmonth period ended June 30, 2021, despite a 10day labour wage strike at Mutlu Akü during June, which has been settled.
Production from Rombat is expected to be at least 10% lower than the year-ago period, mainly because of “dampened consumer confidence” from the Russia-Ukraine conflict.
In results for the past full year reported on March 17, the company posted increases in revenue and operating profit as its businesses, which include automotive components, generated a 23% increase in overall revenue from the previous year to ZAR12.62 billion.
Pruitt reveals rise in BCI members’ battery sales
BCI members have reported total passenger car battery sales of nearly 99 million in 2021, East Penn Manufacturing CEO Chris Pruitt announced on May 2.
Pruitt told BCI’s annual convention in Florida — where he was re-elected as president of the US trade body for a second term of office — that the sales (OE and replacement) were a 43% increase over 2020, with AGM batteries up more than 28%. Other group sizes are in greater demand, he said.
“The past year was a year of recovery — from the pandemic and its economic impact,” Pruitt said.
“Our industry has fared better than most, thanks in large part to our strong domestic manufacturing base, and our strong domestic supply chain — including the key lead suppliers and recyclers.”
Meanwhile, Pruitt said BCI was pushing ahead for yet tighter blood levels for the industry.
“We want to reach a maximum universal 20μg/dL of lead in workers by 2025.”
Pruitt said that when this level is compared to the US Occupational Safety and Health Administration’s (OSHA) recommendation of 50μg/dL, it showed “how powerful a lead we are taking”.
In terms of federal legislative lobbying, Pruitt said BCI continued to actively engage with legislators on Capitol Hill.
“We are excited by the fact that the federal government has recognized that battery manufacturing is key to America’s success to achieve energy independence,” he said.
Lead industry welcomes Ghana action on batteries stewardship
The ILA said on May 3 it welcomed new procedures published by Ghana’s government to improve battery recycling operations in the West African nation.
The new standard operating procedures (SOPs) were developed in cooperation with organizations including the ILA, Battery Council International, EUROBAT and with the Sustainable Recycling Industries and the Material Stewardship Program of the global lead and lead battery industries.
Lydia Essuah, director of policy, planning, monitoring and evaluation at Ghana’s Ministry for Environment, Science, Technology and Innovation, said: “We will make low-quality battery recycling a thing of the past in Ghana. Lead acid battery recycling is a lucrative industry, so we expect all recyclers to meet the technical guidelines.”
Selina Amoah, a deputy director at Ghana’s Environmental Protection Agency, said the SOPs and technical guidelines had been drawn up to ensure they could be widely understood and implemented.
The SOPs would also serve “as an additional tool for regulators to promote sound practices in the sector, which will lead to reduction in the risks to the environment and public health”, Amoah said.
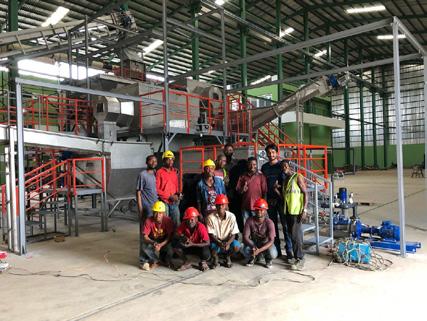
‘Facing challenges’
According to the ILA, improper recycling of lead acid batteries remains a problem in many low- and middleincome countries, causing pollution, with potentially serious impacts on the environment and human health.
ILA regulatory affairs director Steve Binks said: “We are positive about the developments and hope that the transition to a sound battery recycling industry will continue. Other countries face similar challenges, and we hope that the SOPs will not only be used in Ghana, but also shared with, and applied in other settings.”
The SOPs, which are available online, were developed over 18 months in a project coordinated by Sustainable Recycling Industries and experts from the Mountain Research Institute, the Ghana National Cleaner Production Center and the Oeko-Institut — guided by the Ghana’s EPA, Factory Inspectorate Department and other regional and international experts.
In 2020, a global alliance of lead and battery associations condemned all informal lead battery recycling in response to a report launched by the international children’s charity Unicef, on July 30, which said a third of the world’s children were victims of lead poisoning.
Unicef said in an interview with the Ghana News Agency in November 2021 that it would begin testing people — with a focus on children — for blood levels in the country.
