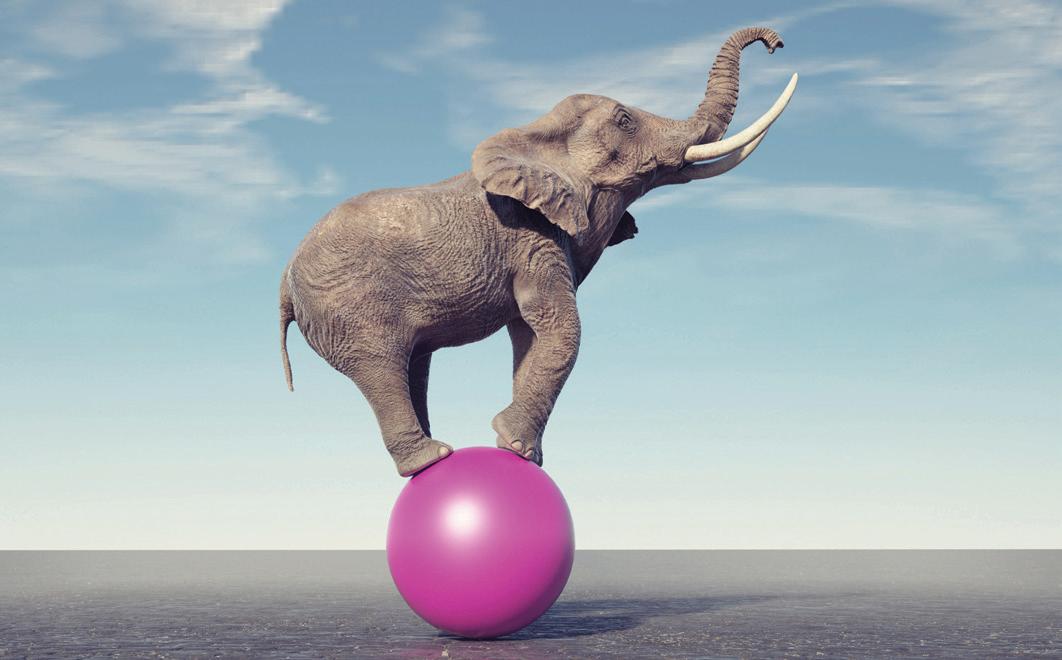
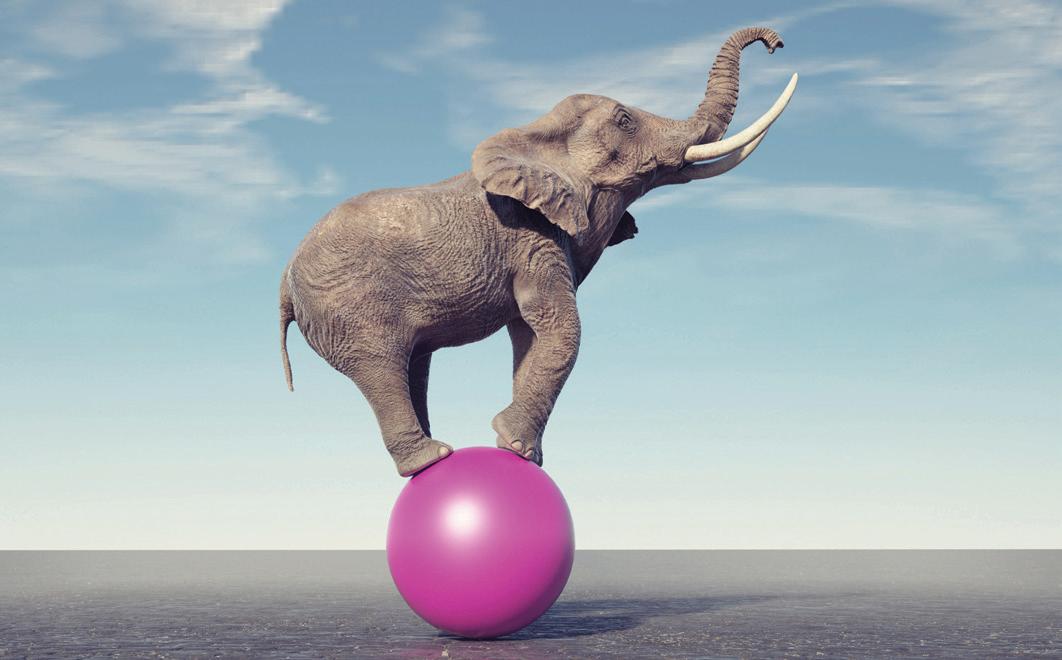
No Steam Required.Curing
Accelerate TTBLS Crystal Growth with Less Time and Energy Use

Improve your product AND your bottom line. Treated SureCure is a fundamentally better way to create TTBLS crystals, with more uniformity and more efficiency in, both, time and energy use, compared to steam curing and other methods. Battery manufacturing and performance will benefit from tested and proven enhancements like stronger plates, more-consistent curing, increased cycle life, and improved charge acceptance — all while providing verifiable savings.
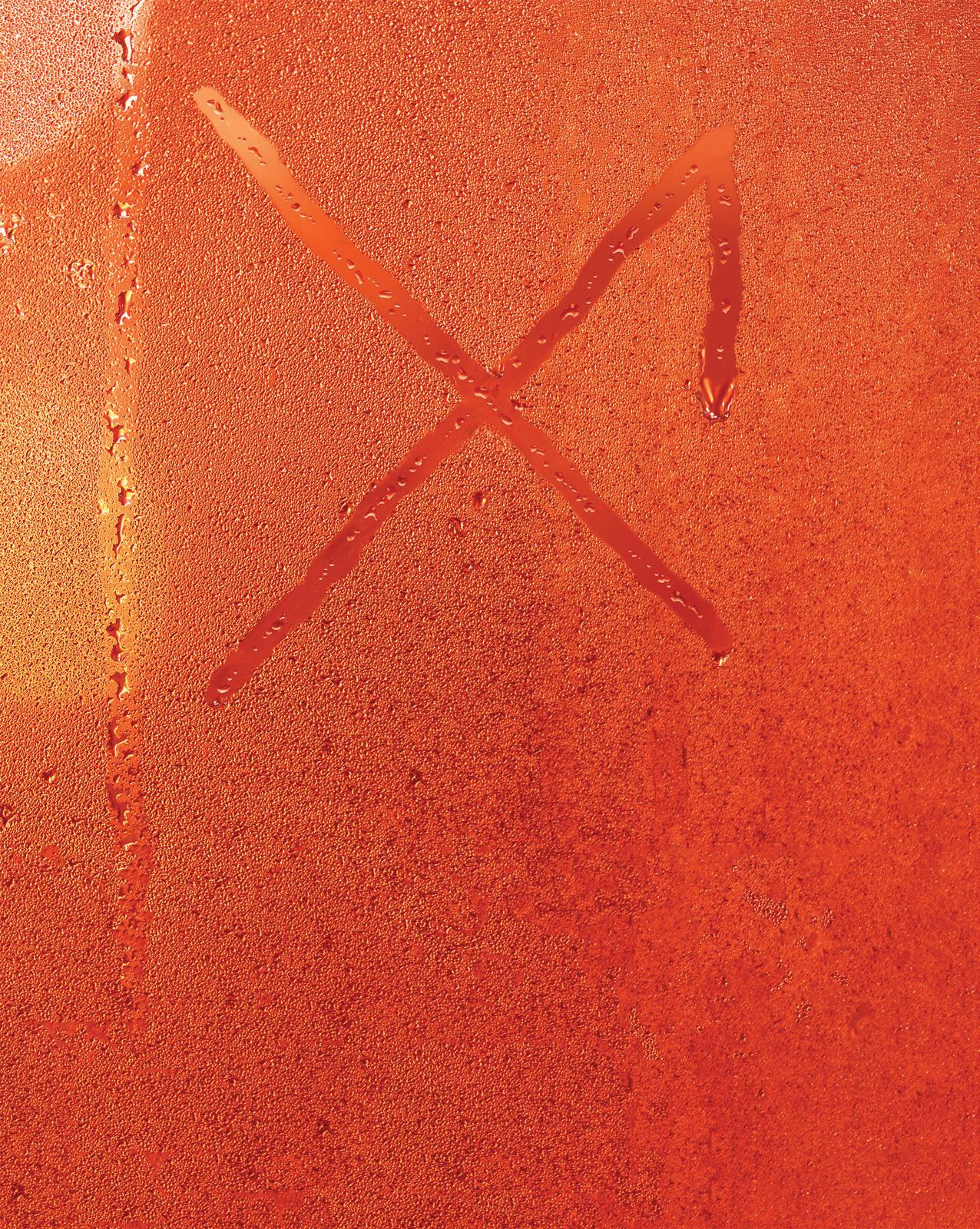
INDUSTRY NEWS Hammond Bolsters Asian Production Capacity With New Treated SureCure® Manufacturing Line
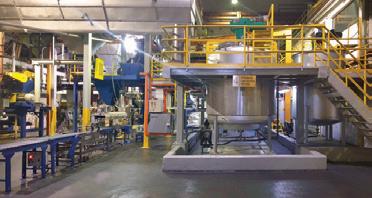
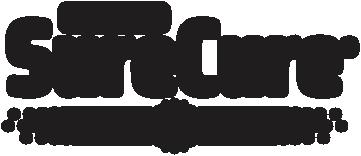
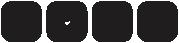
With full-scale operations of its North American Treated SureCure® manufacturing line underway, Hammond Group announced increased production capacity at its Malaysian plant. The facility in Kuala Lumpur is capable of making just over 4.1 million pounds of Treated SureCure® per year. Demand for one of its most effective additives had risen to such a degree that the company doubled capacity by bringing
production online in the US in early 2023. In addition to SureCure® products, Hammond Malaysia produces Advanced Negative Expanders tailored to assist with SLI, Deep-Cycle, PSoC and
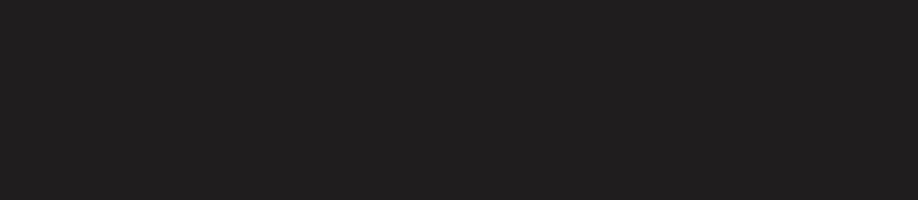
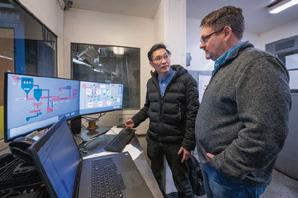
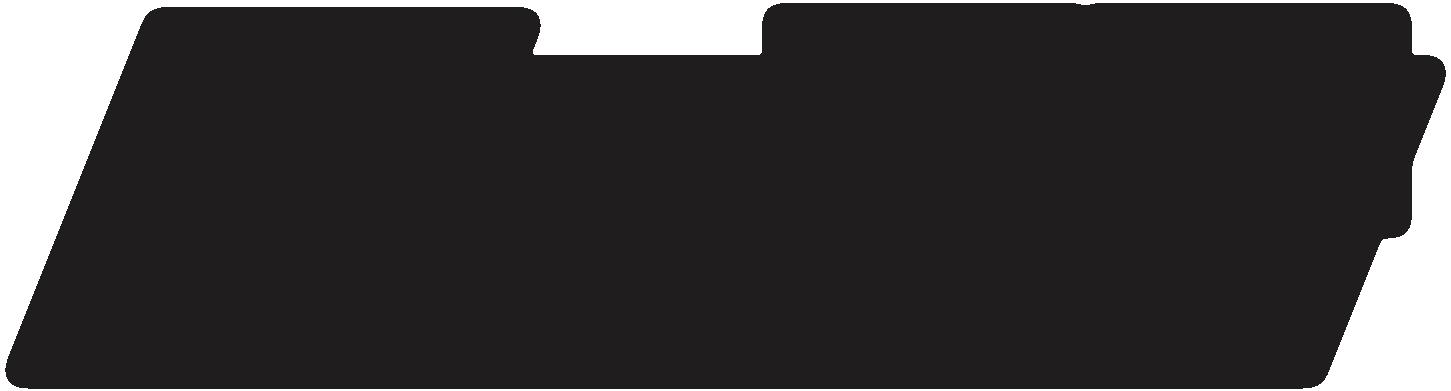
Energy Storage needs. The plant is ISO:9001 Certified and allows for quick turnaround on orders to customers throughout Asia. Read more at HammondGlobal.com/news.
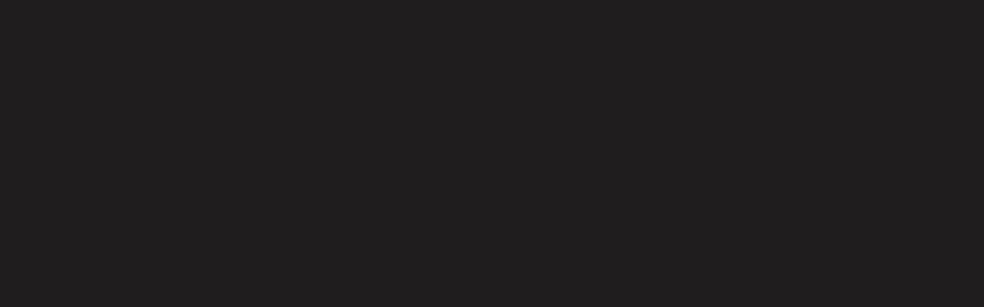
OBITUARY: 'A LIFE WELL LIVED'
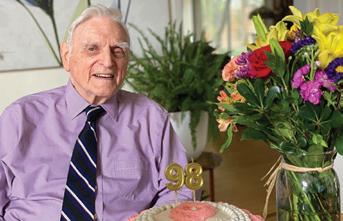
COVER STORY: ALL ARE WINNERS
JOHN BANNISTER GOODENOUGH
The father of the lithium ion cell, and one of the three figures that created today’s huge lithium battery business, died on June 25 a month short of his 101st birthday
A QUESTION OF BALANCE
For the last 15 years, the lead and lithium battery industries has been engaged in a war of words about their relative merits. But each has its virtues and places in the ESS spectrum
NEXT STOP SCOTLAND!
Flow batteries continue to make inroads into the energy storage landscape of the future. The recent IFBF discussions bodes well for next year's excursion in the Highlands
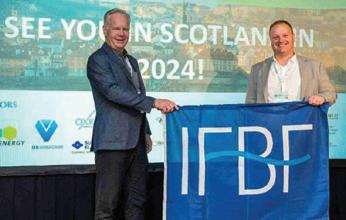
The last great myth of the 21st century: climate change is containable and even reversible
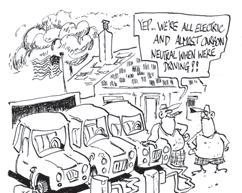
IN THIS ISSUE
Lithium ion phosphate — the now acknowledged standard for energy storage at scale

EDITORIAL: The developed world vs the rest of the planet | 10 PEOPLE NEWS The battery industry gets ready to give back to Cambodia | Farewell to John Bannister Goodenough, the father of the lithium ion cell | Meylemans takes over as EUROBAT GM
NEWS | 25 RECYCLING NEWS | 28 COVER STORY: A QUESTION OF BALANCE In defence of lead … and lithium
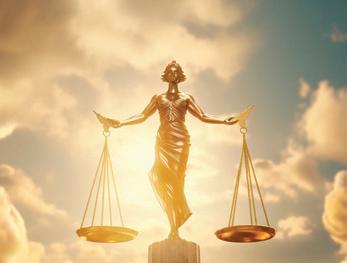
THE ESS PERSPECTIVE | 35 THE SUNLIGHT PERSPECTIVE | 39 THE AMARA RAJA VIEW
EVENT REVIEWS: EUROBAT General Assembly; International Flow Battery Forum; Advanced Technology and INNOVATION SHOWS
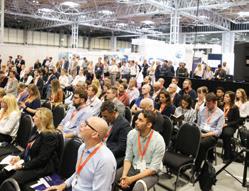
UPCOMING EVENTS: ESJ details the conferences and shows ahead
Editor: Michael Halls | email:mike@energystoragejournal.com | tel: +44 7977 016918
Digital editor: John Shepherd | email: john@energystoragejournal.com | tel: +44 7470 046 601
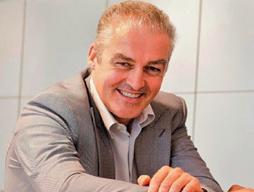

Advertising manager: Jade Beevor | email: jade@energystoragejournal.com | tel: +44 1 243 792 467
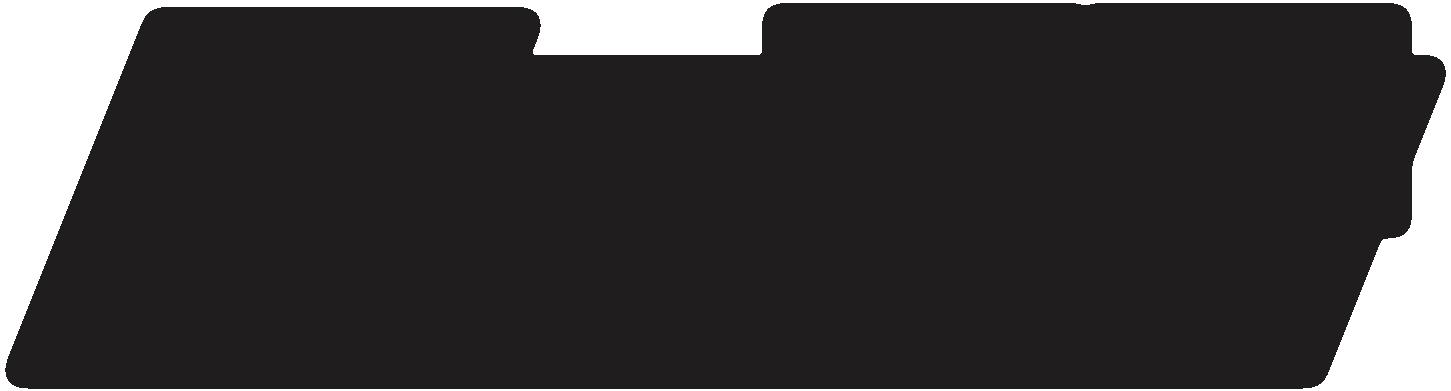
Finance: Juanita Anderson | email: juanita@batteriesinternational.com | tel: +44 7775 710 290
Energy
Publisher: Karen Hampton karen@energystoragejournal.com
+44 7792 852 337
Editor-in-chief: Michael Halls mike@energystoragejournal.com
+44 7977 016 918
Subscriptions and admin: admin@energystoragejournal.com | tel: +44 1 243 782 275
Design: Antony Parselle | email: aparselledesign@me.com
The contents of this publication are protected by copyright. No unauthorized translation or reproduction is permitted. Every effort has been made to ensure that all the information in this publication is correct, the publisher will accept no responsibility for any errors, or opinion expressed, or omissions, for any loss or damage, cosequential or otherwise, suffered as a result of any material published.
Any warranty to the correctness and actuality of this publication cannot be assumed. © 2023 HHA Limited. UK company no: 09123491
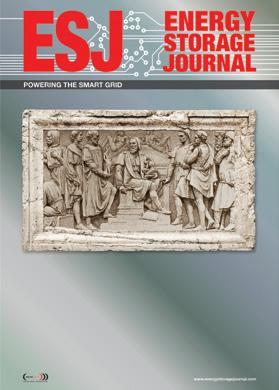
The developed world vs the rest of the planet
It’s the latest and possibly the last great myth of the 21st century: climate change is containable and even reversible through concerted human action.
And the frantic drive into renewables and its corollary energy storage — for this read the battery business — will save the planet.
From simple manufacturers of an essential component in modern and industrial life, we, collectively, have become visionaries for the future and saviours of mankind. That pesky carbon dioxide and that tricky global warming will be solved by our engineers, our entrepreneurs and not-forgetting our everresourceful innovators.
But one question doesn’t seem to be attracting much attention. And that’s whether the huge sums of money being committed to reducing emissions are worth the effort?
Certainly, it sounds the case when listening to the soundbites of politicians, that salvation is at hand. US president Joe Biden last year called the signing of the Inflation Reduction Act committing the country to huge tax breaks as the “biggest step forward on climate change ever.” The Brookings Institution, a think-tank, reckons the final cost of the package will top $1 trillion and almost three times larger than the US government estimate of $369 billion. The IRA, said Brookings, “has the potential to lower energy costs, contribute to lower inflation, increase productivity, and raise economic output over time”.
It might be nice to think this is the case. The fact is that though the developed world — essentially North America, Japan and Europe —
is making huge strides in reducing its emissions of CO2 levels, it is still a far-cry from carbon neutrality.
And meanwhile any shortfall created is being picked up elsewhere. Given what’s happening in other parts of the world, this is going to be just a drop removed from an ever-growing ocean of greenhouse gases.
Energy Storage Journal is not a climatechange denier, nor do we believe our drive into renewables and energy storage is a waste of money, time or effort.
However, on a planet of almost 8 billion people our efforts are not, so far, enough — failure of a sort will become inevitable.
The emerging world will not hesitate to put climate change lower down a list of priorities that contains elements such as better health care, education and a better standard of living, A quick look at their growing needs is reflected on their targets for climate neutrality — China aims for its CO2 emissions to peak by 2030 (and which already emits roughly a third of all climate change gases) and to be carbon neutral by 2060.
China provides more than half of the world’s steel and cement, but the CO2 emissions from just those two sectors in China are higher than the European Union’s total CO2 emissions.
India, with a similar population of around 1.4 billion souls, is aiming for climate neutrality by 2070. Already in 2022 India’s emissions are higher than that of Europe in its entirety.
The move into electric vehicles across the developed world is unlikely to make much of
China provides more than half of the world’s steel and cement, but the CO2 emissions from just those two sectors are higher than Europe’s total CO2 emissions.
a dent into the emissions from those two countries — auto manufacturers may boast that some 500 EV types will be launched in the next five years but China’s own cement and steel manufacturing already accounts for more than the whole of the emissions from Europe.
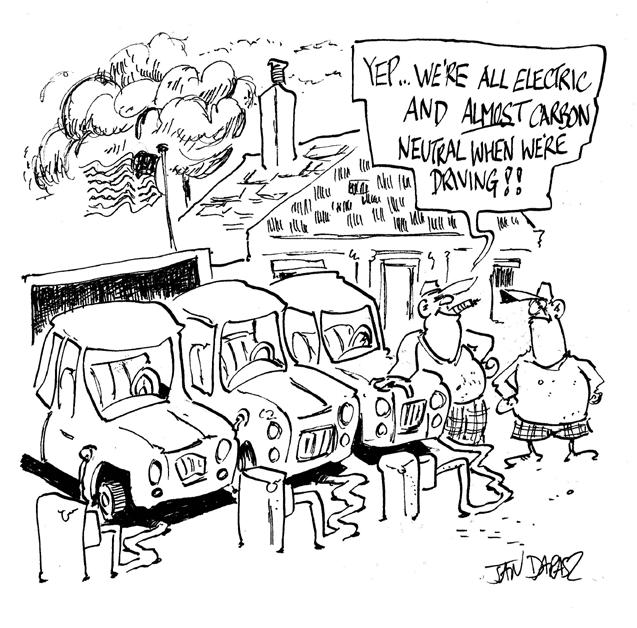
There’s also no need to simplify the world into the good guys and the bad ones — the developed North versus this pair of the environmentally irresponsible two. The fact is the rest of the developing world is on the same trajectory as China and India. We tut, tut — hypocritically — at our peril about emerging nations’ irresponsibility in wanting a standard of living closer to ours at the expense of the environment.
Robert Bryce, the commentator, points to the issue of energy inequality in his brilliant and highly recommended blog, https://robertbryce.substack. com.
“The average American consumes 20 times more energy per year than the average resident of Africa, … there are 1.4 billion Africans, who, on average, consume about 600kWh of electricity per head, per year. The average American consumes that every three weeks.”
He writes: “The average American consumes 20 times more energy per year than the average resident of Africa, and four times more than the average of Asia. There are 1.4 billion Africans, who, on average, consume about 600kWh of electricity per head, per year. The average American consumes that much electricity every three weeks.
“The reductions in the US and Western Europe are being swamped by increases in the rest of the world, and in particular, in India and China. Thus, the big challenge facing the world is not how many Teslas are being sold in Marin County, but how many coal plants are going to be built in Bangladesh, Cambodia, and other desperately poor countries.”
He points out that nearly 19 gigawatts of new
coal-fired capacity was brought online last year, with the biggest new additions happening in India, Japan, and Pakistan. Between 2000 and 2022, global CO2 emissions increased by 10,700 million tonnes. Of that increase, about 10,300 million tonnes occurred in the AsiaPacific region.
So where does this all leave the battery industry? First the good times will continue for lead manufacturers and, if the world supply of the huge quantities of metals required holds up, the lithium battery manufacturers will do excellently too.
But we shouldn’t deceive ourselves as being visionaries of the future or saviours of the planet. Or not yet anyway.
Mike Halls, EditorIn testing times, the battery industry needs a reliable partner
As the lead battery sector steps up the industry’s presence in a range of applications, from automotive to energy storage, telecoms and critical power, the subject of expanding R&D has re-emerged as an important topic of discussion at conferences.
At Battery Council International’s annual conference in 2022 panellists and delegates alike called for more investment in R&D and greater efforts to engage government agencies, national laboratories and the next generation of battery scientists and professionals to focus on advanced lead batteries.
R&D was again a topic of debate at BCI’s 2023 annual conference –and is also a constant on the agenda of other global industry bodies
including the International Lead Association and the Consortium for Battery Innovation.
R&D focus
Mark Hulse, vice president of sales and marketing for Maccor, acknowledges that the lead battery industry has increased its focus on R&D as lithium and other battery chemistry contenders push further into battery markets —and he welcomes that.
Maccor has strong connections with businesses in lithium ion, lithium metal air and solid state and Hulse is now encouraging the lead battery industry to let Maccor help them as they strive to make the next technological advances in their products.
Hulse has been with Maccor for nearly 30 years and says it is great to see a resurgence of R&D for lead acid. However, he also sees a need to focus on additives and related materials to further improve lead products. And it’s especially important for Maccor to be forging new partnerships with lead battery makers too, “because we cut our teeth on R&D and supporting advances in technologies”, Hulse says.
Maccor has strong connections with businesses in lithium ion, lithium metal air and solid state and Hulse is now encouraging the lead battery industry to let Maccor help them as they strive to make the next technological advances in their products.
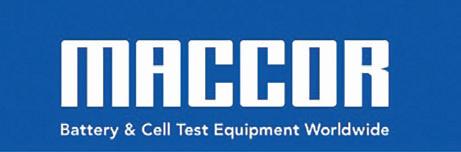
The company does work with systems for some lead acid firms but usually more in areas where those
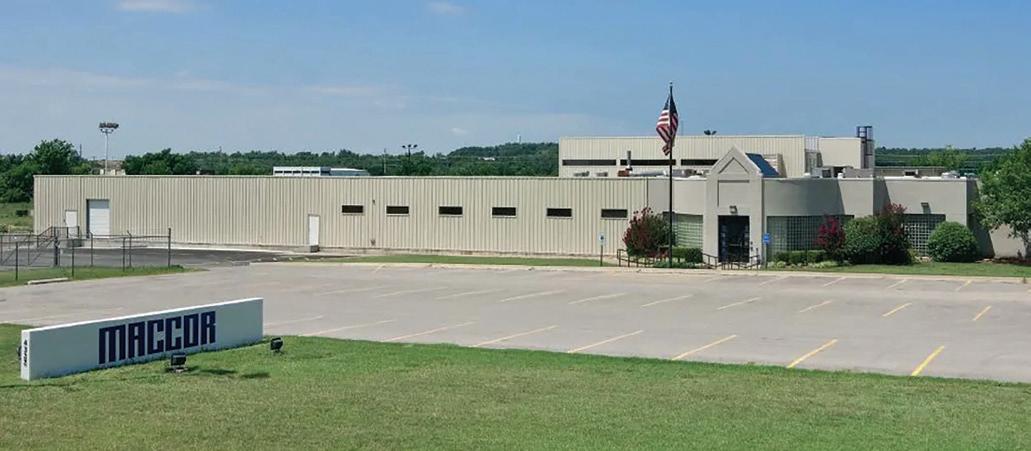
players are also developing products using other battery chemistries.
As lead acid is a mature technology, R&D waned for some years, but with lead acid now firmly on the R&D track, Hulse says “they would greatly benefit from our speed, accuracy, performance and reliability”.
“We have the most accurate systems and one of the fastest systems in terms of control measuring and that is what you need in terms of R&D.
“You need to be able to measure the smallest of changes in equipment and materials and for that the most important thing to have is accuracy.”
Chemistry agnostic
Maccor has sold more test channels than all of its competitors combined and Hulse points out that Maccor’s expertise can supply channels that run down to nanoamp scale.
And while Hulse is keen to expand work with lead acid, Maccor’s testing tech is chemistry agnostic. Of particular importance is that program tests can be tailored to whatever the chemistry or product is.
It does not have to be a battery it could be another kind of energy storage device such as a super or ultra capacitor.
“We’ve been around a long time and that’s what we’ve been about from day one — giving our customers the most accurate and fastest channels.”
Maccor’s ‘Watchdog’ system can also check on internet and PC connections during testing and if a problem occurs, such as a cable being unplugged, can automatically suspend the test and retain results up to that point.
“All of our channels have what we call isolation relays. The isolation relay opens up to isolate the device under test if a test is suspended for any reason. Also, if a customer is having an issue we have the best customer service department in the industry.”
Applications
Existing clients cover a wide range of applications including materials, medical, home & garden, cell manufacturing, pack manufacturing, e-mobility, automotive and aerospace. Maccor is also involved working with US national labs in research for the Department of Energy and federal government.
In terms of cost, Hulse acknowledges that in tough economic times budgeting for the best can be a difficult call for finance chiefs (even if advised to do so by technical managers) but then it is important to think about the cost of not investing in the best testing technology out there.
“If money was no object I know most everybody would come to us because they know we’re the best in the business for everything from testing to performance and reliability and customer service.”
Ownership cost
Hulse said the importance of understanding cost of ownership has grown over the past 20 years or so as cheaper testing systems have emerged. But the comparisons are stark. Maccor has many customer’s with systems that are more than 15 years old and still running reliably with the company’s support.

