
6 minute read
The extreme makeover: DHL Stadium
The extreme makeover:
DHL Stadium
During the nadir of South Africa’s Covid lockdowns, the task fell to an intrepid team of architects, engineers, designers and system suppliers to meet an almost impossible task: to complete an extensive refurbishment of the hospitality areas of the DHL (Cape Town) Stadium in line with the closing of the former Newlands Rugby Stadium. They had to accommodate Western Province Rugby hospitality suite owners inside the newly enhanced Greenpoint-based stadiums, as well as various other sporting codes, notably soccer, and major concert organisers.
EBESA Gareth Griffiths
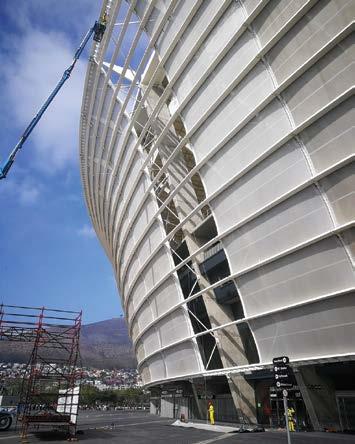
According to the architects, EBESA, the suite holders lease agreement at Newlands came to an end when WP Rugby signed the new agreement with DHL stadium. Newlands suite holders had first preference to sign a new lease agreement at DHL stadium. As the stadium is a multi-use stadium and host to big concerts, and soccer and rugby events, the suite holders have first right to attend events. Should they decline, the suite is then available for hire from the stadium for the specific event.
The DHL Stadium was completed in 2009 to meet the requirements for hosting the FIFA World Cup Soccer in 2010. The business plan at the time always envisaged that the stadium would become financially sustainable over time.
To achieve the objective, the City of Cape Town identified two critical commercial goals: the need to secure an anchor tenant, as well as being able to compete as a world-class stadium.
To secure the anchor tenant the completion of an additional 168 suites, and seven executive lounges, with a total hospitality capacity of 7 329 seats would be required. The agreement was signed with Western Province Rugby (anchor tenant).
The suite construction commenced in February 2020, and final completion was in April 2021.
Carina Marais, professional senior architectural technologist at EBESA, says that their client, Cape Town Stadium, was closely involved in all stages of design and during the construction period. To make the design modern, practical and sustainable, the team visited various large similar facilities around South Africa to benchmark and get insights from the appropriate stadium operators.
All in all, 20 594m² of CT Stadium floor area received this upgrade, a massive undertaking itself because fast construction methodology was required of the systems due to a limited time frame.
Whilst the existing business lounge area was quite large, the client required EBESA to design a flexible solution that split this area into three spaces and also add several new suites. This meant addressing the constraints of the existing floor plates, designing around that and allowing for streamlining of circulation of users from the main vertical access point to individual areas. Much planning went into food warming kitchens, refuse collection points and ablution facilities in line with the new upgraded layout.
Marais tells TO BUILD that the project team needed to operate and build lightweight.
“The existing floor slab was rated by the stadium’s original engineers to support a simpler load; simple outdoor stadium seats for the Football World Cup 2010 and subsequent events. After that event, the upper floors of the stadium were reconfigured as hospitality areas, bearing more weight. Cognisance of this had to be taken by the designers of the new layout, since the loading of these slabs was approaching their upper limit already.”
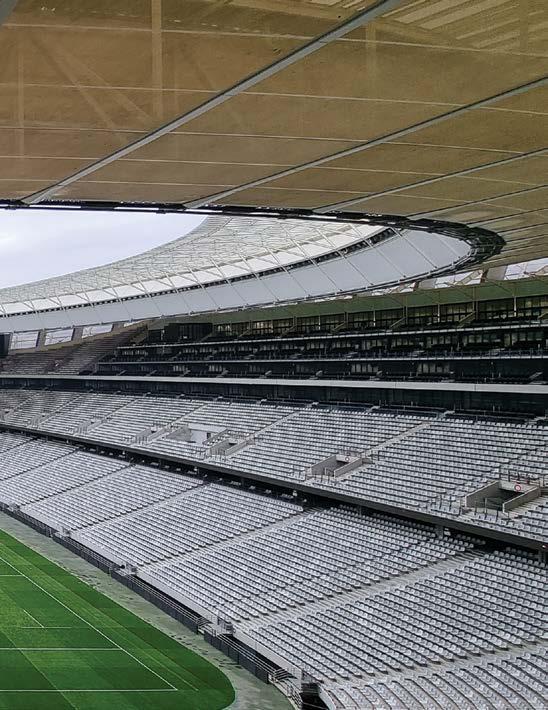
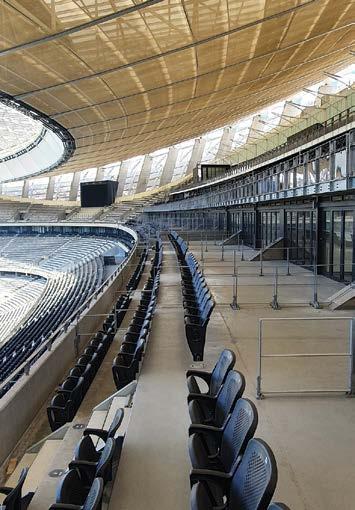
Structural challenges
All partitions and walls constructed at all refurbished and new levels had to be lightweight dry walling or similar. The design allowed for a drywall system which varies between 0.39, 0.49 and 0.59 kN/m2 of weight.
No screeds could be accommodated on levels 7 and 8. The existing waterproofing membrane on Level 6 and 7 had to be removed before new vinyl, tiled and epoxy floor finishes were installed. The imposed loading on the level 7 and 8 slabs had to be limited to 3 kN/m2.
