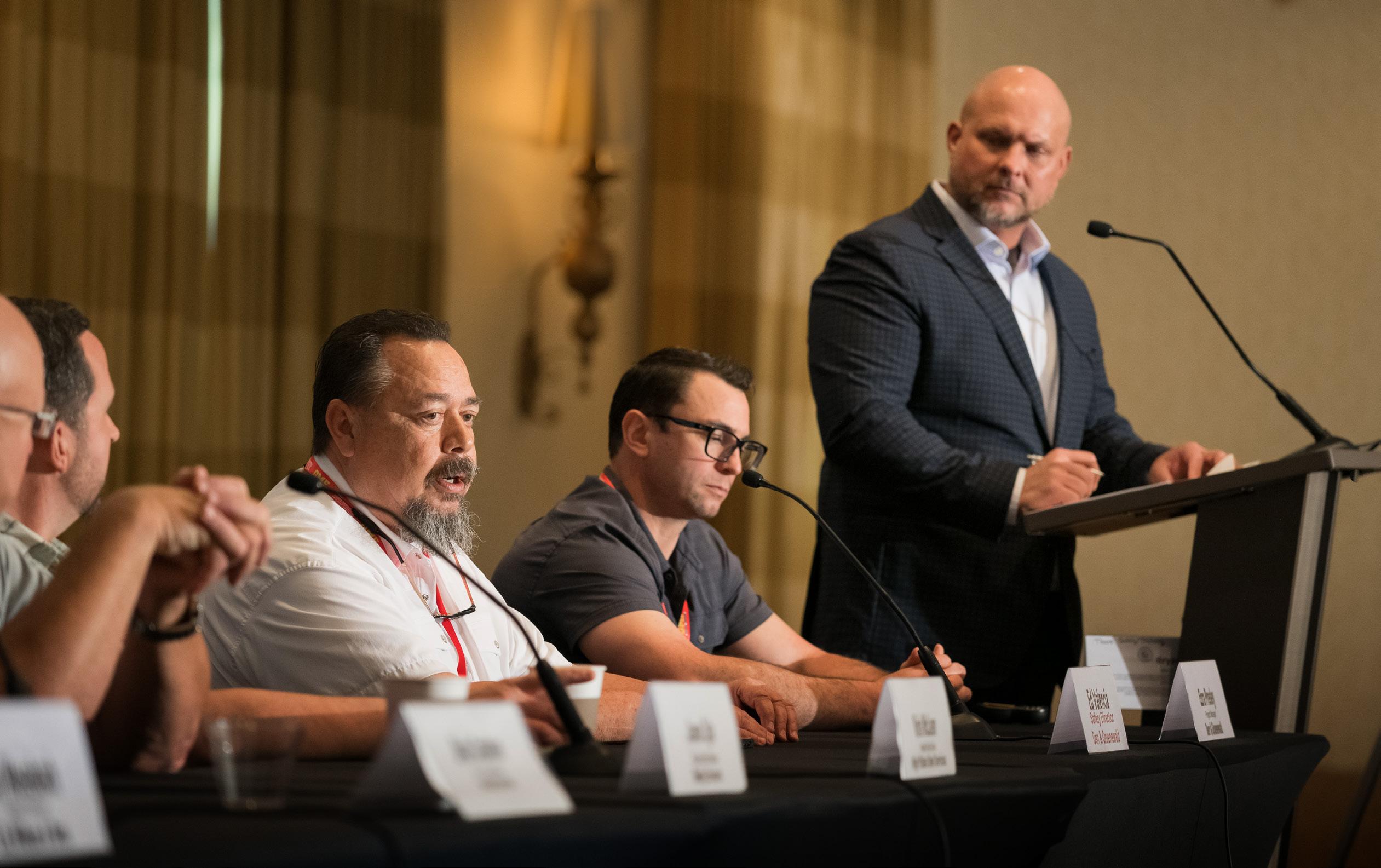
10 minute read
For More Than Safety's Sake
For More Than Safety's Sake
The role of training and safety excellence in recruiting, quality, and culture
By: Macie Murie
Worker safety is consistently one of the top priorities on any construction project, and with good reason. Since 2008, construction has experienced more total deaths than any other industry, and that figure doesn’t include fatalities from suicide. Our industry also has higher injury rates than most other professions, and unfortunately, safety costs.
The industry loses $5 billion annually due to construction-related deaths. The number is measured by lost productivity, loss of family income, and pain and suffering, according to the Midwest Economic Policy Institute.