Compare that to one client that had to be ‘rescued’ by Maccor after they bought a cheaper system that
barely lasted a few months before problems with reliability began to emerge, costing the firm time and money. They eventually bought a system from Maccor and the original purchase sits there unused.
Maccor sold its first Windowsbased system nearly 26 years ago now (earlier systems were DOS based) yet they can run even the latest version of Maccor’s software without hardware upgrades.
When a company buys a tester Maccor never charges for software updates as long as they purchased the system from Maccor, which is unique in the business and there is also constant customer support with Maccor’s expert service team via phone and email.
However, Maccor has a strong presence in Asia too, where the vast majority of its customers are involved in batteries but there are also those who need to test fuel cells and rely on Maccor’s precision technology and support.
Looking ahead to how the business will develop in the coming years, Hulse says Maccor is focusing on a new processor coming on line that’s going to allow customers to run even faster speeds – in the range of sub-one millisecond.
Environmental susbtainability
Maccor is also responding to increasing demand for sustainability and climate-friendly services. The company’s new 8500 series is a return to grid system for higher voltage type applications, so it can handle anything ranging from approximately 50v to 1200V.
The 8500 requires less energy to run, therefore making it a powerful but green tech option.
The domestic US market currently represents around 60-65% of Maccor’s market and Hulse says Europe is probably in the lead as far as international markets go, with the UK and Germany being the biggest.
As global demand for sustainable supplies of energy continues to escalate, battery makers will be among those who are best suited to step up and help countries make the most use of renewables.
But battery manufacturers will need a reliable, accurate and trustworthy technology partner to convince power companies to buy their products – and Maccor stands ready to rise to the challenge.
“We’ve been around a long time and that’s what we’ve been about from day one — giving our customers the most accurate and fastest channels.”
Mark Hulse, vice president of sales and marketing for Maccor
Adding a helping hand
ABC making a difference to children in Siem Reap
The ABC conference committee and Sorfin Yoshimura have once again set up an initiative — the ONE Minute Giveback — to support a local children’s charity hospital in Siem Reap. The initiative is set to run throughout the entire 20ABC.
After the very successful 18ABC in Bali in 2019, the ONE Minute Giveback will continue in Siem Reap! In partnership with Sorfin Yoshimura Conference Works, the organizer of ABC will be working towards a HUGE CSR effort to raise funds for Angkor Hospital for Children so they can continue to improve the health and lives of those most in need. In a difficult world post Covid now more than ever our giveback activity has a real chance of helping the lives of those less fortunate than us!
• One in five Cambodians survive on less than US$2.70 a day. (Cambodian Ministry of Planning, 2020)
• A child born in Cambodia is five times more likely to die before their fifth birthday than a child born in a wealthy country.(World Health Organisation, 2015)
Cambodia is one of the poorest countries in the Asia and Pacific region and is still emerging from decades of conflict.
This year the ONE Minute Giveback will be supporting Angkor Hospital for Children with all proceeds directly improving the lives and health of local children in Siem Reap and help ensure families living in poverty have access to healthcare for their children via the free medical services the hospital provides.
FIVE GREAT WAYS YOU CAN GIVEBACK
2. DONATE ONE MINUTE
4.
DONATE ONLINE
If you are able to make a donation to support Angkor Hospital for Children through the ONE Minute Giveback we would love to hear from you. To deliver our aims of the Giveback we are looking to partner with organisations that will help make a difference in Siem Reap!
Contact:
Mark Richardson, mark@conferenceworks.com.au, +61 412 160 133
Scott Fink, sfink@sorfin.com, +1 917 773-3675


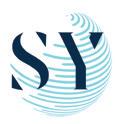
Donate ONE Minute of your time onsite during 20ABC and drop by the giveback area in the foyer of the main exhibition hall. We will be sorting, packing and stacking goods and items that the hospital has identified as critically needed.
3. DONATE ONE DOLLAR
Delegates' partners will be out taking onsite donations with the help of our event team. Any cash donation from the value of ONE United States Dollar is greatly appreciated and will be gifted to the Hospital onsite during the event.
Information about Angkor Hospital for Children is available on AHC’s charity page www.angkorhospital.org.
Delegates are able to donate to AHC directly via their websites
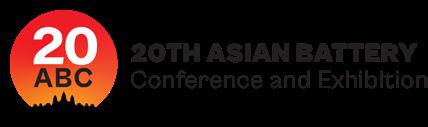
5. ONSITE
We will be accepting donated items onsite. We will share a ‘Wishlist’ of items our charities have requested. Should you wish to donate larger amounts of items please contact the team to discuss.
to those less fortunate
THE ANGKOR HOSPITAL FOR CHILDREN
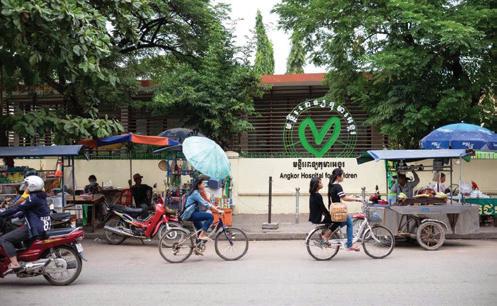
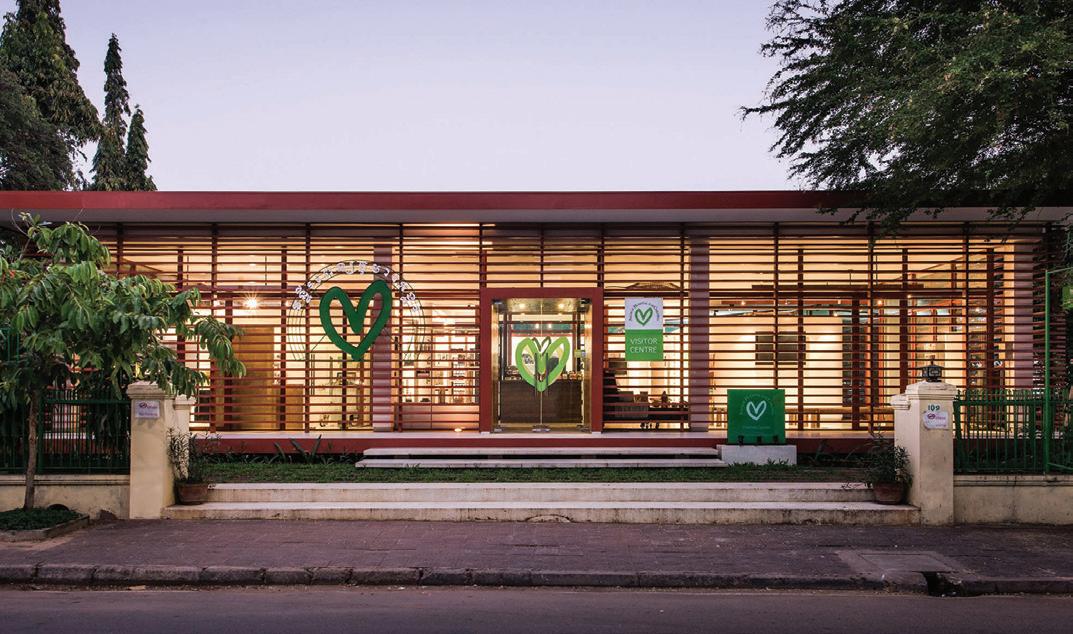
Every child — rich or poor — deserves to be healthy.
Angkor Hospital for Children is a leading children’s healthcare organization based in Siem Reap, Cambodia. We’re a teaching centre of excellence inspiring a new generation of health workers. We’re working in some of Cambodia’s poorest communities to empower caregivers with vital health information.
Our community is made up of hospital staff, board members, volunteers, partners and supporters, united under a common mission: improving healthcare for every child in Cambodia.
Why we’re here
Over the last 20 years healthcare in Cambodia has improved significantly. However, children still die from preventable causes. Access to quality healthcare within Cambodia is not universal. There is a lack of care available for children with long-term, rare or acute conditions — particularly for those in the poorest and most remote villages.
Last year in numbers
• 97,978 Total treatments were provided from outpatient care to specialty services.
• 1,447 Children received life-saving emergency treatment in our specialist PICU.
• 40 Government health facilities received our support to set up systems to improve patient care, install life-saving equipment and provide training and mentorship to health professionals.
• 2 Doctors completed their three-year sub-specialty training programme to become a paediatric specialty doctor, to address the gap in specialty care in Cambodia.

• 63,919 Virtual and in-person attendances were recorded in AHC’s educational sessions for external healthcare professionals, nursing and medical students, and AHC staff.
• 142,446 Attendances were recorded in AHC’s prevention and health education activities in villages, schools and communes.
John Bannister Goodenough, 1922-2023: 'A life well lived'
We are sad to report that John Goodenough, father of the lithium ion cell, and one of the three figures that created today’s huge lithium battery industry, died on June 25 a month short of his 101st birthday.
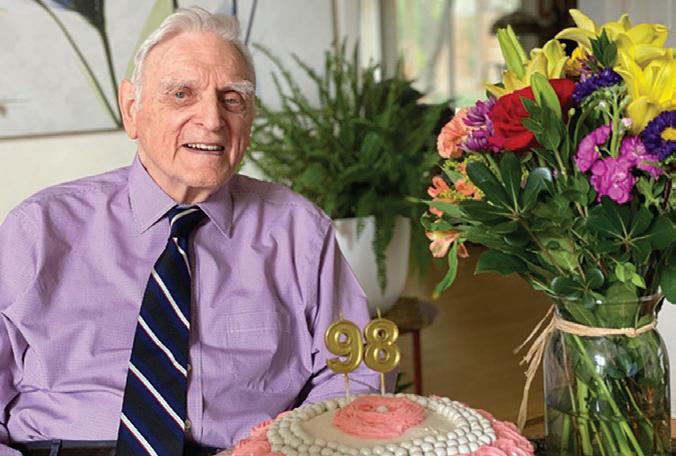
John, who was interviewed several times for Energy Storage Journal, was awarded the joint Nobel Prize for Chemistry in October 2019 with the two other pioneers of the lithium battery, Stanley Whittingham and Akira Yoshino.
In our subsequent interviews with Whittingham and Yoshino each acknowledged the huge debt the world owes to Goodenough who discovered the cathode material of choice and so made the lithium ion battery truly portable and rechargeable.
“John was an unassuming, modest and gentle man whose work has touched everyone’s life,” said Bob Galyen, the former CTO of CATL and a friend. “It was a life well lived and John had an intellect of astonishing proportions and his contributions to science extend well beyond the lithium cell.”
Oddly enough for someone whose research has ended up in the household or pocket of most of the planet, he was regarded as a backward child. It was only much later that it was found that he was dyslexic and he later described how he dealt with this problem by studying abstract mathematical thought and Greek and Latin.
Aged 18 he left school as top of his class and received a scholarship to Yale. After the bombing of Pearl Harbor, he volunteered for service, but was not called up until January 1943. This gave him time to complete his undergraduate degree in mathematics. He had entered Yale as a freshman with a background in Latin and Greek and little idea of what he would do after the war was over.
He graduated while working as a meteorologist in the US Air Force. A crisis of faith around this time led him to dedicate himself to a life of service starting with studying physics at the University of Chicago or Northwestern University.
“When I arrived at Chicago the registration officer, professor Simpson, said to me, “I don’t understand you
veterans. Don’t you know that anyone who has ever done anything interesting in physics had already done it by the time he was your age; and you? You want to begin?”
Undeterred, he earned a master’s degree in 1951 and a doctorate the following year.
For the next six decades his astonishing academic career and research led him from his early work at MIT on computer memory to the University of Oxford in his 50s where most of his ground-breaking work on lithium cells was pioneered. The last three decades of his life were at the University of Texas, where he held the Virginia H Cockrell centennial chair in engineering.
He was still working until his late 90s and in the last years of his life was pioneering a solid state battery.
As recently as 2017 he announced patents for new battery cells using a solid glass electrolyte instead of a liquid one, using an alkali metal anode. The glass electrolytes allow for the substitution of low-cost sodium for lithium. This had the possibility of being a second world-changer to the energy storage industry.
Caring little for money, John signed away most of his rights. He shared patents with colleagues and donated stipends that came with his awards to research and scholarships.
He was married to Irene Wiseman for 65 years. She died in 2016. In the latter part of her life he would work at
the university in the morning and visit her care home in the afternoons, she suffered from dementia.
In addition to being a Nobel laureate John was feted internationally being a member of the US National Academy of Engineering a member of the National Academy of Sciences, French Academy of Sciences, the Spanish Royal Academy of Sciences, and the National Academy of Sciences.
He wrote more than 800 articles for scientific journals, 85 chapters and eight books. He was a co-recipient of the 2009 Enrico Fermi Award and elected a Foreign Member of the Royal Society and was presented with the National Medal of Science by US president Barack Obama.
Among his many publications is a very personal one: “Witness to Grace”, in which he describes how his intellectual journey had also included “a religious quest for meaning in what or whom I would choose to serve with my life.” He was born into an agnostic family but during the war years he developed a faith and was a devout Christian to the end of his life.
Career development
To return to his spectacular career: the crucial point in Goodenough’s researches and associated lithium battery’s development was when he was offered a position of professor and head of the Inorganic Chemistry Laboratory at Oxford University.
Up till then. Goodenough had been working as a research scientist at MIT’s Lincoln Laboratory where he had been part of an interdisciplinary team that developed the first randomaccess memory (RAM) for the digital computer.
His fundamental research had focused on magnetism and on the metal–insulator transition behaviour in transition-metal oxides. He also developed a set of semi-empirical rules to predict magnetism in these materials in the 1950s and 1960s, now called the Goodenough–Kanamori rules which is a core property for high-temperature superconductivity.
Goodenough’s contribution was to the development of the ferrimagnetic, ceramic memory element, a contribution that put him in charge of a ceramics laboratory and that gave him a decade in which to explore the magnetic, transport, and structural properties of transition-metal compounds.
In 1952, he joined the group at MIT Lincoln Laboratory charged with the development of a ferrimagnetic ceramic to enable the first RAM for the digital computer.
“The air defence of this country depended on having a large digital computer, and the computer had no memory!” Goodenough later said.
“The rolled alloy tapes first tried did not switch fast enough. Although the Europeans who had developed ferrimagnetic spinels were convinced that it would be impossible to obtain the required squarish B-H hysteresis loop in a polycrystalline ceramic, the magnetic-core RAM was delivered within three years of my arrival with a read/ rewrite cycle time of less than the required six microseconds.”
In the course of this work, Goodenough showed how cooperative orbital ordering gives rise to crystal distortions, and he used this ordering to articulate the rules for the sign of the spin-spin magnetic interactions in solids.
These rules have subsequently provided a true guide to the design as well as the interpretation of the magnetic properties of solids; they are known as the Goodenough-Kanamori rules, and they inspired the title of Goodenough’s first book, Magnetism and the Chemical Bond
Although these were astounding advances in both physics and chemistry. It was his appointment to Oxford University in 1976 that so much came together.
Once there, Goodenough recognized
that the layered sulfides would not give the voltage needed to compete with batteries using a conventional aqueous electrolyte, but that an oxide would provide a significantly higher voltage.
From previous work, he knew that layered oxides analogous to the layered sulfides would not be stable, but that discharged LiMO2 oxides could have the same structural architecture as discharged LiTiS2
Goodenough assigned a visiting physicist from Japan, Koichi Mizushima, the task of working with Goodenough’s postdoc, Philip Wiseman, and a student, Philip Jones, to explore how much Li could be extracted reversibly from layered LiMO2 cathodes, and with M = Co and Ni he found he could extract electrochemically over 50% of the Li at a voltage of around 4.0V versus a lithium anode, nearly double that for the sulfides, before the oxides began to evolve oxygen.
Their groundbreaking findings with Li1-xCoO2 were published in the Materials Research Bulletin 15, 783-789, (1980).
The report concluded with the statement, “Further characteristics of the intrinsic and extrinsic properties of this new system are being made.”
However, when Goodenough went to patent his cathodes, no battery company in the UK, Europe, or the US was interested in assembling a battery with a discharged cathode, so he gave the patent to the AERE Harwell Laboratory.
Nevertheless, with his postdoc Peter Bruce, now a professor in St Andrews, Scotland, and a new student, MGSK Thomas, Goodenough continued in Oxford to demonstrate that the Li+-ion mobility in Li1-xCoO2 is even higher than that in the sulfide cathode LiTiS2.
This finding meant that a Li1-xCoO2 cathode would provide the needed voltages and rates that would usher in what was later termed the “wireless revolution”.
Meanwhile, Rachid Yazami in Switzerland, exploring Li insertion into graphite, reported that a discharged graphite anode did not have a problem with dendrites if the carbon/LiCoO2 cells were not charged too rapidly, and Akira Yoshino in Japan then assembled the discharged cell Carbon/LiCoO2 to demonstrate the Li-ion battery that was licensed to the SONY Corporation, which marketed with it the first cell telephone.
Today, almost everyone from five
years upwards has an application of this battery in his or her pockets.
Michael Thackeray was working on the Zebra battery (see Energy Storage Journal passim), a modification of the sodium-sulfur battery, in South Africa when he read the article in the Materials Research Bulletin. He immediately applied for a sabbatical to work with Goodenough in Oxford.
He came to the city with the announcement that he was inserting Li reversibly into magnetite, the ferrimagnetic spinel Fe3O4 used by Greek sailors in an early version of the compass. He wished to replace cobalt, which is expensive and toxic, with iron, which is abundant and benign. The spinels A[B2]O4 contain a three-dimensional framework of BO6/3 octahedra sharing edges; in the layered LiMO2 oxides they form 2-dimensional layers.
The A atoms of a spinel occupy interstitial tetrahedral sites that are bridged by empty, face-sharing octahedra, and Goodenough realized from his earlier work on spinel memory elements that the Li inserted into Fe[Fe2]O4 was entering and displacing that interstitial A-site Fe into the bridging interstitial octahedral sites to create a rock-salt structure with the [Fe2]O4 framework remaining intact.
Bill David, at the Rutherford Laboratory, had just joined Goodenough’s group from the Clarendon with a PhD involving structural analysis, so he and Thackeray demonstrated that Goodenough’s hypothesis was correct.
Meanwhile, Goodenough told Thackeray to investigate the electrochemical reversible insertion of Li into the spinel Li[Mn2]O4; it gave a voltage of 3.0V versus lithium. Manganese is also abundant and benign. On his return to South Africa, Thackeray showed his students that extraction of Li from Li[Mn2]O4 gives a voltage of 4.0 V versus lithium. A modification of the Li1-x[Mn2]O4 spinel cathode was later used by Nissan to power their Leaf electric car.
By then the next stage in the development of the lithium battery was complete. Akira Yoshino in 1985 fabricated the first prototype of the LIB and received the basic patent. This configuration was commercialized by Sony in 1991 and by A&T Battery in 1992.
“It’s rare that we’ll see a figure like John Goodenough again in our lifetimes,” said one commentator. “He had a life of modest and quiet achievement — a well lived life and with a legacy that the whole planet can thank him for.”
EUROBAT’s Westgeest steps down, Meylemans takes over as GM
Alfons Westgeest, general manager of EUROBAT, announced on June 5 he was stepping down and Gert Meylemans, previously director of communications, would take over.
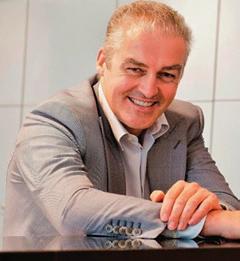
Westgeest, who tried to retire four years ago but came back, has been a central figure in EUROBAT since his involvement in 2002 and arguably the key creator of the present trade organization.
Westgeest, a well-known and well-liked figure in all sections of the European energy storage industry, said he had enjoyed his time with EUROBAT.
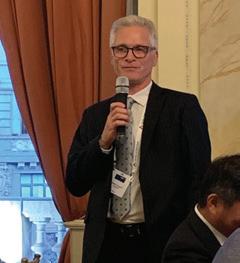
“It’s not just been fun to build up and strengthen the organization but we have achieved real success in helping influence the direc-
tion of battery regulation across the EU.”
Marc Zoellner, president of EUROBAT and CEO of Hoppecke Batteries, in a touching speech at the conference dinner, paid tribute to Westgeest’s relentless commitment to building up EUROBAT and its members.
“I will truly miss him and thank him for the wonderful work he has done,” he said.
Meylemans, who joined EUROBAT in August 2018, said he had a very tough act to follow but “hoped to continue to build on the great work Alfons has done”.
EUROBAT — the association for European automotive and industrial battery manufacturers and
Skyllas-Kazacos joins Tivan advisory group
Vanadium redox flow battery pioneer Maria SkyllasKazacos has joined a new technical advisory group set up by minerals processing tech company Tivan.
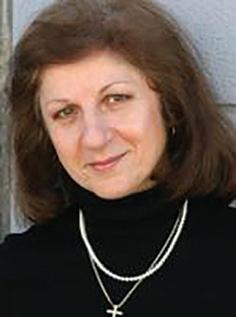
Tivan said on May 31
Skyllas-Kazacos’s technical knowledge and experience would be keenly sought in developing and standardizing the global value chain in VRFB.
Other initial appointments to the group included Stéphane Leblanc and Simon Flowers.
Leblanc is a former MD of Rio Tinto Iron & Titanium. Flowers is the director and principal of Sustainergy Consulting and a former international team leader with US energy firm ConocoPhillips.
The group will provide independent technical advice to support development of two projects, including Tivan’s Mount Peake in Australia’s Northern Territory — which the company says has one of the largest flat-lying, shallow vanadium-titanium deposits in the country.
The other is the Speewah vanadium-titanium-iron project in Western Australia, of which Tivan acquired 100% ownership in April.
supply chain in EMEA — was formed in 1957 and was originally based in Switzerland.
But it was only when it moved to Brussels at the turn of the century that it became the lobbying and trade body that it is today.
EUROBAT is a non-profit association under Belgian law and is staffed by association management company Kellen. Westgeest became Kellen Europe’s board member for global develop-
ment in 2022.
Before EUROBAT, Westgeest was the founder and managing partner of Ernst & Young’s association management practice in 1988 in Brussels. He joined EY in 1981 and left the firm in 2004.
This year’s EUROBAT general assembly and convention was held on June 6-7 in Madrid.
See our event review towards the end of the magazine.
Roden joins ENTEK International as North America account manager
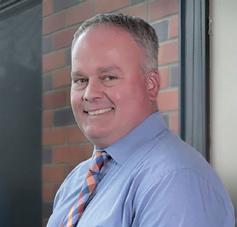
James Roden has joined ENTEK International’s lead acid separator sales team as North America account manager, the company announced on May 31.
Roden, who has more than 10 years of sales experience in the automotive industry, will be based at ENTEK’s headquarters in Oregon.
ENTEK announced last year that it was to expand its manufacturing of AGM battery separators to India and the US, in response to expanding demand for energy storage solutions for inverters, industrial applications and electric vehicles.
In March, the company said it was also investing
$1.5 billion to build a lithium ion battery separator production facility in the US state of Indiana. The Terre Haute plant, on a 340-acre greenfield site, will be the biggest investment to date by the US-based producer of wet-process lithium-ion battery separator materials, in support of the growing EV industry in Indiana and across the country.
Taylor succeeds Longney as TBS group MD, Davis retires
ship as TBS starts a new phase of its development program.
However, Longney will remain a director of TBS and support Taylor in his new role.
Taylor has been with the company since 2019 when he joined as group operations director, responsible for all UK manufacturing operations, supply chain and facilities management at the Gloucestershire HQ.
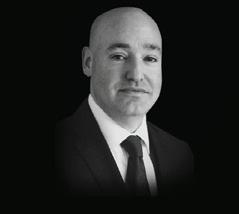
announcement on July 3, TBS announced that the much-respected Paul Davis was retiring from the firm after 39 years.
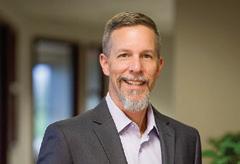
Frank Macchiarola joined the American Clean Power Association as chief policy officer on June 20, the trade organization announced.
Davis joined TBS in February 1984 as a service technician, moving to sales several years later.
UK-based TBS Engineering has announced the appointment of Richard Taylor as its new group MD following the announcement that David Longney will be stepping down.
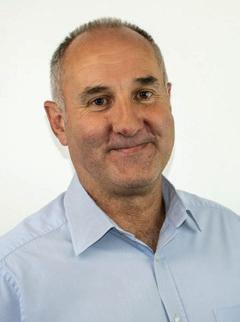
TBS said on July 3 that Longney, who has worked with the company for nearly 40 years, had decided to make way for new leader-
In 2022, Taylor accepted a new role as group aftermarket director.
Longney said: “It was a difficult decision to step down, however, I believe in my time as MD we have moved the business forward in many ways, placing TBS in a strong competitive position for the future.
"In a separate LinkedIn
Straw named director of new ENTEK Manufacturing unit
turer and supplier of replacement wear parts in the industry.”
Straw will have profit and loss responsibility for the division and reports to Linda Campbell, VP of extrusion sales.
Macchiarola, former senior VP of policy, economics and regulatory affairs at the American Petroleum Institute, is leading a team working on regulatory and legislative proposals to boost development of advanced clean energy technologies.
Jason Grumet, ACP’s chief executive officer,
said: “The clean energy sector is at a pivotal moment, and growing our team to embrace the opportunities before us will ensure this industry has the bench strength in place to match the moment.”
Doe Run promotes Mangogna to VP operations and COO
Tammy Straw has been named as director of ENTEK Manufacturing’s new wear parts division, which will make and sell replacements for all brands of twin-screw extruders.
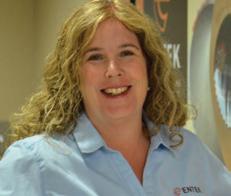
The June 9 announcement followed the February opening of ENTEK’s 98,000 ft2 manufacturing and engineering facility in Henderson in the US state of Nevada.
ENTEK Manufacturing president Kim Medford said the new division was key to the group becoming the number one manufac-
Straw has worked with ENTEK for 24 years and has been the company’s marketing and business development manager since 2016, also leading ENTEK’s inside sales team.
She is also the vice chair of the NPE sales and marketing committee for the US Plastics Industry Association.
Also joining the new Wear Parts Division is Kelsey Dennis, who will be responsible for wear parts sales. She has been with ENTEK since 2010, and most recently worked in customer support and inside sales.
The Doe Run Company, the mining group and natural resources firm, announced on June 28 it had promoted Brian Mangogna VP for mining and milling to be chief operating officer and VP for operations.
Mangogna has spent almost 25 years with Doe Run, starting as a metallurgist, advancing over the years as mill superintendent, mill manager and general manager for the company’s Southeast Missouri (SEMO) Mining and Milling Division. In 2021 he joined the executive team and was promoted to VP of mining and milling.
In his new job he will oversee day-to-day opera-
tions for the company’s mining and metals operations, its battery recycling plant as well as its mines and mills.
Mangogna said: “Doe Run has a long history of being a global provider of lead, copper and zinc — three base metals that enable modern society — but can also recover cobalt, nickel, tin and antimony from resources within our control, whether ore bodies or metals by-products."
Metair moves interim CEO, CFO appointments to permanent positions
Interim CEO of battery and auto components group Metair Investments, Sjoerd Douwenga (pictured), has been appointed to the role permanently, the company said on May 31.
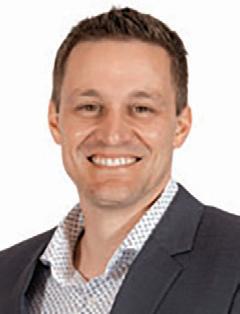
Interim CFO Anesh Jogia has also been appointed permanently. He will also work as executive director
ABTC appoints Deutsch as CFO
and a member of the firm’s investment committee.
The interim appointments of Douwenga and Jogia were announced in March, following the resignation of then CEO Riaz Haffejee.
Metair said the permanent appointments “will allow for a seamless leadership transition”.
The group’s energy storage division includes Turkey’s Mutlu Akü lead battery business, Romanian lead and lithium company Rombat and South Africa’s First National Battery.
In March, Metair reiterated that plans to sell off the energy storage business remain suspended as a result of the geopolitical climate in Europe and global financial instability.
ECS award for Argonne Lab scientist Meng
Senior Argonne National Laboratory scientist Shirley Meng has been honoured by The Electrochemical Society for her work on battery tech innovations.
Argonne said on July 10 Meng will be presented with the ECS 2023 battery division research award in October, in recognition of her work on interfacial science, which has led to improved battery technologies.
Meng is chief scientist at the Argonne Collaborative Center for Energy Storage Science and is a professor at the Pritzker School of Molecular Engineering at The University of Chicago.
Her research focuses primarily on energy storage materials and systems, specifically rechargeable bat-
teries for EVs and trucks, power sources for the internet of things and gridscale storage integration with renewables.
ECS highlighted two papers published last year by Meng in the Journal of The Electrochemical Society, one exploring the use of external mechanical pressure to regulate the growth of dendrites that form at the interfaces in batteries and lead to an electrical short.
The second paper looked at the process of lithium plating and stripping in rechargeable lithium batteries.
The battery division research award was established in 1958 to encourage excellence in battery and fuel cell research.
American Battery Technology Company said on May 22 it had appointed Jesse Deutsch as CFO.
Deutsch has more than 25 years of financial leadership experience including as a former CFO of global brands such as Kraft Foods.
He now oversees all financial operations of the company including those supporting an acceleration of battery recycling and battery metals manufacturing.
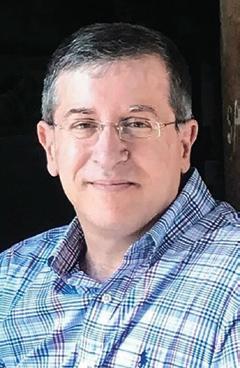
Deutsch, who has an MBA from New York Uni-
versity and a Bachelor of Science in economics from The Wharton School of the University of Pennsylvania, will also have responsibility for corporate functions including financial planning and analysis, accounting and controls, risk management, financial performance and revenue growth, investor relations, and reporting and compliance.
ABTC’s CEO Ryan Melsert said: “As we ramp up our commercial scale manufacturing operations over the coming months, we are excited to have such an experienced leader as Jesse join ABTC.
“We have an immense number of financial and strategic opportunities in front of us, and with this enhanced leadership team we are looking forward to driving them to execution.”
Deutsch’s appointment followed ABTC’s announcement in January that it had expanded its team toward commissioning of the firm’s lithium battery recycling plant.
Oliver Gross appointed senior fellow at Stellantis
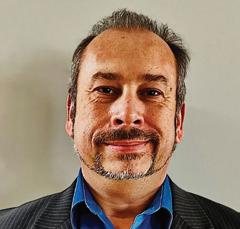
Oliver Gross has been promoted to a new post as a senior fellow for energy storage and electrification at auto giant Stellantis.
Gross confirmed the appointment to Energy Storage Journal on May 12.
Gross is an expert in lithium ion and NiMH chemistries with a focus on motive applications.
His career to date has included being responsible for operations of analytical labs, electrical, environmental and abuse test labs, pilot lines and
supporting services.
Gross has also designed, developed and brought to manufacturing cells and modules for consumer electronics, military, aerospace, and automotive industries.
Ecobat looks for new CCO as Soule departs
Ecobat chief commercial officer Thea Soule has left the company, Energy Stor-
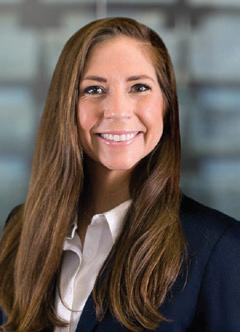
age Journal has learned. Soule, who joined Ecobat in 2020, said on August 15
that she had recently left her post — but she did not give details.
Asked whether she would remain in the battery-related world, Soule said there would be “more news to come on my next endeavour”.
An Ecobat spokesperson told Energy Storage Journal: “We can confirm Thea’s departure and express our gratitude for her contributions. The search for a chief commercial officer successor is underway, and updates on the CCO appointment will follow.”
Former Microsoft exec Steen named Freyr CEO
Former Microsoft executive Birger Steen has been appointed CEO of Freyr Battery, as part of a leadership shake-up announced by the company on August 10.
Steen, is a former worldwide VP of distribution and small-medium business at Microsoft in Seattle, VP and GM at Microsoft Russia and GM at Microsoft Norge.
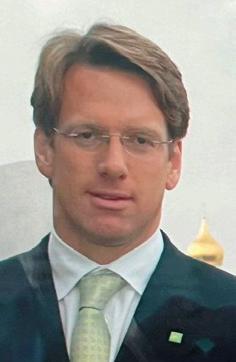
He chairs the boards of Nordic Semiconductor and Pagero and succeeds Freyr
co-founder Tom Einar Jensen — who has been appointed executive chair of the Norway-based battery developer’s board.
Both appointments, effective August 21, follow the retirement on August 9 of founder and executive chair Torstein Dale Sjøtveit.
Sjøtveit said Freyr would “continue to push the frontiers of innovation and apply new technologies to next-generation battery manufacturing”.
Freyr plans to develop up to 43GWh of battery cell production capacity by 2025, with an ambition of up to 83GWh in total capacity by 2028.
Last month, Freyr said it had been awarded €100 million ($112 million) from the European Union to support its Giga Arctic project in Norway.
Last November, Freyr announced it had bought a site in the US state of Georgia to build its planned Giga America battery cells manufacturing plant.
Soule was a key speaker at June’s Pb2023 International Lead Conference in Athens, where she told delegates that, after spending much of her career in Brazil’s agricultural industry, she had spent the last three
years learning and integrating outside-industry experience into the world of battery recycling.
Separately, Stefanie Scruggs has been promoted to chief sustainability and HSE officer. “Since joining Ecobat last summer, she has expertly elevated the critical work we do to help the world meet its essential energy storage needs by promoting a circular energy economy,” the firm said.
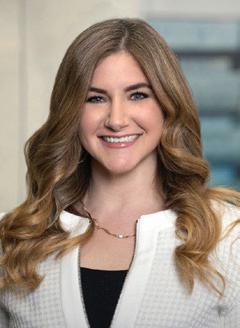
“From improving blood lead levels to releasing the Ecobat Sustainability Report, Stefanie’s leadership has pushed our organization to the forefront of sustainability and safety standards. Under her guidance, Ecobat has adopted improved HSE initiatives and increased accountability for meeting safety goals.”
Zodl to join Clarios as CFO
Clarios said on August 21 it had appointed Helmut Zodl as its new CFO effective September 1.
Zodl joins Clarios from GE Healthcare where he was also CFO and led the spin-off of the company from its parent, listing GE Healthcare on the NASDAQ.
A native Austrian, Zodl is also a former group CFO for air condition-

