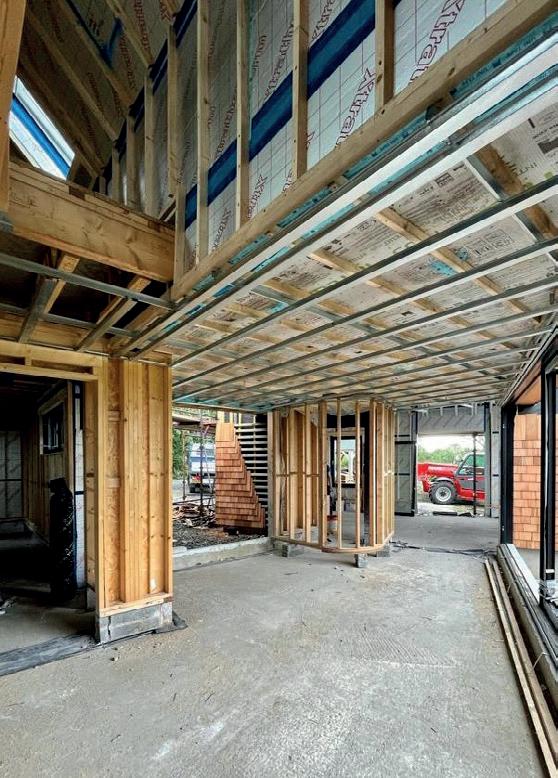
1 minute read
Designing your panels
When designing the timber frame structure, it is really useful to consider which dimensions to use for the structural grid or layout in order to minimise cutting processes and waste. Since most board products such as sheathing, lining and flooring are supplied in sheets 2400mm long and 1200mm or 600mm wide, the most obvious structural grid dimensions are 400mm or 600mm.
Next, consider the type of structure. The most common method of designing and constructing a domestic timber frame building which you should encounter is the platform frame system, in which each storey is erected so that the previous floor becomes the platform for the next. The ground floor is usually of solid concrete, upon which the ground floor storey is constructed.
An open panel platform system describes a sheathed timber frame of studs, plates and lintels; covered with a breather membrane and complete with openings for windows and doors. Internal linings, insulation, vapour control layer (VCL), services and claddings are all added on site. A closed panel system is a development of the open panel, in that the wall panels are delivered complete with insulation, VCL and internal linings. The windows and doors can be prefitted and service ducts, cables and pipes can also be included.
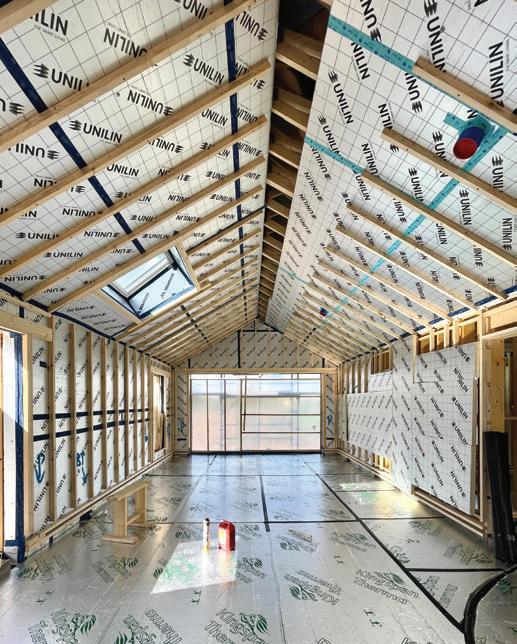
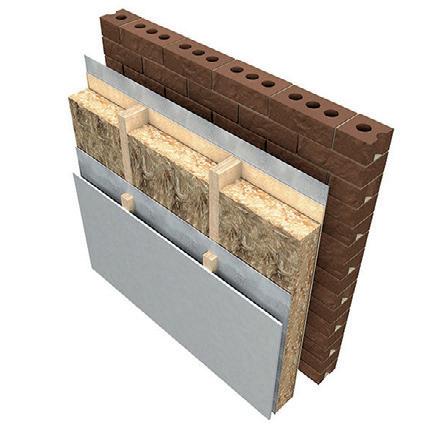
Floor and roof panels known as cassettes can also be prefabricated in the factory, in both open and closed panel construction.
The advantages and disadvantages of each option can be summarised as follows:
Advantages Disadvantages
Less expensive to produce
Faster to fabricate in the factory
OPEN PANELS
Easier to adjust on site
Less expensive to repair if they get damaged in transport or on site
Easier to dry our if they get wet during construction works
Requires less work on site
Quality control of fittings, openings, airtightness and insulation is easier to manage in a factory than on site
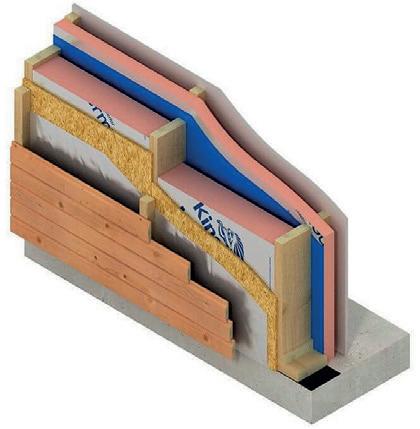
CLOSED PANELS
Less likely to be tampered with by follow-on trades
Doesn’t save as much time on site
Less quality control over the fitting of insulation and membranes on site
Requires more work on site
Can suffer abuse from other trades, eg. notching of timber members
More scope for errors around openings
Requires a detailed design by the manufacturer
Less scope for adjustment on site
More complex to repair if they get damaged in transport or on site
More expensive to produce
More difficult to dry out if they get wet internally during construction works