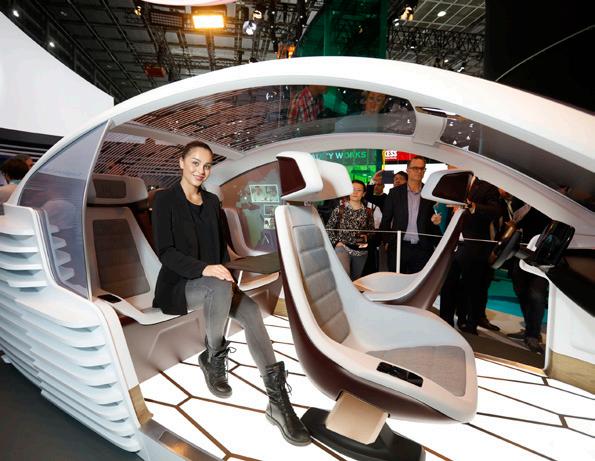
33 minute read
Upfront
70 Years of K In Düsseldorf – A World Career Made in Germany
Now online: the anniversary in historical photos and stories
The same year that saw Queen Elizabeth II ascend to the throne, the first artificial heart valve implanted in the U.S., and the musical “Singin’ in the Rain” inspire millions at the movies, history was also made in Germany with the inaugural edition of K, hosted in Düsseldorf from October 11-19, 1952. At that time nobody expected this event only just taking off would develop into the world’s leading trade fair for the plastics and rubber industry.
Today, K in Düsseldorf can look back on a 70-year success story. It is the most relevant information and business platform for the plastics and rubber industry worldwide. Its position as the leading trade show for the entire industry, where theme leadership and innovation go hand in hand to pave the way for visions for the future, is undisputed. No other platform has such a high internationality as K. For K 2022 from October 19 - 26, around 3,000 exhibitors from 61 nations are expected and the Düsseldorf Exhibition Center is completely booked.

How it all started
However, K in Düsseldorf also started small: the debut event “Wunder der Kunststoffe” (Miracles of Plastics) in 1952 registered 270 exhibiting companies – exclusively from Germany. They occupied approximately 14,000 square meters of net exhibition space.
At the premiere, 165,000 visitors admired especially the colorful consumer goods exhibited by plastics processors. Because from 1952 to 1959, K Düsseldorf was purely a showcase of the German industry. Any interested visitor, be it a layperson or a specialist, was admitted to visit the trade fair. Major attractions on show were products designed to make life more beautiful and convenient. Today, we smile at the advertising of that time, which was also aimed at the “modern housewife” and introduced her to such postwar achievements as trendy PVC raincoats or sheer nylon stockings - aesthetic epitomes of the economic miracle.
The more the plastics industry specialized and high-tech plastics for special solutions in electronics, medicine, automotive, or aerospace attracted attention beyond standard polymers, the more specialists visited the trade fair. In 1963 the break was made: K in Düsseldorf became a special-interest only trade fair of international standing. Since then it has maintained its position as a leading global trade fair for the entire industry. In 2019, over 220,000 trade visitors from almost 170 nations traveled to K.
The international origin and composition of exhibitors will also guarantee the completeness of the product ranges and a comprehensive overview of the world market at the upcoming K in autumn. Nowhere else will there be such a wealth of innovations and no other trade show will provide such a variety of impulses for the future of the global plastics and rubber industry.
Event’s own microsite: experience 70 years of K in Düsseldorf
Before K 2022 even opens its doors, Messe Düsseldorf is celebrating K’s anniversary with its own microsite, inviting everyone to delve into seven decades of K history and to marvel at historical photos and stories. Embark on a travel through time at https://70years.k-online.de/en
Anyone who would like to share their personal K story, anecdotes, encounters, funny, or amazing experiences, please use LinkedIn or get in touch with our press team.
For information on visiting or exhibiting at K 2022, contact Messe Düsseldorf North America; Telephone: (312) 781-5180; E-mail: info@mdna.com; Visit www.k-online.com and www.mdna. com; Follow us on twitter at http://twitter.com/mdnachicago
UPFRONT
Myers Industries Expands Production with Acquisition of Rotational Molding Facility in Georgia
Investment further expands and strengthens Myers’ rotational molding capabilities
Myers Industries, Inc. (NYSE: MYE) recently announced that it is increasing its production capacities through the acquisition of the Decatur-based rotational molding manufacturing assets of Step2 Co, LLC for an undisclosed sum.
This investment comes as Myers continues to expand its rotational molding capabilities across the United States. Myers’ Material Handling Segment utilizes rotational molding to provide high-quality, durable products to a broad range of endmarkets including outdoor recreation, construction, vehicle, and industrial applications. The 41,000 square foot Georgia facility adds production capacity to support both new and existing customers in the southern United States.
“The addition of this Decatur rotational molding location represents another milestone in the execution of our long-term strategy that is unlocking additional growth and expansion opportunities to serve our customers,” said Mike McGaugh, President and CEO of Myers Industries. “This marks our third meaningful investment in rotational molding in under two years and strengthens our position as a valuable partner for our rotational molding customers within our Material Handling Segment. We look forward to integrating this location into our Myers footprint and accelerating our organic growth efforts.”
This expansion demonstrates Myers’ commitment to growing its customer sales and service range while building a presence in new markets. This is the latest action taken as part of Horizon 1 of the Company’s 3-horizon strategy, which is focused on: Self-help, Organic Growth, and Bolt-on M&A. The expansion follows Myers acquisitions of Elkhart Plastics and Trilogy Plastics – further increasing Myers’ market-leading reach as a rotational molder serving a variety of niche markets.
Myers Industries, Inc. is a leading manufacturer of a wide range of polymer and metal products for industrial, agricultural, automotive, commercial, and consumer markets. The Company is also the largest distributor of tools, equipment, and supplies for the tire, wheel, and under-vehicle service industry in the U.S.
Visit www.myersindustries.com to learn more.
Beaver County Cracker Plant more than 95% Built as Company Prepares for Operation
POTTER TWP. — A Pennsylvania petrochemical plant years in the making will likely be online in a matter of months, with crews putting the finishing touches on Shell’s ethane cracker facility. Shell Chemicals recently confirmed the company’s multibillion-dollar Potter Township complex, long considered one of the largest construction projects in the nation, is now more than 95% complete.
In the next two weeks, Beaver County crews will begin performing “air blows” in the site’s ethane cracking unit and “steam blows” in the polyethylene units. Similar to the steam blowing activities completed in June of last year, nearby residents can expect “low levels of noise” intermittently through the end of March “2022 is an exciting and important year for our project,” Shell representatives said on Facebook. “ We will be operational later this year.”