ing, white goods and industrial automation firm Midea in China.
Clarios president and CEO Mark Wallace said Zodl’s international expertise in the automotive industry made him an outstanding choice for his new post.
Zodl succeeds John DiBert, who left Clarios in April to become CFO at Air Canada in his hometown of Montreal
Leoch to cooperate on solid-state batteries with Chinese university
Lead and lithium battery giant Leoch signed a framework agreement on June 8 to cooperate on solid-state tech R&D with China’s Fuzhou University.
Singapore-headquartered Leoch said the move is in line with development of its new energy batteries business — and can nurture training and scientific research on both sides.
Leoch owner and chairman Dong Li (pictured) said process control, scientific research technol-
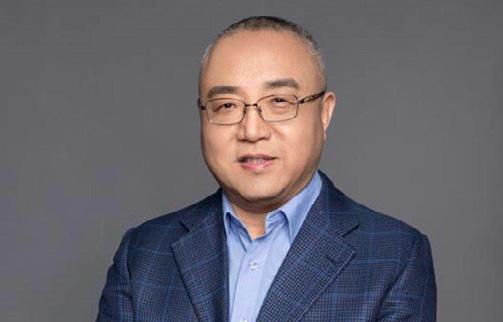
ogy and collaboration are key to advances in battery technologies.
He said he looked forward to Leoch working with the university’s materials science and engineering college.
In March, Leoch announced plans to build a manufacturing plant in Mexico to ramp up its market presence in the Americas.
Dong Li said then that the location had been chosen because of its unique geographical location and
export policy advantages for the region — such as the USMCA free trade
Banner posts battery sales record despite ‘burdensome EU red tape’
Lead battery manufacturer Banner reported record full-year sales of €307 million ($333 million) on June 6 — but warned increasing European red tape and rising energy prices were major burdens.
The Austria-based firm said auto batteries were the key driver of its sales for the year ended March 31, which it said were up by more than 7% over the previous year.
Banner said it sold more than four million starter batteries over the period.
Meanwhile, a new licensing partnership with Leoch International for the Banner brand in China and an extension of the company’s licensing deal with Duracell should boost future sales in Asia and Europe.
Banner said the past financial year was characterized by far-reaching, global changes throughout the entire automotive industry, rising energy, raw material and labour costs and increasingly problematic supply chain issues.
Group commercial CEO
Andreas Bawart said the rise in sales was despite “massive cost increases in every area from raw materials to labour and naturally the meteoric upturn in energy prices.
“A short-term improvement is not in sight and un-
fortunately the EU and Austria are contributing to these difficulties.
“A vast number of regulations have been introduced, the implementation of which has led to a huge increase in the administrative burden upon small and medium-
sized enterprises like ours.” Bawart said it was inexplicable that political leaders were presiding over a situation where European battery makers “are suffering enormous competitive disadvantages” while trying to challenge Asian competitors.
Brill Power unveils ‘chemistry-agnostic’ battery booster for performance, safety
Brill Power unveiled chemistry agnostic tech on June 14 that it claimed could significantly improve battery performance and safety.
Brill, a spin-out from Oxford University, said its power battery intelligence platform boosts battery performance explicitly for larger battery systems in industrial, commercial and utility-scale applications.
The company’s BrillCore hardware and proprietary BrillOS operating system
are at the heart of the technology — providing “intelligent active loading of battery cells or modules” to overcome inherent performance limitation of the weakest cell in the pack that limits existing BMS solutions.
Active loading allows all of the potential from battery cells to be utilized, extending battery lifetime by up to 60%, Brill claims.
According to Brill, BrillOS is chemistry-agnostic and can be updated
wirelessly to be compatible with future battery technology.
Brill CEO Christoph Birkl said the system addressed “all of the pain points” that can be encountered by battery pack and systems developers. “Industrial and gridscale battery systems are necessarily large and expensive investments, so any frailty in the technology can have profound implications for the success and viability of the solution.”
Fire-damaged EV cargo ship towed to Dutch port with batteries blamed for blaze on board
Stricken car carrier the Fremantle Highway was being towed into a Dutch port, as Energy Storage Journal went to press, after a fatal onboard blaze, with initial reports suggesting an EV battery was to blame.
According to Lloyds List, nearly 500 EVs were among the 3,784 cars on board the vessel when fire broke out on July 25, while en route from Germany to Singapore via Egypt.
Dutch broadcaster RTL has released a recording of an initial emergency re-
sponder reporting that the fire “started in the battery of an electric car”.
But the Netherlands Coastguard has distanced itself from the recording, saying it is too early to say what triggered the blaze that led to the death of one of the 23 crew members and injured many others.
Rijkswaterstaat, part of the Dutch Ministry of Infrastructure and Water Management, said yesterday there were no indications that the fire was continuing.
A towing operation began this morning to take the Fremantle Highway into the port of Eemshaven, with experts from a number of agencies on board the vessel.
Rijkswaterstaat said the cargo could be safely unloaded at the port allowing investigators to establish the cause of the blaze.
Only two of the rescued crew members remained in hospital as of July 30, according to vessel charter company Kawasaki Kisen Kaisha.
The Fremantle Highway was built in 2013 and has the capacity to carry 6,000 vehicles.
An industry observer told
NY governor launches ESS fire safety taskforce
A new multi-agency fire safety taskforce has been ordered to spearhead inspections of ESS sites across New York State.
State governor Kathy Hochul said on July 28 the Inter-Agency Fire Safety Working Group would ensure the safety and security of ESS sites following fires at facilities in Jefferson, Orange, and Suffolk Counties this summer.
Despite such fires being “exceedingly rare” Hochul said state agencies would begin immediate inspections of energy storage sites
through the working group.
She said this would help prevent fires and ensure emergency responders have the necessary training and information to prepare and deploy resources in the event of a fire.
Hochul said the working group will review ESS operations and operators — as they examine the condition of their batteries to verify operation within design parameters, correct any deficiencies, check on-site fire suppression measures and confirm fire suppression plans with
local fire departments.
Findings from probes into the incidents will include a list of recommendations for stationary energy storage equipment and installations.
The findings and recommendations will be shared with organizations including the New York City Fire Department, National Fire Protection Association, International Code Council, the New York State Fire Prevention and Building Code Council and Underwriters Laboratories.
The governor did not sin-
Energy Storage Journal: “As terrible as the incident has been, one can only imagine how much worse thing might have been if the ship had been filled to capacity.”
In a separate report published on July 27, Allianz Commercial said fires on vessels like the Fremantle Highway remain one of the biggest safety issues for the shipping industry.
The report said lithium ion fire risks will likely ease over time as manufacturers, carriers, and regulators address the current challenges.
“In the meantime, attention must be focused on pre-emptive measures to help mitigate the peril.”
gle out sites involved in recent fires, but one is known to be Convergent Energy’s BESS facility in Warwick.
The utility reported on June 29 that investigations were underway following a fire involving one of its Powin Centipede systems.
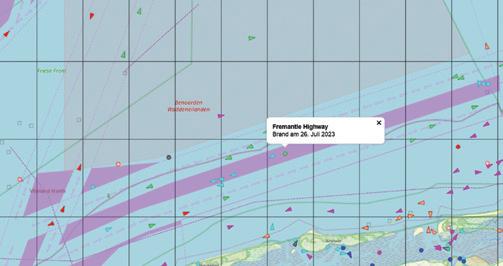
In June 2022, Hochul unveiled plans for 22 largescale solar and battery storage projects for some 2,408MW in New York State.
Last May, New York City fire commissioner Laura Kavanagh said she would consider supporting further measures aimed at stamping out lithium ion battery fires following a number of incidents, some fatal, involving e-scooters and ebikes.
“As terrible as the incident has been, one can only imagine how much worse thing might have been if the ship had been filled to capacity.”
Pexapark backs solar-BESS agreement ‘first’ for UK
Software and advisory firm Pexapark said on July 5 it is supporting a milestone hybrid power purchase agreement (PPA) and optimization agreement that will boost the solar-storage market in the UK.
The deal, announced by equity fund DIF Capital Partners, covers a 55MW solar farm with a 40MW/80MWh battery storage system in Leighton Buzzard and is the UK’s first bankable and unsubsidized co-located hybrid PPA, according to Pexapark.
The move will provide
secured revenue across the solar-BESS system over a 10-year term.
In the UK, 45% of all planning applications for solar projects submitted in the past two years have been for hybrid systems that include battery storage, Pexapark said.
And the company said its own analysis indicates that 64% of renewable energy businesses in the wider European market are now seeking to introduce or increase the proportion of energy storage in their portfolios.
However, Pexapark said PPAs for co-located proj-
ects have remained difficult to agree on because of their complex operational usage profiles and contracting structures, which has limited options available for financing solarhybrid schemes.
Brian Knowles, director of storage and flexibility at Pexapark, said the innovative nature of the UK agreement “reflects our commitment to finding new PPA solutions for unsubsidized renewable energy developers and offtakers, with contracted revenue that offers attractive returns and low risk profiles for investors”.
California close to 6GW online BESS milestone
California now has nearly 6GW of battery storage capacity online, the California Independent System Operator (CAISO) revealed on July 11.
CAISO president and CEO Elliot Mainzer said total BESS capacity on the grid increased to 5.6GW as of July 1.
“Just three years ago, we had about 500MW on the grid and this rapid growth of energy storage in Cali-
fornia has significantly improved our ability to manage through challenging grid conditions,” Mainzer said.
He said it was essential for the state to continue to invest in innovative technologies such as energy story in the face of more frequent climate extremes including record heatwaves and droughts.
CAISO says 1MW of electricity provides roughly enough power to meet the
demand of 750 homes, while 5,000MW can provide enough electricity to power around 3.8 million homes for up to four hours before the batteries need to be recharged.
The battery systems are increasingly being paired with new or existing solar resources at the same location because such facilities can provide greater operational efficiency and flexibility, the operator says.
SVOLT breaks ground for Thai battery plant
SVOLT said on July 10 it had broken ground for construction of a battery modules and packs factory in Thailand.
The Chinese battery maker said the Chon Buri province facility, expected to be completed by the end of this year, will strengthen its presence in the thriving Thai EV market.
The facility is designed to have an annual production capacity of around 60,000 modules.
One line will be dedicated to the production of modules for hybrid electric vehicles, while the second line is designed to produce modules and packs for plug-in hybrid electric vehicles and battery electric vehicles.
Both production lines will use independently developed pouch cells and prismatic cells, with advanced automated welding processes and monitoring equipment
ensuring efficient, highquality production.
Chairman and CEO Hongxin Yang said SVOLT’s advanced lithium battery tech would form the basis of a local battery chain supply network that would contribute to China’s new energy market expansion.
SVOLT’s Thai operations are through its wholly owned subsidiary SVOLT Energy Technology (Thailand).
Canada agrees battery incentives deal for Stellantis, LGES plant
Stellantis and LG Energy Solution (LGES) are resuming construction of their NextStar Energy EV battery plant in Canada under a deal worth up to C$15 billion ($11.4 billion) in tax breaks for the project, Ontario’s provincial government confirmed on July 6.
The battery partners had been pressing provincial and federal government leaders to scale up support for NextStar in line with that available in the US under the Inflation Reduction Act.
Now Ontario is to provide C$5 billion in tax breaks for the project with a further C$10 billion coming from the federal government.
Production at the plant is planned to start in 2024 with an eventual annual production capacity in excess of 45GWh.
A statement issued by Ontario premier Doug Ford and other ministers said the incentives were a direct response to those offered by the US government — but warned they could be reduced or cancelled if the US should drop its support for battery makers.
Ford said the deal also extends to a project by Volkswagen and its subsidiary PowerCo SE to establish the auto giant’s first overseas EV battery cell manufacturing plant in Ontario. Volkswagen could receive up to C$13 billion in performance incentives.
However, incentives are linked to the amount of batteries that Stellantis produces and sells, in line with the conditions in the agreement for the Volkswagen battery cell manufacturing plant.
NextStar Energy is one of eight battery plants that LGES has secured in North America in response to its growing EV market.
European Court of Auditors warns on EU battery ambitions
The EU risks falling behind in its bid to become a global battery powerhouse, according to a report published on June 19 by the European Court of Auditors.
Access to raw materials remains a major roadblock, along with rising costs and fierce global competition. The EU’s efforts to grow its battery production capacity might therefore not be enough to meet the increasing demand, meaning it may fall short of its 2035 zero-emission goal, the auditors warn.
“Nearly one in every five new cars registered in the EU in 2021 had an electrical plug, and the sale of new petrol and diesel cars is to be banned by 2035. This has made batteries a strategic imperative for the EU,” says the report.
“But Europe’s battery industry is lagging behind its global competitors, particularly China, which accounts for 76% of global produc-
tion capacity.”
Annemie Turtelboom, the ECA member who led the audit, said: “The EU must not end up in the same dependent position with batteries as it did with natural gas — its economic sovereignty is at stake.”
Between 2014 and 2020, the battery industry received just €1.7 billion ($1.9 billion) in EU grants and loan guarantees, on top of state aid of up to €6 billion authorized between 2019 and 2021, mainly in Germany, France and Italy, says the report.
The EU’s battery production capacity is developing rapidly, with the potential to grow from 44GWh in 2020 to 1,200GWh by 2030 claims the report. However, this projection is not guaranteed and could be jeopardized by geopolitical and economic factors.
“First,” says Turtelboom, “battery manufacturers may abandon the EU in favour of other regions, not
least the US, which offers them massive incentives. Unlike the EU, the US directly subsidizes the production of minerals and batteries, as well as the purchase of electric vehicles made in the US using American components.
“Second, the EU depends heavily on imports of raw materials, mainly from a few countries with which it lacks trade agreements: 87% of its raw lithium imports come from Australia, 80% of manganese imports from South Africa and Gabon, 68% of raw cobalt imports from the Democratic Republic of Congo, and 40% of raw natural graphite imports from China.
“Although Europe has several mining reserves, it takes at least 12-16 years from their discovery until production, making it impossible to respond quickly to increases in demand.”
“Third, the competitiveness of EU battery production may be jeopardized
Basquevolt opens solid state center
Basquevolt, the solid state lithium battery developer and manufacturer, inaugurated its innovation center in mid-June in an official ceremony presided over by the president of the Basque government, Iñigo Urkullu and the company’s investment partners.
The company claims that its technology will revolutionize the lithium battery market as the greater efficiencies and safety of solid state batteries replaces existing lithium chemistries.
The company CEO, Francisco Carranza, said he expects to start producing its 20Ah cells by the end of the year. A spokesperson said solid state lithium technology
can “reach a high energy density — 1,000Wh/l and 450Wh/kg) — while reducing overall battery pack costs.
“Basquevolt battery cells can be produced through a more efficient,
less complex process, creating a 30% reduction in the capital investment needed per GWh in a gigafactory and 30% less energy used per kWh produced, compared to lithium-ion batteries.”
by rising raw material and energy prices. At the end of 2020, the cost of a battery pack (€200 per kWh) was more than double the amount anticipated. In the last two years alone, nickel has risen in price by over 70% and lithium by 870%.”
The auditors also criticise the lack of quantified, time-bound targets. Some 30 million zero-emission vehicles are expected on European roads by 2030 and, potentially, nearly all new vehicles registered from 2035 onwards will be battery-powered. However, the EU’s current strategy does not assess the capacity of its battery industry to meet this demand.
The auditors warned of two potential worst-case scenarios should the EU battery production capacity fail to grow as projected.
The first is that the EU could be forced to delay its ban on vehicles with combustion engines beyond 2035, thus failing to meet its carbon-neutrality objectives.
The second is that it could be forced to rely heavily on non-EU batteries and electric vehicles, to the detriment of the European automotive industry and workforce, to achieve a zero-emission fleet by 2035.
GS Yuasa announced the start of operations on June 15 of a 240MW/720 MWh BESS to support a wind power facility in Japan.
Yuasa said the lithiumion BESS delivered to the North Hokkaido Wind Energy Transmission Corporation started operations last March, following a
16-month installation period that ended in November 2021.
The system, equipped with about 210,000 modules and 3.3 million cells, will be maintained by Yuasa for 20 years.
Yuasa manufactured the batteries, which use the firm’s proprietary Starelink
battery maintenance service and associated remote monitoring technology to constantly monitor the voltage of all cells.
The BESS will help to suppress output fluctuations caused by weather changes and aid grid stabilization, the company said.
EU batteries chief on guard over battery subsidies from China, US
European Commission VP and batteries czar Maroš Sefcovic has said the bloc is monitoring “massive” Chinese and US battery industry subsidies — but signalled a conciliatory approach to protecting European manufacturers.
Sefcovic said while attending the opening of BASF’s joint center for battery material production and battery recycling in Germany on June 29: “We are looking carefully at China’s massive subsidies to its industry, in particular clean-tech innovation and manufacturing, and ways to protect our own.”
The EU is also in contact
with its “US friends” regarding the Inflation Reduction Act, which he said could lead to unfair competition, close
markets, and fragment critical supply chains.
Such incentives in several countries are affecting the EU’s capacity to succeed in the green and digital transition.
Sefcovic said the EU still needed to work and trade with China but should “focus on de-risking rather than decoupling”.
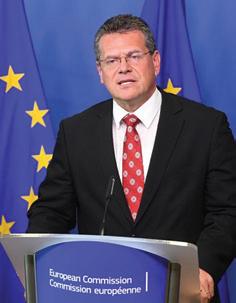
However, where trade is not fair, he said Europe must respond more robustly.
According to BASF, its new plant in Schwarzheide is Germany’s first production site for high-performance cathode materials and also the first fully automatic
Report reveals €13bn cost of Europe battery materials plan
The EU needs to invest more than €13 billion ($14 billion) by 2040 to guarantee just a quarter of key battery materials from European sources to power its green energy agenda, says analysis released on May 9.
The study by European electrochemical and thermal energy storage research center, CIC energiGUNE, assessed the impact of the Critical Raw Materials Act published by the European
Commission in March.
Study author and CIC sustainability expert, Andrea Casas, says analysis of the European Commission’s own estimates show the bloc will need to invest €7 billion by 2030 and €13.2 billion by 2040 to guarantee European sources of 25% of the region’s demand for lithium, cobalt, nickel, manganese and natural graphite.
EU member states could expect to contribute up to
€5 billion in public funding by 2040 towards the overall total, if the bloc wants to follow the lead of the US in supporting its battery sector under the Inflation Reduction Act.
However, the study does not comment on whether the bulk of the investment will come from European Commission coffers or private investors.
large-scale production plant for cathode materials in Europe.
The plant is sold out for the next few years and will supply products tailored to the specific requirements of cell manufacturers and automobile manufacturers in Europe.
Meanwhile, Sefcovic, who has championed the European Battery Alliance that was set up in 2017, said it has attracted more than €180 billion ($196 billion) of investments to date.
“There are now more than 160 industrial projects being developed along the entire value chain, with around 30 announced lithium-ion gigafactories and around 70GWh installed capacity by 2022.
batteries for mobility and energy storage is expected to increase 89-fold by 2050, Casas says.
Meanwhile, the demand for rare earths used to manufacture permanent magnets used in wind turbines or electric vehicles should increase six to seven times by 2050.
Casas says it is indisputable that critical raw materials are essential to EU plans for a network of battery gigafactories to support the clean energy transition.
The COO of Volkswagen’s PowerCo battery cells subsidiary, Sebastian Wolf is among the latest keynote speaker to be announced for this year’s Batteries Event, which will open in Lyon, France, on October 10.
Conference organizer Avicenne Energy has also published the first detailed preliminary program for the event, where more than 150 speakers
are set to address more than 1,000 delegates.
The Batteries Event will be held at the Centre de Congrès until October 13 and cover a range of topical issues impacting the industry ranging from trends and best practices to battery production and recycling.
Program and registration details are online. See also the events section of this magazine.
According to Casas, other strategic raw materials are also likely to require large investments such as copper for electrifying infrastructure, silicon for solar panels or platinum group metals for hydrogen electrolysis.
To date, the EU is almost exclusively dependent on imports for many critical raw materials, Casas says.
“In addition, the suppliers of these imports are often highly concentrated in a small number of third countries, both at the extraction and processing stages.”
All this becomes even more relevant when taking into account global demand for lithium to manufacture
However, she says it is also necessary “to be clear that deploying this plan will require significant investments to ensure the effectiveness of the measures taken”.
The European Commission’s Critical Raw Materials Act defined this year, for the first time, a list of strategic raw materials vital to powering the bloc’s green tech agenda, including domestic battery manufacturing for EVs and energy storage systems.
The Commission has said that by 2030, Europe should not be dependent on any single third country for more than 65% of its supply of any strategic raw material, unprocessed and at any stage of processing.
Morrow loan deal boost for for giga plans in
Morrow Batteries said on July 5 it had achieved an 86% yield of battery cells production at its customer qualification in South Korea just four months after opening.
CEO Lars Christian Bacher praised the results, saying industry standards put the initial average yield of new production lines at 70%.
Morrow started test production at Chungju-si in
February and has produced more than 600 prismatic cells with NMC battery chemistry.
The Norway-based battery maker said its industrial scale-up is now on track.
Morrow said it will produce a few hundred LFP batteries at B-sample stage during the summer.
The customer qualification plant will have a capacity of 2,000 battery cells per month.
Australia critical minerals blueprint launched
Australia unveiled a new critical minerals strategy on June 20, including a pledge to pump A$500 million ($332 million) of fresh investment into sectors including battery materials supply.
Resources and Northern Australia minister Madeleine King said the country aimed to become a “globally significant producer of raw and processed critical minerals”.
Independent modelling has found increasing exports of critical minerals and energy-transition minerals could create more than 115,000 new jobs and add
A$71.2 billion to GDP by 2040, King said.
But jobs could more than double that figure and GDP increase to A$133.5 billion by 2040 if Australia builds downstream refining and processing capability and secures a greater share of trade and investment.
Australia is the world’s largest producer of lithium — accounting for some 47% of world supply in 2020.
King said it is the third largest producer of cobalt and fourth largest producer of rare earths and produces significant amounts of metals such as aluminium, nickel and copper.
€500m R&D financial support awaits EU battery projects
Battery developers are being urged to make bids for millions of euros in financial support still up for grabs in Europe.
Wouter Ijzermans, executive director at the Battery European Partnership (BEPA), gave details of around €500 million ($547 million) in potential aid still available from the EU’s Horizon Europe R&D program during the International Flow Battery Forum in Prague on June 27 (see our events section).
BEPA works in tandem
Norway
On May 12, Morrow said it had agreed a loan deal of NOK567 million ($53 million) to support development of its battery cells projects at Arendal in Norway, where production is to
begin in 2024.
An investment decision to start on the next facility — the Eyde 1 14GWh per annum batteries production plant — will be taken in the first half of 2024.
Fitch upgrades China’s CATL to A- rating
Fitch Ratings, the international credit rating agency, announced on June 26, it had upgraded CATL, the China-based battery producer to a senior unsecured rating to A- from BBB+.
To put this into context this says the likelihood of defaulting on its debt is equivalent to that of Spain or Poland not paying their international obligations. Both countries are also rated A-.
Fitch says it expects the firm to have a compound annual growth rate of 18% over the next three years and its EBITDA (earnings before interest tax deductions and amortization) of around 15%.
Fitch says: “The company’s performance in 2022 and the first quarter this year demonstrates solidification of its dominant market share, technological capability and capacity leadership. These are commensurate with or stronger than peers’ in the respective industries.
“The ratings are con-
strained by the current nature of the volatile, evolving EV battery sector, which sees rapid changes in its competitive environment and technology. Regulatory risks in specific markets could also constrain CATL’s overseas growth, but Fitch believes the risks are manageable.”
Fitch believes CATL will continue to maintain its leading global market position and has a strong order book that supports future growth with adequate leverage headroom.
According to SNE Research, CATL had a 37% share of the global EV battery market in 2022. “We expect CATL to continue overseas penetration through exports and growing localized production amid tighter geopolitical regulation,” Fitch said.
CATL’s EV battery is a leader in international markets with a non-China market share of 22.3% in 2022.
with BATT4EU — a program established under Horizon.
Ijzermans said nearly €1 billion had originally been earmarked in funds under Horizon, of which €503 million had been allocated to date. Of the remainder, €21 million has been set aside specifically for nonlithium sustainable batteries for stationary storage with European supply chains.
Applicants for the nonlithium battery chemistry funding have until April 18, 2024 to apply.
Emeren, Matrix partnering for BESS projects in Italy
Solar developer Emeren said on June 27 it was partnering Matrix Renewables to develop up to 1.5GWh of energy storage projects in Italy.
The companies are working on a development service agreement for the BESS portfolio ahead of an expected new capacity market auction in late 2023 aimed at boosting the deployment of solar in Italy.
Potential battery chemis-
tries to be used in the projects were not disclosed.
The first tranche of developments accepted by Matrix, which is part of private equity firm TPG, includes more than 260MW of standalone BESS projects, the companies said.
Emeren CEO Yumin Liu said BESS systems are vital for the future of renewable energy and the company wants to become a leader in the market.
ESS in 50MW iron flow Germany battery project
