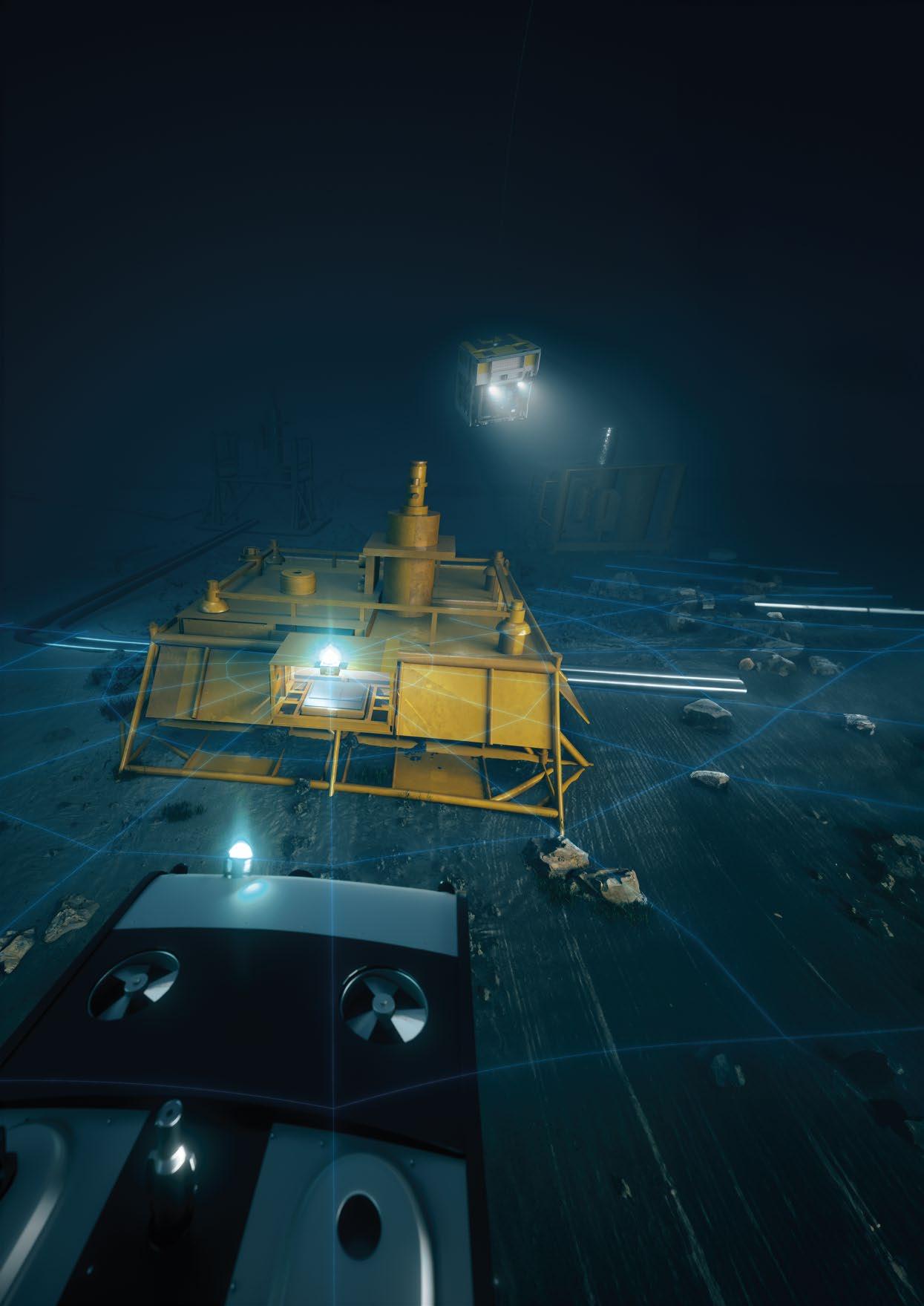
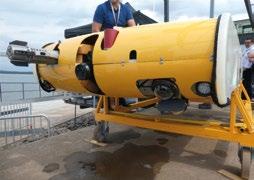
Revolutionising AUV Deployment Enabling Long-Term Residency 9.
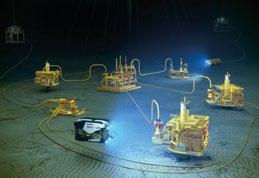
Revolutionising Subsea Inspections Using ROV Mounted ASVM 19.
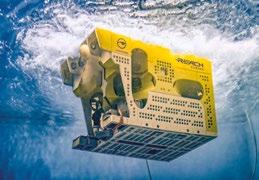
Kystdesign ZEEROV on the Road to Net Zero 23.
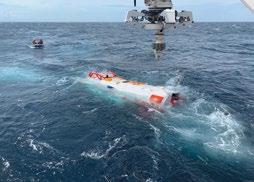
Submarine Rescue is Non-Negotiable
Revolutionising AUV Deployment Enabling Long-Term Residency 9.
Revolutionising Subsea Inspections Using ROV Mounted ASVM 19.
Kystdesign ZEEROV on the Road to Net Zero 23.
Submarine Rescue is Non-Negotiable
• Delivering data in most adverse conditions: underwater acoustic modems with advanced communication technology and networking
• Accurate USBL, LBL and hybrid positioning of underwater assets, navigation for divers
• Modem emulator and multiple cost-saving developer tools
• Sonobot 5 - the autonomous surface vehicle for bathymetry, monitoring, search & rescue, and AUV support
• Quadroin - the novel bionic AUV for surveys and monitoring
sales@evologics.com sales-us@evologics.com
06. Events Calendar & Welcome to Ocean Robotics Planet
09. Revolutionising AUV Deployment Enabling Long-Term Residency
15. The Future of Subsea Residency with Saab’s Sabertooth
19. Revolutionizing Subsea Inspections using ROV-mounted ASVM Solutions
23. Kystdesign ZEEROV on the Road to Net Zero
29. Exail’s New DriX O-16 USV Designed for Long Endurance Transoceanic Missions
32. Poster: DriX O-16
35. Submarine Rescue is Non-Negotiable
39. Baltic Sea’s “Extreme Litoral” is a Multi-Domain Battlespace
43. Expeditionary Fast Transport Capable of Autonomous Operations
47. Port and Harbor Security: An International Imperative
51. Woods Hole Oceanographic Institution Receives Funding for New Family of ROVs
55. The Underwater Glider User Group (UG2)
57. Keeping European Gliders On Track & On Mission
61. Final Mission for the “Ran” AUV Under Thwaites Glacier in Antarctica
ISSN 2755-239X
EDITOR-IN-CHIEF
Richie Enzmann
COPY EDITOR
Will Grant
SALES DIRECTOR
Nick Search
DESIGN & LAYOUT
Milan Farkas
CONTRIBUTORS
Richie Enzmann, Alexander Steele, Alison Pike, Chris Buckle, Corey Halsell, Edward Lundquist, Elaine Maslin, Frode Rabben, George Galdorisi, Georgia Coward, Jan Siesjö, Michael Sheppard
SPECIAL THANKS TO
Aidan Thorne, Anna Wåhlin, Anthony Hammond, Audrey Leon, Bill Mallin, Callum Shaw, Carl Brendtson, Charlotte Sherwood, Curtis Lee, Dawn D’Angelillo, Francisco Bustamante, Gwenaëlle Allaire, Jack Rowley, James Colebourn, John Benson, Jostein Jansen, Marion Seyve, Matt Bates, Michael King, Oda Ryggen, Paul Fletcher, Rachael Reader, Raymond Ruth, Richard Mills, Rob Howard, Sophie Hudson, Willard Balthazar
Austal USA
Base Materials
Blueprint Subsea
Blueye Robotics
Cellula Robotics
Digital Edge Subsea
EvoLogics
Exail
Forum Energy Technologies
Greensea IQ
IVM Technologies
Kystdesign
NETmc Marine
National Oceanography Centre (NOC)
Norwegian Offshore Rentals
Oceaneering
QYSEA
Saab Seaeye
Sonardyne
Sulmara
U.S. Navy
Underwater Glider User Group
Woods Hole
Oceanographic Institution (WHOI) Zetechtics
NOVEMBER
UNDERWATER INTERVENTION / WORKBOAT SHOW
New Orleans, LA (12–14 November 2024)
MAST
Adelaide, Australia (19–21 November 2024)
OFFSHORE ENERGY
Amsterdam, The Netherlands (26–27 November 2024)
JANUARY
EXAIL MARITIME USERS CONFERENCE
Amsterdam, The Netherlands (21 January 2025)
MARITIME RECONNAISSANCE & SURVEILLANCE TECHNOLOGY
London, UK (27-28 January 2025)
MARINE MEASUREMENT FORUM (MMF)
Exeter, UK (29 January 2025)
FEBRUARY
NAVY TECH
Helsinki, Finland (11-13 February 2025)
SUBMARINE NETWORKS
London, UK (18-19 February 2025)
SUBSEA EXPO
Aberdeen, UK (18-20 February 2025)
MARCH UNDERSEA DEFENCE TECHNOLOGY (UDT)
Oslo, Norway (25-27 March 2025)
APRIL SEA AIR SPACE
National Harbor, MD, USA (6-9 April 2025)
OCEAN BUSINESS
Southampton, UK (8-10 April 2025)
WINDEUROPE
Copenhagen, Denmark (8-10 April 2025)
OCEANS IN ACTION
Biloxi, MI, USA (15-17 April)
MAY IPF WEEK
Virginia Beach, VA, USA (28 April-1 May 2025)
COMBINED NAVAL EVENT (CNE)
Farnborough, UK (20-22 May 2025)
JUNE MTS/IEEE OCEANS
Brest, France (16-19 June 2025)
GLOBAL OFFSHORE WIND
London, UK (17-18 June 2025)
My name is Richie Enzmann. Allow me to welcome you all to the latest issue of Ocean Robotics Planet!
