
10 minute read
Putting Your PEOPLE FIRST: 2021 Training and Safety Excellence Award Winners
TRAINING
World Class
Premier
Shelby Erectors Ironworker Skills Institute
Gold
Gardner-Watson Decking
SAFETY
World Class
Cooper Steel Derr & Gruenewald Construction, LLC FM Steel, LLC High Plains Steel Services
Premier
Black Cat, LLC Gardner-Watson Decking Quality Steel Services
Gold
Pro Steel Erectors
Tracy Bennett is Managing Editor of Connector and Principal Partner of Mighty Mo Media Partners, a marketing consulting firm. Her technical expertise is in construction, lifting equipment, and workforce development.
Award winners share safety trends and training tips
As part of SEAA’s strategy to expand benefits for members, the Safety & Education Committee now annually recognizes member companies for implementation of craft training programs and achieving exceptional safety records. This is the second year for the awards. The next deadline to submit is March 1, 2022. Apply online at SEAA.net/ awards.
In 2021, five companies received the Craft Training Excellence award and nine companies received the Safety Excellence Award. In all, four of those companies received both awards, an indication of how inter-related training and safety are.
Profiled here are the companies that received World Class recognition, the highest level. See list of all winners (left).
Training Trends
Applicants are evaluated on the portability of credentials, availability of apprenticeship programs, training, and recruitment efforts. Evaluations are made in comparison to other companies of similar size, based on the number of ironworkers employed from Jan. 1 to Dec. 31, 2020.
Both award-winning companies are based in Colorado. Derr & Gruenewald Construction, LLC (DGC) employs about 150 people, while High Plains Steel Services has under 30 employees. Both companies also received World Class recognition for its safety records in 2020.
DGC, a member of Ironworkers Local 24, is based in Henderson, Colo, working primarily in the Midwest and Western United States. Established in 1977, DGC offers pre-construction, steel fabrication and erection, engineering and detailing services, as well as pre-cast concrete and metal decking construction. Among the company’s highest profile jobs to date are the Pepsi Center (now called the Ball Arena) in Denver, which is home to the NBA’s Denver Nuggets and NHL’s Colorado Avalanche. They also helped build the McEnery Convention Center in San Jose, Calif.
Founded in 2012, High Plains Steel Services, LLC of Windsor, Colo., is an erector with full-service structural and miscellaneous steel fabrication and industrial coatings divisions, working primarily in the Rocky Mountain region. The company also owns and maintains its own fleet of cranes. In 2017, High Plains uses an NCCER Industrial Ironworker Apprenticeship Program, which is a registered and certified Department of Labor apprenticeship program.
Connector caught up with DGC’s Corporate Safety Director Ed Valencia and Kris McLean, President of High Plains Steel to ask about recent trends in training.
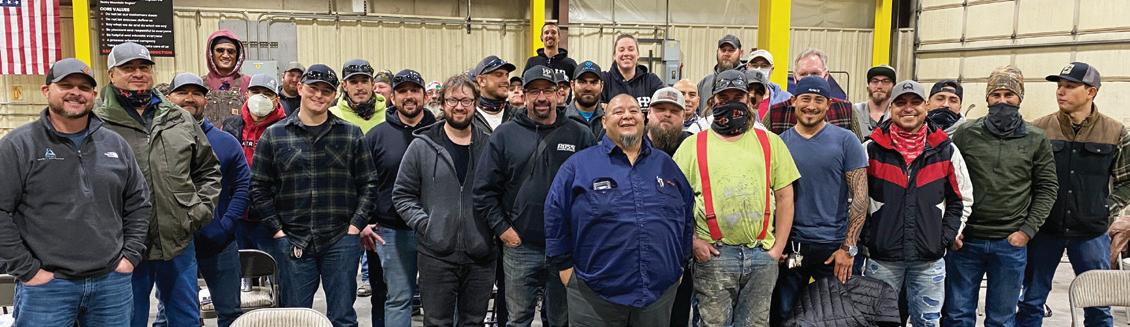
Team members of High Plains Steel Services participate in pre-task meetings every day for both fabrication and erection activities.
What lessons did you learn in 2020 about virtual training?