Battery storage firm ESS announced plans on June 15 to build a 50MW/500MWh iron flow battery system in eastern Germany in partnership with domestic energy firm LEAG.
The flow battery system at the Boxberg Power Plant site is to be commissioned in 2027, following definitive agreements and financial close for the project, which are expected in the third quarter of this year.
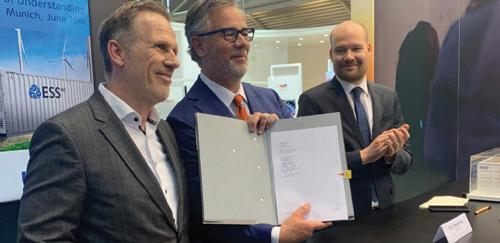
ESS said the 50MW battery module is set to become a standardized building block in LEAG’s plan to deploy 2GWh-3GWh of long duration energy storage.
LEAG and partners plan to invest €200 million ($217 million) and say additional investments are expected as plans progress.
LEAG is a major operator of large-scale lignite mining and coal-fired generation in eastern Germany and wants to transform the coal-dependent region.
The firm plans to develop 7GW-14GW of renewable generation paired with 2GWh-3GWh of energy storage and 2GW of green hydrogen production.
Wind and solar generating infrastructure is already being developed at Boxberg.
India to review EV policy amid lithium ion over-reliance on China
India’s drive to encourage increased take-up of EVs is set to be reviewed amid fears of an over reliance on China, according to the India Lead Zinc Development Association.
ILZDA said in its latest e-newsletter, released on June 14, that the powerful NITI Aayog policy thinktank — also known as the “brains trust” advising Indian prime minister Narendra Modi — plans to
review policies on lithium ion-powered EVs because about 75% of the vehicles are imported from China.
A section within India’s government reckons the country should not be heavily reliant on China and should instead explore other green sources to power future vehicles, ILZDA said.
NITI Aayog director Sudhendu Sinha told the International Conference on Lead & Lead Batteries in
EMEA director of ESS Alan Greenshields told Energy Storage Journal the power module for Boxberg will be built at the company’s Oregon
plant in the US — but there are “ongoing discussions about the right point in time” to also have the firm’s batteries assembled in Europe.
New Delhi last December that the industry should be quick to counter any suggestions that new energy technologies could replace lead as a traditional battery industry.
Sinha said India could not become reliant on any particular battery chemistry or technology and warned that while a number of battery technologies can coexist, “those that are not focused on safety, the environment, safe and sound disposal and traceability will gradually become extinct”.
Nano One in LFP collaboration with Our Next Energy
Nano One Materials and Our Next Energy have signed a joint development agreement to collaborate on the validation, qualification and production of a North American supply of LFP cathode active materials (CAM), the companies said on June 14.
The CAM will be produced at Nano One’s Pilot plant in Candiac, Quebec for potential use in cells for Our Next Energy’s Aries and Gemini energy storage system batteries.
Nano One said it is repurposing the Candiac site to use its patented One-Pot process for the pilot production of LFP CAM, with re-commissioning scheduled for the third quarter of 2023.
Dan Blondal, Nano One CEO and founder, said the partners aimed to develop a “robust and economicallyresilient LFP battery supply chain that is decoupled and environmentally differentiated from the dominance of the overseas market”.
Our Next Energy started production of its Aries LFP battery pack earlier this year.
The company is also building its first battery cell factory, ONE Circle, which is a 20GWh facility in Michigan that should start operations in 2024.
Nano One announced in February it had completed a key milestone in its cathode materials and techno-economic modelling process with an unnamed global auto manufacturer.
ABB starts up 50MW BESS in Philippines
ABB has started up the 50MW BESS it supplied to Universal Power Solutions to strengthen the reliability and stability of the grid on the main Philippines island of Luzon.
ABB said on June 7 its NMC LFP system was its first eStorage Max, preengineered, modular, largescale BESS delivered in the Asia-Pacific region.
Financial details of the project in Limay were not disclosed.
ABB said Limay forms part of a broader contract with Universal, part of San Miguel Corporation Global Power Holdings, for a total 240MW BESS capacity to support the grid on the islands of Luzon and Visayas.
ABB said the Philippines aims to achieve 35% renewable energy generation by 2030 and 50% by 2040.
Calogero Saeli, Global product group manager at ABB, said the project will ensure that the grid is more stable and able to cope with reliability challenges associated with moving to a stronger mix of renewables.
Morrow opens Norway R&D hub
Morrow Batteries opened its research and innovation hub on June 9 that will spearhead further development of the company’s battery tech.
The Morrow Research Centre in Norway is at the University of Agder’s Campus in Grimstad and will produce small battery cells to validate and determine various battery components’ optimal composition and structure.
The facility spans
2,000m2 with an additional 1,700m2 of office space.
Morrow said the center is backed by an unnamed large European automaker through a joint development agreement.
The on-site research team will be responsible for advanced material testing and battery cell testing, including experimenting with new processes and materials.
The facility’s lab includes
Slovenia gets EU green light for BESS state aid
The European Commission said on June 9 it had approved a €150 million ($163 million) state-aid scheme to develop battery storage and renewables in Slovenia.
This follows a spate of recent approvals for EU member states to support battery storage-related projects, amid concerns the bloc is lagging behind the US and Asia in investments.
Slovenia plans to provide individual grants of up to €25 million per beneficiary
to encourage investment in ramping up clean energy projects.
The aid package was approved under the EU’s state aid temporary crisis and transition framework, designed to incentivize the production of equipment for the transition towards a net-zero economy.
In May, the Commission announced approval of an €837 million Spanish aid scheme to finance battery production.
KORE Power set for $850m US battery cells plant loan
KORE Power said on June 9 it had received a conditional commitment for a US federal loan of $850 million to build an advanced battery cells plant in Arizona.
KORE said the loan from the US Department of Energy’s loan programs office, through the Advanced Technology Vehicles Manufacturing initiative, will be used to fund construction of the 1,330,000 ft2 KOREPlex facility.
KOREPlex will produce NMC and LFP cells for EV and BESS batteries to be made at the site.
Civil works on the facility started late last year and operations should start by the end of next year or early 2025.
KORE is working with local colleges and universities in Arizona to establish training programs for the facility’s future workforce.
With its initial lines fully operational, the KOREPlex will have an annual production capacity of 6GWh of battery cells.
The company says it could further increase annual domestic production based on demand for lithium ion batteries.
a dry room and equipment for making and testing active cathode materials and for conducting advanced analyses of materials, electrodes and battery cells.
Morrow is scheduled to start industrial-scale battery cells production at its gigafactory in Arendal, on Norway’s south coast, in 2024.
Schuler project to expand battery sector expertise
A project designed to boost business opportunities for European firms serving the battery sector and counter the impact of Asian rivals was launched on June 2, the Schuler Group has announced.
Schuler said the ‘ENLARGE — interoperable production as enabler for a data-driven battery value chain’ project is backed by funding from Germany’s federal education and research ministry.
The aim is to pool the expertise of German and European companies to serve the growing market for battery cell production equipment and to create a counterweight to established suppliers, especially from Asin region, Schuler said.
The project is to run for three years and aims to develop uniform systems for data exchange, described as a “kind of meta-
standard for battery cell production” to boost cooperation and networking among firms.
Hermann Uchtmann, head of battery mass production solutions at Schuler, said: “The goal is flexible, networked and adaptive battery production.
“This is the only way that mechanical and plant engineering in Germany and Europe will be able to bid for equipment for the gigafactories that are being set up around the world.”
In addition to Schuler, project partners and associates include the German Engineering Federation, Fraunhofer Research Unit for Battery Cell FFB, Fraunhofer Institute for Manufacturing Engineering and Automation IPA and Siemens.
Schuler completed its acquisition of the Sovema Group last September.
Toray investment ‘to boost Korean separators business’
Toray Advanced Materials Korea (TAK) said on June 1 it had signed a contract to acquire a 70% stake in Toray Battery Separator Film Korea (Toray BSF). Both companies are part of the Toray Industries group.
South Korea-based Toray BSF is also the core production base for separators supplied by the group’s operations in Japan to battery makers worldwide.
TAK said the acquisition, for an undisclosed
sum, would help the group strengthen Korea’s battery supply chain at a time when demand for separators is expected to accelerate — largely driven by the EVs market.
The deal comes after South Korea said in April it was launching a multibillion dollar program to defend and expand its battery industry, amid fears lucrative US tax breaks and incentives are tipping the global battery trade balance stateside.
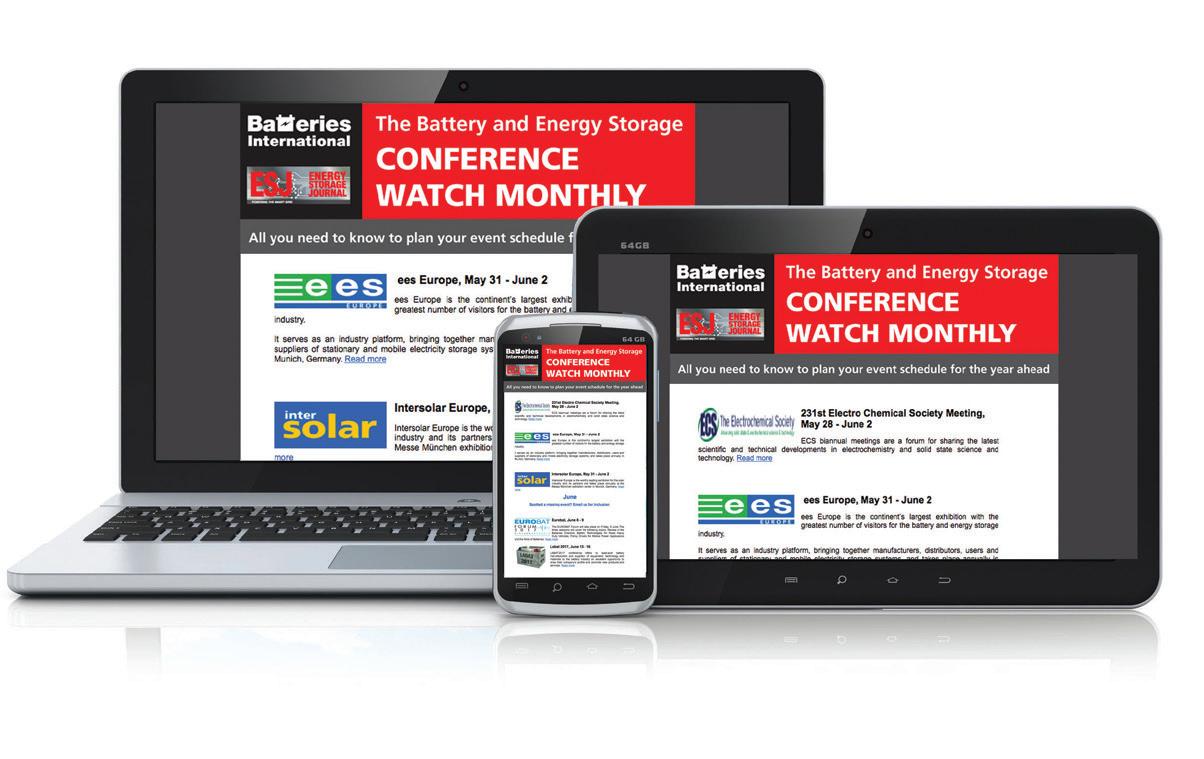
Posco de-risks battery material supply chain with EcoGraf graphite deal
Posco International, the South Korean steel giant, is to buy battery anode material products from EcoGraf the Australian graphite manufacturer, under a 10-year supply deal, the companies said on May 31.
They will also cooperate on EcoGraf’s development of graphite mining projects in Tanzania — with South Korea-based Posco set to provide financing, engineering and construction.
Technical collaboration on developing customized purification technologies will “de-risk short-term battery material supply” in South Korea, Europe and North America, the firms said.
Australia-listed EcoGraf is to supply 7,500 to 12,500 tonnes of battery anode material in the first year following the start of production, rising to 20,000 to 40,000
tonnes annually in years six to 10.
Posco said the deal helped provide a secure supply for its Posco Future M group business [which changed its name from Posco Chemicals last March] and which manufactures natural graphite anodes for lithium ion batteries used in electric vehicles.
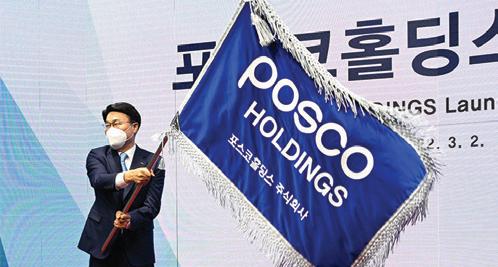
A successful technical assessment of EcoGraf’s product performance has already been conducted.
According to EcoGraf, while traditional demand for graphite is largely tied to the steel industry, there is increasing demand for graphite suitable for use in electric vehicles.
Spherical graphite (SpG), also known as battery-grade graphite, is the product that is consumed as an anode in lithium ion batteries.
EcoGraf said flake graphite concentrate is processed into ultra-high-purity (>99.95% C) with particle sizes ranging from 10 to 25 microns.
These are then used as a battery anode material, with SpG’s special electrical conductivity making it a critical component in anode manufacture.
EcoGraf said on April 18
it had signed a framework agreement with Tanzania’s government for the Epanko graphite project.
The company said it would use its proprietary HFfree purification technology to process Epanko’s flake graphite without the use of hydrofluoric acid to produce high performance battery anode material.
Redflow to supply California microgrid flow battery
Redflow announced on June 1 it will supply a 20MWh flow battery system for a solar-storage microgrid project in northern California.
The zinc-bromine BESS for the Paskenta Band of Nomlaki Indians — a federally recognized sovereign
nation — has been approved and funded by the California Energy Commission (CEC) under its $140 million long-duration energy storage grant program.
Redflow will supply 2,000 ZBM3 batteries in its 200kWh modular en-
ergy pods, for delivery in 2023 and 2024.
The company has signed a definitive supply agreement with Faraday Microgrids covering battery supply and technical support.
A formal notice to start on the project was to have been issued in July.
The project represents Redflow’s largest single sale and deployment of batteries to date, following the installation of a 2MWh flow battery system in California for Anaergia last year.
The Automotive Cells Company (ACC) has formally opened its €7 billion ($7.5 billion) flagship gigafactory in France — with the first of three 13.4GWh production blocks at the site starting operations by the end of the year.
ACC, a consortium of Stellantis, TotalEnergies (via its Saft subsidiary) and Daimler’s Mercedes-
Benz, said on May 30 the other two units at the Billy-Berclau Douvrin gigafactory, in the Hautsde-France region, will come on line by late 2024.
The site will produce lithium ion battery cells and modules across an area of more than 60,000m2, with total annual production capacity reaching 40GWh by 2030.
ACC said construction of the site took 17 months at a cost of nearly €800 million.
Meanwhile, production is set to start at ACC’s two other gigafactory projects in Germany in 2025 and Italy in 2026. By 2030, a total of 2.5 million battery modules will be leaving all three gigafactories each year, CEO Yann Vincent said.
Redflow CEO Tim Harris said the 20MWh BESS is one of several large-scale opportunities in the pipeline as the firm continues to focus on US and Australian markets.
“For this project, Redflow’s battery system is designed to charge from solar and discharge throughout the remainder of the day, reducing grid demand and boosting the energy security of the Paskenta Rancheria,” he said.
The microgrid is part of the Tribe’s efforts to achieve greater energy sovereignty and reduce the use of fossil fuels.
Powin selects Jabil to produce BESS in US
Powin said on May 23 it had selected Floridabased Jabil to produce its Stack750E utility-scale energy storage system product in the US.
Starting in the fourth quarter of 2023, Jabil is to produce an initial annual capacity of 2GWh, with plans to ramp up to 4GWh per year.
Powin said it selected Jabil based on factors that included the firm’s environmental health, social equity and sustainable practices.
Stuart Bolland, Powin’s COO, said the deal underlined its commitment to building a domestic energy storage supply chain.
The move will reduce supply chain risk and benefit Powin customers who can take advantage of incentives under the Inflation Reduction Act for buying US-content products, Powin said.
The US Department of Energy has reversed its decision to award Microvast a $200 million grant
to build a lithium ion battery separator plant, amid claims the company has links to China.
Republican senator John Barrasso claimed on May 22 the company had “close ties to communist China” and should not receive US government aid or loans.
Barrasso has also introduced draft legislation that would prevent the DOE from making financial awards to firms “beholden to China”.
However, Microvast founder, chairman and CEO Yang Wu said on May 24 neither China’s government or the Chinese communist party had any ownership of the firm or influenced operations in any way.
Wu, an American citizen, said he was surprised at the DOE’s decision to withdraw the grant, “which was designed to help build a new facility in Kentucky that would employ hundreds of people”.
In the meantime Micro-
Brazil takes Li investments drive for backing on NYSE
Brazil has turned to one of the world’s major financial centers to energize investment in the country’s battery materials industry.
Secretary of geology, mining and mineral transformation, Vitor Saback, was at the New York Stock Exchange on May 9 to seek backing for the launch of the lithium valley project in the state of Minas Gerais.
Saback, representing mines and energy minister Alexandre Silveira, said the aim was to garner investment in the Jequitinhonha valley to exploit lithium reserves and become a supplier to the global batteries market, while creating jobs and improving livelihoods of the local population.
The investment drive came four months after
newly-elected president, Luiz Inácio Lula da Silva, was sworn into office pledging an investor-friendly approach to expanding the energy sector.
According to Saback, the area around the valley comprises 14 municipalities that have the largest lithium reserves in the country.
Lithium sector players Companhia Brasileira de Lítio, Sigma, Atlas Lithium Corporation, Latin Resources, Deep Rock and Lithium Ionic all have projects in the region at different stages of development, the mines and energy ministry said.
Studies by the Brazilian Geological Survey indicate the existence of 45 “high economic potential” deposits in the area.
vast intends to continue to invest significantly in its US expansion, Wu said.
“The DOE decision does not alter our plans to commercialize our polyaramid separator. We will continue to invest in a pilot line that will add 10 million m2 of capacity this year.”
Texas-headquartered Microvast was founded in 2006.
Chief financial officer Craig Webster said the firm’s priority was to complete its 4GWh cell and module manufacturing plant in Tennessee — on which work started in 2021 and in which Microvast has invested more than
$300 million.
“Based on our backlog of orders, we expect revenue in the US this year to be in excess of $100 million,” Webster said.
“The DOE decision also has no impact on our liquidity position, and in fact, it gives us more flexibility on how we plan to undertake our expansion initiatives in the US.”
In 2022, Microvast established its new energy storage division in Colorado along with a technology and testing center to support the growth of utilityscale energy storage systems in the US.
€4m expansion plan for BMZ’s Visatronic
Visatronic, the newly acquired subsidiary of Germany’s BMZ lithium battery systems group, is to invest nearly €4 million ($4.3 million) to expand production capacity.
BMZ said on May 31 that the electronic flat modules producer, which it took over as of March 1, plans to increase the production area at its plant in Mainhausen by 800m² to eventually double manufacturing capacity and sales — although the company did not disclose any numbers.
Visatronic’s workforce is also set to expand to nearly 100.
The project follows increased orders from customers, the company said.
BMZ founder and CEO Sven Bauer said in March that the takeover of Visatronic — a long-standing supplier to the battery company — “strengthened another important madein-Germany factor in battery manufacturing”. Bauer said such moves were indispensable for tech companies in times of uncertain supply chains.
Russian EV, ESS battery prototypes ‘ready this year’
Russia claimed on May 12 it will have produced prototype batteries to power a domestic range of EVs and energy storage systems by the middle of the year.
State-owned Rosatom says its energy storage manufacturing subsidiary, Renera, will have the first
lithium ion battery prototypes ready by mid-2023.
The company said the EV batteries will have a driving range of up to 500km and be adapted to operation and charging at low temperatures, taking into account Russia’s complex weather.
Fortum, Terrafame launch battery material experimental partnership
Fortum and Terrafame are partnering up for an experimental battery recycling project, the Finnish companies announced on June 14.
The project aims to use metals that energy company Fortum recovers from lithium ion battery black mass in Terrafame’s battery chemical production. Operations were set to start in June and the project is expected to span several years.
The partners said fully replacing the mining of pri-
mary raw materials, such as nickel and cobalt, with recycled materials was “not possible in the near future”. However, Tero Holländer, head of the batteries business line at Fortum Battery Recycling, said the partnership aimed to boost sustainability of using Finland’s minerals wealth to develop a domestic batteries industry — and was a step towards “a more selfsufficient European battery manufacturing industry with less need to use im-
ported raw materials”.
Fortum said on April 27 it had started commercial operation of its lithium hydrometallurgical battery material recycling facility in Finland.
The company claimed the plant was the largest in Europe in terms of recycling capacity and can also recover 95% of the valuable and critical metals from battery black mass and reuse them to produce new lithium ion battery chemicals.
Altium signs non-binding MoU with Marubeni Corp
Altilium Metals said on July 6 it had signed a nonbinding memorandum of understanding with Marubeni Corporation for a lithium ion battery recycling partnership.
The companies plan to develop an EV battery recycling businesses in the UK and Europe — including creating a UK supply chain of end-of-life lithium batteries.
Altilium Metals claims
to be the only company in the UK recovering lithium, nickel and cobalt in a battery-ready cathode active material from waste EV batteries at its scale facility in Devon.
The firm said it recently completed a feasibility study for the potential development of an EV battery recycling facility in northeast England with the capacity to process scrap from more than 150,000
EVs per year and producing more than 20% of the UK’s expected CAM (cathode active material) demand by 2030.
Altilium CEO Kamran Mahdavi said the Marubeni partnership will also cover work to secure the supply of feedstock including black mass and gigafactory scrap as well as further developing Altilium’s proprietary CAM technology.
Study to consider switch from lead to Li processing at Glencore’s Portovesme
Lead and zinc processing at Glencore’s Portovesme subsidiary in Italy could be replaced with a lithium ion battery recycling operation in partnership with Li-Cycle, the companies revealed on May 9.
The announcement came just weeks after Energy Storage Journal reported that a review into the future of lead smelting and refining at Portovesme was under-
way.
Glencore and Canadabased Li-Cycle have signed a letter of intent to jointly study the feasibility of — and later develop — a hub facility at Portovesme to produce materials including nickel, cobalt and lithium from recycled batteries.
The definitive feasibility study will start mid-2023 and should be
completed by mid-2024.
Subject to a final investment decision, the partners say construction of the hub could follow with commissioning in late 2026 to early 2027.
Glencore’s global head of recycling Kunal Sinha said if the repurposing of the site goes ahead, Portovesme would become the group’s first facility to produce battery-grade lithium.
RecycLiCo Battery Materials said on June 12 it was launching a 50-50 lithium ion battery recycling joint venture in Taiwan with Zenith Chemical Corporation.
The companies will build their initial 2,000 tonne per year commercial plant at an estimated cost of $25 million.
RecycLiCo said both sides had agreed on phased funding for the project.
Zenith’s 50% contribution will be funded in cash while RecycLiCo will have a 10% stake in the joint venture in return for a licence of its technology, with of its interest paid in cash.
Zenith specializes in the production of nickel-based chemicals, including highpurity nickel sulfate for lithium ion batteries.
The partners said that since signing a memorandum of understanding last February, they have worked with an unnamed battery materials company to validate RecycLiCo’s process and confirm the quality of it high-nickel cathode precursors and lithium chemical products.
Under the joint venture deal, which is subject to various regulatory approvals, RecycLiCo will receive a royalty on net product sales and Zenith will receive four million RecycLiCo shares and six million share purchase warrants.
RecycLiCo chairman Paul Hildebrand said Zenith’s technical expertise in chemical processing would help the partnership progress rapidly to starting operations.
RecycLiCo was formerly American Manganese until the company announced its name change last October.
US $192m boost for Li R&D, battery recycling, innovation
The US is launching an advanced battery R&D consortium focused on securing supplies of critical battery materials needed for nextgeneration EVs.
The Department of Energy announced the move on June 12 as part of a $192 million funding program including a new battery recycling
initiative that will feature a national disposal and collection education program.
Up to $60 million of the overall funding will support creation of the R&D consortium aimed at encouraging EV manufacturers, universities, mineral and material suppliers and others to work together in
planning the next phase of an anticipated expansion of EV sales.
The DOE is also continuing its lithium ion battery recycling prize scheme, which was launched in 2019 and has awarded $5.5 million to date for innovative solutions to collecting, sorting, storing and transporting
European Li recycling ‘viable by 2035 with more investment’
The EU could see lithium ion battery recycling become a profitable business before 2035 but the sector will need greater investment to get there, says a new study released on August 16.
More than €2 billion ($2.1 billion) in investments into the EU recycling market for lithium batteries are forecast by 2030, according to the study by the strategy consulting business unit of PricewaterhouseCoopers and Germany’s RWTH Aachen University.
Handling further market growth through to 2035 will require additional investments of €7 billion, but EU recycling could then become viable and sustainable with a projected revenue of
Hoppecke is to work with China’s Huayou Recycling Technology on lithium ion battery recycling development, the companies announced on May 16.
The Germany-based lead battery company has signed a memorandum of understanding with Huayou, a subsidiary of Huayou Cobalt.
Details of the agreement were not disclosed, but Hoppecke said the move
around €8 billion and a potential fall in battery costs.
However, while recycled material can contribute up to 60% of battery requirements in 2040, a completely closed loop “will not be possible until well beyond then”.
Regulatory changes in the EU, such as those included in the new Batteries Regulation, will help drive recycling, the study says.
Meanwhile higher electrification rates and the rampup of EU cell production to around 900GWh in 2030 could boost the recycling market to around 6,000 kilotonnes of end-of-life batteries in 2040.
In 2035, recycled material may account for up to 30% of Li, Ni, and Co demand
aimed to “create future solutions for a circular economy for lithium ion batteries”.
Hoppecke said it was the first European company with which Huayou had agreed a cooperation deal.
Hoppecke said it aimed to use its expertise to support future lithium battery recycling, which it said was “significantly more complex and complicated” than with lead acid batteries.
for battery cell production. By 2040, battery recycling in Europe is predicted to rise 10-fold compared to 2030, which the study says will initially be driven by gigafactory scrap.
“With more recyclate available at competitive cost, a positive impact on battery prices can be expected through reducing CAM price by up to 20%, further spurring electrification and recycling market uptake.”
A report published last year by Belgium’s KU Leuven research university warned the EU could face problems around 2030 from global supply shortages for five metals — especially lithium, cobalt, nickel, rare earths, and copper.
In January, Hoppecke announced that its newly launched batteries production plant in Poland secured ISO 9001:2015 and ISO 14001:2015 certification for quality and environmental management.
Poznan is home to the manufacture of Hoppecke’s latest pure lead AGM batteries series, where production was launched in spring 2022.
spent and discarded lithium ion batteries.
A total of more than $7 million has now been allocated as part of the overall funding program to support the latest iteration of the prize as well as a new ‘breakthrough contest’.
US energy secretary Jennifer Granholm said the investments will ensure the US “has a secure and sustainable domestic supply chain and strengthens our economy”.
Narada lead batteries pledge to boost environmental credentials
China-based Narada Power says it is committed to ramping up its recycling of lead batteries as part of its corporate social responsibility commitments.
Details of the lead and lithium battery giant’s recycling and environmental management activities are included in Narada’s CSR report for 2022, published earlier this month.
Narada says its Huabo Technology subsidiary handles and uses about 1.2 million tonnes of waste lead batteries and lead-containing waste each year.
That allows the production of 590,000 tonnes of secondary lead annually, which can save 5.9 million tonnes of primary lead ore each year.
Narada says it has also been an active participant in a pilot national centralized battery collection and transfer program for lead battery producers.
The company says it has set up 22 transportation hubs serving more than 370 battery collection outlets in seven cities and provinces including Zhejiang, Anhui and Hubei provinces, “forming a fully-closed industry chain”.
The company has achieved a national ‘standardized recycling rate’ of waste lead batteries in excess of more than 60% from 2019 to 2021 and plans to go further.

