

Our SRP
Sandvik Rock Processing Solutions
WELCOME
Dear colleague,
Welcome to a new issue of our global business area newsletter Our SRP and welcome back from vacation if you’ve had some. Even though the vacation period may seem like a distant memory I hope you had the opportunity to recharge your batteries and are ready for the successes and challenges of the remaining few months of 2024.
Safety #1
I want to start with safety. The second quarter with 6 Lost time injuries (LTIs) were followed by 1 LTI in August and in addition we had 1 Restricted Work Injury in July. In July and August we achieved both BA SRP 2024 targets on LTIFR and TRIFR and we have also had a significant increase in Hazardous close out ratio! It is important to continue in this direction towards the close out ratio target. Stay focused on safety so that we together continuously are improving in this area!
Some highlights
One recent highlight was the successful split between Crushing and Screening and all the planning that’s been done in a very positive way. When the people involved are enthusiastic to see it work then the details just follow! Another highlight was the fact that we generated better earnings on a relatively low invoicing level in Q2 and it sets us up very well for generating good earnings going forward, on a higher level of invoicing. For more highlights, please take a look in the newsletter which is filled with recent activities and achievements.
Going forward
Now going forward: In the short-term we need to hold our line because there’s no fundamental shift in demand right now. We also need to focus hard on the significant risks to safety in our facilities and thirdly we need to turn the corner on cash. We need to start to generate cash, take our stocks down and speed up the collection of overdue money from our customers.
The next report
I will get back in October with a Words from the President following the Sandvik Q3 report. You are also very welcome to join SRPs Q3 webinar which will be on October 24 (keep an eye out for the invitation on the intranet). Thank you very much for all your strong efforts so far this year. And thank you for keeping SRP as safe a place as possible.
Stay well and stay safe.
Richard Harris, President Sandvik Rock Processing Solutions
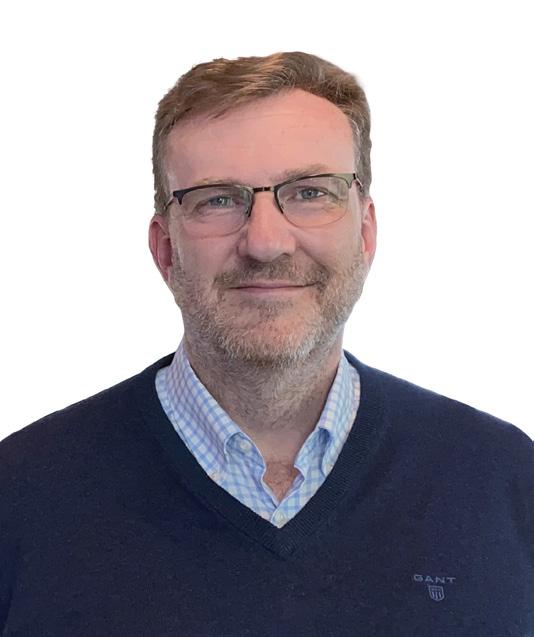
Health and wellbeing day in Lahti.................................
Towards a more sustainable future..............................
Svedala socializing sports area.....................................
Equipment gets new life...................................................
New President Mobiles Division.....................................
Welcoming our two new
First deal in Indonesia in many years...........................
Largest screening media order to date.......................
BHP awards strategic order to SRP Australia..........
The Takraf project reaches a new milestone............ Success story in China......................................................
Launch of Essential Maintenance packages............. Mobiles welcomes
Publisher: Conny Rask Editor and production: Åsa Myers asa.myers@sandvik.com +46 766 982 707
On the cover
Electra Mining Africa took place in Johannesburg, South Africa from 2 – 6 September 2024. Sandvik SRP was an exhibitor and presented the digital solutions we offer to our customers in Africa.
Read more on page 16.
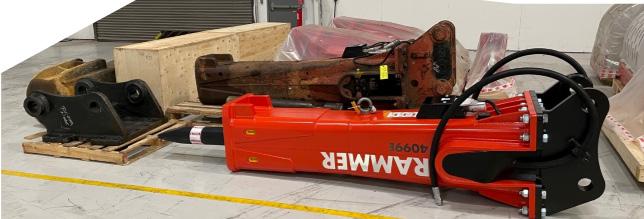
A Second Life - Launching the Renewed & Certified Program
In the first quarter of 2024, Attachment Tools North America introduced a new initiative aimed at promoting sustainability and driving profitable growth.