Valencia: Virtual training is a great way keep employees moving forward in safety performance, but employees still need face-to-face time and hands-on training for complete training.
McLean: It works! However, not for every type of training. We have shifted from no virtual training to doing training that way 30 to 40 percent of the time. This saves both time and money, and it aligns with our focus on becoming 100% digital in other areas of our company. In 2020, we leveraged Tekla PowerFab and other software to become paperless in all aspects of management, quality control, safety, shop production, and erection.
Studies show that the first four hours of a shift is when workers are most likely to suffer traumatic injuries. How important are daily safety meetings in relationship to mitigating risks at the start of the day? What do you do to keep safety meetings engaging, informative, and productive?
Valencia: In my opinion, the No. 1 hazard on a project is managing the schedule. To mitigate that, pre-planning is essential. In fact, pre-planning is among DGC’s four guiding principles when it comes to safety. We consider this to be the most crucial aspect to creating a safe and productive project. This is the second year in a row that High Plains Steel Services has Jobsite safety planning is received World Class recognition for Craft Training. as important as planning for production schedules, manpower and logistics. Our structural engineers create detailed plans for shoring systems, erection procedures and critical lifts. A key part of this for us, the subcontractor, is working for a reputable controlling contractor who will provide level and stable boneyards and a clean and organized project.
McLean: We religiously have pre-task meetings with fabrication and erection teams before pre-task meetings with fabrication and erection teams before starting work each morning. Daily tasks and safety risks are identified and all employees sign off before starting work. This ensures that all employees know the intent of the work to be completed and all potential risks.
Are there any new OSHA regulations or changing standards that are on your radar? If so, how will you address this through training?
McLean: Yes, the big one is pending vaccine mandates. Until we get a clear direction from OSHA, we are a bit up in the air regarding best practices, which is frustrating. (Editor’s Note: As of 11/05/21, OSHA issued an Emergency Temporary Standard for employers with 100 or more employees, which had a comment period that was open until 12/06/21.)
Did you participate in the 2021 Stand Down to Prevent Falls? If so, what is the value of doing “stand downs”? Do you ever do this for other topics besides Fall Prevention?
Valencia: Yes,we participate in it every year. Last year we also created a campaign to raise awareness about pinch points and hands safety to bring awareness to a problem we were observing.

This is the second year in a row that High Plains Steel Services has received World Class recognition for Craft Training.
McLean: Yes, all of our erection crews participated in the Fall Prevention Stand Down. These events are not much different from our usual weekly safety meetings, however , I do think it’s good to have a spotlight on the risks we face. It takes the day-to-day monotony of safety meetings and mixes it up a bit.

At Derr & Gruenwald Construction, project managers and superintendents lead the safety program as they manage the project.
Safety Depends on Maintaining a Stable Workforce
The Safety Excellence Award was issued to nine SEAA members in three categories for achieving excellent 2020 safety records. Recipients were selected based on evaluations of their EMR ratings, OSHA 300A statistics, and safety program processes over the last three years. Scoring was based on points assigned to a multi-criteria analysis, and conducted in blind review by members of SEAA’s Safety & Education Committee.
Four companies achieved World Class recognition. In addition to DGC and High Plains Steel Services, also profiled for their Training Excellence, are Cooper Steel and FM Steel Construction, LLC.
Connector interviewed each company to get a look inside their safety culture and understand the best practices they are applying. The following individuals were interviewed.
❚ Jason Farris, VP of Safety Compliance, Cooper Steel, Shelbyville, Tenn.
❚ Ed Valencia of DGC
❚ Michael Mulsow, Director of Operations, FM Steel Construction, LLC, Gilbert, Ariz.
❚ Kris McLean of High Plains Steel
How would you describe the safety culture at your company? What role does the C-Suite or other leaders play in driving the safety culture at your company?
Farris: Cooper Steel’s culture is based on our Core Priorities 1-Safety, 2-Quality, then 3-Production. We continuously look for ways to improve in all three areas, but we never stray from that order. We believe our people are our most important resource. For that reason, feedback on safety concerns travel both ways, top down and bottom up. Everyone is involved in improving the safety culture.