Workers plan to follow local noise ordinances during the cleanliness checks, noting the activities “have been modeled to fall within permitted levels”. Shell plant: Shell begins ‘steam blowing’ at Beaver County cracker plant.
The company has yet to announce a firm opening date, but crews began start-up activities early last year around the time Shell CEO Ben Van Beurden announced the chemical plant will be “fully operational” in 2022.
In July, the project was considered 80% complete as staff commissioned the 250-megawatt natural gas and steam cogeneration facility and first exported power to the PJM electricity grid – a major milestone on the path to startup.
The plant, located along the Ohio River, will convert natural gas into ethylene, used in plastics manufacturing to make a range of products from automotive parts to food packaging.
Shell leadership first revealed plans to build on the former Horsehead Corp. zinc property a decade ago, hoping to take advantage of the region’s abundant natural gas while cutting transportation costs to the majority of the company’s customer base in the northeastern United States. Construction began in late 2017 after Shell secured $1.7 billion in Pennsylvania corporate tax credits.
UPFRONT
SOCIAL CIRCLE, GA, USA — Diversified Plastic, Inc., a leading international rotational molder based out of Latta, South Carolina, introduces a new rotational molding oven to their facility in Social Circle, GA.
With the implementation of the new rotational molding oven, it will assist in the overall increase of productivity and allow DPI to produce larger quantities of plastic products. DPI currently has 25 plastic product lines that vary from material handling carts to commercial trash containers. This new oven has the capability to manufacture all of DPI’s product lines in an efficient manner.
“We are enthusiastic to introduce the new rotational molding oven to our facility,” stated Scott Oaks, vice president of Diversified Plastics, Inc. “It will help us to manufacture our plastic products more efficiently and allow us to expand our product lines.” Since 1976, Diversified Plastics, Inc. has been the leading rotational molding manufacturer of custom and standard material handling carts and plastic storage containers. DPI specializes in material handling carts for the industrial, textile, hospitality, laundry, agricultural, and marine industries. DPI also provides waste and recycling plastic containers for restaurants, sports venues, stadiums, apartments, condominium complexes, and corporate offices.
In addition to providing custom material handling solutions and waste containers for any application, DPI’s diverse product assortment includes bulk material handling carts, plastic utility carts, laundry carts, bulk containers, tote boxes, round containers, spring platform trucks, elevated carts, easy access carts, tilt trucks, and more.
To contact Diversified Plastics, Inc., call 1-800-768-7636 or email sales@dpiroto.com. Visit dpiroto.com for more information.
ACE to Build the Largest Battery Recycling Plant in North Texas
The Lone Star State is gaining another massive facility. ACE Green Recycling has announced plans to build and operate what will become North America’s largest emissions-free and sustainable battery recycling plant. While a specific location hasn’t yet been revealed, the company shared in a statement that the operations will take place somewhere in Texas.
“Texas sits at the heart of the world’s global energy revolution with key access to an abundant pool of top engineering and technical talent. ACE’s new facility aims to be part of that revolution and build a greener, more sustainable future for America,” said Nishchay Chadha, ACE’s Co-Founder and Chief Executive Officer in a statement.
The 400,000-square-foot facility will recycle both lead-acid and lithium-ion batteries found in automobiles, power storage, mobile phones, and laptops. While some battery recycling methods rely on fossil fuel-heavy smelting, recycling operations at ACE are entirely electric, reducing carbon emissions to zero. The company is also exploring solar energy for other plant activities.
Development of the facility will take place gradually. The expected start to phase one of operations will begin in the third quarter of 2023, leading with the recycling of lead-acid batteries. When operating at full capacity, ACE says the complex will process and recycle up to 100,000 metric tons of used lead-acid batteries and 20,000 metric tons of used lithium-ion batteries annually by 2025.
At full productivity, the facility intends to rid landfills of more than 10 million pounds of hazardous waste and recycle more than 15 million pounds of plastic annually. The recycling park will generate 100 Texas jobs.
Because of the lack of large-scale recycling plants in the U.S, the country relies on importing and exporting battery scraps and new battery materials. The plant intends to reduce dependence on foreign suppliers.
UPFRONT
LyondellBasell’s high pressure LDPE technology
ROTTERDAM, THE NETHERANDS — LyondellBasell (NYSE: LYB) recently announced that Zhejiang Petroleum & Chemical Co. Ltd. (ZPC) will license again the LyondellBasell high-pressure polyethylene technology at their facility located in Zhoushan City, Zhejiang Province, P.R. of China.
The Lupotech process technology will be used for both a 100 KTA Autoclave and a 300 kiloton per year (KTA) Tubular line. Both production trains will be producing mainly ethylene vinyl acetate copolymers (EVA). Furthermore, an additional 400 KTA Tubular line producing low-density polyethylene (LDPE) homo polymers will be built at the same site.
“We are excited that ZPC decided to grow their assets of licensed LyondellBasell polyolefin technologies with their latest award of our tubular Lupotech T and autoclave Lupotech A technology. In the near future, ZPC will produce in total more than 2,700 KTA polyolefins based on our process technology,” said Neil Nadalin, Director Global Licensing and Services at LyondellBasell. Nadalin added: “The latest additions will be dedicated to produce high value EVA and LDPE applications such as solar panel lamination and encapsulant enabling the global energy transition as well as the production of cost efficient homopolymer LDPE resins.“
Mr. Li Shuirong, Chairman of Zhejiang Petroleum & Chemical Co. Ltd., stated: “The selection of LyondellBasell’s Lupotech process technologies represents a win-win situation for both ZPC and LyondellBasell. These technologies allow us to not only expand our production capabilities, but also further improve the excellent performance and quality of our LDPE and EVA products.”
Decades of experience in high-pressure application design makes the Lupotech process the preferred technology for EVA/ LDPE plant operators. High reliability, unmatched conversion rates and effective process heat integration are key attributes of the Lupotech process, designed to ensure this technology’s on-going energy efficiency.
More than 14,000 KTA of LyondellBasell high pressure LDPE technology has been licensed by LyondellBasell in over 80 lines around the world.
New licensees take advantage of LyondellBasell’s in-house expertise of continuous production improvement, product development according to the latest environmental regulations, and our know-how in high pressure design, by optionally joining our Technical Service program.
In addition to the Lupotech T and Lupotech A process technology, the LyondellBasell licensing portfolio of polyolefin processes and catalysts includes:
Hostalen – Leading low-pressure slurry process for the production of high-performance multimodal high-density polyethylene (HDPE).
