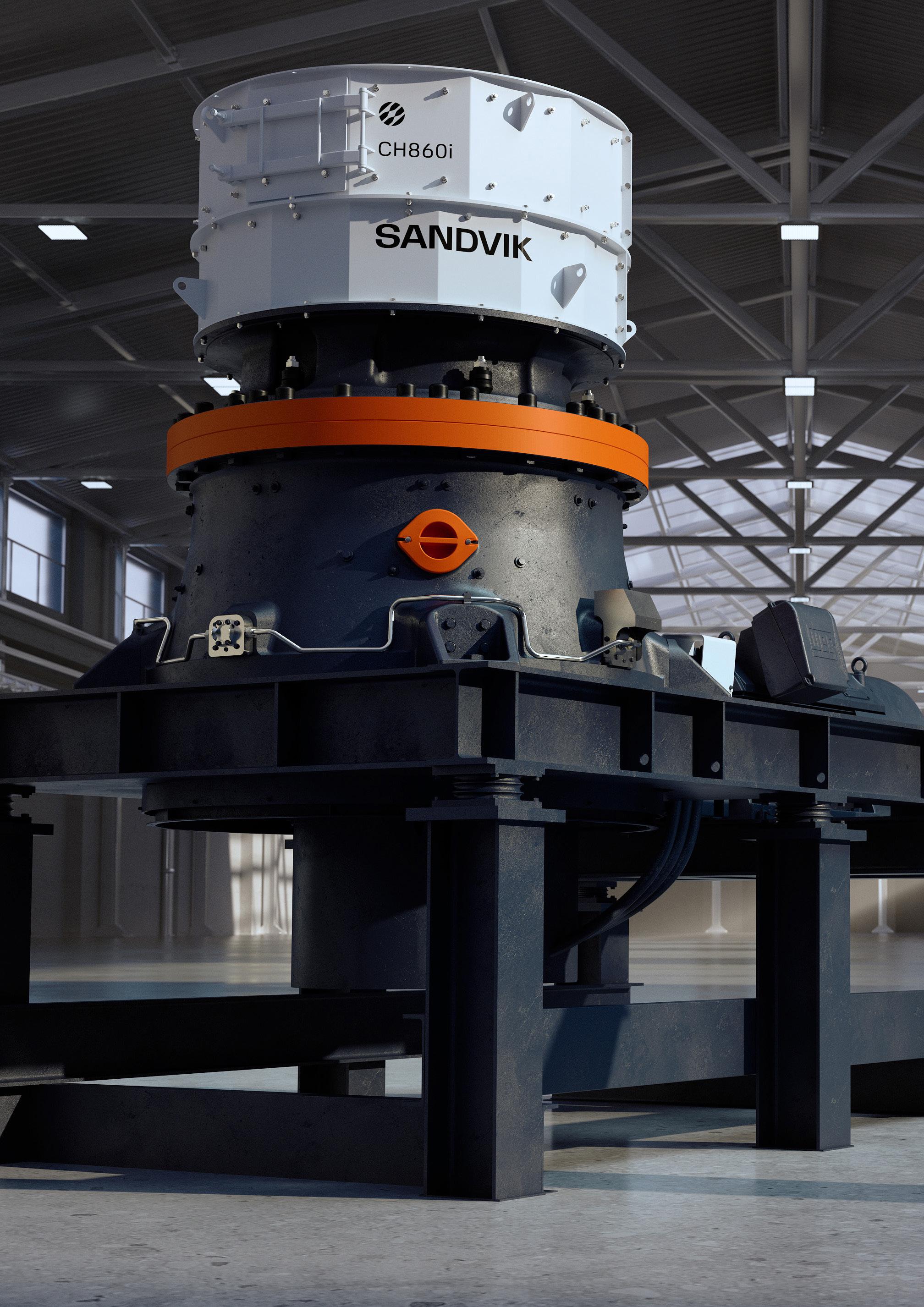
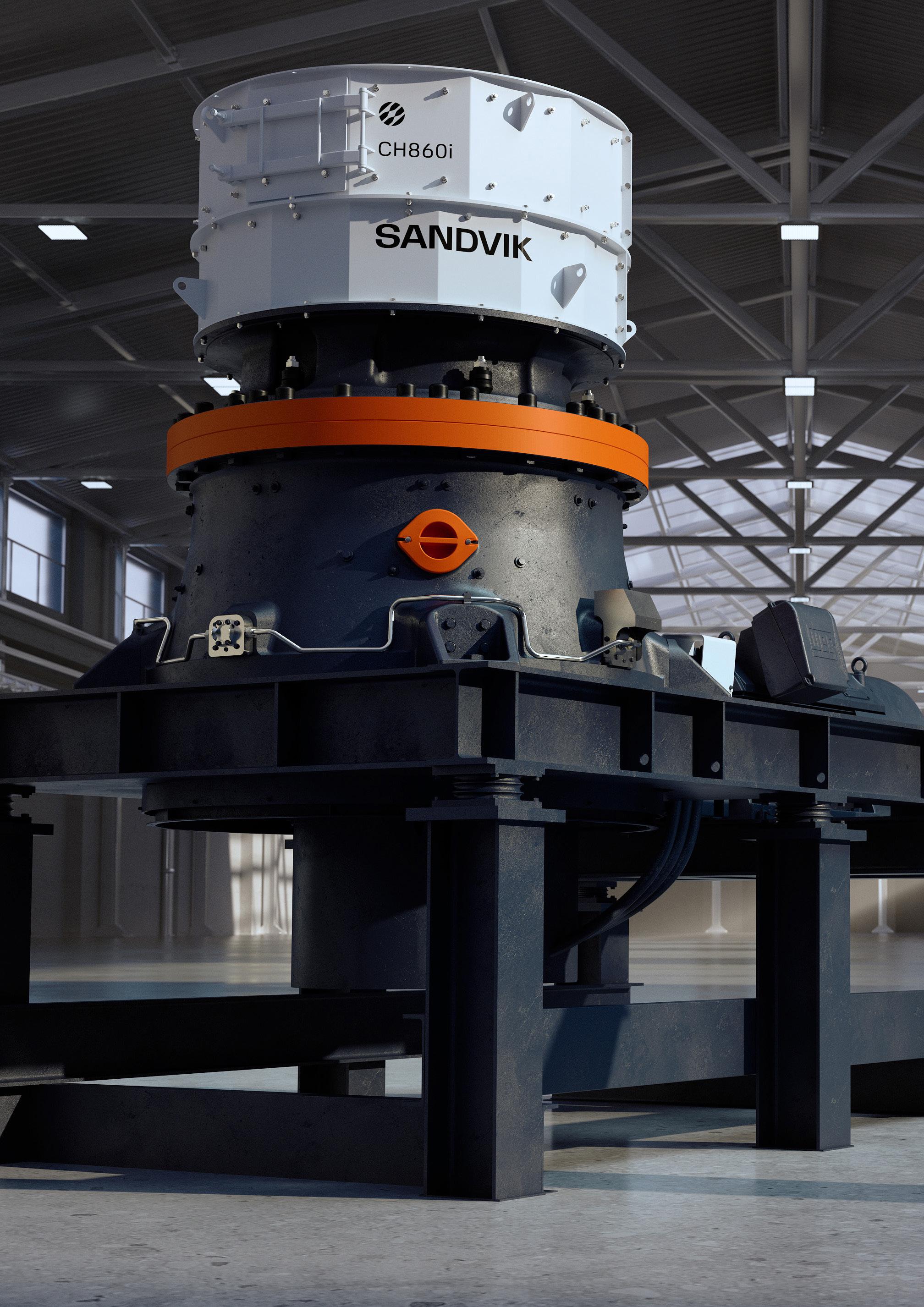
Our SRP
Sandvik Rock Processing Solutions
WELCOME
Dear colleague,
Welcome to the first issue 2024 of our business area newsletter Our SRP, where you can read about some of our many activities worldwide at Sandvik Rock Processing Solutions.
I’m sure you’ve heard by now that on July 1 our Stationary Crushing and Screening Division will split into two separate divisions. There will be one division for Crushing Solutions and one for Screening Solutions. I am happy that we now also have two Presidents appointed: Therese Withington for Screening Solutions and Peter Unelind for Crushing Solutions. You can find more details on page 6 in this newsletter.
Safety first
As always, I’d like to mention safety. In February we’ve seen a significant decrease of both Lost time injuries and Total recordable injuries, which is good news. Let’s make sure this trend continues! We also see a good development in the reporting of hazards. However, we need to get better at also implementing preventive and corrective actions when a hazard has been detected, so that we can improve the Close out ratio.
Q1 webinar and strategy update
We are approaching the end of the first quarter 2024 and the Q1 results will be released on April 22. A few days later, on April 25 you are invited to join in the Q1 webinar, where we will talk about our performance. During the webinar we will also take the opportunity to present the updated business area strategy, so stay tuned. An invitation will be coming out shortly.
Until then - stay well and stay safe.
President SandvikRock Processing Solutions
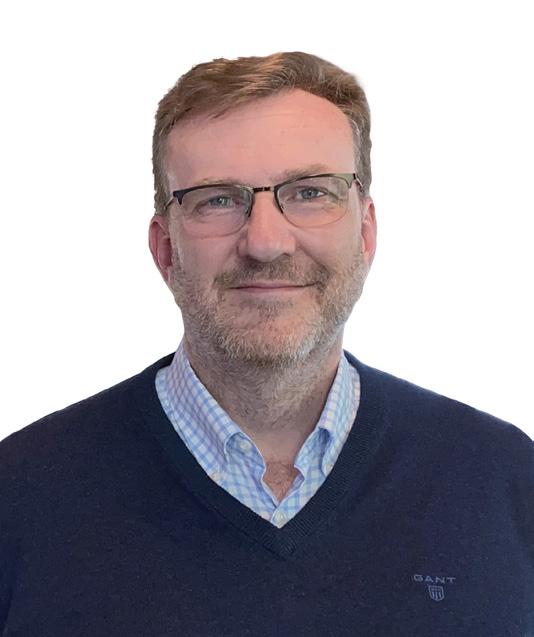
On the cover
In March Stationary Division launched the upgraded 800i cone crusher series. It has new mechanical upgrades for increased reliability and uniformity, together with the new automation and connectivity system ACS-c 5.
This year, Sandvik Rock Processing Solutions (SRP) had no less than three strong candidates nominated for the Sandvik Sustainability Award in Memory of Sigrid Göransson - one from each of Stationary, Mobiles and Attachment Tools divisions.
The Stationary candidate “Screen, Feeder, and Exciter Refurbishment Program” has made it to the final round and the winner of will be announced during the Annual General Meeting on April 29.
All sustainability initiatives contribute significantly to our collective journey for a more sustainable future. To read more about the Sandvik Sustainability Award, all of this year’s finalists and nominees, go to the Sandvik Group intranet news of February 26
More information:
pontus.alexandersson@sandvik.com
Strong sustainability initiatives at SRP
Stationary Division
Screen, Feeder, and Exciter Refurbishment Program – The program focuses on extending the lifespan of equipment through refurbishment and upgrades. By reducing the need for new components, we contribute to resource conservation.
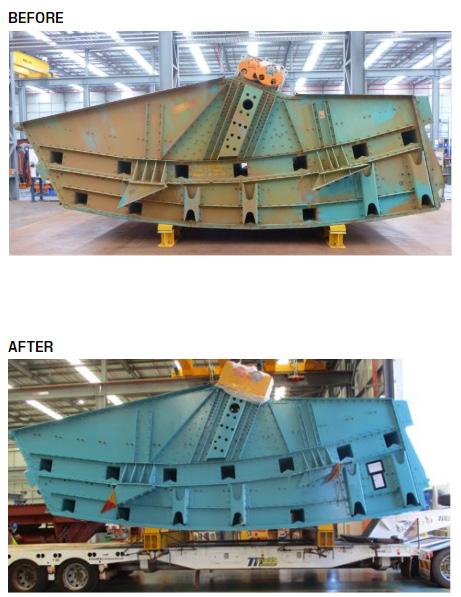
Attachment Tools Division:
Renewed and certified hydraulic hammer offering – This initiative is related to a world leading hydraulic hammer offering and the ambition to bring into market a more sustainable and feasible offering for customers wanting to buy second life equipment.
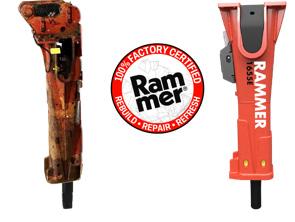
Mobiles Division
The fully electric UJ443E heavy jaw crusher –Electrification is a key driving force within our new product development strategy.
By the end of 2025, more than 90 percent of the mobile offering will be available with an electric drive alternative.
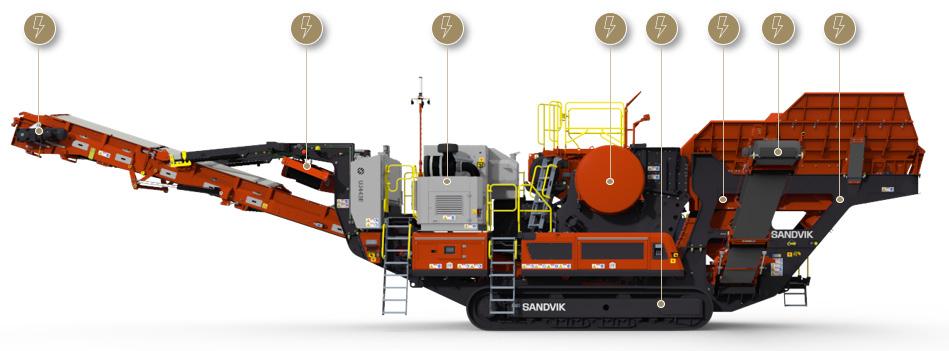
68 Safety walks in Cleveland
During 2023 Attachment Tools in Cleveland (USA) initiated and completed a total of 68 safety walks on the site. The safety walks involved participation from operations and office employees working together in focused efforts during the year.
