

Our SRP
Sandvik Rock Processing Solutions
WELCOME
Dear colleague,
Welcome to a brand-new issue of our business area newsletter, where we aim to give you a short overview of the activities and achievements that we accomplish together - world-wide - here at Sandvik Rock Processing Solutions (SRP).
Our updated strategy
You have probably seen by now that we have updated our business area (BA) strategy (page 7). The BA strategy is interlinked with the division strategies and in it you will recognize strategic objectives from all of our divisions. On our intranet strategy pages you will find a lot of useful information about the new strategy, including some presentation material. I can also recommend you to take a look at the strategy calendar that was published daily during May. The calendar gives you bite-size information about the BA strategy, with examples and short videos explaining the different elements. I encourage you to discuss in your team how your strategy and objectives support the overall goal.
Safety
We have been on a good track as regards LTIs (Lost Time Injuries), but in April unfortunately 3 Lost time injuries occurred (Stationary Jandakot Australia, ATD Cleveland US and Sales Area Northern Europe Sweden) and 3 Restricted Work Injuries. The Hazardous close out ratio has increased slightly, which is good, but is still not reaching the 95 % target. I want to repeat that it is crucial to continuously improve the reporting of hazards. And equally important that we implement preventive and corrective actions based on the investigation findings!
We have now entered June, with the annual vacation period coming up in the northern hemisphere. I will get back in July, after the Quarter 2 report, with a Words from the President and a short video that replaces the Q2 webinar. Until then, thank you for all your hard work and efforts this first half of the year. And, most importantly, make sure to enjoy some well-earned relaxation if your vacation is approaching.
Stay well and stay safe.
Richard Harris, President Sandvik Rock Processing Solutions
In
Safety innovation in Brazil ..............................................
Continuous improvements in Cleveland.....................
Five accident-free years in France...............................
Health promotion activity in China................................
Celebration of National Safety Week in India...........
Language fika in Sweden ...............................................
EHS Recognition Scheme.................................................
Remonte Monitoring Services........................................
Have you seen the updated SRP strategy.................
Poised to complete the SP Mining integration.........
New demand process for IT requets............................
Increased order intake on impactors...........................
S-range expanding to replacement business...........
Jaw crusher sales to new heights.................................
ATD present
Recycling projects in Mexico...........................................
Rio Tinto supplier recognition.........................................
Conecta for customer events..........................................
Dealer and customer visits in Ballygawley.................
Partner Takraf visits the Jandakot facilities..............
Publisher: Conny Rask Editor and production: Åsa Myers asa.myers@sandvik.com
On the cover
The first Sandvik branded SP Mining screen to leave our Jandakot (Stationary Division) workshop in Western Australia, Read more on page 8.
Safety innovation in Brazil
A working at heights risk was identified in the assembly area of the Taubate production unit in Brazil (Stationary Division). Due to the nature of the tasks carried out at height, a standardized safety solution was not suitable for addressing this risk in a sufficient manner.
In March, the EHS team at our Taubate factory in Brazil implemented a safety device to enable employees in the assembly area to carry out their work activity at height safely. The purpose of this device is to mitigate the fall from heights risk for any activity carried out above 2 meters from ground level. The safety mechanism will engage to prevent injury, should there be an accidental fall or trip.
The device is easy to use on different work fronts and comfortable for the employees. Its height can vary between 4.5 and 6 meters, thus meeting all our needs. The safety review of the device and its operation were verified and validated by an external engineering company.
To know more, please contact andre.santos@sandvik.com or arley.fernandes@sandvik.com.
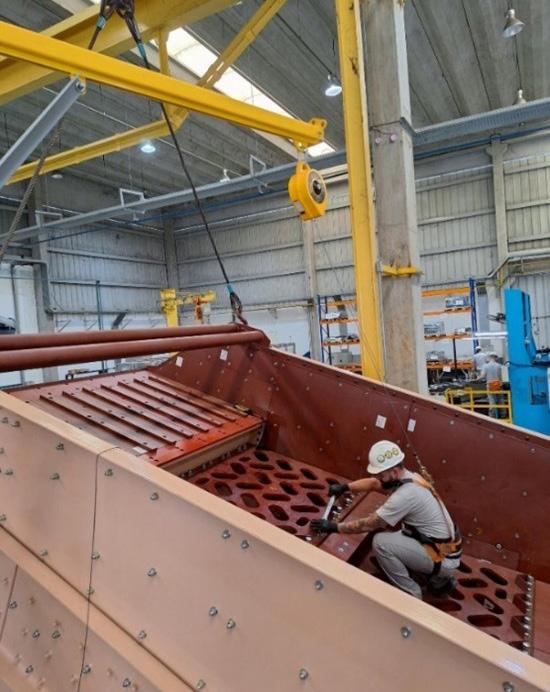
Continuous improvements in Cleveland
Attachment Tools in Cleveland (USA) embarked on a journey of continuous improvement in 2023. The initiative involved curating a list of 100 improvement opportunities, both big and small. The primary goal was to foster a culture of innovation and enhance organizational awareness regarding the positive changes and achievements within our ranks.
To date, we have successfully logged 109 improvements. A few notable examples include:
• New digital evaluation forms for our Renewed and Certified hammer program, streamlining the assessment process.
• A completely revamped CNC (computer numerical control) manufacturing approach for a critical part, resulting in a remarkable increase in output — from 2 products per day to an impressive 18 products per day.
These efforts reflect our commitment and dedication to driving meaningful progress across the organization. More information: mikael.k.larsson@sandvik.com
5 accident free years in France
SRP in France (Stationary Division) is proud to announce five accident-free years. This achievement testifies to our commitment to continuous improvement, underpinned by a strong health and safety culture and the sharing of best practices. This requires active involvement at all levels of the company, with the participation of every employee.
Our warmest thanks go to all SRP France employees for their contribution to this important milestone. As we celebrate our accident-free fifth anniversary, our main objective remains to maintain a risk-free working environment for all. More information: pricilia.mbongo@sandvik.com
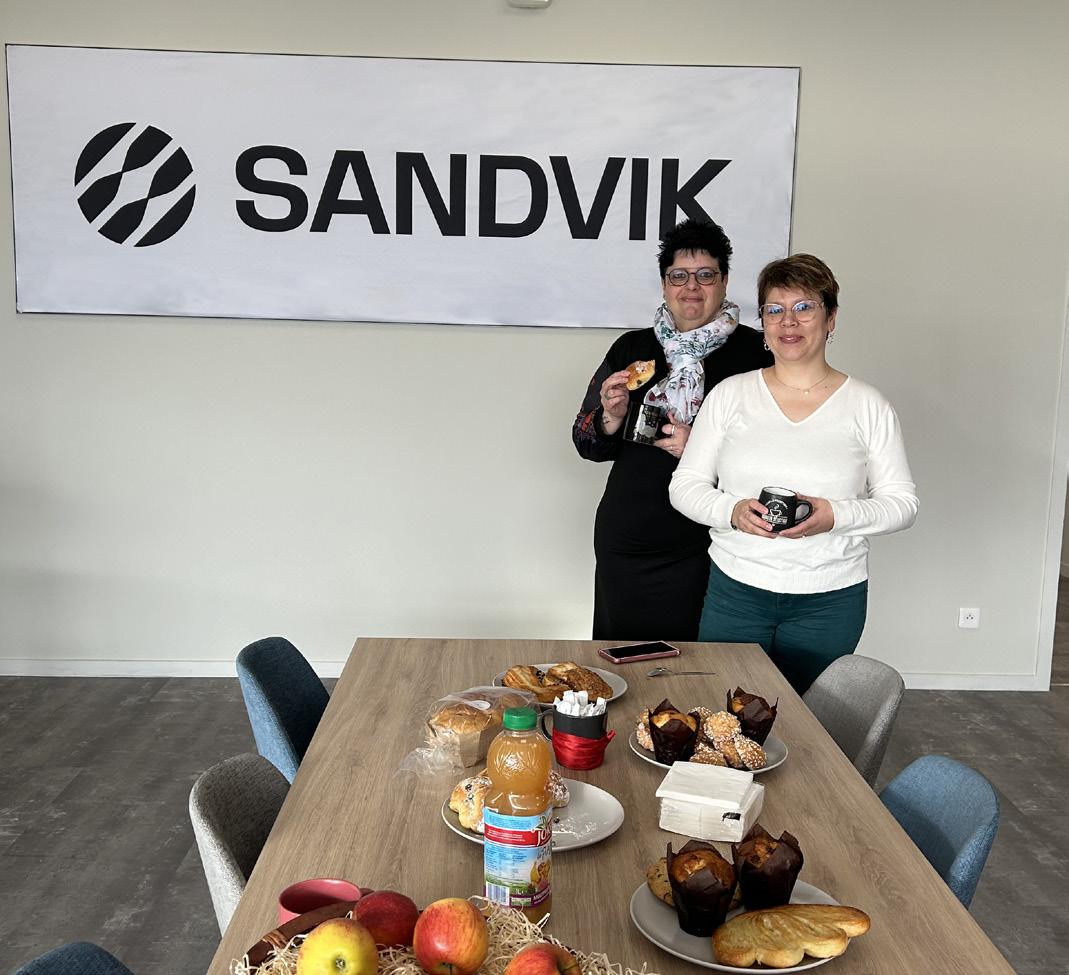
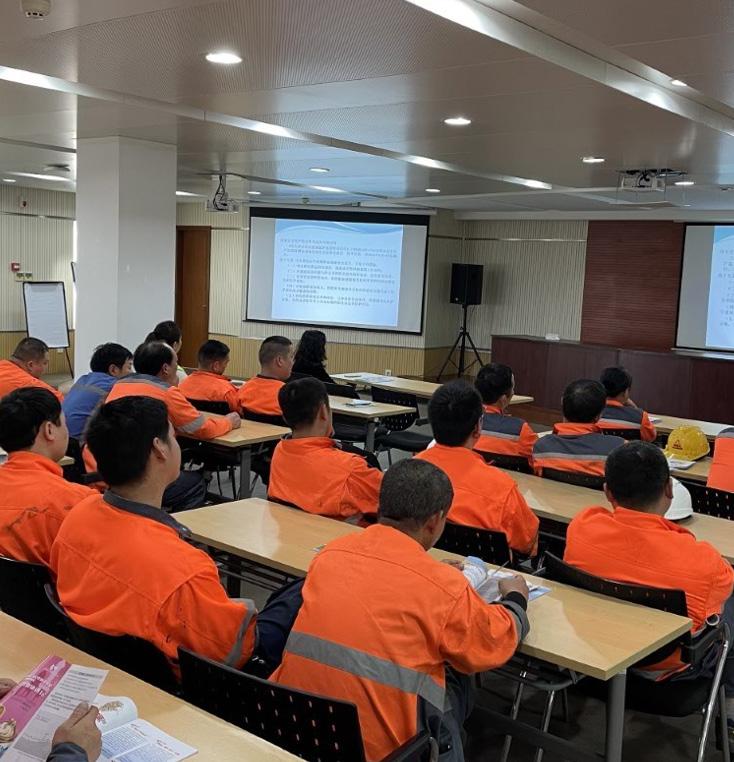
Health promotion activity in China
During the last week of April in China, we observe the National Occupational Disease Prevention Act promotion week. Simultaneously, our SRP Fengxian site prioritizes the health and safety of our employees as a central concern in our daily operations. On April 26th, we hosted an event where medical professionals from the local community hospital introduced common disease prevention strategies, mental health awareness, and the requirements outlined in the national act against occupational diseases. This initiative was conducted with the support of the local public health supervision authority.
