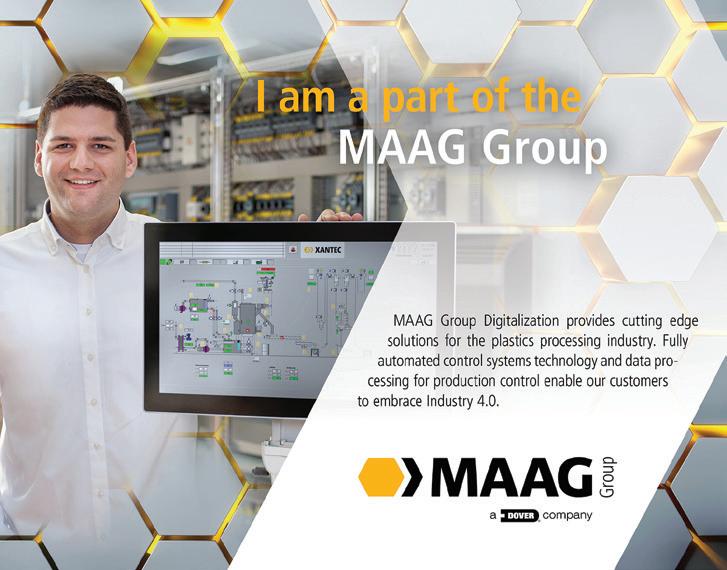
15 minute read
Upfront
MAAG Group Supplies Ravago with System Components and Controls for Plastics Production
OBERGLATT,
SWITZERLAND — The Swissbased MAAG Group has been contracted by Belgian company Ravago to install a new line for the recycling of polyolefins. The decisive factor in the contract award was MAAG Group’s highlevel system expertise as a global solutions provider supplying process technology for the polymer, chemical, petrochemical, pharmaceutical, and food industries. MAAG Group is supplying the line as a complete plant system, all from a single source - including the control technology. The control system comes from XANTEC Steuerungs-und EDVTechnik GmbH, which MAAG Group acquired in 2020. The Ravago contract affirms the Group’s strategy of boosting its activities in the field of digitalization and Industry 4.0, offering customers intelligent, agile, and competitive solutions.
Founded in 1961, Belgian company Ravago is today a fullservice provider to the petrochemical industry, committed to continuous advancement in plastics applications. The focus of the company’s diverse operations is on plastics production, especially recycling and compounding. Ravago produces 1,000,000 metric tons of plastics annually, at 30 locations.
When looking for a partner to build a new polyolefin recycling line at Arendonk in Belgium, Ravago chose MAAG Group. It was particularly attracted by the idea of a complete solution from a single source, which MAAG Group was able to deliver based on the consolidated expertise of its Group members.
Various MAAG Group system components form part of the new line: The ERF 500 high-performance melt filter from filtration and recycling systems specialist ETTLINGER is suitable for processing materials with up to 16% impurity levels while guaranteeing long operating times with no filter changing. ERF melt filters can process a wide range of polymers, and effectively remove foreign matter such as paper, wood, aluminum, copper, rubber, silicones, and high-temperature plastics.
MAAG Group’s contribution to the line includes an FSC 300 hydraulic screen changer for filtration systems, as well as the PEARLO® underwater pelletizing system. The efficient system, designed for high throughput rates, not only produces highly uniform spherical pellets; its handling, cleaning, assembly, and commissioning are also very easy.
The control technology for all line components comes from XANTEC. The new addition to the MAAG Group specializes in the planning, design, and manufacture of control systems for the plastics and rubber industry. So, it was able to deploy all its expertise and experience in the automation of filtration and granulation systems on the project. For the customer that means optimally designed process control, which improves both the cost-effectiveness and the quality of its production.
“Our systems expertise, recently enhanced in relation to digitalization and Industry 4.0 through the acquisition of XANTEC, is a clear benefit for the customer. They have an integrated solution from a single source, safe in the knowledge that the individual components will interact perfectly from day one,” asserts MAAG Group President Ueli Thuerig.
The new line is scheduled to be commissioned in 2021. The plant design is conceived so that it can also be transferred to other locations of the global Ravago corporation.
UPFRONT
Roll Out Cart (ROC) Molders Reduce Cost and Meet Warranty Claims with G2
Roll out carts are a big business, especially considering that most households in the United States have at least two. At almost $60 per unit, the ROC market is worth hundreds of millions annually and justifiably requires significant investment by molders. For instance, a single cart mold can cost $500,000. As well, manufacturers offer a 10-year warranty to consumers and cities that purchase carts for waste disposal programs, so they need be able to add adequate UV/AO stabilizer while controlling cost.
