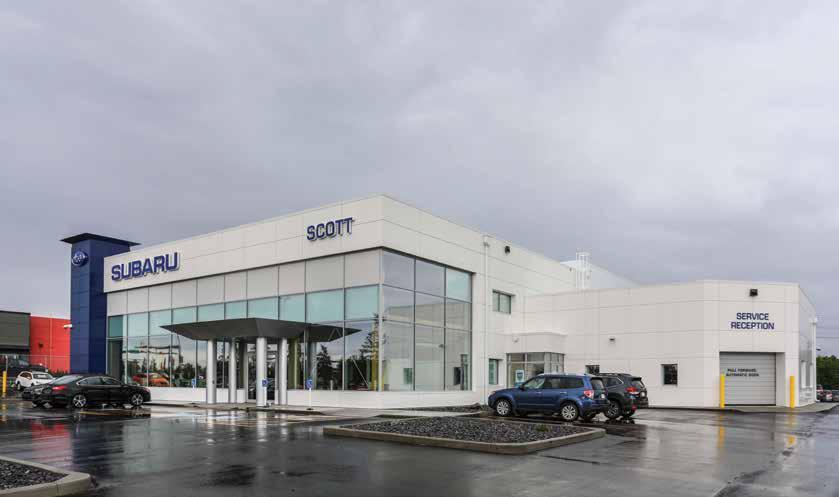
9 minute read
Shifting Gears
from SABMag 67
by SAB Magazine
A Passive House Car Dealership in the Making
1. The typical car dealership is ideal for Passive House with its inherently compact form and favourable volume to heat loss area.
Advertisement
By Andrew Peel, Peel Passive House Consulting
The world’s first certified Passive House car dealership opened for business in the fall of 2019. Designed by Cover Architectural Collaborative, Sublime Design and Peel Passive House Consulting and constructed by Black Creek Developments, the 2,420 m2 (26,020 ft2) facility in Red Deer, Alberta houses the new Scott Subaru dealership. It coincides with the 50th anniversary of The Scottsville Auto Group who developed the project.
“Building smarter and showing that retail facilities can still be structured in a way that is functional, and also provide a nicer work environment for employees and customers, has long term benefits. We hope this will inspire others to build similar type structures.” - Garrett Scott, Owner,
Scottsville Auto Group
Motivation
While not an avid environmentalist, owner/developer Garrett Scott sought a low impact building that would support his growing business and recognized the myriad benefits of constructing to the Passive House Standard.
This is not the first environmental building initiative Subaru has undertaken. Its Indiana automotive assembly plant was the first zero-landfill factory in the US and inspired the decision to pursue Passive House certification on this project.
Setting the Standard
Most, if not all, large car manufacturers have strict corporate standards regarding aesthetics, layout, and service requirements for their facilities and Subaru is no exception. In addition to these corporate standards, the client had some of its own. Chief among these was that any decisions made in pursuit of Passive House certification must not compromise customer or vehicle service in any way. An additional major factor impacting the design was the local winter design temperature of -20oF (-29oC). Navigating these requirements proved challenging and demanded the best of the whole design and construction teams.
Base Design
The building is divided into three main zones: a showroom, a repair shop, and a car drop-off zone. The showroom includes a car display area, customer reception and lounge and sales offices on the first floor, and back offices, meeting rooms, and staff kitchen on the second floor. The repair shop comprises a ground floor with 6 service bays and parts storage, and a second floor with mezzanine, storage, and cat walk. The dropoff zone is a single storey area used to collect customers’ cars for repair and show off new cars housed in the parking lot to customers at night and during periods of inclement weather.

