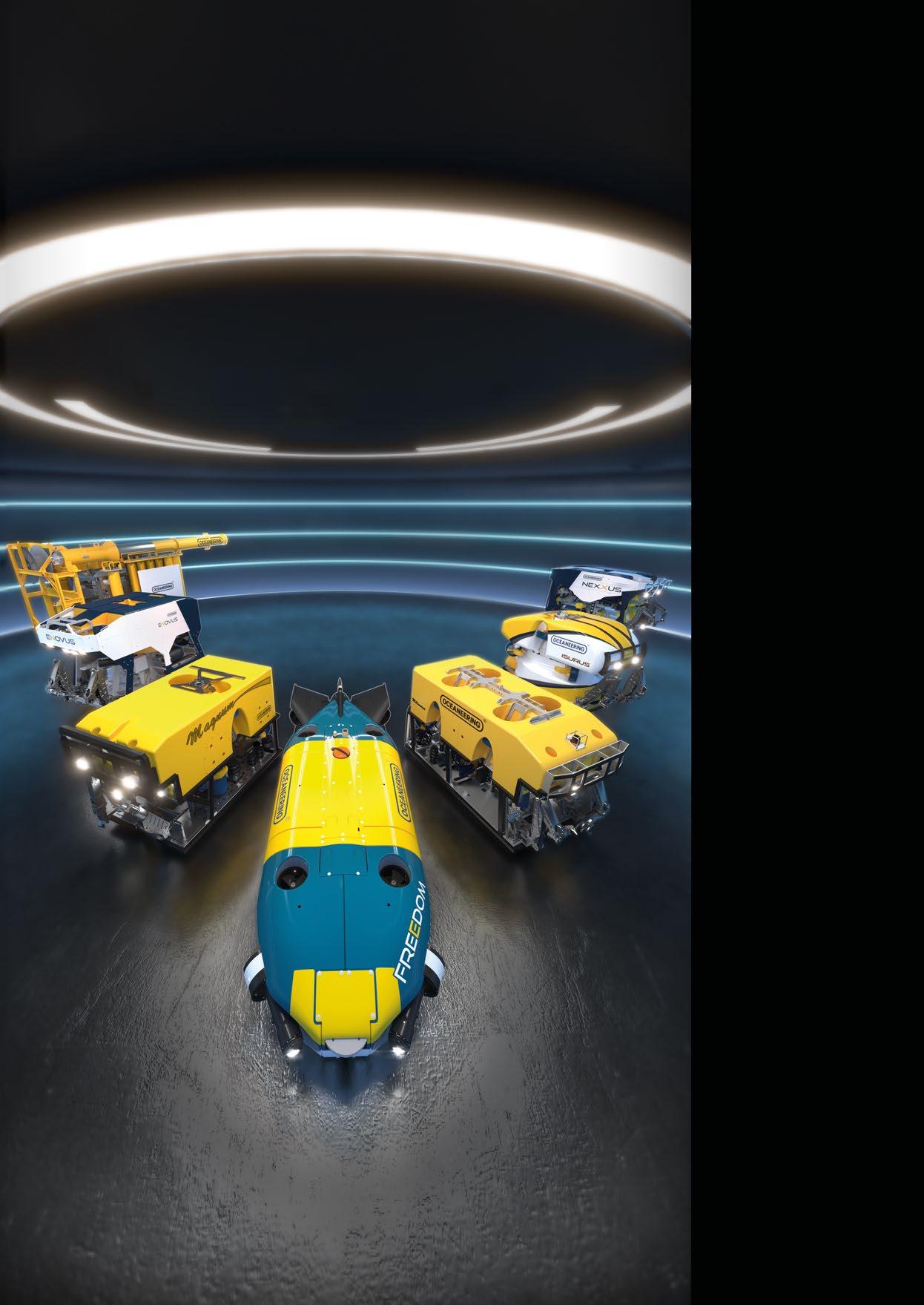
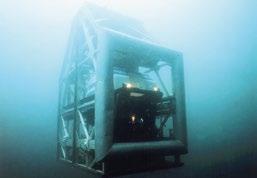


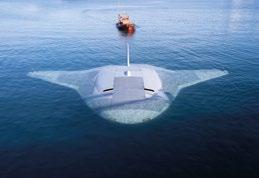

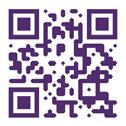

kongsberg.com/discovery
kongsberg.com/discovery
• Delivering data in most adverse conditions: underwater acoustic modems with advanced communication technology and networking
• Accurate USBL, LBL and hybrid positioning of underwater assets, navigation for divers
• Modem emulator and multiple cost-saving developer tools
• Sonobot 5 - the autonomous surface vehicle for bathymetry, monitoring, search & rescue, and AUV support
• Quadroin - the novel bionic AUV for surveys and monitoring
sales@evologics.com sales-us@evologics.com
06. Events Calendar & Welcome to Ocean Robotics Planet
08. The Evolution of Oceaneering
13. The Future of Electric Manipulators
17. Underwater ROV Operations in Mixed Reality Using the Apple Vision Pro
21. Facilitating a New Lease of Life in ROV Buoyancy
25. Overcoming the Challenges of Next-Generation UUVs with Exail Phins 9 Compact INS
29. Fleet Architecture Relies on a Mix of Manned and Unmanned Platforms
32. Poster: Manta Ray
35. Manta Ray to Support Long-Duration Undersea Missions: Making Waves in Autonomy
39. Uncrewed Maritime Systems Development Takes Center-Stage: Testing Unmanned Surface Vehicles is an International Endeavour
43. VideoRay: An American ROV Revolution – Part 2
49. Thirty Years of Inertial Navigation Evolution Puts Kongsberg Discovery at Apex of Motion-Sensor Market
53. Case Study: How the REMUS 300 UUV is Leveraging the Latest Technologies in Compact, Power-Efficient Research-Quality CT Sensors
56. Celebrating Collaboration Success on Renewables for Subsea Power
59. The Ten Years of Ocean Robotics
ISSN 2755-239X
EDITOR-IN-CHIEF
Richie Enzmann
COPY EDITOR
Will Grant
SALES DIRECTOR
Nick Search
DESIGN & LAYOUT
Milan Farkas
CONTRIBUTORS
Richie Enzmann, Edward Lundquist, George Galdorisi, Jon Robertson, Jonas Follesø, Marc Deglinnocenti, Mariah Pulver, Maxime Leroy, Stephen Sloan
SPECIAL THANKS TO
Amelia Smith, Audrey Leon, Bill Mallin, Bopha Le Guernic, Brian Storie, Charlotte Bulloch, Charlotte Sherwood, Chris Gibson, Colin McKinnon, Curtis Lee, Darioosh Naderi, Dawn D’Angelillo, Francisco Bustamante, Gill Vosper, Graceann Robertson, Guy Frankland, Heather Andrade, Helene Cox, Henning Langlete, Jack Rowley, James Colebourn, James DellaMorte, Jeroen Romijn, John Benson, Jill Bell, Jostein Jansen, Kieran O’Neill, Margo Newcombe, Marion Seyve, Matt Bates, Oda Ryggen, Paul Fletcher, Rob Howard, Sam Waltz, Sophie Hudson, Willard Balthazar
Base Materials
BEC Plastics
Blueprint Subsea
Blueye Robotics
C-TEM
DARPA
DeRegt Cables
Digital Edge Subsea
EvoLogics
Exail
Greensea IQ
HII
Hydro Group
Kongsberg Discovery
NBOSI
Northrop Grumman
Norwegian Offshore Rentals
Oceaneering
Popoto Modem
QYSEA
Saab Seaeye
SeaTrac
Silicon Sensing
Spectis Robotics
TechnipFMC
U.S. Navy
Valeport
Verlume
VideoRay
Zetechtics
AUGUST ONS 2024
SEPTEMBER
Stavanger, Norway (26–29 August 2024)
UNCREWED MARITIME SYSTEMS TECHNOLOGY – USA
Arlington, VA, USA (23–25 September 2024)
MTS/IEEE OCEANS
Halifax, NS, Canada (23–26 September 2024)
WINDENERGY
Hamburg, Germany (24–27 September 2024)
OCTOBER
SUBMERSIBLE OPERATORS GROUP
Oslo, Norway (8–10 October 2024)
FLOATING OFFSHORE WIND
Aberdeen, UK (9–10 October 2024)
GLIDER SCHOOL 2024
Gran Canaria, Spain (21–25 October 2024)
NOVEMBER
EURONAVAL
Paris, France (4–7 November 2024)
UNDERWATER INTERVENTION / WORKBOAT SHOW
New Orleans, LA (12–14 November 2024)
MAST
Adelaide, Australia (19–21 November 2024)
OFFSHORE ENERGY
Amsterdam, The Netherlands (26–27 November 2024)
2025 MARITIME RECONNAISSANCE & SURVEILLANCE TECHNOLOGY
London, UK (27-29 January 2025)
NAVY TECH
Helsinki, Finland (11-13 February 2025)
SUBSEA EXPO
Aberdeen, UK (18-20 February 2025)
UDT 2025
Oslo, Norway (25-27 March 2025)
OCEAN BUSINESS
Southampton, UK (8-10 April 2025)
COMBINED NAVAL EVENT (CNE)
Farnborough, UK (20-22 May 2025)
My name is Richie Enzmann. Allow me to welcome you all to the latest issue of Ocean Robotics Planet!
Dear Reader,
Issue 40 marks the 10th anniversary of our quarterly publication. This coincides with another anniversary: namely, Oceaneering being in business for a whooping 60 years! Some of you may know that I myself started off my ROV career with Oceaneering many years ago, so the company holds a special place in my heart. To mark these wonderful milestones, we have a line of Oceaneering vehicles on the front cover of the magazine, and you can read about the history of the company and its many achievements in more detail.
We also dive into a lot of interesting technologies in this issue, such as piloting Blueye’s X3 mini-ROVs using the Apple Vision Pro headset. This mixed-reality headset has incredible spatial mapping and passthrough technology, allowing the pilot to interact with the physical world even when wearing the headset. The Vision Pro uses cameras to record your surroundings before it overlays content in 3D and renders the scene onto the two 4K displays in front of each eye. I for one am very interested to see this tech’s transition from the experimental to the real world.
