
7 minute read
UBC Okanagan, Skeena Residence
from SABMag 69 - OUR ANNUAL CANADIAN DIRECTORY of Products and Services for Sustainable High-Performance
by SAB Magazine
Multi-unit residential building design takes care in detailing
By Brian Wakelin
Advertisement
The new UBCO Skeena Residence at the Okanagan Campus of the University of British Columbia comprises approximately 72,600 gross square feet over six storeys and has been designed to Passive House standards. The ground floor includes common housing amenities and building service spaces while the upper five storeys include accommodation for 220 students together with associated social spaces. Skeena completes an ensemble of residence buildings encircling the central green space on campus – known as Commons Field. The project focuses on student life and support services while meshing seamlessly with the existing campus.
The five identical residential floors include shared bathrooms flanked by two bedrooms. This layout allows space for quiet study when required. Additionally, each floor contains both a study lounge and a house lounge with views of the surrounding mountains, the lounge being equipped with a kitchenette, dining table and couches. Locating these spaces at opposite ends of the floor ensures that quiet study is not interrupted by noise from the social home lounge.
On the first level, the Skeena Residence has a large laundry room located adjacent to the student lounge. Separated by a glass wall, the relationship between the two spaces encourages chance meetings and spontaneous gatherings. Moreover, the transparency offers passive surveillance, or visibility that promotes a sense of security. In short, the design of the building supports community life.
The design of the Skeena residence was driven largely by the requirements of the building program and by the successful layout of the neighbouring student residence. The two bedrooms with shared bathroom module uses an optimal length and width, which also optimizes the number of floors required to accommodate the building requirements – the objective being to minimize the amount of energy required to heat and cool the building.
1. View across the central green space to the UBCO Skeena Residence.
Site plan
N
This Passive House goal of minimal energy use for heating and cooling also informed other design choices. Given that irregular building forms with multiple indentations and corners, or projections such as steps, overhangs, or canopies create challenges for insulation, airtightness and the elimination of thermal bridging, a simple and efficient planar volume performs most optimally. Mechanical systems also work best within a narrow, contiguous box. This limits aesthetic parameters to material, colour, pattern, and texture. Thus, the simpler the building, the more important material choices and detailing become.

The exterior is clad in a combination of brightly coloured fibre cement panels and darker metal panels. A feeling of depth is created by bringing the fibre cement panels forward of the metal, emphasizing the depth of the window reveals. This gives articulation to the simple form, without introducing complexity that would compromise energy performance.
Design decisions are also swayed by other practicalities such as standard and locally-available materials and techniques. The building is a wood frame with some concrete on the ground floor. A wood structure was chosen for its inherent insulative properties as well as its ready availability and ease of construction.
PASSIVE HOUSE MULTI-UNIT BUILDING DESIGN
Designing multi-unit buildings to the Passive House standard presents a unique set of challenges and opportunities, making the inclusion of building enclosure specialists critical from the outset.
The process for Skeena required accelerated decision-making and involved more work during schematic design than for traditional projects. For example, understanding thermal bridging implications and other energy-loss considerations necessitated front-loading assembly and junction detailing. These details were also critical for determining if Passive House heat recovery units could service the project, or if cooling would be required in the Okanagan’s hot summer climate.
2. The recessed entrance with metal cladding above. Including building enclosure specialists from the outset is critical in Passive House design. 3. A simple and efficient planar volume was chosen to simplify detailing for insulation, airtightness and the elimination of thermal bridging. 4. Positioning the fibre cement panels forward of the metal cladding brings articulation to the simple form without introducing complexity that would compromise energy performance.
Detailing of the mechanical systems early on was also vital to maintaining the schedule and budget. To achieve Passive House performance goals, mechanical service pipes required thicker insulation than for a conventional building. Because the design of the building was approached holistically, we were able to maximize the amount of insulation possible for the pipes while still fitting within typical assembly dimensions. It was also possible to adjust other building components to achieve the energy goals.