The C-Suite sets the tone with our Core Priorities, and they are actively involved in our safety culture. All jobsite safety audits are reviewed weekly by executive management. The safety department meets bi-weekly with executive management to discuss the direction of our safety program and what roles we all can play to ensure we are always improving. We are continuously seeking feedback from all levels throughout the company on how we can become stronger and safer. This information is shared with all levels of management.
Valencia: At Derr & Gruenewald, project managers and superintendents lead the safety program as they manage the project. This means they apply safety planning to the specific situations of that job.
Mulsow: As a newer company, we have a lot of younger guys that all seem to welcome safety without hesitation. And management believes in leading by example.
McLean: We have a safety committee that reviews every reported injury and updates policies accordingly. The safety committee members include all of our executives, HR Manager, and Operations Managers for both our Fabrication and Erection Divisions, Safety Manager and our Insurance Brokers Safety Manager, as well as myself. We analyze policy, near misses, changing regulations, and injuries to make sure we are staying on top of trends and keeping our team safe.
Falls are the biggest risk for steel erectors. Are there other risks that are on your radar, and what best practices can you share?
Farris: Ensuring employees new to the industry are getting the proper training is a priority for fall prevention. We study plans for the project ahead of time to make sure the proper fall protection systems are in place. We put a lot of emphasis on pre-planning so our crews have the proper equipment they need to perform their jobs safely.
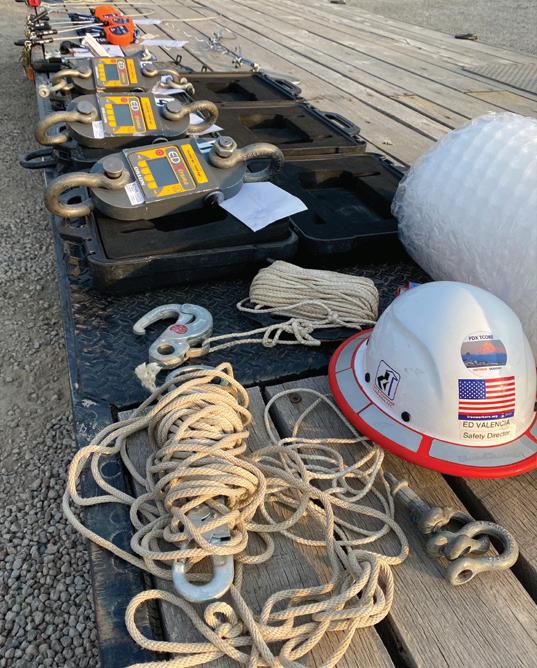
Testing equipment used by DGC to confirm fall distances in drop testing.
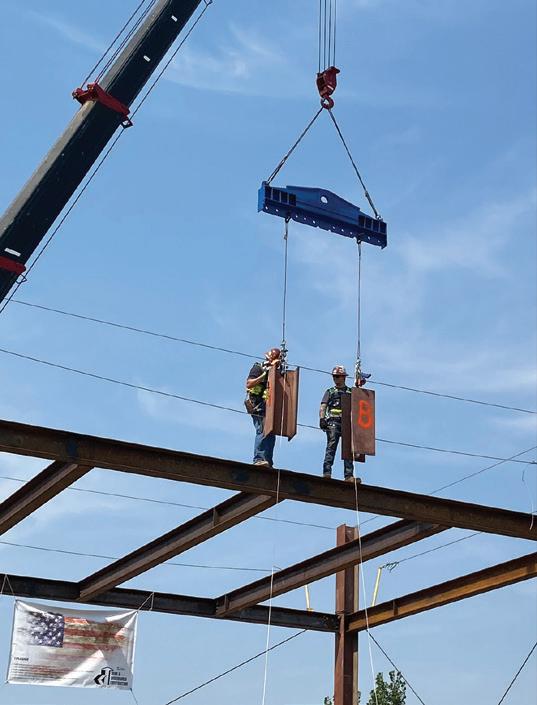
DGC has opened use of its training tower to other SEAA members.
