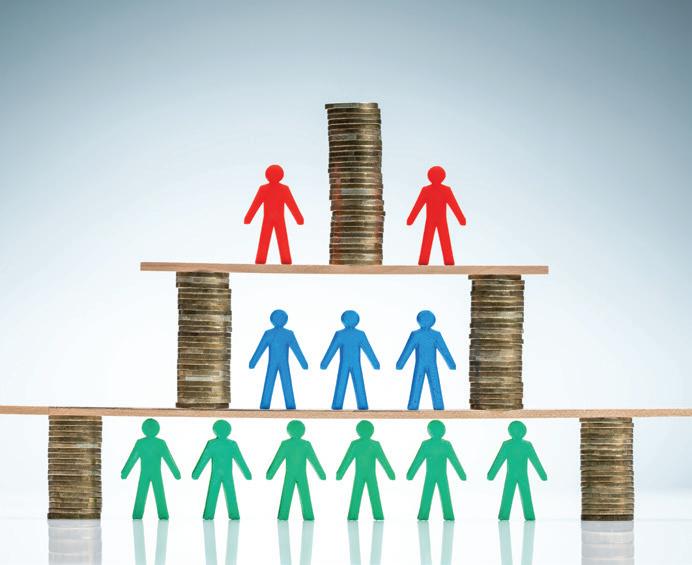
16 minute read
Industry 4.0
INDUSTRY 4.0
EPISODE 5
Rob Miller, Wittmann Battenfeld Canada Inc. / ROTOLOADTM
Perhaps it’s your Turn
I have spent quite some time pondering the direction for the next few episodes.
Not that there is any shortage of Industry 4.0 topics, ideas, principles… actually, quite significantly the opposite. If you ask 20 experts, you will for sure get at least 25 answers…
I have had a number of interactions with other industry colleagues, discussing primary machinery, mold technology, downstream/post molding processes, considering where there might be opportunity to leverage Industry 4.0 to the greatest potential financial gain.
One of the things that I did as I was planning was to go back and read through my previous episode submissions. As I did, it was quickly evident to me that each of the Industrial Revolutions made physical labor substantially easier. The primary purpose of each of the four major monumental shifts of thought seemed to have the main purpose of reducing or making more efficient the labor content of any manufacturing process.
Therefore, in the end, I believe that the human aspect of our manufacturing has the greatest potential gain in efficiency from Industry 4.0 concepts.
To be totally honest, I am not sure how many episodes it may take to fully examine some of these ideas and concepts, but I believe it to be very beneficial to work through some of this.
I would like to start by taking a brief minute to introduce three common terms used in manufacturing, technology, economic, and business discussions, HUMAN, STRUCTURAL, and RELATIONSHIP Capital.
HUMAN CAPITAL is your people. The description can go much deeper, to include your employee experience and knowledge, the relationship that the company has with those employees, training policies and procedures, and employee satisfaction…do they enjoy their jobs and the company that they work for.
STRUCTURAL CAPITAL relates to your legacy processes, policies, vision, and mission statement that all contribute to the culture of the organization.
RELATIONAL CAPITAL is essentially as it sounds. It is the relationships that you share with your customers, suppliers, employees, investors, etc.
The intent is to suggest that there is a point where these three factors within your organization intersect, and at that intersection is where you really experience the highest level of value.
You may be asking…where is he going with this? Please stick with me, and I assure you that I will land the plane. (that is what my kid’s say anyways)
There was an economist back in the late 1800’s, Mr. Alfred Marshall, and one of his quotes is the following. “The most valuable of all capital, is that which is invested in human beings”. Mr. Marshall was known for the original theory of Supply and Demand, as well as contributions to the theory of marginal productivity.
Marginal Productivity essentially states that if you are paying an employee a certain wage, that your business revenue should increase by the same value, at the same rate, for the work produced by that same employee.
Now, a lot has changed since the late 19th century, and some of these prominent theories of the time don’t really apply any longer, or at least are disputed. As I explored this topic, I was left to wonder if each of our employees actually add their hourly wage in comparable value to our bottom line?
Fast forward a hundred years or so, and we find another economist, Mr. Thomas A. Stewart. One of the quotes that I found quite interesting when applied to these theories was “Human capital grows two ways: When an organization uses more of what people know, and when more people know more stuff that is useful to the organization.”
I will begin to lower my landing gear now…
I think one of the most common statements that I have ever heard in this ROTO industry, is that every facility that I have ever visited or discussed could use more people.
If this lack of available labor is one of the most common barriers to our meet our production needs, and even more important, our true potential capacity, then why are we not leveraging our RELATIONSHIP CAPITAL, along with our HUMAN CAPITAL, to build the STRUCTURAL CAPITAL of our organizations.
Final approach…
Our people often already know what can be done to make the process easier, more cost efficient, less labor intensive, safer, better, and in every way, improving the bottom line!
