
25 minute read
Design Comment
DESIGN
COMMENT
Michael Paloian, Integrated Design Systems, Inc.
Design Documentation: Do We Still Need It?
We live in an age where everything is automated by computers and appears to be done perfectly within the blink of an eye. This is especially true in the design profession. When I first started working as an industrial designer more than 40 years ago, things were very different. I had to sit at a drafting table for hours, weeks, and months slaving over part drawings which were meticulously detailed with a pencil, calculator, and a skilled hand. The slightest design change would require the erasure of many hours of work and investing countless additional hours to incorporate the changes. All parts were detailed using conventional orthographic drawing methods to describe every feature of a part. Most parts required multiple drawing sheets to fully describe all the features in numerous cross sections and views. Part drawings were finalized by manually adding dimensions, tolerances, material specifications, and countless other notations. Finally, a tool maker would receive a set of blueprints which would then be manually programmed into an NC machine or interpreted by a patternmaker and made into a wooden pattern. Everyone of these steps provided an opportunity for human error, which could result in costly tooling revisions. Thank God those days are gone!
Today most designers don’t even know what an orthographic drawing is, much less know how to create one. 3D CAD has completely changed the workflow and design process by enabling designers to create 3D models of an entire assembly and all associated parts with all the appropriate draft angles, radii, clearances, and dimensions. These individual virtual parts are then sent to a tool maker who simply enlarges them based on required shrinkage, designs a mold from the CAD files, and eventually cuts a mold directly from the data. The entire process from start to finish can theoretically be completed without ever physically touching a part or requiring any human intervention. However, the process is not completely automated yet and humans must intervene at various critical phases, which require some form of documentation. The documentation I’m referring to is a production control drawing.
A wonderful benefit of 3D CAD is its ability to create a fully associative set of production control drawings for every part and assembly, which are automatically updated with design revisions. Although tool makers cut molds directly from the 3D CAD files, production control drawings are primarily used to identify critical dimensions, materials, surface finish, color, and any other important parameters critical to product form, fit, or function. Production documentation should be treated as a legal document between an OEM and a molder. If parts deviate from the stated specifications within the documents, they can be legally rejected for non-compliance. Furthermore, if a product failure leads to litigation resulting from injury, production control drawings are often cited in arguments by the defense or plaintiff. It’s therefore extremely important for designers to be very deliberate in specifying every notation on a production control drawing. Careless omissions or incorrect specifications pertaining to assembly, materials, tolerances, and countless other important factors affecting a product could result in serious consequences.
Next time you launch a new product don’t overlook the importance of production control drawings. Remember to consider them a very important legal document as well as an important source of information for the molder and tool maker.
I look forward to hearing from you. Please feel free to contact me at paloian@idsys.com with your comments or questions.
2020 ARM ANNUAL MEET
Susan Gibson, JSJ Productions, Inc.
In an environment placing in-person conferences on hold due to COVID-19, many association events have moved online. The Association Rotational Molders (ARM) hosted its 2020 Fall Meeting September 21-15, 2020 online. The virtual conference gathered an exceptional attendance of more than 500 viewers (246 molders and 257 suppliers, consultants, designers, educators, and staff).
The event featured a wide spectrum of topics and featured over 10 hours of education and an online Exhibit Hall with over 50+ exhibitors. The ARM online meeting easily held the attention of attendees.
The meeting was kicked off with a report on the State of ARM by Adam Webb, ARM Executive Director. Webb reported: over 65 informative videos have been added to the Association’s online library; a 2-day online Regional Meeting on Part Cure and Process Control was held online; the Roy Crawford Foundation has awarded 5 new scholarships to children of ARM members; and the Benchmarking Survey was released. After 3 years planning for a Spring Meeting in Italy in collaboration with the IT-RO (Italian Rotomolding Association), the event was cancelled due to COVID-19. ARM invited the IT-RO and the ARM-CE to join ARM Webinars. Membership is growing and has experienced a 13% growth over the first 9 months of 2020. ARM webinars were viewed over 6,000 times with over 2,000 unique viewers. The Design webinar was presented by Michael Paloian, Integrated Design Systems, with the assistance of Dr. Nick Henwood, ARM’s Technical Director. In August, Michael Paloian was presented with the Charles D. Frederick award for his contributions to the industry. In 2018, a webinar training series was presented by Dr. Nick Henwood, Jim Henry, and Larry Whittemore. In 2019, 5 webinars on Finishing Parts were presented by Rick Carlsen, Dr. Nick Henwood, and more. Webb reported the Association is in a strong financial position, and invited attendees to attend Rotoplas in Rosemont in 2021.