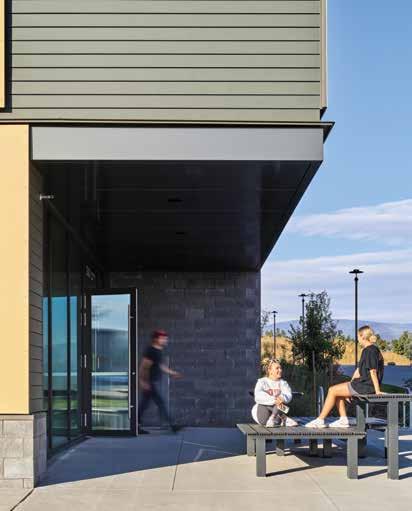
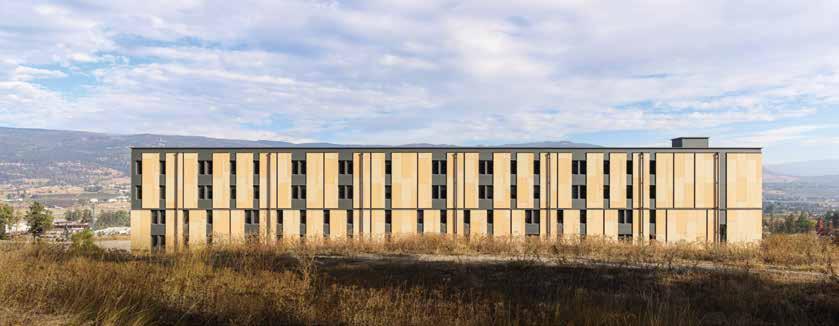
Floor plan - Levels 3 to 6

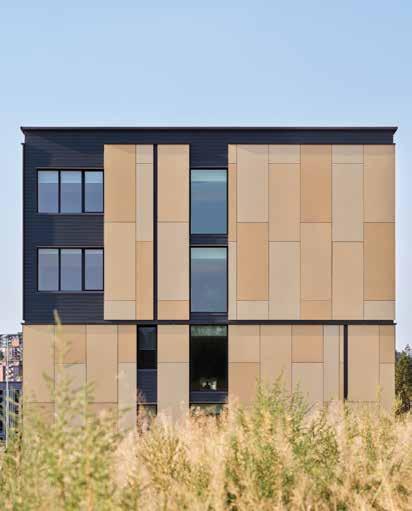

PROJECT CREDITS
CLIENT University of British Columbia ARCHITECT Public: Architecture + Communication CONSTRUCTION MANAGER Sawchuk Construction Management STRUCTURAL ENGINEERS Bush Bohlman & Partners LLP MECHANICAL ENGINEERS AME Consulting Group ELECTRICAL ENGINEERS Jarvis Engineering Consultants BUILDING CODE CONSULTANTS GHL Consultants Ltd. CIVIL ENGINEERS AND LANDSCAPE ARCHITECTS WSP PASSIVE HOUSE CONSULTANTS RDH Building Science PASSIVE HOUSE CERTIFIER Peel Passive House Consulting Ltd. COMMISSIONING AGENT Kane Consulting PHOTOS Andrew Latreille
PROJECT PERFORMANCE Passive House Metrics Heating demand
7.08 kWh/m2a Cooling and dehumidification demand 2 kWh/m2a Primary energy renewable 70 kWh/m2a Air leakage 0.08 ACH (post-construction test)
2
12 3
9
5
4
7 8 9 1
6
10 11 1. Exterior wall construction:
26ga steel siding 1" vertical z-bar 8" mineral wool thermal insulation Vapour-open air barrier membrane 3/4" plywood sheathing 2x6 wood framing w/ mineral wool thermal insulation 5/8" gypsum wall board Vapour retarder paint primer
2. Typical floor finish:
Carpet finish 1-1/2" gypsum cement underlayment 3/4" plywood subfloor 9-1/2" engineered wood I-joist 1/2" resilient ceiling channel 5/8" gypsum board ceiling, two layers
3. Fiberglass thermal spacer 4. Window:
Triple glazing 3mm annealed LoE2 + argon cavity + 3mm annealed clear + 3mm LoE in vinyl frame with fiberglass reinforcement
5. 24ga metal head closure 6. Weep hole with perforated metal backing 7. Double-sided tape and sealant 8. Drainage mat 9. Foil-faced through-wall flashing 10. 24ga preformed metal sill with end dams 11. Perforated metal flashing clip 12. Wood interior sill
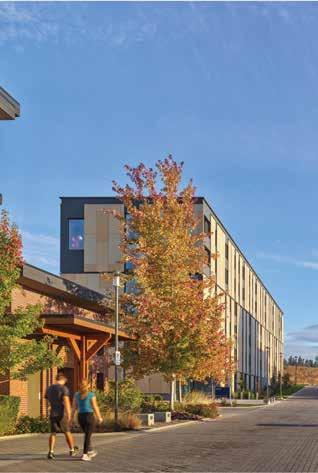
Window section detail
The density of occupants in a student residence necessarily presents further challenges. With a student population comes a far greater number of fridges, hair dryers, and computers per square metre than a typical mid-range residential building. These appliances create a significant plug load, or electrical draw.
