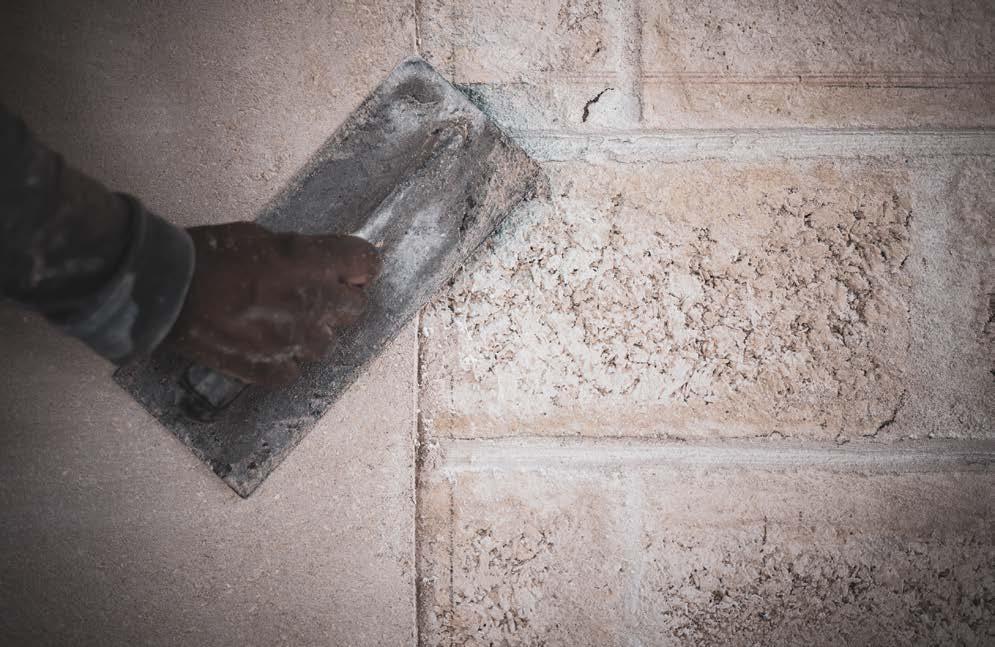
7 minute read
84 Harrington Street - A world first for the circular
84 Harrington Street -
A world first for the circular economy
A global first, 84 Harrington Street is officially the world’s tallest building constructed using hempcrete blocks and hemp building materials, say the owners, designer and materials provider. This makeover and partial rebuild of an existing building boasts one of the most expansive uses of hemp-based building block material in South Africa.
Gareth Griffiths, Wolf+Wolf and Afrimat Gareth Griffiths
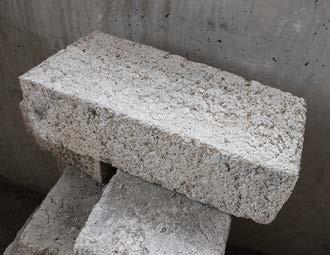
I was fortunate enough to be taken for an extensive tour of the building site, courtesy of project architect, ‘Wolf’ Wolf of Wolf+Wolf Architects, Cape Town. Wolf has considerable experience in designing buildings with hemp, from as early as the build of Tony Budden’s first ‘Hemp House’ overlooking the valley and beach in Noordhoek, Cape Town. Budden is a founder and active director of the developers of the new building, the Hemporium.
According to Hemporium and Afrimat Hemp, “84 Harrington Street is setting the benchmark for how to build a safe, carbon-neutral, multi-story building using hemp blocks and hemp systems.”