Highlighting the presentations, Chris Gick, NOVA Chemicals, said the global uncertain outlook on materials in the near term is based on uncertain recovery due to COVID-19, uncertain fiscal stimulus, potential structural changes, crude oil pricing, and capacity additions over the next couple years. Shutdowns, project delays and operability will continue to affect supply, but there is a resilient demand for PE. Margins remain well below re-investment levels, and costs are likely to rise heading into winter.

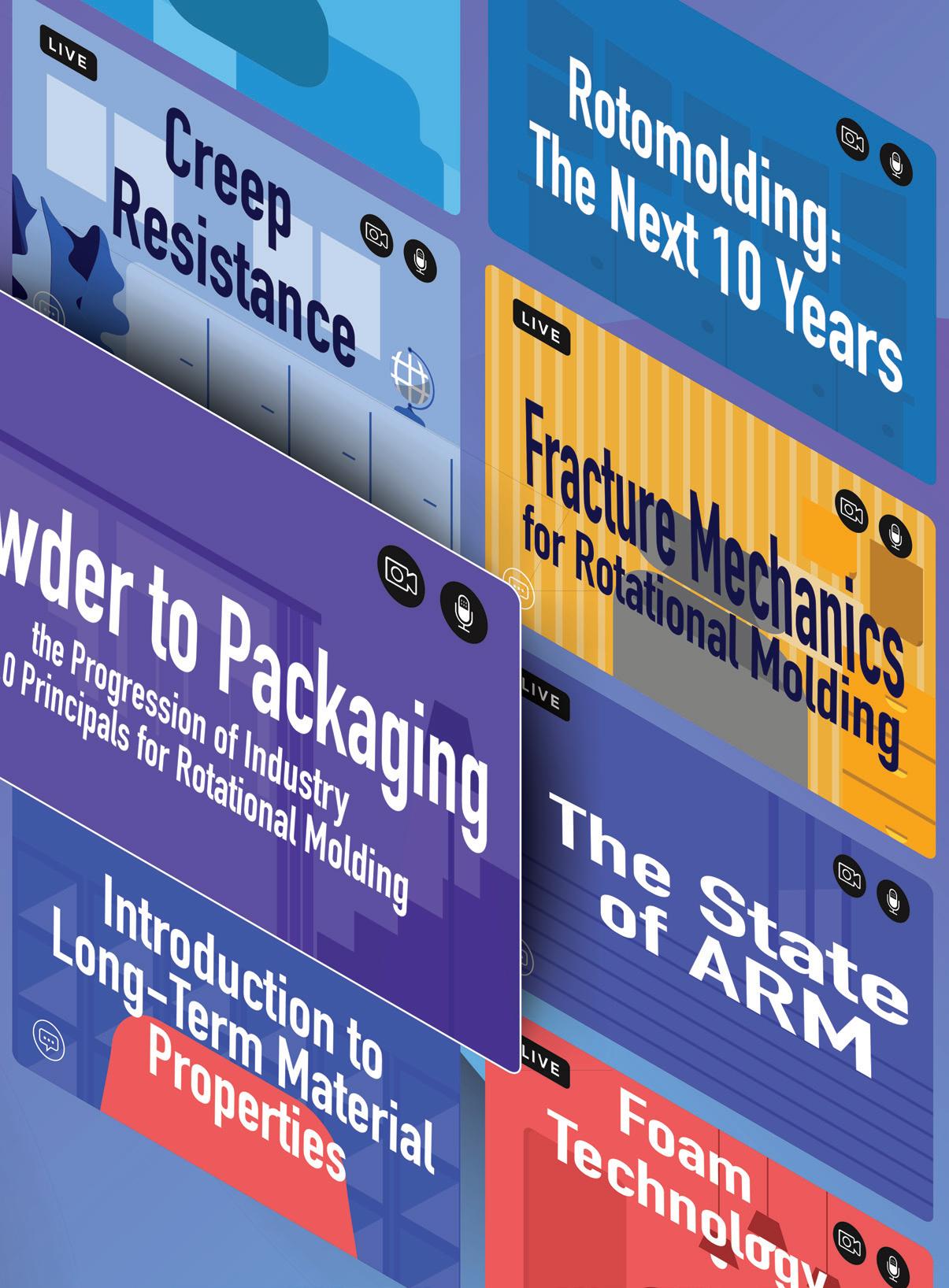
Paul Nugent reviewed ideas presented by the late Professor Roy Crawford in his article titled “Vision 2020”. Nugent said some of these ideas have come to fruition and some haven’t. He shared his view that the rotomolding industry is split 90/10 with 90% representing an entrepreneurial group that is cost conscience, relatively low tech with limited capital, re-inventive, and they will continue to grow. However, he stated the smaller (10%) group are more technically driven and the ones by in large driving the development of new ideas. Nugent indicated the vast majority of rotomolded products will be utilitarian in nature and Associations will continue to refine the 90/10 approach. There will continue to be pressure from the Green Lobby to reduce plastics and energy use in general. Automation will grow but will not take over, and materials will continue to center on PE (driven by application specialists).
