
6 minute read
Management
Building Blocks of Calibration Systems Key terms used in calibration
When it comes to measurements, calibration is how we know we are doing what we say we are doing. Calibration is an important quality control measure considered as part of the AISC certification process. AISC offers various certifications steel fabricators and erectors.
When developing an effective calibration program, it is important to understand the terms, review examples of best practices, and determine the frequency needed for calibration.
In the 1890s, a Swedish arsenal worker named Carl Edward Johansson discovered a system to make accurate measurements. The Jo Block was born! Made from a block of steel at a constant temperature of 68° Fahrenheit gave it accuracy within two-millionths of an inch, making it possible for the interchangeability of parts, which one could call the building blocks of mass production. A complete set of block gauges would have numbered over 100,000 blocks. Johansson discovered that all measurements were possible with a combination of 81 blocks with a range from one-tenth of an inch to four inches. In 1923, Johansson moved to the U.S. and met Henry Ford. The meeting resulted
Lee Pielaet is the President of Pioneer Steel Services, Inc., Missoula, Mont., which helps companies achieve, manage, and upgrade their AISC Certifications. He is an ASQ-Certified Quality Auditor, AWS Certified Welding Educator, and AWS Certified Welding Inspector. Contact him at lpielaet@ pioneersteelservices.com. in Johansson helping standardize the Ford Motor Co.
Today we don’t need Carl Edward Johansson to help us with our calibration needs, but you will want to look for an outside calibration laboratory to help develop your program. It is important that the calibration lab you select is certified to International Organization for Standardization (ISO) and by the International Electrotechnical Commission (IEC), 17025, the leading standard used by testing and calibration laboratories. The calibration labs must meet the general requirements for the competence to carry out tests and calibrations, including sampling. The certification also covers testing and calibration performed using standard methods, non-standard methods, and laboratory-developed methods.
Critical terminology
Before we discuss calibration best practices, the following terms should be made clear: Calibration/Verification, Traceability, Accuracy, Tolerances, and Welding Validation. Calibration and Verification—These terms can mean the same thing. Most believe that calibration includes the determination of measurement uncertainty (MU). MU is a must for the chain of traceability to national or international standards. If the MU is not known, it is thought by many to be only verification. The bottom line is that it is up to a company to determine the terminology which works best for them.
Traceability is the ability to relate individual measurement results through an unbroken chain of calibration to a national standard, such as the National Institute of Standards and Technology (NIST) or National Bureau of Standards (NBS). Accuracy is the extent to which the measured value of a quantity. Does the measurement agree with the accepted value of a standard, including the MU? Tolerances are the permitted amount of deviation from the exact value specified and dictated by the manufacturer, standard, code, and specifications for calibrated items. Welding Validation—calibration and verification of welding machines can be confusing and has led many to use the new term “Welding Validation.” This term is not yet standardized, and currently, the American Welding Society provides no definition that is universally accepted.
Examples for erectors, fabricators These terms will help clarify the following best practices, and the principles applied to these examples will be the same through your specific calibration system. Steel Measuring Tapes: The following passage from NIST describes how they calibrate steel measuring tapes. “Calibration of metal tapes is made with the tape under tension and supported on a horizontal flat
Twenty One Years in Business
