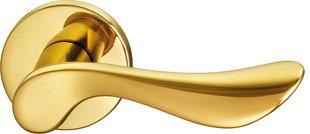
7 minute read
Integration of Human Aspect in Design FSB-Berthold Dieker
Integration of Human Aspect in Design
by Berthold Dieker - Franz Schneider Brakel (FSB)
Advertisement
The abbreviation FSB is synonymous throughout the world for aesthetically and functionally high-quality door and window handles - and much more.
Foundation – History and Mission of FSB FSB originated in Iserlohn, where Franz Schneider founded the company in 1881. In 1909, the company's headquarters were relocated to the East Westphalian town of Brakel. FS proudly added the B for Brakel to his signet and the FSB brand was born.
The rise to an architectural brand begins in the 1950s. After the closure of the Bauhaus and the turmoil of the war, design and architecture were experiencing a sustained revival. Ray and Charles Eames inspired with their functional furniture designs, Arne Jacobsen designed classics such as the stackable “Series 7” chair. Dieter Rams design works at Braun are today the blueprint for products from the company with the apple logo. The decade from 1953 to 1963 was a defining moment for FSB: Johannes Potente created his trailblazing and still valid hand-molded design. Posthumously, his anonymous industrial design also received its due appreciation: it was included, among others, in the permanent design collection of the Museum of Modern Art in New York.
In the 1980s, under the intellectual leadership of the designer Otl Aicher (1922 – 91), the very own activities were questioned substantially. Otl Aicher moved as a young man in the immediate vicinity of the “Weisse Rose”, a resistance movement to the siblings Scholl against the Nazi regime in Germany. After World War II, in 1953, together with his wife Inge Aicher-Scholl, he founded the College of Design in Ulm, which in the years of its existence (1953 - 1969) was to decisively influence German and international design up to the present day. Otl Aicher became famous with his work for companies such as ERCO Lichttechnik and Lufthansa, as well as for the visual appearance of the 1972 Olympic Games in Munich.
The result of the collaboration with Otl Aicher was a fundamentally new design culture at FSB that was essentially based on the cultural history of grasping in general and the history of handles in particular.
Figure 1. Iconic FSB 1020 design by Johannes Potente
This analytical examination produced, among other things, the “Four Point Guide to Good Grip”, which from then on should serve as a guideline for the assessment of good design: thumbrest, forefinger furrow, support for the palm and gripping bulk. The process of questioning was accompanied by a 16-volume book edition, which today is available to the standard repertoire of many scientific libraries - and now also in the library of the TU Delft!
As an inspiration for the FSB logo, Otl Aicher used a door handle designed by the philosopher Ludwig Wittgenstein for his sister’s house in Vienna. “Only when used the rod becomes a lever”, Wittgenstein described his simple and elemental design. For Aicher, this grip was a kind of ideal grip, not so much as an optimal hand shape, but rather as the sum of all the handles, the absolute quintessence.
In 1986, FSB invited luminaries such as Mario Botta, Peter Eisenman, Hans Hollein, Alessandro Mendini, Shoji Hayashi, Arata Isozaki and Dieter Rams to a design workshop in Brakel. What was long considered to be a low-interest product suddenly became one of the first “author design” projects and thus a serious design task.

Figure 2-3. “Four Point Guide to Good Grip” and “FSB hand” by Otl Aicher
Concept – Integration of the Human Aspect in the Design Process In the aftermath, many architects from all over the world knocked on FSB, not only to learn more about the good grip, but to lend a hand and to design their own grip program. Not all designs could be realized, but the portfolio of FSB today includes designs by internationally renowned architects and designers such as Jasper Morrison, Hans Kollhoff, Christoph Ingenhoven, David Chipperfield, John Pawson, Ortner & Ortner Baukunst, Santiago Calatrava, Dominique Perrault, Graft, Studio Werner Aisslinger and many more.
