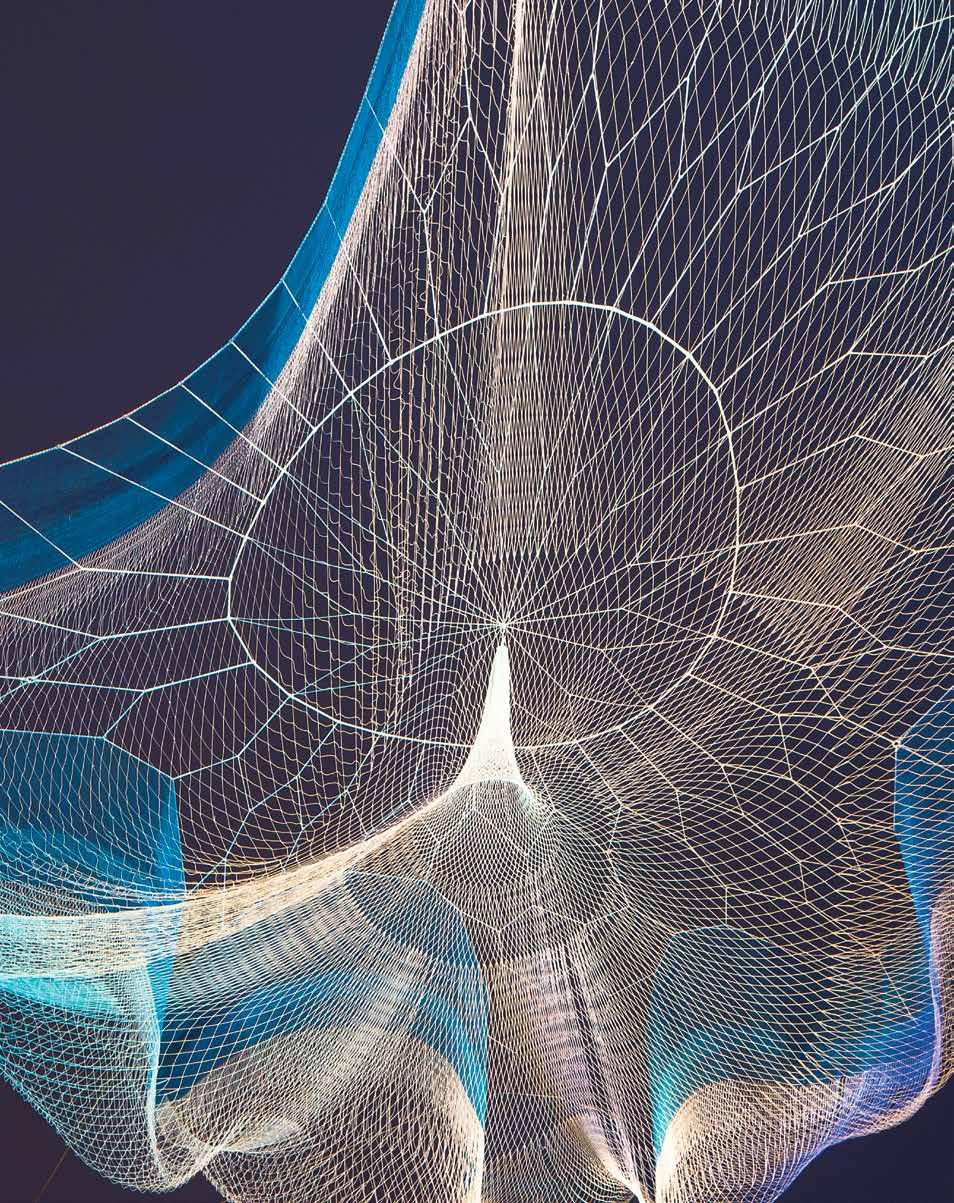
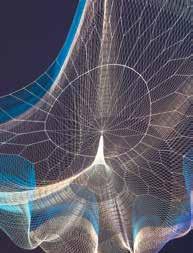
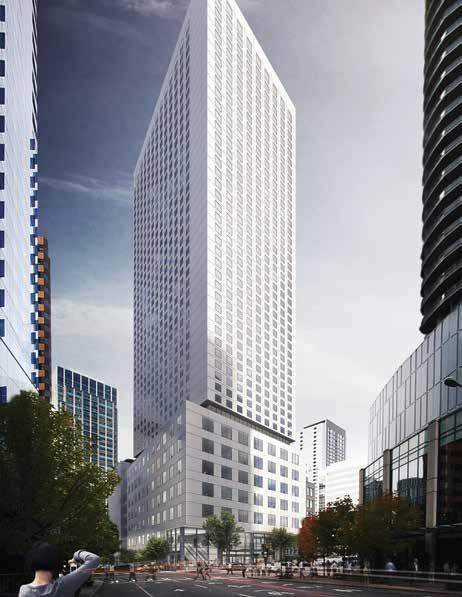
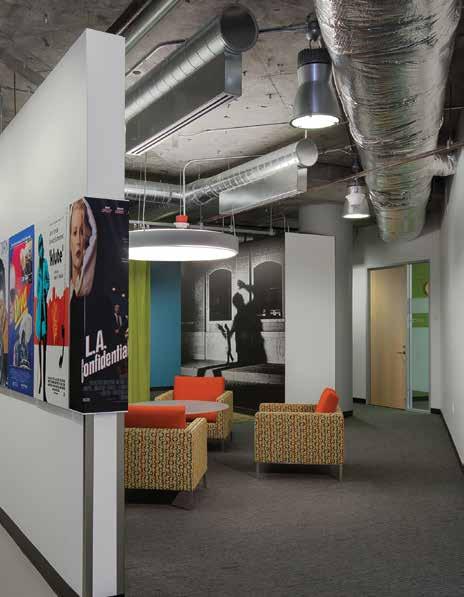
We’ve had more major projects under construction concurrently than any other time in Sellen’s history, and as a result the Sellen family has grown, reaching the 1,000-employee mark for the first time ever. We saw this coming over two years ago, and, knowing that we would be reaching these heights, our leadership team established priorities designed to help us stay true to our values and our vision — to be the best builder in the industry. For one of these priorities, we asked our project teams to improve our lean planning efforts by advancing our culture of continuous improvement and eliminating waste at all our projects. They proved to be up for the challenge.