As a market leader, we recognize the need for more than just high-quality and productive products. We must also ensure circularity and a better future for our children. To achieve
this, we have launched the Rammer buyback program, designed to renew and certify our products for a second life. This program not only reduces our carbon footprint but also supports business growth.
We have implemented new processes and digital tools to provide a comprehensive solution, from our operations in Cleveland
Health and wellbeing day in Lahti
The Lahti Site (Attachment Tools Division) held its annual Health and Well-Being Day at the beginning of summer. The day was planned and executed by the occupational safety and health committee, in which all personnel groups are represented. The morning started with a healthy breakfast with friendly colleagues at the restaurant Rammer. It was a full house!
Every year, there are stands for the Health and Well-Being theme. This year, for example, you could test your eyesight or try new electric bikes. Around 80 colleagues took part in the day, testing new equipment, doing quick relaxation exercises, or participating in body movement measurements. The most popular stand has been, and still is, the InBody measuring station, a quick, non-invasive body composition analysis. People are following their development through their measurements. The goal of the day is to encourage wellbeing and provide helpful tips on how to achieve it.
More information: salla.nurmiranta@sandvik.com
to our sales teams and customers. Each renewed hammer sold through this program results in a CO2 saving of nearly 40% compared to the sale of a new hammer. More information: mikael.k.larsson@sandvik.com
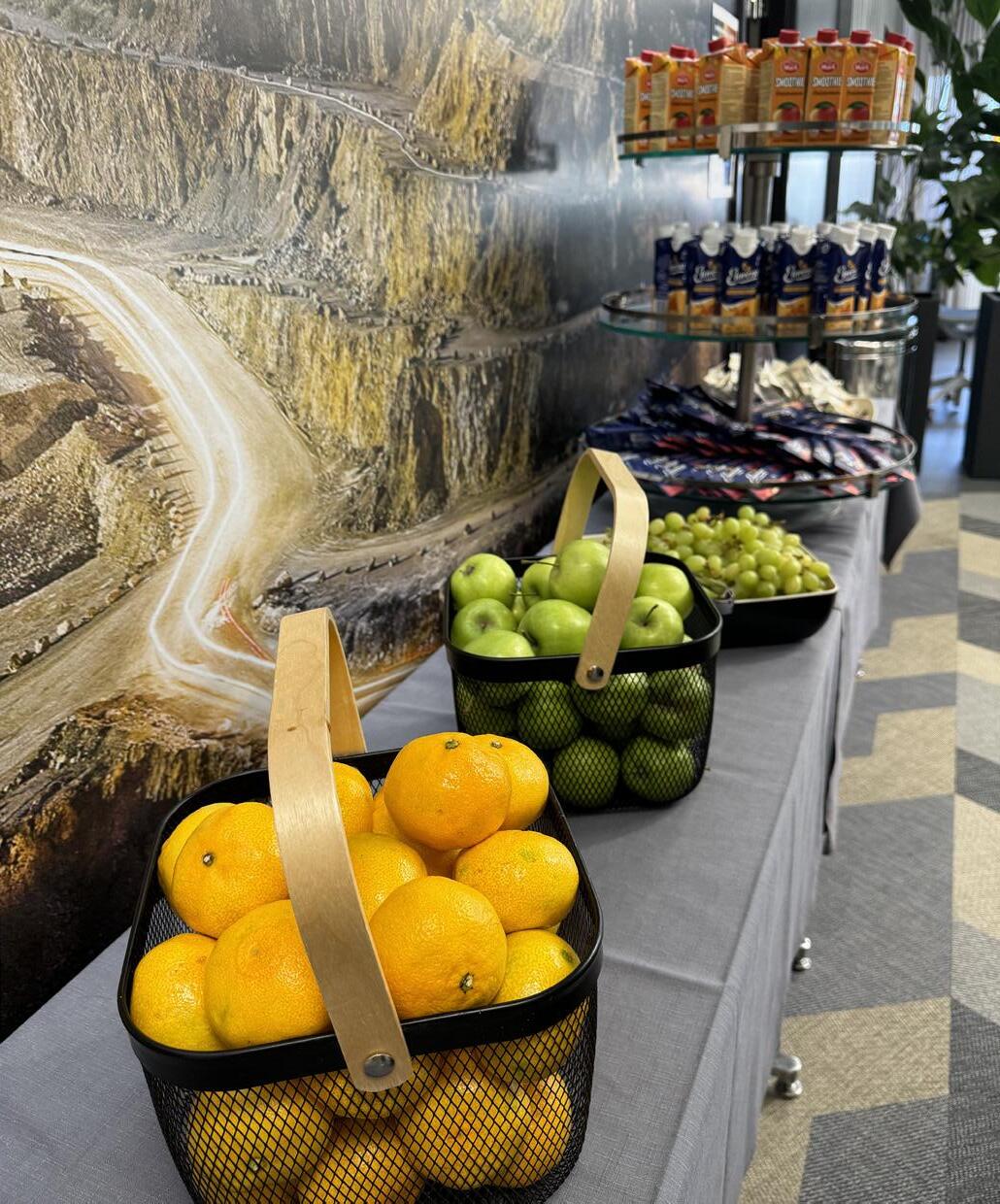
Towards a more sustainable future
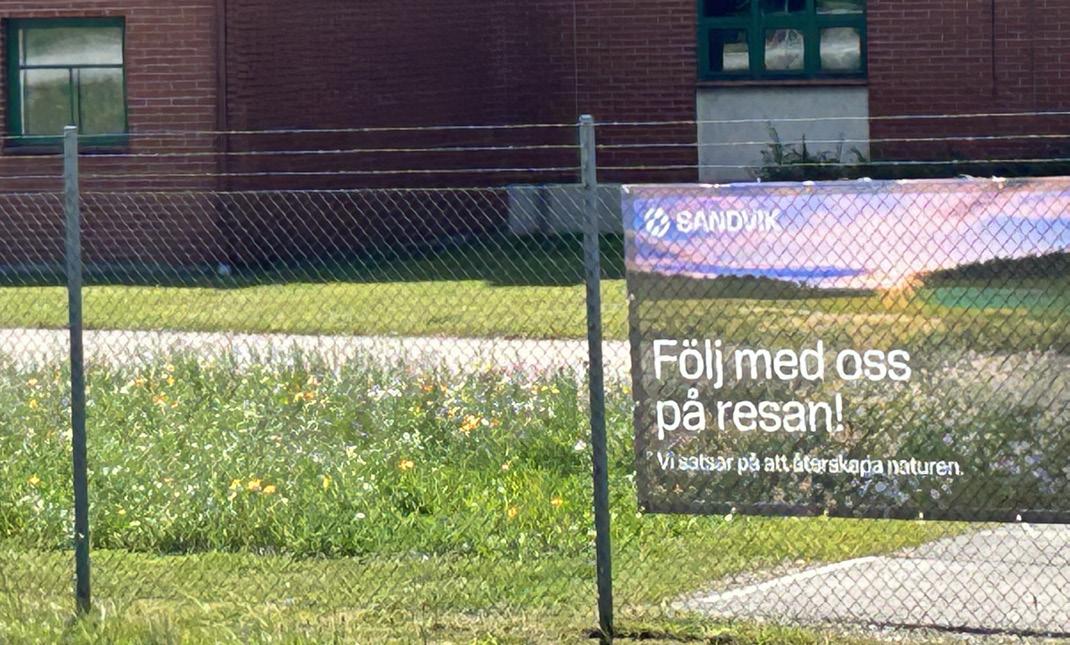
As a step towards a more sustainable future, the Svedala site in Sweden (Crushing Solutions Division) has put out insect hotels and planted two meadows with a big variety of flowers on the premises. The purpose of the meadows are to care about plant and insect life. One of the meadows can be seen if you arrive with the train to Svedala. The other is visible from one of the streets (Kyrkogatan). More information: asa.friberg@sandvik.com
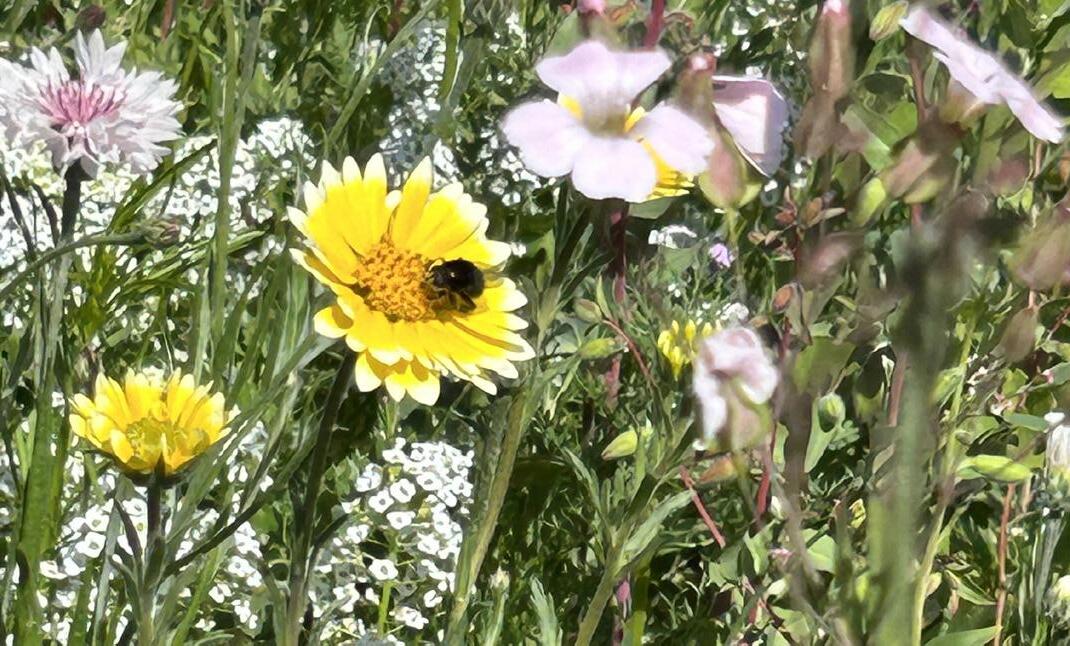
Grand opening of Svedala
Socializing Sports area
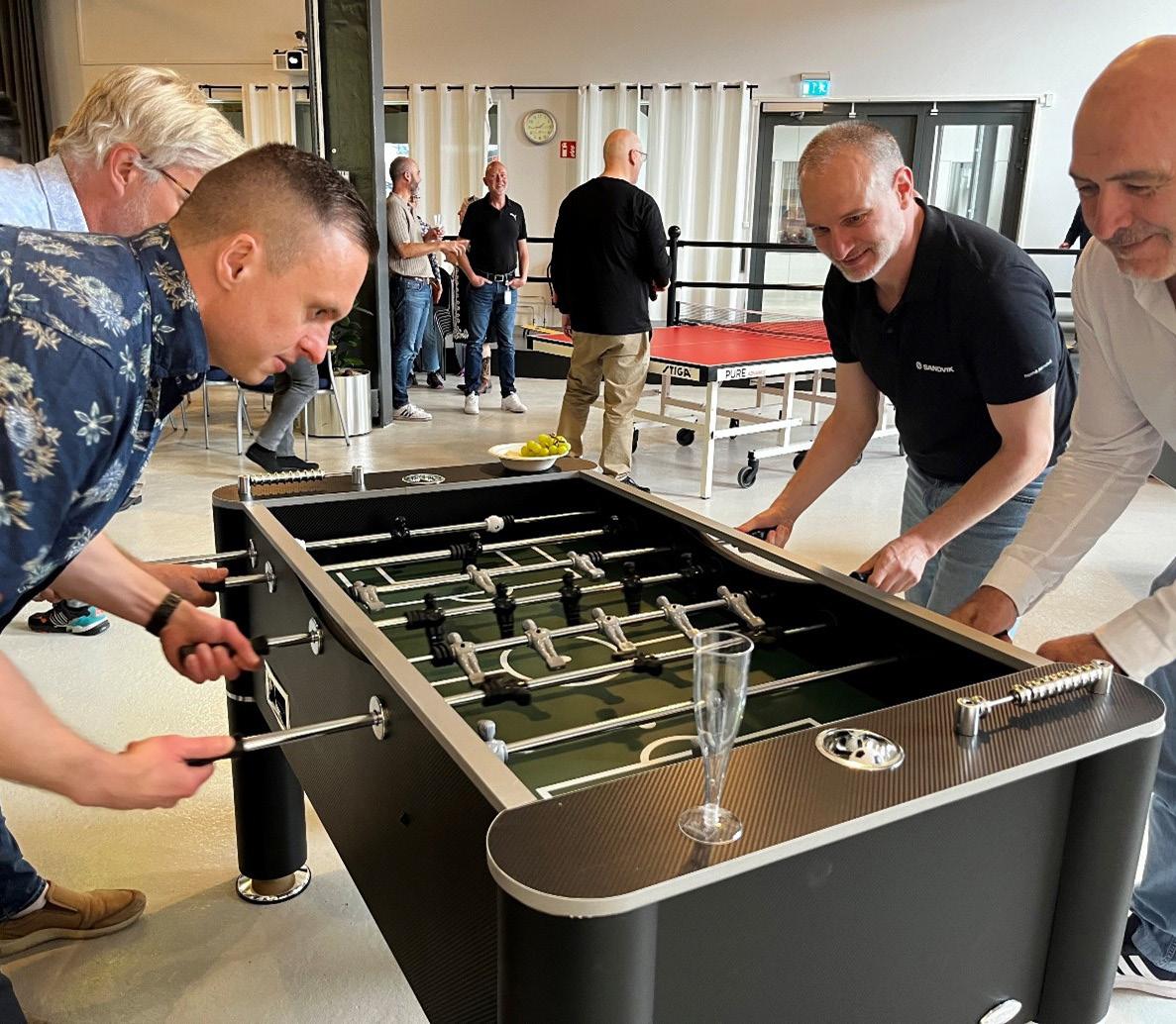
Based on feedback from the Peakon employee survey the Svedala site, Sweden (Crushing Solutions) identified an urge for more socializing activities, opening for better collaboration, cross-functional innovation and fun at work.
During a lunch workshop with the Diversity & Inclusion network we continued to elaborate this and one of the initiatives from the workshop was the Socializing Sports team that got the task to cater for spontaneous and fun ways of collaborating.
This in turn resulted in two set ups: one quiet dining room set-up with games and brain puzzles and a more active sports area set-up where we have gathered larger games, like fussball.
The first area was inaugurated just before the vacation period (at Stationsplan), and plans are well on the way to expand to other parts of the site as well. More information:mikael.lindberg@sandvik.com
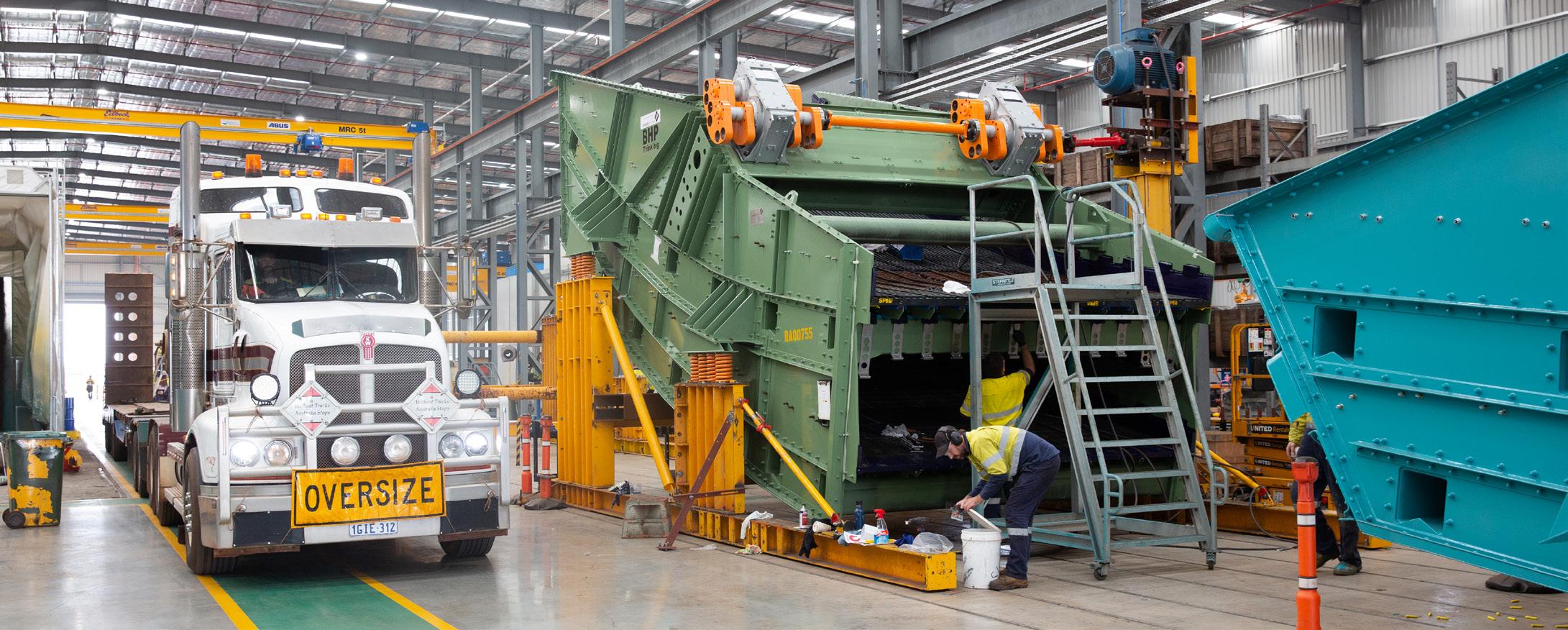
Equipment gets new life
Screening Solutions in Jandakot, Australia has developed a process to refurbish and reuse screens, feeders and exciters, thereby extending the life of the equipment and improving sustainability.
