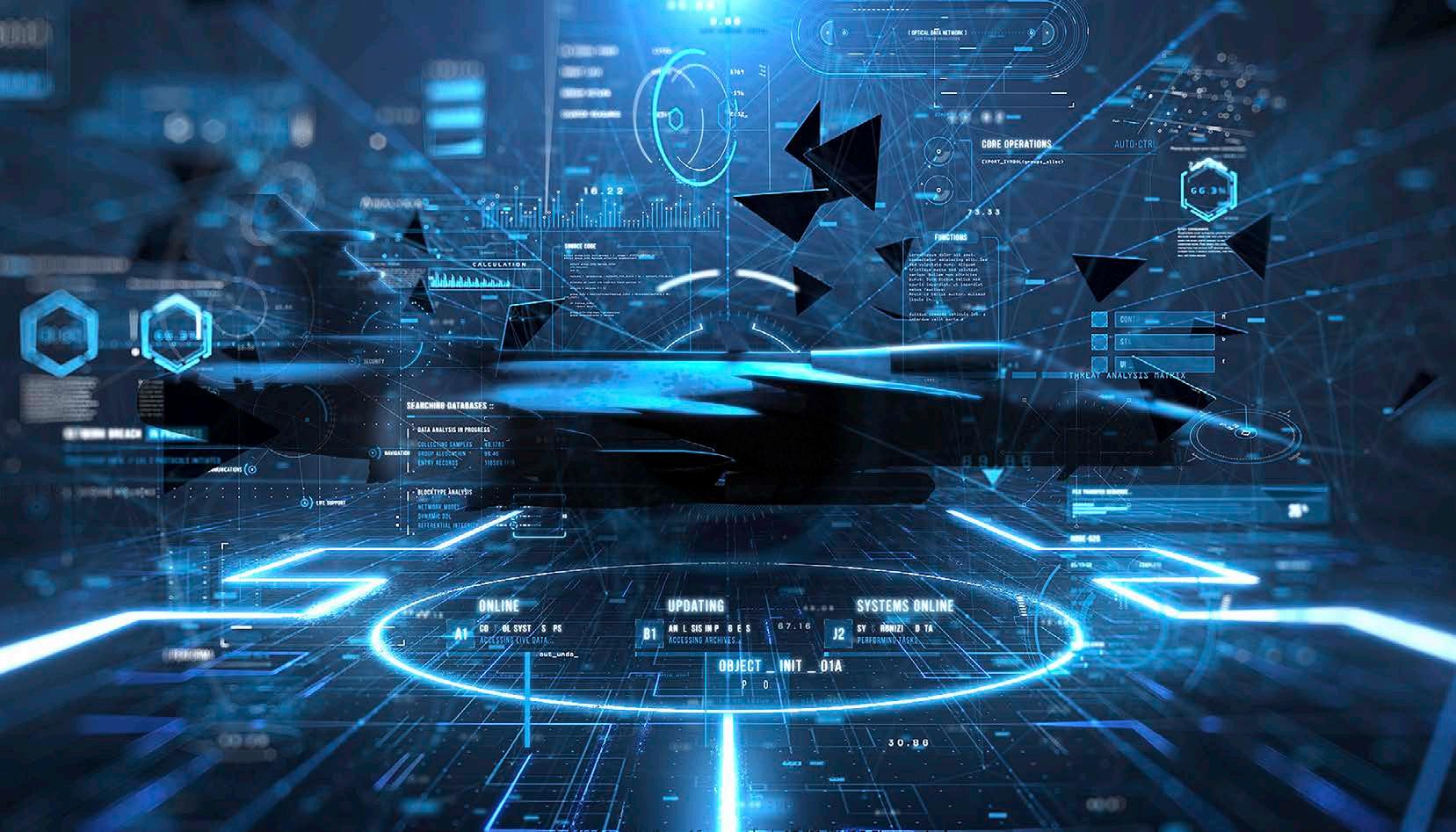
11 minute read
Defence - Darren Olivier
Defence
Darren Olivier
Advertisement
GETTING YOUR DIGITAL SYSTEMS RIGHT
In this era of high maintenance, fuel and labour costs, ever more complex aircraft and weapons systems, and a need to extract more use out of fewer platforms, it makes sense for air forces to invest heavily in technological approaches that maximise efficiency. Yet far too many air forces, especially in Africa, continue to neglect this in favour of traditional approaches to aircraft fleet management, for which they end up paying a high price.