Dear Reader,
On the front cover of this issue, we have Sonardyne enabled resident vehicles inspecting subsea infrastructure. With the increasing need for persistent monitoring and data collection in subsea environments, we’re beginning to see ambitious residency programmes being rolled out. You can read about how Sonardyne are providing the “secret sauce” to provide that all important capability.
Another interesting technology in this issue is the latest ROV mounted advanced subsea visual metrology (ASVM). Oceaneering share their experience with us on this exciting new tech, and how it compares with what has more commonly been used for inspections in the past: Lidar.
We also look at the Kystdesign ZEEROV work class all electric ROV, developed in conjunction with Reach Subsea. This vehicle will be used remotely on Reach’s USV and is scheduled to be integrated and ready next year. We delve deeper into this intriguing project and its development process.
This issue’s centrefold shows the majestic looking new DriX O-16 transoceanic USV along with its little brother, the DriX H-8 USV, both from Exail. I was honoured to be invited to the christening of this brand-new type of USV. The DriX O-16 will soon also have onboard ROV and AUV launch capabilities. You can read more about my visit to the Exail shipyard in La Ciotat, France inside.
In the world of defence, Captain Lundquist reports on the Littoral OpTech workshop he led in Gdynia, Poland. The Baltic Sea’s extreme littoral is a multi-domain battlespace, and the workshop emphasised the increased importance of unmanned systems in the region, where a belligerent Russia has alarmed its neighbours because of its actions in Ukraine. He also reports on the upgrade of the Spearhead-class expeditionary fast transport vessels (EPF) that will possess autonomous capabilities. Meanwhile George Galdorisi shines light on the importance of port and harbour security using unmanned systems.
Finally, we look at the last mission of the Ran AUV. Its last known location was somewhere under the Thwaites Glacier where it disappeared. Some of you might remember that two years ago I was fortunate to see Ran in action within the framework of an AUV workshop. Hopefully, the University of Gothenburg will be able to replace this iconic vehicle to continue their quest to better understand the polar regions. In my opinion it’s important that we are bold and sometimes take risks – even if it means losing some of our prized tools and equipment – to further scientific advancement, and the discovery of our hidden planet.
You can read about all of this in more detail and much more besides. I very much hope you enjoy this quarter’s issue.
Best regards, Richie Enzmann
With the ever-increasing capability of and demand for robotics across the subsea sector, it’s no surprise that there is also an increasing need for persistent monitoring and data collection in subsea environments. We are already seeing ambitious programmes being defined in oil and gas fields. Networks of subsea communications will enable autonomous underwater vehicles (AUVs) to carry out inspection of critical infrastructure such as pipelines and templates, communicating the data back to the shore while remaining resident within the field.
As crucial climate change mitigation areas such as deep-sea floating wind developments and offshore carbon capture and storage (CCS) sites increase, the interest in resident subsea AUVs is only likely to grow. With increasing infrastructure deployed in subsea environments, the need for persistent monitoring and inspection whilst reducing cost and carbon expands.
Advancements in AUV technology are enabling longer endurance and improved manoeuvrability, allowing for remote subsea inspections without the need for ship-borne ROVs. Subsea residency, where AUVs remain deployed for extended periods (weeks to years), is becoming feasible.
Subsea AUV residency offers numerous advantages, revolutionising underwater operations. By enabling prolonged data collection, these systems provide continuous monitoring of critical infrastructure, as well as ocean conditions, and impacts on marine eco-systems. After initial investment, resident systems can bring down the per operation cost of
inspection by minimising the need for regular crewed vessel deployments. Safety is also enhanced through reduced human presence in harsh offshore environments.
Resident systems also feature real-time data transmission to onshore remote operation centres through the seabed infrastructure communication gateways, enabling rapid decisionmaking and facilitating interaction with the subsea infrastructure.
Through Sonardyne’s subsea solutions, AUVs can position and navigate themselves within the resident field as well as transfer data between subsea infrastructure, other vehicles and onshore remote operations centres.
At Sonardyne we provide optical and acoustic communications for subsea AUV navigation and positioning, enabling supervised autonomy for survey, inspection and light intervention. Acoustic systems provide broad command and control, while optical systems allow high-bandwidth, lowlatency communication for real-time human intervention.
When moving between subsea structures, long range positioning and navigation is supported through an acoustic infrastructure that delivers broad area coverage, similar to a satellite network providing positions and navigation capabilities onshore. The subsea network is capable of supporting optimal routes through the field to ensure efficient mission profiles.
Communication gateways on the infrastructure provide navigation aiding in the form of Long Base Line (LBL), remote command and control of wireless assets (AUV, wireless monitoring systems etc), and overall visibility of the underwater environment for the onshore command centre.
The LBL network provides centimetric acoustic positioning to guide the AUV around the operational field as well as to its dock. This method comprises the installation and calibration of an array of seabed transponders around the field. The AUV interrogates these transponders and measures the two-way acoustic time travel. It then converts these acoustic travel times into ranges to position itself within a few centimetres.
If the AUV is also fitted with our SPRINT-Nav hybrid inertial and DVL navigation system, the number of transponders can be reduced with no loss of accuracy. This combination of inertial and LBL positioning is known as “Sparse LBL”. The SPRINT-Nav system uses Simultaneous Location and Mapping (SLAM) algorithms to maintain confidence in its real-time location.
Once the AUV is within close range of a structure that requires inspection, an onshore operator can assume control remotely through our ultra-high bandwidth Bluecomm optical communication modems. This allows delicate, precise, six degrees of freedom manoeuvres to be carried out, enabling detailed examination.
Remote control can also be taken to ensure successful landing into the AUVs docking station, again BlueComm takes over from the acoustics to enable remote onshore operators to guide the AUV to dock with greater precision.
We are working to deliver open communication standards between subsea infrastructure and the AUVs that operate within them. These open standards will ensure interoperability so that any AUV, carrying any transponder can communicate within the field to perform tasks all enabled by Sonardyne’s technology.
An optimal residency scenario could involve multiple AUVs alternating between missions and charging, ensuring continuous operations. Long-range AUVs could perform extended missions before returning to docks near installations, facilitating efficient data transfer and recharging for subsequent missions.
“Subsea marine robotic platforms are now well establishedandwidelyused.Astherequirementfor more persistent monitoring and regular inspection tasksincreases,thereisaneedtothinkbeyondthe roboticplatformitselfandmoreaboutthecomplete marine robotic system. This includes everything fromhumansinonshoreremoteoperationscentres, all the way through to the ability for the vehicle to safelydocksubseaandrechargeitsbatteriesbefore its next mission.
Of course key to any AUV monitoring and/or inspectiontaskistheabilitytopositionandnavigate the vehicle in the field and to a subsea dock, where present. So having a subsea navigation, positioning and communications infrastructure in place that ensures reliable data delivery to the ultimate end user is essential. At Sonardyne we have a 50+ year trackrecordofprovidingreliablesubseatechnologies for this very purpose and see the evolution of AUVs fromshortrangeplatformsdeployedfromshipsinto long endurance and field resident platforms as an excitingopportunity.”
AidanThorn,BusinessDevelopmentManager–MarineRobotics,Sonardyne.
A Sonardyne acoustic network will allow multiple AUVs to have communication and navigation coverage simultaneously. This enables AUVs to work independently. Alternatively, if required, a command or piece of information could be sent to all AUVs in the field at once. Two-way communication allows the AUVs to confirm receipt of their commands.
Underwater docking stations serve as home bases for resident AUVs, providing power recharging, data transfer, and protection during idle periods. Once docked, data is then downloaded optically, enabling faster transfer of larger amounts of data – including images or video – than is possible acoustically. Optical systems have a limited range compared to acoustics, tens of metres rather than thousands, but where deep sea docking, comms and data transfer is required at shorter ranges this is a strong solution.
Resident AUVs can have diverse applications across multiple sectors. In environmental science, they enable continuous monitoring of ocean parameters, supporting climate change research and ecosystem health assessment. These vehicles are also valuable for offshore energy companies, conducting regular inspections of subsea infrastructure to prevent failures.
Additionally, resident AUVs contribute to seabed mapping, marine archaeology, and defence, offering persistent surveillance and data collection capabilities that enhance our understanding and management of marine environments while bolstering maritime security.
The potential of AUV subsea residency is immense, but several challenges must be addressed to fully realise this potential. Ensuring the reliability of complex robotic systems over extended deployments remains a significant engineering challenge. Future developments may incorporate self-diagnosis and self-repair capabilities to address this issue. Additionally, the vast amounts of data generated by resident systems present both opportunities and challenges. Developing efficient methods for data transmission, storage, and analysis will be crucial for maximising the value of these systems.
