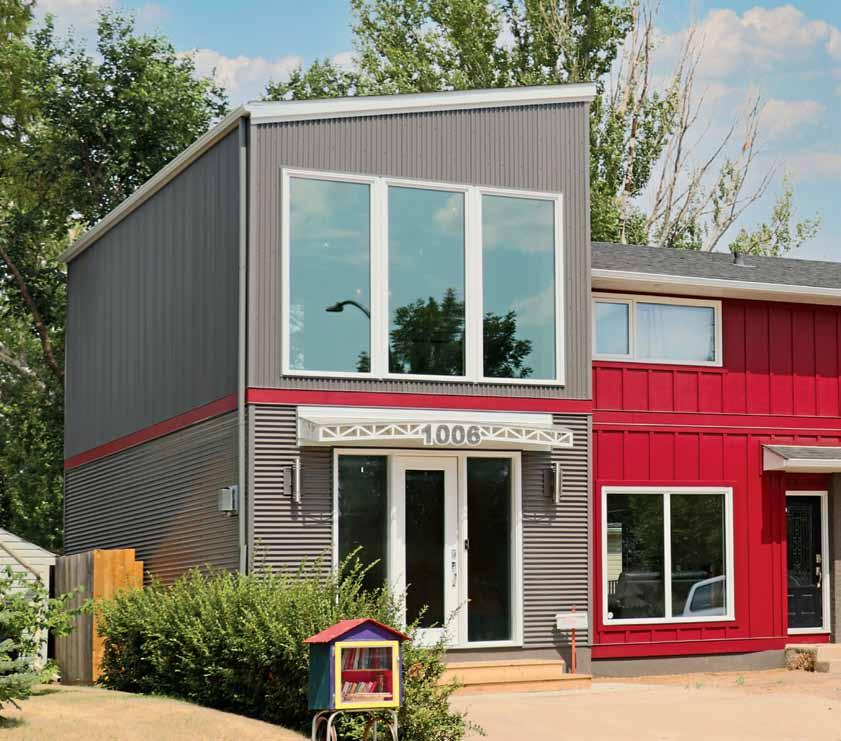
10 minute read
Firehall Inspired
Couple Embraces an Unusual Renovation
After 14 years and countless discussions about a possible renovation to accommodate their growing family, Paul and Amanda Titman decided to do something about their Richmond Heights two-storey. What they did was a little out of the ordinary. It involved cranes.
Advertisement
For Something a little Different
“My sister and brotherin-law worked with the Go2Guys on a renovation,” says Amanda. “We’ve lived in this house for 14 years and had no plans to move anywhere else, but there were some issues. We had talked for years about converting the attached garage to living space. But the structure just wasn’t adequate so it sat there and became badly used storage space. Because of my sister’s experience, we decided now was a good time to take it on.”
In Richmond Heights, the majority of the homes built during the 1960s to the 1980
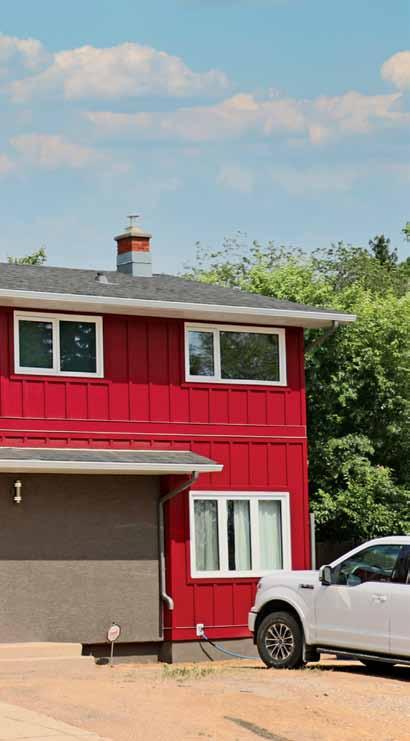
by: KArin Melberg sChwier Photos: lilliAn lAne

are single-family bungalows and two-storeys. Paul and Amanda’s 1968-era home was tipping over the 50 year mark. In recent years, properties in the area have been giving way to infills. Some are similar in style, and others are adding some architectural diversity to the neighbourhood. Paul and Amanda wanted to do a facelift from ordinary to something different.