In this issue, we’ve highlighted some of the pivotal projects and teams that have truly embraced the principles of reducing waste and maximizing value. Many of the processes and tools that they have used are by no means revolutionary — they are standard tools used by others in the industry — but on these projects, Sellen teamed with our clients and design partners to take them to the next level of innovation with resounding success.
On page 6, we’ve told the story of Cirrus, the newest residential tower to grace Seattle’s skyline, and how a combination of foresight, design ingenuity and continuous improvement in the field led to a building that epitomizes the city’s future. We’ve also featured 47+7 on page 12, a six-story apartment building that was literally assembled from hundreds of off-site prefabricated pieces.
And we can’t talk about efficiency without talking about pull planning, a scheduling process that has been a tried-and-true staple on Sellen projects to plan construction activities for nearly a decade. Over the past year, Sellen, R.C. Hedreen Co. and LMN Architects took pull planning to the next level by using it to organize and manage the entire design phase for what will be Seattle’s largest hotel.
With that, I invite you to sit back and enjoy Craft as we commemorate a year of successes and firsts with our partners. Cheers!
Bob McCleskey Chairman and Chief Executive Officer Sellen ConstructionISSUE 5
WINTER 2015
PUBLISHER
Sellen Construction
sellenmarketing@sellen.com
PRODUCTION
Erin Hobson
Amanda Erickson
Connor Davis
Won Moc
Liz Kent
GRAPHIC DESIGNER
Loretta Grande
WITH THANKS TO
Bill & Melinda Gates Foundation
CollinsWoerman
GID Development Group
Greystar
LMN Architects
Museum of Flight
Nell Studio
Pike Place Market Development Authority
R.C. Hedreen Co.
Sean Airhart
Seattle Sounders FC
Sustainable Living Innovations
Town Hall
University of Washington
Wallace Properties
Weber Thompson Architects
SELLEN CONSTRUCTION
227 Westlake Avenue North Seattle, WA 98109
T: 206.682.7770
www.sellen.com
PAPER INFORMATION
100% Post Consumer Waste Recycled
FSC Certified
Green Seal Certified
Green-e (Certified Renewable Energy)
Acid Free
Processed Chlorine Free
This past year has been a banner year for Sellen in more ways than one.
Sounders fans had something new to cheer for with the completion of “The Ninety,” a 2,500-square-foot space in Seattle’s Pioneer Square. Sellen took great care in renovating the previously unoccupied historic building and transforming it into a gathering place where dedicated Sounders fans can celebrate their team and admire trophies and uniforms on display. Televisions and projectors placed throughout the space show team highlights and history.
Fifty years ago, the Museum of Flight was created to preserve the history of aviation and its most impressive artifacts. Now it is one of Seattle’s most popular attractions. The museum has grown extensively since it first opened at the Seattle Center, and Sellen is proud to have been part of that growth. Sellen’s relationship with the Museum of Flight began nearly 15 years ago in 2001 with the construction of the Personal Courage Wing. Since completing the project, the Museum of Flight and Sellen have enjoyed a long-term partnership that has included many unique projects.
In April, the team was reunited for work on the Aviation Pavilion. The 140,000-square-foot pavilion will hold 21 aircraft, including the B17 and B29 bombers, Boeing’s 747 and 787, Air Force One and the Concorde. The project will complete in mid-2016, but the museum is already looking ahead at the next 50 years.
“We are taking bold steps forward to preserve our collections and exhibits, enhance our visitor experience and provide a deeper and more lasting educational impact on the community,” said Doug King, president and CEO of the museum. “We are proud to be working with our tremendous community partners — including Sellen — as we look to the next 50 years.”
In July, crews completed the Montlake Triangle for the University of Washington (UW). Sellen and Gary Merlino Construction built the project as a joint venture. The project involved lowering the Pacific Place roadway, reconstructing part of the Burke-Gilman Trail, and building a land bridge over Montlake Boulevard to facilitate pedestrian and bicycle traffic around the area. The 6.3-acre green space will be the main
thoroughfare for students and commuters traveling among the campus, Husky Stadium and the new light rail station. Landscape architect Gustafson Guthrie Nichol designed the project, which was an owner joint venture among the Washington State Department of Transportation (WSDOT), Sound Transit and the UW. According to Sound Transit and WSDOT, by 2030 approximately 25,000 people will flow through the area each weekday.
The Ninety’s most eye-catching feature is a 2,000-pound glass sculpture custom designed by Dale Chihuly. The vibrant sculpture hangs above a massive, 30-foot table that Sellen built from reclaimed wood. The project, designed by Olson Kundig, began in January and was completed in just over two months.
