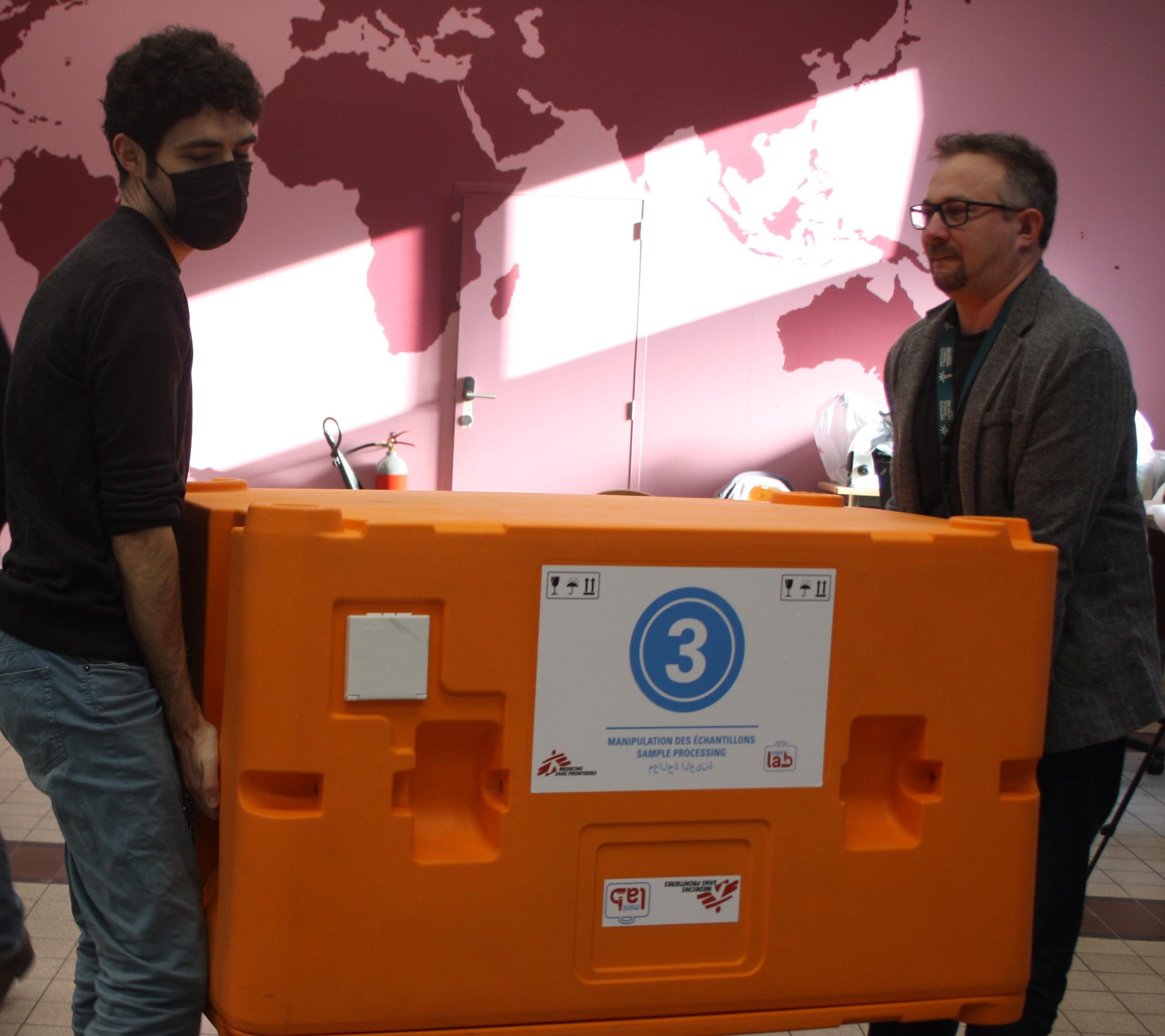
4 minute read
Roto Around the World
Ian Hansen, RotaConsult
DOCTORS WITHOUT BORDERS UTILIZE ROTOMOULDED MINI-LAB TO IMPROVE PATIENT CARE
Figure 1: Verification the container can be lifted by 2 people, inclusive of all necessary equipment.