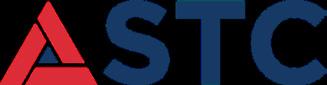
YOUR ITALIAN PARTNER FOR BATTERY RECYCLING AND LEAD PRODUCTION
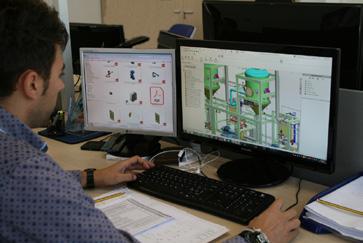
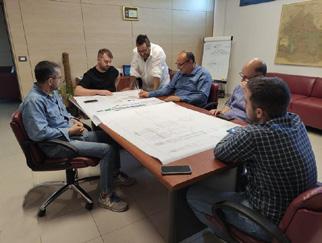
CUSTOMER SERVICE IS A KEY FOR ALL STC
ACTIVITIES TO FULFILL OUR CLIENTS NEEDS AND BUILD TOGETHER LOYAL AND
LONG-TERM RELATIONSHIPS
From simple clarifications to serious emergencies, STC skilled team is always available to provide advice through plant surveys or remote assistance. The “Problem-Solving” attitude and flexibility of STC Team is one of our most precious and distinctive skills. Among the others, we offer:
Optimization and improvement of existing processes pre-sales support project management equipment construction construction management after-sales services and spare parts management engineering services procurement management training of plant operators
R&D and laboratory services Contact our experts for inquiries and technical details at info@stcitaly.com
WE LOOK FORWARD TO HEARING FROM YOU www.stcitaly.com
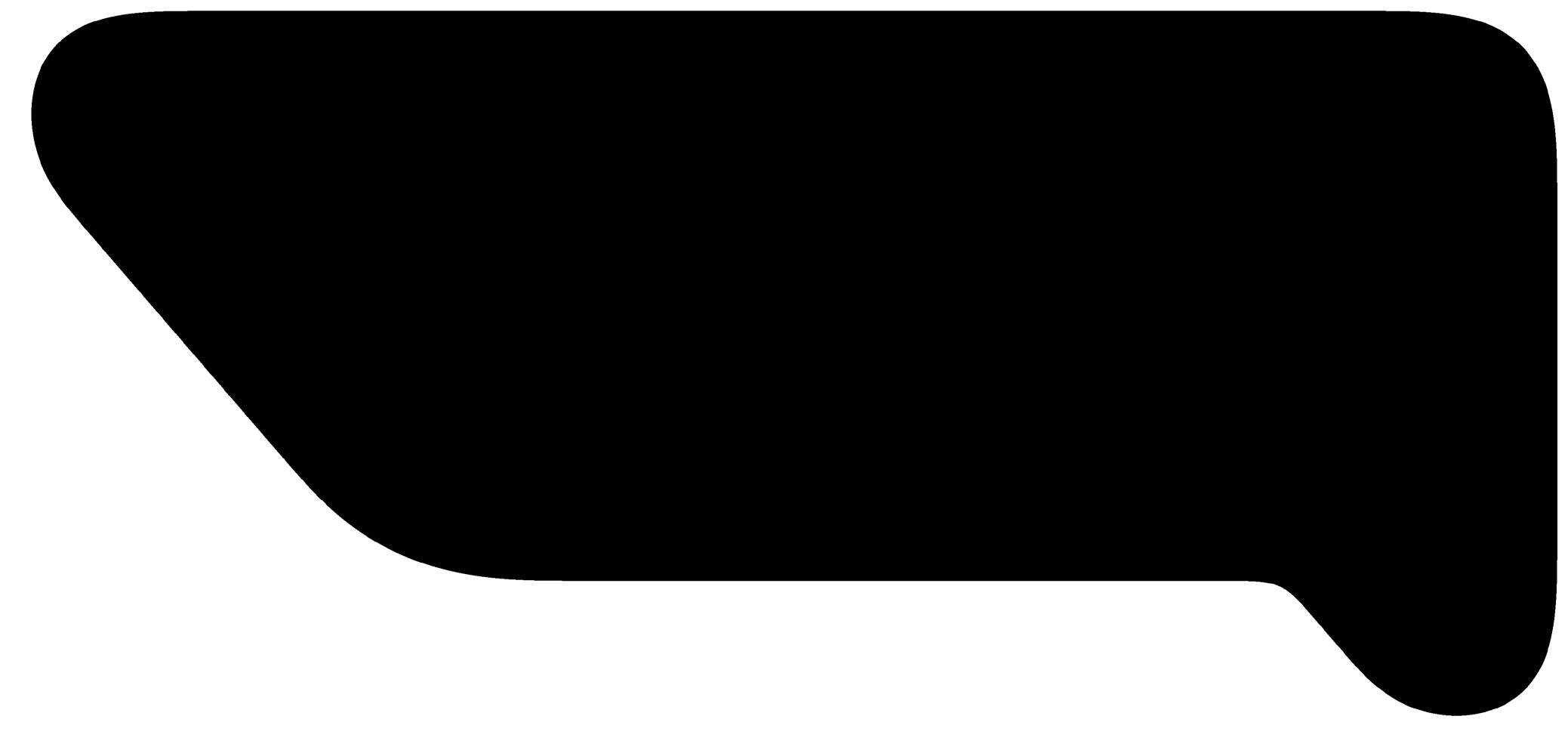

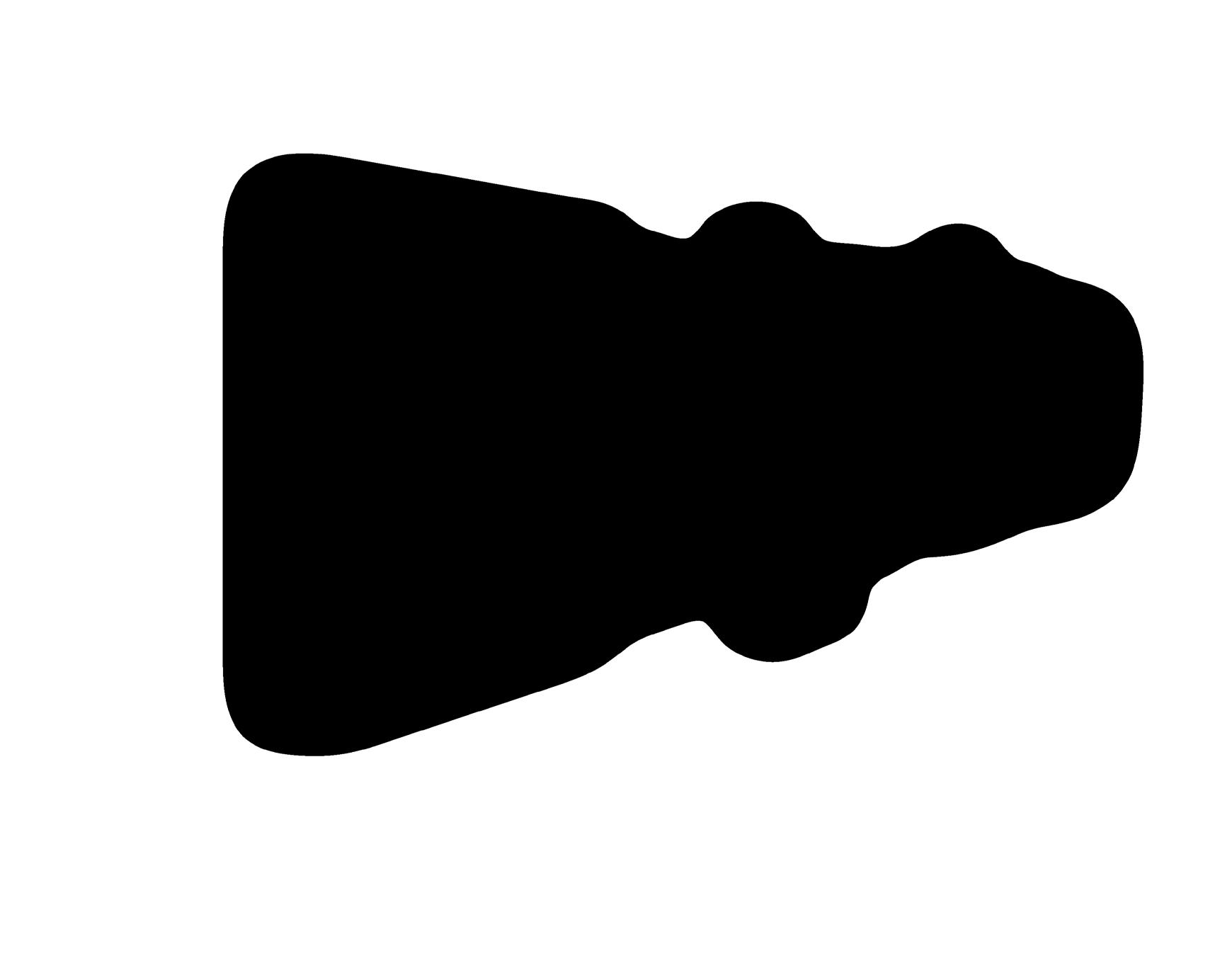
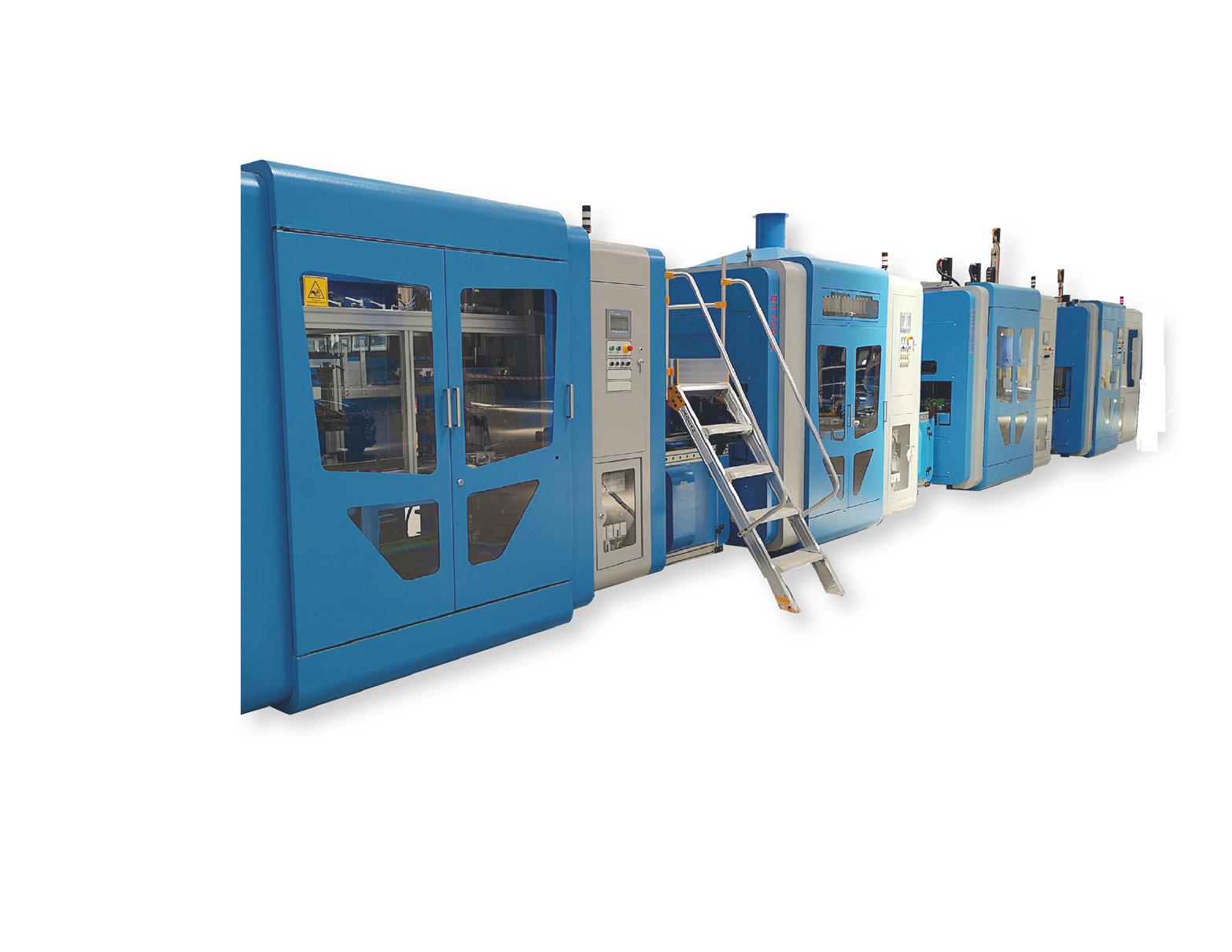

Volt Resources $2m share placement plans for graphite restart in Ukraine
Australia-based Volt Resources said on June 30 it had received firm commitments to raise $2 million in a share placement to help restart graphite production in Ukraine — and to continue producing lithium ion battery anode, alkaline and lead battery product samples for customer testing.
The funds would go to Ukraine’s Zavalievsky graphite mine, about 280km south of Kyiv, a processing plant and boost the export of graphite products to customers in Europe, Volt said.