Apart from enhancing health awareness among our staff, this activity also fosters trust between the local authority, our staff, and our Fengxian site. Notably, this marks the second time we have collaborated with the local authority for a knowledge-sharing event at our Fengxian site. In September 2023, we also organized a first aid course, facilitated by the local public health department. More information: mike.wu@sandvik.com
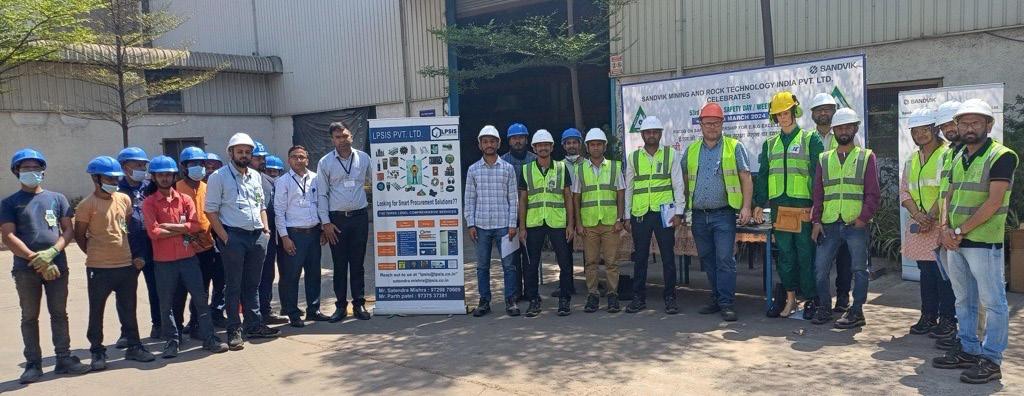
Celebration of National Safety Week in India
On the 53rd National Safety Week in India in March all employees, including contractors, at Assembly Center Pune, Regional Sourcing Office India (Pune) and the SRP foundry in Vadodara reiterated their commitment towards safety & environment. The National Safety Council of India had set this year’s theme to be “Focus on Safety Leadership for ESG* Excellence” and the event started
with a “Safety Oath” by the leadership team along with all the employees. This was an opportunity for everyone to reflect on the role of each individual as a safety leader for maintaining a safe and sustainable workplace and to re-affirm our commitment towards it. Then a series of activities, including various trainings, were carried out at both the Pune and Vadodara sites during the week.
Employees wholeheartedly participated in the activities including poster and slogan competitions, safety trainings etc. More information: pravin.dumbare@sandvik.com
*ESG= Environmental, Social, Governance
Language fika in Sweden
The Svedala site (Stationary Division) D&I Network has introduced an activity called language fika*, and the first meeting was held in March. At the language fika, 25 colleagues met up over some nice cake to get to know each other. The conversations were held, almost completely in Swedish. There was a good mix of participants, both from different departments and with language skills ranging from just a few Swedish words to native Swedish speakers. Friendly colleagues, gestures and laughter helped everyone understand each other (more or less). Svedala has so far hosted two language fikas, and the plan is to arrange them on a monthly basis.
If you have any questions about the language fikas or want to join in an upcoming fika just contact albin.svennelid@sandvik.com or someone else from thhe Svedala D&I network.
*Fika is a Swedish tradition that involves taking a break to enjoy coffee (or tea) and pastries while socializing with others.
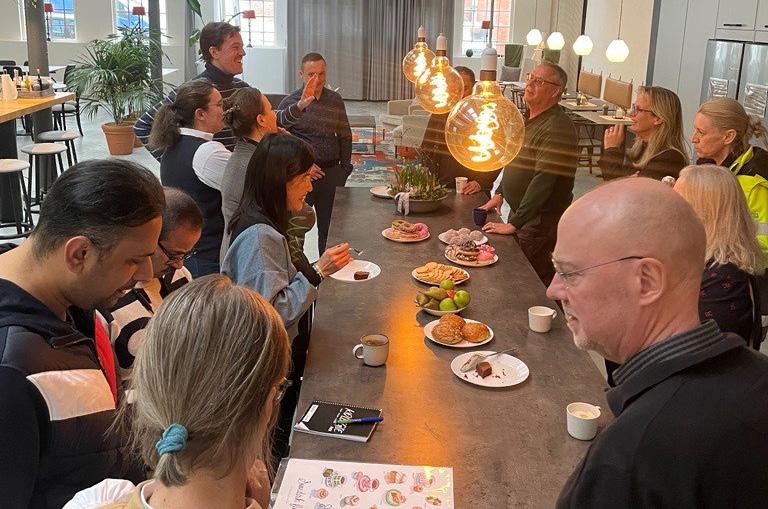
EHS recognition scheme

Mobiles Division has launched a Recognition Scheme to recognize and reward safety observations or planned task observations. The latter are used to recognize and reinforce positive safety behaviors as well as promoting conversations where unsafe behaviors are observed to try and prevent their reoccurrence in the future. Along with a safe environment (helped by raising of hazards), these safer behaviors can help us on our journey to zero harm. So far, the team has reviewed over 100 safety observations that were submitted from January – April and have recognized two observations.
The Power Pack team was demonstrating a lift, which, although they felt it was difficult, they completed safely. During the lift, Derek Knox, Assembly Operative had a good suggestion for a small stillage which could be fabricated to greatly reduce the difficulty of the lift. Derek’s suggestion won due to completing a lift safely and at the same time driving an improvement to minimize the lift in the future. A great example of identifying a solution to support driving a safety improvement.
We also selected Jamie Winnery for recognition as an issue was raised. There was good collaboration between the functions and an improved way of working was implemented. Jamie listened to evening shift assembly as they described a challenging problem where feeders had to be flipped to fit motors. They described what they thought a good solution for a flipping table could be, Jamie designed it and specified it according to the requirements of the stress engineer. More information: tom.givans@sandvik.com
Remote Monitoring Services –From Pilot to Paying Customer
From December 2023 to March 2024, we had the opportunity to pilot our new offering Remote Monitoring Services (RMS) with our customer Björkdalsgruvan. Björkdalsgruvan is a gold mine located in the northern part of Sweden. They are running a close circuit with 2xCH865 in tertiary stage. During this pilot we used our digital platform SAM to monitor the customers equipment and operation remotely, we provided the customer with monthly reports outlining overall performance, highlighted any issues present in the data and of course provided our customer with recommended actions to solve those issues!
During this period, we helped our customers to solve mechanical issues, avert events that could have led to unplanned stops and
provided expert guidance regarding their equipment’s settings and operation. The results were satisfying for both Sandvik and Björkdalsgruvan, together we will continue with the RMS after the pilot phase. We are now running RMS as a full-scale product.
For the upcoming quarter we plan to launch more pilot studies for RMS where we aim to learn more about our customers’ needs and create an offering that will advance and strengthen our service portfolio! More information: ali.jumaa@sandvik.com

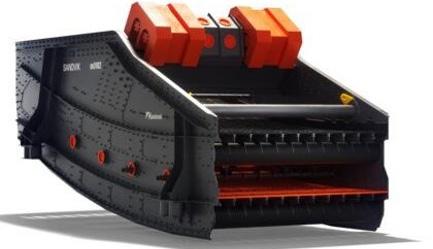
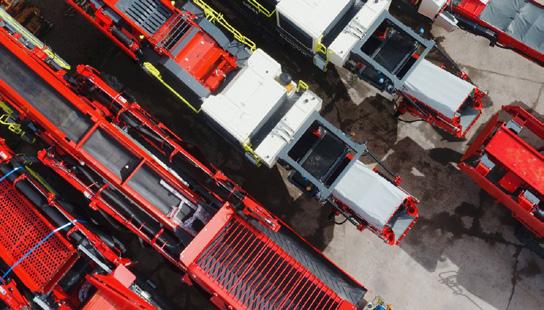
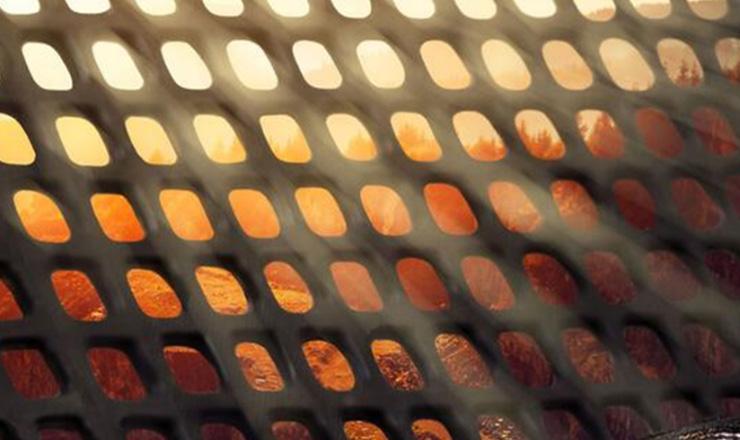

Have you seen the updated SRP strategy and calendar?
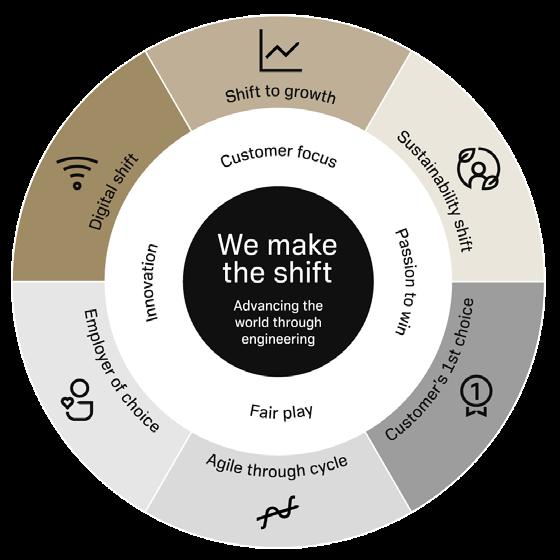
Since we created Sandvik Rock Process Solutions in 2021 there has been a fast pace in developing our business and today we are not the same company as when we started. We have grown our revenues from 7.6 BSEK in 2021 to 11.5 BSEK in 2023. We have acquired companies to widen our offering and at the same time continued to develop our existing offering. All with the ambition to be #1 in eco efficient rock processing!
Given all of this we have made a strategy review and the new updated strategy was launched at the end of April. We have updated the intranet strategy portal and here you can read about our objectives, growth areas and key initiatives. As well as about growth drivers and competitors in our industry. We will continue to update the strategy section going forward.
The SRP strategy is not just a document, it’s a living road map that we all contribute to! It is important that we continuously discuss where each and every one of us fit in. Each piece of the puzzle is important.
Check-out the strategy calendar
During the month of May there have been daily posts on the intranet, that have highlighted and explored a new strategy topic each day. Among other things there were several short videos with SRP managers talking about the different elements and how their areas support the strategy. Did you miss the whole calendar or some of the calendar entries? Not to worry, all the calendar posts can be found on the intranet.