THE South African Air Force (SAAF) is better than most of its African counterparts in that it has established an excellent base foundation around two main systems: The Operational Support Information System (OSIS) and the Ground Control and Command System (GCCS), both of which have resulted in large gains in efficiency and availability over the years. However, over the past two decades, the SAAF has somewhat neglected both systems, preferring to maintain them rather than to invest in substantial improvements, further integration and expansion.
This column will look at the lessons
learned from the implementation of OSIS in particular, although the situation is broadly similar for other SAAF computer systems like GGCS, and offer some recommendations on how both the SAAF and other African air forces can improve upon them in order to digitise more of their operations, reduce costs and increase availability.
OSIS & SLIS
OSIS has its origin in a decision made in the late 1980s by the South African Department of Defence to move away from a mainframe-based central logistics system for all services: the Logistics Information Management System (LIMS), to having each service create its own specialised logistics platform. This was finalised in 1993 as the Logistical System Master Plan (LSMP3). Thereafter the Army, Air Force and Navy each pursued custom modern logistics systems, with the Air Force choosing the Pretoria-based Paradigm System Technology to build the SAAF Logistical Information System (SLIS).
SLIS was initially trialled in beta form on the Oryx and PC-7 MkII Astra aircraft fleets in the mid 1990s, where it quickly showed its value over the SAAF’s existing approach. After a rewrite from the ASSYS programming language to Uniface to address support and cost concerns, the addition of operationally-focused functions such as the ability to track staffing, crewing and missions, plus the Navy’s adoption of a variant of SLIS, the system was renamed Operational Support Information System (OSIS) and gradually rolled out to the rest of the force.
It’s important to highlight just how well-specified and designed OSIS was, given how complex the problem it set out to solve was. An average modern aircraft has tens of thousands of components and sub-assemblies, each of which needs to be tracked individually in order to both efficiently manage stock and prevent faulty parts from being installed. An Oryx helicopter has over 30,000 unique components, a Gripen more than 60,000. There are hundreds of separate maintenance procedures for each aircraft type, each of which must be modelled, tracked and linked to the relevant unique aircraft and components. Every action that can affect an aircraft or one of its components, plus all of their individual states, must be tracked, auditable and available in real time to any user with the relevant authority. Plus, all this has to be done for units dispersed around the country, with vastly different aircraft types, while supporting extended operations away from home base.
The SAAF project teams behind LSMP3 and SLIS did excellent work to both model the service’s logistical challenges and to then create a specification for an allin-one system that would be able to handle all of the above problems and more, with the final OSIS system also adding the ability to manage the availability, currency and skills of technical staff & air crew, track the vehicles and facilities of an operational base, and run forecasts and simulations to predict aircraft availability, parts needs and other measurements for months or years into the future.
Paradigm System Technology proved to be excellent partners, designing and building a system that incorporated all of the specified requirements and has worked for decades without needing major rework.
In fact, after receiving permission to offer SLIS/OSIS commercially as the Equipment Programme Management System (EPMS), Paradigm was able to sell the system to the Royal Air Force (RAF) where it formed the core of the Logistical Information Technology System (LITS). Elements of EPMS were later included in the AirCraft Computerised Equipment Support System (ACCESS) and Army Maintenance Information System (SIMAT) for the British Army and French Army respectively.
LITS in particular has been regarded as transformative by the Royal Air Force, where it gave the service the ability for the first time to have up-to-the-minute reporting on the status of every single aircraft and component, across every unit, while creating substantial operational improvements in readiness, safety, cost and forward planning. Its introduction, once the usual entry into service issues had been resolved, is even widely regarded as helping to bring about entirely new ways of thinking about and organising logistics.
OSIS has proved beneficial too. According to a study by Maria-Jacoba Hattingh in 2005 the introduction of OSIS
Effective digital management of defence logistics has become essential.
