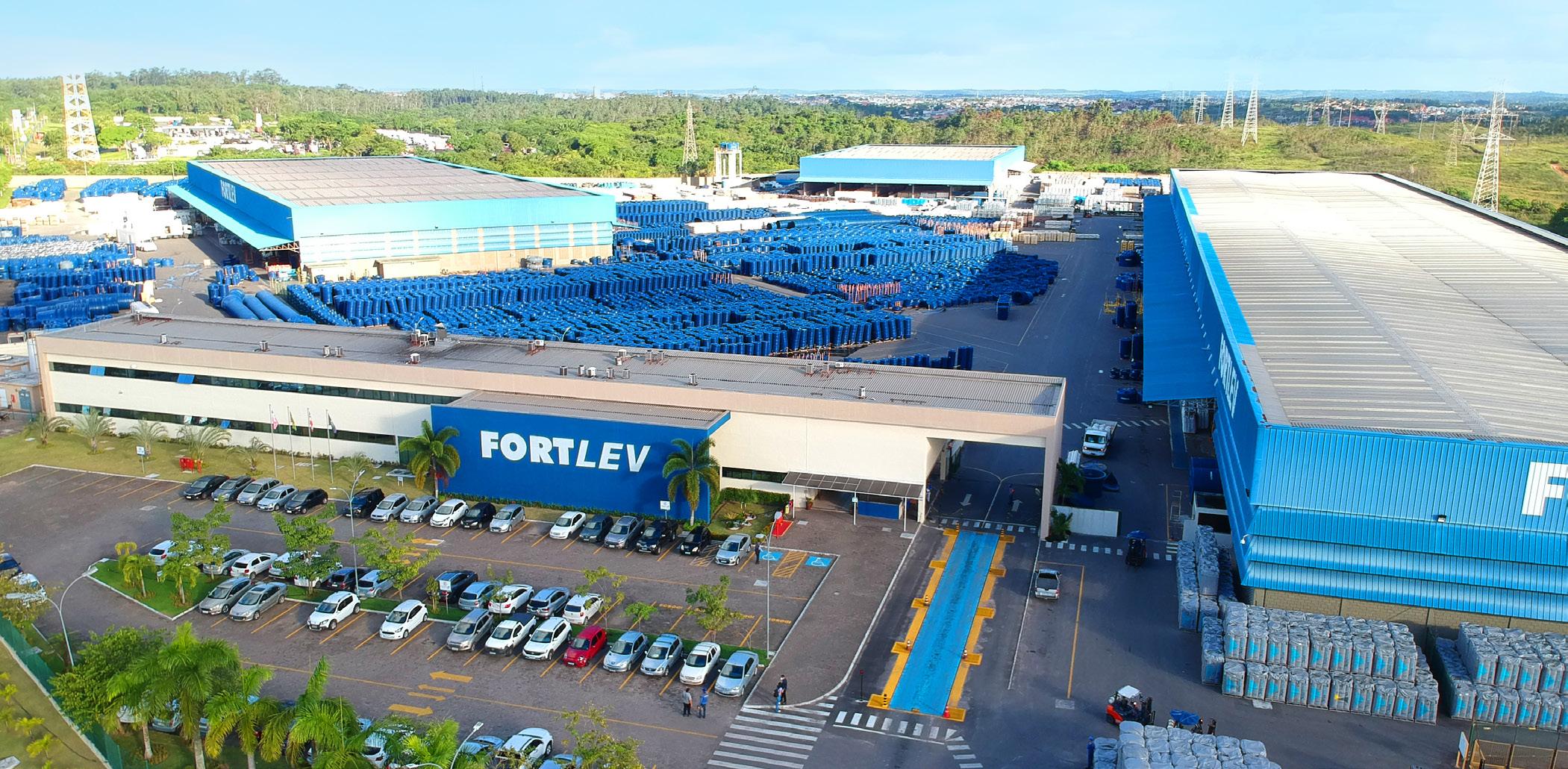
4 minute read
Roto Around the World
Ian Hansen, RotaConsult
Fortlev facilities in Brazil
FORTLEV - A ROTOMOULDING GIANT – 100% BRAZILIAN
Fortlev is the number one manufacturer of water tanks in Brazil, making thousands of tanks a day. This scale is not surprising when you consider Brazil has a population of about 215 million and is the 5th largest country in the world.
