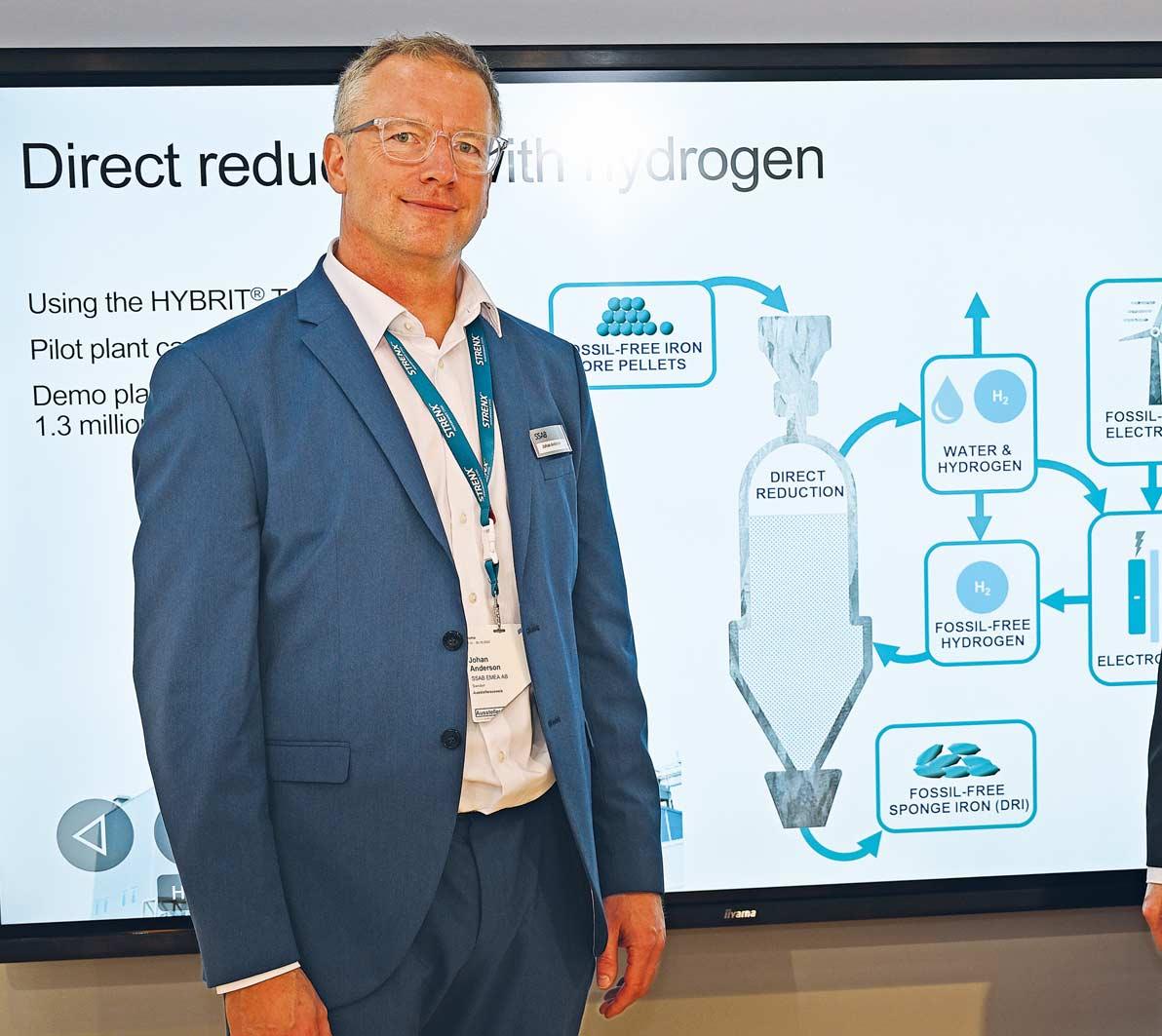
8 minute read
SSAB | Der schwedische Stahl konzern SSAB hat hohe Investitionen getätigt, um die weltweit erste fossil freie Stahlerzeugungstechnologie zu entwickeln, die praktisch keinen CO₂Fußabdruck hinterlässt. Johan Anderson, Global Strategy Projects (li.),
L SSAB
Die Zukunft des Stahls neu erfinden
Advertisement
Die traurige Wahrheit ist, dass sich jede noch so gut gemeinte NullEmissionStrategie in die sprichwörtliche Tonne treten lässt, wenn alternative Antriebskonzepte zwar den CO₂Ausstoß einer Baumaschine lokal verringern, die Herstellung der eigentlichen Maschine nebst derer Teile aber eine emissionsschleudernde Angelegenheit bleibt. Der in Schweden ansässige Stahlkonzern SSAB ist seit Jahren darum bemüht, auf diesen Zustand hinzuweisen und hat hohe Investitionen getätigt, um die weltweit erste fossilfreie Stahlerzeugungstechnologie zu entwickeln, die praktisch keinen CO₂Fußabdruck hinterlässt. Johan Anderson, Global Strategy Projects, und Benedikt Figura, Regional Marketing Manager bei SSAB, haben mit bauMAGAZINChefredakteur Dan Windhorst über die Notwendigkeit sowie Vorzüge fossilfreien Stahls gesprochen.