Every few years customers bring their used equipment back to Sandvik. Technicians inspect the equipment, determining what to reuse and what to replace. By the end of the process the refurbished product is as good as new. Last year approximately 1000 metric tons of metal were reused, preventing an estimated 1900 metric tons of CO2 emissions.
See how it’s done
Watch the video to find out more about this amazing initiative. The video was also included in the latest episode of Studio Sandvik
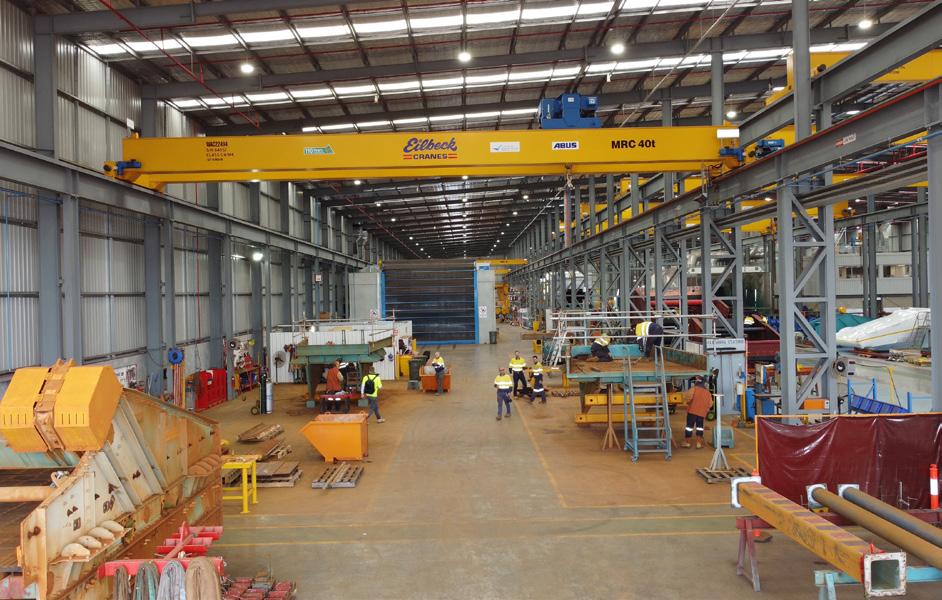
There are a lot of sustainability initiatives going on in our business. Stay tuned for some sustainability success videos that will be shared on the on the SRP intranet during the coming months. There will be examples from all of our divisions, from around the business area.
Manny Maloney new President, Mobiles Division
We are pleased to announce the appointment of Manny Maloney to the role of President Mobile Crushing & Screening Division, Sandvik Rock Processing Solutions, effective August 1 2024.
Since joining Sandvik in 2010, Manny has amassed extensive knowledge of our organization and the mining and construction industries, including in his last role as Vice President of Sandvik Mining and Rock Solutions’ (SMR) Sales Area South-East Asia.
With in-depth knowledge of the Sandvik organization and the mining and construction industries and over 20 years of international managerial experience, a professional legal background, and strong commercial acumen, Manny is well-equipped for his new role. Manny will be based in Stockholm (Sweden) reporting to the Business Area President as a member of the business area management team.
We look forward to working with Manny and in driving Mobiles Division to new heights. More information: manny.maloney@sandvik.com
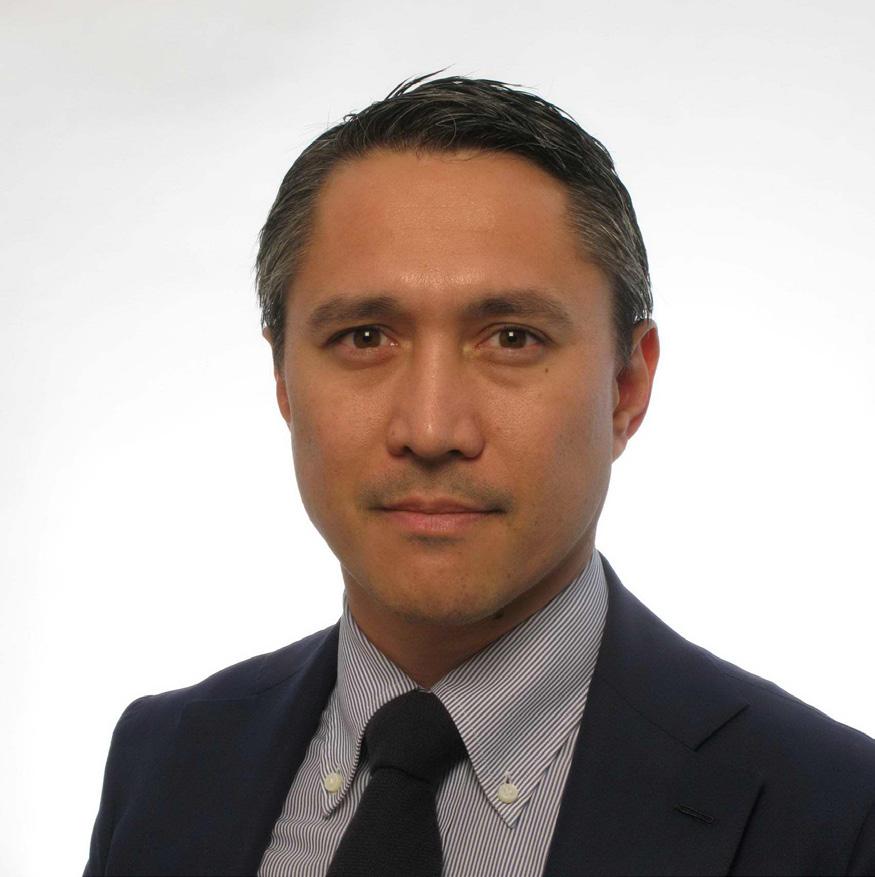
Welcoming our Crushing Solutions and Screening Solutions Divisions
On July 1, SRP’s Stationary Crushing & Screening Division was officially divided into two divisions: Crushing Solutions Division and Screening Solutions Division. All of this has been communicated on the intranet and and if you missed the information, you can read more about the details here, or by searching for “two new divisions” on the intranet.
The headquarter for Crushing Solutions, lead by Peter Unelind, is based in Svedala, Sweden, whereas Screening Solutions, managed by Terese Withington, has its headquater in Perth, Australia.
In the summer the newly formed Screening Solutions management team visited the Jandakot complex in Western Australia for their first face-to-face meeting (see image to the right).
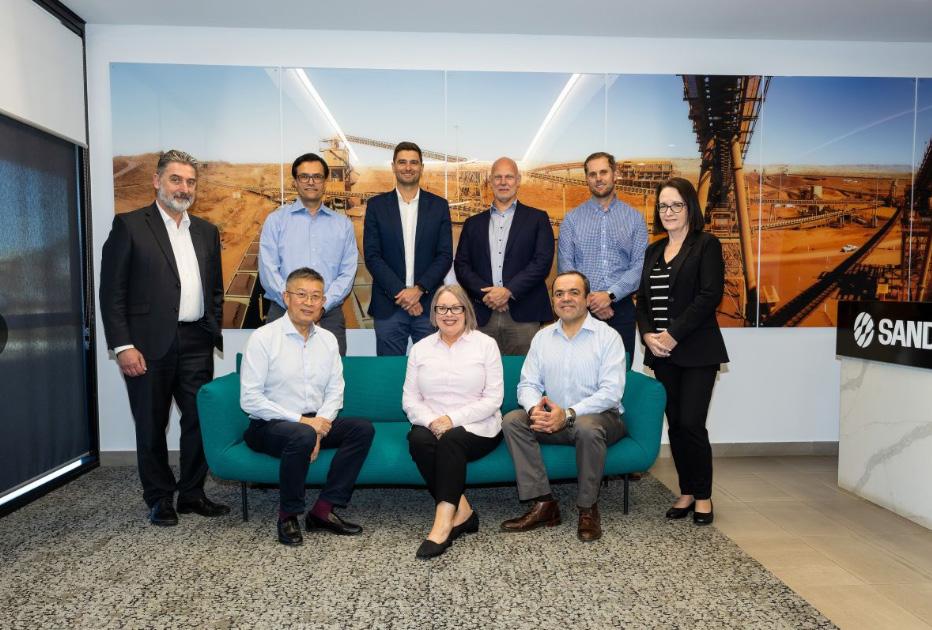
We are proud to announce that the integration of the Schenck Process (SP) mining business into Sandvik in Australia, is now complete. By combining our decades of expertise, innovative technologies and shared commitment to excellence, we are now strategically positioned to offer an unparalleled range of vibrating screens, feeders, crushers, screening media and train load-out to the mining and aggregates industries globally.
Milestones that Redefined Our Future
From the outset, our integration journey was driven by the vision to leverage the combined strengths of Sandvik and SP Mining to deliver cutting-edge, eco-efficient rock processing solutions. Among the significant milestones, one of the most symbolic was the rebranding of our first SP Mining screen in May. This
moment served as a tangible representation of our unified capabilities and a testament to the efforts of our Australian team.
Transformation on a National Scale
Since acquiring SP Mining in 2022, the integration has involved a series of transformative projects, each playing a crucial role in the seamless merger of the two entities. Notably, the rebranding of four major facilities across the country has provided a visual shift at these sites and is a powerful reminder of our commitment to excellence, innovation, and unified brand identity.
Empowering Our Workforce
In addition to rebranding our facilities, we have equipped our workforce with new Sandvik workwear and PPE, reflecting our focus
SP Mining integration in Australia completed
on both safety and unity. Similarly, our fleet of vehicles has undergone a refresh, signaling to the broader mining community that we are moving forward as one cohesive entity.
