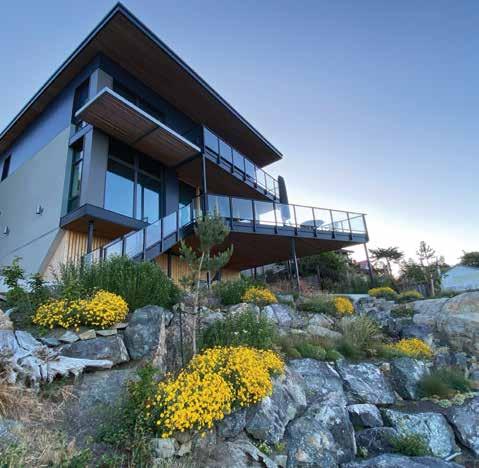
4 minute read
Site-sensitive project advocates for market transformation
from BC Focus summer 2023
by SAB Magazine
By Allison Holden-Pope
Pontoon Cove Eco House is a single-family dwelling that projects out from a sloped oceanfront property and culminates in a triangular deck which reaches out above the rocky point below. This sustainable home on Vancouver Island, near Saxe Point in Esquimalt, exceeds Step Code 5 with a heating demand below the Passive House standard, and sufficient solar panels on the roof to hit net zero operating demand.
Advertisement
We worked with a Certified Passive House Designer to design the house in accordance with the Passive House rating system, and the design and construction team are well versed in Passive House detailing and thermal bridge free construction. Our holistic approach to sustainability balances beauty and pragmatic functionality in a minimalist design inspired by the site and West Coast Modernism.
We maintained and encouraged the natural ecosystem on the property by ‘rewilding’, that is, removing invasive species and providing dark and natural habitats for the local flora and fauna. The elevated design eliminated the need for blasting the rocky site during construction.
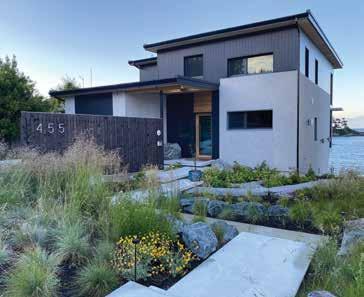
A rain garden of native plantings collects and naturally filters water and is supplemented by a 400-gallon storage tank with over capacity diverted to the on-site drainage swale, along with all other water from the site’s hard surfaces, allowing water to seep into the aquifer. The permeable driveway and raised paths minimize impact on the natural site. Additionally, an experimental moss roof will reduce the heat island effect, create habitat, and reduce run-off.
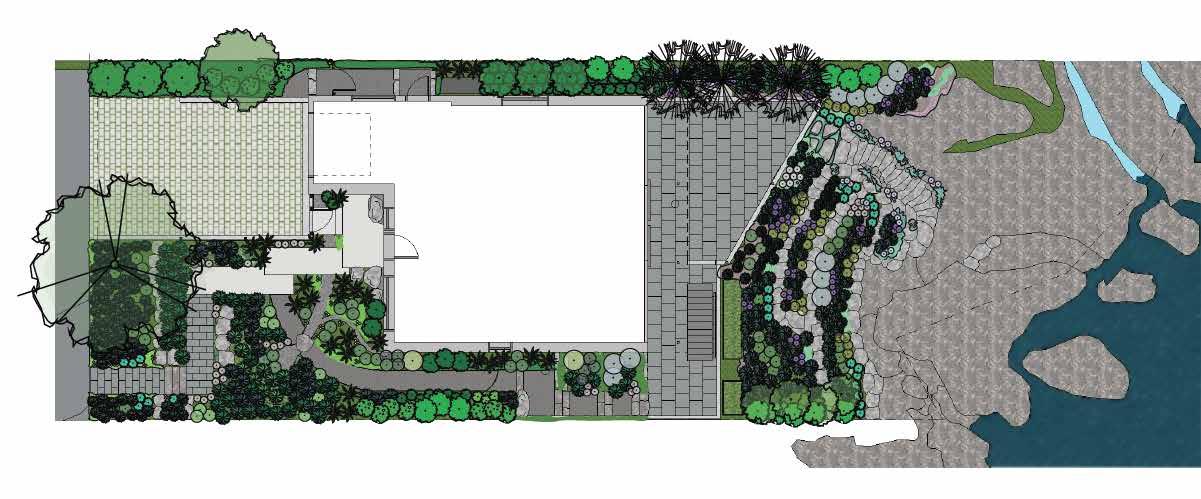
Floor Plans
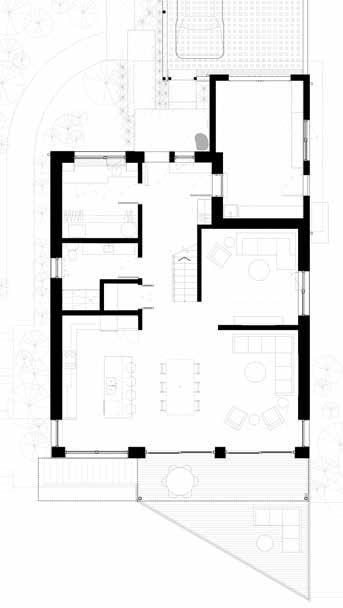

1. Garage
2. Mudroom / mechanical
3. Bathroom
4. Pantry / future lift
5. Media room / library + flex bathroom
6. Kitchen
7. Dining room
8. Living room
9. Outdoor living / open deck
10. Office
11. Native moss green roof
12. Bedroom
This project’s passive cooling and ventilation strategies, using the stack effect and carefully placed operable windows in combination with rooflines, deck projections, and solar shading devices, resulted in only two overheating days per year according to the Passive House Planning Package (PHPP). The house uses Passive House certified fiberglass windows, with floor-to-ceiling windows along the south-facing ocean-front side of the house.
Project Credits
Architect ONE SEED Architecture + Interiors Inc
Construction Interactive Construction Inc
Landscape Design Greenspace Designs
Structural Engineer Blackwell
Geotechnical Engineer Ryzuk Geotechnical
Energy Consultant Adapt Energy Advising
Photos Interactive Construction Inc and ONE