We also learn about the inertial navigation solutions that both Kongsberg and Exail have on offer. Then we continue with our VideoRay article where Captain Marc interviews Chris Gibson to learn more about the future of mini-ROVs and see what VideoRay has in store for us.
This issue’s centrefold shows a great image of the Manta Ray from Northrop Grumman. This is a huge underwater glider with extreme endurance and mission capabilities planned for military purposes.
Elsewhere in defence, Captain Lundquist looks at another interesting robotics technology: the Containerized Tethered Elevated Mast (C-TEM) shipboard tethered unmanned aerial system solution. The C-TEM opens up many use cases that are only limited by the warfighter’s imagination.
Finally, Jon Robertson from Saab Seaeye talks about the future of electric manipulators and suggests that electric manipulators could soon overtake the hydraulic ones.
You can read about all of this in more detail, and I hope you enjoy this quarter’s issue.
Best regards, Richie Enzmann
Working under high pressure DeRegt delivers
Working in oceanic depths under great pressure requires cables and connections you can rely on. At DeRegt Cables we provide outstanding technical solutions and custom-engineered cable solutions for the most challenging of circumstances. When you are raising the bar, we deliver the right solution.
• Top notch cable design
• Reliable cable manufacturing
• High end cable termination
• Thorough cable
•
Oceaneering International is celebrating its 60th anniversary in 2024. Co-founded by Mike Hughes and Johnny Johnson in 1964, the company started as World Wide Divers, headquartered in Louisiana. Hughes and Johnson, both from Tennessee, ventured into the oil and gas industry as divers before pooling resources with three others to purchase insurance and establish their own company. Hughes recalled, "It cost $2,000 to put down the initial premium for insurance. We thought each of us would put in $400. We formed World Wide Divers, which was a big name for five guys working out of a rented house in Bayou Vista (Louisiana)."
World Wide Divers later merged with Cal Dive and Can Dive in 1969 to form Oceaneering International. Cal Dive, founded by Lad and Gene Handelman, Bob Ratcliffe, and Kevin Lengyel in Santa Barbara, California, was known for its mixed-gas diving techniques. Ratcliffe invented the industry-standard diving helmet known as the Rat Hat. Can Dive, established by Phil Nuytten in Canada, was instrumental in developing several diving suits, including the Newtsuit, a one-atmosphere suit providing enhanced mobility and safety at greater depths.
The diving industry saw rapid advancements in the 1960s, with new technologies improving diver safety and efficiency. The Rat Hat, featuring lightweight fiberglass materials, reduced physical strain on divers and allowed for longer, more comfortable dives. It also boasted improved communication systems, crucial for coordinating complex underwater operations.
At an early Oceaneering board meeting, the need for further innovations was discussed. Hughes said, “Phil Nuytten had thought about the development of a capable one-atmosphere diving suit. We had started to understand with depth, costs, and risks go up exponentially. But with a suit like the JIM or the WASP, there would be no more need for decompression. You’d be limited to what you could do in the suit, but you could adapt to make it work better.”
Oceaneering acquired the JIM Atmospheric Diving Suit (ADS) in 1975, allowing divers to work safely at deeper depths without decompression. This suit revolutionized the deepsea diving industry. Oceaneering introduced the WASP ADS in 1978.
“But these suits had their limitations,” Hughes said. “Then water depths in oil and gas operations continued to increase, and it became necessary to go toward remotely operated vehicles.”
Oceaneering pushed into deeper depths, looking for the next big innovation in the marine industry. The U.S. Navy had developed a small ROV for observation, but Oceaneering saw potential for more. Johnny Johnson had written a company memo stating, “this is a development that we need to keep an eye on.” This would mark the beginning of Oceaneering's journey into ROV development. The acquisition of Solus Ocean Systems in 1984 not only brought in ROV systems, but expertise and talent as well.
Kevin McEvoy, who currently serves as Chair of the Board of Directors for Oceaneering, came onboard after the Solus acquisition. He said that the shift from divers to ROVs didn't happen overnight, it took a period of adjustment for the oil and gas industry.
“It took a long time because the infrastructure subsea wasn’t designed for remote intervention, it was designed for diver intervention. Oceaneering was well-known for its oneatmosphere business. But as work got deeper, divers couldn’t go that deep because of decompression protocols.”
McEvoy explained that it took about 15 years for ROVs to be fully integrated into the oil and gas industry. “There were a lot of improvements made in ROV systems in that time that made them more reliable and made oil companies more willing to depend on them.”
KEY ROV TECHNOLOGIES THROUGHOUT THE DECADES
1982 – The Hydra ROV: Hydra ROV established itself as a reliable vehicle for unmanned subsea intervention and would go onto serve as a backbone for Oceaneering’s work class ROV assets. The Hydra® ROV set a record dive to 7,002 feet in 1985 and 7,520 feet in 1987.
1993 – The Magnum® ROV: Built for deepwater operations, Magnum operates in depths of up to 10,000 feet and severe weather conditions. The Magnum Plus offers enhanced flight control in a smaller package and offering 170-hp, high-thrust, tophat- or cage-deployed system designed for subsea intervention and deepwater tooling.
1997 – The Millennium® ROV: Emphasizing reliability and standardization, the Millennium features higher horsepower and capabilities for increased depths and larger payloads. The Millennium Plus ROV features a dual-manipulator, 220-hp work class system with an enhanced thruster configuration.
2017 – Liberty™ Resident System:
A fully self-contained docking station for ROVs and AUVs, with 550 kWh of battery power for remote operations, communicating with an Onshore Remote Operations Center (OROC).
2017 – Freedom™ AUV: Entering commercial operations in 2023, the Freedom™ AUV offers the data resolution and completeness of coverage in a single pass usually only obtainable using an ROV, but with the speed and mission efficiency of a traditional AUV.
2019 – Isurus™ ROV: Building on the success of the Magnum® Plus by combining experience, reliability, and full work class capabilities with best-in-class performance in high-current environments, the Isurus™ ROV enables activities in severe current conditions and is ideal for renewables and high-speed ROV surveys.
ROV systems would go onto revolutionize the subsea industry by enabling remote inspections, maintenance, and repairs in hazardous underwater environments. Oceaneering is a leader in this field, operating the world's largest fleet of ROVs.
Oceaneering International has consistently pushed the boundaries of subsea engineering and technology, transforming industries from deep-sea diving to space exploration. The company's expansion into entertainment, aerospace, and other robotics-focused industries was initially driven by the
Oceaneering has been involved in notable underwater recoveries showcasing the company’s technological capabilities and expertise.
Andrea Doria: In 1981, 12 Oceaneering divers successfully retrieved the safe of the Italian luxury liner from 240 feet of water. The Andrea Doria sank in 1956 when it collided with the Swedish passenger vessel, the Stockholm.
RMS Lusitania: In 1982, Oceaneering launched a major salvage operation to explore and recover parts from the Cunard Ocean liner RMS Lusitania, which was torpedoed by German U-boats and sank offshore Ireland in 1915. The team recovered three of the ship’s four propellers from a depth of 305 feet off the coast of Ireland, providing insights into the wreck's state.
The Titanic: In 1986, Oceaneering supported the first manned exploration of the Titanic, providing technical support and ROVs to capture detailed images and videos of the wreck.
Liberty Bell 7: In 1999, Oceaneering located and retrieved the Liberty Bell 7 spacecraft from 16,000 feet underwater, nearly 38 years after it sank following splashdown.
desire to retain talented staff and leverage expertise in challenging environments. Oceaneering's successful projects, such as redevelopment of the Universal Studios' Jaws ride in the early 1990s and engineering and designing tools for NASA, demonstrated the company’s problem-solving capabilities and adaptability.
From its early days of diving innovations to becoming a leader in subsea technology, entertainment systems, and space systems, Oceaneering's relentless pursuit of excellence and commitment to solving complex problems have cemented its legacy as an industry pioneer. As the company continues to innovate, its impact across multiple industries remains influential and enduring.
Learn more about us at oceaneering.com/about/oceaneering-turns-60
John T. “Johnny” Johnson, co-founder of Oceaneering, passed away on June 27, 2024. Johnson, who retired in 2004, was known for his contributions to the company and the diving industry.
Of Johnson’s passing, Hughes said: “If I had to choose one person to occupy a foxhole with me and defend it in battle, it would be Johnny Johnson.”
Kevin McEvoy, Oceaneering’s Chairman of the Board and longtime employee, said: “Johnny was a consummate gentleman and very visible ambassador for the company throughout the Gulf Coast region, where he led the company’s business development and sales efforts for many years.”
Rod Larson, President and CEO of Oceaneering, said: “As a co-founder of World Wide Divers, Johnny’s contributions to the diving profession, the oil and gas industry, and Oceaneering cannot be overstated. His legacy and influence within the diving and ROV communities are a testament to his professionalism. Those who knew him best will remember him for his kindness, wisdom, and willingness to mentor others.”
Our condolences go out to Johnny’s friends and family, including his daughter Jennifer.
By Jon Robertson, Managing Director at Saab Seaeye
When it comes to the adoption of all-electric vehicles, one of the most significant roadblocks has been the development of an effective electric manipulator and tooling system. The prevalent thought was, "If you need hydraulics for manipulators and tools, you might as well have hydraulic propulsion".
The journey of electric manipulators within the ROV (Remotely Operated Vehicle) industry is marked by numerous challenges, primarily due to their limitations in power density compared to their hydraulic counterparts. Designing electric manipulators that can meet the rigorous demands of subsea operations has been no small feat, requiring high power density, which in turn has driven up costs and complexity. However, recent advancements are beginning to align technology and cost, leading to more reliable and robust products.
The task of surpassing the capabilities of hydraulic manipulators, which have long been the industry standard, has necessitated innovations that offer not just comparable but superior performance. The sheer power of hydraulic systems has historically made them the preferred choice for underwater manipulative tasks, further complicating the adoption of electric alternatives. Enter the Seaeye eM1-7 Electric Manipulator, a ground-breaking development poised to reshape this narrative.
