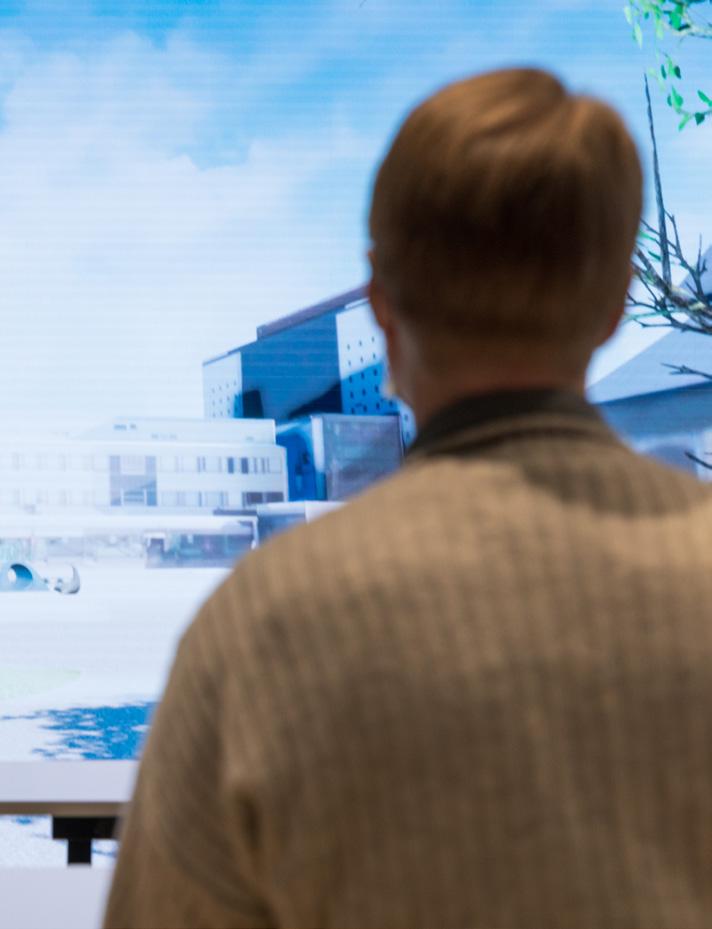
12 minute read
Construction industry materials from waste
SUSTAINABLE GEOPOLYMER BUSINESS
There are various factors that are critical for creating business: the availability of suitable raw materials, product characteristics and applications, the market’s products and competing products, the most potential end products, the structure of the potential business ecosystem and possible business models, and the life-cycle costs of the end products relative to competing products. The companies worldwide currently running business based on geopolymer composites were benchmarked for their products and business models at LUT University. Geopolymer-based concrete is utilized relatively little in construction at the moment because 1. current material standards hinder the acceptance of geopolymer technology; 2. the availability of industrial side streams varies by location, and so do the their volumes and qualities; and 3. the cost of geopolymer production easily exceeds that of ordinary Portland cement (OPC) production.
Advertisement
The most common side streams that are used in geopolymer composites are blast furnace slag and coal fly ash, which are also used as supplementary cementitious materials in OPC concrete, and the current utilization rate of these side streams is generally high. Many slags/ashes that can be, and currently are, used for soil stabilization purposes in earthworks and in fertilization can serve as aggregates in concrete making. This can create significant competition in the secondary raw material market, and the availability of local secondary raw material sources can become a bottleneck for GPC production. Moreover, the coal fly ash that was found to be better suited for GPC production than biobased fly ash is a disappearing resource in Europe.
The most common drivers for any industry to adopt new materials are the cost efficiency and/or superior performance of the material. Materials based on secondary raw materials – such as geopolymer composites – are usually more expensive than those made of virgin materials. In this case, when an alkali activator was used in GPC it was found to be the determinant to the cost of geopolymer composite and the overall cost was estimated to be significantly higher compared to that of conventional concrete. Thus, as the price competition is not in favour of geopolymer composites, they must beat the competing materials in their environmental and/or technical performance in order to attract market demand. It is noteworthy that legislation can, through various means, also guide companies to use secondary raw materials to promote circular economy, so that the price of a material or product no longer determines the generation of demand.
THE POTENTIAL OF GEOPOLYMERS LIES IN THEIR PROPERTIES AND ECO-FRIENDLINESS
The strengths of geopolymer composites include, among others, fire and water resistance, corrosion resistance of chemicals, acids and salts, insulation properties, flexural tensile strength and very fast curing time compared to concrete. In addition, as geopolymer composites are at their best low carbon and 3D-printable, this creates an attractive combination of properties to industry, which are particularly well suited to various solutions in e.g. the construction and process industries. For example, process tanks in different shapes with optimum flow properties can be printed from geopolymer composites because steel reinforcements limiting the shape in casting are not required. In addition, production is fast, labour and production costs are lower than in casting, and the printing process is resource-efficient and sustainable. However, it is important to find new usable side streams, as well as new applications where geopolymer composites provide added value that no other material can.
