
7 minute read
Quality is a Team Sport- Training tips to make your life easier by by Todd Alwood, AISC
Quality is a Team Sport
Training tips to make your life easier
Quality Management impacts every area of a business. Emphasize how understanding the role of quality in each specific departments empowers employees to contribute to its effectiveness and integration.
If there’s one thing we know about training, it’s that actually doing something is more effective than talking about it. We can talk about how helping your staff develop their skills–investing in their success as an individual–cuts down on attrition. We can talk about how important it is that everyone on a team knows what their quality management system does and how it works.
But doing is more effective than talking–and people who do it know more than people who talk about it. The seven people you’ll meet here do steel construction quality training on a regular basis. Every shop or jobsite is different, but these lessons have broad applicability. Read on for their tips, tricks, and lessons learned.
Develop a sense of ownership
Nate Lindell with Project + Quality Solutions
When training employees on the Quality Management System (QMS) in a steel fabrication setting, focus on its tangible benefits and real-world applications. Instead of simply explaining requirements and processes, illustrate how the QMS enhances steel product quality, reduces errors, and boosts customer satisfaction. Demonstrate that the QMS is more than rules; it’s a valuable tool supporting their work and the company’s success.
Engage employees by involving them in the training. Ask for their input on QMS improvements and implementations specific to their roles. This fosters ownership and accountability, making training more relevant. When employees sense their stake in the system, they’re more likely to invest in its success and adhere to its requirements.
Highlight that the QMS spans all business areas. Emphasize how understanding its role in their specific departments empowers employees to contribute to its effectiveness and integration. This not only enhances individual contributions but also reinforces its overall impact on the company’s success.
Train for understanding, not just compliance
Tom Anderson with Atema Employees do as they are told to be compliant, but they might not understand the reasons why a requirement is necessary or must be followed. This might lead to disengaged employees who don’t take ownership of their work. When we teach why a process is needed, what issues are prevented, and how it makes the employees work better, they are more likely to be engaged and take ownership of their work.
As an example, welders use rod ovens at a jobsite. Welders know they should take what they need from the rod oven and promptly return the unused rods. But do they know why? Do they understand how weld quality is affected by hydrogen?
Suppose management takes the time to teach why rods must be stored in a heated oven and how weld quality can be adversely affected by hydrogen in welds. In that case, this training goes beyond bare minimum compliance and will help educate employees who understand why their actions and their work matter.
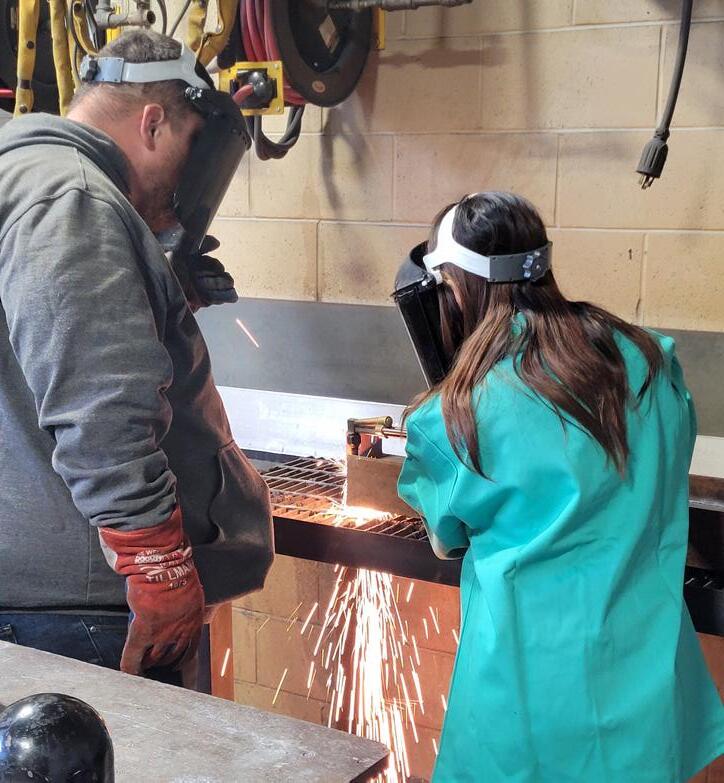
Listen to your employees and your data
Joshua Mizzell nand Nick Accordino with Cooper Steel
Training is one of the most important parts of business, but only when the training is administered in such a way the trainee perceives it as an essential tool in their everyday work. How do we accomplish this? By supplying training that not only yields accountability but ensures the trainees’ engagement and understanding of every aspect of the tool they are given. Having the buy-in of the individuals being trained is bar none the most important part of a company’s assets, but they must first understand the plan and the purpose of the topic at hand.