The objective of these safety walks is to proactively identify and address potential hazards in our day-to-day operations. By actively engaging in the process, we aim to create a safer working environment and mitigate any risks that could lead to injury. During the year we have found and eliminated 68 hazards! We all actively participate and share observations in our daily work and collaborate towards creating an even safer workplace.
More information: julie.schilling@sandvik.com
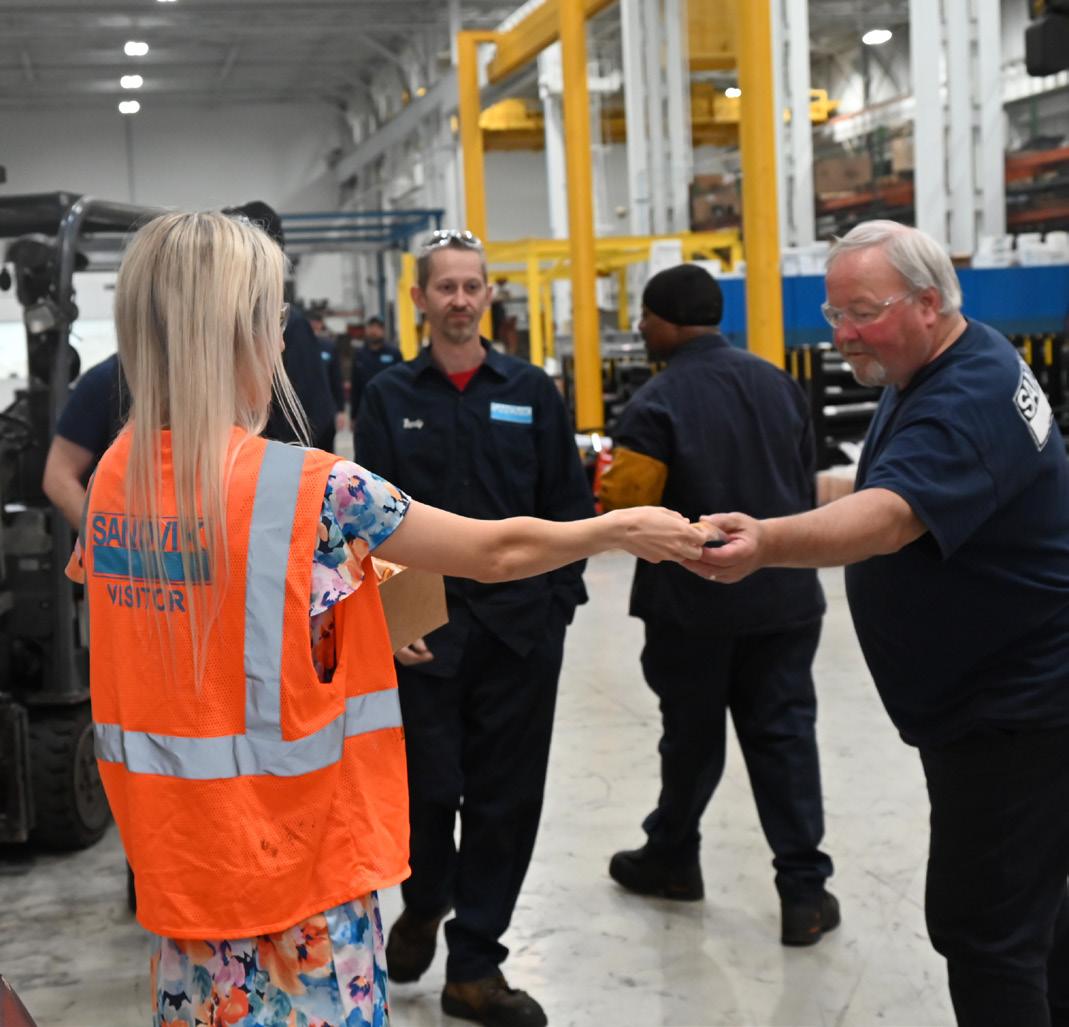
The crucial role of Speak Up
In today’s complicated landscape of regulations, business and governance, the role of whistleblower systems has become even more vital in fostering transparency, accountability, and ethical conduct. At Sandvik, we take this seriously with our Speak Up program. It is the responsibility of all employees in Sandvik to report misconduct, fraud, or any unethical behavior without fear of retaliation through the Speak Up system.
Here’s why it’s so important:
1. Early Warning System: Speak Up lets anyone confidentially report problems in a timely manner. This helps us fix things before they get worse, protecting our reputation and avoiding legal trouble.
2. Sandvik Values: By encouraging people to speak up we are fostering an environment of open communication and trust, to create a community where everyone supports one another and upholds strong ethical principles. That helps us to make Sandvik a better place for Everyone.
3. No Retaliation: Sandvik Speak Up system and relevant procedures are designed according to the requirements in EU Whistleblower Directive. We have zero tolerance for retaliation.
4. It’s the Law: Many jurisdictions, like the EU, require companies to have whistleblower systems.
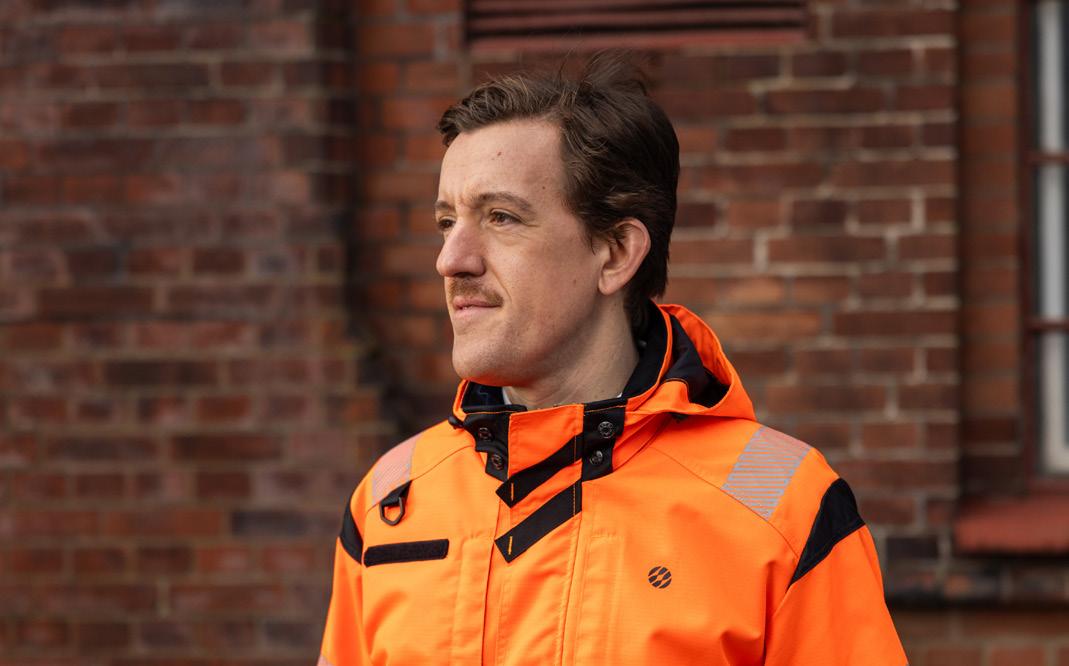
All reporters and their input were kept confidential and were thoroughly Reviewed by SRP Ethics Committe that consist of BA General Counsel, BA HR VP, BA Compliance Director and BA Compliance Officers
Having Speak Up is more than just a policy; it’s about creating a culture where everyone feels valued and heard. So, if you have any concerns, please just “speak up” or reach out to SRP Compliance team. More information: melih.kavukçu@sandvik.com
Skill development community initiative in India
SRP India (Stationary Division) contributes to skill development and employability of local youth in the country with the Sandvik Crushing and Screening Basic Operation and Maintenance (O&M) Training program.
This is a customised training program, where a selected group of trainees completes an 8-month program including classroom training by our Sandvik experts and on-the-job training at customer sites across the country. The program is designed based on the principal of ‘Learn and Earn’ as the trainees are provided stipend while acquiring the practical training and necessary skills at our customer sites.
With this unique training program Sandvik has been able to create a pool of skilled manpower, catering to the growing demand of our customers in the region and altering the socioeconomic dynamics, making youth self-sustainable.
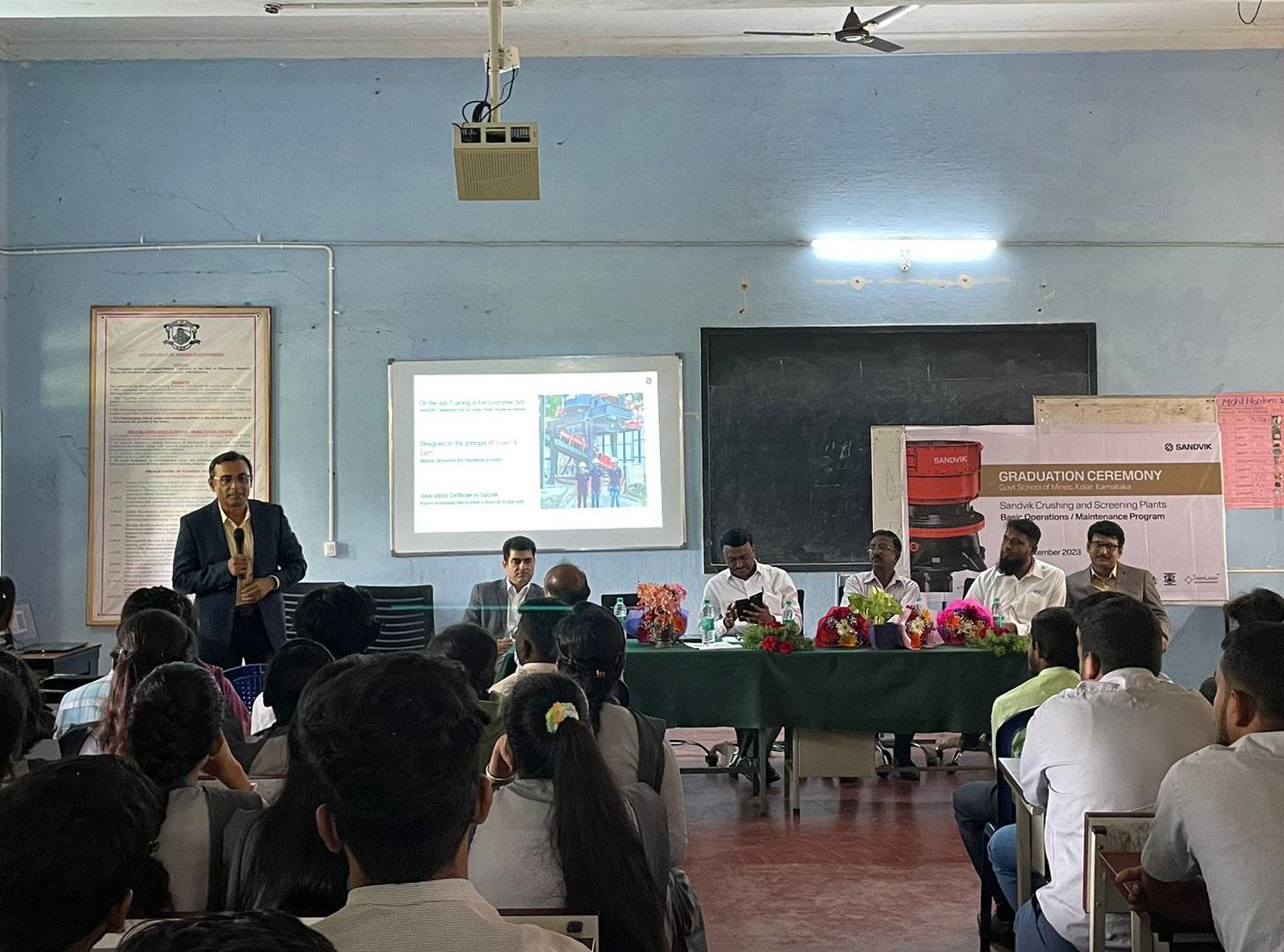
The completion of the third batch of the Sandvik Crushing and Screening Basic Operation and Maintenance Training program was celebrated with the SRP India management team who handed out certificates to the students.
The program is a collaboration with the Directorate of Technical Education & Employment (DTET), Karnataka through Govt. School of Mines, Govt. Polytechnic KGF and Teamlease Education Foundation (implementation partner).
More information: ravi.arora@sandvik.com
AC Shanghai EHS certified
Assembly Center (AC) Shanghai in China (Stationary division) received its brand-new ISO 45001 & 14001 certificates in December of 2023. This was the first time AC Shanghai applied since the company setup in July of 2021.
Many thanks to local employees and colleagues from other production units and assembly centers, as well as the Global EHS team, for their great effort and support on the preparation and implementation of the ISO 45001 & 14001. Showing that we have a certified management system for EHS is a first step, now we’ll work together on continuous improvements, step by step, to drive our Safety First Culture.