The placement will also support the preparation of feasibility studies for a small-scale battery anode material production facility in the US, and a larger such facility that can be used as a “template design” for facilities in the US and Europe.
Volt has a 70% stake in the ZG Group in Ukraine and is focused on the exploration and development of its wholly-owned graphite and gold projects in Tanzania and Guinea.
Operations at Zavalievsky were suspended after Russia’s invasion of Ukraine on February 24, Volt confirmed in a regulatory filing on March 1.
Managing director Trevor Matthews said on June 30 the decision to recommence the graphite mine and processing operations was “a positive step forward for the Zavalievsky management and staff, local communities and businesses that depend on the graphite business for their livelihoods”.
Volt reported on February 3 that it was evaluating the electrochemical performance of its ultra-high purity non-spherical material for use as an expander in lead acid batteries. The company said work was being performed “under the close oversight” of a potential off-take partner — an unnamed lead battery company.
Volt says the development of non-spherical graphite products for the alkaline and lead battery markets will improve the economics of the firm’s planned battery anode material facilities in the US and Europe.
Battery industry leaders join forces to protect children
Four battery associations representing the entire lead battery value chain are joining the Protecting Every Child’s Potential (PECP) initiative. This was founded in October 2020 by battery manufacturer Clarios, Unicef and Pure Earth, a US non-profit organization to help protect children’s health from lead exposure globally.
The International Lead Association, Battery Council International, Association of Battery Recyclers and EUROBAT are joining PECP as part of their joint Material Stewardship Project.
All four associations will work to help ensure children in low and middleincome countries— where regulatory controls are often absent — are not exposed to lead.
They will provide assistance, including pro bono technical support, to help regulators and businesses in low and middle-income countries to adopt global best practices — building on existing projects around the world supported by the ILA and BCI.
The associations have already established a global programme to create a sustainable future by championing best practices in lead mining, lead production, lead battery manufacturing and recycling, and by encouraging responsible practices through supply chain management and product stewardship.
BCI executive vice president Roger Miksad said: “We believe the learnings of the North American industry can be adapted and shared with others through knowledge transfer to improve on-the-ground conditions in many targeted communities.”
ILA managing director Andy Bush said PECP was aligned closely with the association’s own material stewardship activities, “promoting the adoption of safe and responsible battery recycling in all regions of the world”.
EUROBAT executive director Rene Schroeder said PCP “brings the industry’s efforts for sound battery recycling to the next level and we are thrilled to be a part of the campaign”.