If there is a manual labor process in our facility, it can be almost guaranteed that our team (Relationship Capital) can help us make it more efficient. This definitely includes some of our trusted employees, but also extends beyond to find valuable supplier relationships, and to open up communication with our customers to get a feeling for what they would see as beneficial, but also what they may be willing to pay for.
Not that we should be asking our customers to pay for our automation, however, there are perhaps benefits that they may see an advantage from, and therefore, continue to be a valuable contributing partner.
This is where the Industry 4.0 principles begin to take shape.
INDUSTRY 4.0
EPISODE 5
As I have commented several times, Industry 4.0 is all about the data.
If we can leverage our STRUCTURAL, HUMAN, and RELATIONSHIP capital, and use simple technologies to inexpensively collect DATA that will help us and our teams make productive, efficient, and quality improving decisions about our processes, why would we not want to move forward in these initiatives?
If we go back a few paragraphs, we can look at this from the “marginal productivity” perspective, but more related to the technology investment, rather than the hourly wage.
Any investment in technology should have a return on investment strategy that allows each aspect of your labor profile to generate significantly more than your project, or hourly investment.
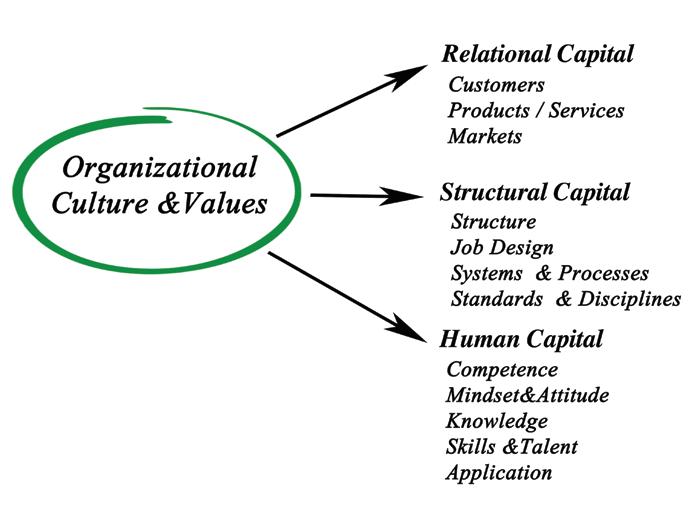
So…
I have realized that I am one thousand words into this episode, and not discussed any specifics.
The more that I thought, wanted to explain and write, it was clear to me that we need to start on a common thought process before we get into any specific realworld applications and how to solve them.
I have some thoughts of my own, but I would really like to do an experiment. In this new reality of travel challenges, we don’t have the ability to meet face to face, and to tour your facilities to discuss these important topics.
I would really appreciate the challenge of looking deeper into your questions, issues, and problems, to leverage the RELATIONSHIP CAPITAL that I have developed.
That way, I can work with your challenges to sketch out high level outlines, and present detailed propositions as to how Industry 4.0 can solve and improve your labor challenges.
Would you be willing to please consider writing to me by email at rob.miller@ wittmann-group.ca.
The source of all questions/comments will be kept expressly confidential, unless otherwise given permission. That way, it won’t be my thoughts, ideas, and solutions, but those that are generated by you and important to you, the innovative, experienced and sometimes challenged molders that are experiencing labor related issues on a daily basis.
Thanks in advance for your participation, and I look forward to hearing from you soon!
Until next issue, please stay healthy!
What Rotomolders Need to Know about Polymer Chemistry – Part 1
Dr. Nick Henwood, Rotomotive Limited
Rotomolders tend to be more mechanically minded than chemically minded and typically they do not have a deep understanding of polymer chemistry. Fortunately, the technical experts within polymer supply companies can often help with material selection decisions and resolve performance issues. While this approach usually works from a practical standpoint, “knowledge is power” and molders will benefit from sufficient understanding of polymer chemistry to make the right choices, especially when they are receiving conflicting advice from different suppliers!
The Association of Rotational Molders (ARM) frequently receives queries from members who are trying to navigate their way through a maze of information to make the right choices. As ARM’s Technical Director, most of these queries land on my desk. I always try to provide the most direct and straightforward answers that I can, but often a little background information is required to explain my comments and recommendations. In this series of articles, I will seek to provide useful insight without getting readers too immersed in unnecessary detail, concentrating on some of the more common questions that I get asked.
One such question relates to the function and effect of comonomers in different polyethylene (PE) grades. Most often this comes down to questions like “what’s the difference between a rotomolding resin made from butene versus one made from hexene?” Butene and hexene (strictly speaking: butene-1 and hexene-1) are examples of comonomers that are used during the production of different PE grades, including roto grades. They do essentially the same thing for PE, but their presence can cause some differences in grade performance. PE is a semicrystalline material; in its solid state, the molecules contained in PE may exist in one of three different configurations.