The Fortlev success story began in 1989, in Viana, a city in the Greater Vitória Metropolitan Region, in Espírito Santo, Brazil, with the manufacture of Fibre Reinforced Plastic (FRP) water tanks.
Compared to the cement tanks available in the market the FRP tanks were considered durable and strong, while being light in weight. This is how the company name Fortlev came into being, from the Portuguese words “forte” (strong) and “leve” (light).
In 1998, Fortlev innovated and launched their blue polyethylene water (box) tank range, again using a material that provided strength, flexibility, and safety for water storage. Of course, they manufactured these water tanks using the rotational moulding process. Fortlev began to dominate the national water storage market as cement tanks were quickly replaced by FRP and PE tanks.
In 2005, to keep up with growing customer demand they opened a second factory in the state of Bahia, which gave Fortlev direct access to the growing tank market of the arid northeast region of Brazil. Fortlev invested in new technology when they built a plant in Bahia to melt compound and pulverise their own polyethylene raw materials, which enabled them to exercise control over its entire rotomoulding production process.
In 2005 Fortlev, established its own sheetmetal mould fabrication plant to eliminate the long lead times for new moulds. This investment in plant and skilled tradesmen not only reduced lead times it also reduced the costs involved for new moulds and the maintenance of existing moulds. They currently have more than 1,000 moulds in operation.
The desire of Fortlev to continue to innovate was demonstrated in 2007 when Fortlev, in partnership with Braskem, the local polyethylene producer, travelled to Australia. Australia was seen as a model for the development of innovative water storage solutions.
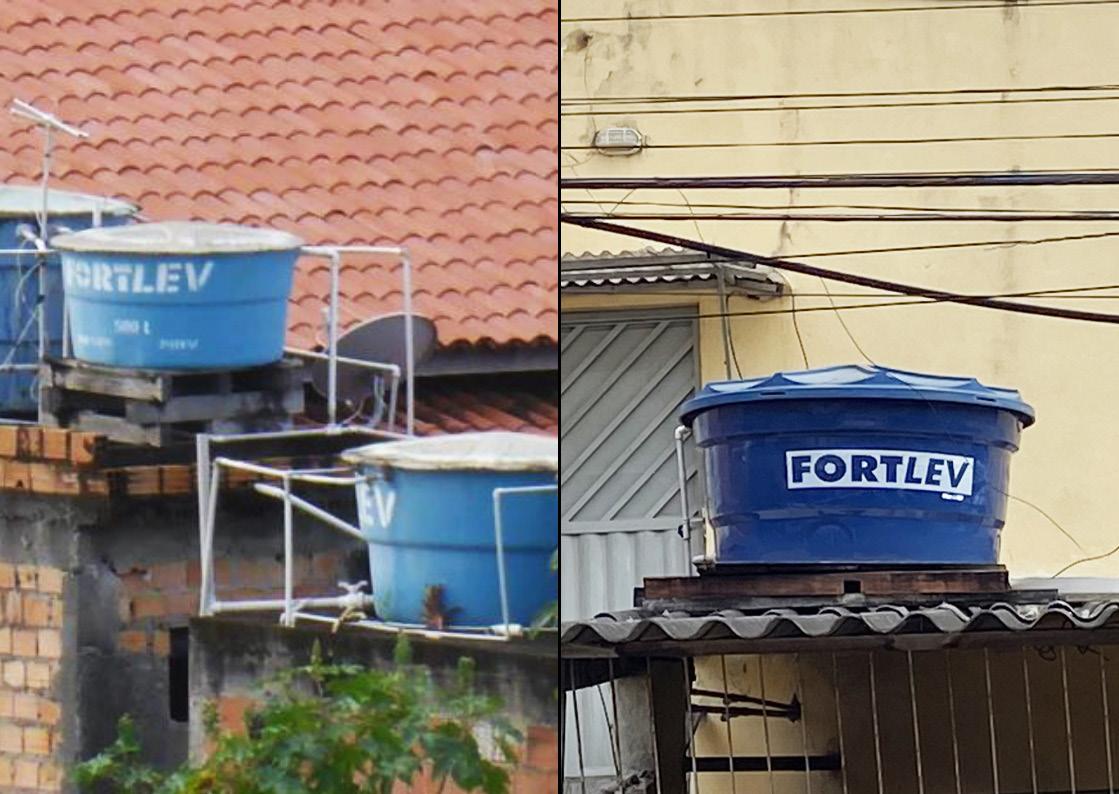
Before (FRP tanks) and After (PE tanks)
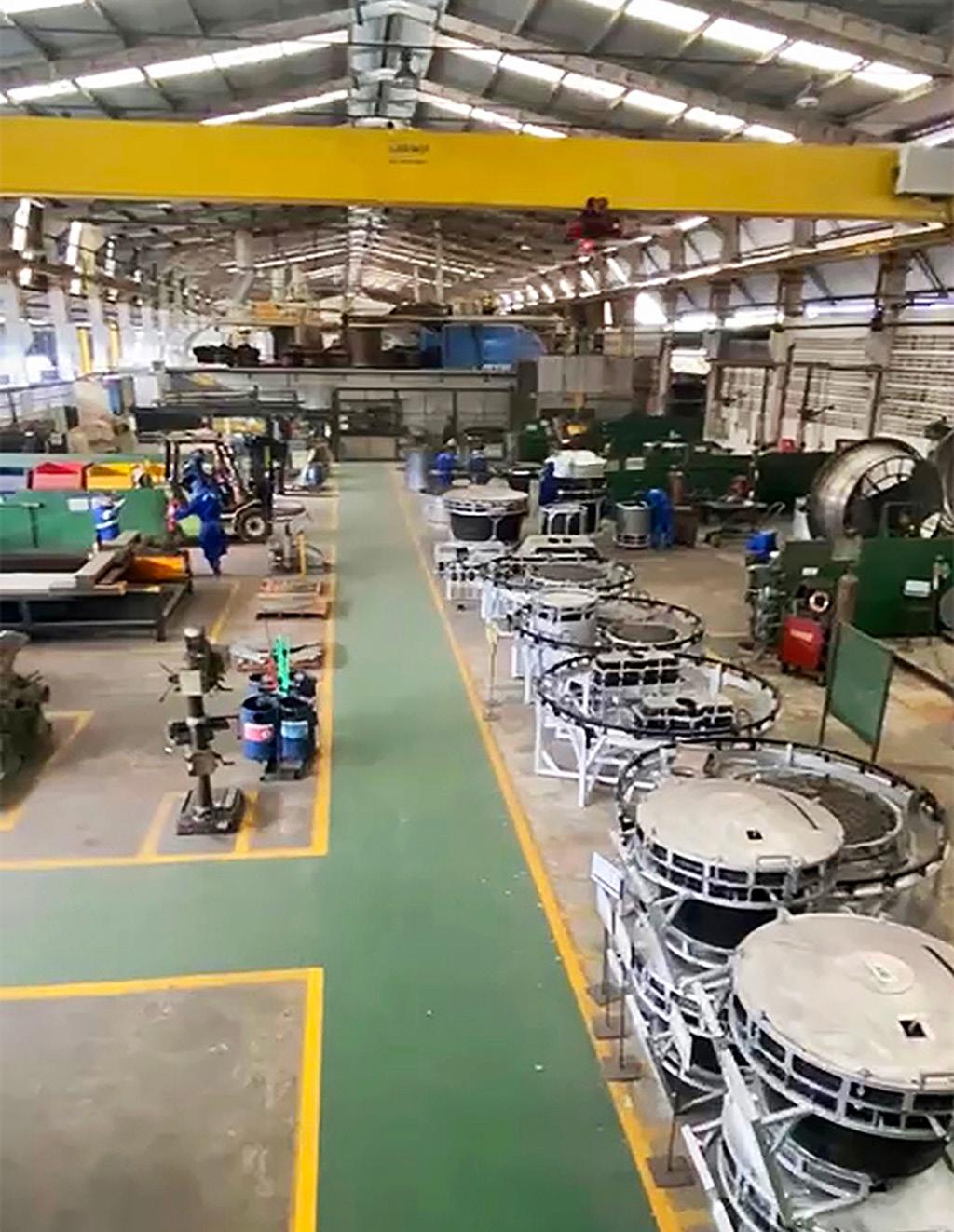
Fabrication of sheet metal moulds Rototour of Germany & Poland, organised by ARMA, with Fortlev team members joining other moulders from around the world.