A Bold New Future
With these efforts now complete, we proudly display the Sandvik brand at Jandakot, North Ryde, Sunshine and Rockhampton in Australia. The completion of this integration is a transformational milestone that enables our business and customers to benefit from the combined innovative expertise of Sandvik and SP Mining, now under one powerful, unified brand. More information: peter.newfield@sandvik.com
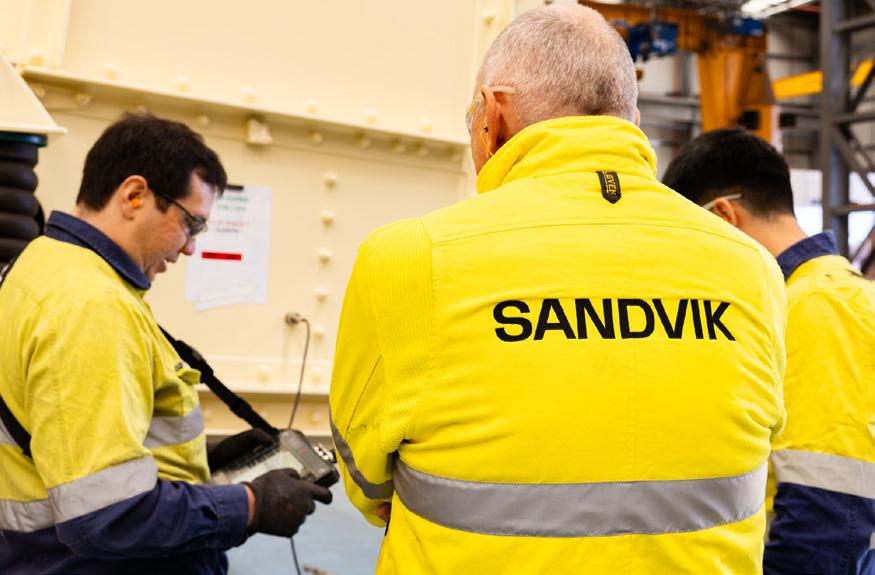
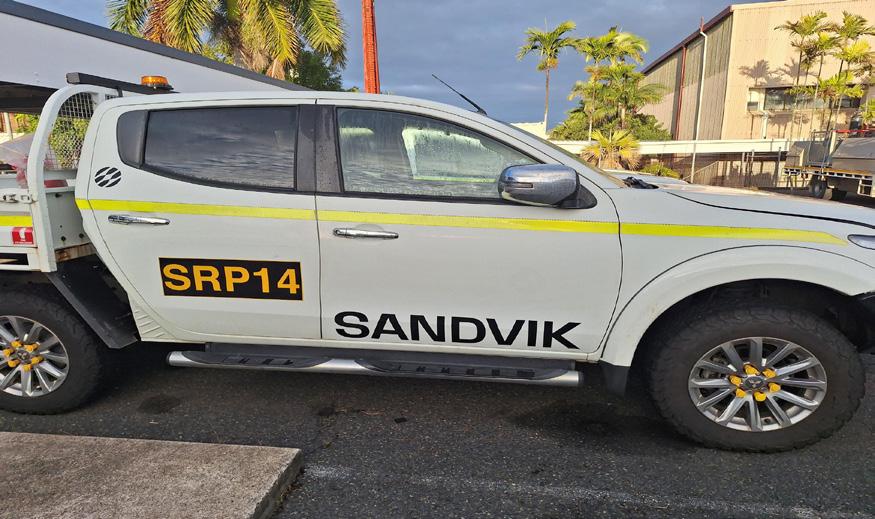
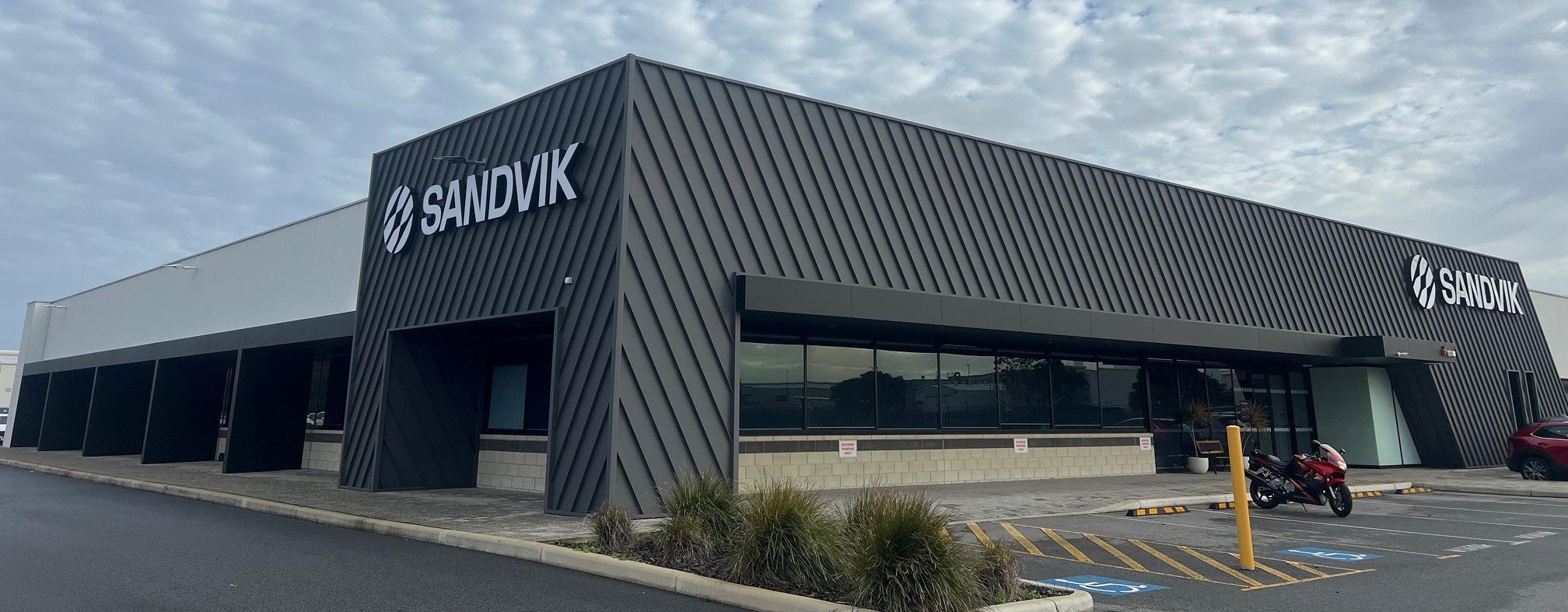
The Jandakot facility
New from Digital, Service & Automation
Automation, ACS-c 5
Thanks to great teamwork and customer focus we have managed a successful upgrade of Seepsulas old SanRemo systems in Finland. They are up and running in full production with their brand-new ACS-c 5 systems. The system was commissioned faster than planned and the design is working as expected. We were also able to make quick adjustments to the hardware deliveries and gathered feedback for further improvements while supporting the customers remotely. A happy customer and great effort from everyone involved!
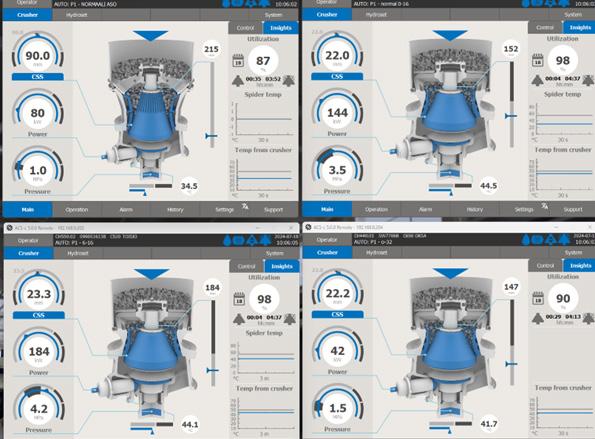
SAM
Connected
SAM connected continues to grow. During the second quarter and northern hemisphere summer vacation period we successfully connected five crushers with one of our major customers TATA Steel, making them the first connected site in India. We have now pushed the number of connected units globally to over 90 connected crushers! During Excon 2023 we had the opportunity to showcase SAM to a number of customers leading to several connected units that will be onboarded to SAM during the year.
Our connectivity journey will continue during the year with new connections in NEU, SEMEC, LAM and NAM with customers aiming to connect several crushers at their sites!
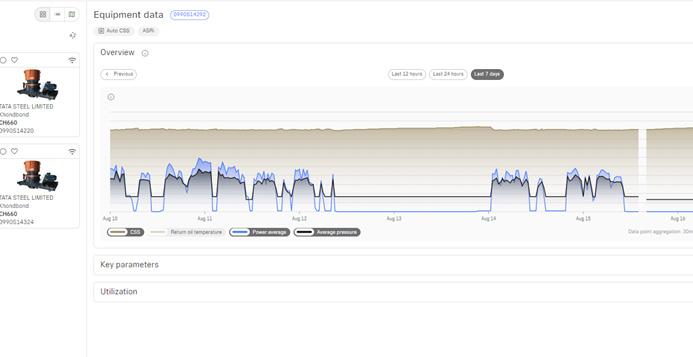
Remote Monitoring Service for crushers
A successful Remote Monitoring Service (RMS) pilot during the beginning of 2024 earned us our first paying customer and solidified our ambitions to push RMS to several sales areas. Our next steps towards launching RMS globally will be to study our customers’ needs
with more pilots, which will help us to further define the offering and to scope the process for our future Remote Monitoring Technicians. During the third and fourth quarter we have plans to initiate pilots with our mining customers in LAM and in Africa.

Seeing is no longer believing
Seeing is no longer believing, is the name of the cybersecurity awareness campaign that is taking place internally at Sandvik in October.
Raising awareness
The campaign is focusing on raising awareness of the effects that AI has on cybercrime and what happens when we no longer can believe what we see. How can we protect ourselves as a company and as individuals. The campaign will start with a nano-learning on the topic
already in September. There will also be information on the intranet and two online events October 22. One event for everyone at Sandvik and one focusing on finance.
