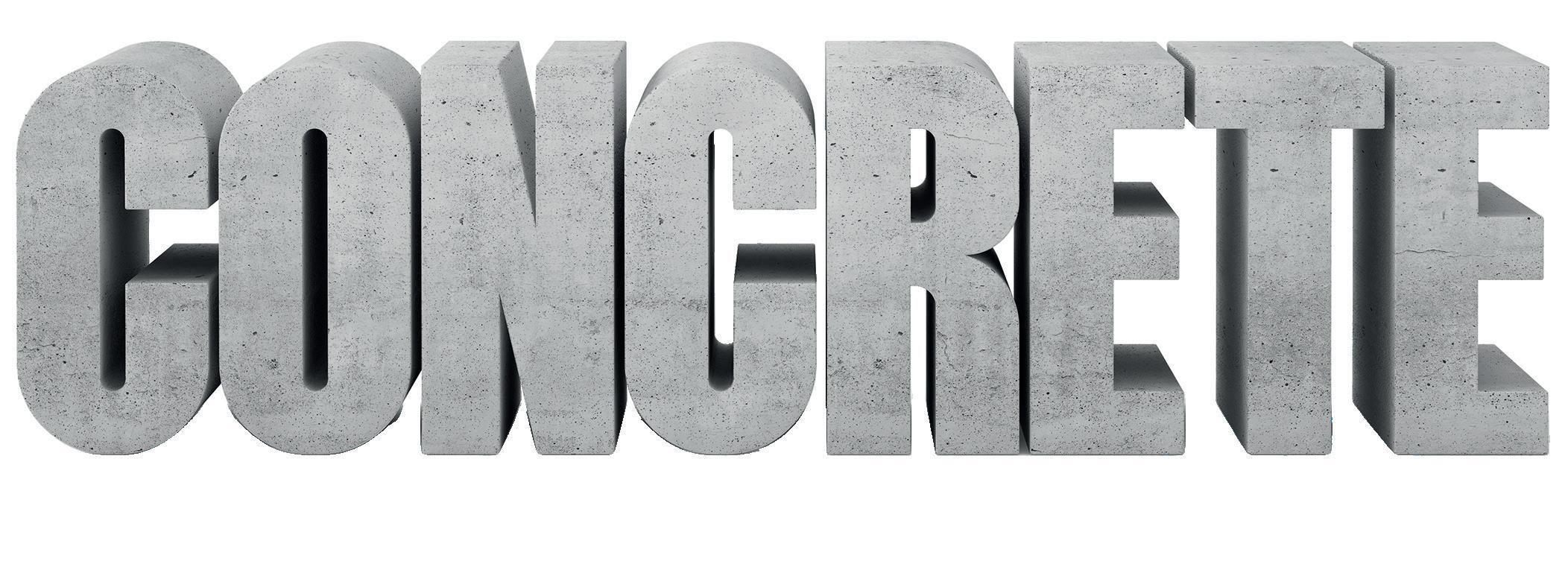
2 minute read
without carbon
How the National Cement Company of Alabama is steering towards a green future
The National Cement Company of Alabama (NCCA) first began producing cement at its current site in Ragland, Alabama in 1908, then operating under the name of the Atlantic & Gulf Portland Cement Company. The company changed its name to National Cement Company in 1920, enjoying various owners up until 1974, when it was purchased by the Vicat Group, a French company with origins stretching back as far as the early 1800s, when Louis Vicat first invested in artificial porous cement production. Following the acquisition, Vicat Group set upon a program of modernization and plant improvements that have brought NCCA to its present-day status.
Today, the company produces Portland Cement Type I, II and III and masonry cements, which it ships via truck and rail from four terminal distribution locations around Atlanta, Georgia, and one in Greenville, South Carolina. NCCA also operates readymix concrete subsidiaries, in the shape of Kirkpatrick Concrete and Hodgson Concrete in Alabama, and Walker Concrete in Georgia.
Among the biggest challenges currently facing cement producers like NCCA is a growing emphasis on decarbonization, with pressure mounting both within the industry and beyond, from the consumer to the governmental level. NCCA’s own decarbonization plan sets out the company’s ambition to achieve carbon neutrality by 2050 through the value chain, and the company took a significant step towards this earlier this year, as it commenced a two-year, $300-million project to install new cement production equipment throughout its Ragland plant. As Spencer Weitman, President of the NCCA, explains, the equipment will take advantage of the “very latest carbon reduction practices and modern energy technologies,” chiefly substituting fossil fuels with alternative fuels.
“The primary goal of the improvement project is to meet the global climate challenge head-on, and to be ready for the southeast’s impending demand for building materials with a lower carbon footprint,” Spencer comments. The company has already added a new vertical raw mill, a preheater tower with an advanced kiln line and cooler, an automated clay storage system, an alternative fuel storage facility, and a fully automatic integrated laboratory and control center. Meanwhile, the ongoing installation of electrical motors is expected to reduce energy consumption by as much as ten percent.
“We’ve also eliminated coal as a fuel source, replacing it with biomass,” Spencer continues. “This alone has delivered a 30 percent carbon footprint reduction. The next step for us will be the production of Portland Limestone Cement (PLC) or Type IL, an innovative blended cement that contains up to 15 percent limestone.