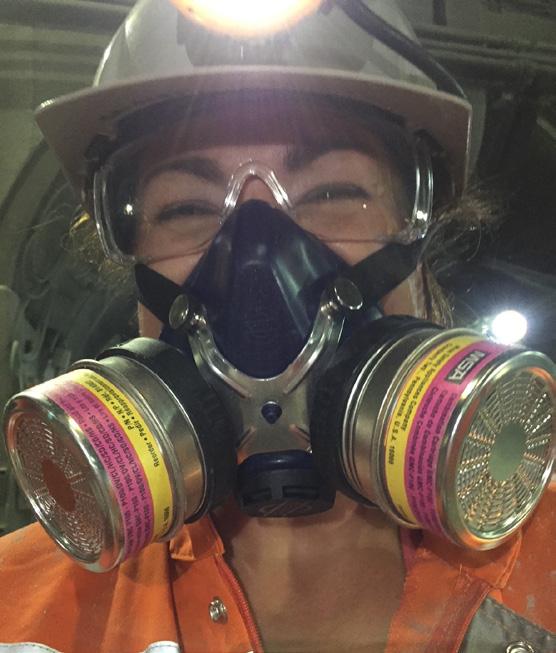
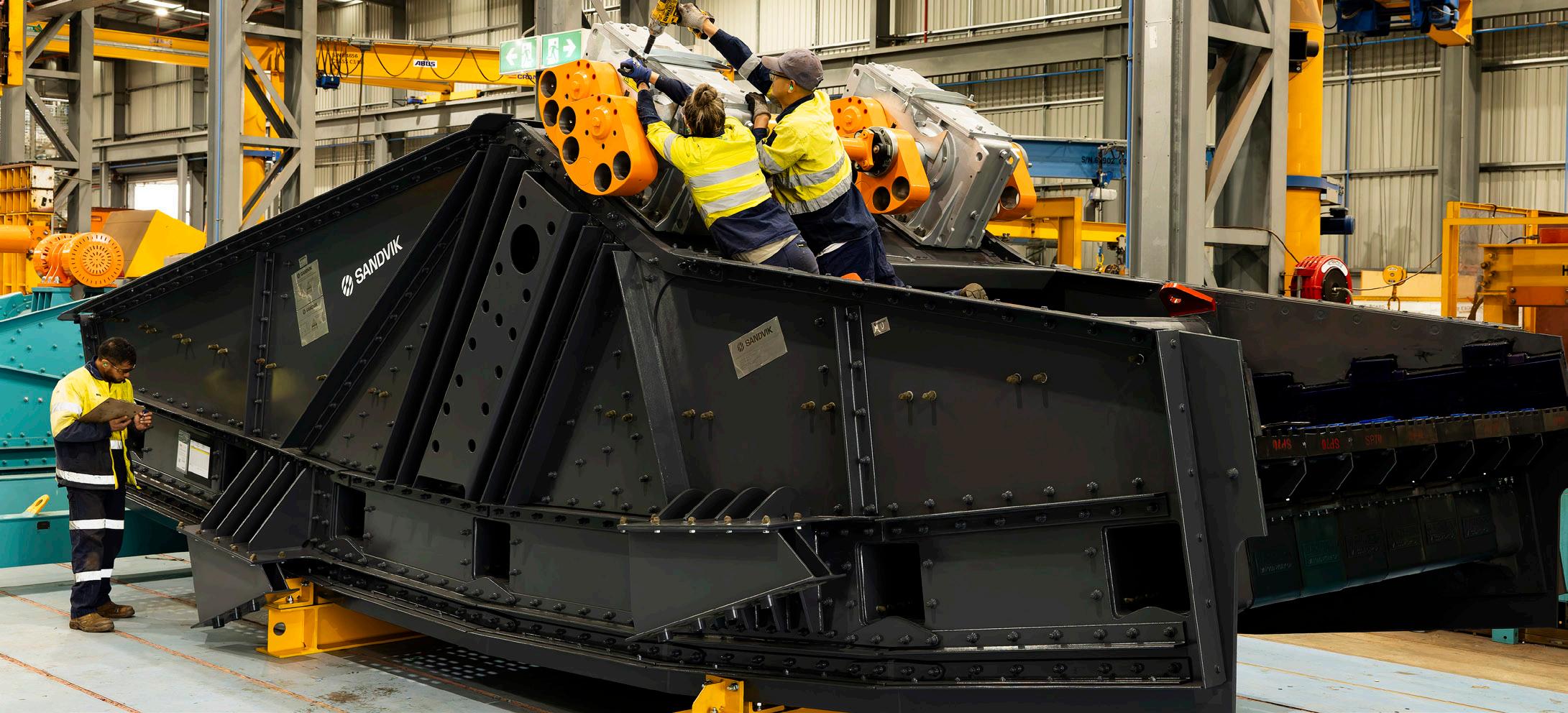
Poised to complete the SP Mining integration
Following our acquisition of the Schenck Process (SP) mining related business in November 2022, our teams have been working hard behind the scenes to bring our new offering and capabilities to market.
In October last year, we reached a key milestone in the integration of SP Mining into our business area, when we changed the names of the legal entities that came with the Schenck Process acquisition. The newly acquired entities provide us with a much better global reach, particularly in geographies where we previously had little presence. This is especially true in Australia, where Sandvik Rock Processing only had a small team, while SP Mining had the majority of its engi-
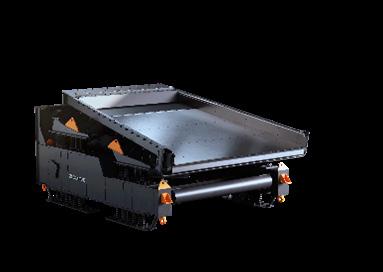
neering and R&D teams as well as production and service facilities in Australia. Schenck Process Australia, which employed over 400 people became Sandvik Rock Processing Australia, which is now a major hub for our new, global Screening Solutions Division (as of July 1).
Since the renaming of the legal entities, the integration of the SP Mining business around the world has been a key focus for our teams. Part of this work includes the rebranding of all aspects of the business. In parallel the SP Mining and Kwatani equipment offerings have been united under the Sandvik brand. The result is an unparalleled range of vibrating screens, feeders, screening media and train loaders.
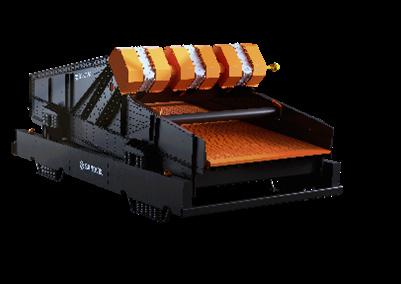
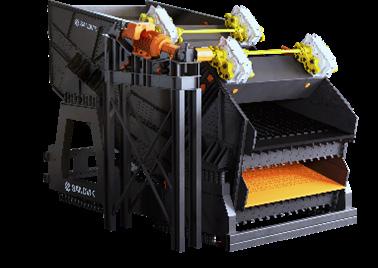
In early May we achieved another key integration milestone, shipping out the first Sandvik branded SP Mining screen from our Jandakot production facility in Western Australia. Pleased with the result, our Global Head of Marketing – Screening Solutions, Peter Newfield, previously Head of Marketing APAC for SP Mining, said,
“Apart from the change to the look, branding and Sandvik nomenclature, nothing else has changed. Our legendary reliability, technology and aftermarket support remains as our customers have come to expect. We are now better equipped than ever to help our customers to optimise their comminution and material handling operations for maximum performance, safety, and efficiency.”

Commenting on the new offer, Newfield says that combining the industry leading screening, feeding, and loading expertise of Schenck Process Mining and Kwatani with Sandvik’s mastery of crushing and wear protection, allows us to bring an unrivalled equipment line-up to market.
“This unique offering is underpinned by the expert process knowledge of our teams, a full range of digital tools, high quality OEM spare parts, consumables, and life-cycle services.”
But the integration isn’t just limited to the equipment. Newfield says that it has been a major project that involves every part of the business. In essence, the acquired Schenck Process entities have become Sandvik Rock Processing entities and so SP Mining staff had to embrace the Sandvik culture and learn our company’s systems, and ways of working.
“Of course, a big part of the integration is making sure that our key stakeholders understand the benefits of us becoming a fully integrated part of Sandvik. It takes time for people to adjust to change, and they need to know what is happening throughout the process. We have worked hard to communicate the changes to all our key stakeholders including our customers and employees.” He said.
“We are now changing the branding of all our Australian facilities, our motor vehicles, and the work clothes that our people wear on the job every day. Our website and other marketing collateral is also being changed
to showcase our new product offerings and brand.” Newfield says that he expects the rebranding projects to be complete by the end of June which is the final step in the integration process.
“Our new offering along with the advances that our combined R&D teams are making, allow us to partner with our customers to address our industry’s biggest challenge - making mineral processing more eco-efficient.”
Contact: peter.newfield@sandvik.com
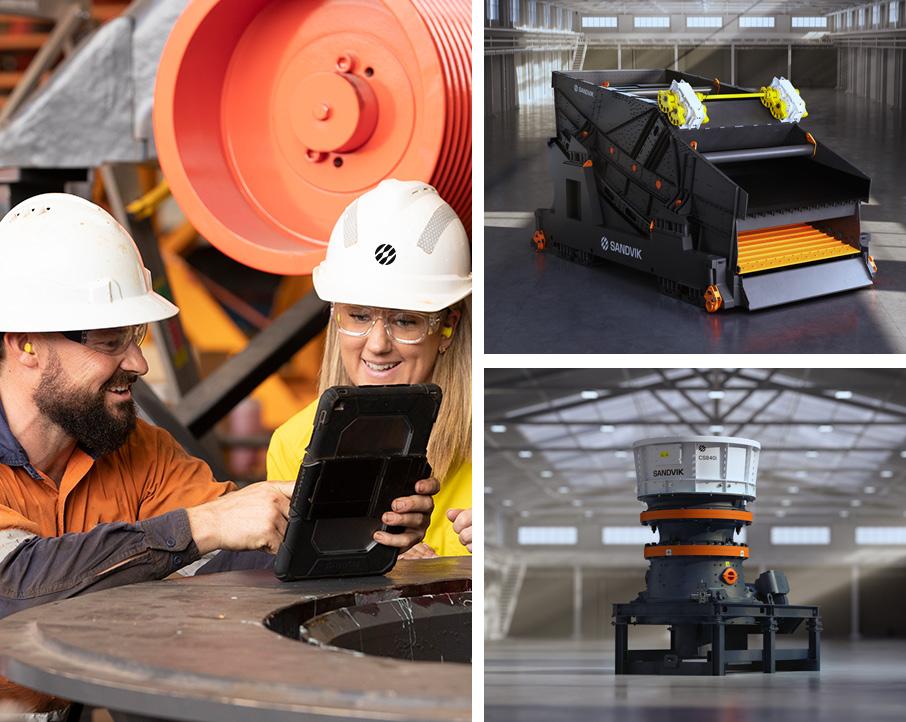
New Demand process for all new IT requests
To support our global governance and management of our IT assets, systems and licenses, all IT investments (see list of examples below*) that are done in any part of SRPs divisions or functions, should go through the New Demand process.
To be able to be proactive and support your part of our business in the best way, the earlier the SRP BA IT team is involved on these new demands, the better it is, preferably the contact should be initiated before an IT supplier is chosen. For any New IT Demand please send your requests to this email address: DL_0990.SRPNewITDemand@sandvik.com
We are looking for your support to reenforce organizational awareness of this way of working. Please send me any IT proposal that is brought up in your management teams, for approval: peter.c.larsson@sandvik.com
*List of relevant IT investments, and in any doubt please reach out
• New applications/systems
• New servers
• New service providers
• Licenses with new suppliers/for new applications
• Online (cloud / SaaS) apps for business usage
Increased order intake on HSI and VSI Impactors
Order intake in 2024 on our HSI (Horisontal Shaft Impact Crushers) and VSI (Vertical Shaft Impact Crushers) ranges is showing a good performance resulting in a monthly record for April. Stationary Division has secured significant orders for the impactor range, thanks to the support from various sales areas, for example India, SEMEC, Northern Europe and Latin America. The diverse sales mix, both geographically and in terms of crusher models and applications, contributes to a more stable profitability for this product range.
The success relates to several factors. Primarily the focused and intensive collaboration between global sales, the crushing solutions product teams, performance developments, and many others who share the passion to win. While impactors are predominantly used in the infrastructure segment for crushing sand for concrete production, we are proud to announce two orders for VSI crushers for recycling steel mill slag in Finland.