More information: mike.wu@sandvik.com
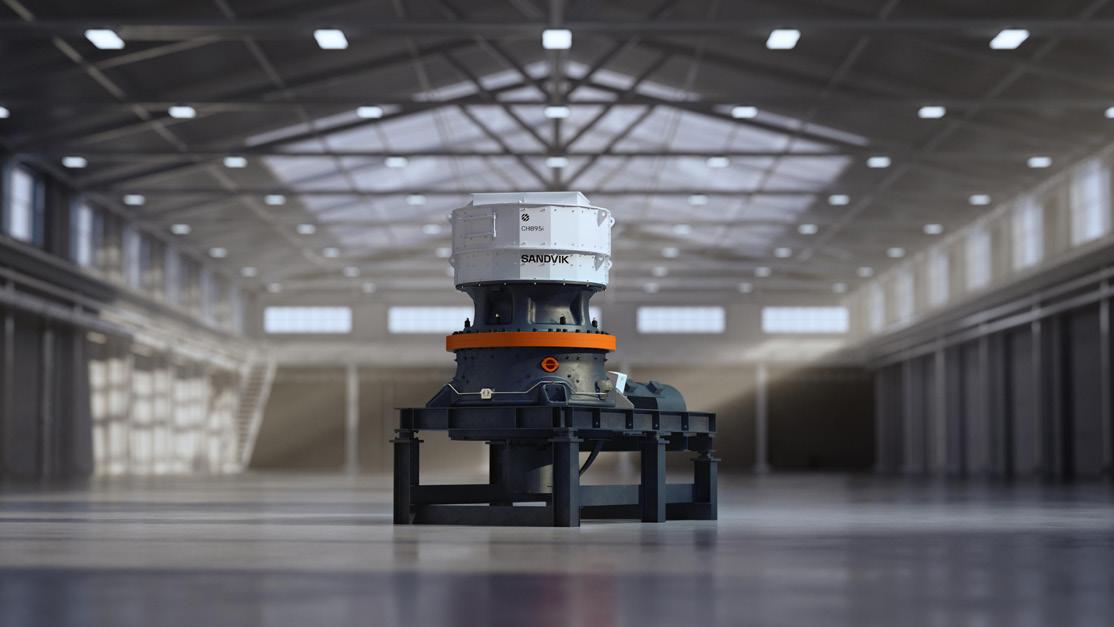

Two new divisions in SRP
Sandvik Rock Processing Solutions (SRP) makes changes in its structure and Stationary Crushing & Screening division will become two new divisions, Crushing Solutions and Screening Solutions.
The ambition is to have the operational set-up of Crushing Solutions and Screening Solutions up and running from July 1, 2024 and newly appointed heads of each division will report to SRP President Richard Harris.
Crushing Solutions continues to have its center in Svedala, Sweden. Operations in Sweden, China/Shanghai and India will report to Crushing Solutions.
Screening Solutions will have its center in Jandakot, Western Australia. Operations in Australia, South Africa, South America and China/Tianjin will report to Screening Solutions.
Sales Areas in their current form will be hosted in Crushing Solutions. We will maintain traction in our sales targets and synergy capture across in the combined crushing and screening business.
Assembly centers/production units will operationally support both screening and crushing as today and strong collaboration will continue to be essential. More information as regards the currently combined functions will come from the new presidents for each division.
For more information read the full intranet news of February 1 2024 as well as the appointment news of March 18.

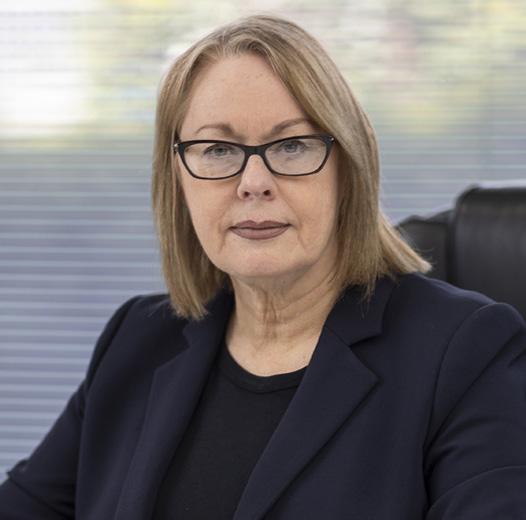
Quarry Academy 2023 in the USA
Quarry Academy in the USA is an educational seminar designed for the aggregate industry, teaching participants how to produce aggregates efficiently. The program has been run by Sandvik and Dyno Nobel for 16 years. Last year’s seminar took place in mid-November in Texas, USA.
During the event the Quarry Academy team announced the winner of the 2023 Quarry
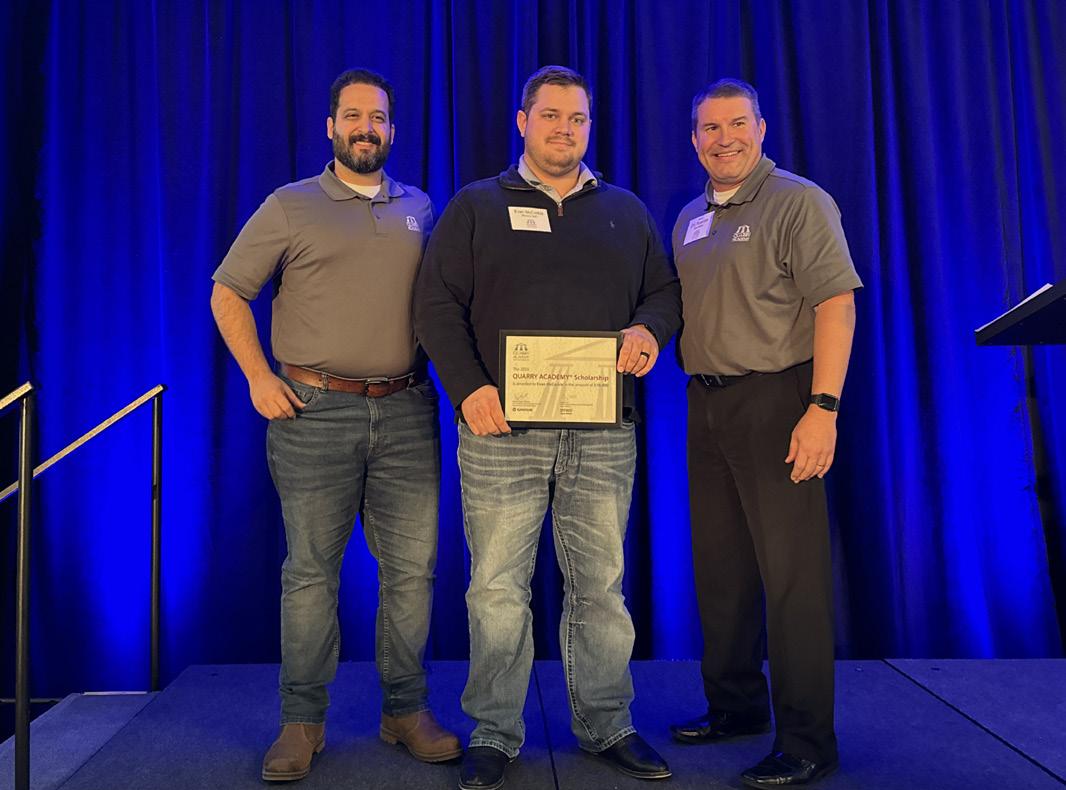
Academy scholarship: Evan McCorkle, a mining engineering student from the Missouri University of Science & Technology.
Raphael Carmona, VP Sales Area North America at Sandvik Rock Processing Solutions, says: “We are proud to support students like Evan. Our industry needs talent like his to keep building the foundations of this country in even more sustainable ways.
Attending the Quarry Academy seminar is a great way to learn more about the industry while building the bridge from education to the work world.”
More information: www.quarryacademy.com or virginia.varela-eyre@sandvik.com
New technical learning portal for service technicians
Global Technical Learning and Development is happy to announce the launch of a new learning management system aimed to support the global service technician community within Stationary Division.
The learning portal hosts engaging technical learning content in the form of e-learnings, webinars, instruction films and learning material, with more to come!
The global learning and development team is working to have the complete technical learning offer for service technicians available in one place over time. The content is downloadable and accessible even in remote locations via the learning management mobile app, all to support easily accessible learning for the service technician community. More information: helene.axelsson@sandvik.com

Security review for SRP shows great progress
Business area Sandvik Rock Processing Solutions (SRP) was recently part of an independent Sandvik-wide security review undertaken by Price Waterhouse Cooper (PWC). The results indicate that SRP has made very good progress in meeting its targets and has reached a more mature posture within the Group. We still have a lot of work to do and are currently assessing recommendations provided for the next steps in our maturity journey.
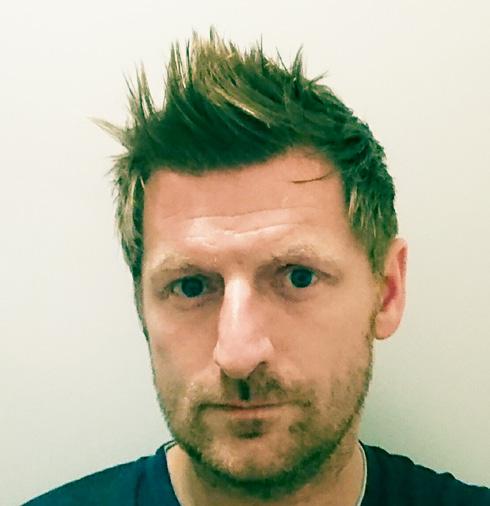
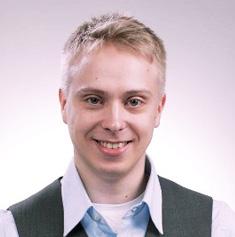
The SRP security team wishes to thank all the divisional speaking partners, system owners and teams that have helped us to achieve our goals in 2023, it’s very much a team effort and we should be pleased with the results. Let’s look forward to 2024 with the same level of collaboration and ensure we continue to make the improvements necessary to support and protect our business. More information: dean.mulley@sandvik.com
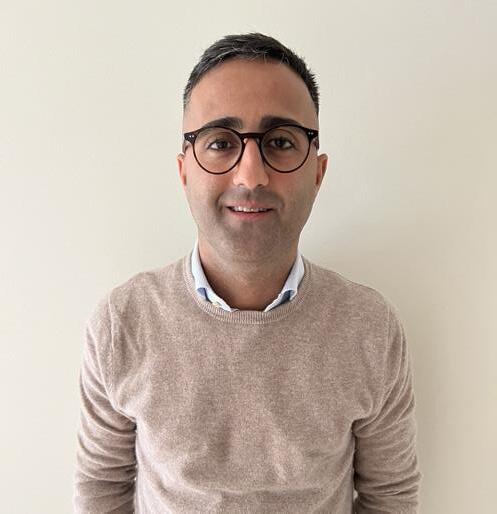
Welcome to our updated SRP IT intranet pages
Did you know that SRP IT has a dedicated area on the Intranet? Here you can find all of the latest; for example information about the SRP IT Role and Vision, who we are, what we can support with as well as information about our IT Strategy and how we work with Information Security. Link to the SRP IT page.
More information: maud.ekman@sandvik.com
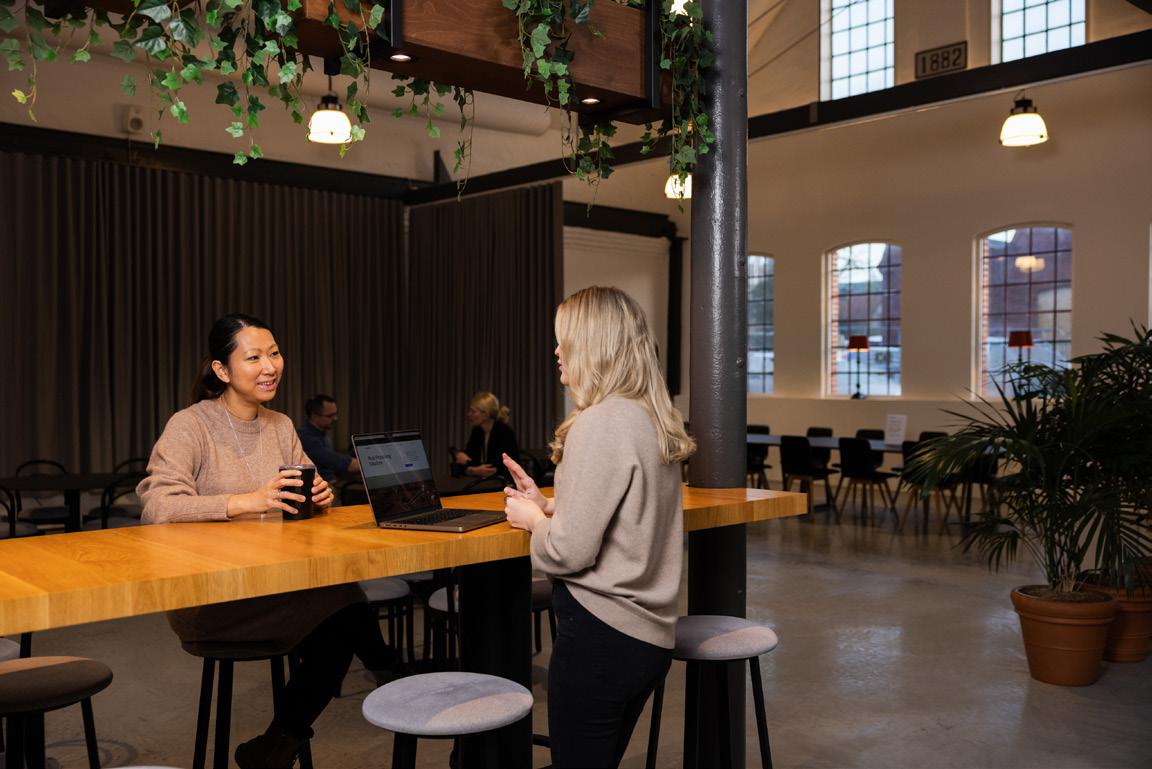
The Digital Shift Community (DISCO) Days is a global online event aiming to ignite Sandvik’s Digital Shift.