The eM1-7 Electric Manipulator is a testament to how far we've come in the field of electric manipulators. It combines advanced features with meticulous engineering to redefine what these devices can achieve. At its core, eM1-7 Electric Manipulator incorporates compact modular electric joints, revolutionising arm control with impressive lifting capacities. It can handle up to 122 kg at a full 2-meter extension and a staggering 454 kg at minimum extension. Constructed from sturdy yet lightweight aluminium, this manipulator is built to last without sacrificing agility. Weighing 116 kg in air and 84 kg underwater, it operates seamlessly at depths up to 4,000 meters, with options extending to 7,000 meters.
One of the eM1-7 Electric Manipulator's standout features is its intelligent power management system, which efficiently regulates power consumption and handles regenerative power during free-fall loads. Its versatile functionality, including six degrees of freedom and adaptable jaws, provides exceptional dexterity. This versatility, combined with an increased range of motion, significantly enhances the manipulative capabilities within the industry.
The eM1-7 Electric Manipulator is more than just a technical marvel; it represents a forward-thinking approach to underwater operations. Its sophisticated control system sets the stage for increased automation, reducing the reliance on operator expertise while ensuring consistent and reliable task execution. This reduces the need for human intervention in hazardous underwater environments, significantly minimising the risk to human operators.
Precision in position and force feedback, coupled with consistent performance and intelligence, points towards a future of advanced manipulator arm control. Saab UK’s vision
extends to integrating subsea exchangeable end effectors and force-sensing capabilities, making the manipulator even more adaptable and responsive to various tasks and environments. The inclusion of advanced object detection systems signifies a potential shift from manual control and supervised autonomy to fully autonomous operations—a historically challenging milestone in the industry. This adaptability and readiness for future upgrades highlight Saab UK’s unwavering commitment to continuous innovation and the safety of human operators.
The eM1-7 Electric Manipulator heralds a new era for electric manipulators in the evolving landscape of underwater robotics. Its advanced features and forward-thinking design address the long-standing challenges of power density and operational reliability, offering a glimpse into a future where electric manipulators are not just a viable alternative to hydraulic systems, but a superior choice. As we continue to innovate and push the boundaries of what is possible, the eM1-7 Electric Manipulator stands as a beacon of progress, signalling a bright future for the industry.
Jonas Follesø, Chief Technology Officer at Blueye Robotics
The introduction of the Apple Vision Pro headset from Apple opens exciting new possibilities for underwater operations in mixed reality. We have just scratched the surface for this technology, and with this article we will share our first impressions from using the Apple Vision Pro for ROV operations and demonstrate what the future might hold.
Since day one, the Blueye underwater ROVs have been operated using iOS and Android devices. This has allowed us to leverage hardware and software innovations in the iOS and Android ecosystem. Blueye customers can choose from a large selection of compatible devices, from mobile phones to rugged tablets and large-screen setups.
Since the first prototypes of the Blueye underwater ROV, our team has experimented with various digital headset alternatives. The original idea was that the headset would be your digital diving mask, offering an immersive view of the underwater world.
For the Blueye Pioneer's initial release in 2017, we partnered with MovieMask (now known as DroneMask) and bundled their headset with our underwater ROV. The MovieMask is a simple device that allows you to insert your mobile device into a headset with lenses that give the impression of looking at a much larger screen. The MovieMask also blocks out light, removing the problem of hard-to-read screens in bright sunlight.
However, the MovieMask headset has some significant drawbacks, perhaps the biggest being its lack of spatial awareness when worn. With the headset on, you cannot see your surroundings. Improvements in device hardware, with brighter and better screens, have reduced the problem of using mobile devices in direct sunlight. Hence, the use of MovieMask to mitigate this is no longer that relevant.
The Apple Vision Pro is a mixed-reality headset with incredible spatial mapping and passthrough technology, allowing you to interact with the physical world even when wearing the headset. The Vision Pro uses cameras to record your surroundings before it overlays content in 3D and renders the scene onto the two 4K displays in front of each eye—all in less than 15 milliseconds. You interact with the device using eye tracking, simply looking at elements and selecting them using gestures such as pinching your fingers.
The Apple visionOS is based on iPadOS and can run most iPad apps out of the box. This means that both the Blueye App and the Blueye Observer App are already available for the Apple Pro Vision. Running the Blueye App on Pro Vision gives you the impression of controlling the drone on a crisp 4K screen as big as you’d like.
You can configure a virtual control center with multiple screens showing sonar imagery, maps, mission planning, reference documents, or your dive plan. The screens can be anchored in 3D space and you can move around with the headset and interact with the physical world.
The Pro Vision is not a peripheral to the iPhone or iPad but a self-contained unit with a high-performance M3 chip onboard. The Blueye App runs directly on the headset, and you connect an Xbox Controller or other compatible game controller to operate the drone.
The Vision Pro is the first version in a new product category from Apple. Over the years, we can expect product improvements in battery life, weight, ruggedness, price point, and other aspects of the device. However, already in its initial version, the Vision Pro offers exciting new possibilities for better, more immersive underwater operations in a compact form factor.
We believe the Vision Pro headsets can be used as compact, portable virtual control center for our underwater drones. Large, dedicated screens for sonar, video, maps, and telemetry that can easily fit inside a backpack.
All the functionality in the scenario demonstrated in this article, and video is done using hardware and software that is commercially available today. No prototypes or beta versions were used.
The Vision Pro will help spatial computing and mixed reality become more mainstream and increase innovation in the field. The other big player in the mixed reality space, Meta, has recently announced that they are opening their mixed reality headset operating system to third-party hardware makers. The Meta Horizon OS is based on Android, and even though you cannot run all Android apps out of the box today, there is a possibility that the Blueye Android app might also become available on mixed- and virtual reality headsets in the future.
Oculus Multibeam Imaging Sonars
High
Stephen Sloan, Head of Commercial at Base Materials
The global offshore remote operated vehicle (ROV) market is burgeoning. But, with a growing demand for deep sea exploration, ever-increasing operational costs, and more stringent environmental regulations, ROV owners and operators face significant challenges. As a result, ROV owners and operators must future-proof the performance of their vehicles efficiently, cost-effectively, and sustainably.
ROV buoyancy modules are mission-critical equipment for the facilitation of subsea exploration, from offshore energy (renewables and oil & gas), and oceanographic research, to defence applications, search and rescue vehicles, and more. Taking a whole-life approach ensures high-quality buoyancy modules perform as required in situ for their intended service life. That’s because a whole-life approach to ROV buoyancy modules – one that realises the value in repairing
and refurbishing old, damaged, and worn modules, rather than simply buying new – will significantly reduce capital expenditure, optimise return on investment, and decrease waste to landfill.
In short, ROV buoyancy modules that perform for the duration of and beyond their intended life are both a better investment and better for meeting net-zero targets.
The rapid pace of technological advancements in subsea equipment requires continuous investment to stay competitive. But on average the cost of a new set of modules to an ROV owner or operator can be anywhere between 64,000 to 1.3 million USD and above for specialist applications.
This represents a significant investment which, caused by ever-advancing subsea buoyancy materials and manufacturing processes, simply isn’t a feasible option for all. Many ROV owners and operators already have strained capital resources and are exacerbated by economic volatility in industries like oil & gas, which heavily utilise ROVs.
As a result, owners and operators must consider repairing or refurbishing existing ROV buoyancy modules as a more costeffective alternative to purchasing new ones. This ensures that they continue to meet original specifications and operational industry-recognised standards. Extending the service life of existing equipment, which is as critical across the subsea buoyancy sector, as it is any other, presents the opportunity for owners and operators to increase return on expended assets.
Repair and refurbishment services offered by leading buoyancy module materials manufacturers, which include anything from repairing scuffs to recoating the protective skin to enhance abrasion and impact resistance, can help to
reduce capital expenditure by as much as 40%. This represents a significant opportunity to maximise operating profits and optimise return on investment.
One essential consideration that can determine whether repairing and refurbishing your existing modules will maximise return on investment, is whether your existing buoyancy modules are manufactured from a material that is fit for the purpose. For instance, macrosphere-based syntactic foam systems were used to create what are now legacy, lower-cost buoyancy module systems. However, these materials generate a relatively low buoyancy per cubic metre; are highly prone to significant loss of buoyancy from minor damage; and are difficult to effectively refurbish and repair due to the nature of their manufacture.
As a result, while macrosphere-based syntactic foam systems are still used today for shallow depths or large volume applications, and where they are less likely to be damaged in operation – for example, on a trenching ROV – the majority of the ROV industry utilises pure syntactic foam systems which are far more durable. Furthermore, when they are repaired and refurbished, they enable greater value to be realised.
In addition to the cost case for repairing or refurbishing today’s syntactic foam ROV modules, the process of doing so is approximately 25 to 30% quicker than the manufacture and delivery of new modules. This is an essential consideration,
particularly for explorations in remote environments. This enables ROV operators to potentially reduce overall operational costs by refurbishing existing modules where possible, rather than buying new modules at a premium. One way to combat the potential downtime caused by the delivery of new modules, particularly for time-sensitive projects, is having a refurbished set on-site as a spare.
From a monetary perspective, the benefits not only lie with owners and operators. Repairing and refurbishing existing ROV buoyancy modules offers ROV manufacturers a valuable secondary revenue stream. By reselling refurbished vehicles, manufacturers can leverage their existing systems to tap into the demand for a more cost-effective alternative to a completely new ROV.
This diversification can mitigate the impact of current and future fluctuating sales of new units, providing a steady income stream even during market downturns. This helps to build a more resilient and diversified business model, that can enable manufacturers to become a one-stop-shop for both new and refurbished equipment. While ROV operators benefit from a solution that removes the need to buy new and the required associated investment.
Sustainability is no longer an afterthought. It is an increasingly important consideration in the ROV space for manufacturers, owners, and operators alike, driven by a combination
of motivational drivers, including reputation and a commitment to reducing emissions and adapting to the impacts of climate change as part of The Paris Agreement.
The journey towards net zero carbon emissions has seen a growing emphasis on the development of ROVs that have a minimal impact on the environment, whether from the utilisation of recyclable materials, low energy production processes, or the incorporation of electric and hybrid propulsion systems.
