
13 minute read
In the Field
At the Texas Children’s Hospital in Houston, Texas, a Maeda minicrane is used to hoist steel beams onto the roof of the building. If a steel erection crew chooses to hoist a mini-crane to the roof of a building to work at height, the surface must be solid, and the crane must be set up within 1% of level. Photo provided by Maeda USA.
Steel Work offers Major Role for Mini-Cranes Equipment selection should include job parameters, setup, and certification requirements
If you’re considering a mini-crane for your next steel erection project, know your jobsite and how you’ll be using the crane before you call your crane provider. Determine ground bearing pressures for the crane setup location, and know the weight of the loads you’ll be handling. Figure out whether the crane will be hoisted to height, and whether it’ll be traveling through any doorways on the way up. These factors will determine the size and capacity of the crane you choose.
Dan Swiggum, business development manager at ATS Specialized Training in Sun Prairie, Wis., says “because they don’t run
Lucy Perry operates WordSkills Editorial Services in Kansas City, Mo. She has spent 25 years following the North American construction industry. She can be reached at wordskillseditor@gmail.com. cranes on a regular basis, ironworkers need a very operator-friendly crane. That’s the minicrane.” He says his steel erection customers like mini-cranes especially for sports stadium construction sites, “where they can hoist the machines to the upper deck of a structure to work from height.”
Customers choose a mini-crane for applications where a big crane would be impractical, so the first step is to assess jobsite access, says John Carpenter, sales manager for Maeda USA, Houston, Texas. “The process begins when they decide why they need a mini-crane. If they can do the job with equipment they’ve already got, of course there’s no need for a mini-crane, but nine times out of ten they actually need a smaller crane because of access issues, or work space constraints and obstructions.” He has a list of standard questions he asks customers:
• How is the mini-crane getting to the workspace? Will it be hoisted with another crane? Will it travel through single or double doors?
• Are there stairs, curbs, or other obstructions to navigate?
• Will the work take place inside a building or confined area?
• Will it matter if the machine produces emissions?
• Is propane or electric model required?
“Once we help the customer determine the appropriate model, power package, and accessories, we then discuss details such as ground bearing pressure on tracks and outrigger reaction forces (commonly referred to as point loads).”
“That’s data that the structural engineers require when a crane is working on a rooftop, parking garage, or elevated deck,” he says. “We run the data for the customer’s specific defined lifts using a Maeda factory program, once they provide us with the load weight and crane configuration.” Crane mats under the mini crane’s outrigger pads are required. Sometimes shoring is required to support the work area for the crane. Some mats are for surface protection, others are for outrigger force dispersal of the crane and load, Carpenter explains.
“It all depends on ground and work surface conditions. It’s the contractor’s responsibility to use proper mats, shoring, or other load dispersal methods for the particular jobsite. In the steel erection business, if they’re considering a difficult-to-access job or a tight workspace, we’ll discuss the project in detail with them, and help them determine which model of mini-crane they’ll need, depending on their load weights and lift heights.”
In choosing the right crane for the job, there are myriad crane sizes, depending on the application. Jennifer Denman, of Phoenix, Ariz.-based Smiley Lifting Solutions, which is the North American dealer for Japanese Spydercrane mini-cranes, says that sometimes a non-traditional approach is the right answer. A top-down pick from another story of the building will reduce the machine size and ease installation. Mini-cranes are relatively light cranes that are able to work on elevated surfaces.
In this application, “Customers will look for something that can pick more and will have longer cables,” explains Joe Wheatley, Western district sales manager for Baltimore, Md.-based JekkoUSA, exclusive U.S. distributor of Jekko mini-cranes. A larger winch on a mini-crane will offer more cable to work with, he explains. That has been very popular with Wheatley’s steel erection customers. Another consideration is line pull. “Steel erectors want the capacity at single-part line so they have faster winching to get the job done faster,” he says. to the roof of a building, but the setup is the same as if he were working on the ground below. The surface needs to be firm, and the crane must be set up within 1% of level.”
Bryan McClure owner of Trivent Safety Consultants, Denver, Colo., echoes the importance of proper setup. “You need to determine ground-bearing pressures for the crane’s outriggers and the crawler. That’s the biggest issue,” he believes. McClure suggests steel erectors make sure they’re setting the crane
Set up for success
Swiggum cautions that people sometimes take mini-cranes for granted because of their size. “Whether it’s a mini-crane or a 2,000-ton crawler crane, it’s all about the ground conditions of the surface you’re setting the crane on. An ironworker may take a mini-crane up on a smooth finished concrete if possible, or utilize some kind of wood cribbing underneath the outrigger pads. “This prevents the crane from moving around while you’re operating it,” he says. “It’s best to put wood blocking under the crane, even just a thin layer.”
Mike Faloney, southeast district sales manager for JekkoUSA, says the customer also needs to know the working radius, capacity, and height of the load. “Those three things


A steel erector in the San Francisco Bay Area used two Spydercranes provided by Smiley Lifting Solutions to erect a mezzanine in an indoor hotel courtyard. Photo provided by Smiley Lifting Solutions.