ARM President Rick Carlsen presented an overview of the SWOT Analysis survey presented online. There were a total of 47 respondents (27 rotomolders, 14 suppliers, and 5 others).
Strengths identified included: flexible and creative parts; low-cost tooling; short runs are ok; durable parts, low entry capital needs; and capability for producing large parts. Weaknesses identified included: slow process with higher cost; materials limitations; manual, availability and skill labor issues; and a reputation for being dirty, hot, and exhibiting low tolerances. Opportunities included: conversions; automations (seen as a huge opportunity); new materials; and consumer market analysis. Threats included: lower cost competitive process; labor availability and skill; off shoring, and the environment. Carlsen called on rotomolders to consider how they compete and match up to these stereotypes identified in the survey.
“In a 4.0 world, how we compete in terms of cost, quality, and doing business is important,” he said. There are some legitimate opportunities and threats. “We have to determine how we are going to deal with these.”
Henry Hay and Anna Rajkovic, NOVA Chemicals, led a discussion on PCR, the plastics recycling process, and PCR streams. Recycling is important and plastics waste is an issue due to the amount in landfills and waste streams. “Plastic waste is the issue, not plastics, and the cycle of plastics is not viewed holistically,” they said. People are unaware of the value of plastic beyond its first use. Plastics is 4.7 % of the MRF stream by weight and 2.4% of the GHC emissions reductions. 88% of plastics is HDPE and PET. Mixed plastic is .6% of the recycling stream including residue. People don’t tend to discard rotomolded products, which have a long life (i.e., kayaks and toys). He used three methods to evaluate PCR incorporation: dilution by dry blending; dilution by compounding; and stratification by inside layering.
“There is an impression that benefits of powder automation can only be experienced by large molders running millions of pounds of resin,” stated Rob Miller, RotoLoad. Even molders running several colors and very small runs can benefit from the automation of their resin process and implementation of Industry 4.0 principals. He presented case studies for rotomolders of all sizes. It is all about the data, how to collect it, and how to use it. The ROI is 2% targeted savings which equals $14K in annual savings.
Chelsea Pomo, RMI, presented a look at the Product of the Year Award received by Rotational Molding, Inc., for their Kymera Body Board. She went through the process from starting design, completion of tooling, which was cast aluminum with a semipolished finish on some areas. RMI addressed two issues during the troubleshooting phase: the stern tube port and the inconsistent shape of the hull. Once these issues were worked out, the part was removed from the mold and vacuumed into shape until the cooling was complete.
ARM Technical Director Dr. Nick Henwood addressed longterm Material Properties and why they are so important. Many rotomolded parts are subject to stress and are frequently designed and used in outdoor environments. “Rotomolders are in the durables business,” he said. Many times, rotomolded products have a life spanning decades. Most rotomolded parts are made from PE, a material that can be affected over the long-term, and the properties of PE can change, he noted. UV sunlight attacks both the base polymer and colorants. There is a potential for slippage of polymer chains and there can be a propagation of cracks from micro defects. Dr. Henwood recommended if long-term properties are deemed to be important in your rotomolding application, pay attention and test.
Thomas Steele, Solvay, discussed the need for UV protection of plastics including the effects of light on a rotomolded parts and factors affecting performance. He talked about how antioxidants perform and affect UV performance and other considerations when selecting a stabilization package. The expanding family of polyolefin grades and the flexibility of the rotomolding process have led to substantial growth in the marked for rotomolded products. Rotomolded products have special stability needs since they undergo multiple exposures to heat and shear during part production. The majority of products will see some exposure outdoors, and protection is needed to pre-empt degradation and prevent property loss, discoloration, and part failure.
Mike Haubert, Mosaic, said modern pigments are capable of achieving weatherable formulas in most shades. Testing should always be done on new colors in critical applications. Design of FDA colors in almost any roto application is possible with today’s technology, he noted.
