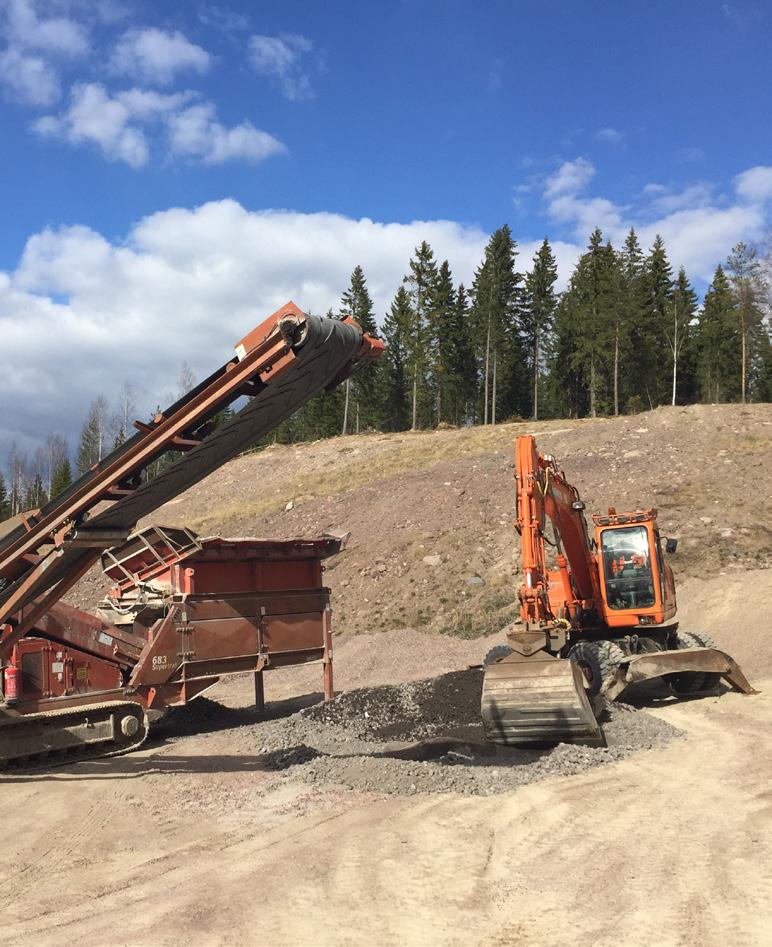
4 minute read
of industrial side streams
POTENTIAL OF GEOPOLYMER COMPOSITES
– QUALITY, ENVIRONMENTAL FRIENDLINESS AND 3D PRINTING
Advertisement
Geopolymer technology provides a good starting point for curbing climate change and reducing CO emis2 sions from the construction industry thanks to the ability of geopolymers to act as an alternative to the industry’s most commonly used binding material, Portland cement.
The strength of the geopolymer composite developed in the course of the UIR project lies in the use of waste materials, which promotes sustainability and reduces energy consumption compared to the same volume of Portland-cement production. Tangible environmental impacts can be eliminated by using organic and inorganic waste materials in the cement industry to change characteristics and even as fillers. A range of different source materials containing high levels of silicon dioxide and aluminium can be used for geopolymer synthesis.
THE ROLE OF ‘LOCAL’ IN BUILDING A SUSTAINABLE FUTURE
The aim of the UIR project was to respond to the need to find an environmentally friendly way to build in the future. LUT University contributed to the project by conducting research to ensure the quality of the new material. LUT University studied five types of raw materials produced as side streams in different industrial sectors in South Karelia and the potential of using these raw materials commercially for the 3D printing of geopolymers at construction sites and in factory conditions. The initial investment needed for transporting, storing and pre-treating these raw materials was also studied. Raw material transport was explored from the perspective of two main functions: logistics and transport management. Cost analyses were produced focusing on suppliers as well as strategic and operative functions. The annual investment needed for each raw material’s pre-treatment technology was also described in the reports. Parameters were determined for the geopolymer synthesis and strength requirements for the different types of geopolymers.
PROVEN VERSATILITY AND DURABILITY
The temperature and speed at which a material hardens and the direction and duration of its compressive strength are key factors in determining the strength of 3D-printed powder-based geopolymers. The structural and mechanical characteristics of geopolymers and their excellent chemical and fire-resistance properties make them a good raw material for 3D printing.
A computer-based scaling exercise suggested that the original material costs of geopolymer composites were approximately 32% higher than those of conventional concrete of the same grade (M45). Geopolymer development can lead to beneficial characteristics, such as durability, reduced use of natural resources, lower maintenance costs and better mechanical properties.