Chroma Color’s G2 has helped roll out cart molders reduce cost through let down reductions from 3% to 1%, while still delivering enough UV/AO to support a 10-year warranty. And since G2 comes in solid pellet form, molders can bypass a large amount of cost creep found with liquid color in the form of replacing hose kits & pumps, added housekeeping and other costs related to consolidation and agitation. Using highly loaded G2 is also a space-saver given lower inventory requirements and thus fewer drums or gaylords.
Chroma Color’s G2 product line has proven performance in diverse applications, including outdoor durables, packaging, industrial, non-automotive transportation, and much more. Convertors continue to be impressed by this game-changing technology. Whether it is injection, extrusion or blow molding, G2 continues to hit the mark.
Chroma Color Corporation is a leading specialty color and additive concentrate supplier serving a diverse range of markets, including packaging, healthcare, pharmaceutical, wire, cable, consumer products, and others. Chroma Color’s growth strategy includes robust organic and inorganic growth and having made six acquisitions over the last three years. Chroma’s extensive technical leadership and manufacturing expertise, coupled with its game-changing colorant and light management technologies, have delighted customers for over 50 years.
For more information about G2 visit: https://chromacolors.com/g-series-g2-g3-ultrapet/
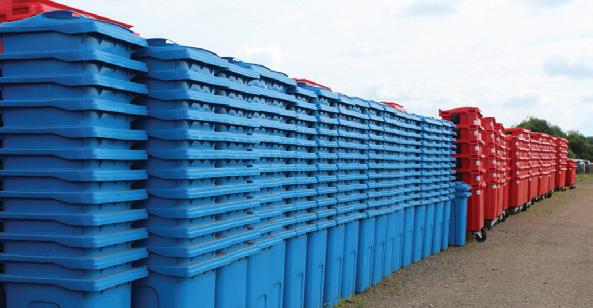
Snyder’s Revolutionary “CageBuster®” IBC Tote Success Drives Demand for a New Larger Size
Snyder Industries recently introduced a revolutionary new intermediate bulk container (IBC), called “CageBuster,” which is positioned as a more cost effective and environmentally friendly alternative to the traditional caged IBC tote.
The unprecedented demand for the revolutionary CageBuster IBC Tote value proposition has now resulted in Snyder introducing a new larger 330 gallon size to compliment the popularity of the original 275 gallon product offering, which was introduced just a year ago.
“We had always planned on developing a 330 gallon size, but the overwhelming response to CageBuster from the market place required us to expedite the product development of a new larger size,” said Mike Melymuk, the Director of IBC Sales and Marketing.
The CageBuster has a unique, all plastic design that is over three times thicker than a caged IBC tote, which provides a superior structural integrity, resulting in over 50% cost savings over the useful life of the IBC tote, while addressing the environmental concerns related to the ongoing container disposal and replacement programs associated with caged IBC totes.
Besides being a world leader in the design and manufacturing of returnable intermediate bulk containers, also known as tote tanks, Snyder Industries also maintains major market positions within many other proprietary product categories, including large single and double wall storage tanks, material handling bins, insulated boxes, refuse containers, and specialty pallets.
Snyder Industries is part of Tank Holding, which also includes the brands of Norwesco, Bonar Plastics, Bushman, Chemtainer, Meese and Stratis owned by Olympus Partners, and the management team, currently operates over 30 manufacturing plant locations and employs approximately 850 people throughout North America.
UPFRONT
Tank Holding Acquires Rotational Molding Inc.
Tank Holding, North America’s largest rotational molder, has acquired California based rotational molder Rotational Molding Inc. RMI designs and manufactures high-quality proprietary products in bulk laundry and linen carts, material handling bins and containers, refuse and recycling, bulk storage tanks, as well as a variety of other products including outdoor and custom products.
“RMI represents an important part of Tank Holding’s overall growth strategy, which is to strengthen leading positions in markets that are adjacent to our legacy core business, where we can leverage our industry knowledge and expertise to create greater value for our customers,” said Greg Wade, CEO of Tank Holding.
The RMI acquisition provides additional synergy opportunities with Tank Holding’s other recent acquisitions, Waste & Recycling Plastic Containers, Chem-Tainer, and Meese, who are other major players in similar markets. Together, these market leading brands and product offerings provide the industry with the broadest product portfolio and the largest footprint of manufacturing facilities. The transaction includes the operations of the facility located in Gardena, California.