Eric Maziers and Eric Laine, Total, discussed the characterization of long-term polymer materials’ mechanical characteristics, made from the test specimen of the structure. Institut Pprime, CNRS, ISAE-ENSAMA Université de Poiters, has worked together with Total Research and Technology Feluy, Belgium, for the past 15 years in the field of mechanical properties assessment of rotomolded parts. One of the main goals is to develop a method to characterize static and creep properties of rotomolded parts that are fast, accurate, and allow long-term FEA’s. The long-term protocol is based on this method, the shift factor is defined, afterwards the master curves at any temperature can be established. Next, is the reconstruction of the true strain-time curves, and finally the long-term creep behavior law will be established.
Dr. Waigaonkar, BITS, discussed the necessity of fracture mechanics in rotomolding. He described fracture toughness as an important material property and discussed the determination of fracture toughness and comparison of materials based on fracture toughness. The determination was that crack and crack-like flaws are nearly unavoidable and ignoring fracture mechanics can lead to
failure of parts at loads below what is expected using the traditional approach. Fracture toughness can be calculated using systematic experimentation. Increasing thickness of roto parts results in low fracture toughness. Fracture toughness can be used to compare materials, and it provides additional information regarding factors likely to initiate fracture so that steps can be taken to avoid it.
Hassan Riaz, NOVA Chemicals, discussed the existing role resins can play on product development. In their approach, they initially look backwards to determine what the molder’s needs are, and they’ve found there are four main drivers: productivity; cost reduction; manufacturing flexibility; and quality.
Alex Pritchard, a third-year Ph.D. student at Queen’s University Belfast, presented and overview of Rotomolding Foam Technology, a method for analyzing foam technology, study results, and the development of future foaming of the renewal energy section. The study represents a collaboration of 12 PhD students on large scale, multi-layer rotomolded structures.”
“Foaming is important due to its buoyancy properties, strength, and size scalability,” he said. The study is to better understand how foams develop in the low-pressure environment of rotomolding.
Kevin McTavish gave an overview on the welding process. He featured various components utilized in the repair of plastics.
Karem Akoul, QUB, discussed The Use of CAD and Virtual Reality to Optimize the Design and Build a New rotomolding Factory, a collaboration between Queen’s University Belfast and CPK Cases to study the benefits of using CAD and Virtual Reality in optimizing the layout and planning of a rotomolding factory. This forward-looking technology is germane to the future of rotomolding factories and product development. Once the product has been developed, further use benefits are: design of cooling; jigs, frames and chassis; balancing the machine arms, using the mass properties of CAD tools, and FEA analysis for heating and cooling optimization.
Rounding out the conference were video plant tours presented on Rotomold USA, RMI, and Plasticraft. A big credit to the following sponsors for making this event possible: Roto Polymers, NOVA Chemicals, Paladin Sales, Ferry Industries, DOW, ExxonMobil, Jerico Plastic Industries, Lyondellbasell, Stoner Molding Solutions, Rotomachinery, Entec, M. Holland, McCann Plastics, H. Muelhstein, Quantum Polymers, Nexeo Plastics, Rotoline, Orenda, Powder King, MAAG, Amerikart, Foam Supplies, Inc. Ingenia, Norstar Aluminum Molds, Polnac, Rock Lake Robotics, Trademark Plastics Corporation, Avantech, Axel, Brunk, CellMark, Chem Trend, Custom Plastics, Diversified Molds & Castings, Drader Injectiweld, Fabfour, Hightower Products, Lone Star Chemical, Matrix Solutions, McLube, Midwest Patterns, Narato, NIX, Persico, PPE, PSI Brand, Relance Mixers, Rotoloc, RotoWorld® Solvay, thintanks, VIVE, Rising Sun, and Fangda Roto.
Stay tuned and plan to attend 2021 Rotoplas to take place September 20-23 at the Donald E. Stephens Convention Center, Rosemont, IL.
Bring Your Spa Products to Life
Add sparkle and shine with Stone Effect Color Compounds!



Jerico’s complete line of aesthetic compounding materials brings a natural granite or stone look to your rotational molded products. Stone Effect specialty color compounds are designed for outdoor applications like hot tubs, lawn and garden accessories, and patio furniture. Use one of our popular Stone Effect colors or explore different color intensities using our line of Stone Effect color concentrates. Either way, we work with you to acheive your optimum color and design expectations every time!
Call or Click Today!