OUTPUTS:
Market potential report
Description of a viable, sustainable business ecosystem
Report of the acceptance procedure
FROM MATERIAL TO A CONSTRUCTION PRODUCT
In order to access the markets in the EU, construction products must comply with extensive standards and regulations set for the products. EU regulation is set to improve the free movement of construction products in the EU by laying down uniform rules for the marketing of these products and by providing a systematic way to assess the performance of construction products. In this way legislation and product standardization also work as a baseline for industries to verify the safety of novel geopolymer materials and products.
A product’s applicability for use in construction must always be assessed case by case based on its intended use, local conditions and the requirements laid down in the particular construction regulations. Commercial manufacturers of noise barriers, for example, need to comply with common European product standards. When entering the markets, a product must meet the requirements set in the EN 14388:2015 standard and, applicable national and local instructions must also be observed. The Finnish Transport Infrastructure Agency has issued its own guidance on noise barriers along motorways and railways in Finland. Product characteristics required of all noise barriers relate to, for example, sound absorption performance as well as resistance to loads and forest fire.
PRODUCTS MADE FROM GEOPOLYMER COMPOSITES REQUIRE TYPE APPROVAL
While the intended use, local conditions and product regulations set the requirements for the actual end product, specific requirements for the material used in the product manufacturing must also be met. Geopolymer composites are a new material not yet covered by EU construction product standards. Therefore, an applicable reference to indicate the conformity of the material properties was needed.
As many of the geopolymer composite material properties are comparable to concrete, the standardized tests for concrete and the associated product standardization framework were used as a reference. The primary properties of concrete are resistance to compression and flexion. Depending on the end product, additional performance requirements are set for the material; in flooring tiles, for example, a certain level of resistance to abrasion must be achieved.
This project involved establishing a general protocol for meeting the safety-related, environmental and mechanical requirements of construction products. This document is intended to help companies to seek approval for commercial geopolymer composite products in the future.
Other potential slags/ ashes Blast furnace slag / coal fly ash Certain fractions of consumer waste
BINDER PRECURSORS Certain ashes / other
ALKALI ACTIVATORS Mining tailings / side rock Slag/ash
AGGREGATES
GP COMPOSITE MAKING Construction Demolition Earthworks Fertilization
ADVENTURES INSIDE A CITY MODEL
As the old saying goes, a picture is worth a thousand words. The claim may seem exaggerated, but it provides an interesting reference point and inspires thoughts of what it would be like to step into a picture and move around in it. The adage also answers the question of what would be the best way to present the results of a project that created revolutionary technologies that solve future challenges and can be used to build sustainable, high-quality living environments based on a completely new design language.
The City of Lappeenranta joined forces with LAB University of Applied Sciences and Design Reform to build two city models: a browser-based one and one based on a video game engine. Both are efficient interactive tools that provide a technically accurate and visually impressive overview that professionals can use in urban planning and residents can access to get involved in designing their living environment.
The city models were designed and built taking into account the scalability and potential uses of the information and materials produced during the course of the project as well as the possibility of also benefiting from the outputs of the project in the future. Requirements were agreed for accuracy, quality and information content beforehand based on the project’s objectives in order to produce enough source data. The high standard of the source data enabled the use of a range of modelling software and the creation of the kind of accurate and visually striking city model that the project sought for different environments.
The browser-based city model is easily accessible to the public and allows them to browse and comment on various kinds of plans. The model was built using an application called MAPGETS, developed by FCG Oy for the visualization of three-dimensional data. Local residents were able to use the browser-based model to give feedback on current urban planning initiatives and to explore the project team’s visions for the centre of Lappeenranta in 2030 and 2050. The project also gave local residents the opportunity to add content. The model features ideas submitted to the New City Products competition as well as urban structures designed by students of Pontus School.
A separate Virtual Reality Expo was built in the Venla meeting room of Lappeenranta City Hall, where the public can explore a virtual city on a grander scale. It is based on Unreal Engine video game technology and features a large, high-resolution LED wall and a sophisticated sound system that together transport visitors to a realistic virtual environment depicting the centre of Lappeenranta. The content developed for the game engine model can also be used flexibly in other environments, such as virtual reality headsets and three-dimensional CAVE (Cave Automatic Virtual Environment) solutions. Going forward, the environment in the City Hall can be incorporated into various kinds of urban planning workshops, meetings, lectures and press conferences.
OUTPUTS:
Virtual Reality Expo
Virtual city model based on a video game engine.