“Tank Holding is the ideal partner to succeed our company’s history and accelerate our growth objectives. We are confident they will continue the success for both our customers and employees for the years to come,” said Mario Poma, CEO of Rotational Molding Inc.
The RMI announcement represents Tank Holding’s 11th acquisition in the past two years, and further enhances the company’s far-reaching portfolio of products to serve a wide variety of end markets through a growing number of distribution channels.
Besides being a world leader in the design and manufacturing of polyethylene tank and container products, Tank Holding also maintains major market positions with many other proprietary products, including intermediate bulk containers, insulated material handling bins, laundry and linen carts, refuse containers, and specialty pallets.
Tank Holding, which includes the brands of Norwesco, Snyder Industries, Bonar Plastics, Bushman, Chem-tainer, Meese and Stratis Pallets, owned by Olympus Partners and the management team, currently operates 33 manufacturing plant locations and employs approximately 900 people throughout North America, prior to the RMI acquisition.
Olympus Partners is a private equity firm focused on providing equity capital for middle market management buyouts and for growing companies. Olympus manages in excess of $8.5 billion mainly on behalf of corporate pension funds, endowment funds and state-sponsored retirement programs. Founded in 1988, Olympus is an active, long-term investor across a broad range of industries including business services, food services, consumer products, healthcare services, financial services, industrial services, and manufacturing.
President of Diversified Plastics, Inc. Named Industrialist of the Year
LATTA, SC, USA — Tommy Wallace, the President and Owner of Diversified Plastics, Inc. (DPI), a leading international rotational molder based out of Latta, South Carolina, received the Industrialist of the Year Award by the Dillon Herald, a local SC newspaper.
Since 1976, Diversified Plastics has been the leading rotational molding manufacturer of plastic material handling carts and plastic storage containers for the industrial, textile, hospitality, laundry, agricultural, and marine industries. In addition, they produce waste and recycling containers for restaurants, sports venues, stadiums, apartment/condominium complexes, and corporate offices.
DPI’s diverse product lines also include bulk material handling carts, plastic utility carts, laundry carts, bulk containers, tote boxes, round containers, spring platform trucks, elevated carts, easy access carts, tilt trucks, and more.
“We are happy and blessed to be here for 44 years,” stated Tommy Wallace. “The key to our success has been establishing a good leadership team and experienced employees.”
Wallace also notes how well Dillon County has treated Diversified Plastics, Inc. over the years. With the county support, they have been able to grow the business to a staggering 200,000 square foot manufacturing and warehouse space that allows their products to sell throughout the United States and overseas.
With the assistance of local banks, they have been able to continue to grow their success by reinvesting and keeping equipment up to date which allows for high-quality product output. In addition to the Latta location, they also have recently added a location in Social Circle, Georgia.
To contact DPI or to request a quote, call 1-800-768-7636, email sales@dpiroto.com, or visit dpiroto.com.
UPFRONT
Huntsman Announces the Acquisition of Gabriel Performance Products, Further Expanding its Specialty Chemicals Portfolio
THE WOODLANDS, TX, USA — Huntsman Corporation (NYSE: HUN) today announced its agreement to acquire Gabriel Performance Products, a North American specialty chemical manufacturer of specialty additives and epoxy curing agents for the coatings, adhesives, sealants, and composite end-markets, from funds owned by Audax Private Equity.
Under terms of the agreement, Huntsman will pay $250 million, subject to customary closing adjustments, in an allcash transaction funded from available liquidity. Gabriel had 2019 revenues of approximately $106 million with three manufacturing facilities located in Ashtabula, Ohio, Harrison City, Pennsylvania, and Rock Hill, South Carolina. Based on calendar year 2019, the purchase price represents an adjusted EBITDA multiple of approximately 11 times, or approximately 8 times pro forma for synergies. The transaction is expected to close in the first quarter of 2021 after regulatory approvals.
Commenting on the acquisition, Scott Wright, President of Huntsman’s Advanced Materials division, said: “The acquisition of Gabriel Performance Products broadens the offering in our specialty portfolio and is complementary to our recent acquisition of CVC Thermoset Specialties. Gabriel makes highly specialized toughening and curing agents and other additives used in a wide range of composite, adhesive and coatings applications. We expect that the Gabriel business will strengthen our North America footprint and provide significant commercial synergies as we expand and globalize their specialty products across our global footprint and customer base. The acquisition will further enhance our competitiveness and our world class formulations business by improving our ability to create differentiation in our customers’ applications.”