“We looked for pictures of design elements that we
Elegant Home Decor & Lighting for Every Style


Family-Owned and Operated. Visit Our Updated Boutique Showroom or Shop Online.
401 2nd Ave N | 306-242-3266 | www.fandangolighthouse.com
Winter Snow, Ice and Parking Lot Maintenance
• Very Large to Very Small Capability • Sanding & Priority Service Available
Proudly providing snow removal and parking lot sanding services to the community of Saskatoon for over 14 years. Contact us to find out how we can serve you. Booking winter clients now. Saskatoon Snow
by Ahlstedt's 306.291.9504 www.saskatoonsnow.ca
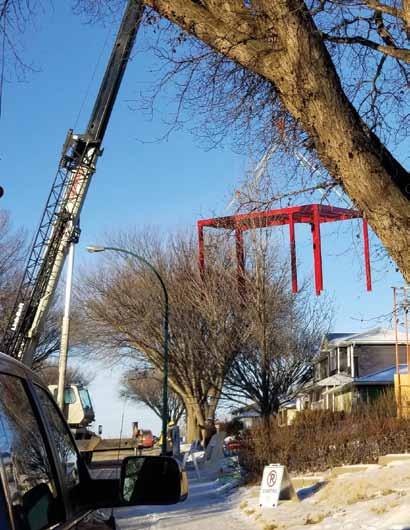
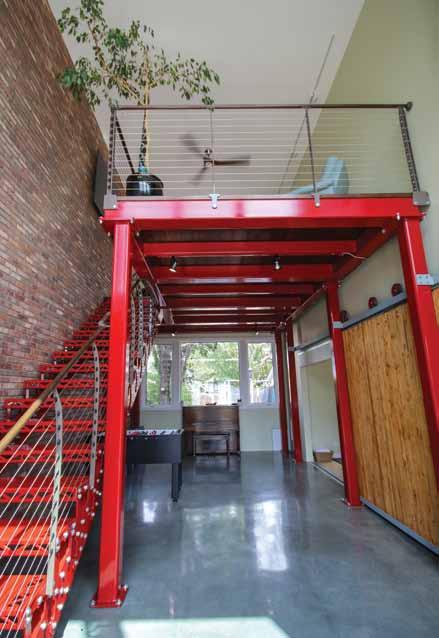
The open staircase is based on Victorian-era cast iron treads. The loft was fabricated off-site and installed with cranes before the addition was framed in.
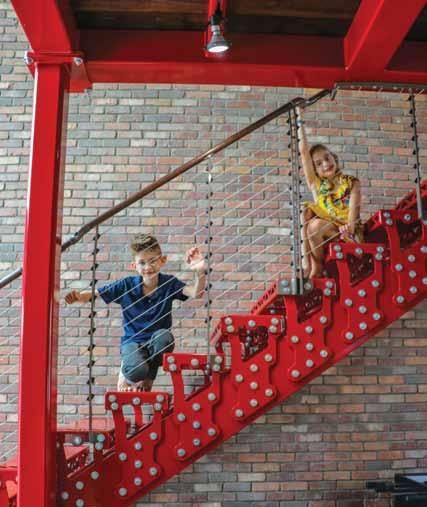
wanted to incorporate,” says Paul, who is an industrial painter. He also knows his way around metal design and fabrication, and his 3D printer gets a lot of use. “We decided to design and build what we liked. Resale was not our primary goal since we’re planning on living here longterm. We skewed more to our likes and needs.”
Pedal to the metal
In June 2019, the couple sat down with Tyler Wilson, Go2Guys project manager, to discuss the renovation on the 1800-sq. ft., four-bedroom house.
“At first, the focus was on more space since the existing garage was used as a catch-all for junk and was under-utilized. We originally knew that we wanted something a bit unusual, and we were open to something that didn’t match the home style of the neighbourhood.”