However, for ROV buoyancy modules specifically, there are significant sustainability benefits to be realised in prioritising the maximisation of the service life and reduction of the replacement of modules, ahead of short-term performance. This is because in addition to reducing capital expenditure, giving existing modules a second life where possible – which can be as many as five years of further use – reduces waste to landfill. So much so, if even just 1% of the current ROVs in operation globally were decommissioned, this would represent approximately 30 to 40 cubic metres of syntactic foam going to landfill.
A global ROV Original Equipment Manufacturer (OEM) recently turned to Base Materials to extend the operational life of its customer’s 15-year-old ROV.
The company’s refurbishment and repair service extended the service life of an old, damaged, and worn set of buoyancy modules by up to five years while reducing waste to landfill and removing the need to purchase new modules.
In just a matter of eight weeks, from its 10,000 square feet state-of-the-art production facility in Birmingham, UK, Base Materials replaced module metallic inserts to allow the installation of new equipment to the ROV module, and enable attachment onto a new frame. Additionally, it added customer stencils and markings to the ROV, along with nonslip coatings on the buoyancy modules to ensure the safety of operatives walking on the equipment.
Following the successful replacement of the modules, the OEM and their customer have requested Base Materials to refurbish and repair a second set of buoyancy modules.
ROV buoyancy modules are mission-critical equipment, and is imperative that ROV manufacturers, owners, and operators realise the various economic and environmental benefits of giving old, damaged, and worn modules a new lease of life, rather than simply buying new.
From optimising return on investment to meeting organisational net zero targets and more, there is undeniable value to be realised for all in enabling ROV modules to perform for the duration of their intended life and beyond.
Maxime Leroy, Subsea INS Product Manager – Exail
The rapidly advancing field of unmanned underwater vehicles (UUVs) presents a series of unprecedented challenges that demand cutting-edge technological solutions. As these next-generation UUVs embark on increasingly complex missions—ranging from intricate geophysical surveys to critical underwater inspections—they are encountering a unique set of obstacles. Precision navigation in harsh environments; stringent Size, Weight, and Power (SWAP) constraints; operational versatility; and reliable data processing are just a few of the hurdles that need to be addressed. In response to these demands, Exail has introduced the Phins 9 Compact Inertial Navigation System (INS), designed to meet these challenges with unmatched efficiency and performance.
Navigating complex underwater terrains—frequently lacking external references—while conducting surveys demands an INS that delivers exceptional accuracy. UUVs must operate effectively in environments that range from deep-sea abyssal plains to rugged underwater landscapes, with varying currents, depths, and terrains that complicate navigation. Maintaining
accurate positional and attitude data in these conditions is critical, not only for the success of the survey mission but also for ensuring operational safety and reliability.
The Phins 9 Compact INS, with its high-performance FiberOptic Gyroscope (FOG)-based Inertial Measurement Unit (IMU) and advanced accelerometers, is designed to tackle this issue head-on. With an impressive heading accuracy of 0.07° and pitch & roll accuracy of 0.01°, it delivers exceptional reliability and precision. The system’s DVL-aided position accuracy of 0.1% TD ensures that UUVs can navigate accurately and deliver survey-grade measurements, even in the most challenging conditions.
The compact design of modern UUVs necessitates solutions that are both lightweight and power-efficient. Traditional navigation systems often fall short of meeting these requirements without compromising on performance. The Phins 9 Compact INS addresses this challenge by offering a remarkably small footprint and power consumption of less than 7 watts. This SWAP efficiency is crucial for UUVs, which must maximize their payload capabilities and operational endurance. By integrating the Phins 9 Compact, UUV manufacturers can enhance their vehicles' performance, while maintaining the necessary space for additional equipment, and extending mission durations. The Phins 9 Compact represents a significant advancement in subsea navigation technology. It is an ideal solution for new generation AUV manufacturers, and e-ROV operators looking to save power without compromising on data processing capabilities.
Operational versatility is another critical requirement for modern UUVs. These vehicles are used for a broad spectrum of tasks, from survey-grade seabed mapping, to intricate inspection and repair operations. The Phins 9 Compact is engineered to adapt to diverse applications, providing reliable performance across different mission profiles. Its versatile design ensures that it can be deployed effectively for coastal and offshore surveys, defense applications, and beyond. This means that it’s a valuable asset for UUV operators facing a range of operational demands.
Effective data processing is critical for real-time navigation and decision-making. UUVs need navigation systems that can deliver accurate data while conserving power resources. The Phins 9 Compact INS excels in this aspect, providing high-precision data essential for operational adjustments and real-time decision-making. Its reliability further enhances its value, particularly for long-duration missions. This ensures that UUVs can operate effectively in remote and challenging environments without frequent maintenance or risk of failure.
Phins 9 Compact is a key component of Exail’s renowned Phins Compact series INS, which has established a solid reputation, and now equips over 80% of autonomous underwater platforms worldwide. Among its recent successes, the Phins 9 Compact has been selected by Bedrock to enhance its new AUV, a modular platform designed for rapid deployment in geophysical surveys. This INS is designed to enhance the AUV's navigational accuracy and operational efficiency, delivering precise measurements for mapping and data collection, while effectively addressing Total Horizontal Uncertainty (THU) and Total Vertical Uncertainty (TVU).
Charles Chiau, CTO and co-founder of Bedrock, commented, “The INS was crucial in tackling uncertainties and performance challenges for our AUV. We needed an INS solution that could meet requirements in form factor, power, support, compactness, accuracy, and performance, and Exail's Phins 9 Compact INS perfectly aligns with these needs.”
In a similar vein, Exail’s Phins Compact C3 INS has been chosen by Eelume to equip its new S-Series all-terrain AUVs. These AUVs, engineered for navigating challenging underwater terrains, benefit greatly from the Phins Compact C3 INS’s high accuracy and robust navigation data, facilitating efficient exploration, and monitoring in complex environments such as hillsides and under-ice areas.
Thomas Nygaard, CEO of Eelume, stated, “We needed a compact navigation system that fits with our eco-friendly approach and delivers exceptional navigational accuracy and agility for missions in intricate underwater terrains. Exail's Phins Compact C3 INS meets all of these criteria.”
Additionally, the Phins Compact C3 INS has demonstrated its value in Alseamar’s Murene Diver Propulsion Vehicle (DPV). By significantly enhancing navigation accuracy and stability, this INS enables divers to maintain precise positioning and course stability, which is vital for intelligence and offensive missions.
In conclusion, Exail’s Phins 9 Compact INS is a groundbreaking solution designed to tackle the pressing challenges faced by next-generation UUVs. With its advanced technology, compact design, and exceptional performance metrics, the Phins 9 Compact addresses the need for reliable navigation, survey-grade measurements, efficient SWAP management, operational versatility, efficient data processing, and robust reliability. Its successful integration into cutting-edge UUV platforms highlights its transformative impact, driving advancements in subsea exploration and operational efficiency. As UUVs continue to push the boundaries of underwater capabilities, the Phins 9 Compact INS stands ready to meet the demands of this evolving field.
Containerized Tethered Elevated Mast (C-TEM) Drone Extends Line-of-sight Communications for U.S. Navy’s Hybrid Fleet
By
Both manned and unmanned surface ships of the U.S. Navy’s “hybrid fleet” will be able to extend their communications range and improve situational awareness using tethered drones. General Dynamics Mission Systems has been contracted by the Navy to deliver the Containerized Tethered Elevated Mast (C-TEM) shipboard tethered unmanned aerial system solution. The company is partnering with Dragonfly Pictures, Inc (DPI)., a small business based in Essington, Pa., for the C-TEM program. The Navy has ambitions of a large fleet of unmanned large and medium surface vessels to augment its surface force.
According to a July 15, 2024, report from the Congressional Research Service entitled Navy Large Unmanned Surface and Undersea Vehicles: Background and Issues for Congress, “The Navy wants LUSVs to be low-cost, high-endurance, reconfigurable ships with ample capacity for carrying various modular payloads—particularly anti-surface warfare (ASuW) and strike payloads, meaning principally anti-ship and landattack missiles. Each LUSV could be equipped with a vertical launch system (VLS) with 16 to 32 missile-launching tubes.”
The report describes the MUSV as “low-cost, high-endurance, reconfigurable ships that can accommodate various payloads. Initial payloads for MUSVs are to be systems for supporting Intelligence, Surveillance, Reconnaissance, and Targeting (ISR&T), Counter-ISR&T, and Information Operations (IO) missions.”
Scott Beauchemin, vice president for Surface Systems at General Dynamics Mission Systems, said there are numerous advantages of a tethered drone systems to elevate a sensor or other payload, especially in contested environments.
“C-TEM extends sensor, network, and communications capabilities on an as-needed basis. With all-weather long-endurance mission support, automated flight control, and a low visual signature in-flight, C-TEM is ideal for both manned surface platforms and unmanned surface vessels (USVs), which will become more and more prevalent in the U.S. Navy’s fleet,” Beauchemin said. “In addition to its encrypted high-bandwidth data exchange capability, C-TEM can also be outfitted with numerous capability packages, ranging from radar, electronic warfare (EW), counter UAS, ISR (Intelligence, surveillance, and reconnaissance), and other missions.”
As a containerized system, C-TEM can be installed easily and requires a small footprint and minimal integration to existing systems. Beauchemin said it can be quickly deployed and retrieved for continuous sustained operations in all weather conditions. The system requires very little operator intervention. Station keeping and sensor direction are managed autonomously, and safe recovery protocols are automatic.
Because its power comes from the host platform via the tether, it does not require battery changes or refueling.
“C-TEM use cases are only limited by the warfighter’s imagination,” Beauchemin said.
C-TEM can be quickly deployed and retrieved for continuous sustained operations in all weather conditions. The containerized system is easy to install and requires minimal integration to existing systems. If the host platform is coming out of service for maintenance, the C-TEM container can be easily relocated to another platform to return to duty.
“Terrestrial communications remain a critical tool for digital connectivity for manned and unmanned vehicles. Elevating antennas from moving platforms is no easy task as it requires a well-coordinated dance between air-sea platforms,” said Mike Piasecki, DPI’s president. “We believe C-TEM systems can have meaningful impact on future naval unmanned maritime missions around the globe.”