During two half days all Sandvik employees will have the opportunity to participate in a variety of sessions, including both internal and external speakers. Take the opportunity to learn about big trends in the digital field, and/or dive deep into specific technical matters during focused sessions.
Welcome to DISCO Days April 18-19 2024
One of the speakers during the event will be Pär Sikö, VP and Head of Digital Offering, Sandvik Rock Processing Solutions. He will talk about Lost in Data – Time for the next step, about data collecting and the challenges he sees. The event also covers, among other things, an interview with Stefan Widing about how AI is eating software as well as a keynote with research and advisory company Gartner about AI opportunities and threats. To sign up for the event and read more about the program, check out the intranet news that will be published March 21.
More information:
digitalshiftcommunity@sandvik.com
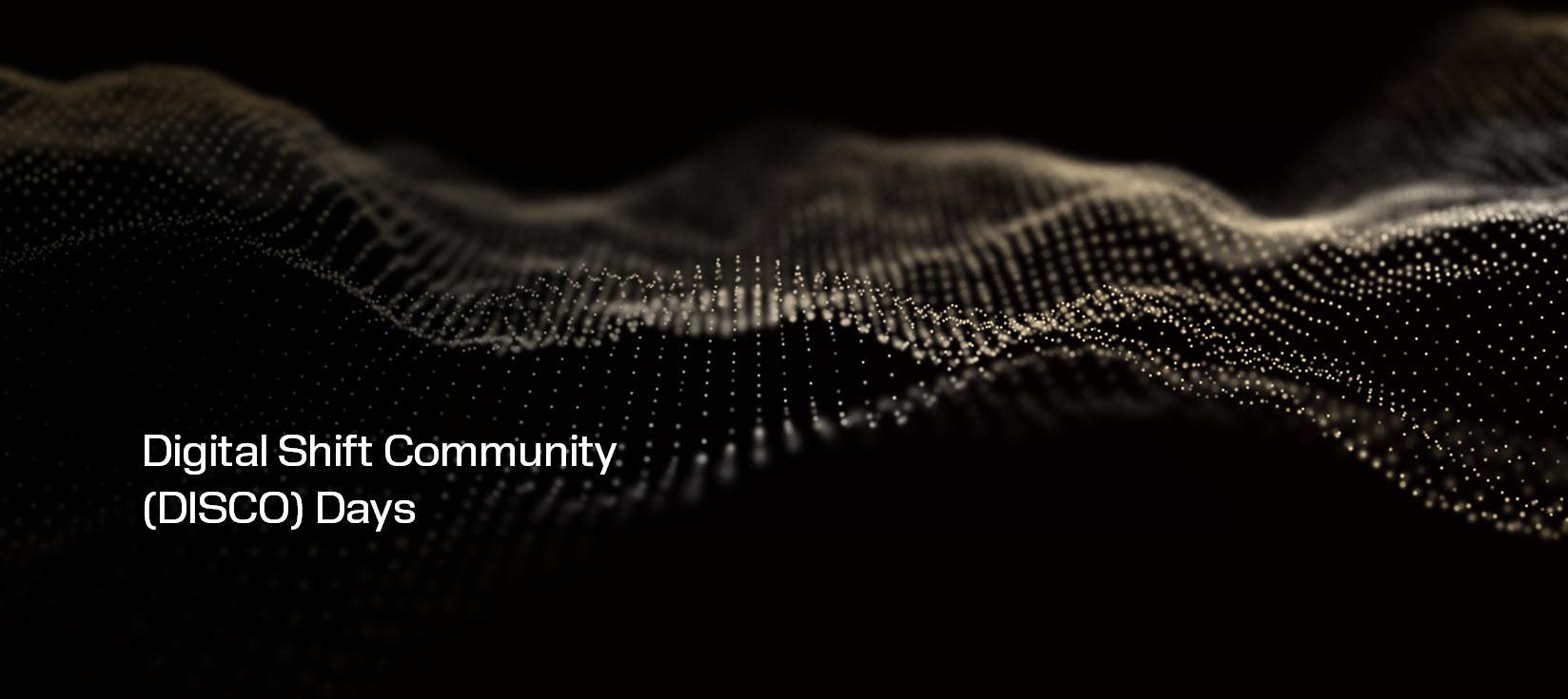
Sandvik Startup challenge 2023
The Sandvik Startup Challenge is a global opportunity for innovative startups to collaborate with Sandvik. In 2023 there were three different challenges available, and one was within Sandvik Rock Processing Solutions (SRP). SRP invited solutions to evolve “Enhanced industrial process insights” to drive plant efficiency and sustainability improvements.
The winner was Luxemburg-based startup Warden Machinery. They won the challenge with a solution based on cameras, sensors, and AI-enabled software for continuous monitoring of rock material. The next step in the challenge is to test the solution in our Dalby test plant in addition to running a Minimum Viable Product (MVP) project to test and validate the proof of concept at a customer site during 2024.
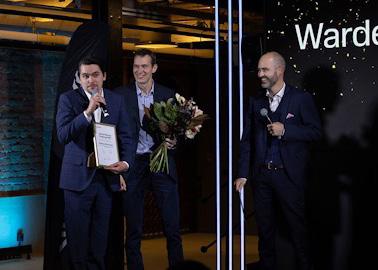
The challenge goal is to advance equipment insights with material flow monitoring between different equipment, leading to improved transparency. This can help customers in reducing their environmental footprint, improve operator guidance, and optimize production targets.
The Future vision is to capture the full potential of our customers production processes.
More information: Digital and Automation solutions, koushik.ravichandran@sandvik.com
Easier to find repair drawings with new Sharepoint functionality
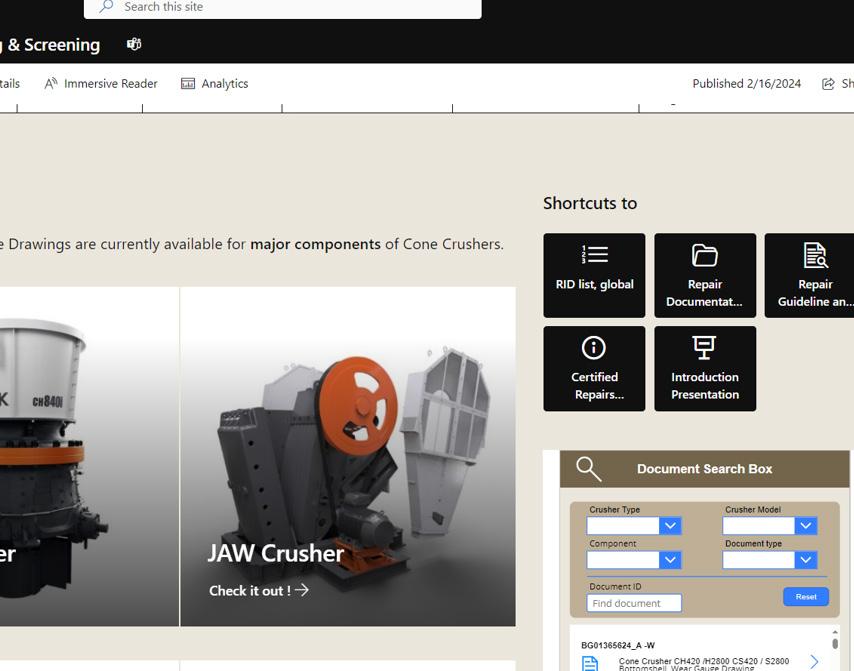
Certified Repairs is a sustainable and cost-effective part of Stationary Division’s service offering. We inspect and repair original components in our certified repair workshops, using Sandvik spare parts. The customers then receive the repaired components back with a repair warranty in as-new condition. One key enabler for selling and delivering this Service is the Sharepoint “Repair and Rebuild Stationary Crushing & Screening” where we manage all our technical repair documents including e.g., guidelines and repair drawings.
With focus on user friendliness and to improve our support for sales area colleagues and repair partners, there are now some new Sharepoint functionalities including:
• Overview tiles for each crusher with shortcuts to all valid instructions and guidelines, repair drawings and Sandvik standards
• Shortcuts to important lists, libraries, and views
• Document Search App, used to find specific documents
We have launched Certified Repairs for major components of cone crushers in South Africa, US, China, and Australia, aiming at increasing both the offering and the geographical reach in the coming years. More information: anika.kraemer@sandvik.com

SRP shines at EXCON in India
In December 2023 Sandvik Rock Processing Solutions (SRP) participated in the EXCON 2023 Expo, held in Bengaluru, India. EXCON is the largest construction equipment exhibition in South Asia, with more than 1,400 exhibitors and around 100,000 visitors. SRP participated together with business area Sandvik Mining and Rock Solutions (SMR), showcasing equipment and rock tools over a period of five days. EXCON gave an excellent opportunity to display the new brand identity of Sandvik and it got everyone’s attention!
SAM showcased
Also, for the first time ever, the CH660 Cone Crusher and SAM, our Connectivity solution were highlighted at EXCON. The team took our customers and dealers through the full journey, from alarms to analyzing trends to purchasing parts. We had the opportunity to showcase SAM to a wide array of potential users and gather their feedback. We have had handshakes and agreements with both dealers and end customers, addressing both the existing fleet and new crushers to expand the connected fleet. It has been truly inspiring to see your front line take over the booth, demonstrating the features of SAM and CH660 and tying it all to our digital user journey!
A quote from a customer that set the tone for EXCON “This is the new generation of crushing, and Sandvik is in the forefront of development.”