Doctors Without Borders/Médecins Sans Frontières (MSF) is an independent medical humanitarian organization which originated in France and provides emergency medical assistance to people in extreme circumstances around the world. Their main areas of work include trauma surgery, pediatrics, malnutrition, infections, tropical and neglected diseases, vaccines, and COVID.
MSF work in many low- to middle-income countries, and by doing so identified problems in undertaking bacteriological diagnosis. They were not able to find a suitable self-contained clinical microbiology laboratory solution on the market. Thus, they developed the Mini-Lab in an attempt to provide affordable, standardized, high-quality clinical bacteriology in remote,
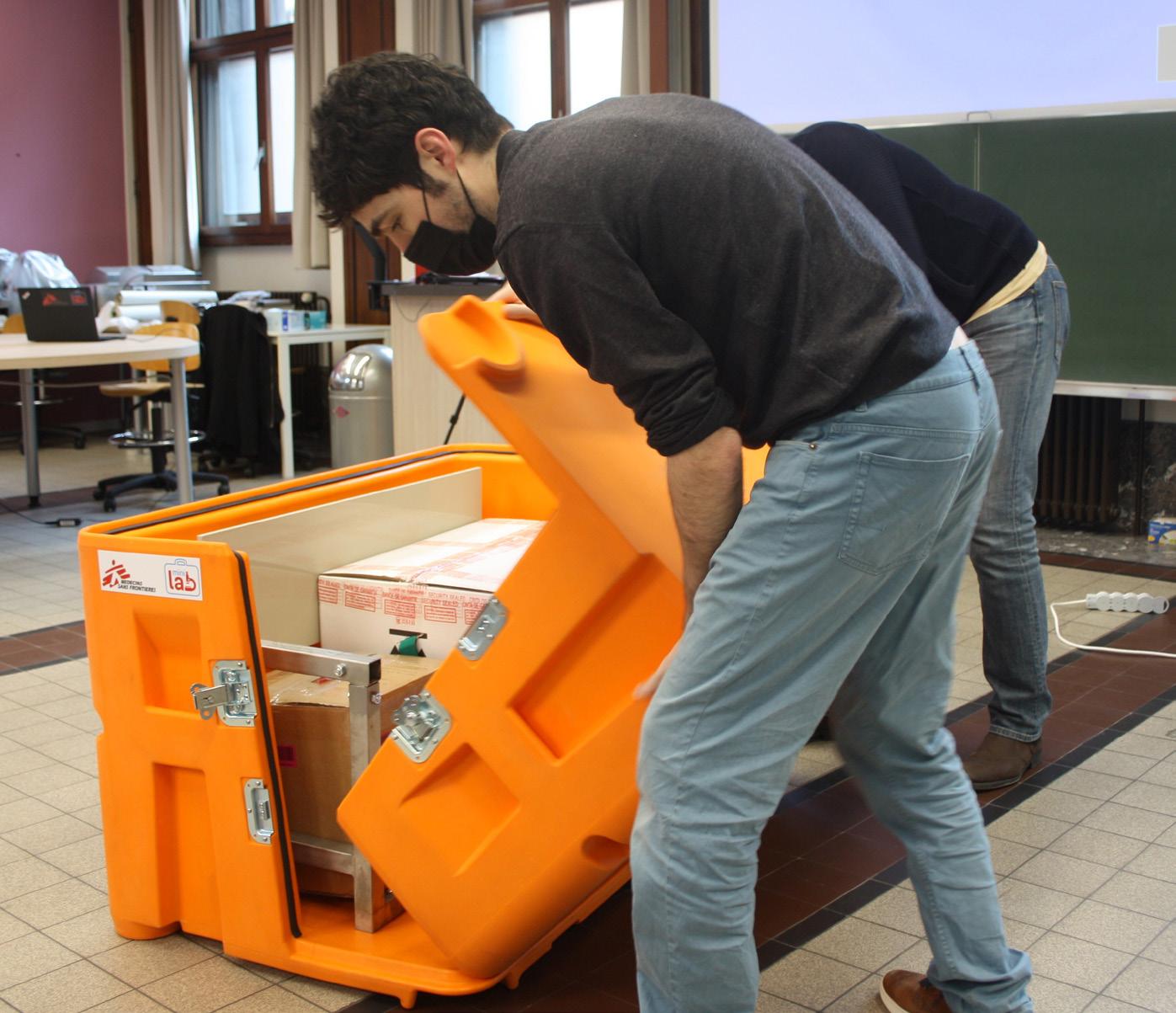
Figure 2: Container being unpacked.