In order to provide pertinent training, we collect data throughout the different layers of the company. Logging non-conformances, quality discrepancies, trending issues, and also conforming products. Each item is broken down into various categories, helping
show trending patterns and providing us with topics for training. These topics are then incorporated into our Learning Management System, a system that requires the interaction of each employee by reading a segment of information and taking a quiz. These are accompanied by hands-on discussions, which help ensure the employee is engaged and fully understands the root cause and potential repercussions of said topics. This is done monthly, quarterly, and whenever we feel an important topic needs to be discussed.
We believe it is critical to ensure that all employees are in a safe and comfortable environment with the understanding that all questions are encouraged. Our goal is to have each employee interact not only with us as managers but also with each other. They are an asset to the quality department just as the quality department is an asset to them.
Make training part of the daily routine
Drew Heron with Deem Structural Steel
One of the ways we have found success in implementing our quality management system and getting buy-in from our field employees is to have a “Quality Minute” every morning. We do this when we are having our daily safety meetings and field personnel are filling out the daily job hazard analysis. This is always a great time to get everyone focused on the task at hand and put quality and safety in the forefront. Quality and safety go hand in hand. We discuss any current quality issues we are having on the project or any potential quality problems we may encounter during the scope of our daily work. In addition to project-specific quality items, we discuss topics that have
been identified company-wide. Doing these daily keeps things simple and easier to digest for our team members.
Embrace modern communication methods
Mark Yerke with S&R Enterprises, LLC
One of the biggest tips/tricks we have utilized at S&R is the use of Microsoft Teams to record quality management system training for the field. If we’ve learned one thing since early 2020, it’s that it is now easier to reach people by video recordings or conferences via phone and computer apps than ever before. So, whether it is a 30-second clip on a small change to RCSC or a 30-minute training video on proper use of the Skidmore, a video hits home and can be more engaging than paper. Gone are the days of just handing out a 100-page manual update for field craft workers to read–now is the time to break that down into manageable modern bites!
Inspect your inspectors and train your trainers
Dennis Haught with Quality Management Company
Too many times management mistakenly assumes that personnel conducting quality inspections are, in fact, conversant in performing required inspections. So to bolster one's training program and to ensure personnel are capable of performing inspections, management should verify the comprehension of personnel via testing and/or exercises. Additionally, management needs to make sure that those individuals who are responsible for training personnel are also well qualified in the subject matter that they are teaching. We can’t stress enough the importance of training the trainer! •
A certified advantage!
During an AISC Certification audit, the QMC auditor commonly uses opportunities for improvement (OFI) to suggest different ways a participant might add value to their quality system. So what is an OFI? It’s a suggestion or opinion based on the auditor’s experience that could add value to the QMS or the erector’s safety management systems. They don’t require action or a response, but they should be discussed during the participant’s management review meeting. It’s essentially free expert advice.
One common OFI that QMC auditors write is for participants to continually educate their QCIs using various sources. One major opportunity to do so is QualityCon at NASCC: The Steel Conference. The next one is in San Antonio,
Texas, March 20-22, 2024. QualityCon will feature more than 20 sessions focused on quality systems and how to help improve yours. In a particularly useful 2023 session (Contractor QC Training and Task Management Tips and Traps), Tim Duke of Williams Erection Company talked about how to motivate workers to buy into the QC process, streamline documentation, and assure that the process works as intended. (If you missed it, that’s ok! AISC has the recording available as a free download at learning.aisc.org, where you’ll find hundreds of other sessions on steel-related topics.)
Todd Alwood is Vice President of Membership & Certification for the American Institute of Steel Construction.