Initially, the couple was interested in a timber frame construction. But the more they researched, they kept coming back to Pinterest photos and other online images of reclaimed industrial spaces. Whenever a converted warehouse or firehall showed up in a movie they were watching, they grew more certain.
“We were really drawn to that look of old industrial
Paul took the lead on the metal design and off-site fabrication elements. He worked closely with the construction company on how the loft feature would be installed.
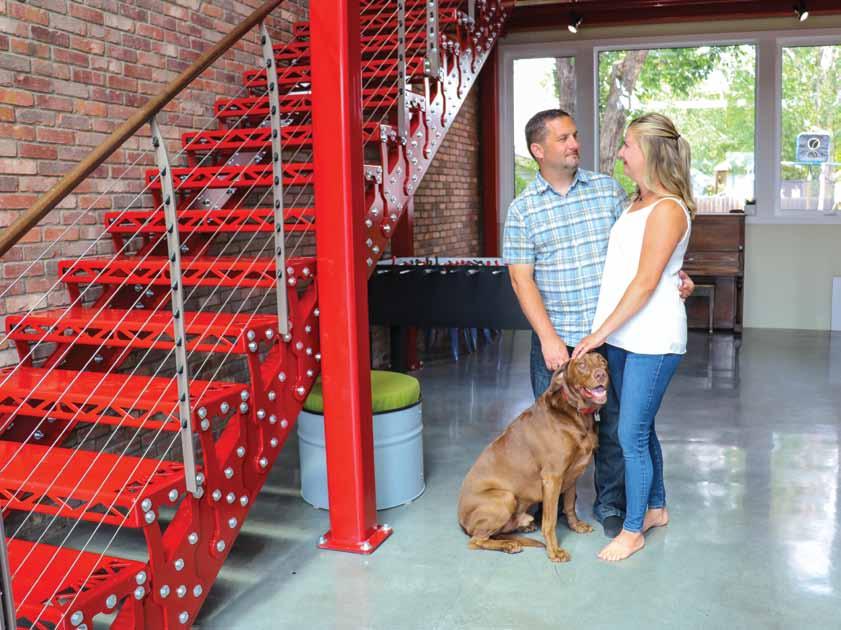
buildings,” says Amanda. “That loft look with metal and brick appealed to us so we thought why not do that?”
Why not indeed? This was a first for the construction company, but after “brainstorming and rolling a few ideas around,” Tyler says it was a matter of logistics, consulting with engineers and letting Paul take the lead on design.
The attached garage and concrete were completely removed, and replaced with an ICF grade beam with an insulated slab. Because of the metal fabrication and painting, it was not possible to construct the loft inside the addition so it was built off-site.
“The six-inch concrete was poured and the eight-inch pads were already placed beneath that,” says Tyler. The weather was a challenge; it got very cold very early in November 2019 with long stretches of 30 below weather. The concrete had to be protected while it cured.
From the Top Down
That’s when the cranes came in.
Before the addition was framed in and the roof put on, two huge cranes lifted the loft—like a giant table— and placed it as precisely as possible.
“Paul estimated the loft weighs about 3,000 pounds,” says Tyler. “We didn’t want to drag it around on that finished concrete floor so we had to be pretty precise about placement. Once the cranes left, there wouldn’t be any adjustments and we got it pretty dang close the first time.”
Even before the supports were completely bolted down, it was “all hands on deck” to complete the addition and get it closed in, a marathon job completed on Christmas Eve. The six 8x8 loft posts are secured with 3/4 inch bolts, seven inches long. Tyler says wedge anchors inserted into pre-drilled holes in the concrete were used for the best stability.
“The addition is basically a salt box with one wall covered completely in brick,” Paul explains. “Floor to ceiling is 21.5 feet and it took the mason over three weeks and 4,508 bricks to complete.”
The loft, then, is technically not a built-in part of the addition, though the floor is edged to appear so. “Cork flooring was laid down on 1x6 pine lap joint boards and subfloor placed directly on metal beams,” Paul explains. The top perimeter around the cork floor is custom-milled fir with aluminum trim for a cohesive look. The lap
The project had just started in June 2019 when the couple spent a memorable week in Italy. They discovered Murano glass near Venice, and brought back six light fixtures carefully swaddled in their suitcases. They were installed as pendant lighting high over the front entrance near the top of the climbing wall. Not only a treasured memento of their trip, the colourful glass is an artful feature day and night. The birch and steel climbing wall does double-duty as a floor-to-ceiling piece of abstract art.