The aircraft weighs 55 lbs. (25 kg) with a 15 lb. (7 kg) payload installed and can fly as high as 500 feet (150 m) above the launch platform.
The hybrid fleet of manned and uncrewed vessels are integral to distributed fleet architecture that augments the large “high-value” cruisers and destroyers with smaller “low-value” LUSVs and MUSV.
A Government Accountability Office 2022 report on “Uncrewed Maritime Systems -- Navy Should Improve Its Approach to Maximize Early Investments, said “the Navy is embarking on a robust effort intended to rapidly develop and field uncrewed maritime system prototypes and overcome technical challenges prior to acquiring these systems in significant numbers.”
The report stated that the Navy is reexamining its maritime strategy to respond to increased competition from nations investing in new weapons and technology designed to
disrupt U.S. naval advantages. While the U.S. military has remotely operated uncrewed aerial vehicles for over 3 decades, uncrewed maritime systems are still in their infancy from both technical and operational perspectives. To execute its strategy, the Navy needs to make significant investments in the development of technologies to enable these uncrewed maritime systems to operate both autonomously (or semiautonomously) as well as in conjunction with the existing fleet.”
The C-TEM contract was awarded to General Dynamic Mission Systems, a mission integrator for the Navy's hybrid fleet of manned and unmanned platforms, in June 2022 via the Unmanned Surface Vehicle Family of Systems multiple award contract by the Naval Sea Systems Command in Washington, D.C. The contract, including options if exercised, has a cumulative value of $39.4 million.
Looking for a way to revive old, damaged or worn buoyancy modules, giving them a second life?
Our subsea buoyancy repair and refurbishment service is designed to do just that. An alternative solution as modules become worn and damaged, extending service life to ensure you get maximum usage.
Repair any damaged or missing sections
Repaint or change of paint colour
Recoat with a fresh protective skin
Application of any logos, stencil graphics or non-slip coatings
Opportunity to make modifications or change configuration
Visit our website or scan the QR code to find out more base-materials.com BEFORE AFTER
Manufacturing custom-machined components for ROV and associated applications. Any quantity of components at a competitive cost.
Our components can operate in extreme conditions and offer high levels of reliability. Fast efficient response to quotes, and a high level of customer service. Our level of expertise in this field is a benefit to our customer base.
Northrop Grumman has been pioneering capabilities in the undersea domain for more than 50 years. Now, they are creating a new class of uncrewed underwater vehicles (UUV) with Manta Ray. Taking its name from the massive “winged” fish, Manta Ray will operate long-duration, long-range missions in ocean environments where humans can’t go.
Northrop Grumman developed a unique full-scale demonstration vehicle using several novel design attributes that support the Defense Advanced Research Projects Agency’s (DARPA’s) vision of providing ground-breaking technology to create strategic surprise. Manta Ray is:
ƀ Payload-capable to support a variety of missions
ƀ Autonomous, without the need for on-site human logistics
ƀ Energy-saving, with the ability to anchor to the seafloor and hibernate in a low-power state
ƀ Modular, for easy shipment in standard shipping containers to support expeditionary deployment and in-field assembly world-wide
ƀ It started with a challenge – how could we help the U.S. military conduct extended undersea missions?
In 2020, the Defense Advanced Research Projects Agency (DARPA) released a request for proposals on a new class of uncrewed underwater vehicle (UUV). Their request sought to advance capabilities in energy management, efficiency, power, fueling and more for long-range and long-duration missions.
Undersea missions can be very difficult, with challenges like high pressure, low temperatures, spotty communications and power supply for long missions, especially when operating far from port. For this purpose, an advanced UUV was needed that was bigger, more efficient, resilient and autonomous, or able to act independently without human supervision.
Northrop Grumman answered the call. The company designed, built and, earlier this year, tested Manta Ray, a full-scale UUV that will voyage to the depths of the ocean on extended missions.
Here are four benefits of this new technology.
Manta Ray has a unique size and shape that allows it to save power and energy for long missions. It is classified as an extra-large glider UUV, or XLUUV.
GIiders are a type of UUV that have been used since the 1960s to explore the ocean. Organizations like DARPA, the U.S. Navy and the National Oceanic and Atmospheric Administration use gliders to gather data on lengthy missions.
“A glider has a really intriguing propulsion mechanism, falling forward [with purpose] through the water all the time, both upward and downward,” said Brian Theobald, principal investigator and chief engineer for Manta Ray at Northrop Grumman.
“When Manta Ray needs to go up or down, it changes buoyancy by pumping sea water to change the weight of the vehicle.”
Gliders only need to change buoyancy for a few minutes at the top or bottom of their path. The rest of the time, they glide forward using minimal power and energy. This technology makes gliders operate more efficiently, which will enable Manta Ray to save power for long missions.
The U.S. Navy defines XLUUVs as vehicles that are too large to launch off a ship or submarine; instead, they are launched from a pier. Manta Ray’s extra-large size provides endurance, with more room for power systems, and the ability to carry critical payloads or sensors for a variety of long-range, longduration missions.
“Our team had to be creative and innovative to find solutions that would work for a glider UUV as big as Manta Ray,” said Structural Engineer Hayley Sypniewski. “It’s not a one-to-one scale with typical glider UUVs; because of its size, we added more buoyancy engines, a bigger payload bay, an enhanced towing system and an extremely efficient and large hull system.”
How do you ship a UUV of this size around the world for missions? You split it up.
Most large undersea vehicles, like submarines, are so big when fully assembled that they can’t be put on a truck or ship to transport. Manta Ray was designed with these considerations in mind. Thanks to its modular design, Manta Ray can be separated into parts for easy shipping. Then, it can be assembled in-field.
With missions around the world, the U.S. military and our allies must be expeditionary. Manta Ray allows them to bring critical capabilities wherever they are needed.
In January 2024, the Northrop Grumman team in Maryland shipped Manta Ray to Southern California for in-water testing. During the tests, Manta Ray demonstrated its ability to glide, ascend and descend, turn, hover and anchor. It can do some of these skills autonomously, avoiding the need for on-site human logistics or a human captain and increasing survivability.
“Manta Ray’s uncrewed capability is critical because we want to keep humans out of harm’s way during long missions in potentially dangerous environments,” said Joe Deane, Manta Ray program manager.
Manta Ray solves a unique mission set in a ground-breaking way. By extending the range and capabilities of XLUUVs, Manta Ray can complete missions in challenging undersea environments, while keeping our warfighters safe.
Plug and play external equipment. No configuration needed.
Attach grippers, sonars, UTM, CP probes or other sensors to the Blueye X3 ROV with ease using Blueye Smart Connectors. Allow the software to automatically configure the equipment
SeaTrac’s solar-powered uncrewed surface vehicle (USV) SP-48 works relentlessly on nearly any marine mission 24/7, in-shore or offshore, for months at a time. No other USV is as easy to deploy and operate while supporting so many payloads. With a low cost of ownership and right-sized for transport and fleeting, SeaTrac is the industry’s ultimate USV.
Tell us about your mission or request a demo.
Captain George Galdorisi (U.S. Navy – retired)
For several years, momentum has been building throughout the U.S. Department of Defense for one technology, uncrewed surface vehicles (USVs), to make up a large portion of the Navy’s Fleet. The Chairman of the Joint Chiefs of Staff suggested that a much larger 500-ship U.S. Navy was necessary. In a direct reference to the importance of unmanned systems in reaching this goal, he noted: “Part of the move to pursue a 500-ship fleet rests upon the hope for as many as 140 to 250 unmanned vessels,” which he called, "Sailorless ships.”
In an era of great power competition, uncrewed surface vehicles have begun to take center stage and are now on an accelerated development path. Like their air and ground counterparts, these USVs are valued because of their ability to reduce the risk to human life in high threat areas, to deliver persistent surveillance over areas of interest, and to provide options to warfighters that derive from the inherent advantages of uncrewed technologies.
To be clear, the advantages of accelerating the development of uncrewed surface vehicles have not been restricted to the United States. The U.S. Navy isn’t the only navy keenly interested in uncrewed surface vehicles. Indeed, the past few years may well be remembered as a high-water mark for the insertion of USVs (and to some extent, UAVs used in conjunction with these USVs) into a number of international exercises, experiments, and demonstrations that have, literally, spanned the globe.
Over the course of these events, uncrewed surface vehicles have performed an increasingly ambitious and complex series of missions, giving great confidence to those nations and navies who see them as an important part of their fleets. The highlights of these events show the keen interest of the navies of many nations in finding new missions for these systems.
International Maritime Exercise (IMX), held under the auspices of U.S. Naval Forces Central Command and Commander Task Force 59 (CTF-59) in the Arabian Gulf, focused on the integration of crewed and uncrewed vessels and included operations with several regional partners.
Navies and coast guards of the nations involved in IMX worked to fully explore the capabilities of uncrewed systems such as the Saildrone, the MARTAC MANTAS and Devil Ray, and many other USVs from participating nations. This is the first time that this many nations participated in an event of this type.
In the run up to International Maritime Exercise, the Commander of U.S. Naval Forces Central Command/U.S. 5th Fleet, Vice Admiral Brad Cooper, noted: “The Navy has been working with manufacturers to test new technologies, including firms such as Saildrone and MARTAC under a contractor-owned, contractor-operated model.”
What is noteworthy about CTF-59 operations in the Arabian Gulf is the fact that IMX was not a “one-of.” Rather, creweduncrewed integration operations in the Arabian Gulf continue. The U.S. Navy now has 20 USVs in or near the waters of the Arabian Gulf. Indeed, the United States and its allies want to ultimately have a force of 100 uncrewed surface vehicles patrolling waters from the Red Sea to the Arabian Gulf.
One U.S. USV company, MARTAC, was a primary participant in IMX. Their uncrewed surface vehicles, MANTAS and Devil Ray, were mainstays of this exercise. Here is how one defense analyst, writing in Inside the Navy, captured the essence of MARTAC’s participation in this major exercise:
MARTAChasastrongpresenceis5thFleetoperating with Task Force 59, a Middle East-based task force workingonthedevelopmentofunmannedsystems… Typical missions for MARTAC include intelligence, surveillance and reconnaissance, port and harbor security and sensing capabilities, in addition to classified missions.
