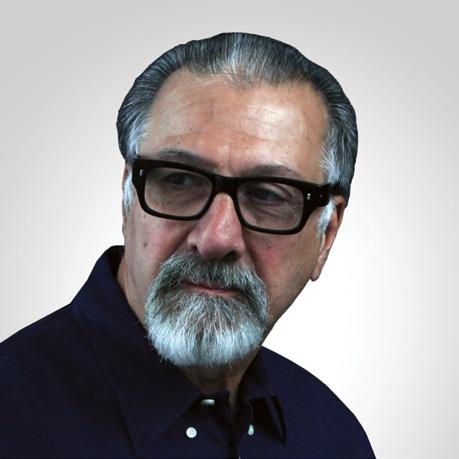
2 minute read
Design Comment
DESIGN
COMMENT
Michael Paloian, Integrated Design Systems, Inc.
What Design Guideline would Benefit Rotational Molders and Designers the Most?
The answer to the title question is reasonable tolerance guidelines. Our industry has approved and accepted guidelines for tolerances which are summarized below:
Most rotational molders recommend the ideal tolerance range of +/-.02in/in. This variation may be acceptable for molding a water trough for farm animals or a simple one-piece tank, but that’s about all you can reliably design. Don’t even think of designing anything that must fit or mate to another part.
Let’s examine what this variation really means by applying some numbers to the tolerance. Assume you want to design a large 3-foot long by 2-foot-wide commercial ice chest with a hinged lid that must seal all around with a tight-fitting rubber gasket. You must now be prepared to accept the possibility that the main case could be approximately 3/4“oversized and the top cover could be 3/4 “undersized resulting in a potential 1- 1/2“ mismatch. The ¾” is based on 3 feet long x 12”/ft x .02in/in = .72”. Although this is based on industry-standard tolerances, it is readily apparent that this would not be an acceptable or functional product. No designer could accept these ridiculous tolerance variations for such a product as well. Based on this simple example, one might ask how complex, intricate, and highly functional rotational molded parts are manufactured. The answer to the question is obvious, molders are maintaining much tighter tolerances than those accepted as industry standards.
Let us now examine some of the parameters affecting tolerance variation. • Material shrinkage – Tool makers must account for material shrinkage by designing the mold a certain percentage larger than the actual molded part. Polyethylene resins shrinkage ranges from 1.5% to 2.5%. The actual shrinkage depends on the type of polyethylene as well as the molecular weight. • Part geometry & design – Part geometry and design will have a significant impact on tolerances. For example, parts such as a double-walled cooler chest will shrink much less a hollow container or tank because the core of the former will restrict shrinkage. Therefore, if a uniform shrinkage is applied to the entire part, the overall final exterior dimensions could very likely be greater than expected. • Tool design – Tool design will also affect shrinkage. The addition of heatsinks, wall thickness, etc. will affect heat transfer into the part and affect shrinkage which affects tolerances. • Tooling fabrication method – Rotational molds can be created in aluminum sheet metal, steel sheet metal, cast aluminum, or
CNC machined aluminum. Tolerances will be highly dependent on the construction method and materials. • Processing parameters – Rates of heating and cooling will also affect shrinkage, tolerances, and distortion. • Craftsmanship – Accuracy during machining of patterns or
CNC machining will add to the tolerance buildup. • Pigments – it is a known fact that pigments affect shrinkage and tolerances. Different pigments will affect alter the shrinkage rate of polyethylene.
So, what can the industry do? I believe it would be a worthwhile investment to attempt to quantify these parameters with the goal of reducing the tolerance span to more realistic ranges. It will require research, money, and time. Many of the parameters I cited can be readily quantified, but others will require research. It would be an ideal project for a university that would move the industry into the next phase of expansion and growth.
POLYETHYLENE
Ideal
Commercial
Precision
PLUS/MINUS
0.02”
0.01”
0.005”
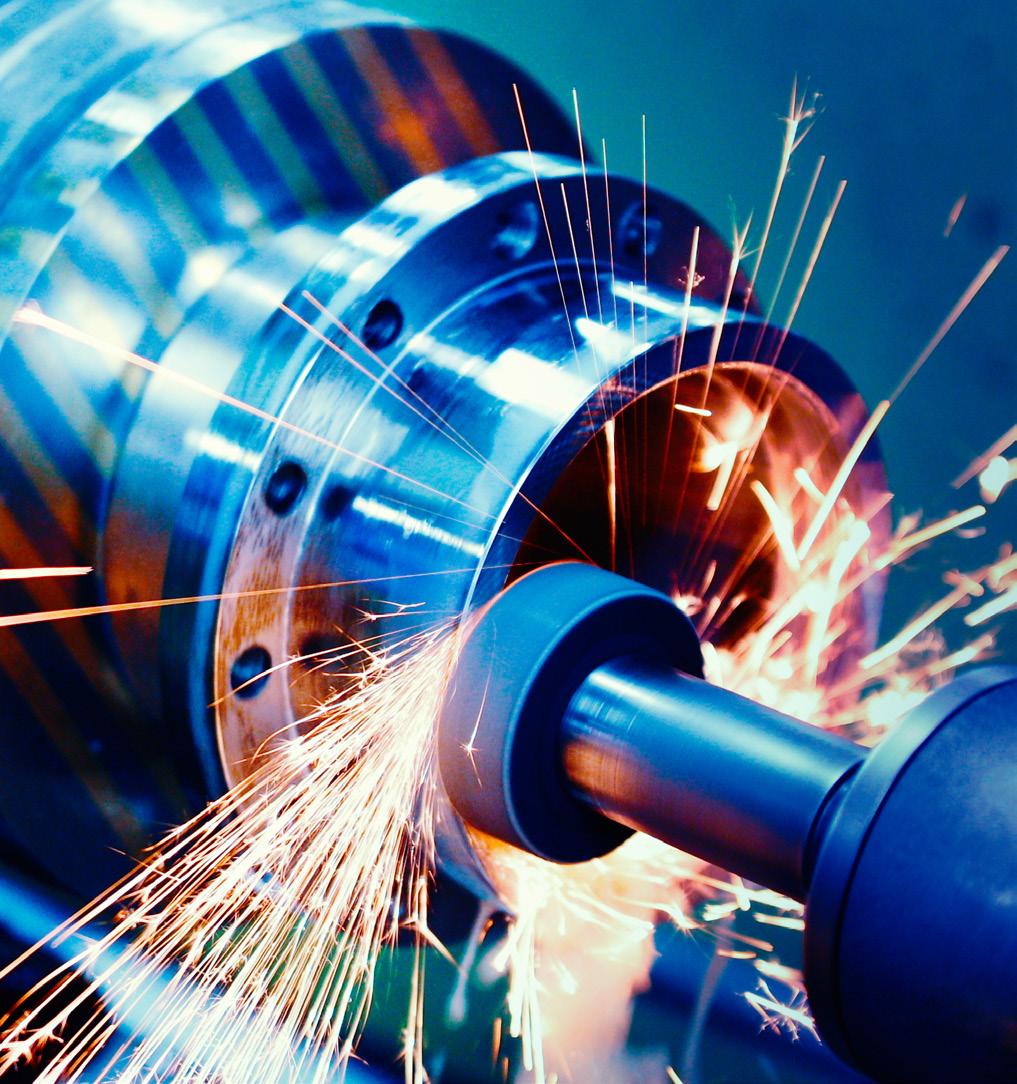