However, today’s safety and training leaders recognize the impact of investing in creating a culture of safety. During a panel discussion at the 2023 Convention & Trade Show in St. Augustine, Florida, attendees were able to hear from the
2023 World Class Safety Excellence and Craft Training Excellence Winners.
The Safety Excellence Award went to seven SEAA member companies in three categories. Recipients were selected based on evaluations of their EMR ratings, OSHA 300 statistics, and safety program processes over the last three years.
Scoring was based on points assigned to a multi-criteria analysis, conducted in blind review by members of SEAA’s Safety & Education Committee. Applicants were evaluated on the portability of credentials, availability of apprenticeship programs, training, and recruitment efforts, in comparison to other companies of similar size.
“Good safety records, comprehensive training aligned with long-term career paths, and awards recognitions, are among the criteria that prospective employees consider when deciding where to apply. Beyond the inherent value of being a safe company, it’s also a great marketing tool in a highly competitive market,” said outgoing Safety & Education Committee Chairman Bryan McClure, during the panel. The following are excerpts from the panel discussion.
What are the negative impacts to a business when EMR rates are above the average?
Kulvinskas: Most quality projects require that you have an EMR rate below 1. Above average rates will negatively affect your business and the ability to win projects.
Valencia: If you have an above average EMR, you are paying higher insurance premiums. Some insurance companies won’t want to cover your company at all and owners and general contractors might not hire you because there is a higher risk for injuries on their projects.
Zyla: However, it can be a positive motivator within your company to help drive staff to work together to drop the number. Being a multi-year calculation, it’s a long-term effort to have it drop.
What is another way to take advantage of good EMR ratings and safety records?
Kulvinskas: We are very proud of our .61 EMR rating which we achieved in 2022 with over 400,000-man hours. During the hiring process, we let candidates know that safety is our focus, and they need to share our goal of everyone coming home safe after work.
In what ways does training for safety also contribute to training for and maintaining quality control?
Valenica : Safety and quality go hand in hand, by emphasizing safety during training employees develop a mindset of precision and thoroughness which naturally extends to maintaining quality control measures. With a positive safety and quality program you will without a doubt be productive.
Zyla : Training for safety not only helps protect employees and reduce workplace accidents but also contributes to maintaining quality control by promoting efficient processes, preventing errors, and fostering a culture of continuous improvement. It reinforces each other to create a safer and higher-quality working environment.
In what ways does your company develop team leaders?
Mosebach: We have found that workers who came up through the field have become the best leaders. When people show initiative and drive, we take that and help them build a career in the industry.
Cox: All of our foremen and team leaders are promoted from working in the field. We look for workers who are positive, detail oriented, and safety conscious. All of our leaders must embrace safety because it’s one of our main priorities.
What is something unique that your company does through the onboarding and career path development process?
McLean: We offer a tremendous amount of training for employees, and we have also implemented a certified ironworker apprenticeship program.
Mosebach: We focus a lot on developing our crane operators. They start as a laborer putting cranes together, then move into the truck driver role transporting the parts of the crane, then into the seat of a crane. At minimum, this is a two-year process. We want our workers to know the ins and outs of the cranes before they even think about moving into a more demanding role.
Presley: We prove to our new employee’s that safety is our priority by showing them the research and testing we have successfully completed on our training tower through videos and hands on training.
What is your company’s philosophy on continuous skills improvement?
Zyla: We do a Personal – Professional Improvement program that has a direct effect on profit sharing in Shelby Erectors. It carries a 30% weight against your total score of 100%. We want everyone at Shelby Erectors to not only grow professionally but also personally. We have an NCCER Apprenticeship Program that new and existing employees have to pass. Our safety training focuses a lot on new equipment and PPE that is coming out. On a personal level we leave it up to the individual to choose bettering themselves—from learning a different language, computer skills, or how to manage your finances.
McLean: We are currently revamping our entire training program to offer regimented, employment term-based training as well as providing opportunities for company sponsored advanced training for skills such as Ironworker Apprenticeship, Certified Welding Inspectors, and Certified Crane Operators.
What tools or technologies do you use in safety education and skills training?
Valencia: We use a safety audit tracking application called I-Auditor. It keeps track of repeated hazards on the project so we can focus on the trends we need to eliminate. We also use a detailed application that is like a virtual “Wallet Card” for tracking training. This allows us to look at the matrix to assure all employees are receiving the proper training for their task.