SUCCESS BEYOND EXPECTATIONS
TARGETS MET IN MANY RESPECTS
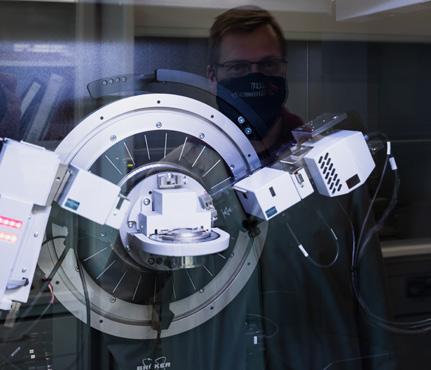
This was a hugely ambitious project, and there is reason to be proud of the results. Eight different performance indicators were chosen for the project even before the application was submitted. The indicators, and how well the project succeeded relative to the indicators, are discussed in more detail below.
1. The project team wanted to develop a 100% recyclable concrete-like circular economy material for the construction industry based on a geopolymer composite with a circular economy material content of more than 95%. The project exceeded expectations in this respect. Recipe 4 proved to be the winning formula with a circular economy material content of 99.6%. The material is fully recyclable and printable.
2. The goal was to limit virgin side streams to less than 5% and achieve a circular economy material content of more than 95%. The virgin material content of the new geopolymer composite material developed in the course of the project can be as low as 0.4% and its circular economy material content as high as 99.6%. These are great achievements. We consider Recipe 4 our winning formula. Recipe 3 also hit the target with a circular economy material content of 95%. The project team sought to create technologically advanced new materials capable of withstanding the extreme weather conditions of northern climates by comparing especially the physical and chemical performance of the materials against the requirements of product standards (e.g. strength, flexibility, thaw resistance of water-based and anti-freeze solutions, water absorption and extractability). All the materials created were subjected to standard construction industry tests. Tests designed to establish how materials react to different
industrial or weather conditions were also performed. The tests showed that geopolymer composites can, at their best, match the performance of similar construction industry products in terms of flexural strength and durability. On the other hand, the fact that geopolymer composites harden so quickly gives them a huge advantage and exciting characteristics from the perspective of a range of applications.
3. 4. The team wanted to design revolutionary, aesthetically pleasing and safe multifunctional structures that could solve real-life urban planning challenges, for example, by featuring shapes that have better soundproofing properties than similar products. Most of the feedback on design collected from the public (more than 75%, which was the target) was positive and encouraging. New designs make a city more attractive. The effectiveness of the noise barrier could not be tested in practice during the project. Testing the barrier’s soundproofing properties in laboratory conditions would have required a large number of printed modules, which was not possible within the timescale.
5. The ambitious goal at the beginning of the project was to get the authorities to sign off on the methods and criteria of type approval, which is required for the CE marking of the pilot products. There is no internationally harmonized standardization system (“CE marking method”) for the material itself at the moment, but this does not prevent the use of geopolymers in urban construction. There are no restrictions on material with respect to, for example, noise barriers and skate park structures. Breaking through to the market and pursuing business are nevertheless more difficult, albeit not impossible, as a result. Type approval takes time, and the project team ultimately decided to just lay down the criteria and the protocol but not actually seek type approval for the pilot products.
6. Circular economy-based new and sophisticated business models have the potential to create, either directly or indirectly, between 50 and 200 new jobs in local industry. The project team explored five different business models. Creating jobs based on the new business models is a goal to be pursued over several years. When the final report was published, it was still too early to say whether the project succeeded in this respect. The new material developed during the course of the project combined with 3D printing is a novel solution, and spreading the message and commercializing the solution will take time. Experts estimate that this could take as long as between five and eight years.
Global market potential is particularly important when the domestic market is relatively small. One of the solutions piloted during the course of the project was a 3D-printed noise barrier for railways. Global market potential was not explored, but the project team estimated that approximately 25% of the noise barriers supplied to Finnish railways annually could be produced using three or four printers.
7.
8. The project team set out to look for comprehensive solutions with a low carbon footprint using low-emission raw materials and production technologies at various stages of the supply chain. One specific target was for the new geopolymer composite material to produce 90% less CO emissions 2 from the use of cement (0% cement) compared to concrete. The target was exceeded, and it is safe to say that a new potential construction material was born.
The industrial side streams used in the recipes were sourced locally, with the exception of coal fly ash, which was used in a few recipes and transported from a production facility of a commercial operator in Hausjärvi approximately 200 km away. The goal was to limit the transport distance of raw materials to 100 km
for local industrial side streams. The availability, volume and quality of the side streams used to make the material vary depending on location, and their test–retest reliability is therefore not easily scalable. The recipes need to be fine-tuned for each application.
It is clear that circular business models are here to stay. The business processes included in the models are designed to recycle resources infinitely, minimizing the use of virgin raw materials and carbon footprint. However, businesses will only adopt new materials if the new materials offer a competitive advantage over the materials they already use. This needs to be given particular attention during a potential follow-up project, which is being brainstormed at the moment.