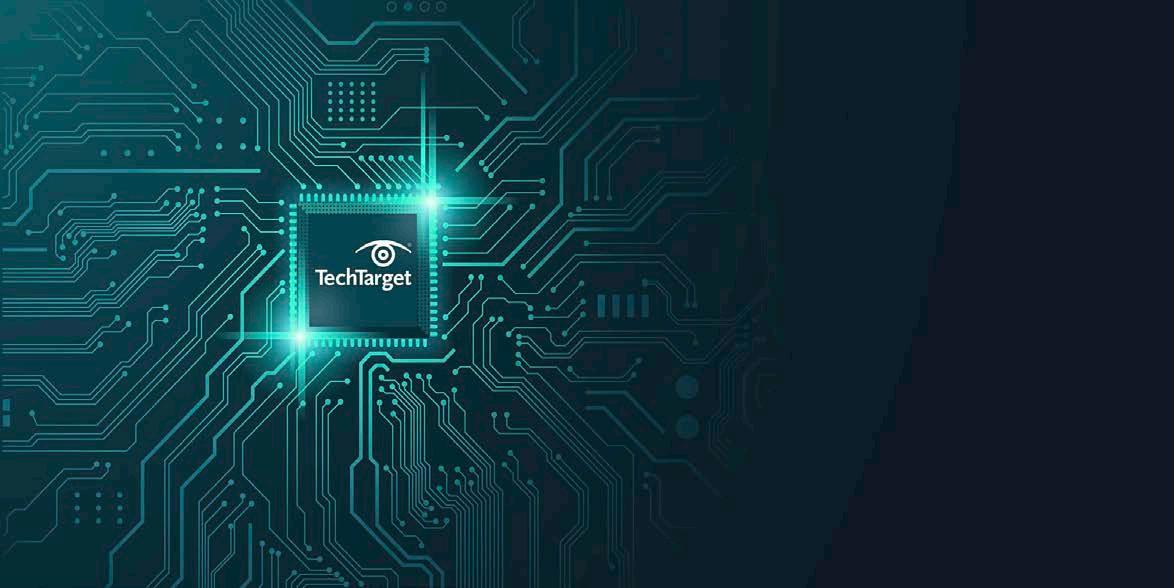
to the SAAF, while marked by issues arguably beyond the project team such as poor network connectivity between bases, problems caused by the ongoing SAAF re-organisation and a general resistance to change, nonetheless resulted in substantial improvements to aircraft readiness, flight safety, data integrity, planning and the sharing and availability of needed information. Substantial problems remain, however, and unlike the RAF, the SAAF has never seen the full set of benefits from having an integrated logistics management system, despite having a nearly identical solution. Today only a fraction of OSIS’s power and functionality is being used.
LOSS OF INSTITUTIONAL FOCUS
So what went wrong? In short: A loss of institutional focus; an acquisition project process that was bad for software; and an attempt to treat OSIS and GCCS like regular commercial enterprise software rather than as the specialised custom solutions they were.
By the time OSIS reached maturity in
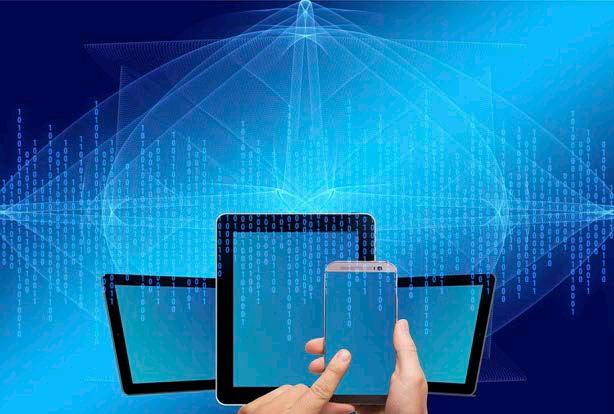
GIGO - If garbage is fed into a digital system if will produce garbage results - a situation the SAAF is approaching.
the late 1990s to early 2000s, the SAAF had lost focus on its previous ambitions to transform the force’s logistics. Senior leadership were too preoccupied with handling transformation, budget cuts and a huge re-organisation to be able to pay enough attention to implementing an entirely new logistical system, even if the potential savings could be substantial. That’s why, for instance, OSIS was gradually rolled out to flying squadrons without there being a concurrent upgrading of the outdated network infrastructure linking them to the rest of the SAAF. This created a perception that OSIS was too slow to be usable, even though the fix was merely a network upgrade away.
That inattention was justified on the basis that those neglected priorities could be returned to in more stable times, but the SAAF has become so used to scrambling in survival mode after each budget cut that it has effectively lost the ability for organisational transformation. Both the current Chief of the Air Force and his predecessor launched ambitious strategies to re-organise the SAAF along more efficient lines. Neither plan got off the ground.