More information: ravi.arora@sandvik.com
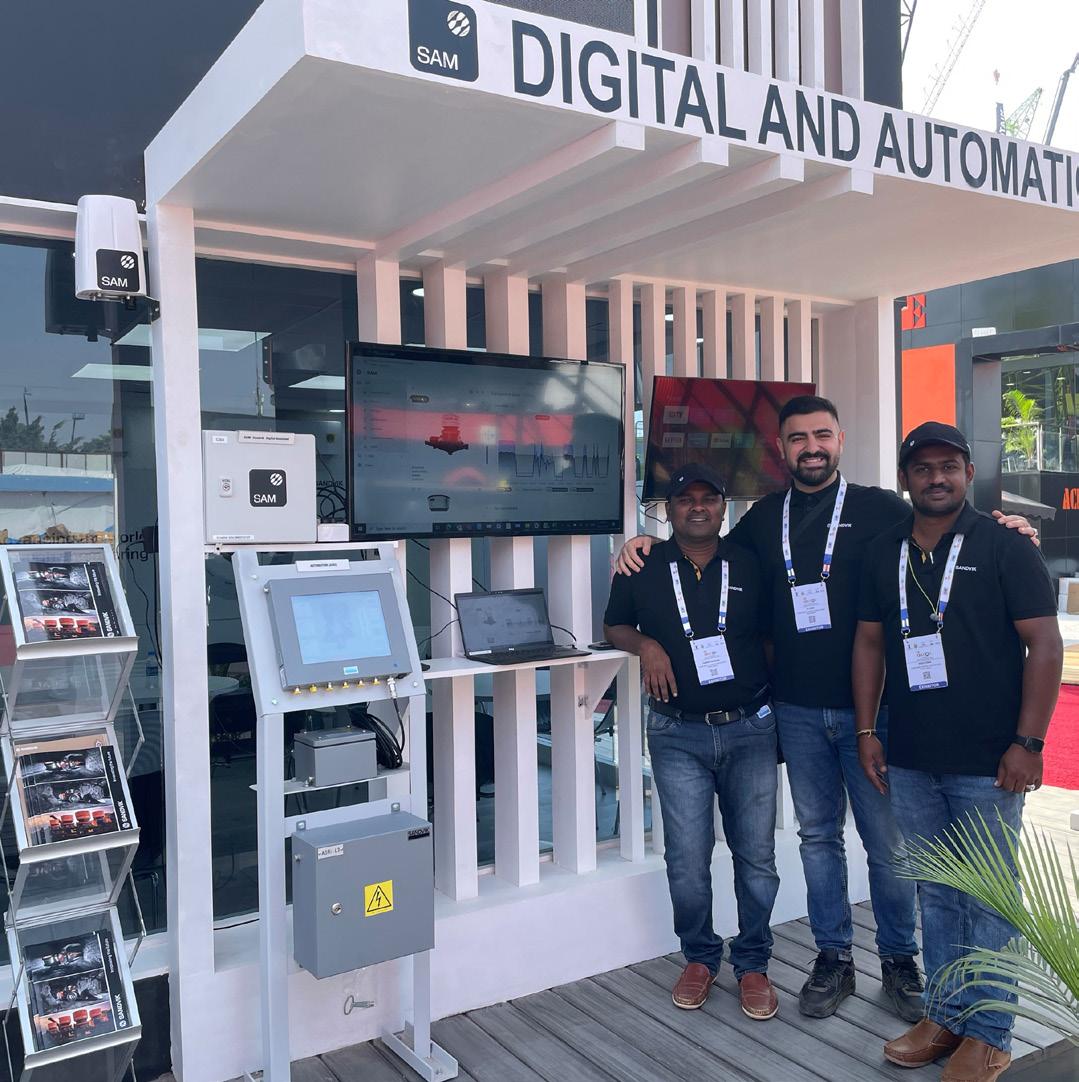
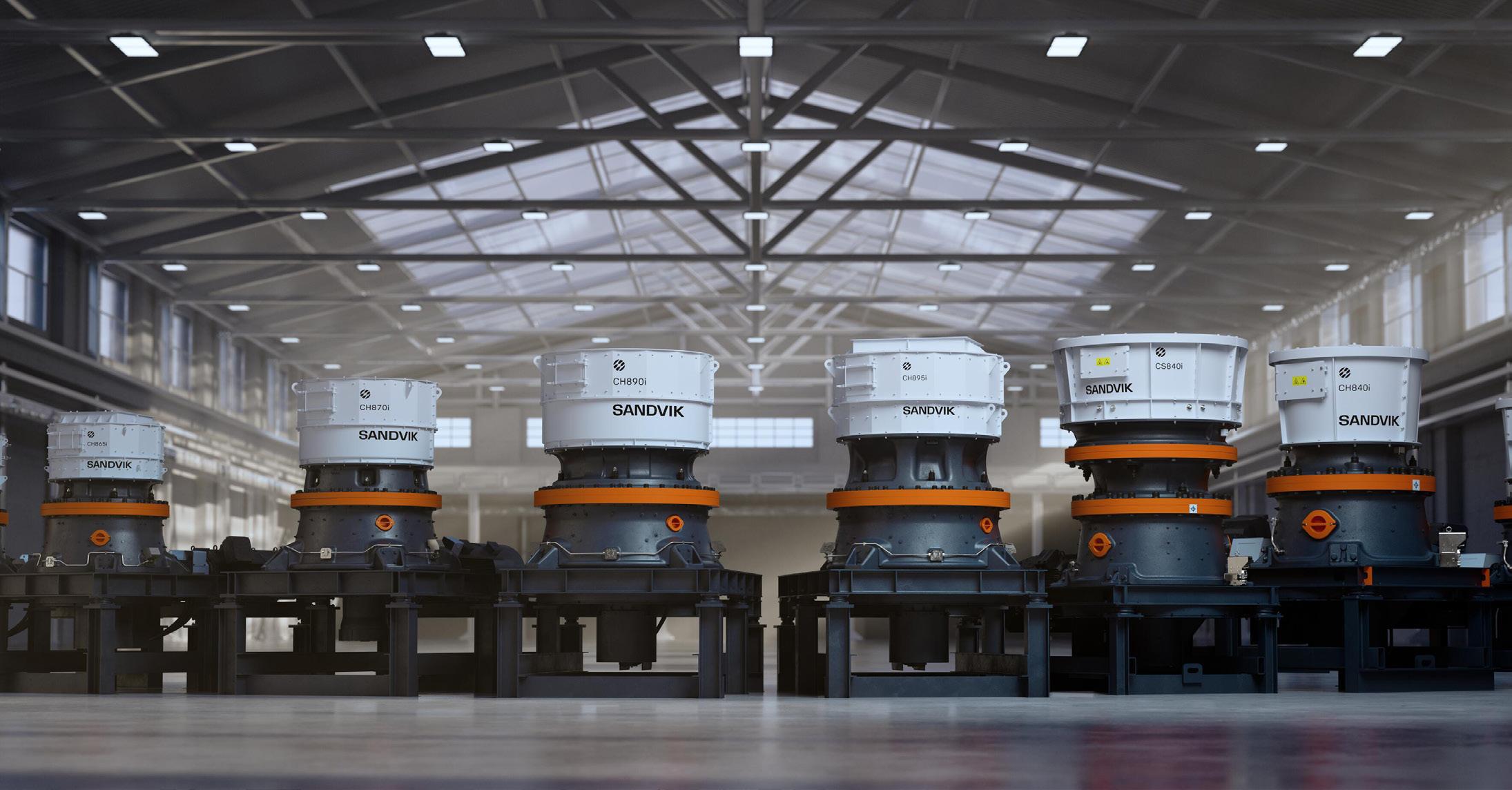
Launch of upgraded 800i cone crusher series
March 1, Stationary Division launched the upgraded 800i cone crusher series. It has new mechanical upgrades for increased reliability and uniformity, together with the new automation and connectivity system ACS-c 5.
“The upgraded 800i crushers are a natural next step in setting the bar for crushing. They have an ideal combination of high crushing forces, reliability, and simplicity, which make them easier to operate, manage, maintain and service than ever before. This in turn leads to productivity and uptime gains that are gamechangers for operational performance.” Javier Valdeavellano, Lifecycle Manager 800i cone crushers. 800i crushers target installed inefficiency in operating mines, as well as in greenfields. For example, in flowsheets including 3-stage crushing and conventional grinding, assisting SAG/AG circuits with pebble crushing, and optimizing particle size distribution for lump ores and
heap leach applications. The 800i crushers are also suitable in High Pressure Grinding Rolls (HPGR) circuits. They crush more and deliver finer particle sizes to the downstream processes.
Can be connected to SAM
All 800i crushers come equipped with the latest ACS-c 5 and are ready to be connected to SAM.
“As previously announced, we have added a new platform for our users. To enhance our user’s ability to monitor their equipment and thus gain insights regarding their operation, SAM has now been adapted to be used on Smartphones. This allows our users to monitor their fleet, view equipment data & insights, alarms, access manuals and much more, wherever they are.” Ali Jumaa, Digital Solution Specialist.
More information: javier.valdeavellano@sandvik.com, rockprocessing.sandvik/smartcrushing
Sales Area North America (Stationary Division) hosted its biannual dealer meeting on January 31 – February 1, 2024, in Florida, USA. The event was attended by all dealers in the sales area.
The meeting was held under the slogan Delivering Value Together. The Sandvik team presented updates on the division and the Sales Area, on product development, logistics, aftermarket, including parts and warranty, digitalization, marketing and training. In the spirit of the partnership with distributors, the speakers encouraged interaction, including perspectives on market outlook and product discussions during the three workshops in the program.
Raphael Carmona, VP Sales Area North America, says: “This year’s meeting has proved extremely successful. These opportunities are invaluable for us. We get to present our latest updates and our network provides us with feedback on how to better serve customers: product design, training needs, etc. Dealers highly value the opportunity to exchange ideas with other distributors. We had the highest turnout this year, which may have been a factor on the excellent quality of discussions during the two days.”
To ensure participation, the meeting format, including content, location, duration and communication considered feedback received beforehand and from previous events. Equally, future gatherings will consider input received from both dealers and the Sandvik team.
More information:
virginia.varela-eyre@sandvik.comSA North America hosts largest ever dealer meeting
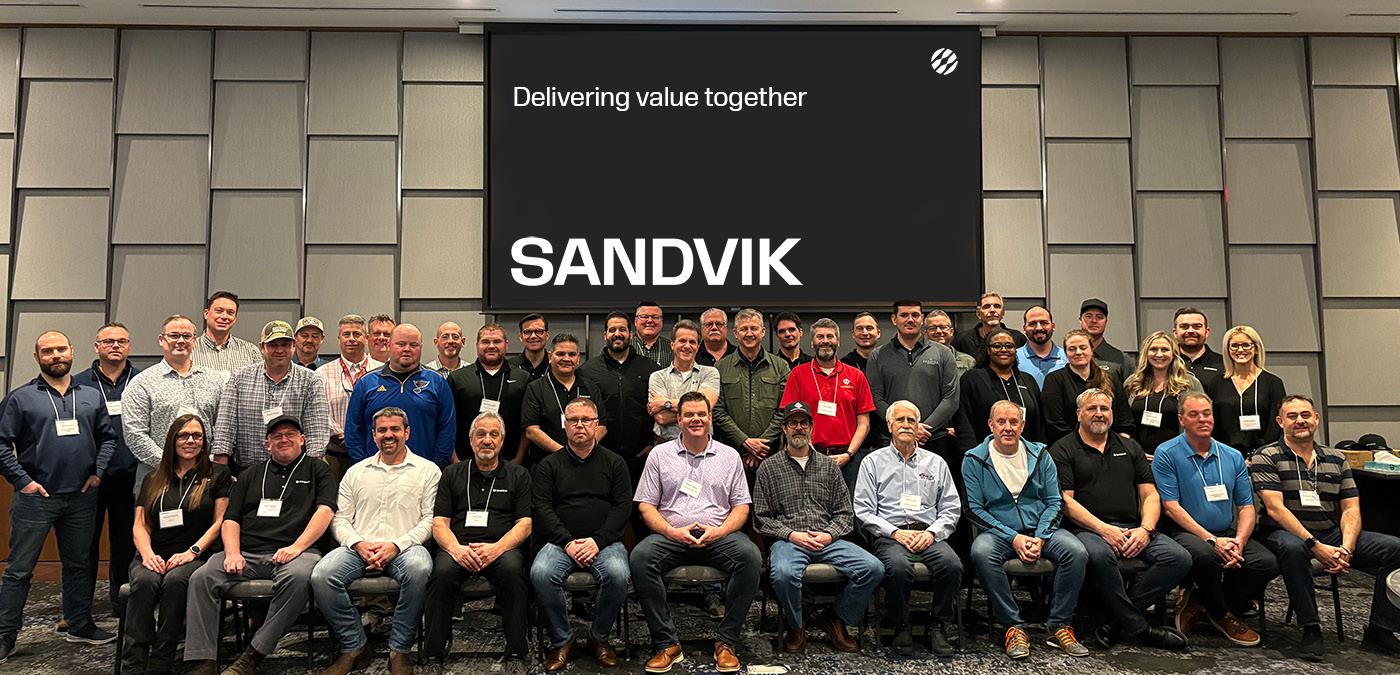
Magnetic drum separators on QA screen range
The Mobiles’ team has launched its first product of 2024, magnetic drum separators for the QA screen range.
The magnetic drums were designed specifically for recycling applications and can be retrofitted to Sandvik mobile screens to remove ferrous metal within the feed material. Unwanted ferrous metal particles can be collected and turned into a valuable sellable product for metal recycling.
More information: melissa.baker@sandvik.com
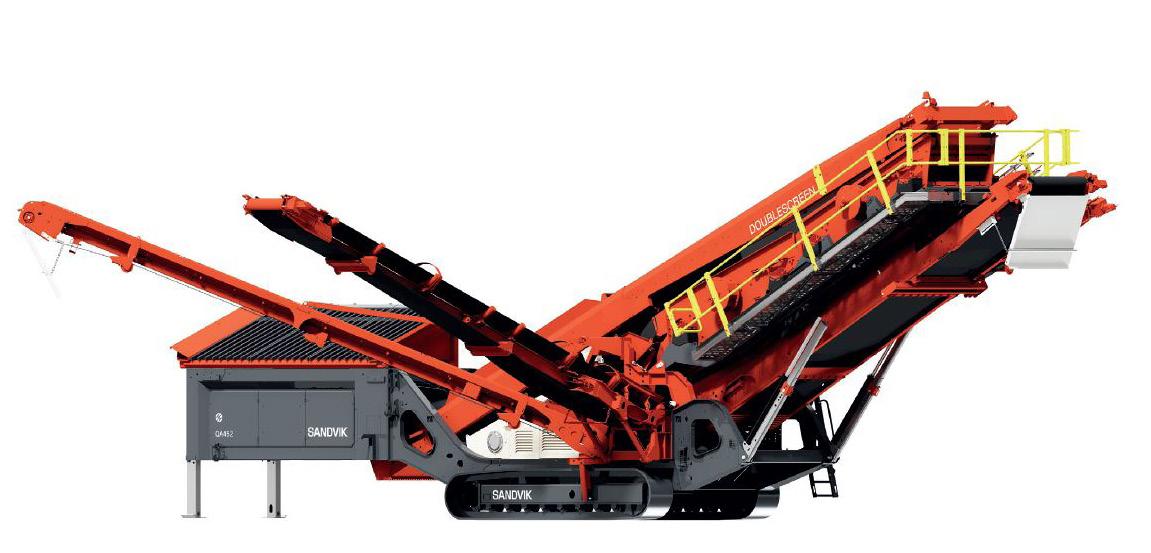
SRP Annual Meeting in Brazil
Our SRP Latin America (Stationary Division) annual meeting in Brazil served as a moment for reflection, evaluation, and strategic planning. We took stock of the achievements of 2023 and charted the course for 2024.
Our commitment to people and the environment remains at the forefront of our mission. As a company, we are dedicated to providing increasingly sustainable solutions for the mining and construction markets. Brazil, with its vast mining potential, holds a special significance in our global operations.
During our meeting, we showcased comprehensive crushing and screening solutions that contributes to the advancement and excel-
lence of the industry. These solutions not only meet the demands of the market but also align with our vision of responsible and sustainable development. We also reaffirmed our dedication to innovation, excellence, and environmental stewardship. Through collaboration and strategic partnerships, we aim to continue driving progress in the mining and construction sectors, both in Brazil and other Latin American countries.
Together with our team in Brazil, we look forward to another year of growth, achievement, and sustainable impact. Thank you for being part of our journey.
