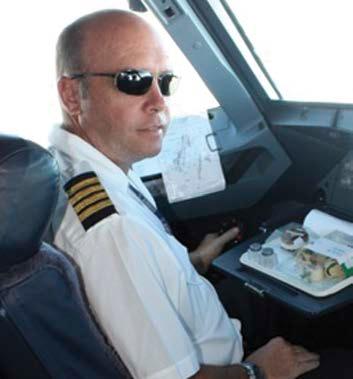
8 minute read
AIRLINE OPS MIKE GOUGH SPLIT SECOND DECISIONS
“This will be a go-orientated takeoff. However, in the event of a decision to stop before V1, I will call STOP, close the thrust levers and apply full reverse thrust. You will monitor and call DECEL, Reverse Green and notify ATC. I will bring the aircraft to a stop, set the park brake, and tell the cabin crew to Standby or remain seated.”
THIS WAS A PART OF EACH and every working day for me and my colleagues until the industry, and specifically my current employer, (up till this point) went to hell in a handbasket.
Advertisement
The ‘sing song’ was performed during the preparation for the first flight of the day, and for subsequent sectors (flights) we were permitted to simply mention ‘Standard RTO’, to save a bit of time and verbiage. This is how we were to prepare ourselves for that one-in-three-thousand chance of having to decide that it was safer to stay on the ground than to continue with the take-off, in a worst case scenario, at around 260 kilometres per hour.
A quick look at that statistic – one in three thousand – is a little scary. That is the average of rejected takeoffs (RTOs) in commercial transport aircraft versus normal takeoffs, globally. flights per day globally (pre-pandemic) that means we should be seeing at least one or two rejected takeoffs per day. The statistic for runway over-run events (being unable to stop and barrelling off the end of the runway) as a result of a high-speed RTO happens once every 4 500 000 takeoffs, which is somewhat more reassuring that the calculations we make actually work.
I have been fortunate that within the 25 years of airline operations that I have been exposed to, I have had one, low-speed, RTO.
My situation occurred during a training flight in an Airbus 319. It was literally a dark and stormy night at Johannesburg, departing for Maputo, with a trainee First Officer in the right hand seat. It was his sector, so he was Pilot Flying for the take off.
As per the RTO briefing, the Captain is responsible not only for the decision to stop, but also for the actions to initiate it, irrespective of whose sector it is. The FO in this case stabilised thrust (as per Standard Operating
Procedure) to ensure even spool up of the IAE V2500 engines. Then the thrust levers are then advanced through the Climb detent into the Flex / MCT detent. Click Click.
At this point, the Captain is required to forcibly remove the FO’s hand from the levers, and be ready to close them should the need arise.
This handover should be done no later than 80 knots, which is the “Thrust Set” call by the Pilot Monitoring – in this case me.
At around 50 knots, I heard one of the Generator Control Units (GCU) relays open with an audible clunk, situated behind the FO’s seat, and knew that trouble was about to be visited upon us.
A few seconds later, the Electronic Centralised Aircraft Monitoring system (ECAM) pinged to life, illuminating the master caution light, and displaying an amber electrical warning indicating an AC Bus 2 Fault. Simultaneously, some display information on the FO’s side disappeared.
“Stop” said I, reverting to ‘simulator’ mode, and thumped the thrust levers closed and into reverse. My somewhat bewildered right-hand-man turned to me and asked “Why?” Definitely not as per script and SOP, but I had my attention elsewhere. I should have heard ‘Decel’ and ‘Reverse Green’, and then a call being made to the control tower.
As the actual stop occurred above 72 knots, the spoilers automatically deployed, triggering the Autobrake system into maximum RTO effort. This causes a spectacular deceleration, with scant regard for passenger comfort. In our case, being low-speed, we were at a near standstill before the next runway exit, and I disengaged the Autobrake to keep us moving. I made a quick call to ATC, and they too wanted to know why we were stopping. I ignored that for the interim and vacated on the next left, and got my FO back on track with changing to the ground frequency for taxi instructions.
We cleared the runway, reassured the passengers, did a computer reset for the GCU, waited for the
The American Airlines Boeing 737Max hard on the brakes after rejecting takeoff at - or past - V1.