Spherilene – Flexible gas phase process technology for the production of linear low-density polyethylene (LLDPE), medium-density polyethylene (MDPE) and HDPE.
Spherizone – The breakthrough multi-zone circulating reactor provides a unique and innovative platform to manufacture polypropylene products with novel architecture and enhanced properties.
Spheripol – The leading polypropylene (PP) process technology with more than 30 million tons of licensed capacity. With globally recognized quality grades featuring leading monomer yield and investment costs to make it the technology of choice.
Metocene PP – Innovative add-on technology for the production of specialty polypropylene products using single-site catalyst systems.
Avant – Advanced Ziegler-Natta, including non-phthalate, chromium and metallocene catalysts for entire range of polyolefin production.
As a leader in the global chemical industry, LyondellBasell strives every day to be the safest, best operated and most valued company in our industry. The company’s products, materials and technologies are advancing sustainable solutions for food safety, access to clean water, healthcare and fuel efficiency in more than 100 international markets. LyondellBasell places high priority on diversity, equity and inclusion and is Advancing Good with an emphasis on our planet, the communities where we operate and our future workforce. The company takes great pride in its worldclass technology and customer focus. LyondellBasell has stepped up its circularity and climate ambitions and actions to address the global challenges of plastic waste and decarbonization. In 2022, LyondellBasell was named as one of FORTUNE Magazine’s “World’s Most Admired Companies” for the fifth consecutive year. For more information, please visit www.lyondellbasell.com or follow @LyondellBasell on LinkedIn.
UPFRONT
Tank Holding Acquires Semco Plastic Company, Inc.
Tank Holding, North America’s largest rotational molder, has acquired Missouri based blow and injection molder Semco Plastic Company, Inc. effective May 9, 2022. Semco manufactures a variety of high-volume custom and proprietary products serving the recreational, commercial, outdoor, engine and other industries. Products such as OEM fuel tanks, portable fuel containers, equipment components, refuse containers, backboards and more are designed, tooled, manufactured, assembled, packaged, and shipped utilizing turnkey solutions and services to a diverse customer base with the experience and capability to produce high quality molded products out of a single facility.
“The acquisition of Semco is consistent with our strategy to invest into adjacent plastic processing technologies while continuing to demonstrate our commitment to provide our customers further capabilities. We believe there is tremendous opportunity for us to utilize blow molding to expand our proprietary product offering while also complementing our commitment to custom molding. The addition of blow molding and injection molding capabilities to our vast rotational molding network provides us with the unique position to offer more plastic molding options to our valued customers. Semco, with its successful seventy-five-year history and continuous investment in equipment and capability, delivers the competency and scale we desired to enter into these complementary molding technologies,” said Greg Wade, CEO of Tank Holding.
The Semco acquisition provides synergy opportunities with Tank Holding’s core business along with several recent acquisitions, including six last year and Dutchland this year which were focused on custom molding and proprietary products. These market leading brands and multiple molding capabilities provide the industry with the broadest product portfolio and the largest footprint of manufacturing facilities.
“Semco has been in our family for four generations, and we have built a great business with great people. We’re proud of our significant investments in the business with modern technology and building expansions to keep up with growth and offer competitive value to our customers. The Semco announcement represents Tank Holding’s 19th acquisition in the past three years and further enhances the company’s penetration into custom molding .
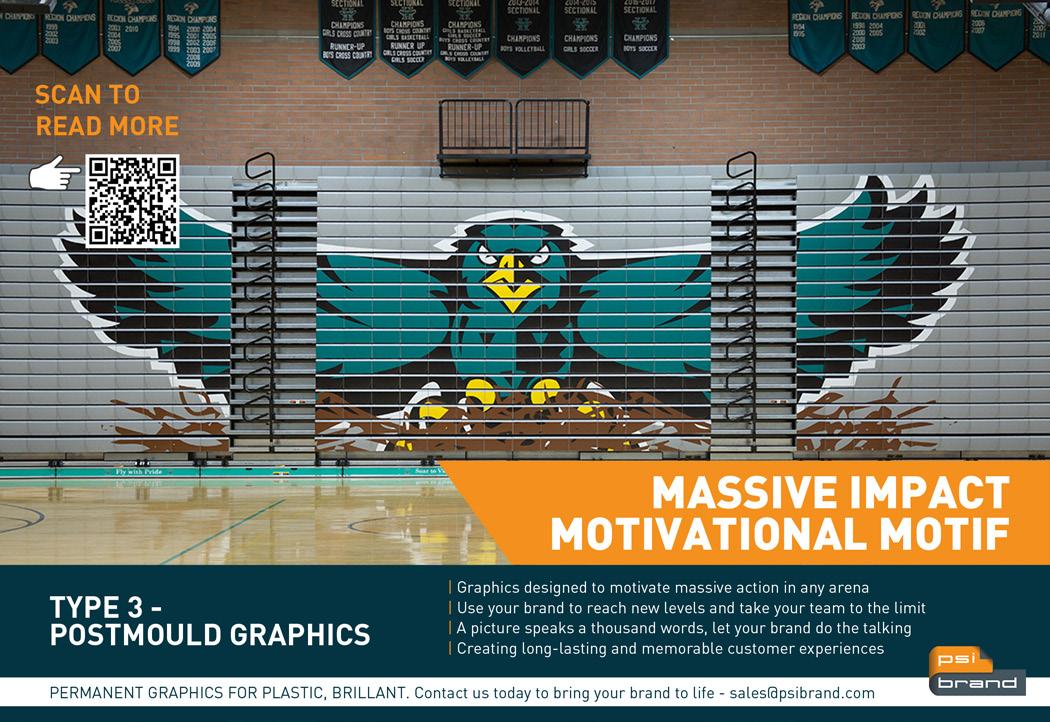
UPFRONT
US, Western Europe Fret over Uncertain Ukraine War Endgame
WASHINGTON, D.C. USA — An interminable and unwinnable war in Europe? That’s what NATO leaders fear and are bracing for as Russia’s war in Ukraine grinds into its third month with little sign of a decisive military victory for either side and no resolution in sight. The possibility of a stalemate is fueling concerns that Ukraine may remain a deadly European battlefield and a source of continental and global instability for months, or even years, to come. Energy and food security are the most immediate worries, but massive Western support for Ukraine while the world is still emerging from coronavirus pandemic and struggling to deal with the effects of climate change could deepen the toll on the global economy. And should Russia choose to escalate, the risk of a broader conflict rises.
