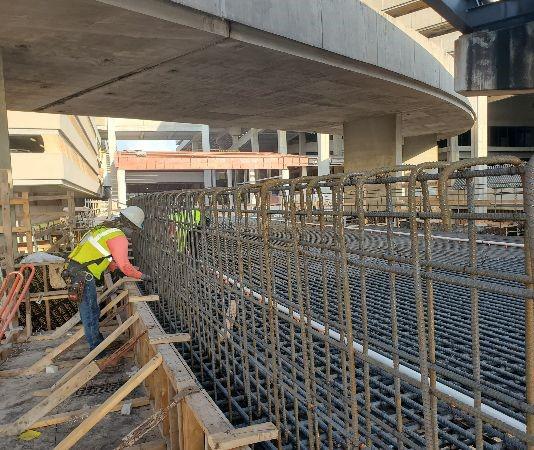
8 minute read
Product Focus
Up Next Issue
Structural Class III ($1 Million to $2.5 Million) Williams
■ A Perfect Fit for Pedestrian Bridge
Brightline is a privately owned passenger train line in Florida. More than just a transportation service, the overall project is part of a real estate vision to re-energize neighborhoods with transportation hubs by building modern, attractive stations. The Aventura Station, for which Hodges Erectors, Inc., assembled and placed a pedestrian bridge is one of those stations.
The passenger trains are designed to accommodate wheelchairs and other assistive devices. They feature bike storage, luggage check, and dining. The high-speed locomotives are American-made and are powered by clean biodiesel for lower emissions and reduced noise.
“Brightline’s new south terminal at Orlando International Airport is part of the company’s Phase 2 expansion into Central Florida, and eventually Western Florida with a Tampa hub. Ultimately the project is expected to have a $6.4 billion economic impact on the state. We are very proud to be a part of this major Florida project,” said Jorge Amador, President of Hodges Erectors, Inc.
Assembling the pedestrian bridge on the street side of a space-constrained job site took several weeks to complete, and was the easy part of this project. Unforeseen circumstances added complexity to a task that already required close coordination with the GC, Lemartec Corp., Florida East Coast Railway, and Florida Power and Light. It was decided early on that the only way to accommodate our work was to make the lift at night,” said Jorge Amador, President of Hodges Erectors. Disruptions to traffic on an adjacent roadway and live railroad track with high voltage power lines overhead had to be minimized.
Crane challenges
First, Hurricane Ian delayed the date that the bridge was to be installed. The crane that Hodges Erectors’ crane rental partner had planned to use—a 650-ton all-terrain crane with Superlift attachment—was no longer available due to being requisitioned for emergency powerline repairs in the aftermath of the hurricane.
“Beyel Brothers came up with an alternative plan to use a 300-ton crawler crane instead and were generous to discount the cost based on our original crane choice,” said Jeff Justice, General Superintendent for Hodges Erectors.
The Liebherr LR 1300 SX lattice boom crane required more loads to be trucked in, more room for setup, and had to be setup in a different location than originally planned. In addition, the railroad required that the crane be de-rated to 50% capacity for any lifts over railroad tracks.
Justice mapped out on site the exact location for the center of the crane and the minimum and maximum radii, and carefully calculated the actual total weight of the bridge, accounting for weight added for galvanizing, bolts, decking, etc.
Tulsa Downtown Pergola, Tulsa, Okla.
Misc. Metals Class I (Up to $500,000)
Erector and Fabricator: Basden Steel Corp.
Architect and Structural Engineer: Corgan
GC: Flintco
Contract Value: $478,415
Tons of Steel: 37.3 tons
Topped Out: December 2022
Structural Class IV ($2.5 Million and up) Derr & Gruenewald Construction
Beyel Brothers then used 3D Lift Plan from A1A Software to establish the lifting plan and rigging plan. They checked for clearances to nearby power lines (that were to be de-energized for the lift), confirmed
TIA Blue Side Expansion, Tampa, Fla.
Misc. Metals Class II ($500,000 to $1 Million)
Erector: Shelby Erectors
Fabricator: Commercial Metals Company
Architect and Structural Engineer: Hensel Phelps
GC: Superior Construction
Contract Value: $728,796
Tons of Steel: 834 tons
Topped Out: May 2022 adherence to the 50% de-rating, and established ground bearing pressures.