(330) 730-1140 | jericoplastic.com
Family-Owned and Operated Since 1997 Committed to Excellence in Rotational Molding Phone (330) 334-5244 JericoPlastic.com Fax (330) 334-9123 info@jericoplastic.com
ROTOMOLDING THE NEXT 10 YEARS All Aboard! We’ll take a look forward for our industry in a moment but first, a look back to the days when travel really was conducted in style! If you ever want to experience what it must have been like for the glitterati to travel in the 1920s, take a trip on the remarkable Belmond Orient Express. There Paul Nugent, MNOP are lots of short trips around Europe available but once a year they recreate the iconic trip from Paris to Istanbul (formerly Constantinople) using the original carriages. The smoke billowing from the steam engine has been replaced by diesel but the bonus is that they now have air-conditioning! One thing that has not been replaced, however, is the incredible atmosphere created on-board. The staff make this a superlative experience with butlers, haut-cuisine, bands to welcome you at every station and elegant service at every turn. We’d like to do it again but our fear is that we would spoil the memory – I think we’ll leave this one as a once-in-a-lifetime…
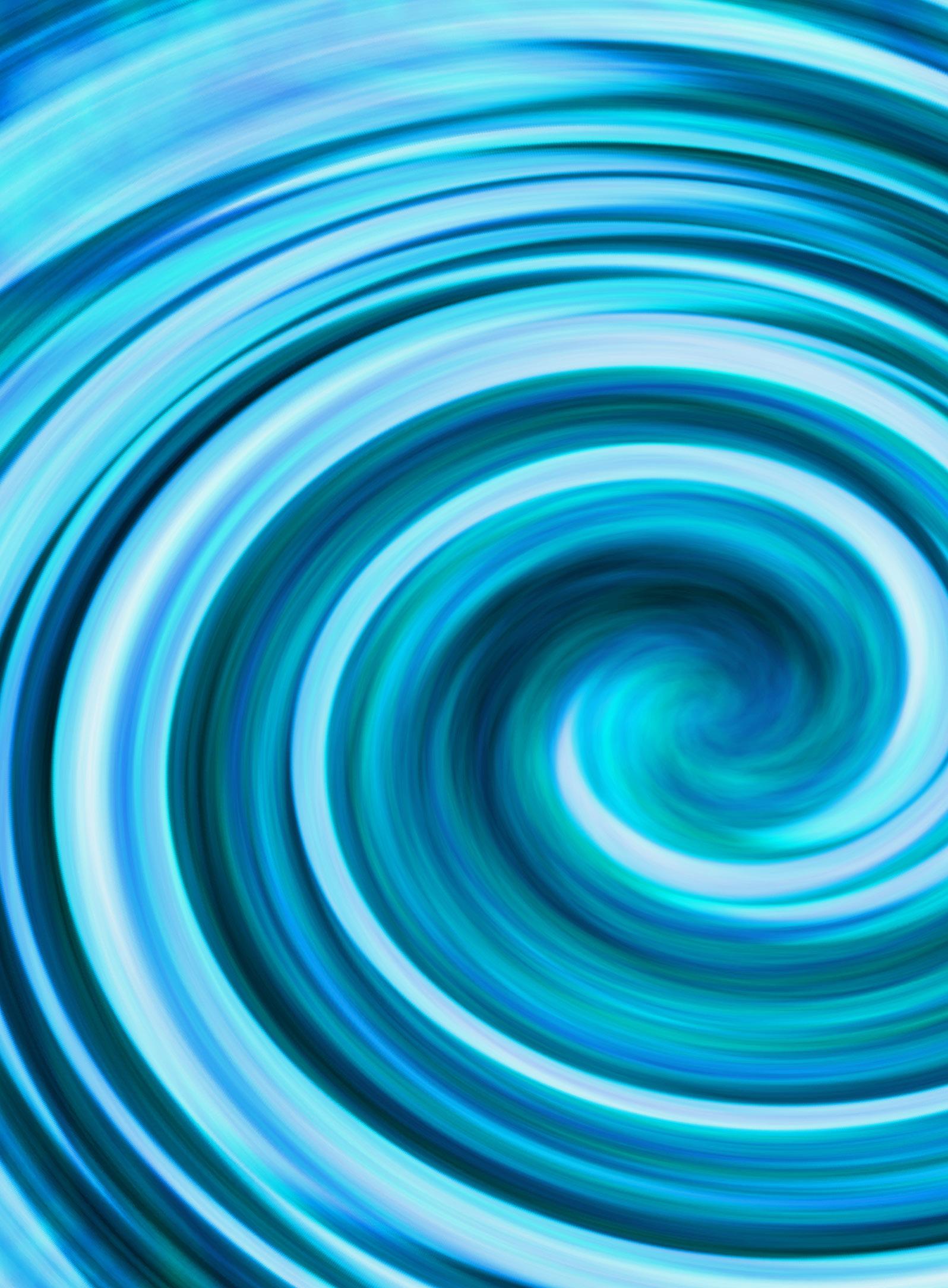
ROTOMOLDING THE NEXT 10 YEARS Vision 2020 Back in 2000, Prof. Roy Crawford penned a future review of technology for rotomolding. It is always difficult looking forward over such a long time-span (I have challenges with one year, never mind twenty) and the list of areas he covered was broad. From that list, here are twenty things that he hoped would come to pass and some observations about what has generally occurred. 1. Many More Materials Available There has been some (limited) expansion of the molders’ palette, most often within polyethylene but also in polyesters and with some improvement in polypropylene. However, much of the engineering polymer world remains off-limits to standard rotomolding. 2. Better Heat Transfer in Polymers This was a look at improving cycle times by having materials which can transfer heat more quickly – no real development has occurred in this area.