Let’s continue to work and win together, to leverage this positive momentum and make this a successful year for our impactor range. Read the full intranet news here. More information: heiko.kertscher@sandvik.com
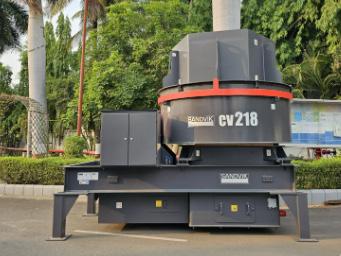
S-range expanding to replacement business
Product line S-range from Screening Solutions (Stationary Division) has recently increased the capability to expand and support stationary replacement business of screens in the infrastructure customer segment. This by engineering a series of metric dimension configurated screens based on the design of late 2023 launched SJ-Infra series with increased availability. These metric versions are an enabler for one-to-one replacement at markets where the majority of the installation base are metric configurations instead of imperial. These new

configurations are developed in terms of proactive territory specific replacement concept (TSR) and aimed to replace Sandvik legacy fleet like CS-series but also installations of the main competitors in each relevant sales territory. In case you have a potential replacement opportunity, or want more information, don’t hesitate to contact: mikko.vesanto@sandvik.com
The journey of Stationary Division’s Jaw crushers product Line this year has been nothing short of remarkable. With an outstanding kickoff in sales, the expansive range of Jaw crushers, including the CJ613, CJ615, and CJ815 models, has captured the market’s attention.
Year-to-date, our tally stands at an impressive 18 units sold, marking a 50% surge in Order Intake compared to previous year. This exceptional performance is mirrored in the balanced sales split between the Mining and Infrastructure sectors, a testament to the universal appeal of our products.
Experience the power of collaboration:
Elevating jaw crusher sales to new heights
At the heart of this triumph lies teamwork & focus. Through unwavering collaboration, our sales area and product line teams have seamlessly merged their expertise and communication channels, igniting a synergy that propels our business forward. This effort has not only sharpened our business focus but also propelled the sales trajectory of our premium Jaw crushers to unprecedented heights.
Voices from the sales areas:
Victor Dossetto (Vice President sales area SRP Latin America):
“In Latin America we are fully convinced that a close cooperation and transparent communication in both directions, create success stories. Great JIG orders in Latin America during the last months are the best demonstration of this statement.“
Raphael Carmona (VP Sales area SRP North America):
“This deal is going to help us to increase our references of big jaw crushers in hard rock applications in North America, part of our growth strategy for the Sales Area. It was only possible due to a great collaboration between frontline and backline, working together to suit the market and customer needs.”
Cristian Rusu (Vice President sales area Southern Europe, Middle East and CIS):
“I’m grateful to be part of such an incredible team and I want to thank all my colleagues from sales area and backline that worked as one team in developing and pushing a campaign into the market.”
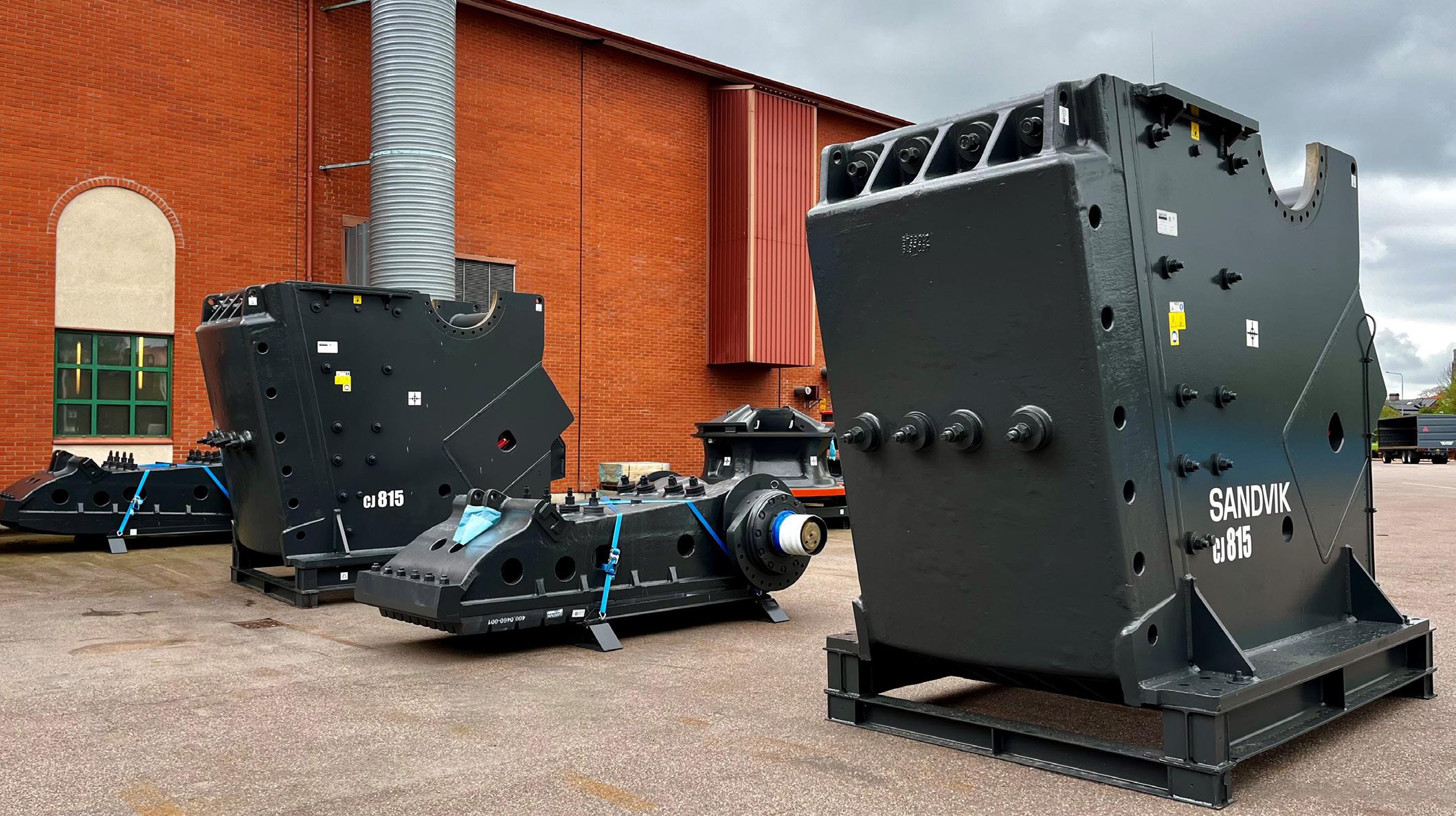
ATD present at Intermat in Paris
Sandvik Attachment Tools’ presence at the recent Intermat expo in Paris exemplifies our commitment to engaging with key stakeholders and showcasing the strength of our Rammer brand on a global stage. With our business partner in France, BRH Plus, we had the opportunity to engage with customers, discussing how our products best meet their needs. The enthusiastic turnout at the expo underscores the strong demand for our products and the trust placed in the Rammer name. Additionally, the endorsement received from Finnish Ambassador Mr. Matti Anttonen reinforces the excellent reputation and recognition that Rammer enjoys, not only within Finland but also internationally. Attachment Tools Division (ATD) President Elina Pyykkö and Director of Sales and Product Support Olli Karlsson had a great opportunity to introduce the latest products and innovations to him. Our participation in events like Intermat reinforces our position as a leading provider of innovative solutions in the industry, driving growth and strengthening our relationships with business partners worldwide. More information: julie.schilling@sandvik.com
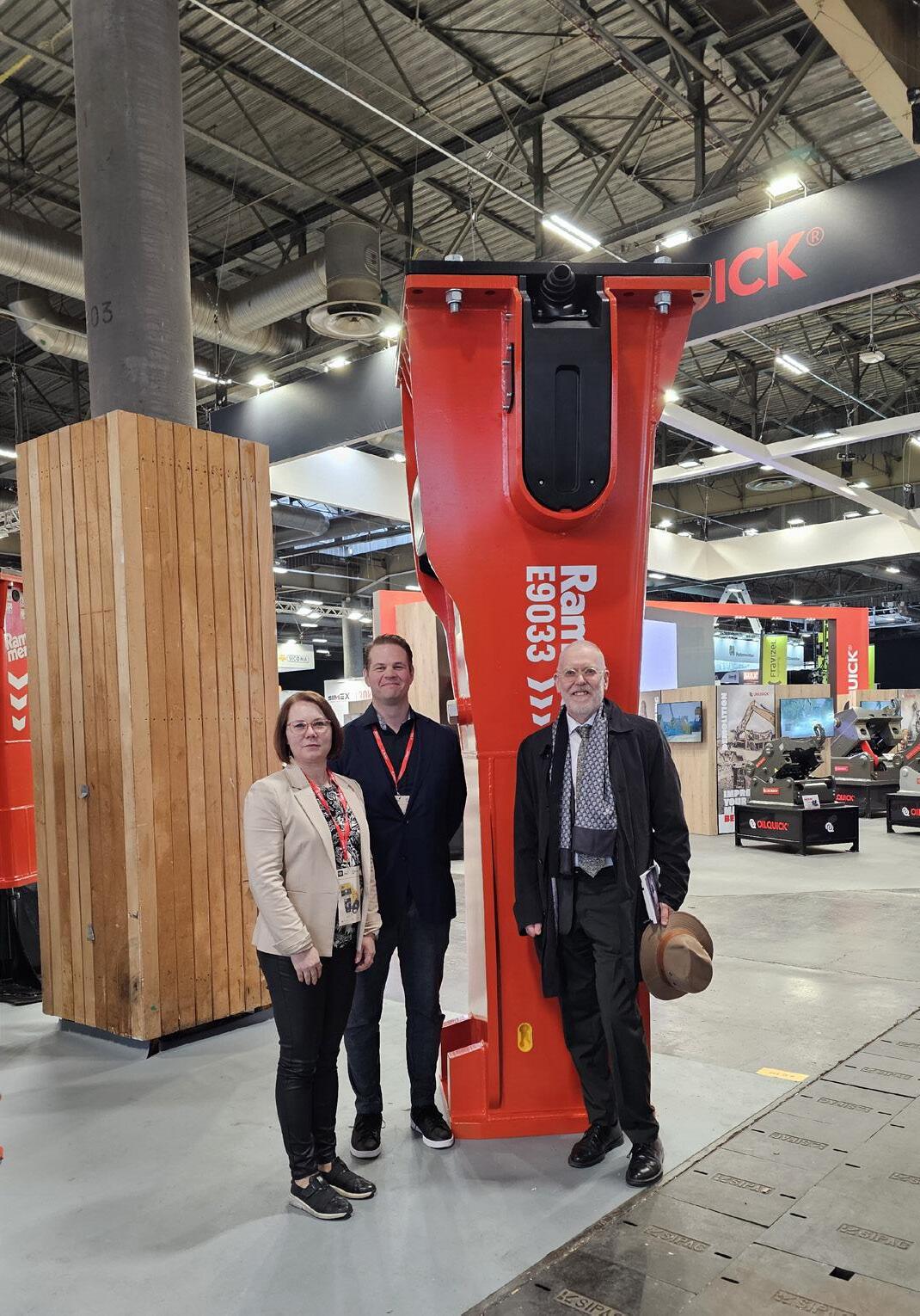
Impressive results from M&T Expo in Brazil
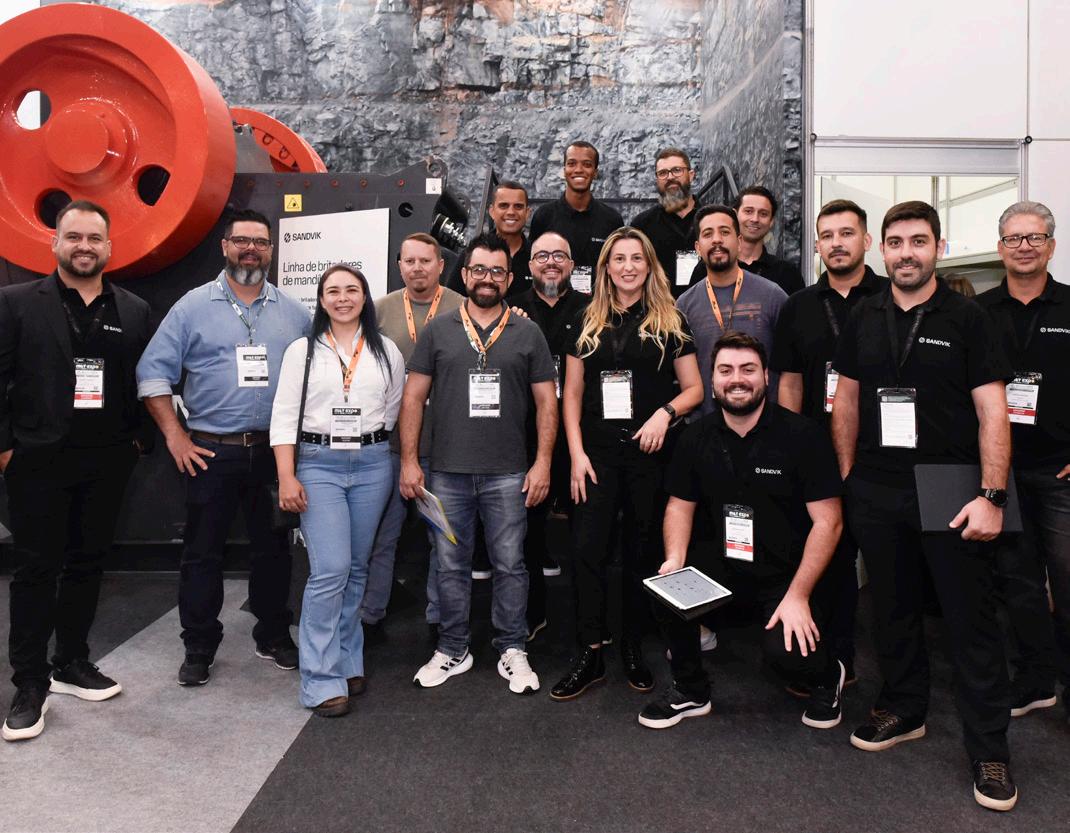
We are immensely pleased to share Sandvik’s success at the M&T Fair in Brazil - one of the most important events for the aggregate sector in Latin America. During this significant fair, we celebrated the sale of 8 crushers, further consolidating our presence and impact in the market. Besides these notable sales, we had the honour of presenting our new screening offering, which generated a series of promising contacts and leads for future businesses.