Looking ahead, several exciting trends are shaping the future of AUV subsea residency. Coordinated groups of resident AUVs could work together to cover larger areas and perform complex tasks more efficiently through swarm robotics. Future resident platforms may blur the lines between AUVs and Uncrewed Surface Vehicles (USVs), with vehicles capable of operating both on the surface and underwater for maximum versatility.
The combination of resident AUVs and USVs with technologies such as floating wind farms, ocean thermal energy conversion systems and seafloor observatories could create powerful collaborations for ocean exploration and resource utilisation.
“Marine technology, especially in the autonomy and roboticssector,isgrowingatanincrediblerate.We’re seeingincreasingnumbersofourcustomersutilising our products for their remote and autonomous operations, confident that over 50 years of marine navigation, positioning and communications knowledge and experience will aid their success. We’re excited to be part of this next wave of technology developing resident, autonomous capabilities for AUVs to operate continuously infield with minimal human intervention.”
DarrylNewborough,TechnicalDirector,Sonardyne.
The advent of AUV subsea residency represents a quantum leap in our ability to explore, monitor and manage the world's oceans. As these technologies continue to mature, they promise to provide unprecedented insights into marine ecosystems, enhance the efficiency and safety of offshore operations and play a crucial role in addressing global challenges such as climate change and sustainable resource management. Sonardyne are actively working with AUV developers, infrastructure providers and end-users to ensure subsea residency is delivered. As we look to the future, the continued development and deployment of resident AUVs will undoubtedly play a pivotal role in shaping our relationship with the marine environment, driving innovation, and unlocking the subsea space.
High resolution imaging in turbid water for improved situational awareness and target identification. Available in 375kHz to 3.0MHz. Depth rated to 500m, 1000m, or 4000m.
Jan Siesjö, Chief Engineer at Saab
Subsea residency is revolutionising underwater operations, offering a game-changing solution for industries like aquaculture, energy, and marine research. By allowing autonomous vehicles (AUV) to remain underwater for extended periods, this technology can reduce costs and enhances efficiency in challenging environments.
One leading solution of subsea residency is Saab’s Sabertooth AUV a very powerful but lightweight inspection, maintenance and repair (IMR) platform. Saab has been researching and developing the AUV to be used as a subsea resident system, where the vehicle would be housed at a docking unit to be recharged and deployed over a continues time-period.
Subsea residency refers to the capability of AUVs, such as the Sabertooth, to remain operational underwater for extended durations—up to six months—without requiring surface support. This technological advancement is transforming the offshore wind and energy sectors by significantly improving efficiency, safety, and environmental sustainability.
Deploying resident AUVs near offshore installations facilitates rapid response to equipment failures and maintenance demands, dramatically reducing operational downtime and associated costs. The continuous underwater presence of these systems minimises reliance on surface vessels, streamlines remote operations, and reduces deployment times for remotely operated vehicles (ROVs).
From a safety perspective, subsea residency mitigates the risks faced by human operators in harsh marine environments. Autonomous systems can perform critical tasks such as inspections and repairs while operating beneath the ocean surface, eliminating exposure to dangerous weather conditions and enhancing overall operational safety.
In marine research and environmental monitoring, subsea residency allows for extended, uninterrupted data collection in critical underwater environments. These long-term deployments enable comprehensive environmental mapping, exploration, and ecosystem oversight, offering early detection of pollution, ecological shifts, and other environmental changes. Such capabilities are crucial for supporting sustainable operations and proactive conservation efforts, ensuring the continued protection and management of marine ecosystems.
Sabertooth is designed for exceptional performance in deepsea environments, capable of operating at depths of up to 3,000 meters. Its advanced features include autonomous docking, extensive range, and 360° hovering, which allow it to handle complex underwater tasks with remarkable ease. The vehicle’s dual-mode functionality adds to its versatility, enabling seamless transitions between autonomous and manual operations, adapting to a variety of mission needs.
Enhancing its deep-sea capabilities, Sabertooth's subsea docking station allows the vehicle to remain submerged for over six months. During this time, it can autonomously recharge and upload data, significantly reducing the need for surface vessels. The vehicle’s six degrees of freedom, including 360° manoeuverability and the ability to hover, further ensure its proficiency in navigating intricate underwater environments. This advanced manoeuvrability complements Sabertooth’s deep-water and docking features, making it a leading solution in subsea residency technology and ideal for complex underwater operations.
Sabertooth’s subsea residency is driven by cutting-edge technologies that ensure robust and precise operations in complex underwater environments. Its autonomous navigation is facilitated by an Inertial Navigation System (INS) and Doppler Velocity Log (DVL), which provide high-accuracy positioning and navigation even in low-visibility conditions. These systems are further augmented by mission-planning software and advanced autopilot functions, enabling the Sabertooth to autonomously stabilise its heading, depth, and altitude without requiring human oversight.
Looking to the future, advancements in next-generation navigation systems will likely build on sonar-based technologies, incorporating onboard sensors to further enhance navigation accuracy. While DVLs have been an industry standard for over two decades, improving feature-based navigation is essential for advancing subsea residency. Sonar technology on AUVs provides a promising solution by utilising seafloor markers and environmental features to confirm precise positioning and improve mission reliability.
One company leading innovation in this space is Modus Subsea Services, based in the UK and now part of Manta systems. It has pioneered the development of underwater intervention drones (UIDs) designed for subsea residency. In 2022, Modus achieved a significant industry milestone by securing the first-ever resident subsea drone contract with Equinor, delivering UID missions that provide life-of-field support and intervention capabilities. This collaboration marks a critical step forward in the commercialisation of autonomous subsea intervention technologies.
Subsea residency technology, exemplified by systems such as Sabertooth, holds immense potential for the future as technological innovations continue to evolve. A key advantage is the significant reduction in dependency on surface vessels, resulting in dramatically lower operational costs across subsea industries. This cost-efficiency allows for the reallocation of resources to other critical operational areas, enhancing overall project viability and scope.
In addition to economic benefits, subsea residency promotes more sustainable operational practices. By minimising the need for frequent surface vessel deployments, these systems significantly reduce carbon emissions, contributing to a lower environmental footprint.
The ability of these systems to function in extreme environments— such as under polar ice or in tumultuous sea conditions—unlocks new opportunities for exploration, resource extraction, and environmental monitoring in regions previously beyond reach. A prominent example is the Sabertooth's role in locating and surveying Shackleton’s Endurance beneath the Antarctic ice, offering invaluable insights into both historical exploration and modern marine technology. This capability marks a pivotal advancement, broadening the horizons of marine research and industrial applications in previously inaccessible underwater domains.
As subsea residency technology progresses, platforms like Sabertooth are set to revolutionise underwater operations, delivering unparalleled efficiency, versatility, and exploration potential.
By Alexander Steele, Michael Sheppard, and Corey Halsell, Oceaneering
Rapid and reliable subsea surveys are crucial for deepwater oil and gas operations, as they generate data vital for assessing asset integrity and ensuring safe operations. Traditional technologies like Laser Imaging Detection and Ranging (LiDAR) have served the industry for decades, but emerging advancements, such as advanced subsea visual metrology (ASVM), are proving to deliver more precise results, faster and more affordable.
ASVM provides a significant improvement in the speed and accuracy of data acquisition during subsea inspections. This technology combines stereo optics, 4K video, and processing tools to generate dense 3D point clouds, allowing for millimeter-precise measurements. By using ROV-mounted cameras and high-power LED strobe lighting, ASVM reduces issues like turbidity and motion blur while ensuring distortion-free images.
A key advantage is its real-time communication with an onshore remote operations center (OROC), where experts monitor the data as it is captured. This enables immediate feedback, ensures data quality, and even allows for remote piloting, reducing the need for personnel offshore and enhancing operational safety. ASVM inspections are also more environmentally friendly, with fewer vessel deployments and a smaller carbon footprint.
LiDAR has been widely used for subsea inspections, where remotely operated vehicles (ROVs) position the equipment to scan the seabed. A single 360-degree scan can take up to four hours, and multiple scans are required to cover all sides of a structure. Afterward, technicians must retrieve the equipment and the data it captured for post-processing, leading to further delays.
LiDAR also has drawbacks when considering image detail. Its scans are not in color, making it difficult to detect gradations in structures or marine growth. Additionally, as data is not available in real-time, issues such as poor visibility or interference from marine life may not be discovered until after the scan is completed, potentially compromising the results.
In August 2023, Oceaneering used ASVM to inspect wells and pipeline end manifolds (PLEMs) at 1,500 ft depth, as part of an annual inspection campaign. The client, who traditionally used LiDAR, sought a faster, more efficient alternative. Our photogrammetry solution, deployed with a Millennium® ROV, completed imaging passes in under 30 minutes, with real-time data streaming to an onshore team for support. The inspection produced detailed colorized models, enabling advanced analysis and comparison with historical data. A variance of only 4.6mm over 65m confirmed the solution's accuracy, supporting long-term asset integrity assessments.
In November 2023, Oceaneering was contracted by a major oil and gas operator to inspect a 36-inch riser in the Southern Caribbean using the Ocean Patriot dive support vessel. Initially, the client requested Oceaneering’s assistance in confirming external wall loss at two locations on the riser. Previous inspections indicated 70% wall loss at the first location and 30% at the second, based on an internally deployed magnetic flux inspection tool.
Due to the client’s requirement for high-accuracy, quantitative measurements to confirm the defect sizes to support an integrity analysis, ASVM was the ideal solution. Oceaneering evaluated several technologies, including computed tomography (CT) scanners and general visual inspection, but selected ASVM for its precision, dynamic nature, and speed of deployment.