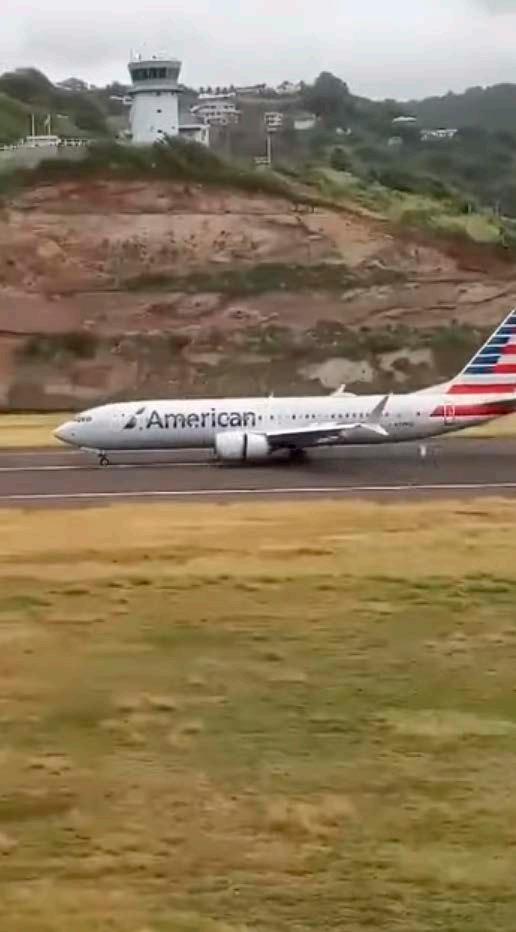
brakes to cool with engines running (we had extra tankering fuel on board) and after phoning the boss, we were on our uneventful way.
In this case, we were nowhere near any of the limiting factors that would make this a scary event. These limits depend on a multitude of aspects, and can obviously get quite complicated and technical.
First, of course is runway length, and its condition (dry, wet contaminated, snow etc). This essentially dictates the maximum weight that the aircraft can be, at the commencement of the take-off run. Most operators utilise a computerised application that provides accurate speeds (specifically that all important Decision Speed, V1), and thrust settings.
Provided, of course, that the crew input the data correctly. GIGO, and this has resulted in several major incidents and accidents.
There is always a trade-off between commercial efficiency in terms of using reduced thrust for each takeoff to save engine costs, and being on the limits of performance in terms of being able to stop on the remaining runway. Often, these calculations may show a stop margin of one metre, which is acceptable, and if everything is done properly, will be accurate. This means that if the decision to stop is made at V1 speed, there will be one metre of runway remaining when the aircraft comes to a stop.
Tight margins to say the least, but legal and safe when done correctly.
In some situations, the runway is in excess of the accelerate – stop distance (ASD) required by a particular aircraft type. There may well be other limitations that need to be considered, for example an obstacle beyond the airport environment that requires a certain amount of minimum energy for the aircraft to clear it by a certain height, if one engine should fail at or beyond V1.
A video clip of a Boeing 737 departing an island runway in the USA has done the rounds recently, showing what appears to be a high speed RTO, with what looks like the rotation to become airborne having been started. As I have yet to see any factual reporting on this, it is pure conjecture to assume that the stop was initiated after V1.
It is, however, a fantastic display of the effectiveness of the RTO braking / reverse thrust system, and has the aircraft stopped with ample runway to spare. It looks like it hit a flock of birds at high speed and the Captain elected, in literally a split second, that things would be safer if kept on the ground.
For what reasons would we want to stop on the runway? This, for decision making is divided into two main categories: Low speed (below 100kts) and High speed (100kts to V1).
things would be safer if kept on the ground

A screengrab of a passenger video of some of the large birds that caused the rejected takeoff. A good decision by the Captain.
Passenger comfort is not a priority, smoking brakes and tyres showing the maximium effort stop.