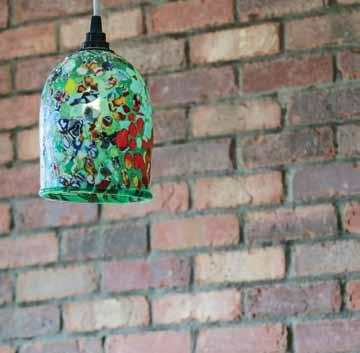
boards on the underside are stained a dark brown. The exposed metal beams, visible from the main floor, reinforce the industrial feel and the red is a nod to the firehall feel.
out of the ordinary
“The sound deadening was definitely worth it in walls,” says Amanda. With three kids aged nine, 12 and 14, thundering around on metal stairs (there’s Buddy the dog, too, but he’s not so keen on the open staircase) and with such height in the addition, sound can carry. Echoing wasn’t a huge problem, but acoustic drywall and buffalo board ensured adjacent bedrooms would be peaceful. Furniture in the loft living space also absorbs sound.
The open staircase is designed based on Victorian-era cast iron treads. A wood handrail features

transitions to bypass the metal loft support beams. Paul, no stranger to metal working, made them on a 3D printer. The plastic connection points were painted to match the uprights and corner posts.
“The climbing wall is constructed of Baltic birch and one quarter-inch steel plate. We decided to install an auto belay since we are not climbers and safety was a concern,” says Paul who is, ironically, not comfortable with heights. “It has not been used much yet since it was finished during the pandemic. But now as other kids are starting to come over, it has seen use.” The wall does double-duty as a 20-foot vertical piece of foyer art, drawing the eye up through the space to the loft area.

Concrete Thinking
The floor is clear-coated concrete. It was sanded to drop some of the shine and slippery surface. While concrete is a common flooring material, says Tyler, in residential applications it’s usually covered so care had to be taken not to damage it.
“We like the wearability, durability and ease of cleaning the concrete,” says Amanda. “And it looks good and carries through that warehouse aesthetic. We also have a Tidal fit swim spa behind the addition. In fact, one of the reasons for the addition was to keep the water more contained instead of tracking across hardwood in the rest of the house.”
Concrete is a popular choice for homeowners who want the warehouse look, but there are some
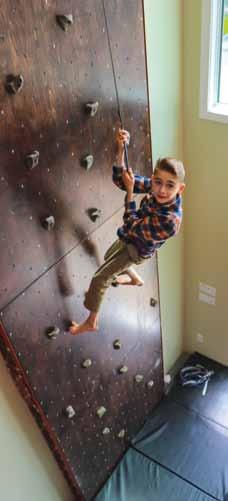
Since everyone in the family is an inexperienced climber, Paul and Amanda installed an automatic belay feature for safety.
The brick and metal add to the firehall feel of the interior. A mason spent over three weeks laying the bricks on the 21.5 foot wall.