Blakley Construction Services in Nashville, Tenn., regularly uses Jekko mini-cranes to replace steel components in limited working areas inside sewer or water treatment facilities. In this photo, Blakley technicians use a Jekko SPX429 to place an effluent support in a Metro Nashville wastewater processing plant. Photo provided by JekkoUSA
determine the crane for the job. He also asks customers what size area they have to work in. “They also want to look at the footprint of the area. Some machines can be folded up to take up a smaller footprint,” explains Faloney. “It’s usually a 14’x14’ square, but that can be knocked down to 14’x7’ if the crane is half-jacked,” referring to configurations in which the crane’s outrigger is not fully extended. For most mini-cranes this is completely acceptable, provided the operator is closely abiding by the crane’s load charts for safe load lifing.
Denman explains that mini-cranes have very flexible outrigger positioning, which enable operators to set up around a column or in a tight space. When doing so, it is important to carefully follow the load chart according to the outrigger positions.
Swiggum adds: “There are 57 different positions some of these cranes can be configured in, and that has to match up with the quadrant you’re going to work in. It’s all laid out in the crane manual,” he explains. “You also need to know the correct outrigger position.” Make sure, as well, that you know where you’re setting the outriggers so that you’re not crushing an extension cord or any electrical equipment that energizes the crane, he says. Because of their flexibility for positioning, Denman reminds operators to utilize the remote control. She says, “Wireless remote controls can allow the operator to get in the best position available to execute their lift. Don't work in the blind!”
In addition, Swiggum cautions operators to check for nearby structures and overhead powerlines to avoid booming into them. “I remind customers that it’s a small crane, but if you yank on the lever it will swing fast. I tell guys it’s no different approach than if they were operating a big lattice-boom crane—Slow and steady wins the race.”
Certification standards
If a crane can lift more than 2,000 lbs., and the work you’ll be performing is categorized as ‘construction’, you must have certified crane operators to run a mini-crane. The operator must be evaluated by his or her employer or a third-party testing organization to be qualified to operate the crane, per OSHA’s Cranes & Derricks in Construction rule.
“If an ironworker holds up the beam that’s lifted with that crane, that crane operator has to be certified,” says Swiggum. “Mini-cranes are considered a small hydraulic fixed-cab crane. There’s a core exam about general operational questions, but then they take a specialty exam for fixed-cab crane that’s 26 questions, and takes an hour to complete.” His organization, ATS, uses the National Commission for the Certification of Crane Operators (NCCCO) to certify crane operators.
Graham Brent, CEO of the NCCCO Foundation, says since there are currently no accredited crane operator certification programs developed specifically for mini-cranes, the NCCCO Foundation’s Crane Type Advisory Group (CTAG) reviewed the models available and determined that the telescopic-boom crane (non-rotating controls) type is the “most similar” available for compliance with Subpart CC of the OSHA Cranes & Derricks rule. “For NCCCO that would be the Telescopic Boom—Fixed Cab (or TSS) certification,” explains Brent.
NCCER also tests mini-crane operators under the telescopic boom/crawler-mount crane category for NCCER operator
certification purposes. Depending on the type of mini-crane, one can be used on NCCER telescopic boom/crawler mount practical exams as well. “However, it is critical that the operator is able to do all of the tasks on the practical exam for the associated crane, such as check engine fluids and travel the crane,” explains Chris Wilson, senior projects manager at Alachua, Florida-based NCCER.
If the steel erector is renting the mini-crane with an operator, he needs to know the operator is a certified crane operator, notes Carpenter of Maeda USA. “Most steel erectors are pretty crane-savvy because they’re around cranes and lifting equipment all the time; however, mini-cranes should be treated just like larger cranes when it comes to safety and proper operation. A smaller contractor may not have a certified crane operator, so the crane company may offer turnkey hoisting service with a qualified crane operator.”
The steel industry is a big customer base for mini-cranes, he continues. Some customers will plan ahead and know that it’s the right machine for their application, but a certain percentage of calls come from people who’ve only determined the crane they have already is too big for the jobsite. “It’s often more cost-effective to mobilize a mini-crane if they don’t have to use a big crane,” he points out. “We’re finding they’ve become more mainstream as the steel industry gets more familiar with them. We’re helping steel erectors do their jobs safer, and more efficiently, often saving time and money without having to mobilize in a big expensive crane. Mini-cranes are problem-solvers for unique and difficult lifting applications.”
Since there are currently no accredited crane operator certification programs specifically for mini-cranes, both NCCCO and NCCER have determined that the telescopic-boom crane (non-rotating controls) type is the “most similar” available for certification compliance with Subpart CC of the OSHA Cranes & Derricks rule. Photo provided by NCCCO Foundation.
WIRE ROPE AND PERIMETER CABLE


