
11 minute read
News
from SABMag 67
by SAB Magazine
RAIC REPORT Main Street Design Challenge launched to foster innovation in Urban Design
By Tanner Morton, Communications Coordinator
Advertisement
A new Canada-wide design challenge launched on June 3, 2020 to generate responsible, sustainable, and resilient design solutions to be implemented during COVID-19 recovery, and post-pandemic, on affected main streets across the country.
The Main Street Design Challenge (MSDC), developed by the Canadian Urban Institute (CUI) and the Royal Architectural Institute of Canada (RAIC), invites all Canadian residents interested in place-making and design to develop solutions to help build the resiliency of main streets across the country.
The Challenge demonstrates how thoughtful and innovative design plays a key role in the revitalization of main streets, including kickstarting the economy, fostering vibrant, liveable, and healthy communities, increasing public safety, reducing social isolation, and restoring the public’s confidence to return to streets and public spaces.
An online portal opened for submissions on June 22, 2020—with deadlines for the different cycles of the competition. All submissions meeting the project guidelines will be published online on a rolling basis in a free, open-access Main Street Design Playbook on October 5, 2020—recognized across the globe as World Architecture Day.
The Main Street Design Challenge is an initiative of Bring Back Main Street a nationally coordinated research and action campaign by the CUI to ensure the people, businesses, and organizations that recognize the main streets of cities and towns across Canada as a vital heart of their community.
The Mitsubishi Electric heat pump system is also very quiet, and is a great solution for office, commercial, education and residential applications.
Thirty-six outdoor units and 148 indoor units were used in the 104,000 square foot building. On February 14, 2020, a tour was given to Terada-san, President and CEO, of Mitsubishi Electric Sales Canada Inc. along with Dermot McMorrow, VP and GM, Syed Abid, Commercial Sales Manager and Tova Davidson, Executive Director of Sustainable Waterloo. Adrian Conrad, Chief Operation Officer of the Cora Group hosted the tour. The Cora Group was awarded Mitsubishi Electric’s Sustainable Building of the Year Award. Congratulations to the Cora Group for their success in sustainable building development.
CPCI RELEASES NEW EPDS FOR WALL PANELS AND STRUCTURAL PRECAST CONCRETE
The Canadian Precast Prestressed Concrete Institute (CPCI) has released new environmental product declarations (EPD) for Architectural and Insulated Wall Panels and for Structural Precast Concrete Products. The new EPDs allow architects, engineers, building owners, and other specifiers to better understand the environmental impacts of precast and prestressed concrete products.
The industry-wide EPDs, jointly released by the Canadian Precast/Prestressed Concrete Institute (CPCI) and the Precast/Prestressed Concrete Institute (PCI), are issued within clearly defined product groups based on the precast concrete Product Category Rules (PCR).
The EPDs were independently prepared by Athena Sustainable Materials Institute in accordance with ISO 14025 and ISO 21930; the Product Category Rules for Preparing an Environmental Product Declaration for Precast Concrete (UN CPC 3755).
They were also independently verified by ASTM International (in accordance with ISO 14025) and by ndustrial Ecology Consultants (in accordance with ISO 14025 and the Product Category Rules). Get your copies
at https://www.cpci.ca/en/resources/technical_publications/ and scroll down to the Sustainability section.
2
evolv1 is the first office building in Canada to receive the Zero Carbon Building-Design Certification from the Canada Green Building Council. According to the CaGBC’s Zero Carbon Building Standard, the certification means the project modelled a zero-carbon balance for future operations, incorporated an efficient energy and ventilation system to meet a defined threshold for thermal energy intensity, and designed onsite renewable energy systems capable of providing a minimum of 5% of building energy consumption.
The building was designed to not just maximize energy efficiency, but to produce 108% of its energy needs. As part of this mandate, all components needed to be energy-efficient, including the HVAC system.
Mitsubishi Electric Heating and Cooling was selected to supply 100% of the heating and cooling to the office building. Specifically, Mitsubishi Electric’s City Multi Water-Source VRF Heat Recovery System was chosen because it not only regulates the flow of refrigerant to the fan coils, but it also changes the water flow rate to minimize the pumping energy.
1.Terada-san, President and CEO, of Mitsubishi Electric Sales Canada Inc. presents Mitsubishi Electric’s Sustainable Building of the Year Award to Adrian Conrad, Chief Operation Officer of the Cora Group. 2.The evolv1 building.
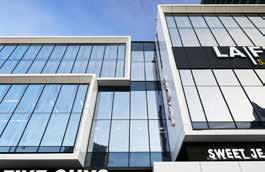

TM
ENERGY-EFFICIENT, DURABLE AND AFFORDABLE: A NEW TAKE ON FIRST NATIONS HOUSING
When architect Douglas Cardinal contacted Maisons Chicoine Homes (MCH), a builder located near Gatineau, QC, with a vision to create a new housing model for First Nations communities, the result was Cardinal House.
The two-storey, 1,100-square-foot, three-bedroom home uses prefabricated floors and exterior wall panels of cross-laminated timber (CLT) from Element 5 which were factory made, then trucked to the site and assembled in three days by MCH. The Cardinal House concept offers a healthy (mouldresistant), energy-efficient, long-lasting and affordable home to meet the housing needs of First Nations communities. Watch the brief video: https://youtu. be/27z6t3eKK7A.

