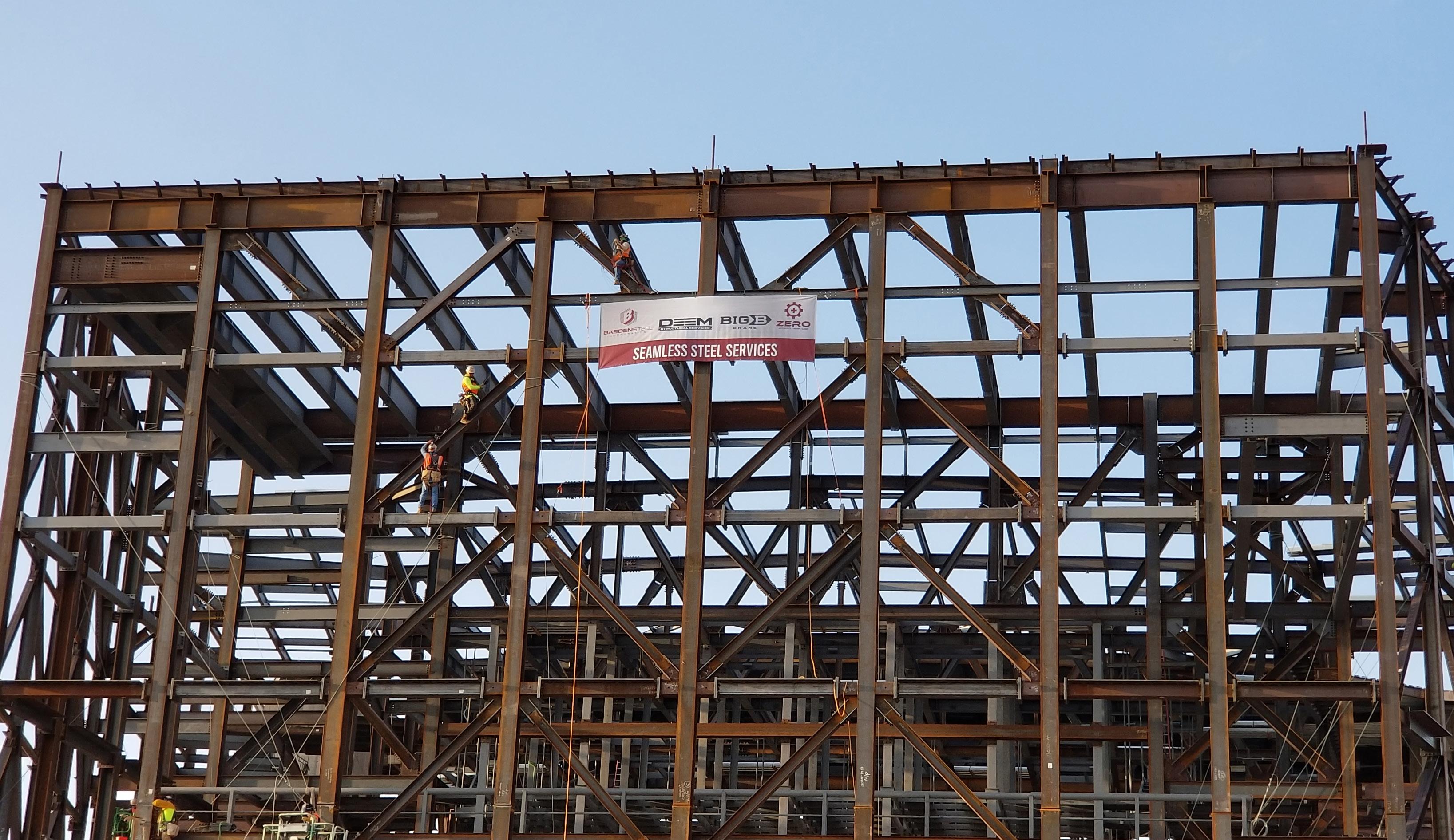
12 minute read
Management - Asking the Right Detailing Questions
Why Communication Problems in Construction Increase the Price Tag
Years ago, David Deem worked as a project manager at a structural fabricator that did its detailing in-house. If he had a question about sequencing, connections, or any other, well, detail on the details, he’d walk over to the detailing manager’s office. Today, Deem is President of Deem Structural Services, Longview, Texas, and President of SEAA.