3. Use Granules Instead of Powder
Improved flow properties, reduced dust and higher bulk density has meant that Paul and Orla Nugent travelling onboard the Belmond Orient Express. there has been some growth in this area but limited commercial interest has meant that 6. Alternate Mold Materials generally it remains a niche area for rotomolding. Aluminum, steel, electroforming remain the core materials. 4. More Liquid Polymers Glass fibre and cast resin molds are used for prototyping or PVC, caprolactam, and polyurethane are still in use but cold-cure liquid systems but past attempts to broaden their use there have been no major additions to liquid systems in the in traditional molding systems have had limited success. industry. 7. Air Tight, Pressurized Molds 5. Foam Sandwich Structures This was a nod to the use of alternate gases and pressure as a Foam is still a major area of interest for many molders and is method for process control but there is limited need for this certainly used in a number of applications, particularly large approach and also considerable challenges in maintaining water tanks. There are practical issues in implementing and seals in a constantly expanding and contracting mold which controlling it which limit its use for most molders: many have means it has not been widely adopted. run trials but find it difficult to commercialize successfully 8. Fluid Heating and Electrical Molds and have quietly shelved the process. This is an area where there has been considerable progress,
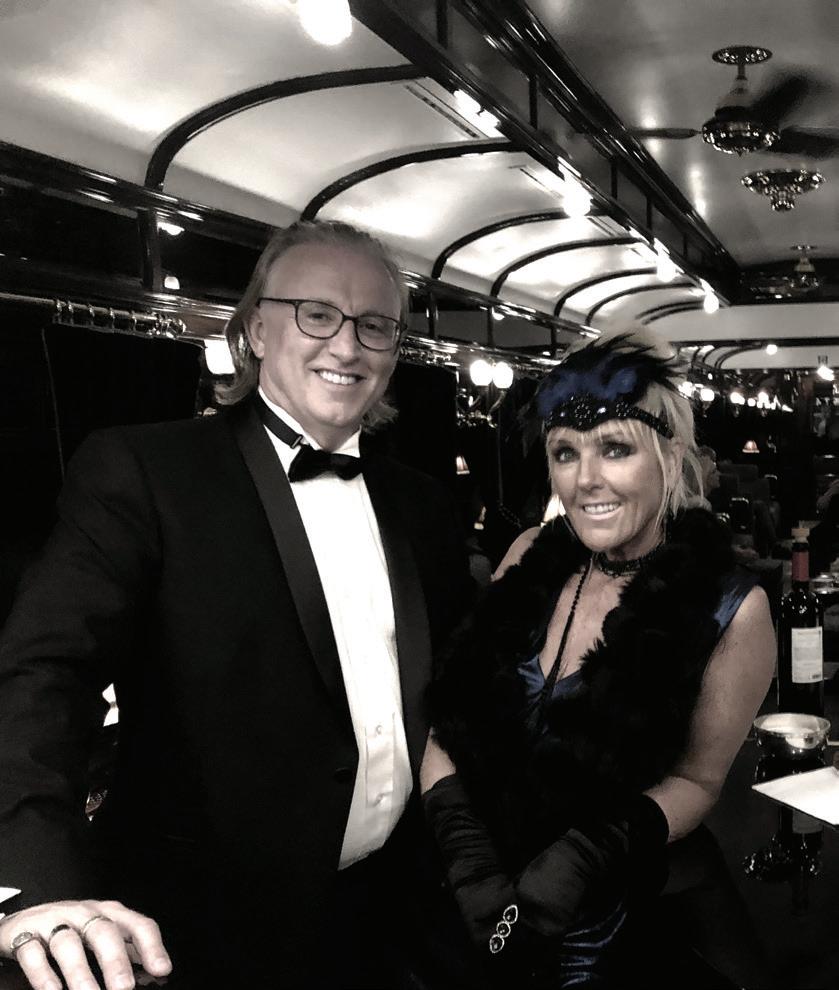
most notably in Europe. Automated equipment with heating channels or coils allows for new possibilities in controlling heat-flow and part wall thickness control.