Kulvinskas: In addition to classroom training which is led by safety field reps, we use videos, online training courses, and have implemented a safety checklist in our Fieldwire application. We have found that this combination really works for us and our crew members.
Mosebach: Luckily, we went paperless in 2011. It has put learning in the hands of every crew member. This has made a world of difference for us as a company because it has allowed me to diversify their training and the presentation is available to everyone on the crew when its needed.
What are you doing to pass knowledge down as senior team members retire?
Mosebach: We pair some of the up-and-coming young employees with the more experienced guys to get some of the knowledge passed along. Most of the old school guys are not your typical teacher type, but we have been lucky that some of our younger workers are willing to sit back and watch the older guys work, and it appears they’ve been taking notes.
Valencia: We facilitate job shadowing where junior employees can observe and learn from retiring team members during their day-to-day tasks and expose employees to various roles to broaden their skill sets.
What safety or training issues keep you up at night?
Zyla: When we get a job where the bridge deck fall distance is between 6-ft. and 17.5ft. it’s a difficult distance for what we do. It’s not that easy to construct something when on a bridge deck with those distances, and we are not really fans of the retractable lifelines at those heights. We take the worstcase scenario of the retractable being fully out, and at this point you need maximum fall distance. It’s a constant challenge with primary contractors when we come across this issue.
McLean: Engagement. We have a society of people who are checked out and unaware of what is happening around them and it can be dangerous. Situational awareness is a key to being safe and keeping your teams safe on the jobsites.
Mosebach: Fall protection. It will be a never-ending battle. There will always be someone who thinks they are invincible and unhook for some reason.
Valencia: We all like to think that we are doing enough training but beyond the frequency of the training, it is just as important—if not more important—to know that the employees completely understand all of it and can easily apply it to the field. •
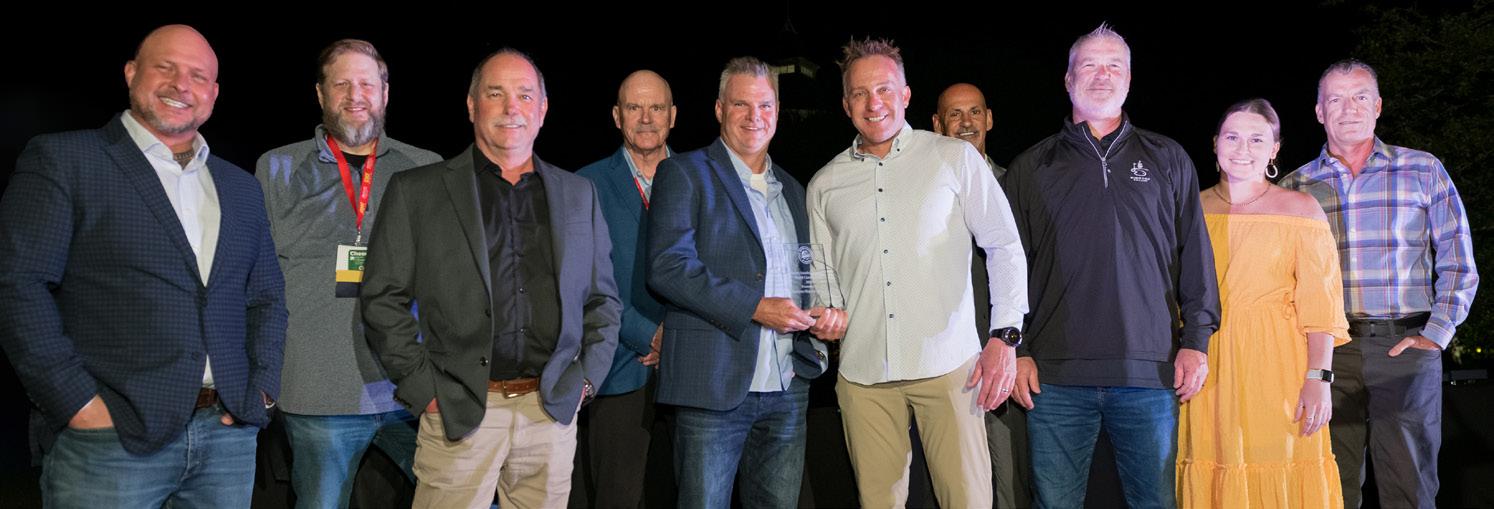
Gardner-Watson Decking’s President Geoff Kress and Vice President Jason Kulvinskas (center) surrounded by the rest of their team receive the World Class recognition for the Safety Excellence Award.