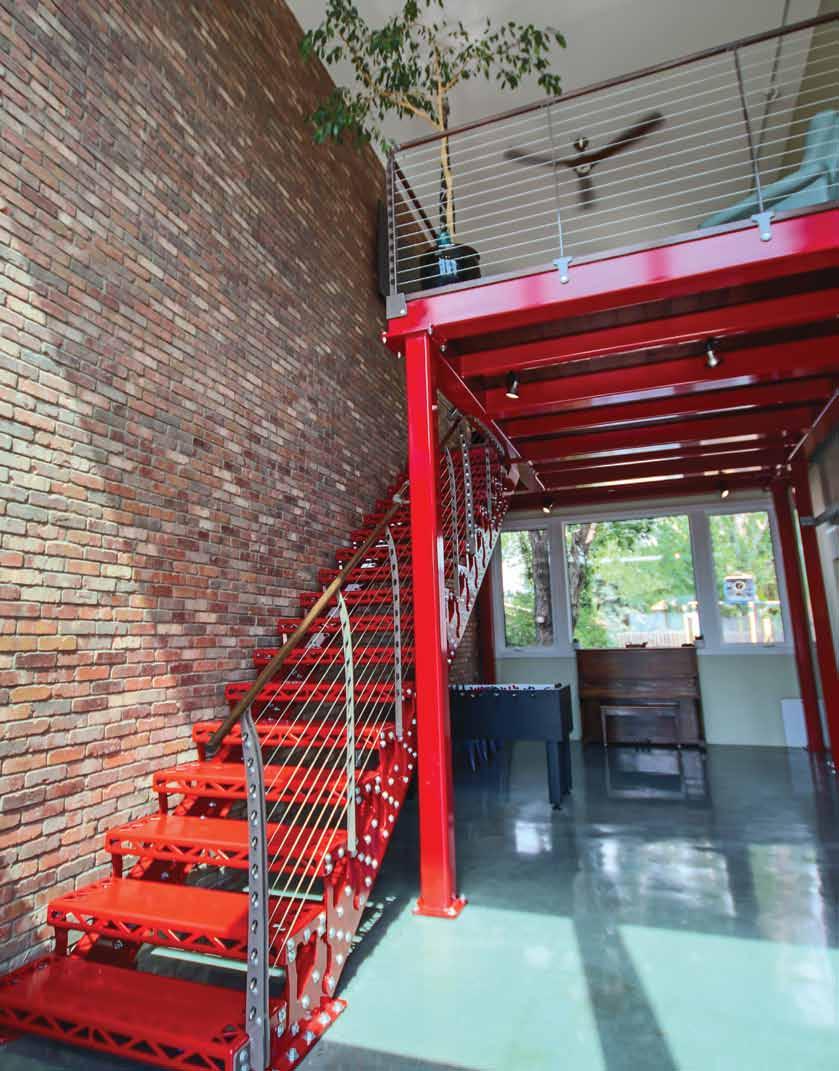
691 bolts in staircase 4508 bricks on west wall 21.5 feet addition height 20-foot climbing wall with 30 jugs (hand and footholds) 2—80-foot cranes
considerations. It is not a forgiving surface; a dropped wine glass will not bounce. And there can be issues with concrete wicking moisture from below ground, and it may develop cracks.

From the beginning, Paul and Amanda designed what pleased them as a family without worrying about future resale. Children William, Lucas, and Arie Anna are happy with the outcome.
Softening elements
Paul and Amanda wanted interior and exterior elements that would add warmth and texture. Even though they were drawn to the industrial warehouse look, they knew the house had to have some cozy elements to soften the hard materials.
“The cork floor in the loft definitely adds warmth. The fireplace on the main adds character and we put a dark stain on woodwork,” says Amanda. “Now I’m glad we didn’t have the budget for a glass barn door between the addition and the original house. Instead we used stacked two by fours and stained them, and I think it adds to the warehouse feel.” Iron caster wheels on the door track add a vintage steampunk element.
Extensive glazing allows for a lot of natural light, something that has its own softening effect on interiors and a tall ficus tree enjoys the large windows. The family hopes to put in an apple tree.
“Due to the height in the addition, we went as large as possible without going commercial.” Two windows on the main floor in the living room and office area were also replaced and garden doors were added so nearly all rooms in the home are bathed in natural light.

neighbourhood Watch
“We were not overly concerned about blending in with other homes in the neighbourhood,” explains Paul. He did get some pushback on his wish to use shiny galvanized steel on the addition exterior, the sort used for grain bins. “I got outvoted on that one.”
“If push comes to shove, something completely unexpected happens and we have to move, we’re still happy with the investment,” he adds. “We’ve built it the way we wanted without being constrained by some anonymous future buyer.”
But with the red metal beams and industrial staircase, the visible nuts and bolts, the brick wall, and its grey corrugated metal and fire-engine red hardy board exterior, the couple is happy with the outcome. They feel they’ve captured that look they were drawn to when they sifted through all those Pinterest photos of firehalls and converted warehouses.
Karin Melberg Schwier