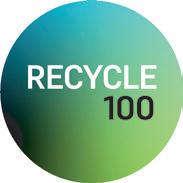
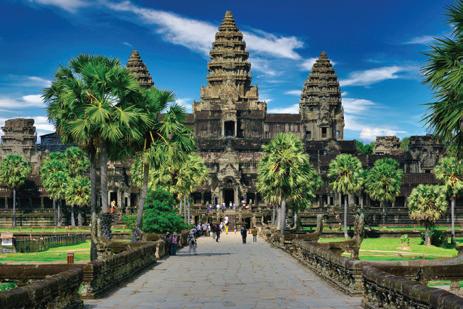
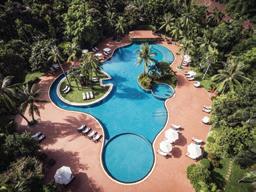
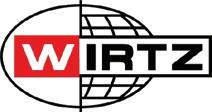
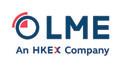


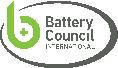


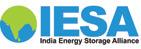
In defence of lead … and lithium
technology at Exide Technologies spotted in the early 2010s that many of the objections, mostly about price, were being overcome.
“We’re watching lithium batteries slowly climb the energy storage chain,” he said. “They’ve started to make the jump from laptop batteries to small hand-held tools. It won’t be too long before they will be powering golf buggies and forklift trucks.”
Trinidad’s projections proved true.
Now it’s hard to find a hand-held tool — from electric screwdrivers to chainsaws to vacuum cleaners — that doesn’t have its battery counterpart. In the past four to five years lawn mowers powered by lithium batteries have entered the market for electric versions given they offer freedom from a power cable.
And yet further up the energy chain, lithium batteries now account for roughly a quarter of the motive industrial forklift sector and their market share is growing by around 2% annually.
A decade ago if you mentioned “intercalation” to lead battery engineers their minds would go blank, probably thinking that it was something consenting adults did in the privacy of their home. Talk to the equivalent lithium technician and mention how important cast-on straps are in battery manufacturing and they’d think the same. Probably worse in fact.
In part it was easy to see the confusion, there was a bigotry on both sides of the battery chemistry mixed with an enormous combination of arrogance and ignorance.
And this came from both sides.
From the lead side of thinking, lithium batteries were just another fad that the battery industry would fight off.
“We’d seen off the challenges from fuel cells, supercaps, the laughable two-tonne EV1 from General Motors and even sodium sulfur batteries in cars,” one engineer said to Energy Storage Journal just before the Covid pandemic.
“We were confident that while lithium had its role to play in mobile phones and laptops but knew that it couldn’t fill the spaces needed where heavy duty energy was needed.
“And it was at a laughable cost — we were looking at $1,000/kWh for lithium batteries to power a car when a gallon of gas [petrol] was just a few dollars.”
But commentators such as Francisco Trinidad, the former director of battery
The price of lithium batteries may be close to double that of lead batteries (given some of the extraneous features required) but other factors come into play.
The total cost of ownership can be lower for lithium. The TCO, for example, falls if forklifts are to be used 24/24 in a multiple shift operation. The batteries no longer need to be changed so the downtime of being re-charged is avoided. There’s less inventory too, with no need for the extra battery for the charging. Moreover, the battery lifetime for lithium is longer.
“This ascent up the product chain was inevitable,” says Ray Kubis, a former president of Eco-Bat and EnerSys and now the chairman of bipolar battery firm Gridtential. “The amount of
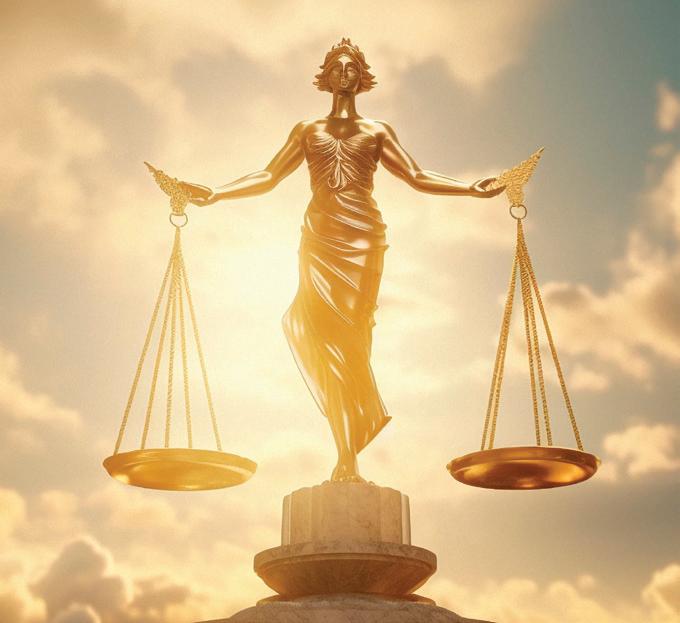
For the last 15 years, the lead battery industry has been trying to come to terms with its potential usurper, lithium ion in all its shapes and forms. Most of the major firms have made real headway in their understanding but there’s still a long way to go. From both sides.
money thrown each year into research by the lithium battery industry is probably the equivalent of all the money invested in R&D for lead in the past 20 years … or even longer.
“Their investments have not been wasted and we’ve watched how lithium performance has shot up. If only if lead had done the same.”
In one of the more poignant reminders of this is the fact that some of the latest lead R&D using equipment, such as the synchrotron at the US’ Argonne National Laboratory, were first used to investigate lithium batteries over 10 years ago.
And lithium research at the ANL has not stopped. Just this February, working with the Illinois Institute of Technology, the research team announced they had tested a lithium-air battery that could power a vehicle with a 1000 mile driving range on a single charge.
Larry Curtiss, team leader and Argonne Distinguished Fellow, said at the time: “The lithium-air battery has the highest projected energy density of any battery technology being considered for the next generation of batteries beyond lithium-ion.”
This was as much as four times above the present day lithium ion and Argonne said “could even power domestic airplanes and long-haul trucks”.
Finding lead R&D
Mention of the advances being made in lithium highlight the attractiveness of the sector to new researchers and why most potential PhD candidates avoid lead — after all this is a chemistry that dates back to 1859 and Gaston Planté’s first rechargeable battery.
This explains the often insufferable style of many in the lithium battery industry. They see themselves as being at the cutting edge of technology and frequently as potential saviours of the planet as we drift into a new decarbonized world powered by renewables.
The fact remains, however, that they are not potential saviours of anything but advancers of an alternative energy technology.
In particular, all the earlier criticisms of lithium batteries on safety, price and recyclability hold true, at least to some extent. For some people — a leap of faith is the only way to find the industry’s claims justifiable.
“Much of the earlier enthusiasm for lithium came from over-excited motor car journalists, ignorant politicians looking for the next bandwagon to land on and a general public hungry for something new,” was the sweeping
CHOOSING THE CHEMISTRIES: THE NEXT PAGES
• No one size of battery fits all needs and the same goes for chemistries, as our cover feature articles show.
• Lead majors Sunlight and Amara Raja explain why they are among contemporaries integrating lithium into their portfolios.
• Lithium ESS proponents Freyr, Fluence and Eleven ES give us their commercial perspectives and we also go back to battery basics, to consider various competing lithium technologies.
over-statement one lead aficionado told Energy Storage Journal quite recently.
There may be some truth in the matter but a more informed look has to check out the technology.
In the area of safety, much improvements to lithium batteries need to be made. At the time of going to press a cargo vessel carrying electric vehicles was being towed to port after a suspected EV battery fire that immobilized the ship. In February 2022, the Felicity Ace container ship sunk at sea after days battling an EV fire for days.
This January, Havila Kystruten, a Norwegian shipping firm, announced a blanket ban on EVs and hybrids from travelling in their fleet — an astonishing edict given that 80% of all new vehicles sold in Norway are electric.
A report in 2021 by IDTechEx, a research consultancy reported that onein-three EV fires occurred with ‘no obvious cause’ while the car was parked. It also noted that 17% of EV fires occur in regular driving and a quarter occur when charging.
While electric vehicles do not pose a greater fire hazard than regular cars, their fires are more difficult to put out. They require a considerably larger amount of water to extinguish. While a burning petrol or diesel vehicle may need 1,600 to 2,000 litres of water to be put out, a fire in an EV often requires as much as 11,000 litres, mainly to cool down the burning battery.
Lithium critics can also point to the huge summer of EV recalls in 2021 when GM led a crowded field of manufacturers at a cost of approximately $1 billion, for GM alone.
Claims about recyclability continue to dog the lithium sector. The image it tries to project is one of being green — decarbonizing the world and so environmentally positive.
In fact it is the opposite. Despite the best efforts of some of the cleverest researchers, there is no way yet of recycling the commonest lithium battery — LiFePO4 — at a profit. The lithium extracted is minimal and the iron and
other elements have little commercial value. Instead the batteries have to be collected, smashed up into the black mass or smelted or hydrometallurgically treated. All that requires expense and energy for little of commercial value.
Recycling of lithium batteries containing cobalt, nickel and manganese can be profitable but waste battery streams carrying these metals can’t be guaranteed.
Recycling problems
Since lithium batteries cannot be put into landfill — they leach and poison the groundwater — they must be processed. The old rule on recycling lithium said that the price of recycling was 10% of every $1000 that a battery cost when new.
Another aspect of the green credentials of lithium is the cost of shipping it around — lithium mined in, say, the Atacama desert in Chile is dispatched to China where it is processed and then the cells are shipped to be made into batteries in Germany where they are put into cars that are then distributed around the world. At the end of battery life they are then shipped back to China.
But the counterpoint to all this is simply that of cost. Although the lead industry is eager to talk up the fact that the price for lithium batteries has risen in the past year and analysts suggest it is likely to remain at $150kWh for some time, the fact is that the price of lithium batteries has plummeted in the last decade from above $1,000kWh to present levels.
And even while the cost of manufacturing and shipping batteries is far higher than lead, overall the total cost of ownership of batteries for EVs can be less than lead if other factors are considered.
In the end, it’s a straightforward and astonishingly simplistic choice — lithium batteries are better than lead ones. Sometimes. And sometimes vice versa with lead over lithium.
Lithium iron phosphate — the new BESS standard
The demand for utility-scale battery energy storage systems that emerged during the early 2000s unlocked a global market for lithium ion batteries that hadn’t previously existed.
Cells based on nickel, manganese, cobalt chemistry dominated supply of lithium ion batteries for stationary storage as well as electric vehicle markets.
As lead times stretched and prices held, in 2018-2019 cell manufacturers in China began tapping into stationary storage markets in the US and Europe, with cells produced using lithium iron phosphate chemistry, regarded as inferior due to lower energy density.
Compared with China and the US,
the two largest markets for grid BESS globally, Europe has lagged despite its mature renewables market, shaped by early policy focused on decarbonizing power supplies.
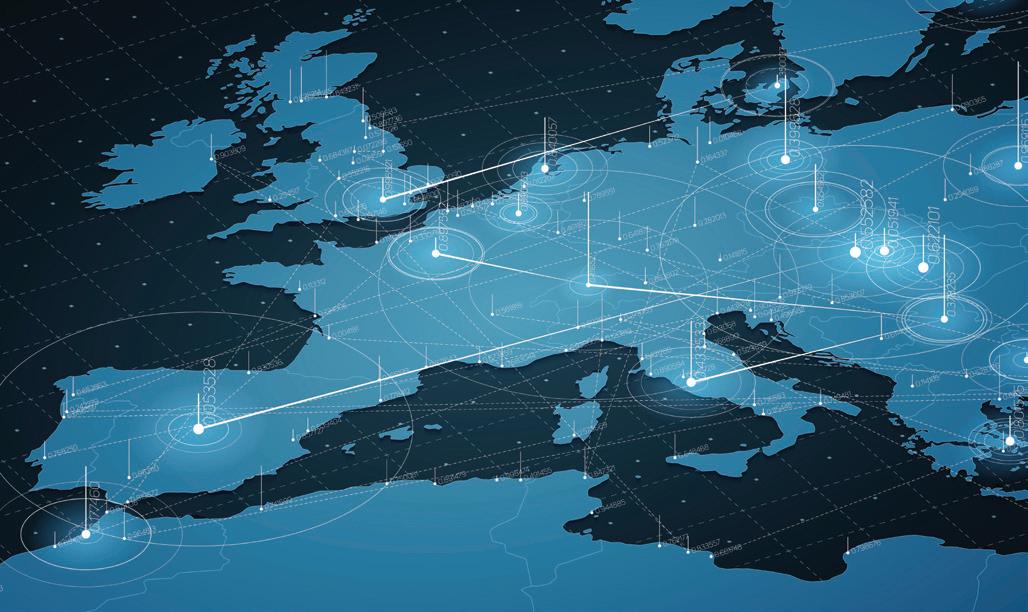
In the coming years, Europe should pick up the pace of grid battery installations, from existing markets, including the UK and Germany, from Italy and Spain, where solar buildout is driving demand for storage, as well as from new markets, including Greece.
From 5GW to 95GW of grid storage Aurora Energy Research forecasts that Europe will install at least 95GW of grid-scale battery energy storage
systems by 2050, surpassing 42GW in 2030, from an installed capacity of just 5GW of installed capacity in 2023.
Average battery duration will increase over time, driven by the buildout of wind and solar generation, which will need storage to meet times of peak demand for power. Aurora predicts that batteries with over four hours’ storage capacity will account for 61% of total installed battery capacity in 2050, compared with 22% in 2025.
Today, Europe’s bid to establish a lithium ion battery industry is still in its infancy.
In the wake of headline-grabbing
Aurora Energy Research forecasts that Europe will install at least 95GW of gridscale battery energy storage systems by 2050, surpassing 42GW in 2030, from an installed capacity of just 5GW of installed capacity in 2023.
Europe’s emerging battery manufacturers see lithium iron phosphate technology as the most suitable and sustainable supply of materials. Sara Verbruggen reports on one side of market opinion.
gigafactory announcements, investors and owners are at vastly different stages of qualifying and preparing their cell technologies for industrialized production. Most aim to capture demand from the grid BESS market as well as EVs and several are backing LFP technology.
Freyr aims to have a gigafactories producing LFP cells from around the mid-2020s in Norway as does ElevenES in Serbia.
Sunlight Group, in Greece, which has been expanding its battery ranges to encompass lithium ion as well as lead acid, is installing a prototype/ pilot line for LFP cells to eventually be used in its lithium ion batteries. Italvolt, in Italy, will start with mass production of NMC cells initially but also plans to produce LFP cells at some point.
Rhomotion, a London-based team of analysts keeping tabs on a growing pipeline of more than 3000 energy storage projects globally, says the share of grid BESS projects that use LFP technology has grown markedly.
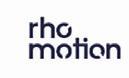
This growth has been mainly at the expense of NCM but also lead acid and other chemistries. In 2020 NCM accounted for half this share, LFP just over a third, lead acid less than a tenth, with other technologies accounting for the remainder. In 2023 LFP technology accounts for nearly 90% of the BESS grid battery chemistry split.
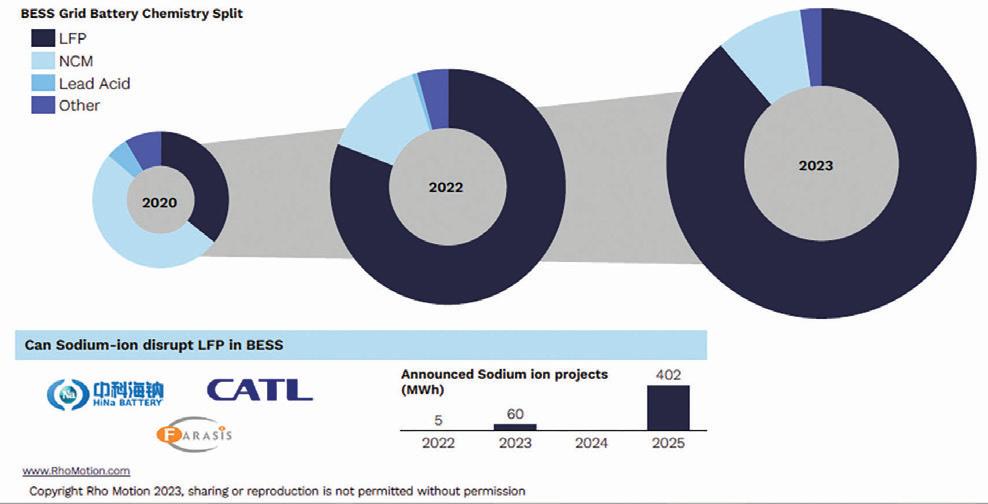
China is the leading market in terms of installed grid BESS capacity, predominantly using LFP cells, which have been exclusively supplied by Chinese manufacturers. Iola Hughes, research manager at Rhomotion, says recent policies around the inclusion of storage with new solar and wind installations have catalyzed even further BESS expansion in China.
The US is the next biggest market for grid BESS. Thanks to last year’s Inflation Reduction Act, standalone BESS will now benefit from the investment tax credit, likely to stimulate more grid storage investments. Hughes says it could still take a year or two for this to reflect in higher volumes of projects getting built and connected.
Europe’s predicted escalation in installations is contingent on changes to energy storage classifications, policy and increased revenue generating mechanisms.
According to Wood Mackenzie, in Europe most regulatory hurdles will be resolved before the end of this decade as demand for flexibility
surges and concerns over security of supply increase.
Several factors have contributed to the rising interest in LFP in markets other than China.
One has been around perceptions that batteries made from LFP cells are safer than those made of NMC cells. Hughes refers to a thermal runaway event that led to a fire in one of the Tesla Megapack modules during precommercial testing in 2021 at Neoen’s 250MW Victorian Big Battery in Australia.
“In 2021-2022 dedicated storage system integrators began turning to LFP, following some developers expressing a move away from NMC,” he says Bloomberg also points out that more production can be expected outside of China, following the last of the worldwide patents that control LFP production outside of China having run out in 2022.
Technological progress is another factor, with performance improvements in LFP cells occurring year-onyear.
Bloomberg also points out that more production can be expected outside of China, following the last of the worldwide patents that control LFP production beyond China having run out in 2022.LFP continues to dominate, is a diversification of chemistries coming
With a 10-15 year head-start in scaling-up their processes, Asiabased battery cell producers have been able to improve production efficiency, thus pricing, compared with competitor producers in Europe and the US, Hughes says.
Márton Pap, project manager for ESS and programme development at ElevenES says: “We can benefit from the low energy prices in Serbia and the relatively low labour costs. Nevertheless, we agree that the EU should introduce incentives to European players so they can be competitive even in the early phases of their developments.”
When establishing partnerships with cell suppliers, BESS suppliers and integrators look for counterparty bankability, scale and track record.
According to Pap, ElevenES is one of the most solid lithium-ion battery projects in Europe, due partly to the industrial experience and heritage of its parent, Al Pack Group, that will help during the scaling up process, and partly due to its step-by-step approach.
“We are moving one step at a time so we can learn and get experience on a smaller scale before moving on to a larger scale: lab, R&D center, Mini Pilot, Mega Plant (1GWh), Giga Phase I (8GWh), Giga Phase II (40GWh).”
ElevenES makes prismatic cells, a format that has been in the market for several years. Blade-like cells are a sub-group of prismatic cells, characterized by relatively thin and long dimensions. The connect points in ElevenES’ cells are at opposite ends, as opposed to on top.
“Customers have to adapt their modules to accommodate this but that isn’t a problem for most of them. In return they can benefit from the advantages of this cell format,
Freyr reaches key milestone, moves toward commercial production for H2 2025
During the past year Freyr, in Norway, has reached key milestones on the journey to industrialized production based on semi-state LFP cell technology, developed by 24M.
Freyr is targeting commercial production in the second half of 2025 from sites in Norway and also in the US to meet demand for stationary storage projects in both markets.
“They need these cells, yesterday. The urgency cannot be understated so we would expect to start seeing them deployed in storage systems for installations in projects soon after,” says Freyr’s investor relations head, Jeffrey Spittel.
In December Freyr formed a company with Nidec. The Japanese company is also a customer.
Nidec Energy will be a customer for Freyr’s cells to use them to manufacture battery energy storage systems for various stationary storage applications.
Before the JV was set up, Nidec had an undisclosed independent lab test a package of 24M sample cells, which showed similar gravimetric energy density performance for LFP graphite batteries similar
and stable behaviour across the cells over several cycles, plus ther-
mal stability, says Spittel. Freyr is gearing up to begin shipping cells to potential customers to test, from its now completed Customer Qualification Plant — a 13,000 square metre demonstration production line — in Mo I Rana, in northern Norway. The cells will be tested within labs, including at third party facilities, equipped to collect data on how the cells perform and compare against data gathered on cells from other suppliers.
While 24M’s semi-state technology is simpler to produce it is not mature, so the plant’s role is a critical step in scaling up the production process, according to Spittel.
One of the next steps for Freyr is to get cells produced on the line out to potential customers so that they can submit them to testing, which would get these potential new accounts to a similar place where Nidec already is.
The majority of output will be to meet demand for stationary storage markets, including front-ofmeter utility-scale installations as well as commercial and industrial applications. “The interest is off the charts,” says Spittel.