ASVM’s ability to deliver sub-millimetric accuracy, combined with Oceaneering's internal quality assurance processes, made it the ideal choice. The system was mobilized quickly, and its 4K imagery and video capabilities were pivotal for capturing detailed data. Each inspection site was carefully cleaned prior to image capture, and Oceaneering's onshore survey and data management
teams monitored the process in real-time, providing immediate feedback on data quality.
During the inspection, the team discovered that the previously documented defect location was incorrect. Using the ROV-based ASVM solution, the anomaly was located at the same elevation but in a different position, allowing the team to capture the full dataset for depth and size measurements. The photogrammetry acquisition was completed successfully and without incident.
Oceaneering’s in-house teams processed the data, generating deliverables that included a detailed report, tri-axial measurements, 3D models, still images, and video. The ASVM system also enabled the team to model additional structures around the riser, which could prove useful should further intervention be required by the client.
ASVM is revolutionizing subsea inspections, offering faster, more precise data acquisition than traditional methods. As this technology becomes more widely adopted, it will offer even greater value to the industry, helping operators ensure the integrity of their assets while reducing costs and environmental impact.
For almost 25years, NETmc Marine has been at the forefront of video recording technology, with many of the world’s largest, and not so large, inspection companies relying on our technology and technical support to ensure smooth operations and compliant video content. Be it single or multi-channel, structures or pipelines, no matter your video source, NETmc Marine has a cost effective recording solution.
Ultra-portable, quickly deployable, agile, and adaptable ROV systems that assist with inspection, condition assessment subsurface situational awareness underwater technology trusted by organizations like Maersk, The Norwegian Coast Guard, Oceaneering, and the US Navy.
Designed to push the boundaries of subsea exploration, ZEEROV (Zero Emission Electric ROV) delivers a new level of performance, versatility, and sustainability. With its advanced electric propulsion system KD300E, ZEEROV is a zero-emission vehicle that offers a more environmentally friendly alternative to traditional ROV’s.
Courtesy of Kystdesign
The electrification project began with an idea to build an electric thruster that could be retrofitted to an existing Supporter ROV. It started as an R&D project for the thruster, but when the development team realised that the retrofit would be more complex, they concluded that it would be easier to build up a bespoke electrical ROV instead. The rationale is that you need to start with the backbone: the power distribution, etc.
While Kystdesign worked on the thruster development, Reach Subsea approached them to build a fully electric system for the autonomous unit they are building with Kongsberg, the Reach Remote USV. This is when Kystdesign decided on the standalone ROV design project that became ZEEROV.
Initially the main design challenge was the size of the Tether Management System (TMS), because the Reach Remote USV is a very small boat with a moonpool. There are restrictions on sizes, and Reach Remote wanted 400m of tether on this TMS. Once the Kystdesign team were confident that this was possible to achieve, they moved forward with both the design of the ROV and the TMS.
In terms of timelines, the ROV development started 2 years ago, and the thruster/motor retrofit began 1-2 years prior to that. Today the ROV unit and TMS are fully complete.
Kystdesign made the thruster and from that they started to design the power backbone for the ROV. Since the vessel is battery powered and only has the diesel generator as a backup, one of the first steps was to figure out how to distribute
and transfer the power. On the topside there is a battery with inverters and the transformer to convert the power to 4000Vac. This runs at 180Hz to keep the transformer size to a minimum.
When this project was started the Kystdesign team thought about doing DC all the way, but the technology wasn’t where they wanted it to be. This is still something they can change at a later stage, but right now the more common AC transformer is being used.
For the ROV, instrumentation has been kept in line with previous iterations. Fibre handling and the instrument power consume about 10kW, and this includes the control pod and the sensor. An 800V transformer was used and 115kW was allocated for propulsion and tooling. A new PCU (Power Control Unit) was built, that is more or less like a subsea PDU (Power Distribution Unit). From the PCU, the power is distributed via a
breakout box or power outlet. It has 12 outputs altogether; seven for the thrusters, one for the auxiliary HPU for the Manipulator and Tooling, because the electrical manipulator isn’t ready for market yet. Kystdesign is still waiting for Saab or Nauticus to launch their electric manipulators, so right now they rely on the Schilling manipulators and add on hydraulic systems. Furthermore, there are four spare power outlets of 800V for future tooling, as the main challenge with electrifying an ROV is that most of the tooling is still hydraulic. As such, the tooling is being run from the ROV or the vessel.
Kystdesign also made a downscaled version of the thruster motor. It has the same inverter that runs on 800V, but on 5-10kW instead of 10-30kW for the thrusters. The breakout box has three functions: it’s the power distribution to each consumer, but with the possibility to turn it on and off – so it can be isolated in case of a ground fault or broken cable.
The thrusters are more powerful than initially expected. This necessitates a longer work window between tides and to withstand higher currents. However, because the system is fully electrical, it also means higher operating temperatures. Of course, when there is an increase in temperature, you have to decrease power consumption. To put this into perspective, in the 10°C water temperature test pool in Norway, the system is balanced when using 20kW continuous power on the thrusters. But if the thruster power is increased to 30kWh then there is about 15 minutes until it overheats. You can still do quite a bit in that time frame, and if you decrease the power back to 20kW then the system will cool down quite rapidly.
The initial ZEEROV unit was the result of a cooperative endeavour between Kystdesign and Reach Subsea. The Work Class ROV is now ready for market. Kystdesign has a state of the art 10-metre-deep test pool to qualify ROV systems and equipment, in addition to a test chamber for testing and qualifying components and sub systems up to 700 Bar. They also cooperate with ocean research institutes, such as UIB, to test and qualify for ultra deep waters. Kystdesign are very happy that they have a good relationship with their clients, as this allows them to cooperate on further improvement and fault handling.
Kystdesign owns this design so it will be up to them on how to further their business case. For now, Reach Subsea have their focus on the follow on as their first client for the ZEEROV. Because the system is still new, they will have to learn how to handle its functions and the technology in
general. However, the same software backbone is used for the control system (albeit in a slightly different layout), and the remote capabilities are the same as the existing systems.
As the software is uniform across vessels, it’s possible to use all existing Kystdesign ROVs on the same remote system. In fact, when they upgrade the software for one system, then they perform an upgrade for all previously manufactured systems at the same time.
The depth rating of the ZEEROV will be 3,000m, but this initial unit for Reach Subsea will be rated for 2,000m. Its only real limitation is in its buoyancy material. It will be approximately 3.5t dry weight, with a payload capacity of 600kg, and a lift through weight of 3,000kg.
The utilization of a USV for this project is important, as it allows the clients to include a larger payload and bigger
tools. However, this does require further planning as once the vehicle has been deployed, there will be no human operators onboard to change any components out.
The extra tooling skid for this project is being built by Reach Subsea. Ideally, they would like it to be operated in the same manner as the Supporter. However, the electrical tooling to do this is not fully available yet. As such, they will have to develop this further.
Reach Subsea and Kystdesign plan on using the Reach Remote USV with the integrated ZEEROV for survey and light IRM jobs. These will include oil and gas and wind farm projects. This configuration is also fully equipped for hydrographic surveys and defence applications. Kystdesign is experiencing great interest in ZEEROV from all over the world, and they are convinced that electric ROVs will be the right choice for large parts of the future ROV market.
10 YEARS OF OCEAN ROBOTICS PLANET
SIGN UP TO STAY INFORMED ABOUT THE MARINE & UNDERWATER ROBOTICS INDUSTRY.
Enzmann,
On the 17th of September a large crowd of around 200 people gathered in La Ciotat, France to celebrate the christening of Exail’s new DriX O-16 Unmanned Surface Vessel (USV). They were all excited to see the newly built and tested USV in its full glory.
The concept of the transoceanic USV was unveiled at Oceanology International in London, UK earlier in the year, and Exail has been working hard to make the concept a reality.
The demo day started with a visit to the Exail production facility where several DriX H-8 were under construction on the production line. This clever setup allows technicians to work on all parts of the vehicles simultaneously, from the top of the mast down to the gondola beneath the keel. Currently, there were five different vehicles which have been built, as demand for the vehicles have increased recently. These are the smaller models that have already been operational for several years. There is now a DriX Series with the H-8, H-9, and O-16 models. Overall, there have been 30 units sold so far, and these have been operated in 19 countries accumulating 180,000 hours of sailing experience over the past seven years.
The tour continued to the remote operations centre where the DriX USVs can be remotely piloted from anywhere in the world. The Centre’s current setup of workstations caters for 24/7 operations of two DriX USVs, across 12-hour shifts. It’s interesting to note that over the years Exail have trained
over 150 personnel to operate these vehicles. The operations centre boasts several screens where maps with waypoints can be accessed for route planning, as well as camera views and hydrographic as well as geophysical data, all of which can be displayed in real time. It was from the Operations Centre that the DriX O-16 was operated during our demo.
The group took Exail’s support vessel to sea, where the speed of up to 16 kts and the manoeuvrability of the DriX O-16 were both demonstrated. Here one could really appreciate the speed of the vessel, along with its ability to deal with the waves and currents. This operational demo took between 30 minutes to an hour before the smaller group of guests returned to shore.