Cybercrime is a constantly growing business, and with the general development in technology, where AI is a major component, cybercriminals are getting a boost with better and easier fraud methods. More information: monika.kullberg@sandvik.com
Intelligent Process Automation
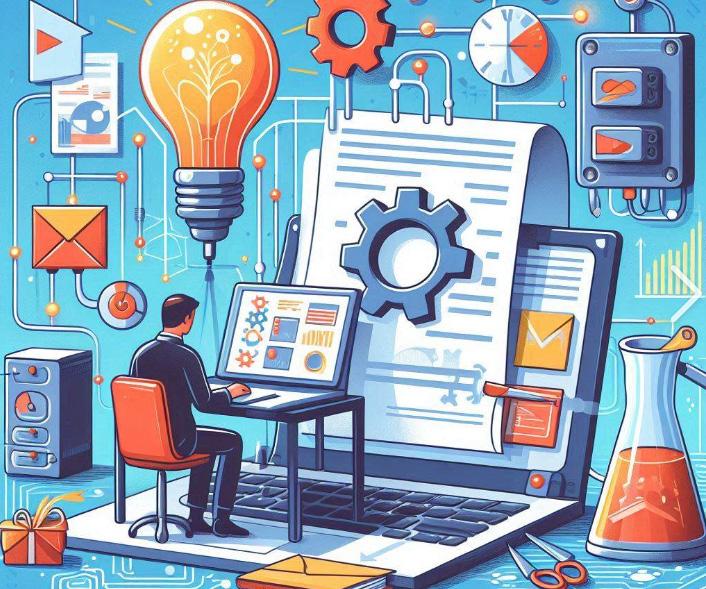
Since summer a new platform for Sandvik Group is in place, moving our process automation capabilities to UIPath.
With Intelligent Process Automation (IPA) we can enable the varying businesses within Sandvik SRP to take advantage of automation opportunities, such as:
• Reduce the time and effort required to complete routine or repetitive tasks, allowing employees to focus on more complex or value-added activities.
• Improve the speed and accuracy of customer-facing processes. This can lead to a better overall customer experience and increased customer satisfaction.
• Reduce the likelihood of errors and inconsistencies in business processes, resulting in improved quality and accuracy of outputs.
If you want to know more about IPA or if you have an automation idea within your business process then contact BA IT or create a request for a new IT Demand
Let us work together to create automated business processes to improve customer and employee satisfaction. More information: maud.ekman@sandvik.com
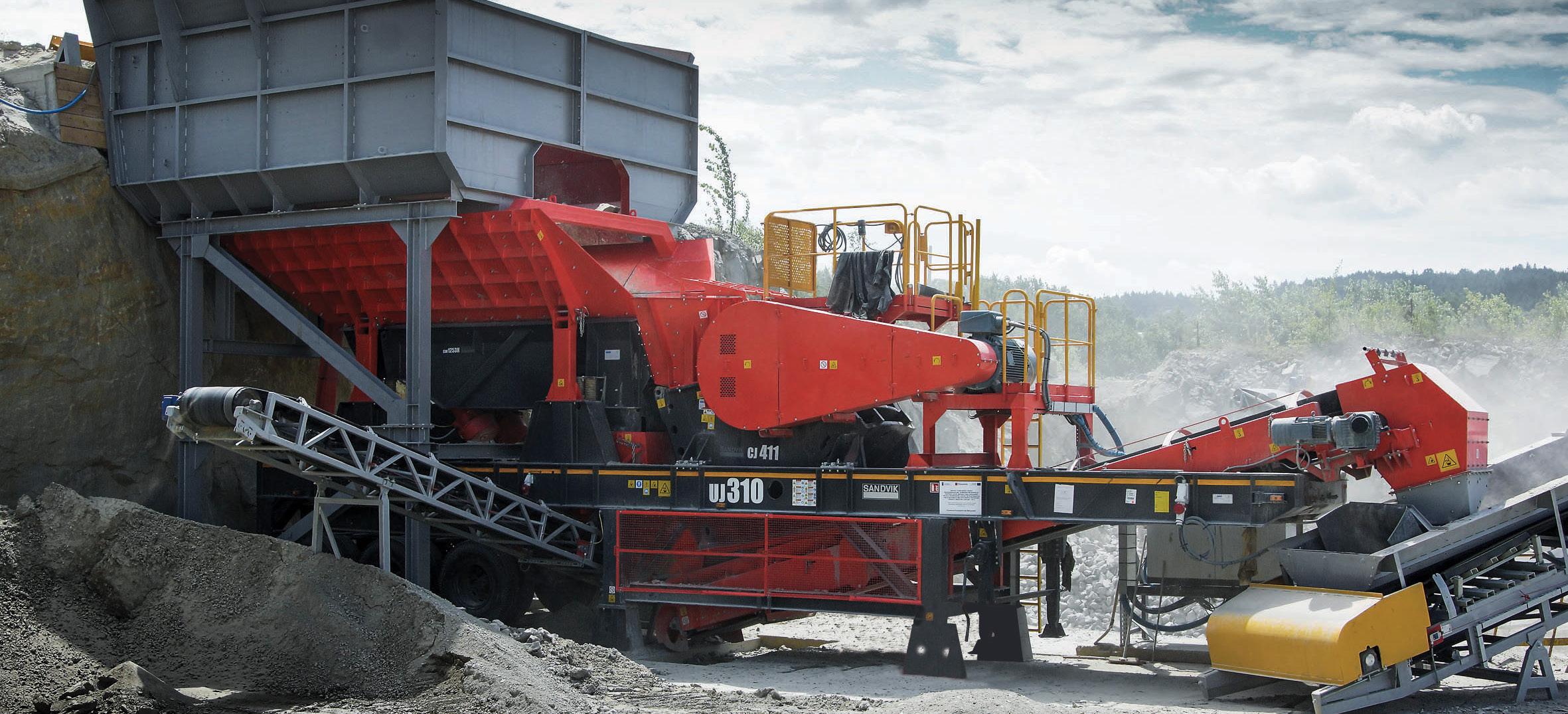
Mobiles Division
First deal in Indonesia in many years
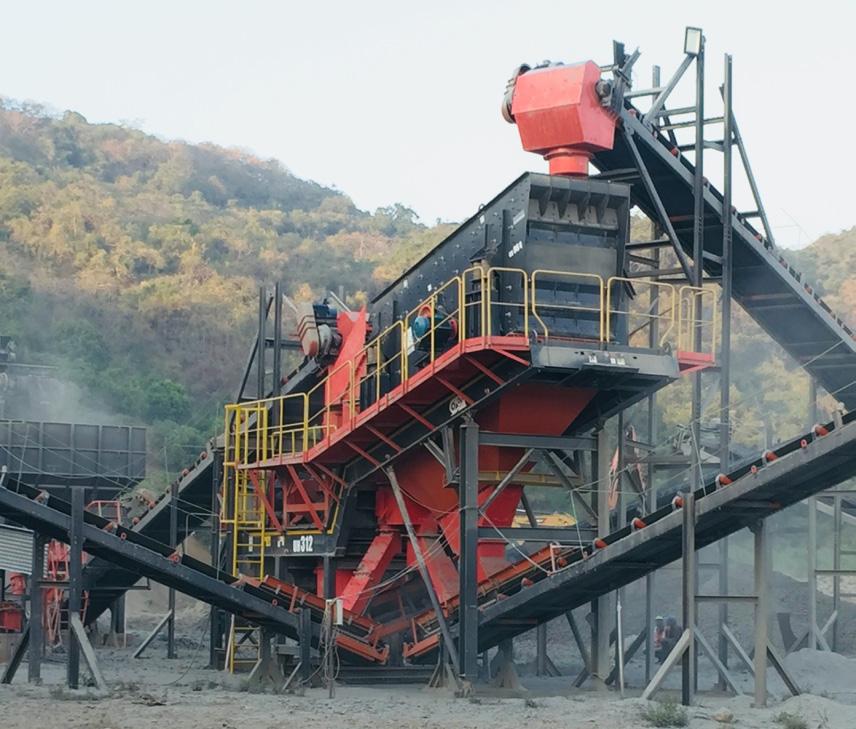
After a ten month bidding process and negotiation, Mobiles Division, in collaboration with the Indonesia sales team in sales area Oceania (Crushing Solutions Division), was appointed to supply a fully electric UJ310 wheeled jaw crusher, a UH312 wheeled cone crusher and adjoining plants to the Pani Gold Project.
The Pani Gold Project in Gorontalo, Sulawesi, Indonesia, will become one of the largest primary gold mines in Indonesia. The project is owned by PT Merdeka Mining Indonesia, a subsidiary of Merdeka Copper Gold, a major mining company. During the tender process, the project design and schedule kept changing within a tight four-month time
frame. This included changes in crusher requirements from fully-mobile to semi-mobile, alongside capacity requirements and the product size changing. Additionally, there was a request for a fully-electric equipment to comply with environmental demands.
The Indonesia sales team and Mobiles Division worked closely with the customer’s project team to find the best solution for their current and future requirement. This deal is the first order for Mobiles division in Indonesia in many years, and is a strategic step for Mobiles Division and SRP as there are several expansion projects in which SRP expects to be involved. More information: castanea.sylva@sandvik.com
Fully electric Sandvik UJ310 wheeled jaw crusher like the one which will be sent to Indonesia, here with the old branding. Below: UH312 wheeled cone crusher (also with old branding).
The screening media business in Africa is a high priority strategic growth area for our business and represents an important part of the business case rationale for the acquisition of SP Mining. The order consists of 1,300
305x305 polyurethane panels for a mining customer in Zimbabwe. Special thanks to everyone involved in this order. The collaboration was an exceptional display of Passion to Win and Customer Focus.