Today he brings an erector’s perspective. A beam leaving the fab shop doesn’t have much value on its own, at least not until the steel erector does its job. So how can that beam have the most value—to make the most money for everyone involved? “It’s all about good communication,” Deem said, “and asking the right questions.”
Challenging elements of the job site can cause small problems to snowball into large ones in a hurry, which can make communication problems in construction especially costly. Today’s software can track beams from the time they’re drawn to the time they arrive on-site, flagging problems far ahead of time. But things happen and beams sometimes don’t arrive when they’re needed. This is why no software can replace good communication practices.
Tim Heston is the senior editor of The Fabricator magazine. He has covered the metal fabrication industry for 25 years. This article is excerpted with permission from his original article “Best communication practices in structural steel fabrication.” Read the full article here.
“It’s always good practice to get on-site to see what the erector is dealing with,” Deem said. He described a snow-covered job site at a university campus. The erectors had just two days, from early Saturday morning to late Sunday afternoon, to build a pedestrian bridge. That particular job was completed on schedule because everyone was on the same page, and all drawings and other documents had exactly what the erector needed to know.
Sequence matters
Picture a crane picking a beam between two buildings with no extra room for maneuvering. The structural beams needed to be delivered in just the right sequence at just the right times. This calls for close collaboration among the detailer, erector, and fabricator.
But if a fabricator and detailer move ahead before an erector is chosen, it can lead to greater costs and extended schedules. When the erector is finally chosen, they are told to start with Building A. But it’s abundantly clear from looking at the drawings and the job site that it would be so much easier to start with Building B. But the ball’s already rolling, and the erector makes do, though expenses and delays keep mounting. Good communication could have avoided all these headaches, and much of it could have been covered during the site-specific erection and safety plan.
“We love to have the detailers involved, when possible,” Deem said. “Regardless, though, there are things detailers can ask fabricators from the get-go. These involve the sequence and schedule, as well as shipping requirements.”
Say a detailer sees a girder in the plans that’s 100 feet long, but the site won’t allow for a 100-ft. girder, be it because of space constraints, limited crane capacity, or a combination of both. “If that’s the case, what splices do we need? Where are they? Are they bolted or welded? Is there value engineering involved? Will it be shop welded or field welded? These are all things that, as erectors, if we’re invited to the party, we’ll be glad to discuss,” Deem said.
Just one missing beam can add entire days to the project schedule, sometimes more. Cranes need to be at the right spot for a particular pick. Weights on trusses need to be added and removed in just the right sequence for structural stability during erection. “In many cases, all the material has to be there in the right place, with the crane in the right spot, or it’s just not going to get erected,” Deem said.
The best connections
“You now have a lot of connection design responsibility being delegated to fabricators, who then delegate it to the detailer,” Deem said. “And in many ways, that’s a good thing, because the erector can communicate directly with the detailer to achieve connections that are safe, more efficient, and work better for everybody.”
Deem called these “erector-friendly” connections— those that are safe, easy to perform, and abide by OSHA requirements. If a worker needs to climb a high ladder just to access a connection, there’s a good chance the connection is not erector-friendly.