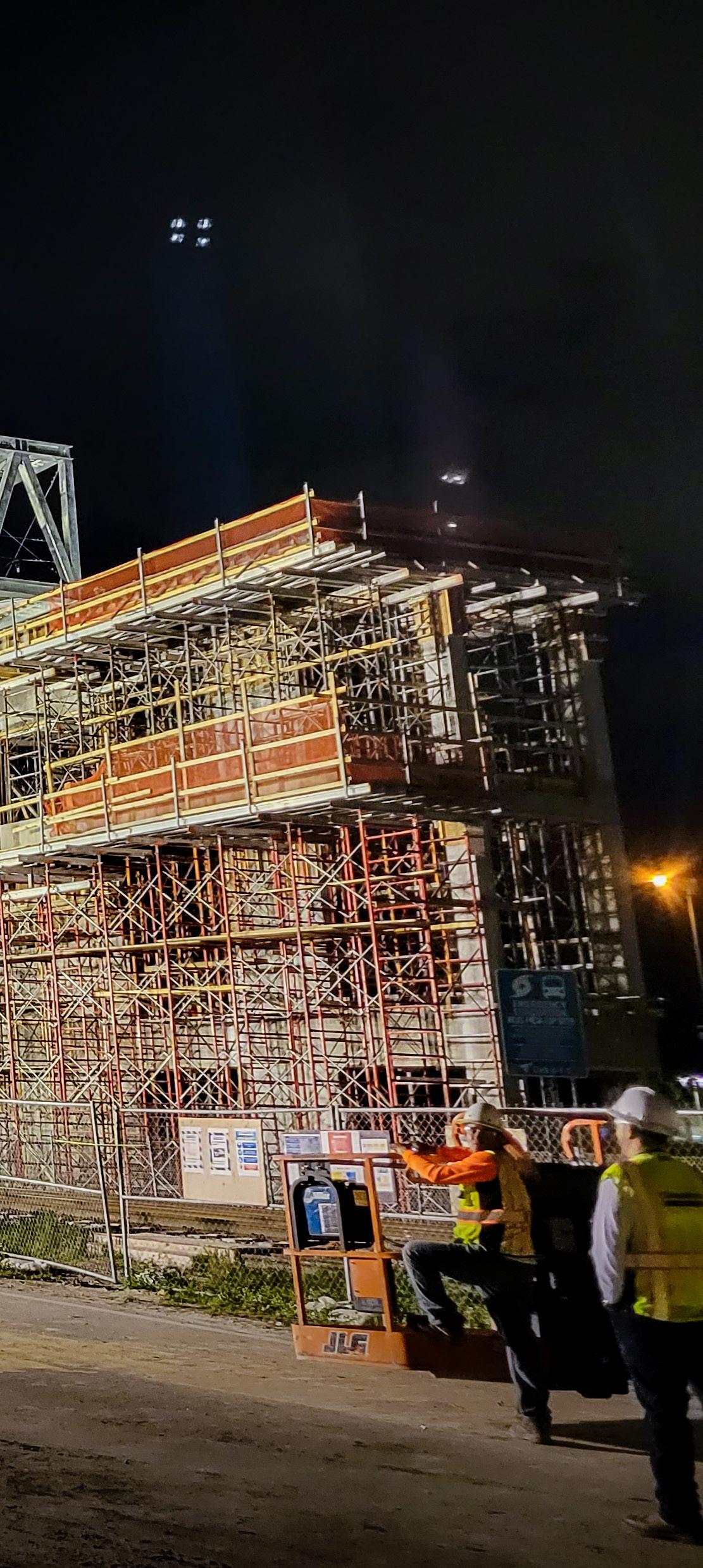
“Then just a week before the crane was due to be delivered, the crane operator was in a car accident. Beyel Brothers didn’t have anyone else available that was qualified to operate this crane,” said Justice. They had to hire someone new.” In the meantime, construction continued on the structures where the bridge was to be set, creating an even more challenging bridge placement maneuver. The 78-ton, 135-foot long bridge had to be lowered into 16 foot wide sections on either end with less than 2 inches of leeway on the sides.
“To make sure the bridge section would fit, the GC conducted an as-built analysis on the structure, measuring anchor bolts, embeds, and concrete structures. Hodges Erectors did the same for the bridge,” said Justice. “With that information, we determined, that although tight, it would fit, as long as the bridge remained plumb during the lift,” he said. The day before the lift, the team conducted a load test to confirm the weight was below the restricted capacity and to verify that the bridge would lift up level, adjusting rigging as needed.