Europe’s predicted escalation in installations is contingent on changes to energy storage classifications, policy and increased revenue generating mechanisms.
“They need these cells, yesterday. The urgency cannot be understated so we would expect to start seeing them deployed in storage systems for installations in projects — Jeffrey Spittel.
mainly the higher volumetric energy density,” Pap says.
While the blade-like cell format was initially produced for EV applications due to increased volumetric density of around 20%-30%, longer duration BESS — set to grow in Europe in the coming years — will favour cells that hold more energy. Pap says a trend observed in China is for the main LFP producers to offer blade-like cells to the stationary ESS market, which suggests it could be introduced in Europe as well.
ElevenES is working on improving various parameters of its cells such as energy density and cycle life. Each application has different priorities. EVs need higher gravimetric and volumetric energy density for instance, whereas in the case of stationary ESS systems, longer life-time is important.
The company is working on an ESSspecific cell that will feed into serial production which is planned for early 2025 within the company’s 1GWh factory, which could see the BESS installations featuring ElevenES’ LFP
cells from 2025-2026.
ElevenES is planning to allocate about 50% of its production to the EV sector, and about 25%-30% to the stationary ESS market. The Mega Plant, with 1GWh capacity, will supply ‘C’ and ‘D’ samples for the automotive industry, but for the ESS market it will already provide serial production. Giga Phase I in 2026 and Giga Phase II in 2028 will serve both market segments with large-scale, highly automated, efficient serial production.
ElevenES starts prototype production
Earlier this year ElevenES, in Serbia, produced the first samples of its LFP prismatic cells for sample ‘A’ testing for applications, including electric cars, buses and energy storage systems.
An ‘A’ sample is a functioning prototype of a battery cell that can be tested by potential customers and can be tested for chemistry as single cells. Several of ElevenES’ partners and potential customers will test the A cells in small systems, by building a module out of eight-15 cells and testing them as a module.
The difference compared to ‘C’ and ‘D’ samples is down to the manufacturing process in ElevenES’s Mini Pilot Plant, which includes manual steps, compared with the fully automated process of ElevenES’ future mega and giga plants where serial production will occur. The company will also supply ‘B’ samples, which are adjusted ‘A’ samples.
Its mini pilot plant, which has begun prototype cell production, will be preceded by the installation of 1GWh of annual production capacity by the third quarter of 2024.
Márton Pap, project manager for ESS and programme development at ElevenES, says: “For the LFP industry in Europe — or anywhere outside of China — the biggest challenge is scaling up. On our mini pilot plant line we are already able to identify and address or iron out issues that could otherwise potentially hinder scaling up to automated production in our planned giga plants.”
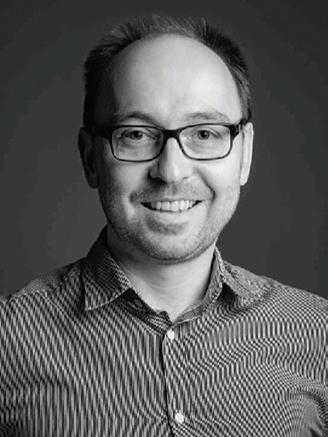
The facilities include a 1GWh factory, as well as planned 8GWh and 40GWh lines.
ElevenES is working towards achieving at least 60% of EU/localized content in its LFP cells within three years’ time. “This is challenging to do. Almost every part of an LFP battery cell in operation in a battery system comes from Asia or China today,” says Pap.
“It requires sourcing local materials and we’re in talks with Chinese companies with regard to their plans to establish in Europe. Ultimately, we’ll produce the cathode active material in-house, which means sourcing supplies of lithium carbonate and iron phosphate. We’re working to a 2026/2027 timetable,” Pap says.
ElevenES was set up in 2019 by its parent company — a manufacturer of aluminium packaging used in the pharmaceuticals and food industries, called AI Pack Group.
The CEO could see that the coating processes used in making the aluminium packaging could be adapted for producing lithium ion battery cells, says Pap.
Future customers for the company’s cells include, besides automotive original equipment manufacturers, producers of turnkey battery systems that also source components down to cell level as well as suppliers of racks and modules to the stationary storage industry.
ElevenES is working towards achieving at least 60% of EU/localized content in its LFP cells within three years’ time. This is challenging to do. Almost every part of an LFP battery cell in operation in a battery system comes from Asia or China today
“Feedback from everyone towards having a localized supply chain for the European and regional ESS market has been positive, for the most because of simpler logistics and shorter supply chains.
“Some see a European lithium ion battery supply chains as a way of avoiding potential trade wars and embargoes. There is, of course, the question about price but we’re happy to see them follow our progress and in some cases we’ll engage in co-development of modules,” Pap says.
— Márton Pap
Fluence: all flavours of lithium accepted
In Europe Fluence has projects and installations in 14 different markets, with the largest being the UK, Ireland and Germany.
The company’s most recent and also largest project in Europe is for transmission system operator TenneT for a combined capacity of 200MW, located at a substation in Audorf Süd in Schleswig-Holstein and Ottenhofen in Bavaria. TenneT’s Grid Booster concept will use Fluence’s Ultrastack, an energy storage system designed for transmission grids, which has been developed and tested in Fluence’s technology centre in Erlangen, Germany. LFP cells will be used.
Marek Kubik, Fluence’s managing director, for western Europe sales, says the company is cell agnostic and when establishing partnerships with cell suppliers Fluence looks for counterparty bankability, scale and track record.
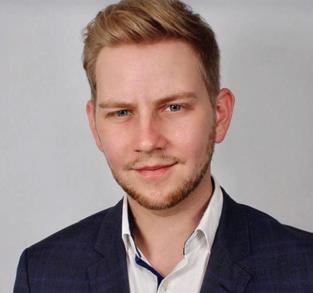
“Cells are just one part of a whole system, which comprises modules, racks, the BMS, connections and other components, all of which have to be integrated to work seamlessly in each deployment. Therefore, the choice of cells can be influenced by
several different factors.”
From 2008, Fluence mainly used LFP cells in its first installations, expanding to NMC in around 20152016. In Europe almost all grid batteries installed by Fluence use LFP cells, while in the US some installations have NMC.
The company works with several cell suppliers, including CATL for LFP and Northvolt for NMC. An additional supplier is undergoing qualification.
In the US where demand for longer duration batteries of up to eight hours is increasing, there can be a preference for NMC cells, according to Kubik.
NMC cells have a higher energy density, compared with LFP and so can be used to build more compact BESS installations with a smaller footprint which can mean less land will need to be acquired or leased for projects. NMC cells can also be sourced outside of China, such as South Korea or Europe, which avoids tariffs in the US market being applied to LFP cells from China. In the balance these factors can lead to a reduced LCoS for certain projects in the US, he says.
Kubik says: “While NMC has a better performance profile, LFP cells are cheaper. However, market, location and project specifics will have a bearing on which technology to go with for each installation.”
Kubik says Fluence will not rule outsourcing actual LFP cells from Europe-based producers, though price is an important factor.
“There is increasing value and demand for more regionalized supply chains — from batteries to other core components. Energy storage doesn’t need subsidies but a political choice to onshore supply chains may need incentives.
“We see incentive schemes, such as the Inflation Reduction Act in the US, being the strongest driver for such localization of supply chains, but ultimately costs are decisive, requiring either higher customer willingness to pay or cost improvements elsewhere.”
KEY FACTORS IN LITHIUM ION CELL TECHNOLOGY
Price. LFP cells tend to be cheaper than NMC due to combination of raw materials and production in China. They were heading towards parity with lead before the pandemic and later invasion of Ukraine by Russia, but have spiked some 30% higher than before on supply chain shortages.
Safety. While thermal runaway can be more aggressive and occur more quickly with NMC cells, LFPs off-gas more, which can lead to explosions. BESS projects are designed in such a way that minimizes the risks concerning either. “The ‘LFP is safer than NMC debate’ is nuanced,” says one commentator. “LFP batteries can go through thermal runaway but it is about 10 times as unlikely as some other lithium combinations.”
Density. NMC cells have higher density over LFP, which can result in a BESS with a smaller footprint. Depending on the project specifics, the higher cost of NMC cells can be offset where space is at a premium, or connections and cabling is reduced due to the more compact design possible with NMC.
Recyclability. There are more recycling facilities in place for NMC and higher potential for recycling as nickel and cobalt are more valuable.
Raw materials availability. As BESS demand continues to expand this could become an increasingly important factor since metals such as iron are more abundant than critical metals found in NMC.
Supply chain localization. This is an emerging factor but one which is becoming increasingly important. If the materials used to make LFP cells can be sourced nearer to where cell manufacturing takes place, such as the same country, continent or region, dependency on other countries, not just for cells but actual raw materials is minimized.
Fluence is cell agnostic and when establishing partnerships with cell suppliers Fluence looks for counterparty bankability, scale and track record
— Marel Kubik
Sunlight
What dilemma in moving between lithium and lead battery chemistries?
Now in its fourth decade of operations, Sunlight is one of the titans of the lead batteries business and a major international figure in the industry.
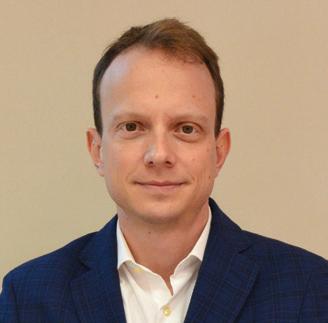
The Greece-based group has been a dynamic European battery industry player that has established itself as an international force to be reckoned with — driven in no small part by hitting the acquisitions trail with a vengeance just a few years ago.
There appears to be no looking back and Sunlight is keen to show it is a first among equals of battery manufacturers. “Sunlight has been implementing a robust expansion plan with significant M&As around the world,” Deligiannakis says.
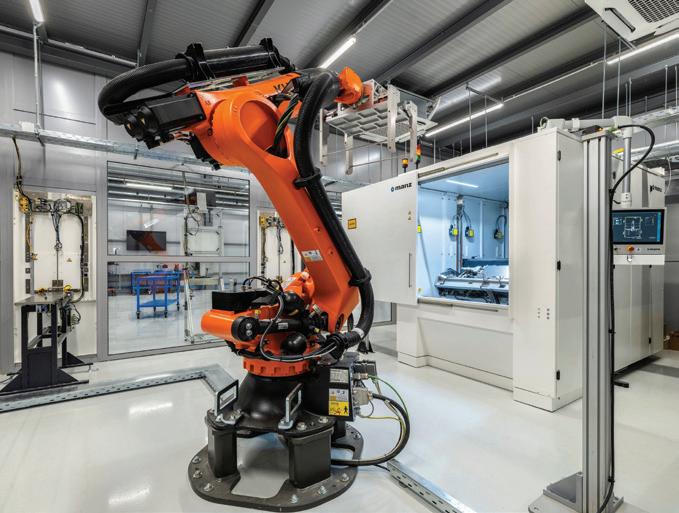
“Our objective and driving force for expansion is to increase or production capacity by adding manufacturing facilities to our existing units.”
The group also had in mind to expand its geographical reach in terms of sales and after-sales services.
Ongoing is the ambition to further deepen the vertical integration of the company by incorporating as much of the production processes in-house as possible.
Deligiannakis acknowledges the group’s roots in the lead battery business — which he says is the oldest and most widely used rechargeable battery technology that has supported electrification for more than a century to date and has helped the global economy grow.
Despite this illustrious past, he says Sunlight sees lead as approaching the limits of its technical capabilities while new technologies have — and will continue to emerge — as research into more cost-effective, sustainable and eco-friendly energy storage technologies continues apace.
“However, there are definitely aspects of lead-acid that still render this battery technology commercially vi-
able in terms of the cost and performance related to their intended use.”
Understanding the characteristics of competing battery chemistries and their suitability for different applications is key their future deployment, Deligiannakis says.
“This means that lead still has a future, albeit not necessarily across all variations and applications.
“It falls on all of us, the industry experts and leaders, to develop the best battery types for each application, considering all pertinent factors, as this will continue adding value to our operations and addressing the expectations and needs of customers and markets in the future.”
For Sunlight, the company has opted to forge ahead in lead with a focus on manufacturing products for a single application: flooded motive power.
Deligiannakis says the rationale is
Group’s Paris Deligiannakis spoke to John Shepherd about the company’s investment in lead, as well as its commitment to being in the vanguard of advances in lithium.
Lead still has a future, albeit not necessarily across all variations and applications
— Paris DeligiannakisSunlight lithium assembly facility in Xanthi
such lead acid products still have a role to play in less-intensive shift applications with limited, if any, charging capabilities.
For example, lead batteries are more cost-effective for low/medium density applications, which still constitute a viable market.
Sunlight has specialized in industrial mobility for decades, he says. “We know how to produce them well, at scale and on time to meet customer needs.”
It is for this reason that Sunlight’s board has given the green light for ongoing investment in lead production and why, Deligiannakis says, the group remains committed to producing high quality lead batteries for specific applications.
“Lead-wise, we see our growth coming from existing products and investments are geared towards expanding capacity and optimizing production via automation, with the focus being solely on flooded motive power.”
Sunlight is also investing about €10 million ($11 million) to more than double the annual capacity of its Komotini lead recycling plant in northeastern Greece by 2025 from the current 45,000 tonnes annually to 100,000 tonnes of soft lead and lead alloys.
Meanwhile, the group has invested in complementary lead R&D facilities to expand production efficiency and quality.
Innovation in internet of things (IoT) solutions relating to lead is another facet of Sunlight’s armoury for capturing more commercial markets.
IoT platforms developed by the group include ‘Sunlight GLocal’ and ‘Sunlight KnoWi’.
KnoWi is a battery monitoring system that can be used to monitor the status of motive batteries and the forklift trucks they power, in real time, from anywhere using WiFi and GSM connectivity.
The platform instantly improves the efficiency of forklift fleets, offering
SUNLIGHT READIES LFP CELL PILOT FACILITY
Sunlight Group has been transforming itself from a producer of lead acid batteries, for industrial mobility and other markets, to an energy storage company embracing a technology-agnostic approach.
Today the company designs, develops and produces battery systems based on lithium ion as well as lead acid chemistries that use its controls, BMS and software to optimize batteries in mobility, industrial and storage markets.
This year Sunlight Group will complete its €130m LFP cell pilot facility, co-funded by the EU as an IPCEI, which will be fully operational by the end of 2023.
The pilot line is the precursor to Sunlight Group’s plans to eventually establish an LFP cell factory, in northern Greece, within the next few years and to be serial producing cells in 2027/2028.
In parallel it will produce batteries for the ESS market, using sourced LFP cells, at its lines in Europe and in North Carolina in the US, where a new factory is being established that will be Sunlight Group’s second plant in America.
One of the key markets the company is targeting is grid storage and Sunlight Group is in talks to partner companies that integrate batteries within BESS systems and those that provide turnkey battery installations. It is progressing towards making announcements in the next few months about these partnerships.
According to Deligiannakis, in the meantime the company is also investing in establishing its own team focused exclusively on the grid BESS market, which will span R&D, engineering as well as
smart and accurate performance data, presented in a comprehensive, userfriendly way, Deligiannakis says.
GLocal is the firm’s proprietary smart cloud-based platform for its lithium ion batteries.
Despite its historic links to lead, he says the Sunlight of today is technology agnostic. “Our talented 200-strong R&D team (part of the group’s combined multi-national 3,300 workforce) works in five dedicated R&D centers across our operations exploring different chemistries and technologies.”
commercial activities.
One of the company’s main advantages is its investment in its R&D team as well as decades of manufacturing experience. This means it can work closely with a partner, such as a BESS integrator or supplier, to hone its LFP batteries for that partner’s specific requirements, which would also feed into the company’s own proprietary LFP cell R&D activity.
Deligiannakis says: “We are technology agnostic when it comes to batteries. For example, our industrial battery products range includes both lithium ion and lead acid — that gives our clients flexibility when it comes to which solution best suits their requirements.
“In the EV market NMC and LFP each have their different advantages. However, when it comes to the ESS market, particularly the grid BESS market, it is immediately clear that LFP is the best technology. Safety and increased cycle life are the big factors.
“With LFP, you aren’t dependent on sourcing critical minerals either, which means the batteries can be cheaper to produce and are more sustainable.”
He and his team focus on sales to OEMs and dealers in Europe as well as on the commercial performance of all EU-based commercial subsidiaries, in addition to product management for all of the group’s traction and small ESS products. He has more than 15 years of experience in strategy and commercial roles, including with firms such as McKinsey & Company and Vodafone Greece.
The main lithium battery technology Sunlight is working with is lithium iron phosphate. Deligiannakis says LFP’s “excellent characteristics” include no use of contentious raw materials such as nickel or cobalt used in NMC-type batteries.
He says LFP is expected to gradually become the dominant li ion battery chemistry, representing 40% of the global battery market by 2030.
The company is assembling lithium ion energy storage systems at its Xanthi facility in Greece and is building a
Investments are geared towards expanding capacity and optimizing production via automation, with the focus solely on flooded motive power
second such plant in the US, exclusively dedicated to lithium, in Mebane, North Carolina.
Separately, three automated production lines are being installed in Xanthi (one already commissioned) and one in Mebane.
“We’re investing heavily in these lithium assembly production lines, installing highly automatic and topperforming production lines with a 5GWh annual capacity.
Another two are operating in the newly-acquired facilities of Germanybased Triathlon.
“We’re also planning to invest €100 million in a new lithium ESS assembly plant, operative by mid-2025, with a 15GWh annual capacity of high-and medium-voltage systems for gridscale, commercial and industry, and home storage applications.”
In a related move, Sunlight is lead-
ing ‘ReLife’ (recycling LFP), an EU-supported three-year project, in partnership with a consortium of industrial and academic partners including Germany’s Technische Universität Bergakademie Freiberg and the Helmholtz-Institut Freiberg für Ressourcentechnologie.
The project’s initial aim is to establish a pilot plant with a recycling capacity of 500 tonnes of batteries annually at Xanthi, which Sunlight says will be one of a handful worldwide recycling all sizes of LFP batteries.
Following the successful operation of the pilot recycling plant, additional capital investments can ramp-up production and establish a full-scale facility with an annual recycling capacity of thousands of tonnes, Deligiannakis said.
As for the manufacture of lithium battery cells, Sunlight is installing a production-scale pilot line for LFP lithium cells at Xanthi — a €130 million-plus investment (€50 million funded by the EU as a designated ‘important project of common European interest’ and €80 million from Sunlight).
The pilot line can also be adjusted to work with sodium-ion batteries, which Deligiannakis said is regarded as a promising chemistry for energy storage that Sunlight’s own R&D ex-
perts are looking into.
Expected to be commissioned in the first quarter of 2024, the pilot line will develop “the optimal LFP cell that will then be produced on an industrial scale” in Europe.
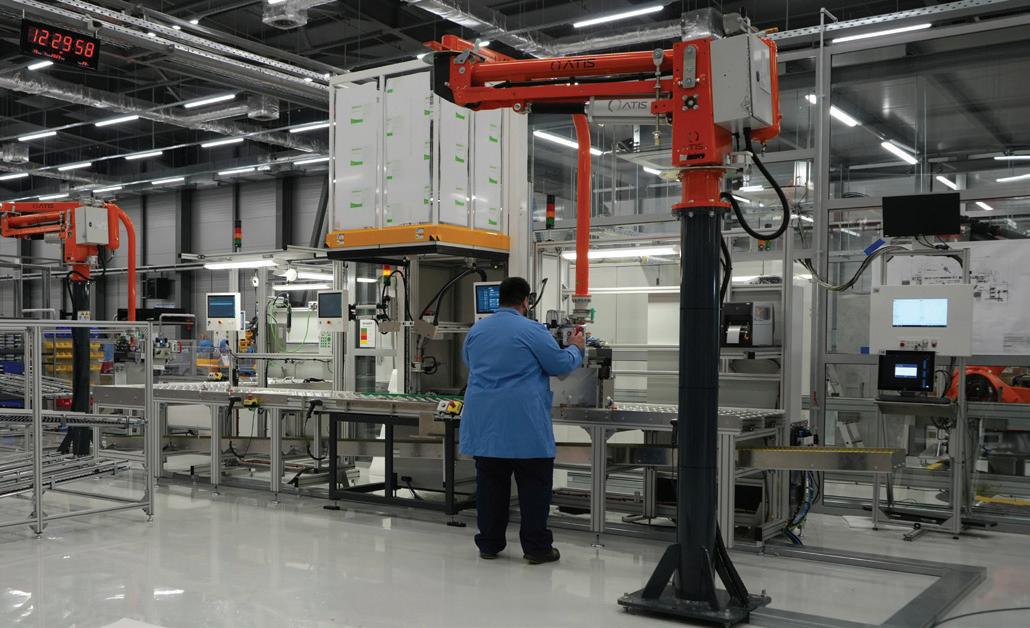
The pilot will also serve as a “preparatory investment” in support of European ambitions for lithium ion battery cell gigafactories.
DEALS APLENTY ON ROAD TO EXPANSION
Since December 2021, Sunlight has completed seven M&As.
In June 2023, the group announced its most recent investment agreement with longstanding Portuguese commercial partner Logbatind, to further establish itself in the Iberian market.
The most significant of these was its deal, for an undisclosed sum, with Germany-based Triathlon Holding.
This February, Sunlight said it had acquired a controlling 51% stake in Triathlon. It announced the acquisition of all remaining shares in Triathlon in July.
With LFP, you aren’t dependent on sourcing critical minerals either, which means the batteries can be cheaper to produce and are more sustainable
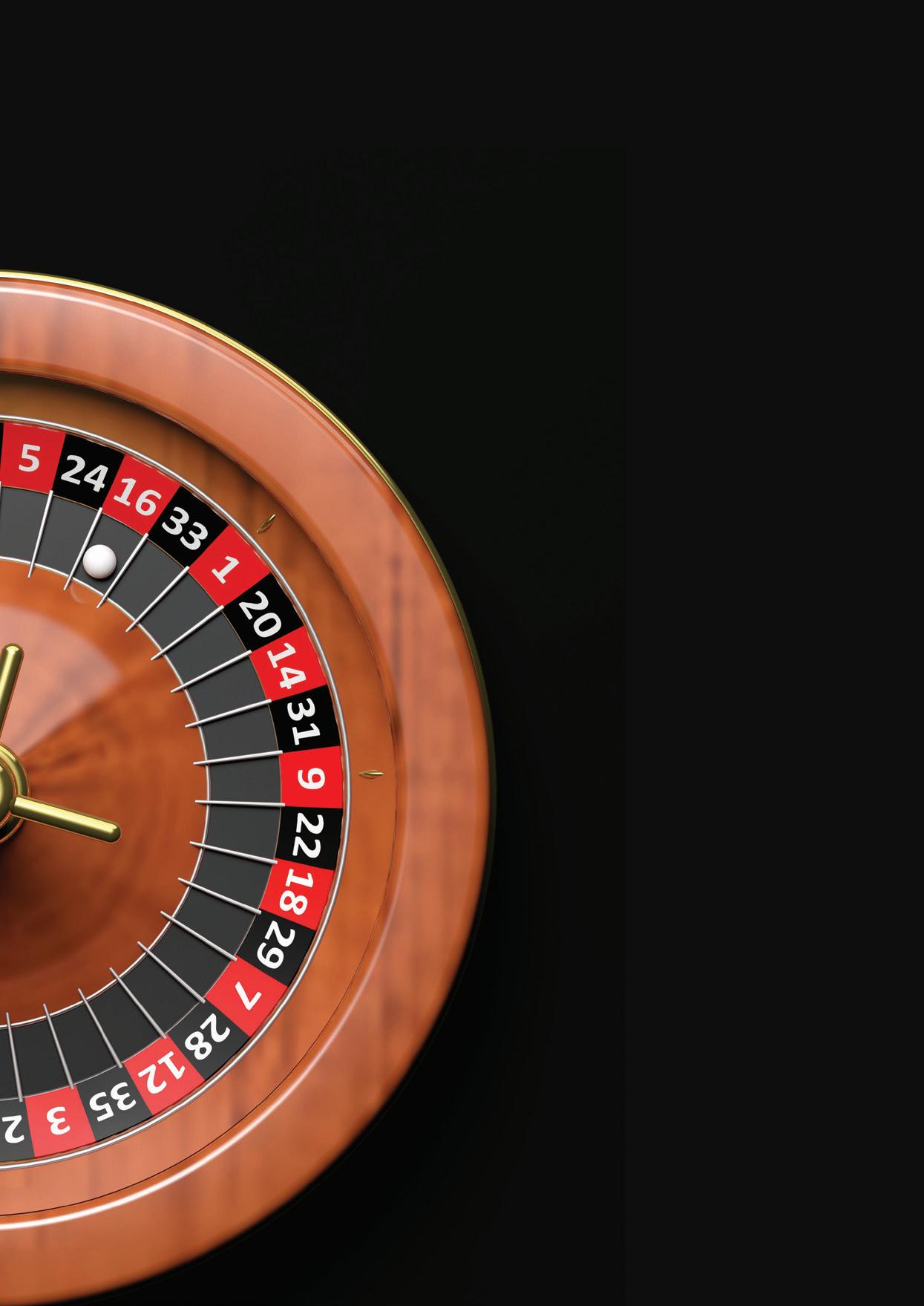
Amara Raja invests to grow beyond India
Nearly four decades on from when Ramachandra Galla founded Amara Raja, he ushered in a new era for the group in June 2021 with his announcement that he was stepping down.
In his 36 years at the helm, Ramachandra saw the company — named after his parents-in-law Amaravati and Rajagopala Naidu — grow from humble beginnings to become an Indian multinational conglomerate.
His son, Jayadev Galla, previously vice-chairman of the board, took over the group following the company’s annual general meeting in 2021, with a commitment to investing in a portfolio of businesses to maintain its technological and business leadership in the energy and mobility space.
Recent initiatives have included the launch of a subsidiary to spearhead the addition of lithium ion technology to Amara Raja’s long-standing lead battery manufacturing operations.
In the summer of 2022, Galla also revealed the company was looking into the possibility of expansion through greenfield investments or acquisitions for its lead battery business in the Indian-Ocean rim.
Now the head of corporate communications for the Amara Raja Group, Brijesh Menon, says the batteries giant has aspirations to grow even beyond Asia.
He told Energy Storage Journal: “We are looking at expanding our global presence, not just in the IndianOcean rim where we already have a significant presence but even in the North American and Europe regions.
“We are searching for the right fit opportunity for an acquisition.”
Menon said the company ships more than 50 million lead acid batteries annually with numbers “growing robustly every year” on the back of sales to help power the automotive, telecoms, datacentres and green ener-
gy storage markets, which he said are all high growth industries.
“Amara Raja Batteries has been one of the fastest growing battery manufacturers in the world and we hope to continue this streak.
“Our ambition is to more than double our turnover in the next five years. New products, new markets are all on the cards.”
The company posted net revenue equivalent to around $1.1 billion in the 2021-22 financial year.
Menon said the firm’s aspirations are aligned to India’s national mission to become a regional economic powerhouse on the fast track to growth, with a significant contribution from the fast-developing batteries sector.
Active encouragement of green energy initiatives by the Indian government, which has set a goal of reaching net zero by 2070, has provided the impetus to energy storage equipment manufacturers, Menon said.
The ‘China plus one’ strategy (a business strategy to avoid investing only in China and instead diversify into other countries) is also gaining momentum, he said.
“And if India can overcome its supply chain and recycling challenges then definitely it can dominate a larger market.”
Part of that move towards dominance comes with Amara Raja’s diversification into lithium ion.
The company announced plans to start developing lithium ion cells in February 2021, joining main rival Exide Industries in branching out into the lithium sector.
In May 2022, Jayadev Galla pledged to “fast track” the group’s development of a customer qualification plant for lithium cells while also building on its lead battery foundations.
And in December 2022, Amara Raja said it had agreed to a build a 16GWh lithium battery cells factory together
with research facilities in the southern Indian state of Telangana.
The new plant, situated in what the company has dubbed its ‘giga-corridor’ initiative, will include a 5GWh battery pack assembly unit, under the terms of a memorandum of understanding signed with the state government.
The first phase of that initiative should be in place in the next twoto-three years, Menon said. This will include a 2GWh battery cell manufacturing facility, a customer qualification plant with a 60MWh annual production capacity and an advanced energy innovation center.
Menon said R&D continues apace and Amara Raja Li ion battery packs in various vehicles have already clocked up more than 200 million kilometres on the road.
“Amara Raja also has strategic investments in companies that are doing some cutting-edge work in Li ion technology, so any breakthroughs there will of course benefit us.”
However, he said the company is not actively pursuing further such partnerships as of now.
Meanwhile, to boost control over raw materials supply at a time when Amara Raja is expanding its operations, Menon said the process of fully integrating the plastic battery components business of its supplier division Mangal Industries, with its battery manufacturing operations, is well underway.
The move was first announced in September 2022.
Amara Raja, which already receives Mangal’s entire output of plastic components for batteries, said the deal will also simplify operations and improve efficiencies.
Menon said Mangal provides plastic containers, covers, small parts, handles and jars that are used in batteries with a capacity of 37,000 tonnes per annum and more than 145 injection moulding machines.
He said the deal was in keeping with the battery firm’s mission to “consolidate and unlock synergies as we continue to pursue value accretive growth opportunities that will lead Amara Raja Batteries to the leadership position in the energy and mobility space.
Amara Raja’s batteries business, which was recently launched into the lithium ion sector, is committed to maintaining its lead automotive base and now new products and fresh markets are all on the cards, says communications chief Brijesh Menon
EUROBAT General Assembly
Madrid, June 6-7, 2023
Europe at the crossroads in mapping out energy future
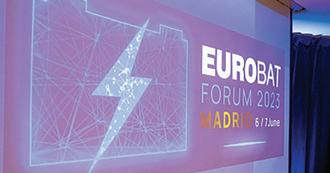
Delegates to this year’s event heard from various speakers how Europe’s potential position as a major player in energy storage was at a critical juncture.
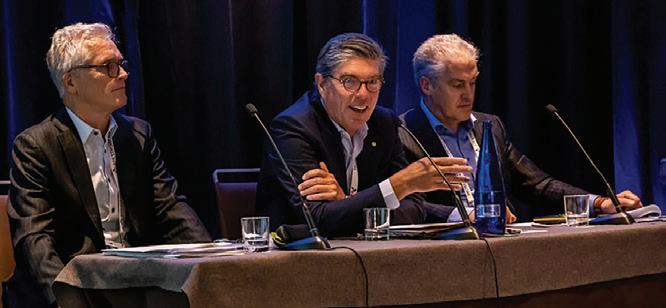
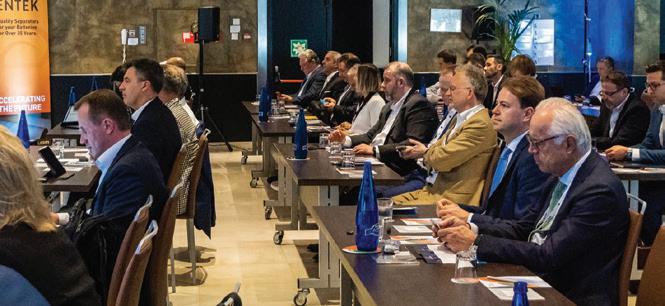
Mike Blakeney, head of government and public affairs at the Cobalt Institute, said the offer of $369 billion of tax credits from the US under this year’s Inflation Reduction Act was not being matched by anything comparable from the European Union.
“At the moment what’s on offer from us stands at about $3 billion,” he said. He warned that the next
18 months would be critical in persuading investors to come into Europe and that it was time to “unlock private capital… we need to incentivize investors through initiatives looking at insurance terms, export credits and guarantees, contracts for difference and more,” he said.
The theme was taken up by Luis Marquina, head of AEPIBAL, the Spanish energy storage association, who reckoned that European political, business and technical involvement needed to step up a gear.
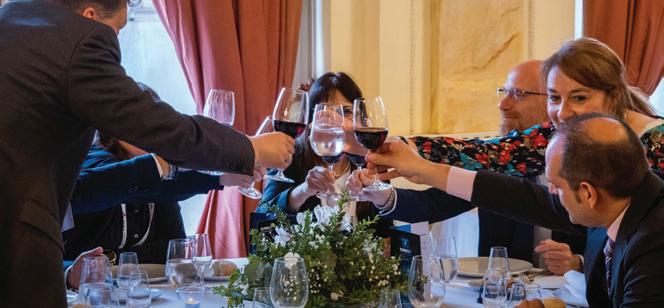
“Now is the time for leadership in our industry,” he said. “And if it doesn’t come now, it’ll be too late. China already is at the forefront of innovation, we cannot be left behind.”
William Adams, head of battery and base metals research at Fastmarkets, said the question whether Europe had enough battery raw materials was complicated by the fact that Europe, China and the US will all rely on resources from the rest of the world. Competition between nations, businesses and industry sectors for supply will be a limiting factor in the near future.
He saw, however, the overall picture for European supply as improving over time. “In the future Europe will need to rely on imported concentrate for lithium,” he said.
“But it need not rely on imported processed material. Europe will see its mine supply grow and its processing capacity can grow at a faster pace, but it will rely on imports of raw materials or intermediates.
“In time, it can substitute mine supply with recycled material/battery scrap as the volume of end of life batteries picks up leading to a more circular economy.”
In his speech to delegates, EUROBAT president and CEO of Hoppecke Batterien, Marc Zoellner, emphasised the significance of Spain and the battery industry.
He said the battery sector played a crucial role in the country’s industrial landscape, contributing significantly to its economy and the EU’s ‘Green Deal’ objectives.
“Spain aims to become a leading player in battery manufacturing, driving the country’s competitiveness in the global clean energy market and positioning itself at the forefront of the energy transition.”
Meanwhile, there was a changing of the guard for EUROBAT as general manager Alfons Westgeest announced he was stepping down and Gert Meylemans, previously director of communications, would be taking over.
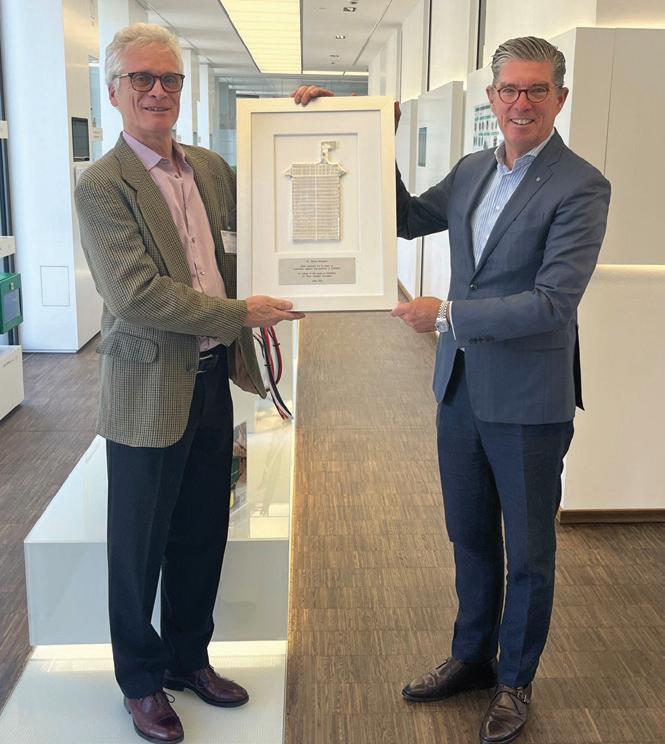
Westgeest had in fact tried to retire four years ago but came back, much to the industry’s delight. He continued to be a central figure in the Brussels-based group since his involvement in 2002 and is arguably the key creator of the present trade organization.
He is a well-known and well-liked figure in all sections of the European energy storage industry and said he had enjoyed his time with EUROBAT.
“It’s not just been fun to build up and strengthen the organization but we have achieved real success in helping influence the direction of battery regulation across the EU.”
Marc Zoellner, president of EUROBAT and CEO of Hoppecke Batteries, in a touching speech at the conference dinner, paid tribute to Westgeest’s relentless commitment to building up EUROBAT and its members.
“I will truly miss him and thank him for the wonderful work he has done,” he said.
Meylemans, who joined EUROBAT in August 2018, said he had a very tough act to follow but “hoped to continue to build on the great work Alfons has done”.
EUROBAT is a non-profit association under Belgian law and is staffed by association management company Kellen. Westgeest became Kellen Europe’s board member for global development in 2022.
Before EUROBAT, Westgeest was the founder and managing partner of Ernst & Young’s association management practice in 1988 in Brussels. He joined EY in 1981 and left the firm in 2004.
The next meetings will be held on June 4-5, 2024 in Brussels.
NEW BOARD MEMBERS
Lampros Bisalas, CEO of Sunlight Group Energy Storage Systems, and Fujio Owa, CEO of Fiamm Energy Technology, were appointed new members of the EUROBAT Board at the general assembly as Alfons Westgeest stepped down as general manager and Gert Meylemans took over.
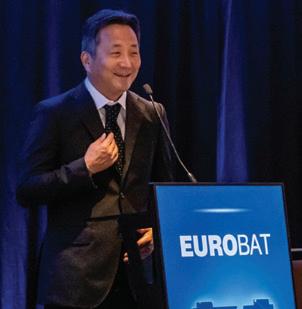
EUROBAT said in a statement: “We look forward to working with both gentlemen and to leverage their valuable experience to drive innovation, contribute technical expertise to the EU policy-making process and help craft a positive and consistent regulatory framework for the battery industry in the EU and beyond.”
The existing board members are: Andreas Bawart (Banner), CharlesLouis Ackermann (Accumalux), Dave Shaffer (EnerSys), Christian Rosenkranz (Clarios), Filippo Girardi (Midac), Frank Cecchi (Saft), Graeme Fraser-Bell (Entek), Marc Zoellner (Hoppecke) and Stefan Stübing (Exide).
IFBF
Prague, Czech Republic, June 27-29, 2023
Buoyant industry all set to let the good times flow
Brimming with optimism would be how one could best describe the flow battery industry as the curtain went up for its annual gathering last year in Brussels. This year, ‘raring to go and uncompromising’ neatly sums up the mood of their get-together in Prague.
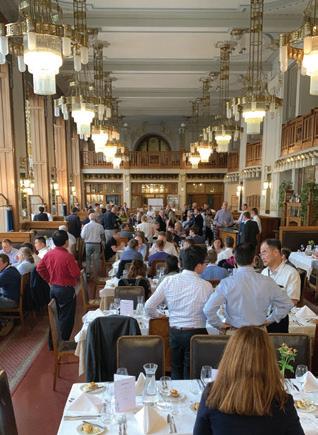
There was more than a spring in every delegate’s step, fresh from a flurry of flow battery news including the announcement by iron flow battery firm ESS that it would be building a 50MW/500MWh system in Germany.
Australia’s Redflow had not long secured a 20MW microgrid project for Northern California, while Invinity Energy Systems said just weeks earlier it was developing a 30MWh VRFB battery in the UK.
Another piece of good news was that flow battery technology will also now be included in the EU Battery Passport scheme.
And just six months before the conference, CellCube announced a deal to build a manufacturing and assembly line for its vanadium redox flow batteries in Australia.
All this news and more was regaled to delegates and IFBF secretary and secretary-general of Flow Batteries Europe (FBE), Anthony Price, who was rightly enthusiastic as he opened proceedings.
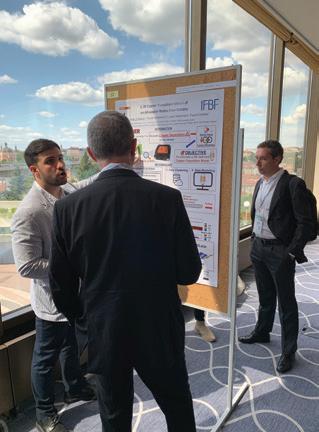
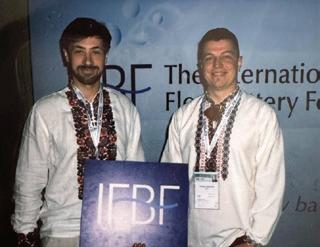