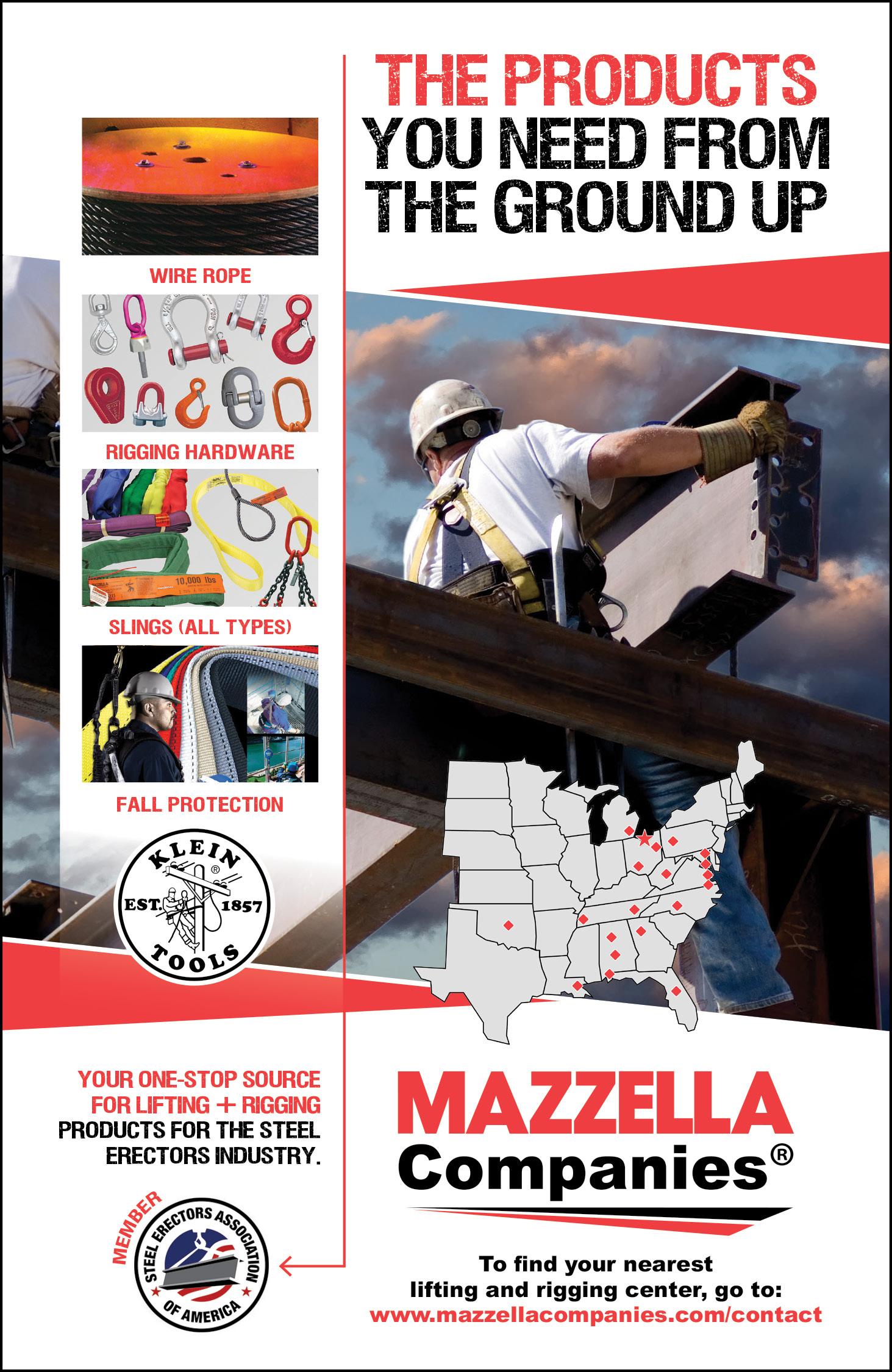
From the steel erector’s perspective, there can never be too many erector aids, such as L-shape plate welded onto the end of a hollow structural section that provides necessary support during the erection sequence.
On multistory structures, specific column-splice locations also make the erector’s job easier. Deem emphasized that practices might vary depending on the job and erector, but his company prefers column splices to be about 4 ft. from the top of steel (deck plate), spaced in such a way so that the erector can erect two floors at a time. With the first floor installed, the erector would work upward, installing girders and deck plate for the second and third stories, with a column splice 4 ft. above the third-story deck plate. The next column splice would be two stories up from there, 4 ft. above the fifth-story deck plate, and so on. This column-splice sequence allows erectors to work in twostory “batches.” Place those splices farther apart, and the erector needs to strategize how to pick, manipulate, and place interior beams between those tall columns.
Some structures, like three-story buildings, might specify single tall columns with no splices at all. It’s not ideal, Deem said, and it does require some upfront discussion, particularly if exterior columns make it impossible to place interior beams. The key again is communication.
Double connections
OSHA does not allow double connections at columns and beam webs—that is, two connections sharing connection holes— without certain erector aids. Bolts do need to be staggered, so that no one bolt needs to support all three members. But the staggered arrangement still needs those erection aids. These can be an angle seat (welded angle iron support) or connection flange with a notch that allows space for at least one bolt from the opposite member to remain in place as the second member is bolted in place. Without these, the erector needs to have a welded seat or a member to support the load during the double-connection process. Fabricating these on-site isn’t ideal, of course, with a massive crane on-site and a schedule to keep.