The U.S. and its allies are pumping a steady stream of lethal weaponry into Ukraine to keep it in the fight. While most analysts say Kyiv is holding its own at the least, those infusions must continue if they are to support President Volodomyr Zelenskyy’s vow to win, or at least continue to match or beat back Moscow’s advances.
Just as Russian President Vladimir Putin has not signaled a willingness to intensify the invasion with either a general mobilization of troops or the use of unconventional arms, neither has he shown any sign of backing down. Nor has Zelenskyy, who is now asserting that Ukraine will not only beat back the current Russian invasion but regain control of Crimea and other areas that Russia has occupied or otherwise controlled since 2014.
“It’s very difficult to see how you could get a negotiated solution at this point,” said Ian Kelly, a retired veteran diplomat who served as U.S. ambassador to Georgia, another former Soviet republic on which Russia has territorial designs. He added, “Neither side is willing to stop fighting and probably the likeliest outcome is a war that lasts a couple of years. Ukraine would be a festering sore in the middle of Europe.”
“There’s no way that Ukraine is going to step back,” Kelly said. “They think they’re gonna win.” At the same time, Kelly said that
no matter how many miscalculations Putin has made about the strength and will of Ukraine to resist or the unity and resolve of the NATO allies, Putin cannot accept defeat or anything short of a scenario that he can claim has achieved success. “It would be political suicide for Putin to withdraw,” Kelly said. U.S. officials, starting with President Joe Biden, seem to agree, even after Defense Secretary Lloyd Austin raised eyebrows by saying after a visit to Kyiv last month that Washington’s goal is not only to help Ukraine defend itself but to “weaken” Russia to the point where it does not pose a threat. “Neither side is willing to stop fighting and probably the likeliest outcome is a war that lasts a couple of years.” Putin “doesn’t have a way out right now, and I’m trying to figure out what we do about that,” Biden said on Monday even after he signed legislation designed to reboot the World War II-era “lendlease” program and appealed to Congress to approve a $40 billion package of military and humanitarian aid for Ukraine. So, what to do? French President Emmanuel Macron has placed a premium on a negotiated settlement that saves face for both Russia and Ukraine. “We will have a peace to build tomorrow, let us never
UPFRONT
forget that” Macron said on Monday. “We will have to do this with Ukraine and Russia around the table. The end of the discussion and the negotiation will be set by Ukraine and Russia. But it will not be done in denial, nor in exclusion of each other, nor even in humiliation.”
U.S. officials aren’t so sure, although they allow that the endgame is up to Ukraine. “Our strategy is to see to it that Ukraine emerges from this victorious,” State Department spokesman Ned Price said recently. “Ukraine will do so at the negotiating table. Our goal is to strengthen Ukraine’s position at that negotiating table as we continue to place mounting costs on the Russian Federation.”
But the high-stakes uncertainty over what constitutes a “victorious” Ukraine has alarmed officials in some European capitals, notably those in the Baltic states of Estonia, Latvia, and Lithuania, which are NATO members bordering Russia and especially worried about Moscow’s possible future intentions.
For Baltic nations and other countries on NATO’s eastern flank, the threat is real, and memories of Soviet occupation and rule remain fresh. Concessions to Russia in Ukraine will only embolden Putin to push further west, they say.
“To be honest, we are still not talking about the endgame,” Lithuanian Foreign Minister Gabrielius Landsbergis lamented to the Associated Press in a recent interview. He said any territorial concessions in Ukraine would usher in a world where the “rulesbased order” has been replaced by a “jungle rules-based order.”
Landsbergis suggested that Western nations issue public statements about what success would be. “Where we would consider what we would take for victory, actual victory? What would be the scenario that we would like?”
Landsbergis has been outspoken in calls for Putin to be ousted as Russia’s leader, going well beyond the U.S. position and that of other NATO leaders. He says regime change in Moscow is the only way to protect European and Western security in the long term.
“Coming from me it’s much easier to say we need regime change in Russia, so we’ve been quite blunt and open about it,” he said. “Maybe for United States it’s much more much more difficult to be open about it, but still, at some point we have to talk about this because it’s so important.”
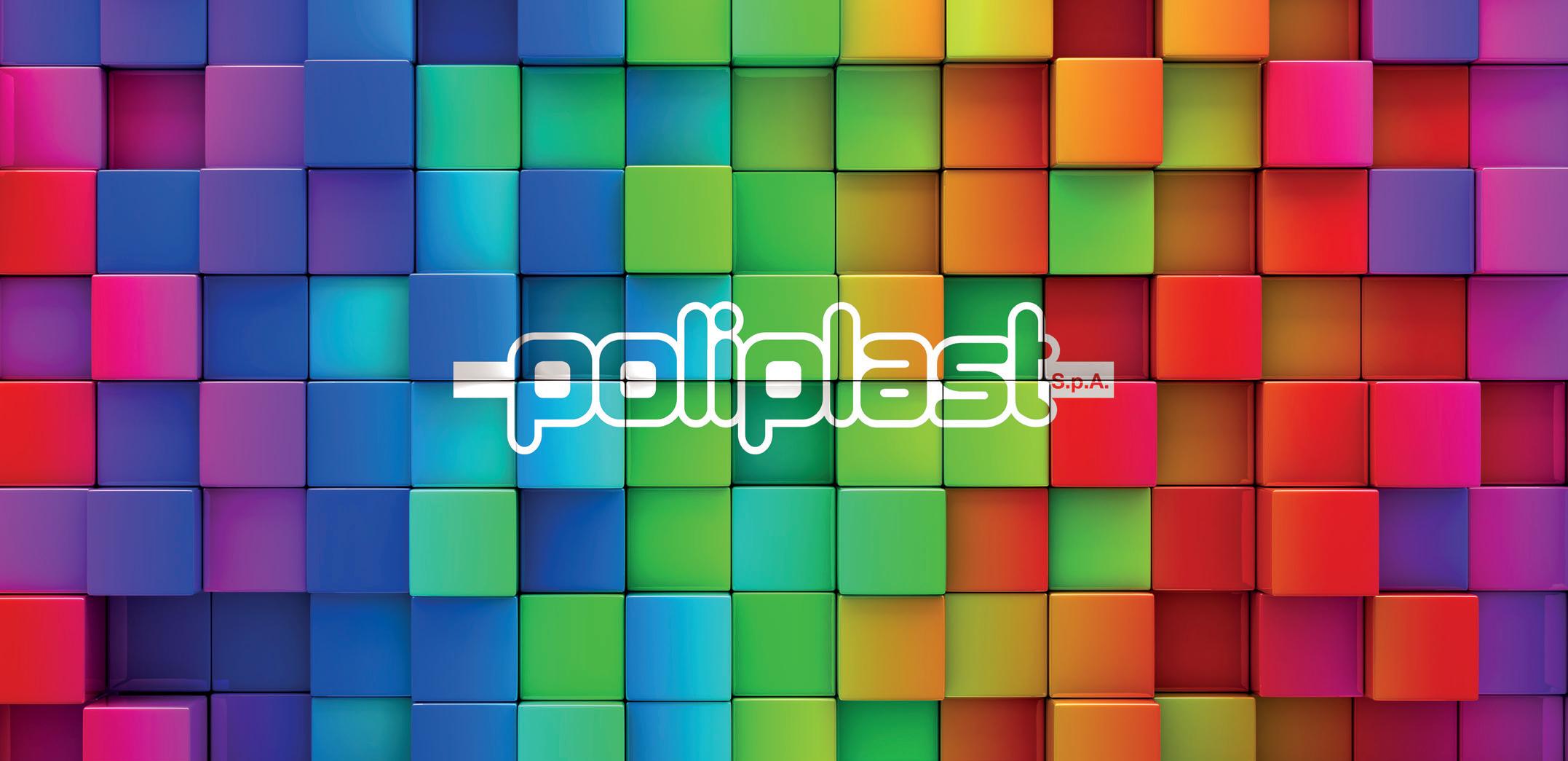
UPFRONT
Smartbar sets the Standard for Site Safety
ADALAIDE, AUSTRALIA — Australian born and bred, SmartBar has been making and designing its leading bull bar technology at its home in Adelaide since 1996.