Insulated Footing. A tent is erected around the foundation walls and heated to allow the project to continue construction during winter. © Cover Architecture.
PROJECT CREDITS
ARCHITECTURE Cover Architectural Collaborative and Sublime Design MECHANICAL & ELECTRICAL 908 Engineering PASSIVE HOUSE CONSULTANT AND ENERGY MODELLING Peel Passive House Consulting CONSTRUCTION MANAGER Black Creek Developments
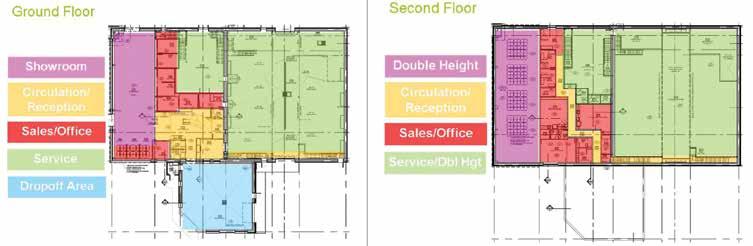

South elevation showing insulated spandrel panel (red) and standard curtain wall glazing. © Cover Architecture.
Envelope
- Walls: 305-mm (12-in.) LVL studs filled with cellulose; 76-mm (3-in.) exterior insulation and 2x6 interior service cavity. Usi = 0.084 W/ m2K (R-68) - Floor: 305 mm (12-in.) below-slab floor insulation that fully wraps the footings. Usi = 0.109 W/m2K (R-52) - Roofs: 1,340mm (52-in) cellulose-filled, open-web wood truss roofs. Usi = 0.040 W/m2K (R-145).
One key envelope challenge was to mitigate the impact of the 65 per cent glazing on the west facing storefront dictated by corporate design requirements. Red Deer lies between two of the country’s sunniest cities, Calgary and Edmonton, receiving up to 50 per cent more west radiation than is typical in Germany (the conditions for which the Passive House Standard was originally developed).
Numerous solar control measures were explored, including overhangs, deciduous tree planting, external blinds, and electrochromic glazing. Ultimately, the only viable option was installing insulated spandrel panels in the top row of glazing coupled with automated operable internal blinds with manual override. Unfortunately, these measures were insufficient to fully mitigate the high cooling load.
Another envelope challenge was the client’s original requirement for seven overhead doors. The Passive House consultants devised an alternative design requiring only two doors. However, the client felt this disrupted service too much and eventually agreed to a compromise of four doors. The initial concern with these doors was heat loss due to operation. Investigations revealed minimal air exchange, as the doors are shut quickly after a car passes through them.
Car Exhaust Hose. The idea to vent each of the six service bays with a separate exhaust fan, thus cutting the exhaust rate by 83%, had to be modified to a two-fan system which still met the Passive House space heating demand target.

The greater concern turned out to be standby air leakage. Unfortunately, conventional North American doors are not rated for airtightness, so could not be relied upon. Accordingly, the team looked to Europe both for the doors and for an independent assessment of their airtightness. For this, the project team referenced European Standard EN 13241-1, which defines airtightness classes.
The author’s team located a product with an equivalent leakage of 0.04 ACH@50Pa, which increased the whole building leakage by an acceptable 10 per cent. Additionally, careful detailing ensured a durable seal between the door frame and the wall.
Ventilation
Ventilation is provided by three ERVs, each serving one zone of the building. The ERVs serving the repair shop and dropoff zone are sized to meet peak loads. The mechanical engineer originally specified an air change rate of 3.0ACH to deal with any pollutants that may build up during servicing. After detailed review, it was agreed to reduce this specification to 2.0ACH to limit energy demand.
Car exhaust contains harmful pollutants that must be directly exhausted to the outside of the building. To meet code requirements, each of the six service bays must have 400 CFM of exhaust capacity. Normally, all bays are connected to the same exhaust fan, which results in all bays being exhausted simultaneously, even when only one bay is in use. For this project, it was proposed to vent each bay with a separate exhaust fan, cutting the exhaust rate by 83%. Unfortunately, a coordination issue led to only two fans being installed. While the full energy savings were not realised, the Passive House space heating demand target was still met.
To further reduce losses, the team explored supplying the makeup air directly to the car engines to avoid having to heat it. This setup was vetoed by the client, due to concerns over its impact on servicing. The team investigated options for heat recovery on the exhaust, including heat recovery ventilation (HRV), coaxial tubes, wrap-around coils, and heat pipes. However, none of the manufacturers would warranty their equipment for use in car exhaust systems, rendering these measures unfeasible.
A further consideration was to install a ground earth tube to pre-heat the make-up air. The high air volume of this option would require a large capacity tube at a substantial cost. The average winter ground temperature is approximately 4oC (39oF), limiting the energy that can be extracted, and still necessitating the installation of a make-up air heater. In the end, the additional heat loss of the exhaust had to be compensated through an improved building airtightness of 0.4 ACH@50Pa (0.039 cfm/ft2). With diligence, this target was achieved.