So how does the DriX O-16 compare with the original DriX H-8? The 16 in its name comes from its length as the USV is 15.75m long and weighs 10.5 tonnes. It has enhanced sea handling capabilities and increased range of up to 30 days, during which time it can cover between 2,500nm and 3,500nm. This range means that it’s able to undertake transoceanic missions.
Its considerable range is also very well suited for deep water hydrography, and its design was based on the lessons learned over seven years of tracking regular DriX H-8 operations. In fact, the hydrographic sensors on this new vehicle are capable of surveying to full ocean depth, using Kongsberg EM124 or EM304, or any equivalent multibeam echo sounder.
Reliability and redundancy were important in the DriX O-16 design because of potential long range, high endurance missions. For this reason, the sensors require very little energy.
The mast is equipped with cameras (including infrared for night vision), lidar, and radar. The lidar is useful for detecting close objects in high resolution, while the radar is for detecting objects far away.
When performing surveys of the subsea cables of windfarms, these equipment are very useful for obstacle avoidance: preventing collision between the vehicle and the wind turbine piles.
Another important feature of this new DriX O-16 is the dual hybrid propulsion and station keeping ability. The dynamic positioning allows for a hovering mode which is important for the launch and recovery of the ocean robotics payload. These payloads will be various inspection class ROVs, AUVs, and the FlipiX ROTV (Remotely Operated Towed Vehicle).
DriX O-16 is available as a stand-alone drone and Exail also offer a range of services including proof of concept on customer projects enabling clients to acquire hydrographic data. In fact, this has previously presented a useful option for potential clients to get familiar with the USV technology before deciding to purchase.
Currently, the DriX O-16 is integrated with all the sensor solutions for hydrographic survey, and the integration of the ROVs, AUVs, ROTVs to the payload bay is under way. This payload bay located at the aft of the vehicle is where the launch and recovery of the vehicles will take place. Although the DriX O-16 is now fully available and capable for hydrographic missions, these future vehicle payload options are expected to be available sometime in 2025.
Rent from our inventory of almost 1000 products
Two locations for greatest accessibility Norway and the UK
Equipment you can count on. People you can trust.
www.offshorerental.no
Looking for a way to revive old, damaged or worn buoyancy modules, giving them a second life?
Our subsea buoyancy repair and refurbishment service is designed to do just that. An alternative solution as modules become worn and damaged, extending service life to ensure you get maximum usage.
Repair any damaged or missing sections
Repaint or change of paint colour
Recoat with a fresh protective skin
Application of any logos, stencil graphics or non-slip coatings
Opportunity to make modifications or change configuration
By Chris Buckle, Commercial Manager, Forum Energy Technologies (FET)
When a submarine is in distress, there is no time to negotiate, and no cost is spared. Having a rescue vehicle available in advance to quickly deploy is a cost that should be considered as an absolute necessity. I would offer this is the case, not just for countries and their military branches operating subsea, but also for private organisations that are travelling deeper than ever before.
As militaries crank up spending – the ten countries with the largest defence expenditures incurred almost USD $2 trillion in 2023 alone – conversations around subsea rescue are as fervent as ever and on a wider scale than ever before. There is a recognition that the different parts of a military’s subsea operations are all vital elements of a wider arsenal.
What I have found interesting, however, is that submarine rescue provisions are not always fully considered when a country’s submarine fleet is commissioned or expanded. This is surprising given that were an incident to occur and the organisation is not in a position to save its team, the reputational impact would be huge. Why then do organisations not find a rationale for making this important investment?
The rationale behind submarine rescue capabilities is simple: the cost of inaction is unacceptable. Submarines, by their very nature, cannot be immediately reached when in distress, unlike surface ships, where a quick evacuation or external aid might be possible, submariners can be trapped hundreds of meters below the surface, with limited oxygen and no straightforward way to escape.
Further, the psychological and political impact of losing an entire crew in such a harrowing manner cannot be overstated. This is why FET is always looking to bring the newest proven technologies to the market to ensure that our systems suit a wide range of operations in the defence market.
Beyond these obvious reasons for investment, a submarine disaster can have a ripple effect on global security and naval operations. The public and political backlash from such incidents may force navies to withdraw or restrict submarine operations, hampering strategic goals at a time when nations are depending more than ever on their submarines for deterrence.
The loss of even a single submarine, particularly if it carries sensitive or classified materials, can lead to serious national security consequences. Indeed, the ability to rescue submariners in peril can be considered a form of deterrent in its own right and can reassure crews that they are not alone when in need.
Finally, the long-term and strategic benefits are unmistakable. A Submarine Rescue Vehicle (SRV) is designed to be in service for 20 years, and this duration extendable via life extension programs.
Defence is, by its very nature, a dangerous business but steps should be taken to mitigate all risks.
Tuesday, 11 February, 2025
Scandic Marina Congress Centre, Helsinki, Finland To
Thursday, 13 February, 2025
27 - 28 January | London, UK
Featured speakers include:
Captain Matthew Syrett, Deputy Head Maritime and METOC, National Centre for Geospatial Intelligence (NCGI), UKStratCom
Mr Kyle Hunt, Principal Advisor and Acting Deputy Director, National Maritime Intelligence-Integration Office, US Navy
Rear Admiral (UH) Krzysztof Jaworski, Commander, Maritime Component Command, Polish Navy
Commander Alan Darlington, SO1 Information
Exploitation, Navy Digital, Royal Navy
Captain Dr. Robert Koch, Branch Head Cyberspace, NATO ACT
Subheading
Early bird rate available until the 27 November
By Capt. Edward Lundquist, U.S. Navy (Ret.)
The Baltic Sea and its approaches have emerged as a potential multi-domain battlespace involving Northern Europe and Russia. The high volume of critically important maritime activity converges and concentrates in these complex coastal waters.
Maritime activity, such as fishing, shipping and offshore wind energy, are expected to increase dramatically in the next 20 years. Likewise, tensions are running high as a belligerent Russia has alarmed its neighbors and all of Europe because of its actions in Ukraine.
It was not so long ago that much of the Baltic Sea was the realm of Russia and her Warsaw Pact clients. However, the former Communist states of Poland, Lithuania, Estonia and Latvia are now full-fledged members of the NATO alliance, as are the newest NATO members, Sweden and Finland. Today, Russia’s footprint in the Baltic Sea has been reduced to the port of St. Petersburg and the enclave of Kaliningrad.
The recent Littoral Op-Tech workshop, held in May at the Polish Naval Academy in Gdynia, Poland, provided a unique opportunity for operators, strategists and policy experts to examine and discuss the geopolitical significance of Poland and the Baltic Sea, as well as threats, challenges and opportunities in the region, which have been amplified since Russia’s invasion of Ukraine.
The Gdynia symposium was the most recent in the series of conferences that have been held around the world to study and discuss key maritime littoral operating areas. Workshops in Stockholm, Sweden, Helsinki, Finland, and now Gdynia, have focused on the Baltic Sea. The workshop in Tokyo, Japan looked at the South China Sea; the event held in Cartagena, Colombia, examined the Caribbean and Eastern Pacific; the Halifax, Canada, workshop, looked at the Arctic; and the conference at Souda Bay, Crete, Greece, emphasized the challenges in the Eastern mediterranean.
“The Littoral OpTech series of workshops are about learning from each other,” said workshop chairman, retired Swedish navy Capt. Bo Wallander, now with Saab AB, which sponsored the event. “While littoral environments and maritime traffic varies, all navies that defend or operate in coastal waters share some similar challenges.”
According to Wallander, the littorals are the areas where land and sea converge, and where most people live and global commerce travels. The proximity to islands and shores means littoral warfare includes a broad spectrum of threats in all domains, to include land, surface, air, undersea and seabed threats, as well as cyber and space-based threats. The Baltic Sea is an “extreme littoral” environment because the number of different nations with maritime borders on the Baltic Sea; the varied and extreme currents, different types of bottoms and coastlines, numerous islands, shifts in temperatures and salinity, and atmospheric conditions which impact sensors; and the significant amount of shipping traffic.
From a naval warfighting perspective, the Baltic Sea is especially challenging. “It is a very complex environment with limited space, and where it is easy to hide and difficult to detect targets,” Wallander said. “This means very short reaction times. The littorals are also characterized as having a great number of non-military actors like merchant ships, fishing and pleasure boats.”
In his keynote remarks, Rear Adm. Wlodzimierz Kulagin, Chief of Armaments Brach of the Polish Navy Inspectorate, said that having the workshop in Poland while there is a war going on at the nation’s eastern border is a statement of solidarity to the allies, all of Europe, and especially and to Ukraine.
“Enhanced cooperation and exchange of information to build maritime situational awareness is a starting point for each country,” Kulagin said. “The crucial factor remains the same: our military reaction time.”
Kulagin said “operational calculus” has been adjusted with the entrance of Finland and Sweden into the NATO alliance, and the added value they bring for defense, deterrence and mutual security cooperation in the region.
During the last Littoral OpTech workshop in Helsinki in 2022, the participants concluded that seabed warfare should be treated as a new warfighting domain, especially in light of sabotage events involving the Nord Sea pipelines.
For that reason, and the threat from underwater weapons such as submarines and mines, the workshop emphasized the increased importance of unmanned systems in the region, particularly in the undersea domain.
Eric Olsson, a retired Royal Swedish naval officer representing Embeddedart AB, which was one of the sponsors for the workshop, spoke about the challenges of operating below the surface of the sea.