• Some molecules will be folded up in regular structures; these are in the crystalline phase. • Some molecules will not be folded up and are present in a more irregular arrangement; these are in the amorphous phase. • A few molecules may stretch between different crystalline regions, with their ends embedded into two different regions; these are called tie molecules (see Figure 1).
The proportion of crystalline versus amorphous phases will have a big effect on PE characteristics. High crystallinity grades are stiff and relatively brittle, while low crystallinity
Figure 1: Tie Molecules
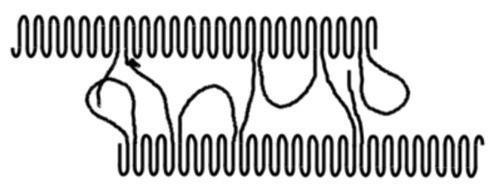
grades are more flexible and resistant to impact. In simplistic terms, the crystalline phase is what gives PE its stiffness and the amorphous phase is what gives PE its toughness. Selecting an appropriate grade for an application will involve finding a balance between stiffness and toughness needs.
Crystalline PE is denser than amorphous PE, so measuring the density of the overall material will provide a good indication of the relative proportions of crystalline and amorphous phases. Roto grades in the density region 0.935-0.945 g/cm3 represent a roughly equal balance between crystalline and amorphous phases; they are reasonably stiff and reasonably tough. Injection molding PE grades have a significantly higher density (>0.950 g/cm3) and are stiffer, but generally more brittle. Cast and blown film grade PE’s mostly have a lower density (<0.925 g/cm3) and are less stiff (i.e. more flexible) and significantly more tough.
A word of caution should be struck regarding terminology. The most technically accurate term for roto grade PE would be “linear medium density polyethylene” (LMDPE). However, custom and usage in different geographic areas of the world has resulted in some confusion in terms. For example, in North America, roto grade PE is often referred to as “linear low density polyethylene” (LLDPE) or as “high density polyethylene” (HDPE). While this confusion is unhelpful, we have to acknowledge that it exists!
During the manufacture of PE, comonomers are introduced into polyethylene reactors to reduce and control the density of the PE grade being made. With no comonomer, the reactor product will be so-called “homopolymer” HDPE: a very stiff material with a density >0.963 g/cm3. This product cannot be easily rotomolded, but it can be used for other polymer processes, such as injection molding.
Comonomers control the balance between the crystalline and amorphous phases in a PE grade. The more comonomer that is incorporated in the PE, the lower its density will be. The
comonomer molecules work by forming branches on the main PE backbone chains. These branches partially prevent the PE chains from folding into regular structures, which lowers the crystallinity, as well as the density of the PE produced.
The inferiority or superiority (depending on which property is being considered) of PE grades made with different comonomers is the subject of considerable discussion amongst the various technical authorities in rotomolding. My personal viewpoint has been established by my own tests and work carried out in a variety of different geographical areas, where practice can vary. This has been quite instructive. In the European roto market for example, rotomolding PE grades are offered that utilize all three common comonomer types:
Butene-1 4 Carbon atoms present in the comonomer
Hexene-1 6 Carbon atoms present in the comonomer
Octene-1 8 Carbon atoms present in the comonomer
In contrast, most of the PE roto grades offered in North America utilize hexene-1. Similarly, roto markets in Australasia and South Africa predominantly use hexene-1 grades, because their local suppliers have chosen to utilize this particular comonomer in their production of PE generally. Markets in South Asia, India and China tend to use butene-1 grades; once again, the practice of local suppliers sets the tone. Given this geographic diversity, what are the real differences between PE grades made from different comonomers?
It should be stressed that the comments and conclusions in this article relate specifically to the PE grades used for rotomolding. if we were looking at extruded and cast film applications (which there are many rotomolded products made successfully with butene-based grades. However, this also depends on other factors. The main area where we may see differences between similar Melt Index (MI)/density combinations is related to the long-term properties of PE grades. The normal measure we use for long-term properties is Environmental Stress Crack Resistance (ESCR) and here we do see differences in performance between grades made with different comonomers.
The most common ESCR test method used for roto grades of PE is ASTM D1693. Sample coupons are notched (to provide a point of stress concentration), bent almost double (to provide a constant sample strain) and immersed in a stress-cracking agent at an elevated temperature (to significantly accelerate sample failure). Sample coupons are monitored, and the time taken for them to fail is expressed in hours. Figure 2 shows samples that have “passed” and “failed”.