Largest screening media order to date
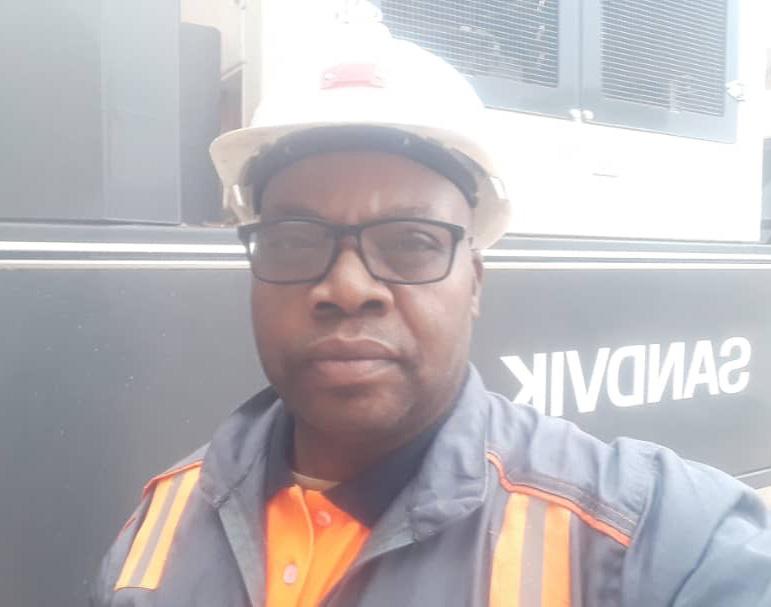
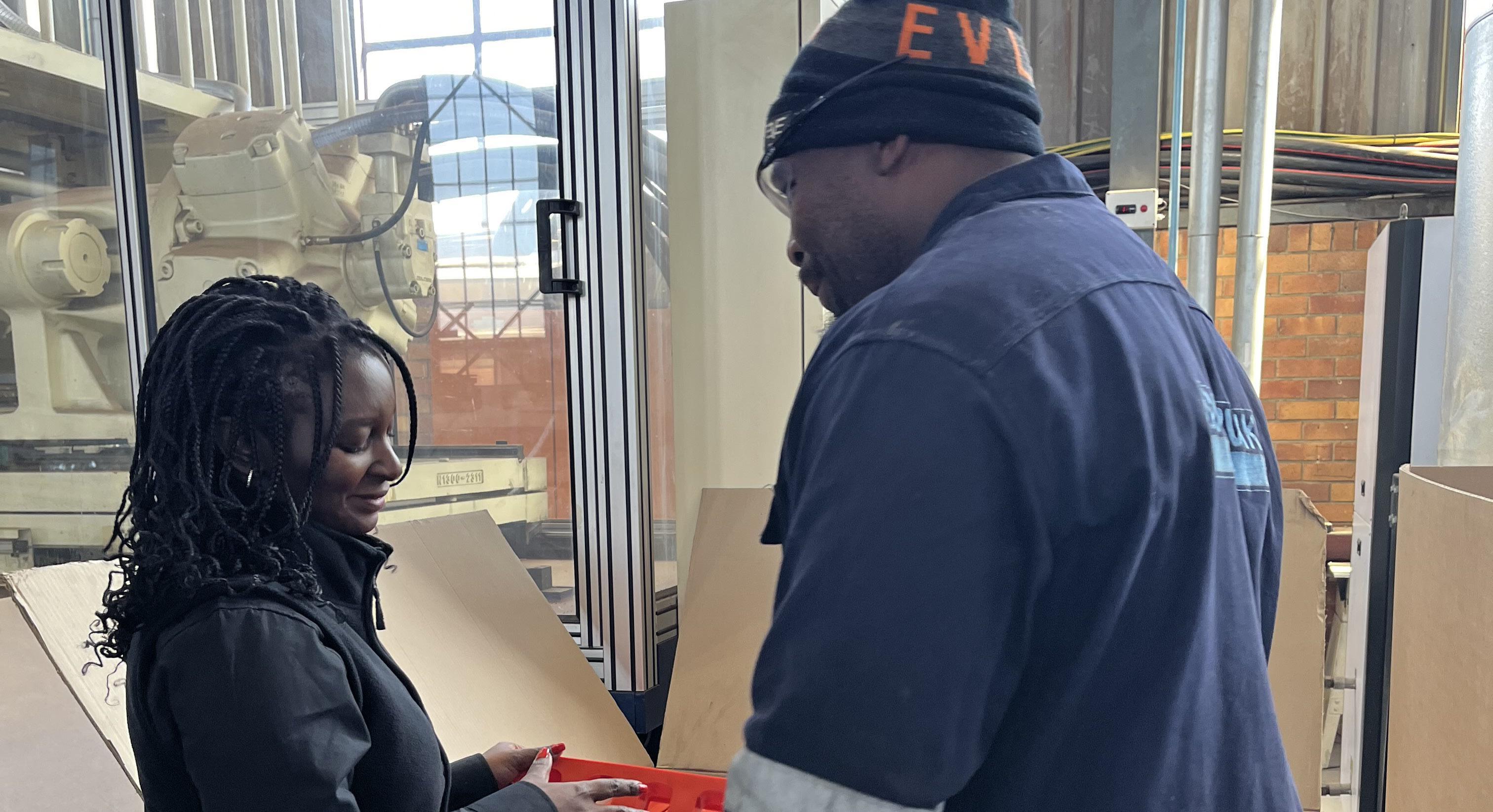
David Kavayi, Field Service Technician SRP was involved in the customer engagement for the order
BHP awards strategic order to SRP Australia
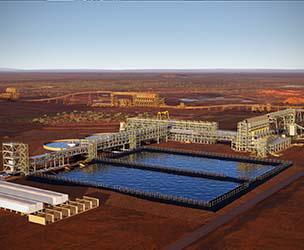
SRP Australia is excited to announce the signing of a new design and supply contract worth 115 million SEK with BHP, a global leader in the iron ore segment. This strategic order marks a significant milestone for SRP Australia and underscores our commitment to delivering solutions and exceptional value to our clients. The new contract, which was finalized on 26th August, includes the design and supply of eight SM4901M (4.9m wide x
9.7m long) single deck linear motion vibrating screens complete with isolation underpan. The massive machines will be installed at BHP Jimblebar’s new beneficiation plant, the first major wet processing facility for BHP’s Western Australian Iron Ore Operations in four decades. BHP currently operates the Jimblebar mining hub in the Pilbara region of Western Australia, approximately 39 km east of Newman. The current Jimblebar fines
product has a high proportion of gangue minerals relative to the benchmark product specification.
Beneficiation is a process that improves the economic value of the ore by removing the gangue minerals resulting in a higher-grade product (concentrate) that attracts premium pricing. More information: ami.parimoo@sandvik.com
The TAKRAF project reaches a new milestone
As previous announced Sandvik SRP has been awarded a 5,5 MUSD contract in December 2023, to supply Crushing and Screening equipment through our partner TAKRAF for the SNIM iron ore mine in Mauritania. SNIM (Société Nationale Industrielle et Minière) is the 2nd largest African iron ore producer with a 12 million tons yearly supply.
TAKRAF’s scope is the complete iron ore in-pit crushing, screening and material handling system together with a train loading station in Mauritania, while Sandvik’s scope is CG820, CH870, SP1630M, SL2462, XL1020 Boom breaker and Electrical equipment. The expected delivery is in Q2, 2025.
The project has now reached the second payment milestone of 30 %. More information: goran.petrevski@sandvik.com
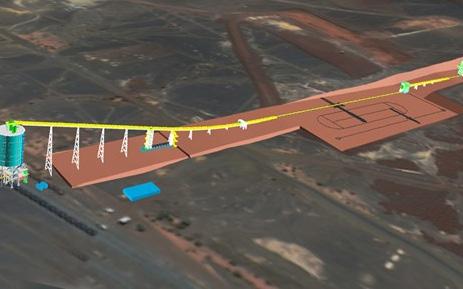
In the spring of 2024, Chinese iron mine producer Xinkaiyuan Mining renewed its service agreement with SRP for the third time. The company has five Sandvik crushers, which have been running with high efficiency and no unplanned stops since 2017 (CS430 x1 & CH660 x2), 2019 and 2021 respectively (CJ412 x2).
Between 2013 and 2017 Xinkaiyuan Mining’s production had to be shut down due to a market decline. When the operations restarted in 2017 SRP service engineers conducted an audit followed by maintenance and on-site training of operational staff, to ensure that the Sandvik machines (purchased in 2013)
were in best condition. The first service agreement was then signed at the end of that year.
Significant increase
Since then, our lifecycle services team has enabled Xinkaiyuan Mining not only to maintain reliable production – with no unplanned stops – but also to continuously optimize the production process in response to changing production conditions. Since the ore grade in the mine is changing, Sandvik experts have, for example, conducted annual comprehensive analysis to identify production bottlenecks, and propose solutions for an optimized mining process.
The service solutions have resulted in reduced safety risks, a reduced workload for the operational staff and a significant increase in production efficiency. The production line capacity has increased by 20 percent - from 500,000 to 600,000 metric tons per year!
The lifecycle services team continues to support the Xinkaiyuan Mining iron mine production and together we will achieve even better unplanned downtime records and capacity improvement targets. More information: asa.carlsson@sandvik.com
Success story in China
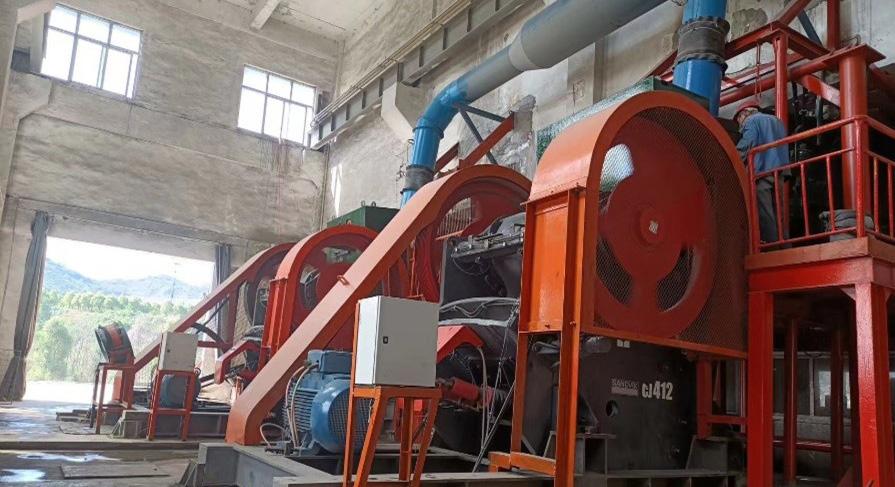
Mobiles Division Launch of Essential Maintenance Packages
Sandvik launches new Essential Maintenance Packages for its range of mobile crushing and screening equipment to help customers obtain peak performance & maximize uptime.
With the new lifecycle offering of Essential Maintenance Packages, Sandvik has designed an effective solution for customers to maintain their Sandvik mobile unit, providing all the necessary parts for up to 1,000 hours of operation in one convenient package.

Customers will get everything they need in one convenient kit, to carry out the work themselves. The packages are easy to order with one part number and come with an easyto-follow step-by-step guide for self-sufficient maintenance.
The kits include all necessary items specific to each model and application, including parts to cover engine drive-train and plant maintenance components. They can be
Mobiles Division
purchased with or without wear items (+) to suit the specific needs of the application. All items are clearly marked, color-coded and easily identifiable. More information: melissa.baker@sandvik.com
Sales territories Finland and Sweden visit Ballygawley

Mobiles Division recently welcomed sales territory Finland and also Sweden, alongside customers to the production site in Ballygawley, Northern Ireland.
During the visit the teams were taken to a local quarry to see the Sandvik UJ443E heavy jaw crusher working alongside a number of prototype machines. Following the site visit, the team had a tour of the production site and saw a number of key products on the production line. More information: andrew.haldane@sandvik.com
Image left: The Finnish sales team and customers during their visit to Ballygawley
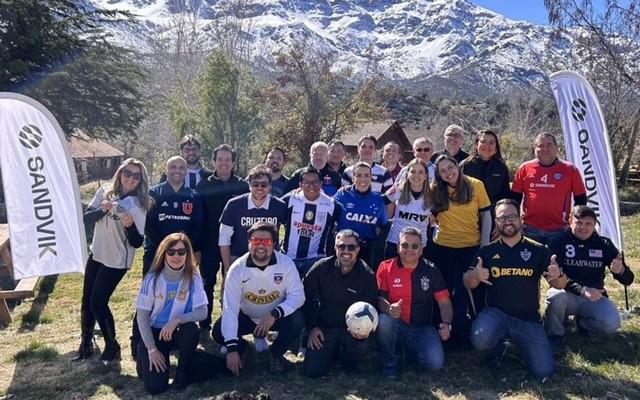
Sales Area Latin America
Extended Management Team meeting
We’re excited to share the highlights from our recent SRP Latin America extended management team meeting, which took place in Chile, from the 6th to the 8th of August. Beyond strategy discussions and knowledge sharing, this event underscored the power of coming together and building genuine connections.