Dan Windhorst
m tonnenschwere Bagger, Muldenkipper oder Walzen überhaupt produzieren zu können, ist eine gewaltige Menge an Stahl vonnöten. Und genau hier beginnt das Problem mit dem Entstehen erheblicher CO2-Emissionen. Das Stahlunternehmen SSAB nimmt das seit einigen Jahren zum Anlass, um für die eigenen Bestrebungen der fossilfreien Stahlproduktion zu werben. Gleichzeitig versucht der Stahlkonzern aber auch,
DAN WINDHORST JAN LINDBLAD JR

SSAB
Mit Johan Anderson (Global Strategy Projects) und Benedikt Figura (Regional Marketing Manager) haben zwei erfahrene SSAB-Stahlspezialisten die Bauma-Besucher über die Vorzüge von fossilfreiem Stahl informiert. Gleichzeitig stellten die beiden SSAB-Experten bewährte Hardox- sowie Strenx-Lösungen vor. Der erste fossilfrei produzierte Stahl.
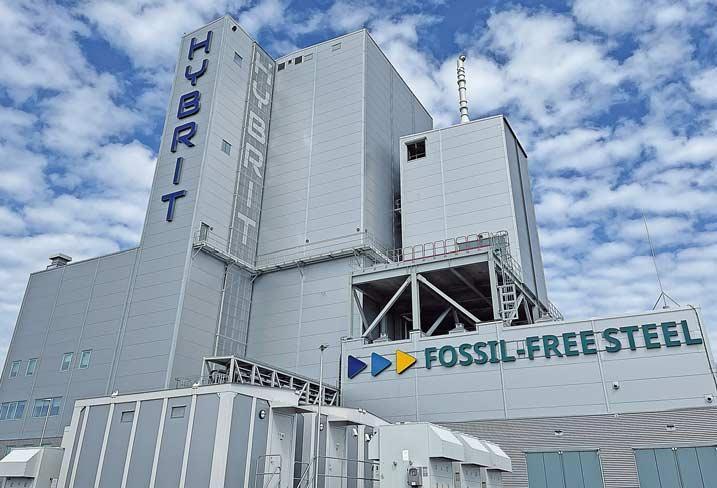
Bereits 2016 schlossen sich der Stahlkonzern SSAB, der Eisenerzproduzent LKAB sowie das Energieunternehmen Vattenfall zusammen und gründeten mit Hybrit eine Initiative, die die Stahlerzeugung revolutionieren soll. Eine weltweit einmalige Pilotanlage im schwedischen Lulea wurde bereits im Sommer 2020 fertiggestellt.