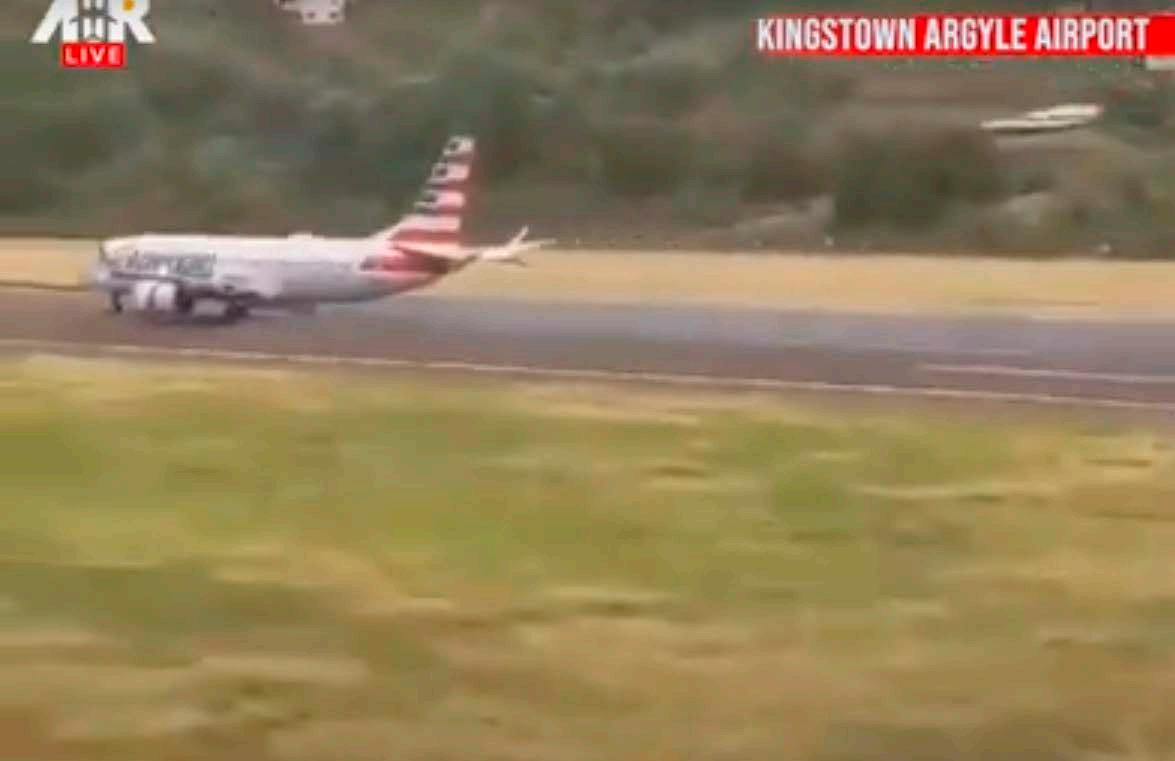
The Low speed scenario (as per my situation) is more Captain’s discretion, and influenced by the manufacturer’s operating instructions. In the case of Airbus, it is recommended that any warning that is annunciated must be considered and acted on appropriately.
Above 100kts, it becomes more defined, but every possible scenario cannot obviously be predicted and anticipated. For Airbus and Boeing, the obvious reasons are fire warning or severe damage (the latter was probably the case with the Boeing video), sudden loss of engine thrust, and the wonderful line of ‘malfunctions or conditions that give unambiguous indications that the aircraft will not fly safely’.
When training in the Airbus simulator, I like to use the simple concept of anything held in your left hand (side stick which is flight controls) and anything held in your right hand (thrust levers, which is everything engine related). This covers the Airbus information that sidestick fault, engine fail, reverser unlocked, reverser fault, and thrust lever fault are rock solid reasons for a decision to stop beyond 100 knots and before V1. While doing the take-off calculations, we are given a diagrammatic display of the runway and stop margins available, as well as a choice of minimum and maximum V1 speeds. The reasons for a V1 split get pretty technical, and is a bit much for this discussion.
A long runway, with a low V1, can easily result in the ability to reject a take-off beyond V1 and still remain safely on the tarmac, although the reasoning for that has to be that the aircraft has been rendered incapable of flight.
Considering the debris seen flying from an on-board view of this abort, I think the Captain took a wellinformed decision that resulted in a safe outcome.
That is what is important here, and each RTO adds to the data base of knowledge that continues to give us an operational insight as to how well (or poorly) the critical high-speed decisions turn out, within the context that the calculations are made and the actions executed.
Well done that crew.