Ferry 5.0m carousel and 500L tanks
Braskem developed a special C6 grade of polyethylene for Fortlev to mould a novel underground water tank in partnership with an Australian rotomoulder.
Over the years, in addition to having the factory in the state of Espírito Santo, seven more factories were strategically installed in six Brazilian states: Bahia, Santa Catarina, São Paulo, Pernambuco, Goiás, and Amazonas. The objective was to guarantee the daily supply of its products to the more than 60,000 points of sale throughout the country. Today Fortlev has 8 factories that serve 100% of Brazilian municipalities, with more than 30,000 delivery trips per year.
Since their 13,000km odyssey to Australia, Fortlev has continued to invest in people’s skills through engagement with the global rotomoulding community, and sending key employees to rotomoulding conferences around the world in order to keep up with industry developments. They have also taken advantage of the Rototour factory tours organised by ARMA during the last decade, which has taken many Fortlev staff into more than 50 rotomoulding factories in Europe, United Kingdom, China, Australia, India, and South Africa.
10 years ago they invested in micro-pellet technology in order to achieve competitive cost advantages; eliminating the requirement for pulverisers and reducing labour. This also delivered a reduction in warehousing space and transport costs around Brazil to their
growing number of rotomoulding plants. Today the volume of rotomoulding PE manufactured is >6,000Mt per month. Or >70,000Mt (>160 million lbs) per annum.
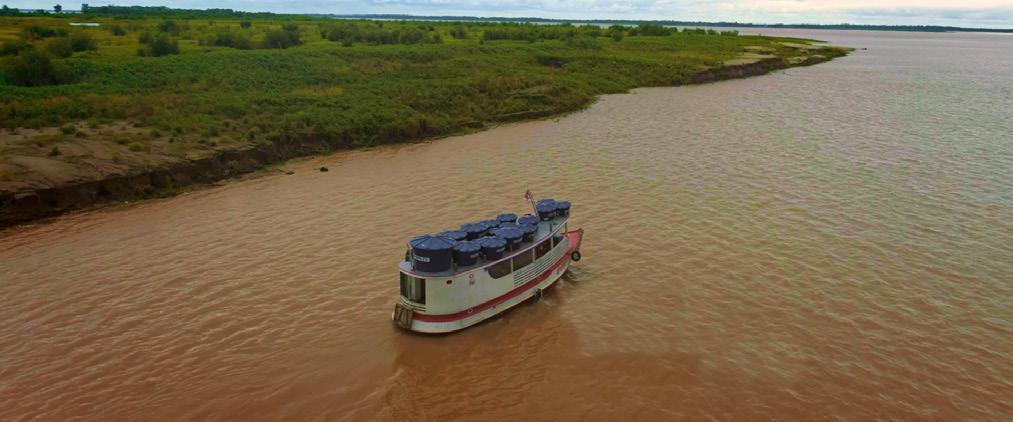
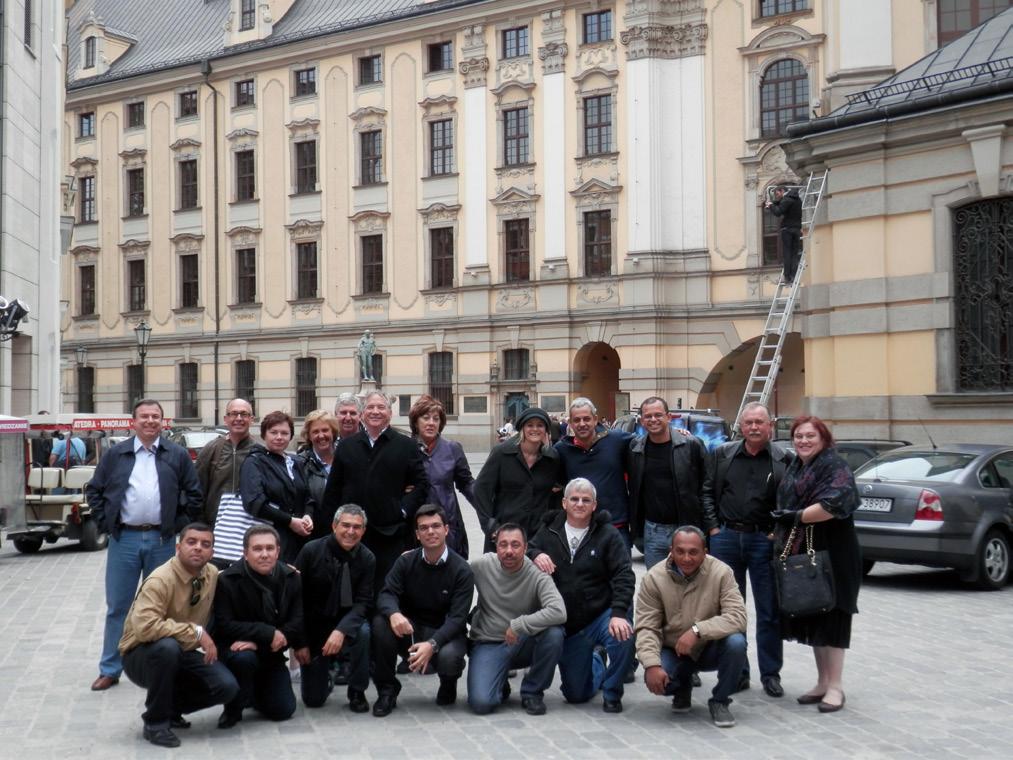
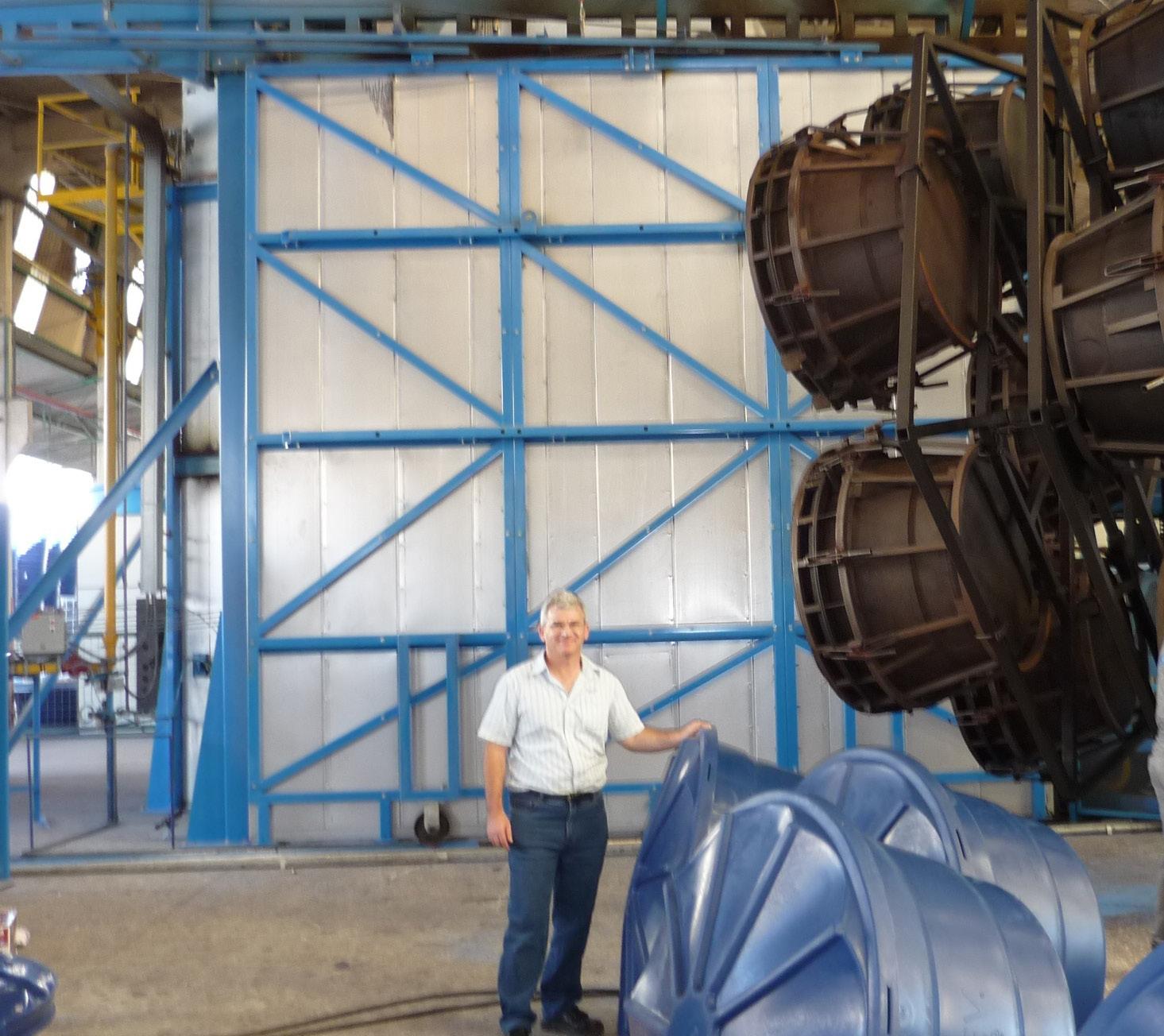
Fortlev operates over 50 rotomoulding machines throughout Brazil, mainly in shuttle and carousel configurations. Rotomoulding is known as a labour-intensive process, but Fortlev is moving to
more automation. New technology has been introduced to minimise labour with the introduction of some high volume Rotoline CR5.20 carousel machines featuring automated mould opening and closing, in addition to on-line part weight control.