challenging, and low resource locations. It is capable of being deployed rapidly around the world, and upon arrival, is easily used by non-expert microbiologists after brief training. If medical staff in the field have the ability to diagnose a patient accurately, they are better able to treat an infection.
All Mini-Lab components are transported in 6 protective containers, which hold all necessary equipment, furniture, metal frame, shelves, data management systems, training, documentation, and consumables. The boxes transform into sturdy laboratory benches which can set up a clinical bacteriology laboratories in in an area less than 20 m2 (215 ft2).
Container-benches include standard personal protective equipment and all electrical components to provide safe electricity connections. Deployment and installation instructions are designed in an ‘IKEA style’ document aimed at lay users. The Mini-Lab’s goal is to be deployed to improve patient care.
The original transportable, modular prototype containers were evaluated in the field during 2019-2021. They were first manufactured using wood panels, then fiberglass (FRP), however, the containers are now being manufactured in polyethylene by rotational moulding.
MSF engaged Philippe Vigouroux of ID Roto Solution, (www. idrotosolution.fr) an independent design company located in France, to create an industrial solution based on the knowledge and experience gained working with the prototype containers.
The early wooden containers were low cost to make, easy to customize, and required no tooling investment, however they were too heavy, requiring 4 people to carry each one. The FRP containers were lightweight and required low mould investment. Container customisation was possible, however, impact resistance was low during transport and the unit cost price was high.
The rotomoulding solution was chosen because it had good impact resistance and enabled one container design to offer different solutions. It was a compromise choice (or midway) between cost and weight compared to the alternative wooden and FRP solutions.
One Mini-Lab system requires 6 containers. The 6 containers require 12 rotomoulded pieces. The mould design was complex requiring moulds made from up to 5 pieces. ID Roto Solution worked closely with Italian mould maker Persico (www.persico.com) to transform their computer design into a CNC aluminium mould. A French based company, Rototec,
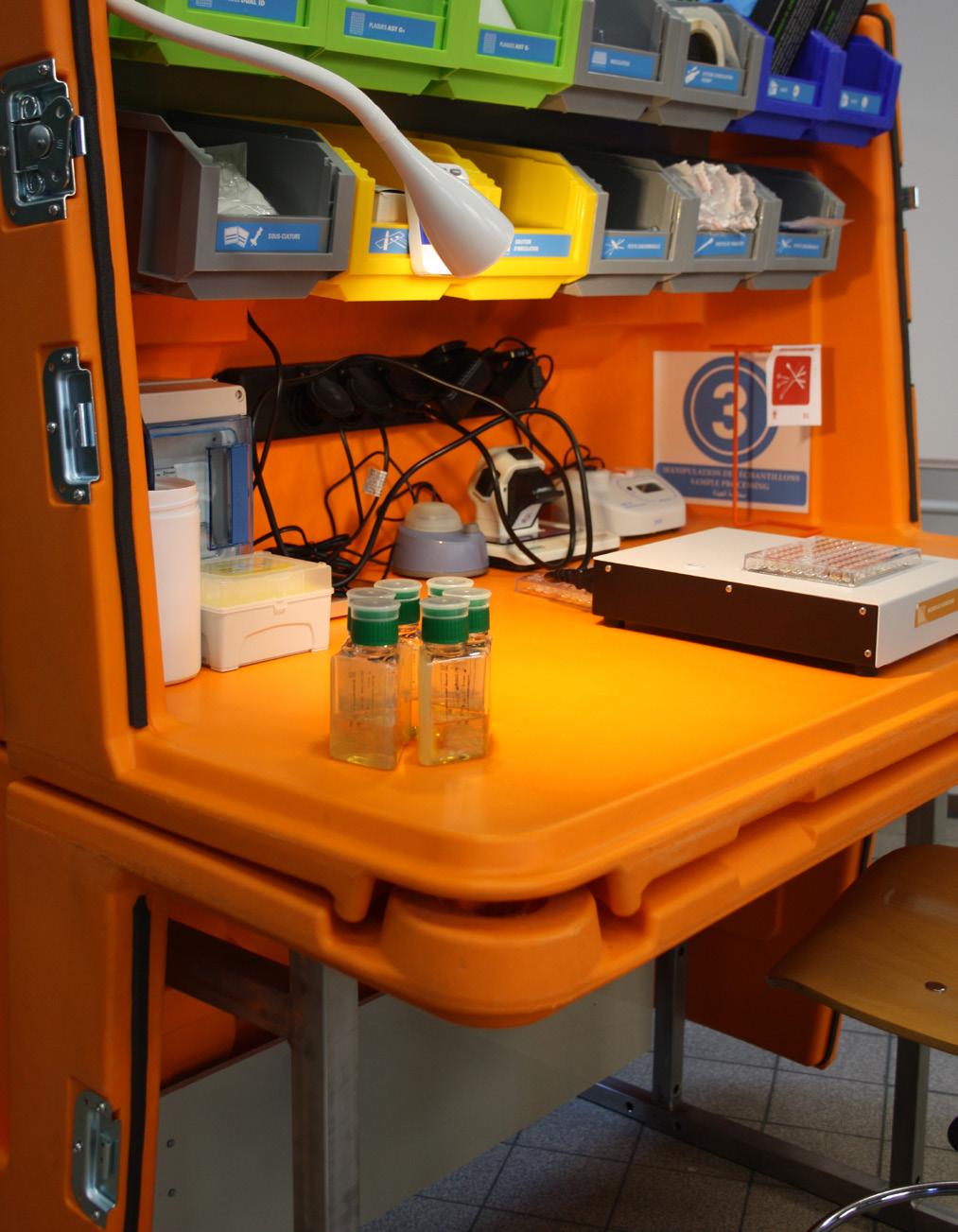
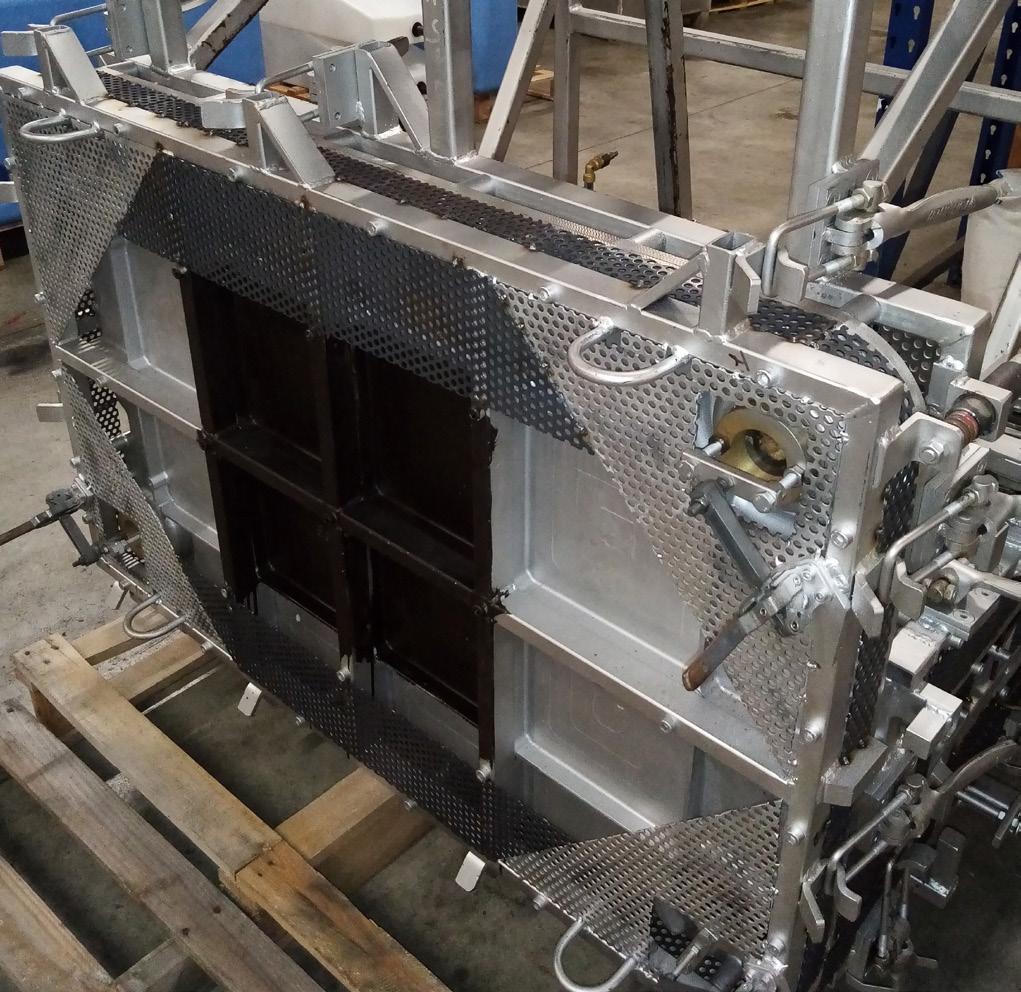
Figure 4: One of the aluminium moulds.
who specializes in the rotomoulding of technical parts was engaged by MSF to manufacture the prototype plastic parts. Based on the MSF’s designs and specifications, ID Roto Solution came up with the requirement to make the parts using a One Shot polyethylene foam system. When the containers are unfolded and used as work benches for microbiology, the internal work surfaces had to be flat. One Shot foam was the most cost effective material solution. A polyurethane foam solution was considered, but this would have significantly increased the amount of investment required for the project, for minor benefit.
After the moulds arrived from Persico, a little fine tuning and mould optimisation work was carried out by Rototec to ensure that the final product met the quality requirements of MSF.
As ID Roto Solution had expected, the product design, with the use of optimum materials, was able to meet all the key requirements for this application, namely medium weight, high mechanical resistance, flat surfaces when used as a work bench, good chemical resistance, and a lower price than the fiberglass/ polyurethane foam alternative.
MSF spent years of engagement, creativity, and persistence developing the Mini-Lab solution. Once they identified their requirements they engaged a professional design company to translate their prototype containers into an industrial solution.
ID Roto Solution was able to demonstrate to MSF the possibilities of innovative rotational moulding technology and as a result the first rotomoulded Mini-Labs are scheduled to be deployed to remote locations from mid-2022.