M&T Expo plays a crucial role in the machinery and equipment scene for construction and mining in Latin America, and our presence at the fair was marked by the exhibition of safe and sustainable solutions in crushing and screening. The integration of our screens with the crusher range allows us to offer customers a more complete and efficient solution.
Our participation in the M&T Fair strengthens our commitment to provide innovation and excellence to our customers, contributing significantly to the continuous progress of the aggregates sector in Latin America. More information: cristiane.fontes@sandvik.com
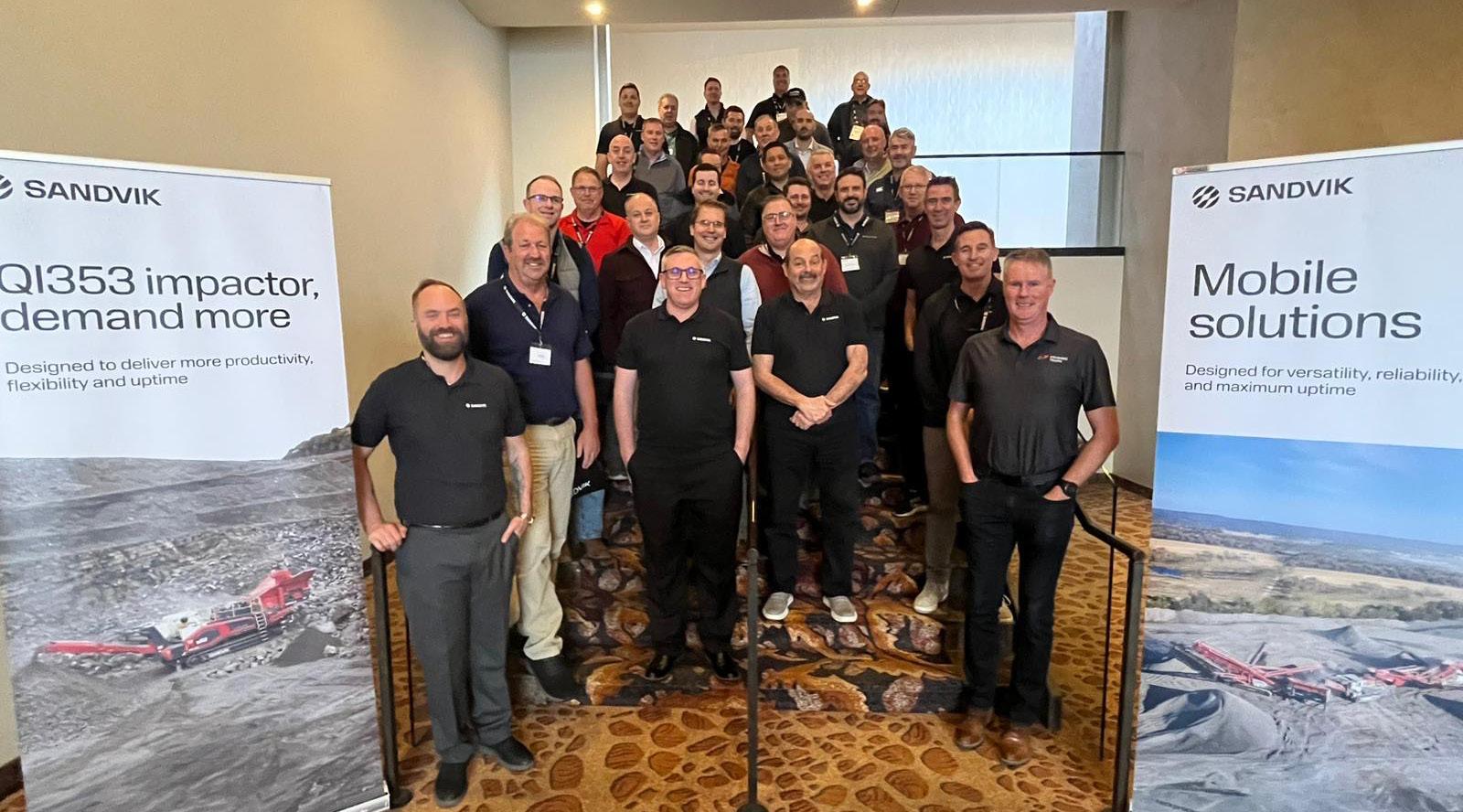
Hat trick success for Mobiles Division
Sandvik Mobiles participated at the 2024 AGG1 show in Nashville in March and took the advantage to host their Americas’ Dealer Conference and Product Council during the same week. The AGG1 show in Nashville is the leading World of Asphalt exhibition which is held annually and brings together manufacturers in the asphalt and aggregates industries. Amongst the impressive display on the Sandvik booth was the QI353 HS, third generation mobile impact crusher complete with modular hanging screen.
During the three-day show, a dealer conference for the Americas’ market was organized for distributors from USA, Canada and South America. It provided the perfect opportunity to meet new distributors and see many longstanding partners face to face. The conference had a packed agenda with topics outlining our growth ambitions, latest product developments, customer support, digital solutions and aftermarket.
On the third day, product specialists and sales representatives for mobile crushing and screening equipment were invited to a Product Council. The purpose of the meeting was to share information on our future New Product Developments & strategic direction. It provided the opportunity to listen to direct feedback on future developments, product trends and future requirements.
Overall, the combined events represented not only our commitment to our dealer network and mutual success, but also reinforces our position in the marketplace. Contact: melissa.baker@sandvik.com
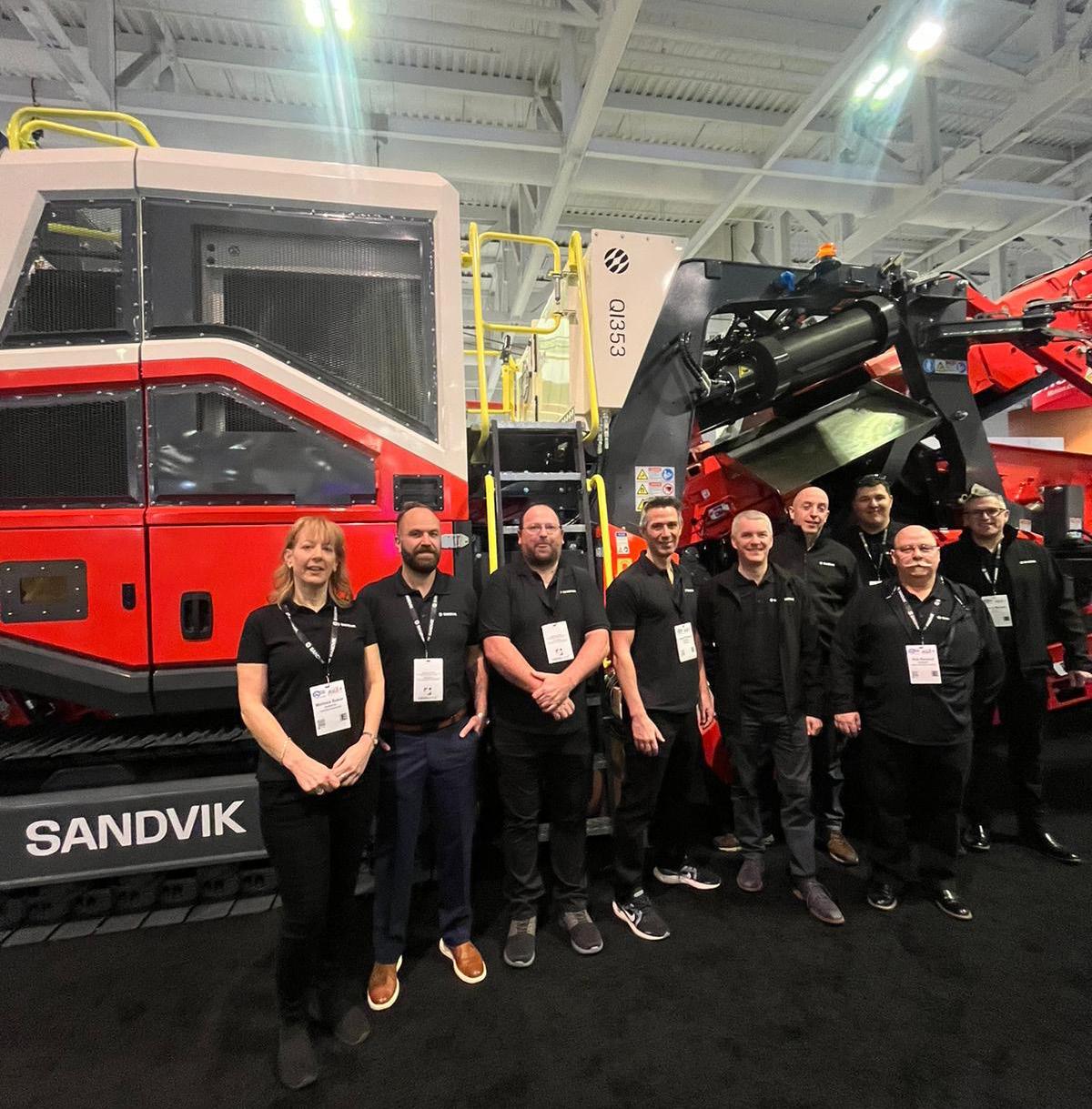
Mobiles Division recycling project in Mexico
Mobiles Division has together with our dealer SVF MAQ recently been selected by CEMEX to supply a Sandvik QJ341 jaw crusher for a demolition material recycling project (debris from the 1985 and 2017 earthquakes in Mexico City). CEMEX is one of the top cement/aggregates producers in the world and this is our first tracked mobile unit being supplied to Cemex in Mexico.
