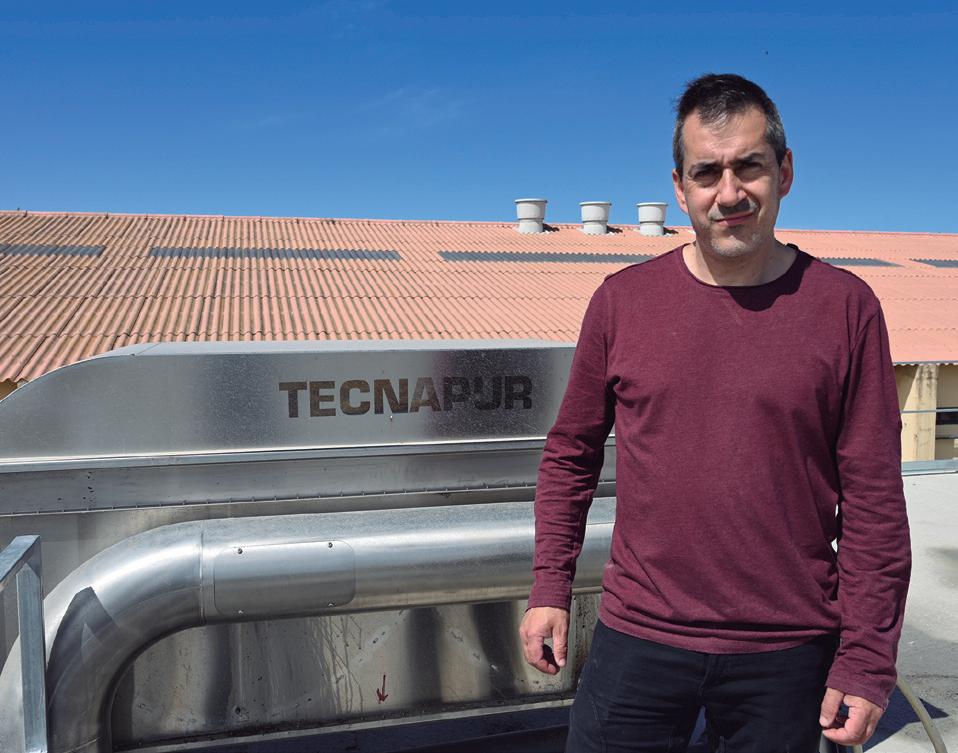
5 minute read
Global Pig
from 47 ROTECNA WORLD
A. CASSANYÉ: “THE TECNAPUR SYSTEM IS VERY VERSATILE, EASY TO USE AND HAS A LOW HANDLING COST”
With a capacity for 1,600 sows, the Cassanyé Farm belongs to the Gescaser family business, founded in 1973, and located in the town of Almacelles (Lleida).
Advertisement
Swine farming has always been very present in Antonio Cassanyé’s day-to-day life. From a young age, he lived very close to his father’s farm, located in Almacelles (Lleida), and in 1998, at the end of his studies in Agronomy, he joined the family business. Aware of the environmental demands that the sector must face, last January, Cassanyé decided to install the Tecnapur solids and liquids separator. Over these months, the farmer has already seen first-hand the benefits of working with Rotecna’s slurry management system.
What is the origin of the farm?
Cassanyé Farm belongs to the family business Gescaser, founded in 1973. In its early days, the farm began as a
Antonio Cassanyé with the Tecnapur separator. Photo: Rotecna.
fattening farm. A few years later, after the good results obtained, my father decided to introduce the first sows, ten at first. Since then, the business has been growing, and after several renovations and expansions, the farm can currently accommodate some 1,600 bristles.
How is it distributed?
On the one hand, we have a gestation unit that has approximately 1,200 places. On the other hand, we also have a lactation unit with 400 slots, a replenishment with 500 spaces and a heat detection unit.
What led you to install Tecnapur’s mechanical slurry separation system?
We decided over the last year, and we did so to comply with all the requirements set by environmental legislation regarding the treatment of slurry to move forward with our activity. That is, we decided to install Tecnapur to be more environmentally friendly and more selfsufficient. With this vision of the future, last January, we started implementing the Tecnapur separator, and now we are finishing the testing period to implement the
system throughout the farm. During this time, we have made all the necessary adjustments for the correct use of the system and to be able to extract the maximum nutrients from each of the slurry portions.
How did you decide to go for the Tecnapur separator?
We looked at several separation systems on the market, but they were more expensive, and their use seemed more complex. Finally, we decided on Rotecna’s solids and liquid separator because, compared to other systems, we consider the Tecnapur system to be very versatile, easy to use and has a low handling cost.