9. Thickness Control Built into Molds
An interesting concept for including ultrasonic systems in a mold to observe wall thickness build-up as it occurs in real time. Some development work at The Queen’s University of
Belfast may show whether this can be made to be practical.
10. Multi-use Vents & Mold Atmosphere
Automated machines have the ability to incorporate systems on molds which would otherwise be affected by the general heating applied during traditional molding. Vents with multiple gas inlets and actuators for opening and closing in sequence with the internal temperature of the mold have been engineered by a number of suppliers.
11. Open Flame Machines Disappear
Projecting that the rotomolding machine base would be modernized at the end of a twenty-year period was one of
Roy’s hopes. The reality is that open flame machines are still very much in use and often represent an easy, low-cost entry point for new molders; there are also molders who favor the approach for certain lines of products.
12. More Automation – Ejection, Mold Handling & Material Feeding
Again, by concentrating heating only on the mold surface, automated machines allow for ancillary systems around the mold to operate within normal engineering temperature ranges. Ejector pins, powder feeding, molding opening, and closing mechanisms can all be added without concern for the effect of harsh heating and cooling environments on components.
13. Simplified Rotation – Single Axis
Still conceptual but fascinating. The idea of robotically programming a single axis to move a mold in a directed fashion which tracks the powder movement rather than having two fixed perpendicular axes could open up improved wall thickness control on even traditional machines.
14. Mold Temperature Control as Standard
Roy and I both had a keen interest in promoting process control ever since the introduction of the Rotolog system back in 1990. Our hope was that it would become the standard for all machines and operations – the reality has been mixed.
While many molders are aware of the benefits and use one of the many systems available today, the level of adoption has been lower than hoped and is still far from universal.
15. Conveyor Belt System – Sequential Molds with
Varying Cycle Times
This was a very interesting concept, perhaps inspired by similar machines which have been in operation in New
Zealand for many years, whereby molds would pass along a conveyor system through a long programmable tunnel oven with varying cycles customized to each in sequence. It has not been implemented fully as far as I am aware.
16. Reduce Cycle Times to 25%
A dramatic call to action to improve the efficiency and appeal
of the rotomolding process, as yet unachieved. Heating systems, material heat transfer properties and mold servicing challenges conspire against this goal although some molders have achieved considerable efficiency in the aggregate through the use of multiple molds and machines, material handling, and off-line mold handling which can almost achieve what Roy was hoping to see.
17. Full Process Control
Tracking part quality and all production steps has certainly been achieved on automated machines which can literally produce parts from start to finish at the push of a button; it has also been partially achieved on more traditional machines.
18. Suppliers to be More Innovative
The rotomolding supplier base is an engine for new ideas that the industry has depended upon for many years. Most rotomolders are small and without significant engineering capabilities which means development work in material, molds and processes is often ‘out-sourced’ to suppliers who can justify such work on the basis of multiple potential users.
19. Molder Responsibility to Drive Markets & Adopt
New Technology
This is the other side of the coin to the previous point – molders need to encourage suppliers by implementing their developments or helping refine them to make them more useful. This is particularly true for material development, new mold components, etc.
20. Unity as an Industry
Happily, there has been progress in this area with global cooperation between international associations with sharing of information and access to materials and events. There is also a good degree of interaction between molders in different regions sharing technology and even customers.
Backdrop
The rotomolding industry backdrop provides an insight into why some of these areas may have progressed more than others. Rotomolding generally has a two-tier structure wherein many molders are smaller and highly entrepreneurial with limited engineering capabilities and relatively low expectations for quality. Applying new technology is often outside the budget or comfort zone of what can frequently be a lean structure of an owner directly supervising machine operators’ in the factory. A smaller portion of the industry has better resources in terms of funding and engineering expertise and is therefore able to more successfully implement new ideas. Globally this split is perhaps around 90/10 but regions such as Europe have a higher concentration of top-level molders with a result that technology levels are generally more advanced there.