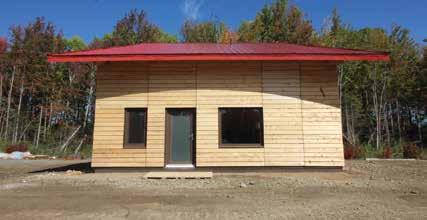


Green Innovation. Outstanding Quality.
ISOKORB® STRUCTURAL THERMAL BREAKS INSULATE BALCONIES IN HALIFAX HIGH-RISE
Maple Apartments is one of the largest mixed-use residential high-rises in downtown Halifax. Developer Southwest Properties aimed to create a “contemporary, iconic addition to the urban landscape” while minimizing the building’s energy use. Structural thermal breaks helped achieve these goals by limiting heat loss through the floor slabs by thermally isolating the building’s cold exterior balconies.
The inclusion of structural thermal breaks between the interior floor slabs and exterior balconies greatly reduces heat loss through the penetration, while increasing the temperature of interior floors by up to 19°C compared to non-thermally broken slabs during cold weather periods.
The design team specified the Isokorb® Type CM load-bearing structural thermal breaks by Schöck North America.
The thermal breaks consist of a graphiteenhanced polystyrene insulation module that runs the full length of the slab.
Stainless steel reinforcing bars are positioned at the top of the insulation module to accommodate tension forces imparted by the cantilevered slab.
Compression concrete modules placed at the bottom of the assembly transfer compressive forces from the cantilevered slab which, in conjunction with the tension bars, accommodate the moment at the connection.
Additional stainless steel reinforcing bars run diagonally through the insulation body to address shear loads at the connection. By minimizing the cross-sectional area of the structural elements that penetrate the insulation body, as well as using less thermally efficient materials (stainless steel transfers 70% less energy than mild carbon steel), structural thermal breaks can reduce heat transfer by up to 90% at the connection.
Nedlaw Living Walls
So much more than just a, “green wall.” A Nedlaw Living Wall Bio-Filter is a patented building subsystem that cleans indoor air, improves occupant health and wellness, and increases building performance.
www.nedlawlivingwalls.com