In January, Sellen began construction on a 20,000-square-foot tenant improvement for Classmates, an online social networking company that connects people to their former classmates. In four months, the Sellen crew demolished the existing space and created a network of open work spaces, a break room and kitchen in Seattle’s Century Square building,
which was also built by Sellen in 1986. Inspired by the client’s name and purpose, JPC Architects incorporated a school theme in the design. Lockers line the hallways, and the reception area features a yearbook wall with book spines from local high schools. One of the spines is actually a secret door, which opens into a meeting space.
“The Ninety has been a fantastic asset for our organization. We continue to find creative ways to grow and utilize the space and provide value to our fans and the community.”
— Sounders FC Business OperationsPHOTO: WON MOC PHOTO: BENJAMIN BENSCHNEIDER PHOTO: WON MOC PHOTO: CONNOR DAVIS
Between downtown Seattle and the gateway to the South Lake Union district stands the dark, curvy Cirrus apartment tower. The tower signifies many things in flux about Seattle, from the recent growth in the technology workforce to the surge of new developments. Without knowing the history behind it, Cirrus could easily be mistaken as yet another high-rise residential tower currently at the center of the Seattle development debate. To do this, however, would be to ignore the teamwork and innovations that went into shaping the building, including residentcentric design and lean construction techniques, making Cirrus not only a successful project but also a unique addition to the Seattle skyline.
This success story begins on the east coast with the GID Development Group. Based in Boston, GID started in 2008 and develops mixed-use and residential urban spaces around the country. The company’s tenet, as expressed by the President of GID Development Jim Linsley, is simple yet rare for a developer.
“We are not merchant builders,” Linsley said. “Our ethos is not to build a commodity product that we develop then quickly sell.”
Fueled by this mindset of finding a long-term investment, GID tied
up a central, visible site for Cirrus on the border of the South Lake Union district in 2011 about a year in advance of the recent surge of developments, showing uncanny foresight. Linsley calls the location of the Cirrus building site a “knot in the middle of the bow tie.”
“It’s where the world of traditional retail, office and the hotel environment merges with the upcoming high tech industries of South Lake Union,” Linsley said. “This is becoming the new gravitational center of Seattle.”
Having decided on a location, GID found innovative partners in Weber Thompson Architects and Sellen to design and construct a building that would be highly desirable to residents.
It is hard to ignore how different Cirrus is when compared to the many monolithic high-rise buildings in downtown Seattle. Cirrus is sculptural in nature, with curves, angles and rectangles. This sculptural massing and shaping of the building resulted from Weber Thompson’s blending of art and science to produce a structure that creates a lifestyle
At the beginning of the project, the Cirrus concrete form and pour team took seven days to complete one level. By the end, they had minimized that time to five days. Here’s how:
The team started out using a “division of labor” approach, a common practice where individual crews focus on specific tasks. The idea was good in theory but not in practice, as the team had trouble viewing the project as a whole. The team members used two primary tools to determine what, if any, adjustments could be made to increase efficiencies. These were:
Shared Resources: Separate crews were eliminated and team members instead worked as a single unit with one goal in mind. Every Friday, they gathered to forecast the workload for the following week. Each team member shifted from task to task on different days to help others get the job done faster.
Visualization Technique: They drew the concrete form and pour process step-by-step in colors on a large architectural plan-view drawing, which enabled them to identify and eliminate unnecessary steps and tasks to make the process as efficient as possible.
instead of just another nondescript residential building.
“The sculptural moves of the tower are purposeful in seeking to capture views from inside out and to relate to the immediate context and greater urban fabric around the building like downtown, Lake Union and the Space Needle,” said Blaine Weber, senior principal at Weber Thompson.
From the start, Weber and his team placed an emphasis on the tenants, a significant departure from the conventional approach to building design.
“As architects, we sometimes pay more attention to aesthetics, and the idea of lifestyle gets lost in
the mix,” Weber said. “But we have an obligation to residents to create places and spaces that are pleasant to live in.”
For example, the team approached the building’s amenity zone as an extension of the individual residential units. Located on the 41st floor, the zone is open to all Cirrus residents. The indoor space includes lounges, game rooms, a theater, exhibition cooking and dining areas, and petfriendly spaces. The outdoor area has a fireplace, garden, koi pond and open-air seating. It is hard not to feel a sense of an urban lifestyle when surrounded by the space’s high-quality finishes and spectacular views.
SQUARE FEET OF CONCRETE POURED PER FLOOR 11,000 NUMBER OF DAYS TO COMPLETE ONE FLOOR
5 CREW MEMBERS NEEDED PER POUR 33
“(The project site) is where the world of traditional retail, office, and the hotel environment merges with the upcoming high tech industries of South Lake Union. This is becoming the new gravitational center of Seattle.”
– Jim Linsley President, GID Development Group
“The social elements are important because this is where people interact and connect,” Weber said.
With the huge growth in technology jobs in Seattle, the demand for residential housing continued to heat up. This compelled GID to find an innovative builder who could quickly and soundly build Cirrus. Sellen emerged as the right partner during the preconstruction phase.
According to Linsley, the Sellen team had to be flexible because of the way that GID typically operates.
“We pick apart and analyze problems and are not afraid to change course when necessary,” Linsley said. “Sellen never looked at that as being frustrating; they always viewed it as serving the client and providing us with the best information possible.”
Taking a page from lean methodology, the Sellen project team established a culture of continuous improvement during construction.
“We were never satisfied with the status quo and consistently looked for ways to sharpen our skills and be more efficient,” said Sellen Sr. Superintendent Jason Barnwell.