These bull bars are far from average, boasting an innovative, lightweight, and resilient design that increases safety for the vehicle and, just as crucially, for pedestrians.
SmartBar bull bars are manufactured from flexible, durable polyethylene material, rather than metal, giving them the ability to absorb impact and then spring back to their original shape.
“The absorption of the impact makes our product a lot safer for pedestrians. Rather than hitting a solid object, our product absorbs some of the force in an impact,” SmartBar sales and development manager Kieran Jenkins said.
“It’s a rotationally moulded hollow section bar, so the material properties and the hollow nature of the product is what allows the bull bar to compress and absorb the impact.”
Each of the bull bars undergoes rigorous testing to ensure the quality and safety is above and beyond, covering compulsory, and non-compulsory testing requirements of Australian Safety Standard AS4876.1-2002.
When the Centre of Automotive and Safety Research conducted tests to measure head trauma and accident survival probability of a person at certain speeds, a SmartBar bull bar outperformed all other frontal vehicle protection systems available.
In a simulated collision with a pedestrian at 30km/h, it was proven that in many cases a vehicle fitted with a SmartBar bull bar was less likely to cause a fatal injury through impact than the original front-vehicle assembly.
What sets a SmartBar bull bar apart is that it acts as an injuryprevention and cushioning device in a slow-speed collision, such as with a pedestrian, reducing the likelihood of serious injury.
Factors such as vehicle design, crush rate, airbag deployment, approach angles, accessory fitment, strength, weight, and aesthetic are all taken into consideration during the development of every SmartBar bull bar.
“In terms of mining, the other benefits of our products are they’re lightweight so you can help to minimise the weight of the vehicle, and the polyethylene material is great for corrosion resistance as well,” Jenkins said.
SmartBar also offers rear protection, which is vital on a mine site, especially when manoeuvring in close confines.
The rear protection bar provides the same vehicle, occupant, and pedestrian safety as the rest of the SmartBar range, and is manufactured from the same flexible, durable polyethylene material. It provides unparalleled levels of vehicle and occupant protection without compromising pedestrian safety.
“The rear protection bars have the same absorbing properties to again provide vehicle protection at the rear and can be used as a step for access to roof racks,” Jenkins said.
“The under-vehicle armour is also lightweight and has great corrosion resistance, so that’s going to protect the car from rocks and impacts from underneath when you’re driving over uneven ground common on mine sites.”
The bull bars are also available in Hi-Vis Orange for increased on-site safety, while rear protection bars are available in Hi-Vis Yellow.
“Pedestrian safety has been a big focus of ours right from the start, not only in mining but across all industries in general,” Jenkins said.
With an array of light vehicles travelling across a mine site all day, ensuring pedestrian safety is crucial. And when it comes to safety, SmartBar is in a league of its own.
“Pedestrian safety has been a big focus of ours right from the start, not only in mining but across all industries in general,” Jenkins said.
— Kieran Jenkins
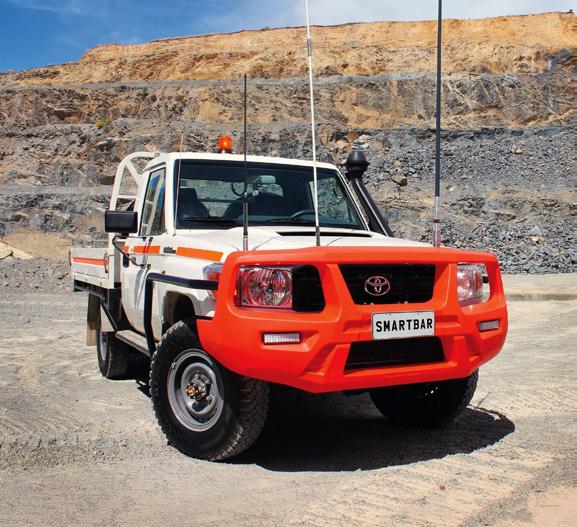
UPFRONT
Tank Holding Consolidates Refuse Brands
Tank Holding, North America’s largest rotational molder, has consolidated and rebranded all the company’s refuse container brands into one brand, Snyder Refuse. This will be conveyed on all related products and marketing communications.
The consolidation brings the recently acquired brands of WRP Containers, RMI, Duracast, and RMU brands together under one brand with 7 FOB shipping points. “Snyder Refuse product offerings provide the industry with the broadest product portfolio and the largest plastic refuse container manufacturing footprint in the industry,” said Sean Barber, director of sales and marketing for Tank Holding’s refuse product segment. “The consolidated brand also aligns both commercial and residential product lines into one integrated platform to more efficiently respond to customer needs nationally,” Barber continued.
The Snyder Refuse product portfolio includes Front Load, Side Load, and Rear Load commercial dumpsters ranging in size from 2 cubic yards to 8 cubic yards, receptacles, and liners. The Residential offerings include Round Cans ranging in size from 200 gallon to 450 gallon, and Roll Out Carts in the 40-to-100gallon range.