More information: cristiane.fontes@sandvik.com
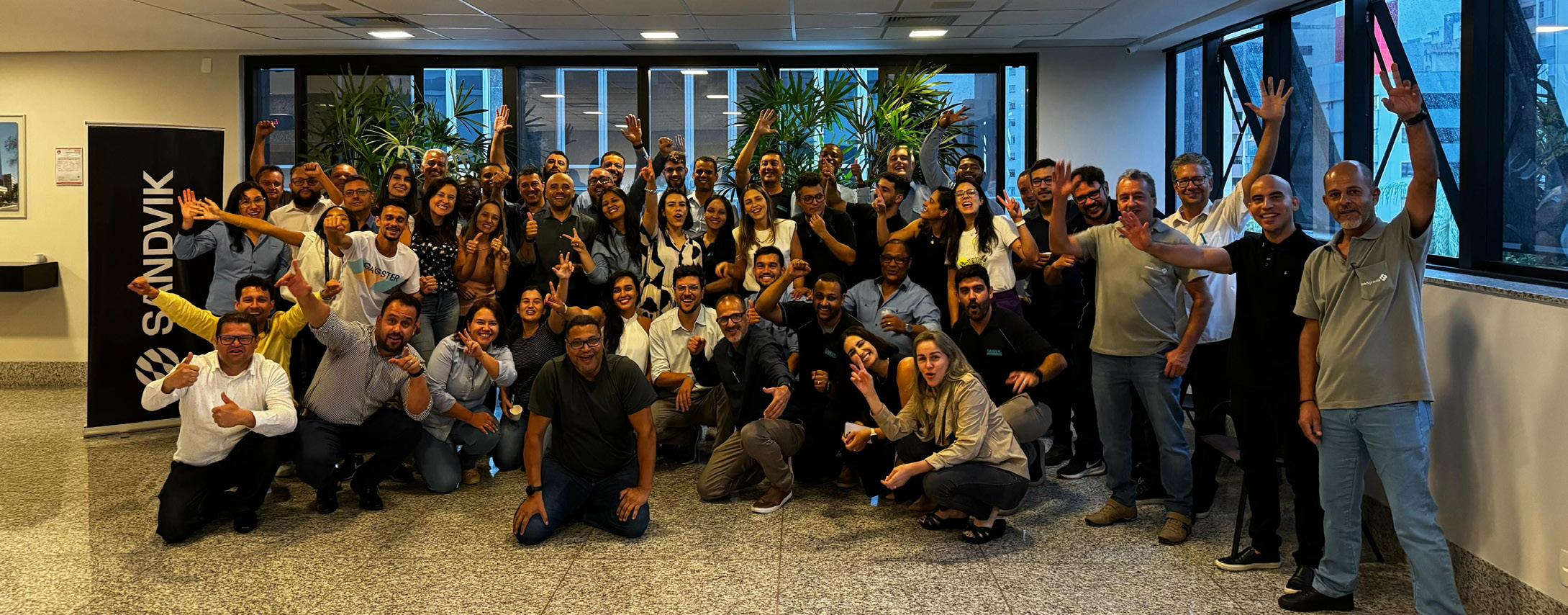
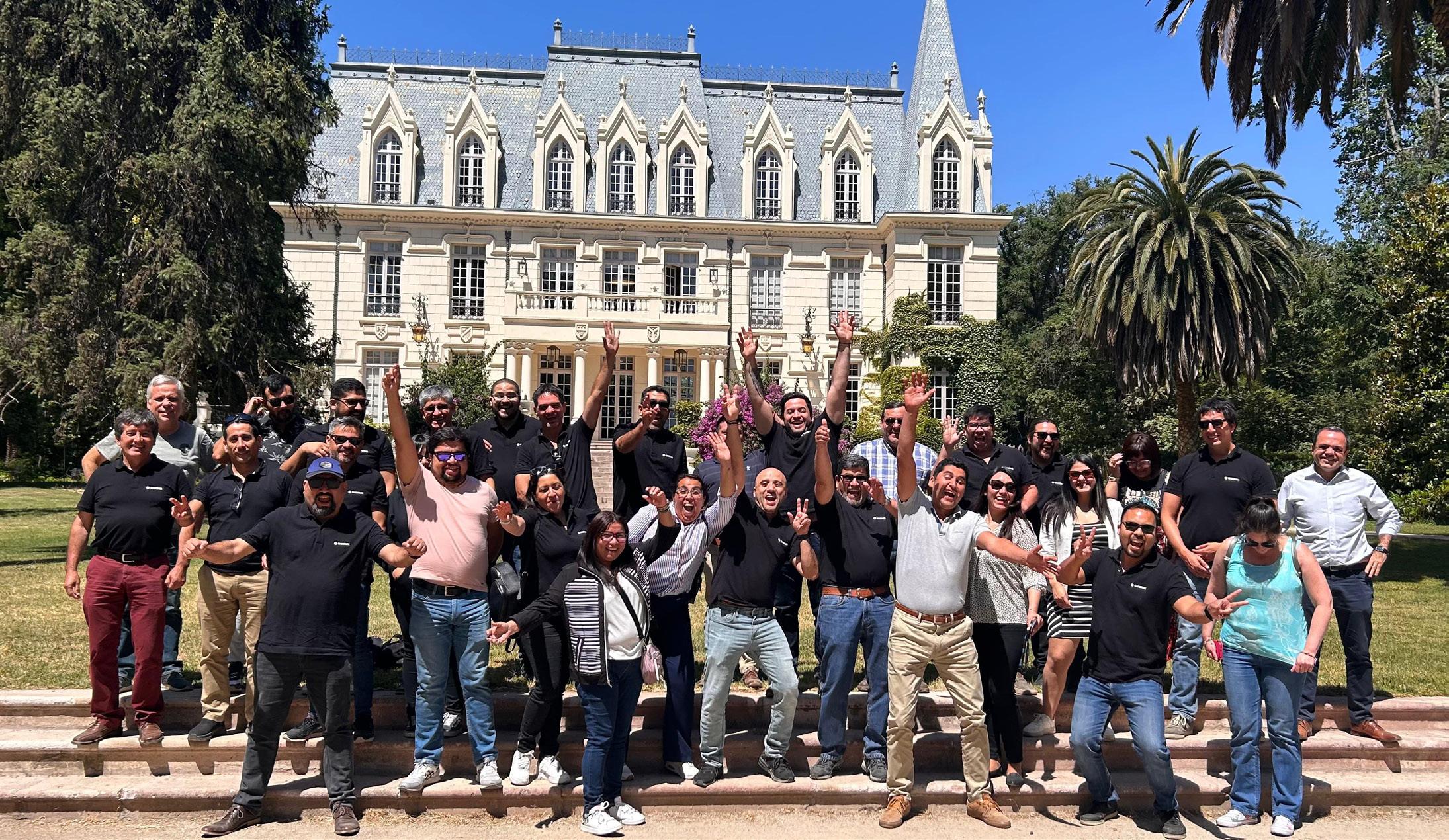
Annual Meeting with the Chilean Sales Team
In December, our dedicated sales team in Chile (Stationary Division) gathered to celebrate the achievements of 2023 and to plan for 2024. The meeting started with a joint lunch followed by team-building activities that promoted collaboration, communication, and unity among the team members. Through team building, we strengthened our bonds and renewed our commitment to achieving shared goals.
As we discussed plans for the upcoming year, there was a true sense of excitement and determination to make 2024 a success. We explored strategies, set ambitious targets, and reaffirmed our dedication to providing exceptional service and solutions to our clients in Chile.
The meeting served as a powerful reminder of the strength and talent within the sales team, as well as the potential for growth and achievement that lies ahead.
With the integration of Schenck, we’ve become a more complete team, and everyone plays a pivotal role in this achievement. Together, as one unified Sandvik family, we will soar to new heights in the mineral processing industry. We extend our heartfelt gratitude to each and every one for contributing to our success story. Here’s to a future filled with collaboration, innovation, and success! More information: cristiane.fontes@sandvik.com
US dealer expands territory
Eltrak Bulgaria Ltd. has been appointed as new distributor for Sandvik Paschal Associates is a long time Sandvik distributor of stationary crushing equipment, parts and services in the USA for the states Maryland, Georgia, the Carolinas, and the Virginias. Now the company will also be serving customers in Florida. Paschal Associates, Ltd has been a leading provider to the aggregate and mining industries since 1956. According to Paschal Associates there is great opportunity to service the Florida producers with a focus on engineered products to improve production efficiencies and improve end product quality.
More information: virginia.varela-eyre@sandvik.com
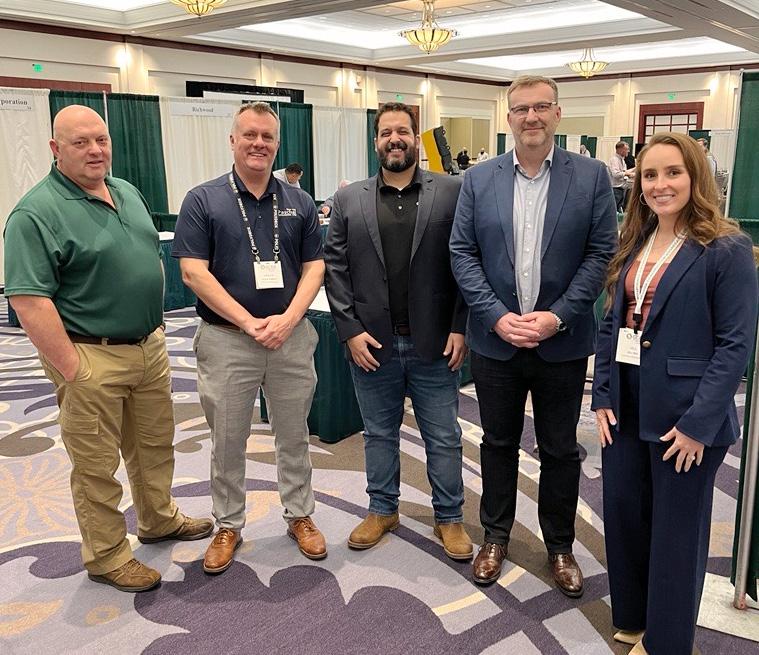
New distributor in Bulgaria
Eltrak Bulgaria Ltd. has been appointed as new distributor for Sandvik SRP SEMEC, Balkans territory, in Bulgaria.
Eltrak Bulgaria is a dealer of leading global brands such as Caterpillar and is committed to providing efficient and reliable solutions for construction and mining needs. The company’s extensive network, with headquarters in Sofia and additional trade and service centers in Burgas, Varna, and Stara Zagora, ensures comprehensive coverage and support for customers throughout the country.
The partnership also includes technical service delivered directly to customers’ job sites, through over 42 mobile service units which cover the entire territory of Bulgaria. This reinforces Sandvik’s commitment to enhancing customer support.
The distributor agreement was formally signed in January 2024. We look forward to the positive impact of this partnership on Sandvik SRP SEMEC’s business in Bulgaria. Welcome to the Sandvik family!
More information: gaia.laquay@sandvik.com
Mobiles division extends distributor agreement
Mobiles Division extends its dealer agreement with Retec Equipment Limited to now cover the whole of the UK and Ireland territory. Retec is a premium supplier and reseller of specialist equipment in the recycling and quarrying industries, with more than 40 years’ expertise in the industry.
Sandvik has successfully been working with Retec for the sales of its mobile crushing and screening range in the UK since 2021. Initially appointed for the London and South-Eastern counties, Retec has established an excellent foothold in the industry and developed the Sandvik business in these Southern counties over the past few years.
More information: andrew.haldane@sandvik.com
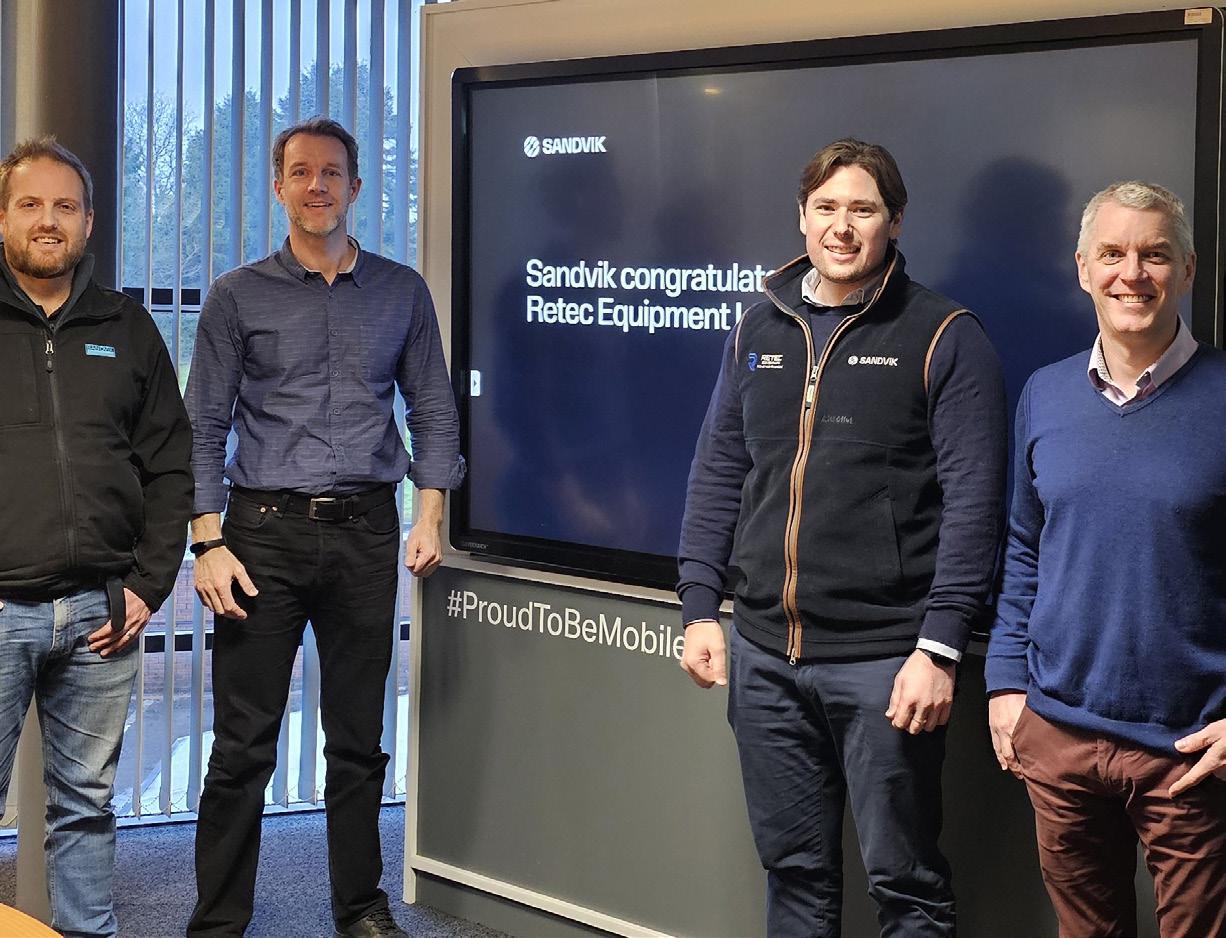
New distributor in Poland
Mobiles Division recently announced the appointment of Volvo Maszyny Budowlane Polska as its new distributor in Poland. The company will be responsible for selling Sandvik mobile crushers and screens in combination with full aftermarket support through the supply of spare parts and local customer service. Established in 2004, Volvo Construction Machines Poland is based in Młochów and has become a leading supplier of construction equipment in Poland. With over 200 employees, the company is well established across the country with 100+ service technicians located across four regional and six local branches.