How many cubic meters of slurry do you handle per day?
Currently, the farm is generating about 50 – 60 cubic meters of slurry per day. Still, during the testing period, we have treated about 20 cubic meters a day to check the system’s operation.
How do you handle the slurry through the separator?
The slurry generated by the animals is collected in a reception raft in which we have an agitation system so that the slurry is always homogeneous. There is also a pump that propels the slurry to the separator. The separator has a chamber with a flow regulator adjustable according to the slurry’s density, allowing us to handle more liquid and thicker slurry. In addition, this chamber has a retention system of unwanted solids that enables us to generate a solid portion without polluting materials, such as plastic fragments of crotals. After the camera exits, the slurry passes through a system of double-pressed and scratched sieves with round holes that prevent the passage of animal hair. Finally, we get the solid portion and the liquid portion.
Regarding the initial volume of slurry, what percentage do you get from each portion?
These first few months we are testing, and the proportion of slurry we input from the one we separate, the solid portion we obtain comes to about 15%.
What do you do with each of the portions?
The intention we have is to use the liquid portion for spray irrigation. As for the solid part, we have different options on the table. On the one hand, there is the option to allocate this portion to its use as composting and, on the other hand, take

it to management centres to use as a source to produce biogas, compost, etc.
At the farm level, what is the cost of separating in terms of labour, electricity consumption, etc.?
First, the cost of managing the liquid portion is reduced since we use it to water, and therefore we do not have to move it with vats. Secondly, the machine has low power consumption. Finally, it operates automatically with very little maintenance, so its cost for labour, which is very small, is intended for cleaning, greasing and general maintenance.
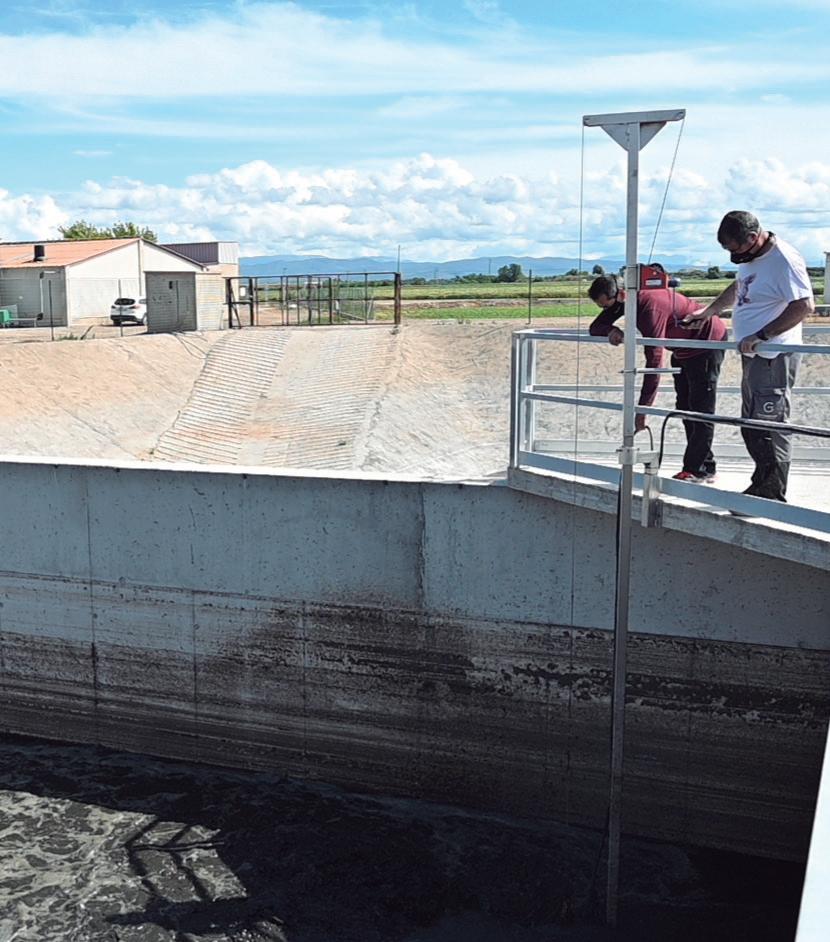
What other Rotecna products do you have installed?
In addition to the separator, we have installed polypropylene panels, plates for piglets and some hoppers. We decided on these products because they’re from a brand that I have known for years and that is fully established within the sector because of the quality it offers. Rotecna’s products work very well for us, are durable, adapt very well to animals, and are easily managed by farm employees.
What are your main health concerns? What biosecurity measures have you taken?