This approach translated into measurable efficiencies to meet the aggressive schedule. Using lean concepts such as visualization techniques and shared resources, Sellen crews incorporated efficiencies in their day-to-day processes that enabled them to complete a floor every five days by the time they reached the 10th floor, as opposed to the seven days they needed at the beginning of the project. This reduced man-hours by up to 30 percent.
“We started to look at taking minutes out of every step,” Barnwell said. “Multiply that by the whole crew and you are saving first hours and then days.”
In the end, Sellen responded to the challenging schedule by completing the 335-unit, 41-floor high-rise in just under 27 months.
All the innovation behind the Cirrus project is nothing without results.
Weber Thompson’s design of a lifestyle and tenant-focused space, and Sellen’s construction of a quality residential tower made Cirrus very desirable to residents.
In April, Cirrus was already 11 percent pre-leased. Since the city authorized occupancy in July, it has been 32 percent occupied with 114 people living in the building. As four new Amazon buildings across the street complete over the next few years and Seattle continues to grow, Linsley said he expects it to lease even faster.
“That whole zone is becoming a place that simply didn’t exist and wasn’t even a vision five years ago,” Linsley said.
“They are buildings of their own time, not seeking to copy from another era. They signify buildings of integrity, designed and constructed in this day and age – they are projects designed for the future and not the past.”
– Blaine Weber
SeniorPrincipal, Weber Thompson Architects
Across the street from the newly completed Cirrus, construction of a sister building, Stratus, started in July and will complete in January 2018.
“While Cirrus is dark and very masculine, and Stratus is light and almost feminine, the two are nonetheless complementary,” Weber said.
Stratus will be very similar to Cirrus but with some differences in aesthetics, massing and finishes. Overall, Stratus will be bigger with 396 units (40 more than Cirrus) and 43 stories (two stories taller than Cirrus). An outdoor plaza area will link the two buildings.
To leverage the camaraderie and teamwork established during the Cirrus project, GID hired the same team for the design and construction of Stratus, including the majority of the sub-consultants and subcontractors. The opportunity of constructing a similar building across the street from Cirrus creates new and exciting chances to innovate.
“We are expecting all the lessons learned, experiences and successful relationships to carry over to the next project,” said Bill Badger, Sellen’s project director. “This will allow us to look for new ways to be efficient in our approach and execution.”
Knowing the story behind the design and construction of Cirrus and looking ahead to the rise of Stratus, it is hard to categorize each as just another nondescript high-rise tower. Cirrus defies conventional stereotypes, and Stratus will reinforce that notion.
“They are buildings of their own time, not seeking to copy from another era,” Weber said. “They signify buildings of integrity, designed and constructed in this day and age — they are projects designed for the future and not the past.” ■
OPPOSITE PAGE: The shared indoor space includes lounges, game rooms, a theater, exhibition cooking and dining areas, and pet-friendly spaces
THIS PAGE: The outdoor social area features views of downtown Seattle, Lake Union and Puget Sound
In May of 2014, the team of R.C. Hedreen Co., LMN Architects and Sellen began designing what will be the largest hotel in Seattle at the corner of 8th Avenue and Howell Street. The design process, however, held one significant departure from tradition: the team used pull planning to guide the entire design phase, setting in motion a higher level of integration, coordination and efficiency.
“Pull planning was our main tool in this project,” said Paul Davison, project designer with LMN Architects. “It got everyone talking and that’s one of its greatest successes.”
Pull planning is not new to the industry. The lean scheduling tool is traditionally used by contractors during the construction phase to develop the schedule and sequence activities to be as efficient as possible, thus embodying the lean tenets of reducing waste and maximizing value. Designers also use it to evaluate the schedule at specific milestones.
For this project, however, Hedreen, LMN Architects and Sellen decided to take pull planning to another level in two significant ways. They used the tool to reorganize and actively manage the design process, from design development to construction documents, and they also involved key subcontractors early to participate in a design-assist role. Using pull planning to this extent was a first for all team members, and it demanded a commitment from the very beginning.
In pull planning, all stakeholders involved in a specific scope or phase outline every deliverable needed to reach the deadline. Each deliverable is assigned to someone who estimates the time it will take to complete it and handwrites it on a sticky note.
Working backward from the end date, the team then sequences each deliverable based on the necessity — or “pull” — of the downstream deliverables. This process, and the
resulting posted sticky notes, form the foundation of a schedule with little redundancy, an efficient workflow and clear assignments.
The decision to use pull planning was in part from a desire by Sellen to promote team integration, as well as a necessity borne out of the sheer size of the project.
“We’ve seen real value when everyone on the team is committed to an integrated design and construction process,” Sellen CEO Bob McCleskey said. “We are promoting design-build delivery and using lean tools on many of our projects to improve overall project delivery and communications.”
To help facilitate and kick off the pull planning, the team brought in a lean consultant. They spent two days building the schedule and setting the foundation for the process.
Throughout the next 15 months of design, leaders from all major disciplines — including the owner and key subcontractors — would meet every three weeks, assess
Some are milestones, some are deliverables — all are simple sticky notes — but behind each one is a commitment.
IMAGES: RENDERINGS COURTESY OF LMN ARCHITECTSTOP: Rendering of the street level entry on 8th Avenue and Howell Street OPPOSITE PAGE: R.C. Hedreen Co.’s new 45-story hotel will be the largest in Seattle when completed
upcoming deadlines, and “pull” them, developing detailed deliverables for the approaching milestones. LMN Architects led a weekly conference call to review progress, address delays and tackle potential impacts. Davison said there was a learning curve, but they were eventually able to scale a 40-minute weekly check-in down to 15 minutes.