More information: andrew.haldane@sandvik.com
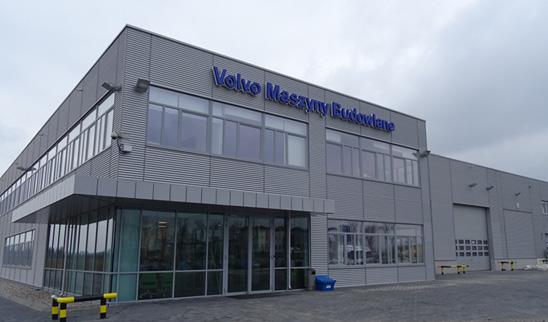
Dealer and customer visits to N. Ireland
The Mobiles’ team in Northern Ireland welcomed the Finnish sales area team alongside a number of customers in January to view the new UJ443E heavy jaw crusher. The team travelled to a site where they were able to see our recently launched heavy jaw crusher, the UJ443E, working alongside our hybrid QA452e Doublescreen. The team also welcomed distributors Volvo Poland (Poland), Retec Equipment (UK & Ireland) and AFOI Malliaropoulos (Greece) to our site in Ballygawley in January and February. More information: james.murray@sandvik.com
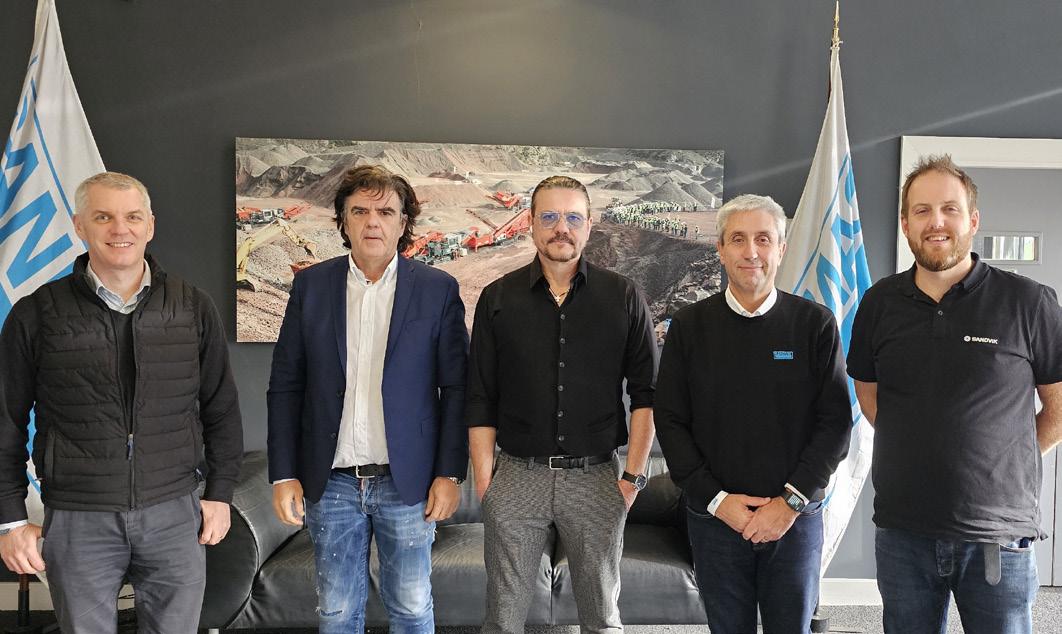
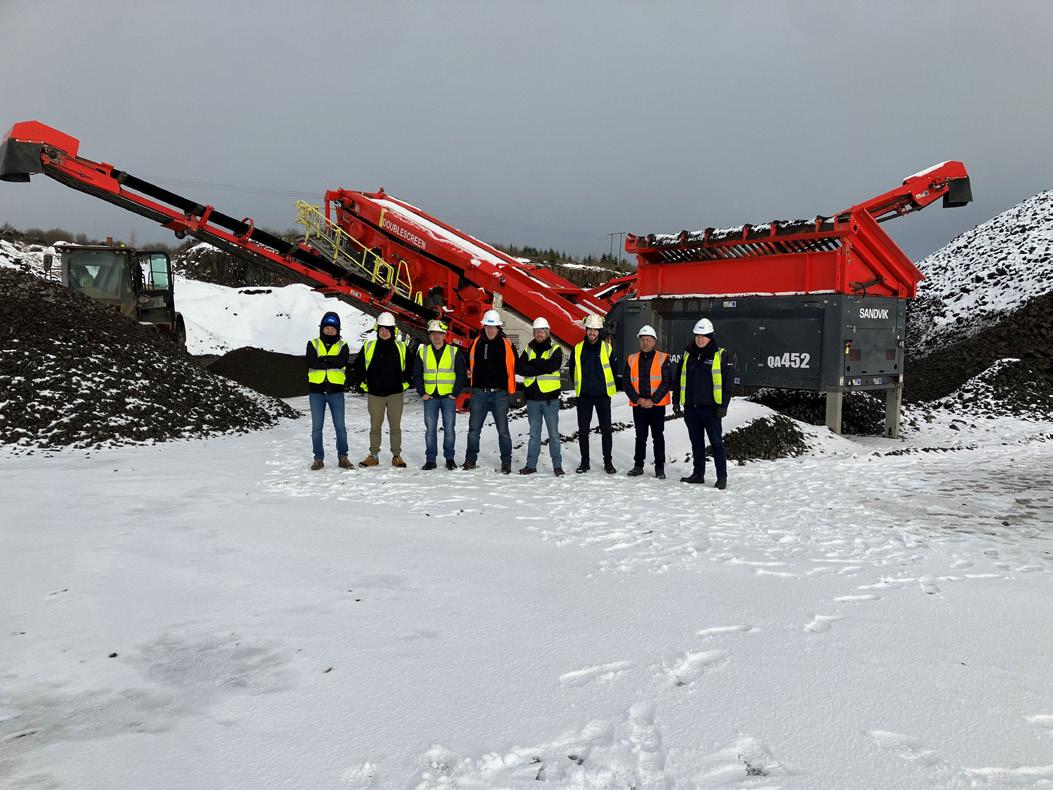
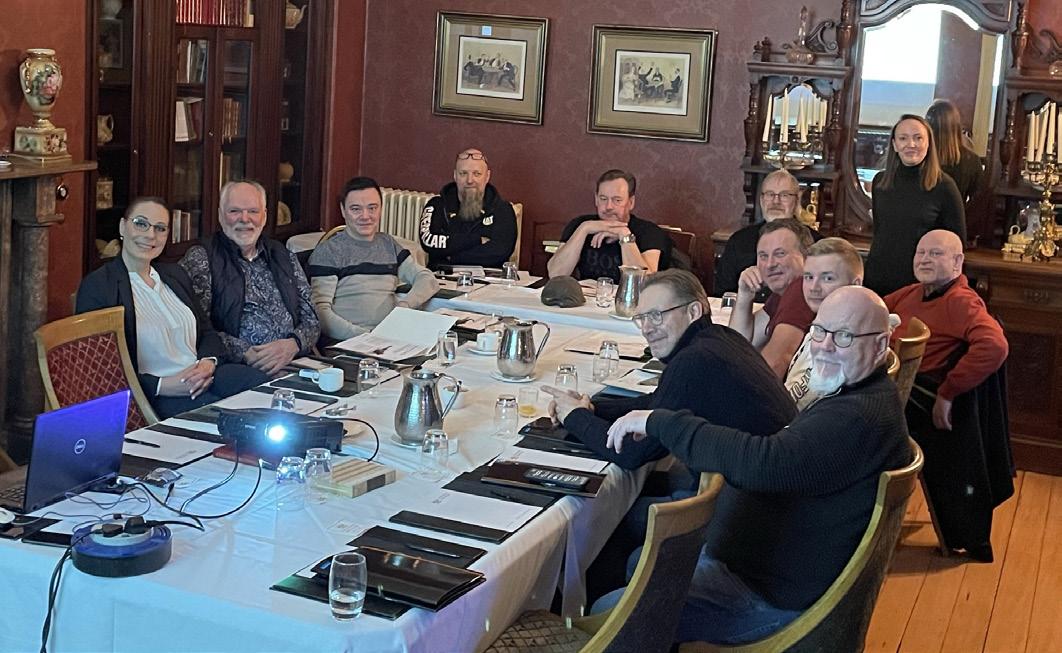
Mobiles new ERP system goes live
In February, Mobiles Division implemented its new Enterprise Resource Planning (ERP) system. The new ERP system will improve the overall operating efficiency within the business and help support our future growth. The team has worked hard to implement this system over the last number of months, and we would like to extend a big thanks to everyone for their hard work and dedication in getting the project over the line.
More information: brian.quinn@sandvik.com
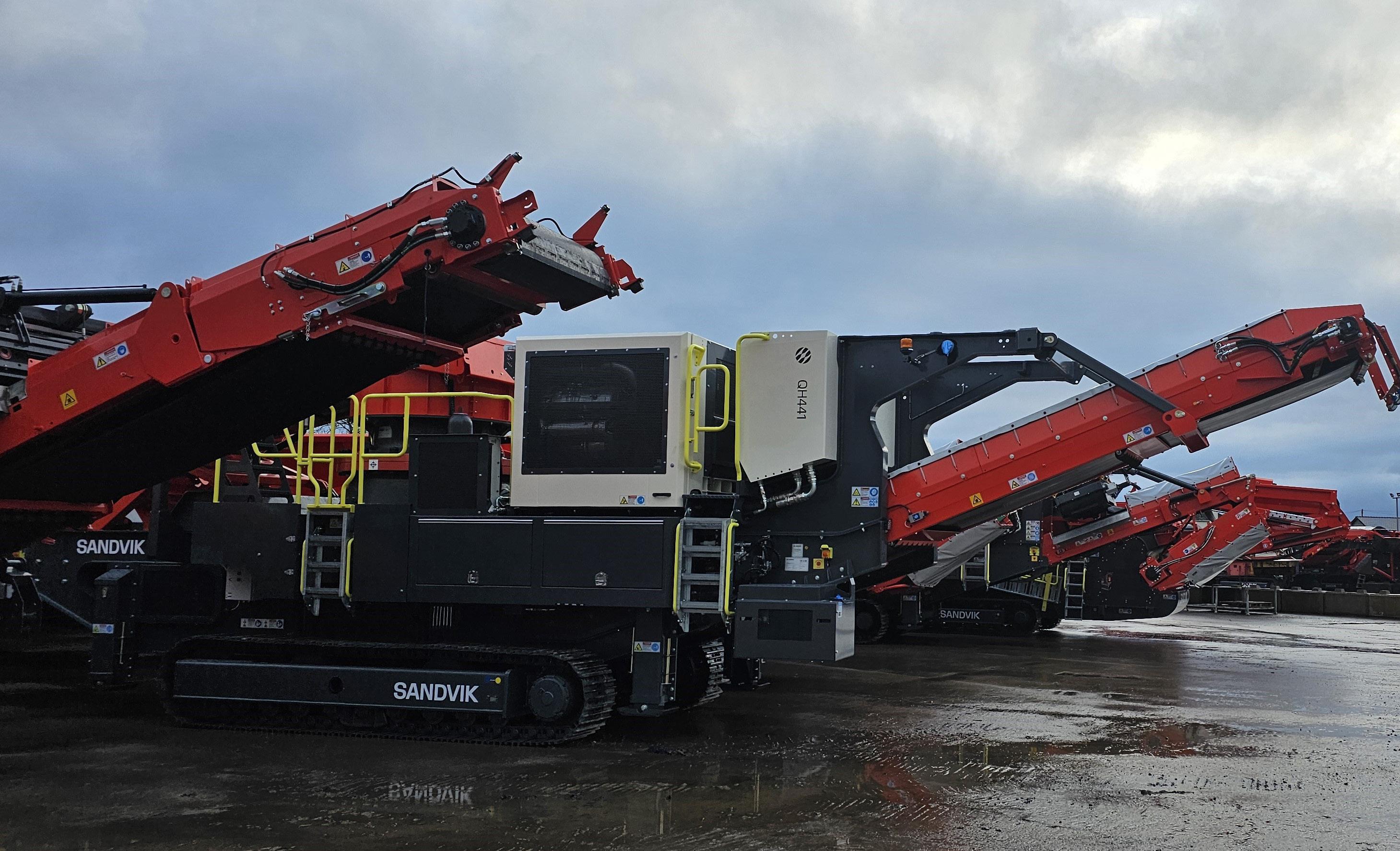
New brand identity across full product range
On March 1st 2024, Mobiles Division began rolling out our new brand identity across the full equipment line. Our new branding has already been implemented on our newly released products, the first being the UJ443E heavy jaw crusher. But we are delighted to be able to share some images of the new identity across the full range of mobile crushing and screening equipment.