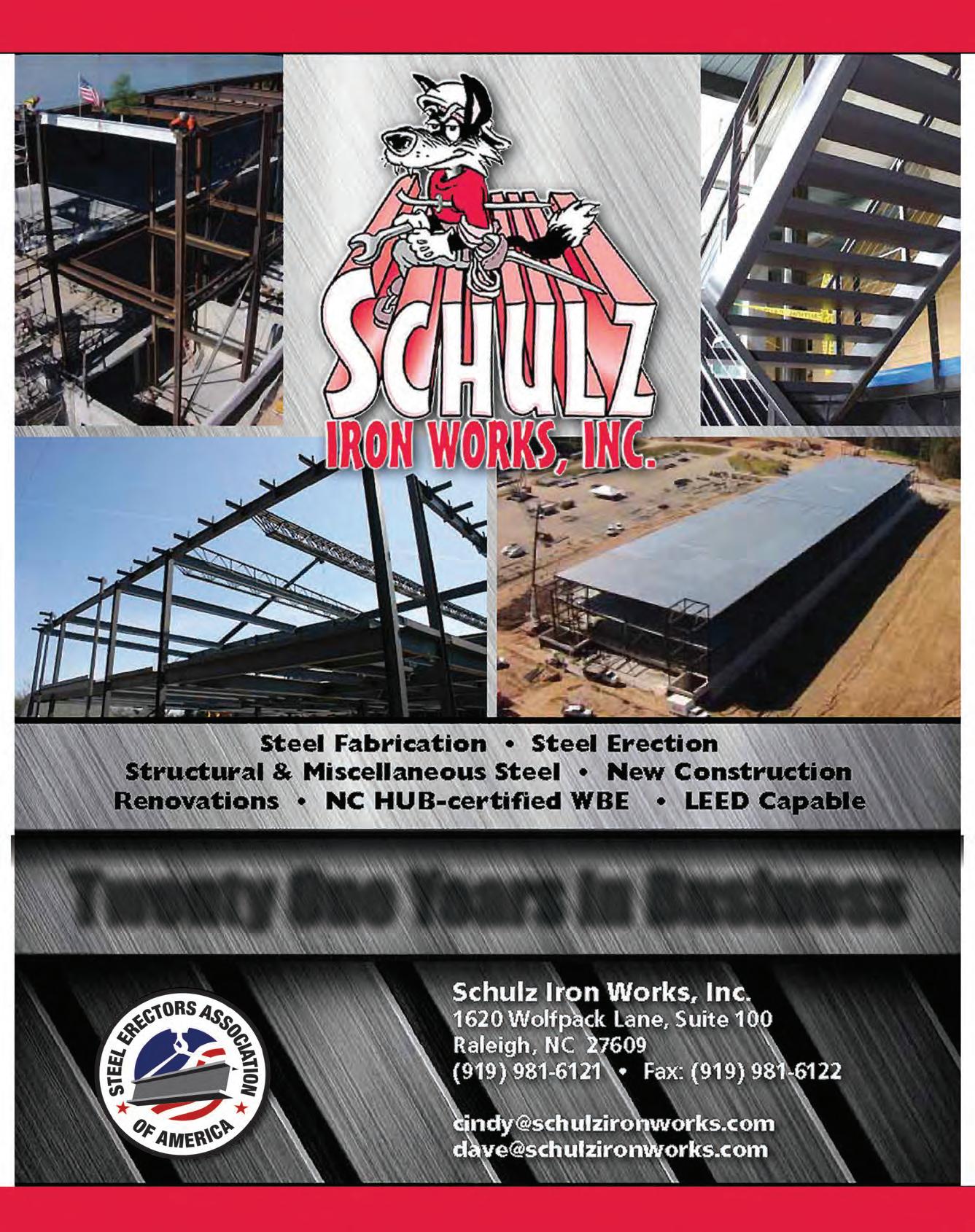

surface. Tapes less than or equal to 60 m in length typically include seven measurement points. The location of these measurement points must be specified and included in a calibration purchase order. The default tape calibration includes seven equally spaced points, which includes a measurement of the full length of the tape."
Many companies use this default to verify the steel measuring tapes used by the quality control process against their calibrated tape — the methods daisy-chaining this verification to national or international standard. Amperage/Voltage Meters: Typically used through a maintenance program, as well as in its calibration program, many meters are bench-tested before they are sent out by the manufacturer. This test may not be a calibration, but verification traceable to a national standard. The fact that an item is new does not make it calibrated. Think of the tool quality found in your local discount tool store verses a trusted tool supplier. There are governing bodies that accept new amperage/voltage meters as calibrated for the first year, and then require them to be calibrated annually. The fabricator/erector should be cautioned to check the codes, specifications, and contract documents before determining their minimum requirements. Welding Validation is one of the Calibrations or Verifications that takes place at the Fabricator/Erector level. Welding machines must be calibrated for Amperage/Voltage Meters. This verification is done at least annually by most fabricators, and quarterly or more frequently, if required. Welding machine manufacturers usually state the end-user cannot adjust welding machines. Calibration/ Verification or Welding Validation confirms the needs of a customer or that weld procedure specification, product, service, or system have been met. The methods of obtaining validation are many. Variables could include machine type, process type, project requirements, codes, and specifications.
In AISC 207 Chapter1.14 of the AISC Certification Standard may not be clear as it pertains to welding machines. What is clear is that it is required, so don't be surprised if you must present your welding machine calibration record at your next audit. Use a calibrated handheld amp/ voltmeter to verify the welding operator is following the WPS. Also, confirm that the machine being used meets the requirements of the code and contract document. If documented, you can check that you are meeting the needs of the systems listed above. Some codes require a frequency of calibrating the test gauge and the frequency of verification. Bolt Tension Indicator (Skidmore) requires annual calibration (see RCSC Specification). A calibration history must be kept for AISC Erector Certification.
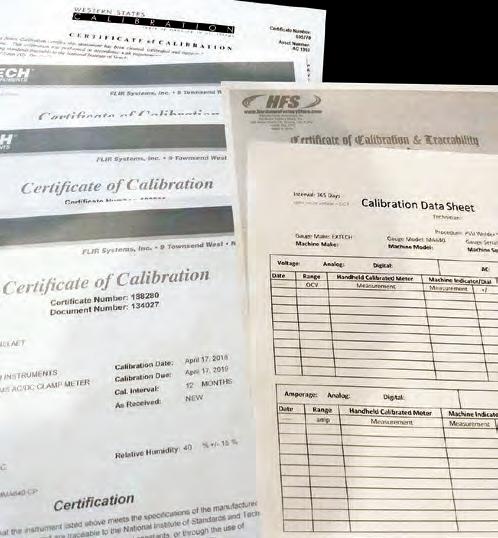

Determining the frequency
How do you decide the frequency of calibrations, verifications, or welder validations? When not covered by code, specification, or contract documents, the following considerations can help determine what best fits your business. After you purchase a calibrated item or you send a gauge to be calibrated by an outside calibration laboratory (again, many hold the ISO 17025 certification), you will receive a record of this calibration. This is a good time to review the calibration policies within your own company.
A number of resources and online forums can provide direction, just use caution when applying knowledge from an unidentified or unknown source. One good resource is the National Institute of Standards and Technologies
The shorter the intervals between calibrations, the more you may reduce the risk of inaccurate measurements. When determining the frequency of calibration, verification, or welding validation, consider factors that may affect measurement accuracy. Requirements of your quality program should consider how often the item is in use, environmental conditions, including humidity, temperature, vibration, and where the item is stored and used.
Frequencies can be set using various options: CAU (Calibrate after use), CBU (Calibrate before use), Number of Users, Hours, Days, Weeks, Months, and Years. •