SEED Architecture + Interiors Inc
The kitchen, dining, and living rooms, all within 7m of an operable window, have large views to the ocean and Olympic Mountains beyond. Overhangs and shading devices are designed to optimize daylighting and solar heat gain in the winter months, while providing shade in the warmer months.
The double air-barrier approach to all assemblies ensures fresh air is flowing through the house exclusively via a HRV with 84% efficiency. This approach resulted in a blower door test of 0.35ACH,
PROJECT PERFORMANCE
Site Area 687m²
Gross Floor Area 310.4 m² (measured to exterior cladding)
Treated Floor Area 219.7 m² (as per PHPP)
Energy Intensity 37.4 kWh/m²/year (PER data in PHPP)
Heating Demand 14.2 kWh/m²a (PHPP)
Base Building 13.5 kWh/m²a (heating, cooling, ventilation)
Process Energy 23.9 kWh/m²a (DWH, lighting, appliances, expected plug loads)
Reduction in Energy Intensity App. 80%-90% more efficient
Recycled Materials Content Project used products with high recycled content, such as blown-in cellulose, metal cladding, and salvaged lumber
Water Consumption: Rainwater catchment system and lowflow fixtures reduce consumption by 20%.
In addition to the passive solar heating captured through the south-facing high-performance windows, and temperature regulation facilitated with high thermal mass concrete in the first floor and passive cooling, this house utilizes a highefficiency mini-split heat pump for heating and cooling.
The home exceeds Step Code 5, with an energy intensity of 13.5kWh/m2a – below the Passive House standard. The 30module PV array on the roof generates 14,841 kWh/annum. With the annual energy intensity at 8,216.8 kWh/annum, the array generates enough power for net zero operating, providing almost twice the home’s energy demands.
Interior
The gas connection was capped at the street to reduce reliance on fossil fuel in the future. Appliances are Energy Star rated electric, and an emergency sub-panel was provided to allow the house to operate critical loads on the electricity from a car battery or solar panels, in the event of a grid outage.
The home boasts many high-performance assemblies with lifecycle considerations at the forefront of all material selections. The floors, walls, and roofs use engineered lumber and recycled cellulose insulation. Living spaces are all above grade with a wood framed floor over a concrete wall crawl space made of Carbon Cure Eco Mix concrete. This technology introduces recycled CO2 into the concrete, making it a permanent carbon sink.
Exterior
Siding strapping rainscreen
Weather resistive barrier (W.R.B. + A.B.)
Plywood sheathing, taped @ all joints (A.B. + V.B.)
TJI joist c/w 9-1/2” cellulose insulation in cavity, R36 (R3.78”/in. @ 9.5”)
2x6 wood stud wall (structural load bearing) C/W 51/2” batt insulation cont. in stud wall cavity, R24 (R4.4/in. @ 5.5 in.)