To add to the complexity, when students are not chilling drinks, drying wet hair, or researching on their laptops, they are engaged in humidity-intensive activities such as showering. To prevent the buildup of excess moisture, building air is changed every three hours via highly efficient heat recovery ventilators thus mitigating the possibility of mould, odours or stale air. To drive down greenhouse gas emissions the Skeena Residence is not connected to the available natural gas network and a roughed-in connection for a future photo-voltaic array has been provided at the roof.
BRIAN WAKELIN IS A PRINCIPAL AT PUBLIC: ARCHITECTURE + COMMUNICATION IN VANCOUVER.
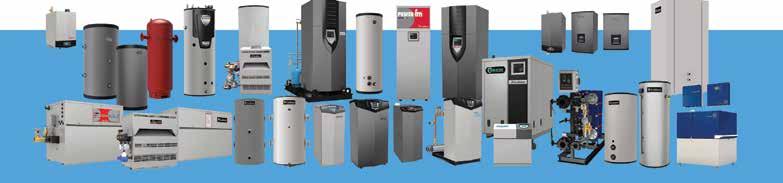
Some just see a Some just see a blueprint. blueprint. You see a chance You see a chance to grow your business. to grow your business.
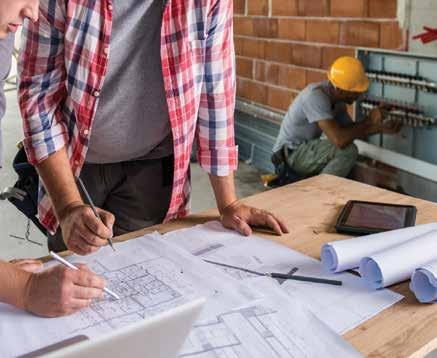
Your business is all about cash flow, project performance and planning, going big too soon, having the best people, innovating and working with partners that really want to help you grow your business. Your business needs innovative partnerships that incorporate the newest product technologies and digital tools — reliable brands that make things better. That’s why AQUATECH™ is proud to offer Lochinvar® heating and hot water boiler solutions that perform for you and your customers. Energy efficiency. Quality performance. Broad product selection. Technical support. Call us today and explore how our over 40 years of experience can support you.
Represented by
Aqua-Tech Sales and Marketing Inc. P: 905.631.5815 • F: 905.637.8655 • aquatech-canada.com
Super low U-values Tough frames Beautiful aesthetics Passive house applications
The future is FIBERGLASS
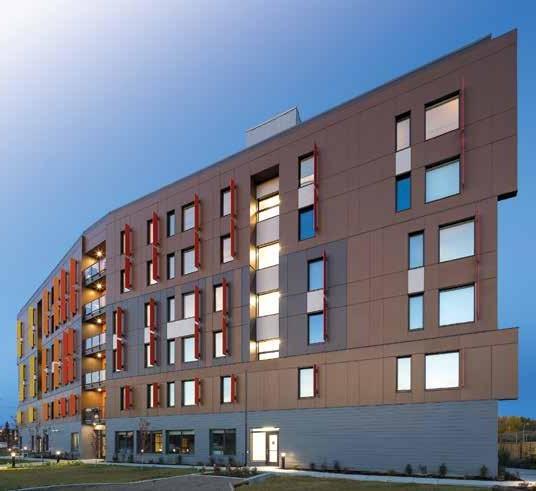
DUXTON Windows & Doors Winnipeg, MB 204.339.6456 duxtonwindows.com
SHOWN HERE Fort St. John Passive House Low Hammond Rowe Architect RENU Engineering Inc. | WCPG Construction Ltd.