We are exposed to multiple external factors that can influence our production, and the most important one is the threat of PPA, which seems to be close by. In this sense, to avoid the entry of any threat, we have an external fence and aviary fabrics. In addition, we
Piglets resting under the Ni-2 Weaner. Photo: Rotecna. The farm works with the agitator to homogenize the slurry. Rotecna.
disinfect all vehicles when necessary. We have differentiated a dirty area and a clean area, etc.
Are there any future challenges?
At the business level, the main challenge is to produce quality meat. At the environmental level, we face demanding challenges that we hope to meet with creditworthiness with the Tecnapur system. In this sense, we will install two separators on two other farms of the company, and in one of them, we want to complete the system with the installation of the physicochemical reactor. Therefore, we want to be at the front line to make sure all challenges are opportunities.
Scan the QR code with the mobile camera.
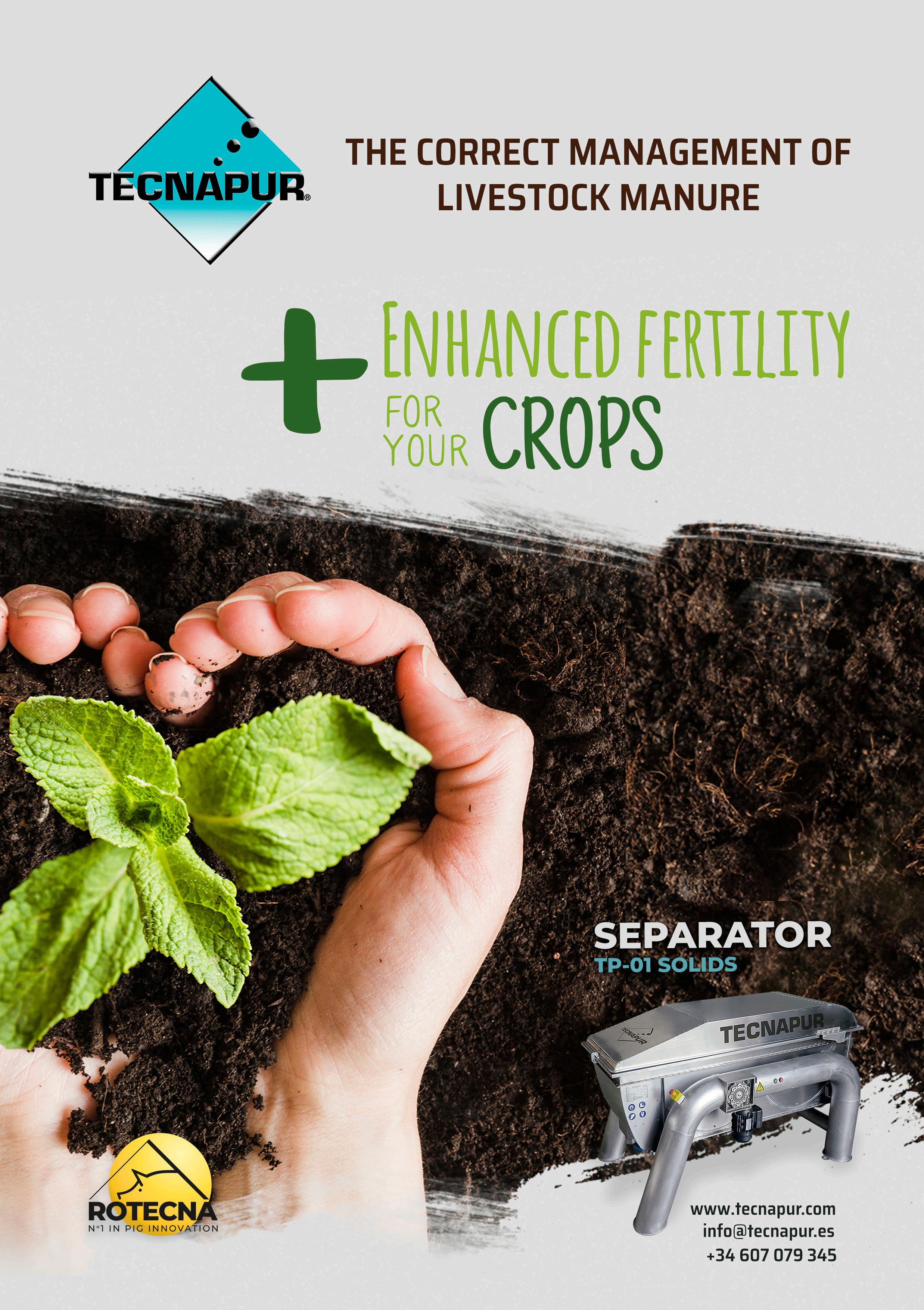