Lightweight suspended ceilings were used for Level 6 to 8. A maximum weight limit of 6kg/m2 had to be achieved. Gypsum ceiling boards could only be accommodated in small quantities.
Level 7 and 8 were constructed by means of new steel columns positioned as far as possible in line and within the drywalls, and these were anchored off level 7, the former stadium roof.
A 150mm thick bond-dek floor system was chosen as a result of lightweight requirements (Level 8) and to achieve the 120min fire rating. The roof consisted of structural steel trusses and girders with purlins over to support the roof sheeting and access is only provided for maintenance purposes.
“The curtain wall installation was extremely challenging. This was due to the restricted work space between the edge of the slab and the façade membrane. Due to the membrane and the outward sloping nature of the stadium, the usual stick system installation off a scaffold could not be achieved. The installation was therefore altered to a fixed panel system that was lowered from the floor above and winched in towards the slab edge on the lower level,” explains Marais.
“The logistics required for the material handling to get materials into the stadium and onto the workspace on Levels 6,7 and 8, proved to be very challenging. The estimated weight of the heaviest load of material was to be 1.7 tons. All other building material would be grouped in the same or lesser loads. “The positions identified for the mobile cranes would also be used for the parking of the concrete pumps. The podium could only carry a certain load and care needed to be taken with the position and movement of construction equipment and trucks.”
Furthermore, the restrictions of serious lightweight specifications by the structural engineer, the 120min fire rating, and the requisite acoustic performance of the spaces had to be taken into account.
“A major system supplier to the project, Saint-Gobain, delivered expert advice at all times, and their team workshopped the drywall layouts closely with the architects to achieve the best and most cost-effective drywall solutions for the project. They then compiled a project-specific document with specifications, construction details and installation guides,” adds Marais.

Milestones achieved
From a project point of view, the Covid lockdowns delayed the works, but was only by 33 working days in total. It also impacted the materials supply chain, especially imported goods or locally manufactured materials during industry lockdowns.
Suppliers faced difficulty in fixing international pricing as well as various technical issues.
“The removal of the existing mesh façade to the stadium had to be done by the suppliers from Germany so that the client did not lose their guarantee on the material. It then had to be stored and re-installed by the same suppliers. They were also challenged by travel restrictions due to Covid.
“One of the highlights of this project and project team, was that as a collective we worked together and were able to complete the construction during 2020 Covid restrictions, and finish the project on time and within budget,” Marais concludes.

Project team
Developer: Cape Town Stadium Architect: Ebesa Architects Main Contractor: Grinaker LTA Quantity Surveyor: Narker and Associates Project Manager: Qunu Engineers & Project Managers Ceiling and Partitioning Sub-Contractor: Scheltema & Co and Fast Track Contracting (Pty) Ltd System supplier: Saint-Gobain - Ecophon, Gyproc and Isover.
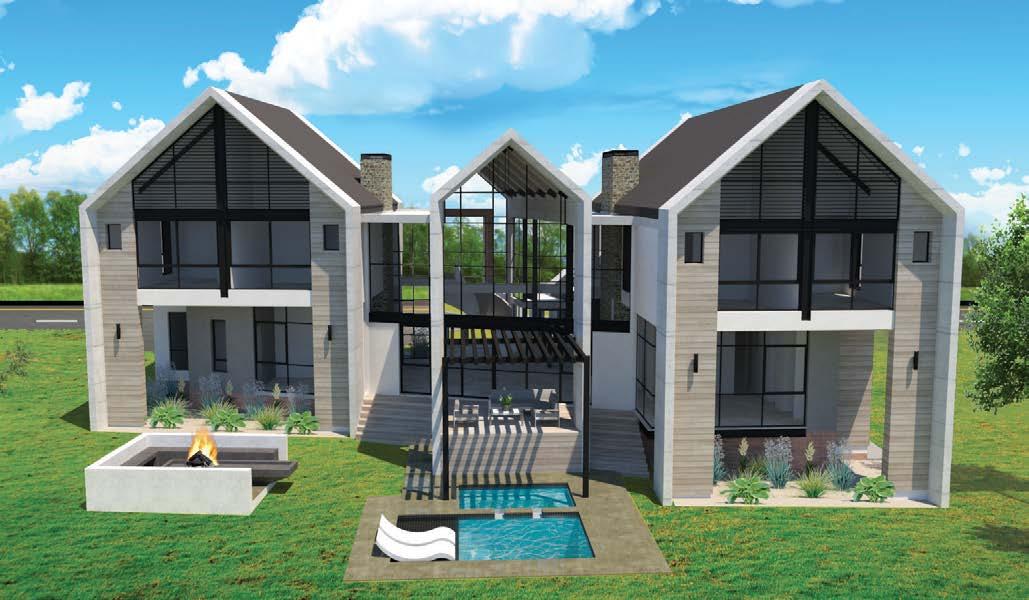
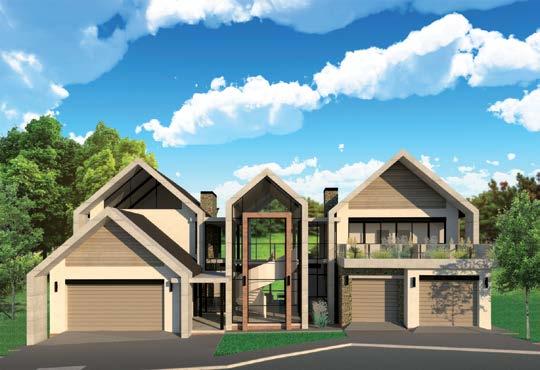