For the larger portion of the industry, available technology and the general approach to molding has remained largely unchanged over the last 20 years – same machines, same process, same issues (and still using open flame machines in some cases!). For the more technical molders, there have been good opportunities with automation and improved production techniques but the costbenefit decision to pursue them is oft-times limited by relatively
small order quantities and the complexity of handling rotomolded parts during demolding. However, in cases where large scale production is required the application of automated processes can be impressive.
Technical Development
shrinkage rates. Answer: uniformity of heating and cooling. For traditional machines, heat transfer rates across a mold surface can vary due to proximity to the heat source, speed of air-flow, and orientation due to rotation as well as design of the cooling system. This creates a temperature map across a mold during heating and cooling which leads to different Where to go next? Creating a wide-ranging list of ideas for the rates of thermal expansion in different parts of the mold future is possible: can we develop materials with the long-sought (parting line distortion), contributes to part thickness gloss and scratch resistance (with ease of molding and low-cost) variations (material is attracted to hot areas when rotation of that molders demand for retail applications? What about bio- the powder mass allows) and regions of the mold which can reinforced materials which manage to retain strength? Reactive cool more quickly or more slowly (polyethylene shrinks a lot materials which improve their properties after demolding? and is readily affected by cooling rates). For directly heated Easy direct mold powder feeding techniques? Teaching tools electrical machines, much of this can be overcome, although using VR systems for operators specific to new machines? Part cooling rates may still be an issue. Is it possible to design thickness detection during molding? Programmable rotation a more uniform system of heating and cooling across the controls for standard machines to improve powder distribution entire mold surface which would create a more stable mold and part thickness? The list can go and part environment? on endlessly and while there are many molders and suppliers actively 10 Years On looking at all aspects of the process, Looking forward then, some three areas have often struck me as The ROTO90% group will closing thoughts: A 90-10 fundamental: release agents, material fundamentals, and uniformity of continue to grow faster but industry split between the larger entrepreneurial base and heating and cooling. materials expertise will grow the smaller technical core will (a) Release Agents more in the ROTO10% group. endure: the ROTO90% group
A release system is essential for will continue to grow faster but molding any polymer and the materials expertise will grow chemistry involved at the mold- more in the ROTO10% group. polymer interface is perhaps A vast majority of rotomolded more complex during the rotomolding process than any parts will still be utilitarian but the creative designers and more other due to a combination of high temperature, polymer advanced molders will continue to delight the world with some reactions, additive interactions, oxidative processes, etc. The amazing products. process of mold release application is manual and often mis- Associations will continue to refine their 90/10 approach and understood and the build-up of deposits on the mold surface adapt to the positive and negative aspects of a remote life on-line. equally so. An industry initiative to study the interaction of Pressure will grow from the environmental lobby to reduce plastic typical release chemistry with standard additives and examine and energy use in general (both laudable objectives depending on alternate systems from other industries could bear fruit for the how they are applied within industries); rotomolders as individual process as a whole. companies and industry as a whole must have responses to the (b) Material Fundamentals negativity about plastic being nurtured in society. Benefits, durability,
Development of new materials is the key to the next circular processes, and lifecycle savings need to be stressed. generation of rotomolded products. This requires an The use of automation in rotomolding will continue to grow; understanding of the fundamental properties of polymers slowly. There are too many variables in running a rotomolding vs. the conditions they are exposed to during molding. The business for it to become the norm across the entire industry but rotomolding process is essentially a subset of polyethylene – there will be instances of genius created where product design, the properties and melting behavior of polyethylene defines volumes, and resources coincide. how parts are formed via sequential layers which fuse together Material development will still center on polyethylene, without any significant level of shear; any alternative material expanding the boundaries incrementally, although the use of must perform in a similar fashion to polyethylene in order to polyethylene as a base component for alloys may help expand into function in traditional rotomolding processes. A search for new property ranges. The main drive for specialty materials will materials which react differently and can perhaps be used in be driven by application specialists who are closest to the end-user multi-layer systems is warranted as well as continuing the and their needs and work directly with mid-level material suppliers path of using polyethylene as a base for alloying. with the resources and interest to pursue them. (c) Uniform Heating and Cooling Hopefully we will all be well in 2030 to take a look back and see
What do the following issues have in common? Parting line how things take shape on day 5188. Until we meet again next year. distortion; variable wall thickness; part warpage; and varying Day 8840