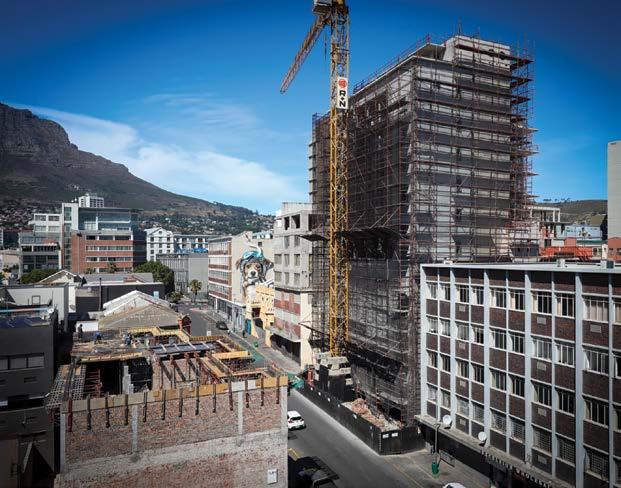
There is a massive increase in the global demand for bio-based construction, which is driven by the need for the reduction of CO2 emissions. Hemp construction is considered the gold standard for CO2 reduction in buildings.
Previously, hemp houses built in South Africa made use of hempcrete, but not as bricks. For a project of 84 Harrington’s scale, this was not feasible, and inspiration was taken from hemp blocks developed in Europe. The creation of hemp blocks is a viable way to commercialise hemp in the construction industry.
Wolf says that the hemp blocks specified were 110mm x 190mm x 390mm in size, comparable to a standard building block. Previously, ‘Hempcrete’, such as used at the Noordhoek Hemp House and elsewhere, was imported but now it is locally produced. Wolf is such a strong advocate of the material that he used it in the construction of his own studio, located in Cape Town’s environmentally sensitive heritage district, the Bo-Kaap.
Environmental benefits
The project, built on an existing brownfields site, involved the preservation of certain aspects of the legacy building on that site, notably the facade and some of the existing five floors. To this was added seven additional floors using conventional reinforced concrete (RC) framing technology. Locally produced Afrimat Hemp on site. Thermally Activated Building Systems (TABS) were added to the new RC members, with chillers at roof garden level, to introduce a measure of natural passive climate control. This is expected to be highly successful, in addition to the use of hemp interior walling, which helps keep a comfortable climate indoors by helping to absorb moisture from the air. The designers are confident that the results of this intervention will mean that only the restaurant, office and retail spaces will require HVAC. There is a chemical molecular-level affinity between hemp and lime, which lends the properties needed by the product to become a mainstream construction material. This means that it provides a strong internal walling material with better acoustic and insulation properties than conventional gypsum-board. The internal walls are cavity walls and services can run inside the cavity as per standard practice. Plastering is done using airplast, which is smoothly plastered and left exposed, therefore able to maximise CO2 absorption.
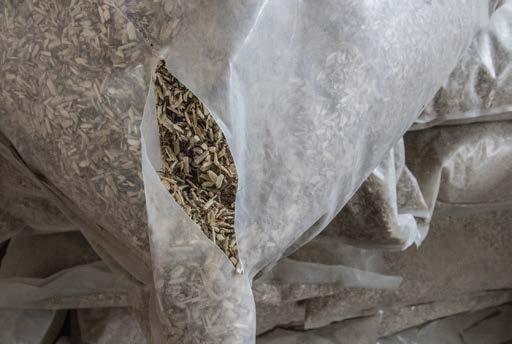
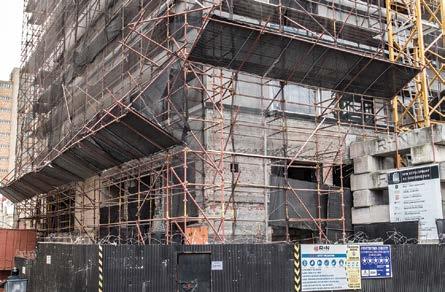
Facade and existing 5 floors. Double volume Hemporium, restaurant above.