In another international exercise focused on missions for uncrewed maritime systems, the Australian Defence Force (ADF) hosted Exercise Autonomous Warrior (AW). Nations participating in this Royal Australian Navy-led exercise included Australia, New Zealand, the United Kingdom, and the United States, and featured a total of thirty autonomous systems. The uncrewed surface vehicles that were part of this two-week exercise were the Saildrone, MANTAS, and Devil Ray featured in IMX; the Atlas Elektronik ARCIMS; the Elbit Systems Australia SEAGULL; and the Ocius Bluebottle.
Another event, the bi-annual Rim of the Pacific Exercise (the world’s largest international maritime exercise) was especially noteworthy as the U.S. Navy inserted four uncrewed surface vehicles in this major international exercise. The Rim of the Pacific exercise gave the event’s twenty-six participating nations an opportunity to see these USVs in action.
The RIMPAC Commander put special emphasis on the uncrewed vehicles participating in RIMPAC, as well as creweduncrewed integration:
What’salsonewinthisRIMPACisalotmoreintegration ofunmannedsystems—onthesurface,intheair,and underthesurface.Thefourunmannedsurfacevehicles thattheNavybroughttotheexercisecarriedspecialized payloads for anti-submarine warfare, intelligence, surveillance and reconnaissance, domain awareness andcommunicationscapability.Sothat’sallkindofnew.
One of the important lessons learned regarding the operations of uncrewed surface vessels during RIMPAC was what was important to the sailors operating these four USVs. One official from the Navy’s program office for unmanned maritime vehicles noted that: “One of the biggest pieces of feedback we’re getting is that they’re [sailors operating these USVs during RIMPAC] talking about payloads, they’re talking about capabilities. They’re not talking about autonomy. They’re not worried that [the USV is] going to ever run into something.”
On the other side of the world, NATO exercises REPMUS and the follow-on Dynamic Messenger, provided an opportunity for NATO nations to evaluate uncrewed systems and their ability to coordinate on, above and under the sea. Led by Portugal and conducted near the Troia Peninsula, these exercises focused on the integration of 120 autonomous assets into a single network. Several NATO commands: NATO’s Allied Command Transformation, NATO3345’s Allied Maritime Command, the NATO Center of Excellence, and NATO Center for Maritime Research and Experimentation were part of these exercises. This enabled partner nations to learn best-practices regarding how to shepherd uncrewed systems into their respective navies.
Later, the U.S. Navy-led exercise Digital Horizon, a threeweek event in the Middle East, focused on employing artificial intelligence and 15 different uncrewed systems (12 USVs and 3 UAVs), many of which were operated in the region for the first time. The exercise, meant to be a continuation of IMX but on a significantly larger scale, was hosted by Task Force 59, and built on the work done during IMX. Indeed, Digital Horizon was the largest international uncrewed exercise ever held.
Digital Horizon brought together new, emerging uncrewed technologies and combined them with data analytics and artificial intelligence to enhance regional maritime security and strengthen deterrence. The exercise featured 17 companies that collectively brought 15 different types of uncrewed systems, ten of which operated with U.S. 5th Fleet for the first time. One of the objectives of Digital Horizon was to use uncrewed maritime vehicles to conduct intelligence surveillance and reconnaissance missions, including identifying objects in the water and spotting suspicious behavior.
From the perspective of the U.S. Navy, these exercises and initiatives are important and represent a significant course change as the Navy works to convince Congress that its plans for uncrewed systems are sound. Secretary of the Navy, the Honorable Carlos Del Toro, explained the Navy’s new “show, don’t tell,” philosophy built on an ongoing series of exercises, experiments and demonstrations, further indicating that he believes the Navy is: “On the same page as Congress.”
The Navy has a responsibility to be able to prove that the technology that Congress is going to invest in actually works and it meets what we need to address the threat. I think that’s the responsible thing to do…I don’t see it as a fight between Congress and the Department of Navy. I think we’re aligned in our thinking about what has to be done.
Looking ahead, world navies are keen to bring both commercial-off-the-shelf (COTS) uncrewed maritime systems, as well as other USVs in various stages of development, to exercises, experiments, and demonstrations. This will enable them to not only demonstrate their own capabilities, but to also learn best practices by observing the operations of unmanned maritime systems of other nations. These efforts are virtually certain to accelerate the development of these USVs, and for the U.S. Navy, hasten the goal of a 500-ship Navy that is envisioned to have 350 crewed ships and 150 uncrewed vessels.
Captain George Galdorisi is a career naval aviator and national security professional. His 30-year career culminated in 14 years of consecutive service as executive officer, commanding officer, commodore, and chief of staff. He enjoys writing, especially speculative fiction about the future of warfare. He is the author of 18 books, including four consecutive New York Times bestsellers. His latest book, published by the U.S. Naval Institute, is Algorithms of Armageddon: The Impact of Artificial Intelligence on Future Wars.
The latest evolution in bathymetric measurement
Density corrected depth data directly from one instrument
By Capt. Marc Deglinnocenti, U.S. Merchant Marine (ret.), oldarmada@gmail.com
America was founded in 1776 amidst a revolution with an innovative form of government for its time. VideoRay is an American company founded in 1999 that develops and builds innovative Remotely Operated Vehicles (ROVs) for the current technological ROV revolution. Even their first ROV released in 2000 was considered revolutionary with a 76 metre (250 ft.) depth rating. The VideoRay Pro only weighed 3.6 kilograms (8 lbs.) and was equipped with dual thrusters, lights, and a video camera. That may not sound like much in today’s ROV market, but it was a big hit with Fish and Game Departments and Law Enforcement Agencies all over the USA.
Since then, they have come a long way, and they are now a major contender in the ROV marketplace. Today VideoRay offers three main ROVs which they placed in their Mission Specialist category. Even though they might have been released at different times, one newer Mission Specialist ROV was never really designed to replace the other older ROVs within that category. These three Mission Specialist ROVs are more like not-so-identical triplets with each having their own area of expertise. They are the extremely versatile seven thruster Defender which sports over 500 different equipment
configurations, and they are working on more! The Pro 5, which is a more economical ROV with three thrusters. It has the same 305-metre deep diving rating as the Defender. The newest Mission Specialist ROV is the Ally. It has great lifting ability with two floatation configurations and four thrusters. It is designed to fit into pipelines and other tight spots. All these Mission Specialist ROVs are designed to have modular plug out and plug in components for quick mission changes and quick repairs in the field. That’s a great product line for any ROV company, but what’s in store for VideoRay’s future?
I finally hit pure gold when it comes to what VideoRay is working on in the future. Up to now they have been pretty tight lipped about what they are about to release on the ROV market. That gold was revealed to me in a face-to-face interview with Chief Executive Officer, Chris Gibson, of VideoRay. I decided to start out a little more subtly with my questions this time.
CAPT. MARC: I must start with your successful line of ROVs called Mission Specialists. I understand that they each have their separate areas of expertise, but can you tell me a little more about how they have technology in common?
CEO GIBSON: All the Mission Specialist ROVs are modular in design and can be broken down in the field. Many of the parts plug in and out, so if you have a thruster that gets hopelessly jammed with fishing line that might take hours to remedy, all you have to do is unplug it and plug in a replacement thruster, and you’re back up and running within minutes.
CAPT. MARC: So, are these thrusters interchangeable between different models of your ROVs?
CEO GIBSON: Yes, all Mission Specialist ROVs use the same thrusters, and we build our own thrusters right here, but that’s not all. The control modules are also interchangeable between models as well as many other components.
CAPT. MARC: You mean to tell me that the same topside controller can be used on any of the three ROVs?!
CEO GIBSON: Yes. That is exactly right. One topside controller unit runs any of the three ROVs. We even have a splash
controller unit that’s waterproof for small boats and docks that also runs all three ROVs. If a computer control module on one ROV, like on the Defender, isn’t quite right, then you can unplug it and plug in one from the Pro 5 or Ally. So, the same goes for the topside controller units and many other parts such as the batteries, lights, thrusters, and even the compass.
CAPT. MARC: I knew that the three ROVs were modular, but I didn’t know that many of the parts were interchangeable between models, especially the control modules and controllers. What else do the Mission Specialist ROVs offer your customers?
CEO GIBSON: Reliability. Without going into specifics, we have customers that work in the nuclear energy sector. It is critical to them that electricity is restored as soon as possible. They use our ROVs to do just that in the most dangerous of environments. We have the Navy and Coast Guard that rely on our equipment to remove dangerous explosive ordnance and clear shipping channels as soon as possible. Equipment that breaks down in the field is absolutely unacceptable for those types of jobs where time is of the essence. We also have customers that are far out at sea. An oil platform that uses helicopters to transport other brands of ROVs that are always breaking down is a frustrating and an expensive waste of time for them. We understand that here at VideoRay. That also goes for oceanic research vessels hundreds of miles out at sea. If a mission cancels due to defective ROV equipment, it can cost a lot to scrub a mission like that. We make that same point to all our technicians. We even send them out in the field with our customers so that they can see for themselves how important reliability in these systems is.
CAPT. MARC: I crewed a research vessel and then later captained one of my own. Let’s talk a bit more about those types of ships. Is there anything else you do for them besides making your ROVs tough to break with interchangeable parts?
CEO GIBSON: Captain Marc, we are a leader in that sector too that not many people can appreciate. You must have seen how large some of those deep water ROVs can be. They need powered davits and cranes just to lift them off the deck. We have deep water ROVs that can dive down to 1,000-metres and are single person deployable.
CAPT. MARC: Yes, one of the ROVs I worked with was the size of a small car that needed a hydraulic sea crane davit to lift and deploy it. The 1,000-metres of tether was thick and was in a huge spool that took up a lot of deck space. The crew had to attach additional floatation to the tether as it was being deployed. The reverse was true whilst retrieving the tether. The whole process took hours.