ILA to support Basel review of lead battery recycling standards
The ILA is to join an international review of battery recycling standards under the Basel Convention.
ILA’s special adviser, Brian Wilson, attended the 15th meeting of the Conference of the Parties (COP) of the Basel Convention in Geneva, which met from June 6-17 to discuss the need to update existing technical guidelines for the safe and environmentally sound recycling of used lead batteries.
At the COP, which was attended by more than 1,500 delegates from 200 countries, it was agreed that a special technical group would be set up to review and update the guidelines.
The group will also review the need to introduce and prepare guidelines for responsibly recycling other battery technologies.
The Basel Convention’s secretariat approved the ILA’s request to nominate Wilson to provide technical assistance to the group.
Speaking after the meeting, Wilson said: “There was universal support for the request to update the technical guidance for lead battery recycling. The technical contact group also noted differences between batteries in terms of their management, recycling and safe disposal including the fact that technologies for disposing of, or recycling lithium ion batteries are still emerging.”
Steve Binks, ILA regulatory affairs director, said the trade body’s work with the group was “an important part of our commitment to safe and responsible battery recycling in low and middle-income countries”.
“The Basel technical guidelines are the recognized standard and ILA will now contribute to updating them.”
GS Yuasa expands battery line
GS Yuasa said on June 15 it had launched a new EFB automotive battery as the Japan-headquartered firm moves to expand its European supply coverage to more than 500,000 vehicles.
The new YBX7012 startstop product marks an expansion of its YBX EFB range.
The company said the 12V L1 DIN case type battery provides 50Ah and 540A (EN) and is aimed at petrol and hybrid vehicles with a one litre engine.
Jon Pritchard, general manager of GS Yuasa Battery Europe’s automotive, motorcycle and industrial components division said: “Our OE quality Yuasa YBX automotive range is the UK market-leader and already provides the widest coverage of any brand on the market.
“For our customers, and the workshops they supply, this means they are able to fit batteries to more makes and models than ever before, especially as vehicles with advanced emission reduction systems, such as start-stop, become more prevalent in the park. The 7012 EFB alone will increase UK park coverage by around 50,000 vehicles.”
The announcement came after the company broke ground at the site of a new HQ and distribution centre in the UK on March 23.
Recycler Gravita invests in solar
Lead recycler Gravita India has installed solar energy systems with a total electricity generating capacity of 1,300kW across its manufacturing facilities in the country.
Gravita said on May 27 the total investment for the projects was Rs60 million ($772,000) and underlined the company’s commitment to achieving carbon neutrality throughout its operations.
The solar installations will provide up to 8% of Gravita’s energy needs and reduce carbon emissions by around 1,550 tonnes per year, the company claimed.
On May 12, Gravita revealed plans to use a byproduct of a new waste rubber recycling operation at its plant in Ghana as potential fuel for its lead and aluminium recycling business.
Gravita said in a regulatory filing that its Recylers Ghana subsidiary had started commercial production and recycling of waste rubber in the West African nation — and that it would use pyrolysis oil generated during the process as an alternative source of energy to support its lead and aluminium recycling there.
The company did not give details of how it would further refine the pyrolysis oil from the Ghana rubber recycling operation, which has an annual capacity of around 6,000 tonnes annually.
Lawmakers praise Stryten Energy for support of US energy policy
Stryten Energy has been praised for its “cuttingedge” role in support of US energy policy, during a tour of the company’s Kansas plant on June 20 by congressman Tracey Mann.
Stryten announced in March that it had formed two new divisions — Motive Power and Essential Power — focused on developing and producing multiple battery technologies, including lead, for the energy storage market.
Mann, who represents the district that is home to Stryten’s Salina plant, said: “Now more than ever, the US must utilize an ‘all of the above’ energy strategy that prioritizes American energy independence.”
“Stryten Energy is committed to solving the world’s most pressing energy challenges and enhancing America’s energy freedom — it is an honour to have such a forwardthinking and cutting-edge business in the Big First District.”
The Salina manufacturing facility, one of 12 Stryten sites across the continental US, produces transportation batteries that are sent directly to aftermarket retail locations and battery distributors.
Stryten’s vice president for corporate communications, Melissa Floyd, said: “Domestic manufacturers like Stryten are working hard to meet the current demand for energy storage in the US and we appreciate Representative Mann’s support for an energy strategy that prioritizes American energy independence.”
Mann’s visit followed an April 22 tour of the plant made by fellow Kansas lawmaker Sharice Davids.
Representative Davids, a key negotiator for the House of Representatives as Congress finalized a bipartisan supply chain package, said: “Stryten is a great example of the energy and supply chain solutions we should continue to grow here at home,” Davids said.
Exide Industries reveals site for ‘multi-gigawatt’ Li cells plant
Lead-acid batteries group Exide Industries has named the site in India where its Exide Energy Solutions (EES) subsidiary will build a multi-gigawatt lithium ion cells manufacturing plant.
Exide said EES entered into an agreement on July 26 for the 80-acre site at the Hi-tech, Defence & Aerospace Park, in Karnataka state, where it will build the plant in collaboration with China’s SVOLT Energy Technology.