zielgerichtete Aufklärungsarbeit zu betreiben. Und genau das zeigt sich in einer für diese Branche nicht immer ganz typischen Offenheit, indem wichtiges und zuweilen internes Wissen frei zugänglich mit Außenstehenden geteilt wird. »Sinn und Zweck ist es, einen Dialog zu führen. Wir möchten, dass die Entwicklung nicht nur bei uns stattfindet, sondern eine größere Allgemeingültigkeit erhält«, so Johan Anderson. »Geht es um das Ziel, so viel Emission einzusparen wie möglich, gibt es keine zwei Meinungen, weshalb wir auch bereit sind, unser Wissen mit anderen zu teilen. Natürlich sind unsere Ideen über das Patent geschützt. Wir haben aber ein generelles Interesse daran, dass andere Stahlproduzenten und Hersteller mitziehen«, ergänzte Benedikt Figura.
Ein langer Weg bis zum erklärten Ziel Dass SSAB eines Tages dazu in der Lage war, fossilfreien Stahl zu produzieren, ging mit einer inten siven Wegstrecke einher: Bereits 2016 schlossen sich der Stahlkonzern SSAB, der Eisenerzproduzent LKAB sowie das Energieunternehmen Vattenfall zusammen und gründeten mit Hybrit eine Initiative, die die Stahlerzeugung revolutionieren soll. Bei dieser Technologie, so SSAB, wird die Kokskohle, die traditionell für die erzbasierte Stahlerzeugung benötigt wird, durch fossilfreien Strom
UNTERNEHMEN
Der börsennotierte SSABKonzern ist ein in Nordeuropa und den USA ansässiges Stahlunternehmen. Es beschäftigt Mitarbeiter in mehr als 50 Ländern und verfügt über Produktionsstätten in Schweden, Finnland und den USA.
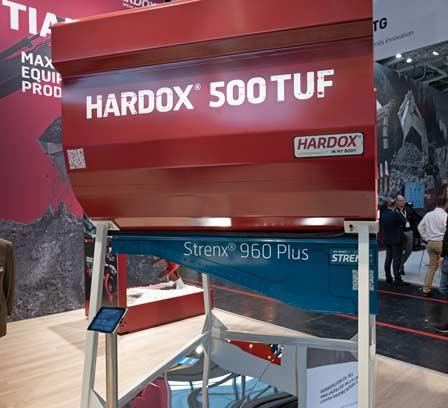
Benedikt Figura, Regional Marketing Manager SSAB und Wasserstoff ersetzt, wodurch Wasserdampf anstelle von CO2 freigesetzt wird. Das Ergebnis ist die weltweit erste fossilfreie Stahlerzeugungstechnologie, die praktisch keinen Kohlenstofffußabdruck hinterlässt. Das überhaupt erste Stahlblech wurde Mitte 2021 bei SSAB mit wasserstoffreduziertem Eisenschwamm hergestellt. Erster Abnehmer war damals die Volvo-Gruppe, die damit anschließend ihre ersten Maschinen fertigen konnte (das bauMAGAZIN berichtete in Heft 10/22, Seite329). Dabei handelte es sich um einen knickgelenkten A30G-Dumper, der an den Baukonzern NCC übergeben wurde. Neun Monate nachdem Volvo das weltweit erste Fahrzeugkonzept aus fossilfreiem Stahl bekannt gegeben hatte, erfolgte die Auslieferung. »Um die Dekarbonisierung der Bauindustrie erfolgreich zu gestalten, müssen die Akteure in der Wertschöpfungskette zusammenarbeiten und gemeinsam handeln«, so Melker Jernberg, Präsident bei VolvoConstruction Equipment.