If beam connections share the same hole pattern, yet only one beam has an angle seat at the connection, the drawings should specify on which side of that connection to start, per the sequence. Or, a fabricator can simply place an angle seat on both sides, so that no matter the sequence, the connections go together per OSHA requirements.
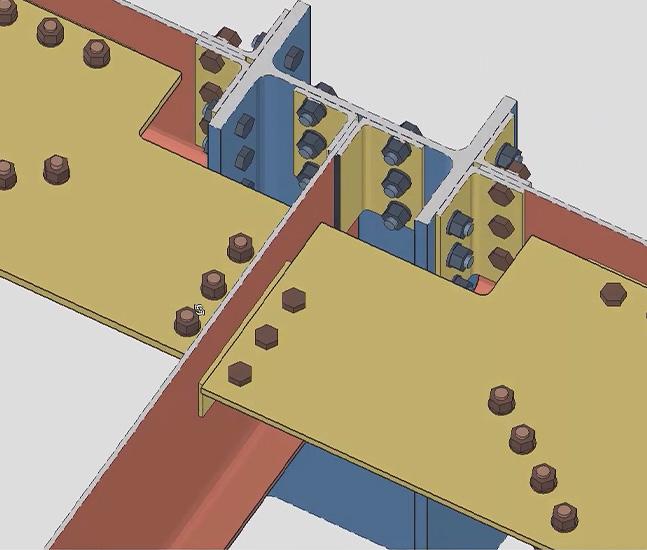
OSHA also requires erectors to use perimeter safety cables before erecting the next tier, and those cables need to go through holes or otherwise be securely attached to the perimeter columns. “If a fabricator sends me a perimeter column without holes or tabs to run our cables through, OSHA says I’m not allowed to stand that column until I do something about it,” said Deem.
Specifics vary depending on the job, but often the ideal column has four anchor bolts or rods; holes at the top of columns for a shackle or a pull pin; holes for perimeter cables; plenty of double-connection aids; perhaps even a few tie-line holes for a fall-arrest system; bolted joist seats; and, not least, some extended shear tabs to allow easy connecting, including the bolting and torqueing that’s needed at moment connections.
The right shear tabs can make an erector’s job much easier, faster, and safer—and it’s a key erector aid that can be discussed, especially if connection design has been delegated to the fabricator. With representatives from the erector, detailer, and fabricator sitting at the table, the three can discuss if and where shear tabs make sense. With everyone on the same page, the fabricator then can write a request for information (RFI) to get those shear tabs approved.
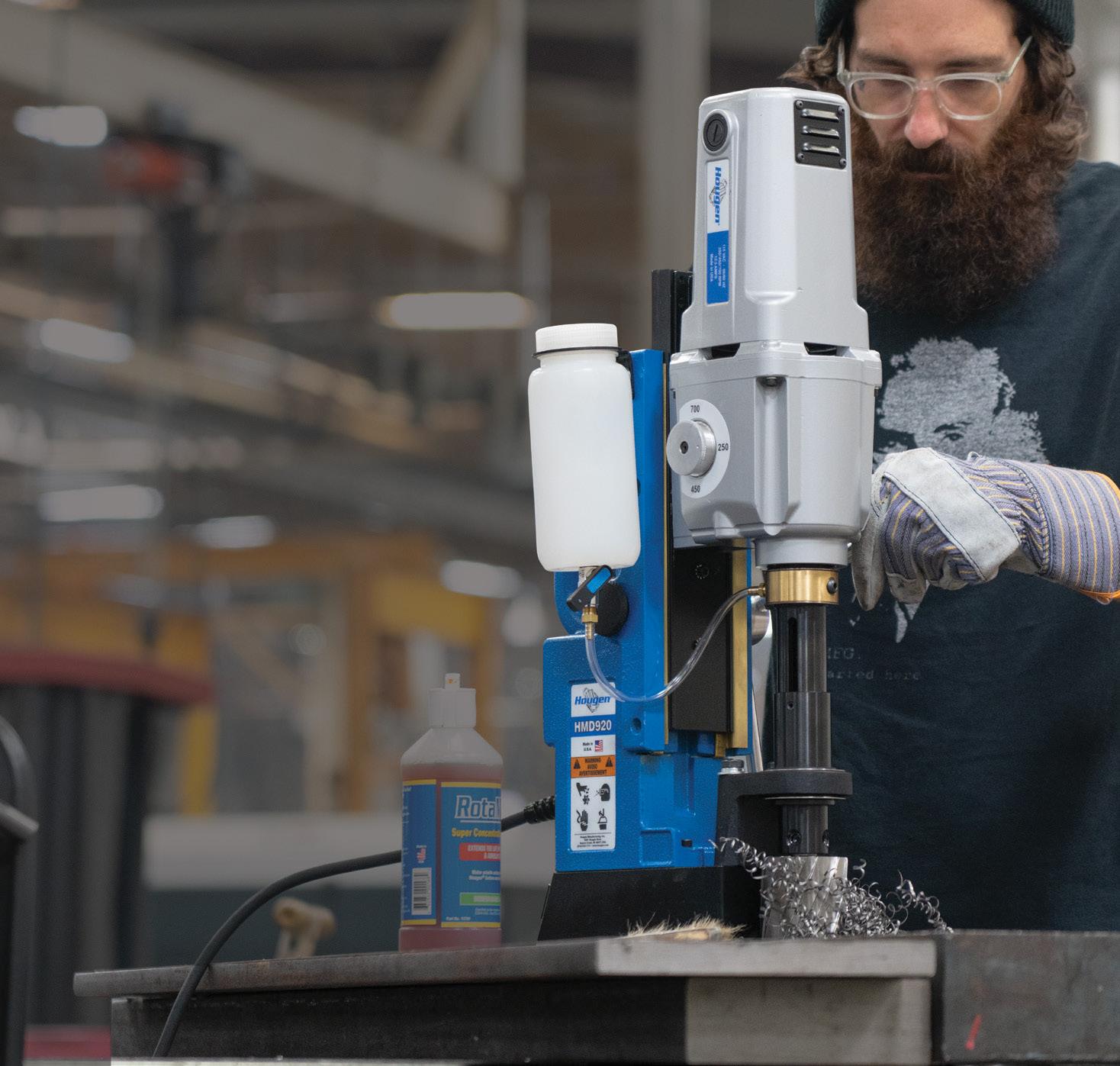
Deem conceded that extended shear tabs do require welding, which is something fabricators may not want to do. In these cases, Deem has proposed a shear-tab alternative, if the loads will allow. “It’s essentially a shear-tab connection that’s a bolted angle clip. Those angles are bolted in the shop. Then when it comes to me, it’s essentially a shear tab.”
Another common issue comes with bracing connections, with HSS or similar
Solving 10 Common Field Errors with SDS2 by AllPlan