Then, OSIS suffered from the myopia of the DoD and Armscor planners who created defence acquisition policy such as VB1000 and its successors, which codified the way in which new systems should be acquired and supported. While that policy was excellent
and extremely thorough for acquiring complete military systems, such as aircraft or ships, it was badly suited for acquiring software solutions like OSIS, which did not have associated hardware and had an impact on the entire organisation.
So rather than adopting a software solution via an ongoing support and development contract with the supplier, software like OSIS and GCCS was acquired via proper military projects then immediately farmed out to Denel’s InfoPlan (later SITA) for basic operational maintenance, and occasionally upgraded via new military projects in much the same way as you’d upgrade an aircraft.
It’s a terrible approach that doesn’t work, yet it’s still being used in the
SAAF today. In contrast, the RAF has continuously developed and enhanced
LITS over the years thanks to long-term support and development contracts with
IBM, the original LITS consortium lead. And because it has been an ongoing and renewed contract, many of the original team continue to work on the system, thus preserving domain knowledge. It has also never stopped pushing the adoption of LITS within the organisation, ensuring that its feature set and ease of use were constantly expanded to meet the needs of even lowlevel personnel. In contrast, SITA is not suited to supporting specialised and custom defence software, as it’s primarily oriented around managing commercial support contracts for government’s commercial off-the-shelf software (COTS), for which the market has a ready supply of fungible skills. Defence systems like OSIS are too small a part of its portfolio to make it worth investing the money and effort to create in-house
teams, so it mostly outsources both support and training to an ever-dwindling supply of external contractors with the requisite skills. As a result, there is almost no ongoing development, no incorporation of improvements, little to no work on
extending data sharing and interoperability, and no incentive to drive better adoption of OSIS and its more advanced features within the SAAF.
The end result is quite predictable: Because the squadrons and maintenance units were not given the training, equipment and process reforms required to use OSIS’s entire feature set, they tend to see only its value as a parts tracking database and treat the entering of any other data as a chore for reporting purposes. In fact, in most units the line personnel don’t even have access to OSIS at all. Instead they work from a 1980s-style entirely paper-based approach that’s then entered every few weeks into OSIS by a dedicated data capturer. This not only destroys the value OSIS has a real-time view into the state of the Air Force, but it leads to numerous data capture mistakes and other data quality issues that are often caught only during the compilation of quarterly and annual reports.
This has become a negative feedback loop, where the lack of use of OSIS at squadron levels, and the poor enforcement of data quality leads to it being mistrusted and seldom used by senior leadership and planners, which in turn leads to even less use at squadron level.
Quite bizarrely, this means that in the past decade the SAAF has actually regressed in technological terms when it comes to its handling of logistics and reporting, reverting from a highly functional integrated system to an inefficient and errorprone system of paper records, manual data entry and spreadsheet-based collation.
So what are the lessons learned? How could the SAAF get itself out of this situation, and how could other African air forces avoid making the same mistake?
The answer is deceptively simple in its explanation, but enormously difficult in its implementation: You need to treat your specialised custom software that enables core capabilities, such as integrated logistics, as a top level project, every bit as important as acquiring a new aircraft type. Effort made up front to first rethink and model, the organisation and its functions, in such a way as to prepare it for a digitisation effort, will pay off and will prevent failures where software solutions are forced to be made extremely complex and brittle in order to cater for poorly designed workflows and processes.
It’s better to test out both a solution and any new concepts it brings with smaller and less risky experiments, such as the OSIS beta on the Oryx fleet, and to then gradually add features and roll outs, rather than trying to solve all the problems at once.
And finally, critical software like this should be supported by long-term fullservice contracts, preferably with the original supplier, rather than attempting to have irregular development bursts followed by maintenance by a third party. It works out cheaper in the end too.

AMO 1288
Your one-stop-shop for repairs and overhauls of aviati on rotables and special processes.
