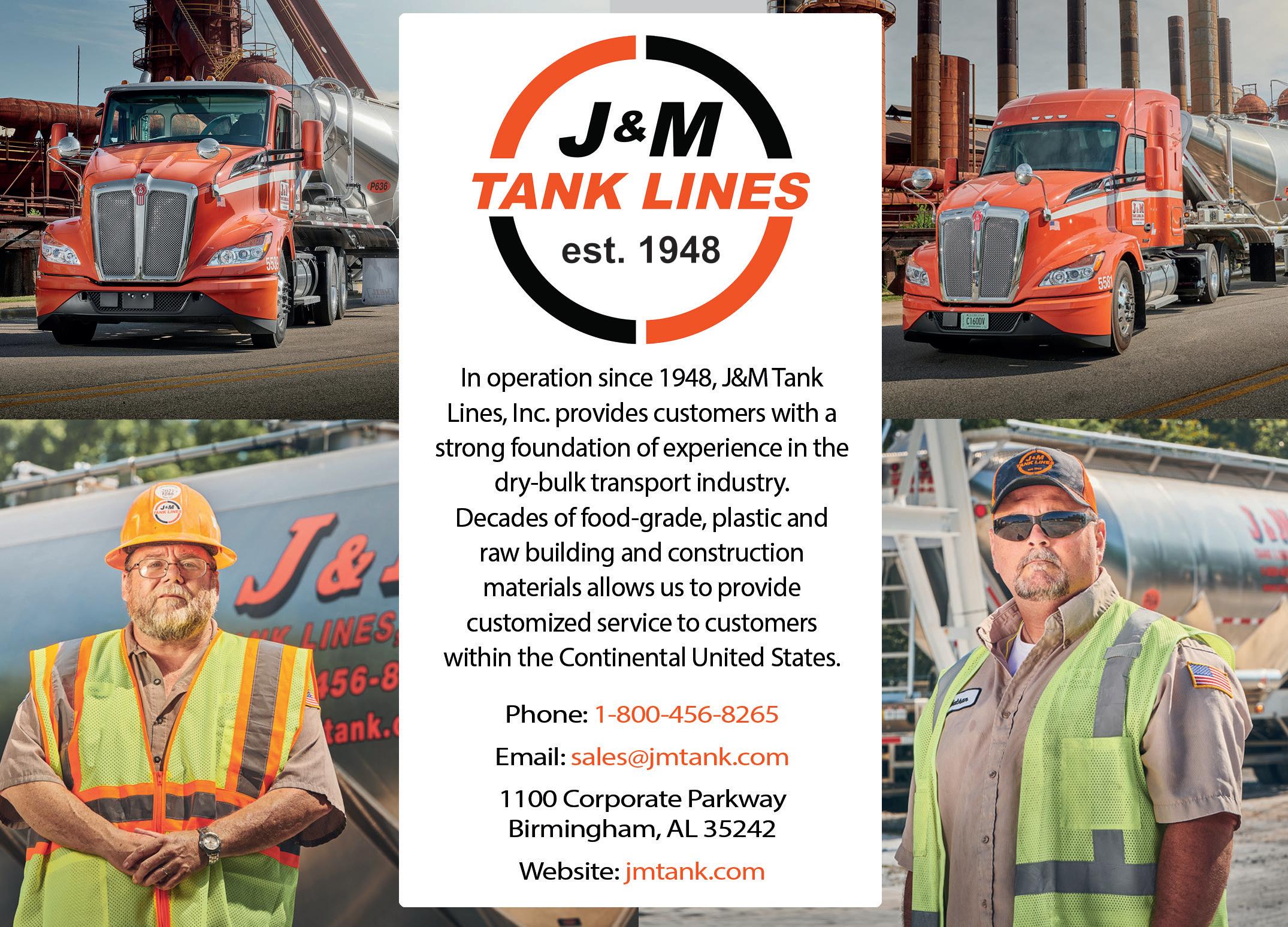
4 minute read
National Cement Company of Alabama
J & M Tank Lines
J & M Tank Lines has been a familyowned company since 1948. While headquartered in Birmingham, Alabama, we have operations strategically located across the southeast to offer the best coverage and service to our customers. As an industry leader in dry-bulk transport, J & M is backed by an elite force of professional drivers and industry experts dedicated to service and safety.
Built on a foundation of integrity and respect, we strive to provide quality service to all. Our purpose is to create an empowering environment for our stakeholders, encourage a team mindset and to exceed industry service and safety standards.
quarrying, with the remaining 3200 acres consisting of timber or grasslands.