Dekarbonisierung der Stahlindustrie Im industriellen Maßstab möchte SSAB den Markt bereits in vier Jahren mit seinem fossilfreien Stahl bedienen. Ein hehres Ziel, keine Frage, aber laut Johan Anderson »notwendig und machbar, da bis 2026 unglaublich viel passieren wird.« Der Stahl experte nimmt Bezug darauf, dass die Verwendung von fossilfreiem Stahl künftig nicht nur bei Baumaschinenherstellern relevant sein dürfte, sondern gleichzeitig auch die Bauherren großer Städte sowie Automobilhersteller tangiert: Ein rein batteriebetriebenes Elektrofahrzeug (BEV) zu ent-
DAN WINDHORST
wickeln und dadurch emissionsfrei zu fahren ist das Eine. Geht es jedoch um die Nutzung von ebenfalls emissionsfrei produziertem Strom sowie der Verwendung emissionsfrei hergestellter Materialien, die zur Karosserie- und Teilefertigung benötigt werden, sind laut Anderson bislang viele Fragen ungeklärt. Grundsätzlich, so Anderson und Figura, nehme SSAB eine Vorreiterrolle bei der Dekarbonisierung der Stahlindustrie ein. »Eine fossilfreie Wertschöpfungskette zu schaffen, die von der Erzmine bis zum Endprodukt reicht, ist ohne Frage eine echte Mammut-Aufgabe, aber sie muss genau jetzt angegangen werden«, sagte Johan Anderson.
Erster Stetter-Fahrmischer mit Hardox-Trommel
Verschleißfester – und das ohne Mehrgewicht: Mit einer Mischtrommel, die komplett aus dem Stahl Hardox 500 Tuf von SSAB hergestellt wurde, möchte Stetter eine neue Generation von Fahrmischern schaffen. Grundsätzlich konnte am gesamten Aufbau einiges an Gewicht reduziert werden. Änderungen am Design beispielsweise, die für eine schlankere Trommel gesorgt haben, tasten jedoch nicht das gewohnte Ladevolumen von 9 m³ an. Die Nutzlast des Fahrmischers bleibt erhalten.

Feierte Weltpremiere auf der Bauma: Der Fahrmischer UltraEco II aus dem Hause Stetter verfügt über eine Mischtrommel, die komplett aus Hardox 500 Tuf gefertigt wurde. Der Hardox-Stahl 500 Tuf stand auf der Bauma im Oktober bei SSAB ebenfalls im Mittelpunkt.
Das neue Hochleistungsverschleißblech Hardox 500 Tuf von SSAB hatte sich bislang bereits bei der Produktion von Baggerschaufeln bewährt: Dort wird traditionell auf verschiedene Stahlvarianten gesetzt. Einzelne Teile einer Schaufel müssen mal härter, mal zäher gestaltet sein, weshalb dafür unterschiedliche Stahlarten vonnöten sind (das bauMAGAZIN berichtete in Heft 9/22, Seite 60). Unter Hinzunahme von Hardox 500 Tuf hat zum Beispiel der dänische Hersteller Sjørring einen Baggerlöffel konzipiert, der aufgrund dieses Stahls über eine besonders hohe Verschleißfestigkeit und Haltbarkeit verfügt. Mit der Verwendung von Hardox 500 Tuf beim Fahrmischer von Stetter tut sich nun ein weiteres Einsatzgebiet auf.
Gute Verarbeitungseigenschaften Während des Herstellungsverfahrens werden die HardoxSpiralsegmente vor dem Einbau definiert gekantet, was nach dem Einbau in die Trommel mögliche Spannungen im Material reduzieren und so die Lebensdauer erhöhen
Johan Anderson, Global Strategy Projects SSAB
Zu Recht bekräftigt er, dass die Welt nun mal mit Stahl gebaut sei und die weltweite Nachfrage jährlich ansteige. Da die Stahlunternehmen der Welt jedoch nach wie vor erhebliche CO2-Emissionen verursachen, seien nachhaltige Lösungen nicht nur zwingend, sondern eben auch dringend erforderlich.

Zum Stand der Dinge Eine weltweit einmalige Pilotanlage im schwedischen Lulea wurde bereits im Sommer 2020 fertiggestellt. Der nächste Schritt besteht darin, 2025 eine Demonstrationsanlage in Betrieb zu nehmen, zeitgleich mit der Umstellung der Hochöfen von SSAB im schwedischen Oxelösund. Dadurch ist SSAB eigenen Angaben zufolge dazu in der Lage, ab 2026 eisenerzbasierten, fossilfreien Stahl für den kommerziellen Einsatz zu produzieren.