Thermal bridge free at floor and structural elements
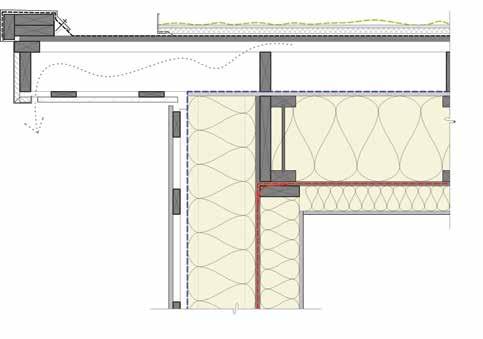
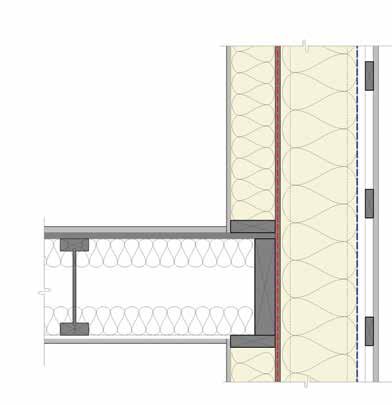
Wall to floor detail
Moss roof Torch-on roofing membrane
Venting
Wood soffit
Siding strapping rainscreen
Weather resistive barrier (W.R.B. + A.B.)
2x6 wood stud wall (structural load bearing) C/W 51/2” batt insulation cont. in stud wall cavity, R24 (R4.4/in. @ 5.5 in.)
Wall to roof detail
Tape at all joints
Weather resistive barrier (W.R.B. + A.B.)
TJI joist c/w 11-7/8” cellulose insulation in cavity, R36 (R3.78”/in. @ 9.5”)
Plywood sheathing, taped @ all joints (A.B. + V.B.)
2 x 4 purlins (service cavity) c/w 3-1/2” batt insulation R15.4 (R4.4 @ 3.5 in.)
Environmentally sensitive selections include highrecycled content, durable, and low-maintenance exterior materials and healthy no-VOC interior materials. About 90% of all dimensional lumber offcuts were repurposed at other projects. The interior stairs were constructed of salvaged lumber and a 100% recyclable steel stringer, while the two trees removed from site were milled for use as interior finishes. Moreover, the front door is a custom wood product as are the large (approximately 10 feet square) wood tilt and slide doors.

The home was designed for maximum flexibility and functionality, and future-proofed for ageing-in place without the need for significant renovations. A shaft currently used as storage on the main and upper level can be adapted for a future lift; and the main floor media room can be converted to a bedroom with a washroom and walk-in zero-threshold shower nearby.
Pontoon Cove Eco House raises the bar for local green building practices and contributes to our push for market transformation and encouragement of product suppliers and trades to provide environmentally responsible, low-embodied carbon, and high-performance options.
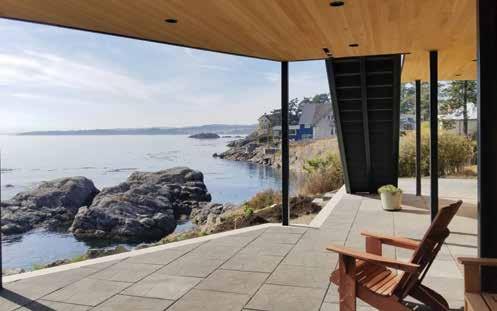
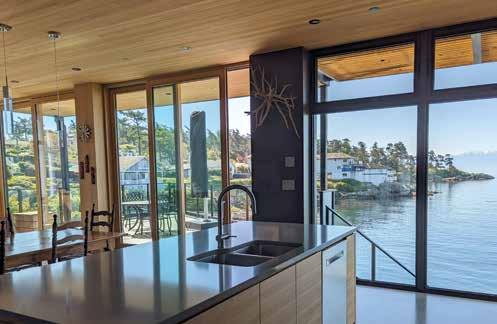
In fact, we used this project as an opportunity to lobby the local municipal council for an improved sustainability agenda and accommodations for green building practices, such as relaxed height restrictions to allow for deeper assemblies. The council noted that Pontoon Cove Eco-House represents ‘forward thinking’ and reflects the sustainability goals that should be encouraged in Esquimalt.
Allison Holden-Pope, Architect AIBC, Passive House Canada
Trained Design Professional, LEED AP BD+C is principal of ONE SEED Architecture + Interiors Inc.