“We’re currently studying the best management of our land to gain the best carbon offsets for the future,” Spencer reveals.
“Long term, we will embrace carbon capture and sequestration, capitalizing on technology that is maturing every day.
“The Vicat Group is also researching and building new ways to reduce the carbon footprint of all their plants worldwide,” he adds. “We’ll adopt their designs and technology in order to further reduce our carbon footprint, in addition to what we’ve already accomplished.”
Also speaking to Construction Today, Hervé Lapillonne, Project Manager at NCCA, echoes Spencer’s comments. “In several countries, Vicat Group is very active on the topics of carbon neutrality, with hydrogen, ethanol, solar energy, calcined clay and algae tests underway in some of its plants,” he says. “At NCCA, we have the advantage of being smaller and more agile than Vicat Group as a whole. Although we’re a creator of CO currently, we’re therefore wellpositioned to develop innovative solutions in the future.”
“All in all, we expect our investments to make our cementitious product one of the lowest carbon cements in this market,” Spencer reiterates. “It’s a big step in the entire industry’s efforts to achieve carbon neutrality throughout the concrete value chain.”
NCCA’s aim for 2050, like the majority of carbon goals, requires change on the grandest of scales. To reach it, however, is the product of a series of small changes, driven largely by the work of hundreds of dedicated individuals. To this end, Spencer is effusive about what he describes as the company’s “unique family culture,” which he believes creates the foundation for much of NCCA’s success.
“Here, everyone knows everyone,” he confirms. “We’re a lean, largely flat organization. Our management is approachable, and they take it upon themselves to interact with our employees as