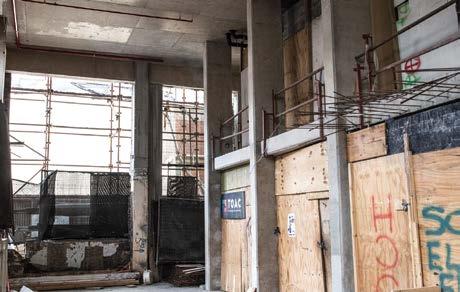
Careful preservation of structural elements retained as part of the ‘urban memory’
Construction began with siteworks on the original building including challenging and careful preservation of the structural elements that were to be retained as part of the “urban memory”, says Wolf.
The new ground level is to be breathtaking; a double volume ‘Hemporium’ which will serve the dual purpose of educating the public about the properties of hemp and renewable materials, while also being a shop and a ‘hemp museum’. Above this, overlooking the double volume lower ground, is the restaurant.
Hemporium, restaurant above
Above that is the planned hotel, which looks to follow the apartment hotel model. Fasttrack construction has begun on these suites, maxing maximum use of hemp, hempcrete plaster and pinus radiata cladding. The timber used was sustainably harvested during the moon phase approximately three days prior to the new moon of the three months preceding the winter solstice, from the building-owner’s own plantation on a farm in Constantia.
According to Boshoff (Bossie) Muller of Afrimat, “A hempcrete block is a non-structural infill block weighing 30% of conventional building material. It is naturally superior on acoustic and thermal insulation and has very good fire resistant properties. Because of the lightness of the block it is easy to build with and can be cut with a normal saw.
“Airplast, used on-site for plastering and bonding is a specially formulated limebased mortar and plaster for hempcrete construction. It’s got excellent bonding capabilities as a mortar and is used as a plaster to waterproof hempcrete walls. It also allows a hempcrete wall to breathe and naturally regulate humidity,” Boshoff says. “Regarding the product, lime and cement are made in similar processes. Lime burns at 950˚C versus cement at 1400˚C (less energy used at calcining stage). Lime relies on CO2 absorption to set. About 75 to 80% of CO2 burned off during the calcing stage is reabsorbed in the lifecycle of the product in situ. Our raw material is mined at our Robertson plant,” he adds.
It is this property that offers a huge advantage to the use of lime-based concrete and also hempcrete; it actually reabsorbs CO2 from the air (as long as it is left exposed to air). Meanwhile, the South African government has initiated a drive to create employment within the industrial hemp sector, therefore the timing to develop hempcrete-based construction materials is ideal.