More information: michelle.donnelly@sandvik.com

Mobiles’ attends Future Minerals Forum
Mobiles Division joined Sandvik Mining and Rock Solutions (SMR) and other SRP team members at the Future Minerals Forum in Riyadh in the Kingdom of Saudi Arabia. SMR and SRP had a joint venture on the Business Sweden Pavilion stand alongside other Swedish organizations. The team was invited to attend the Swedish Embassy for a welcome evening and also able to meet organizers of the Sweden Pavilion and hear from other attendees. We also took the opportunity to meet with our dealer MEDCO and discuss their strategy for 2024.
More information: kamran.akram@sandvik.com
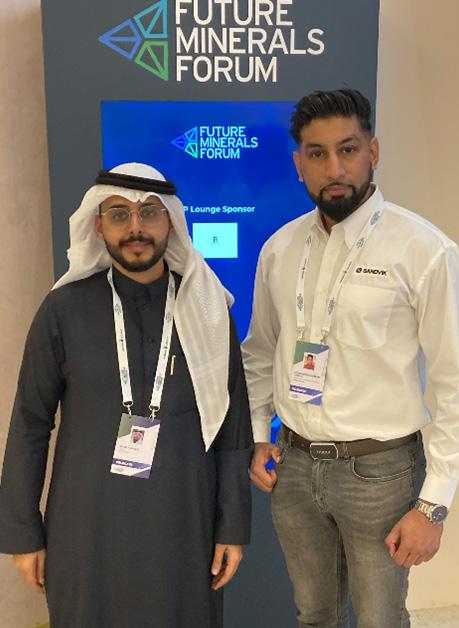
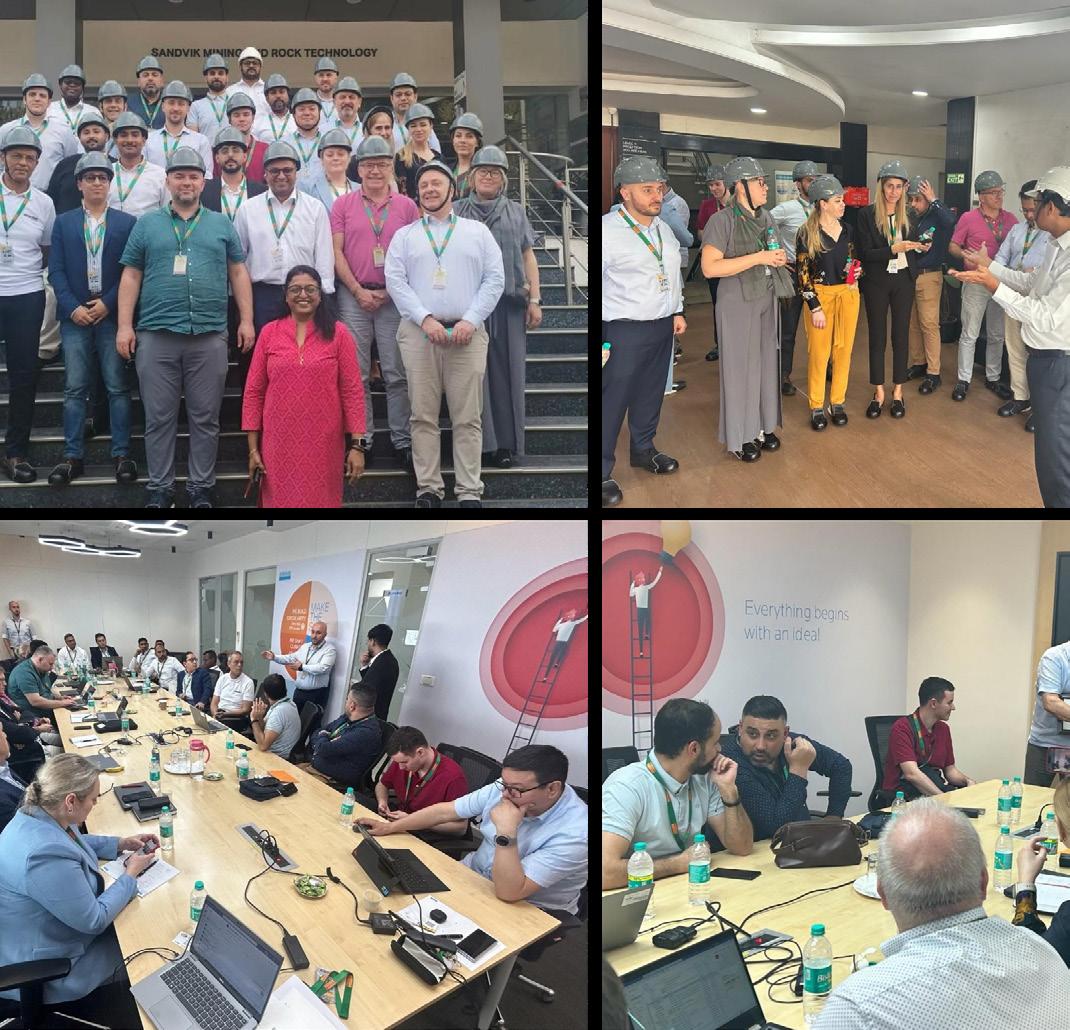
Successful distributor event
At the beginning of March our SEMEC team (Stationary Division) had a great meeting with its distributors in Pune, India. The visit included a factory tour and a lot of good productive discussions and team building activities. The meeting did not only strengthen the relationships with our valued distributors, but it also highlighted the mutual success we’ve achieved together. Here’s to continued collaboration and future accomplishments!
More information: gaia.laquay@sandvik.com
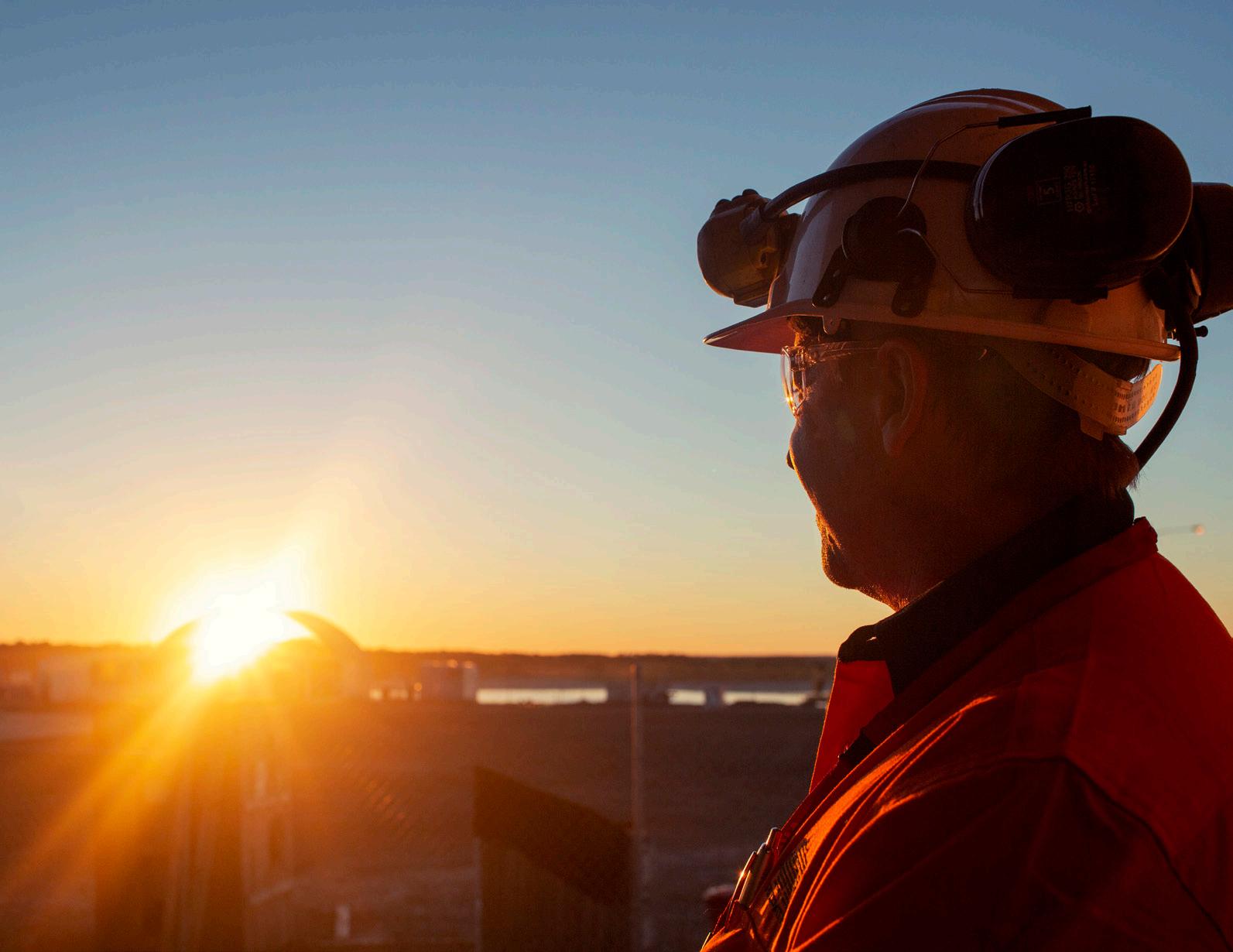
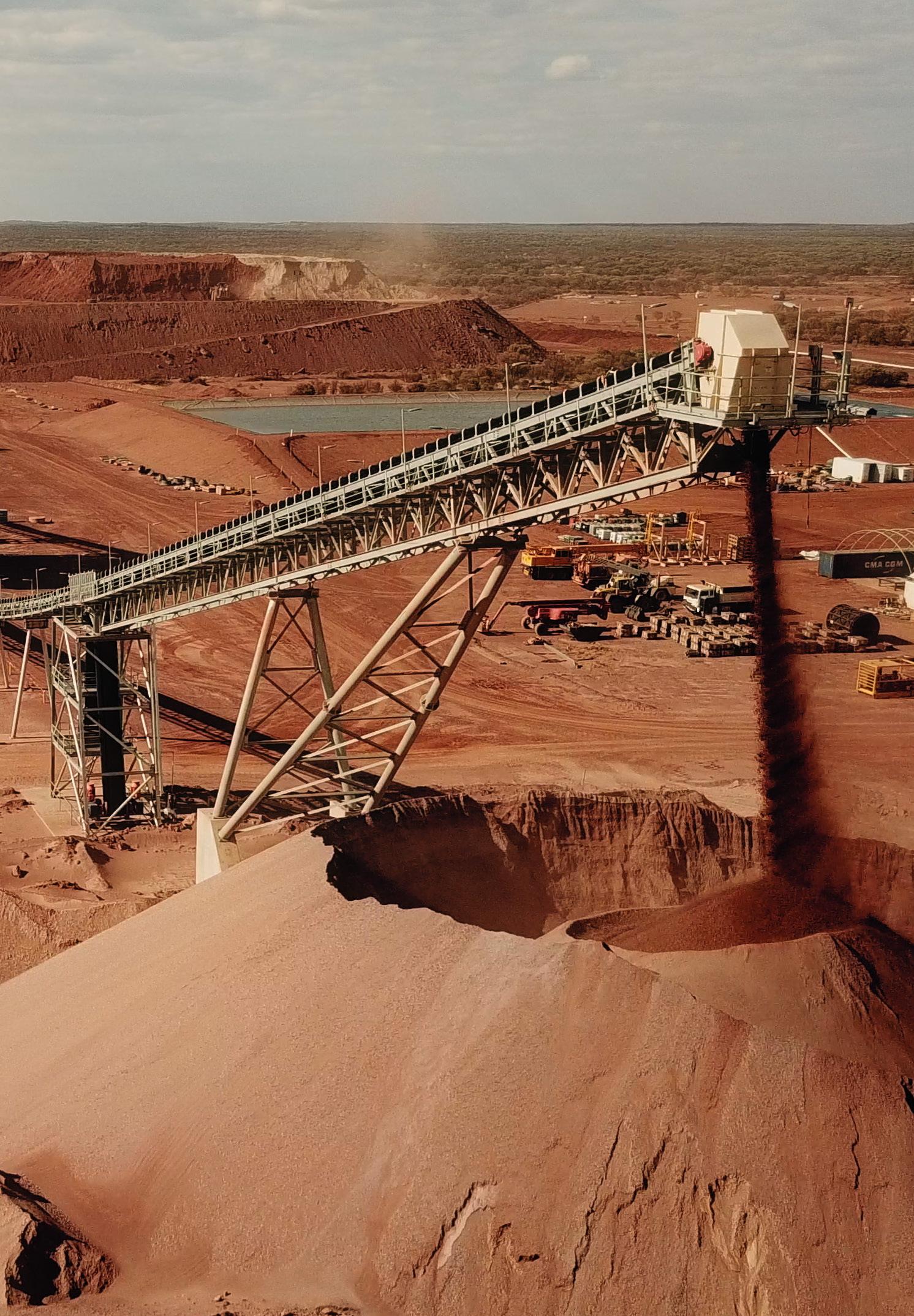