The customer reception area. Mitsubishi Electric Sales provided the split-type heat-pumps units, both indoor and out, and low profile fan coils.
Heating and Cooling
Heating and cooling are provided by a ducted variable refrigerant flow (VRF) heat pump system, with indoor units concealed within the suspended ceilings in the corridors. Electric resistance coils were installed in the supply air of each indoor unit to provide heat during peak heating conditions, when the heat pumps are expected to stop operating due to low temperatures. Despite the low nighttime summer temperatures and humidity levels in Red Deer, active cooling could not be avoided due to the solar and internal heat gains. The team tried diligently to reduce the size of indoor units, but the high solar gains in the showroom worked against this effort.
Service Hot Water
Two separate service hot water loads are present in the building. The first is for the washrooms and staff kitchen. This demand is relatively low and served by a single carbon dioxide (CO2) - based heat pump. The tank is located in the repair shop to mitigate concerns over freezing of the water pipe transferring heat from the outdoor unit to the storage tank. This provides additional free cooling during summer.
Breakdown of site energy demand by service. Services in blue use electricity, while services in red use natural gas. Office includes kitchenette energy demand.

The second load is the result of the client’s requirement to wash each and every car entering the repair shop. This daily load is appr oximately 2020 L/day @ 60 C (530 gal/day @140 F), which could only be met by a portable, on-demand, gas-fired water heater (the only equipment using natural gas in the building). An electric version was not feasible due to the required electric capacity and operating cost. Additionally, Alberta’s electricity grid is relatively carbon-intense, leading to high carbon emissions. As technology develops and the grid gradually decarbonizes, this unit can potentially be replaced by an electric version in the future.
The resultant primary energy renewable (PER) demand was 34 kWh/ m2/yr (11 kBTU/sf/yr), or 56 per cent of the total energy budget, for this service alone. To reduce this, the project team searched for a suitable drain water heat recovery device to recapture some of the waste water heat. No device designed for horizontal installation was found on the market, so a custom unit designed for vertical installation was specified. The mismatched orientation substantially reduced heat recovery efficiency, but the device still provides a noticeable reduction in the overall service water demand.
Building Energy Performance
The building energy modelling was completed using the Passive House Planning Package (PHPP), a monthly steady state modelling program. Capturing all the heat flows within the building proved more complicated than initially thought. The unique uses in the building required a detailed investigation of internal heat gains (IHGs). The project team compiled a list of equipment early in the project to support more accurate building energy modelling from the start. As no energy consumption data on car repair equipment could be found, the project team worked with the client to develop reasonable assumptions around usage and power ratings.
The predicted energy performance of the building is: • Space Heating Demand: 14 kWh/m2/yr • Space Cooling Demand: 2 kWh/m2/yr • Total Site Electricity: 45 kWh/m2/yr • Total Site Natural Gas: 23 kWh/m2/yr • Primary Energy Renewable: 69 kWh/m2/yr • Airtightness (measured): 0.40 ACH@50Pa (0.039 cfm/ft2)
The owner began operating the building in the Fall of 2019. Performance data from the first winter was not available at the time of writing.
Summary
Challenges that cold climates present to Passive House design are nothing new. But the combination of climate, client and project requirements and operational realities forced the design team to continually re-evaluate proposed solutions in order to optimize the design and ensure certifiability. A team committed to the project goals and willing to seriously explore alternative solutions is essential for success.