“Every project is a prototype, and at the start you’re creating the right process for that project,” Davison said. “Continuing to use this meant that people reconnected … and it allowed us to learn and improve our process.”
As with every prototype, managing the design with pull planning was not without its challenges. Davison said many revolved around the fact that design does not always follow a linear process but is instead an iterative one. This sometimes made it difficult to break down design work into small, discrete deliverables that could be resolved within a set timeline.
To help estimate the durations for each deliverable the design team relied on historical data and past experiences while Sellen provided continuous cost estimating.
Overall, Davison said using pull planning changed the way LMN Architects organized the design phase. For example, certain scopes were designed and bid out earlier than usual because they were needed to allow other disciplines to meet their deadlines and keep the project moving forward.
“You’re more cognizant of when the information is critical, so you’re not having people draw things too early that may need to get reworked when more information comes down the line,” said Hedreen’s Vice President of Design Shauna Decker. “You’re really looking at the project holistically from all disciplines; it was definitely time well spent.”
All agreed a primary benefit that came from committing to pull planning was increased team integration and coordination. Decker said that by bringing the major trades on during design development, systems
were well integrated and able to be designed to the budget early, as the construction drawings were, in some cases, the shop drawings. She hopes this level of coordination will avoid many issues that would have otherwise come up in the field where solutions often become more limited and expensive to resolve.
“Pull planning was essential in the amount of collaboration that the team has had, getting into ‘the big room’ every three weeks and collectively mapping out the project,” Decker said. “I think it made for a more efficient process.”
By the end of design, the sticky note had become more than just a simple piece of paper — it represented a promise, a handwritten commitment made by all team members to both the process and the project.
“There’s an idea of this promise note,” Davison said. “I could say it’s a deliverable, but it’s different when somebody says that they will promise to do something.
“A ‘deliverable’ just suggests that you’re handing something over, and it doesn’t necessarily speak to quality; a promise speaks to having done something physically and personally delivering on that promise.”
Both Decker and Davison said they would definitely consider using this same process on future projects. But with construction finally beginning on the hotel in August and set to complete in summer 2018, their sights are set on the more immediate future.
“It has been a bit of a heroic effort getting here, and I am so appreciative of our entire team,” Decker said. “I’m excited to see what we’ve done on paper become a reality.” ■
the project holistically from all disciplines;
was definitely time well spent.”
SQUARE FEET
1,470,168
STORIES
45 GUEST ROOMS
1,260 SQUARE FOOTAGE OF EACH OF THE TWO BALLROOMS
20,000 PURSUING LEED CERTIFICATION
GOLD UNDERGROUND PARKING STALLS
450
“You’re more cognizant of when the information is critical. … You’re really looking at
it– Shauna Decker Vice President of Design, R.C. Hedreen Co.
collaborated to deliver 47+7, an apartment building unlike any other in Seattle.
BY: CONNOR DAVIS PHOTOGRAPHY: WON MOCImagine opening a puzzle box and finding that the individual, unsorted pieces you were expecting to find have instead been pre-assembled into larger sections, ordered sequentially so that each fits neatly with the section below. Suddenly, a project that could have taken hours has been reduced to a matter of minutes.
Now imagine applying this same concept on a larger scale — six stories tall and 13,000 square feet, to be precise. This was the goal that Sustainable Living Innovations (SLI), CollinsWoerman and Sellen set out to achieve with the new “47+7” apartment building in Seattle.
THIS PAGE: The building features distinctive, exposed steel beams, columns and concentric braced frames
OPPOSITE PAGE: An inside look at the efficiently designed layout of each unit
Like many groundbreaking ideas, SLI can trace its origins back to a garage.
“Mark and I used to have our strategy sessions in the parking garage,” said Arlan Collins
of his discussions with fellow CollinsWoerman and SLI co-founder Mark Woerman. “We would walk out of the office and talk for hours, just standing there in the garage, coming up with ideas.”
It was during one of these talks in 2008 when Arlan and Mark began discussing an entirely new way of designing and building.
“Our vision was to make buildings truly green — using half the energy, half the water, half the time to build — and improving the quality of living in each unit,” Collins said.
To reach these goals, they would rely heavily on prefabricated parts manufactured in a controlled environment, away from the job site. This idea led to the genesis of SLI, a multifamily housing technology company, and marked the beginning of the 47+7 apartment building’s seven-year journey from concept to reality.
After several years of development, the SLI team hit its first major milestone in 2011: the completion of a two-bedroom prototype.
“It took three years of a lot of hard work by a lot of people,” Collins said, referring to the 25 different companies that helped create the original prototype.
The unit was built with a kit of parts that were prefabricated off site and assembled inside a warehouse in Seattle’s SoDo district. The wall panels arrived with all of the plumbing, electrical and sprinklers pre-installed, requiring only a few connections to form a functioning mechanical and electrical system. Once assembled, these high-quality components created a four-star living space.
The initial prototype met the original goals — reducing waste and expediting construction schedules — but it still needed some fine-tuning.
“The look, fit, finish and structure were right,” Collins said. “But the parts didn’t perform at the expected level.”
The team went back to the drawing board, building upon what they had learned from the first prototype. After another three years of retooling, SLI was ready to bring its vision to fruition. 47+7
With six years of development behind them and a full team ready to turn concept to reality, all that was needed was an investor. The team found one in Wallace Properties, which provided funding for the project.
“It showed a lot of promise for the future,” said Kevin Wallace, president and chief operating officer of Wallace Properties. “We were interested to see how the concept proved out.”