“We focus a lot on developing our crane operators. At minimum, this is a two-year process.” Jonathan Mosebach, Safety Director, L.R. Willson & Sons
Safety & Training Panelists
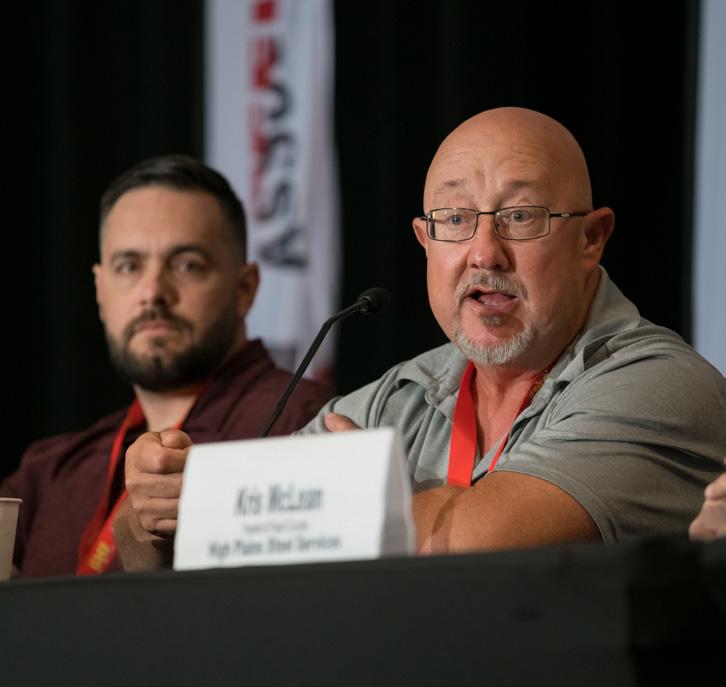
“We want everyone at Shelby to not only grow professionally but also personally.” Jason Zyla, Safety Manager, Shelby Erectors
Derr & Gruenewald Construction, LLC
Ed Valencia, Corporate Safety Director
Ezra Presley, Project Manager
Derr & Gruenewald Construction is a full-service steel fabrication, steel erection, detailing, metal decking and precast concrete contractor. Based in Colorado, the company performs work throughout the United States. In 2023, Derr & Gruenewald Construction received World Class recognition for both its Craft Training and Safety programs. As a Category 1 employer, they employ more than 121 ironworkers annually.
Gardner-Watson Decking
Jason Kulvinskas, Vice President
Mark Cox, Project Manager
Gardner-Watson Decking began in 2005 as a one crew operation in Florida with one truck and one client. The full-service metal decking installation company now employs 190 plus and operates more than 20 crews nationwide. Floor and roof deck projects include distribution facilities, data centers, hospitals, arenas, cold storage, warehouses, and other jobs. In 2023, Gardner-Watson Decking received World Class recognition for the Safety Excellence Award.
High Plains Steel Services
Kris McLean, President & Project Executive
High Plains Steel Services, LLC is a premier structural steel fabricator and steel erector located in Northern Colorado. Established in 2012, High Plains Steel Services is driven by its core values and leverages their strong and experienced team with leading edge technology and company owned facilities and equipment to provide turn-key steel construction solutions. In 2023, High Plains Steel Services received a World Class Safety Excellence Award.
L.R. Willson & Sons
Jonathan Mosebach, Safety Director
L.R. Willson & Sons, Inc. was founded in 1951 and started as a one man show. From its humble beginnings, L.R. Willson & Sons now employes more than 250 people and has become a leading structural steel, precast, and tilt up erector, and crane rental company serving the Baltimore/Washington Metropolitan construction markets. In 2023, L&R Wilson & Sons received premier level recognition for the Safety & Excellence Award.
Shelby Erectors
Jason Zyla, Safety Manager
Founded in 1997, Shelby Erectors is a labor subcontractor that specializes in bridge construction—the installation of reinforcing steel and Stay-in-Place metal decking. The family-owned business is led by Jennifer Nix, owner and President, and employs workers on job sites across Florida. In 2023, Shelby Erectors received a World Class Craft Training Award (Category 2; 61-120 Ironworkers employed annually), and a Gold Safety Excellence Award.
Additional Safety Excellence Winners
Empire Steel Erectors, Premier Level Black Cat, LLC, Gold
Macie Murie is Assistant Editor of Connector and Associate Client Manager for Mighty Mo Media Partners.