Olsson talked about the cutting-edge technology available today for maritime sensor systems and the ability to carry those sensors on unmanned autonomous platforms. But, he said, attention must be given to developing the ability to send information between systems below, on and above the surface.
“There is a complexity with subsurface communication and the ability to communicate intelligence and to deliver it where it is needed, especially when you're talking wide amount of information,” Olsson said. “We need autonomous vehicles on the surface to be the communication link between subsurface vehicles and the above water networks, and be the link to the kinetic effectors to bring effective power into the battle space.”
“Technology is great, but it needs to have a level of maturity,” said Olsson.
Dr. Roger Berg, the director of technology management at Saab Kockums, said “disruptions” in technology and business models have “changed warfare forever,” especially for sensing and reacting in the confined Baltic Sea.
Berg cited several new kinds of precision navigation and timing that to replace GPS when needed; inexpensive drones that have replaced exquisite sensors and weapons delivery
systems; and hand-held devices that can call for fire support in a fraction of the time that it used to take to get permission to shoot.
The workshop also provided a timely and relevant opportunity to recognize the 75th anniversary of the NATO Alliance.
“The event examined a rethinking of the strategic security of the Baltic and how we engage with the new technologies and peer competitors,” said James Bergeron, politicalmilitary advisor to the NATO Allied Maritime Commander in his keynote address at the workshop. “Our best chance for avoiding major conflict is to signal that we're quite ready to prevail, if we must.”
By Capt. Edward Lundquist, U.S. Navy (Ret.)
The Navy has begun building out a fleet of unmanned surface vessels to perform a variety of combat and support missions. One such ship is the Spearhead-class expeditionary fast transport (EPF), operated for the U.S. Navy by Military Sealift Command.
The lead ship, USNS Spearhead (T-EPF 1), was delivered to the Navy in 2012. The Navy’s program of record is to build 16 of the high-speed catamarans at Austal USA in Mobile, Ala. USNS Apalachicola (T-EPF 13) normally carries a crew of 41, but she was modified during construction to operate without a navigation crew when needed. It can still carry troops (up to 312 personnel) or other passengers, but it can also carry priority cargo through dangerous high-threat environments without anyone onboard.
The 338-foot Apalachicola entered service in February 2023. Although it is not part of the Navy’s growing fleet of LUSVs and MUSVs, the Navy has said that Apalachicola is the first “fully operational US naval ship” with the ability sail autonomously in sea lanes frequented by other commercial vessels.
“The autonomous capabilities being demonstrated by this prototype system represent a major technological advancement for the EPF platform, the Navy at large and our industry partners. EPF-13 will be the first fully operational U.S. naval ship to possess autonomous capability including the ability to operate autonomously in a commercial vessel traffic lane,” said Program Executive Office, Ships Strategic and Theater Sealift Program Manager Tim Roberts.
Austal USA is partnered with General Dynamics Mission Systems as the systems integrator to build the EPF. “We design, integrate and test the Expeditionary Fast Transport's electronic mission systems, including the backbone computing infrastructure, called the Total Ship Computing Environment (TSCE), and internal and external communication, electronic navigation, aviation and armament systems,” said Scott Beauchemin, vice president of surface systems at General Dynamics Mission Systems. The company joined with Austal and L3Harris to provide the autonomy capability for Apalachicola
Beauchemin said his company has 25 years of experience in providing autonomy for unmanned systems. “Autonomy gives the warfighter a greater range of weapons and effectors – thereby taking sailors and marines out of harm’s way.”
Apalachicola underwent significant testing in 2022 – called Unmanned Logistics Prototype trials – to assure the autonomous systems worked properly, and to demonstrate that a large ship like a n EPF can safely and effectively become a self-driving platform. The Navy looked at Apalachicola’s ability to navigate at night and in different weather conditions and sea states.
According to a Navy statement, “Each test event increases the perception capabilities and complexity of behaviors demonstrated by the autonomous systems. Test evolutions include point-to-point autonomous navigation, vessel handling and transfer of vessel control between manned to unmanned modes.”
The statement said that the trials lay the groundwork for future autonomous vessel operations, to include vessel encounter and avoidance maneuvering and compliance with International Regulations for Preventing Collisions at Sea (COLREGS).
An L3Harris press release said that “Apalachicola was able to demonstrate autonomous ‘station keeping,’ where Apalachicola was able to match the course and speed of another vessel. The General Dynamics-built FutureWaves and a hull-monitoring system were incorporated by Austal USA and integrated with ASView by L3Harris, which allowed the vessel to navigate around, through or in response to varying sea states and weather conditions. L3Harris was
also able to integrate an acoustic sensor, McQ Sonowatch, to detect maritime sounds, such as a ship's horn, increasing the COLREGS-compliant capability.”
Following the successful conclusion of the testing, the ship continues to operate with a normal crew but retains her autonomous systems.
Of the 16 EPFs built or under construction at Austal, the final three are considered Flight II ships, with some enhanced medical capabilities. They will be followed on the production line by the expeditionary medical ship (EMS), which will be similar but larger than the EPF, and will be fully equipped for medical care. In addition to their normal capabilities, EPF 14, 15 and 16 are equipped with a “forward resuscitative care capability with a limited Intensive Care Unit (ICU) and medical ward.”
In addition to autonomous operations, Apalachicolaconducts traditional logistics missions, warfighting experimentation and demonstrations, humanitarian support projects, disaster response and maritime law enforcement activities.
When its autonomous capability is engaged, Apalachicola is the U.S. Navy’s largest ship platform in the fleet. EPFs are fast. They can transport 600 short tons of military cargo for 1,200 nautical miles at an average speed of 35 knots supporting rapid movement of conventional or special forces, equipment and supplies. The EPF’s high speed, shallow draft, and ability to load and unload in austere ports enables expeditionary force agility without reliance on shore-based infrastructure. The ships were originally part of a joint Army and Navy program, designated as the Joint High-Speed Vessel (JHSV). The Army dropped out and the ships were redesignated as EPFs in September 2015.
The term “globalization” is used to describe the lifelines of seaborne international commerce. Globalization has lifted hundreds of millions of people out of poverty. Most would agree that seaborne trade has been the engine of globalization in the past, that it continues to be so today, and that it most likely will be in the future.
While many people focus on the importance of ships in carrying this seaborne trade, they often forget that the critical nodes that support this globalization and burgeoning world trade are the world’s ports and harbors. From Antwerp, to Rotterdam, to Los Angeles, to Shanghai, to other megaports, as well as hundreds of smaller ports, these harbors are critical to world prosperity. A disaster in one of these ports similar to what happened in the harbor in Beirut in 2020—an oil tank explosion, a fire or other catastrophe on a large oil tanker, or any of a host of other events—could close one of these ports for an indefinite time and also spill an enormous amount of pollution into the oceans.
The magnitude of providing comprehensive security for an average size port—let alone some of the world’s mega-ports— can lure port authorities into wishing away the challenge. But in an increasingly dangerous world where not just terrorists, but others, may wish to make a statement or lash out at a particular nation, ports present an all-too-inviting target.
Faced with this challenge, port authorities must ensure security twenty-four hours a day, every day. This task includes threat detection and security response, continuous inspection of port assets, as well as on-demand inspections after storms or other disasters, ongoing surveys to ensure navigable waterways, hull inspections, and a wide-range of other missions.
In 2024, the state of the art of providing security for ports and harbors has not advanced substantially. There are two primary methods of monitoring a port. Most large ports have cameras placed at strategic locations and monitored by watchstanders. Port officials also provide security with a variety of manned surface vessels that patrol on a regular schedule. This traditional approach is good, but it can lead to gaps in coverage that render ports less secure than they could be.
Cameras appear to offer a cheap and effective solution, but what people forget is that someone— often several people— must monitor the video the cameras collect. With some ports maintaining scores of cameras—or more—this entails having a command center and enough watch-standers to monitor the cameras in real-time, twenty-four hours a day.
Similar issues accompany the use of manned craft to patrol a harbor of any size. Manned vessel operations are increasingly expensive, are often limited by weather and water conditions, and physically stress port professionals. These craft must be manned—typically by at least two people at a time—and due consideration must be given to just how long people can bounce along in a small vessel. Add bad weather or choppy seas, and the limits of human endurance lead to either not using the craft at all or switching crews more frequently.
Given the challenges of providing comprehensive security for ports with current state-of-the-art systems and capabilities, it is little wonder that port officials are searching for technology solutions that will enable them to provide better security at lower cost.
The Port of Los Angeles (POLA) is one of the world’s megaports and is the busiest port in the United States. It comprises 42 square miles of water, 43 miles of waterfront and 26 passenger and cargo terminals. POLA handled over 9.3 million twenty-foot equivalent units (TEUs) of cargo in the last year for which statistics are available.
Current capabilities to secure the Port of Los Angeles involve monitoring the video provided by hundreds of cameras throughout the port, as well as patrolling the port’s expanse of water with a fleet of manned vessels. This methodology stresses the ability of POLA authorities to provide around the clock security.
For these reasons, Port of Los Angeles officials decided to explore the possibility of using unmanned surface vehicles to enhance the security of the port. To that end, port officials invited Maritime Tactical Systems Inc. (MARTAC) to visit and demonstrate the capabilities of their MANTAS, a high-performance, commercial off-the-shelf 12-foot USV built on a catamaran-style hull.