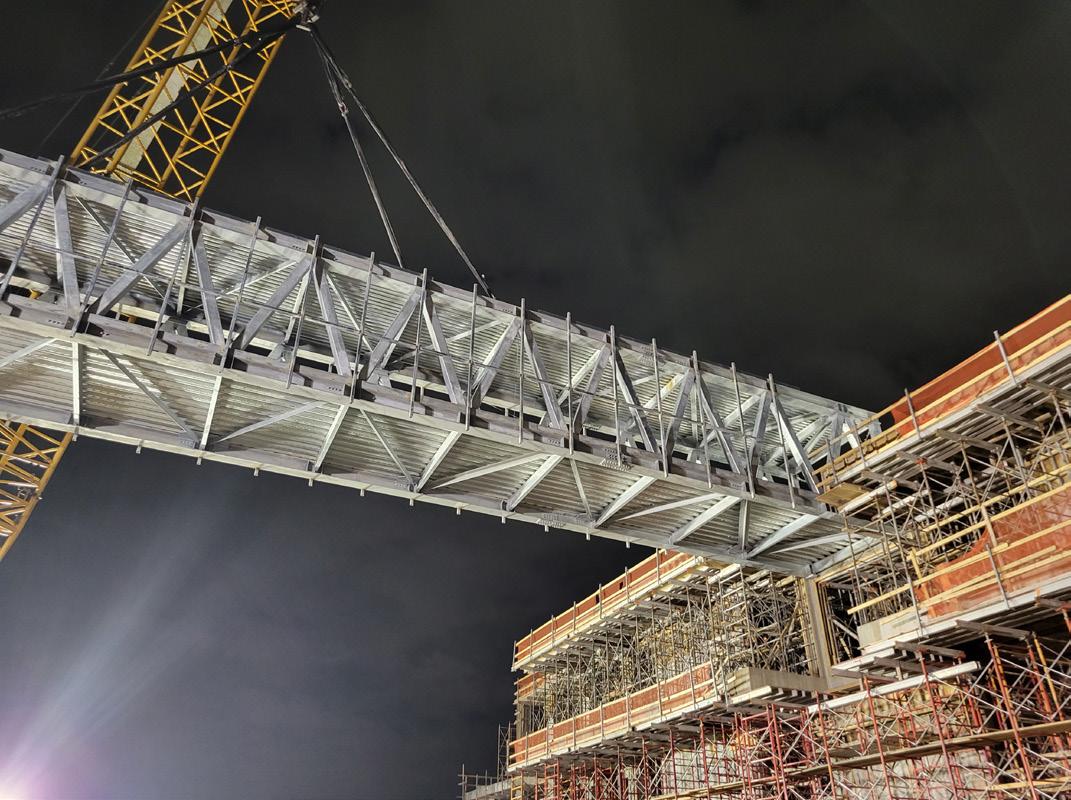

One shot, three hour window
“We coordinated with Florida Power and Light to de-energize the power lines between 5 am to 11 am the day the crawler crane arrived, and again the next day from 2 am to 8 am.” During that time, the road where the crane was set up was closed to traffic, and the railroad closed the tracks to all trains from 2 am to 5 am. Previously, the railroad and Hodges Erectors had established a plan for aborting the lift if a freight train were to arrive ahead of schedule.
“Three hours, this was the maximum time allotted for us to get the bridge lifted and set in place—so it had to be a perfect fit,” said Amador. At 2 am the crane lifted the bridge just off the ground and waited. At 2:30 am the railroad sounded the all clear whistle. By 5 am the bridge was in place, then the crane was moved away from the tracks.
And if that wasn’t enough pressure, this project had attracted the attention of local media and the public. More than 50 onlookers watched the bridge placement. “That’s the most eyes I’ve had on an active bridge erection in all my years of doing this job,” said Justice, which was an indication of the importance of the project to the community.