As the industry adage goes, errors cost $10 for a detailer to fix, $100 for the fabricator, and $1000 for the erector. Many software solutions still depend on the structural steel detailer to examine the complete node, consider conflicts that might occur during erection, and make tedious adjustments on each member in the model or drawing. SDS2’s automated connection design is built with the end goal in mind—a completed project. It is the only steel detailing software with erectability intelligence, considering the complete node in its connection design calculations and reducing the potential for human error when it comes to identifying job site complications.
Below are ten common field issues that SDS2 automatically checks and adjusts for as you generate your model and drawings. Some functions—in particular, those built on AISC, CISC, or OSHA specifications—run by default with SDS2’s automated connection design functionality. But many can also be controlled and customized with additional setup options according to fabricator and erector preference.
1. Insufficient Bolt Clearance

2. OSHA Safety Connections
3. Erection Aids
4. Inadequate Framing Clearance.
5. Incorrect Material Orientation.
6. Conflicts with Opposing Connections
7. Inadequate Connection Clearance
8. Tool Clearance
9. Shank Out
10. Over-Designed Connections, such as eliminating unnecessary bolts member connecting at a 45-degree (or nonperpendicular) angle to a base member. It’s common for those bracing connections to have just one hole. That means the erector must partially bolt and then use tools to ensure everything is properly aligned before tightening the connection. In these cases, two or more bolt holes make an erector’s job much easier. The company’s preferred connection is bolted bracing, which eliminates welding—a time and money saver.

Minimizing field work
The more field welding and cutting a project takes, the more complex and expensive it becomes. Deem described several instances in which an erector’s initial bid assumed connections would be bolted. Then as the contract documents made their way through approvals, the engineer increased the loads, which in turn required more full-pen welds.