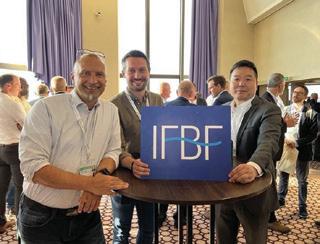
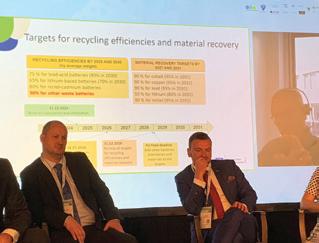
“Look at the growth in the sector — we have heard project reports from Asia, Europe, the Middle East and America that show how better batteries are meeting market needs,” he said.
According to a paper presented by FBE, some 8GW of flow batteries are forecast to be put into operation around the world by the end of the decade.
However, talking to Energy Storage Journal at networking and other events behind the scenes, many thought several other commercial initiatives will push that figure further.
Indeed, this year’s event received more than 40 papers, complementing the broad range of commercial, regulatory, policy and technical issues discussed during the conference.
Another key measure of the IFBF’s growing influence was the exhibition — this year more than a dozen stands representing battery makers,
materials and service providers to name but a few, all set out in a designated conference room of their own.
Poster presentations were there aplenty too, highlighting R&D that is going on behind the scenes.
But a related exciting innovation was the ‘Poster Speed Pitch’, introducing the industry’s next generation of potential flow battery innovators, who each had just 60 seconds to outline their R&D work on stage during the main conference and lobby delegates to visit their poster stand.
How flow batteries could be the future of powering the rebuilding of more challenging environments was underscored by the attendance of two representatives from Ukrainian company R.Flo.
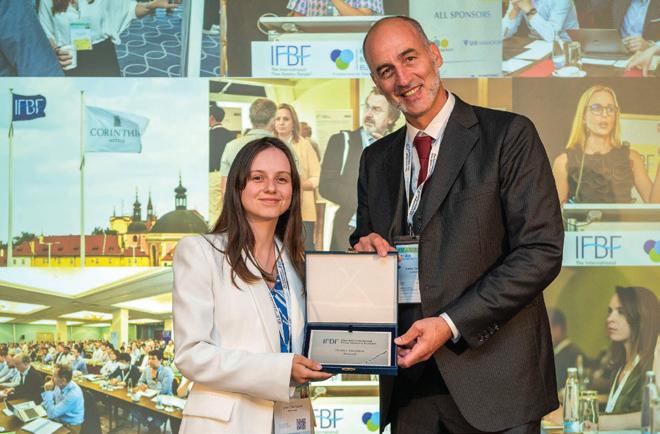
Head of technology Yaroslav Kolosovskyi and CEO Andrii Bondar were made to feel especially welcome by delegates. The pair explained that their attendance was only possible thanks to being provided with safe passage out of their homeland by the Ukrainian Armed Forces.
Also looking to the future was the flow battery industry itself and some changes are already underway.
Patrick Clerens, managing director of Clerens NV, announced that his organization would take over the “heavy lifting” needed behind the scenes in running future IFBF events — but with industry champion Price remaining very much a key player in proceedings, as we report in our news pages elsewhere in this issue.
Price said the partnership would help to expand the breadth of coverage, networking and showcasing opportunities for the flow batteries sector.
IFBF now heads toward its 15th year and has a date in Scotland, thanks to an invitation by Invinity Energy Systems CEO Larry Zulch for IFBF to convene there in 2024 — and visit its flow battery facility in the country.
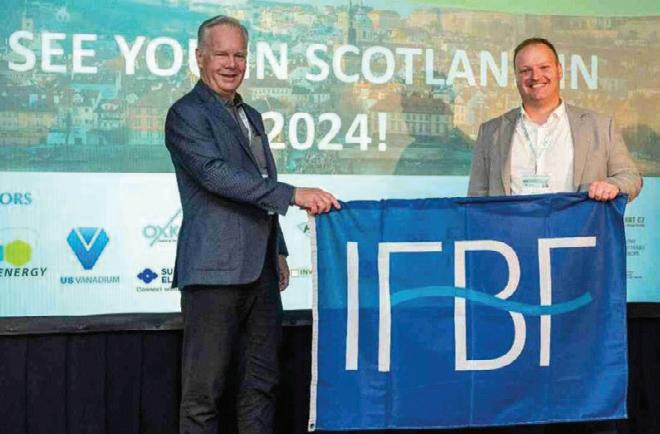
The company builds its cell stacks in Scotland, Vancouver and China.
Zulch had earlier unveiled Invinity’s next-generation VFB project, ‘Mistral’, suitable for large scale (+500MWh) wind, utility and solar installation projects based on the firm’s VS3 technology.
He also provided food for thought when he suggested it might be time to
drop ‘redox’ when talking about flow batteries in favour of only ‘vanadium flow batteries’, as the sector “enters the mainstream”.
However, a quick show of hands among the audience indicated mixed views.
The logistics of the Scotland trip will be announced in due course, but the conference was left in no doubt about Anthony Price’s preferred means of travel...
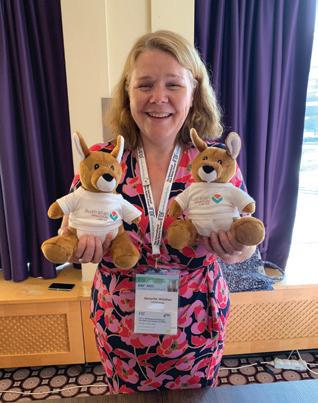
He told delegates that advances in the industry are such, they would be able to take a cruise in the not-toodistant future on a vessel powered by flow batteries.
Watch this space!
Advanced Tech and Innovation shows, NEC, Birmingham, UK June 29-30, 2023
Four events in one. This was held in two giant halls at the UK’s National Exhibition Centre. These were The Advanced Materials Show, Ceramics UK, Battery Cells & Systems Expo and Vehicle Electrification Expo.
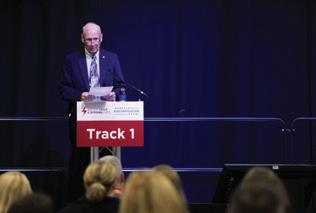
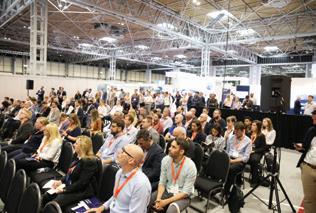
Innovative mix and match technology exhibition highlights the evolving cross-fertilization of related ideas
Not just a good event, but a truly interesting one. That was the concluding comment of one attendee at the launch of this the second year of these four co-located shows. The venue was the same as last year but the location within the National Exhibition Centre on the outskirt of Birmingham in England, was a prime spot: a few hundred metres from the main entrance into the largest conference centre in the UK.
The NEC is huge and this exhibition took full advantage of the space
available using two of the 20 interconnecting halls on this 182,000m³ venue.
The layout within the two halls is important. Each of the four conferences fitted (roughly) into one quarter of the overall space enabling visitors to stroll, for example, from one area, perhaps the vehicle electrification area seamlessly into a related subject area, such as that for battery cells and then into advanced materials.
The charm of the idea is this ability to wander. Nowadays one can’t
speak of just a single technical area without looking at the related technologies. In this it was cleverly put together. Too much of modern electrochemical advances are isolated from their context in terms of materials and engineering.
In each corner there was a stage with around 100 seats facing the speakers in which that subject theme of the conference was discussed and there was a constant succession of well known figures and lively panel discussions throughout both days of the exhibition.
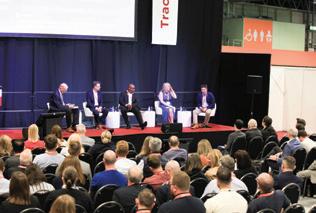