The composition of costs was studied with respect to both on-site and factory-based 3D printing of geopolymers. Time, costs and quality were taken into account, as these factors correlate positively with cost. The cost of 3D printing a house on site was also estimated to be lower than that of conventional factory-based printing.
PRINTER DEVELOPMENT AND PRODUCT OUTPUTS: PRINTING 3D printer for a geopolymer composite
Advances in printer technology have also made industrial-scale 3D printing of conventional concrete and concrete-like materials a more common and viable alternative, although universal printing standards are yet to be adopted.
3D printing provides a pathway to economically and ecologically sustainable construction featuring versatile, elaborate designs. The new concrete-like material developed in the course of the UIR project also needed its own printer.
STRONG PRINTING KNOW-HOW IN SOUTH KARELIA
The role of Imatra-based Fimatec Oy was to develop a 3D printer that can ultimately be used to print the new concrete-like material on a large, industrial scale.
The printer development process consisted of a number of steps, starting with early versions that were based on a robotic arm. The first
versions were capable of running small-scale material tests using a geopolymer composite. The development work during the project increased understanding about the properties and further development of geopolymer composites that need to be taken into account in printer production. For example, water plays an important role in forming the structure of geopolymers, which is why ways to control its volume need to be explored as part of the printer development process in order to optimize flow characteristics. The printing media also need to be mixed for a specific period of time to achieve the required chemical reaction. Finally, development efforts need to take into account the flow of materials
and various printer settings, such as temperature and layer thickness as well as the number of modules that can be printed at a time.
BRIGHT FUTURE AHEAD FOR GEOPOLYMER COMPOSITES
3D printing enables a wide range of near-organic designs, which Fimatec developed in collaboration with design experts from Design Reform. The final development version of the printer was capable of producing new kinds of urban products, such as noise barriers, benches, planters and skate park structures. The pilot products are modular, and the same module can be used in different products that can be placed in various kinds of environments and used in different
ways. The finished products were placed around Lappeenranta and Imatra for local residents to admire and enjoy.
Geopolymer composites are challenging to print with current 3D printer technology due to issues with the performance and uniformity of the material. 3D printing technology suitable for printing geopolymer composites still needs to be developed further before it can be used for industrial-scale serial production. It is nevertheless worth noting that geopolymer composites appear to be easier to produce by means of 3D printing than concrete. It has been estimated that 3D printing will be deployed on a large scale in the construction industry within 5 to 10 years.
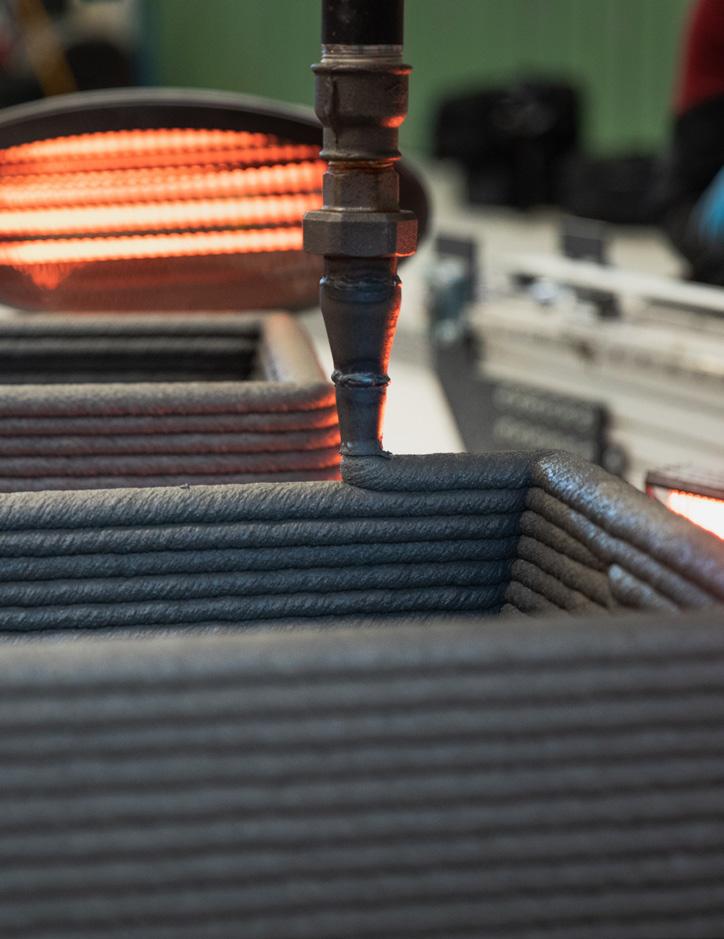