The MANTAS can be equipped with a wide variety of abovesurface sensors (EO/IR/thermal video) and below-surface sensors (sonars and echo-sounders), as well as other devices such as chem/bio/nuclear sensors, water quality monitors, and above/below surface environmental sensors.
During the visit to the Port of Los Angeles, MARTAC representatives provided a comprehensive briefing on MANTAS capabilities, took a three-hour boat tour to observe the entirety of POLA authorities’ span of operations, and then provided a remote demonstration where port officials controlled and observed a MANTAS T12 operating off the eastern coast of Florida. The demonstration validated the going-in assumption that employing a thoroughly tested and proven USV is a viable solution POLA is keen to pursue.
After observing the MANTAS remote demonstration, it was determined that the capabilities of this USV met the requirements for the wide variety of missions for the Port of Los Angeles. That said, port officials asked MARTAC to scale-up the MANTAS to a 24-foot and 38-foot version. It was felt that the 12-foot MANTAS was so stealthy that ships in transit could not see it. Additionally, the larger T24 and T38 could operate for longer periods and carry additional sensors. The T38, now referred to as a Devil Ray, has now been featured in a number of U.S. Navy exercises and has also demonstrated the ability to provide port security in other locations such as the Port of Tampa.
The enhanced port and harbor security methodology described in this article has not been evaluated previously, and there is a reason. The technology to provide reliable, adaptable and affordable USV support to augment manned capabilities and expand the reach of port security officials at facilities such as the Port of Los Angeles simply did not exist just a few years ago. But that has now changed.
This POLA demonstration with the MANTAS T12, followed by the Port of Tampa demonstration with the larger Devil Ray T38, has certified that commercial-off-the-shelf unmanned
surface vehicles can ably conduct a comprehensive security inspection of a mega-port. As a facility with a longstanding need to augment its manned vessel patrol activities with emergent technology in the form of unmanned surface vehicles, the Port of Los Angeles and Port of Tampa demonstrations provided two best practices examples of the artof-the-possible for enhancing port security.
All nations would be well-served to leverage emerging technology to enhance the security of the ports and harbors that make the global economy hum. To fail to do so would be inviting a disaster that is eminently preventable.
Captain George Galdorisi is a career naval aviator and national security professional. His 30-year career culminated in 14 years of consecutive service as executive officer, commanding officer, commodore, and chief of staff. He enjoys writing, especially speculative fiction about the future of warfare. He is the author of 18 books, including four consecutive New York Times bestsellers. His latest book, published by the U.S. Naval Institute, is Algorithms of Armageddon: The Impact of Artificial Intelligence on Future Wars.
WHOI will produce two medium-size remotely operated vehicles (mROVs) beginning later this year with a relatively small footprint and operated by smaller teams of engineers, making them more easily transported and designed to work from the Regional Class Research Vessels fleet scheduled to begin entering the US. Academic Fleet in 2026. (Concept rendering by: Dave Fustino/ETHOS, llc/©Woods Hole Oceanographic Institution)
A new, integrated system will enable ocean science, exploration, and restoration efforts from a wider range of vessels, paving the way for more successful and efficient operations.
The Woods Hole Oceanographic Institution (WHOI) has received complementary awards from the U.S. National Science Foundation (NSF) and the National Oceanic and Atmospheric Administration (NOAA) to produce two medium-size remotely operated vehicles (ROVs). The vehicles will support growing demand to conduct research, exploration, and restoration on the seafloor and in the water column from ships with limited deck space and berthing. The vehicles are scheduled to begin construction in 2024, start engineering trials in late 2025, and be fully available for the scientific community in 2027.
The new, mid-sized class of ROVs (mROVs) are being designed with a relatively small footprint and will be operated by smaller teams of engineers. The mROVs will also be more easily transported and operated than the current 6,500 meter-capable ROV Jason, which was built and is operated by WHOI’s National Deep Submergence Facility (NDSF) and has completed nearly 300 missions since 2006. The mROV’s size will expand opportunities to reach depths of 4000 meters (nearly 2.5 miles), on missions that do not require the full capabilities of a large ROV like Jason. Technology such as cameras, lights, manipulator arms, and mission-specific sensors and samplers will be added as needed.
“The success of ROV Jason over the past two decades has demonstrated to the scientific community the utility and versatility of remotely operated vehicles,” said NDSF Director Andy Bowen. “What is needed now are platforms that fill the niche between large, work-class vehicles such as Jason and small vehicles used primarily for observation, while still retaining the functions scientists need to conduct leadingedge work in the deep ocean.”
Introduction of the mROVs will significantly expand research and restoration opportunities for the oceanographic community, which is presently limited to just a few vehicles capable of supporting their work. Their development is motivated partly by construction of the NSF-funded Regional Class Research Vessels (RCRVs), which are scheduled to begin entering the U.S. Academic Fleet in 2026. These small, multifunction ships are intended to support research of the coastal and near-shore waters that are among the most complex and rapidly changing parts of the ocean—areas well-suited for exploration using a tool such as an mROV.
“The demand for ROV-enabled science has grown steadily over the past decade and the nimbler mROV will support many of the missions that Jason would otherwise perform, freeing up time for demands in deeper water or with needs for the larger ROV,” said Brian Midson, NSF Program Director for Ship & Submersible Support. “We are eagerly anticipating
the ability to support even more exciting science in some of the most challenging to access regions of the planet.”
“By capitalizing on the Ocean Exploration Cooperative Institute (OECI) with this inter-agency project, we all benefit from the capabilities of OECI organizations, including WHOI’s vehicle engineering, the operational expertise of the University of Rhode Island, and the operational support of the University of Southern Mississippi (USM).” said Jeremy Weirich, Director of NOAA Ocean Exploration.
“NOAA is excited that this investment will increase capacity for the restoration and monitoring of natural resources in the Gulf of Mexico that were injured by the Deepwater Horizon oil spill,” said Carrie Robinson, Director of the NOAA Fisheries Office of Habitat Conservation. NOAA’s largest funding contribution to the award is supported by the Mesophotic and Deep Benthic Communities restoration projects, which aim to restore vital seafloor habitats damaged by the oil spill.
Design and construction of the mROVs will be facilitated by a partnership between WHOI and Greensea IQ, a leader in ocean robotics technology located in Richmond, Vt., and Plymouth, Mass. The primary objective of the partnership between Greensea IQ and NDSF is to create an environment of open collaboration that will facilitate the integration of existing as well as new subsea platforms, that will benefit all of science and discovery in the ocean. Greensea IQ’s open architecture platform will provide the backbone for these developments. The adoption of common standards, tools, and technologies that are shared throughout the community via NDSF will modernize and strengthen the deep submergence capability within the US.
Construction of both vehicles will begin in coming months with conceptual and preliminary designs by WHOI and Greensea IQ, supported by a science advisory committee composed of federal, academic, and industry experts. Engineering and sea trials are expected to follow in late 2025, aided by use of Greensea IQ’s OPENSEA open-architecture vehicle operating system.
“WHOI and Greensea IQ are collaborating to break down barriers that often hinder innovation, leveraging their combined strengths to advance ocean research,” says Ben Kinnaman, Greensea IQ CEO. “Greensea IQ has a rich history within the scientific community with the adoption of OPENSEA by several research institutions such as MBARI and Schmidt Ocean Institute. By extending OPENSEA, our open architecture platform, further into the science community via NDSF, Greensea IQ will make a higher impact that will support a more diverse community of scientists and researchers.”
One of the vehicles will be operated by NDSF and the other by USM. In addition to providing more opportunities to conduct advanced, ROV-supported operations, the integration of two mROVs into the research and natural resource management communities will also help spur growth of the ocean-based blue economy workforce. The need for maintenance and operation staff will enable NDSF and USM to recruit a larger, more diverse technical staff to support the mROVs on land and in the field and to create further technical advances in marine robotics.
“The mROVs themselves are only the tip of the iceberg,” said Bowen. “The mROV concept advances exploration and understanding and we're excited to be expanding our impact through this unique new program.”
The Underwater Glider User Group (UG2) is making waves as a community-based coalition to bolster scientific collaboration and resource sharing between glider operators, data users, manufacturers, academia, and federal agencies. Born out of the 2017 Interagency Ocean Observation Committee (IOOC) U.S. Underwater Glider Workshop and the 2019 International Glider Workshop, UG2 emerged from a shared vision to enhance the capabilities and effectiveness of underwater glider missions and technology in United States waters. These workshops identified key actions to improve ocean monitoring, operational reliability, data management, interagency, and international coordination. Additionally, the glider community recognized a critical need for a platform where members could exchange insights on glider technologies, share scientific achievements and challenges, and discuss data handling and management.
Since its inception, UG2 has experienced significant growth, boasting nearly 500 members now. The group has also achieved several milestones, including launching a bi-monthly webinar series, appointing a full-time coordinator, forming a steering committee, and successfully hosting four glider-focused workshops. Now based at the Center for Ocean Leadership (COL) under the University Corporation for Atmospheric Research (UCAR) and supported by the U.S. Integrated Ocean Observing System (IOOS), UG2 continues to be a driving force in advancing the glider community.
In September of 2024, UG2 hosted its most recent workshop at the University of Michigan, Ann Arbor, U.S., bringing together 140 glider users from diverse backgrounds –including project managers, data experts, industry experts, pilots, researchers, and students – from across the U.S., Canada, Australia, New Zealand, and Europe. Over three days, participants gathered for dynamic discussions on underwater glider technologies and their practical applications. The Workshop featured engaging presentations, collaborative breakout sessions focused on data management, sustained glider networks, microcredentials, and interactive training opportunities for early career participants to facilitate knowledge sharing and networking within the glider community –the core mission of UG2.
