
4 minute read
Graphically Speaking
Getting Connected – Improving Customer Experiences
Jim Crawshaw, PSI
What does ‘getting connected’ mean in rotational molding?
This means improving the customer experience, by connecting them with your products, and ultimately you, the brand ambassador. This is enabled through track and trace methods, a crucial part of rotomoulding and it is undeniably known as the future of all manufacturing known as, Industry 4.0.
Considering the significant cost, resource, and productivity advantages it provides, it is not hard to see why traceability offers so many benefits to connect your products with the manufacturer and the end-user.
Benefits of tracking in rotomoulding
Factors which directly benefit rotational moulding include: • Product recall – for quick and efficient identification of effected products • Quality control – provides a higher level of control through the manufacturing and after-sales servicing process • Operational efficiency – to locate and minimise waste of both materials and operational resources • Customer satisfaction – a robust system that better positions you to respond to your customers’ problems and make improvements to provide higher-quality products and meet their needs
How to track plastic products
A common question we get asked by rotomoulders is, ‘what methods are used for tracking plastic products’? There is no short answer as there are many, so we have created this article to help uncover these methods, as one or more may suit your specific application.
To start you need to identify the purpose of your tracking endeavour, reasons include: • Unique product identity – PSI recommends a serial number and/ or barcode • Production tracking i.e., date of manufacture, batch number, product specification – again we recommend serial numbers and/or barcodes • Distributor reselling – best solution is a product barcode • Product servicing, location, and data log – by manually using physical serial reference or digitally using barcode or RFID • Product information i.e., link to webform – such as QR Code • Anti-theft or multi-asset tracking – best solution here is RFID
Putting it simply, a unique identifier can be just a consecutive serial number associated to the product or part.
When should you use Serial Numbers?
One of the most common questions we get asked is ‘what is a good serial number system for my product’? Allow me to share an effective case study used by New Zealand rotomoulder and specialist boat crafter, Viking Kayaks. • Purpose – To identify product through production and identify for any product recall • Problem – use of hot-poker for scribing. This was very dependent on user, delivered poor aesthetics, and was not easily visible • Solution – Black & White serial no. in-mould graphic every cycle along with custom branding • Testimonial – “It looks sharp and means we can easily identify a boat from time of manufacture, right through to recall, now that’s customer service.”
So what about Barcodes?
Barcodes are one of the most effective methods for electronically tracking plastic products, and we turn to Victoria Australia for an original example at WaterStore Poly Tanks in Australia, who used barcodes to maximum effect.
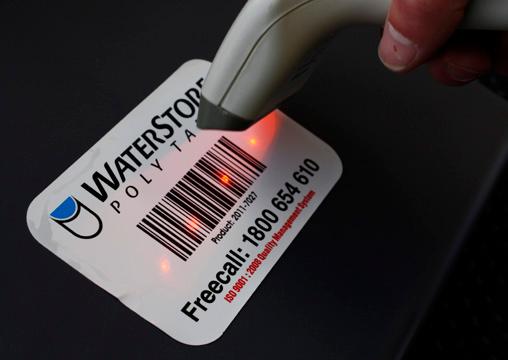
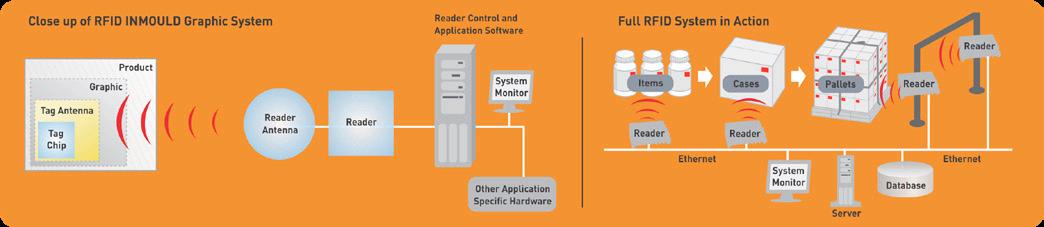
• Purpose – to identify product from production through to maintenance, connecting and ERP system for water-tank specialists • Problem – use of self-adhesive labels which peel off and completely disappear, a logistical nightmare! • Solution – pre-printed in-mould and post-mould graphics for every product • Testimonial – “Works well for our guys at the oven right through to the installers and maintenance team, lasting as long as the product. Also doubles as a branding tool and source of contact which is nice.”
What is RFID, and how is this used for plastics?
Can I use QR Codes?
What is often unknown is how to use QR codes effectively, however Saeplast Iceland found massive benefits through use of a QR codes. • Purpose – gain instant access to online tutorials on correct product specifications and use • Problem – end-user not being able to determine correct purpose of product and how to use the threefold tracking system • Solution – user scans QR with smartphones to access information as and when required • Testimonial – “As an insulated container, correct use is critical, especially when integrating the RFID and/or barcode system.”
RFID is the acronym for Radio Frequency Identification, a means of identifying objects via a wireless communications protocol using radio waves. This is an extremely adaptable method of tracking, and Saeplast Iceland pioneered the ‘threefold’ system featuring RFID. • Purpose – the ‘threefold’ tracking system was developed to provide multiple product tracking options #1. for product hire #2. enable processing of data #3. access instructions for product use on website • Problem – use of spin-weld RFID, and other secondary selfadhesive decals, which both proved time consuming and poor results aesthetically • Solution – a printed, 3-in-1; QR Code, Barcode, RFID in-mould graphic on each product, every cycle • Testimonial – “This insulated container is unique for us and the end-user. Barcode tracking is used for manufacture, QR Code to access to online ‘how-to’ tutorials and an RFID system to trace on the produce journey, from the source right through to the shop-front.”
What value can rotomolders take away from this article?
With our experience and know-how, we at PSI Brand are well positioned to propose and assist the best traceability solution that suits rotomoulders. No onesize fits all, so we will arm you with the tools and methods required to determine the best solution for your process.
Go to our website https://psibrand. com/track-and-trace/ and feel free to ask questions with Jim Crawshaw at +646 8344808 or email jim@psibrand.com