Snyder Refuse is a brand of Tank Holding, which also manufactures a wide variety of proprietary plastic products, like bulk storage tanks, intermediate bulk containers, laundry and linen carts, insulated material handling bins, food handling containers, and hoppers as well as a broad range of custom products. Tank Holding products are marketed through a number of industry leading brands like Norwesco, Snyder Industries, Bonar Plastics, Bushman, Chem-tainer, Meese, and Stratis Pallets. The company is owned by Olympus Partners and the management team. Tank Holding currently operates over 40 manufacturing plant locations and employs over 1500 people throughout North America..
ROTOLOAD™ powder weighing & dispensing systems
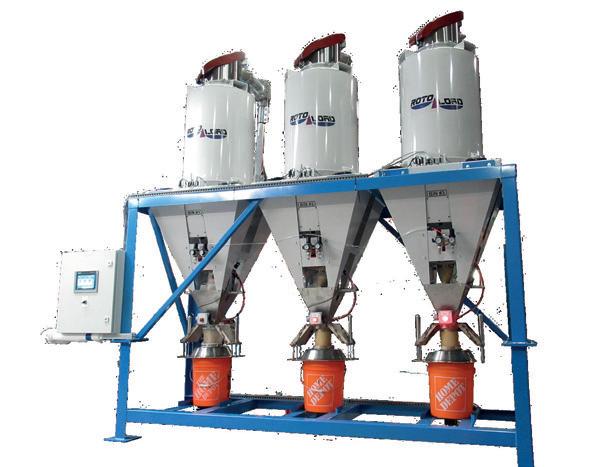
» ROTOLOAD™ is the ONLY solution to ALL of your powder resin handling needs. » ROTOLOAD™ is the ONLY comprehensive line of powder resin conveying and weighing equipment, specifically designed to meet the demands of the Rotational Molding Industry. » ROTOLOAD™ uses vacuum to load your material, hold it above your process machine, and dispense, quickly and accurately. In addition it is the ONLY solution to the question of how to reduce under and overweight parts, mess, downtime and resin loss.

Manufactured by Wittmann Battenfeld Canada Inc.: 35 Leek Crescent | Richmond Hill, ON L4B 4C2
2022 ARM Executive Forum
Omni Amelia Island - Florida
Susan Gibson, JSJ Productions, Inc.
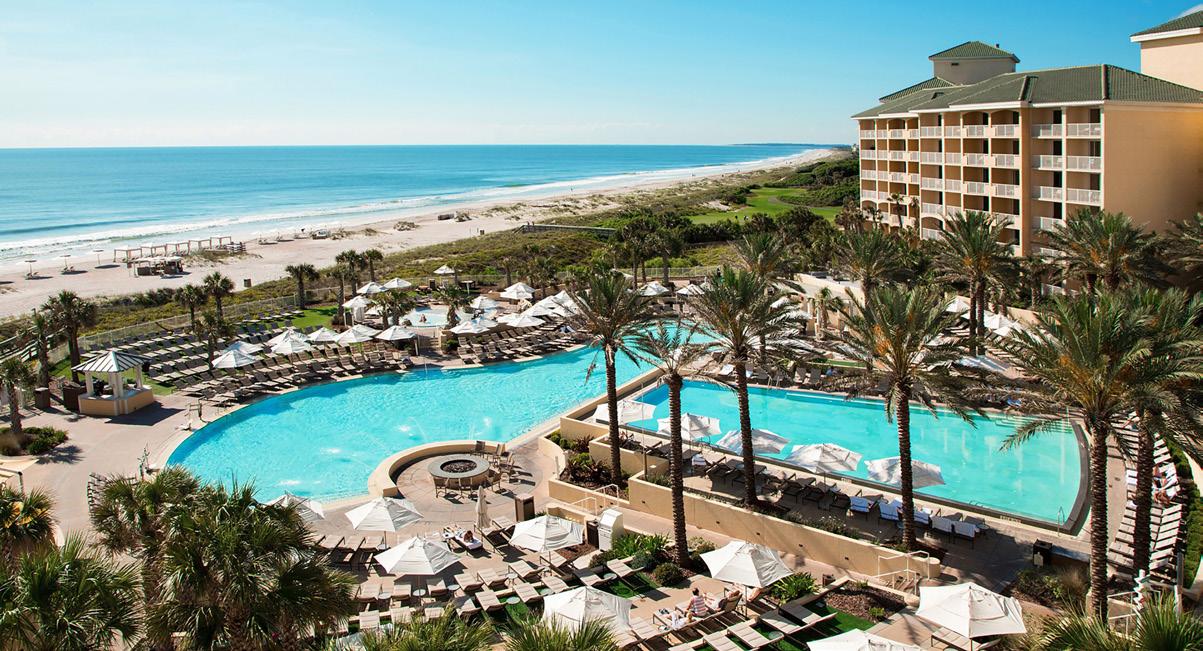

Matt Bushmann (Plasticraft Corporation) Darcy Bien (Stretch Strategic Leaders) Daven Claerbout (Dutchland Plastics)
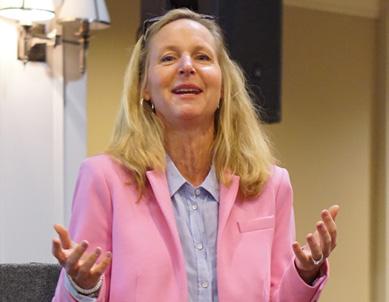
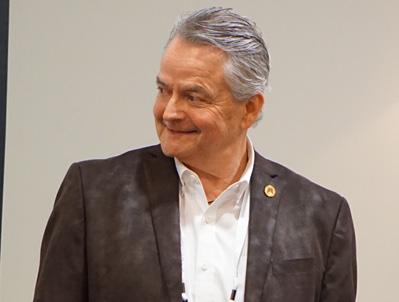
The ARM Executive Forum is held each spring, bringing together industry executives to learn, share ideas, and network. This year’s in-person Forum took place March 14-16 at the Omni Amelia Island in Florida. The event drew ninety-some molders and suppliers from across North American and several foreign countries.
