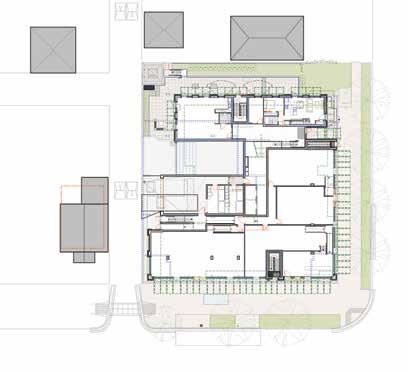
5 minute read
The Peak New rental apartment promises big cuts in operating costs
from BC Focus summer 2023
by SAB Magazine
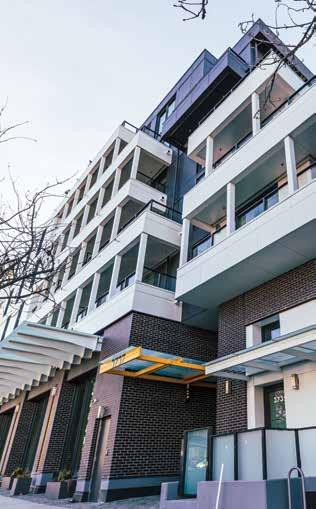
By Luke Han (Zhen)
Advertisement
“The Peak” is a six-storey mixed-use building in Vancouver with 52 rental suites and four commercial retail units on the ground floor. The goal of the project was to provide much needed rental housing options in the area and support a more vibrant commercial core.
With a growing population, limited increases in income, and a limited supply of new, purpose-built rental housing in recent decades, the need for rental housing has grown significantly. To keep the project affordable, profitable and liveable throughout its life, The Peak was designed and built to meet the voluntary energy requirements of the Passive House Institute. The result is a highly durable building with lower operating energy consumption, lower building maintenance, and improved occupant comfort.
The site is part of a neighbourhood centre identified under the City’s Affordable Housing Choices Interim Rezoning Policy. The original zone is C1 (three-storey building). Since this project applied for rezoning, one of the conditions is that it must meet the Green Buildings Policy for Rezonings. This sets out requirements for all applicable developments applying for rezoning to help transition the industry toward more sustainable building practices. In our case, we decided on the passive house energy compliance path.
1. “The Peak”, a six-storey mixed-use building in Vancouver has 52 rental suites and four ground-floor commercial retail units, provides much needed rental housing and commercial space for the neighbourhood.