Exide indicated earlier this year that it might be about to invest in the region of Rs6,000 crore — Rs60,000,000,000 ($793 million) — in building the greenfield facility.
EES has now executed a lease cum sale agreement with the Karnataka Industrial Areas Development Board for the site, Exide said in a regulatory filing on July 27.
The filing did not disclose financial details or say when work on the project might start but said the new plant would cater for “new-age electric mobility and stationary application businesses” in India.
India’s Ministry of Corporate Affairs issued a certificate of incorporation on March 24 for the EES subsidiary, which will coordinate development of the Karnataka plant and run future operations at the site.
Exide has said previously that SVOLT, which has its headquarters in China’s Jiangsu province, would support the setting up of the Karnataka plant on a turnkey basis.
In August 2021, SVOLT closed a series ‘B’ financing of Rmb10.28 billion (about $1.6 billion), following a series ‘A’ financing of Rmb3.5 billion at the end of February 2021.

Clarios, Natron Energy to team up for ‘world first’ in sodium ion production
Lead batteries giant Clarios and Natron Energy announced on May 4 they were teaming up to manufacture what they said would be the world’s first mass-produced sodium ion batteries.
Clarios’ Meadowbrook facility in Michigan will become “the world’s largest sodium ion battery plant when mass production begins in 2023” — placing the US at the forefront of sodium ion battery manufacturing, the firms said.
Natron will install new cell assembly equipment at Meadowbrook, with support from the US Department of Energy’s Advanced Research Projects AgencyEnergy (ARPA-E), but details were not disclosed.
The companies said the similarity in manufacturing requirements will enable them to use part of the Meadowbrook lithium ion facility for sodium ion production at a lower cost and faster time to market compared to building a new factory.
Meadowbrook was built as part of the American Recovery and Reinvestment program and has produced automotive lithium ion cells for the past decade.
Under the terms of the firms’ collaboration agreement, electrodes and large format cells based on Natron’s proprietary Prussian blue electrode sodium ion chemistry will be manufactured in an existing Clarios plant in Michigan.
Clarios’ vice president of technology, Craig Rigby, said: “As a world leader in battery technology, Clarios is invested in sharing its experience in the emerging battery space and to provide expertise in scale manufacturing
Amara Raja pledges ‘fast track’ for lithium project as firm joins CBI
India’s Amara Raja Batteries has pledged to “fast track” its development of a customer qualification plant for lithium cells while also building on its lead battery foundations.
The announcement came after the company became the latest member of the Consortium for Battery Innovation.
CEO and MD Jayadev Galla said in a regulatory filing about the company’s activities to the National Stock Exchange of India on May 20: “We are steadfast in our long-term strategy of energy and mobility leadership, and are building upon our strength to expand our global footprint for the lead acid battery business, while at the same time making good progress in the viable new energy technologies space.”
Executive director of the Andhra Pradesh battery maker’s lead acid business, Harshavardhana Gourineni, said the company had successfully overcome temporary hurdles in the supply chain in the past year and is now “well set to make the most of new opportunities”.
Amara Raja has been involved in the development and production of improving lead battery technologies since it was established in 1985.
The company announced in February 2021 that it would begin work on developing lithium ion cells. for advanced technologies.” In September 2020, Natron said it had achieved an Underwriters Laboratories (UL) listing for its BlueTray 4000 battery design, which uses Prussian blue chemistry and which was released in 2021 targeting the telecoms
UK launches critical minerals supply plan The UK has joined a growing list of nations to issue a critical minerals alert, warning on July 22 that its plans to become a ‘giga batteries’ producer supplying electric vehicles and energy storage systems could stall because of expected shortages of raw materials.
Business, energy and industry minister Kwasi Kwarteng said in a new policy paper launching the UK’s first ‘critical minerals strategy: “Global demand growth for certain minerals, driven in many cases by decarbonization targets, could outstrip supply chain capacity, which will struggle to expand quickly enough owing to long lead times for mine development and mineral processing.”
Kwarteng cited data from Benchmark Mineral Intelligence indicating that “rising demand has caused lithium prices to increase nearly 400% year-on-year as of May 2022”.
Cobalt, lithium and vanadium are already on a list of UK-designated critical minerals published by the government in late 2021 and now nickel has been put on a “watchlist”, Kwarteng said.
Emera and Novonix Deliver microgrid battery prototype
Emera Technologies and Canada-based Novonix Battery Technology Solutions announced on June 6 the delivery of a customand data centres market.
Last November, Clarios signed a deal with the American KULR Technology Group “to develop the manufacturing and re-use of lithium ion batteries and their chemical elements in the US”.
designed microgrid battery prototype.
The firms announced a partnership to work on the project in February last year.
Novonix has developed the battery to support Emera’s residential BlockEnergy microgrid system, which was launched in Florida in October 2020 as the “first utility-owned community microgrid platform”.
The microgrid connects homes in a shared energy network, enabling rooftop solar power to be stored and distributed to the entire community through smart distributed controls.