Tractor and Equipment Co
We are a local full-service marketing company that has been working with Tractor and Equipment Co for over ten years. We offer visual content development with multiple RED Digital Cinema cameras, graphic development, web, photo, and print, as well as a host of other marketing and branding services. Through the years, we have worked with international brands such as BMW, Shell Oil, Komatsu, and Amerex, and are happy to help you with anything you may need for Tractor and Equipment Co in the future.
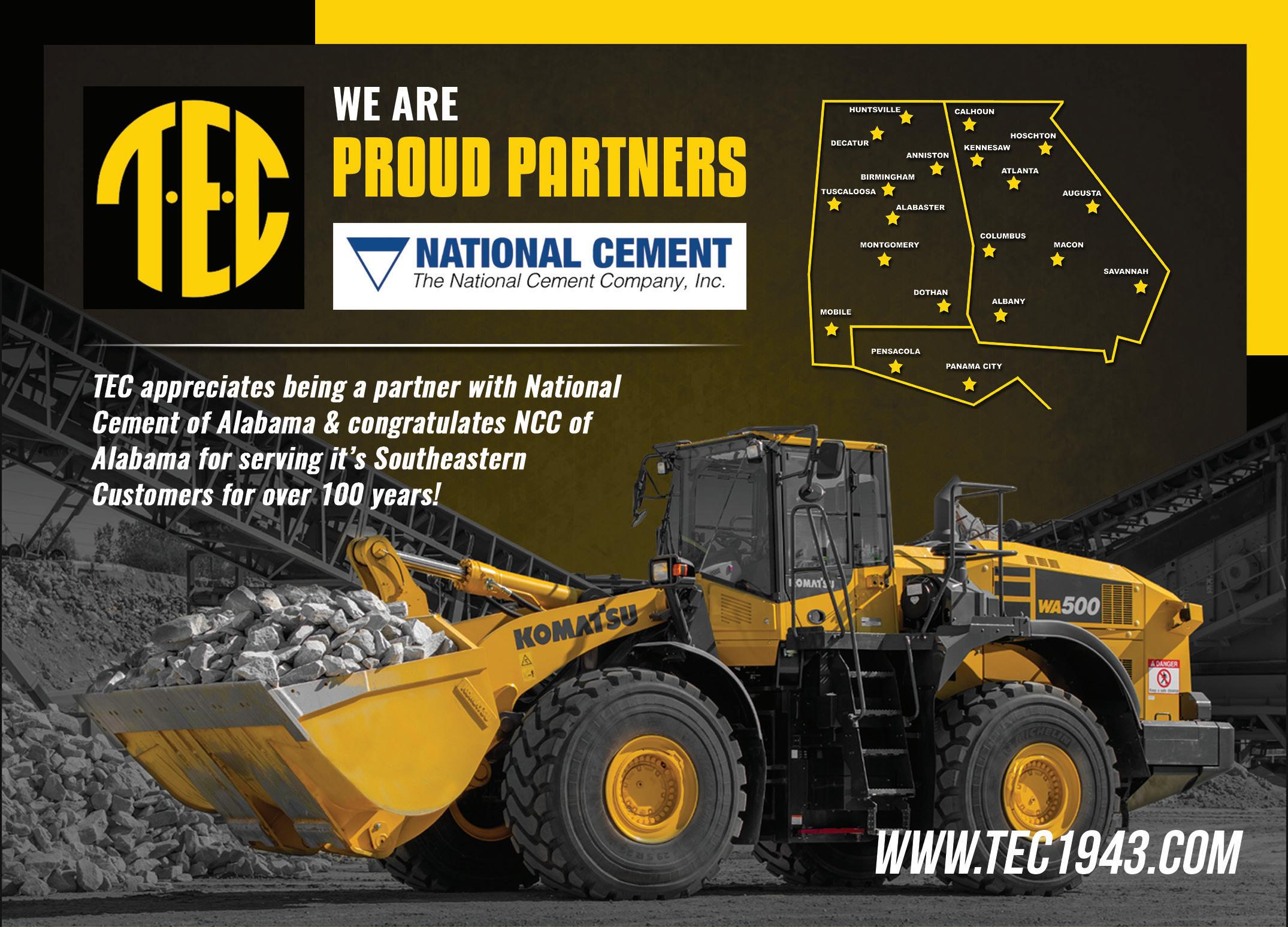
This will drop our carbon footprint by another ten percent. We’re currently in the process of conducting testing and making various initial production runs.”
By 2023, it’s expected that all Type I general-purpose Portland cement (OPC) produced in Ragland will be switched to Type IL PLC. But these aren’t the only efficiency measures underway at NCCA. The company is also revolutionizing its shipping operations, prioritizing energy-efficient modes of transportation.
“On a ton-mile basis, shipping by rail is more fuel efficient than shipping by trucks, lowering greenhouse gas emissions by up to 75 percent on average,” Spencer tells us. “Therefore, our carbon neutrality goal impels us to look at moving a larger volume of freight by rail.”
National Cement also owns approximately 4000 acres of land, of which around 800 acres are used for the plant site, storage, and