2. The envelope consists of a 2x8 stud wall and an interior 2x3 service stud wall with the cavity filled with fiberglass batt insulation and an intelligent vapour variable membrane sandwiched between the double stud walls. Westform metal WF HF 12 soffit panels provide full ventilation of the soffits.
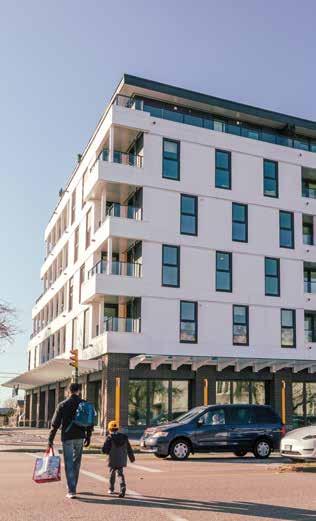


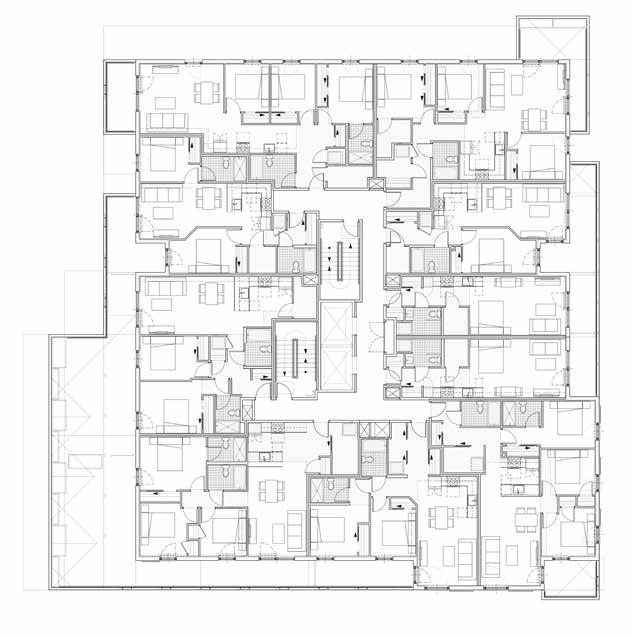
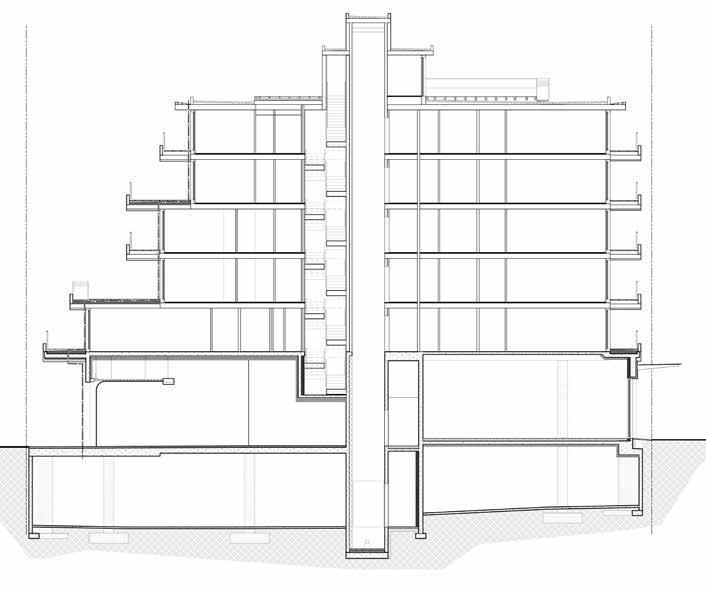
Project Credits
Architect Cornerstone Architecture
Structural Engineer London Mah & Associates
Mechanical Engineer Dialog
Electrical Engineer Nemetz (S/A) & Associates Ltd
Civil Engineer CitiWest Consulting Ltd.
Commissioning Agent MC Air Balancing and True Mechanical
Building Envelope Commissioning Aqua-Coast Engineering
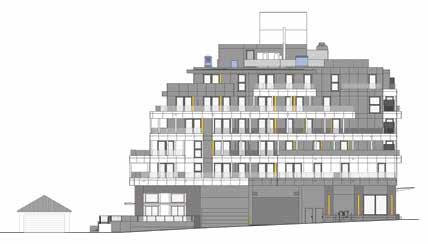
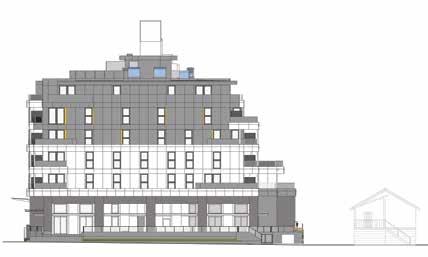
General Contractor/Construction Manager Edge
Construction
Photos Luke Han. Photo 4 Innotech Windows + Doors
3. Since this project applied for rezoning it was subject to the Green Buildings Policy for Rezonings which is helping the industry transition to more sustainable building practices. In this case, The Peak followed the passive house energy compliance path.
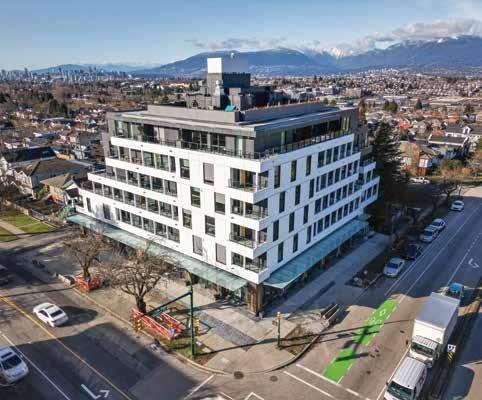
The wood framing and joists were prefabricated offsite and assembled onsite. The exterior wall assembly consists of 2x8 structural stud wall with an interior 2x3 service stud wall. The cavity is filled with fiberglass batt insulation with an intelligent vapour variable membrane sandwiched between the double stud walls. This membrane acts as the air barrier and as a vapour retarder in winter as it protects against condensation. In the summer, it maximizes vapour openness to facilitate rapid drying to the interior.