Usually, the actual design process is preceded by a large number of technical clarification talks. First of all, basic requirements are explained that will make the new design compatible with the many standard FSB products, such as substructures of roses and plates for the window and door handles. It is also important to meet the highly complex requirements of legal and normative regulations for door and window handles, especially in the core market of FSB, namely Germany.
The cost-effectiveness of a design is also analyzed very carefully in advance to keep the costs for the necessary production tools as low as possible. Important here is the basic shape, (L or U form) and the symmetry or asymmetry of the handle. To avoid threading a jacket sleeve into the door handle, L-shaped handles are not permitted for emergency exit doors in Germany and closed U-shapes are required. In order to avoid additional costly production tools for L and U shaped grips, it is therefore advisable to design the initial design as a U form. Symmetrical shapes also require a saving in production tools. Taking these aspects into consideration, very efficient designs can be realized with two production tools, while inefficient designs require up to eight tools.
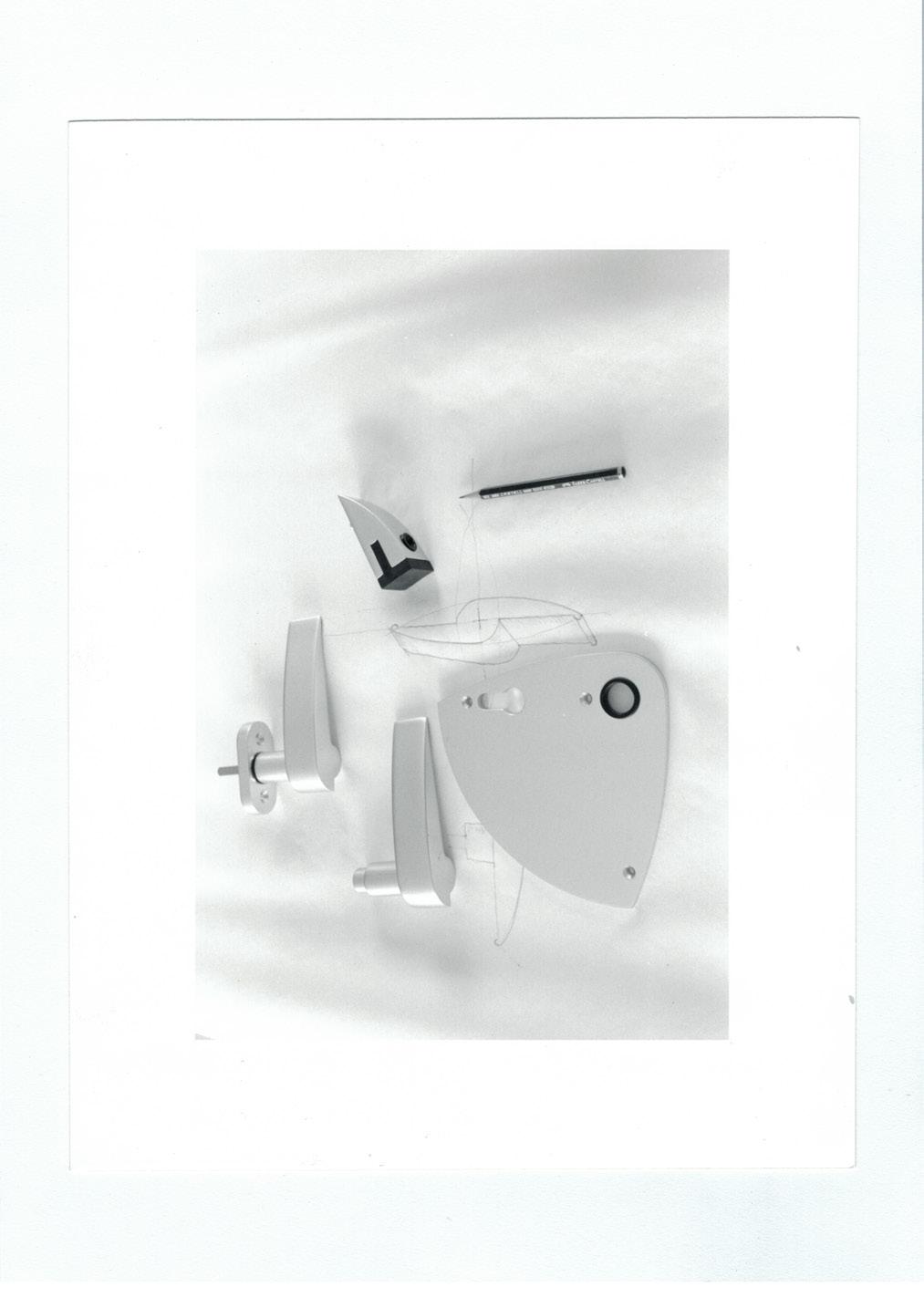
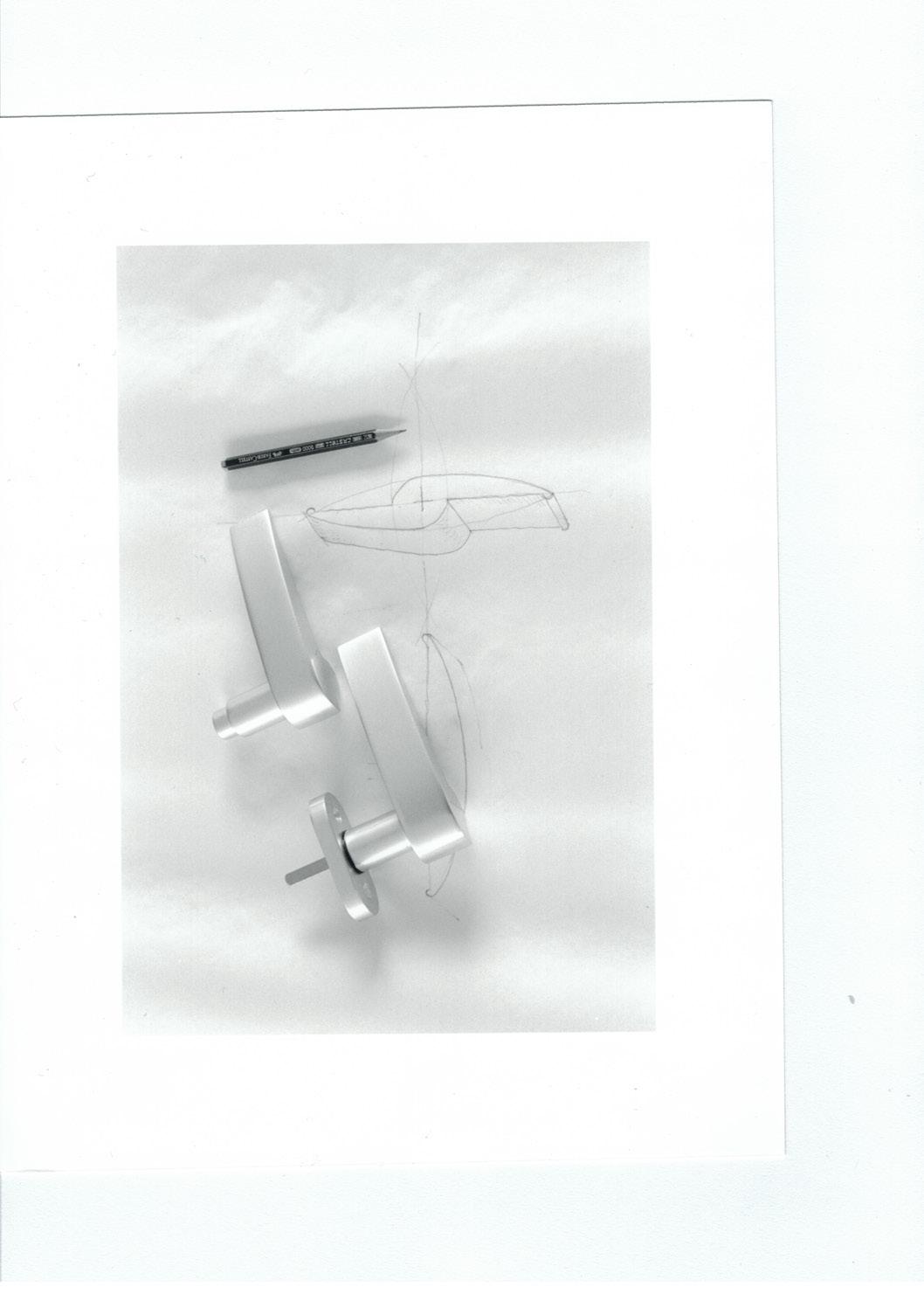

Figure 4-5-6. Joseph Paul Kleihues’ sketches of the bespoke handle design for the Kant Triangle High-rise block
When all these questions have been clarified, the designer can start his work. In further discussions with the employees from the technical department at FSB, the design is further substantiated on the basis of drawings, 3d plastic models and prototypes. Once the final form has been found for the new handle, internal investigations and test series as well as the construction of the tools will follow at FSB.