Hybrit, so das Unternehmen weiter, habe das Potenzial, die CO2-Emissionen um 10 % in Schweden und 7 % in Finnland zu reduzieren und einen Beitrag zu nachhaltigen Lösungen für die Stahlproduktion zu leisten. Der Konzern SSAB hat überdies verkündet, bis etwa 2030 die Kohlendioxidemissionen aus dem eigenen Betrieb weitgehend zu eliminieren. Das Hybrit-Projekt ist eine strategische Initiative für SSAB und spielt eine wichtige Rolle beim Übergang Schwedens und Finnlands zu einer fossilfreien Wirtschaft der Zukunft. d
Volvo liefert E-Lkw mit fossilfreiem Stahl aus
Im September hat Volvo Trucks die Serienproduktion von schweren ElektroLkw mit einem Gesamtzuggewicht von 44 t aufgenommen. Einige dieser ElektroLkw werden auch die ersten Lkw der Welt sein, die mit fossilfreiem Stahl von SSAB gebaut werden. Damit folgt
Volvo Trucks dem ConstructionEquipmentSegment der Gruppe, das bereits einen mit fossilfreiem Stahl gefertigten A30GDumper ausgeliefert hat. Zu den Kunden, die fossilfreien
Stahl in einigen ihrer ELkw der Marke Volvo einsetzen werden, gehören Amazon und DFDS sowie – über das Transportunternehmen Simon Loos –
Unilever. Der erste mit Wasserstoffhergestellte Stahl wird für den
ChassisRahmen des ELkw verwendet, dem Rückgrat des
Fahrzeugs, auf dem alle anderen
Hauptkomponenten montiert sind. Wenn die Verfügbarkeit von fossilfreiem Stahl zunimmt, soll er auch in anderen Teilen des
Lkw eingesetzt werden.
VOLVO TRUCKS
Als nach eigenen Angaben erster Lkw-Hersteller hat Volvo damit begonnen, fossilfreien Stahl für seine Lkw zu verwenden. Die ersten E-Lkw mit diesem Stahl werden jetzt ausgeliefert.
soll. Der Blechstreifen des Spiralkantenschutzes, so SSAB, werde zudem in einem speziellen Lochschweißverfahren und mit gleichmäßigem Überstand zur Spiralkante angebracht. Auf diese Weise soll eine Schweißnaht ent stehen, die wirksamer gegen Verschleiß geschützt ist. Grundsätzlich gilt: Das Schweißen und Bearbeiten von Hardox 500 Tuf ist mit denselben Werkzeugen möglich, die auch für andere HardoxSorten zum Einsatz kommen. Der Stahl bietet eine hohe Festigkeit, Zähigkeit und extreme Härte und soll laut SSAB eine um 70 % bis 100 % längere Standzeit im Vergleich zu üblichem 400 HB ARStahl bieten. Zudem soll das Verschleißblech über einen verbesserten Verformungsschutz verfügen.

Eine erfolgreiche Zusammenarbeit Seit 2015 nutzt Stetter HardoxVerschleißbleche für die Mischtrommel und spirale. Dem voran gegangen sind Verschleißtests – einhergehend mit der Tatsache, dass Stetter bereits seit dem Jahr 2000 verstärkt auf den Leichtbau mit erhöhter Verschleißfestigkeit gesetzt hatte. Der Einsatz von unterschiedlichen Zuschlagstoffen im Frischbeton hat laut Stetter zu einer höheren Beanspruchung der Trommelwandlung und der Mischspiralen geführt, weshalb gehärtete Stähle immer mehr in den Mittelpunkt gerieten. Seit 2016 ist Stetter zudem Teil der »Hardox In My Body«Mitgliedschaft: Die von SSAB ins Leben gerufene Qualitätszertifizierung soll bestätigen, dass ein Produkt unter Anwendung von HardoxVerschleißstahl hergestellt wurde und damit eine hohe Beständigkeit gegen abrasiven Verschleiß aufweist. d
SCHWING STETTER (2)
Der Blechstreifen des Spiralkantenschutzes wird in einem speziellen Lochschweißverfahren angebracht.