RIGGING HARDWARE

SLINGS

FALL PROTECTION

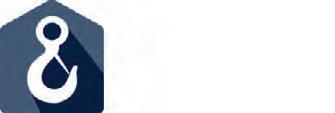
PROUD MEMBER
(877) 331-3280
RIGGINGWAREHOUSE.COM
Steel Masters LP, Houston, chose two Maeda MC305 mini-cranes over larger, more conventional options to complete its part of a project to renovate Texas Medical Center in downtown Houston.
The job called for steel beam erection and lifting columns and trusses on the multi-floor addition to be built above the existing parking garage of the towers. Seeking alternatives to the high cost and traffic disruption that accompany tower cranes, Steel Masters sought out Inman Texas Company, the Texas dealer of Maeda mini-cranes.
“The Maeda MC305 provided the answer for us,” said Mark Melton, equipment manager of Steel Masters. “It was light enough to place directly on the parking garage deck but could achieve our lifting requirements of up to 6,500 pounds. Compared to the alternative, which was bringing in a tower crane, they proved to be much less expensive as well.”
Steel Masters leased two MC305s from Inman Texas and lifted both to the parking garage deck with a large mobile crane, which was then removed from the job site — quickly and easily with no traffic disruption whatsoever.

Key features of the MC305 are 47 ft. lift height; 6,560 lb. capacity; 360 degree swing; and 51 in. width to fit through standard double doors.
MAGNETIC DRILLS ANNULAR CUTTERS From maintenance to repair to fabrication, Hougen has the tools and equipment for work on-site or in the shop. Whether it’s small lightweight low profile mag drills to large multi-speed models to a wide range of annular cutters for sheet metal or plate materials, Hougen provides the power, performance & solutions for your holemaking needs.




The MC305’s ability to maneuver in a confined workspace also was an important consideration, as was fuel economy, according to Melton.
“Maeda’s mini-crane is powered by a very efficient Yanmar diesel engine, so the fuel savings was great,” he said. “We could work all day on a tank of diesel.” The minimal overall weight of the MC305 also allowed Steel Master to move safely and efficiently across the top of the garage as work progressed, and the zero turning radius of the mini-crane proved adept working in the tight working conditions, according to Melton.
The crane has multiple outrigger length settings that can be easily extended or retracted. The load charts are programmed into the OEM Load Moment System which is integrated with the outrigger interlock safety system and sensors.The remote control with digital display and load weight readout is standard on all MC models.
“Maeda mini cranes are equipped with all of the safety systems that larger mobile cranes are equipped with, just in a scaled down, small package,” said John Carpenter, Inman Texas sales manager. •
APRIL 14 - 17*, 2020 Sheraton Grand Chicago


Owners will witness first-hand the incredible developments in SAFETY and technology. Contractors and ironworkers understand that the conference is attended by the best minds in the construction industry and geared toward their success and continued growth. 10,515 CONSTRUCTION PROFESSIONALS HAVE TAKEN ADVANTAGE OF THIS PREMIERE CONSTRUCTION EVENT. SHOULDN’T YOU?
MORE ATTENDEES THAN EVER ARE EXPECTED. THESE ARE A FEW REASONS WHY: • Discover how TECHNOLOGY is advancing our workforce • Find out how IMPACT is helping break through to owners in new regions • See what the FUTURE of construction technology looks like
HERE IS A SAMPLE OF THE BREAKOUTS CREATED FOR YOUR SUCCESS: • Tech Comes to Rebar • Business Managers and Politics in an Election Year • Communicate Clearly: Crisis Communication • Why Does Diversity Pay? • Metal Buildings of the Future! • Safety Pre-Qualifications for Industrial Opportunities • The BlueBeam Revolution • How Do I Know My Tech Vendor is Good?
DON’T MISS THE INDUSTRY’S PREMIER CONSTRUCTION CONFERENCE!
To register visit the Events Tab on the IMPACT website (WWW.IMPACT-NET.ORG) Or scan the QR code.

*ATTENTION CONTRACTORS! DON’T MISS THE NEWLY-ADDED CONTRACTOR ONLY DAY!