Are those fillet welds sufficient to take the loads? They might be sufficient, or they might not. But if the erector is involved in the discussion, then at least the question is being asked.
Often a fabricator will send the angles for the erector to field-cut, which can be problematic, because on many job sites, no one can fire up a gas cutting torch without approval from the engineer of record. Of course, doing more fabrication in the shop doesn’t always make erection easier. A fabricator might think adding stiffener plates on both sides of a beam is helping, but on-site the beam with both stiffeners simply doesn’t fit. So the erector has no choice but to cut the plate out and field-fabricate during erection. With the right communication with the erector, the detailer and fabricator would have known to leave one stiffener plate off, to be welded in the field.
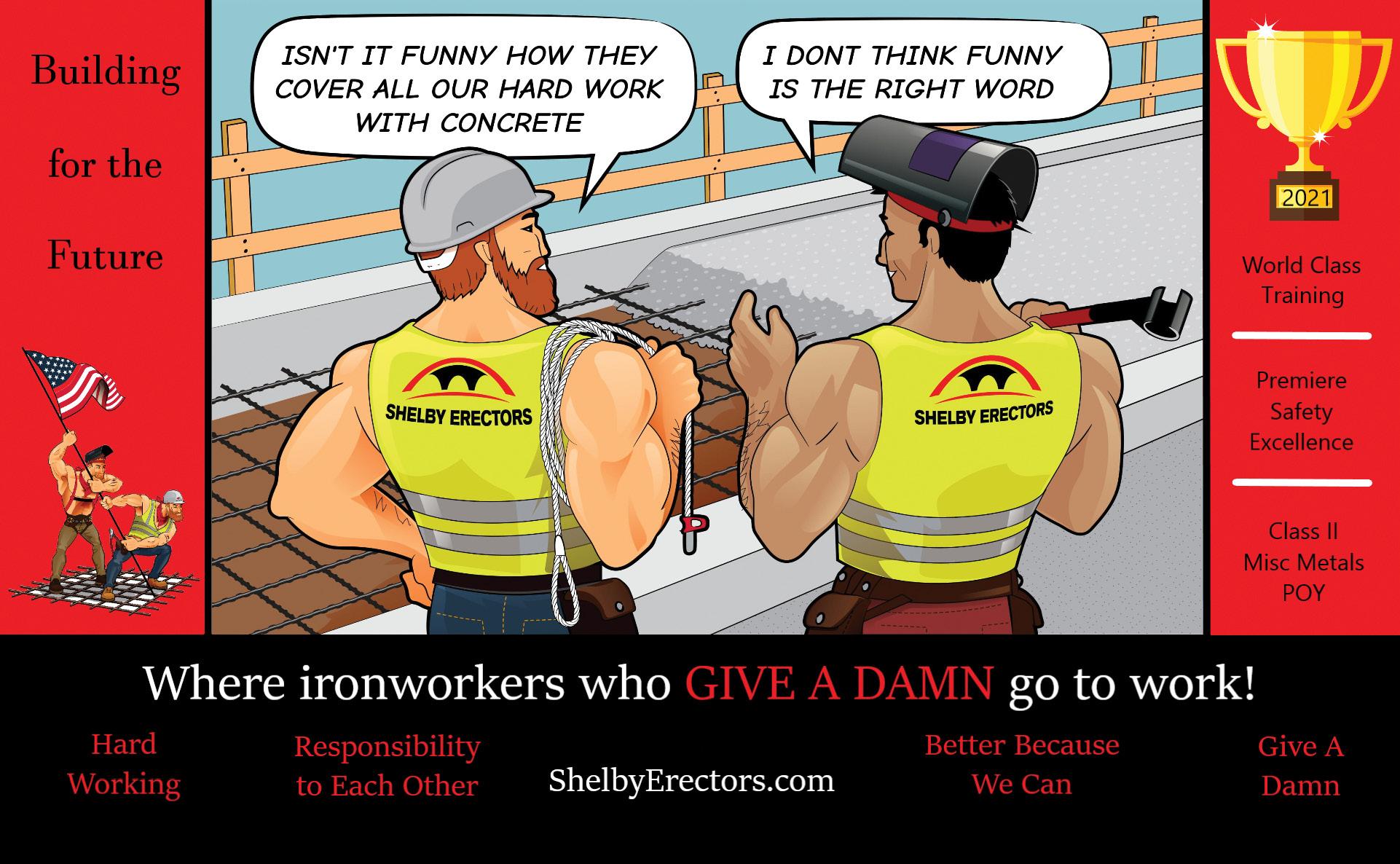
Another pet peeve: a weld-all-around symbol on a drawing. “That’s every erector’s favorite weld symbol,” he said sarcastically. “Sometimes you can’t even weld all the way around. And we know we probably don’t need to weld it all the way around. This is where we need detailers, through the RFI process, to ask the question.”