A key highlight of the workshop was the strong participation from early career professionals and students, who comprised over 35% of attendees. Recognizing them as the
next generation of glider users, the workshop provided tailored training sessions on writing proposals and developing elevator pitches, along with numerous networking opportunities. For the first time, UG2 leadership also offered constructive feedback on all student and early career posters and presentations, culminating in awards for the highest scoring in each category. This initiative highlighted and encouraged student and early career engagement and fostered the collaborative UG2 spirit!
Looking ahead, UG2 leadership is set to publish a comprehensive post-workshop report by the end of the year, detailing the action items and objectives for UG2 and the broader glider community. In exciting news, the next UG2 Workshop will be in 2026, with more details coming soon. To learn more about becoming a UG2 member or about this group, please visit www.underwatergliders.org or email info@underwatergliders.org
Since the first underwater gliders were introduced in the 1990s, they have become an essential workhorse for gathering ocean data, regularly carrying out missions of six to eight months and more. Their low-power, longendurance capabilities enable them to profile and regularly transmit high resolution oceanic, biological and climate research data, over long periods, in near-real time to shore.
Typically, they profile from the surface to the bottom, or to 200–1,000 m depth, taking 0.5–6 hours to complete a cycle from the surface to depth and back. As standard, they are usually equipped with a CTD sensor and a range of optical sensors. But they also need regular servicing, particularly of their sensors and payload bays, to ensure they’re ready for the next, often seasonally critical, mission.
The UK’s National Oceanography Centre (NOC) has been fulfilling this need, providing a European servicing capability since April 2022, collaborating with Slocum Glider manufacturer Teledyne Marine. Building on its extensive glider expertise, the accredited European Glider Service Centre at NOC’s Southampton waterside site focuses on servicing payload bays and sensors, including calibration and pressure testing.
A large proportion of the work is on conductivity, temperature, depth (CTD) sensors, but the NOC Glider Service Centre team is looking to expand this offering to include calibration of additional optical sensors and servicing glider buoyancy pumps – the glider’s driving force. Alongside the service offerings, NOC also provides glider training and, from early 2025, it will be providing piloting services.
Daniel Woods, commercial development manager, explains: “Teledyne sold its 1,000th glider in 2022, which is a fantastic milestone for the number of gliders in circulating and being used to observe the ocean globally. Autonomy increasingly leads the way in ocean research, weather forecasting and naval operations, with gliders playing a major role, thanks to their unrivalled range, duration and low cost. That creates a demand for servicing capability, including here in Europe. With our expertise in glider operations and maintenance, with one of the largest fleets of Slocum Gliders, it was an obvious step to offer these services to others.”
Teledyne supported the collaboration. “We have our own global glider service centre in North Falmouth, Massachusetts,” says Melissa Rossi, Senior Director, Customer Service & Repair, Marine Vehicles, at Teledyne Marine. “But having a centre in Europe means faster turnaround times for our European Slocum users, particularly around sensor calibration. This means more on-mission time for them and, for science users especially, being able to hit those seasonal missions they’re most interested in for the science needed to better understand the ocean and its interaction with earth systems.”
UserstodateincludetheUniversityof BergenandIreland’sMarineInstitute.
Steve Woodward, Engineering Manager – Gliders, at NOC, says, “NOC’s glider heritage goes back to 2006, with trials off Majorca, followed by deployments in 2007 and 2008, as part of a project to study deep convection in the Gulf of Lions in the Mediterranean, led by Dr David Smeed (research scientist in NOC’s Marine Physics and Ocean Climate group). Since then, glider capabilities have grown. They’re carrying more and more sensors, producing more data and doing ever longer missions. Six to nine-month missions are fairly common and we’re close to regularly doing 12-month missions. That is a big advantage to data gathering.”
Advances have meant NOC are starting to use gliders to gather data under ice sheets and to recover data from other deep-sea instruments. They’re also being used for adaptive sampling, where, if they detect a change in temperature, indicating a thermocline, they can either start sampling in that area or follow that body of water.
NOC has a fleet of around 30 gliders, a majority of which are Slocum Gliders, which form part of the National Marine Equipment Pool Facilities and run by Marine Autonomous and Robotic Systems (MARS) group at NOC. In addition to those, it’s provided servicing for a further 13 payload bays from other organisations’ gliders.
The work usually includes performing CTD sensor calibrations in NOC’s calibration laboratory, reducing lead times along with reducing the risk to sensors caused by additional transport and handling. Access to two hyperbaric pressure testing tanks at NOC also allows for testing down to 6,000 m water depth equivalent.
The University of Bergen has been a customer since the service centre opened its doors mid-2022 and it now carries out the CTD calibrations and other repairs for all of the Slocum gliders
in the university’s fleet. “Their experience in working with ocean platforms is evident from the detailed technical support and advice we receive while services are being carried out,” says Fiona Elliott, head engineer, at the University of Bergen.
Excellent communication and prompt servicing times also allow the university to more accurately schedule its glider operations, essentially halving previous downtimes experienced while completing calibrations, she says.
“This means we are able to keep more gliders in the water and we know measurements they’re collecting are reliable,” Elliott adds.
The service centre work offers a mutually beneficial relationship to NOC and the organisations it supports, says Woodward. “We’re able to apply the experience we have, but we also learn and enhance our capabilities with the work we do as part of the Glider Service Centre, working on perhaps 12 to 15 sensors a year we wouldn’t otherwise have been working on. This then feeds back into the science our researchers and scientists do at NOC. Our income from the servicing also goes directly back into the science, literally funding some of our glider work and supporting advances in ocean science. It also creates a community. We’re all connected and that benefits everyone in the glider user community, feeding a wider ecosystem.”
In addition to the servicing, the centre has been providing training courses. These cover everything Slocum Glider users need to know about using the platform, from theory to preparation to maintenance, as well as use and processing of glider data, mission planning and logistics. This includes practical deployment and recovery sessions in the harbour at NOC. These have been attended by a wide range of institutes, universities and commercial organisations from around Europe, but also as far afield as South Africa.
Organisations with staff that have attended glider training courses include the University of Hamburg, Green Marine UK, PO Maritime, the Royal Netherlands Institute for Sea Research (NIOZ) and Sea Technology Services in Cape Town.
The next course is planned for April 1-5, 2025, perfectly timed for the week before Ocean Business, also hosted at NOC, which will hopefully suit delegates who want to attend the event as well.
Some specialist courses, run by component manufacturers, such as Rockland Scientific, who make instruments to measuring turbulence, are also hosted at NOC. By being able to use sensors already at NOC, as well as its laboratories, it is easier for overseas companies to provide training in Europe.
More widely, NOC is also providing commercial glider services, which include an agreement with the UK Met Office which involves use of NOC’s gliders to deliver near real-time ocean measurements. This includes temperature and salinity, that are critical to ocean and weather forecasting. This project started in 2022 and is running until August 2026. From early 2025, it’s also looking at delivering some glider piloting services.
Ran, the seven metre-long, bright orange, autonomous underwater vehicle (AUV) and a highly valued component of the International Thwaites Glacier Collaboration (ITGC), has gone missing in action in West Antarctica. The Kongsberg manufactured AUV has contributed key data to ITGC, including the first data from under Thwaites ice shelf and high-resolution maps that show where Thwaites Glacier was grounded in the past. Ran disappeared the first weekend of February during an expedition to Thwaites Glacier with the South Korean icebreaker RV/IB Araon. On the last planned mission of the cruise, it failed to re-surface at the meeting point and searches with acoustic instrumentation, helicopter, and drones were fruitless.
“We have had to give up. Ran is very likely still deep under Dotson Ice Shelf, the target for the last mission”, said Professor Anna Wåhlin, who was project leader on board the Araon and a key collaborator on ITGC at the University of Gothenburg in Sweden.
"There are not many uncharted areas left on Earth. To see Ran disappear into the dark, unknown depths below the ice, executing her tasks for over 24 hours without communication, is of course daunting. Experience from over 40 missions below ice gave us confidence, but in the end, the challenging environment beat us."
Ran’s modern technology and sensors measured and documented the surroundings in the water, including a unique capacity to get high resolution maps of the ice base. It carried out long missions under ice, and was used successfully in Antarctica, Greenland, New Zealand and many other locations.
During dives under the 200–500 m thick ice, Ran did not have continuous contact with the research vessel. Routes
are programmed in advance and thanks to an advanced navigation system, Ran can find its way back to open water. Ice shelf cavities are often completely unknown, and missions are built up in several stages, starting near the bottom and outside the ice while gathering information needed to go survey the ice underside.
Anna Wahlin continued: “The valuable data we received from Ran and other underwater vehicles are very rare, and part of the reason is the risk involved in getting them. Our aim is to replace Ran. We plan to explore ways to obtain funding to bridge the gap between the amount insurers will pay as the residual value of Ran and the cost of a replacement AUV at today’s prices.
“Although we got valuable data back, we did not get all we had hoped for. These scientific advances were made possible thanks to the unique submersible that Ran was. This research is needed to understand the future of Antarctica's ice sheet, and we hope to be able to replace Ran and continue this important work.”
We are fearless in imaging a greener energy future and committed to making it a reality.