Fraser Wood Siding manufactures premium quality prefinished wood siding and Shingles. Made from Canadian softwood, sustainably harvested from 100% PEFC Certified forests and backed by an industry leading warranty.
fraserwoodsiding.com
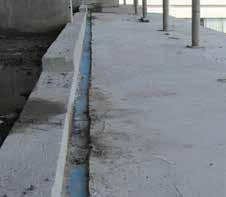
2
1. The Maple Apartments in Halifax. 2. The Isokorb® thermal break installed.
SEE A LOT MORE
PRODUCTS at SABMag’s 2020 Directory of Sustainable Products and Services for Sustainable, highperformance building organized by product category and by LEED category.
https://sabmagazine.com/product-directory/
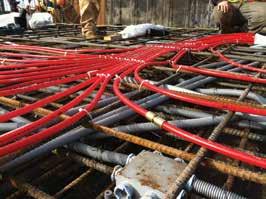
The First Wood and Aluminum Clad Wood, Certified Passive House Windows and Doors Manufactured in Canada.
Klimatrol Radiant Floor Heating
Klimatrol, 25 Years providing Radiant Floor Heating and Cooling system. We use only the highest quality PEX pipe and provide field support to ensure your system is correctly installed. www.klimatrol.com
CERTIFICATION/QUALITY ASSURANCE A VITAL PART OF THE NATIONAL BUILDING CODE IN ERA OF UNCERTAINTIES
The main threats to infrastructure assets are many but include first and foremost damage or destruction caused by extreme weather events. These threats have led to Infrastructure Canada’s Climate-Resilient Buildings and Core Public Infrastructure Initiative. Led by the National Research Council of Canada (NRC) this “ground-breaking work focuses on integrating climate resiliency into building and infrastructure design, guides, certification and codes.”
The federal government’s new LCA initiative (low-carbon assets through life cycle assessment) guidelines will enable public and private sector portfolio holders to incorporate the quantification of Life Cycle Carbon & Total Cost Of Ownership (TCO) of built assets (real property, public infrastructure) into their procurement processes. For more information: https://www.infrastructure.gc.ca/plan/crbcpi-irccipb-eng.html and https://nrc.canada.ca/ en/research-development/research-collaboration/programs/low-carbon-assets-throughlife-cycle-assessment-initiative This work will contribute to an infrastructure landscape that can keep Canadian communities safer from extreme weather and deliver the Best Bang for the Buck (lowest total cost of ownership). When it comes to purchasing certified buildings and above- and below-ground infrastructure products, the best value comes from the appropriate durability and resilience over the entire lifecycle. So how to achieve best value for an investment? We know that specifying products that meet the right building code standard is a minimum first step. Specifying products that meet a certification program built on superior quality assurance processes, above and beyond the minimum building code standards, will protect your investment, manage risk, and provide safety assurance to your end users, tax payers, and/or service community.
Why Precast Concrete Certification?
Certification helps ensure that the essential components of a quality assurance system are present and functioning properly, resulting in the highest probability of reducing risk, meeting specifications, and completing a successful project. Therefore, the primary purpose of a certification program is to help ensure that products are manufactured in accordance with specifications and community expectations. In other words, certification helps ensure “as designed becomes as built” and should be considered by every designer as a means of reducing risk and ensuring quality and safety.
The national and provincial building codes require conformance to the CSA standards for precast concrete materials and construction when it comes to structural, architectural and drainage precast concrete products. CPCQA is a nationally recognized and accepted certification program that provides an independent third-party certification of conformance to the CSA standards.
The CPCQA certification program requires precast concrete manufacturers to meet the requirements of the latest editions of CSA Standards for structural, architectural and drainage products and the PCI Quality Control Manuals MNL-116 and 117 (US equivalent), with the more stringent requirements being the governing criteria. Certified plants are audited annually with at least two unannounced audits. Strict compliance with published standards is necessary to maintain certification. Certification confirms a manufacturer’s capability to produce quality products and systems.
CPCQA Multi-Stakeholder Advisory Council
CPCQA’s Quality Assurance Council (QAC) of 23 members, comprising architects, engineers, provincial government officials, ACO’s and six precast concrete producers, embodies a high level of expertise and acts independently to design and vet the certification program.
Continuous Feedback and Addressing Client Concerns
CPCQA has two key client groups – the owners / agencies / specifiers who specify the program and the precast concrete producers who participate. Both of these groups have formal methods for providing feedback to the Quality Assurance Council on the program. Addressing this feedback is a formal part of the QAC agenda at each of their three annual meetings.
Owners or specifiers concerned about the quality of precast concrete from a CPCQA certified plant can fill in the Quality Concern Reporting Form on the CPCQA website and submit it confidentially to the Managing Director of CPCQA at QACAdministrator@precastcertification.ca. CPCQA is the only certification program in North America that has an official Quality Assurance Reporting Program and Quality Conflict Resolution Mechanism.
At present the Canadian Precast Concrete Quality Assurance (CPCQA) Certification Program certifies over 80% of the precast concrete production in Canada. The CPCQA program is the only program endorsed by the Canadian Precast/ Prestressed Concrete Institute (CPCI) and the Canadian Concrete Pipe and Precast Association (CCPPA).
Helpful Specification Guide
Available for free download at: https://www. precastcertification.ca/en/certification_specification/
Certification Validation and Online Certified Plant Lists
Detailed information about certified plants is actively updated and securely maintained by CPCQA in the certified plant listings, as follows: - Architectural and Structural Precast Concrete Products: https://www.precastcertification.ca/en/ certified_plants/architectural-structural/ - Concrete Pipe, Manhole Sections and Precast Concrete Drainage Products: https://www.precastcertification.ca/en/certified_plants/pipe-manhole-drainage/
More information: precastcertification.ca; qacadministrator@precastcertification.ca or 888749-5123.
AUTHOR: BRIAN J HALL, B. B. A., MBA | MANAGING DIRECTOR, CANADIAN PRECAST/PRESTRESSED CONCRETE INSTITUTE, AND VICE CHAIR - ROYAL ARCHITECTURAL INSTITUTE OF CANADA FOUNDATION. BRIANHALL@CPCI.CA.
One of the most environmentally sustainable and socially responsible academic buildings in North America. Winner of the Institutional [Large] Award, 2020 Canadian Green Building Awards.
Architect: Baird Samson Neuert Architects. Contractor: Ellis Don.

INLINE FIBERGLASS LTD. provided the bird-friendly, triple-glazed high-performance windows that contributed to achieve 71% energy savings and 67% in greenhouse gas emissions compared to Canadian Model National Energy Code reference building. The building is one of the first to use principles of Thermally Active Building Systems (TABS) to achieve LEED Gold certification.
A C NADIAN GREEN BUILD I N G AWARDS 2020