As a test, the standard ASTM ESCR evaluation method has its faults, the main one being that it can only provide a rough
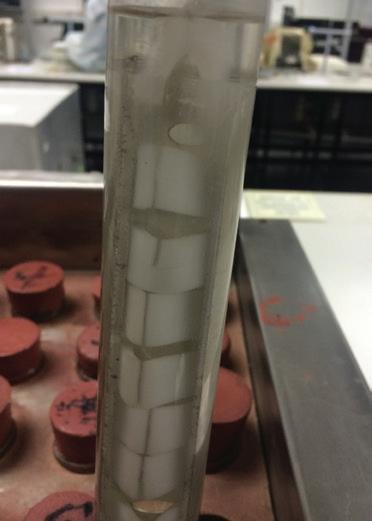
The assessment would be different Figure 2: Passed/Failed ESCR Samples differentiation between grades. It offers relatively low precision, mainly use much lower density PE grades) or injection molding but it does enable grades to be classified into long-term property applications (which mainly use much higher density PE grades). groupings such as “poor”, “good” or “excellent”. PE roto grades Comonomer choice is likely to make much more of a difference with a MI of 5 g/10mins and above will generally have “poor” with lower density PE grades, simply because so much more of ESCR, whatever the comonomer choice. This is because the MI it is needed to achieve the required density (normally at <0.925 has a greater effect on ESCR than any other factor. PE grades g/cm3). With the higher density PE grades used, for example, in with a lower MI (2 – 4 g/10mins) will have “good” to “excellent” injection molding (0.950-0.965 g/cm3), there will be a smaller ESCR properties and this is the area where there are measurable levels of comonomer, or even zero comonomer. differences due to comonomer choice. For roto grade PEs in this
Rotomolding grades are mostly in the range 0.935 – 0.945 g/ MI range, hexene-1 grades tend to exhibit higher ESCR values cm3. Therefore, the choice of comonomer is likely to have a more than butene-1 grades. The further benefit of octene-1 compared limited effect on properties. This is what is generally observed; to hexene-1 is harder to observe in the roto grade range.

Differences between hexene and octene are significantly more performance needs. This will be a matter of individual design pronounced when testing lower density grades, such as those judgment. As a general rule, long-term performance issues used for film applications. should be considered for any part that will be subjected to
The explanation for the differences observed in ESCR for significant continuous or cyclic loading over its lifetime. lower MI grades is mainly explained by the presence of tie Examples of such parts are underground chambers, molecules. These were introduced as a concept earlier, where they overground storage tanks and chemical containers. were described as molecules with their ends embedded into two different crystalline regions. This configuration allows them to The contents of this article should be considered as an effectively tie crystalline regions together in a form of network, explanatory guide only. For a more detailed consideration which provides improved resistance to long-term damage of the about grade selection, individual material suppliers can provide overall structure. In relatively low MI roto grades, the occurrence specific information. For critical applications, it may also be of tie molecules increases from butene-1 to hexene-1 to octene-1. advisable to undertake comparative performance testing. This is illustrated in Figure 3. The probability of more tie For ARM members, there are a number of additional molecules increases the tendency to bind areas of crystallinity information resources available, including the Resin Properties together in a network structure. This will increase the ESCR List and various subject specific webinars. of a PE grade and may also result in a small improvement in some short-term properties, including low temperature impact strength. 35
The data shown in Figure 3 is provided for illustrative purposes. It was generated in a study 30 of PE film grades, so the actual probabilities may not be strictly applicable to rotomolding grades. However, the overall trends will be the same. The general effects on ESCR are illustrated in Figure 4. The ESCR value of a specific grade will be affected by other factors, as well as tie molecules. For the standard ASTM “Bent Strip” test, both density and MI will significantly affect the values found experimentally. Figure 4 is illustrative only, Probability of the Molecules (%) 10 15 20 25 for density values in the 0.935 – 0.940 g/cm3 5 range and for MI values in the 2 – 10 g/10mins range. While the ESCR of “General Purpose” 0 roto grades (MI 5.0 - 7.0) are all relatively poor, C8 C6 C4 greater differences are seen when comparing Figure 3: Effect of Comonomer Type on Probability of Tie Molecules “Tank” grades (MI 3.0 – 4.0).
In conclusion, the following guide is offered related to comonomer effects: 1000 C4 C6 C8
When using typical “General Purpose” roto grades (5 MI and above), there will be little practical difference in performance between butene and hexene comonomers, at similar MI/density combinations. When using typical “Tank” Grades (3 – 4 MI), discernible differences in performance between similar MI/density combinations should be expected. The main measurable differences in performance between grades will relate to long-term factors, as exemplified by properties such as ESCR. The influence of the comonomer in the grade selection will depend mainly on the application and its required long-term
900
ESCR (hr)
800
700
600
500
400
300
“Tank” Grades
200
100
“General Purpose” Grades
0 2.0 2.5 3.0 3.5 4.0 4.5 5.0 5.5 6.0 6.5 7.0
Melt Index (g/10min)
7.5 8.0 8.5 9.0 9.5 10