CEO GIBSON: Ah ha! Now, you can understand how a large bulky tether can limit your deep water ROV operations. We have been working around that problem and have found a solution to it. We are developing tether systems that are ultrathin. We have mostly moved away from using the tether to power the ROVs. We have been developing longer-lasting more powerful on-board batteries to do that. This makes our ROVs much more user friendly without sacrificing portability and ease of handling. As a matter of fact, our new tethers are extendable and can be stored on the deck of research vessels without taking up that much space at all.
CAPT. MARC: Well, getting that future tether innovation from you will indeed interest our readers. Can you tell me anything else about future VideoRay innovations or products?
CEO GIBSON: I can tell you that we are working on technology that will in some cases eliminate the tether completely.
CAPT. MARC: Does that mean that you are entering the Autonomous Underwater Vehicle (AUV) market?!
CEO GIBSON: No Marc. We see AUVs as large surface area search tools, they complement VideoRav systems. We are evolving from a traditional ROV company, adding more capabilities, into an underwater robotics company. Tethers give us more ROV controls and emergency recovery safety for our ROVs, but there are times when a tether might get in the way.
So, these are very specific use ROVs that we are developing that have autonomous capabilities that are being readied for the Mission Specialist line.
CAPT. MARC: I understand that tethers offer more safety. What about your plans for an all-new future ROV?
CEO GIBSON: We have many plans for the future, but most of them are confidential. I can tell you that we are indeed developing a whole new ROV as you have suspected. That ROV will have a 3,000 metre (9843 ft.) depth rating. It will have some new technologically advanced 4K colour cameras too.
CAPT. MARC: That’s great news. You’ve given me exactly what my readers were looking for without going into a lot of details. Thank you so much!
CEO GIBSON: You are most welcome. It’s now time for your guided tour of our facility here in Pottstown.
I then got a VIP tour of their headquarters and production facility by a VIP himself – Chief Operating Officer, Paul Czachor escorted me to a test tank that they had there at their main facility. He showed me both their dry controller unit and their splash controller unit. Both were up and running, and although the controller units looked different at first glance, they really had the same switches, levers, dials, and buttons in relatively the same places. The splash controller unit was a bit more compact and quite waterproof. The controllers worked the same for me though. Yes, I was allowed to “fly” the famous Defender and their new Ally ROVs. Both were easy to control compared to their earlier Pro 4 that I operated on San Diego Bay. Yet, when I wanted the ROVs to move or spin quickly, they responded quickly. How does it get any better than slow and easy controls when you want them yet instant speed and power when you want that too? In all honesty both ROVs operated like a dream with autonomous station keeping when I wanted that as well.
We then proceeded to their ROV, 1,000-metre rated, control module assembly room. I’m not allowed to say how many technicians were on duty, nor was I allowed to photograph them. I can say that there were more than most other ROV facilities that I have visited in the past. As a matter of fact, they were in the process of expanding their production areas to accommodate even more. Some of that expanded area was where the new Ally ROV was being assembled.
The assembly process was classified, and I promised not to reveal their specific procedures. It was there that I met Todd Holtz who is the Director of Product Innovation and who just happened to be the lead designer of the versatile Defender and the new Ally ROVs. He was busy overseeing the assembly process of the Ally, but he did spare some of his time to explain to me what his new assembly process actually involved. It reminded me of the movie Charlie and the Chocolate Factory where their chocolate had to be aerated just like everyone else’s, but his factory was the only one that aerated its chocolate by waterfall. Well, the Ally has to be assembled just like everyone else’s ROVs, but VideoRay’s method is quite unique as well. I don’t believe that any other ROV factory uses it. It ensures maximum assembly efficiency whilst providing maximum quality control, and it’s quite top secret.
Another classified area was the battery lab and battery assembly line. Photographs were not allowed there either. Their batteries are a bit revolutionary in the fact that they are extremely powerful, interchangeable, and very lightweight. Paul let me hold one. It looked heavy, but it was quite light when I grabbed hold of it. The 1,000-metre rated casing made it look heavier than it actually was. He said they make two types of batteries, and both are made in-house. One is a lithium-ion type, and the other is nickel-hydride type. Paul said, “Our batteries deliver a high punch of power!”
I learned a great deal from my visit to VideoRay. You can even learn more at their website at VideoRay.com which is quite extensive and detailed in its content. VideoRay has a colourful past and a great current product line that’s hard to beat with a bright future ahead. They love their customers and support them in any and every way they can. They listen to their customers’ wants and needs and then deliver pure satisfaction. That attitude no doubt led to their most recent 92.6 million dollar U.S. Navy contract to supply them with and improve the Defender ROV over the next five years. That’s in addition to their previous Navy contracts. I sincerely recommend that you contact VideoRay for your next ROV purchase. Don’t forget to tell them that Captain Marc sent you though. They respect their customers’ confidentiality, and as a government contractor they take security very seriously.
- Six Powerful Thrusters - Carbon Fibre & Aluminium Shell - Depth rated to 120m / 400ft - 4K Ultra HD Low-light Camera - Field Swappable Batteries
Kongsberg Discovery has spent the past three decades harnessing its understanding of inertia to develop a highly versatile sensing technology. It’s this technology that forms the backbone of its portfolio of solidstate Motion Reference Units (MRU) and Motion Gyro Compass (MGC) units. Both have become the de facto industry standard across a wide spectrum of applications, all of which require precise attitude, heading and position data, and reliable performance over time.
"In 1986, we embarked on a mission to simplify and commercialize inertial navigation technology for the maritime market at an affordable cost.”, says Vidar Bjørkedal, Vice President SEATEX Sales at Kongsberg Discovery. “Our engineers spent six years honing the technology, and in 1992
we launched our first MRUs. They deserve huge credit as pioneers. In addition, a culture of continuous improvement and happy customers are the reason we're still in business 30 years on."
Inertial technology is one of the company's strongest legacies. With over 20,000 MRUs installed, and the product name becoming an industry-wide generic term, the Kongsberg MRU has changed the face of the maritime world. Following the success of the MRU line, the MGC was released in 2014. This was followed more recently by the miniMRU. “Don’t be fooled by the classic look of the sensors, the internal components are constantly evolving and improving.”, Bjørkedal says. “In fact, the latest MRU 5+ is the highest-accuracy MEMSbased sensor available in the market.”
Fusing our inertial sensors with GNSS in the latest generation of Seapath 130 and 385 takes navigational sensing to an even higher level of accuracy. “Our mantra is to always do better and we're confident the best is still to come," Bjørkedal adds.
The company's MRUs feature a cluster of highly tuned accelerometers and Kongsberg-developed MEMS gyros. These deliver precise measurements of rotations and accelerations with incredible accuracy. Based on this the MRUs can calculate speed, attitude, and many other parameters. The MGCs, with their north-seeking gyros also bring true heading output. Particular benefits include a high output data rate, high reliability, compact size, light weight, and low power consumption. Neither the MRUs nor the MGCs require any maintenance as there are zero wear-out parts. For most applications, recalibration is also a thing of the past.
MRUs can be used as embedded sensors in just about any piece of equipment or working platform that requires accurate motion stabilisation, from offshore jack-up operations, dynamic positioning (DP) systems, riser monitoring and motion damping for fast ferries, to helideck monitoring and even motion compensation for beds on cruise ships. Typical Active Heave Compensation (AHC) applications include offshore cranes, gangways, winch systems, Launch & Recovery Systems (LARS), and hoisting equipment in drilling draw-works.
The MRU feeds data to the controller that regulates the motion compensation system. "We invested a lot of time developing the software and algorithms that process the different angular variables.”, says Bjørkedal. “Customers can select from more than 350 variables for a particular application, which makes these units extremely flexible."
MRUs were game-changing because they replaced both manual eyeball operations, and heavy mechanical passive heave compensation systems that required a lot of maintenance. With so many components, the risk of damage due to high forces was also very high. "MRUs enable customers to widen the operational window so equipment can be deployed in rougher sea states within safe limits. They also serve to reduce the overall cost of operations," Bjørkedal adds.
Kongsberg's type-approved and wheelmarked MGCs go one step further, providing not only simultaneous motion compensation for multiple onboard applications, but also replacing conventional gyrocompasses for navigation of all ship types. "We're one of very few vendors globally that can supply a single type-approved sensor that can cater to all applications onboard a vessel – for navigation, cranes, DP, you name it. That is revolutionary," says Bjørkedal.
Similar to the MRU family, the MGCs are scoped to cater for different use cases and accuracy requirements. The MGCs are built using a different gyro technology, with ring-lasers (RLG) replacing the MRUs' MEMS-based gyros. These gyros are so sensitive they are able to detect the Earth’s rotation, enabling the MGC to calculate true north.
For vessel navigation, the stability of the MGC can be translated to less rudder usage and thus reduced fuel consumption and emissions. "This is because fewer course adjustments are necessary, which reduces the impact of the rudder and extends the lifespan of the steering system. That also goes for high-speed vessels," Bjørkedal says.
The exceptional north-seeking capabilities of the MGC outperforms conventional gyrocompasses, and this is especially visible at higher latitudes. “This capability is beneficial not only for dedicated Polar ships, but will also be very relevant if northern sea routes are used amid retreating Arctic sea-ice," Bjørkedal notes.
The latest generation of MRUs and MCGs are built on the legacy of more than 30 years of experience. “Customers report that the units just keep on working, which is a clear testament to their reliability and durability,” Bjørkedal says.
He adds that both product families are “bottom-line sustainable”. Because they require no maintenance, downtime is a thing of the past, eliminating the need for service engineers to visit the vessel. "Through our global service network, we also offer
a trade-in program where we supply replacement units should the operator or partners require freshly calibrated sensors."
Kongsberg Discovery is dedicated to providing excellent service throughout the lifetime of our products. “This means that we guarantee availability for service and repairs at least 10 years after the product has reached end-of-life (EOL) and no longer sold,” Bjørkedal adds.
The MRU and MGC form the core of Kongsberg Discovery's Seapath platforms targeting complex hydrographic surveys and seabed mapping. The latest Kongsberg EM2042 MBES brings the miniMRU fully embedded to simplify installation and create a unified INS and multibeam system. The inertial sensor works together with state-of-the-art multi-frequency GNSS receivers and processing algorithms to provide the best possible position, velocity, attitude, time, and heading data for critical operations. All available GPS, GLONASS, Galileo, Beidou, and QZSS satellites are used in the position solution.