Simon Unwin (Sales and Applications Manager) and Julio Flores (Dealer Manager, South America) also visited Veracruz, Mexico to provide training to Mobiles’ dealer SVF MAQ. About 10 people attend from SVF and the team provided an overview of Sandvik Rock Processing Solutions and conducted in depth training on our mobiles’ equipment and aftermarket offering to ensure they are fully equipped to value-sell our equipment. More information: julio.flores@sandvik.com

Rio Tinto supplier recognition event in Australia
In April we had the pleasure of representing Sandvik as a supplier of Rio Tinto at their yearly supplier recognition event. The event inspired us, having so many vendors rewarded for their safe, innovative and sustainable solutions delivered last year to Rio Tinto. We had a lot of opportunities to connect with our customer and discuss future possibilities.
Sandvik has a highly qualified team that delivers a premium product and excellent customer service through customised engineering on Screening Solutions and high-performing Crushing Solutions. Let’s continue our journey of supporting Rio Tinto and all the other customers.
Do you have any safety, health and operational excellence ideas to add to our products? Reach out to your leader and share your ideas! Thank you all for your Customer Focus. More information: simone.tomaz@sandvik.com


Conecta for customer events in Latin America
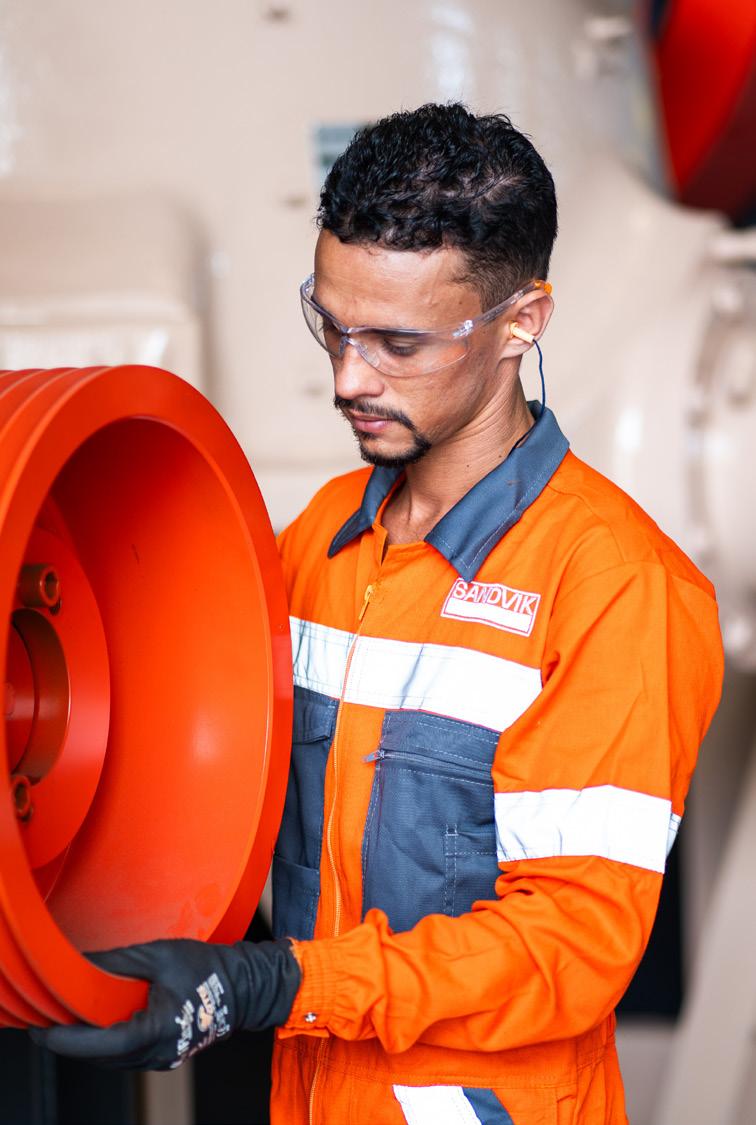
We are extremely excited to announce the launch of the Conecta Sandvik Rock Processing - Latin America Program (Stationary Division), setting new standards in mineral processing. This event was not just a mere meeting, but an enhanced experience designed to showcase our equipment and solutions and foster meaningful connections with our customers, facilitating a valuable exchange of knowledge.
In March, we held the first Conecta event with Vale customers at our service center in Vespasiano, Brazil. It was an exceptional opportunity
for collaboration and joint development, in which our experts were directly engaged with our customers.
Over three days, we shared insights and carried out operation and maintenance training for the Sandvik CH 860 crusher, led by the SRP team. We are excited to expand Conecta to other customers in Latin America, with the next event already scheduled for customers in Chile. If you are curious to know more about Conecta please watch the video. Contact: cristiane.fontes@sandvik.com
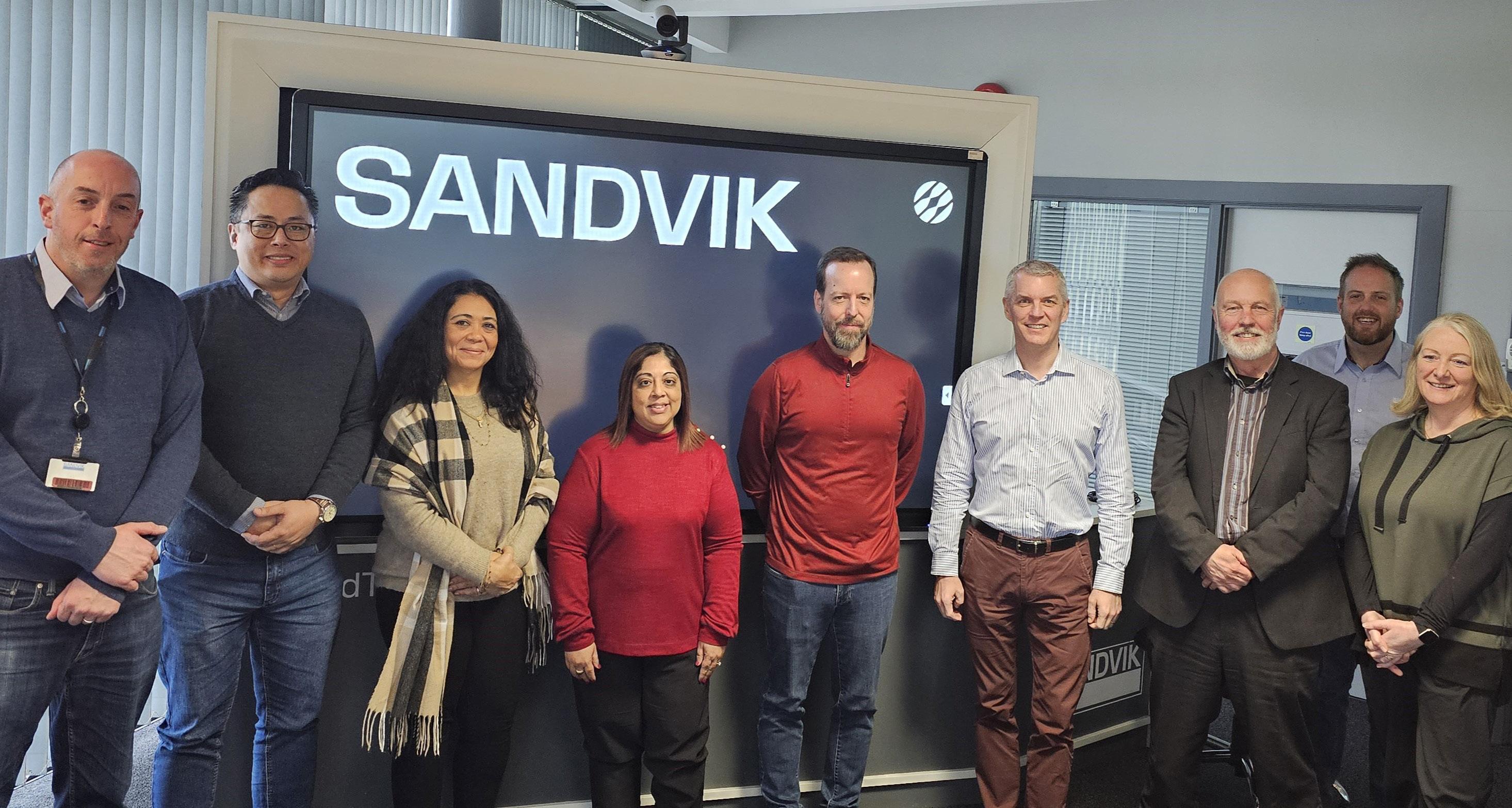
Dealer and customer visits in Ballygawley
Mobiles Division recently welcomed multiple distributors and customers to its Ballygawley site. In March we welcomed a delegation hosted by Invest Northern Ireland and the Department of Business and Trade to the site, alongside a potential customer. We received some excellent feedback from the potential customer.
A few weeks later we had a visit from Per Olav Fredheim, from our Norwegian distributor Fredheim Maskin. The team had great discus-
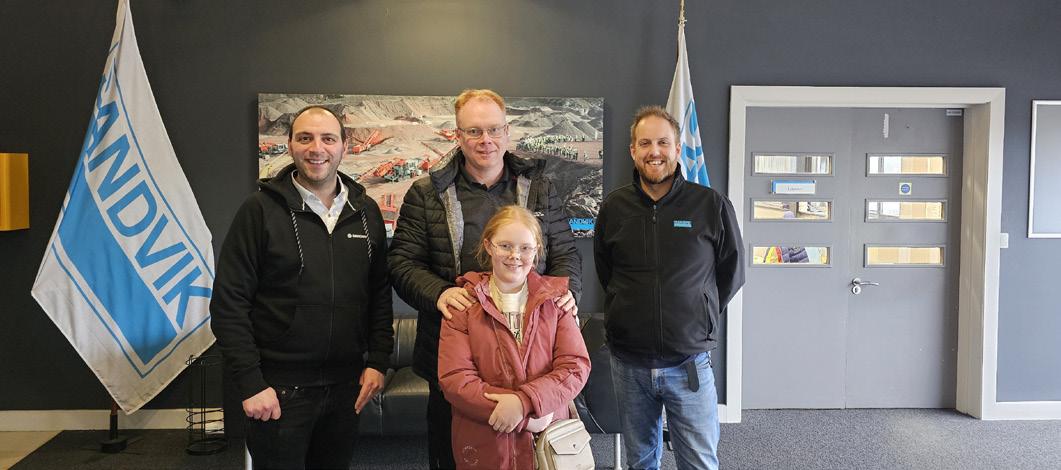
sions with Per which included some feedback on the Sandvik UJ443E pre-production unit and also led to two QJ341 orders.