The site was located on the corner of Northeast 47th Avenue and 7th Avenue Northeast in Seattle’s University District. Named after the intersection, 47+7 would be a 24-unit, six-story apartment building. Each one-bedroom unit was a smaller version of the prototype developed in SoDo, prefabricated with the utmost quality and carefully assembled on site. Now the team just needed to put it all together.
Learning the intricacies of SLI’s technology took some time for Sellen’s crews during the early stages. However, the installation sequence of the prefabricated panels was nearly identical on each floor, allowing the team to streamline its processes as the project went on. According to Sellen Senior Project Manager Adam Rohde, installing floor panels took nearly a day on the first level but less than an hour once they reached the top floor.
“It was easy to get excited about the job,” Rohde said. “It was an outof-the-box, innovative approach to putting the puzzle together in a totally different way.”
Through continuous improvement, the team achieved its goals for quality and schedule. The crew celebrated the topping out in December 2014, just four months after breaking ground. Completed in March 2015, the finished product was a visually striking building with 24 high-quality units, built with an accelerated schedule and ready to perform at a high level.
Today, every unit in the new 47+7 building has been leased, and it operates on less electricity than
similar multifamily buildings. Features such as solar panels, which provide much of the building’s hot water, and ultra-efficient appliances and light fixtures make residents proud to call 47+7 their home.
“Every resident is invested — not just in the look of the building but what it stands for: living a greener, healthier lifestyle,” said Crystal Lash, community manager at 47+7. “There’s a ‘wow’ factor because there’s nothing else quite like it on the market.”
In the end, 47+7 proved that SLI’s technology could attain its goals: reducing waste, cutting down construction schedules, and resulting in a high-quality end product that could be quickly brought to the market.
“It was a great effort by everyone to do something as pioneering as this,” Wallace said. “We’ve made a contribution to the future of construction and sustainability that the whole team should be proud of.”
And they’ve only just scratched the surface of its potential.
SLI is currently preparing for its next wave of projects around the country, including a 40-story apartment building in Seattle, a 15-story lowincome building in Honolulu and three projects in downtown San Francisco.
“We couldn’t be happier about how it’s taking shape and how the market is responding to it,” Collins said. “This idea that we can manufacture a building has been around since the 1930s. The fact that we finally got it done and that it has gone so well is due to the incredible effort of everyone on the team.” ■
Step
On-site crews poured the concrete foundation and set the precast elevator cores.
“Every resident is invested — not just in the look of the building but what it stands for: living a greener, healthier lifestyle. There’s a ‘wow’ factor because there’s nothing else quite like it on the market.”
–Crystal Lash, Community Manager at 47+71: Step 2: Steel columns and beams for the exposed frame were hoisted and bolted together, requiring no welding at the job site. Step 3: Prefabricated panels, manufactured in an off-site warehouse, were securely attached to the structure to form the floor and three of the walls. Step 4: Once the top floor of panels was finished, workers installed floor-toceiling glass on the remaining wall.
Location: Seattle, WA
Square Footage: 221,859
Architect of Record: IA Architects
This 15-floor tenant improvement project consisted of office improvements and an employee break area. The office features cinematic elements as a tribute to the once-neighboring King Cat and UA 150 theaters. Each floor was designed to pay homage to a specific movie genre, including comedy, western,
Interior Architect: SABArchitects
Interior/Graphic Designer: Nell Studio
Opened for Business: July 2015
action, mystery, science fiction and horror. Custom marquee signs were installed in every floor, which allow each department to literally spell out its own messages. Other key features include posters from iconic films, classic movie quotes and “popcorn” ceilings, giving the office a true movie theater feel.
CLOCKWISE FROM LEFT: Breakout meeting area on the mystery themed floor; a four-person conference room featuring mob movie posters; a meeting center staging area lined with iconic movie quotes; a science-fiction themed meeting space
PHOTOGRAPHY: CLEARY O’FARRELL
“Movies are universal and everyone has their favorite movie quote. We wanted the space to be a fun and lively work environment to promote interaction and dialogue. Who doesn’t love going to the movies?!”
– Nell Sanger Interior Designer, Nell Studio
YEAR SPAN OF MOVIES
FEATURED FROM 1969 - 1999
30
MOVIE POSTERS
300
MOVIE QUOTES
2,230
ORIGINAL KING CAT THEATRE MARQUEE SIGN
1
After starting her career as a temporary project assistant more than two decades ago, Carrie Boettcher is dedicated to helping project teams be at their very best, from start to finish.
BY: CONNOR DAVIS PHOTOGRAPHY: LORETTA GRANDE / WON MOCAt a time when you’re as likely to see a tower crane in Seattle as you are a raindrop, keeping a wide variety of projects running smoothly is critical. That’s where Sellen’s Field Support Director and Vice President Carrie Boettcher comes in.
Boettcher plays a vital role at Sellen, tasked with continuously seeking to improve Sellen’s field operations. She might not have ended up at Sellen, however, if not for a phone call and a piece of advice from a stranger two decades ago.
Born and raised in Massachusetts, Boettcher received her associate degree in art but said she wasn’t sure where to go from there. She tagged along with a friend who was moving to Seattle, signed up for work with a temp agency and waited for the phone to ring.
“I remember the woman from the agency calling and saying they had a job for me in Auburn,” Boettcher said. “She told me it was an opportunity to work for a great company called Sellen Construction, and that I should really consider it.”
She started her career with Sellen as a temporary project assistant in 1995 at what would become Emerald Downs. Boettcher joined Sellen permanently after a year and enrolled in the University of Washington’s construction management program working as an engineer on various projects for a decade.