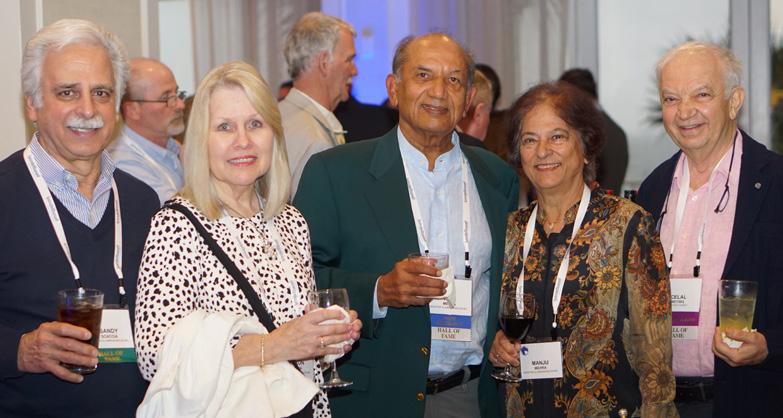
Sandy and Sharon Scaccia (Nortar Aluminum Molds), Ravi and Manju Mehra (Norstar International), and Celal Beysel (Floteks Turkey) Chris Lefas (Orenda Automation Technologies)
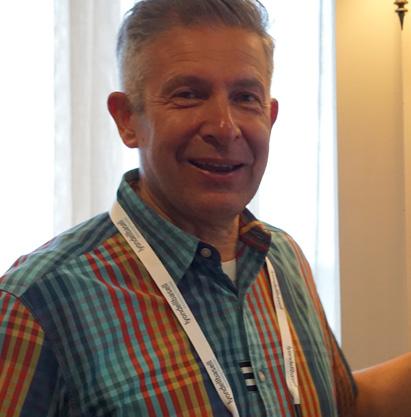
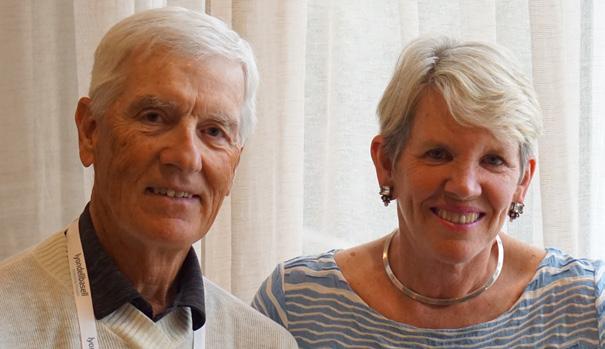
Peter and Doren Connors (Remcon Plastics) Steve Copeland and Brandi Frey (Jerico Plastic Industries)

Networking was at its best on the first day as attendees discussed potential ideas for investing ARM funds for the future good of the association and industry. Led by Matt Bushman and Daven Claerbout, many worthy ideas were generated from the basics of promoting rotational molding, the production of an animated video around the concept of “Pellet to Part”, to creating software for balancing molds, just to name a few.
On the second day, the education program kicked off with a special presentation on “Growth Oriented Strategic Planning” by Darcy Bien of Stretch Strategic Leaders.
Bien presented a 10-step strategy that began with first completing a strategic planning process assessment. Then working through training processes, planning, implementation, and expansion.
“In order to strategically plan, you must really understand your customer,” Bien said. She advocated boiling the company’s Strategic Plan down to a one-page flyer and making it readily accessible to the leadership and employees.
Bien encouraged the executives to ask themselves such questions as: what is your purpose; what are you core values; what differentiates your company from others; what is your vision; who do you serve; and why you? She said you must have a reason to believe. 67% of all companies fail in strategy according to Bien. They monitor P&Ls, but they fail to monitor a strategic plan, which lays out their growth plan.
Bien reported the number of companies that reach $1MM in revenue is .4%; the number that reach $10MM is 4%. She said when a company reaches $10MM in annual revenue, they will need a second in command. When a company is in the $10$40MM revenue arena, it ceases to be a small business. Her recommendation is to not consider selling a business unless it is worth at least $10MM.
Len Dunman, Mercer Transportation, drew on his 40+ years’ experience and addressed the issues and challenges facing transportation logistics. “Transportation is spouting challenges faster than a volcano,” Dunman said. Some of the biggest challenges they are seeing today are with drivers and equipment. “We have an acute driver shortage, and this is due mostly to the fact that the typical driver population is older. The job requires
living on a truck 2/3 weeks a month, pay issues, etc. “There is a maturing level for drivers, and we are experiencing that right now,” Dunman said. The same aging issue applies to equipment. Trained mechanics are getting older and younger people are not entering this field. This is causing fewer and fewer trained mechanics in the workforce.
“The certainty of future autonomous trucks and the high costs that will bring is presenting a big challenge to the logistics industry,” Dunman said. The effect of social unrest in many urban areas causing drivers to have to be armed, along with government issues to contend with, not the least of which is high fuel costs, are also among the challenges faced.
Plasticraft CEO Bob Fettig, spoke about a medical service business in which he is involved and owns five facilities. Called “The Doctor’s Office”, the model provides an alternative way to get medical attention and services without all the bureaucracy and insurance issues associated with the traditional model. “The Doctor’s Office is a model with quality care at a fair price,” Fettig said. It offers physicians a new way to practice medicine and a value-add benefit to the patients that use them.
Jonathan Grau and Jen Cox of the National Council for Mental Wellbeing addressed the timely issue of mental health in the workplace. “The landscape for this issue has been very challenging over the past two years,” Grau stated. “There is a stigma around mental health issues and how we approach each other, which in turn affects our entire organizations,” he added. Since the outbreak of COVID, employees have been dealing with anxiety, depression, and substance abuse. The two advised on what to look for and how to get employees the help they need.
“Safety is a top priority, and when an employee is challenged with mental health issues, they are at odds between safety and productivity. Long hours, high stress, and scheduling can be physically demanding. They can have a decreased sense of purpose, meaning, and self-actualization,” Cox said.
Grau and Cox shared that the statistics in the manufacturing industry indicate a high alert: 1/10 are reporting a substance abuse issue; suicide rates are twice as high as in the general population; and 27% of the manufacturing workforce think work and life are out of balance. “We all have stress, and stress isn’t always bad. It is when it gets overwhelming that we need to adjust,” Cox said. “If you ignore the whispers, you may hear the screams.”
Professional HR executives Rhonda Griffin (Centro Incorporated), Bonnie Taylor (Myers Industries), and Paula Orcutt (Dura Cast Products, Inc.), discussed trending HR issues in the workplace. All agreed many companies are having to be creative and use never thought of before plans to recruit and retain employees.