Peter Huntsman, Chairman, President and CEO further commented: “With this acquisition we conclude a series of strategic initiatives in our Advanced Materials division we started in 2019 before the COVID-19 pandemic. Our initial intent was to complete the acquisitions of Gabriel and CVC simultaneously, together with the divestiture of our India DIY business earlier this year.
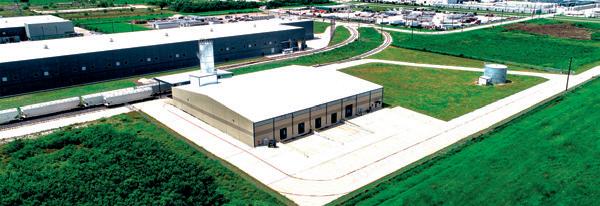


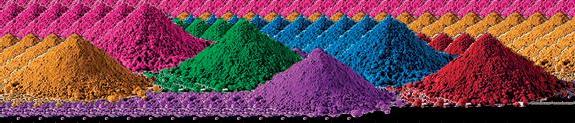
UPFRONT
United States (USA), 2021-01-12 – Emerson: Emerson Opens New $49 Million Global Headquarters for Welding and Assembly Technologies in Brookfield, Connecticut
New innovation facility in Brookfield’s Berkshire Industrial Park to house 220 professional staff, engineering and production employees
BROOKFIELD, CN, USA — Emerson (NYSE:EMR) announced recently the opening of its new Branson welding and assembly technologies’ global headquarters in Brookfield, Conn. This opening completes Emerson’s $49 million investment announced in April 2019 and supports Branson’s plastic joining, ultrasonic metal welding, and ultrasonic cleaning technologies for the medical, textile, automotive, food and beverage, packaging, and electronics industries.
“We are proud to support the Brookfield community and American manufacturing with this strategic investment,” said Vernon Murray, president of welding and assembly technologies for Emerson. “This new facility will help us continue to drive innovation and deliver the solutions our customers need and expect. Our new Brookfield headquarters also offers a more collaborative work environment for engineers and manufacturing leaders to serve our customers.”
The innovative technological capabilities available with this new 146,000 – unprecedented levels of customer support, including: • 16,000-square-foot engineering lab for research & development, customer application development, and materials testing. • Advanced additive manufacturing equipment for rapidresponse prototyping and production tooling. • 48,000 square feet of manufacturing space for Computer
Numerical Control (CNC) milling machining centers, equipment assembly, and customer application runoffs. • Collaborative workspaces to facilitate information to develop customer solutions more efficiently. • Dedicated training workspace for seminars, training classes, technical support services, and other customer needs. • Energy efficient construction methods including space wattage limitations, energy-saving LED lighting, automated controls for daylight harvesting and recovering heat from manufacturing operations to help warm the facility. • User-center design methodology to promote employee health and wellness.
Emerson plans to host seminars and events to introduce clients to the advanced capabilities of the new facility, as soon as COVID-19 safety protocols permit. Emerson purchased the 13-acre parcel for the new facility in Brookfield’s Berkshire Industrial Park, less than two miles from Branson’s former Danbury headquarters.
For more information about Emerson’s welding, assembly, and cleaning solutions, go to: https://www.emerson.com/ en-us/automation/welding-assembly-cleaning. https://www. emerson.com/en-us/news/automation/21-01-welding-assemblyheadquarters
Avient to Expand Color Concentrate Capabilities in Vietnam
CLEVELAND, OH, USA — Avient Corporation, a premier provider of specialized and sustainable material solutions and services, will complete an expansion of existing production capabilities for color concentrates at its Binh Duong site in Vietnam by next month. The move will improve speed-to-market and service level for local customers seeking unique color solutions to enhance aesthetics and appeal of high-quality end products.
“Demand for plastics has become one of the Vietnam economy’s fastest growth areas,” says Say-Eng Lee, vice president and general manager, Color & Additives Asia for Avient. “As consumption grows, requirements for high-quality color concentrates are becoming more challenging as well, as top brands focus on novel color solutions. We have increased our production space by over 30 percent and added to our stateof-the-art machinery portfolio to shorten lead times for developing and producing high-quality color concentrates. As a result, local customers will benefit from an efficient and agile setup, along with expert technical support. In addition, we can be more responsive in
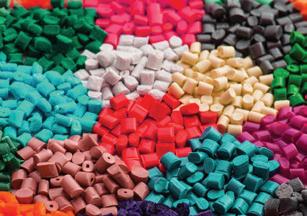
UPFRONT
accelerating customer development times and help them to reduce time to market.”