On the same day we also had our Dutch distributor, Herwijnen Machinery, visiting alongside a customer to see the Sandvik UJ440i in person. The feedback has been really positive and dealer manager, Paulo Prazeres has continued discussions with the dealer and customer. More information: michelle.donnelly@sandvik.com
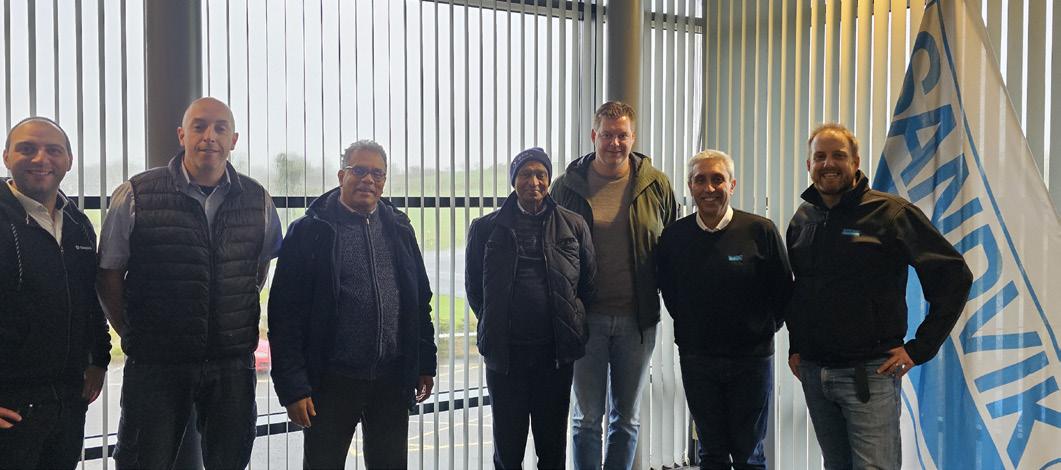
As previous announced Sandvik (Stationary Division) has been awarded a $21 million AUD contract in July 2023, to design and supply two train load-out (TLO) systems for the Simandou iron ore mine in Guinea, West Africa. Recently the CEO of our partner Takraf in the Simandou project, visited the Jandakot facilities in Perth (Australia). During the visit we discussed the project execution, schedule and progress made so far. Both Sandvik and Takraf are very happy and content with the ongoing collaboration. There were further discussions held between both teams around collaboration for some ongoing projects and Takraf expressed their willingness to partner with Sandvik in Australia.
Takraf also visited the shop floor and were very impressed with the manufacturing facility and various types of the screens being currently assembled. The vibrating screen in the photo below is SL4392M, the biggest double deck flat screen ever built.
Simandou is home to the largest untapped high-grade iron ore deposit in the world. The premium grade of Simandou iron ore will be a vital part of the energy transition and broadens Rio Tinto’s global portfolio of iron ore products, complementing their existing, longterm iron ore production in Australia’s Pilbara region and in Canada. More information: amit.parimoo@sandvik.com
Partner Takraf visits the Jandakot Facilities
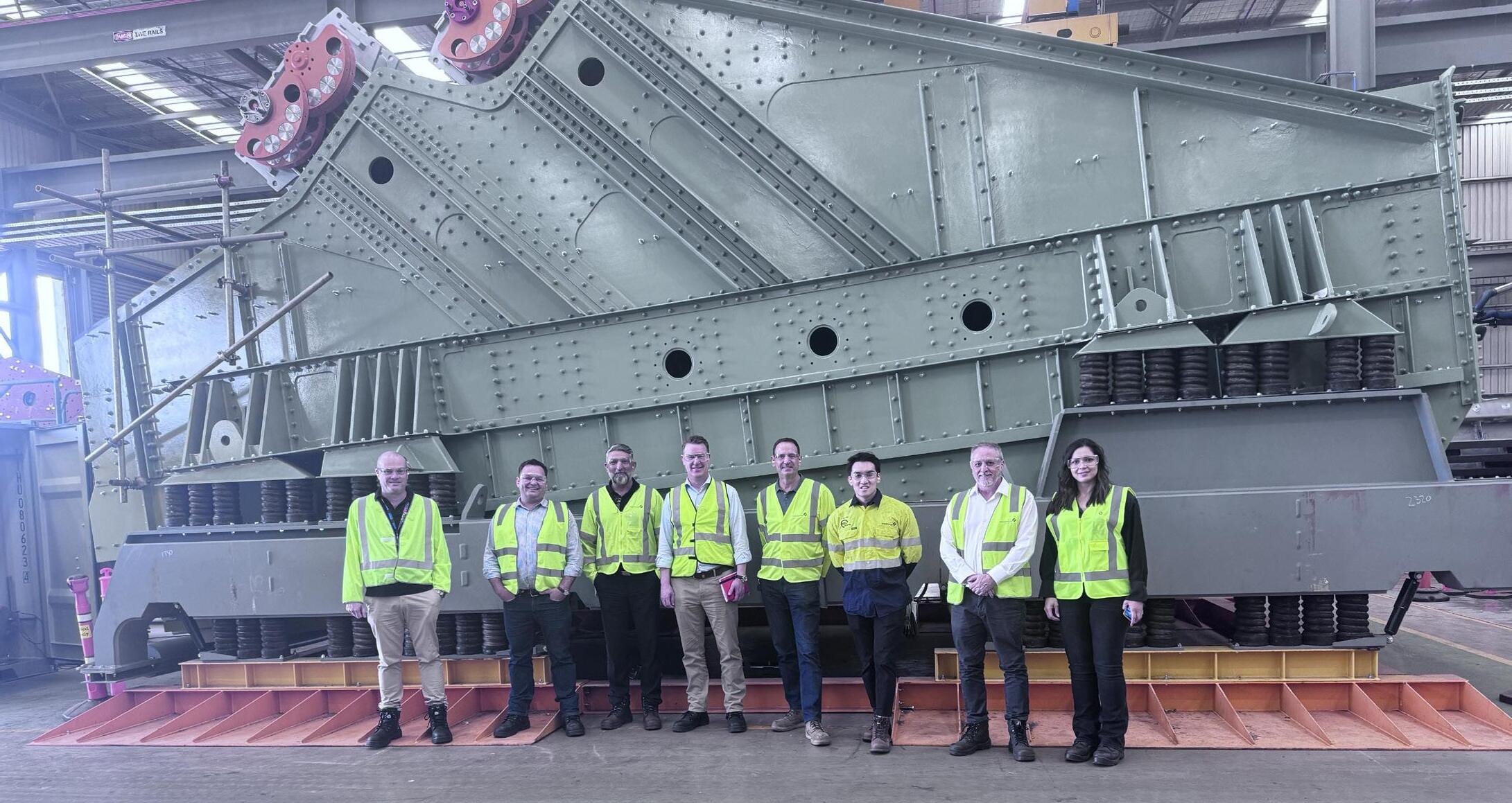
A training success story for distributors in SEMEC
Continuing our efforts to enhance our team’s proficiency in handling crushing equipment, a 3.5-day deep dive technical training program was conducted for our distributors during the last week of April. This initiative engaged participants from STET Portugal, Eltrak Bulgaria and Greece, Lutze Benelux, and our internal teams.
Facilitated by an exceptional group of trainers, including a dedicated expert from the SEMEC Lifecycle management area, mentorship of the crushing equipment lead technical trainer from the divisional learning and development department, and the participation of the SAM champions from the digital and automation team, our training promoted a culture of collaboration and knowledge sharing.
The positive feedback after the event, along with the anticipation for future sessions during the year, underscores our commitment to continuous development and excellence.
This initiative represents another milestone in our journey to provide top of the line training and enhance the capabilities of our global workforce and distributor base. Through collaboration, knowledge sharing, and innovation, we aim to elevate our service standards and drive success in our ever competitive landscape.
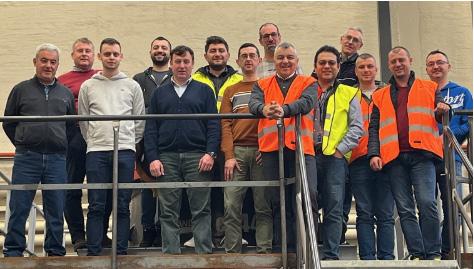
The expertise gained from this training will not only enable better equipment service but also promote our aftermarket offering to continue solidifying our leadership position in the market. More information: freddy.ramirez@sandvik.com
Mobiles’ training fortnight
Friday 26 April marked the completion of two weeks of training for the Mobiles Division team. It was a busy few weeks, with a variety of training activities taking place both in person and virtually, where we covered topics including:
• Induction refresher training
• CPR Training
• EHS 360 including identifying hazards and safety observations
• Excel training
• Machine tracking refresher training
We were also delighted to have NI Chest Heart and Stroke on site to provide training on Heart Health and Stress Awareness to all staff. We had great participation and engagement from everyone and look forward to implementing the new skills attained. Contact: tom.givans@sandvik.com
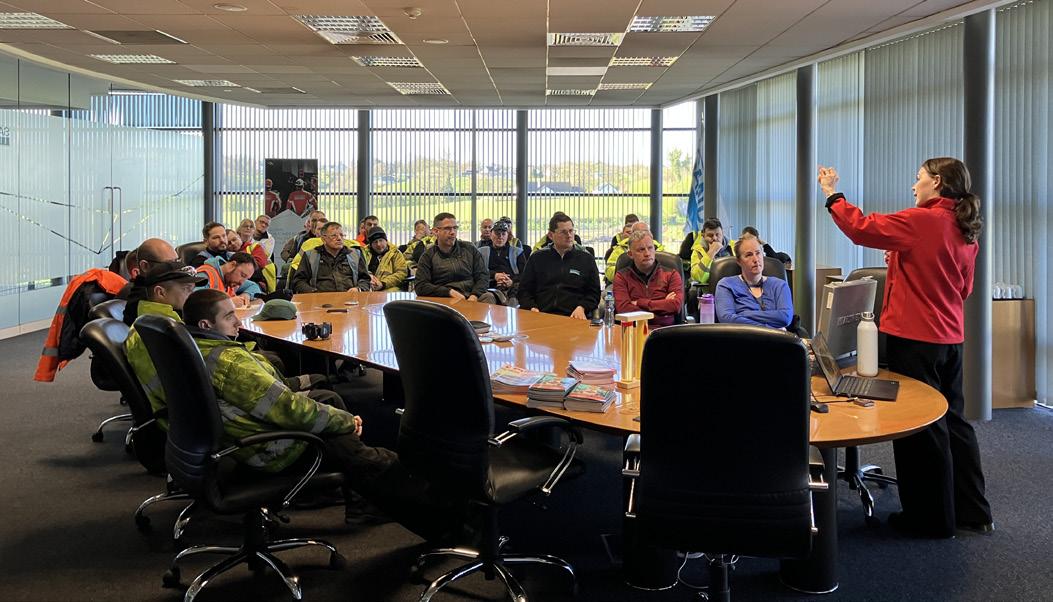
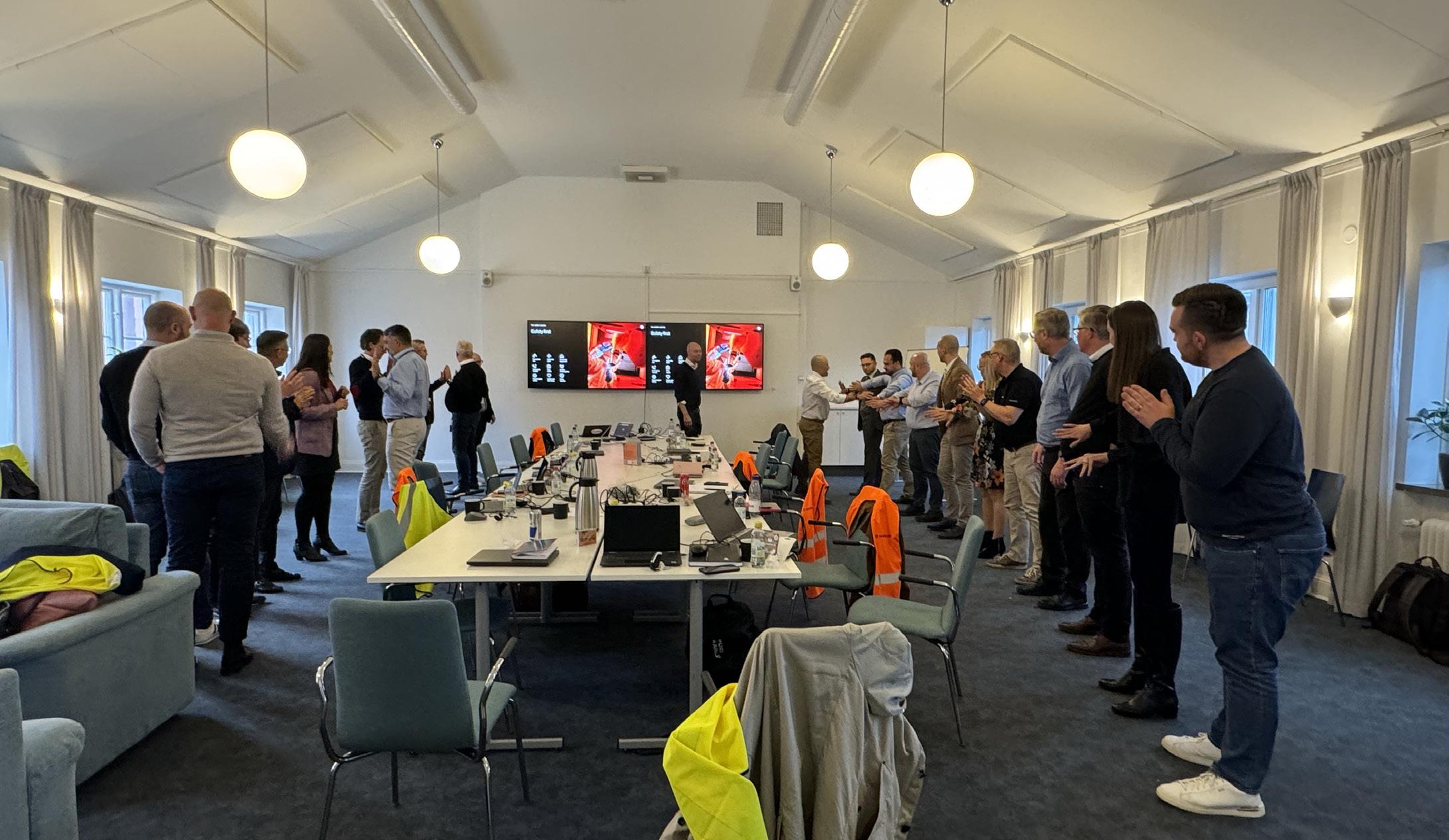
Global sales meeting in Svedala
Stationary Crushing & Screening Global sales hosted the Global sales meeting to share learnings between the teams and outline how we can continue to develop and serve our customers in the best way.