According to Wolf: “The Government has issued the first set of permits authorsing local hemp cultivation on about 50 sites around the country. Some of those in the Western Cape are in Vredendal, Paarl and Stanford, to name a few.”
Sustainable timber, Airplast bonded and plastered hemp walls.
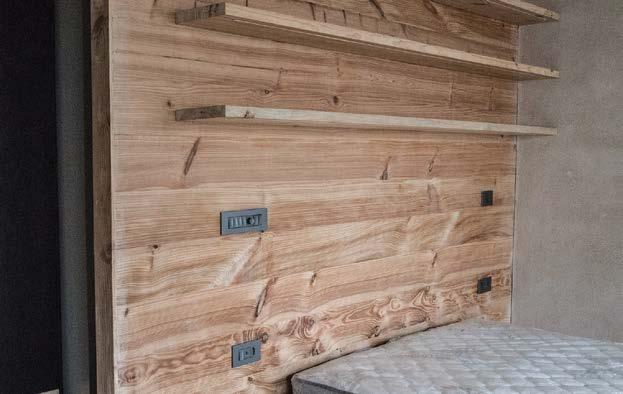
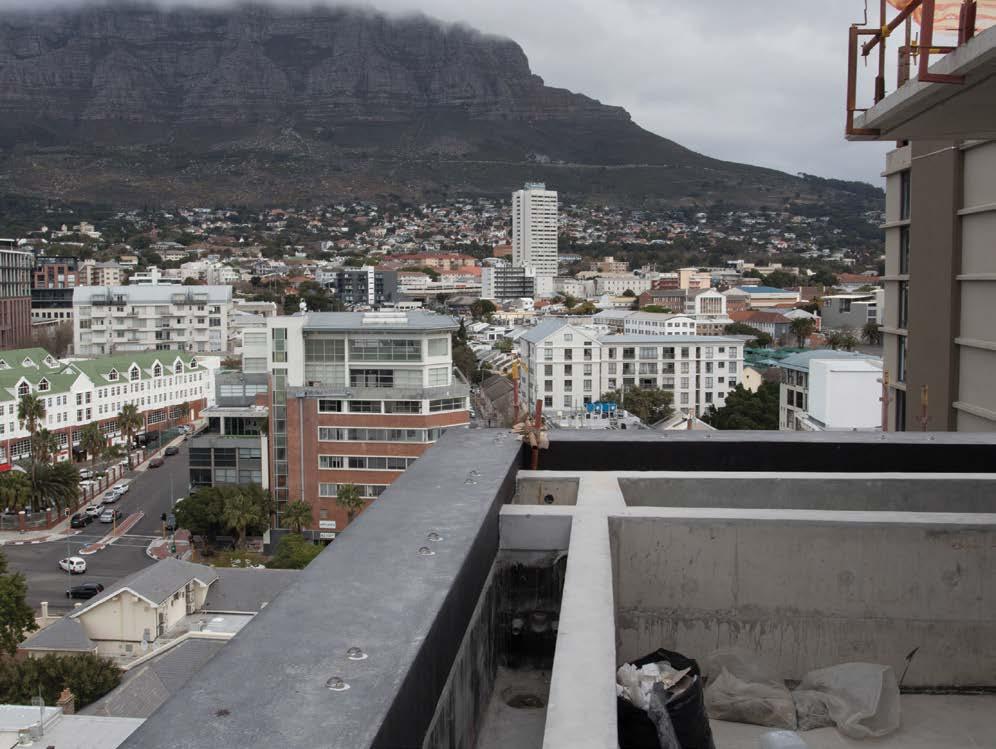
Topping out - view from higher building suite level over Table Mountain. All accommodation has hemp walling bonded and plastered with Airplast plus timber fittings made from sustainably harvested new-moon harvested pine.
Accolades
“I bought 84 Harrington in 2016, with the idea being that it would become the flagship Hemporium store, a steak restaurant, and house the ‘Hemp Hotel’, a place where people can experience living in a hemp-constructed space,” says Duncan Parker, Founding Partner and CEO, Hemporium.
“From a sustainability and eco-construction perspective, we wanted to take hemp construction in South Africa to the next level, while also contributing to the inspiring hemp construction projects being undertaken globally.
“We also believed that once licenses for the commercialisation of hemp in South Africa were issued, having innovative examples of what can be achieved with hemp would assist with leading the way for the fledgling hemp industry in South Africa,” he adds. “Afrimat, a mid-tier mining company, prides itself on having an innovative and entrepreneurial culture, always looking at global trends. A subsidiary, Afrimat Hemp, focuses on carbon-neutral construction and unlocking value in the industrial hemp sector,” says Boshoff Muller, Managing Director, Afrimat Hemp.
“Afrimat Hemp has developed its own formulated lime binder for hempcrete and is producing hempcrete blocks at one of its commercial block plants,” he adds
Project Team
Owner/developer: Duncan Parker / Hemporium (Pty) Ltd Architect: Wolf + Wolf Architects Contractor: R&N Construction Hempcrete and Airplast system supplier: Afrimat Hemp
The benefits of using hemp in a multi-story building:
• Hemp is 100% natural, CO2 absorbing, energy saving, and durable. • The superior acoustic performance ensures privacy between units. • Vapour-permeability: The ability of hempcrete to easily absorb and release moisture assists with regulating the buildings’ internal humidity, thus maintaining a healthy indoor air quality. • The lower density of the hemp blocks reduces the load of the walls on the foundations & therefore the cost of concrete. • Using hemp blocks reduces the
CO2 footprint of a building as well as its operational CO2 footprint.