The windows and doors, manufactured by Innotech Windows + Doors in Langley, BC, are Passive House Institute certified. The windows and doors provide outstanding thermal insulation and superior air, water, and sound resistance due to their hybrid frame construction, 46mm IGU with triple glazing, and multipoint locking hardware. The tilt and turn function of the windows also allows for larger operable windows that provide passive natural ventilation for the residents.
Wood blocking, rabbet sides and bottom, install cladding inside rabbet locations; drill and fill pilot hole with polyurethane sealant; install stainless steel fasteners
Insect screen at top and bottom of wall-cladding (typical)
Pre-finished metal flashing protection strip at base of wall
Cant strip to divert water to scupper location
Pedestals as req’d
Air-barrier
Self-adhered membrane extend vertically over sheathing
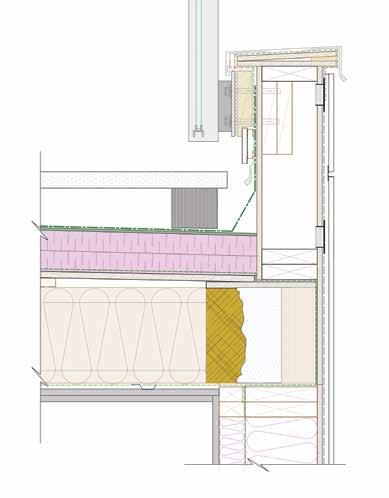
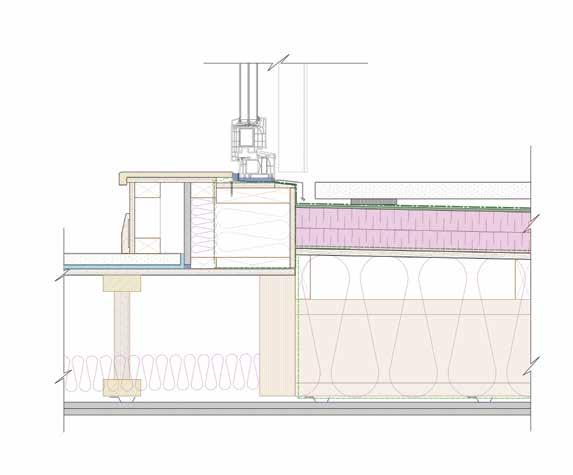
Pre-strip continuous smart air/vapour barrier prior to framing
3’6” MIN. (NTS) high Glazed guardrail sidemounted
26 Ga. Cap flashing standing seams or ‘S’ Locks installed with wind clips
Air barrier turned down over top of plate, tape-sealed overlap
Spray foam rim beam
Mineral insulation
Continuous smart air/vapour barrier taped to vertical air/vapour barrier
Continuous reveal
2” Dia.vent plugs16 c/c at base and top of cavity
Selected windows on the east, south, and west façades have automated exterior blinds installed to eliminate unwanted solar heat gain in the summer. These blinds are programmed to deploy automatically based on the illuminance (lux) levels. They block up to 92% of heat, reducing the building’s energy costs. Residents can override the deploying of the blinds with a control in their suite, and the blinds will also retract when excessive wind speeds are detected.
The building is designed with six high efficiency heat recovery ventilators (HRV) on the roof to supply continuous fresh air to all the suites. The HRV extracts exhaust air from the bathroom and kitchen areas through a heat recovery core, where 85% of the heat energy contained therein is used to preheat air from the exterior which is supplied to bedrooms and living rooms. A single roof-mounted heat pump further tempers the air with coils in the supply air stream – providing heating in the winter and cooling in the summer.
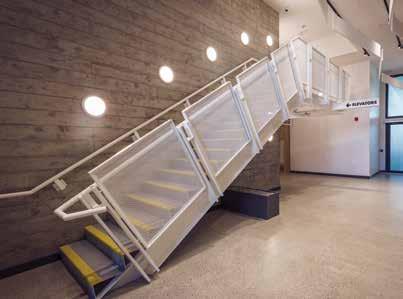
Hot water in this building is generated by four CO2 heat pumps in the parkade. Heat pumps move heat rather than create heat. This allows them to be three to four times as efficient as a conventional electric resistance hot water tank. This technology was chosen because it is very efficient for heating water and CO2 is a climate friendly refrigerant. Refrigerants can leak from heat pumps. Conventional refrigerants have a global warming potential of 2000 – 4000. The CO2 gas in this system has a global warming potential of 1.