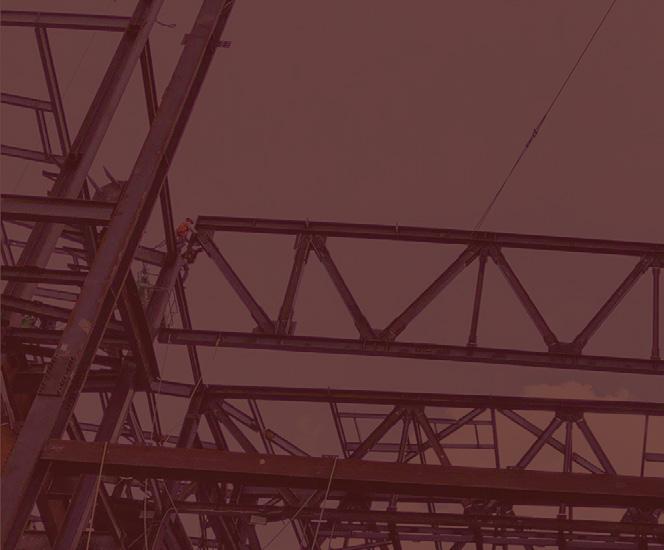
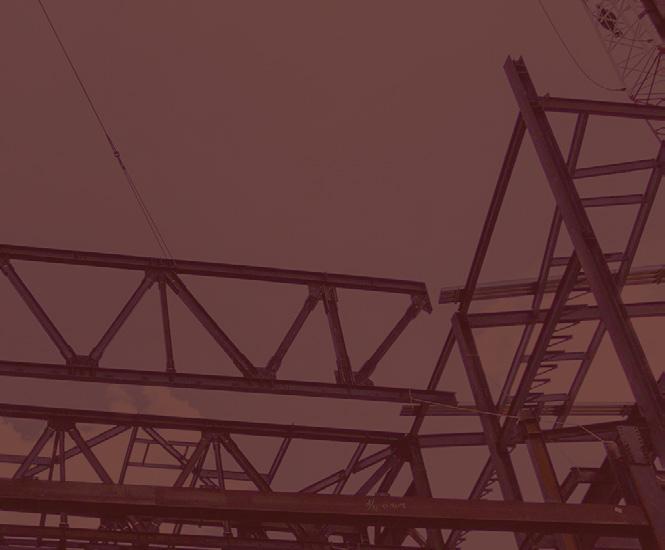
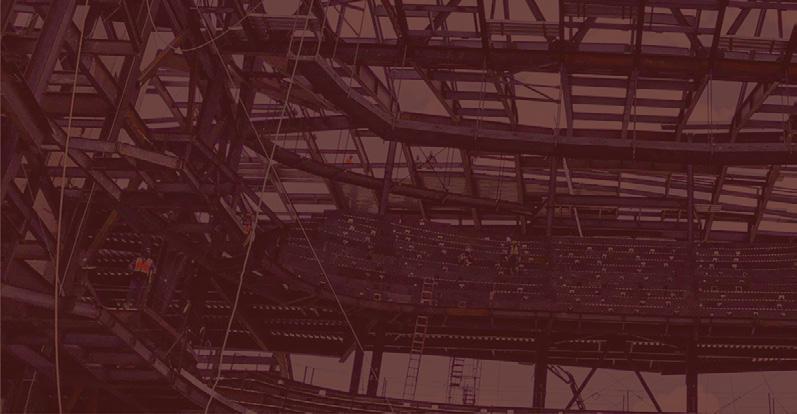
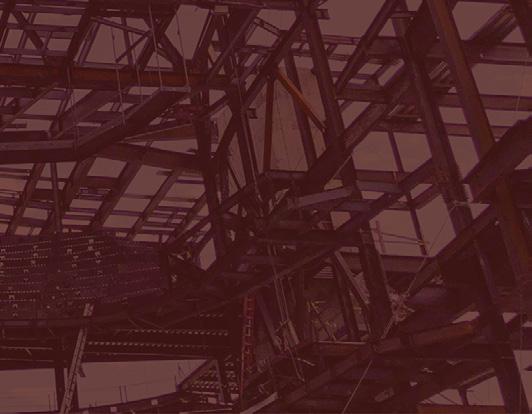
■ Pergola over Tulsa
A developer for a prominent downtown building in Tulsa, Okla., was looking for a structure to provide shade at a newly renovated café area on the second floor terrace. Seeking an elegant, eye-catching design, the 100-foot long pergola consists of five arches. The AESS Category 1 structure is made of white galvanized rolled 10-inch WF for the columns and arches, with 3-inch pipe infill and 10-inch HSS connecting the columns and bearing the center arches. Each arch is just over 18 feet tall and 20 feet wide.
The AESS finish of the design was inherently one of the three primary challenges Basden Steel Corp. had to overcome. This project received a white paint over galvanized base and required multiple full pen welds.
The other challenges were the timing and the location. The project came to Basden at the beginning of winter, and the entire project was designed, fabricated, and erected in less than four months. Limited available space for crane setup in the urban downtown meant that multiple lanes on a major street had to be closed.