Leadership has evolved from a focus on physical strength to intellectual capability, and now, we recognize that the human element in a tech-driven world, is a strength. Technology transforms processes, but only genuine human connections enable us to lead with empathy and foster a collaborative, sustainable work environment. In this year’s meeting we had the opportunity to deepen our bonds, celebrate our diversity, and strengthen our team spirit and commitment to create a space where everyone feels valued and motivated.
True leadership transcends technical skills — it’s about inspiring and supporting each other with deep, sustainable and shared values and we’re very excited to apply these insights and shape a future with a positive impact in our business and industry. More information: cristiane.fontes@sandvik.com
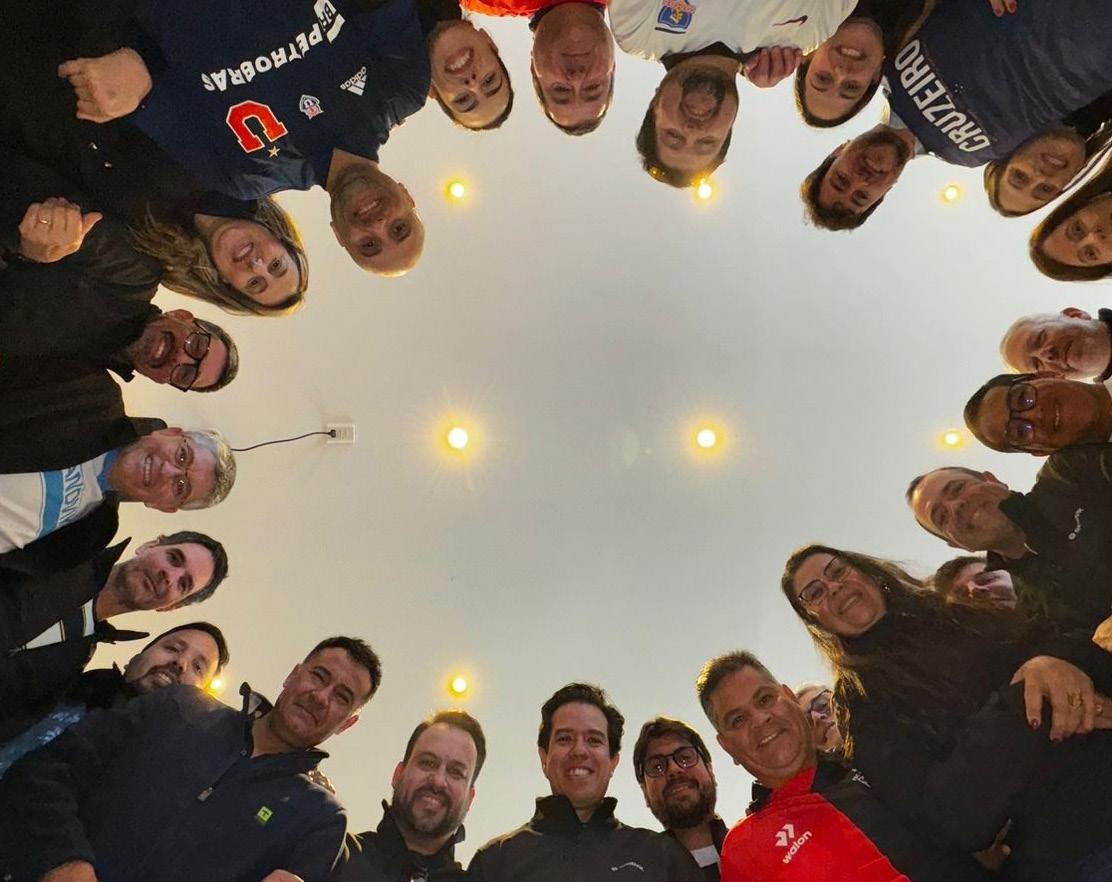
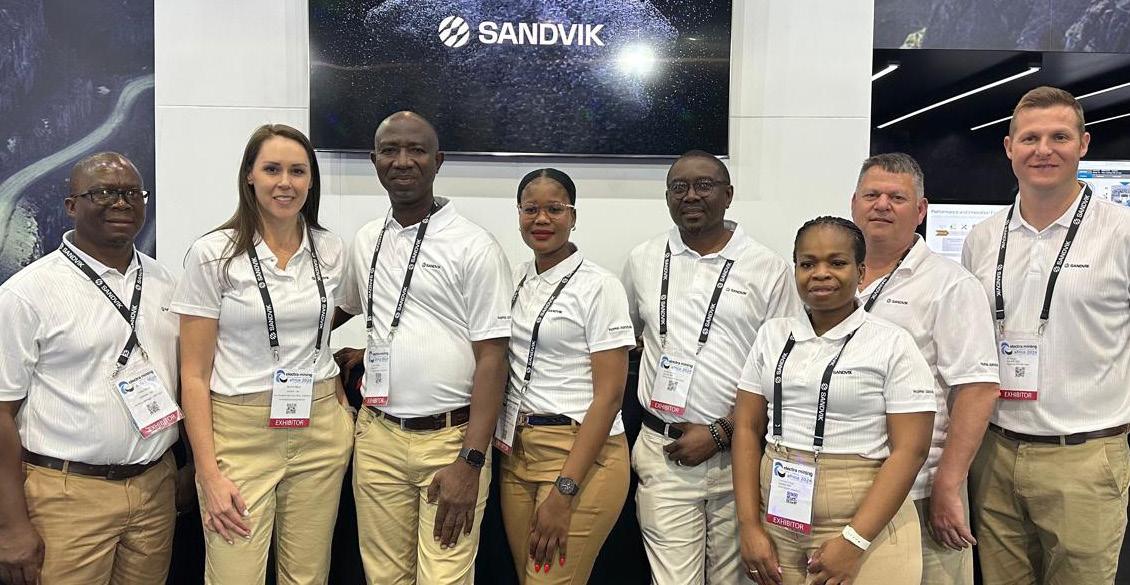
Great week at Electra Mining Africa
Electra Mining Africa took place at The Expo Centre, Nasrec in Johannesburg, South Africa from 2 – 6 September 2024. Electra Mining is one of the largest trade shows in Africa. Sandvik SRP was an exhibitor and presented the digital solutions we offer to our customers in Africa.
We exhibited as Sandvik Rock Processing and showcased our integrated crushing and screening solutions, emphasizing the ways in which automation and digital solutions may benefit customers in terms of increased output, reduced costs, and sustainability.
Additionally, we invited a few prestigious publications with an emphasis on Africa to our stand and discussed our transition to how Sandvik is driving the shift to eco-efficient rock processing. The team had an opportunity to interact with existing and potential customers and key mining industry stakeholders.
We had a great week at Electra Mining Africa thanks to positive customer interactions. Our presence improved connections with current customers and laid the groundwork for future communication and cooperation with prospective customers. More information: marilyne.modern@sandvik.com
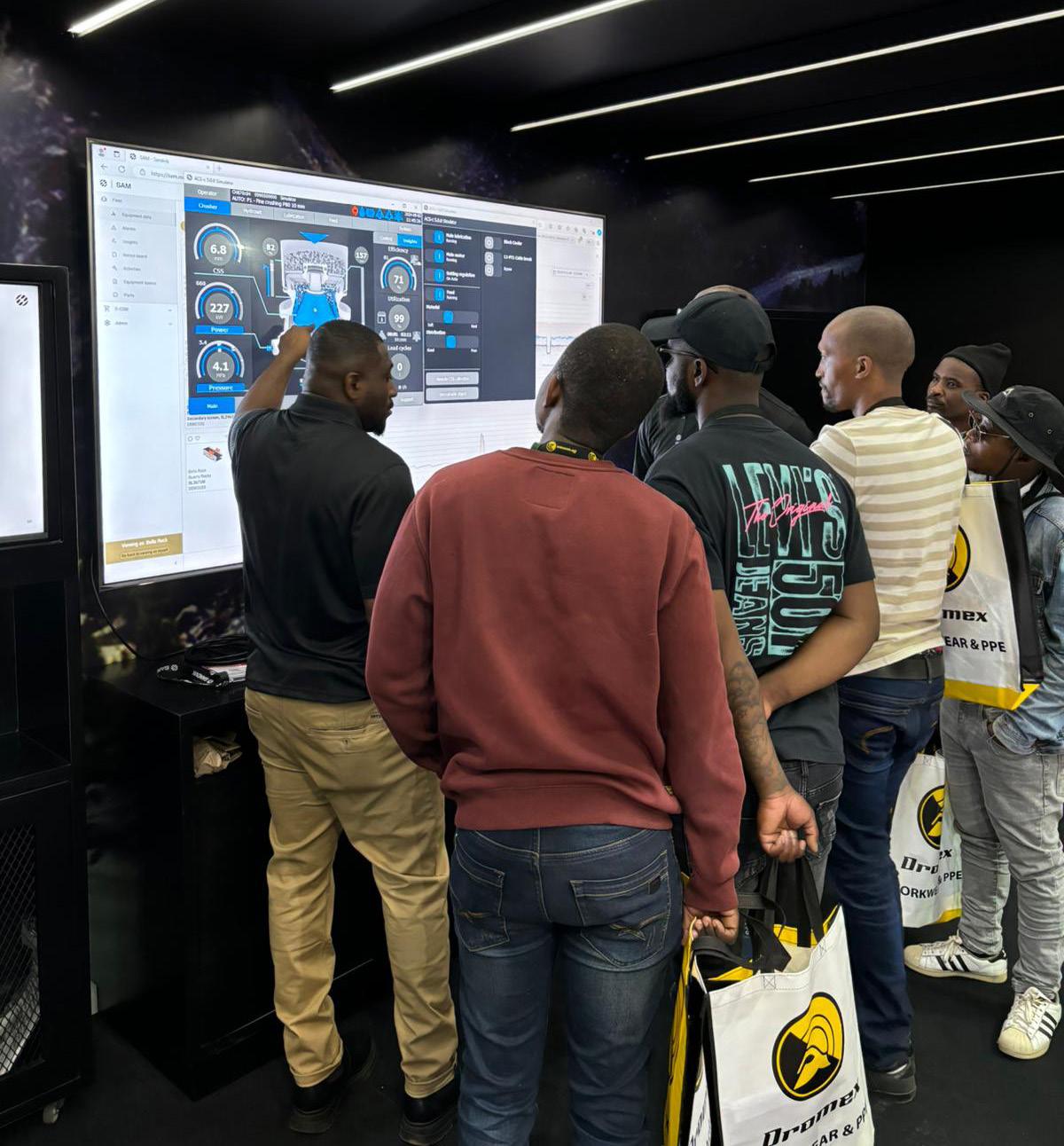
Sales Area Latin America Events in Peru
The month of July, celebrated as the Independence Month of Peru, was particularly eventful for us, with several key activities in the country.