Carrie Boettcher Vice President, Field Support Directorknack for personnel development with her passion for work in the field.
“Scheduling and lean go hand in hand, so it made sense to move into a position that supported both,” Boettcher said. “At that point, I felt like I was where I was meant to be.”
In 2014, Boettcher moved into her current role to become the foremost champion of Sellen’s lean efforts.
Sellen’s first hands-on experience with lean came in 2008 at the Seattle Children’s Hospital Bellevue Clinic and Surgery Center project. For some who had been in the construction industry for decades, buying into the new concept took time.
fundamental tenets — collaboration, reduced waste and innovation — had been deeply ingrained in Sellen’s culture for a long time.
“Lean is just an extension of who we are,” Boettcher said. “We’re constantly pushing to be collaborative, to be better at what we do and to learn from each other so that mistakes are never repeated. It gets into your blood and becomes who you are.”
And the benefits of lean extend beyond just Sellen. After seven years of seeing lean tools used in the field, Sellen’s partners have taken notice.
She next transitioned to a training and development role in 2007, working with superintendents to implement planning and scheduling techniques. She also began learning about the principles of lean, a style of management that increased collaboration and reduced waste.
When a scheduling position at Sellen opened up in 2011, it was a unique opportunity to combine her
For example, at Sellen’s Swedish Issaquah Campus project in 2011, one of Sellen’s most experienced superintendents had his doubts about using lean methods. Boettcher was working with that project team and remembered his turnaround.
“He was against lean at the beginning and totally convinced of its merits by the end,” Boettcher said. “For him to say that you can teach an old dog new tricks was pretty moving.”
With each project, it became apparent that though Sellen had only officially adopted lean in 2008, its
“Lean tools have helped our clients prioritize decisions and make them in a timely manner,” Boettcher said. “Subcontractors ask our superintendents when they’re going to start pull planning and developing weekly work plans because they know how well it works.”
With continuous improvement being another pillar of lean practices, Boettcher’s work is never truly done, but she enjoys the challenge.
“I like being able to help superintendents by making something easier or helping to address a problem they’re facing,” she said. “That’s why I get up in the morning.” ■
“We’re constantly pushing to be collaborative, to be better at what we do and to learn from each other so that mistakes are never repeated. It gets into your blood and becomes who you are.”
Even from a young age, Lynn Perkins was always looking to push the limits. As a child she loved architecture, but architecture was a man’s profession in the 1960s, so she pursued an undergraduate degree in biology instead. Her first professional position was a sixyear stint as an assistant publicist for CBS News and Public Affairs broadcasting, but she said she ultimately had to acknowledge that she didn’t resonate with the product.
“I decided if I was turning my back on a plum job and not using my degree, I should figure out what I would like to do,” Perkins said. “So I took some time off from the normal career trajectory and started building houses.”
Very few women were in the construction trades in the 1970s. Being “very handy” and a “great connector,” Perkins put together a group of women in the trades — one of several women-centered groups she has formed over the years. One of the women in this group was a tile setter and taught Perkins the trade, which she pursued for five years.
With this renewed love of building, she decided to finally pursue a degree in architecture beginning at the University of New Mexico, one of the few schools researching solar technology at the time. Perkins moved to the University of Washington to finish her master’s degree, and her
first position the summer she arrived was as a tile setter with Western Tile.
Perkins built an expertise in designing laboratory projects and got a job as a project manager for the Fred Hutchinson Cancer Research Center. She said she loved the technicality of science facilities, but a recruiting call from the Bill & Melinda Gates Foundation to help manage the design and construction of the new campus proved too hard to refuse.
“The opportunity was irresistible, both in terms of the project and for the possibility of amplifying my personal impact in making a difference in the world,” Perkins said.
Perkins joined the foundation in 2006 at the same time as Sellen was beginning preconstruction on the new campus, which was occupied in April 2011. The foundation was experiencing rapid growth and needed a new, dynamic space.
The Global Development Division had just formed, and Warren Buffett had just doubled the foundation’s endowment with a gift of $37 billion. At that point, the foundation was giving away $1.5 billion per year. Buffet’s gift doubled that amount immediately.
“The campus itself is as complicated as the science world. … It’s exciting, it’s challenging and what I get to do supports the work of the foundation,” Perkins said. “I don’t get to make policy, I don’t get to hire experts from around the world or write grants, but I do get to support
“I have been privileged to be able to follow my bliss throughout my career in a number of different fields, backed by a good education and lots of opportunities that were open to me. Everyone deserves chances like those I’ve had.”
a mission I deeply care about: to ensure everyone has the opportunity to live a healthy and productive life.”
Once the campus was complete, Perkins said the foundation began envisioning an iconic art piece that could tie the two buildings together and “live at the heart of the campus.” The campus artwork curator, Richard Andrews, and Melinda Gates knew of the artist Janet Echelman’s work.
After commissioning Echelman, Perkins worked with the artist for three years from idea to unveiling. The result was the Impatient Optimist, a sculpture named after Bill Gates’ biography published in 2012.
In February of 2015 a Sellen team installed the sculpture, which now hangs between the two U-shaped buildings above the campus courtyard. The art is intended to capture the essence of the foundation and its work.