Welding costs money. A continuous weld costs more than a stitch weld. Overhead welding costs even more. Tough-to-access full-penetration welds are costlier still.
Avoiding days lost
Imagine a situation in which the detailer contacts the general contractor and asks about a dimension for an elevator shaft in the middle of a building.
He doesn’t get an answer, so to protect himself, he puts the connecting beam on hold. Of course, that hold halts the entire erection sequence—all because of a few W10x12 beams.
“So now I’m out there with a huge crane, and I can’t hang any of the building, all because of these little W10s,” Deem said. “But if we’re proactive, we can keep things on schedule.”
The erector can field-fabricate to the dimensions when they’re available. In the meantime, erection can continue on schedule. Yes, this might increase field fabrication costs slightly, but it’s nothing compared to the days lost while beams are on hold as an RFI remains unanswered.
“I can get paid for work I did,” Deem said. “But anyone will tell you that it’s extremely difficult to get paid for work you didn’t do.” When a project is on hold, it can be extremely difficult to get paid for those lost hours. •
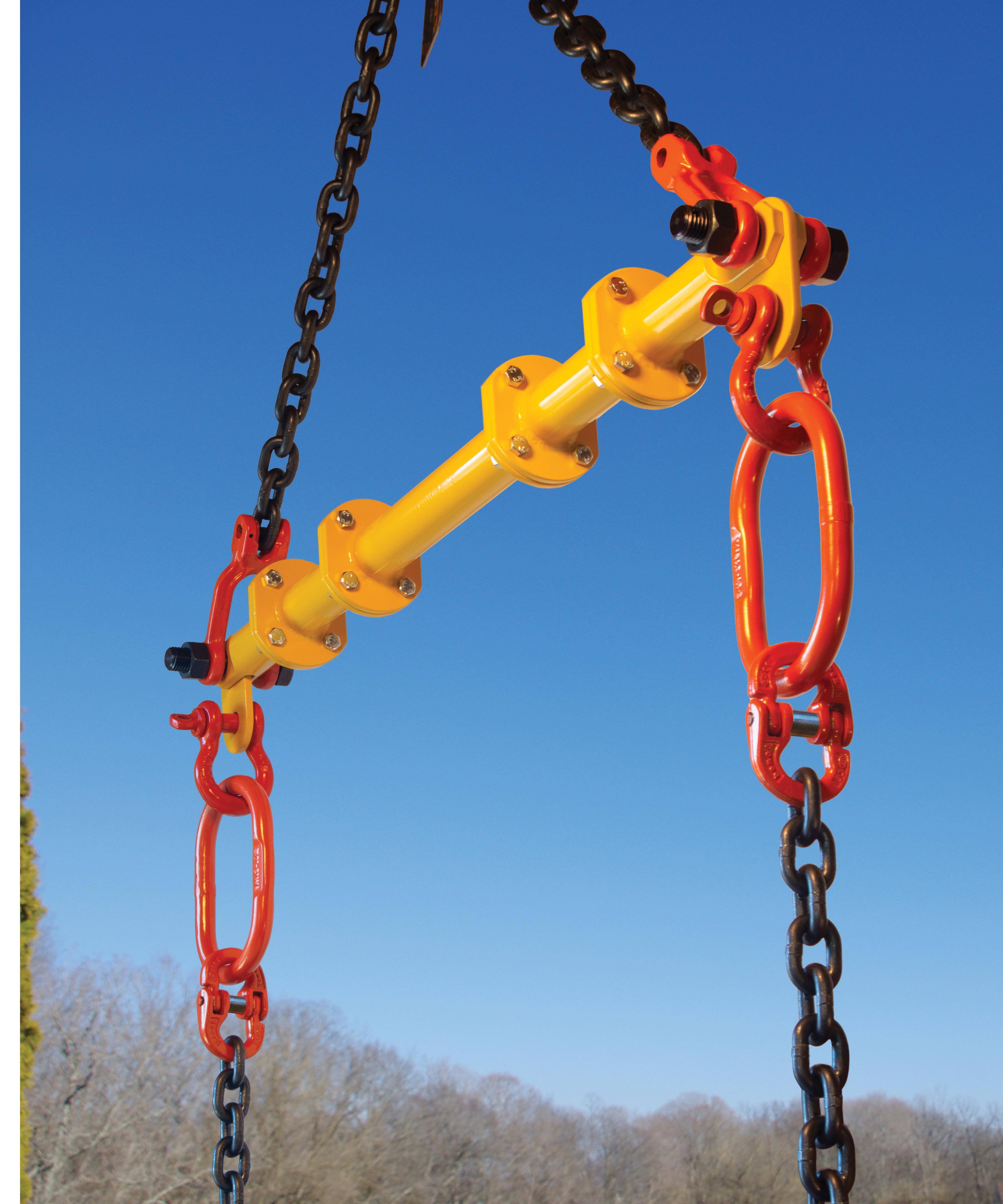
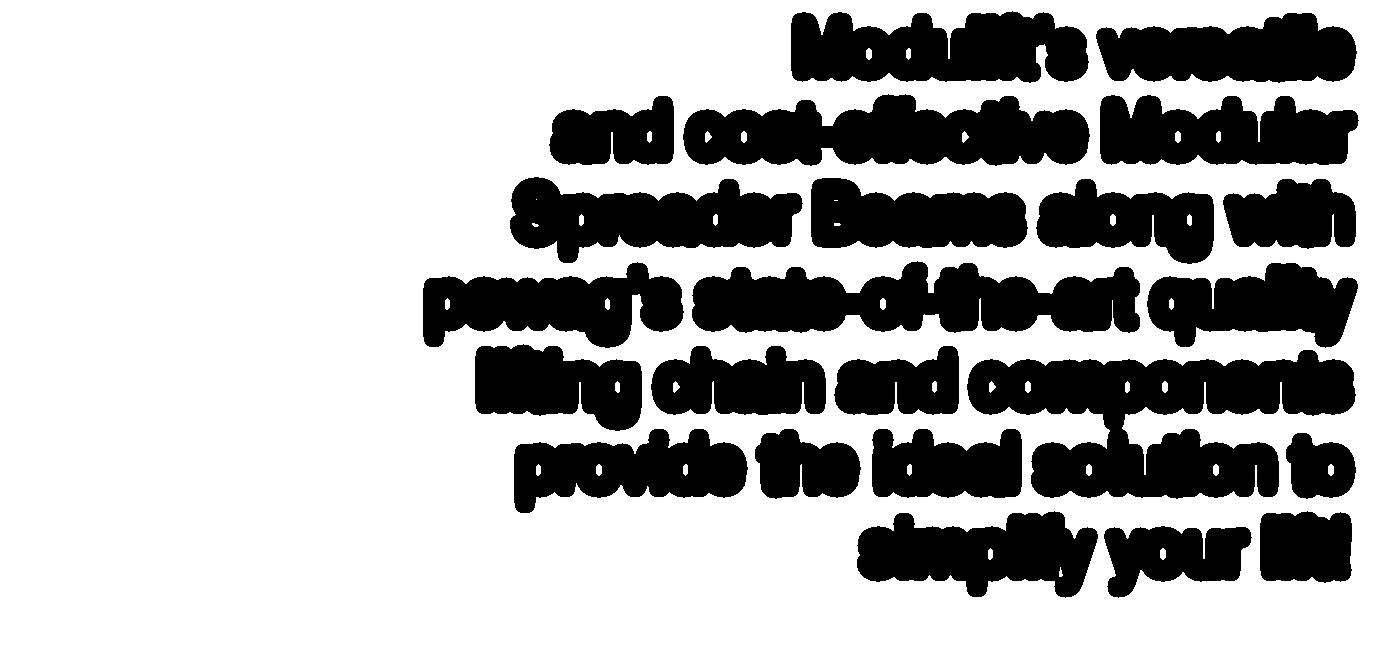