Working with research partner, the US Sandia National Laboratory, the companies say testing of the new battery should be completed later this year.
Novonix co-founder and CEO Chris Burns said work on the project opens the gateway to exciting new possibilities for a cleaner, more reliable power grid with renewables being produced, stored and consumed within local communities.
Novonix was created from work by Jeff Dahn’s research group at Dalhousie University that focuses on lithium ion battery research and works exclusively with Tesla.
However, a Novonix spokesperson would not say whether the new battery is lithium based and said testing procedures would not be revealed at this stage.
Vernon clean-up saga enters next phase
A ‘Superfund’ listing request — to potentially unlock millions of dollars in federal funding to support clean-up activities at the former Exide Technologies recycling facility in Vernon — was issued by the California Environmental Protection Agency (CalEPA) on July 1.
CalEPA is calling for the site and its surroundings to be added to US Environmental Protection Agency’s (EPA) ‘National Priorities List’, which is also known as the Superfund.
California governor Gavin Newsom said the move was designed to “aggressively pursue federal funds” available under the Biden administration’s Bipartisan Infrastructure Law, which was passed by Congress earlier this year. This provides $1.5 billion to revitalize brownfields across the US plus additional funds to protect human health and the environment.
CalEPA secretary Jared Blumenfeld said: “Vernon is one of the most contaminated lead sites in the country. A Superfund listing would bring federal resources and expertise to the table that have frankly been missing for too long.”
California has allocated $700 million for the facility and residential clean-up to date and has remediated nearly 4,000 properties, CalEPA said.
Work by California’s Department of Toxic Substances Control (DTSC) at the former Exide site is scheduled to continue until the autumn of 2025, at which point 6,000 properties and additional facilities will have been cleaned up.
However, the DTSC estimates completion will cost an additional $150 million, for which there is no funding in place, CalEPA said.
Meanwhile, industrial properties surrounding the facility have yet to be investigated and their cleanup costs are unknown, the agency said.
The Vernon site, five miles south of downtown Los Angeles, has been shuttered since 2014. It had been operated by Exide as a lead battery recycling and smelting facility for almost a century, producing around 110,000 tonnes of lead a year.
The DTSC said last January that it had hit its target of removing the soil from 3,200 properties in the area around the old Exide facility by the end of 2021.
Banner marks 85 years in batteries business
Banner Batterien has marked 85 years in the battery manufacturing business with an anniversary celebration for staff.
More than 500 employees, including some 200 from the company’s 13 sales organisations, joined the event at Banner’s headquarters in Leonding, the firm announced on June 14.
The anniversary celebration was the first major gathering of staff since the lifting of pandemic restrictions and a number of long-serving members of the workforce were honoured during the event.
Banner’s roots branch back to when company founder, Artur Bawart, launched a small business in the 1930s and Banner became involved in the battery business in 1937.
Today, the firm is Austria’s only car battery producer and counts itself as being among the industry’s five largest manufacturers in Europe.
The company owners and cousins are commercial CEO Andreas Bawart and Technical CEO Thomas Bawart.
On May 24, Banner reported an uptick in sales to €286 million ($307 million) in annual results after what it said was a challenging year.
New Italy AGM line for Ahlstrom-Munksjö
Fibre-based materials producer Ahlstrom-Munksjö said on April 7 it had started production of an absorbent glass mat line in Italy.
The Finland-headquartered firm said the line is at its plant in Turin, where it has invested in additional manufacturing capacity for filtration and energy storage materials — although it did not give investment or production details.
The AGM line will serve applications where glass microfiber media is required, supporting AhlstromMunksjö’s expansion into industrial filtration as well as in supplying the lead batteries market, the company said.
Giuseppe Costa, vice president of filtration and performance solutions for Asia and EMEA, said the launch signalled a “a strong step into the energy storage market by bringing on-stream a platform which will be fully qualified for the manufacture of AGM media”.
EnerSys reports boost in annual sales
EnerSys reported a 13% increase in sales in annual results posted on May 25.
The lead and lithium batteries producer said net sales for the full year ended March were $3.36 billion compared to just under $3 billion in the year ago period.
EnerSys said the rise was due to a 10% increase in organic volume resulting primarily from strong demand and a 3% increase in pricing.
Sales in the motive power segment amounted to $1.4 billion — an increase of 17% over the previous year. Sales of energy systems, which combines enclosures, power conversion, power distribution and energy storage, increased by more than 11% to $1.5 billion.
Adjusted Ebitda was $340 million compared to $345 million previously, against a backdrop of inflation and supply chain disruptions.
CEO David Shaffer said key milestones achieved in fiscal 2022 included the launch and UL safety listing of EnerSys’ NexSys lithium ion batteries.
Shaffer said the company had also exceeded its capacity goal for its proprietary TPPL technology, where demand, he said, “continues to outpace our ability to supply”.
“We expect to benefit further from the strength of this demand as we make progress toward increasing capacity by an additional $200 million in fiscal 2023.”