The artist sought to represent a healthy productive life as seeing each day in its fullest color, so she took a 24-hour time-lapse of the Seattle sky and graphed its color saturation radially as a three-dimensional form. Knots are meant to represent the number of lives that can be affected by a single person — the impact that an individual working for the foundation can make. It’s also reminiscent of bed netting, which helps protect people from mosquitos carrying malaria, a primary focus of the foundation. The sculpture is lit from dusk to dawn. Lighting is keyed into the sunrise conditions at the foundation’s offices around the world and each location is represented by a different color palette.
“It’s something you need to look up at; it’s aspirational representing possibility; it’s optimism,” Perkins said.
A few years ago, Melinda Gates, knowing that the status of women and girls in the world is critical to advancing the human community, directed that all grants and strategies be viewed through a gender lens to make sure that gender inequalities were not getting in the way of desired impact. Having gone through the women’s equality movement of the 1970s,
Perkins said she found this prospect exciting and extremely moving.
“No society can achieve its potential with half of its population marginalized and disempowered,” Perkins said.
In one example Perkins offered, the foundation is working with women in Africa who do most of the child rearing and household and agricultural work to increase agricultural yields and enable them to save money.
“If you empower women to save money … they pay for school fees, they buy school uniforms,” Perkins said. “It has a huge impact.”
Many of the conversations at the foundation now focus on the advancement of women and girls worldwide in both subtle and overt ways. Throughout her life and career, Perkins has focused on equality and making an impact in this world.
“I have been privileged to be able to follow my bliss throughout my career in a number of different fields, backed by a good education and lots of opportunities that were open to me,” Perkins said. “Everyone deserves chances like those I’ve had.” ■
The Bill & Melinda Gates Foundation created Global Citizen, a new website initiative, with the notion that all citizens have a role to play in their communities and on this planet.
There are a billion people all over the world trapped in extreme poverty. For the first time in history, there are people that believe that can be changed. That’s what Global Citizen does — inspires people with success stories from all over the world.
“People have a natural drive to want to help others,” Perkins said.
“People forget how good it feels to help others — we forget how big an impact we can have on other people’s lives.”
Find out how you can inspire: globalcitizen.org
Sellen+ was an idea long in the making. In past years, Sellen has hosted educational networking events that covered topics such as sustainability and virtual design. Sellen+ is the next iteration of these events, taking them one step further by showcasing Sellen’s communityfocused projects and the people behind them. The goal of the series is to bring our partners and community organizations together for conversations around the important and impactful work happening in the Puget Sound area.
“We are in a unique position to connect diverse groups of people,” Sellen President Scott Redman said. “Our vision for the program is to create a more robust dialogue around the work being done by some of the leading organizations in our community and how that work might impact the real estate, design and construction industry.”
The first official Sellen+ event took place in May and featured Ben Franz-Knight, the executive director of the Pike Place Market Preservation and Development Authority. FranzKnight offered an inside look at the Market, beginning with its humble start as a series of local produce stalls to its establishment as one of the city’s most iconic attractions. He also spoke about the current MarketFront expansion and the impact that the long-awaited transformation will have on the community. Partners from across the
A/E/C industry, including the Miller Hull Partnership and Vulcan, were in the audience.
“I came away from the experience understanding that Sellen’s commitment to community starts with an investment in their own people and that ... the greater Sellen team knew and understood our project,” Franz-Knight said.
The next Sellen+ program will be a discussion about community leadership. The panel will consist of leaders who have chosen to engage in their communities through volunteerism, leadership and
If you are interested in learning more about Sellen+, have an idea for a topic, or would like to attend the next event, please contact our marketing team at sellenmarketing@sellen.com. We hope to see you at the next Sellen+ event.
philanthropy. While different in format, the discussion will again be topical and intriguing to a mixed audience.
“Sellen+ will be different every time,” Redman said. “We hope to help our clients and partners as they seek to have their stories told.” ■
“We are in a unique position to connect diverse groups of people.”
– Scott Redman President, Sellen Construction
PHOTO : COURTESY OF MOHAI
McKinstry
Metals Fabrication Company
Morrow Equipment Company
Moss Adams
Nelson Electric
Norkote
Northshore Sheet Metal
NorthStar CG
Northwest Construction
Olympia Sheet Metal
Olympian Precast
Olympic Interiors
OxBlue Corporation
Pacific Construction Supply
Pacific Earth Works
Paco Ventures
Parker Smith & Feek
Patriot Fire Protection
PCS Structural Solutions
Pederson Bros.
Performance Dimensions Group
Peri Formwork Systems
Perkins+Will
Pine Street Group
Pioneer Masonry Restoration Company
Port Tension Cables
Pozzi Bros. Transportation
Prime Flooring
Prime Electric
PSF Mechanical
Puget Sound Steel Company
Purcell Painting & Coatings
Ralph’s Concrete Pumping
RPM Steel
S.P.E.C.
Salmon Bay Sand & Gravel Company
Seaport Steel
Seattle’s Finest Security & Traffic Control
Seneca Group
Sequoyah Electric
Sessler
SGS Glass Company
Smith Fire Systems
Snap-Tex Northwest
Snyder Roofing
Star Rentals
Steel Encounters
Stirrett-Johnsen
Stoneway Concrete
Stoneway Electric
Synergism Stone
Systematic Supply
T-Bar Construction
Technical Waterproofing
The Erection Company
Titan Electric
Treble Interiors
University Mechanical Contractors
United Rentals
U.S. Bank
Valley Electric
VECA Electric
Walters & Wolf
Washington Commercial Painters
Washington Glass & Glazing
Water Tectonics
Western States Fire Protection
Western Tile & Marble
Yakima Steel
ZGF Architects
“Safety is caring about people first and productivity second.”
Matt Waid, Carpenter Foreman