We held our annual meeting, which not only celebrated Peru’s vibrant culture and rich history but also highlighted the region’s significant contributions to our industry. The event showcased the warm hospitality of our local team and their exceptional technical expertise, reaffirming the synergy and collaborative spirit that drive us forward.
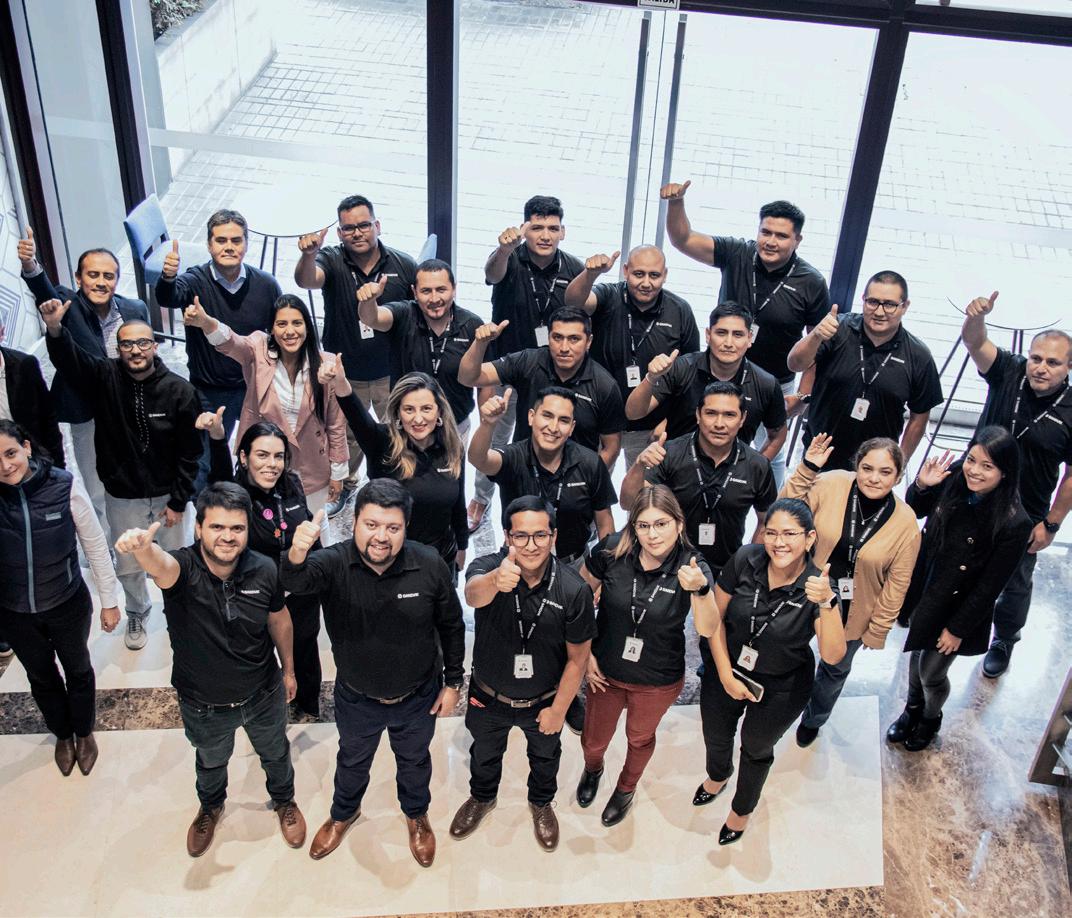
In addition, we had the privilege of participating in the Encuentro Minero Surface 2024 in Trujillo, organized by CONAMIN. This event provided an excellent opportunity to connect with key leaders in the mining sector and strengthen our relationships with valued clients. We presented our high-capacity crushing and screening solutions, emphasizing their role in enhancing operational efficiency and advancing sustainable mining practices. We also took part in the T&T Congress, where we introduced our HX900 wear protection solution, designed to maximize durability in
challenging conditions. The success case of this solution’s application at Vale in Brazil generated significant interest among attendees, showcasing the potential of the HX900 in the market.
These activities reinforce our commitment to excellence and innovation, allowing us to strengthen our relationships in the region and drive our growth in the Latin American market. More information: cristiane.fontes@sandvik.com
Quarry Academy® seminar 2024
The Quarry Academy® seminar will take place on November 19-21, in San Antonio, Texas (USA). This educational seminar looks at the full production stream of surface quarry operations and shares best practices on how to produce aggregates in an efficient manner. It is run in a three-day format, which includes lectures, workshops, use of simulators and a visit to Cemex’s Balcones site, one of the largest limestone aggregate quarries in the USA.
The popular program is organized jointly by Sandvik Rock Processing and Sandvik Mining and Rock Solutions, together with Dyno Nobel. 2024 marks the 18th year this event has
taken place in the USA. It is primarily aimed at aggregate producers in the industry, with capacity for up to 150 attendees. Spaces for Sandvik employees will be very limited and will be assigned on a first-come, first-served basis. If they are sold out, you will be added to a waitlist. However, if you attend with customers, you will be guaranteed a spot.
For further details, please contact virginia. varela-eyre@sandvik.com or visit: www. quarryacademy.com or see the intranet news published on June 13: Quarry Academy® seminar 2024 : registration is now open | Sandvik Intranet

Mobiles Division
New distributor appointed in Armenia and Georgia
Mobiles Division recently appointed Armstrong LLC in Armenia and its sister company of GLK Machinery in Georgia as new distributor. They will be responsible for selling Sandvik mobile crushers and screens in combination with full aftermarket support through the supply of spare parts and local customer service.
Armstrong and GLK are leaders in the distribution of a wide range of heavy equipment in segments such as material handling, crane technology and mining in the South Caucasian Region. Based in Yerevan, the capital of Armenia, they are active in Armenia and Georgia and
offer their customers premium equipment developed and produced by leading brands in these segments. Their stated mission is to provide customers with the most modern construction and materials handling equipment available today. In addition they promise a high level of aftersales service and a dedicated specialized team, with customer satisfaction always at the forefront.
GLK LLC has also recently purchased two wheeled units, a UJ210 jaw crusher and a UH311 cone crusher for a new quarry in the region. More information: kamran.akram@sandvik.com


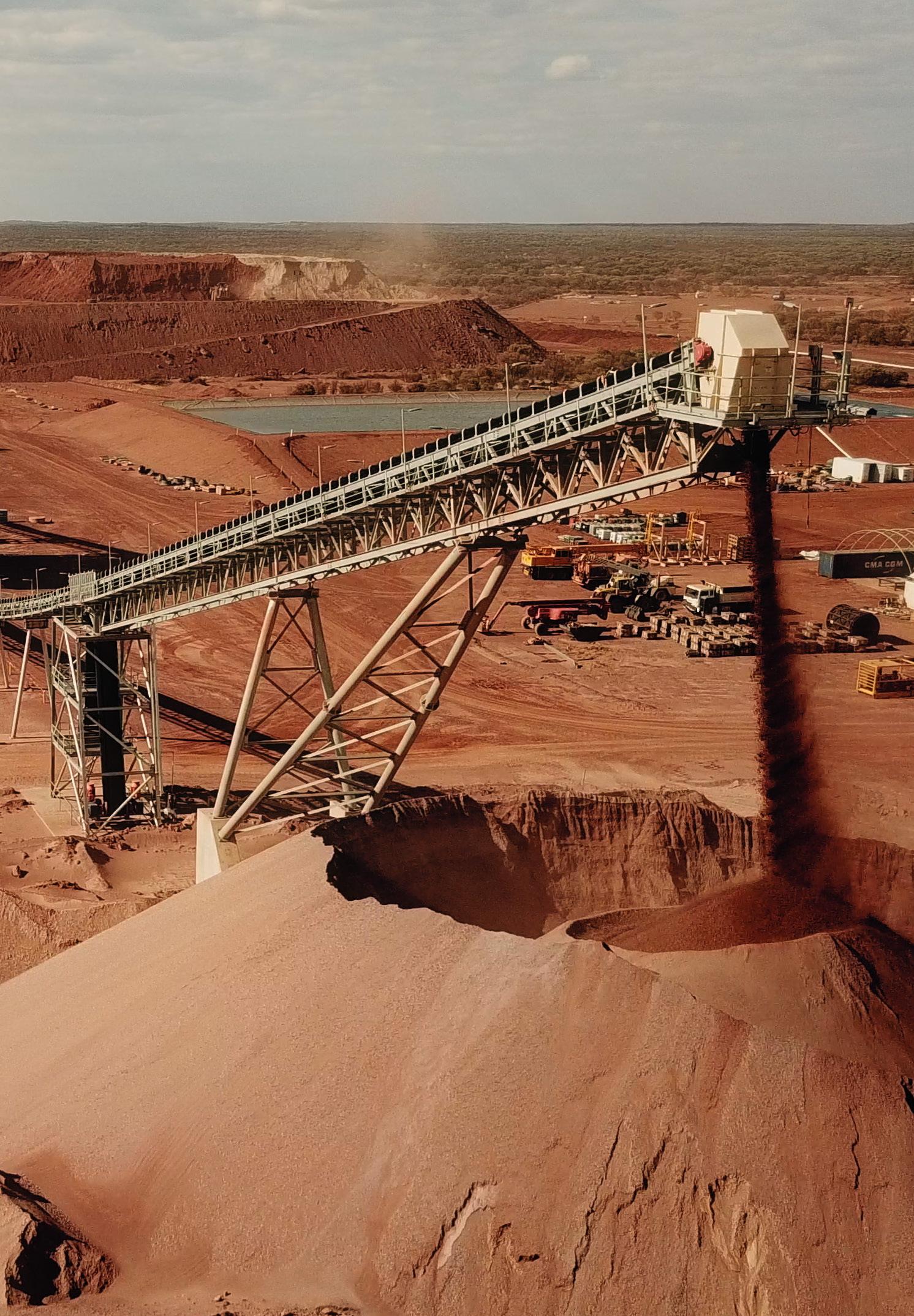