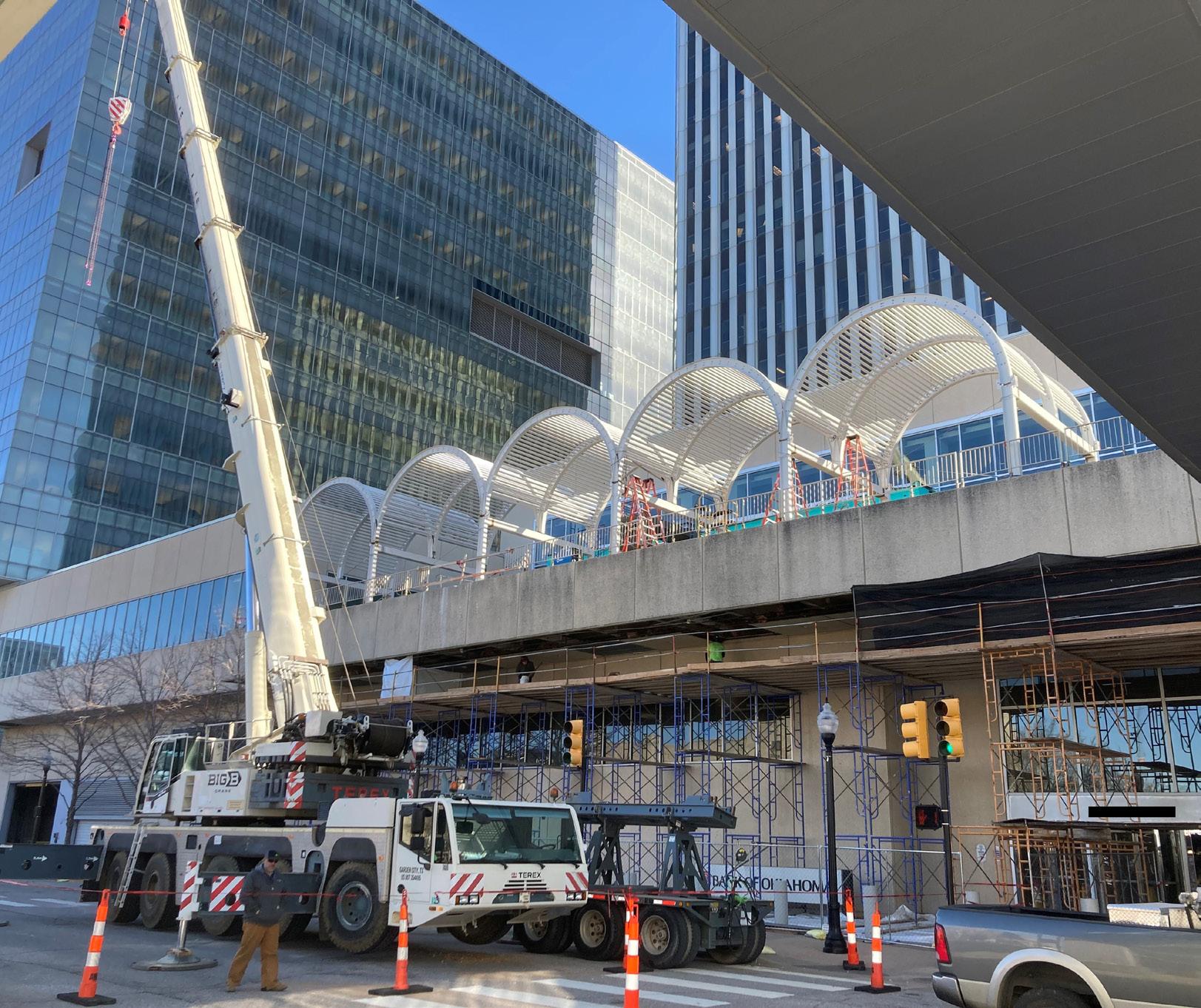
Alterations & Sequencing
To deliver the design team’s vision, Basden Steel first altered weld locations from the middle of the 10-inch WF rolled beams to actual connection points, to allow for better fit up and to allow for more tolerance in the connections with the roll of the radius.

The arches needed to be assembled individually at street level and then lifted as fabricated domes. “Trying to adjust the radii in the air would have proven very difficult. With the AESS requirements, we had to limit our use of erection aids and splice plates for temporary stability,” said Austin Jones, Contract Administrator and Field Operations Manager.
Developing an erection sequence that provided for all the design intendents was critical to the success of the project. The engineered erection plan was prepared by the late Rodney Baxter. He also determined that the four-prong rigging system was the solution to perfectly level picks of the arches. On site, minor adjustments were made using chain falls. “He was invaluable to ensuring all parts of the project were planned. He is highly missed,” said Jones.