"The deep architecture and Seapath's outstanding dead reckoning leaves lower-end sensors, which are liable to position drift, in the shade. We also rapidly adopt new technology and are the only maritime company to have already implemented and tested the latest Galileo updates," says Bjørkedal.
In terms of sustainability, using Seapath makes surveys better and faster, avoiding time-consuming duplication of work and extending operational windows. "We are pushing boundaries on what's possible. Because we focus on realtime data performance, using Seapath you will get the survey right first time, with very little need for expensive postprocessing of data," Bjørkedal adds.
The choice of inertial sensor has the greatest effect on performance while the choice between Seapath models is dependent on what type of equipment is connected and operational requirements. The Seapath 130 is typically used for one MBES or where you need a compact system, whereas the larger, rack-mounted Seapath 385 model is the right solution for demanding installations with several connected sensors, such as research or offshore survey vessels.
The Seapath is unique in the fact that performance can be upgraded very easily by changing out the MRU to a higherperforming model or to an MGC. All MRUs are identical, and no survey or setup is required if replacing an MRU 3 with an MRU 5+, for example. The same goes within the MGC range.
"Looking back to 1994 when we launched our first INS product, the Seapath 400, we had four GPS antennas to aid the motion sensing. Now the inertial sensors are the core of many of Kongsberg Discovery’s products and aiding can be provided by a single GNSS antenna or many other technologies both above the waterline and below,” explains Bjørkedal.
In summary, inertial technology is critical for robust and accurate maritime operations. All Kongsberg Discovery's MRU/MGC solutions are uniquely flexible. "The segments we serve tend to be bespoke, so in addition to providing standalone units for integration into third-party systems, we also collaborate directly with customers to adapt the technology to their unique challenges. Given our long heritage in this domain, we will always find a solution," Bjørkedal explains.
Speaking for the company's engineers – who have dedicated tens of thousands of manhours to adapting and perfecting inertial solutions for a demanding market – Product Line Manager Finn Otto Sanne concludes, "We're very lucky to have a working environment characterised by innovation and new ideas. That has been a key to success when working with the state-of-the-art technologies needed to harness the subtle forces of inertia.
“We're very proud of our work, the unique competence we've built up over more than 30 years and the tangible products out there that are helping maritime companies perform at the highest level."
NBOSI’s Model 103 conductivity/temperature (CT) sensor is a key component within HII’s REMUS 300 unmanned underwater vehicle (UUV). In this case study, we take a look at this low-drag, research-quality sensor and how it delivers a unique package of capabilities that help keep the REMUS 300 at the leading edge of its highly specialised field.
The REMUS 300 is a cutting-edge, small-class UUV designed for military and commercial use. Built by HII, this versatile vehicle offers advanced modularity and payload flexibility.
The REMUS UUVs excel in various applications, including mine countermeasures, search and recovery, environmental assessment, hydrographic surveys, marine archaeology, and anti-submarine warfare. The REMUS UUVs have seen significant international success, with over 600 units sold across more than 30 countries.
The UUV’s design aligns with the U.S. Navy’s Modular Open Systems Architecture (MOSA) and Unmanned Maritime Autonomy Architecture (UMAA) standards. Its modular structure allows for mission-specific configurations, supporting depths up to 305m.
In February 2020, HII delivered the first prototype to the U.S. Navy for evaluation under the next-generation SUUV programme, also known as Lionfish, leading to its selection as the programme's vehicle of record in March 2022. The U.S. Navy and the Royal New Zealand Navy have both placed
orders for the REMUS 300 for various operational needs. More recently, HII announced in 2023/24 that the U.K.’s Royal Navy had contracted to purchase nine REMUS 300s, along with three REMUS 100 UUVs.
Key features include a robust structure, advanced sensors, flexible energy options, and a new Odyssey graphic user interface (due for release in 2024) for mission planning and monitoring. It supports a variety of payloads, including side-scan sonar, environmental sensors and high-resolution cameras. Navigation and communication are enhanced by inertial navigation systems, GPS and acoustic modems.
Propelled by a direct-drive DC brushless motor, the REMUS 300 can achieve speeds up to 5 knots and ranges between 110km and 165km, depending on its configuration. Its endurance varies from 10 to 30 hours with quick-swap lithium-ion batteries in three sizes from 1.5 to 4.5 kWh, making it a highly adaptable and efficient solution for a wide range of underwater operations.
In the ever-evolving field of underwater exploration, precision and efficiency are paramount. The low hydrodynamic drag, low power requirement CT sensor from Neil Brown Ocean Sensors Inc. (NBOSI) has been part of the REMUS 300’s standard sensor suite since the vehicle’s launch.
The NBOSI CT sensor stands out in the market due to its free-flushing, fast-responding, quiet, vibration-free, rugged and low-power design, which is insensitive to mounting location. Unlike traditional two-electrode cells, it does not require an energy-consuming and noisy pump. Additionally, the NBOSI sensor’s compact, rugged and low-drag design allow it to be mounted anywhere on the vehicle's exterior without compromising data quality or hydrodynamic efficiency.
Integration is simplified with a straightforward RS-232 data interface, providing raw or engineering-unit data at up to 10Hz. Fully potted for durability, these sensors are capable of operating beyond 6000 dbar. To ensure reliability under extreme conditions, NBOSI regularly conducts in-house pressure validation testing to 9,800psi (6750 dbar).
The HII REMUS 300 requires small, accurate, reliable and low-power sensors. Among these, the NBOSI conductivitytemperature (CT) sensor has successfully addressed the unique challenges presented by the REMUS 300 platform.
The need for precise and accurate sensors in such a compact vehicle posed significant challenges. These sensors had to be low-powered and occupy minimal space within and outside the vehicle’s hull. Additionally, they needed to maintain a low-drag, hydrodynamic profile and meet specific pressure ratings to operate effectively at designated depths. Crucially, the sensors had to minimize acoustic and electrical interference to avoid disrupting the vehicle’s primary survey sensors.
In response to these demands, NBOSI’s CT sensor was selected for the REMUS 300. This decision was driven by the sensor’s ability to deliver high accuracy while maintaining a small footprint and low power consumption. The NBOSI CT sensor’s design ensures minimal drag and interference, making it ideally suited for the REMUS 300’s rigorous operational environment.
The data collected by the NBOSI CT sensor is vital for the REMUS 300’s missions, which include scientific data collection and various survey activities. Measurements of temperature and conductivity (and, by extension, salinity) are essential for defining the oceanographic environment. These parameters are used in conjunction with a separately mounted pressure sensor to calculate the speed of sound in water. This calculation is critical for enhancing the accuracy of other onboard sensors, such as the Acoustic Doppler Current Profiler (ADCP) and multibeam echosounder.
Improved sensor accuracy translates directly to better navigation performance. Understanding water density, as
determined by temperature and salinity measurements, allows operators to adjust the ballast and trim of the UUV, optimizing its stability and performance based on the specific environmental conditions of the mission area.
Technically, the NBOSI CT sensor integrates seamlessly into the REMUS 300’s architecture. It consists of a pressure-tight temperature/conductivity probe mounted on the vehicle’s forward end cap. The probe connects via an attached cable to a matched electronics board within the REMUS 300, ensuring smooth data transmission and processing.
The data provided by the NBOSI CT sensor is crucial for calculating sound speed, which is applied to the ADCP to enhance the accuracy of velocity measurements. This, in turn, improves the performance of the Inertial Navigation System and the REMUS’ central computer in determining the UUV’s position over time. Additionally, sound speed calculations are used by the REMUS to accurately measure distances using underwater navigation beacons, aiding even more precise triangulation of the vehicle’s position.
As HII continues to evolve the REMUS product line, the focus remains on increasing modularity, reliability, and ease of manufacturing and maintenance. Ongoing improvements in sensor technology, such as NBOSI’s new 500 Series integrated CTD sensors with a precision pressure sensor, direct sound speed output and easier vehicle integration with zero interior footprint required, will drive continued innovation in underwater exploration.
HII’s experience with NBOSI underscores the importance of a collaborative approach and exceptional support, leading to successful mission outcomes and long-term operational excellence.
Industry representatives and project stakeholders gathered on 25th June at Verlume’s Operations Facility in Dyce, Aberdeen, UK for a Renewables for Subsea Power (RSP) Technology Showcase event.
Celebrating a successful 13-month deployment in the UK North Sea, attendees were presented with the key achievements from the ground-breaking low carbon and communications project and also had the opportunity to see the key technology systems in-person as part of a guided tour around various technology stations:
ƀ Verlume’s Halo subsea energy storage and intelligent energy management system.
ƀ Mocean Energy’s Blue X wave energy converter.
ƀ Transmark’s ARV-I Autonomous Underwater Vehicle (AUV) and AUV dock mounted onto the Halo basket.
ƀ Baker Hughes’ Subsea Electronics Module.
The RSP project has been a fantastic example of a collaborative approach to delivering reliable low carbon power and communications to subsea assets and long-term underwater vehicle residency. Both the AUV dock and Subsea Electronics Module were 100% powered by renewable energy throughout the duration of the project.
Industry players mentioned above were involved in the project as well as support from Serica Energy, Harbour Energy, TotalEnergies, PTTEP and Shell – Marine Renewable Program and Net Zero Technology Centre.
Next steps for the project include ongoing discussions for commercial deployments of this solution in offshore applications across the world, such as long offsets, umbilical remediation, carbon capture and storage and decommissioning.
10 YEARS OF OCEAN ROBOTICS PLANET
National Oceanography Centre
MATS is a key event in the marine technology calendar, attracting delegates from around the world, hosted at the National Oceanography Centre’s dockside location in Southampton.
Join us for a packed three days of insightful presentations and networking opportunities, focusing on new developments and innovations.
05–07 NOVEMBER SOUTHAMPTON
World's most compact high-performance inertial navigation system
Unmatched navigation accuracy: heading 0.04°, roll & pitch 0.01°
Easy integration through optimized SWaP-C
Unrivaled reliability in harsh environments