The meeting took place at our site in Svedala, Sweden. A lot of time was spent on presenting, aligning, and discussing each Sales Area strategy and how we best can support the overall strategy, the constant changing markets and secure and grow the sales revenue.
Many participants were invited; both to present but also to contribute to the discussions and add their perspectives. Guests from the BA, Division Management team, Crushing, Screening, and Service solutions contributed with very interesting discussions and workshops on commercial management, legal, product road maps, innovation and division strategy etc. Richard Harris, Peter Unelind and Terese Withington also shared their thoughts, but also expectations on the Global Sales team. More information: mattias.lindh@sandvik.com
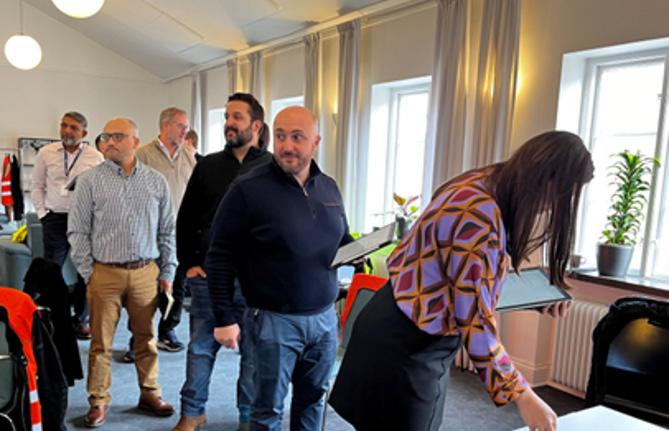
Mobiles’ team completes Couch to 5k
On April 25, the Mobiles Division team in Northern Ireland completed their month-long Couch to 5k training, with a final run around a local park. There was a fantastic turnout from the team and thankfully the rain stayed away for everyone completing their run!
This initiative was followed on May 6 by the start of our May Walking Challenge. We were excited to see lots of progress made by the team through this initiative too. Contact: healthandwellbeing@sandvik.com
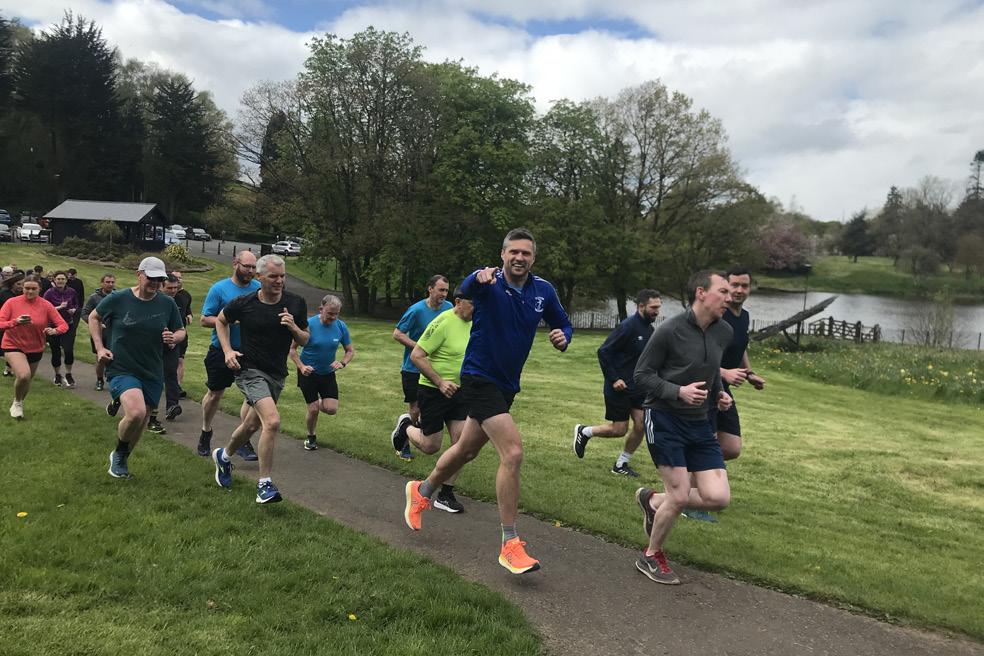
On Tuesday 30 April, Andrew Bolton, Tracked Product Line Manager, Sandeep Bhattacharjee, Wheeled Product Line Manager, Robert Callaghan, Product Support Engineer and Michelle Donnelly, Marketing Professional presented to our dealers in the EMEA/APAC region.
The webinar was designed following feedback from the distributors and aimed to provide them with an update on our upcoming equipment and aftermarket launches, the key features of each product and our launch plan. The team also shared an overview of our NPD pipeline and outlined some changes to the NPD launch process.
The team will present to the distributors on a quarterly basis going forward. Through these sessions, we will further support our dealers to ensure they are equipped with all the information they need to market and sell Sandvik Mobiles’ products in their territories. Contact: Michelle.Donnelly@Sandvik.com
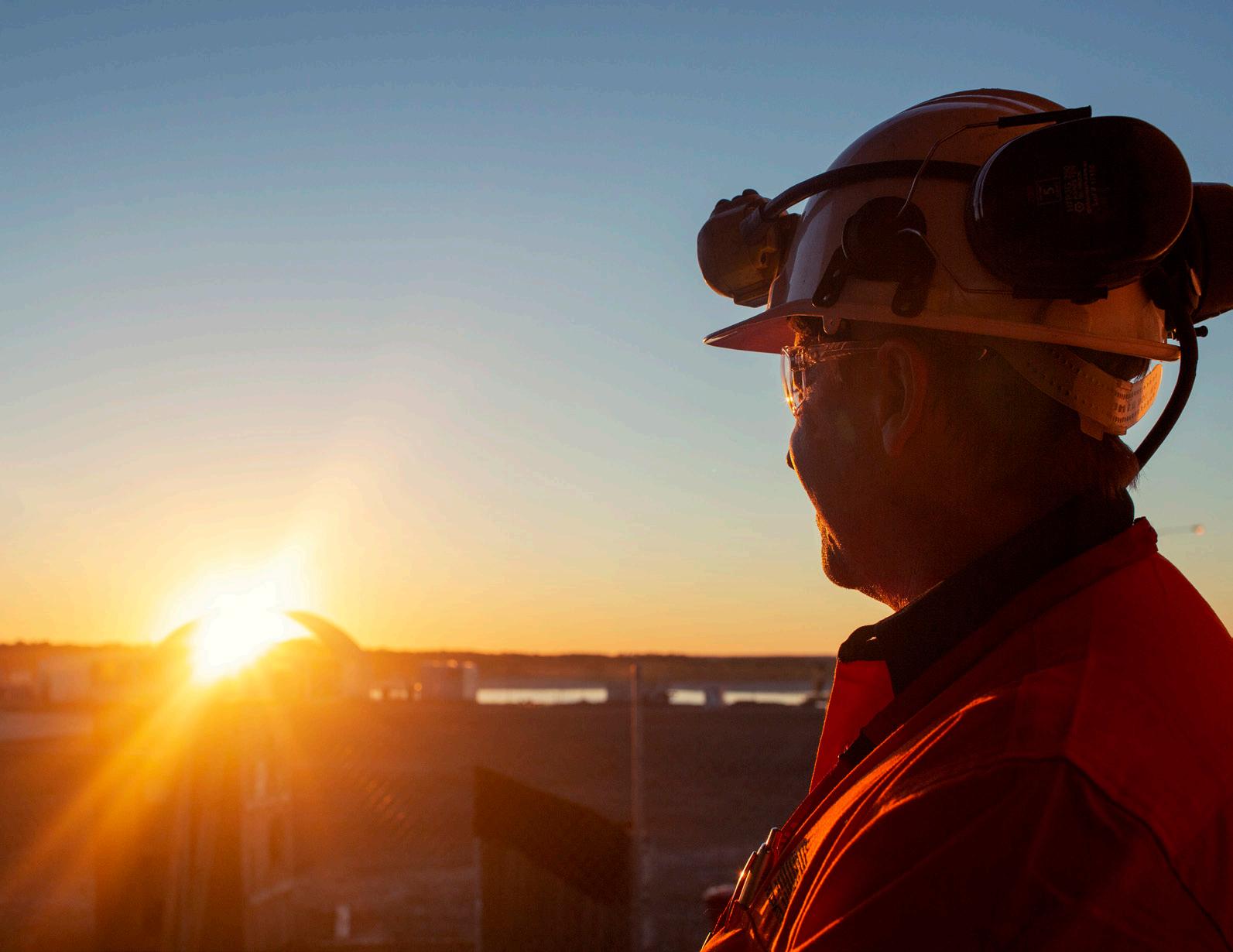