References: Fig 1, 2, 3 & 5 Médecins Sans Frontières
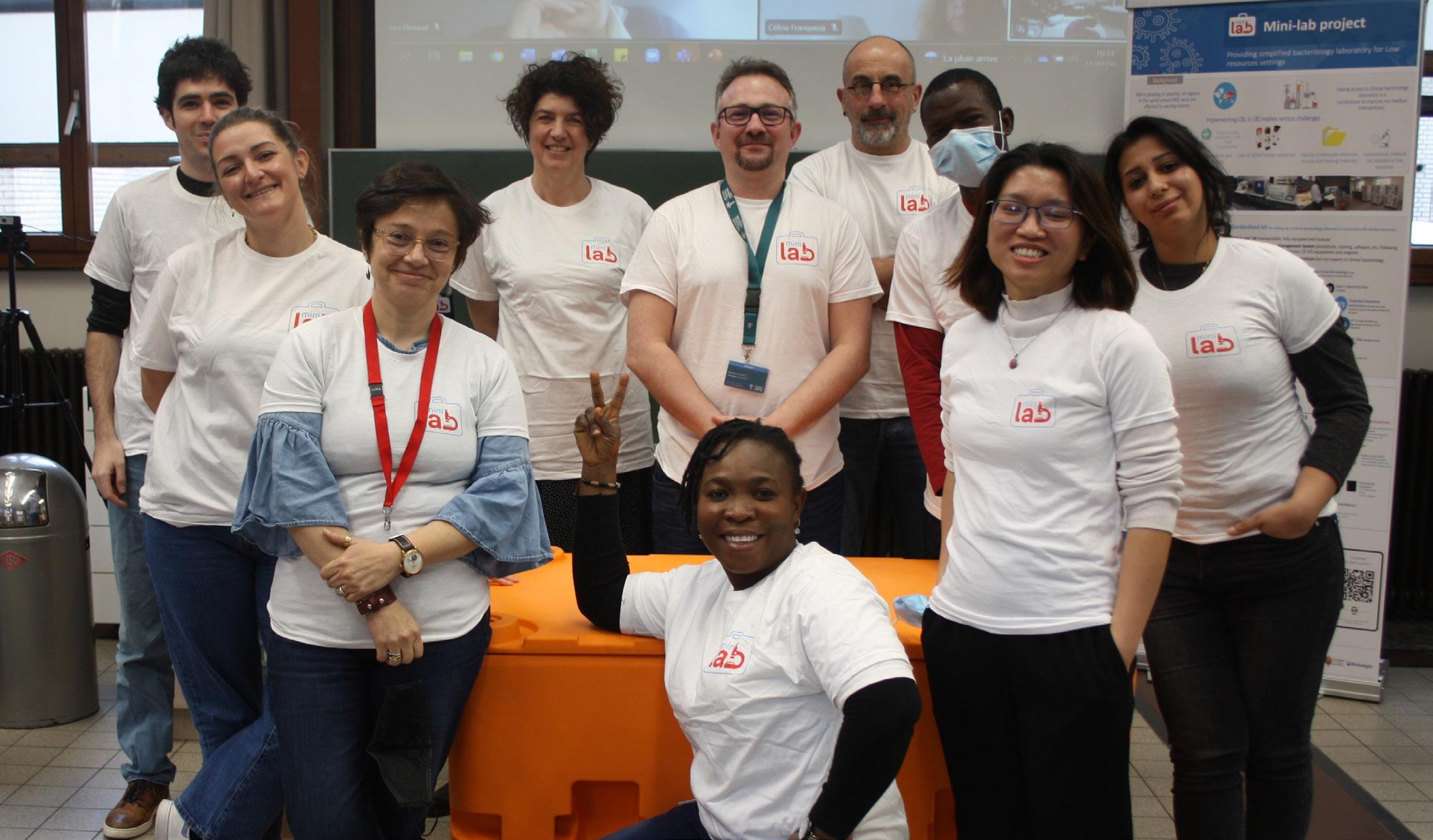