This process from the first interview to the finished latch takes about 6 - 12 months. In some cases, the handles are made only for the projects of the design architect and are not offered as catalog goods. With a marketable design and with the consent of the architect, the inclusion of the grip program in the catalog and thus a series production can start. Depending on the design of the handle and the intended use, four different base materials are available - aluminum, stainless steel, bronze and brass. Since the production of an aluminum handle is comparatively simple in terms of technology, it is usually started with this material and, if required, additional materials are added.
Application As a good example of the design process described above, Joseph Paul Kleihues’ project for the Kant Triangle Highrise Block can serve. The eleven-storey commercial block sited next to an urban railway line in Berlin stands on a triangular plot on Kantstrasse that also gave the building its name. The tower building, which was designed by architect Josef Paul Kleihues and completed in 1995, is notable for a large moving sail on its roof. It demarcates and structures an urban space abutting a Wilhelminian block and acquires the character of a campanile both on account of its classical configuration of plinth, shaft and crown and through the use of larger-than-life pictorial elements. Whereas the architect uses silver bolt-heads to decoratively
enhance the fixings for the stone slabs in the five-storey plinth area, he piles the building elements above up like containers, structures the stairwells with the aid of portholes and “lashes” everything down with steel bands. The weathervane on top, lovingly referred to by Berliners as the “Shark’s Fin”, points into the distance whilst also greeting passing rail passengers.
Elegant door levers embellish the doors to the commercial block like small sculptures. It immediately becomes evident that Kleihues designed them in 1992 specifically for the Kant Triangle. Their geometrical layout of circles and segments is echoed in enlarged form by the actual building. At the same time, the sequence of curves that go to make up the handle and backplate are a mirrorimage of the high-profile weathervane sail on the roof of the tower block, which in turn embodies the bulbous triangle defining the building’s ground plan. As well as delivering variations on the overall architectural form, however, the stylish door levers, backplates and locking bolt also, when operated, highlight the turning motion of the handle. The product collection also embraced a door knob, window handle, bathroom rose and door stop. This program was available in aluminium and went in serial production for some years. It was also used for several other projects, mainly designed by Joseph Paul Kleihues.
Figure 7. The Kant Triangle High-rise block designed by J. P. Kleihues
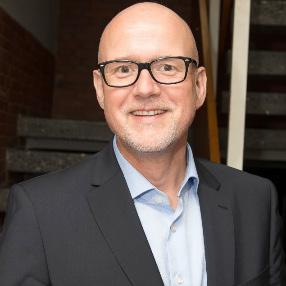
Dipl.-Ing. Berthold Dieker graduated in 1996 in Architecture at Dortmund University of Applied Sciences. Between 1996 and 2007 he worked as project leading architect in different architecture offices in Germany. After that he started working as architectural consultant for FSB. From 2017 he is Architectural Consultant International at FSB.
Source Disclosures: Bettina Rudhoff, Graspable Structures Getting a Handle on Architecture, 2 nd Edition, Brakel 2018