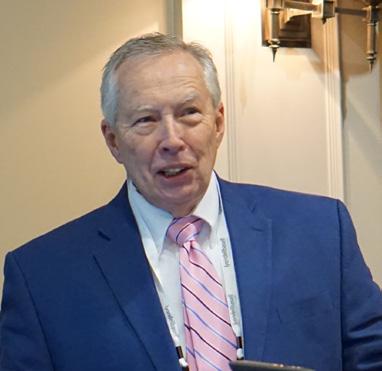
Len Dunman (Mercer Transportation) Bob Fettig (Plasticraft Corporation) Jen Cox (National Council for Mental Wellbeing)

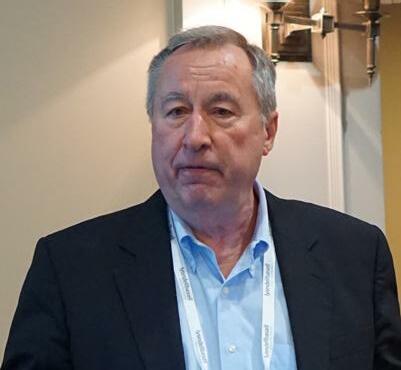

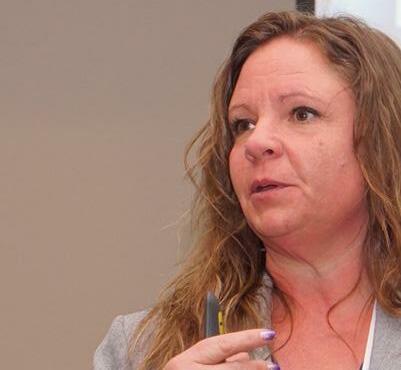
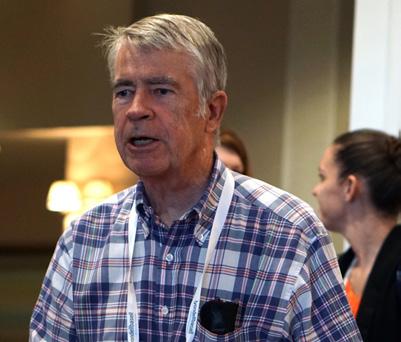
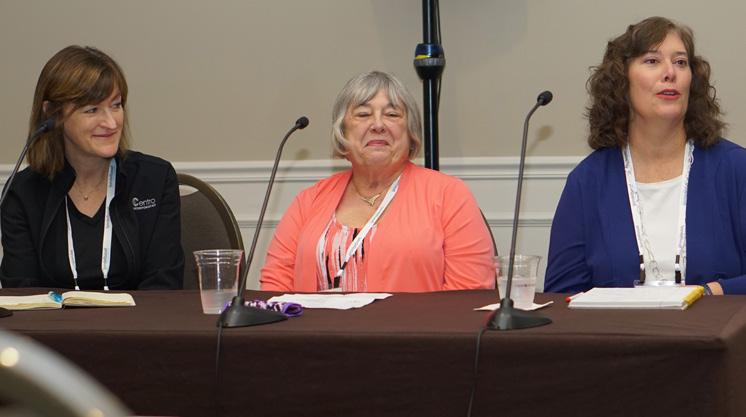
Rhonda Griffin (Centro Inc.), Bonnie Turner (Myers Industries), and Paula Orcutt (Dura-Cast Products Inc.) ARM Executive Forum attendees
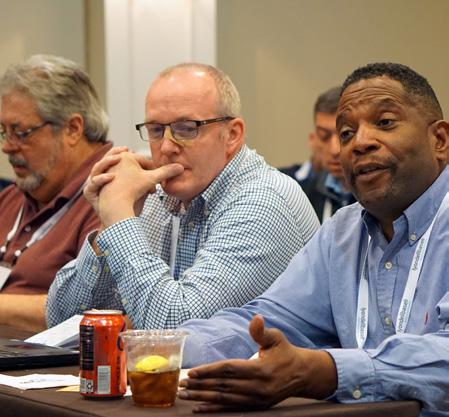
Orcutt shared the results of an industry survey she conducted as part of getting her doctorate in HR. Her 30-question survey drew comments from a number of respondents, 80% of which were male, 20% female, and 4% were under 20 years of age. Of the ranking issues, company culture was top of the list.
Turner addressed recruiting and retention and some of the things Myers is doing to hire new and keep existing employees. One is working with the Center for the Homeless in their area where they pick up enough people to cover all their shifts. They offer such plans as weekend shifts and working 36 hours and getting paid for 40. Turner suggested asking employees, “What are 3 things you like best about your job, and what are 3 you would change”? Then go to work to ensure the top three things are strong and then address the three things they would change.
Wayne Wiid, Pioneer Plastics of South Africa, and Jon Smalley, SmaK Plastics, talked about scheduling efficiencies. Wiid introduced a system his company employs, the MMS Manufacturing System. Wiid shared that Pioneer produces a large number of custom parts per month (23-30,000) and they heavily rely on this system. The system is integrated from the start of a product all the way through to accounting, billing, and shipping of that product. Each product is issued a bar code that keeps track of it all through the process. Sales personnel can track every step of the production process.
Smalley presented a system his company utilizes – RotoEdge. RotoEdge is web-based and works well for multiple plants. The system has just been moved to an Amazon web service to further eliminate employee mistakes and the chaos that creates. RotoEdge was designed to take chaos out of the process and keep production moving efficiently. “This is a stand-alone software, each machine has a touch screen, and all is tied to a main database,” he said.
Steve O’Brian of Shiftboard, talked about ways workforce flexibility can combat labor shortages. “It has always been challenging to align the workforce with the work at hand,” O’Brian said. But then add the pandemic and you’ve further complicated an already tedious process.”
O’Brien said manufacturers have lots of business, but also lots of supply chain and labor issues. Manufacturing ranks highest of any industry sector for these issues, and these challenges will remain challenges for the foreseeable future. 25% of the manufacturing labor force is 55 years of age or older. The workforce is aging, and many females have left the workforce altogether. Younger employees don’t think like the older employees do. They place more value on purpose…“how does what I do matter”.
Workforce flexibility is a common challenge. Manufacturers will face stoppages, inability to fill positions, lots of unplanned overtime, shift changes, etc. The way to change this, according to O’Brian is to plan ahead. Plan ahead now for how future orders will be handled. Ask what will you need to produce the product and what staffing will be required?
In addition to the stellar educational program, attendees were given opportunities to enjoy the area with social outings including an art class, a not quite 5K Run, Fort Clinch Bike Tour, Golf Tournament, and a Kayak Tour.
A big thank you to the 2022 ARM Executive Forum Sponsors which included: Roto Polymers, Jerico Plastic Industries, NOVA Chemicals, LyondellBasell Industries, Muehlstein-Channel Prime Alliance, and Quantum Polymers, Inc.
Save the date for 2022 ARM Fall Conference, which will take place November 6-9 in Atlanta, Georgia.
— Bonnie Turner, Myers Industries