On March 9, the EnerSys board announced a $150 million stock repurchase authorization, ahead of launching the company’s inaugural sustainability report on April 29.
Birla Carbon announces ‘milestone’ investment in capacity expansion
Carbon additives company Birla Carbon announced on May 31 it was investing in a combined production capacity expansion of 200 kilotonnes across key markets.
Birla said the expansion would cover markets in Europe, India, and China in support of rubber and speciality applications. The expansions should be finished by 2024.
The expansion plans follow the company’s May 16 announcement that its prices for all carbon black products manufactured in North America would increase by 15% from July 1.
Group director Santrupt Misra said the unspecified investment marked “another milestone in the transformational journey” of the company.
“Birla Carbon will continue to focus on building new capabilities and enhancing the availability of carbon black across key regions, further consolidating its global leadership.
“Whether it is unique, highly specialized processes to tailor materials for speciality applications, security of supply, or consistent quality… the new capacity will enable us to sustainably serve growth in a range of segments including tyres, rubber goods, plastics, coatings, and other speciality markets.”
In July, the company launched an online ‘virtual showroom’ — highlighting the diverse industrial usage of carbon black including in battery technology.
Birla has developed a range of performance conductive additives that are designed to improve the energy density, power density, and charging speed of lithium and lead acid batteries.
The company uses a virtual car to showcase the value and widespread usage of carbon black by examining its usage in the intricate parts of the vehicle.
Birla said the virtual showroom marks its foray into digital innovation to explain the usage of carbon black products, not just in battery technology but also in mechanical rubber goods, coatings, inks, plastics, and tyres.
The initiative followed the company’s announcement on July 14 that it had raised $50 million in the form of a ‘green loan’ to refinance a part of the capital expenditure incurred for tackling emissions at its North Bend plant in the US.
Remy Battery gets ISO 9001:2015 certification
Remy Battery Company, the Milwaukee-based battery firm in the US, announced on July 18 that it had been awarded ISO 9001:2015 certification.
ISO 9001:2015 is a globally recognized quality management standard developed and published by the ISO Organization.
The standard is based on several principles, including having a strong customer focus, the involvement of high-level company management, an outlined approach to processes, and ongoing improvement of this very approach.
“Remy Battery’s dedication to work towards ISO 9001:2015 accreditation demonstrates our commitment to our company policy of continually improving procedures, products, and services,” says Mike Moeller, president of the firm.
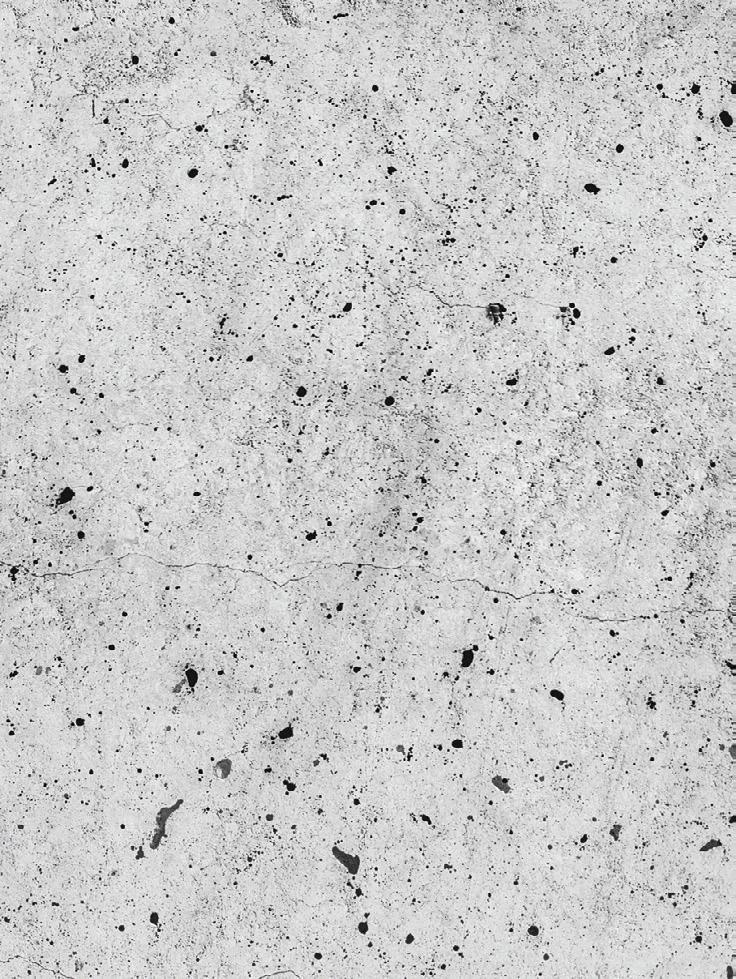
Watt-Flex® heaters have a patented split-sheath design that eliminates costly BORE SEIZURE. Continuous coil technology offers the longest lasting, most even heat used in:
- GRID CASTING and FORMATION - COS DIE and LEAD PUMP - COVER SEALING PLATEN
It's time you switched to Watt-Flex® cartridge heaters.