The Euclid Chemical Company
In response to the technical and environmental challenges faced by cement manufacturers, Euclid Chemical offers EUCEMTM ICARE, a patentpending strength enhancement technology that offers unequaled performance and reduced CO2 emissions potential.
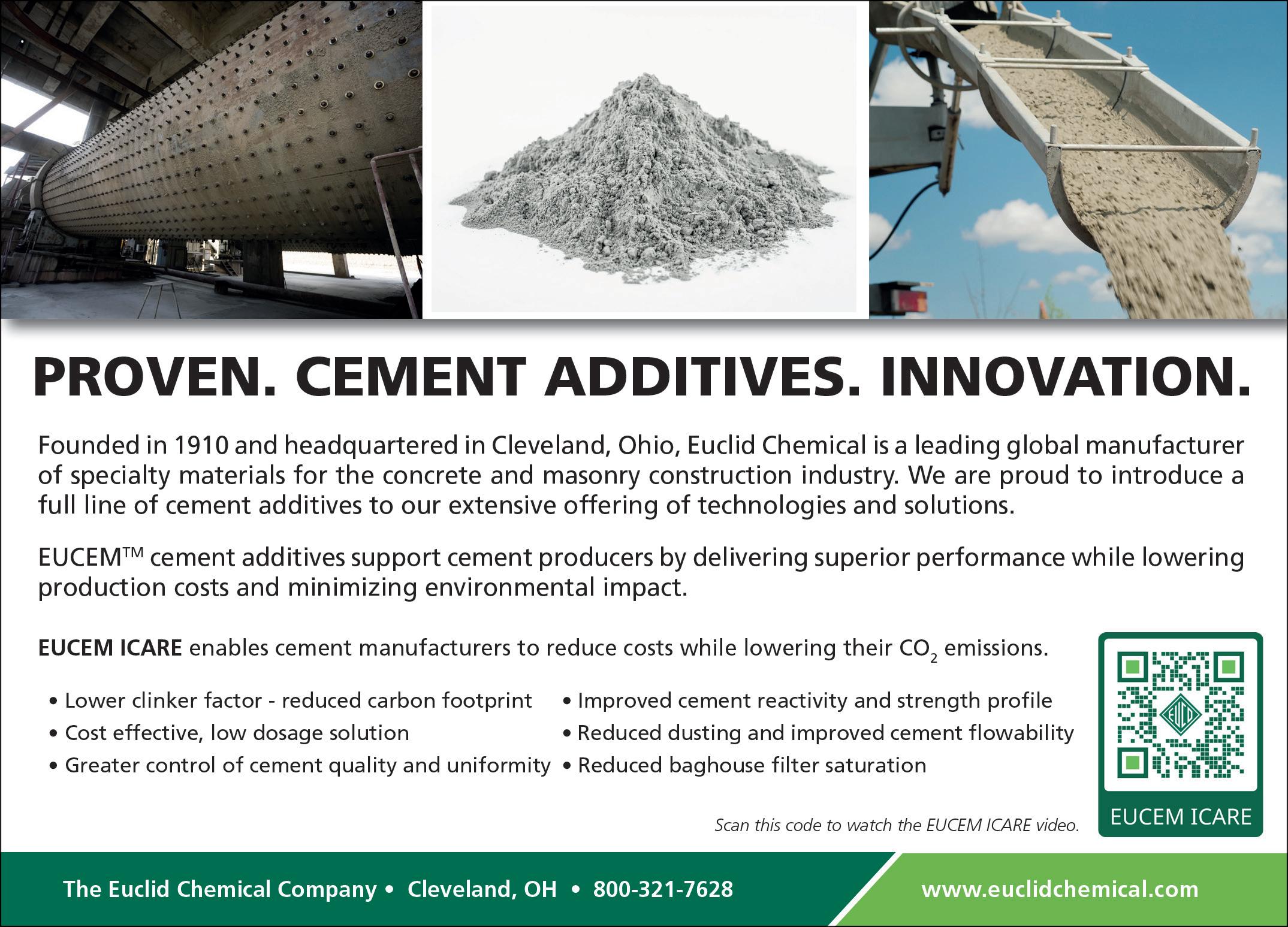
EUCEM ICARE products improve cement strengths while overcoming process constraints. With the EUCEM ICARE CP range, manufacturers can achieve full cement activation potential via improved cement fineness and particle size distribution. With EUCEM ICARE VRM, customers can expect improved cement quality and reactivity through optimization of the vertical mill process.
EUCEM ICARE maximizes cement activation potential and improves transport properties, while decreasing energy and production costs, clinker factor, and CO2 emissions.
best they can. We’re also hands on in our role, which gives us the ability to react to events and make crucial decisions at speed.”
It’s a quality that came into particular use during the Covid-19 pandemic. “We were able to organize ourselves rapidly, implementing strong health and safety measures to test, isolate, and protect our people,” Spencer recalls. “Fortunately, our industry was deemed essential, as was the construction industry that we serve. Therefore, we continued to operate effectively, with projects running as best they could, and the ongoing production and shipment of cement.

“Resilience is the word,” he then insists, reflecting on some of the logistical challenges of the period. “Although we source the maximum volume of product possible from within the US, we still rely on supplies from Turkey, Egypt, Germany, and elsewhere. Regardless, we kept going, working closely with many of our supplier and vendor partners to navigate the tough times. They stepped up to ensure they had inventory in stock, or would help us by expediting parts or materials that we needed for our plant operations. It’s a testament to the long-term relationships we’ve built up and maintained over the years.”