During recent years Fortlev have made substantial investments to improve their moulding operations, including technology for safety and more accurate weighing of materials. They use the latest technology to run a centralised industrial management and monitoring system for both its information technology (IT) and operational technology (OT) networks. This provides real-time data from within the manufacturing operation, including weight of material, power, and gas consumption.
Although water storage solutions remain Fortlev’s main focus, the company has diversified into the manufacture of PVC roof sheets and PVC pipes and connections, along with becoming the largest distributor of solar panels in Brazil.
With a diversified portfolio of products, Fortlev dominates the Brazilian market. Fortlev use rotational moulding to produce different types of products, from small to large capacity tanks (up to 30,000L or 8,000USG) for water storage, industrial tank applications storing specialty chemicals, and domestic septic tanks.
Continued investment in technology and innovation over the past two decades has rewarded the company making it one of the largest independently owned water tank manufacturers in the world.
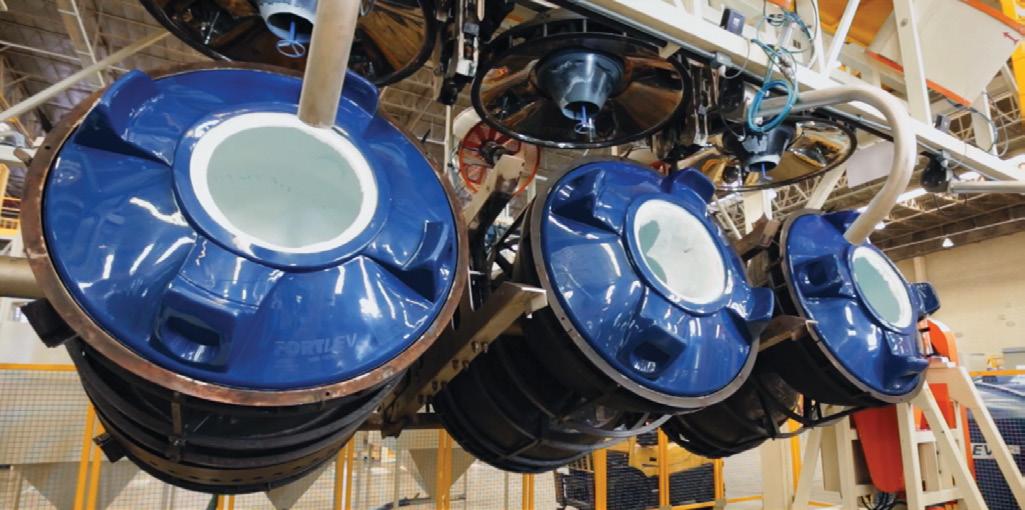
Rotoline TQ50DC fully automatic multi-layer machine