Heat pump dryers are used in all suites. They are much gentler on clothing since they dry at lower temperatures than a conventional vented dryer. Instead of venting that hot, wet air outside, the air is looped back into the second coil where it’s cooled down causing moisture to condense out of the air and down the drain.
Without having to make up the exhausted hot air with cold outdoor air, no heating energy is wasted. Storm water is captured on site from all areas, including rooftops, paved areas, and landscape. To limit thermal bridging, rainwater leaders are located on the exterior of the building so the cold water is not running inside the thermal envelope. A stormwater detention chamber is provided to limit the post-development stormwater runoff rate from the site.
Thermal bridging details were designed ahead of time with computer models and physical mockups. Sequencing of construction was planned to make sure there is a continuity of the air barrier and thermal insulation. Every opening and penetration through the building envelope is sealed with high performance tape or sealant.
The building’s space heating demand is modelled to be 11.7 kWh(m2a). In the final air tightness test, the result achieved was 0.48 air changes per hour at 50 pascals (ACH50) – surpassing the required 0.60 ACH50 to meet Passive House certification. The result is a highly energy efficient building with very low operating costs and significantly more comfortable residents.
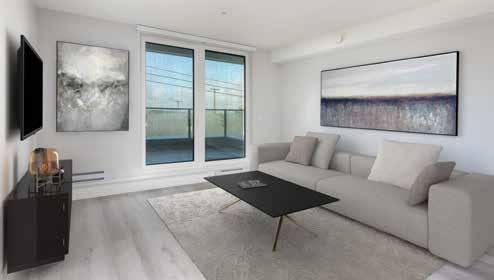
Luke Han (Zhen) Architect AIBC | MArch | BEDS is with Cornerstone Architecture.
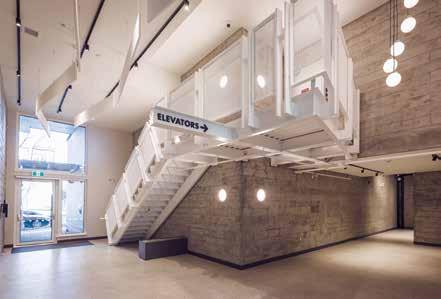
A Sound Investment For Your Project
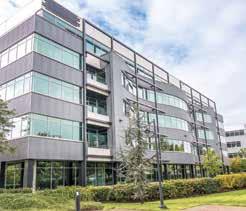
Steel cladding is a durable, attractive and environmentally friendly choice for your project. It comes in a wide variety of colours and styles to suit any style of project – such as ‘The Peak’ Passive House apartment building (top left), and the Pontoon Cove Eco House (top right).
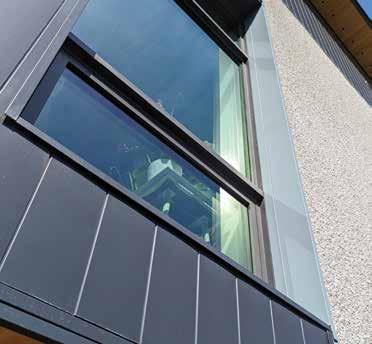
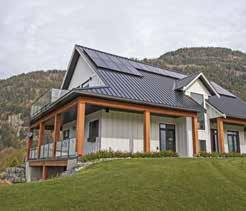
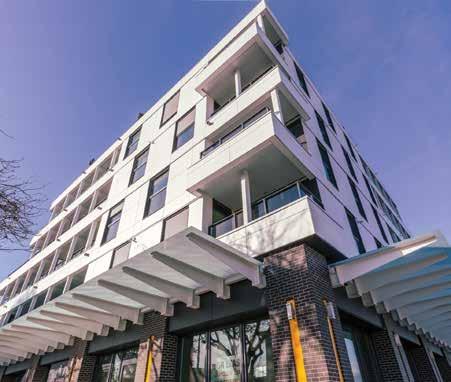