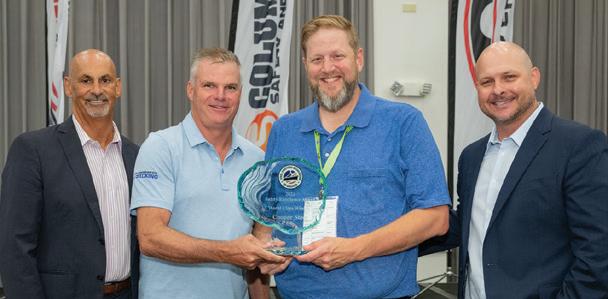
Cooper Steel’s culture is based on its Core Priorities: 1-Safety, 2-Quality, then 3-Production.
Valencia: We recently built a research and training tower that we use to conduct drop tests on all the equipment we specify to confirm fall distances and to ensure that the systems work. For example, we drop tested our test weight on a 10 ft cable anchorage basketed around a beam with an 8 ft SRL; the system failed and the weight hit the ground. Of course, we also always follow the manufacturers recommendations. In addition, we are in the process of developing rescue training to complete our fall protection training curriculum.
Mulsow: Fall prevention always comes down to proper tie off. We use outside safety training from Trivent Safety Consulting for all employees before allowing them to get up on the steel.
McLean: Lately, the use of cut off disks has been a hot topic in our organization. Traditionally, a cutting torch is used in the field, however, over the last 10 years we are seeing greater adoption of cutting disks across the industry. This practice is contributing to the bulk of our near misses and incidents. After talking with other safety professionals, it sounds like these cut off disks easily fragment, becoming like shrapnel when one flies apart.
How did you navigate new safety requirements around COVID-19 protocols on job sites?
Farris: Sharing tools was prohibited unless they were disinfected between use, and employees disinfected their tools and equipment daily. We found that face masks greatly increased heat stress in the warmer months, so when it was an option, we chose to maintain social distancing rather than wearing face masks. We also moved employees into separate hotel rooms to reduce the risk of transmitting COVID. FM Steel’s management believes in leading by example when it comes to safety.
Valencia: Besides following all state mandates, we created an awareness campaign.
Mulsow: Most of the time, employees were able to work six feet apart. The biggest struggle was when two workers were in the platform of a boom lift or scissor lift. In those situations, face shields and masks were required.
McLean: Initially we created a COVID 19 Safety Policy which outlined mask wearing, reporting of sickness, return to work policies, etc. It has been revised a couple times in the last year and a half due to changing circumstances. We are currently approaching new regulations, such as vaccine mandates, on a project-by-project basis until OSHA provides a final determination.
Looking ahead to 2022, all four men agreed that the biggest safety challenge they face is related to having enough qualified workers. “Maintaining a properly trained workforce is a constant challenge,” said Farris. The key is finding a good balance of new employees working with experienced employees. Mulsow agrees. “It is difficult to keep up with training as we constantly hire new workers to meet the labor demands,” he said. Related to safety issues caused by a labor supply shortage, McLean says that finding ways to reduce turnover is integral to achieving good safety records. •
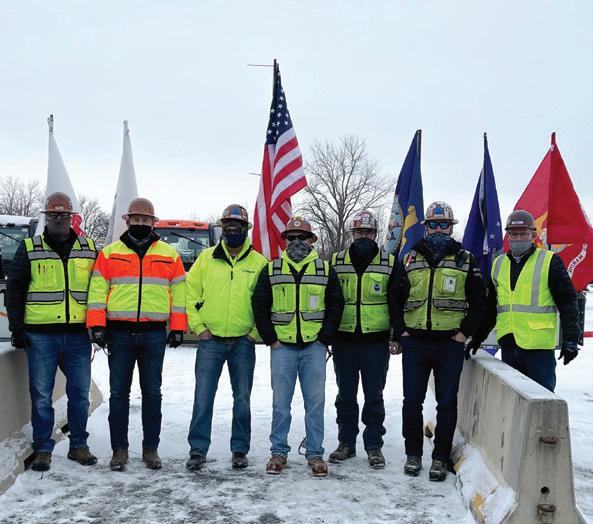
During a Topping Out Ceremony, the Cooper Steel team celebrates safety on the job site.

FM Steel’s management believes in leading by example when it comes to safety.