“My favourite part of the show has been having all the different elements in the same place: advanced batteries, EVs, ceramics and the like,” said one delegate.
“It’s been really good to have those cross-fertilization discussions and linking up with people who we may not have had the opportunity to link up with if it had been a single industry-focused event.”
One of the underlying themes discussed was how the UK would fare in attracting gigafactory battery manufacturing given the huge tax subsidies offered by the US in last year’s Inflation Reduction Act.
Bob Galyen, the former CTO of CATL and also acknowledged as one of a small coterie of international lithium battery experts the IRA was going to provide huge benefits for US automanufacturers and battery makers.
“If you look at research from Benchmark Mineral Intelligence,” he said, “you’ll see that Tesla and its battery partner could receive $41 billion in government tax credits by the end of 2032 — that’s far more than its key Detroit rivals.
The rewards from the production credits that are part of the IRA are based on volumes of business so the more batteries and EVs a company makes in the US (or in countries included in the Treasury regulations), the more money it gets via tax credits. Tesla, which had started battery production in 2013 at its first gigafactory has put Tesla and Panasonic far ahead of their competition.
“It’s first mover advantage,” one UK attendee told Energy Storage Journal. “So those ahead of the game will stay ahead of it until 2030 when the credits taper off.”
Another attendee predicted (rightly it transpired) that Tesla would use the investment credits to cut the price of its cars. Already Tesla sells more of its EVs than the rest of the competitors in the sector combined.
Some of the technologies discussed by speakers at the show had the potential to be truly revolutionary.
Galyen’s talk also provided a fascinating insight as to the areas in lithium battery technologies which he regarded as being both cutting edge and soon to be mainstream. He was particularly enthusiastic about Titan AES which uses ultrasound technology for quality inspection and homogenous product manufacturing.
The next step forward in lithium battery recycling will come from Chromatopgraphic separation which could well be a leap ahead from solvent extraction.
The 2023 exhibition and four-track conference featured Andy Palmer, Inobat; Nusrat Ghani MP, UK government; Emanuel Eweka, AMTE Power; Neil Glover, Rolls Royce; Bhavika Ramrakhyani, Costain; Bob Galyen and many others.
Organizations featuring at the event included Thermo, Fisher Scientific, Goodfellow, Rigaku Europe, ABB Limited, Elysia – Battery Intelligence by WAE, Atlas Copco and many more.
Steve Bryan, managing director at the organizers, Event Partners, said: “We are absolutely delighted with the support we have seen for this event from the advanced technology and innovation industries. The technical battery, EV, advanced materials and ceramics industries in the UK are undergoing an unprecedented level of growth currently driven by both government and private investment.
“We were pleased to see major global organizations, start-ups and thought leaders together for two days of networking, collaboration and insight to help shape the next few years of these major industries.”
Exhibitor reaction to the show was positive: “the footfall has been good, there’s been a lot of interesting discussions and the speaker agenda has been excellent,” said one exhibitor.
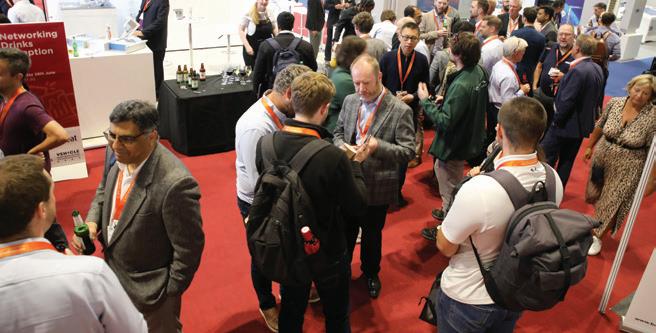
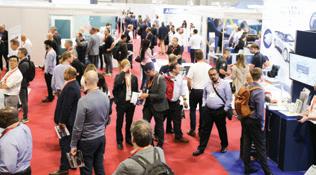
The statistics were good and atten-
dance was up from 2022’s 3,100 to this year’s 3,800. In all there were some 260 exhibitors and 89 speakers.
The next Battery, Cells and Systems Expo and Vehicle Electrification Expo is on May 15-16, 2024 and will be co-located with The Advanced Materials Show and The Advanced Ceramics Show at the NEC, Birmingham UK.
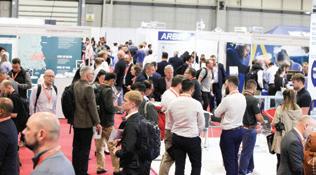
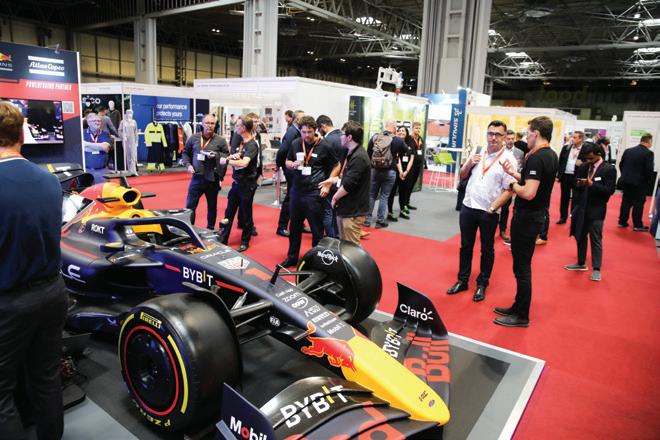
Intersolar Mexico
Mexico City, Mexico.
September 5 – 7
Intersolar Mexico serves as the industry’s go-to source for invaluable technology trends and premier B2B contacts in the promising Mexican solar market. It sits at the cross-section of photovoltaics, solar heating & cooling technologies, and energy storage.
Together, the two events will be the largest gathering of professionals in Mexico for international manufacturers and distributors looking to meet regional buyers in the fields of solar, renewable energy and cleantech.
Contact Solar Promotion International
E: info@solarpromotion.com https://www.intersolar.mx/organizers
International Congress for Battery Recycling — ICBR
September 6 – 8
Valencia Spain
ICBR 2023 is the international platform for reviewing the challenges faced by the Battery Recycling Industry on a global basis.
For 28 consecutive years, ICBR has brought together the international community of experts and decision makers of the entire Battery Recycling value chain, including battery recyclers and manufacturers, collection organizations, OEM’s, policymakers, materials and services providers and many more.
Contact ICM AG
E: info@icm.ch www.events.icm.ch
RE+
September 11 – 14
Anaheim, CA. USA
RE+ brings the modern energy industry together to foster a cleaner future for all. The largest and most comprehensive event in North America for the clean energy industry, RE+ is comprised of: Solar Power International (our flagship event) and Energy Storage International and brings together an extensive alliance of renewable energy leaders for multiple days of programming and networking opportunities.
Contact Solar Power Events
E: registration@re-plus.com
https://www.re-plus.com
The Battery Show
North America
September 12 – 14
Novi, MI. USA
The Battery Show connects you with more than 8,000 engineers and executives, and more than 600 leading suppliers across the advanced battery supply chain.
A powerful end-to-end showcase, this leading global industry event covers today’s emerging advanced battery technology for the automotive, portable electronics, medical technology, military and telecommunications, and utility and renewable energy support sectors.
Explore the full spectrum of cutting-edge solutions you need to make faster, smarter, and more cost-effective products at the most comprehensive industry event in North America.
Contact Informa Markets
E: registration.ime@informa.com www.thebatteryshow.com
World Energy Storage Day
September 22 • Online
With Energy Storage rising to the forefront of industry developments, World Energy Storage Day is commemorated on 22nd September every year by various global industry stakeholders, policy makers, think tanks and associations to acknowledge its importance across the globe.
A rising focus on the effective integration of renewable energy, the importance of electric vehicle and reliable, resilient energy supply, energy storage is becoming an increasingly important tool in the electricity ecosystem.
Contact India Energy Storage Association
E: event@indiaesa.info
www.energystorageday.org
Battery Tech Expo Sweden
September 27 – 28
Gothenburg, Sweden
The Battery Tech Expo Nordic 2023 will bring together the latest technologies and services involved in the battery technology covering battery storage, battery management systems, fuel cell technology, lithium-ion batteries to name a few.
The event will welcome senior deci-
sion makers and users from across the power industry who share a professional interest in the technology and science of battery technology.
Held in Gothenburg, the hub of battery technology industry of Sweden, the event will provide a unique opportunity to showcase the latest technological products and services from within the industry.
Contact 10fourmedia
E: david.reeks@104-media.com
www.batterytechexpo.se
Energy Storage Canada
October 3 – 4
Toronto, Canada
Energy Storage Canada (ESC) is the voice of leadership for energy storage and the only industry association in Canada that focuses on advancing opportunities and building the market for energy storage.
ESC has made energy storage a key focus for policy makers. We educate stakeholders and drive awareness about the value that energy storage delivers. We work to create new competitive markets and ensure regulatory fairness. Our mission is to advance the energy storage industry in Canada through policy advocacy, collaboration, education, and research.
Contact Energy Storage Canada
E: information@energystoragecanada.org
www.energystoragecanada.org
The Battery Show India
October 4 – 6
Greater Noida, India
The Battery Show portfolio brings together engineers, business leaders, top industry companies, and innovative thinkers to discover ground-breaking products and create powerful solutions from across the globe.
From raw materials to components, find what you need to power your next project at the Battery Show India. The exhibition brings together more than 200+ brands showcasing the latest solutions across the transportation, stationary, portable and industrial sectors.
Contact Informa Markets
www.thebatteryshowindia.com
Energy Storage Global Conference — ESGC
October 10 – 12
Brussels, Belgium
ESGC 2023 will explore the extent to which energy storage can help avoid dependency on fossil fuels and will cover three main topics that represent the whole value chain of energy storage, offering great opportunities to industry, researchers, and policymakers to exchange views and debate key issues faced by the energy storage sector.
Contact European Association for Storage of Energy — EASE
E: info@ease-storage.eu www.ease-storage.eu/easeevents/energystorage-global-conference/
Batteries Event
October 10 – 13
Lyon, France
The Batteries Event will cover aspects of the circular economy chain, starting from the production of the battery through raw materials, cell manufacturing, use and safety, management and applications, going through market trends, research and development, new technologies and finally closing the loop with a focus on recycling, second life and regulations. International battery industry key players such as OEM, cell and pack manufacturers, end users, experts, researchers and recyclers will come together to discuss.
Contact AVICENNE Energy www.batteriesevent.com
Battery Tech Expo,Prague
October 18
Prague, Czech Republic
Central Europe is rapidly emerging as a key location in the Battery Technology landscape. With a well-established and rapidly developing automotive industry, and a growing number of gigafactories both in operation and planned to come on-stream, the next few years will see a rapid expansion in battery production capacity in the region.
Contact
10fourmedia
David Reeks, event director
E: david.reeks@104-media.com www.batterytechexpocentraleurope.com
EV Battery Technology Conference and Exhibition
October 23 – 24
Long Beach, CA. USA
Battery technology is the future.
The world’s emerging appetite is for electric vehicles. The automakers and companies for batteries are investing copiously to construct lighter, denser and affordable batteries.
The formation and assembling of the battery signify its performance and cost.
But for the future, wholly different chemistries and bigger breakthroughs are anticipating an emergence.
This is where our EV Battery Technology Conference and Exhibition is going to come in place and will provide you with an exclusive platform to divulge deeply into this subject. To let influential voices and key players from the EV industry speak about conviction. The conference will provide an exquisite opportunity for EV enthusiasts to behold all the latest and greatest the EV industry has to offer. From electric scooters to electric bikes to electric cars and buses, everything will be on a display to give you the best and a niche experience in the EV spectrum.
Contact MetaTech
E: info@metatechevents.com www.evbatterytechconference.com
Li-ion Battery Europe 2023
October 29 – 31
Budapest, Hungary
Li-ion Battery Europe 2023 is at the forefront of expediting the development of EV & Li-ion Battery in Europe, gathering policymakers, investors, manufacturers, raw material suppliers, component suppliers and technical service providers internationally to build partnerships.
Highlights include:
• Build and expand your network with 800+ International C-level key players
• Get a complete overview of opportunities and challenges in optimising Li-ION projects
• Take part in over 15 hours of networking time with a unique crowd of financial and Li-ION stakeholders
• Join a dynamic, interactive event
featuring brainstorming sessions, open space time, networking moments, and much more
• Pre-day VIP Salon and Field Trip Energy Storage Journal readers and subscribers are welcome to use the following promotional codes for a 10% discount:
Standard Ticket — LIBEBIS. Valid from July 1st – October 31st, 2023.
Contact
Shanghai Metals Markets — SMM
E: Youngyang@metal.com
www.li-ion-battery-europe-metal.com
Battery Safety Summit
November 6 – 7
Tysons Corner, VA. USA
The Annual Battery Safety Summit will bring together the key players from around the world to present the latest R&D advancements for integrating and implementing LIB safety to meet ever-increasing energy demands.
With constantly increasing market demands for higher energy density cells globally, it is critical that advances in chemistry and engineering for next generation batteries have a significant focus on safety.
Accurate testing, modelling and battery management systems are critical for predicting and controlling the complex electrochemical, thermal, and mechanical behavior of LIBs.
Contact
Cambridge Enertech
E: ce@cambridgeenertech.com
www.cambridgeenertech.com/batterysafety
Battery Experts Forum
November 7 – 9
Darmstadt, Germany
The Battery Expert Forum is the largest battery conference in Europe. The forum offers an unparalleled platform for exchanging information on the latest developments in battery technology, presenting innovative products and services, and making valuable business contacts through renowned exhibitors, a comprehensive conference program and first-class trade visitors.
Contact
Battery Experts Forum
E: info@battery-experts-forum.com
www.battery-experts-forum.com
Battery Innovation Days
November 14 – 15
Bordeaux, France
Battery Innovation Days (BID) fosters dialogue among the research community, policymakers, industry players and end-users to boost battery research and innovation in Europe.
Contact CLERENS
E: info@batteryinnovationdays.eu
www.accelevents.com/e/batteryinnovation-days-2023
The Energy Management Exhibition
November 22 – 23
London, UK
EMEX is the UK’s must-attend energy event for everyone wanting to increase their organisation’s energy efficiency and reduce carbon emissions. EMEX connects all commercial energy consumers with leading experts, policy makers and suppliers.
EMEX is more than just an event. It’s a platform where practitioners and experts from various backgrounds and sectors are coming together to share their knowledge and experiences from successful implementations of energy efficiency strategies.
Contact Mark Allen Group
E: julia.pugh-cook@markallengroup.com www.emexlondon.com
SAVE THE DATE
Future Battery Forum
November 27 – 28
Berlin, Germany + Online
The management conference brings together the entire value system of battery technologies: Across various industries more than 300 users, battery system and cell manufacturers and their suppliers will spend two days exchanging information, making new contacts and enriching each other.
Contact IPM AG
E: fbf@ipm.ag
www.futurebattery.eu
London EV Show
November 28 – 30
London, UK
The next edition of the London EV Show will once again bring the entire EV value chain under one roof to network with major industry players and identify numerous business opportunities in a hypercompetitive EV market.
The event aims to enable a large showcase of the new EV models & innovative solutions, a powerful speaker line-up and an enthused audience of policymakers, business leaders, investors, thought leaders and a wide range of end-users.
Featuring a massive exhibition space and highly-actionable conference agenda, London EV Show is a must-attend EV event of 2023.
Contact Valiant Business Media
E: info@londonevshow.com
www.londonevshow.com
Advanced Automotive Battery Conference USA
— AABC USA
December 11 – 14
San Diego, CA. USA
AABC was founded more than 20 years ago to review the status of automotive battery technology and provide informed glimpses into the future.
The 2023 program will uncover the underlying technical and business issues that will impact the pace and path of vehicle electrification worldwide.
Join us to network with chief battery technologists from leading automotive OEMs, who will share their development trends and projected battery needs, as well as their key suppliers who will present their latest offerings and roadmaps for the future.
Contact Cambridge Enertech
E: ce@cambridgeenertec.com
www.advancedautobat.com/us
Intersolar North America
January 17 – 19
San Diego, CA. USA
Intersolar North America and Energy Storage North America is the premier U.S.-based conference and trade show focused on solar, energy storage, and
EV charging infrastructure.
Dedicated to accelerating the energy transition, the combined event delivers actionable education, invaluable networking, and an immersive exhibit hall experience – which includes the popular Solar Games installer competition.
Attendees get in-depth technical training and forward-looking education from top experts. Experience the solar industry’s best practices for the design, installation, and maintenance of code-compliant PV, storage systems, and EV charging infrastructure. Tour the expo floor to review the bestin-class companies and the top solutions, services, and products for the year ahead.
Join 6,000+ energy leaders and 300+ exhibitors in Long Beach, CA, to help shape the next phase of our clean energy transformation.
Contact Diversified Communications
E: ISNAinfo@divcom.com
www.intersolar.us
SAVE THE DATE
The Smarter E India — ees India
January 17 – 19
Gujarat, India
The market potential for electrical energy storage in India is expected to be tremendous in the future – especially driven by incoming policies for the e-mobility industry. With the great success and support of ees Europe, Europe’s largest exhibition for batteries and energy storage, ees India becomes the most powerful energy storage exhibition in India.
The exhibition is the industry hotspot for suppliers, manufacturers, distributors and users of stationary electrical energy storage solutions.
Covering the entire value chain of innovative battery and energy storage technologies – from components and production to specific user applications.
Contact
Solar Promotion International
E: info@solarpromotion.com
www.thesmartere.in/en/ees-india
ENERGY STORAGE EVENTS

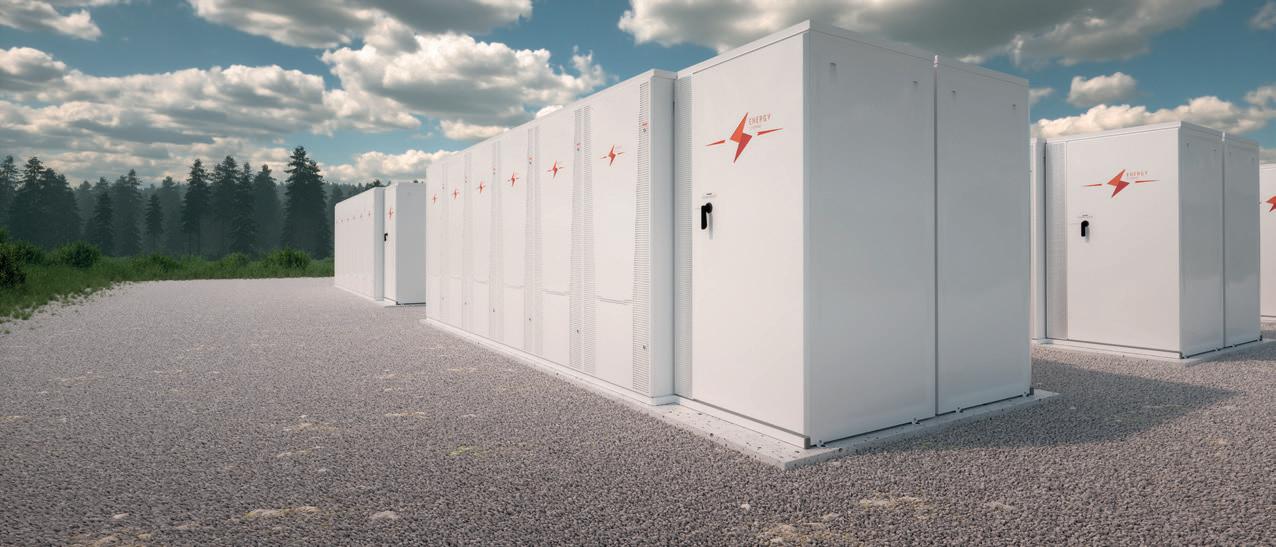
—
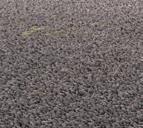
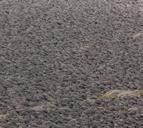
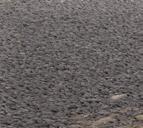
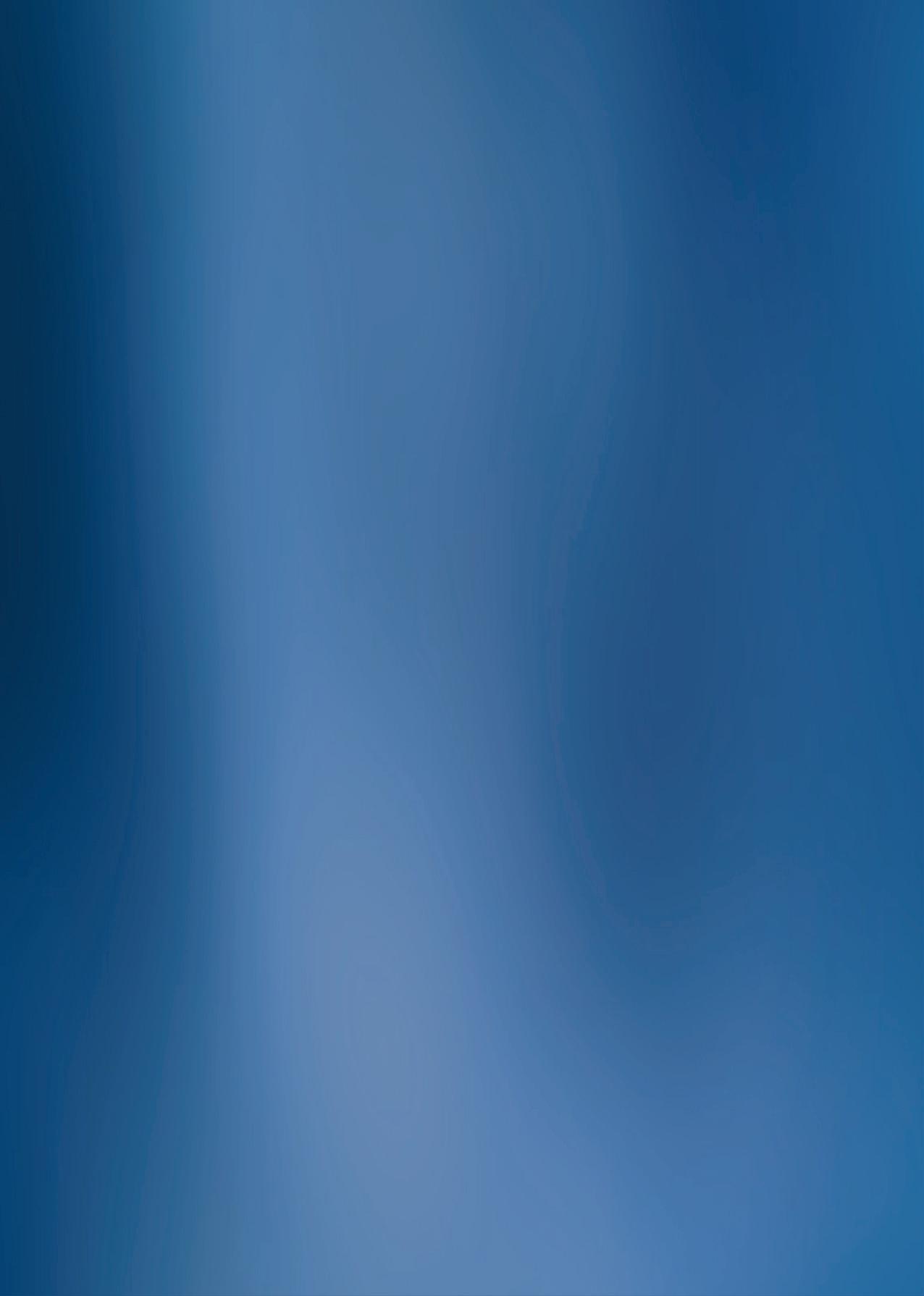
The Leading Exhibition Series for Batteries and Energy Storage Systems
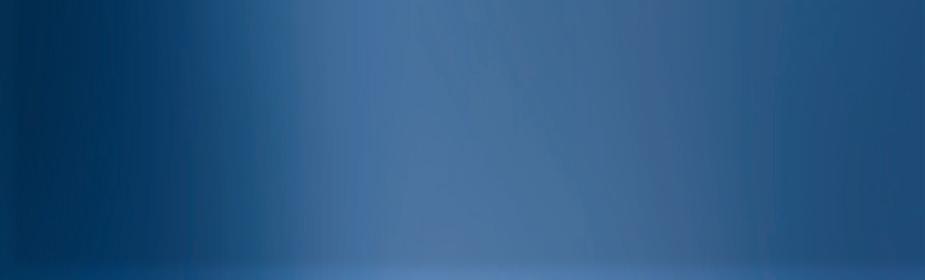
■ February 21–23, 2024, GANDHINAGAR, INDIA INDIA‘S LEADING ELECTRICAL ENERGY STORAGE EXHIBITION www.ees-india.in
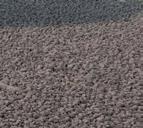
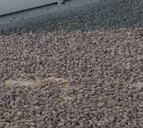
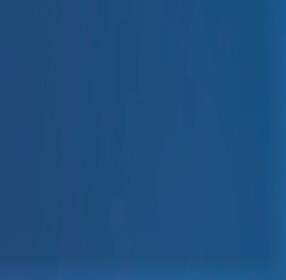
■ JUNE 19–21, 2024, MUNICH, GERMANY EUROPE’S LARGEST EXHIBITION FOR BATTERIES AND ENERGY STORAGE SYSTEMS www.ees-europe.com
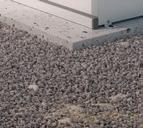
■ AUGUST 27–29, 2024, SÃO PAULO, BRAZIL SOUTH AMERICA’S HOT SPOT FOR BATTERIES AND ENERGY STORAGE SYSTEMS www.ees-southamerica.com
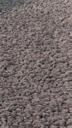
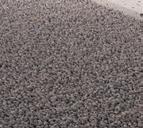
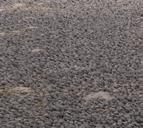
Follow us




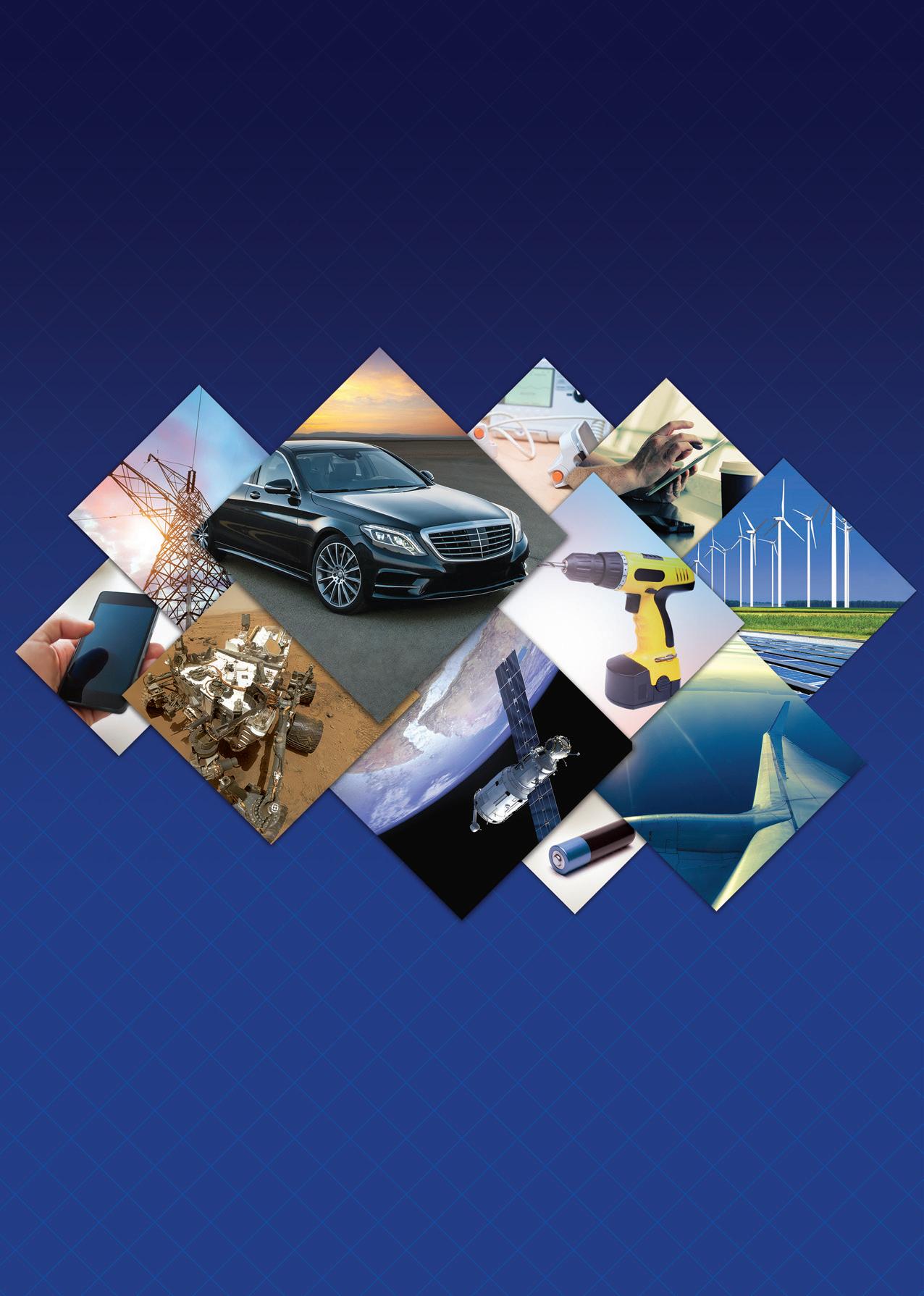