According to Vietnam Economic News, Vietnam’s plastics industry is currently experiencing an annual growth rate of 16 to 18 percent, with key segments including packaging, construction and electronics. Avient’s enhanced local turnaround for color concentrates will support middle to high end markets with consistent color quality, creative application of special effects, and unique colors to enhance product appeal and match branding requirements. With the expansion, Avient will also improve lead times for color matching locally.
Notably, Avient’s sustainable color concentrates can also support steps within the country to encourage plastic waste recycling and reuse. For example, the use of recyclable CESA™ IR additives, which enable black plastics to be identified for recycling, can reduce the environmental impact of dark colored packaging. Avient also recently strengthened its global commitment to help customers tackle and overcome the challenge of plastics recycling with the official opening of its new CycleWorks Innovation Center in Italy. The new center will focus on facilitating partnerships and enhancing new technologies to further the viability of recycling.
Avient also offers color concentrates for biodegradable plastics PLA, PHA, PHBV, PBS, PBAT and special blends of those materials, which do not compromise the organic recyclability of the resins they enhance.
Avient Corporation (NYSE: AVNT), with projected 2020 pro forma revenues of approximately $3.7 billion, provides specialized and sustainable material solutions that transform customer challenges into opportunities, bringing new products to life for a better world. Examples include: • Barrier technologies that preserve the shelf-life and quality of food, beverages, medicine and other perishable goods through high-performance materials that require less plastic • Light-weighting solutions that replace heavier traditional materials like metal, glass and wood, which can improve fuel efficiency in all modes of transportation • Breakthrough technologies that minimize wastewater and improve the recyclability of materials and packaging across a spectrum of end uses
For more information, visit www.avient.com.
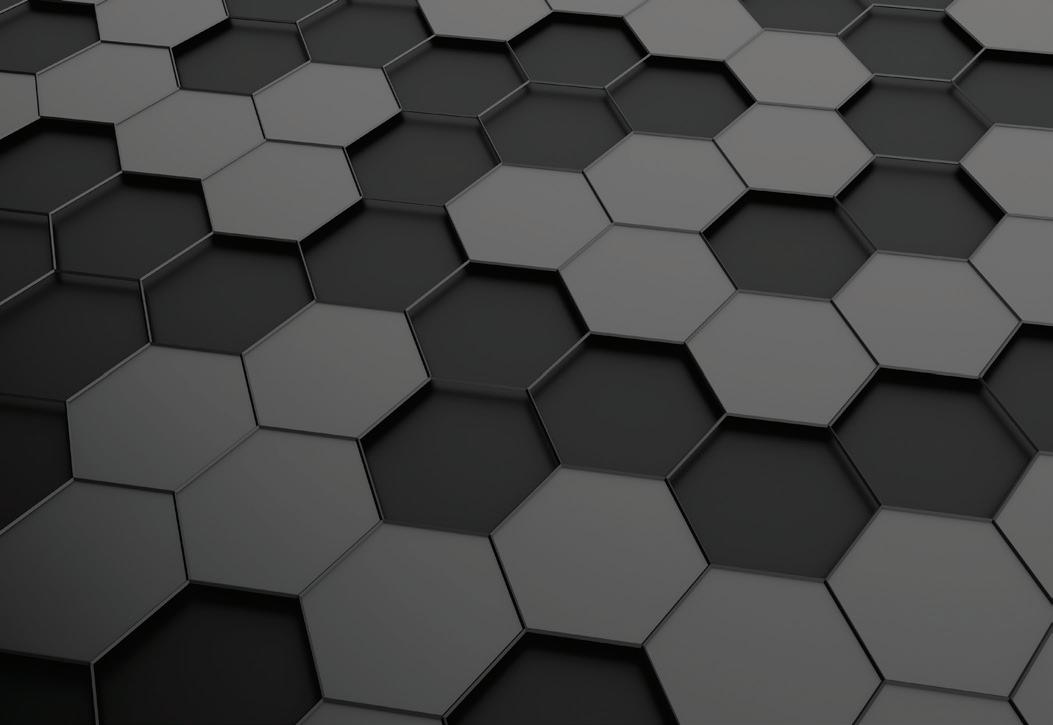
CNC Molds

Fabricated Molds
YEARS STRONG
1939-2020
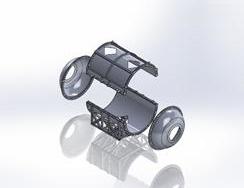
Cast Aluminum Molds
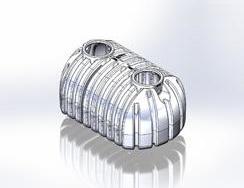