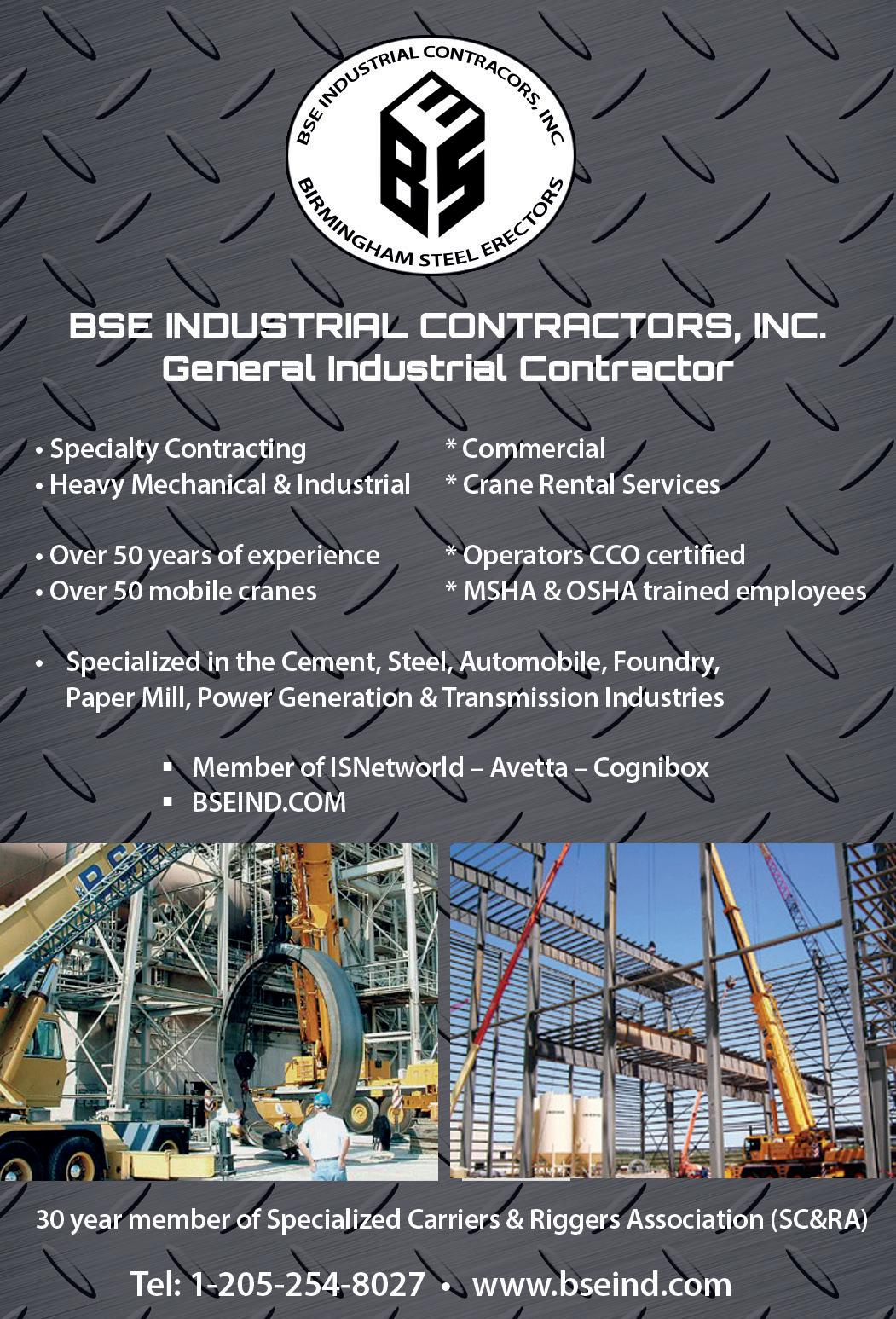
Alongside the expansion of NCCA’s Ragland plant, the company has also increased the capacity of its terminals in Greenville, South Carolina and Jefferson, Georgia. Now, the company is building three new terminals: one in Stockbridge, Georgia, servicing the company’s Atlanta customers, along with two in its Nashville market: one in Dickson, and another in Lebanon.
“These terminals will help us reduce truck deliveries from our Ragland plant,” Spencer confirms. “We’ll be adding to our fleet of rail cars to handle these new terminals, and increasing the loading capacity at the Ragland plant to load more rail cars. We’re continually upgrading our fleets and plants.”
For now, the NCCA remains in transition. “We have one of the most beautiful plants in the country now with the technology available,” Hervé states. “The balance, the emission control, and the tools and devices we now have at our disposal is amazing. We’re ready to face the future with great confidence.”
“With the launch of our new production facility, new raw materials, new fuels, an increasing rail fleet, and the addition of more distribution terminals, we have a lot of moving pieces in play,” Spencer concludes. “In the near future, our focus is to increase efficiency across our operations, so that five years from now we’ll have a highly efficient and productive plant. We’ll continue to execute our carbon reduction plan, servicing our customers with quality, consistent products, that allow us both to grow in tandem.” ■ www.nationalcement.com/nccal
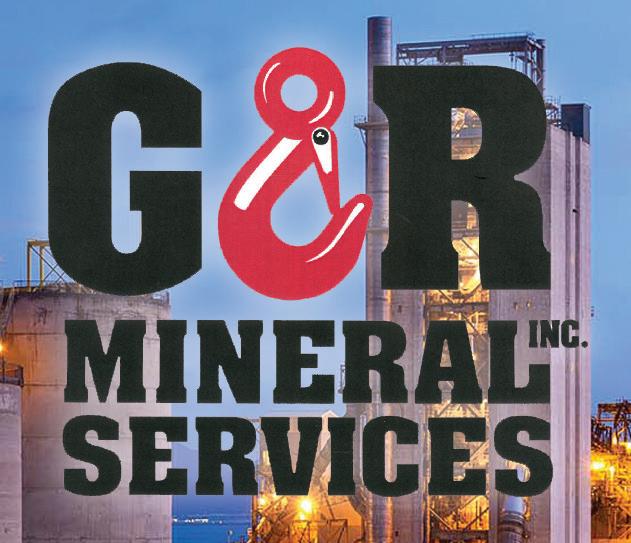