BNT Internati onal (PTY) Ltd. Unit D3, Denel Industrial Park, Denel North Entrance (off Atlas Road), Kempton Park, Gauteng, South Africa, 1619 Tel. +27 11 395 1677 Email: info@bnt-int.co.za Website: www.bnt-int.co.za

• Quality • Safety • Service Excellence • Honest Pricing
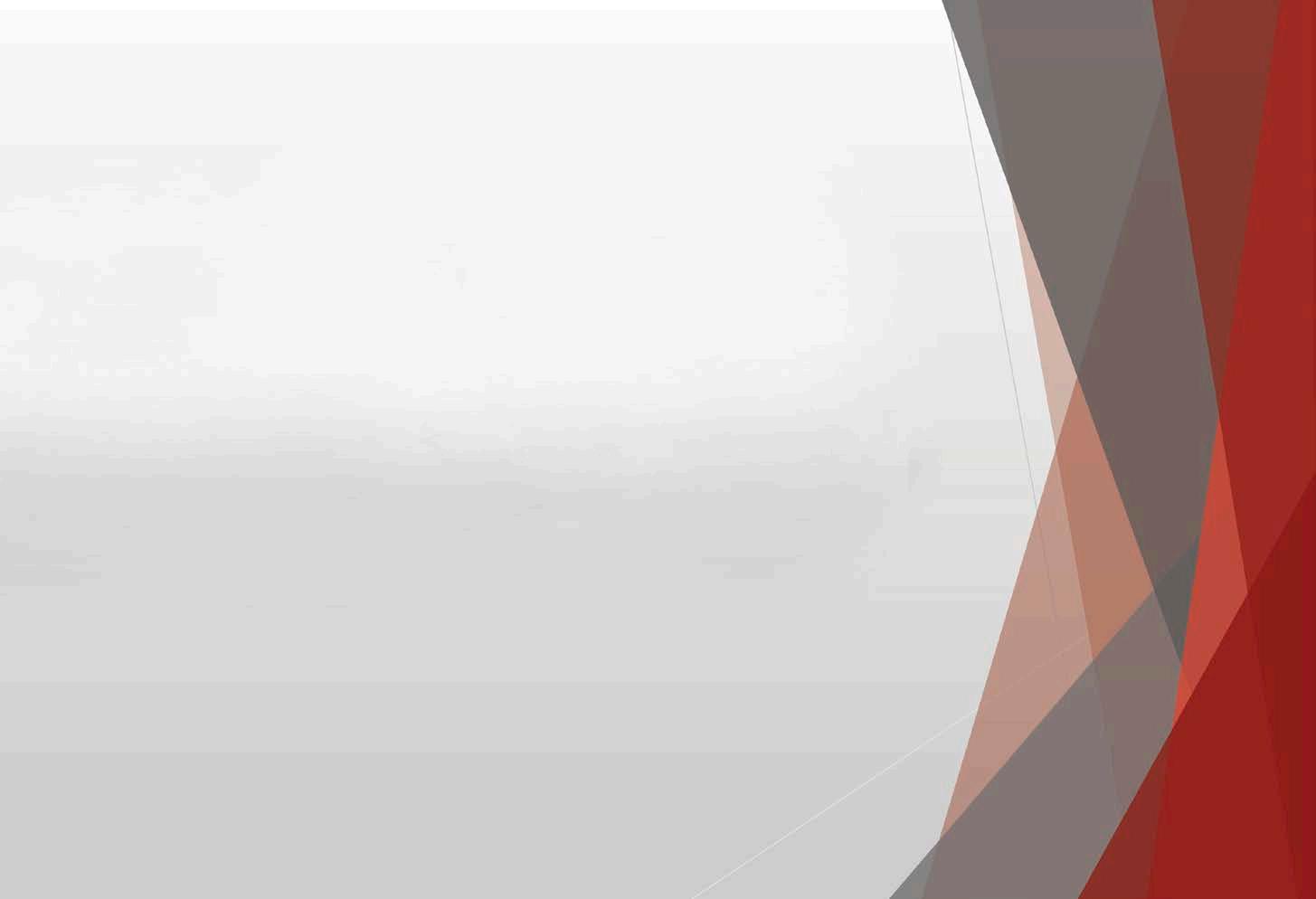
Aviati on Services
• Composites & Aircraft Structures • Wheel overhaul and Repair Services • Brake Overhaul and Repair Services • Non-Destructi ve Testi ng on Aircraft • Hydro Stati c Testi ng • Oxygen bott les • Fire Exti nguishers • Safety Equipment • Aircraft Weighing o Small aircraft s up to larger B737, A320, L-382

SA Flyer 2020|03